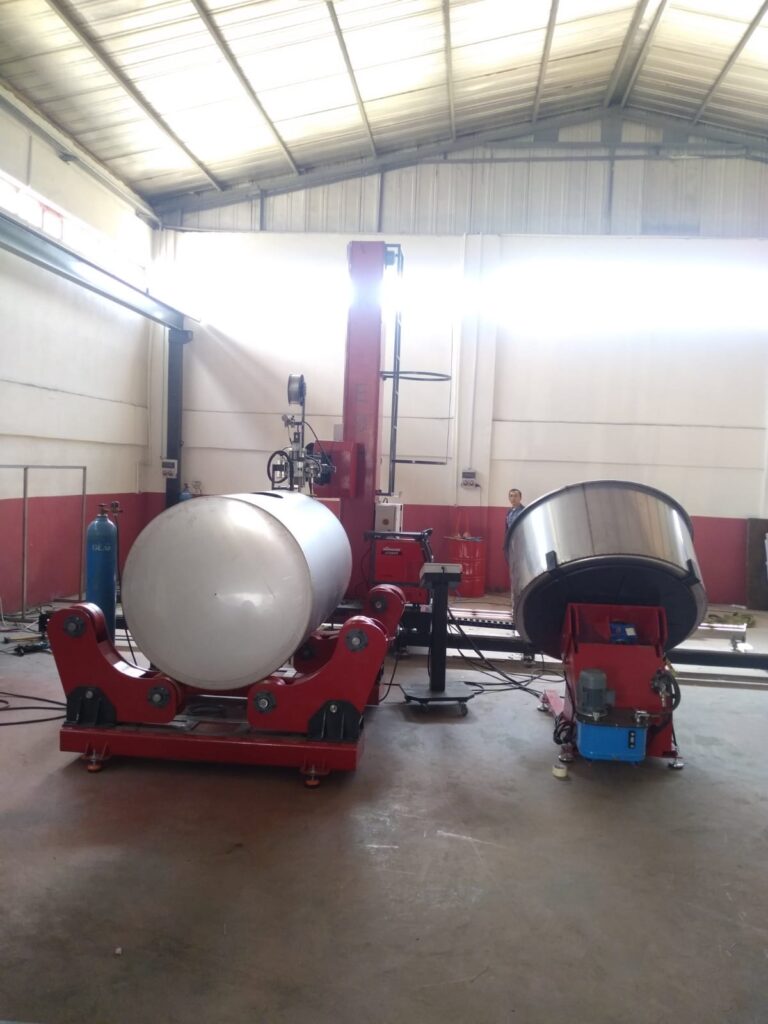
Sistemas de Soldadura de Unión Circular: Los sistemas de soldadura son procesos utilizados para unir materiales, típicamente metales o termoplásticos, a través de la aplicación de calor, presión o ambos, con o sin la adición de material de relleno. Los sistemas de soldadura son fundamentales en la fabricación, la reparación de componentes y estructuras, y se utilizan en una amplia gama de industrias, desde la automotriz hasta la construcción, la energía, y la aeroespacial. Aquí hay una descripción general de algunos de los sistemas de soldadura más comunes:
Soldadura por arco eléctrico (SMAW – Shielded Metal Arc Welding)
- Proceso: Utiliza un electrodo revestido que genera un arco eléctrico entre el electrodo y la pieza de trabajo. El calor del arco funde el material base y el electrodo, creando una unión.
- Ventajas: Es versátil, económico y se puede usar en diversas posiciones.
- Aplicaciones: Usado en la construcción de estructuras metálicas y en reparaciones industriales.
2. Soldadura MIG (Metal Inert Gas)
- Proceso: Se utiliza un gas inerte (como el argón) para proteger el metal fundido del aire. Se emplea un alambre de electrodo consumible como material de relleno.
- Ventajas: Alta velocidad de soldadura, fácil de usar y adecuado para materiales finos.
- Aplicaciones: Ideal para soldaduras de acero inoxidable, aluminio y metales no ferrosos.
3. Soldadura TIG (Tungsten Inert Gas)
- Proceso: Emplea un electrodo de tungsteno no consumible para crear el arco eléctrico, y el material de relleno se alimenta manualmente. Se utiliza un gas inerte para proteger el área de soldadura.
- Ventajas: Produce soldaduras limpias, de alta calidad y controladas.
- Aplicaciones: Se utiliza en metales delgados, acero inoxidable, aleaciones de alta resistencia y en aplicaciones aeroespaciales.
4. Soldadura por resistencia (Spot Welding y Seam Welding)
- Proceso: Utiliza la resistencia eléctrica para generar calor que une dos piezas de metal. Se aplica presión para que las piezas se fusionen.
- Ventajas: Es rápida, eficiente y adecuada para soldaduras de producción en masa.
- Aplicaciones: Se utiliza ampliamente en la industria automotriz, para la fabricación de paneles de carrocería.
5. Soldadura por láser
- Proceso: Utiliza un láser de alta intensidad para fundir el material y crear la unión.
- Ventajas: Gran precisión, alta velocidad de soldadura y baja distorsión térmica.
- Aplicaciones: Soldaduras en aplicaciones de alta tecnología, como la electrónica, aeroespacial y la fabricación de componentes médicos.
6. Soldadura por ultrasonido
- Proceso: Emplea ondas ultrasónicas para generar calor y fusionar las piezas de trabajo.
- Ventajas: Es rápida, limpia y se utiliza principalmente para unir plásticos y metales delgados.
- Aplicaciones: Industria de electrónica y automotriz, especialmente en componentes pequeños.
7. Soldadura a gas (OAW – Oxy-Acetylene Welding)
- Proceso: Se utiliza una mezcla de oxígeno y acetileno para producir una llama que funde los materiales a unir.
- Ventajas: Bajo costo y versatilidad.
- Aplicaciones: Reparaciones y soldaduras de metales no ferrosos, y en algunas aplicaciones de artesanía.
8. Soldadura por fricción
- Proceso: Utiliza la fricción generada por el movimiento relativo de las piezas para generar calor y fusionarlas.
- Ventajas: Proceso sin material de relleno, con alta eficiencia energética y sin la necesidad de protección de gas.
- Aplicaciones: Usada en la industria aeroespacial, automotriz y para la unión de metales difíciles de soldar.
9. Soldadura por arco sumergido (SAW – Submerged Arc Welding)
- Proceso: Se genera un arco eléctrico bajo una capa de fundente en lugar de un gas inerte. El fundente protege el charco de soldadura.
- Ventajas: Alta velocidad de soldadura y penetración profunda.
- Aplicaciones: Ideal para la fabricación de grandes estructuras de acero y tuberías.
10. Soldadura por plasma
- Proceso: Similar a la soldadura TIG, pero utiliza un arco de plasma para una mayor precisión y control.
- Ventajas: Produce soldaduras finas con alta calidad y control en el proceso.
- Aplicaciones: Usada para materiales delgados y en aplicaciones precisas.
Estos son solo algunos de los principales sistemas de soldadura utilizados en la industria. Cada uno tiene sus propias ventajas y limitaciones, y la elección del sistema adecuado depende de factores como el tipo de material, el grosor de las piezas, la calidad de la soldadura deseada y el entorno de trabajo.
Los sistemas de soldadura son fundamentales en diversas industrias, pues permiten unir materiales de manera duradera y confiable. A lo largo de los años, se han desarrollado diferentes técnicas, cada una adaptada a necesidades específicas. La soldadura por arco eléctrico es una de las más utilizadas, con procesos como SMAW, MIG y TIG, que ofrecen flexibilidad en cuanto a materiales y posiciones de trabajo. Mientras tanto, la soldadura por resistencia se destaca en la producción en masa debido a su rapidez y eficiencia. Por otro lado, la soldadura láser y por ultrasonido, aunque más avanzadas, se utilizan en aplicaciones de alta precisión, como la electrónica y la aeroespacial. Técnicas más tradicionales como la soldadura a gas siguen siendo populares por su bajo costo y versatilidad. En términos de eficiencia y rapidez, la soldadura por fricción y por arco sumergido sobresalen, especialmente en la construcción de grandes estructuras metálicas. Sin embargo, la elección del sistema de soldadura ideal depende de varios factores, incluyendo el tipo de material, la geometría de las piezas y el ambiente en el que se trabaja, siendo clave encontrar el proceso que mejor se adapte a las especificaciones del proyecto.
En la evolución de los sistemas de soldadura, se ha observado un enfoque creciente en la automatización y la mejora de la eficiencia. Los sistemas robotizados de soldadura, por ejemplo, han permitido aumentar la precisión y la consistencia en las uniones, reduciendo el riesgo de defectos y mejorando la calidad general de las soldaduras. Estos sistemas son particularmente útiles en industrias como la automotriz, donde se requieren altas tasas de producción y precisión.
Además, la tecnología de soldadura está cada vez más orientada a la sostenibilidad, con procesos como la soldadura de arco sumergido que minimizan la emisión de contaminantes y el uso de materiales auxiliares. La preocupación por la eficiencia energética también ha impulsado el desarrollo de técnicas como la soldadura por láser, que utiliza energía de manera más eficiente al centrarse en una zona muy pequeña de la pieza.
Otra tendencia importante es la investigación en nuevas aleaciones y materiales para soldar. Con el avance de la ciencia de los materiales, las industrias están utilizando metales de alto rendimiento, como las aleaciones de titanio y materiales compuestos, que requieren técnicas de soldadura especializadas. Esto ha dado lugar a la adaptación de sistemas existentes, como el TIG o el MIG, para trabajar con estos nuevos materiales, o el desarrollo de nuevos métodos, como la soldadura por fricción-agitación, que es adecuada para unir materiales como el aluminio y las aleaciones de magnesio sin la necesidad de relleno.
La soldadura también está cada vez más conectada con la digitalización. Las técnicas de monitoreo en tiempo real y el análisis de datos permiten a los operadores obtener información sobre el proceso de soldadura, mejorando la calidad del producto final y reduciendo los costos asociados con los errores. Esto se logra a través de sistemas que analizan variables como la temperatura, la velocidad de avance y la cantidad de material fundido, proporcionando retroalimentación instantánea al operario.
Con todo esto, los avances en soldadura no solo están enfocados en mejorar los procesos técnicos, sino también en hacer que estos sean más accesibles, seguros y adaptables a una gama más amplia de materiales y aplicaciones. Esto sigue transformando la industria, permitiendo la creación de productos más complejos, ligeros y duraderos, desde componentes electrónicos hasta partes de aeronaves y vehículos de alta performance.
A medida que la tecnología de soldadura continúa avanzando, también lo hacen los métodos de control y monitoreo que permiten a los operarios mejorar la precisión y la eficiencia del proceso. Los sistemas de soldadura moderna no solo requieren un control técnico en términos de la ejecución del proceso, sino también un enfoque más profundo en la calidad y la trazabilidad. Las innovaciones en sensores y software permiten obtener datos en tiempo real sobre los parámetros de la soldadura, como la temperatura del arco, la velocidad de avance y la presión ejercida, los cuales pueden ser analizados para optimizar cada aspecto de la unión. La integración de esta información en un sistema de monitoreo centralizado permite a los operadores realizar ajustes inmediatos y evitar fallos en la soldadura, lo que resulta en un mejor control de calidad, menores tasas de defectos y menor desperdicio de material.
La automatización de los procesos de soldadura ha tenido un impacto significativo en muchas industrias, especialmente en sectores de producción en serie, como la automotriz y la aeronáutica. Los robots de soldadura, que antes se usaban principalmente para tareas repetitivas, ahora están diseñados con una flexibilidad mucho mayor. Estos robots pueden ajustar su comportamiento en tiempo real, lo que permite realizar soldaduras complejas con una alta precisión y a una velocidad mucho mayor que la que un operario podría lograr manualmente. Estos avances en la automatización no solo aumentan la productividad, sino que también mejoran la seguridad, ya que los operarios pueden estar alejados de las áreas de trabajo más peligrosas, reduciendo el riesgo de accidentes y exposición a humos tóxicos y radiación.
Además de la automatización, los avances en los materiales de soldadura y los procesos de unión han permitido soldar metales y aleaciones que antes se consideraban difíciles o imposibles de unir. Las aleaciones avanzadas, como las de titanio, níquel y magnesio, tienen propiedades excepcionales de resistencia, pero a menudo presentan desafíos en cuanto a su soldabilidad debido a su alta tendencia a la formación de grietas o su baja conductividad térmica. Los avances en la soldadura por láser, por ejemplo, han abierto nuevas posibilidades para unir estas aleaciones con alta precisión y control térmico, minimizando los efectos adversos en la microestructura del material base. La soldadura por fricción, en particular, ha ganado popularidad en la industria aeroespacial y automotriz, ya que permite la unión de materiales livianos, como el aluminio, sin la necesidad de material de relleno, lo que reduce el peso de las estructuras sin comprometer su resistencia.
El campo de la soldadura también ha sido influenciado por las preocupaciones medioambientales. A medida que las regulaciones sobre las emisiones de gases contaminantes se vuelven más estrictas, los procesos de soldadura han tenido que adaptarse. La soldadura con arco sumergido (SAW), por ejemplo, es una de las técnicas que genera menos emisiones y polvo, debido a que la capa de fundente protege el charco de soldadura. La soldadura por láser también ha demostrado ser eficiente desde el punto de vista energético, ya que permite una concentración de energía en un área muy pequeña, lo que reduce la cantidad de energía necesaria para fundir el material. Las investigaciones en nuevas técnicas, como la soldadura por microondas y la soldadura por fricción-agitación, están orientadas a encontrar alternativas más ecológicas que reduzcan la huella de carbono en la fabricación.
La industria del reciclaje también se beneficia de los avances en soldadura. Los metales reciclados, a menudo de calidad variable, pueden requerir técnicas de soldadura especializadas para asegurar una unión duradera y de calidad. La soldadura por fricción, por ejemplo, es particularmente útil en aplicaciones donde se trabajan metales reciclados, como el acero y el aluminio, ya que el proceso genera menos contaminación y es eficiente incluso con materiales reciclados que tienen una composición no uniforme.
A nivel industrial, la soldadura está comenzando a integrar tecnologías más avanzadas como la inteligencia artificial (IA) y el aprendizaje automático. Estos sistemas pueden predecir el comportamiento de las soldaduras y ajustar automáticamente los parámetros de soldadura para adaptarse a condiciones cambiantes. Estos avances también se están utilizando para la detección temprana de defectos, mediante el análisis de imágenes de alta resolución y sistemas de visión artificial. La inteligencia artificial ayuda a identificar patrones en grandes volúmenes de datos, permitiendo a los fabricantes detectar problemas potenciales antes de que se conviertan en fallos costosos.
Las aplicaciones futuras de la soldadura también se centran en la creación de estructuras cada vez más complejas y livianas, como las que se encuentran en la ingeniería biomédica y la nanotecnología. En la biomedicina, por ejemplo, se están desarrollando técnicas de soldadura para unir microcomponentes en dispositivos implantables, como marcapasos y prótesis. La capacidad de trabajar con materiales extremadamente pequeños y delicados abre un nuevo campo de posibilidades para la soldadura de precisión.
En resumen, la soldadura ha evolucionado significativamente desde sus primeras aplicaciones, con avances en tecnología, materiales y automatización que han permitido una mayor precisión, eficiencia y adaptabilidad en una variedad de industrias. Los desafíos que enfrentan los fabricantes son cada vez más complejos, pero las soluciones innovadoras están allanando el camino para un futuro en el que la soldadura no solo sea más eficaz, sino también más sostenible y segura.
Sistemas de soldadura de cordón de anillo
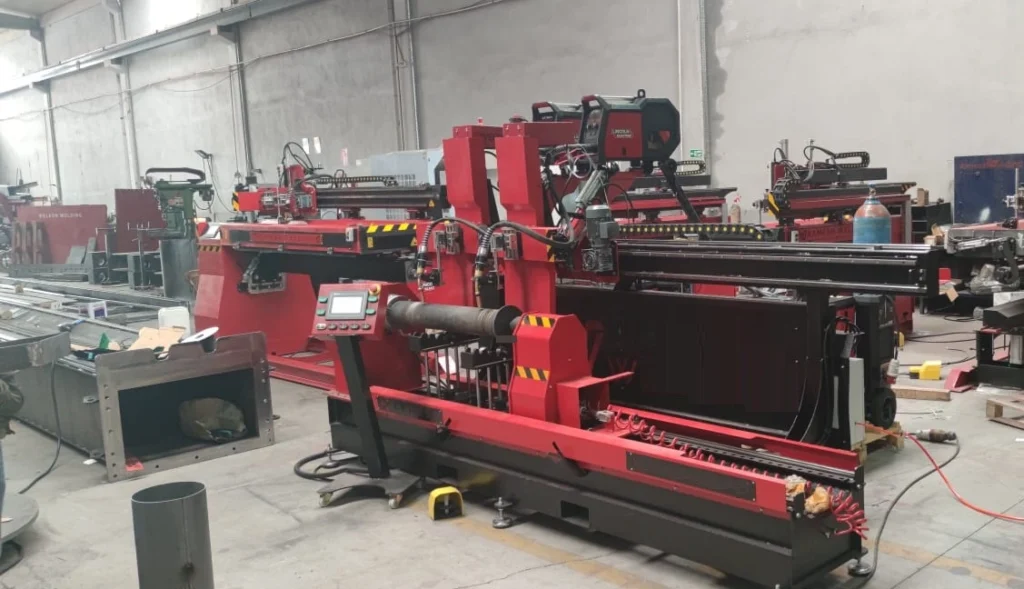
Los sistemas de soldadura de cordón de anillo son una categoría especializada de técnicas de soldadura utilizadas para crear un cordón de soldadura continuo en forma de anillo o círculo. Estos sistemas son particularmente útiles en aplicaciones donde las piezas a soldar tienen una geometría circular, como en la fabricación de tuberías, depósitos cilíndricos, tanques, y otras estructuras de formas similares. La soldadura de cordón de anillo requiere una alta precisión y un control riguroso para garantizar la uniformidad de la soldadura a lo largo de toda la circunferencia de la unión. A continuación, se describen algunos de los procesos y tecnologías más comunes utilizados en la soldadura de cordón de anillo:
1. Soldadura por arco sumergido (SAW)
La soldadura por arco sumergido es uno de los métodos más comunes para realizar cordones de soldadura de anillo, especialmente en aplicaciones de alta producción. Este proceso utiliza un electrodo consumible y un fundente en forma de polvo que cubre el charco de soldadura, protegiendo el área de la soldadura de la contaminación atmosférica. El cordón de anillo se crea mediante la acción de un arco que se mueve a lo largo de la circunferencia de la pieza. La alta penetración y la capacidad de formar un cordón de soldadura continuo y de alta calidad hacen que este proceso sea adecuado para aplicaciones como la fabricación de cilindros, tubos y tanques de gran diámetro.
Ventajas:
- Alta velocidad de deposición.
- Buena penetración y resistencia a la fatiga.
- Baja distorsión térmica debido a la cobertura del fundente.
Aplicaciones:
- Soldadura de tubos y grandes estructuras metálicas cilíndricas.
- Industria del petróleo y gas, construcción de depósitos y calderas.
2. Soldadura MIG/MAG (Gas Inert y Gas Activo)
Los procesos de soldadura MIG (Metal Inert Gas) y MAG (Metal Active Gas) también se utilizan para crear cordones de soldadura de anillo. Estos procesos emplean un electrodo consumible y un gas de protección (inert o activo, dependiendo del material base). A través del uso de un sistema de alimentación de alambre, el arco se mantiene constante mientras la boquilla se mueve a lo largo de la circunferencia, depositando el material de relleno y formando el cordón de anillo.
Ventajas:
- Alta flexibilidad en materiales, adecuado para acero inoxidable, aluminio, y otras aleaciones.
- Menor distorsión en comparación con otros procesos.
- Adecuado para soldaduras finas y de alta calidad.
Aplicaciones:
- Soldadura de tubos y recipientes de presión.
- Industrias de fabricación de equipos médicos y aeronáuticos.
3. Soldadura TIG (Tungsten Inert Gas)
La soldadura TIG, que utiliza un electrodo de tungsteno no consumible, es ideal para aplicaciones que requieren alta precisión y control en la deposición del material de relleno. En la soldadura de cordón de anillo, el operador o un sistema robotizado controla la trayectoria del arco a lo largo de la circunferencia. La ventaja principal de este proceso es la alta calidad de la soldadura, con poca formación de salpicaduras y un acabado limpio.
Ventajas:
- Excelente control del calor y la penetración.
- Ideal para soldaduras de alta calidad y precisión.
- Mínima distorsión.
Aplicaciones:
- Aplicaciones de alta precisión, como componentes aeroespaciales y partes de alta gama.
- Soldadura de materiales como acero inoxidable y aleaciones especiales.
4. Soldadura orbital
La soldadura orbital es un proceso especializado en la que la antorcha de soldadura sigue una trayectoria circular a lo largo de la pieza. Este tipo de soldadura es común en la industria de fabricación de tubos y en aplicaciones de alta precisión donde se requiere un cordón de soldadura continuo en forma de anillo. Se utiliza un sistema automatizado que mueve el electrodo a lo largo de un círculo, asegurando una soldadura uniforme y repetible.
Ventajas:
- Alta repetibilidad y precisión.
- Ideal para soldaduras de anillos en componentes de tubo, tanques y calderas.
- Reducción de defectos de soldadura y alta calidad de la unión.
Aplicaciones:
- Industria del acero inoxidable, fabricación de tubos y sistemas de tuberías.
- Fabricación de equipos para la industria farmacéutica, alimentaria y química.
5. Soldadura por fricción
La soldadura por fricción se puede usar en la fabricación de cordones de anillo, especialmente cuando se busca unir materiales de manera eficiente y sin necesidad de fundir el material base. En este proceso, dos piezas de material se frotan entre sí mientras se aplica presión, generando calor suficiente para causar la unión. Este proceso es útil para crear uniones en piezas de aluminio, acero y otros metales ligeros.
Ventajas:
- No requiere material de relleno.
- Genera una baja cantidad de residuos y poca distorsión térmica.
- Alta eficiencia energética.
Aplicaciones:
- Soldadura de componentes automotrices, como los cascos de motor.
- Industria aeroespacial para unir componentes de estructuras ligeras.
Consideraciones al seleccionar un sistema de soldadura de cordón de anillo:
- Materiales a soldar: La elección del sistema de soldadura depende en gran medida de los materiales que se estén utilizando. Algunos procesos, como MIG/MAG, son adecuados para metales ferrosos y no ferrosos, mientras que TIG es más común en metales más delicados y de alta calidad.
- Tamaño y forma de la pieza: Las piezas con geometría circular o cilíndrica son ideales para la soldadura de cordón de anillo, pero el tamaño de la pieza influye en la elección del proceso, ya que algunos, como el orbital, son más adecuados para tamaños pequeños a medianos.
- Requisitos de calidad: En aplicaciones donde la soldadura debe ser extremadamente limpia, sin defectos, y de alta resistencia, la soldadura TIG o orbital suele ser la mejor opción.
- Velocidad de producción: Procesos como la soldadura por arco sumergido o MIG/MAG son muy adecuados cuando se requiere alta velocidad de producción, como en la industria automotriz o de fabricación de tuberías en grandes volúmenes.
En conclusión, la soldadura de cordón de anillo es un proceso crucial en diversas industrias, y la elección del sistema adecuado dependerá de factores como el tipo de material, la precisión requerida, la velocidad de producción y el entorno en el que se trabaja. Con la evolución de las tecnologías de soldadura, los avances en automatización y control de procesos han permitido mejorar la calidad y la eficiencia de estos sistemas, haciéndolos cada vez más precisos y adaptados a las demandas industriales modernas.
La soldadura de cordón de anillo se ha convertido en una de las técnicas más especializadas y útiles en la fabricación de componentes industriales con formas circulares. Este tipo de soldadura es esencial en sectores como la fabricación de tanques, recipientes a presión, sistemas de tuberías y estructuras cilíndricas, donde la geometría circular requiere una unión continua y uniforme. Los sistemas de soldadura de cordón de anillo permiten crear uniones fuertes y estables, esenciales para la integridad estructural de los productos finales. Uno de los desafíos de este tipo de soldadura es garantizar la uniformidad a lo largo de toda la circunferencia, lo cual requiere equipos y procesos altamente controlados para asegurar la calidad en todo el recorrido de la soldadura.
Los avances en tecnología de soldadura han permitido que los procesos sean más rápidos, más precisos y más eficientes. La automatización ha jugado un papel importante en este desarrollo, ya que permite a los operarios o robots seguir una trayectoria exacta alrededor de la pieza, manteniendo los parámetros constantes a lo largo del proceso. Esto reduce la variabilidad en la calidad de la soldadura y mejora la consistencia, lo cual es crucial en la fabricación de componentes de alta resistencia y durabilidad.
Además de la precisión, la tecnología también ha facilitado el trabajo con materiales más difíciles de soldar. Aleaciones como el titanio, el acero inoxidable y el aluminio, que se utilizan comúnmente en aplicaciones de alta resistencia, requieren procesos específicos para evitar defectos como grietas o porosidad. La soldadura TIG y MIG son particularmente útiles en estos casos, ya que proporcionan un control muy preciso del calor y la energía aplicada, minimizando el riesgo de daños en el material base.
La capacidad para soldar de manera continua y eficiente también ha transformado la producción en sectores que requieren altas tasas de fabricación, como la industria automotriz. Los robots de soldadura, en particular, han permitido que los cordones de anillo se realicen con mayor rapidez y sin comprometer la calidad, lo que se traduce en una mayor eficiencia en la línea de producción. En este contexto, los sistemas orbitales, que siguen un camino circular a lo largo de la pieza, son extremadamente útiles para asegurar una soldadura uniforme y repetible en condiciones de alta producción.
Por otro lado, la soldadura de cordón de anillo también ha mejorado en términos de sostenibilidad y eficiencia energética. Procesos como la soldadura por láser, que se concentran en una zona pequeña con alta energía, permiten realizar uniones sin la necesidad de grandes cantidades de material de relleno. Esto no solo reduce los costos, sino que también minimiza el impacto ambiental, ya que consume menos energía y produce menos residuos. Además, la reducción de la distorsión térmica y la menor emisión de gases contaminantes en algunos procesos de soldadura contribuyen a un entorno de trabajo más limpio y seguro.
En la fabricación de estructuras metálicas complejas y componentes para la industria aeronáutica, por ejemplo, la soldadura de cordón de anillo se utiliza para garantizar que las uniones sean tan fuertes y ligeras como sea posible, permitiendo que las piezas resistan condiciones extremas de tensión y presión sin comprometer su desempeño. La soldadura orbital, que se emplea ampliamente en la fabricación de sistemas de tuberías, permite soldaduras de alta precisión en ambientes controlados, lo que es esencial para aplicaciones donde la hermeticidad y la resistencia son cruciales.
A medida que las industrias evolucionan y las demandas de calidad y eficiencia aumentan, la tecnología de soldadura de cordón de anillo continuará siendo una herramienta vital para la creación de productos complejos y duraderos. Los avances en la automatización, la robotización y el monitoreo en tiempo real permitirán una mayor precisión, seguridad y sostenibilidad en la producción, asegurando que estos sistemas se mantengan a la vanguardia de la tecnología de fabricación.
Con el paso del tiempo, los sistemas de soldadura de cordón de anillo también han comenzado a incorporar tecnologías más avanzadas que permiten mejorar aún más la calidad y la eficiencia del proceso. La integración de sistemas de monitoreo en tiempo real, por ejemplo, ha permitido que las condiciones del proceso de soldadura se ajusten de manera dinámica según las variaciones detectadas en la pieza. Esto no solo mejora la calidad de la soldadura, sino que también reduce el riesgo de defectos, como las grietas o la deformación del material. El monitoreo de variables clave, como la temperatura, el voltaje del arco y la velocidad de avance, asegura que el proceso se mantenga dentro de los parámetros óptimos para cada tipo de material y cada condición de soldadura.
Por otro lado, la inteligencia artificial y el aprendizaje automático han comenzado a desempeñar un papel fundamental en la mejora de los procesos de soldadura. Los algoritmos avanzados pueden analizar grandes cantidades de datos recolectados durante el proceso de soldadura, identificar patrones de calidad y predecir posibles fallos antes de que ocurran. Esto puede ayudar a los operadores a tomar decisiones más informadas sobre cuándo realizar ajustes o reemplazar componentes en los sistemas de soldadura, lo que reduce significativamente los tiempos de inactividad y mejora la eficiencia general de la producción.
La implementación de estas tecnologías de vanguardia no solo permite obtener un mayor control sobre la calidad de las soldaduras, sino que también mejora la seguridad en el lugar de trabajo. La soldadura, especialmente en procesos automatizados, puede generar altos niveles de calor y radiación, lo que puede presentar riesgos para los operarios si no se toman las precauciones adecuadas. Al integrar sistemas de monitoreo que supervisan no solo el proceso de soldadura, sino también las condiciones del entorno, es posible garantizar que los operarios estén protegidos de cualquier riesgo potencial. Además, la automatización y la robótica también pueden reducir la exposición de los trabajadores a condiciones peligrosas, al permitirles operar de manera remota y con un mayor grado de control.
La innovación en los materiales de soldadura también ha sido un factor clave en la evolución de los sistemas de soldadura de cordón de anillo. Con el avance de las aleaciones y los compuestos, los procesos de soldadura deben adaptarse a las nuevas demandas de materiales que son más ligeros, más resistentes o que tienen propiedades específicas para aplicaciones de alta gama, como la industria aeroespacial o la fabricación de dispositivos médicos. Esto ha llevado a un mayor enfoque en la personalización de los procesos de soldadura para adaptarse a las características únicas de cada material, lo que se traduce en un aumento de la eficiencia y la durabilidad de las uniones.
En la fabricación de equipos y componentes críticos, como los que se utilizan en la industria energética, la calidad y la fiabilidad de las soldaduras de cordón de anillo son esenciales para garantizar que los productos finales puedan soportar las condiciones extremas a las que estarán expuestos, como altas presiones, temperaturas y vibraciones. Los avances en las técnicas de soldadura, combinados con un mejor entendimiento de los materiales y las estructuras, han permitido crear soluciones que mejoran no solo la resistencia de las uniones, sino también su longevidad. Esto es particularmente relevante en la construcción de infraestructuras de energía, como plantas nucleares, plataformas petroleras y turbinas eólicas, donde las soldaduras deben resistir ciclos térmicos y mecánicos constantes.
A medida que las técnicas de soldadura de cordón de anillo continúan evolucionando, también lo hacen las expectativas en cuanto a la sostenibilidad de los procesos. La soldadura moderna busca ser más eficiente no solo en términos de tiempo y costos, sino también en términos de consumo de recursos. Esto implica no solo una reducción en el uso de materiales, sino también en la cantidad de energía necesaria para realizar una soldadura. Los procesos de soldadura más eficientes, como la soldadura por láser, son capaces de generar menos residuos y utilizar menos energía que los métodos tradicionales, lo que contribuye a una fabricación más ecológica.
Finalmente, la globalización de los mercados y la competencia constante entre fabricantes han impulsado aún más la innovación en los sistemas de soldadura de cordón de anillo. Los fabricantes buscan procesos que no solo mejoren la calidad de las uniones, sino que también reduzcan los costos de producción y aumenten la velocidad de fabricación. Las empresas están invirtiendo en nuevas tecnologías, equipos y técnicas que les permitan ofrecer productos con un valor agregado, que cumplan con los estándares internacionales y que sean lo más eficientes posible en términos de costo y rendimiento. Esto está llevando a una revolución en la industria de la soldadura, donde los métodos de fabricación continúan adaptándose a las necesidades cambiantes de los mercados globales.
La soldadura de cordón de anillo, por tanto, es un ejemplo claro de cómo las técnicas de fabricación pueden evolucionar constantemente en respuesta a los avances tecnológicos, las necesidades del mercado y las demandas de calidad y sostenibilidad. Este proceso seguirá siendo una piedra angular en la fabricación de componentes esenciales en muchas industrias, desde la automotriz hasta la aeroespacial, y continuará siendo una parte fundamental de la infraestructura industrial global en los próximos años.
Máquinas para soldar cordón de forma circular
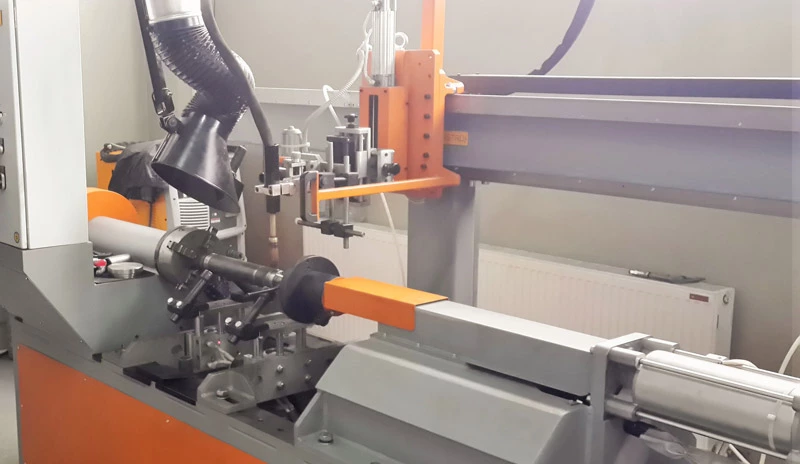
Las máquinas para soldar cordón de forma circular están diseñadas específicamente para realizar soldaduras continuas en geometrías circulares, como tubos, tanques, depósitos, y otras estructuras cilíndricas o con formas anulares. Estas máquinas son esenciales en muchas industrias, como la fabricación de componentes para la industria automotriz, aeronáutica, energía, química y petroquímica, entre otras. Existen varios tipos de máquinas y tecnologías especializadas que permiten realizar este tipo de soldadura, y su elección depende de factores como el tipo de material, el tamaño de la pieza, el tipo de soldadura requerida, y las especificaciones de calidad. A continuación, se describen las principales máquinas utilizadas para la soldadura de cordón circular.
1. Máquinas de soldadura orbital
Las máquinas de soldadura orbital son las más comunes para soldar cordones de anillo en piezas cilíndricas, ya que están diseñadas específicamente para realizar soldaduras continuas alrededor de una pieza en forma de círculo. Estas máquinas utilizan una antorcha de soldadura que sigue un camino circular predefinido a lo largo de la pieza. La antorcha está montada en un cabezal que puede ser ajustado para adaptarse al diámetro de la pieza que se va a soldar.
Características principales:
- Movimiento circular controlado para asegurar un cordón de soldadura uniforme.
- Pueden emplear diversos procesos de soldadura como TIG, MIG, y arco sumergido.
- Se utilizan tanto en aplicaciones manuales como automatizadas, dependiendo de la complejidad y volumen de producción.
- Son ideales para soldaduras de alta precisión y calidad, especialmente en materiales como acero inoxidable, aluminio y otras aleaciones.
Aplicaciones:
- Fabricación de tubos y sistemas de tuberías.
- Soldadura de recipientes a presión y tanques.
- Industria farmacéutica, alimentaria y química, donde se requiere una alta calidad de soldadura.
2. Máquinas de soldadura por arco sumergido (SAW)
En algunos casos, para soldar grandes diámetros de tuberías o componentes que requieren un cordón de soldadura robusto, se utilizan máquinas de soldadura por arco sumergido. Aunque el proceso no se realiza típicamente en un patrón orbital, las máquinas de arco sumergido pueden ser configuradas para soldar de manera continua alrededor de piezas cilíndricas utilizando un alimentador automático de alambre y un sistema de fundente.
Características principales:
- Alta tasa de deposición, lo que permite realizar soldaduras rápidas y robustas.
- Utilizan un fundente que cubre el arco, protegiendo la soldadura de contaminantes atmosféricos.
- Son ideales para aplicaciones donde se requieren soldaduras profundas y de alta resistencia.
Aplicaciones:
- Soldadura de grandes tubos y estructuras metálicas, como los utilizados en la industria petroquímica o de gas.
- Producción de grandes recipientes a presión y sistemas de calderas.
3. Máquinas de soldadura MIG/MAG
Las máquinas de soldadura MIG/MAG (Metal Inert Gas / Metal Active Gas) se utilizan para soldar de manera eficiente cordones circulares, especialmente en materiales ferrosos y no ferrosos. En este caso, la máquina alimenta un alambre de electrodo consumible mientras se introduce un gas protector (inert o activo) para evitar la contaminación de la soldadura. Estas máquinas son bastante flexibles y se emplean tanto en aplicaciones manuales como automáticas.
Características principales:
- Alta velocidad de soldadura y capacidad para trabajar con una amplia gama de materiales.
- Adecuadas para soldaduras de cordón de anillo en piezas de acero, acero inoxidable, aluminio y otros materiales.
- Los robots de soldadura pueden ser integrados con máquinas MIG/MAG para aplicaciones automatizadas.
Aplicaciones:
- Industria automotriz, para la fabricación de componentes metálicos en serie.
- Construcción de sistemas de tuberías, equipos de calefacción, refrigeración, y equipos de energía.
4. Máquinas de soldadura TIG
Las máquinas de soldadura TIG (Tungsten Inert Gas) son muy precisas y se utilizan principalmente para soldaduras de alta calidad, especialmente en materiales delicados o cuando se requieren soldaduras estéticamente perfectas. Aunque las máquinas TIG generalmente no se usan para grandes volúmenes de producción, son ideales cuando se requiere una gran precisión en el cordón de soldadura y cuando la estética y la resistencia de la soldadura son esenciales.
Características principales:
- Usan un electrodo de tungsteno no consumible para crear el arco, y el material de relleno se introduce de manera manual o automatizada.
- Se utilizan gases inertes como helio o argón para proteger el área de la soldadura.
- Permiten un control preciso del calor y la penetración de la soldadura.
Aplicaciones:
- Soldadura de componentes de alta precisión en la industria aeroespacial, médica y electrónica.
- Fabricación de recipientes y componentes en acero inoxidable, aluminio y otras aleaciones de alta calidad.
5. Máquinas de soldadura por láser
La soldadura por láser es una tecnología avanzada que se utiliza en la fabricación de componentes de alta precisión. Aunque la soldadura por láser no es tan común como las otras técnicas para cordones circulares, puede ser utilizada para aplicaciones muy específicas que requieren una soldadura limpia, rápida y de alta precisión. El láser puede ser dirigido de manera precisa alrededor de la pieza circular para crear el cordón de soldadura.
Características principales:
- Alta precisión y mínima distorsión térmica.
- Gran velocidad de soldadura y poca deformación del material.
- Es ideal para materiales finos o componentes pequeños que requieren soldaduras de alta calidad.
Aplicaciones:
- Soldadura de componentes de precisión en la industria electrónica y aeroespacial.
- Aplicaciones de soldadura de alta resistencia en componentes de dispositivos médicos y equipos electrónicos.
6. Máquinas de soldadura por fricción
Las máquinas de soldadura por fricción también pueden ser utilizadas para realizar soldaduras de cordón de anillo, especialmente en materiales como el aluminio. En este proceso, las piezas a soldar se frotan entre sí con presión, generando calor por fricción, lo que produce la unión sin la necesidad de fundir el material base. Es un proceso eficiente que genera menos desperdicio y produce menos contaminantes.
Características principales:
- No requiere material de relleno ni calor extremo, lo que reduce la distorsión térmica.
- Utiliza un enfoque de fricción para unir materiales sin necesidad de fundirlos.
- Ideal para aplicaciones que requieren soldaduras ligeras pero fuertes.
Aplicaciones:
- Industria automotriz, para la fabricación de componentes de aluminio.
- Fabricación de piezas para la industria aeronáutica.
Conclusión
Las máquinas para soldar cordón de forma circular han avanzado significativamente con la incorporación de tecnologías modernas como la automatización, la robotización, y el control preciso de los parámetros de soldadura. Dependiendo de la aplicación y los materiales a utilizar, la elección de la máquina puede variar, pero todas tienen en común la capacidad de realizar soldaduras continuas y de alta calidad en geometrías circulares, lo que las hace esenciales en diversas industrias.
Las máquinas para soldar cordón de forma circular juegan un papel crucial en la fabricación de componentes cilíndricos, desde tanques y tuberías hasta equipos industriales complejos. Estas máquinas están diseñadas para ofrecer un control preciso sobre la soldadura, permitiendo que el cordón de soldadura sea uniforme y de alta calidad a lo largo de toda la circunferencia de la pieza. La soldadura de cordón circular es esencial cuando se requieren uniones fuertes y herméticas, lo que es particularmente importante en aplicaciones como la fabricación de recipientes a presión, sistemas de tuberías en la industria energética, y componentes en la industria aeroespacial.
Una de las ventajas principales de estas máquinas es su capacidad para mantener un movimiento constante y preciso a lo largo del contorno de la pieza. Esto se logra a través de sistemas de control avanzados que permiten que la antorcha de soldadura siga una trayectoria perfectamente circular, eliminando las variaciones de velocidad o ángulo que podrían afectar la calidad de la soldadura. La automatización juega un papel clave en este tipo de soldadura, ya que puede realizarse de manera completamente automatizada o con asistencia mínima por parte del operador. Esto no solo mejora la eficiencia, sino que también reduce la posibilidad de errores humanos, lo que se traduce en una producción más consistente y de alta calidad.
La capacidad de las máquinas para adaptarse a diferentes tamaños de piezas y tipos de materiales es otro aspecto destacado. Estas máquinas pueden ser ajustadas para trabajar con una amplia gama de materiales, desde aceros inoxidables hasta aleaciones de alta resistencia o metales no ferrosos como el aluminio. Esto se logra mediante la selección del proceso de soldadura adecuado (como TIG, MIG, arco sumergido, láser, entre otros), lo que garantiza que cada tipo de material se suelde de la manera más eficiente y efectiva posible. Además, las máquinas pueden estar equipadas con sistemas de refrigeración y control de gases protectores, lo que asegura que el proceso de soldadura se realice bajo condiciones óptimas, minimizando riesgos como la oxidación o la deformación térmica.
Otra característica importante de estas máquinas es la posibilidad de integrar sistemas de monitoreo en tiempo real. Estos sistemas pueden verificar continuamente la calidad de la soldadura, controlando parámetros como la temperatura, la velocidad de avance, la corriente y el voltaje del arco. Cualquier desviación en estos parámetros puede ser detectada inmediatamente, lo que permite a los operadores realizar ajustes en tiempo real para mantener la calidad de la soldadura. Esta capacidad de monitoreo es especialmente útil en aplicaciones donde la precisión es esencial, como en la fabricación de componentes para la industria farmacéutica, de alimentos y bebidas, o en la producción de equipos médicos, donde las uniones deben ser completamente estancas y sin defectos.
El avance de la tecnología ha permitido también que las máquinas para soldar cordón de forma circular sean cada vez más eficientes y respetuosas con el medio ambiente. Los procesos modernos requieren menos energía y producen menos residuos, lo que contribuye a una fabricación más sostenible. Por ejemplo, en la soldadura por láser, la energía se concentra en un área pequeña, lo que permite realizar la soldadura con menor consumo de material y menor generación de calor, reduciendo la distorsión del material y el consumo de energía. Además, al usar tecnologías más limpias, como los sistemas de soldadura con gases inertes, se minimiza la producción de contaminantes en la atmósfera.
Con la integración de sistemas robóticos, muchas de estas máquinas pueden ser operadas en entornos completamente automatizados, lo que no solo aumenta la productividad, sino que también mejora la seguridad en el lugar de trabajo. La automatización permite realizar soldaduras de alta precisión sin la intervención directa de los operarios, lo que reduce su exposición a los riesgos asociados con el proceso de soldadura, como la radiación o el calor excesivo.
La versatilidad de las máquinas para soldar cordón de forma circular también las hace valiosas para una amplia gama de aplicaciones industriales. En la industria automotriz, por ejemplo, estas máquinas son esenciales para la fabricación de componentes metálicos en serie, donde la velocidad y la precisión son fundamentales. En la industria aeronáutica, permiten realizar uniones de alta resistencia en estructuras ligeras, que deben cumplir con estrictos requisitos de calidad y resistencia. Además, en la producción de equipos de energía y en la construcción de infraestructura, las soldaduras circulares garantizan la integridad estructural de los componentes, lo que es fundamental para la seguridad y el desempeño de las instalaciones.
La evolución constante de estas tecnologías, junto con la creciente demanda de productos de mayor calidad y sostenibilidad, asegura que las máquinas para soldar cordón de forma circular seguirán siendo una herramienta esencial en la fabricación de componentes industriales. La mejora en los procesos de soldadura, la reducción de costos y la optimización de la producción son tendencias que seguirán impulsando la innovación en este campo, haciendo que estas máquinas sean más eficientes, más precisas y más accesibles para una gama más amplia de aplicaciones.
Con el tiempo, las innovaciones en la tecnología de soldadura de cordón de forma circular continúan transformando las capacidades de producción en una variedad de sectores. Las máquinas de soldadura orbital, por ejemplo, no solo están mejorando en términos de precisión y versatilidad, sino también en la facilidad de integración con sistemas de control avanzado. Los avances en software de programación y control de procesos permiten a los operadores crear trayectorias de soldadura altamente optimizadas, lo que reduce el tiempo de configuración y aumenta la flexibilidad en la producción. Esto es especialmente valioso en entornos donde se requiere la fabricación de piezas con geometrías complejas o múltiples tamaños de diámetro, como en la fabricación de intercambiadores de calor o sistemas de tuberías de alto rendimiento.
Además, las máquinas de soldadura robóticas están mejorando continuamente en términos de automatización y adaptabilidad. Estas máquinas no solo son capaces de soldar de manera continua y precisa, sino que también se integran cada vez más con sistemas de visión artificial y sensores inteligentes que monitorean la calidad de la soldadura en tiempo real. Los sistemas de visión pueden detectar fallos microscópicos o irregularidades en el cordón de soldadura, alertando a los operadores o ajustando automáticamente el proceso para corregir cualquier defecto. Esta capacidad de “autoajuste” es una gran ventaja en aplicaciones de producción en masa, donde incluso pequeños defectos pueden tener un impacto significativo en la calidad y el rendimiento del producto final.
Por otro lado, los sistemas de soldadura por láser están viendo un aumento en su utilización debido a su capacidad para proporcionar un control excepcional sobre la entrada de calor y la precisión del cordón. A medida que los láseres de mayor potencia y precisión se vuelven más accesibles, las aplicaciones de soldadura por láser continúan expandiéndose, especialmente en la fabricación de componentes finos y de alta tecnología. Esta tecnología es ideal para la soldadura de materiales delicados o de alta gama, como en la industria electrónica, la fabricación de dispositivos médicos y la construcción de componentes para la industria aeroespacial. La principal ventaja de la soldadura por láser es su capacidad para crear uniones extremadamente fuertes y estéticamente perfectas con una mínima distorsión térmica, lo cual es crucial cuando se trabaja con materiales finos o piezas pequeñas.
A nivel de sostenibilidad, los avances en tecnología también están ayudando a reducir el impacto ambiental de los procesos de soldadura. Las máquinas modernas están diseñadas para ser más eficientes en cuanto a energía, utilizando menos recursos y generando menos residuos. Además, muchos procesos de soldadura ahora emplean gases protectores más ecológicos, como el nitrógeno o mezclas de gases menos costosas y más sostenibles. Este enfoque no solo contribuye a una reducción en el costo operativo, sino que también mejora la seguridad y la sostenibilidad a largo plazo de los procesos industriales.
En cuanto a los materiales, la continua innovación en aleaciones y metales de alta resistencia ha creado nuevos desafíos y oportunidades para las máquinas de soldadura de cordón circular. Con la creciente demanda de materiales más ligeros y resistentes, como las aleaciones de titanio y los metales exóticos, las máquinas de soldadura deben ser capaces de adaptarse a estos nuevos materiales, que a menudo tienen propiedades térmicas y mecánicas que requieren un enfoque más especializado. Las máquinas de soldadura de alta precisión, como las de soldadura por fricción o por láser, están particularmente bien posicionadas para manejar estos materiales, ya que pueden ofrecer un control preciso de la temperatura y la penetración sin comprometer la integridad de los materiales.
A medida que la competencia global aumenta, también lo hace la necesidad de reducir los costos de producción sin sacrificar la calidad. Las máquinas de soldadura automatizadas no solo ayudan a mejorar la eficiencia y la consistencia de las soldaduras, sino que también contribuyen a una reducción de los costos operativos. El uso de robots de soldadura y sistemas automatizados de alimentación de materiales permite a las empresas producir más piezas en menos tiempo, lo que reduce los costos laborales y aumenta la capacidad de producción. Esto es especialmente importante en industrias como la automotriz, donde los plazos de producción son ajustados y la competencia es feroz.
A nivel de seguridad, las mejoras en la automatización también han tenido un impacto positivo. La soldadura, especialmente en procesos tradicionales, puede ser peligrosa debido a los altos niveles de calor, radiación ultravioleta, y los gases tóxicos generados durante la operación. Al automatizar el proceso, se reduce la exposición de los operarios a estos riesgos, lo que crea un ambiente de trabajo más seguro y saludable. Las máquinas más modernas también cuentan con sistemas de seguridad avanzados que monitorean continuamente las condiciones operativas y alertan a los operadores sobre cualquier irregularidad que pueda comprometer la seguridad del proceso.
Finalmente, el futuro de la soldadura de cordón circular parece estar marcado por la constante integración de tecnologías inteligentes. El uso de inteligencia artificial (IA) y aprendizaje automático para optimizar los procesos de soldadura está en auge. Los sistemas inteligentes no solo pueden ajustar los parámetros en tiempo real, sino que también pueden predecir fallos potenciales y sugerir mejoras en el proceso basándose en grandes volúmenes de datos recopilados durante la producción. Esta capacidad de “aprender” y mejorar el proceso de manera autónoma puede llevar a una nueva era de soldadura de alta precisión, donde la calidad es aún más consistente y los tiempos de producción se reducen drásticamente.
En resumen, las máquinas para soldar cordón de forma circular están evolucionando rápidamente para abordar las crecientes demandas de precisión, eficiencia, sostenibilidad y seguridad en la fabricación moderna. A medida que avanzan las tecnologías y se optimizan los procesos, estas máquinas seguirán desempeñando un papel vital en una variedad de sectores industriales, asegurando que las soldaduras sean no solo fuertes y duraderas, sino también más rápidas, más económicas y más respetuosas con el medio ambiente.
Equipos industriales para soldadura de cordón circular
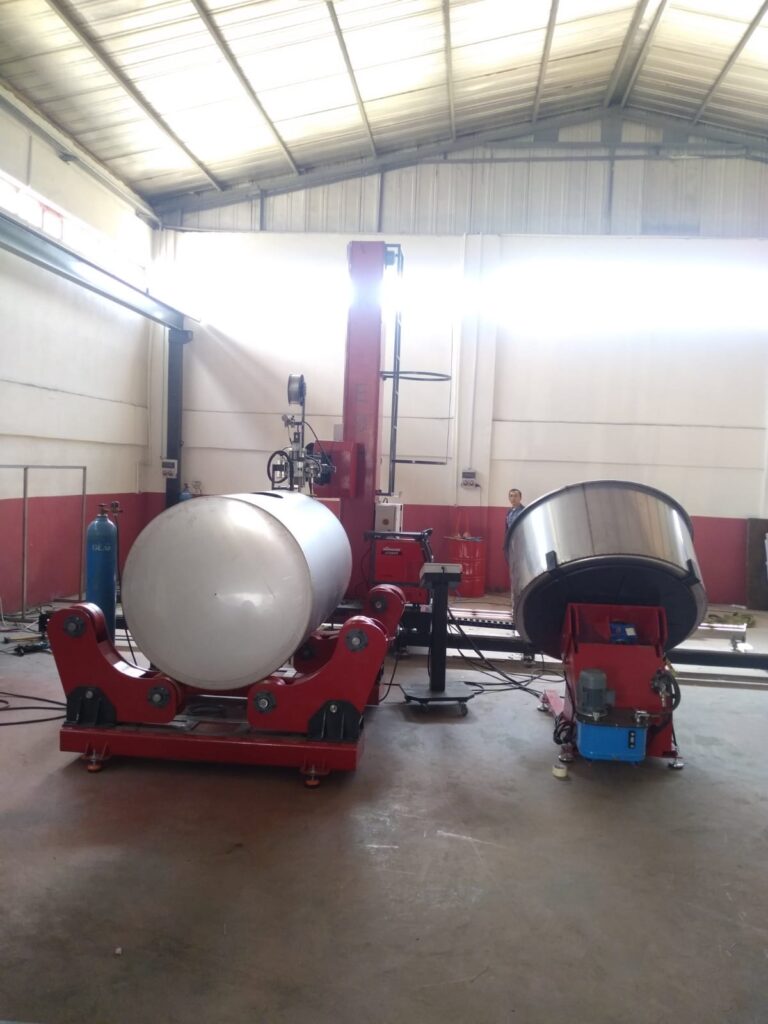
Los equipos industriales para soldadura de cordón circular son herramientas esenciales en diversas industrias, como la automotriz, aeroespacial, petroquímica, energética, y alimentaria, entre otras. Estos equipos permiten realizar soldaduras continuas en piezas de forma cilíndrica, lo que es fundamental para la fabricación de componentes como tuberías, recipientes a presión, intercambiadores de calor, y depósitos. Los equipos varían según el tipo de proceso de soldadura que se utilice, el tamaño y material de la pieza, y los requisitos de precisión. A continuación se describen algunos de los equipos más comunes empleados en la soldadura de cordón circular.
1. Máquinas de soldadura orbital
Las máquinas de soldadura orbital son las más utilizadas para la soldadura de cordón circular en aplicaciones industriales. Estas máquinas están diseñadas para soldar de manera precisa y continua alrededor de piezas cilíndricas, como tubos y recipientes. El proceso orbital es especialmente efectivo para materiales que requieren una soldadura de alta calidad, como el acero inoxidable, el aluminio, y otras aleaciones de metales no ferrosos.
Características principales:
- Antorchas orbitales: La antorcha de soldadura se monta en un cabezal que puede moverse alrededor de la pieza para crear un cordón de soldadura continuo y uniforme. Esto permite una alta precisión y un control exacto del calor.
- Automatización: Los equipos pueden ser automatizados para mejorar la eficiencia y consistencia de la soldadura, especialmente en producción en serie.
- Flexibilidad: La máquina puede adaptarse a diferentes diámetros y tipos de material mediante ajustes en la configuración del equipo.
- Control de parámetros: Los sistemas de control permiten ajustar parámetros como la velocidad, el voltaje, y la corriente para asegurar una soldadura óptima.
Aplicaciones:
- Soldadura de tuberías en la industria energética, petroquímica, y de gas.
- Fabricación de tanques y recipientes a presión.
- Soldadura de componentes de alta precisión en la industria farmacéutica y alimentaria.
2. Máquinas de soldadura por arco sumergido (SAW)
La soldadura por arco sumergido (SAW) es otro proceso utilizado para soldar cordones circulares, especialmente en aplicaciones de mayor escala. Este proceso se utiliza para unir piezas más grandes y gruesas, ya que tiene una alta tasa de deposición y produce un cordón de soldadura fuerte y robusto.
Características principales:
- Alambre de electrodo y fundente: Se utiliza un alambre de electrodo consumible y un fundente que cubre el arco, protegiendo la soldadura de contaminantes atmosféricos.
- Alta eficiencia: El proceso es rápido, lo que lo hace adecuado para aplicaciones industriales de alta producción.
- Control preciso: Los parámetros como la velocidad de avance y la cantidad de fundente son controlados para garantizar la calidad de la soldadura.
- Soldadura profunda: La soldadura por arco sumergido es ideal para materiales de gran espesor, ya que permite una penetración profunda.
Aplicaciones:
- Soldadura de grandes estructuras metálicas, como intercambiadores de calor y componentes de calderas.
- Fabricación de componentes de gran diámetro en la industria de la energía y petroquímica.
3. Máquinas de soldadura MIG/MAG
Las máquinas de soldadura MIG/MAG (Metal Inert Gas / Metal Active Gas) se utilizan comúnmente para soldar cordones circulares en una variedad de materiales, incluidos metales ferrosos y no ferrosos. Este proceso es muy eficiente y versátil, lo que lo hace adecuado tanto para trabajos de precisión como para soldaduras de mayor volumen.
Características principales:
- Alambre de electrodo consumible: El alambre de soldadura se alimenta automáticamente y se funde para formar la soldadura, mientras que se utiliza un gas protector (inert o activo) para proteger el arco de la contaminación atmosférica.
- Alta velocidad de soldadura: El proceso MIG/MAG es rápido y permite realizar soldaduras continuas y limpias.
- Flexibilidad en materiales: Puede utilizarse en una amplia gama de materiales, incluyendo acero, acero inoxidable, aluminio, y aleaciones de cobre.
- Versatilidad en configuraciones: Las máquinas MIG/MAG pueden ser configuradas para soldar en diferentes posiciones y con diferentes tipos de cordones de soldadura.
Aplicaciones:
- Soldadura de componentes en la industria automotriz y de maquinaria.
- Fabricación de sistemas de tuberías y estructuras metálicas en la industria de la construcción.
4. Máquinas de soldadura TIG
Las máquinas de soldadura TIG (Tungsten Inert Gas) son ideales para realizar soldaduras de cordón circular en materiales finos o en aplicaciones donde se requiere una soldadura estética y de alta calidad. Este proceso utiliza un electrodo de tungsteno no consumible y una fuente de energía controlada para crear un arco eléctrico.
Características principales:
- Control preciso del calor: El proceso TIG permite un control extremadamente preciso de la temperatura y la penetración de la soldadura, lo que es ideal para materiales delicados.
- Gas protector: Se utiliza un gas inerte, generalmente argón o helio, para proteger el área de la soldadura de la contaminación atmosférica.
- Soldaduras de alta calidad: El proceso TIG es conocido por producir soldaduras limpias y estéticamente perfectas, con menos salpicaduras y distorsión.
- Sin material de relleno: Aunque el proceso se puede realizar con o sin material de relleno, se puede añadir material de relleno manualmente si es necesario.
Aplicaciones:
- Soldadura de componentes de alta precisión en la industria aeroespacial, electrónica y médica.
- Fabricación de recipientes a presión y estructuras de alta calidad.
5. Máquinas de soldadura por láser
La soldadura por láser es una tecnología avanzada que se está utilizando cada vez más en la industria para la soldadura de cordones circulares. El láser ofrece un control muy preciso del calor, lo que permite realizar soldaduras de alta calidad y precisión sin afectar las propiedades del material circundante.
Características principales:
- Alta concentración de energía: El láser se enfoca en una pequeña área, lo que permite una penetración profunda con un mínimo de distorsión térmica.
- Soldaduras de alta precisión: La soldadura por láser es ideal para aplicaciones donde se requieren uniones fuertes y estéticamente perfectas, sin causar daños térmicos a la pieza.
- Sin contacto: A diferencia de otros procesos, la soldadura por láser no requiere contacto físico con el material base, lo que elimina los riesgos de contaminación y desgaste.
Aplicaciones:
- Soldadura de componentes de alta precisión en la industria electrónica, médica y aeroespacial.
- Fabricación de dispositivos de alta tecnología y componentes de metales exóticos.
6. Máquinas de soldadura por fricción
La soldadura por fricción es un proceso utilizado para unir materiales mediante el calor generado por fricción entre dos superficies. Este proceso puede ser usado para soldar piezas de forma circular, especialmente en materiales como el aluminio y otras aleaciones ligeras.
Características principales:
- Proceso sin material de relleno: La soldadura por fricción no requiere material de relleno, ya que la fricción misma genera el calor necesario para la fusión del material base.
- Baja distorsión: Debido a que el proceso utiliza temperaturas más bajas y menos calor, se reduce la distorsión del material.
- Uniones fuertes: El proceso produce uniones de alta resistencia, especialmente en metales ligeros.
Aplicaciones:
- Fabricación de componentes automotrices y aeroespaciales de aluminio.
- Soldadura de componentes en la industria de la construcción de aeronaves.
Conclusión
Los equipos industriales para la soldadura de cordón circular son cruciales para garantizar la calidad, la eficiencia y la fiabilidad de las uniones en piezas cilíndricas. A medida que la tecnología avanza, estos equipos se están volviendo más sofisticados, integrando sistemas de control avanzado, automatización y técnicas innovadoras como la soldadura por láser y por fricción. La selección del equipo adecuado depende de la aplicación específica, el tipo de material, el tamaño de la pieza, y los requisitos de producción. Sin importar el proceso, estos equipos aseguran que las soldaduras sean de alta calidad, fuertes y duraderas, lo que es esencial para la seguridad y el desempeño de las piezas fabricadas.
7. Máquinas de soldadura por resistencia
La soldadura por resistencia es otro proceso utilizado para la fabricación de cordones circulares, particularmente útil para materiales delgados y de alta conductividad, como el acero inoxidable o el cobre. Este proceso genera calor mediante la resistencia eléctrica en las piezas que se están soldando, lo que resulta en una unión fuerte y duradera.
Características principales:
- Generación de calor por resistencia: Se utiliza corriente eléctrica de alta intensidad, la cual pasa a través de las piezas a soldar. La resistencia al paso de la corriente genera el calor necesario para fundir las superficies de contacto.
- Velocidad rápida: Este proceso es muy rápido y eficiente, ideal para aplicaciones de producción en masa.
- Sin necesidad de material de relleno: Al igual que en la soldadura por fricción, no es necesario usar material de relleno, ya que la fusión de las piezas ocurre directamente en las superficies de contacto.
Aplicaciones:
- Fabricación de componentes automotrices, como carrocerías y otras piezas metálicas.
- En la industria de la fabricación de electrodomésticos, donde se necesita un proceso rápido y eficaz para unir metales delgados.
- En la fabricación de equipos de electrónica, debido a su capacidad para soldar materiales finos sin causar daños térmicos.
8. Máquinas de soldadura por haz de electrones (EBW)
La soldadura por haz de electrones es una técnica de soldadura avanzada que utiliza un haz de electrones acelerados para generar calor en el punto de unión. Este proceso es utilizado principalmente en la soldadura de materiales de alta precisión y en condiciones de vacío, lo que proporciona una soldadura extremadamente limpia y precisa.
Características principales:
- Alta concentración de energía: El haz de electrones genera temperaturas extremadamente altas en una pequeña zona, lo que permite una penetración profunda y una soldadura sin distorsión térmica significativa.
- Ambiente de vacío: Generalmente se realiza en un entorno de vacío para evitar la oxidación del material durante el proceso de soldadura.
- Alta precisión: Es ideal para aplicaciones donde se necesita un control preciso del calor y la profundidad de penetración.
Aplicaciones:
- Soldadura de piezas delicadas y de alta precisión en la industria aeroespacial.
- Fabricación de componentes de alta tecnología, como en la industria médica y de semiconductores.
- Soldadura de materiales exóticos y difíciles de trabajar, como algunos tipos de titanio o aleaciones especiales.
9. Máquinas de soldadura por plasma
La soldadura por plasma es una tecnología que utiliza un arco eléctrico a través de un gas ionizado para crear una soldadura altamente concentrada y controlada. A diferencia de la soldadura por arco tradicional, la soldadura por plasma permite una mayor precisión y control, lo que la convierte en una opción ideal para soldaduras de cordón circular en materiales delgados y de alta resistencia.
Características principales:
- Arco de plasma: El gas ionizado genera un arco de plasma que se concentra en un pequeño punto, lo que permite una penetración profunda y una soldadura precisa.
- Control avanzado de la energía: El proceso de soldadura por plasma ofrece un control superior sobre la cantidad de calor aplicado a la pieza, lo que reduce la distorsión térmica.
- Versatilidad: Es adecuado para una amplia gama de materiales, incluidos metales ferrosos, aleaciones de alta resistencia y materiales no ferrosos.
Aplicaciones:
- Soldadura de componentes finos y de alta precisión en la industria aeroespacial, automotriz, y electrónica.
- Uso en la fabricación de piezas de alta tecnología que requieren un control preciso sobre la calidad y estética de la soldadura.
- Ideal para soldar piezas de alta resistencia a temperaturas extremas.
10. Máquinas de soldadura por arco corto y pulso
Las máquinas de soldadura por arco corto y pulso son una variante del proceso MIG/MAG, donde el alambre de soldadura se alimenta en cortos intervalos mediante pulsos de corriente. Esto permite realizar soldaduras de alta calidad, especialmente en materiales delgados y de alta precisión, sin crear demasiada distorsión.
Características principales:
- Pulsos de corriente: Utilizan pulsos de corriente para controlar el tamaño del arco y la cantidad de calor aplicada en cada ciclo, lo que resulta en un control preciso del proceso de soldadura.
- Reducción de la salpicadura: Este proceso minimiza la cantidad de salpicaduras y la distorsión térmica, lo que es ideal para materiales delicados.
- Alta calidad de soldadura: Produce soldaduras limpias y estéticamente perfectas con una penetración adecuada.
Aplicaciones:
- Soldadura de metales delgados, como acero inoxidable, aluminio y aleaciones ligeras.
- Uso en la industria automotriz, donde se requieren uniones estéticas y de alta resistencia sin distorsionar la pieza base.
- Aplicaciones en la fabricación de componentes electrónicos y dispositivos donde la precisión y la calidad visual son esenciales.
11. Máquinas de soldadura con robots industriales
La soldadura robótica ha revolucionado la industria moderna, especialmente en la fabricación de cordones circulares en piezas de gran volumen y precisión. Los robots industriales son capaces de realizar tareas de soldadura de manera automática, rápida y eficiente, lo que incrementa la producción y reduce los errores humanos.
Características principales:
- Automatización completa: Los robots de soldadura son capaces de realizar soldaduras continuas sin intervención humana, aumentando la consistencia y reduciendo los costos laborales.
- Alta precisión: Equipados con sistemas de visión artificial y sensores de alta precisión, los robots pueden realizar soldaduras de alta calidad, incluso en geometrías complejas.
- Adaptabilidad: Los robots industriales pueden ser programados para adaptarse a diferentes tamaños de piezas y tipos de materiales, lo que les permite trabajar en una amplia variedad de aplicaciones.
Aplicaciones:
- Fabricación de grandes volúmenes de componentes en la industria automotriz.
- Soldadura de estructuras metálicas en la construcción de infraestructuras y maquinaria pesada.
- Aplicaciones en la industria aeroespacial y de defensa, donde se requieren soldaduras de alta precisión en materiales complejos.
Conclusión
La soldadura de cordón circular es una técnica clave en la fabricación de piezas cilíndricas en diversas industrias. Los equipos utilizados en este proceso varían dependiendo del tipo de material, el tamaño de la pieza, y los requisitos de precisión. Desde las máquinas orbitales, que ofrecen una soldadura continua y precisa, hasta las tecnologías más avanzadas como la soldadura por láser o por electrones, cada tipo de máquina tiene ventajas específicas que las hacen idóneas para diferentes aplicaciones. La integración de automatización, monitoreo en tiempo real y sistemas robóticos está llevando esta tecnología a nuevos niveles de eficiencia, calidad y sostenibilidad, lo que permite a las industrias satisfacer la demanda de productos de alta calidad de manera más rápida y rentable.
Sistemas de soldadura de unión circular
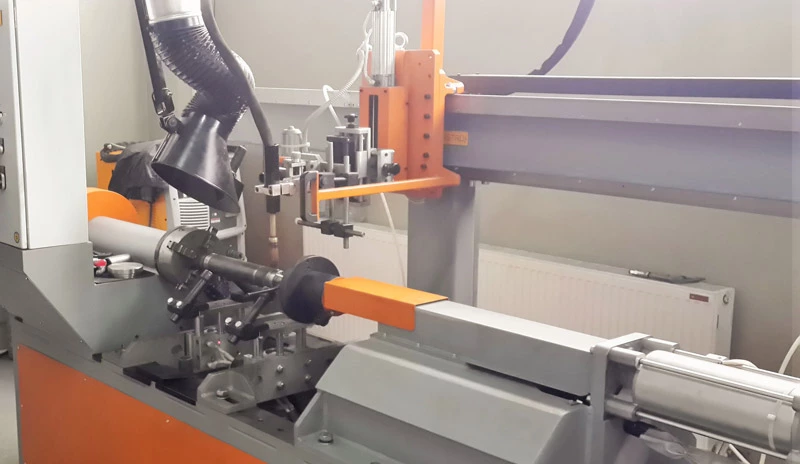
Los sistemas de soldadura de unión circular son esenciales para la fabricación de piezas cilíndricas, como tuberías, tanques, recipientes a presión, intercambiadores de calor y otros componentes industriales que requieren una soldadura continua alrededor de un perímetro circular. La soldadura de unión circular involucra varios métodos, cada uno con sus ventajas específicas, dependiendo de la aplicación, el tipo de material y los requisitos de calidad. A continuación, se describen algunos de los sistemas más utilizados para realizar soldaduras de unión circular:
1. Soldadura Orbital
La soldadura orbital es uno de los sistemas más comunes para realizar uniones circulares. En este proceso, la antorcha de soldadura se mueve a lo largo de un trayecto circular alrededor de la pieza, lo que garantiza una soldadura continua y uniforme. Este proceso es altamente preciso y se utiliza principalmente en industrias que requieren alta calidad de soldadura, como la farmacéutica, alimentaria, aeroespacial y petroquímica.
Características:
- Antorcha orbital: La antorcha de soldadura está montada sobre un dispositivo de control que permite que gire alrededor del material en un trayecto circular preciso.
- Automatización: El proceso es altamente automatizado, lo que mejora la precisión y la consistencia, reduciendo el error humano.
- Aplicaciones: Soldadura de tuberías, recipientes a presión, intercambiadores de calor y otros componentes cilíndricos.
Ventajas:
- Alta precisión y control del calor.
- Resultados consistentes y repetitivos.
- Reducción de defectos en la soldadura debido a la automatización del proceso.
2. Soldadura por Arco Sumergido (SAW)
La soldadura por arco sumergido (SAW) es un proceso de soldadura en el que el arco eléctrico se encuentra sumergido en un fundente granular, lo que ayuda a proteger la soldadura de la contaminación atmosférica y mejora la penetración y la calidad de la junta. Este sistema es especialmente adecuado para soldaduras de alta resistencia en materiales gruesos y grandes diámetros.
Características:
- Fundente protector: El fundente cubre el arco y ayuda a la formación de un cordón de soldadura limpio y fuerte.
- Alta tasa de deposición: Produce una gran cantidad de material fundido rápidamente, lo que acelera el proceso.
- Soldadura profunda: Permite penetraciones profundas, lo que es ideal para piezas gruesas y de gran tamaño.
Ventajas:
- Alta velocidad de soldadura y productividad.
- Menos distorsión debido a la menor cantidad de calor aplicado.
- Ideal para grandes piezas y aplicaciones de alta resistencia.
Aplicaciones:
- Soldadura de grandes estructuras, como calderas, intercambiadores de calor y tanques de almacenamiento de gran diámetro.
- Utilizado en la industria de la energía y en la fabricación de componentes pesados.
3. Soldadura MIG/MAG (Metal Inert Gas / Metal Active Gas)
La soldadura MIG/MAG es un proceso ampliamente utilizado para la soldadura de unión circular, especialmente en materiales finos y medianamente gruesos. Utiliza un alambre consumible como electrodo, que se funde para formar la soldadura, mientras que un gas protector se utiliza para evitar la contaminación del arco.
Características:
- Gas protector: Puede ser un gas inerte (como el argón) o un gas activo (como el dióxido de carbono o mezclas de CO2 y argón), dependiendo de los materiales a soldar.
- Alambre consumible: El alambre de soldadura se alimenta automáticamente y se funde para formar la unión.
- Versatilidad: Es adecuado para una amplia variedad de materiales, como acero inoxidable, aluminio, y acero al carbono.
Ventajas:
- Proceso rápido y eficiente.
- Permite soldar en diversas posiciones.
- Buen control de la soldadura, con poca salpicadura y buena penetración.
Aplicaciones:
- Soldadura de estructuras metálicas, como en la construcción de barcos, vehículos y equipos industriales.
- Fabricación de sistemas de tuberías y recipientes.
- Industria automotriz y fabricación de componentes en acero.
4. Soldadura TIG (Tungsten Inert Gas)
La soldadura TIG es un proceso que utiliza un electrodo de tungsteno no consumible para generar el arco eléctrico. Este proceso es ideal para aplicaciones donde se requiere una soldadura de alta precisión y estética, sin contaminantes y con un control total del calor. La soldadura TIG se usa en materiales delgados y donde la calidad visual de la soldadura es fundamental.
Características:
- Electrodo de tungsteno no consumible: El electrodo no se funde y se utiliza solo para generar el arco eléctrico.
- Gas protector: El argón o helio es utilizado para proteger la zona de la soldadura y evitar la contaminación.
- Precisión: Ofrece un control excepcional sobre la penetración de la soldadura y la forma del cordón.
Ventajas:
- Producción de soldaduras de alta calidad y estéticamente perfectas.
- Ideal para materiales delgados y para aplicaciones de alta precisión.
- Baja distorsión térmica debido al control preciso del calor.
Aplicaciones:
- Soldadura de componentes finos en la industria aeroespacial, electrónica y médica.
- Soldadura de materiales como acero inoxidable y aleaciones de alta temperatura.
- Fabricación de recipientes a presión y tanques de alta calidad.
5. Soldadura por Láser
La soldadura por láser es una tecnología avanzada que utiliza un haz de láser para fundir y unir los materiales. Este proceso ofrece una alta concentración de energía y un control preciso sobre la zona de fusión, lo que lo hace ideal para aplicaciones que requieren soldaduras limpias, rápidas y de alta precisión.
Características:
- Alta concentración de energía: El láser puede concentrar una gran cantidad de energía en una pequeña área, lo que permite una penetración profunda y una soldadura precisa.
- Soldadura sin contacto: La soldadura por láser no requiere contacto físico con el material base, lo que reduce el riesgo de desgaste del equipo y aumenta la durabilidad.
- Aplicaciones en materiales delicados: Ideal para materiales como el titanio, el aluminio y los metales de alta aleación.
Ventajas:
- Alta precisión y velocidad de soldadura.
- Baja distorsión térmica y mínima zona afectada por el calor.
- Proceso limpio y sin necesidad de fundentes o protección adicional.
Aplicaciones:
- Soldadura de piezas en la industria aeroespacial, médica, y electrónica de alta tecnología.
- Fabricación de componentes de precisión en industrias automotriz y de defensa.
- Uso en materiales de alta aleación o aquellos con geometrías complejas.
6. Soldadura por Fricción
La soldadura por fricción es un proceso sin material de relleno en el que el calor se genera por la fricción entre dos piezas que están siendo unidas. Es un proceso eficaz para soldar materiales como el aluminio y otras aleaciones ligeras, y se utiliza en aplicaciones donde la distorsión térmica debe ser mínima.
Características:
- Generación de calor por fricción: Las piezas a soldar se frotan entre sí a alta velocidad, generando calor que permite que las superficies se fusionen.
- Sin material de relleno: La soldadura por fricción no requiere material adicional, ya que la fricción misma crea la unión.
- Baja distorsión: La cantidad de calor generada es relativamente baja, lo que minimiza la distorsión y la deformación del material.
Ventajas:
- Proceso rápido y eficiente.
- Ideal para materiales ligeros y piezas de espesor moderado.
- Minimiza la distorsión y los defectos en la soldadura.
Aplicaciones:
- Soldadura de componentes en la industria automotriz y aeronáutica.
- Fabricación de piezas de aluminio y otras aleaciones ligeras.
- Unión de componentes en la fabricación de equipos de alta precisión.
Conclusión
Los sistemas de soldadura de unión circular son fundamentales para la producción de componentes cilíndricos en diversas industrias. Desde los sistemas automatizados como la soldadura orbital hasta procesos más tradicionales como MIG/MAG, TIG, y soldadura por láser, cada técnica tiene sus ventajas y se selecciona en función de las necesidades específicas de la aplicación, el material, la precisión requerida y la escala de producción. La tendencia hacia la automatización, la precisión y la eficiencia está transformando estos procesos, mejorando la calidad y reduciendo los costos y tiempos de producción.
Los sistemas de soldadura de unión circular permiten unir piezas de forma continua y precisa alrededor de un perímetro circular. Estos sistemas son clave en la fabricación de productos como tubos, recipientes a presión y componentes cilíndricos en diversas industrias. La soldadura orbital es uno de los métodos más utilizados, proporcionando una soldadura automática, precisa y constante. Este proceso, que utiliza una antorcha que gira alrededor del material, garantiza un cordón uniforme y de alta calidad, ideal para aplicaciones en sectores como el aeroespacial, farmacéutico y de procesamiento de alimentos.
Por otro lado, la soldadura por arco sumergido (SAW) es una opción eficiente para grandes volúmenes de producción. Este proceso es adecuado para piezas de gran espesor, utilizando un fundente que cubre el arco para proteger la soldadura y mejorar la penetración. Aunque es menos preciso que la soldadura orbital, su alta tasa de deposición lo convierte en una opción popular en industrias pesadas como la construcción de estructuras metálicas y la fabricación de grandes recipientes.
La soldadura MIG/MAG, por su parte, es un proceso versátil y ampliamente utilizado en la industria para una variedad de materiales. Su principal ventaja es la capacidad de soldar en diversas posiciones, lo que lo hace ideal para aplicaciones en las que las piezas son de diferentes formas y tamaños. Este proceso es rápido y efectivo, y se utiliza en la fabricación de sistemas de tuberías, vehículos y estructuras metálicas.
En el ámbito de la precisión, la soldadura TIG ofrece un control total del calor, lo que la hace perfecta para materiales finos y trabajos de alta calidad. Su capacidad para producir soldaduras limpias, sin contaminantes y estéticamente perfectas la convierte en la opción preferida para sectores donde se requiere una soldadura visualmente impecable, como en la industria aeroespacial y médica.
La soldadura por láser es una tecnología avanzada que utiliza un haz concentrado de luz para fundir los materiales a unir. Ofrece alta velocidad de soldadura, baja distorsión térmica y la capacidad de trabajar con materiales delicados y de alta resistencia. Aunque es costosa y requiere equipos especializados, es ideal para aplicaciones donde la precisión es crítica y los márgenes de error son mínimos, como en la fabricación de componentes de alta tecnología.
Finalmente, la soldadura por fricción, que se basa en el calor generado por el roce entre las piezas a soldar, es otra alternativa para aplicaciones de unión circular. Este proceso no requiere material de relleno y es ideal para materiales ligeros como el aluminio. Su ventaja principal es la reducción de distorsión térmica, lo que permite obtener uniones fuertes y duraderas sin deformar las piezas.
En conclusión, los sistemas de soldadura de unión circular se eligen según el tipo de material, la precisión requerida, el tamaño de la pieza y la velocidad de producción. Cada método tiene sus características y ventajas específicas, y la elección del proceso adecuado depende de los requisitos técnicos y económicos de la aplicación. La innovación en estos procesos, como la automatización y el control de calidad, ha permitido mejorar la productividad y la calidad de las soldaduras, haciendo posible la fabricación de productos cada vez más complejos y resistentes.
El avance continuo en los sistemas de soldadura de unión circular también ha llevado a una mayor integración de la tecnología de monitoreo y control. Los equipos de soldadura modernos a menudo cuentan con sensores y sistemas de retroalimentación que permiten ajustar parámetros en tiempo real para optimizar el proceso. Estos avances mejoran la consistencia y la calidad de la soldadura, reduciendo defectos como porosidad, grietas y distorsiones térmicas, los cuales pueden comprometer la integridad de las uniones.
La automatización y la integración con sistemas robóticos se han convertido en una tendencia significativa en la industria. Los robots de soldadura, especialmente en la soldadura orbital y otras aplicaciones de unión circular, permiten una repetibilidad exacta y la capacidad de realizar soldaduras en áreas de difícil acceso, todo mientras mantienen una alta velocidad de producción. Esto no solo aumenta la eficiencia, sino que también reduce el riesgo de errores humanos y mejora la seguridad laboral, dado que los procesos automatizados suelen ser más seguros en entornos de trabajo peligrosos.
Además, con la creciente demanda de soldaduras más limpias y más respetuosas con el medio ambiente, muchos procesos están evolucionando para reducir el uso de materiales contaminantes como los fundentes y gases protectores. La soldadura por láser, por ejemplo, minimiza la necesidad de materiales adicionales y se caracteriza por una menor emisión de gases, lo que contribuye a una mayor sostenibilidad en la producción.
Otro factor clave en la evolución de los sistemas de soldadura de unión circular es la capacidad de soldar materiales avanzados. A medida que se desarrollan nuevos materiales con propiedades específicas, como aleaciones de alta resistencia, composites o materiales cerámicos, los sistemas de soldadura deben adaptarse a estos desafíos. Por ejemplo, la soldadura de materiales como el titanio, el grafeno o aleaciones complejas requiere procesos altamente especializados, como el uso de soldadura por láser o electrones. Estos materiales a menudo tienen propiedades térmicas, estructurales y químicas únicas, lo que exige una tecnología de soldadura avanzada que pueda mantener la integridad de la unión sin comprometer las características del material.
La monitorización en tiempo real es otro avance importante que ha transformado la soldadura. Los sistemas de monitoreo de temperatura, visualización del proceso y análisis de la calidad de la soldadura permiten a los operadores verificar instantáneamente si la soldadura está cumpliendo con los estándares establecidos. Estos sistemas también pueden identificar defectos durante el proceso, lo que permite tomar medidas correctivas de inmediato para evitar la producción de piezas defectuosas.
Otro aspecto importante que ha evolucionado es la tecnología de soldadura por arco de plasma. Este método combina las ventajas de la soldadura por arco con la precisión y control de la energía proporcionados por el plasma, lo que lo convierte en una excelente opción para la soldadura de unión circular en materiales no ferrosos, como el aluminio y sus aleaciones. Su aplicación está en constante expansión, especialmente en la industria aeroespacial, automotriz y de electrónica, donde la precisión y la resistencia son cruciales.
En términos de capacidades de personalización de los sistemas de soldadura, se ha avanzado en el diseño modular de equipos, que permiten adaptar la maquinaria a diferentes tamaños de piezas y requisitos específicos del cliente. Las máquinas de soldadura orbital, por ejemplo, se pueden ajustar para adaptarse a distintos diámetros de tuberías o recipientes, proporcionando flexibilidad en la producción sin necesidad de reemplazar equipos completos.
El uso de simuladores y software avanzado también se está volviendo cada vez más común en la capacitación de operadores y en el diseño de procesos de soldadura. Estos sistemas permiten modelar de manera precisa cómo se comportará la soldadura bajo diferentes condiciones, lo que no solo mejora la capacitación, sino que también permite a los ingenieros diseñar procesos de soldadura óptimos antes de la producción real. Esta capacidad de predecir el comportamiento de las soldaduras ayuda a reducir los costos asociados con pruebas físicas y posibles errores.
Finalmente, la conectividad de los sistemas de soldadura con otras partes del proceso de producción también está mejorando. Los sistemas de soldadura son ahora capaces de integrarse con plataformas de gestión de producción, lo que permite un control total de la fabricación. Esto facilita la programación, la planificación de la producción y la trazabilidad de las soldaduras, lo que es esencial para cumplir con los estándares de calidad y las normativas industriales cada vez más estrictas.
En resumen, la evolución de los sistemas de soldadura de unión circular está marcada por avances en automatización, monitoreo en tiempo real, precisión y sostenibilidad. Estos avances no solo permiten mejorar la calidad y la eficiencia de la soldadura, sino que también abren la puerta a la fabricación de productos más complejos y de alta tecnología, adaptándose a los nuevos desafíos de la industria.
La industria de la soldadura continúa evolucionando con la incorporación de nuevas tecnologías y procesos que permiten lograr un rendimiento y calidad aún mayores. El desarrollo de materiales avanzados como aleaciones de alta resistencia, composites y materiales compuestos ha impulsado la necesidad de adaptar los sistemas de soldadura para enfrentar los retos específicos que presentan estos materiales. A medida que estos materiales se vuelven más comunes en sectores como la aeroespacial, automotriz, de energía y electrónica, los sistemas de soldadura también deben adaptarse a sus propiedades particulares, como la alta resistencia térmica, conductividad eléctrica o reactividad química.
Uno de los aspectos más destacados en la evolución de la soldadura ha sido la introducción de la inteligencia artificial y el aprendizaje automático. Estos avances permiten a los sistemas de soldadura no solo monitorear y ajustar parámetros en tiempo real, sino también aprender de los resultados para mejorar de forma autónoma. Mediante el análisis de datos de soldadura recogidos durante el proceso, los sistemas pueden predecir posibles defectos o problemas antes de que ocurran, optimizando así la calidad y reduciendo la cantidad de material desperdiciado. Esto es particularmente útil en aplicaciones donde la calidad y precisión son críticas, como en la fabricación de componentes de aeronaves o dispositivos médicos.
La soldadura adaptativa es otro avance prometedor. Este proceso permite que la máquina de soldadura ajuste automáticamente sus parámetros de operación en función de la geometría de la pieza, el material y las condiciones de soldadura, lo que mejora la calidad del cordón de soldadura y reduce la posibilidad de errores. Esto es especialmente útil cuando se trabaja con piezas de geometría compleja o cuando se requiere una alta precisión en la forma y el tamaño del cordón de soldadura.
Además, la sostenibilidad ha cobrado una importancia cada vez mayor en la industria. Los esfuerzos para reducir el impacto ambiental de los procesos de soldadura se han intensificado, lo que ha llevado a la adopción de tecnologías más limpias. Los sistemas de soldadura ahora emplean menos gases de protección, fundentes y materiales consumibles, lo que no solo reduce el impacto ambiental, sino que también disminuye los costos operativos. En algunos casos, la soldadura por láser y la soldadura por arco de plasma, por ejemplo, han demostrado ser más eficientes energéticamente, ya que requieren menos energía para lograr resultados de alta calidad, lo que reduce tanto el consumo de recursos como la huella de carbono de la producción.
La digitalización en la industria también ha promovido una mejora en la trazabilidad y el control de calidad. Los sistemas modernos permiten registrar cada paso del proceso de soldadura, desde los parámetros de operación hasta los resultados de inspección, proporcionando un archivo detallado que puede ser revisado y auditado en cualquier momento. Esto es fundamental en industrias donde los estándares de calidad y la documentación son esenciales, como en la fabricación de dispositivos médicos o en la industria automotriz, donde se deben cumplir estrictas normativas de seguridad y calidad.
La colaboración entre la soldadura y otras disciplinas de manufactura también está avanzando rápidamente. Por ejemplo, los sistemas de soldadura ahora se integran fácilmente con otras operaciones de fabricación, como el corte, el conformado y la inspección. Esto crea un entorno de manufactura más flexible, en el que los sistemas pueden intercambiar datos en tiempo real para optimizar toda la cadena de producción, desde el diseño hasta la entrega final del producto. Además, la integración de tecnologías como la fabricación aditiva está comenzando a desempeñar un papel en la creación de nuevas soluciones de soldadura. Esto permite que las piezas que se van a soldar sean impresas en 3D con la precisión necesaria, lo que puede mejorar la eficiencia en la producción de piezas complejas.
La fabricación de piezas de alta precisión es una necesidad creciente en sectores como la microelectrónica, donde incluso los más pequeños defectos en una soldadura pueden resultar en fallos del producto. La evolución de la soldadura en este sector ha dado lugar a procesos más controlados y sofisticados que garantizan que cada pieza cumpla con los estándares más altos. Los avances en la soldadura de unión circular en estos casos han permitido la fabricación de circuitos y componentes más pequeños y complejos, mejorando las capacidades tecnológicas de productos como los smartphones, dispositivos portátiles y sistemas informáticos.
Además, el mantenimiento predictivo ha ganado relevancia en el sector de la soldadura industrial. Los sensores incorporados en los equipos de soldadura pueden detectar signos de desgaste o mal funcionamiento en tiempo real. Esto permite que los operadores o los sistemas automatizados ajusten los parámetros de la máquina o realicen reparaciones antes de que el equipo falle, lo que minimiza el tiempo de inactividad y mejora la eficiencia general de la planta. El uso de sensores avanzados para monitorear las condiciones de las máquinas también contribuye a la reducción de costos al evitar fallos inesperados y prolongar la vida útil del equipo.
Con la expansión de la Industria 4.0, los sistemas de soldadura están cada vez más conectados y son capaces de compartir datos en redes inteligentes. La interoperabilidad entre diferentes equipos y dispositivos dentro de la fábrica permite una optimización del flujo de trabajo, lo que mejora la eficiencia global de la planta de producción. Esto también se traduce en una mejor planificación y control de los inventarios, ya que las herramientas de soldadura pueden reportar en tiempo real sobre su utilización, los materiales consumidos y las necesidades de mantenimiento.
En resumen, la evolución de los sistemas de soldadura de unión circular continúa avanzando hacia soluciones más automatizadas, precisas, sostenibles y eficientes. Estos avances no solo mejoran la calidad de las soldaduras y reducen los costos operativos, sino que también permiten adaptarse a los desafíos de materiales más complejos y diseños más sofisticados. La integración de tecnologías emergentes, como la inteligencia artificial, la automatización avanzada y la digitalización, promete transformar la manera en que las empresas de soldadura operan, brindando mayores niveles de flexibilidad, eficiencia y control.
A medida que la tecnología de soldadura continúa avanzando, es probable que se vean nuevas innovaciones en materiales y procesos que amplíen aún más las aplicaciones de la soldadura de unión circular. Por ejemplo, la creciente demanda de materiales compuestos y aleaciones exóticas requerirá que los sistemas de soldadura se adapten para garantizar uniones fuertes y duraderas sin comprometer las propiedades de los materiales base. Los sistemas de soldadura deberán evolucionar para manejar la diversidad de propiedades que tienen estos materiales, como sus distintas temperaturas de fusión, composición química y comportamiento térmico.
La soldadura en ambientes extremos, como el espacio exterior o las profundidades oceánicas, también está experimentando avances. En el sector aeroespacial, por ejemplo, la necesidad de soldar materiales ligeros pero resistentes, como las aleaciones de titanio, junto con la protección contra la radiación y las altas presiones durante las operaciones en el espacio, está llevando a nuevas soluciones de soldadura. Los equipos están siendo diseñados para trabajar con precisión en condiciones de vacío o a altas presiones, utilizando sistemas de soldadura avanzados que aseguran que las uniones sean resistentes y confiables incluso en las condiciones más adversas.
En la industria de la energía renovable, especialmente en la fabricación de componentes para energía solar, eólica y baterías de almacenamiento, la soldadura de unión circular juega un papel crucial en la creación de estructuras y equipos de alta resistencia. La soldadura de componentes como las torres de turbinas eólicas o los paneles solares requiere un enfoque específico para asegurar la integridad estructural y la durabilidad a largo plazo en condiciones ambientales extremas. A medida que la energía renovable sigue ganando terreno, la soldadura de unión circular será clave para garantizar la fiabilidad y la eficiencia de los sistemas en este sector en expansión.
En cuanto a la soldadura automatizada, la integración de robots de soldadura avanzados y sistemas de visión artificial ha llevado a mejoras significativas en el proceso. Los robots de soldadura ahora no solo se encargan de las tareas repetitivas, sino que también pueden ajustar en tiempo real los parámetros de la soldadura según la geometría de la pieza y las condiciones cambiantes de la soldadura. Esto permite trabajar con una variedad de piezas complejas sin sacrificar la calidad de la soldadura. La incorporación de inteligencia artificial (IA) en estos robots también puede permitir la optimización dinámica de las trayectorias de soldadura, reduciendo el tiempo necesario para completar una tarea sin comprometer la precisión.
Un aspecto crucial en la soldadura de unión circular es la inspección y el control de calidad. Con la ayuda de tecnologías avanzadas como la tomografía por rayos X, la inspección por ultrasonido y la tecnología de visión 3D, es posible realizar un seguimiento de la soldadura de manera mucho más detallada. Estas tecnologías permiten detectar defectos internos que no son visibles a simple vista, como porosidad o grietas microscópicas, y garantizan que las uniones cumplan con los estrictos estándares de seguridad y calidad. La implementación de estos sistemas no solo mejora la seguridad de los productos finales, sino que también optimiza el proceso de fabricación al identificar y corregir problemas de calidad de manera más eficiente.
La fabricación de piezas personalizadas es otra tendencia creciente en la soldadura de unión circular. La personalización de productos, especialmente en sectores como la automotriz y la industria médica, está impulsando la demanda de soluciones de soldadura altamente flexibles. Los avances en la fabricación aditiva y el modelado 3D están permitiendo que las piezas sean fabricadas a medida, lo que obliga a los sistemas de soldadura a ser igualmente adaptables para manejar estos diseños complejos. Este enfoque permite crear productos más ligeros y eficientes, ajustados específicamente a las necesidades del cliente.
La soldadura de unión circular también se está volviendo cada vez más relevante en la industria de la defensa. Los equipos de soldadura están siendo utilizados para crear piezas cruciales en la fabricación de vehículos blindados, aeronaves militares y otros sistemas de defensa. En este contexto, las soldaduras deben ser especialmente fuertes y resistentes a las condiciones extremas, como el choque, la vibración y las altas temperaturas, lo que pone a prueba tanto la tecnología de soldadura como los materiales empleados.
En cuanto a las normativas y estándares en la soldadura, la constante evolución de la industria impulsa la necesidad de adaptarse a las nuevas normativas ambientales y de seguridad. Los avances en la tecnología de soldadura están ayudando a las empresas a cumplir con los reglamentos internacionales que exigen menos emisiones contaminantes, mayor eficiencia energética y mejor gestión de los desechos. La soldadura de unión circular está siendo cada vez más reconocida como un proceso clave para lograr estos objetivos, ya que sus sistemas automatizados y su precisión ayudan a reducir el uso de materiales y la generación de residuos.
En términos de entrenamiento y capacitación, la adopción de la realidad aumentada (AR) y la realidad virtual (VR) ha permitido la capacitación de soldadores en entornos virtuales. Estas tecnologías ofrecen simulaciones interactivas que permiten a los operadores aprender técnicas de soldadura en un entorno seguro y controlado antes de trabajar con equipos reales. Esto no solo reduce los riesgos laborales, sino que también acelera el proceso de capacitación, asegurando que los operadores adquieran habilidades prácticas sin necesidad de acceder a equipos costosos o materiales reales para las prácticas.
La tecnología de soldadura híbrida, que combina múltiples métodos de soldadura, está también ganando terreno. Un ejemplo de ello es la combinación de soldadura láser y soldadura por arco para aprovechar las ventajas de ambos procesos, como la alta velocidad de la soldadura láser y la capacidad de penetración profunda del arco eléctrico. Esto permite soldar materiales más gruesos y complejos, logrando una unión fuerte y precisa.
En resumen, el futuro de los sistemas de soldadura de unión circular está marcado por la innovación constante y la adaptabilidad a las nuevas demandas industriales. La integración de tecnologías avanzadas como la automatización, la inteligencia artificial, la visión artificial y la fabricación aditiva está permitiendo una producción más rápida, precisa y sostenible. A medida que surgen nuevos materiales, procesos y desafíos, los sistemas de soldadura evolucionarán para satisfacer las necesidades de sectores tan diversos como la energía renovable, la defensa, la microelectrónica y la fabricación de componentes a medida.
Equipos para soldar cordón circular
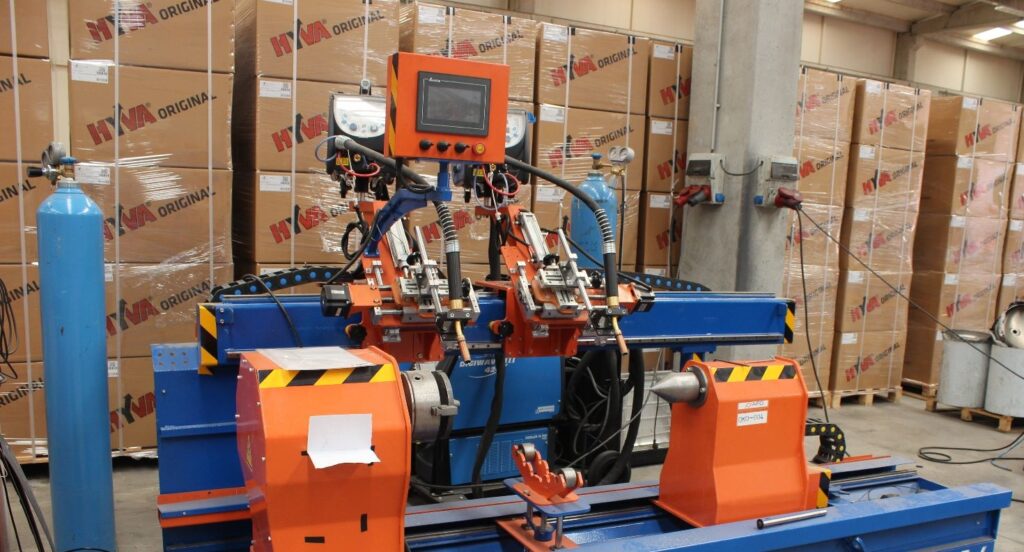
Los equipos para soldar cordón circular son herramientas especializadas diseñadas para realizar soldaduras en piezas que requieren uniones continuas alrededor de un contorno circular o tubular. Estos equipos son utilizados principalmente en aplicaciones donde las piezas tienen una geometría circular, como tubos, recipientes, silos, y componentes de estructuras cilíndricas. Existen varios tipos de equipos que se utilizan en estos procesos, dependiendo de la aplicación específica, el material, y el tipo de soldadura que se necesite. A continuación se describen algunos de los principales tipos de equipos utilizados para soldar cordón circular:
1. Máquinas de Soldadura Orbital
Las máquinas de soldadura orbital son una de las opciones más comunes para realizar soldaduras de cordón circular de alta calidad. Estos equipos utilizan una antorcha de soldadura que gira alrededor del material a soldar, proporcionando un cordón de soldadura continuo y uniforme. Este tipo de equipo es ideal para aplicaciones donde se requiere precisión, como en la fabricación de tuberías para la industria farmacéutica, alimentaria, de energía, y en el sector aeroespacial.
- Ventajas: Alta precisión, calidad constante, automatización, mínima intervención manual.
- Aplicaciones: Soldadura de tubos, recipientes de presión, intercambiadores de calor, y otras aplicaciones industriales.
- Características: Se utilizan principalmente para soldadura TIG (Tungsten Inert Gas), aunque también pueden utilizarse otros procesos como MIG/MAG en algunos casos.
2. Robots de Soldadura
Los robots de soldadura son muy utilizados para realizar soldaduras de cordón circular en ambientes de producción masiva. Estos robots se programan para realizar movimientos precisos alrededor de las piezas, lo que asegura un cordón de soldadura continuo y uniforme. Son ideales para tareas repetitivas y cuando se requiere una alta tasa de producción.
- Ventajas: Alta productividad, reducción de errores humanos, capacidad para realizar soldaduras en posiciones difíciles.
- Aplicaciones: Soldadura de componentes automotrices, estructuras metálicas, y piezas de gran tamaño.
- Características: Estos robots pueden estar equipados con diferentes tipos de antorchas y sistemas de alimentación de material, dependiendo del tipo de soldadura (TIG, MIG, etc.).
3. Máquinas de Soldadura por Arco Sumergido (SAW)
La soldadura por arco sumergido es un proceso utilizado cuando se necesita alta velocidad de soldadura, especialmente para piezas de gran espesor. En este proceso, el arco de soldadura se encuentra sumergido en un fundente granular, lo que protege la soldadura de la atmósfera y permite una mayor penetración.
- Ventajas: Alta tasa de deposición, adecuada para soldar materiales gruesos.
- Aplicaciones: Soldadura de estructuras pesadas, como barcos, plataformas offshore, y grandes recipientes de presión.
- Características: Ideal para piezas de gran tamaño y espesor, pero menos flexible en términos de tamaño de la pieza que otros métodos como la soldadura orbital.
4. Máquinas de Soldadura MIG/MAG
La soldadura MIG/MAG (Metal Inert Gas/Metal Active Gas) es un proceso de soldadura por arco eléctrico que utiliza un gas protector para proteger la soldadura del aire. Este proceso es muy versátil y es comúnmente utilizado para soldar una variedad de metales, incluidas aleaciones de acero, aluminio, y otros metales no ferrosos.
- Ventajas: Proceso rápido y flexible, apto para piezas finas y gruesas, menos sensibilización al calor.
- Aplicaciones: Fabricación de estructuras metálicas, sistemas de tuberías, maquinaria industrial, y piezas automotrices.
- Características: Adecuado para una variedad de materiales, fácil de automatizar, permite soldaduras en diferentes posiciones.
5. Soldadura TIG con Máquinas Especializadas
La soldadura TIG (Tungsten Inert Gas) es conocida por su capacidad para producir soldaduras de alta calidad con una apariencia estética excelente. Este proceso se utiliza a menudo en aplicaciones donde la precisión y la integridad del cordón de soldadura son esenciales. Las máquinas TIG especializadas para soldadura de cordón circular permiten un control preciso de la temperatura y el suministro de material de relleno.
- Ventajas: Alta precisión, excelente control de la soldadura, ideal para materiales delgados y aleaciones especiales.
- Aplicaciones: Industria aeroespacial, fabricación de componentes médicos, industrias de alta tecnología.
- Características: Requiere un operador experimentado, pero produce soldaduras de alta calidad y estética.
6. Máquinas de Soldadura por Láser
La soldadura por láser es una tecnología avanzada que utiliza un láser para fundir el material base. Es particularmente eficaz para materiales de alta resistencia y precisión. La soldadura por láser es capaz de realizar uniones precisas con una mínima distorsión térmica, lo que la hace ideal para aplicaciones que requieren soldaduras limpias y detalladas.
- Ventajas: Alta precisión, mínima distorsión térmica, alta velocidad de soldadura.
- Aplicaciones: Industria de alta tecnología, automotriz, aeroespacial y de dispositivos electrónicos.
- Características: Tecnología costosa, pero altamente efectiva en aplicaciones de precisión.
7. Máquinas de Soldadura por Fricción
La soldadura por fricción es un proceso donde la fricción entre las piezas a unir genera suficiente calor para fundir el material y permitir la formación de una soldadura. Este proceso no utiliza material de relleno y es ideal para metales ligeros como el aluminio.
- Ventajas: No requiere material adicional, produce uniones fuertes, reducción de distorsión térmica.
- Aplicaciones: Conexión de piezas de aluminio, fabricación de componentes automotrices.
- Características: Ideal para materiales ligeros, especialmente cuando se busca reducir la deformación térmica.
8. Sistemas de Soldadura Manuales y Semiautomáticos
Aunque los equipos automatizados son ideales para la producción masiva, en algunos casos, las máquinas de soldadura manuales o semiautomáticas son más adecuadas, especialmente cuando se realizan soldaduras en piezas de tamaño variado o cuando se requiere mayor flexibilidad.
- Ventajas: Flexibilidad, costos iniciales más bajos, control directo por parte del operario.
- Aplicaciones: Proyectos de menor escala, mantenimiento industrial, fabricación de prototipos y piezas únicas.
- Características: Requiere habilidad del operador para asegurar una soldadura de calidad.
En resumen, los equipos para soldar cordón circular varían ampliamente según el proceso de soldadura, el tipo de material y las características de la pieza a soldar. Cada tipo de equipo tiene ventajas y aplicaciones específicas, y la elección del equipo adecuado dependerá de factores como la calidad deseada, la velocidad de producción, y la naturaleza del material a soldar.
La elección del equipo adecuado para soldar cordón circular también está influenciada por el tipo de producción que se va a realizar. En entornos de producción en masa, los sistemas automatizados, como los robots de soldadura y las máquinas orbitales, son muy efectivos porque garantizan un alto rendimiento y una calidad constante en cada pieza. Estos equipos permiten realizar soldaduras de forma continua sin la intervención constante de un operador, lo que no solo mejora la eficiencia, sino también reduce los errores humanos y los defectos en las soldaduras. A medida que la tecnología sigue avanzando, la capacidad de monitorizar y ajustar parámetros en tiempo real es cada vez más común, lo que permite a los operarios gestionar las máquinas de manera más eficiente.
En aplicaciones de bajo volumen o de piezas personalizadas, los equipos de soldadura manuales o semiautomáticos siguen siendo una opción popular. Estos equipos permiten una mayor flexibilidad, ya que se pueden adaptar a diferentes tipos de piezas y geometrías sin necesidad de reconfiguraciones costosas o complicadas. Aunque la velocidad de producción puede ser menor en comparación con los sistemas totalmente automatizados, la capacidad de personalizar la soldadura según las necesidades específicas de cada pieza es una ventaja considerable en ciertas industrias, como la fabricación de prototipos o el mantenimiento industrial.
Además, la creciente demanda de soldaduras más limpias y ecológicas ha impulsado el desarrollo de tecnologías de soldadura que minimizan el impacto ambiental. Los procesos como la soldadura por láser y la soldadura TIG son altamente eficientes y generan menos residuos comparado con otras técnicas más tradicionales. En particular, la soldadura por láser, con su capacidad para realizar soldaduras finas y precisas sin la necesidad de un gas de protección, ha abierto nuevas oportunidades en sectores donde la estética de la soldadura y la minimización de la distorsión térmica son críticas.
Por otro lado, la soldadura por fricción es un proceso innovador que está ganando popularidad en ciertos sectores debido a su capacidad para unir metales sin el uso de material de relleno. Esto no solo reduce el costo de materiales, sino que también mejora la resistencia de la unión, ya que se forma una soldadura sin impurezas de relleno. Este tipo de soldadura es especialmente útil para materiales como el aluminio y otras aleaciones ligeras que requieren un control preciso de la temperatura para evitar deformaciones no deseadas.
En cuanto al futuro, es posible que veamos una mayor integración de la inteligencia artificial y los sistemas de visión en los equipos de soldadura. Estos avances tecnológicos permitirán a las máquinas aprender y adaptarse a diferentes condiciones de trabajo, lo que se traducirá en un proceso más eficiente y menos dependiente de la intervención humana. Los sistemas de visión artificial pueden inspeccionar la soldadura en tiempo real, ajustando los parámetros de operación según las variaciones detectadas en la pieza o el cordón de soldadura. Esto no solo mejora la calidad, sino que también reduce el riesgo de defectos y la necesidad de pruebas adicionales.
El control preciso de los parámetros de soldadura, como la corriente, la velocidad de avance y la temperatura, es crucial para garantizar que el cordón de soldadura cumpla con las especificaciones exactas. En muchos casos, las máquinas modernas están equipadas con sistemas que permiten ajustar estos parámetros en tiempo real para optimizar el proceso, reducir la cantidad de material desperdiciado y mejorar la integridad de la unión.
Los avances en la soldadura de materiales disímiles también están impulsando el desarrollo de nuevos equipos. En muchos sectores industriales, es común encontrar piezas fabricadas con diferentes tipos de materiales que requieren técnicas de soldadura especializadas para asegurar una unión fuerte y duradera. Los equipos de soldadura de última generación ahora pueden manejar una gama más amplia de materiales y metales, lo que permite una mayor versatilidad en la producción.
La soldadura automatizada, en particular, está permitiendo que las industrias se adapten más rápidamente a los cambios en los requisitos de producción. Por ejemplo, los sistemas de soldadura robóticos pueden ser reprogramados fácilmente para soldar diferentes piezas o realizar distintas configuraciones, lo que hace que las plantas de producción sean más flexibles y adaptables a las demandas cambiantes del mercado. Este nivel de flexibilidad es esencial para sectores como la automoción, donde las líneas de producción deben ajustarse rápidamente a nuevas series de modelos.
En resumen, los equipos para soldar cordón circular están evolucionando para adaptarse a una variedad de necesidades y requisitos industriales, desde la producción masiva hasta proyectos personalizados de baja escala. El avance continuo en automatización, tecnología de control en tiempo real, y procesos más sostenibles promete transformar la industria de la soldadura, mejorando la eficiencia, la calidad y la flexibilidad de los procesos. Estos avances también facilitan la transición hacia la fabricación de componentes más complejos, con una mayor precisión y menor impacto ambiental, asegurando que los equipos sigan siendo una herramienta clave en la manufactura moderna.
El futuro de los equipos para soldar cordón circular no solo está marcado por avances tecnológicos, sino también por la necesidad de adaptarse a nuevas demandas industriales y a regulaciones más estrictas en cuanto a sostenibilidad y eficiencia. En este contexto, las innovaciones en materiales y los procesos de soldadura híbridos juegan un papel fundamental. Los materiales avanzados, como los metales ligeros y las aleaciones de alta resistencia, están siendo cada vez más comunes, especialmente en industrias como la aeroespacial, automotriz y energía renovable. Estos materiales requieren equipos de soldadura que sean capaces de adaptarse a sus propiedades únicas y garantizar uniones fuertes sin comprometer la integridad de las piezas.
La soldadura por láser, por ejemplo, está siendo cada vez más utilizada para la soldadura de metales difíciles, como titanio o aluminio, debido a su capacidad para concentrar la energía en una zona muy pequeña y proporcionar una soldadura precisa y limpia. Este proceso es especialmente útil en sectores que requieren alta resistencia y reducción de peso, como la industria aeronáutica y la fabricación de componentes electrónicos de alta precisión. Las máquinas de soldadura láser están mejorando continuamente, con sistemas más potentes y flexibles que permiten la soldadura de una gama más amplia de materiales y grosores.
Por otro lado, la soldadura por arco eléctrico sigue siendo una de las opciones más populares para el cordón circular, especialmente en industrias donde la robustez y la resistencia de la unión son cruciales, como en la construcción de estructuras metálicas y en la fabricación de equipos pesados. Las máquinas de soldadura MIG/MAG y TIG han evolucionado para incluir características avanzadas, como la retroalimentación en tiempo real de la calidad de la soldadura y la ajuste automático de los parámetros, lo que garantiza una mayor precisión y un mayor control sobre la soldadura.
Además, la automatización avanzada y la inteligencia artificial están transformando los equipos de soldadura, lo que permite una mayor personalización y adaptabilidad. Los robots de soldadura con capacidades de aprendizaje automático son capaces de ajustar sus trayectorias de soldadura y parámetros según las condiciones específicas de cada pieza, lo que reduce significativamente el riesgo de errores y mejora la calidad de las uniones. En aplicaciones de producción en masa, esto se traduce en una mayor velocidad de producción y una reducción de los costos laborales.
Otro avance clave es el uso de sensores y cámaras integradas en los sistemas de soldadura. Estos sistemas pueden monitorear la calidad del cordón de soldadura en tiempo real, identificando posibles defectos como la porosidad, la fisuración o la falta de fusión. La visión artificial no solo permite la inspección de la soldadura, sino que también puede ajustar los parámetros automáticamente para corregir cualquier variación durante el proceso. Este enfoque no solo mejora la calidad de las soldaduras, sino que también reduce la necesidad de pruebas destructivas, lo que ahorra tiempo y dinero.
En el ámbito de la soldadura de materiales disímiles, que involucra la unión de materiales diferentes con propiedades físicas y químicas contrastantes, los avances tecnológicos están haciendo posible que los equipos de soldadura sean mucho más versátiles. Las máquinas de soldadura híbrida, que combinan diferentes métodos de soldadura, como el láser y el arco eléctrico, permiten unir materiales como acero inoxidable con aluminio o cobre, dos metales que normalmente no se soldarían fácilmente entre sí. Este tipo de innovación es especialmente útil en la industria automotriz y eléctrica, donde la unión de materiales disímiles es cada vez más común.
La sostenibilidad es otro factor importante que está moldeando el futuro de los equipos de soldadura. Con el aumento de la conciencia ambiental y las regulaciones más estrictas, las empresas están buscando formas de reducir el consumo de energía y los desperdicios de material durante los procesos de soldadura. Las nuevas tecnologías están enfocadas en hacer que los procesos de soldadura sean más eficientes, utilizando menos energía y generando menos residuos. Por ejemplo, la soldadura por fricción y la soldadura por láser son procesos que minimizan la generación de calor y, por lo tanto, la cantidad de energía utilizada en el proceso. Además, los avances en tecnologías de recubrimientos permiten que las piezas sean soldadas con menos material de relleno, lo que reduce los costos y mejora la eficiencia.
En cuanto a la capacitación de los operadores, el entrenamiento en realidad aumentada (AR) y realidad virtual (VR) está ganando popularidad. Estas tecnologías permiten a los trabajadores aprender y practicar técnicas de soldadura en un entorno simulado antes de realizar el trabajo real. Este tipo de capacitación mejora la seguridad, reduce los errores y acorta los tiempos de aprendizaje, lo que se traduce en una mayor eficiencia general en la producción.
En resumen, los equipos para soldar cordón circular están en constante evolución, adaptándose a las nuevas tecnologías, materiales y exigencias industriales. Desde la automatización avanzada y robots de soldadura, hasta máquinas láser de última generación, los avances están permitiendo una mayor precisión, eficiencia y sostenibilidad en el proceso de soldadura. Los desarrollos en tecnologías híbridas, materiales avanzados y sensores inteligentes están abriendo nuevas oportunidades para mejorar la calidad de las soldaduras, reducir los costos y aumentar la productividad, todo mientras se cumplen con los estándares de seguridad y medioambientales más exigentes.
Soldadores de cordón circular
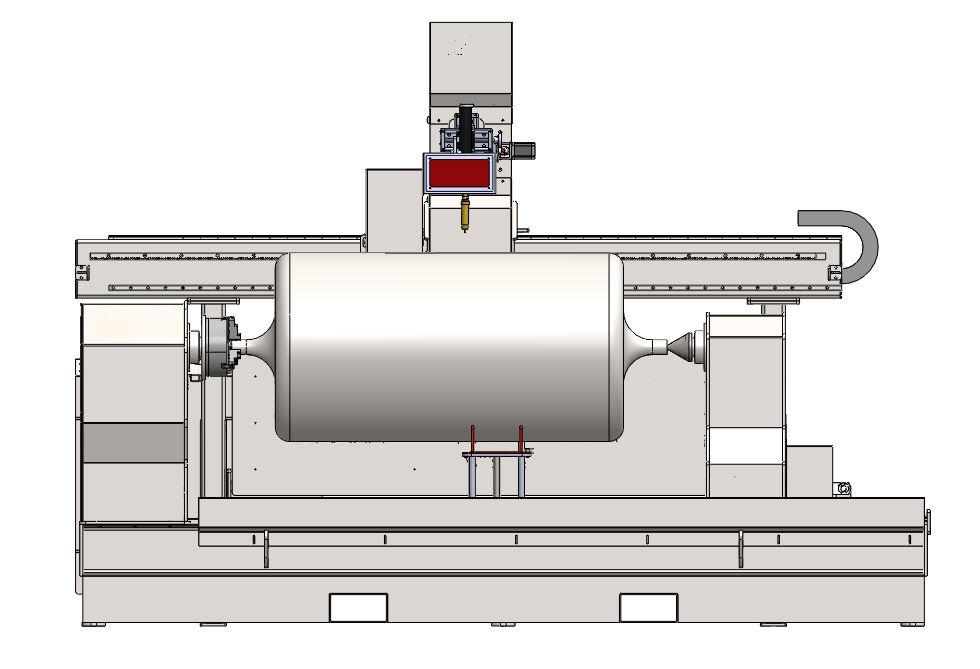
Los soldadores de cordón circular son equipos diseñados para realizar soldaduras continuas alrededor de una pieza o componente de forma circular o tubular. Estos soldadores son fundamentales en industrias donde las piezas tienen geometría circular o en aplicaciones que requieren una unión constante y uniforme alrededor de un contorno, como en la fabricación de tubos, recipientes de presión, intercambiadores de calor, y componentes de grandes estructuras metálicas. A continuación, se describen los tipos más comunes de soldadores utilizados para este tipo de trabajo, junto con sus aplicaciones y características principales:
1. Soldadores Orbitales
Los soldadores orbitales son equipos de alta precisión que emplean una antorcha que gira alrededor de la pieza a soldar, realizando un cordón continuo sin interrupciones. Estos sistemas se utilizan principalmente para procesos de soldadura TIG (Tungsten Inert Gas), aunque también pueden emplearse otros procesos como el MIG/MAG. Los soldadores orbitales son muy valorados en aplicaciones donde la precisión y la uniformidad del cordón son esenciales, como en la fabricación de tuberías de acero inoxidable y otros metales.
- Ventajas: Gran precisión, automatización del proceso, capacidad para soldar en posiciones difíciles o de difícil acceso, calidad constante.
- Aplicaciones: Soldadura de tubos y conductos en industrias como la farmacéutica, alimentaria, aeroespacial y energía.
- Características: La antorcha se mueve en un patrón orbital alrededor de la pieza, lo que garantiza una soldadura continua y uniforme. Estos equipos suelen estar equipados con sistemas de control que permiten ajustar parámetros como la velocidad de la antorcha, la corriente de soldadura y la alimentación del material de relleno.
2. Soldadores Robóticos
Los soldadores robóticos utilizan robots automatizados que realizan movimientos precisos alrededor de las piezas, siguiendo un patrón circular para crear un cordón de soldadura uniforme. Estos robots pueden estar equipados con diferentes tipos de antorchas, como MIG, TIG o incluso láser, dependiendo de las necesidades del proceso de soldadura. Los robots de soldadura son ideales para entornos de producción en masa o cuando se requieren soldaduras repetitivas de alta calidad.
- Ventajas: Alta productividad, precisión, flexibilidad, capacidad para trabajar en ambientes de producción continua.
- Aplicaciones: Fabricación de componentes automotrices, estructuras metálicas, intercambiadores de calor y otros productos industriales.
- Características: Los robots de soldadura pueden realizar soldaduras en una variedad de posiciones y formas geométricas, lo que los hace ideales para trabajos que requieren alta velocidad y flexibilidad. Además, pueden integrar sistemas de inspección en tiempo real para asegurar la calidad de la soldadura.
3. Soldadores Manuales y Semiautomáticos
Los soldadores manuales o semiautomáticos son equipos más simples y económicos que se utilizan para realizar soldaduras de cordón circular en proyectos pequeños o cuando la flexibilidad y la adaptabilidad son esenciales. Los soldadores semiautomáticos pueden ser utilizados en procesos como MIG o TIG, y el operador tiene un control directo sobre la velocidad de avance, la temperatura y la cantidad de material de relleno utilizado.
- Ventajas: Flexibilidad, menor costo inicial, adecuado para trabajos de baja a mediana producción.
- Aplicaciones: Soldadura de componentes individuales, reparación y mantenimiento de equipos, fabricación de prototipos.
- Características: Estos equipos permiten a los operarios realizar soldaduras precisas, aunque no son tan rápidos ni automáticos como los robots o las máquinas orbitales. Sin embargo, permiten una gran flexibilidad en la elección de los parámetros de soldadura y son útiles cuando se requiere intervención manual para ajustar el proceso.
4. Soldadores de Arco Sumergido (SAW)
La soldadura por arco sumergido (SAW) es un proceso utilizado principalmente para soldaduras de gran volumen y piezas gruesas. En este proceso, el arco eléctrico se encuentra sumergido en un fundente granular, lo que protege la soldadura del aire y reduce la cantidad de salpicaduras. Aunque este proceso se usa comúnmente en posiciones planas o horizontales, puede adaptarse para realizar soldaduras circulares en algunas aplicaciones industriales de gran escala.
- Ventajas: Alta tasa de deposición de material, ideal para piezas gruesas, excelente protección de la soldadura.
- Aplicaciones: Fabricación de grandes estructuras metálicas, construcción de barcos, plataformas offshore, intercambiadores de calor de gran tamaño.
- Características: El equipo de soldadura SAW está diseñado para manejar un arco sumergido en un fundente, lo que permite una mayor penetración y velocidad de soldadura en materiales gruesos.
5. Soldadores por Láser
Los soldadores por láser utilizan un rayo láser concentrado para fundir el material base y crear una soldadura precisa. Este tipo de soldadura es ideal para aplicaciones que requieren una alta calidad de soldadura con una mínima distorsión térmica, lo que es común en materiales delgados o en aplicaciones de alta precisión.
- Ventajas: Alta precisión, soldaduras finas con mínima distorsión térmica, velocidad de soldadura muy alta.
- Aplicaciones: Industria aeroespacial, electrónica, componentes automotrices de alta precisión, fabricación de dispositivos médicos.
- Características: Los soldadores por láser pueden realizar soldaduras extremadamente finas y estéticamente agradables, pero requieren un control preciso del equipo. Son ideales para aplicaciones donde la estética de la soldadura es tan importante como la resistencia.
6. Soldadores por Fricción
La soldadura por fricción es un proceso donde las piezas a soldar se frotan entre sí para generar calor, lo que permite que los metales se fusionen. Aunque este proceso no utiliza material de relleno, produce uniones fuertes y es ideal para metales como el aluminio.
- Ventajas: No requiere material de relleno, reduce la distorsión térmica, excelente para materiales ligeros.
- Aplicaciones: Unión de piezas de aluminio y otros metales ligeros en la industria automotriz y aeroespacial.
- Características: La soldadura por fricción es especialmente útil cuando se requieren uniones fuertes sin la necesidad de añadir material adicional, lo que la convierte en una opción eficiente y económica para ciertos tipos de producción.
Consideraciones Finales
Al seleccionar un soldador de cordón circular, es importante tener en cuenta el tipo de material que se va a soldar, el grosor de las piezas, el tipo de unión requerida, el volumen de producción y el presupuesto disponible. Los soldadores orbitales son ideales para trabajos de alta precisión y producción continua, mientras que los soldadores robóticos y manuales ofrecen más flexibilidad en aplicaciones específicas. Los soldadores por láser son perfectos para aplicaciones donde la precisión y la estética de la soldadura son esenciales, mientras que los soldadores por fricción ofrecen una alternativa sin material de relleno para uniones de metales ligeros. En última instancia, la elección del equipo adecuado dependerá de las necesidades particulares del proyecto y las especificaciones del trabajo de soldadura.
La elección de un soldador de cordón circular adecuado depende de varios factores que influyen en el proceso de producción, como el tipo de material, el grosor de las piezas, la precisión necesaria, la velocidad de producción y las condiciones operativas del entorno de trabajo. Es fundamental que el equipo de soldadura sea capaz de adaptarse a los requisitos específicos de cada proyecto para garantizar un cordón de soldadura de alta calidad, resistente y estéticamente adecuado.
En aplicaciones donde se requiere una alta precisión y la soldadura debe ser estéticamente perfecta, los soldadores orbitales y los soldadores por láser son opciones excepcionales. Los orbitales permiten una soldadura continua y uniforme sin la necesidad de intervención constante del operario, mientras que los láseres proporcionan una alta precisión en materiales delgados o en uniones de materiales disímiles, lo que los hace muy populares en sectores como la industria electrónica y la aeroespacial.
Por otro lado, los soldadores robóticos son ideales cuando se busca alta productividad y consistencia. Al integrar sistemas avanzados de inteligencia artificial y sensores, los robots pueden ajustarse automáticamente a las condiciones cambiantes del proceso de soldadura, lo que reduce la probabilidad de defectos y mejora la calidad de las uniones. Estos robots pueden realizar soldaduras de cordón circular en alta velocidad, lo que resulta esencial en líneas de producción en masa, como en la industria automotriz, donde se necesita realizar soldaduras de calidad a gran escala.
Si bien los sistemas automatizados son muy eficientes, no siempre son la mejor opción cuando se necesita flexibilidad o cuando el volumen de producción es bajo. En esos casos, los soldadores manuales o semiautomáticos siguen siendo una opción viable, ya que permiten un mayor control sobre el proceso y se pueden ajustar fácilmente para adaptarse a diferentes configuraciones y geometrías de las piezas. Estos equipos también son más económicos, lo que los hace accesibles para pequeñas y medianas empresas o para aplicaciones de mantenimiento y reparación de equipos.
En aplicaciones de soldadura de grandes volúmenes y materiales gruesos, como en la fabricación de estructura metálica o intercambiadores de calor, los soldadores de arco sumergido (SAW) son una opción preferida debido a su capacidad para depositar grandes cantidades de material de relleno rápidamente. Este proceso, al estar cubierto por un fundente, reduce la cantidad de salpicaduras y protege la soldadura, lo que lo convierte en una excelente opción para trabajos de alta producción y grandes estructuras.
Una de las tendencias más importantes en el futuro de los soldadores de cordón circular es la integración de tecnologías de visión artificial y sensores inteligentes. Estos sistemas permiten monitorear en tiempo real la calidad de la soldadura, identificando defectos o irregularidades durante el proceso. Si se detecta cualquier problema, el sistema puede ajustar automáticamente los parámetros de soldadura, como la corriente, la velocidad de avance o la temperatura, para corregir cualquier fallo. Esta capacidad de autocorrección no solo mejora la calidad de las soldaduras, sino que también reduce la necesidad de inspección manual y pruebas destructivas.
A medida que las demandas de sostenibilidad y eficiencia energética aumentan, se prevé que los soldadores de cordón circular del futuro incorporen tecnologías más ecológicas. Procesos como la soldadura por fricción y la soldadura láser son ejemplos de cómo las tecnologías pueden reducir el impacto ambiental al eliminar la necesidad de gases protectores o material de relleno, y al reducir las emisiones de calor y gases contaminantes. Esto, junto con el mejor control de la energía durante el proceso de soldadura, contribuye a la reducción de residuos y ahorro energético, dos factores cada vez más valorados en la industria.
Además, el desarrollo de materiales avanzados y la necesidad de soldar piezas cada vez más ligeras y resistentes también está impulsando la innovación en los soldadores de cordón circular. Las aleaciones especiales y los metales ligeros, como el titanio, el aluminio y sus aleaciones, requieren equipos que puedan manejar las exigencias específicas de estos materiales, tales como un control térmico más preciso o una capacidad para soldar materiales disímiles sin comprometer la integridad de la unión.
En cuanto a la capacitación de operadores, la industria está invirtiendo más en tecnologías de simulación y realidad aumentada para entrenar a los soldadores. Estas herramientas permiten a los operarios practicar en un entorno virtual antes de enfrentar trabajos reales, mejorando así su habilidad y seguridad sin el riesgo de errores costosos. La realidad virtual (VR), por ejemplo, ofrece una experiencia inmersiva en la que los operadores pueden aprender los movimientos y la técnica necesarios para realizar soldaduras de calidad, sin necesidad de utilizar materiales reales.
En resumen, los soldadores de cordón circular son una parte esencial de muchos procesos de fabricación, y su evolución continúa impulsada por el avance de la automatización, la inteligencia artificial, y las tecnologías sostenibles. La combinación de precisión, velocidad, flexibilidad y eficiencia energética será fundamental para satisfacer las crecientes demandas industriales y las expectativas de calidad. La integración de nuevas tecnologías y mejores materiales seguirá permitiendo que estos equipos desempeñen un papel clave en la fabricación de componentes más resistentes, ligeros y con un menor impacto ambiental.
En el futuro cercano, los soldadores de cordón circular también se beneficiarán de los avances en conectividad y la integración con sistemas de gestión de datos en tiempo real. La industria 4.0 está comenzando a influir de manera significativa en los procesos de soldadura, permitiendo la monitoreo remoto y la gestión de la producción desde plataformas digitales. Esto incluye la recolección de datos sobre parámetros de soldadura, como temperatura, presión y velocidad de avance, los cuales pueden analizarse en tiempo real para optimizar los procesos y predecir posibles fallos antes de que ocurran, lo que se traduce en una reducción de tiempos de inactividad y una mayor eficiencia operativa.
Además, el uso de tecnologías de predicción basadas en big data y machine learning está haciendo posible la creación de modelos predictivos que ayudan a los operarios a anticiparse a problemas como la formación de porosidad, la falta de fusión o la distorsión térmica. Estos sistemas inteligentes pueden ajustar los parámetros de soldadura automáticamente en función de las condiciones de la máquina y las piezas, asegurando que el cordón de soldadura se mantenga dentro de los parámetros de calidad establecidos.
Los equipos de soldadura autónomos también están comenzando a ser una realidad, lo que podría transformar aún más las operaciones de soldadura. Estos equipos son capaces de realizar soldaduras sin intervención humana, usando algoritmos complejos y sensores para ajustar constantemente el proceso de soldadura. Este tipo de tecnología es especialmente útil en la industria del espacio y la automotriz, donde la precisión es esencial y las condiciones de trabajo pueden ser extremas, como en entornos de baja gravedad o altas velocidades de producción.
Otra área donde los soldadores de cordón circular podrían evolucionar es en la mejora de la interacción humano-máquina (HMI). Las interfaces más intuitivas y controladores de soldadura inteligentes permitirán a los operarios ajustar los parámetros con facilidad y obtener información detallada sobre el estado del proceso en tiempo real. La implementación de pantallas táctiles avanzadas, realidad aumentada y controles por voz facilitará la interacción con los sistemas, haciendo que el proceso de soldadura sea más accesible y reduciendo la probabilidad de errores operativos.
Además, la soldadura de materiales disímiles continuará siendo un desafío técnico, pero también una oportunidad para la innovación. Las nuevas técnicas de soldadura, como la soldadura por fricción y la soldadura láser híbrida, están ganando popularidad debido a su capacidad para unir materiales que anteriormente no podían ser soldadas fácilmente. Estas tecnologías son particularmente útiles en la industria automotriz, donde se requieren uniones entre metales como aluminio y acero, que tienen propiedades muy diferentes en cuanto a conductividad térmica y expansión térmica.
La capacidad para soldar materiales innovadores también está empujando el desarrollo de equipos más avanzados. Metales como el titanio, el cobre de alta pureza y las aleaciones de alto rendimiento están siendo utilizados más en la industria aeronáutica, energética y de telecomunicaciones. Estos materiales, aunque más caros y complejos de procesar, requieren sistemas de soldadura con mayor control de la temperatura, adaptabilidad y precisión para garantizar que las uniones sean fuertes y estables sin comprometer las propiedades del material base.
Además, la fabricación aditiva y la impresión 3D de metales están comenzando a integrarse con la soldadura. En un futuro cercano, es probable que los soldadores de cordón circular trabajen en conjunto con máquinas de impresión 3D para crear piezas metálicas más complejas con precisión y menos desperdicio. Esta tendencia se alinea con los esfuerzos de la industria para reducir el desperdicio de material y lograr producción más eficiente y personalizada.
En cuanto a la sostenibilidad, las preocupaciones sobre la reducción de la huella de carbono están llevando a la industria de la soldadura a adoptar nuevas prácticas más ecológicas. El desarrollo de soldadores sin gas y el uso de materiales de soldadura más ecológicos están siendo prioridades. Las iniciativas de reciclaje de materiales y la optimización de los procesos de soldadura para minimizar el consumo de energía y los desechos también están ganando relevancia. De hecho, las futuras tecnologías de soldadura podrían estar completamente alineadas con los objetivos globales de sostenibilidad, utilizando energías renovables para operar y utilizando materiales reciclados para las uniones.
Finalmente, en términos de mantenimiento y reparación, los sistemas de soldadura evolucionarán hacia soluciones más autónomas que permitirán realizar diagnósticos precisos y mantener los equipos sin la necesidad de intervenciones complejas. Los soldadores de cordón circular inteligentes serán capaces de detectar fallos mecánicos o eléctricos, programar ciclos de mantenimiento preventivo y realizar autoajustes para optimizar su rendimiento a lo largo del tiempo, lo que mejorará significativamente su durabilidad y fiabilidad en condiciones de trabajo exigentes.
En resumen, el futuro de los soldadores de cordón circular está marcado por una evolución constante impulsada por la innovación tecnológica. Desde la integración de la automatización y la inteligencia artificial, hasta el desarrollo de materiales avanzados y técnicas de soldadura más sostenibles, el campo de la soldadura continuará adaptándose a las necesidades de la industria moderna. Estos avances no solo mejorarán la calidad de las uniones, sino que también permitirán una producción más eficiente, flexible y respetuosa con el medio ambiente, abriendo nuevas posibilidades para aplicaciones de soldadura en sectores industriales clave.
Sistemas de soldadura para procesos circulares
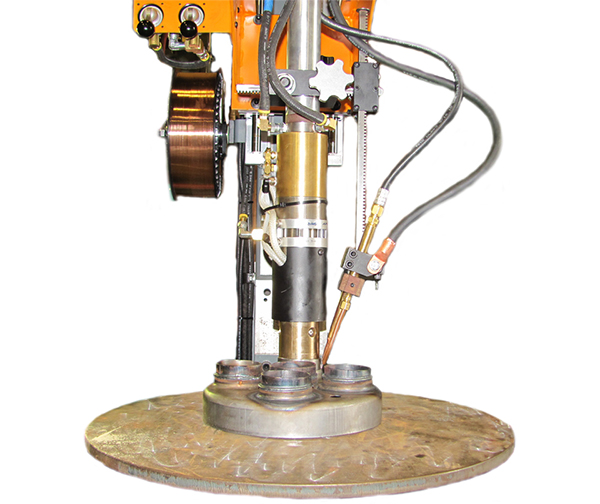
Los sistemas de soldadura para procesos circulares son equipos y técnicas especializadas diseñadas para realizar uniones continuas alrededor de componentes con geometría circular o tubular. Este tipo de soldadura es fundamental en aplicaciones industriales que requieren unir piezas de forma circular o en anillo, tales como tuberías, cilindros, recipientes de presión, intercambiadores de calor, y estructuras metálicas de diversos tamaños. Existen varios tipos de procesos y equipos utilizados para llevar a cabo estos trabajos de manera eficiente y precisa.
1. Soldadura Orbital
La soldadura orbital es un proceso automatizado que utiliza una antorcha de soldadura que gira alrededor de la pieza para realizar un cordón continuo. Este proceso es ideal para tuberías y componentes cilíndricos, ya que garantiza una soldadura uniforme, sin la intervención manual del operario.
- Aplicación: Comúnmente utilizado en la industria farmacéutica, alimentaria, aeroespacial, de energía y en sistemas de tuberías de acero inoxidable.
- Ventajas: Alta precisión, calidad constante, automatización, reducción de la intervención humana.
- Características: La antorcha de soldadura se mueve en un patrón orbital alrededor de la pieza, lo que permite una soldadura continua y controlada. El proceso es muy útil para piezas de pequeño y mediano diámetro.
2. Soldadura TIG (Tungsten Inert Gas) en Forma Circular
El proceso de soldadura TIG es muy popular en aplicaciones que requieren alta precisión y control sobre la calidad de la soldadura. En este caso, la antorcha de soldadura TIG puede ser utilizada en un proceso orbital para soldar piezas con geometría circular.
- Aplicación: Soldadura de tubos, recipientes a presión, estructuras de acero inoxidable y materiales sensibles como el titanio.
- Ventajas: Excelente control de la temperatura, alta calidad de la soldadura, ideal para materiales delgados y aleaciones especiales.
- Características: El proceso TIG es adecuado para trabajos en los que se requieren soldaduras de alta precisión y un cordón de soldadura muy limpio, libre de contaminantes y sin porosidad.
3. Soldadura MIG (Metal Inert Gas) en Forma Circular
La soldadura MIG es un proceso que utiliza un electrodo consumible y gas inerte para crear la unión. Aunque es más comúnmente usado para aplicaciones de soldadura en línea recta, también puede adaptarse para trabajos circulares utilizando equipos de soldadura semiautomáticos o automáticos con controles que ajusten la velocidad de avance de la antorcha y el aporte de material.
- Aplicación: Usada en la fabricación de componentes automotrices, sistemas de tuberías, estructuras metálicas y recipientes de presión.
- Ventajas: Alta velocidad de soldadura, fácil de automatizar, adecuado para una amplia gama de materiales.
- Características: La soldadura MIG en forma circular permite realizar uniones rápidas y efectivas, especialmente en proyectos de producción en masa. Además, el proceso produce menos salpicaduras en comparación con otros métodos, lo que mejora la calidad de la soldadura.
4. Soldadura por Arco Sumergido (SAW) para Procesos Circulares
La soldadura por arco sumergido (SAW) es un proceso automatizado en el que el arco de soldadura se encuentra cubierto por un fundente granular. Este proceso se utiliza para soldar materiales gruesos o de gran tamaño, y puede ser adaptado para soldar en forma circular.
- Aplicación: Comúnmente utilizado en la fabricación de grandes estructuras metálicas, como plataformas offshore, intercambiadores de calor, recipientes de presión y grandes tubos.
- Ventajas: Alta tasa de deposición, ideal para materiales gruesos, soldadura rápida y robusta.
- Características: Debido al fundente que cubre el arco, se obtiene una excelente protección contra la contaminación del aire y se reduce la formación de salpicaduras. Aunque es ideal para soldaduras en planos horizontales o verticales, también se adapta a procesos circulares con equipos automáticos adecuados.
5. Soldadura por Fricción para Uniones Circulares
La soldadura por fricción es un proceso que genera calor a través de la fricción entre las piezas a soldar. Este tipo de soldadura no requiere material de relleno, y es adecuada para uniones de alta resistencia sin comprometer las propiedades del material.
- Aplicación: Utilizada en la unión de materiales como aluminio, acero y titanio, especialmente en aplicaciones automotrices y aeroespaciales.
- Ventajas: No requiere material de relleno, produce uniones fuertes, adecuado para metales ligeros y aleaciones de alta resistencia.
- Características: La soldadura por fricción permite unir piezas cilíndricas sin afectar negativamente sus propiedades estructurales, ideal para materiales ligeros. Este proceso es especialmente útil cuando se necesita evitar la distorsión térmica o la adición de material adicional.
6. Soldadura por Láser
La soldadura por láser utiliza un rayo láser concentrado para fusionar las piezas a soldar. Este proceso se utiliza cuando se requiere una alta precisión y una mínima distorsión térmica en materiales delgados o piezas delicadas.
- Aplicación: Ideal para la industria aeroespacial, la fabricación de componentes electrónicos, y la producción de tubos de alta precisión.
- Ventajas: Alta precisión, mínima distorsión, capacidad de soldar materiales disímiles, velocidad de soldadura elevada.
- Características: El proceso láser es perfecto para soldaduras de alta calidad en piezas pequeñas o de geometría compleja. Debido a su alta concentración de energía, la soldadura por láser produce menos deformación y es adecuada para aplicaciones que requieren una apariencia estética y funcional excelente.
7. Soldadura Robótica
Los robots de soldadura permiten automatizar el proceso de soldadura en formas circulares de manera extremadamente precisa. Estos robots pueden integrarse con equipos de soldadura MIG, TIG o láser, y son especialmente útiles para realizar soldaduras continuas en componentes circulares, como tubos o recipientes.
- Aplicación: Muy utilizada en la fabricación de automóviles, estructuras metálicas y en el sector aeroespacial.
- Ventajas: Alta velocidad de producción, consistencia en las uniones, flexibilidad y adaptabilidad a diferentes tamaños de piezas.
- Características: Los robots de soldadura pueden ajustarse fácilmente a diferentes patrones y tamaños de piezas, realizando soldaduras circulares de manera consistente y precisa. Estos sistemas automatizados pueden realizar tareas repetitivas durante largos períodos sin intervención humana, lo que aumenta la productividad y reduce la posibilidad de errores humanos.
8. Soldadura por Ultrasonido
La soldadura por ultrasonido es un proceso en el que se utiliza vibración de alta frecuencia para generar calor y soldar materiales plásticos o metales delgados. Aunque no es comúnmente utilizado para soldaduras circulares en metales gruesos, es eficaz para unir componentes de precisión.
- Aplicación: Soldadura de materiales delgados, especialmente en aplicaciones electrónicas, y en la industria automotriz para componentes pequeños.
- Ventajas: Alta precisión, sin necesidad de material de relleno, velocidad de proceso muy alta.
- Características: Utilizada principalmente para uniones bajas en peso y alta precisión en componentes pequeños, la soldadura por ultrasonido no es adecuada para materiales gruesos o de alta resistencia.
En resumen, los sistemas de soldadura para procesos circulares abarcan una amplia variedad de tecnologías y técnicas, que permiten adaptarse a las necesidades de precisión, volumen y tipo de material requeridos en cada industria. Desde soldadores orbitales automáticos para aplicaciones de alta precisión hasta robots de soldadura para grandes volúmenes de producción, estas tecnologías continúan evolucionando y se adaptan a los avances en la automatización, la inteligencia artificial y los materiales avanzados. La elección del sistema adecuado dependerá de las características específicas del proyecto, como el tipo de material, el grosor de la pieza, las condiciones del entorno de trabajo y los requisitos de calidad de la soldadura.
Los sistemas de soldadura para procesos circulares son fundamentales en una variedad de industrias, ya que permiten realizar uniones precisas y resistentes en piezas con geometrías complejas, como tubos, recipientes, y otras estructuras cilíndricas. La selección del proceso de soldadura adecuado depende de factores como el tipo de material, el grosor de las piezas, la calidad requerida en la soldadura, la velocidad de producción y las condiciones del entorno operativo.
Uno de los métodos más utilizados en estos procesos es la soldadura orbital, que emplea una antorcha de soldadura que gira alrededor de la pieza para crear un cordón continuo. Este tipo de soldadura es ideal para aplicaciones que requieren alta precisión y un control riguroso sobre la calidad de la unión, como en la industria farmacéutica, aeroespacial y de alimentos, donde la limpieza y la consistencia son críticas. La soldadura orbital es especialmente efectiva en materiales como acero inoxidable y en situaciones en las que el diámetro de las piezas es pequeño o mediano.
Otra opción popular es la soldadura TIG (Tungsten Inert Gas), que es conocida por su capacidad para ofrecer soldaduras limpias y de alta calidad en metales delgados. Cuando se usa en conjunto con sistemas orbitales, permite una soldadura altamente precisa para tubos y componentes cilíndricos, proporcionando un excelente control térmico. Esta técnica es común en la fabricación de componentes aeroespaciales, en la que la integridad estructural y la precisión son esenciales.
Por otro lado, la soldadura MIG (Metal Inert Gas), aunque típicamente utilizada para aplicaciones lineales, también se adapta bien a la soldadura de cordones circulares cuando se utiliza en procesos automáticos o semiautomáticos. La velocidad de soldadura es una de las principales ventajas de este método, lo que lo convierte en una opción preferida en aplicaciones de alta producción, como la fabricación de automóviles y grandes estructuras metálicas. La capacidad de ajustar fácilmente la velocidad y la cantidad de material de aporte hace que este proceso sea flexible para una variedad de aplicaciones industriales.
La soldadura por arco sumergido (SAW), que es un proceso automatizado que emplea un arco cubierto por un fundente, se utiliza principalmente en materiales más gruesos y grandes volúmenes de producción. Aunque este método es más común en la fabricación de grandes estructuras y recipientes a presión, también se adapta bien a la soldadura de piezas circulares. La protección proporcionada por el fundente reduce la posibilidad de defectos y mejora la calidad de la soldadura, haciendo que este proceso sea ideal para proyectos que requieren una alta tasa de deposición y resistencia.
La soldadura por fricción es otra tecnología que está ganando popularidad, especialmente para la unión de materiales como el aluminio y el titanio, que son más difíciles de soldar con métodos convencionales. Este proceso no requiere material de relleno y es particularmente útil cuando se busca una unión de alta resistencia sin comprometer las propiedades del material. La soldadura por fricción es utilizada principalmente en la industria automotriz y aeroespacial para uniones de piezas ligeras y de alta resistencia.
En el ámbito de la soldadura de precisión, la soldadura láser es especialmente ventajosa. Este proceso permite realizar soldaduras extremadamente finas y controladas, ideal para materiales delgados y aplicaciones donde se requiere mínima distorsión térmica. La soldadura por láser es común en industrias de alta tecnología como la aeroespacial, la electrónica y la fabricación de dispositivos médicos, donde la precisión es crucial y los defectos deben evitarse a toda costa.
Además, los robots de soldadura están revolucionando los procesos de soldadura circular. Los robots, cuando se integran con sistemas automatizados de soldadura, pueden realizar soldaduras continuas con una precisión y velocidad que supera la capacidad humana. Estos sistemas robóticos son particularmente útiles en la industria automotriz y de fabricación en masa, donde la repetibilidad y la eficiencia son esenciales. La capacidad de los robots para ajustar automáticamente los parámetros de soldadura según las condiciones de la pieza garantiza una calidad constante y una mayor productividad.
En cuanto a la tecnología de monitoreo, los sistemas de soldadura modernos incorporan sensores avanzados y sistemas de visión artificial para supervisar la calidad de la soldadura en tiempo real. Estos sistemas pueden detectar defectos como porosidad, grietas o falta de fusión, y ajustar automáticamente los parámetros de soldadura para corregir cualquier problema. Esto no solo mejora la calidad del producto final, sino que también reduce la necesidad de inspecciones manuales y pruebas destructivas, lo que aumenta la eficiencia operativa y reduce los costos.
El futuro de la soldadura de cordón circular probablemente incluirá la integración más profunda de inteligencia artificial y aprendizaje automático para optimizar aún más los procesos de soldadura. Los algoritmos de IA pueden predecir el comportamiento de la soldadura en función de una variedad de factores, como la temperatura, la velocidad de avance y las propiedades del material, lo que permitirá ajustes más rápidos y precisos durante la soldadura.
En términos de sostenibilidad, la industria de la soldadura también está avanzando hacia procesos más ecológicos. El desarrollo de tecnologías sin gas y la optimización de procesos para reducir el desperdicio de material y energía son tendencias clave. Además, la implementación de sistemas que permiten el reciclaje de metales y materiales de soldadura está ayudando a minimizar el impacto ambiental de la producción.
Finalmente, los sistemas de soldadura para procesos circulares continúan evolucionando con la integración de nuevas tecnologías, lo que permite a las industrias mejorar la calidad, aumentar la eficiencia y reducir los costos. Con la creciente demanda de precisión, velocidad y sostenibilidad, los sistemas de soldadura seguirán siendo una parte crucial en la fabricación de componentes y estructuras metálicas en una amplia variedad de sectores industriales.
A medida que avanzan las tecnologías en soldadura para procesos circulares, las innovaciones continúan transformando la industria, enfocándose no solo en mejorar la eficiencia y precisión, sino también en la adaptación a materiales avanzados y la sostenibilidad. Los sistemas de soldadura más recientes permiten la integración de tecnologías como la soldadura híbrida, que combina diferentes procesos (por ejemplo, láser y arco) para optimizar la calidad de la soldadura y la velocidad de producción, ofreciendo resultados superiores en comparación con las técnicas tradicionales.
En la soldadura híbrida, el uso combinado de energía láser y arco eléctrico permite crear soldaduras más profundas y estrechas, reduciendo significativamente la cantidad de material de relleno necesario. Esta técnica es particularmente útil en industrias que trabajan con metales de alta resistencia y aleaciones especiales, como el titanio y el acero inoxidable, materiales que presentan dificultades para ser soldadas con métodos convencionales debido a su alta reflectividad y sus propiedades térmicas. La soldadura híbrida también minimiza el riesgo de distorsión térmica, lo que resulta en componentes de mayor calidad, más duraderos y con una menor huella ambiental.
En términos de automatización avanzada, los sistemas de soldadura autónomos están ganando terreno. Estos sistemas utilizan inteligencia artificial para analizar las condiciones del entorno y ajustar los parámetros de la soldadura en tiempo real, sin intervención humana. Este tipo de tecnología puede ajustarse dinámicamente a variaciones en la geometría de las piezas, lo que permite mantener una calidad constante de las soldaduras, incluso en condiciones cambiantes o impredecibles. Estos sistemas también son capaces de realizar diagnósticos predictivos sobre el estado de las máquinas y detectar posibles fallos antes de que ocurran, lo que reduce los tiempos de inactividad y mejora la eficiencia global de la producción.
El uso de sensores avanzados en sistemas de soldadura también está cambiando la forma en que se monitorean y controlan los procesos. Sensores de temperatura, presión y giro proporcionan datos en tiempo real que pueden ser utilizados para ajustar automáticamente la máquina durante la soldadura, asegurando que la calidad del cordón circular se mantenga dentro de los parámetros deseados. Además, los sistemas de visión artificial permiten inspeccionar y verificar la calidad de la soldadura en tiempo real, detectando defectos como porosidad, fisuras o falta de fusión, y ajustando el proceso de inmediato para corregir estos problemas sin necesidad de intervención manual.
Con respecto a la sostenibilidad, la industria de la soldadura está trabajando activamente para reducir el consumo de energía y materiales. Se están desarrollando nuevos materiales de soldadura ecológicos, como electrodos de bajo impacto ambiental y fundentes reciclables, que ayudan a minimizar el daño ecológico asociado con la soldadura. También se están introduciendo técnicas de soldadura sin gas que eliminan la necesidad de gases inertes, lo que reduce tanto el costo operativo como la huella de carbono de los procesos de soldadura.
En el ámbito de la soldadura de materiales avanzados, se está prestando especial atención al trabajo con metales ligeros como aluminio y magnesio, que son cruciales en la fabricación de componentes para la industria automotriz y aeroespacial debido a sus propiedades de ligereza y resistencia. Estos metales presentan desafíos particulares en términos de conductividad térmica y expansión térmica, lo que hace que la soldadura precisa sea más complicada. Para esto, se están desarrollando técnicas como la soldadura láser híbrida y la soldadura por fricción, que ofrecen mejores resultados en términos de resistencia y fiabilidad para uniones circulares de estos materiales.
Además, el uso de inteligencia artificial y algoritmos de aprendizaje automático en los sistemas de soldadura permite una optimización constante del proceso. Estos sistemas pueden analizar grandes volúmenes de datos generados durante la soldadura, como la temperatura, la velocidad de avance y la calidad del cordón, y luego ajustar automáticamente los parámetros para mejorar la eficiencia y la calidad de las soldaduras. Este enfoque reduce significativamente el riesgo de errores humanos y mejora la reproducibilidad de los resultados.
El futuro de los sistemas de soldadura para procesos circulares también incluirá avances en la interacción hombre-máquina. Las interfaces intuitivas, los controles táctiles y la realidad aumentada están mejorando la forma en que los operarios interactúan con las máquinas. Estas tecnologías permiten a los soldadores tener una visión más clara y detallada de lo que está sucediendo en tiempo real, lo que facilita la toma de decisiones rápidas y precisas en el proceso de soldadura.
Además, la creciente demanda de producción personalizada y baja serie está impulsando el desarrollo de tecnologías de soldadura flexible. Las empresas pueden beneficiarse de sistemas modulares y adaptables que les permitan cambiar rápidamente entre diferentes tipos de soldadura o tamaños de piezas sin necesidad de ajustes costosos o tiempos de inactividad. Esta flexibilidad es esencial en industrias como la aeroespacial, donde los requisitos de diseño y producción pueden variar enormemente entre proyectos.
Finalmente, con la continua evolución hacia la industria 4.0, los sistemas de soldadura estarán cada vez más conectados a plataformas digitales inteligentes que permiten la monitoreo remoto y la gestión de datos en tiempo real. Estas plataformas no solo facilitarán el seguimiento de la producción, sino que también ayudarán a optimizar el uso de recursos, a mantener un control de calidad más riguroso y a mejorar la trazabilidad de cada proceso de soldadura. En este contexto, los datos generados por los sistemas de soldadura podrán integrarse con otros sistemas de producción para crear una fábrica inteligente, lo que permitirá a las empresas mejorar la eficiencia y reducir costos en toda la cadena de suministro.
En resumen, los sistemas de soldadura para procesos circulares están evolucionando rápidamente, gracias a los avances tecnológicos que combinan la automatización, la inteligencia artificial, el monitoreo en tiempo real y la sostenibilidad. Estos sistemas no solo mejoran la calidad de las soldaduras y la eficiencia de los procesos, sino que también están abriendo nuevas posibilidades para la producción industrial en diversos sectores. La soldadura de cordón circular continuará siendo una pieza clave en la fabricación de componentes metálicos, y su evolución promete transformar aún más la manera en que las industrias producen y ensamblan componentes críticos.
Máquinas de soldadura de cordón circular
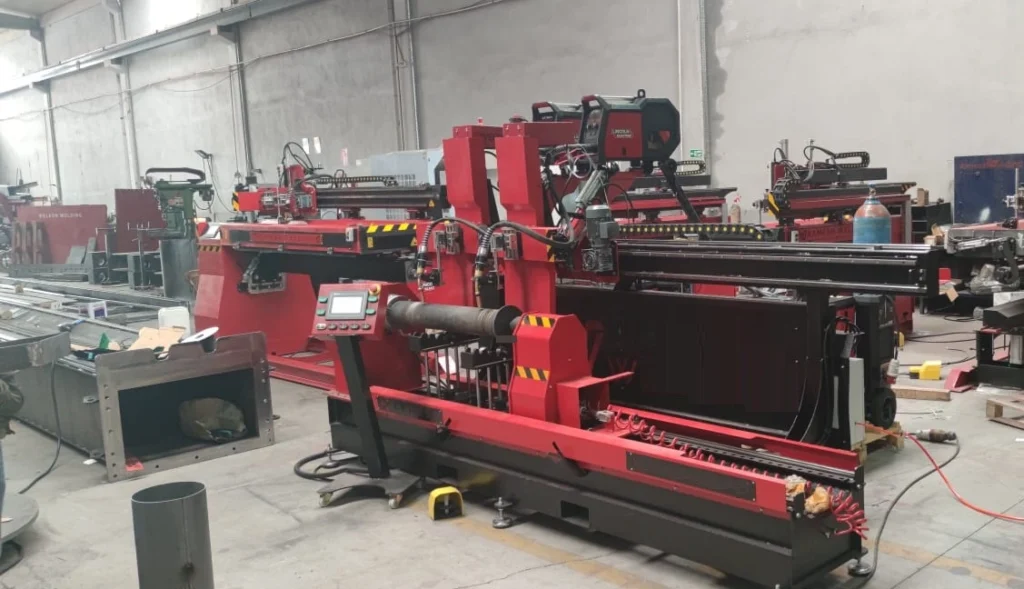
Las máquinas de soldadura de cordón circular son equipos especializados diseñados para realizar soldaduras continuas en piezas con geometrías circulares, como tubos, recipientes y componentes cilíndricos. Estos sistemas están optimizados para ofrecer una soldadura precisa y continua, garantizando la calidad y consistencia del cordón de soldadura alrededor de la pieza. Existen diversas tecnologías y tipos de máquinas que se adaptan a distintos procesos y necesidades. A continuación, se detallan las principales máquinas de soldadura utilizadas en aplicaciones circulares:
1. Máquinas de Soldadura Orbital
Las máquinas de soldadura orbital son uno de los equipos más comunes en la soldadura de cordones circulares. Estas máquinas emplean una antorcha de soldadura que rota 360 grados alrededor de la pieza para crear una soldadura continua.
- Características:
- El movimiento orbital permite cubrir toda la circunferencia de la pieza de manera uniforme.
- Las máquinas pueden ser automáticas o semiautomáticas, y son especialmente útiles para soldar tubos de acero inoxidable, aleaciones de titanio, y materiales sensibles.
- Estas máquinas son capaces de soldar piezas con diámetros pequeños o medianos, y se utilizan con procesos como TIG (Gas Inerte de Tungsteno) o MIG (Gas Inerte de Metal).
- Aplicaciones:
- Se utilizan comúnmente en la industria farmacéutica, alimentaria, de energía, aeroespacial y en sistemas de tuberías de acero inoxidable.
- Son esenciales en industrias que requieren soldaduras limpias y sin defectos, como la construcción de intercambiadores de calor, sistemas de tuberías de alta presión y componentes aeroespaciales.
2. Máquinas de Soldadura TIG Orbital
El proceso TIG orbital es una variante del proceso TIG convencional, donde la antorcha realiza un movimiento orbital alrededor de la pieza. Las máquinas de soldadura TIG orbital son muy precisas y se utilizan para realizar soldaduras de alta calidad en materiales como acero inoxidable y aleaciones especiales.
- Características:
- Estas máquinas son muy precisas y controlan perfectamente el aporte de calor, lo que permite obtener soldaduras sin porosidad ni contaminantes.
- La automatización del proceso garantiza una soldadura constante y uniforme a lo largo del cordón circular.
- Aplicaciones:
- Son ampliamente utilizadas en la industria aeroespacial, alimentaria y farmacéutica, donde la calidad y la precisión son fundamentales.
- Ideales para tubos, intercambiadores de calor, y estructuras metálicas que requieren soldaduras limpias y duraderas.
3. Máquinas de Soldadura MIG/MAG
La soldadura MIG/MAG (Gas Inerte de Metal / Gas Activo de Metal) se emplea en aplicaciones de soldadura rápida y con un alto rendimiento. Las máquinas de soldadura MIG/MAG para cordón circular son generalmente automáticas y permiten soldar con alta velocidad.
- Características:
- Utilizan un electrodo consumible que se alimenta de forma continua, lo que permite una soldadura más rápida en comparación con el proceso TIG.
- El gas utilizado puede ser inerte (para materiales como el aluminio) o activo (para materiales como el acero).
- Estas máquinas suelen ser más fáciles de operar y mantener, especialmente en aplicaciones de producción en masa.
- Aplicaciones:
- Se emplean en la industria automotriz, de construcción, y de fabricación de grandes estructuras metálicas.
- Son ideales para soldar piezas de mayor grosor y en proyectos que requieren alta velocidad de producción, como la fabricación de vehículos y sistemas de tuberías grandes.
4. Máquinas de Soldadura por Arco Sumergido (SAW)
La soldadura por arco sumergido (SAW) es un proceso de soldadura automatizado que emplea un arco cubierto por un fundente. Este proceso es utilizado para unir piezas gruesas y es ideal para soldar cordones circulares en componentes grandes.
- Características:
- La soldadura por arco sumergido es conocida por su alta tasa de deposición, lo que la hace adecuada para soldar materiales gruesos.
- Las máquinas de soldadura SAW pueden ser programadas para soldar de manera continua alrededor de una pieza cilíndrica.
- Este proceso tiene la ventaja de reducir la generación de humo y gas durante la soldadura debido a la cobertura del arco por el fundente.
- Aplicaciones:
- Se utiliza principalmente en la industria de construcción de grandes estructuras metálicas, plataformas offshore, intercambiadores de calor y grandes tuberías.
- Ideal para la fabricación de recipientes a presión, donde se requiere una alta resistencia y durabilidad.
5. Máquinas de Soldadura Láser
La soldadura láser es un proceso altamente preciso y eficiente que utiliza un rayo láser concentrado para fundir el material y crear una unión. Las máquinas de soldadura láser para procesos circulares están diseñadas para ofrecer una soldadura extremadamente precisa y con una mínima distorsión térmica.
- Características:
- La soldadura láser permite un control extremadamente fino sobre la energía aplicada, lo que la hace ideal para materiales delgados y componentes delicados.
- Estas máquinas pueden ser utilizadas para realizar soldaduras finas con una alta precisión y un acabado limpio.
- Aplicaciones:
- Utilizada en la industria aeroespacial, electrónica y automotriz, donde la precisión es clave.
- Ideal para trabajos que requieren una apariencia estética excelente y la minimización de la distorsión en materiales delgados.
6. Máquinas de Soldadura por Fricción
La soldadura por fricción es un proceso en el que se genera calor por medio de la fricción entre las piezas a soldar. Este proceso no requiere material de relleno y se utiliza principalmente para la unión de metales ligeros como el aluminio.
- Características:
- Es especialmente útil para soldar materiales de difícil unión o cuando se requiere una alta resistencia sin la adición de material de relleno.
- Las máquinas de soldadura por fricción pueden adaptarse para soldar de manera circular, aprovechando el movimiento rotacional para generar la unión.
- Aplicaciones:
- Comúnmente utilizada en la industria automotriz y aeroespacial, donde la unión de piezas ligeras y de alta resistencia es crucial.
- Adecuada para la soldadura de aluminio, magnesio y otras aleaciones ligeras.
7. Máquinas de Soldadura Robótica
Las máquinas de soldadura robótica permiten la automatización del proceso de soldadura, siendo capaces de realizar soldaduras de cordón circular con precisión y sin la intervención humana directa. Los robots están equipados con herramientas de soldadura y controladores programables que les permiten realizar soldaduras de alta calidad en piezas de forma circular.
- Características:
- Los robots de soldadura pueden trabajar con varios tipos de procesos de soldadura, como MIG, TIG, láser y otros.
- Son altamente versátiles y pueden adaptarse a diferentes geometrías y tamaños de piezas.
- Aplicaciones:
- Usados en producción en masa y ensamblaje de componentes en sectores como el automotriz, aeroespacial y de fabricación de estructuras metálicas.
- Son ideales para aplicaciones de alta precisión y donde se requiere una alta repetibilidad en la producción.
8. Máquinas de Soldadura por Ultrasonido
Aunque menos comunes, las máquinas de soldadura por ultrasonido se emplean en algunos sectores para realizar uniones precisas, especialmente en componentes pequeños y materiales plásticos o metálicos muy delgados.
- Características:
- Las máquinas de soldadura por ultrasonido emplean vibraciones ultrasónicas de alta frecuencia para fusionar las piezas sin necesidad de calor.
- Este proceso es muy rápido y adecuado para materiales delicados que no pueden ser sometidos a altas temperaturas.
- Aplicaciones:
- Se utiliza principalmente en la industria electrónica y de componentes pequeños donde se requiere una soldadura limpia y sin deformación térmica.
En resumen, las máquinas de soldadura de cordón circular cubren una amplia gama de procesos y tecnologías que se adaptan a diferentes tipos de materiales, tamaños de piezas y requisitos de producción. Desde equipos orbitales automatizados para soldaduras de alta precisión hasta sistemas robóticos para aplicaciones de alto volumen, la elección de la máquina adecuada dependerá de las especificaciones del proyecto, la velocidad de producción, la calidad de la soldadura deseada y las condiciones operativas.
Las máquinas de soldadura de cordón circular están diseñadas para lograr uniones continuas y precisas en piezas con formas circulares o cilíndricas, como tubos, recipientes, y estructuras metálicas. Este tipo de soldadura es crucial en industrias que requieren alta resistencia, durabilidad y precisión, tales como la automotriz, aeroespacial, farmacéutica, y de energía. Las máquinas varían en complejidad, desde sistemas manuales hasta totalmente automatizados, y se seleccionan según el material, el grosor de la pieza, y la aplicación específica.
Una de las principales ventajas de estas máquinas es su capacidad para garantizar una soldadura continua y homogénea alrededor de toda la circunferencia de la pieza. Esto se logra mediante la rotación de la antorcha o mediante movimientos robotizados, lo que asegura que el cordón de soldadura sea uniforme y libre de defectos. Además, muchas de estas máquinas están equipadas con sistemas de control avanzados que permiten ajustar la velocidad, la temperatura, y otros parámetros durante el proceso de soldadura, lo que contribuye a obtener soldaduras de alta calidad y consistentes.
En cuanto a los materiales, las máquinas de soldadura de cordón circular pueden adaptarse a una amplia variedad de metales, desde los más comunes como el acero inoxidable y el carbono, hasta aleaciones más difíciles de soldar, como el titanio y el aluminio. Algunos sistemas avanzados, como los robots de soldadura, pueden ajustarse automáticamente para trabajar con diferentes tipos de material sin necesidad de intervención manual, lo que aumenta la eficiencia y reduce los tiempos de producción.
Una característica importante de muchas de estas máquinas es su capacidad para trabajar de manera automática o semiautomática. Las versiones automáticas son más comunes en la fabricación en masa, donde se requieren grandes volúmenes de piezas soldadas. Estos sistemas están diseñados para realizar soldaduras de manera rápida y precisa, con un control total sobre el proceso. La automatización también reduce el riesgo de errores humanos, lo que mejora la calidad del producto final y disminuye la variabilidad en las soldaduras.
Las máquinas de soldadura de cordón circular también están comenzando a incorporar tecnologías avanzadas de monitoreo y control. Por ejemplo, el uso de sensores de temperatura y cámaras de visión artificial permite realizar un seguimiento en tiempo real de la calidad de la soldadura. Estos sistemas pueden detectar posibles defectos como porosidad, grietas o falta de fusión durante el proceso, lo que permite realizar ajustes inmediatos para corregir cualquier problema antes de que afecte la calidad final de la pieza. Además, estos sistemas permiten realizar auditorías automáticas de calidad, lo que facilita la trazabilidad de los productos y mejora el control de calidad.
El diseño modular de algunas máquinas de soldadura orbital también permite una gran flexibilidad. Esto es útil en aplicaciones donde se necesitan cambios rápidos entre diferentes configuraciones o cuando se requiere soldar piezas de diversos tamaños y formas. Las máquinas modulares pueden adaptarse a diferentes tipos de procesos, como TIG, MIG, o láser, sin la necesidad de una reconfiguración extensa, lo que ahorra tiempo y costos de producción. Esta flexibilidad es especialmente valiosa en industrias con lotes pequeños o que requieren personalización en las piezas soldadas.
El desarrollo continuo de la soldadura láser, por ejemplo, ha permitido que las máquinas de soldadura de cordón circular ofrezcan una precisión aún mayor, ideal para componentes que requieren una mínima distorsión térmica y una alta calidad estética. Estas máquinas son capaces de realizar soldaduras extremadamente finas en materiales delgados y de difícil soldadura, con un control casi perfecto sobre la cantidad de energía aplicada, lo que evita la deformación y garantiza un acabado limpio.
En cuanto a la sostenibilidad, muchas máquinas de soldadura modernas están diseñadas para reducir el consumo de energía y material, minimizando los desechos generados durante el proceso. Algunas utilizan tecnologías de soldadura sin gas, lo que elimina la necesidad de gases inertes o activos, reduciendo el impacto ambiental. Además, los avances en la tecnología de control permiten una mayor eficiencia en la utilización de energía, lo que reduce el consumo general y los costos operativos.
La soldadura robótica también está ganando popularidad en la soldadura de cordón circular, especialmente en la fabricación de productos de alta demanda. Los robots de soldadura ofrecen una alta repetibilidad y precisión, siendo capaces de realizar soldaduras circulares en piezas de diversos tamaños y materiales. Estos robots pueden trabajar de manera continua y sin necesidad de descanso, lo que aumenta la productividad y la calidad de la producción. A medida que la inteligencia artificial y la automatización se integran aún más en estos sistemas, la capacidad de los robots para ajustar los parámetros de soldadura en tiempo real mejora aún más, adaptándose a las variaciones en la pieza o en el proceso de soldadura para garantizar la perfección del cordón circular.
Por último, los sistemas de monitoreo remoto y plataformas de gestión de datos son cada vez más comunes en las máquinas de soldadura modernas. Estos sistemas permiten a los operadores supervisar el estado de las máquinas, obtener informes detallados sobre el progreso de la soldadura y ajustar los parámetros a distancia. Además, el análisis de datos a través de plataformas inteligentes permite realizar mejoras continuas en el proceso de soldadura, optimizando la calidad y la eficiencia de manera constante. En conjunto, estos avances aseguran que las máquinas de soldadura de cordón circular no solo sean más precisas y eficientes, sino también más inteligentes y fáciles de integrar en entornos de producción avanzados.
A medida que la tecnología de soldadura sigue avanzando, las máquinas para soldar cordón circular también están experimentando una evolución constante. La integración de tecnologías digitales y plataformas de control inteligentes está permitiendo una mayor personalización y optimización de los procesos de soldadura. Los sistemas de control numérico (CNC) en máquinas de soldadura permiten ajustar los parámetros de soldadura con extrema precisión, garantizando que cada cordón de soldadura sea consistente y cumpla con las especificaciones exactas del cliente o las normativas industriales. Estos sistemas también permiten un fácil acceso a configuraciones previas y pueden almacenar múltiples programas de soldadura para facilitar cambios rápidos en la producción.
Un aspecto clave de las máquinas de soldadura de cordón circular es su capacidad de integrarse en líneas de producción automatizadas. Los sistemas robotizados y las máquinas automáticas son cada vez más comunes en fábricas donde se requiere un alto volumen de piezas soldadas, como en la industria automotriz, la fabricación de tuberías y la producción de componentes de equipos pesados. Esta integración no solo mejora la eficiencia, sino que también permite la producción continua sin interrupciones, lo que reduce significativamente los tiempos de ciclo y mejora la competitividad de las empresas en mercados de alta demanda.
En la industria aeroespacial, donde se requiere una calidad extrema en cada soldadura, las máquinas de soldadura de cordón circular avanzadas utilizan técnicas como el control en tiempo real de los parámetros de soldadura. Esto permite a los operadores monitorizar continuamente la calidad de la soldadura y ajustarla sobre la marcha si es necesario. Las máquinas pueden estar equipadas con sensores para medir el volumen de material fundido, la temperatura y la velocidad de avance, y también con sistemas de visión artificial para detectar cualquier imperfección en el cordón de soldadura antes de que se produzcan defectos visibles.
En términos de reducción de costos y mejora de la eficiencia, muchas máquinas de soldadura de cordón circular ahora incorporan tecnologías que optimizan el uso del material de relleno y los consumibles. El uso de electrodos de mayor duración, fundentes reciclables y procesos de soldadura sin gas contribuye significativamente a la reducción de residuos y a la minimización de los costos operativos. Además, la implementación de sistemas de diagnóstico predictivo permite a los operadores anticiparse a posibles fallos en la maquinaria, lo que reduce las paradas no programadas y mejora la disponibilidad de las máquinas.
Otro de los avances importantes es la soldadura con alta velocidad utilizando tecnologías como la soldadura por láser de alta potencia. Este tipo de soldadura es especialmente ventajoso en aplicaciones donde se requieren soldaduras de alta resistencia y precisión, como en componentes de avión o turbinas de gas. Las máquinas de soldadura láser pueden realizar soldaduras de cordón circular con un control extremadamente fino sobre la temperatura y la cantidad de energía aplicada, lo que resulta en una mínima distorsión térmica y una excelente calidad de la soldadura.
El uso de inteligencia artificial (IA) en el proceso de soldadura está también ganando terreno. Los algoritmos de IA pueden analizar el comportamiento del proceso de soldadura en tiempo real y hacer ajustes automáticos para mejorar la calidad de la soldadura o corregir desviaciones en los parámetros. Esto no solo mejora la calidad de las soldaduras, sino que también reduce el tiempo necesario para realizar ajustes manuales y optimiza el uso de recursos como la energía y el material de relleno.
Las máquinas de soldadura híbrida, que combinan láser y arco eléctrico, están revolucionando la industria al permitir que las empresas realicen soldaduras más rápidas y con mayor profundidad. Estas máquinas pueden ser especialmente útiles para soldar materiales gruesos o componentes que requieren una alta resistencia, como los que se encuentran en la industria naval o en la fabricación de plataformas de petróleo y gas. La capacidad de combinar diferentes fuentes de energía para lograr una soldadura de mayor calidad y a una velocidad más alta es una ventaja significativa en aplicaciones industriales donde el tiempo es un factor crítico.
Además, la sostenibilidad sigue siendo un enfoque importante en el diseño y desarrollo de máquinas de soldadura. Muchas de las nuevas máquinas están diseñadas para ser más eficientes energéticamente y generar menos residuos. Algunas incluso incorporan sistemas de recuperación de calor que permiten reutilizar la energía generada durante el proceso de soldadura, reduciendo el consumo general de energía. Esta tendencia hacia la sostenibilidad también ha llevado al desarrollo de materiales de soldadura más ecológicos, como electrodos sin cobre o fundentes con bajo contenido de carbono.
Por último, la facilidad de mantenimiento y operación es un factor crucial en la elección de las máquinas de soldadura. Las modernas máquinas de soldadura de cordón circular vienen con interfaces intuitivas, pantallas táctiles y sistemas de diagnóstico remoto, lo que facilita la operación y el mantenimiento. Los operarios pueden realizar diagnósticos de fallos a distancia, programar mantenimientos preventivos y ajustar configuraciones sin necesidad de desplazarse hasta el lugar de trabajo, lo que mejora la productividad y reduce los tiempos de inactividad. La formación remota y la actualización de software a través de plataformas en línea también están facilitando la capacitación de los operarios y la implementación de mejoras en los sistemas sin necesidad de equipos especializados.
Con estos avances, las máquinas de soldadura de cordón circular están evolucionando para ofrecer no solo mayor eficiencia y precisión, sino también para integrarse de manera más fluida en entornos de producción inteligentes y automatizados. Esto está cambiando la forma en que se fabrican productos de alta calidad, permitiendo a las industrias cumplir con las crecientes demandas de producción, precisión y sostenibilidad.
Equipos de soldadura para cordón de soldadura circular
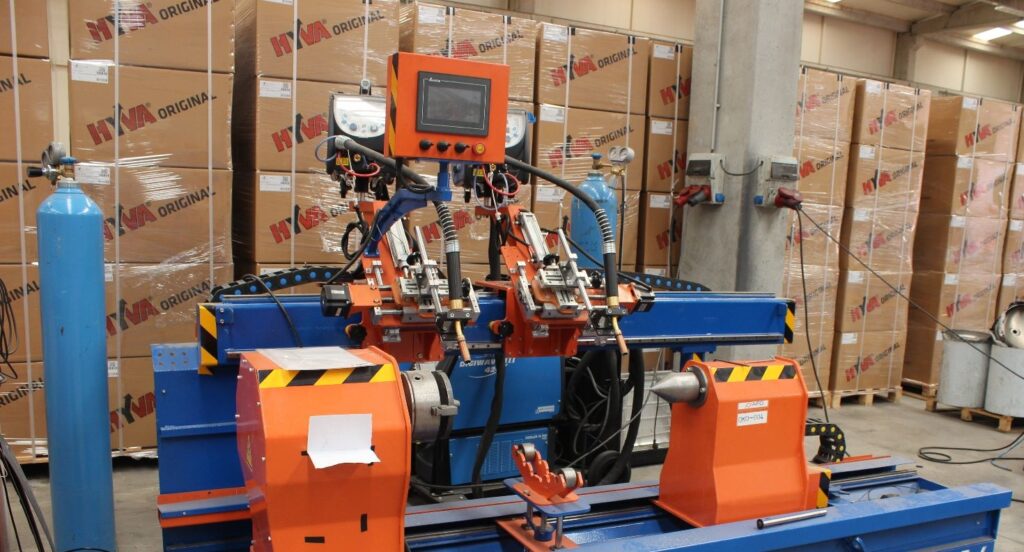
Los equipos de soldadura para cordón de soldadura circular están diseñados específicamente para realizar uniones continuas y precisas alrededor de piezas con geometrías circulares o cilíndricas. Estos equipos son esenciales en diversas aplicaciones industriales, donde se requiere soldaduras de alta calidad, como en la fabricación de tubos, recipientes a presión, intercambiadores de calor, estructuras metálicas, y componentes aeroespaciales, entre otros. Dependiendo de la técnica de soldadura y las necesidades específicas del proceso, se utilizan diferentes tipos de máquinas y equipos.
1. Máquinas de Soldadura Orbital
Las máquinas de soldadura orbital son herramientas especializadas para soldar piezas de forma circular. Estas máquinas cuentan con una antorcha que gira 360 grados alrededor de la pieza para asegurar una soldadura continua y uniforme a lo largo de todo el contorno.
- Características:
- La antorcha de soldadura realiza un movimiento orbital alrededor de la pieza, creando un cordón de soldadura uniforme.
- Son utilizadas principalmente con los procesos de soldadura TIG (gas inerte de tungsteno) y MIG (gas metálico inerte).
- Permiten una alta precisión, lo que las hace ideales para soldar materiales sensibles como acero inoxidable, aluminio, y titanio.
- Aplicaciones:
- Comúnmente usadas en la industria farmacéutica, alimentaria, y aeroespacial.
- Se utilizan para soldar tubos, recipientes a presión, y componentes de intercambiadores de calor.
2. Máquinas de Soldadura TIG Orbital
Las máquinas de soldadura TIG orbital utilizan el proceso TIG, que es conocido por su alta calidad de soldadura y capacidad para soldar metales finos. En este caso, la antorcha realiza un movimiento orbital alrededor de la pieza.
- Características:
- Control preciso del aporte de calor, ideal para materiales delicados o delgados.
- Se utiliza gas inerte (como argón) para proteger la zona de soldadura de la contaminación atmosférica.
- Se puede ajustar la velocidad de avance y la potencia de la antorcha para obtener un cordón de soldadura de alta calidad.
- Aplicaciones:
- Soldadura de tubos de acero inoxidable, componentes aeroespaciales, sistemas de refrigeración, y en la industria de procesos de alta precisión como la farmacéutica.
3. Máquinas de Soldadura MIG/MAG Orbital
Las máquinas de soldadura MIG/MAG orbital utilizan un electrodo consumible y un gas protector para realizar soldaduras rápidas en un movimiento orbital.
- Características:
- Utilizan un electrodo de metal consumible, lo que permite realizar soldaduras con mayor rapidez que el proceso TIG.
- Son especialmente adecuadas para materiales más gruesos y en aplicaciones donde la velocidad de producción es esencial.
- Aplicaciones:
- Usadas en la fabricación de estructuras metálicas grandes, sistemas de tuberías y componentes de automóviles.
4. Máquinas de Soldadura Láser Orbital
La soldadura láser orbital es una de las tecnologías más avanzadas y precisas disponibles para la soldadura de cordón circular. Utiliza un rayo láser altamente concentrado para fundir el material y crear una unión entre las piezas.
- Características:
- Alta precisión, lo que permite una mínima distorsión y un cordón de soldadura estéticamente perfecto.
- El rayo láser puede ser controlado con mucha precisión, lo que lo hace ideal para soldaduras en materiales delgados y de alta resistencia.
- Aplicaciones:
- Soldadura de componentes aeroespaciales, dispositivos electrónicos, y uniones de materiales de alta precisión.
5. Máquinas de Soldadura por Arco Sumergido (SAW)
La soldadura por arco sumergido (SAW) es un proceso automatizado que utiliza un arco eléctrico cubierto por un fundente. Este proceso es adecuado para aplicaciones de soldadura de alta producción y gran espesor.
- Características:
- La soldadura se realiza bajo una capa de fundente, lo que protege el arco y mejora la estabilidad del proceso.
- Este proceso tiene una alta tasa de deposición de material, lo que lo hace ideal para soldar piezas gruesas de acero o materiales similares.
- Aplicaciones:
- Usada en la industria de petróleo y gas, fabricación de barcos, plataformas offshore, y recipientes a presión.
6. Máquinas de Soldadura Robótica
Las máquinas de soldadura robótica están equipadas con brazos robóticos que realizan la soldadura de manera completamente automatizada. Estas máquinas pueden usar diferentes procesos de soldadura, como TIG, MIG, o láser, dependiendo de la aplicación.
- Características:
- Alta repetibilidad y precisión.
- Capacidad para trabajar en entornos de producción automatizados, donde se requiere un alto volumen de piezas soldadas.
- Las máquinas robóticas pueden ser equipadas con sensores y cámaras de visión artificial para mejorar el control de calidad en tiempo real.
- Aplicaciones:
- Se utilizan ampliamente en la industria automotriz, electrónica, y fabricación de equipos de precisión.
7. Máquinas de Soldadura por Fricción
La soldadura por fricción es un proceso donde la fricción generada por el contacto entre las piezas crea calor, que funde el material y lo une.
- Características:
- No requiere material de relleno, ya que la unión se produce por la fusión de los materiales en contacto.
- Ideal para piezas de metales ligeros, como el aluminio y sus aleaciones.
- Aplicaciones:
- Comúnmente utilizada en la industria automotriz y aeroespacial, especialmente en componentes ligeros o de aleaciones especiales.
8. Máquinas de Soldadura por Ultrasonido
Las máquinas de soldadura por ultrasonido utilizan vibraciones ultrasónicas de alta frecuencia para realizar uniones de materiales sin necesidad de calor.
- Características:
- Ideal para materiales plásticos y metales delgados.
- Produce una soldadura limpia y de alta calidad, sin distorsión térmica.
- Aplicaciones:
- Usadas en la industria electrónica y para la fabricación de componentes pequeños y de precisión.
9. Máquinas de Soldadura por Arco Eléctrico
Las máquinas de soldadura por arco eléctrico son las más tradicionales, utilizando un arco de electricidad entre un electrodo y la pieza a soldar para fundir el material de soldadura.
- Características:
- Pueden trabajar con electrodos consumibles o no consumibles.
- Son flexibles y adecuadas para soldar una variedad de materiales y espesores.
- Aplicaciones:
- Comúnmente usadas en la industria de construcción y reparación de piezas grandes, como tanques, recipientes de presión, y estructuras metálicas.
10. Máquinas de Soldadura MIG/MAG
Las máquinas MIG/MAG para cordón circular se usan ampliamente en aplicaciones de soldadura rápida, gracias al uso de un electrodo consumible y un gas protector. Son adecuadas para trabajos de alta producción y grandes volúmenes de piezas.
- Características:
- Soldadura rápida y eficiente con mínimo esfuerzo manual.
- Capaz de trabajar en una variedad de materiales, incluidos acero, aluminio y acero inoxidable.
- Aplicaciones:
- Comúnmente utilizadas en la industria automotriz, fabricación de muebles metálicos, y producción de equipos industriales.
Conclusión
Los equipos de soldadura para cordón de soldadura circular son fundamentales en la industria moderna debido a su capacidad para realizar uniones de alta calidad en piezas circulares y cilíndricas. Existen múltiples tecnologías y opciones, desde sistemas de soldadura orbital hasta robóticos y láser, cada una de ellas adaptada a diferentes aplicaciones y necesidades de producción. La elección del equipo adecuado depende del tipo de material, la precisión requerida, el volumen de producción y los requisitos específicos de cada industria.
Los equipos de soldadura para cordón de soldadura circular están en constante evolución, impulsados por la demanda de soluciones más rápidas, precisas y económicas en la fabricación de piezas y componentes. Estos equipos están diseñados para ofrecer un control total sobre el proceso de soldadura, asegurando un cordón limpio, uniforme y libre de defectos. Desde los sistemas manuales hasta las soluciones automatizadas, cada uno tiene sus propias ventajas y se utiliza en diversas aplicaciones industriales.
Las máquinas de soldadura orbital, por ejemplo, son ideales para aplicaciones donde se requieren soldaduras continuas y uniformes alrededor de piezas de geometría circular o cilíndrica. Estas máquinas emplean un movimiento rotatorio de la antorcha de soldadura para cubrir todo el contorno de la pieza, lo que permite obtener una soldadura perfectamente alineada y resistente. Además, con la capacidad de ser configuradas para soldar materiales delgados o gruesos, estas máquinas son útiles en industrias como la farmacéutica, alimentaria y aeroespacial.
Por otro lado, las máquinas de soldadura MIG/MAG orbitales se emplean en aplicaciones donde se requiere una soldadura más rápida, utilizando un electrodo consumible y un gas protector que facilita el proceso. Estas máquinas permiten una alta productividad, lo que las hace ideales para la fabricación en masa de componentes metálicos. Al ser más accesibles y fáciles de operar, las máquinas MIG/MAG orbitales son muy comunes en la industria automotriz y en la fabricación de productos de consumo masivo.
Las máquinas de soldadura láser orbital son de vanguardia, pues aprovechan el poder del láser para realizar soldaduras de alta precisión. Estas máquinas ofrecen una mínima distorsión térmica, lo que las convierte en una excelente opción para materiales delicados y finos, como los que se usan en la industria electrónica o en componentes de alta tecnología. Gracias a su capacidad para controlar el enfoque del rayo láser, pueden trabajar con una exactitud asombrosa, incluso en piezas pequeñas y complejas, lo que resulta en un acabado estéticamente impecable y de calidad superior.
El uso de robots de soldadura está revolucionando la producción en muchos sectores, ya que estas máquinas pueden realizar tareas repetitivas con una precisión excepcional, eliminando la posibilidad de errores humanos. Los robots de soldadura son capaces de soldar piezas de manera continua y consistente, a menudo sin la necesidad de intervención humana. Esto no solo mejora la calidad del producto final, sino que también incrementa la velocidad de producción, lo que es especialmente ventajoso en entornos industriales con altos volúmenes de producción.
Además de las máquinas más comunes, también existen procesos innovadores como la soldadura por fricción y la soldadura por arco sumergido (SAW), que son útiles en aplicaciones de gran escala. La soldadura por fricción es particularmente eficiente en el caso de metales como el aluminio y sus aleaciones, mientras que el proceso SAW es ideal para soldaduras de gran espesor, como las que se encuentran en la industria del petróleo y gas.
La soldadura por ultrasonido es otro proceso que está ganando popularidad en aplicaciones de alta precisión, como en la fabricación de componentes electrónicos y otros productos pequeños que requieren una soldadura delicada y sin distorsión. Este tipo de soldadura utiliza vibraciones ultrasónicas para fusionar los materiales, lo que resulta en una unión rápida y limpia sin necesidad de calor extremo.
La sostenibilidad y la eficiencia energética también están tomando protagonismo en el desarrollo de máquinas de soldadura. Muchos equipos modernos están diseñados para ser más eficientes energéticamente y generar menos desperdicios, lo que ayuda a reducir los costos operativos y el impacto ambiental. Tecnologías como la recuperación de calor y el uso de gases de soldadura más ecológicos están siendo incorporadas en las nuevas máquinas de soldadura, haciendo que el proceso sea más ecológicamente responsable.
Por último, el avance de la inteligencia artificial (IA) y el monitoreo remoto está facilitando la gestión y optimización de las operaciones de soldadura. Los sensores avanzados y los sistemas de IA permiten monitorear el proceso en tiempo real, ajustando automáticamente los parámetros para mantener la calidad del cordón de soldadura y detectar problemas antes de que ocurran. Estas tecnologías no solo mejoran la calidad, sino que también aumentan la eficiencia, reducen el tiempo de inactividad y permiten una gestión remota de los equipos, lo que resulta en una mayor flexibilidad y control en el proceso de producción.
En resumen, los equipos de soldadura para cordón de soldadura circular están diseñados para ofrecer soluciones flexibles, precisas y eficientes en una amplia gama de aplicaciones industriales. Con la integración de nuevas tecnologías y la mejora continua de los procesos, estos equipos están mejorando constantemente la calidad de las soldaduras, reduciendo los costos operativos y respondiendo a las crecientes demandas de las industrias modernas.
La evolución de los equipos de soldadura para cordón circular sigue avanzando, impulsada por el constante crecimiento de las demandas de precisión, velocidad y eficiencia en diversas industrias. Los avances en la automatización, digitalización y las tecnologías emergentes están transformando la manera en que se realizan las soldaduras, no solo en términos de calidad, sino también en términos de control, sostenibilidad y adaptabilidad a nuevas aplicaciones.
Uno de los principales avances en las máquinas de soldadura es la integración de sistemas de control inteligentes, como los basados en PLC (Controladores Lógicos Programables) o CNC (Control Numérico Computarizado), que permiten un ajuste automático de los parámetros de soldadura. Estos sistemas aseguran que cada soldadura sea precisa, independientemente de las variaciones en la pieza o el material. Los parámetros como la velocidad de avance, el voltaje del arco, la corriente de soldadura y la temperatura pueden ajustarse de manera dinámica durante el proceso, lo que optimiza la calidad del cordón de soldadura y minimiza los defectos.
Además, el uso de sensores avanzados para monitorear en tiempo real aspectos críticos como la temperatura, la distancia de la antorcha y la velocidad de soldadura, permite un control de calidad constante. Estos sensores pueden detectar problemas de soldadura, como sobrecalentamiento, irregularidades en la deposición de material o falta de fusión, y enviar alertas automáticas a los operadores para que tomen medidas correctivas inmediatas. En algunos casos, la inteligencia artificial (IA) es utilizada para predecir fallos y sugerir ajustes en los parámetros de operación, lo que lleva la gestión del proceso de soldadura a un nivel de automatización avanzado.
La soldadura por láser, en particular, ha experimentado un auge significativo, especialmente en aplicaciones que requieren uniones de alta precisión y alta resistencia en materiales delgados o altamente resistentes. La capacidad de realizar soldaduras de alta calidad con mínima distorsión térmica ha abierto nuevas posibilidades en la fabricación de componentes microelectrónicos, aeroespaciales y biomédicos, donde la precisión es crucial. El uso de láser también permite realizar soldaduras de alta velocidad, reduciendo los tiempos de ciclo y aumentando la eficiencia en la producción.
El concepto de soldadura híbrida, que combina procesos como la soldadura láser con arco eléctrico o con fricción, está ganando terreno en industrias que requieren una alta resistencia de las soldaduras y a la vez la capacidad de procesar materiales gruesos. Estos procesos híbridos no solo mejoran la calidad de la soldadura, sino que también permiten aumentar la velocidad de trabajo sin comprometer la integridad estructural del material. Esto es particularmente útil en la industria pesada, como la fabricación de equipos de minería, maquinaria industrial y plataformas offshore.
Otro campo de innovación en las máquinas de soldadura de cordón circular es el uso de tecnologías de soldadura sin contacto, como la soldadura por inducción. Este proceso utiliza campos magnéticos para calentar el material a la temperatura de fusión, eliminando la necesidad de contacto directo con los electrodos. La soldadura por inducción es ideal para materiales sensibles al calor, ya que se genera un calor muy localizado, reduciendo el riesgo de distorsión térmica. Además, permite un control extremadamente preciso sobre la cantidad de energía utilizada, lo que es crucial en la soldadura de aleaciones especiales y metales con baja conductividad térmica, como el cobre o el titanio.
La soldadura por arco sumergido (SAW) también sigue siendo una opción preferida en industrias que necesitan soldaduras de gran volumen y espesor. Este proceso se caracteriza por el uso de un fundente que cubre el arco eléctrico, protegiéndolo de la atmósfera y proporcionando un cordón de soldadura fuerte y resistente. Su capacidad para procesar grandes piezas y su alta tasa de deposición de material hacen que la soldadura por arco sumergido sea esencial en la construcción de grandes estructuras metálicas, como tanques de almacenamiento, plataformas de perforación y buques.
En cuanto a la sostenibilidad, los avances en tecnologías verdes en la soldadura también están ganando impulso. Muchas empresas están optando por procesos más ecológicos que reduzcan el impacto ambiental de la soldadura. Esto incluye el uso de gases de protección más ecológicos, como el CO2 reciclado o el argon reciclado, que ayudan a reducir las emisiones de gases de efecto invernadero. Además, las nuevas máquinas están siendo diseñadas para optimizar el consumo energético, lo que no solo reduce el impacto ambiental, sino que también genera ahorros significativos en los costos operativos.
Los equipos de soldadura robotizados también se están haciendo más accesibles para una mayor variedad de empresas. La integración de robots industriales en las líneas de producción está permitiendo a las empresas optimizar sus procesos de soldadura, reduciendo los errores humanos y mejorando la seguridad laboral. Los robots pueden trabajar en entornos peligrosos o difíciles de alcanzar, y realizar soldaduras precisas de manera constante. Esto es particularmente valioso en industrias como la automotriz, donde la alta velocidad de producción es esencial, y la calidad de las soldaduras debe mantenerse sin compromisos.
La capacidad de realizar soldaduras automatizadas en línea también está mejorando, lo que permite una mayor integración en las fábricas inteligentes o industrias 4.0. Estos sistemas pueden estar conectados a plataformas de software que permiten a los operadores monitorear la producción en tiempo real, ajustar parámetros, y recibir informes detallados sobre la calidad de las soldaduras realizadas. Esto permite la optimización continua de los procesos, garantizando un rendimiento de producción superior y minimizando el desperdicio de materiales y tiempo.
Finalmente, la formación continua y el soporte remoto están facilitando la adopción de tecnologías de soldadura avanzadas. Los operarios pueden recibir capacitación de manera remota a través de plataformas digitales y realidad aumentada (AR), lo que les permite acceder a manuales de operación interactivos, aprender nuevas habilidades y solucionar problemas sin la necesidad de viajar o realizar intervenciones costosas. Además, el soporte remoto y los diagnósticos predictivos están ayudando a mantener las máquinas de soldadura en óptimas condiciones, lo que mejora la fiabilidad y la vida útil de los equipos.
En resumen, los equipos de soldadura para cordón circular continúan evolucionando, impulsados por la innovación tecnológica y la necesidad de procesos más eficientes, precisos y sostenibles. Desde sistemas automatizados hasta nuevas tecnologías de soldadura, los avances están transformando la forma en que se realizan las soldaduras, ofreciendo nuevas oportunidades para mejorar la productividad, reducir los costos y cumplir con los estándares de calidad cada vez más exigentes.
Sistemas de soldadura para uniones circulares
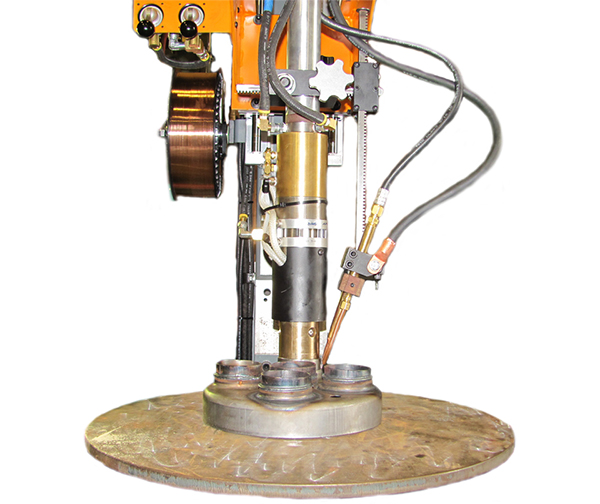
Los sistemas de soldadura para uniones circulares están especialmente diseñados para realizar uniones metálicas en componentes de geometría cilíndrica o circular, como tubos, depósitos, bridas, anillos y componentes giratorios en diversas industrias. Estos sistemas permiten obtener cordones de soldadura continuos, precisos y con alta repetibilidad, lo cual es esencial en aplicaciones donde la calidad de la unión determina el rendimiento y la seguridad del conjunto.
El principio básico de estos sistemas consiste en mantener un control constante del arco de soldadura mientras se desplaza a lo largo de una trayectoria circular. Esto puede lograrse mediante rotación de la pieza, movimiento orbital de la antorcha o una combinación de ambos, dependiendo del tipo de máquina y el proceso de soldadura empleado. Las variantes más comunes incluyen la soldadura orbital, la soldadura TIG/MIG automatizada con rotación controlada, y en casos más sofisticados, la soldadura láser circular o por fricción.
Estos sistemas se utilizan ampliamente en industrias como la aeroespacial, la nuclear, la farmacéutica, la alimentaria y la automotriz, donde las exigencias de precisión, limpieza y resistencia son muy altas. Por ejemplo, en la fabricación de intercambiadores de calor o tuberías de presión, una soldadura defectuosa en una unión circular puede causar fallas catastróficas. Por ello, muchos de estos sistemas incorporan monitoreo en tiempo real de los parámetros de soldadura, como voltaje, corriente, velocidad de avance y temperatura, para asegurar que cada unión se realice dentro de las tolerancias requeridas.
Los sistemas modernos también permiten programar ciclos automáticos, almacenar perfiles de soldadura para diferentes materiales y configuraciones, e integrar funciones de autodiagnóstico o compensación de desviaciones. En combinación con robots o posicionadores, los sistemas de soldadura para uniones circulares pueden integrarse en líneas de producción totalmente automatizadas, reduciendo el tiempo de ciclo y eliminando errores humanos. En definitiva, son una solución clave para lograr soldaduras de alta calidad en aplicaciones donde la geometría circular es un factor dominante.
Los sistemas de soldadura para uniones circulares continúan evolucionando gracias a la incorporación de tecnologías avanzadas que permiten una mayor precisión, control automatizado y adaptabilidad a diferentes tipos de materiales y geometrías. En los procesos industriales actuales, donde los requisitos de calidad son cada vez más exigentes, estos sistemas se han convertido en una herramienta fundamental no solo por su capacidad de generar uniones confiables y resistentes, sino también por su eficiencia operativa. En muchas aplicaciones críticas, como en la industria de procesos, la aeroespacial y la farmacéutica, no se permite margen de error en las uniones soldadas. Por eso, los sistemas que se utilizan deben ser capaces de garantizar una homogeneidad total del cordón, evitar inclusiones o poros y mantener una penetración constante en toda la circunferencia. Esto se logra, en gran medida, mediante el uso de sistemas orbitales de soldadura, los cuales permiten que la antorcha o el electrodo roten alrededor de la pieza mientras mantienen todos los parámetros de soldadura constantes. La ventaja de este tipo de sistemas es que permiten realizar uniones circulares de forma completamente automática, sin depender de la habilidad del operador una vez que el programa ha sido configurado correctamente.
Uno de los aspectos clave de los sistemas modernos para soldadura de uniones circulares es su integración con controles digitales que permiten almacenar múltiples programas de soldadura, monitorear el proceso en tiempo real y ajustar dinámicamente variables como el caudal de gas protector, la corriente de soldadura y la velocidad de rotación. Esto es especialmente útil en entornos donde se trabaja con diferentes tipos de aleaciones o se requiere pasar rápidamente de una configuración a otra. Además, los sistemas con sensores de seguimiento y control adaptativo pueden identificar irregularidades en la superficie de la pieza y compensarlas automáticamente, asegurando que la soldadura se mantenga uniforme incluso cuando hay ligeras variaciones en el material o la forma. Esto permite una mayor tolerancia a las imperfecciones de fabricación, reduce el retrabajo y mejora la eficiencia general del proceso.
La robótica también ha aportado beneficios sustanciales al campo de las uniones circulares. Con brazos robóticos programables y sensores de posicionamiento, es posible soldar piezas complejas con múltiples ejes de rotación o con geometrías que varían a lo largo de la circunferencia. En este contexto, los robots no solo mejoran la precisión, sino que también permiten realizar operaciones en condiciones extremas, como atmósferas controladas, espacios confinados o entornos con alta radiación, donde el trabajo manual sería inviable o peligroso. Otro aspecto innovador es la incorporación de visión artificial y análisis de datos mediante inteligencia artificial, que permiten a los sistemas detectar defectos durante la soldadura, anticiparse a fallas y aprender de ciclos anteriores para mejorar la calidad de las futuras soldaduras. Esta capacidad de autoajuste y mejora continua convierte a estos sistemas en componentes clave de la manufactura inteligente y la industria 4.0.
El tipo de soldadura empleada en un sistema para uniones circulares dependerá de las necesidades del producto final. Por ejemplo, la soldadura TIG es común cuando se requieren acabados limpios y control térmico preciso, mientras que la MIG es más rápida y adecuada para aplicaciones de alta productividad. En el caso de la soldadura láser, se logran uniones extremadamente precisas con mínima afectación térmica, ideales para componentes delicados. Por su parte, la soldadura por fricción se utiliza cuando se quiere evitar el aporte de material o cuando se trabaja con materiales difíciles de soldar por métodos tradicionales. Cada uno de estos procesos puede adaptarse para funcionar en sistemas circulares, ya sea mediante posicionadores rotativos, antorchas orbitales o cabezales especializados.
En general, los sistemas de soldadura para uniones circulares están diseñados para maximizar la calidad, reducir la intervención humana y adaptarse a una amplia variedad de entornos industriales. Su implementación no solo mejora la productividad, sino que también permite cumplir con normativas estrictas de calidad, seguridad y trazabilidad, lo cual es esencial en sectores regulados. A medida que la tecnología avanza, es esperable que estos sistemas se vuelvan aún más compactos, versátiles y conectados, facilitando su integración en líneas de producción automatizadas, donde cada paso del proceso está controlado y documentado digitalmente. Con ello, las uniones circulares soldadas con precisión se seguirán consolidando como una parte crítica de productos duraderos, seguros y eficientes en casi todos los campos de la ingeniería moderna.
Además del perfeccionamiento técnico de los sistemas de soldadura para uniones circulares, existe un creciente interés en su capacidad de adaptarse a la variabilidad de los materiales y condiciones operativas. En entornos industriales reales, no siempre se trabaja con componentes perfectamente estandarizados; las diferencias en composición química, tratamientos térmicos previos, o incluso pequeñas deformaciones en la geometría, pueden afectar el resultado de la soldadura. Para enfrentar esta realidad, muchos equipos modernos incluyen algoritmos de control adaptativo que ajustan automáticamente la intensidad del arco, la velocidad de avance o la frecuencia de oscilación del electrodo, en función de lecturas obtenidas de sensores en tiempo real. Esto permite mantener una calidad de soldadura constante a pesar de variaciones inesperadas, lo que es especialmente valioso en procesos de producción por lotes o en reparación de componentes.
Otra tendencia importante es la miniaturización y portabilidad de algunos sistemas de soldadura orbital y circular. Mientras que los sistemas industriales tradicionales eran grandes, complejos y requerían instalaciones fijas, hoy en día se están desarrollando unidades compactas y portátiles que pueden ser utilizadas en campo, como en instalaciones de tuberías en plataformas petroleras, centrales nucleares o plantas químicas. Estas unidades cuentan con cabezales de soldadura cerrados o abiertos, capaces de adaptarse a espacios reducidos y realizar soldaduras de alta precisión en entornos donde no se puede desmontar el componente o trasladarlo a una estación fija. Esta movilidad ha abierto nuevas posibilidades en trabajos de mantenimiento, ampliación de redes industriales y montaje de estructuras complejas.
En paralelo, la digitalización de los procesos ha llevado a una mejora significativa en la trazabilidad y documentación de las soldaduras circulares. Cada ciclo de soldadura puede ser registrado en detalle, incluyendo los parámetros utilizados, las condiciones del entorno, los datos del operador y los resultados de inspecciones automatizadas. Esta información no solo es útil para asegurar la conformidad con estándares técnicos y normativos, sino que también permite realizar análisis predictivos, identificar tendencias de desgaste en los equipos, y mejorar continuamente el diseño de futuros procesos. Incluso es posible integrar estos datos con sistemas de gestión de calidad o ERP industriales, facilitando una supervisión integral de toda la cadena de producción.
El papel de los materiales de aporte también es crucial en el éxito de la soldadura de uniones circulares. La selección del tipo de alambre, electrodo o polvo, así como del gas de protección, influye directamente en la resistencia mecánica, la resistencia a la corrosión, y la durabilidad de la unión. En soldaduras circulares sometidas a esfuerzos cíclicos, como en ejes, válvulas o piezas giratorias, la calidad del cordón y la ausencia de discontinuidades internas son fundamentales. Por ello, los equipos de soldadura avanzados ofrecen compatibilidad con una amplia gama de materiales de aporte y parámetros específicos para cada uno, lo que permite adaptar el proceso a las exigencias exactas de cada proyecto.
También se ha avanzado mucho en ensayos no destructivos integrados a los sistemas de soldadura. Gracias al uso de ultrasonido, radiografía digital o termografía infrarroja, es posible inspeccionar la calidad de la unión circular poco después de realizada, sin necesidad de interrumpir el flujo de trabajo o esperar largos tiempos de enfriamiento. Estas tecnologías permiten detectar poros, grietas, falta de penetración o inclusión de escoria, y gracias a la automatización, pueden realizarse de forma continua y registrar los resultados en tiempo real. De este modo, se garantiza una producción más confiable, con menor necesidad de retrabajo y mayor consistencia entre lotes.
En conjunto, los sistemas de soldadura para uniones circulares representan una convergencia entre mecánica de precisión, electrónica de control, ciencia de materiales y tecnologías digitales. Son esenciales para industrias que no solo exigen resistencia y durabilidad, sino también estética, limpieza, y una trazabilidad total del proceso. A medida que continúan integrándose con tecnologías como el internet industrial de las cosas (IIoT), la inteligencia artificial y los gemelos digitales, es previsible que estos sistemas se conviertan en nodos inteligentes dentro de fábricas completamente conectadas, capaces de optimizar sus parámetros en función de condiciones cambiantes y exigencias específicas del producto final. Esta evolución, lejos de ser una simple mejora técnica, está redefiniendo los estándares de lo que significa soldar con precisión, confiabilidad y eficiencia en la industria moderna.
Maquinaria de soldadura para cordón circular
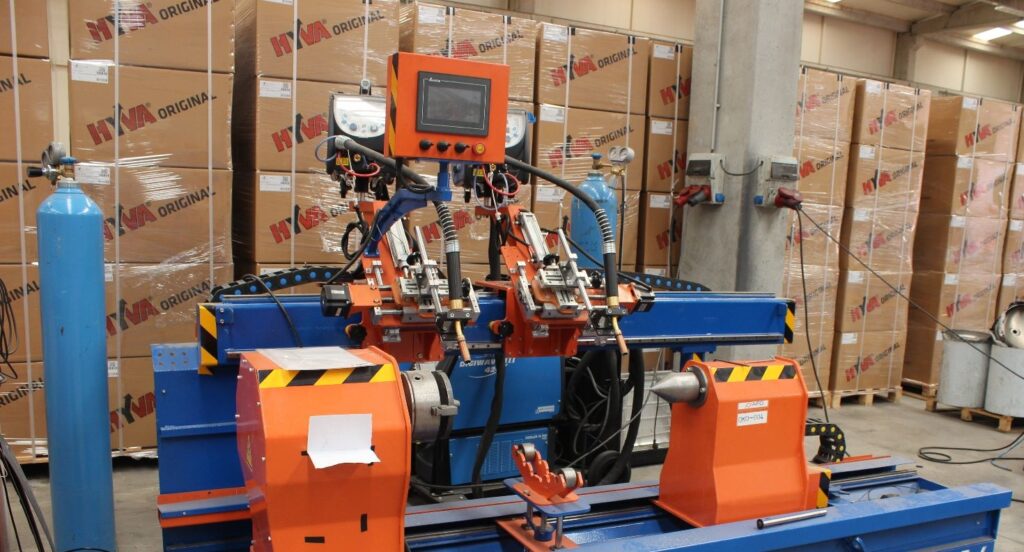
La maquinaria de soldadura para cordón circular está diseñada específicamente para realizar uniones metálicas a lo largo de trayectorias curvas o circulares, como las que se encuentran en tubos, cilindros, bridas, anillos, tanques de presión, rotores y otros componentes cilíndricos. Este tipo de maquinaria se distingue por su capacidad de mantener un control constante y preciso del movimiento relativo entre la fuente de calor (antorcha, electrodo o rayo láser) y la pieza de trabajo, lo cual es crucial para lograr una penetración uniforme y un cordón de soldadura homogéneo en toda la circunferencia. En función del proceso de soldadura utilizado —como TIG, MIG/MAG, plasma, láser o fricción— y del tipo de aplicación, la maquinaria puede incorporar mecanismos de rotación de la pieza, movimiento orbital de la antorcha o una combinación sincronizada de ambos.
Uno de los elementos clave en este tipo de equipos es el posicionador rotativo, que permite girar la pieza a una velocidad constante mientras la fuente de soldadura permanece fija o se desplaza ligeramente según se requiera. En sistemas más avanzados, la antorcha de soldadura gira alrededor de la pieza, lo que es común en la soldadura orbital automatizada, especialmente en trabajos con tubos pequeños o de difícil acceso. Estos sistemas pueden ser completamente automáticos, con programación de parámetros como corriente, voltaje, velocidad de avance, caudal de gas y temporización, lo que permite obtener resultados repetibles con mínima intervención del operador.
La maquinaria de soldadura para cordón circular también puede incluir cabezales cerrados o abiertos, dependiendo del tipo de soldadura y el acceso físico a la zona de unión. Los cabezales cerrados, usados en soldadura orbital TIG, son ideales para aplicaciones donde se requiere una atmósfera protegida muy controlada, como en la industria farmacéutica o aeroespacial. Por otro lado, los cabezales abiertos son más versátiles y permiten soldar diámetros mayores o geometrías menos uniformes, aunque requieren mayor habilidad de programación y control del entorno.
Gracias al avance en la automatización y el control digital, estas máquinas permiten integrar sensores de monitoreo, cámaras de visión artificial, sistemas de registro de datos y funciones de diagnóstico en tiempo real. Esto no solo mejora la calidad de la soldadura, sino que también permite cumplir con requisitos de trazabilidad y certificación en industrias altamente reguladas. Además, muchas de estas máquinas pueden adaptarse fácilmente a líneas de producción, integrándose con robots o manipuladores para formar estaciones de soldadura completamente automatizadas.
En resumen, la maquinaria de soldadura para cordón circular constituye una herramienta esencial para garantizar uniones confiables, resistentes y estéticamente uniformes en piezas de geometría circular, con altos niveles de eficiencia, precisión y repetibilidad en la producción industrial moderna. ¿Te gustaría que te describa ejemplos específicos de este tipo de maquinaria en distintas industrias?
La maquinaria de soldadura para cordón circular está diseñada para abordar los desafíos específicos que presentan las uniones en piezas cilíndricas. A medida que la tecnología avanza, los equipos se están haciendo cada vez más sofisticados y adaptables a una amplia variedad de aplicaciones industriales. Esto incluye desde sistemas altamente automatizados, capaces de soldar sin intervención humana, hasta máquinas portátiles que pueden ser utilizadas en el campo para reparaciones o trabajos de mantenimiento en entornos difíciles.
Una de las principales características de estos equipos es su precisión en el control del arco de soldadura. Los sistemas modernos utilizan sensores inteligentes que monitorean el comportamiento del arco en tiempo real, ajustando parámetros como la corriente y el voltaje para mantener una soldadura uniforme y consistente. Esto es especialmente importante cuando se trabaja con materiales sensibles o cuando las uniones requieren una alta integridad estructural, como en la industria aeronáutica, la fabricación de componentes de alta presión o la industria nuclear.
Además, los posicionadores rotativos son esenciales para garantizar que la pieza se mantenga en una posición ideal durante el proceso de soldadura. Estos sistemas pueden girar la pieza a una velocidad constante mientras la antorcha de soldadura realiza un movimiento continuo a lo largo de la circunferencia. Dependiendo del diseño, algunos sistemas también permiten que la antorcha se mueva en un patrón orbital, lo que mejora la precisión y evita problemas como la falta de penetración o la formación de poros.
Una característica clave en la maquinaria de soldadura para cordón circular es la capacidad de realizar soldaduras en espacios reducidos o difíciles de acceder. Muchos de estos sistemas incluyen cabezas de soldadura compactas y ajustables que permiten trabajar en piezas de diámetros pequeños o en ubicaciones donde el acceso es limitado. Esto es particularmente útil en la industria del petróleo y gas, donde los equipos de soldadura deben trabajar en condiciones extremas y a menudo en tuberías de difícil acceso.
En cuanto a los procesos de soldadura, existen múltiples opciones disponibles, siendo la soldadura TIG orbital una de las más comunes para aplicaciones que requieren un alto nivel de precisión y un acabado limpio. Sin embargo, la soldadura MIG/MAG orbital también se utiliza en muchas aplicaciones industriales debido a su mayor velocidad y eficiencia en comparación con TIG, especialmente cuando se requieren soldaduras de mayor volumen. En aplicaciones donde se busca una penetración profunda con un aporte mínimo de calor, la soldadura por láser orbital es una opción que está ganando terreno, pues permite una soldadura extremadamente precisa con menos distorsión térmica.
La integración de sistemas de control avanzados también es una tendencia importante en la maquinaria de soldadura de cordón circular. Los PLC (controladores lógicos programables) y CNC (control numérico computarizado) permiten a los operadores programar de manera detallada los parámetros del proceso de soldadura, asegurando que las variaciones entre las diferentes piezas sean mínimas. Los sistemas de soldadura automatizados también pueden conectarse a sistemas de monitoreo en tiempo real para realizar ajustes dinámicos en función de las condiciones del proceso, lo que mejora la calidad y eficiencia.
Otro aspecto que ha mejorado en estos sistemas es la adaptabilidad a diferentes materiales. Las máquinas de soldadura para cordón circular están diseñadas para trabajar con una amplia gama de aleaciones, desde aceros inoxidables y aluminio hasta materiales más complejos como el titanio o el cobre. Gracias a la flexibilidad en los parámetros de soldadura y la disponibilidad de diferentes consumibles, estos equipos pueden ajustarse a las necesidades específicas de cada material, asegurando una fusión óptima y una unión resistente.
La portabilidad y la versatilidad de los equipos también están ganando importancia, especialmente en la industria de la construcción y el mantenimiento. Las máquinas de soldadura orbital portátiles permiten realizar reparaciones in situ, lo que ahorra tiempo y costos de transporte. Estas máquinas se han vuelto indispensables en la reparación de grandes estructuras, como plataformas petroleras, sistemas de tuberías de alta presión y otros equipos industriales que no pueden ser fácilmente desmontados para ser transportados a un taller de soldadura.
Finalmente, la sostenibilidad y la eficiencia energética también son consideraciones importantes. Muchas de las máquinas de soldadura modernas están diseñadas para ser más eficientes en términos de consumo de energía y reducción de residuos. Los avances en la tecnología de los gases de protección y la optimización de los parámetros de soldadura contribuyen a un uso más eficiente de los recursos, reduciendo el impacto ambiental del proceso. Además, la recuperación de calor y el uso de sistemas de reciclaje de gases también están ayudando a minimizar los desperdicios y hacer los procesos de soldadura más ecológicos.
En conclusión, la maquinaria de soldadura para cordón circular sigue avanzando en términos de automatización, precisión y adaptabilidad a nuevas aplicaciones industriales. Con el tiempo, se espera que estas máquinas continúen integrándose con tecnologías emergentes, como la inteligencia artificial, la internet industrial de las cosas (IIoT) y los sistemas de monitoreo remoto, para seguir mejorando la calidad de las soldaduras, reducir los costos operativos y aumentar la sostenibilidad en los procesos de fabricación.
A medida que la maquinaria de soldadura para cordón circular continúa evolucionando, la digitalización y la automatización juegan un papel cada vez más crucial en su desarrollo. La incorporación de inteligencia artificial (IA) y aprendizaje automático en estos sistemas no solo optimiza la calidad de la soldadura, sino que también permite la optimización dinámica de parámetros. Estos avances permiten que las máquinas aprendan de las variaciones en los procesos de soldadura y se ajusten automáticamente a diferentes condiciones, como la velocidad de avance de la antorcha, la distancia entre el electrodo y la pieza, y la tasa de enfriamiento, garantizando así resultados consistentes y mejorando la fiabilidad de las uniones.
Los sistemas de inspección en línea también han dado un paso adelante. Las máquinas modernas están equipadas con sensores de alta resolución y cámaras de visión artificial que pueden analizar la calidad del cordón de soldadura en tiempo real, identificando defectos como porosidad, grietas, o falta de penetración a medida que se realiza la soldadura. Esto no solo aumenta la calidad de la producción, sino que también reduce el riesgo de que defectos sean detectados en etapas posteriores del proceso, lo que ahorra tiempo y costos de retrabajo.
Por otro lado, los sistemas de monitoreo remoto permiten que los operadores supervisen el proceso de soldadura desde ubicaciones distantes, lo que es ideal para entornos industriales complejos y de difícil acceso. Esto es particularmente útil en la industria offshore, plantas nucleares o en la fabricación de componentes de alta gama, donde los ambientes pueden ser peligrosos o de difícil acceso. Además, la recopilación y análisis de datos en tiempo real mediante plataformas basadas en la nube ayuda a mejorar la toma de decisiones y la gestión de calidad, proporcionando retroalimentación inmediata sobre el estado de cada ciclo de soldadura y los parámetros involucrados.
La integración de la maquinaria de soldadura con sistemas ERP (Enterprise Resource Planning) también está ganando tracción. Esto permite una gestión más eficiente de los recursos, ya que las máquinas pueden intercambiar datos con otras partes de la cadena de suministro y fabricación, optimizando el uso de materiales y reduciendo tiempos muertos. Además, los datos recopilados durante las soldaduras pueden ser almacenados para cumplir con requisitos de trazabilidad y certificación, lo cual es esencial en sectores altamente regulados como el aeroespacial, automotriz y la fabricación de equipos médicos.
El uso de materiales avanzados también está mejorando la capacidad de los sistemas de soldadura para trabajar con una mayor variedad de metales y aleaciones. Los aceros de alta resistencia, aleaciones de titanio, materiales compuestos y materiales no ferrosos tienen diferentes características de soldabilidad que requieren ajustes precisos en el proceso. Las máquinas modernas son capaces de adaptarse a estos desafíos mediante el ajuste de parámetros como la energía de entrada, la velocidad de avance, y el tipo de gas de protección utilizado, asegurando una calidad de soldadura consistente.
En la práctica, la flexibilidad es una de las grandes ventajas de estos sistemas. Las máquinas de soldadura para cordón circular pueden ser configuradas para realizar una amplia gama de tipos de soldadura, desde soldaduras de alta velocidad y gran volumen, como las que se requieren en la fabricación de tuberías industriales, hasta aplicaciones más especializadas y de precisión, como la soldadura de componentes de precisión en la industria aeroespacial o automotriz. Esto hace que estas máquinas sean altamente versátiles y capaces de adaptarse rápidamente a diferentes exigencias y volúmenes de producción.
Además, la portabilidad y la facilidad de mantenimiento están mejorando continuamente. Aunque las máquinas de soldadura orbital y de cordón circular solían ser grandes y estacionarias, los avances en diseño y ingeniería han permitido que los equipos sean más compactos y fáciles de transportar. Algunas versiones más recientes incluyen unidades portátiles que permiten realizar soldaduras en campo, lo que es muy útil en aplicaciones de mantenimiento en sitios remotos, como plataformas de petróleo o en la construcción de infraestructuras.
Por último, la sostenibilidad sigue siendo un enfoque clave. La industria de la soldadura está cada vez más preocupada por los efectos ambientales de sus procesos. El consumo de energía y la generación de residuos son factores que las nuevas máquinas de soldadura intentan minimizar mediante tecnologías de eficiencia energética. Además, el reciclaje de gases de protección y el uso de técnicas de soldadura más limpias, como la soldadura láser, que minimizan la necesidad de consumibles, también están en auge. Todo esto contribuye a reducir la huella de carbono de los procesos industriales, especialmente en sectores como la fabricación de componentes de alta precisión.
En conclusión, los sistemas de maquinaria de soldadura para cordón circular están experimentando una transformación significativa, impulsada por la automatización, el control inteligente, la integración con plataformas digitales y un enfoque en la sostenibilidad. Con su capacidad de adaptarse a una variedad de aplicaciones y materiales, y su integración con tecnologías emergentes como la inteligencia artificial, la visión artificial y el monitoreo remoto, estos sistemas no solo están mejorando la calidad y eficiencia de las soldaduras, sino que están abriendo nuevas posibilidades en la fabricación moderna.
Sistemas de soldadura con cordón redondo
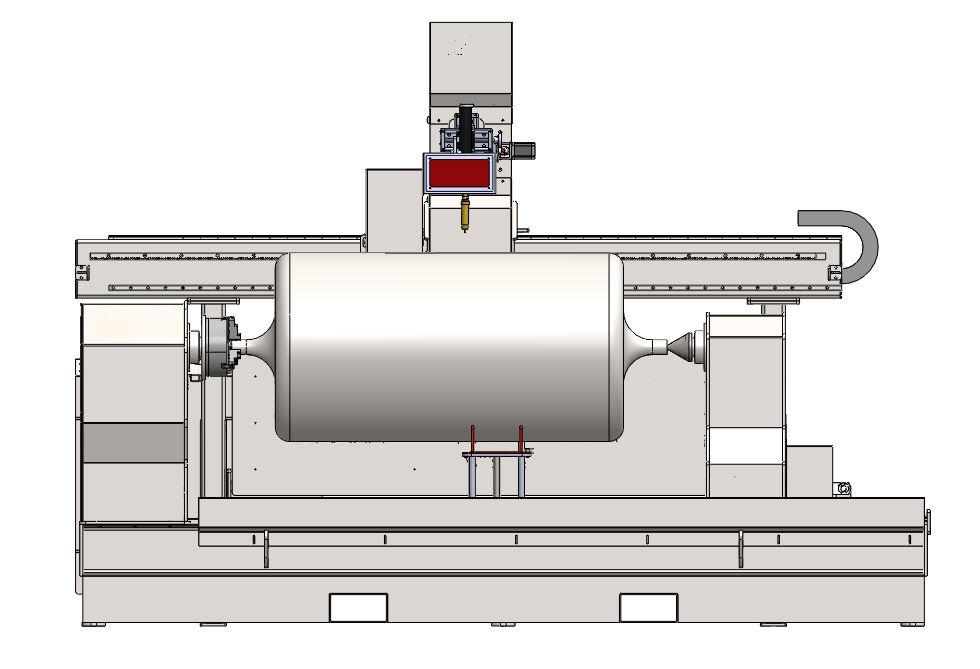
Los sistemas de soldadura con cordón redondo están diseñados específicamente para realizar uniones circulares en piezas de geometría cilíndrica o anular, como tubos, tanques, bridas y otras estructuras redondas. Estos sistemas están orientados a aplicaciones donde la soldadura se realiza a lo largo de una trayectoria circular, asegurando que el cordón de soldadura sea uniforme y continuo alrededor de la pieza. Este tipo de soldadura es fundamental en industrias como la construcción de tuberías, la fabricación de equipos de presión, la industria automotriz, y la aeroespacial, donde las uniones circulares son comunes y requieren alta precisión y resistencia.
Existen diversas tecnologías y procesos que se utilizan para llevar a cabo soldaduras con cordón redondo, dependiendo de los materiales a soldar, el tamaño de la pieza, y las condiciones específicas de la aplicación. Los sistemas de soldadura para cordón redondo pueden ser tanto manuales como automatizados, y están diseñados para ser lo suficientemente flexibles como para adaptarse a una variedad de requisitos de soldadura.
Uno de los métodos más comunes en estos sistemas es la soldadura orbital, que es un tipo de soldadura automatizada en la que una antorcha de soldadura se mueve alrededor de la pieza, siguiendo la trayectoria circular del cordón de soldadura. Este tipo de soldadura es particularmente útil cuando se requiere alta precisión y consistencia, ya que permite un control más exacto del proceso y minimiza las variaciones en la calidad de la soldadura. La soldadura orbital puede realizarse mediante varios procesos, como TIG (Tungsten Inert Gas), MIG (Metal Inert Gas), o plasma, dependiendo de las características del material y la aplicación.
La soldadura orbital TIG es uno de los procesos más utilizados en sistemas de soldadura con cordón redondo, ya que produce soldaduras limpias, con una alta calidad de acabado y una excelente resistencia a la corrosión, lo cual es crítico en muchas aplicaciones industriales. Además, este proceso ofrece una baja distorsión térmica, lo que es especialmente importante cuando se trabajan con materiales delicados o con tolerancias estrictas.
En sistemas de soldadura automatizados, los equipos suelen estar equipados con controladores numéricos (CNC) que permiten programar y controlar de manera precisa la velocidad de avance de la antorcha, la intensidad del arco de soldadura, el flujo de gas de protección, y otros parámetros esenciales. Estos sistemas son capaces de realizar soldaduras de alta calidad de manera continua y con poca intervención humana, lo que incrementa la productividad y reduce los errores durante el proceso. Los controladores CNC también permiten la integración con sistemas de monitoreo en tiempo real, lo que ayuda a detectar posibles defectos en la soldadura durante su ejecución.
En cuanto a los materiales de aporte, los sistemas de soldadura con cordón redondo son compatibles con una amplia gama de electrodos y alambres de soldadura, lo que permite adaptarse a diferentes tipos de metales y aleaciones, como aceros al carbono, aceros inoxidables, aluminio y aleaciones especiales. La selección del material de aporte es crucial para asegurar la calidad de la soldadura, especialmente en aplicaciones que requieren una alta resistencia mecánica y una larga vida útil, como en la industria de los componentes aeroespaciales o la fabricación de equipos para la industria petroquímica.
El uso de posicionadores rotativos es otra característica clave de los sistemas de soldadura con cordón redondo. Estos dispositivos giran la pieza de trabajo mientras la antorcha de soldadura se mantiene en su lugar o se desplaza de manera sincronizada, lo que permite realizar el cordón de soldadura de manera continua alrededor de la pieza. Este enfoque también permite trabajar en geometrías complejas o de difícil acceso, lo que hace que los sistemas de soldadura para cordón redondo sean extremadamente versátiles. Además, los posicionadores pueden ser ajustados para trabajar con piezas de diferentes tamaños y formas, desde pequeños tubos hasta grandes estructuras cilíndricas, lo que proporciona flexibilidad en la producción.
La soldadura por láser es otra opción que ha ganado popularidad en aplicaciones de soldadura de cordón redondo, especialmente cuando se busca una penetración profunda con un mínimo de distorsión térmica. Este proceso es ideal para materiales delgados o cuando se requiere una alta precisión en el cordón de soldadura. Aunque los sistemas de soldadura por láser son generalmente más costosos y requieren equipos especializados, ofrecen ventajas significativas en términos de velocidad, control de la penetración y calidad del cordón.
El monitoreo en tiempo real y la inspección automatizada también son elementos fundamentales en los sistemas de soldadura con cordón redondo. Muchas máquinas modernas cuentan con sistemas de visión artificial o sensores de ultrasonido que pueden detectar defectos como porosidad, grietas o falta de penetración durante el proceso de soldadura. Estos sistemas permiten a los operadores realizar ajustes inmediatos en los parámetros de soldadura para corregir cualquier problema antes de que se convierta en un defecto serio.
En resumen, los sistemas de soldadura para cordón redondo son esenciales para la fabricación de componentes de alta precisión que requieren soldaduras continuas y uniformes a lo largo de trayectorias circulares. Con la evolución de la automatización y la integración de tecnologías como el control numérico, la visión artificial y los sistemas de monitoreo en tiempo real, estos sistemas están mejorando continuamente en términos de precisión, eficiencia y versatilidad. A medida que la tecnología avanza, estos equipos se están convirtiendo en herramientas clave para una amplia variedad de aplicaciones industriales, ofreciendo un rendimiento superior y mayor control sobre la calidad del proceso de soldadura.
Los sistemas de soldadura para cordón redondo están diseñados para trabajar en entornos industriales que requieren uniones circulares con alta precisión y fiabilidad. A medida que la tecnología avanza, estos sistemas se vuelven cada vez más sofisticados, ofreciendo soluciones adaptadas a una variedad de aplicaciones que van desde la fabricación de piezas de alta resistencia hasta la producción en masa de componentes más simples. La soldadura orbital, una de las técnicas más utilizadas en estos sistemas, es especialmente popular debido a su capacidad para garantizar un acabado uniforme y una alta calidad en la soldadura. Esta técnica no solo se emplea en aplicaciones de alta precisión, como las de los sectores aeroespacial y nuclear, sino también en la construcción de infraestructura, como la unión de grandes tuberías y tanques, donde la integridad estructural es crucial.
El proceso de soldadura orbital se logra gracias a la capacidad de la maquinaria para realizar un movimiento de rotación constante, manteniendo la antorcha en una trayectoria circular continua a lo largo del componente. Esta rotación puede ser tanto del posicionador que sostiene la pieza como de la antorcha misma, dependiendo del diseño de la máquina. Esta flexibilidad asegura que las piezas complejas o con geometrías irregulares también puedan ser soldadas de manera eficiente. En muchos casos, la soldadura orbital se realiza mediante procesos de soldadura TIG (Tungsten Inert Gas), que son especialmente adecuados para metales sensibles a la oxidación, como el acero inoxidable o el titanio, ya que ofrecen un control excepcional sobre la penetración y el aspecto del cordón de soldadura. Estos sistemas también permiten ajustes precisos en la velocidad de rotación y el avance de la antorcha, lo que resulta en una soldadura de alta calidad sin distorsión térmica significativa.
Los sistemas automatizados, en los cuales el proceso de soldadura se maneja mediante controladores CNC (Control Numérico Computarizado), han mejorado significativamente la capacidad de estos equipos para realizar soldaduras repetitivas con alta consistencia. Gracias a los sensores de retroalimentación y la capacidad de programación avanzada, los sistemas de soldadura pueden ajustarse en tiempo real para corregir cualquier variación que pudiera surgir durante el proceso. Estos sistemas automatizados también pueden realizar tareas complejas de manera más eficiente que los soldadores manuales, lo que reduce el riesgo de errores humanos y mejora la eficiencia en producción. Además, el uso de robots industriales o manipuladores automatizados en combinación con sistemas de soldadura orbital permite operar en espacios reducidos o condiciones extremas, como en plataformas offshore o plantas industriales de difícil acceso.
En cuanto a la adaptabilidad, estos sistemas de soldadura son capaces de trabajar con diferentes materiales y aleaciones, lo que les permite ser utilizados en una amplia gama de aplicaciones. Desde metales comunes como acero inoxidable y aluminio hasta materiales más avanzados como aleaciones de titanio o superaleaciones de níquel, las máquinas de soldadura de cordón redondo están diseñadas para adaptarse a los requisitos de cada material. La selección del material de aporte es crucial para garantizar la calidad y resistencia de la unión, ya que la compatibilidad entre el material base y el de aporte influye directamente en la integridad de la soldadura.
Otro aspecto importante de los sistemas de soldadura de cordón redondo es el monitoreo de la calidad en tiempo real. Muchos de estos sistemas están equipados con tecnologías avanzadas de inspección no destructiva (END), como ultrasonido, radiografía o cámaras de visión artificial, que permiten detectar defectos como porosidad, grietas, falta de penetración o inclusiones durante el proceso de soldadura. Estos defectos pueden ser corregidos de inmediato, evitando que el componente termine con un defecto estructural que comprometa su funcionalidad. Esta capacidad de detección y corrección temprana es vital en industrias donde los estándares de calidad son extremadamente estrictos, como la fabricación de componentes aeronáuticos o equipos médicos.
La sostenibilidad también juega un papel cada vez más importante en el diseño de los sistemas de soldadura de cordón redondo. Con la creciente presión para reducir la huella de carbono y minimizar los residuos industriales, las máquinas modernas están siendo diseñadas para ser más energéticamente eficientes. La optimización de los parámetros de soldadura, como la corriente, el voltaje, la velocidad de avance y la selección de gases de protección, contribuye a un proceso más eficiente que genera menos desperdicios y consume menos energía. Además, el uso de gases reciclados y tecnologías de reducción de residuos también están ganando terreno en la industria, lo que permite reducir el impacto ambiental del proceso de soldadura.
Los avances en la portabilidad también están haciendo que estos sistemas sean más accesibles para aplicaciones de campo. Las máquinas de soldadura orbital portátiles permiten realizar reparaciones o soldaduras in situ en lugares donde las grandes máquinas estacionarias no pueden acceder. Esto es particularmente útil en la reparación de sistemas de tuberías en entornos remotos o en la construcción de infraestructuras móviles, como en la industria del petróleo y gas. Estas máquinas portátiles son una excelente opción para trabajos de mantenimiento, donde la soldadura debe realizarse rápidamente y con alta precisión.
En resumen, los sistemas de soldadura con cordón redondo están revolucionando diversas industrias al ofrecer soluciones de alta precisión, eficiencia y flexibilidad para la fabricación y reparación de componentes con geometría circular. La evolución hacia sistemas automatizados y el uso de tecnologías como el control numérico, la visión artificial y el monitoreo en tiempo real están mejorando significativamente la calidad de la soldadura, reduciendo costos y tiempos de producción. Al mismo tiempo, la capacidad de adaptarse a una variedad de materiales, la portabilidad y el enfoque en la sostenibilidad están haciendo de estos sistemas herramientas cada vez más indispensables en la manufactura moderna.
A medida que los sistemas de soldadura con cordón redondo continúan evolucionando, hay un énfasis creciente en la inteligencia artificial (IA) y el aprendizaje automático. Estas tecnologías permiten una mayor optimización del proceso en tiempo real, mejorando la calidad de la soldadura y adaptándose automáticamente a los cambios en las condiciones de operación. Por ejemplo, los algoritmos de IA pueden predecir y ajustar los parámetros de soldadura en función de variables como la temperatura, la velocidad de avance, el tipo de material o incluso la variabilidad del gas de protección, asegurando que el cordón de soldadura mantenga una uniformidad constante a lo largo del proceso.
Además, la tecnología de análisis de datos también ha mejorado la capacidad de los sistemas de soldadura para hacer un seguimiento continuo de la calidad y la eficiencia del proceso. Mediante el uso de plataformas de análisis en la nube, los datos recolectados de cada ciclo de soldadura pueden ser almacenados y procesados para realizar informes de rendimiento, estadísticas de calidad y diagnósticos predictivos. Esto no solo ayuda a mejorar la toma de decisiones durante el proceso de fabricación, sino que también contribuye a la gestión de la calidad a lo largo de la vida útil del producto.
Otro avance significativo es la personalización de los sistemas de soldadura para adaptarse a las necesidades específicas de diferentes industrias. Los avances en la tecnología de soldadura permiten ajustar los sistemas para que trabajen con una gama más amplia de materiales de aporte, lo que permite soldar con precisión metales más difíciles de manejar, como aceros de alta aleación, metales exóticos y materiales compuestos. Esto ha abierto nuevas posibilidades en industrias que requieren soldaduras especializadas, como la industria aeroespacial, automotriz y energía renovable, donde las tolerancias y las exigencias de resistencia son extremadamente estrictas.
La integración de sistemas también ha sido una tendencia clave. Los sistemas de soldadura de cordón redondo ahora se pueden integrar de manera fluida con otros procesos de fabricación y gestión de la producción. Por ejemplo, un sistema de soldadura automatizado puede estar vinculado a un sistema de planificación de recursos empresariales (ERP) para coordinar la fabricación de piezas, la adquisición de materiales y la programación de la producción. Esto no solo mejora la eficiencia del proceso de producción, sino que también garantiza la trazabilidad completa de cada componente, lo que es crucial en sectores donde la certificación y la trazabilidad son obligatorias, como la fabricación de equipos médicos o componentes aeroespaciales.
Un aspecto cada vez más relevante en los sistemas de soldadura con cordón redondo es el mantenimiento predictivo. Gracias a los sensores inteligentes instalados en las máquinas de soldadura, los datos generados por los equipos pueden ser analizados para predecir fallos antes de que ocurran. Esto permite programar el mantenimiento de los equipos de forma más eficiente, evitando tiempos de inactividad inesperados y aumentando la fiabilidad de las operaciones. Además, la utilización de modelos de simulación basados en datos históricos y de operación permite a los ingenieros optimizar los ciclos de mantenimiento y mejorar la vida útil de los componentes críticos de la máquina.
El entrenamiento y la capacitación de los operadores también se han vuelto más accesibles y efectivos gracias a las tecnologías emergentes. Muchas máquinas modernas vienen con interfaces de usuario intuitivas que guían al operador a través de los ajustes necesarios para cada tipo de soldadura. Además, las simulaciones de realidad aumentada y las plataformas de entrenamiento virtual permiten que los operadores practiquen y comprendan los parámetros de soldadura en un entorno simulado, mejorando su destreza antes de trabajar en una máquina real.
La adaptabilidad de estos sistemas también se ha incrementado gracias a los avances en la modularidad. Las máquinas de soldadura de cordón redondo ahora pueden ser fácilmente configuradas para trabajar con diferentes tipos de piezas, desde pequeños componentes hasta grandes estructuras, simplemente cambiando las herramientas o los accesorios. Esto es especialmente útil en fábricas que producen una amplia variedad de productos, ya que pueden ajustar rápidamente el equipo sin necesidad de un largo proceso de recalibración.
Finalmente, la sostenibilidad sigue siendo una prioridad para la industria de la soldadura. Las máquinas de soldadura para cordón redondo están diseñadas para ser más eficientes en cuanto a consumo de energía, generando menos desechos y utilizando materiales reciclables. También se están desarrollando procesos que permiten el uso de gases más ecológicos y la minimización del uso de consumibles, lo que ayuda a reducir el impacto ambiental de las operaciones industriales. Las investigaciones continúan en la mejora de las tecnologías de soldadura láser, que permiten soldaduras de alta precisión con una menor cantidad de material de aporte, generando menos residuos y ofreciendo una alternativa más limpia en comparación con los métodos tradicionales de soldadura.
En resumen, los sistemas de soldadura con cordón redondo están experimentando una transformación impulsada por avances tecnológicos en áreas como la automatización, el monitoreo inteligente, la integración de datos y la sostenibilidad. Estos sistemas no solo ofrecen mejores resultados de calidad y mayor eficiencia en la producción, sino que también están mejorando la seguridad y la fiabilidad de las operaciones. A medida que las máquinas se vuelven más inteligentes, más versátiles y más sostenibles, el futuro de la soldadura circular parece estar dirigido hacia una mayor automatización, personalización y optimización de los procesos de fabricación en una variedad de industrias.
Equipos de soldadura para cordón de forma circular
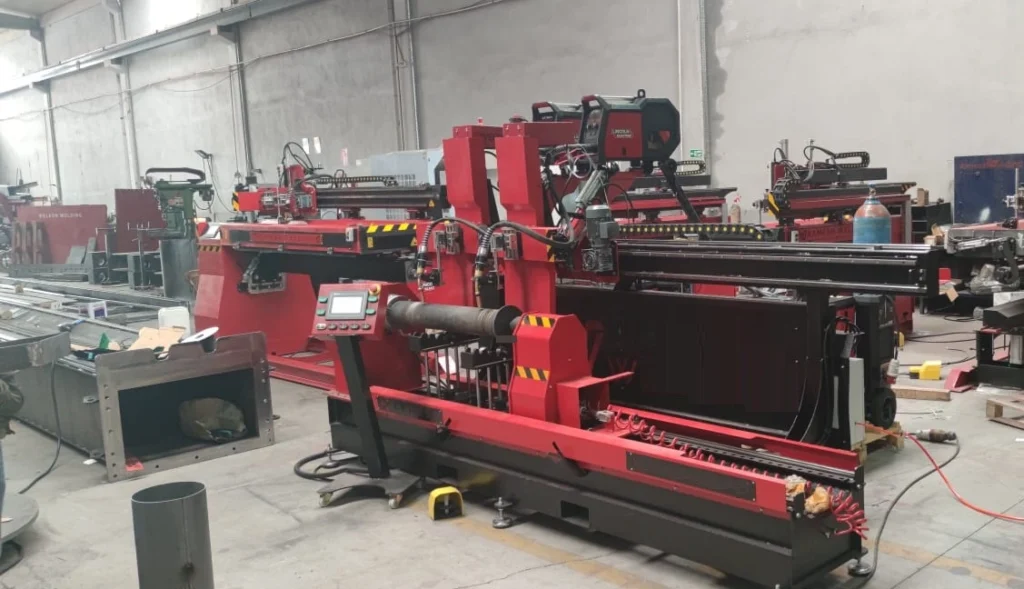
Los equipos de soldadura para cordón de forma circular son esenciales en procesos industriales donde se requieren uniones de alta precisión en piezas con geometrías circulares, como tubos, cilindros, tanques y bridas. Estos sistemas están diseñados específicamente para realizar soldaduras de manera continua y uniforme a lo largo de un trayecto circular, garantizando que el cordón de soldadura mantenga la calidad, resistencia y durabilidad necesarias para aplicaciones críticas. Los equipos utilizados en este tipo de soldadura son altamente especializados y pueden operar bajo diferentes métodos y tecnologías de soldadura, dependiendo de la naturaleza del proyecto y los materiales a soldar.
Tipos de Equipos de Soldadura para Cordón Circular
- Máquinas de Soldadura Orbital: Estas máquinas son las más utilizadas para la soldadura de cordones circulares, especialmente en la industria de las tuberías, la aeroespacial y la farmacéutica. La soldadura orbital permite un control preciso del proceso, ya que la antorcha de soldadura sigue un recorrido circular alrededor de la pieza de trabajo. Este tipo de soldadura es comúnmente realizado con el proceso TIG (Tungsten Inert Gas), que es ideal para materiales sensibles como acero inoxidable y aleaciones de titanio, proporcionando una soldadura limpia y de alta calidad. Las máquinas de soldadura orbital están equipadas con controladores CNC, que permiten programar los parámetros de soldadura para cada operación, garantizando una consistencia máxima.
- Posicionadores Rotativos: Los posicionadores rotativos son dispositivos que giran la pieza a soldar, permitiendo que la antorcha mantenga una posición fija mientras la pieza se mueve alrededor de ella. Esto es particularmente útil cuando se soldan piezas de gran tamaño o cuando se requiere una alta precisión en el cordón de soldadura. Estos posicionadores pueden ser controlados de manera manual o automática, según el tipo de proceso que se utilice.
- Sistemas de Soldadura Automática con Alimentación de Alambre: En sistemas de soldadura más complejos, se puede utilizar maquinaria automatizada que alimenta el alambre de soldadura mientras la antorcha sigue la trayectoria circular. Estos sistemas permiten realizar soldaduras de manera continua, sin necesidad de intervención manual, lo que aumenta la eficiencia y reduce el riesgo de errores humanos. Estos equipos son ideales para aplicaciones de producción en serie, donde se requieren soldaduras rápidas y consistentes.
- Máquinas de Soldadura por Láser: Las máquinas de soldadura por láser están ganando popularidad en aplicaciones que requieren soldaduras con mínima distorsión térmica y una alta precisión en el cordón circular. El láser permite una penetración profunda con una mínima cantidad de material de aporte, lo que resulta en un proceso rápido y limpio. Estos equipos son particularmente útiles en la industria automotriz y aeroespacial, donde los requisitos de precisión y acabado son muy exigentes.
- Sistemas de Soldadura MIG/MAG (Metal Inert Gas / Metal Active Gas): Si bien estos procesos no son tan comunes en soldaduras de cordón circular de alta precisión como el TIG, también se utilizan en aplicaciones industriales donde se requiere una velocidad de soldadura más alta y el material base es más grueso. En la soldadura MIG/MAG, la antorcha sigue un recorrido circular mientras se alimenta el alambre de soldadura, lo que permite una unión rápida y fuerte. Este proceso se usa con frecuencia para soldaduras de acero al carbono y acero inoxidable en aplicaciones como la fabricación de estructuras metálicas.
- Máquinas de Soldadura de Puntos Circulares: Este tipo de soldadura es utilizado principalmente en la fabricación de componentes más pequeños y piezas que requieren una soldadura puntual a lo largo de una circunferencia. A través de un proceso de presión y corriente, se realiza una pequeña soldadura en un punto específico de la pieza, y luego la máquina avanza a la siguiente ubicación, formando un cordón circular.
Características de los Equipos de Soldadura para Cordón Circular
- Automatización: Los equipos modernos para soldadura circular suelen estar automatizados, lo que reduce significativamente la intervención manual. La automatización mejora la precisión y la consistencia del proceso de soldadura, lo que es crucial cuando se trabaja con materiales que requieren una alta calidad de unión.
- Control Numérico (CNC): Los sistemas de control numérico (CNC) permiten la programación precisa de las trayectorias de soldadura, la velocidad de avance de la antorcha, la intensidad del arco y otros parámetros clave. Esta capacidad de personalización es esencial para garantizar que cada soldadura cumpla con los estándares de calidad requeridos.
- Monitoreo en Tiempo Real: Muchos de los equipos de soldadura actuales están equipados con sensores avanzados que permiten monitorear el proceso en tiempo real. Esto incluye la medición de la temperatura del arco, la velocidad de soldadura y el control del gas de protección, lo que asegura que la soldadura se realice dentro de los parámetros óptimos y se detecten problemas potenciales de manera temprana.
- Alta Precisión: La capacidad de mantener un cordón circular uniforme es esencial en aplicaciones de alta precisión. Los equipos modernos ofrecen una alta estabilidad durante la soldadura, lo que permite lograr un acabado estéticamente limpio y técnicamente fiable, adecuado para industrias con altos estándares de calidad.
- Flexibilidad: Los equipos de soldadura para cordón circular pueden ser adaptados a una variedad de procesos y materiales. Esto incluye la capacidad de soldar diferentes metales, como acero inoxidable, aleaciones de titanio y aluminio, y ajustar los parámetros de soldadura según el material base y el tipo de junta.
- Reducción de Desperdicio: Los sistemas de soldadura automatizados y de alta precisión también ayudan a minimizar el uso innecesario de material de aporte y gas de protección. Esto contribuye a la reducción de costos y mejora la sostenibilidad de las operaciones de soldadura.
- Seguridad: Dado que la soldadura implica la generación de altas temperaturas y energía eléctrica, los equipos de soldadura modernos incluyen sistemas de seguridad que protegen al operador y aseguran el correcto funcionamiento de la máquina. Esto incluye sistemas de protección contra sobrecalentamiento, fallos eléctricos y sistemas de control de gases.
Aplicaciones Comunes de los Equipos de Soldadura para Cordón Circular
- Industria de Tuberías: Soldadura de uniones circulares en tuberías de acero inoxidable o aleaciones especiales para sistemas de transporte de gas, agua y petróleo.
- Fabricación de Tanques y Recipientes a Presión: Utilizado en la fabricación de tanques de almacenamiento, reactores y otros equipos de alta presión.
- Industria Aeroespacial: Para la soldadura de piezas complejas y estructuras de aeronaves que requieren soldaduras de alta resistencia y precisión.
- Industria Automotriz: Soldadura de componentes estructurales y chasis de vehículos, donde se requiere una alta resistencia en uniones circulares.
- Electrodomésticos y Electrodomésticos de Cocina: Para la fabricación de productos como ollas a presión, teteras y otros dispositivos que tienen formas circulares.
- Industria Petroquímica y Energía: Para la fabricación y mantenimiento de equipos como intercambiadores de calor, generadores y otros sistemas donde se requieren uniones circulares de alta calidad.
En resumen, los equipos de soldadura para cordón circular juegan un papel fundamental en diversas industrias, proporcionando soluciones eficientes, de alta calidad y consistentes para unir piezas de forma continua a lo largo de trayectorias circulares. La continua evolución de estas tecnologías está permitiendo soldaduras más rápidas, precisas y sostenibles, lo que beneficia tanto a los fabricantes como a los usuarios finales en términos de calidad y costo.
Los equipos de soldadura para cordón circular, al ser especializados, han evolucionado considerablemente con el tiempo, adaptándose a las exigencias del mercado moderno y a las innovaciones tecnológicas en la industria de la soldadura. La clave de estos sistemas radica en su capacidad para realizar uniones circulares precisas y continuas, lo que es fundamental para mantener la integridad estructural de las piezas soldadas. La creciente demanda de eficiencia y la necesidad de cumplir con normativas de calidad más estrictas han llevado al desarrollo de máquinas más avanzadas que no solo facilitan el proceso de soldadura, sino que también mejoran la sostenibilidad del proceso en términos de reducción de residuos y ahorro energético.
A medida que la tecnología sigue avanzando, los sistemas de soldadura circular están incorporando capacidades de inteligencia artificial (IA) para mejorar la toma de decisiones y ajustar automáticamente los parámetros de soldadura. Estos sistemas de IA son capaces de predecir el comportamiento del proceso basándose en datos históricos y condiciones en tiempo real, lo que permite una optimización continua. Por ejemplo, en una máquina de soldadura orbital, la IA puede ajustar la velocidad de rotación, la potencia del arco y la temperatura de manera dinámica para adaptarse a las variaciones del material o la atmósfera de soldadura. Este tipo de control inteligente no solo mejora la calidad del cordón de soldadura, sino que también reduce la probabilidad de defectos como porosidad o grietas.
Los avances en la tecnología de sensores también están transformando los equipos de soldadura para cordón circular. Los sensores de temperatura, presión y desplazamiento permiten a los sistemas medir con precisión las condiciones del proceso, lo que facilita un control más fino de los parámetros de soldadura. Los datos obtenidos de estos sensores se pueden analizar en tiempo real y servir como retroalimentación para ajustar el proceso sobre la marcha. Esta capacidad de ajuste instantáneo es especialmente útil en aplicaciones de alta precisión donde cualquier pequeña variación podría comprometer la calidad de la soldadura.
La integración de sistemas de monitorización remota también está ganando terreno, lo que permite a los operadores controlar las máquinas de soldadura desde ubicaciones distantes. A través de plataformas basadas en la nube, los operadores pueden acceder a los datos de la máquina, recibir alertas sobre posibles fallos o realizar ajustes en los parámetros sin necesidad de estar físicamente presentes. Esta conectividad también facilita el mantenimiento preventivo, ya que los técnicos pueden identificar problemas potenciales antes de que se conviertan en fallos costosos. Además, el acceso remoto a los equipos permite a las empresas mejorar la gestión de la producción, monitorear el rendimiento de las máquinas y obtener información valiosa para optimizar los procesos de soldadura.
En términos de materiales, la capacidad de estos equipos para adaptarse a una gama cada vez más amplia de aleaciones y metales continúa mejorando. Los avances en el control de la atmósfera de soldadura, el uso de gases inertes y activos, y la capacidad de ajustarse a diferentes espesores y composiciones de material han hecho que las máquinas de soldadura para cordón circular sean capaces de trabajar con materiales que antes eran difíciles de soldar, como acero inoxidable duplex, titanio o aluminio de alta resistencia. Esta versatilidad abre nuevas oportunidades en sectores como la industria aeronáutica, donde se requieren uniones de alta resistencia y baja distorsión, o en la energía renovable, donde los materiales avanzados se están utilizando cada vez más para componentes como turbinas eólicas o paneles solares.
La sostenibilidad también está influyendo en el diseño de estos equipos, con una mayor eficiencia energética y una reducción en los residuos generados durante el proceso de soldadura. Las máquinas modernas están optimizando el uso de los consumibles, como el alambre de soldadura y los gases, para minimizar el desperdicio, mientras que las tecnologías de reciclaje de gases y la reducción de emisiones están permitiendo que los procesos de soldadura sean más amigables con el medio ambiente. En este sentido, los sistemas de soldadura de última generación también están diseñados para maximizar la recuperación de calor y minimizar el uso de recursos, lo que contribuye a un enfoque más ecológico de la fabricación industrial.
Otro aspecto relevante es la portabilidad de los equipos de soldadura. Mientras que las máquinas de soldadura orbital y las de gran tamaño se utilizan principalmente en entornos de fabricación grandes o plantas industriales, las versiones portátiles están ganando popularidad, especialmente en aplicaciones de mantenimiento y reparación. Estas unidades más pequeñas y móviles permiten a los operadores realizar soldaduras en el lugar, ya sea en instalaciones de tuberías, plantas de energía o incluso en el ámbito de la fabricación de equipos en campo, donde se necesita flexibilidad y capacidad de adaptación para soldar en ubicaciones remotas o de difícil acceso.
Por último, la capacitación en el uso de estos sistemas sigue siendo crucial para garantizar que los operadores puedan maximizar el rendimiento de las máquinas. Con la creciente sofisticación de las máquinas de soldadura, la formación continua es esencial para que los operadores se mantengan al día con las nuevas tecnologías y metodologías. Además, muchos fabricantes de equipos de soldadura ofrecen programas de capacitación que incluyen simuladores y sistemas de realidad virtual para enseñar a los operadores a manejar las máquinas de manera efectiva antes de que trabajen con equipos reales. Esta capacitación no solo mejora la eficiencia y la seguridad del proceso, sino que también reduce el riesgo de errores y defectos, garantizando que las soldaduras sean de la más alta calidad.
En resumen, los equipos de soldadura para cordón circular continúan avanzando en términos de precisión, eficiencia y sostenibilidad. La integración de nuevas tecnologías como la automatización, los sensores inteligentes, la IA y la conectividad remota está transformando la forma en que se realizan las soldaduras en sectores industriales clave. A medida que estos sistemas se vuelven más versátiles y accesibles, su uso se expandirá en una variedad de aplicaciones, mejorando la calidad, reduciendo los costos y minimizando el impacto ambiental de los procesos de soldadura.
La evolución de los equipos de soldadura para cordón circular también ha sido influenciada por las exigencias de calidad de fabricación en industrias de alto rendimiento. Los avances en la tecnología de soldadura sin contacto, como la soldadura por láser, permiten realizar uniones circulares con una precisión extrema. En estos sistemas, el láser se utiliza para fundir los materiales de base con una precisión casi milimétrica, reduciendo al mínimo la distorsión térmica y los residuos. Esto es especialmente ventajoso en aplicaciones donde se requiere una alta calidad superficial y una mínima deformación del material, como en la fabricación de componentes electrónicos o en piezas aeroespaciales.
Un aspecto importante que ha evolucionado junto con los equipos de soldadura es el uso de robots de soldadura. Estos robots, equipados con sistemas de visión y algoritmos de aprendizaje automático, pueden realizar soldaduras circulares complejas de manera autónoma. Los robots pueden adaptarse a variaciones de la pieza a soldar, ajustando su movimiento y parámetros de soldadura en tiempo real para mantener la calidad constante en un entorno de producción en masa. La capacidad de los robots de soldadura para ejecutar tareas repetitivas con alta precisión aumenta la eficiencia en entornos industriales, reduciendo costos y aumentando la productividad.
Con el aumento de la fabricación aditiva y la impresión 3D, algunos sistemas de soldadura están comenzando a integrar estas tecnologías para ofrecer soluciones híbridas. La soldadura 3D es una extensión del proceso de impresión 3D, donde un cordón de soldadura es depositado capa por capa de manera precisa para crear un objeto. Estos procesos híbridos permiten no solo reparar piezas ya existentes, sino también crear estructuras nuevas a partir de materiales metálicos de forma controlada. Esta sinergia de tecnologías está abriendo nuevas fronteras en la fabricación de componentes metálicos complejos que antes no eran posibles con los métodos tradicionales de soldadura.
Además de las mejoras tecnológicas, los sistemas de soldadura para cordón circular también han tenido que adaptarse a las demandas del mercado global, que exige una mayor flexibilidad y capacidad para producir en lotes pequeños o personalizados. Esto ha llevado a la creación de equipos modulares que pueden ajustarse rápidamente a diferentes configuraciones de piezas y tipos de soldadura. Con estos sistemas, las fábricas pueden producir una amplia gama de productos sin la necesidad de un cambio completo en el equipo, lo que reduce los tiempos de inactividad y los costos de producción. Esta flexibilidad también es esencial en industrias como la medicina o la industria de dispositivos electrónicos, donde se fabrican piezas de alta complejidad en volúmenes relativamente pequeños.
En términos de costos, los equipos de soldadura avanzados siguen siendo una inversión considerable, pero a largo plazo, su rentabilidad se ve reflejada en la reducción de desperdicios, tiempos de inactividad y en la mejora de la calidad. Los sistemas automatizados, junto con los avances en tecnología de sensores y procesamiento de datos, también permiten realizar un mantenimiento predictivo, lo que minimiza los costos asociados con fallos inesperados. A través del monitoreo continuo de los parámetros de la máquina y el análisis de datos en tiempo real, las empresas pueden predecir cuándo un componente de la máquina necesita ser reemplazado, evitando tiempos muertos y aumentando la disponibilidad del equipo.
Otro avance relevante es el uso de tecnologías de soldadura sin materiales de aporte. Estas técnicas, como la soldadura por láser de alta potencia o el plasma de alta frecuencia, pueden unir piezas metálicas sin la necesidad de un alambre de soldadura tradicional. Esto no solo mejora la eficiencia del proceso al reducir la cantidad de material necesario, sino que también permite una mejor fusión de los metales base, ya que el proceso genera menos calor y minimiza la distorsión en las piezas. Esto es especialmente importante cuando se trabaja con materiales delicados o cuando se requiere una mayor resistencia estructural en las uniones soldadas.
La industria naval y la industria de la construcción están adoptando cada vez más estos avances para mejorar la resistencia y la durabilidad de las uniones circulares. Los equipos de soldadura para cordón circular permiten una soldadura consistente y de alta calidad en aplicaciones de alta demanda, como la fabricación de casco de barcos o estructuras metálicas para edificios, donde la integridad de las soldaduras es esencial para la seguridad de las estructuras. La soldadura de alta precisión y sin defectos es crucial para garantizar que las estructuras puedan soportar las tensiones a las que se ven expuestas durante su vida útil.
Además, la conformidad normativa y los estándares de calidad también están impulsando la mejora de los equipos de soldadura. Muchos sectores requieren que los sistemas de soldadura cumplan con normativas específicas, como las de la ISO, ASME o la ASTM, y las máquinas más avanzadas vienen equipadas con funciones de validación de calidad que garantizan que cada soldadura cumple con los requisitos de certificación. Estas funciones incluyen la inspección automática de los cordones de soldadura mediante inspección por ultrasonido, radiografía o inspección visual automatizada, lo que garantiza que no haya defectos internos ni externos.
Finalmente, la capacitación y la adaptación a nuevas tecnologías sigue siendo uno de los pilares fundamentales para el éxito en la implementación de equipos de soldadura avanzados. Las empresas están invirtiendo cada vez más en programas de entrenamiento de alta calidad para sus operarios, lo que les permite estar al tanto de las últimas innovaciones y aprovechar al máximo las capacidades de las máquinas. Esto también incluye el entrenamiento en el uso de software avanzado que acompaña a los sistemas de soldadura, permitiendo a los operadores programar y controlar los procesos de manera más eficiente y precisa.
En conclusión, los equipos de soldadura para cordón circular siguen evolucionando, impulsados por avances tecnológicos, la automatización, y la búsqueda constante de eficiencia y sostenibilidad. Estos sistemas no solo mejoran la calidad de las soldaduras, sino que también optimizan la producción, reducen costos y mejoran la seguridad en las operaciones. Con el tiempo, la incorporación de tecnologías como la inteligencia artificial, mantenimiento predictivo y soldadura sin materiales de aporte seguirá llevando a la industria de la soldadura a nuevas alturas de precisión y eficiencia.
Sistemas de soldado para cordón circular
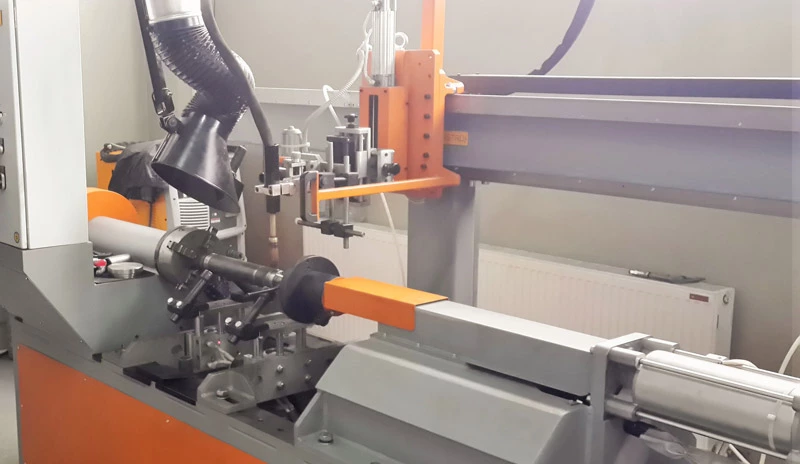
Los sistemas de soldado para cordón circular están diseñados para realizar uniones circulares de alta calidad en piezas con geometrías redondeadas. Este tipo de soldadura se utiliza comúnmente en aplicaciones industriales donde las piezas a unir tienen formas como tubos, tanques, recipientes a presión, entre otros. Existen diversos tipos de tecnologías y equipos para llevar a cabo la soldadura circular, dependiendo de la complejidad de la tarea, los materiales a unir y los requisitos de la aplicación. A continuación, se detallan algunos de los principales sistemas de soldadura utilizados en este tipo de procesos.
1. Soldadura Orbital
La soldadura orbital es uno de los sistemas más populares para realizar cordones circulares. Este proceso se utiliza principalmente en la industria de las tuberías y en la fabricación de componentes de alta precisión, como aquellos en la industria aeroespacial, medicina y energía.
En la soldadura orbital, la antorcha de soldadura se mueve de manera circular alrededor de la pieza a soldar, lo que permite realizar un cordón continuo y uniforme. Este tipo de soldadura suele utilizarse con el proceso TIG (Tungsten Inert Gas), que proporciona una soldadura limpia y precisa.
Las máquinas de soldadura orbital están equipadas con controladores CNC (Control Numérico por Computadora), que permiten a los operadores programar parámetros de soldadura de manera precisa. Esto es particularmente importante para obtener uniones circulares de alta calidad, especialmente cuando se requieren uniones con especificaciones rigurosas.
2. Soldadura por Láser
La soldadura por láser es una tecnología avanzada que se utiliza cada vez más para la soldadura de cordones circulares, especialmente cuando se requiere una alta precisión y un acabado de calidad superior. En este proceso, se utiliza un haz láser focalizado para fundir los materiales en una pequeña área, lo que minimiza la distorsión térmica y asegura una penetración uniforme.
El proceso de soldadura por láser es muy útil en materiales delgados, como el acero inoxidable o aluminio, y se utiliza comúnmente en la industria aeroespacial, electrónica y automotriz, donde las tolerancias son muy estrictas. La alta velocidad del proceso también permite una mayor productividad, lo que lo convierte en una opción eficiente para aplicaciones en serie.
3. Soldadura MIG/MAG (Metal Inert Gas / Metal Active Gas)
La soldadura MIG/MAG es otro sistema que se utiliza en la soldadura de cordones circulares, especialmente cuando se requiere una mayor velocidad de soldadura y las piezas son de material más grueso o menos sensible a la distorsión. Este proceso implica el uso de un gas de protección, que puede ser inert (como el argón) o activo (como el dióxido de carbono o una mezcla de gases), para proteger el área de soldadura.
En los sistemas MIG/MAG, se alimenta un alambre de soldadura que se funde y se deposita para formar la unión. Aunque no es tan preciso como la soldadura orbital o por láser, es muy eficiente y ampliamente utilizado en la industria pesada, como la fabricación de estructuras metálicas y la industria automotriz, para realizar soldaduras de cordón circular en aplicaciones de alto volumen.
4. Soldadura por Arco Sumergido (SAW)
La soldadura por arco sumergido (SAW) es una técnica que utiliza un arco eléctrico entre un electrodo de soldadura y la pieza de trabajo. El proceso se realiza bajo una capa de flux que cubre el área de soldadura, lo que protege la soldadura de la contaminación del aire. Este proceso es altamente eficiente, con alta tasa de deposición y es ideal para soldar materiales gruesos.
Aunque este proceso no es tan común para soldaduras de precisión como la soldadura orbital o por láser, es útil para soldaduras en tubos grandes o recipientes a presión, donde se requiere una unión fuerte y rápida. Es un sistema empleado principalmente en la industria de la construcción pesada y la industria de tubos.
5. Soldadura de Resistencia por Puntos Circulares
En aplicaciones donde se requieren pequeñas soldaduras puntuales a lo largo de un recorrido circular, se puede utilizar la soldadura de resistencia por puntos. Este sistema se basa en la aplicación de presión y corriente eléctrica para generar calor en un área local de la pieza, fundiendo los metales en un punto específico. Luego, el sistema avanza y repite el proceso para continuar con el cordón circular.
Este tipo de soldadura se utiliza en la fabricación de componentes más pequeños, como electrodomésticos y dispositivos electrónicos, donde las uniones no requieren la misma resistencia que las de una soldadura de arco o por láser, pero sí una unión rápida y eficiente.
6. Soldadura TIG (Tungsten Inert Gas)
La soldadura TIG es un proceso de soldadura de arco que utiliza un electrodo no consumible de tungsteno para crear el arco, mientras que un gas inerte como el helio o el argón protege el área de soldadura. Este proceso es muy preciso y es ideal para materiales delgados o piezas de alta calidad, como acero inoxidable, aluminio y aleaciones especiales.
La soldadura TIG se utiliza en la soldadura orbital y en otros sistemas de soldadura para cordón circular, especialmente cuando se requiere un control preciso de la temperatura y la penetración del arco. Aunque la velocidad de soldadura no es tan alta como la de otros procesos como MIG/MAG, la calidad del cordón de soldadura es excelente, lo que la convierte en una opción preferida para aplicaciones de alta gama.
7. Soldadura por Fricción
La soldadura por fricción es un proceso relativamente nuevo que se utiliza en algunos casos para unir piezas de manera eficiente, especialmente cuando las piezas tienen geometrías complejas o se requieren uniones con una mínima distorsión. En este proceso, las piezas a soldar se frotan entre sí a alta velocidad, generando calor por fricción que permite la fusión de los materiales sin necesidad de material de aporte.
Aunque este tipo de soldadura no se utiliza comúnmente para cordones circulares, en aplicaciones específicas como la industria automotriz y la fabricación de componentes de alta precisión, ha demostrado ser eficaz.
Conclusión
Cada uno de estos sistemas de soldadura tiene sus ventajas y limitaciones, por lo que la elección del proceso adecuado depende de factores como el tipo de material, el grosor de las piezas, la precisión requerida, la velocidad de producción y los costos asociados. La tendencia actual es hacia la automatización y la integración de tecnologías avanzadas como la soldadura orbital CNC y la soldadura por láser, que proporcionan un alto grado de precisión y eficiencia en la producción de cordones circulares.
Independientemente del sistema utilizado, lo importante es garantizar que el proceso de soldadura proporcione una unión fuerte, duradera y precisa, cumpliendo con los estándares de calidad requeridos para cada aplicación industrial.
Los sistemas de soldadura para cordón circular continúan avanzando con el tiempo, adaptándose a nuevas demandas tecnológicas y de eficiencia. El objetivo principal de estos sistemas es lograr uniones circulares de alta calidad y precisión, lo que es crucial en aplicaciones industriales como la fabricación de tuberías, estructuras metálicas, componentes aeroespaciales y en la industria automotriz. Los avances en automatización, robótica y sensores inteligentes están transformando estos procesos, permitiendo un control más preciso y eficiente durante la ejecución de la soldadura.
Uno de los aspectos más innovadores es la incorporación de la inteligencia artificial en los sistemas de soldadura. Esto permite a las máquinas ajustar los parámetros del proceso en tiempo real según las condiciones de trabajo, como la variabilidad del material, la temperatura ambiente o la vibración de la pieza. Al monitorear constantemente el proceso, los sistemas son capaces de prever posibles fallos o defectos y ajustarse automáticamente para garantizar la calidad de la soldadura. Esta capacidad de autoajuste es especialmente útil en entornos de producción en masa donde la consistencia y la calidad son fundamentales.
El uso de robots de soldadura ha crecido significativamente en los últimos años. Estos robots, equipados con brazos articulados y sistemas de visión, pueden realizar soldaduras circulares con un alto grado de precisión, incluso en entornos complejos y de difícil acceso. Los robots no solo mejoran la eficiencia de la producción, sino que también permiten un control mucho más riguroso de los parámetros de soldadura, lo que reduce la variabilidad entre piezas y aumenta la calidad general del producto final. Además, al ser capaces de realizar soldaduras de manera autónoma, estos robots reducen la exposición de los operarios a condiciones peligrosas, como la radiación del arco o los gases generados durante el proceso.
La soldadura por láser, que es conocida por su alta precisión y velocidad, ha demostrado ser especialmente útil para realizar cordones circulares con una calidad excelente. Este proceso permite soldar metales delgados o materiales de difícil soldadura con una mínima distorsión y sin la necesidad de material de aporte, lo que mejora la eficiencia y reduce el tiempo de trabajo. El uso de láseres de alta potencia también hace posible la soldadura de metales especiales como el titanio y las aleaciones de alta resistencia, que a menudo se utilizan en sectores como la aeroespacial y la medicina.
El control de calidad es un área donde los sistemas de soldadura para cordón circular también han experimentado avances significativos. La inspección automática mediante tecnologías como ultrasonido, radiografía o técnicas ópticas puede realizarse en tiempo real durante el proceso de soldadura, asegurando que no haya defectos como grietas, porosidades o desalineamientos en el cordón. Estos sistemas de monitoreo automático son esenciales para cumplir con las normas internacionales de calidad, especialmente en industrias donde la fiabilidad de las soldaduras es crítica, como en la energía nuclear o la industria petroquímica.
Además, la incorporación de software avanzado para la simulación y el control de los procesos de soldadura ha permitido a los operarios y técnicos ajustar las máquinas con mayor precisión. Estos programas pueden simular el proceso completo de soldadura, permitiendo a los ingenieros prever problemas antes de que ocurran en el proceso real. Esto ayuda a reducir el tiempo de configuración de las máquinas, optimizar los parámetros de soldadura y evitar errores costosos durante la producción.
Los sistemas de soldadura para cordón circular también están cada vez más diseñados para ser más sostenibles y eficientes en términos de consumo energético y generación de residuos. Las máquinas modernas tienen un consumo energético optimizado, lo que contribuye a la reducción de los costos operativos y disminuye el impacto ambiental. En algunos casos, los sistemas de soldadura ahora incorporan tecnologías de reciclaje de gases o recuperación de calor, lo que no solo mejora la eficiencia del proceso, sino que también contribuye a una producción más limpia.
La capacidad de adaptarse a diferentes materiales es otro factor clave que ha impulsado la evolución de estos sistemas. La soldadura circular se utiliza para una amplia variedad de materiales, desde acero inoxidable y aluminio hasta materiales compuestos y aleaciones especiales. Las máquinas de soldadura actuales son capaces de manejar estos materiales con facilidad, ajustando automáticamente los parámetros de soldadura según el tipo de material, el grosor de las piezas y las condiciones de trabajo. Esto aumenta la versatilidad de las máquinas y permite a las empresas realizar una gama más amplia de tareas con un solo sistema.
Con el auge de la fabricación aditiva, las tecnologías híbridas de soldadura y impresión 3D están emergiendo como soluciones innovadoras. Estos sistemas permiten crear piezas de metal capa por capa mediante un proceso de soldadura controlada, lo que abre nuevas posibilidades en la fabricación de componentes metálicos complejos. La combinación de la soldadura orbital con la impresión 3D está permitiendo crear piezas de geometrías altamente complejas que no serían posibles mediante técnicas de fabricación tradicionales. Este tipo de tecnología también se está utilizando para la fabricación de prototipos o la reparación de piezas que ya están en uso, como en el caso de las turbinas o las partes de maquinaria que requieren una sustitución de componentes con formas precisas.
Finalmente, el mantenimiento predictivo se está convirtiendo en una parte integral de los sistemas de soldadura modernos. Equipados con sensores y tecnologías de conectividad, estos sistemas son capaces de analizar el rendimiento de las máquinas en tiempo real y predecir posibles fallos antes de que ocurran. Esto no solo mejora la disponibilidad de los equipos, sino que también reduce los costos asociados con el mantenimiento no planificado y las paradas de producción.
En resumen, los sistemas de soldadura para cordón circular están experimentando un rápido avance hacia la automatización, la inteligencia artificial, la sostenibilidad y la integración de nuevas tecnologías. La capacidad de estos sistemas para ofrecer soldaduras de alta calidad y precisión, adaptarse a una amplia gama de materiales y mejorar la eficiencia energética está transformando diversas industrias, haciendo que los procesos de soldadura sean más rápidos, más económicos y más sostenibles. Estos avances continúan abriendo nuevas oportunidades para la fabricación de componentes industriales en sectores como la aeroespacial, la automotriz, la energía y la medicina.
El futuro de los sistemas de soldadura para cordón circular parece estar cada vez más orientado hacia una integración más profunda de la tecnología de la información y el análisis de datos. En este sentido, la evolución de los sistemas de soldadura no solo se centra en mejorar la calidad de las uniones, sino también en optimizar los procesos de producción de manera más inteligente. La implementación de big data y análisis predictivos permitirá, por ejemplo, anticipar fallos en el proceso de soldadura o incluso ajustar los parámetros en tiempo real para adaptarse a las condiciones cambiantes de la producción. Esto puede llevar a una reducción significativa en los tiempos de inactividad, aumentando así la eficiencia y reduciendo los costos operativos.
La integración de redes industriales inteligentes, como las que se basan en la tecnología IIoT (Internet Industrial de las Cosas), también está marcando una nueva fase en el desarrollo de estos sistemas. La conectividad de los equipos de soldadura con plataformas de gestión de datos permite a los operarios y responsables de producción tener una visión completa de todos los aspectos del proceso en tiempo real, desde el rendimiento de las máquinas hasta los parámetros de calidad de cada soldadura realizada. Este enfoque mejora el control de la producción y la trazabilidad de los productos, lo que es esencial en industrias donde la calidad y la seguridad son primordiales, como en la fabricación de componentes para la industria nuclear o la aviación.
El entrenamiento de los operarios también está experimentando una transformación significativa gracias al uso de realidad aumentada (AR) y realidad virtual (VR). Estas tecnologías permiten entrenar a los operarios en un entorno virtual, donde pueden aprender a operar los sistemas de soldadura de manera práctica, sin los riesgos asociados con la manipulación de equipos reales. Con la realidad aumentada, los operarios pueden recibir información en tiempo real sobre el proceso de soldadura, como la temperatura del material o la velocidad del cordón, directamente en su campo de visión. Esto no solo mejora la eficacia del entrenamiento, sino que también reduce los errores humanos durante la producción.
Otra tendencia creciente en los sistemas de soldadura para cordón circular es la incorporación de materiales avanzados y aleaciones de alta resistencia. Con la aparición de nuevos materiales con propiedades mejoradas, como el grafeno o las aleaciones ligeras, los equipos de soldadura deben ser capaces de adaptarse a una mayor diversidad de materiales complejos. Los avances en la tecnología de soldadura, como la soldadura por láser de alta potencia o la soldadura por fricción, permiten soldar estos materiales sin comprometer la integridad de las uniones, lo que resulta crucial en aplicaciones de alta ingeniería, como la fabricación de componentes aeroespaciales o automotrices.
El aspecto ecológico también juega un papel cada vez más importante. La sostenibilidad en la fabricación y soldadura se ha convertido en un foco de atención debido a las crecientes regulaciones medioambientales y la presión para reducir la huella de carbono. Los sistemas de soldadura modernos están diseñados para minimizar el consumo de energía, los residuos y los gases contaminantes generados durante el proceso. La mejora en la reciclabilidad de los materiales y el uso de gases inertes más sostenibles son pasos importantes hacia un futuro más verde en la soldadura industrial.
La tendencia hacia la personalización y la fabricación justo a tiempo también está influyendo en el diseño de los equipos de soldadura. Los sistemas modulares que permiten un cambio rápido de configuración y la adaptación a diferentes tamaños de piezas o tipos de soldadura están mejorando la flexibilidad de la producción. Esto es esencial en un mundo industrial cada vez más demandante de productos personalizados, donde los tiempos de entrega rápidos y la capacidad de adaptarse a los cambios de la demanda son factores clave.
Los avances en la inteligencia artificial también están permitiendo que los sistemas de soldadura se vuelvan más autónomos. Los algoritmos de aprendizaje automático pueden analizar grandes volúmenes de datos durante el proceso de soldadura, lo que permite a las máquinas ajustar los parámetros de soldadura automáticamente, optimizando la calidad sin intervención humana. Además, estos sistemas son capaces de realizar análisis predictivos para anticipar cuándo un equipo necesita mantenimiento o si hay algún patrón que sugiera una falla inminente en la soldadura.
En resumen, los sistemas de soldadura para cordón circular están evolucionando hacia una era en la que la automatización, la inteligencia artificial, el análisis de datos y las tecnologías de fabricación avanzada juegan un papel crucial. Estas innovaciones no solo están mejorando la calidad de las soldaduras, sino también la eficiencia y la flexibilidad de los procesos de fabricación. A medida que los avances tecnológicos continúan desarrollándose, se espera que estos sistemas se vuelvan más rápidos, más precisos, más sostenibles y más accesibles para un mayor número de industrias.
Equipos de soldadura de cordón redondo
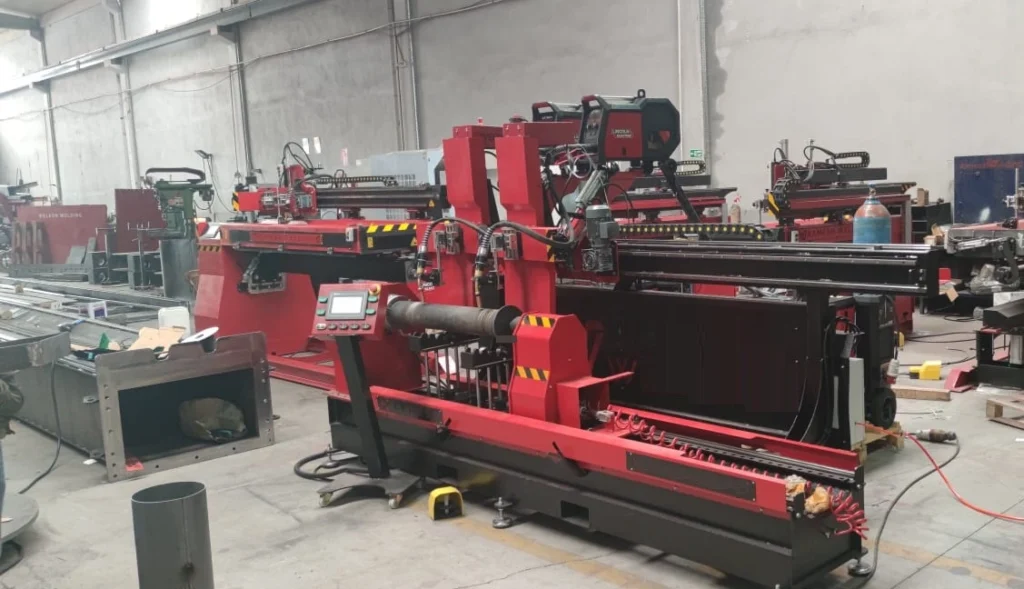
Los equipos de soldadura de cordón redondo están diseñados específicamente para realizar uniones en geometrías circulares, ya sea en tuberías, bridas, tapas de recipientes a presión o componentes cilíndricos en general. Estos equipos cumplen un rol esencial en sectores donde la precisión y la repetibilidad del cordón de soldadura son fundamentales, como la industria petroquímica, alimentaria, farmacéutica, aeronáutica y de generación de energía. Su principal ventaja radica en la capacidad de mantener una trayectoria constante en torno al eje de rotación de la pieza, garantizando uniformidad y control en todo el perímetro de la soldadura.
Muchos de estos equipos están diseñados con sistemas de rotación automatizada, que permiten que la pieza o el cabezal de soldadura gire a una velocidad controlada durante el proceso. Esto es clave cuando se utiliza soldadura TIG, MIG/MAG, plasma o por láser, ya que cualquier variación en la velocidad puede afectar la penetración del cordón y la calidad del acabado superficial. Algunos modelos avanzados integran sensores de posicionamiento y retroalimentación que permiten ajustar el proceso en tiempo real para compensar desviaciones mínimas.
Existen configuraciones tanto horizontales como verticales, dependiendo del tipo de componente a soldar. Por ejemplo, en el caso de soldadura de tapas a cilindros, se suelen usar posicionadores de eje vertical con sujeción neumática o hidráulica, donde el cabezal realiza un movimiento orbital o se mantiene fijo mientras gira la pieza. En aplicaciones más pequeñas o precisas, como la fabricación de sensores o componentes médicos, se emplean sistemas más compactos con motores paso a paso y control numérico.
El nivel de automatización varía dependiendo del modelo y la aplicación. Algunos equipos son semi-automáticos, donde el operario controla ciertos parámetros y posiciona manualmente las piezas, mientras que otros son completamente automáticos o robotizados, programados para ejecutar ciclos de soldadura complejos sin intervención humana directa. En estos últimos, el control del proceso se realiza mediante interfaces gráficas o pantallas táctiles, y es común encontrar sistemas de monitoreo de calidad integrados que verifican cada soldadura mediante visión artificial, termografía o sensores de arco.
Los materiales que pueden ser soldados con estos equipos incluyen aceros al carbono, inoxidables, aleaciones de aluminio, titanio y níquel, siempre que el proceso esté correctamente ajustado. En sectores críticos como el nuclear o el aeroespacial, se requieren altos niveles de repetibilidad, por lo que los equipos deben estar certificados bajo normas estrictas como ASME, AWS o ISO.
En definitiva, los equipos de soldadura de cordón redondo representan una solución técnica avanzada que permite unir componentes circulares con gran precisión, eficiencia y calidad, minimizando errores humanos y aumentando la capacidad productiva de forma significativa. ¿Te gustaría que profundice en algún tipo específico de equipo o aplicación industrial concreta?
Estos equipos se han convertido en una parte indispensable de las líneas de producción modernas que manejan piezas de geometría circular, no solo por su precisión, sino también por su capacidad de integrarse con sistemas de fabricación más amplios. En muchos casos, los equipos de soldadura de cordón redondo no funcionan como unidades aisladas, sino como elementos integrados dentro de celdas robotizadas o estaciones de trabajo automatizadas donde las piezas entran, se posicionan, se sueldan y se inspeccionan sin intervención manual. Este tipo de configuración permite que el flujo de producción sea continuo y eficiente, reduciendo el tiempo de ciclo y mejorando la trazabilidad de cada componente fabricado.
Además de las configuraciones fijas, existen sistemas portátiles que pueden montarse sobre piezas de gran tamaño o que no pueden ser desplazadas fácilmente, como tanques de almacenamiento, tuberías de gran diámetro o estructuras metálicas pesadas. Estos sistemas suelen utilizar cabezales de soldadura motorizados que se mueven sobre raíles circulares o rieles magnéticos, manteniendo la antorcha o el electrodo en posición precisa a lo largo del recorrido del cordón. En muchos casos, están equipados con sistemas de oscilación y ajuste de altura automáticos para compensar las tolerancias del material o las irregularidades superficiales, asegurando una soldadura constante y sin interrupciones.
Otro aspecto relevante es la adaptabilidad de estos equipos a distintas técnicas de soldadura. Aunque los procesos más comunes siguen siendo TIG y MIG/MAG debido a su versatilidad y calidad de acabado, en aplicaciones donde la velocidad es un factor clave, se opta por técnicas como la soldadura por arco sumergido o incluso la soldadura láser. Esta última permite una unión de alta densidad energética con mínima deformación térmica, siendo ideal para materiales sensibles o piezas delgadas. Además, los sistemas híbridos que combinan láser con procesos por arco están comenzando a ganar terreno, ya que aprovechan lo mejor de ambas tecnologías para soldaduras circulares de alta calidad.
La precisión que ofrecen estos equipos no solo depende del sistema de rotación y del cabezal de soldadura, sino también de la forma en que se sujetan y alinean las piezas antes del proceso. Para lograr esto, los equipos están provistos de dispositivos de sujeción altamente ajustables, a menudo diseñados a medida para cada aplicación. Estas mordazas, platos giratorios o sistemas de vacío aseguran que las piezas se mantengan perfectamente alineadas, lo que es fundamental para evitar desviaciones en la raíz del cordón o defectos en la zona de fusión.
El mantenimiento de estos equipos también se ha simplificado gracias a la inclusión de sistemas de diagnóstico predictivo que alertan sobre desgaste en componentes clave como rodillos, motores, fuentes de energía o cables de conexión. Estas funciones permiten programar intervenciones antes de que ocurra una falla, lo que resulta esencial en plantas donde el tiempo de inactividad tiene un alto costo. Asimismo, los fabricantes de equipos han trabajado en el desarrollo de interfaces más intuitivas que permiten a los operarios cambiar parámetros, guardar programas de soldadura o realizar ajustes sin necesidad de formación especializada, lo que mejora la productividad y reduce la dependencia de personal técnico.
En cuanto al entorno de trabajo, estos sistemas pueden adaptarse a condiciones extremas, como temperaturas elevadas, ambientes con alta humedad o exposición a partículas. Para ello, los componentes electrónicos se alojan en carcasas selladas, y se emplean sistemas de refrigeración por aire o líquido para garantizar un funcionamiento estable y prolongado. En muchos casos, los equipos están diseñados para cumplir con normativas internacionales de seguridad eléctrica, electromagnética y de protección contra el polvo o salpicaduras, lo que permite su uso en entornos industriales exigentes sin comprometer su fiabilidad.
La tendencia a digitalizar todo el proceso de soldadura también se refleja en la capacidad de estos equipos para generar informes detallados de cada operación. Estos registros incluyen información sobre voltaje, amperaje, velocidad de soldadura, tipo de gas protector, número de serie del operario y estado del equipo. Esta trazabilidad no solo es útil para auditorías de calidad, sino que también permite realizar análisis retrospectivos para identificar causas de posibles fallas o mejorar los procedimientos. En industrias donde cada unión soldada debe estar documentada, como la fabricación de componentes para aeronaves o centrales nucleares, esta capacidad es absolutamente crucial.
La evolución constante de los equipos de soldadura de cordón redondo no solo responde a los avances tecnológicos, sino también a las exigencias cada vez mayores en cuanto a eficiencia, sostenibilidad y calidad. Las nuevas generaciones de estos equipos están diseñadas no solo para cumplir con los estándares actuales, sino para anticiparse a las necesidades futuras del sector manufacturero. Esto se traduce en una mayor automatización, integración con software de gestión de producción, menor consumo energético, y una interfaz más amigable que facilita su incorporación incluso en entornos de producción que anteriormente dependían de procesos manuales.
Esta evolución hacia sistemas más inteligentes y eficientes también ha impulsado el desarrollo de simuladores y entornos virtuales para la programación y prueba de ciclos de soldadura antes de llevarlos a cabo en la línea real. Utilizando gemelos digitales —réplicas virtuales del proceso físico— los ingenieros pueden predecir con precisión cómo se comportará el cordón de soldadura bajo diferentes parámetros sin desperdiciar material ni tiempo. Estos entornos permiten ajustar variables como el ángulo de la antorcha, la velocidad de rotación, la potencia o la distancia del electrodo, validando el diseño del proceso sin necesidad de producción física inicial. Esta simulación previa también facilita la formación de nuevos operadores y técnicos en condiciones seguras y controladas.
La colaboración entre distintos proveedores de tecnología también ha contribuido a la estandarización de componentes dentro de estos equipos, lo que permite una mayor interoperabilidad entre diferentes sistemas. Por ejemplo, los controladores PLC de marcas reconocidas pueden integrarse con facilidad a plataformas MES o ERP de la planta, permitiendo que los datos del equipo de soldadura se sincronicen con los flujos de producción generales. Esto no solo mejora la trazabilidad y la gestión de recursos, sino que también habilita un mantenimiento más proactivo gracias a la capacidad de analizar tendencias históricas en el comportamiento del equipo.
En contextos donde la repetitividad y la fiabilidad son esenciales, como en la soldadura de anillos para intercambiadores de calor, recipientes de presión o componentes de turbinas, la precisión del cordón circular influye directamente en la seguridad y el rendimiento del producto final. Por esa razón, muchos de estos sistemas incorporan no solo sensores de posición, sino también monitoreo en tiempo real del arco de soldadura, cámaras de inspección óptica y medidores de penetración por ultrasonido que verifican la correcta ejecución de la unión inmediatamente después de cada pasada. De esta forma, los defectos se detectan y corrigen al instante, reduciendo al mínimo el riesgo de reprocesos o rechazo de piezas.
En el campo de la movilidad eléctrica y energías renovables, los equipos de soldadura de cordón redondo también están jugando un papel clave. La fabricación de baterías cilíndricas de litio, por ejemplo, requiere soldaduras precisas en geometría circular para garantizar una conducción eléctrica eficiente y sin defectos. De igual manera, los rotores y estatores de motores eléctricos modernos muchas veces incorporan componentes circulares soldados mediante técnicas láser o TIG, donde la uniformidad del cordón es crítica para mantener el balance y la integridad mecánica de la pieza.
La demanda creciente de producción flexible ha llevado a que estos sistemas también sean compatibles con procesos de cambio rápido de formato. Esto implica que un mismo equipo puede adaptarse en minutos para soldar diferentes tipos de diámetros o geometrías con solo cambiar accesorios o ajustar configuraciones guardadas en el sistema. Esta capacidad reduce drásticamente los tiempos de preparación entre lotes distintos, haciendo posible producir series pequeñas con la misma eficiencia que una línea de producción en masa.
Todo esto hace que los equipos de soldadura de cordón redondo no sean simplemente una herramienta técnica, sino una solución estratégica dentro de las industrias avanzadas. Contribuyen al cumplimiento de normas estrictas, aumentan la competitividad de las empresas al reducir tiempos y costos, y permiten alcanzar niveles de calidad antes impensables en producción a gran escala. Su desarrollo continúa impulsado por la necesidad de mayor automatización, trazabilidad absoluta y adaptación a nuevas demandas tecnológicas. ¿Te interesaría que exploremos ahora alguna aplicación específica o algún componente técnico del sistema más a fondo?
Sistemas de soldadura para cordón circular
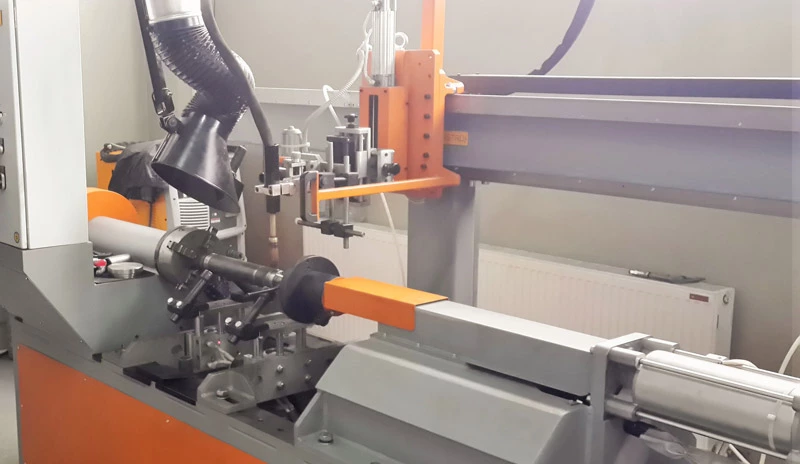
Los sistemas de soldadura para cordón circular representan una solución tecnológica especializada para unir componentes que requieren trayectorias de soldadura en forma de anillo, espiral o circunferencia cerrada. Son esenciales en la fabricación de elementos cilíndricos como tuberías, depósitos, válvulas, rotores, y en general, cualquier componente que involucre una geometría circular. La principal característica de estos sistemas es su capacidad para mantener una velocidad y trayectoria constantes en todo el perímetro de la unión, lo cual garantiza una calidad uniforme del cordón de soldadura, independientemente del diámetro o del tipo de material involucrado.
Estos sistemas pueden estar compuestos por diversos elementos integrados: posicionadores rotativos que giran la pieza o el cabezal de soldadura; mecanismos de avance controlado para la antorcha o el electrodo; y fuentes de energía reguladas digitalmente, capaces de controlar con precisión el arco de soldadura. Dependiendo de la aplicación, se utilizan tecnologías como TIG, MIG/MAG, plasma o incluso láser, cada una con sus propias ventajas en términos de velocidad, penetración, deformación térmica y tipo de material compatible. A menudo, estos sistemas se complementan con controles CNC o software de programación que permiten establecer parámetros exactos para cada tipo de trabajo, almacenar programas, y adaptar los movimientos a tolerancias específicas.
Una de las grandes ventajas de los sistemas de soldadura para cordón circular es su capacidad de integración con procesos automatizados y entornos industriales conectados. Muchos de estos equipos modernos incluyen sensores para el monitoreo de temperatura, voltaje, corriente y posición, así como sistemas de visión artificial para inspección en tiempo real del cordón, lo que permite detectar y corregir defectos inmediatamente. Además, su capacidad para recopilar y registrar datos de cada operación permite asegurar la trazabilidad completa del proceso, una exigencia clave en sectores como la industria aeroespacial, nuclear o alimentaria.
La evolución de estos sistemas ha ido acompañada de mejoras en la ergonomía y seguridad para el operario. Con interfaces gráficas intuitivas, ajustes automáticos y sistemas de protección activa, los riesgos por errores humanos o exposición a condiciones extremas se han reducido significativamente. Asimismo, la compatibilidad con sistemas de realidad aumentada y simulación virtual permite entrenar a los usuarios sin necesidad de intervenir directamente en la producción, aumentando la eficiencia en la capacitación técnica.
En definitiva, los sistemas de soldadura para cordón circular son una solución avanzada que combina precisión, automatización y adaptabilidad para aplicaciones críticas. Su importancia seguirá creciendo a medida que la industria demande más calidad, trazabilidad y eficiencia en procesos de fabricación que involucren geometrías complejas o un alto volumen de producción. ¿Quieres que desarrolle un ejemplo de aplicación específica o un tipo de tecnología dentro de estos sistemas?
Estos sistemas también han sido optimizados para adaptarse a la creciente demanda de flexibilidad en la manufactura moderna. La capacidad de cambiar rápidamente entre diferentes diámetros de piezas o configuraciones de unión permite que una sola estación de soldadura se utilice para múltiples productos sin necesidad de realizar largos tiempos de reconfiguración. Esto se logra mediante componentes modulares y sistemas de sujeción adaptables que pueden ajustarse automáticamente o mediante cambios mínimos de herramientas. En líneas de producción altamente automatizadas, esta versatilidad permite una fabricación bajo demanda mucho más eficiente, con menor desperdicio y mayor personalización, especialmente útil en sectores como el automotriz o la fabricación de equipos médicos donde las especificaciones pueden variar con frecuencia.
Una parte crucial del éxito de los sistemas de soldadura para cordón circular es el control preciso del movimiento. Ya sea que la pieza rote o lo haga el cabezal de soldadura, el sistema debe mantener una velocidad constante y sincronizada con la energía suministrada al arco. Para lograrlo, se utilizan servomotores de alta resolución, controladores digitales en bucle cerrado y sensores de retroalimentación que aseguran que incluso ante variaciones en la resistencia del material o deformaciones térmicas, el cordón mantenga una profundidad y forma constante en todo su recorrido. Esta precisión es especialmente importante cuando se trabaja con materiales sensibles a la temperatura, como aceros inoxidables, aleaciones de aluminio o titanio, donde un leve exceso de energía puede causar defectos estructurales o estéticos.
La integración de tecnologías emergentes como el aprendizaje automático y la inteligencia artificial también está comenzando a formar parte del diseño de estos sistemas. Al recopilar grandes volúmenes de datos sobre los parámetros del proceso, las condiciones ambientales y los resultados de inspección, los algoritmos pueden identificar patrones y realizar ajustes automáticos que mejoren la calidad del cordón o reduzcan el consumo energético. Esto convierte a la soldadura en un proceso no solo automatizado, sino también autoajustable, capaz de mejorar con el tiempo y adaptarse a variaciones en los lotes de materiales o en las condiciones de operación.
En ambientes industriales donde la producción se ejecuta en condiciones difíciles, como en plantas offshore, instalaciones petroquímicas o entornos con presencia de polvo metálico o alta humedad, los sistemas de soldadura para cordón circular se diseñan con protecciones especiales. Sus componentes electrónicos están encapsulados, sus sistemas de refrigeración son reforzados y sus estructuras mecánicas son fabricadas con materiales resistentes a la corrosión o al desgaste abrasivo. Esto no solo asegura una larga vida útil del equipo, sino también una operación confiable en ciclos continuos durante turnos prolongados.
A medida que las exigencias normativas y de calidad aumentan en todos los sectores industriales, estos sistemas se convierten en aliados estratégicos para las empresas que buscan mantener estándares internacionales como ISO 3834, ASME Sección IX o EN 1090. Su capacidad para documentar automáticamente cada unión, registrar parámetros exactos, verificar visual o ultrasónicamente el cordón, y emitir informes automáticos por pieza, los convierte en herramientas fundamentales para el aseguramiento de la calidad. Esto es especialmente relevante cuando el producto final debe ser auditado por terceros o enviado a clientes en sectores altamente regulados, donde cada detalle del proceso debe estar documentado y verificado.
Finalmente, el desarrollo futuro de estos sistemas apunta hacia una mayor conectividad e interoperabilidad. Se están implementando protocolos de comunicación estándar como OPC UA o MQTT que permiten que los equipos de soldadura se comuniquen con plataformas de análisis en la nube, sistemas de gestión de mantenimiento y redes de producción inteligente. Así, los datos generados por cada soldadura no solo quedan disponibles para análisis local, sino que pueden alimentar dashboards remotos, indicadores de eficiencia operativa y sistemas de mantenimiento predictivo basados en inteligencia artificial. Este nivel de integración redefine el papel de la soldadura dentro del ecosistema de la Industria 4.0, transformándola de una operación puntual a un nodo inteligente dentro de una red de fabricación autónoma. ¿Te interesaría que explore alguna marca o modelo específico de estos sistemas, o que te describa un proceso de soldadura paso a paso en una aplicación circular?
Además de su papel técnico, los sistemas de soldadura para cordón circular también están influyendo en el diseño mismo de los productos industriales. La precisión y confiabilidad que ofrecen estos sistemas permiten a los ingenieros diseñar uniones más complejas o más compactas, con menor margen de seguridad en torno al cordón, lo que se traduce en piezas más ligeras, de menor costo o con mejor rendimiento estructural. Por ejemplo, en la industria aeroespacial, el uso de soldadura circular automatizada permite fabricar cámaras de combustión o depósitos de combustible con uniones finas y perfectamente controladas, lo cual sería inviable con técnicas manuales o semi-automatizadas.
Asimismo, en el ámbito energético, estos sistemas tienen un rol fundamental en la fabricación de turbinas, intercambiadores de calor, reactores y otras estructuras críticas. En todos estos casos, la continuidad perfecta del cordón de soldadura es clave para asegurar la estanqueidad, resistencia a presión y durabilidad de las piezas bajo condiciones extremas. Cualquier discontinuidad, por mínima que sea, puede derivar en fallas operativas graves o incluso catástrofes. Por eso, muchas instalaciones cuentan con múltiples estaciones de inspección —algunas integradas al propio sistema de soldadura— que verifican visualmente y mediante ensayos no destructivos la integridad del cordón inmediatamente después del proceso.
En los sectores donde el volumen de producción es alto, como la automoción o la fabricación de electrodomésticos, los sistemas de soldadura circular permiten estandarizar la calidad de los cordones sin depender del operador humano. Esto no solo mejora el producto final, sino que facilita la trazabilidad y la repetibilidad, condiciones esenciales para la producción en serie. Gracias a los avances en robótica colaborativa, incluso es posible integrar brazos robóticos que operan en conjunto con estos sistemas, alimentando piezas, ajustando la posición, limpiando superficies o realizando inspecciones sin detener el ciclo productivo.
Un aspecto clave para maximizar el rendimiento de estos sistemas es la capacitación técnica del personal involucrado. Aunque las interfaces de los equipos son cada vez más amigables y automatizadas, la correcta configuración de parámetros, interpretación de informes de calidad y mantenimiento preventivo aún requiere conocimiento especializado. Por eso, los fabricantes de estos sistemas suelen ofrecer programas de formación continua y soporte técnico remoto, que aseguran que el cliente pueda explotar todo el potencial del equipo desde el primer día.
El diseño modular de los sistemas de soldadura para cordón circular también permite su actualización a lo largo del tiempo. Por ejemplo, un sistema originalmente equipado para soldadura MIG puede ser adaptado posteriormente a procesos láser o híbridos mediante el reemplazo de módulos específicos. De esta forma, el equipo no queda obsoleto frente a nuevos requerimientos, sino que evoluciona con la planta. Esta capacidad de actualización representa una ventaja competitiva frente a soluciones cerradas que no permiten incorporar nuevas tecnologías sin reemplazar todo el sistema.
Incluso en aplicaciones donde las tolerancias no son tan exigentes, como en carpintería metálica o construcción de mobiliario urbano, estos sistemas ofrecen una mejora sustancial en la presentación final del producto. Un cordón circular uniforme y limpio no solo cumple su función estructural, sino que también transmite una imagen de calidad y profesionalismo. Por ello, muchos talleres medianos o pequeños han comenzado a incorporar versiones compactas y económicas de estos sistemas, con resultados muy positivos en términos de eficiencia y acabado.
En síntesis, los sistemas de soldadura para cordón circular representan una confluencia de precisión mecánica, control electrónico, automatización e inteligencia artificial. Son una herramienta esencial no solo para unir materiales, sino para garantizar la repetibilidad, trazabilidad, calidad y competitividad de los procesos industriales modernos. Su impacto no se limita al área técnica, sino que abarca el diseño, la planificación, la logística, la sostenibilidad y la rentabilidad general de la operación industrial. ¿Quieres que ahora pase a mostrarte un ejemplo de cómo se configura o programa uno de estos sistemas en una línea de producción específica?
Máquinas Formadoras de Metales EMS
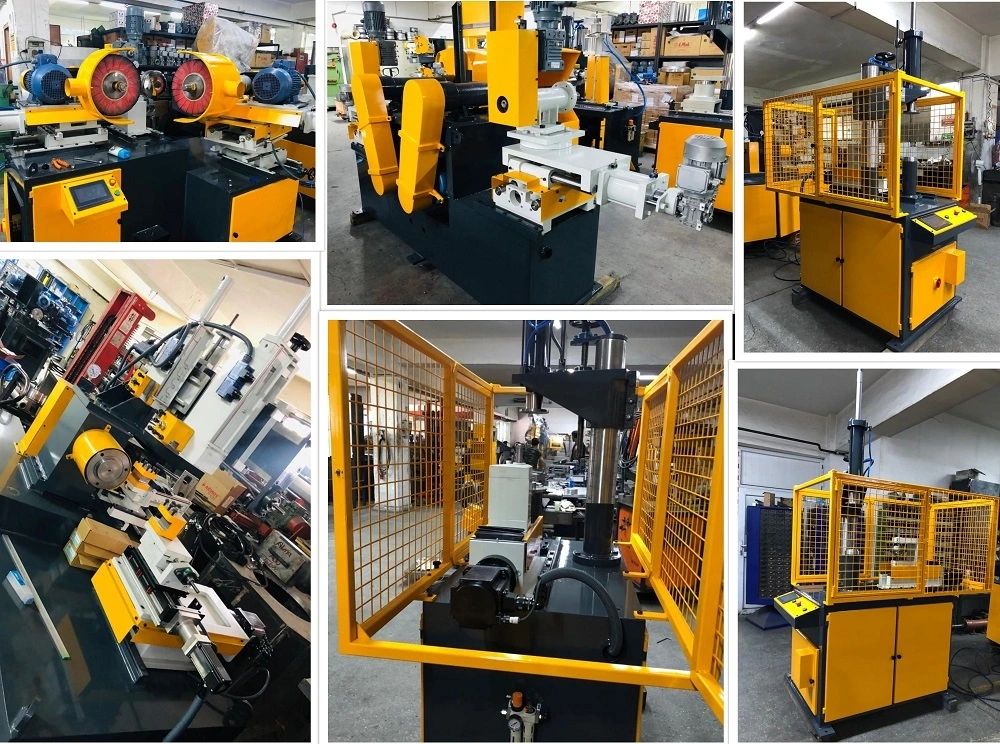
Diseñamos, fabricamos y montamos maquinaria metalmecánica como:
Prensa de transferencia hidráulica
Prensa para mosaicos de vidrio
Prensa hidráulica de embutición profunda
prensa de fundición
Prensa hidráulica de conformado en frío
Prensa de hidroformado
prensa compuesta
Prensa de moldeo de caucho de silicona
Prensa de pastillas de freno
Prensa de melamina
Prensa SMC y BMC
prensa labrotaroy
Máquina cortadora de bordes
Máquina rizadora de bordes
Máquina recortadora de abalorios
Máquina de recorte y jogging
Línea de producción de utensilios de cocina.
Máquina dobladora de tubos
Máquina dobladora de perfiles
Sierra de cinta para metal
Máquina de soldar cilíndrica
Prensas horizontales y utensilios de cocina.
Menaje de cocina, artículos de hotelería
Maquinaria para la producción de utensilios para hornear y cubiertos.
como una línea completa así como una máquina individual como:
Máquinas cortadoras de bordes y biseladoras
Pulidoras y rectificadoras de ollas y sartenes.
Prensas hidráulicas de trefilado
Máquinas troqueladoras circulares
remachadora
Punzonadoras
Máquina de alimentación de prensa
Puede consultar nuestra maquinaria en funcionamiento en: EMS Máquinas Formadoras de Metales EMS – YouTube
Aplicaciones:
Punzonado de bridas
Abalorios y nervaduras
Bridas
Guarnición
Curling
costura de bloqueo
Nervaduras