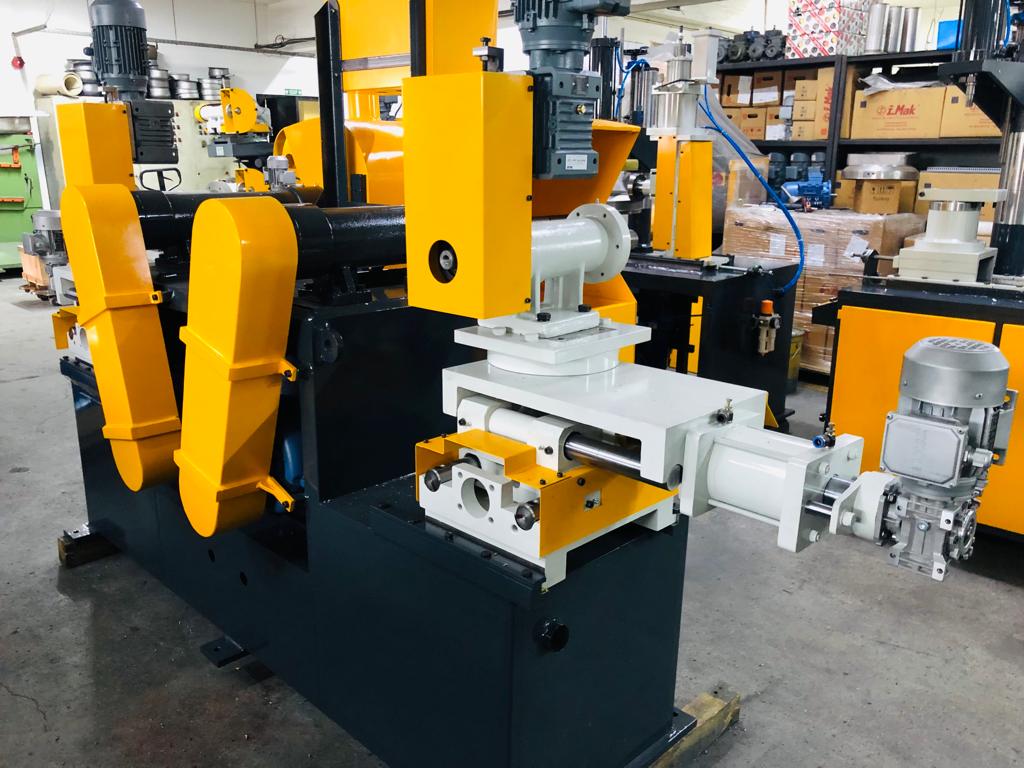
Producción de Máquinas Automáticas para el Pulido: Equipos de pulido automáticos son esenciales en la industria para lograr acabados uniformes, eficientes y repetibles en diversos materiales como metales, plásticos y composites. Estos sistemas automatizados permiten reducir la intervención manual, mejorar la productividad y mantener la calidad constante en grandes volúmenes de producción. Las pulidoras automáticas pueden integrar distintos tipos de movimientos y tecnologías, como el pulido orbital, rotativo, por vibración o mediante robots industriales, adaptándose a las necesidades específicas de cada proceso.
Los sistemas robotizados ofrecen una gran ventaja en términos de flexibilidad y precisión, ya que pueden programarse para manejar piezas con geometrías complejas o para realizar múltiples operaciones de acabado en una sola pasada. Asimismo, las máquinas de pulido por vibración son ideales para el tratamiento de piezas pequeñas en lotes, asegurando un pulido uniforme sin dañar las superficies delicadas. Por otro lado, las pulidoras con control numérico permiten ejecutar procesos de acabado altamente repetitivos con un control exhaustivo de la presión, velocidad y trayectoria del abrasivo, garantizando resultados estéticos y funcionales que cumplen con altos estándares industriales.
El uso de abrasivos adecuados y la selección de parámetros óptimos, como la velocidad del disco, la presión aplicada y el tipo de movimiento, son cruciales para maximizar la vida útil de las herramientas y obtener el mejor acabado posible. Además, la integración de sistemas de extracción de polvo y refrigeración contribuye a mantener las condiciones de trabajo seguras y a prolongar la vida útil de las máquinas. La automatización del pulido contribuye también a la reducción de costos laborales, mejora la seguridad al minimizar la exposición de los operarios a polvo y vibraciones, y optimiza el uso de materiales abrasivos.
Estos equipos pueden adaptarse tanto a líneas de producción en serie como a talleres de fabricación especializados, ofreciendo desde máquinas compactas para pequeños lotes hasta sistemas industriales de gran capacidad. La evolución tecnológica continúa mejorando estos sistemas, incorporando sensores inteligentes para monitorear el proceso en tiempo real y ajustar automáticamente los parámetros para mantener la calidad del acabado, lo que posiciona a los equipos de pulido automáticos como una inversión clave para industrias que buscan eficiencia, calidad y competitividad en sus procesos de acabado.
Además, la integración de tecnologías avanzadas como la inteligencia artificial y el aprendizaje automático en los equipos de pulido automáticos está revolucionando el sector. Estos sistemas pueden analizar datos en tiempo real para detectar variaciones en la superficie de las piezas, ajustar la presión o la velocidad de pulido de manera automática, y predecir el desgaste de las herramientas abrasivas. Esto no solo mejora la calidad del acabado, sino que también reduce tiempos de mantenimiento y minimiza el desperdicio de materiales.
La automatización del pulido también permite una mayor consistencia en los acabados superficiales, un factor crítico en industrias como la automotriz, aeroespacial, electrónica y médica, donde la precisión y la calidad del acabado pueden influir directamente en el rendimiento y la seguridad de los productos finales. Por ejemplo, en la fabricación de componentes metálicos para motores o dispositivos médicos, un pulido homogéneo y libre de imperfecciones es fundamental para evitar fallos prematuros o problemas en el ensamblaje.
Otra ventaja significativa es la capacidad de estos equipos para manejar materiales y acabados diversos, desde el pulido grueso para eliminar irregularidades hasta el pulido fino para obtener superficies espejo. Esto es posible gracias a la versatilidad en la selección de abrasivos, movimientos y sistemas de control, permitiendo adaptarse rápidamente a diferentes requerimientos de producción sin necesidad de cambiar completamente la maquinaria.
En términos de mantenimiento, los equipos automáticos modernos suelen contar con diagnósticos integrados que facilitan la detección temprana de fallos o desgaste, optimizando los planes de mantenimiento preventivo y reduciendo el tiempo de inactividad. Esto es especialmente relevante en plantas industriales con producción continua, donde las paradas no programadas pueden generar pérdidas significativas.
Finalmente, la implementación de equipos de pulido automáticos contribuye a la sostenibilidad del proceso productivo al optimizar el consumo energético, disminuir el uso de abrasivos y facilitar el reciclaje de materiales. Los fabricantes están cada vez más comprometidos con la reducción del impacto ambiental, por lo que la automatización en el pulido es una herramienta valiosa para cumplir con normativas ambientales y mejorar la imagen corporativa ante clientes y consumidores conscientes del cuidado del medio ambiente.
Mesa giratoria indexada
Una mesa giratoria indexada es un dispositivo mecánico diseñado para posicionar piezas o herramientas en una serie de posiciones predefinidas con precisión y repetibilidad. Esta mesa permite que, al girar, se detenga en ángulos exactos o incrementos específicos (por ejemplo, 30°, 45°, 60°), facilitando operaciones secuenciales o multiposicionales en procesos industriales como mecanizado, ensamblaje, inspección o pulido.
La característica principal de una mesa giratoria indexada es su capacidad para “indexar” o detenerse con exactitud en cada posición, gracias a un sistema interno de dientes, clavijas o mecanismos de bloqueo que aseguran la precisión del posicionamiento. Esto es fundamental para operaciones donde la pieza debe ser tratada o trabajada desde distintos ángulos con alta exactitud y rapidez.
Las mesas giratorias indexadas pueden ser manuales, con accionamiento por palanca o manivela, o automáticas, integradas con motores eléctricos, servomotores o sistemas neumáticos, para su uso en líneas de producción automatizadas. También pueden incorporar sistemas de control numérico (CNC) para integrarse en maquinaria avanzada, ofreciendo posicionamientos programables y una mayor flexibilidad.
Estos dispositivos son ampliamente usados en máquinas herramientas como tornos, fresadoras y centros de mecanizado, así como en estaciones de montaje y pulido, permitiendo optimizar tiempos y mejorar la calidad del trabajo al garantizar la repetibilidad y precisión en cada ciclo operativo. Además, su construcción robusta y materiales de alta resistencia aseguran durabilidad y un mantenimiento mínimo en entornos industriales exigentes.
La mesa giratoria indexada mejora significativamente la eficiencia de los procesos industriales al reducir los tiempos de cambio y ajuste manual entre posiciones. Esto se traduce en una mayor productividad y menor margen de error, lo que es especialmente valioso en la fabricación en serie y en operaciones que requieren alta precisión. Su diseño compacto y versátil permite su integración en diferentes tipos de maquinaria y líneas de producción, adaptándose a diversas necesidades productivas.
La precisión en el posicionamiento es uno de los aspectos más críticos de una mesa giratoria indexada. Esto se logra mediante mecanismos internos como engranajes, discos de indexación y clavijas de bloqueo que aseguran que la mesa se detenga exactamente en el ángulo deseado. Algunos modelos avanzados incluyen sensores y sistemas de retroalimentación para verificar la posición y garantizar que el índice se realice correctamente, evitando errores y mejorando la calidad del producto final.
El uso de mesas giratorias indexadas automáticas con motores eléctricos o servomotores permite una programación más flexible, con la capacidad de variar los ángulos y secuencias de trabajo según las necesidades específicas de cada operación. Esta automatización facilita la integración con sistemas de control más complejos, como los sistemas CNC, que pueden gestionar múltiples ejes y movimientos coordinados, aumentando la versatilidad y capacidad de las máquinas.
Además, las mesas giratorias indexadas están diseñadas para soportar cargas variables, desde piezas pequeñas y ligeras hasta componentes pesados y voluminosos. La selección del tamaño, capacidad de carga y tipo de accionamiento debe hacerse en función de la aplicación específica para asegurar el mejor rendimiento y durabilidad. Los materiales utilizados en su fabricación, como aceros tratados o aleaciones especiales, contribuyen a su resistencia al desgaste, rigidez y estabilidad durante el funcionamiento.
El mantenimiento de estas mesas es generalmente sencillo, con componentes accesibles para lubricación y ajustes periódicos que garantizan su precisión y prolongan su vida útil. La implementación de mesas giratorias indexadas en procesos industriales contribuye no solo a mejorar la calidad y precisión de las piezas fabricadas, sino también a optimizar los flujos productivos, reducir costos operativos y aumentar la competitividad de las empresas en sectores industriales diversos.
Además, las mesas giratorias indexadas contribuyen a la seguridad operativa en el entorno industrial, ya que su diseño preciso y robusto evita movimientos imprevistos o desalineaciones durante el proceso. Esto reduce riesgos de daños a las piezas, a la maquinaria y protege al personal que opera o se encuentra cerca del equipo. En aplicaciones donde se manipulan piezas delicadas o de alto valor, contar con un posicionamiento exacto y estable es fundamental para evitar pérdidas económicas y garantizar la integridad del producto.
La adaptabilidad de estas mesas también permite su uso en aplicaciones que requieren múltiples procesos consecutivos, como perforado, fresado, soldadura o inspección visual, donde la pieza debe girarse y posicionarse rápidamente para acceder a diferentes áreas sin necesidad de reubicarla manualmente. Esto facilita la automatización de tareas complejas y contribuye a un flujo de trabajo más continuo y eficiente.
En cuanto a la instalación, las mesas giratorias indexadas pueden ser integradas en sistemas modulares o personalizadas según las dimensiones y características específicas del proceso productivo. Su configuración puede incluir accesorios adicionales como topes, sensores de posición, sistemas de fijación rápida y dispositivos de alimentación para optimizar aún más el rendimiento y la facilidad de uso.
Finalmente, la evolución tecnológica continúa ampliando las capacidades de estas mesas con innovaciones como sistemas de control inteligentes, integración con software de gestión de producción y monitoreo remoto, lo que permite a las empresas modernizar sus operaciones y responder ágilmente a cambios en la demanda o en los requisitos de calidad. Así, las mesas giratorias indexadas no solo son componentes mecánicos, sino también piezas clave dentro de la transformación digital y automatización industrial actual.
Célula robotizada y mesa giratória
Una célula robotizada con mesa giratoria es una solución integrada de automatización industrial que combina un robot programable con una mesa giratoria indexada o rotativa para realizar operaciones complejas y precisas en piezas o componentes. Esta configuración permite que el robot acceda a la pieza desde distintos ángulos sin necesidad de moverla manualmente, optimizando tiempos, mejorando la precisión y aumentando la flexibilidad del proceso productivo.
La mesa giratoria actúa como un dispositivo de posicionamiento que puede rotar la pieza en incrementos definidos o de forma continua, según la programación, mientras que el robot realiza tareas específicas como pulido, soldadura, ensamblaje, inspección, pintura u otras operaciones. La combinación permite secuenciar operaciones en diferentes caras de la pieza sin detener el flujo productivo, maximizando la eficiencia.
Este sistema es muy utilizado en sectores como la automoción, aeroespacial, metalmecánico, electrónico y manufactura avanzada, donde la repetibilidad, la precisión y la velocidad son críticas. Además, la integración de sensores y sistemas de visión dentro de la célula robotizada facilita la detección de posiciones exactas, la corrección automática y el control de calidad en tiempo real, asegurando resultados uniformes y altos estándares.
La programación de la célula robotizada con mesa giratoria puede ser gestionada mediante controladores CNC o software especializado que coordina tanto el movimiento rotacional como las acciones del robot, permitiendo configurar ciclos adaptados a diferentes tipos de piezas y procesos. Esto brinda gran flexibilidad para líneas de producción que manejan variedad de productos o requieren cambios frecuentes.
La instalación de una célula robotizada con mesa giratoria también aporta beneficios en términos de seguridad, al reducir la intervención humana directa en tareas repetitivas o peligrosas, y en sostenibilidad, al optimizar recursos y minimizar errores y desperdicios. Por su parte, el mantenimiento de estos sistemas suele ser modular, facilitando la sustitución o actualización de componentes sin afectar toda la línea productiva.
En resumen, la combinación de una mesa giratoria con una célula robotizada representa una solución avanzada que potencia la automatización industrial, mejora la calidad, acelera la producción y contribuye a la competitividad en mercados exigentes.
La célula robotizada con mesa giratoria facilita la realización de procesos complejos que requieren accesos múltiples a la pieza, permitiendo que el robot mantenga una posición fija mientras la mesa rota la pieza al ángulo deseado. Esto elimina la necesidad de múltiples manipulaciones manuales o reubicaciones, lo que reduce significativamente los tiempos de ciclo y aumenta la eficiencia general del sistema. La capacidad de trabajar en diferentes caras o lados de la pieza en una sola configuración hace que este tipo de células sea ideal para operaciones de acabado, ensamblaje o inspección que requieren precisión y repetibilidad.
Además, la integración de tecnologías de control avanzado permite sincronizar con precisión los movimientos del robot y la rotación de la mesa, optimizando cada etapa del proceso y asegurando que las transiciones sean suaves y sin interrupciones. Esto es crucial para mantener la calidad y evitar daños tanto en las piezas como en las herramientas del robot. La coordinación entre ambos elementos también facilita la programación de ciclos personalizados, adaptándose a diferentes productos sin necesidad de modificar la estructura física del sistema.
Estos sistemas suelen incorporar dispositivos de seguridad y sensores que supervisan la posición de la mesa y del robot, deteniendo automáticamente la operación ante cualquier anomalía para proteger el equipo y al personal. Esta capacidad de respuesta contribuye a crear un entorno de trabajo más seguro y confiable, imprescindible en instalaciones industriales modernas. Asimismo, la automatización reduce la exposición de los operarios a tareas repetitivas o potencialmente peligrosas, mejorando las condiciones laborales y minimizando riesgos.
La flexibilidad que ofrece la célula robotizada con mesa giratoria también permite una fácil adaptación a nuevas líneas de producción o cambios en los diseños de los productos, ya que la programación puede ajustarse sin necesidad de grandes inversiones en hardware. Esta característica es especialmente valiosa en mercados dinámicos donde la personalización y rapidez en el cambio de producción son competitivas. Asimismo, la modularidad del sistema facilita el mantenimiento y las actualizaciones tecnológicas, extendiendo su vida útil y optimizando la inversión realizada.
En términos de aplicación, estas células son usadas en la fabricación de componentes automotrices para pulido y ensamblaje, en la industria aeroespacial para procesos de acabado y verificación, en la electrónica para manipulación precisa de piezas pequeñas y en la producción de bienes de consumo donde la calidad y velocidad son esenciales. La combinación de una mesa giratoria con un robot industrial representa una de las soluciones más efectivas para integrar automatización avanzada en procesos que demandan precisión, versatilidad y eficiencia.
Además, la incorporación de sistemas de visión artificial dentro de la célula robotizada con mesa giratoria permite un nivel superior de control y adaptabilidad en el proceso. Las cámaras y sensores instalados pueden inspeccionar las piezas en tiempo real, detectar imperfecciones, medir dimensiones y guiar al robot para realizar ajustes automáticos en la trayectoria o presión aplicada durante el pulido, soldadura u otra operación. Esto mejora significativamente la calidad del producto final y reduce la necesidad de inspección manual posterior, acelerando el ciclo de producción.
Otro aspecto importante es la reducción de los costos operativos y de mano de obra. Al automatizar tareas repetitivas y complejas con alta precisión, las empresas pueden disminuir la dependencia de operadores altamente especializados para estas operaciones, reduciendo errores humanos y aumentando la consistencia. Además, la célula robotizada con mesa giratoria puede operar de manera continua o en turnos extendidos, incrementando la capacidad productiva sin requerir una expansión proporcional en recursos humanos.
El diseño compacto y modular de estas células facilita su integración en líneas de producción existentes sin necesidad de grandes modificaciones estructurales. Esto permite que las fábricas modernicen sus procesos de manera escalonada y rentable, mejorando progresivamente la automatización y adaptándose a las demandas del mercado. La posibilidad de programar diferentes secuencias y adaptarlas a distintos productos añade un valor extra, ya que la misma célula puede servir para múltiples aplicaciones y lotes variados.
Finalmente, la constante evolución tecnológica abre la puerta a incorporar mejoras continuas en estas células, como inteligencia artificial para optimización automática, mantenimiento predictivo basado en datos recogidos por sensores, y conectividad para integración en redes de producción inteligentes o Industria 4.0. De esta manera, la célula robotizada con mesa giratoria no solo cumple una función operativa sino que se convierte en un elemento clave dentro de la digitalización y transformación de las plantas industriales hacia procesos más eficientes, flexibles y sostenibles.
Mesa giratoria indexada
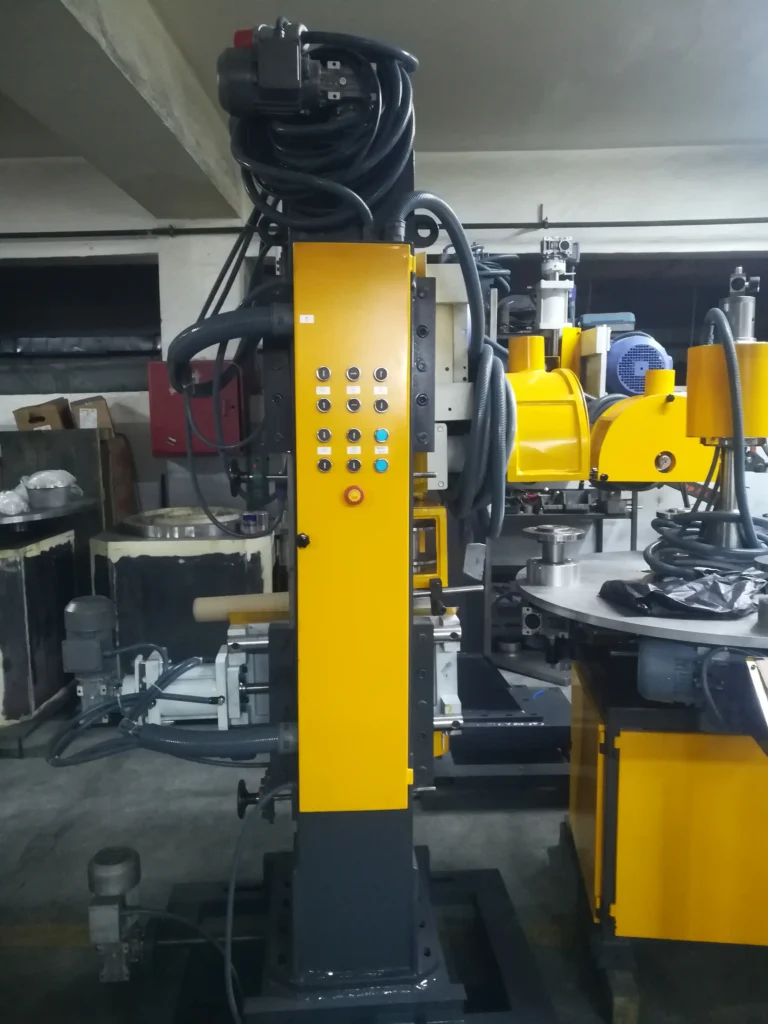
Una mesa giratoria indexada es un dispositivo mecánico diseñado para posicionar piezas o herramientas en ángulos específicos y repetibles durante procesos industriales. Su función principal es permitir que una pieza se detenga con precisión en posiciones predefinidas, facilitando operaciones como mecanizado, ensamblaje, inspección o pulido en diferentes caras o áreas sin necesidad de manipulación manual constante.
Estas mesas cuentan con mecanismos internos, como discos de indexación, engranajes, o clavijas de bloqueo, que aseguran que la rotación se detenga exactamente en los puntos deseados. Esto garantiza una alta precisión y repetibilidad, elementos clave para mantener la calidad en producciones en serie o en trabajos que requieren ajustes exactos.
Las mesas giratorias indexadas pueden ser operadas manualmente o integrarse con sistemas automáticos mediante motores eléctricos, servomotores o sistemas neumáticos, permitiendo su uso en líneas de producción automatizadas. Su tamaño, capacidad de carga y tipo de accionamiento varían según la aplicación y la industria, adaptándose desde piezas pequeñas hasta componentes pesados.
Además de mejorar la eficiencia y la calidad del proceso, estas mesas facilitan la reducción de tiempos muertos y errores, incrementando la productividad y la seguridad en el entorno industrial. Son ampliamente utilizadas en maquinaria herramienta, estaciones de montaje y líneas de acabado, constituyendo un elemento fundamental para la optimización de procesos que requieren posicionamientos precisos y repetitivos.
La mesa giratoria indexada optimiza significativamente los procesos industriales al permitir una rotación controlada y precisa que facilita la ejecución de operaciones secuenciales sin necesidad de reposicionar manualmente las piezas. Esto reduce considerablemente los tiempos de ciclo y minimiza los errores de posicionamiento, lo que es fundamental para mantener la calidad y la consistencia en la producción en serie. Su diseño compacto y versátil permite su integración en una amplia variedad de máquinas y líneas productivas, adaptándose a diferentes requerimientos de espacio y capacidad de carga.
La precisión en el posicionamiento se logra mediante sistemas mecánicos robustos, como discos dentados o clavijas de bloqueo, que aseguran que la mesa se detenga exactamente en los ángulos preestablecidos. Algunos modelos incluyen sensores o sistemas electrónicos que verifican la posición, proporcionando retroalimentación al controlador para garantizar la exactitud y prevenir desviaciones. Esta combinación de mecanismos mecánicos y electrónicos eleva el nivel de confiabilidad del equipo en aplicaciones críticas.
El uso de mesas giratorias indexadas automáticas, controladas por servomotores o motores paso a paso, permite programar secuencias de rotación específicas que se adaptan a diferentes tipos de piezas y procesos, aumentando la flexibilidad de la producción. Esta automatización facilita también la integración con sistemas de control numérico (CNC) o software de gestión de producción, lo que contribuye a una mayor eficiencia operativa y a la reducción de tiempos muertos.
Además, estas mesas están diseñadas para soportar cargas que varían desde piezas pequeñas y ligeras hasta componentes pesados y voluminosos, dependiendo de las necesidades de la aplicación. La selección adecuada del tamaño, capacidad y tipo de accionamiento es clave para garantizar un rendimiento óptimo y la durabilidad del equipo, especialmente en entornos industriales exigentes donde la rigidez y resistencia al desgaste son prioritarias.
El mantenimiento de las mesas giratorias indexadas suele ser sencillo, con acceso fácil a los componentes para lubricación y ajustes periódicos que aseguran la precisión y prolongan la vida útil del dispositivo. Su implementación contribuye a mejorar la seguridad operativa, ya que reduce la necesidad de manipulaciones manuales repetitivas y minimiza el riesgo de errores humanos o accidentes durante el posicionamiento de las piezas.
En resumen, la mesa giratoria indexada es un componente fundamental en la automatización y optimización de procesos industriales, aportando precisión, repetibilidad, flexibilidad y eficiencia. Su capacidad para posicionar piezas con exactitud en múltiples ángulos facilita una amplia gama de operaciones, desde el mecanizado hasta el ensamblaje y el acabado, convirtiéndola en una herramienta indispensable para mejorar la productividad y la calidad en diferentes sectores manufactureros.
Además, la mesa giratoria indexada contribuye a la mejora continua de los procesos productivos al permitir una fácil adaptación a cambios en las líneas de fabricación. Gracias a su capacidad para posicionar piezas en diferentes ángulos de manera rápida y precisa, es posible implementar operaciones más complejas o variar las secuencias de trabajo sin necesidad de realizar modificaciones estructurales en la maquinaria. Esta flexibilidad resulta especialmente valiosa en industrias donde se manejan lotes pequeños o productos personalizados, donde la agilidad y capacidad de respuesta son clave para mantener la competitividad.
Otro beneficio importante es la reducción del desgaste y prolongación de la vida útil tanto de la mesa como de las herramientas asociadas. Al asegurar un posicionamiento exacto y estable, se minimizan las vibraciones y movimientos inesperados que pueden causar daños o deterioro prematuro. Esto se traduce en menores costos de mantenimiento y una mayor disponibilidad operativa de las líneas de producción, lo que impacta positivamente en la rentabilidad de las operaciones.
La integración de mesas giratorias indexadas con tecnologías digitales y sistemas de monitoreo permite implementar mantenimiento predictivo, anticipándose a posibles fallos y optimizando los tiempos de intervención. Los datos recogidos sobre el uso, la posición y el rendimiento del equipo facilitan la toma de decisiones informadas para mejorar la eficiencia y evitar paradas no planificadas. Esta conectividad también contribuye a la incorporación de la mesa dentro de entornos industriales inteligentes o Industria 4.0, donde la interoperabilidad y automatización avanzada son la norma.
Por último, la mesa giratoria indexada tiene un impacto positivo en la ergonomía y seguridad del trabajo al reducir la necesidad de manipulación manual frecuente o forzada de piezas, disminuyendo el riesgo de lesiones laborales y facilitando un entorno de trabajo más saludable. Su uso contribuye a automatizar tareas repetitivas o físicamente exigentes, liberando al personal para concentrarse en actividades de mayor valor añadido, lo que también puede mejorar la satisfacción y motivación de los trabajadores.
En definitiva, la mesa giratoria indexada es una solución clave para optimizar procesos industriales, que aporta precisión, flexibilidad, durabilidad y seguridad, ayudando a las empresas a mejorar su competitividad y adaptarse a las demandas cambiantes del mercado.
Célula robotizada IR
Una célula robotizada IR (Infrared, infrarroja) es un sistema automatizado que integra un robot industrial con tecnología de sensores o cámaras infrarrojas para llevar a cabo tareas de fabricación, inspección o control de calidad con alta precisión y eficiencia. Este tipo de célula utiliza la detección infrarroja para monitorear temperaturas, detectar presencia, medir distancias o identificar características específicas de las piezas durante el proceso, lo que permite mejorar la exactitud y la fiabilidad de las operaciones.
La incorporación de sensores IR en una célula robotizada facilita, por ejemplo, el control térmico en procesos como soldadura, pulido o tratamiento superficial, donde la temperatura es un parámetro crítico para la calidad del producto. También puede utilizarse para la inspección no destructiva, detectando defectos o inconsistencias que no son visibles al ojo humano o con métodos ópticos tradicionales.
Estas células suelen estar programadas para que el robot realice movimientos precisos coordinados con la información recibida de los sensores IR, ajustando su actuación en tiempo real. Esto permite una respuesta dinámica a las condiciones del proceso, optimizando los resultados y minimizando el desperdicio o los retrabajos.
Los sistemas IR son especialmente valiosos en industrias donde el control térmico o la detección de materiales son esenciales, como la automotriz, aeroespacial, electrónica o la manufactura de plásticos y composites. Además, la tecnología infrarroja mejora la seguridad al permitir monitoreo sin contacto directo, reduciendo riesgos para el personal y los equipos.
La célula robotizada IR puede integrarse con otros sistemas de control y monitoreo para formar parte de líneas de producción inteligentes, aportando datos en tiempo real que facilitan la supervisión, análisis y mejora continua de los procesos industriales. En conjunto, esta tecnología representa un avance significativo en la automatización avanzada, combinando precisión robótica con capacidades sensoriales especializadas para procesos complejos y exigentes.
La célula robotizada IR permite una automatización más inteligente y adaptable, ya que los sensores infrarrojos proporcionan información continua sobre las condiciones del proceso sin necesidad de contacto físico, lo que evita interferencias o daños en las piezas y equipos. Esta capacidad es especialmente útil en aplicaciones donde las superficies pueden estar calientes, en movimiento o difíciles de alcanzar, facilitando inspecciones rápidas y precisas que antes requerían intervención manual o equipos adicionales.
Además, la integración de tecnología infrarroja con el robot industrial mejora la capacidad de realizar ajustes en tiempo real durante la producción. Por ejemplo, si un sensor detecta que una pieza está fuera del rango térmico ideal, el robot puede modificar la velocidad, presión o trayectoria para corregir el proceso automáticamente, asegurando así la calidad y minimizando el riesgo de defectos. Esto incrementa la eficiencia y reduce desperdicios, contribuyendo a procesos más sostenibles y económicos.
Estos sistemas también pueden usarse para la clasificación o separación de materiales basándose en características térmicas, lo que añade una capa extra de control y versatilidad a la línea de producción. En combinación con otros sensores y sistemas de visión, la célula robotizada IR puede ofrecer un análisis completo y multidimensional de las piezas, ampliando las posibilidades de automatización en sectores con altos estándares de calidad.
La implementación de células robotizadas con sensores infrarrojos contribuye a mejorar la seguridad en la planta, al reducir la necesidad de que los operadores estén expuestos a ambientes calientes, radiación o zonas de difícil acceso. Asimismo, permite operar en condiciones donde la iluminación o visibilidad convencional es limitada, gracias a la capacidad de los sensores IR para funcionar en diferentes rangos espectrales y bajo diversas condiciones ambientales.
Finalmente, estas células forman parte de la tendencia hacia la digitalización y la Industria 4.0, ya que los datos generados por los sensores infrarrojos pueden integrarse en sistemas de análisis y control avanzados, facilitando el mantenimiento predictivo, la optimización de procesos y la toma de decisiones basada en datos en tiempo real. Esto posiciona a la célula robotizada IR como una herramienta clave para empresas que buscan mejorar su competitividad mediante la innovación tecnológica y la automatización inteligente.
Además, la célula robotizada IR contribuye a la reducción de costos operativos y mejora la eficiencia energética. Al monitorear continuamente las condiciones térmicas y ajustar automáticamente los parámetros del proceso, se evita el sobrecalentamiento o el uso excesivo de energía, optimizando el consumo y prolongando la vida útil de las herramientas y equipos. Esto representa un ahorro significativo, especialmente en procesos industriales de alta demanda energética.
La versatilidad de estas células también se manifiesta en su capacidad para integrarse con diferentes tipos de robots, desde brazos articulados hasta robots colaborativos (cobots), adaptándose a las necesidades específicas de cada aplicación y espacio disponible. Los cobots, en particular, permiten una interacción segura y directa con los operarios, ampliando el rango de tareas que pueden automatizarse sin comprometer la seguridad.
La programación avanzada y el uso de inteligencia artificial en combinación con sensores IR potencian aún más las capacidades de estas células. Los algoritmos pueden aprender y predecir comportamientos del proceso, anticipando posibles fallas o desviaciones y ajustando las operaciones para mantener la calidad y productividad. Esto reduce el tiempo de inactividad y mejora la consistencia del producto final.
El desarrollo continuo de sensores infrarrojos más precisos y compactos también impulsa la miniaturización y mejora en la integración de estas tecnologías, facilitando su adopción en sectores como la microelectrónica o la fabricación de dispositivos médicos, donde las tolerancias son extremadamente estrictas y la detección térmica es crucial.
En definitiva, la célula robotizada IR representa una evolución significativa en la automatización industrial, combinando la precisión y repetibilidad del robot con la capacidad sensorial avanzada de la tecnología infrarroja. Esto permite a las empresas alcanzar mayores niveles de calidad, eficiencia y seguridad, al tiempo que se preparan para los retos y demandas de la industria moderna y conectada.
Mesa giratoria indexada con unidad de pulido CPL
Una mesa giratoria indexada con unidad de pulido CPL es un sistema automatizado que combina la precisión en el posicionamiento rotativo de piezas con un proceso integrado de pulido, optimizando así las operaciones de acabado superficial en ambientes industriales. La mesa giratoria indexada permite situar la pieza en ángulos específicos y repetibles para que la unidad de pulido CPL (Control de Pulido Láser o Control de Pulido por Láser, dependiendo del contexto) pueda trabajar con exactitud en cada cara o sección requerida sin necesidad de manipulación manual.
Este sistema mejora significativamente la eficiencia y calidad del pulido al garantizar que la pieza se mantenga estable y correctamente orientada durante todo el proceso. La unidad de pulido CPL, equipada con tecnología avanzada de control y herramientas de alta precisión, asegura un acabado homogéneo y uniforme, reduciendo defectos y variaciones superficiales que pueden afectar la funcionalidad o estética del producto.
La integración de la mesa giratoria indexada con la unidad de pulido CPL permite automatizar ciclos completos de trabajo donde, tras cada posición indexada, el sistema realiza el pulido correspondiente antes de pasar a la siguiente, incrementando la velocidad y repetibilidad del proceso. Esta coordinación entre posicionamiento y pulido minimiza tiempos muertos y maximiza la productividad, especialmente en series de producción medianas y grandes.
Además, estos sistemas suelen incluir controles inteligentes que monitorean parámetros clave como presión, velocidad y temperatura durante el pulido, ajustándolos en tiempo real para optimizar el desempeño y evitar daños en la pieza o en la herramienta. Esto no solo mejora la calidad final sino que también prolonga la vida útil de los consumibles y equipos, reduciendo costos operativos.
La mesa giratoria indexada con unidad de pulido CPL es especialmente útil en industrias donde los acabados superficiales son críticos, como la automotriz, aeroespacial, electrónica, y fabricación de componentes metálicos o plásticos de alta precisión. Su capacidad para ofrecer acabados consistentes y de alta calidad contribuye a mejorar la funcionalidad, durabilidad y apariencia de los productos finales.
Por último, este tipo de sistema puede integrarse fácilmente en líneas de producción automatizadas o células robotizadas, adaptándose a diferentes configuraciones y requerimientos productivos. Esto aporta flexibilidad y escalabilidad a las plantas industriales, facilitando la modernización y optimización continua de sus procesos de acabado.
La combinación de la mesa giratoria indexada con la unidad de pulido CPL representa una solución integral para optimizar los procesos de acabado en entornos industriales, al permitir un control preciso y repetible tanto en el posicionamiento como en la aplicación del pulido. Esta integración elimina la necesidad de reposicionar manualmente las piezas entre cada etapa, reduciendo así tiempos de ciclo y la posibilidad de errores o daños por manipulación.
El sistema está diseñado para manejar diferentes tipos y tamaños de piezas, adaptándose a variadas geometrías gracias a la flexibilidad que ofrece la indexación en múltiples posiciones. Esto facilita la ejecución de procesos complejos de pulido en varias caras o superficies con un alto grado de precisión y uniformidad, lo que es esencial para cumplir con estrictos estándares de calidad.
La unidad de pulido CPL incorpora tecnologías avanzadas que permiten controlar parámetros como la velocidad de rotación, presión aplicada y trayectoria de la herramienta de pulido, ajustándose automáticamente según las características de cada pieza y el resultado deseado. Esta capacidad de adaptación mejora la consistencia del acabado y reduce el desgaste tanto de las herramientas como de las piezas.
Además, la mesa giratoria indexada con unidad de pulido CPL puede integrarse con sistemas de control y monitoreo digital que registran datos en tiempo real, facilitando el análisis y la optimización continua del proceso. Esta conectividad contribuye a la implementación de estrategias de mantenimiento predictivo y a la toma de decisiones basada en datos, aumentando la eficiencia operativa y reduciendo tiempos de inactividad.
La automatización que ofrece este sistema también mejora la seguridad en el entorno de trabajo al minimizar la intervención manual en tareas repetitivas o potencialmente riesgosas, permitiendo que los operadores se enfoquen en actividades de supervisión y control de calidad. Esto contribuye a un ambiente laboral más seguro y productivo.
En resumen, la mesa giratoria indexada con unidad de pulido CPL es una herramienta clave para la modernización de procesos de acabado industrial, combinando precisión, eficiencia, flexibilidad y seguridad. Su implementación permite a las empresas mejorar la calidad de sus productos, optimizar recursos y adaptarse rápidamente a las demandas cambiantes del mercado, consolidándose como una solución tecnológica avanzada para la fabricación moderna.
Además, la mesa giratoria indexada con unidad de pulido CPL favorece la estandarización de los procesos de acabado, lo cual es fundamental para mantener la uniformidad en grandes volúmenes de producción. Al automatizar el posicionamiento y la aplicación del pulido, se minimizan las variaciones entre piezas, garantizando que cada producto cumpla con las especificaciones técnicas y estéticas requeridas. Esto es especialmente crítico en sectores donde la calidad del acabado influye directamente en el rendimiento o la seguridad del producto final.
La modularidad de estos sistemas facilita su personalización y escalabilidad. Dependiendo de las necesidades específicas de producción, se pueden añadir o quitar módulos de pulido, ajustar la capacidad de carga de la mesa o integrar sistemas adicionales como estaciones de inspección automática o robots para la carga y descarga de piezas. Esta flexibilidad permite a las empresas adaptar rápidamente su equipamiento a cambios en la demanda o en el diseño de los productos, optimizando la inversión en tecnología.
La implementación de tecnologías complementarias, como sensores de fuerza y vibración, mejora aún más el control del proceso. Estos sensores permiten detectar condiciones anómalas durante el pulido, como un desgaste excesivo de la herramienta o irregularidades en la superficie, lo que posibilita intervenciones tempranas para corregir el proceso y evitar defectos o daños costosos.
Desde el punto de vista ambiental, la automatización y optimización que ofrece este sistema contribuye a una reducción del consumo de recursos como abrasivos, agua o energía, así como a una disminución de los residuos generados. Esto apoya las políticas de sostenibilidad y responsabilidad social corporativa que muchas industrias están adoptando actualmente.
Finalmente, la capacitación y formación del personal en el manejo y mantenimiento de la mesa giratoria indexada con unidad de pulido CPL es un aspecto clave para maximizar los beneficios de la tecnología. Contar con operadores y técnicos capacitados asegura un uso eficiente, un mantenimiento adecuado y una rápida resolución de posibles incidencias, garantizando la continuidad y calidad del proceso productivo.
En conjunto, este sistema representa una solución avanzada que combina precisión mecánica, tecnología de control y flexibilidad operativa para elevar los estándares de acabado industrial y apoyar la competitividad en mercados exigentes y en constante evolución.
Mesas giratorias indexadas
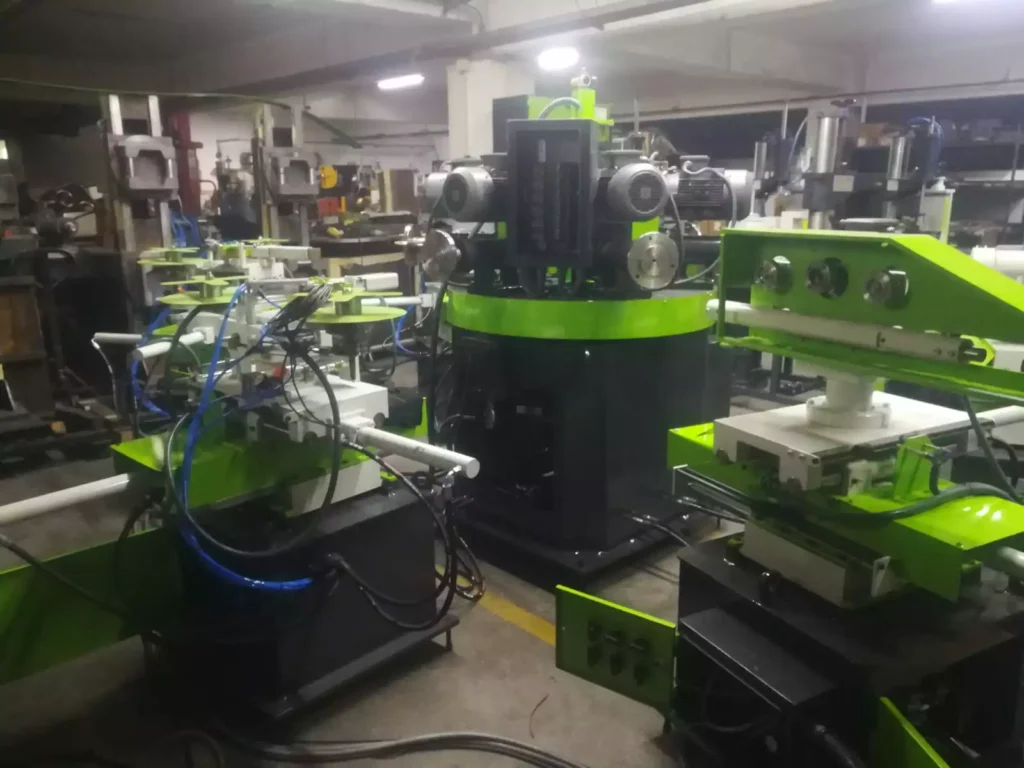
Las mesas giratorias indexadas son dispositivos mecánicos diseñados para posicionar piezas o herramientas en ángulos específicos y repetibles durante procesos industriales. Su función principal es facilitar la rotación controlada de un objeto para que pueda ser trabajado, inspeccionado o ensamblado en distintas posiciones con alta precisión, lo que mejora la eficiencia y calidad en la producción.
Estas mesas cuentan con mecanismos de bloqueo o engranajes que aseguran que la mesa se detenga exactamente en los puntos predefinidos, conocidos como índices. Este posicionamiento exacto permite realizar operaciones secuenciales sin la necesidad de reajustar manualmente la pieza, reduciendo tiempos muertos y errores humanos.
Existen diversos tipos de mesas giratorias indexadas, que varían en capacidad de carga, tamaño, número de posiciones y tipo de accionamiento (manual, neumático, hidráulico o motorizado). La elección depende de la aplicación específica y las necesidades del proceso productivo. Por ejemplo, mesas de alta capacidad se usan para piezas grandes y pesadas, mientras que mesas más compactas son ideales para componentes pequeños en procesos de ensamblaje o pulido.
La precisión y rigidez son características fundamentales de estas mesas, ya que garantizan la repetibilidad y estabilidad durante el trabajo. Muchas mesas giratorias indexadas incluyen sensores o sistemas electrónicos que verifican la posición, aumentando la confiabilidad y permitiendo la integración con sistemas automatizados o control numérico (CNC).
Su uso es común en industrias como la automotriz, metalúrgica, electrónica, y fabricación de maquinaria, donde se requieren procesos con alta repetibilidad y calidad constante. La implementación de mesas giratorias indexadas contribuye a optimizar los flujos de trabajo, mejorar la ergonomía al reducir manipulaciones manuales y aumentar la productividad general.
En definitiva, las mesas giratorias indexadas son componentes esenciales para la automatización y eficiencia en procesos industriales, aportando precisión, flexibilidad y rapidez en el posicionamiento de piezas para múltiples operaciones.
Además, las mesas giratorias indexadas pueden funcionar como núcleo de células automatizadas, ya que permiten coordinar múltiples estaciones de trabajo alrededor de un punto central. Por ejemplo, en una línea de producción donde se realizan operaciones de soldadura, taladrado, pulido o inspección, la mesa gira la pieza de manera controlada a cada estación sin necesidad de que esta sea desmontada o trasladada manualmente, lo que reduce significativamente el tiempo de manipulación y mejora la continuidad del proceso.
Su diseño puede incorporar múltiples puntos de indexado, desde tan solo dos hasta decenas de posiciones, dependiendo de la complejidad del ciclo requerido. Algunas versiones de alta precisión incluso permiten indexado angular variable, útil para piezas que requieren operaciones en ángulos no regulares. También existen modelos con husillos o platos rotativos de precisión extrema para tareas como mecanizado de precisión o ensamblajes electrónicos delicados.
Estas mesas suelen estar construidas con materiales de alta resistencia, como aceros endurecidos o aleaciones especiales, para soportar cargas dinámicas y prolongar la vida útil del mecanismo. Los rodamientos de alta calidad, los frenos de retención y los sistemas de lubricación automática aseguran una operación suave y confiable incluso en condiciones de trabajo intensivas.
En aplicaciones robóticas, las mesas giratorias indexadas se sincronizan perfectamente con los movimientos del robot, ya sea para alimentar piezas, orientarlas para su manipulación o posicionarlas para operaciones repetitivas. Esta interacción entre robot y mesa giratoria aumenta el grado de automatización y permite ciclos cerrados donde varias piezas se procesan en paralelo, optimizando el rendimiento global de la línea.
Su mantenimiento es generalmente sencillo y los sistemas modernos incorporan monitoreo del desgaste de los componentes, lo que permite programar mantenimientos preventivos sin interrumpir el flujo de producción. Este enfoque mejora la disponibilidad del sistema y reduce los costes asociados a fallos inesperados.
El uso de mesas giratorias indexadas también aporta beneficios en términos de seguridad. Al reducir la necesidad de intervención manual en procesos de rotación o posicionamiento, disminuye el riesgo de accidentes laborales. Además, las versiones automatizadas pueden programarse para detenerse de inmediato ante cualquier anomalía, lo que refuerza las condiciones seguras de operación.
En resumen, las mesas giratorias indexadas representan una solución técnica robusta, flexible y eficiente para mejorar el control y la automatización de procesos industriales. Su capacidad para ofrecer posicionamiento preciso, repetible y confiable las convierte en un elemento indispensable en líneas de producción modernas donde se requiere velocidad, calidad y confiabilidad constantes.
Las mesas giratorias indexadas también se destacan por su capacidad de integración con tecnologías avanzadas como sensores inteligentes, sistemas de visión artificial y controladores programables. Estas integraciones permiten que la mesa no solo realice movimientos mecánicos, sino que también tome decisiones en función de las condiciones del proceso. Por ejemplo, un sistema de visión puede verificar si una pieza está correctamente posicionada o si presenta defectos, y luego enviar una señal a la mesa para avanzar, detenerse o rechazar la pieza de forma automática.
En entornos donde se manejan diferentes tipos de productos o variantes de una misma pieza, algunas mesas giratorias indexadas ofrecen configuraciones reprogramables o servocontroladas, donde el ángulo de giro y el número de estaciones pueden ajustarse dinámicamente mediante software. Esta característica es especialmente útil en líneas de producción flexibles o en sistemas de fabricación celular que deben adaptarse rápidamente a cambios en el producto sin necesidad de cambiar físicamente el equipo.
Otra ventaja importante es su compatibilidad con soluciones de Industria 4.0. Gracias a la conectividad de datos, estas mesas pueden enviar información operativa a sistemas de gestión y monitoreo en tiempo real. Esto permite a los responsables de producción tener una visión clara del rendimiento, la eficiencia y el estado de cada componente del proceso, facilitando decisiones basadas en datos y favoreciendo la mejora continua.
En procesos de montaje automatizado, la mesa giratoria indexada puede utilizarse como una plataforma que coordina la entrega secuencial de subcomponentes a estaciones de ensamblaje robotizadas, asegurando que cada parte se posicione en el momento exacto y con la orientación adecuada. Esto es crucial para mantener una sincronización perfecta entre distintas fases de ensamblaje y evitar errores acumulativos que puedan comprometer el funcionamiento final del producto.
Además, estas mesas pueden construirse con características especiales como protección contra polvo o líquidos, resistencia a ambientes corrosivos, o diseño higiénico para sectores como alimentos, farmacéutico o dispositivos médicos. Esto amplía su campo de aplicación y permite su uso en condiciones exigentes donde otros sistemas de posicionamiento no serían viables.
En el campo de la investigación y desarrollo, las mesas giratorias indexadas también se utilizan en laboratorios de pruebas de materiales, donde se requiere exponer diferentes caras de una muestra a condiciones controladas de ensayo térmico, mecánico o químico. Su precisión y repetibilidad las convierten en herramientas confiables para obtener datos consistentes en pruebas repetitivas.
En definitiva, su diseño modular, capacidad de automatización, precisión y adaptabilidad tecnológica hacen de las mesas giratorias indexadas un elemento clave en la evolución hacia fábricas inteligentes, donde la productividad y la calidad van de la mano con la eficiencia energética, la flexibilidad operativa y la reducción de errores.
Dispositivos automáticos para abrillantar
Los dispositivos automáticos para abrillantar son sistemas diseñados para realizar el proceso de abrillantado de superficies de forma controlada, repetitiva y con intervención humana mínima o nula. Estos equipos son esenciales en industrias que requieren acabados estéticos o funcionales de alta calidad, como la fabricación de componentes metálicos, utensilios de cocina, piezas automotrices, electrónicos, y artículos de lujo.
Estos dispositivos pueden estar equipados con ruedas de fieltro, discos de tela impregnados con compuestos de pulido, cepillos suaves o almohadillas especiales, según el tipo de material a tratar (acero inoxidable, aluminio, plástico, vidrio, etc.) y el nivel de brillo requerido. El objetivo principal es eliminar microdefectos, rayas, y marcas de procesos anteriores, dejando una superficie lisa, reflectante y uniforme.
Muchos abrillantadores automáticos funcionan en células de trabajo con estaciones múltiples, donde la pieza pasa secuencialmente por diferentes etapas de preabrillantado, pulido y acabado final. Estas estaciones suelen incluir sensores que monitorean presión, velocidad, temperatura o desgaste de herramientas, permitiendo ajustes automáticos en tiempo real para mantener la consistencia del acabado.
Los sistemas más avanzados integran robots de 6 ejes que manipulan las piezas frente a herramientas de abrillantado fijas, o viceversa, asegurando un contacto preciso y homogéneo incluso en geometrías complejas. Estos robots están programados para seguir trayectorias detalladas, aplicar presión constante y adaptarse a variaciones mínimas en la forma o posición de la pieza.
También existen versiones más compactas y especializadas, como abrillantadores automáticos de una sola estación para líneas de producción de alto volumen donde se repite el mismo proceso continuamente. Estos dispositivos, aunque más simples, ofrecen gran eficiencia en operaciones específicas y reducen considerablemente el tiempo de ciclo en comparación con el pulido manual.
Otra categoría importante son los sistemas CNC de abrillantado, utilizados en aplicaciones de precisión donde se requiere no solo brillo, sino también un control riguroso sobre la planitud o la curvatura de la superficie. Estos equipos trabajan con coordenadas exactas y algoritmos de compensación, ideales para óptica, moldes de inyección o componentes aeronáuticos.
El uso de dispositivos automáticos para abrillantar no solo mejora la calidad y uniformidad del acabado, sino que también reduce el esfuerzo físico, la exposición a polvo y compuestos abrasivos, y los errores humanos. A su vez, permite optimizar el uso de consumibles, minimizar desperdicios y aumentar la eficiencia general del proceso de fabricación.
En resumen, estos dispositivos representan una solución avanzada y rentable para empresas que buscan combinar estética, precisión y productividad en el tratamiento final de superficies.
Además, los dispositivos automáticos para abrillantar pueden personalizarse según los requerimientos de la pieza a trabajar, permitiendo ajustar parámetros como la presión de contacto, la velocidad de rotación, la duración del ciclo y la composición del compuesto abrasivo. Esta adaptabilidad los convierte en herramientas versátiles que pueden integrarse fácilmente en líneas de producción existentes o formar parte de células robotizadas altamente especializadas.
En muchos casos, estos sistemas incluyen alimentadores automáticos o cintas transportadoras que trasladan las piezas desde una etapa de producción anterior hacia la estación de abrillantado, y luego las conducen hacia la siguiente fase, como el lavado, la inspección óptica o el embalaje. Esto permite una producción continua, sin necesidad de intervención manual, reduciendo así los costos operativos y aumentando la productividad.
Los dispositivos automáticos también permiten trabajar con diferentes tipos de acabados, desde un brillo espejo hasta acabados satinados o semibrillantes, simplemente cambiando el tipo de herramienta de pulido y el compuesto aplicado. Por ejemplo, en el caso del acero inoxidable, un disco de tela con pasta blanca puede producir un brillo espejo, mientras que una rueda de sisal con pasta marrón generará un acabado más satinado y técnico.
Además, la integración de sistemas de extracción de polvo y filtrado de aire es fundamental para mantener un entorno de trabajo limpio y seguro. Muchos dispositivos incluyen cabinas cerradas con sistemas de aspiración que capturan partículas abrasivas y residuos generados durante el abrillantado, evitando su dispersión en el ambiente y protegiendo tanto a los operadores como a los componentes electrónicos de la maquinaria.
Algunos modelos avanzados incorporan inteligencia artificial para optimizar el proceso de abrillantado mediante el análisis de datos históricos. Esto les permite, por ejemplo, predecir cuándo es necesario cambiar una herramienta, ajustar automáticamente el ciclo según el estado superficial de la pieza o adaptar la presión en tiempo real para obtener el brillo óptimo sin dañar la superficie.
Este tipo de automatización también favorece la trazabilidad de la producción, ya que cada pieza puede ser registrada con su historial de pulido, incluyendo parámetros exactos utilizados, número de ciclos, fecha, hora y posibles incidencias. Esta trazabilidad es muy útil en sectores como el automotriz o el médico, donde el control de calidad y la documentación son obligatorios y exigentes.
Otra ventaja de los dispositivos automáticos para abrillantar es que permiten alcanzar niveles de calidad imposibles o poco viables mediante trabajo manual, especialmente en geometrías complejas, superficies cóncavas o zonas de difícil acceso. Mediante programación detallada o control adaptativo, el sistema ajusta su comportamiento para seguir curvas, contornos y ángulos sin perder consistencia en el acabado.
En definitiva, estos dispositivos ofrecen una solución altamente técnica y eficiente para empresas que buscan mantener una calidad de superficie constante, mejorar sus tiempos de producción y reducir costos de mano de obra. Su incorporación en la industria moderna responde a la necesidad de procesos estandarizados, reproducibles y escalables, características clave para competir en mercados exigentes y dinámicos.
Asimismo, la evolución tecnológica en dispositivos automáticos para abrillantar ha impulsado la adopción de sistemas modulares, que permiten combinar distintos módulos o estaciones según las necesidades específicas de producción. Esto facilita la expansión o reconfiguración rápida de las líneas de acabado, adaptándose a nuevas piezas o volúmenes sin requerir inversiones significativas en equipos nuevos.
Estos sistemas modulares pueden incluir desde estaciones básicas de abrillantado, hasta módulos especializados para tratamiento con compuestos líquidos, secado o incluso inspección visual integrada, todo conectado bajo un control centralizado. Esta arquitectura modular favorece la flexibilidad operativa y reduce los tiempos de cambio o mantenimiento.
La conectividad con sistemas de manufactura inteligente permite además la integración de estos dispositivos en redes industriales (IIoT), donde el flujo de datos en tiempo real ayuda a optimizar el uso de recursos, anticipar fallas y ajustar parámetros de manera dinámica para maximizar la calidad y la eficiencia. Esto es clave para cumplir con estándares internacionales de calidad y normativas ambientales.
En términos de sostenibilidad, los dispositivos automáticos para abrillantar contribuyen a minimizar el impacto ambiental al optimizar el consumo de compuestos abrasivos y reducir el desperdicio de materiales. Además, la automatización reduce el consumo energético comparado con procesos manuales prolongados, y al contar con sistemas de extracción y filtración, limitan la emisión de partículas contaminantes al ambiente.
Otro aspecto relevante es la ergonomía y seguridad laboral. Al automatizar el abrillantado, se reducen los riesgos asociados a la exposición prolongada a polvo, vibraciones y posturas forzadas, mejorando las condiciones de trabajo y disminuyendo la incidencia de enfermedades ocupacionales relacionadas con procesos manuales de pulido.
El desarrollo continuo de materiales para herramientas de abrillantado, como discos con compuestos sintéticos de alta durabilidad o tecnologías híbridas que combinan abrasivos con fibras flexibles, ha potenciado aún más la capacidad de estos dispositivos para obtener acabados perfectos en menor tiempo y con menor desgaste.
Finalmente, la capacitación y soporte técnico para la implementación y operación de estos dispositivos automáticos es fundamental. Contar con personal especializado en programación, mantenimiento y supervisión asegura que el equipo funcione a su máximo potencial, manteniendo la calidad constante y evitando paradas inesperadas.
En resumen, los dispositivos automáticos para abrillantar representan una inversión estratégica para la industria actual, que busca combinar excelencia en el acabado, productividad y sostenibilidad en un contexto de creciente competitividad global.
Las máquinas automáticas para acabado y pulido son equipos diseñados para realizar procesos de acabado superficial en piezas o componentes de manera eficiente, precisa y repetitiva, minimizando la intervención manual. Estas máquinas son fundamentales en la fabricación moderna para garantizar la calidad estética y funcional de los productos, así como para optimizar tiempos y reducir costos.
Estas máquinas pueden realizar diversas operaciones, desde el desbaste inicial hasta el pulido fino y el abrillantado, utilizando diferentes tipos de herramientas y abrasivos, como ruedas de pulir, cepillos, cintas abrasivas, discos de fieltro o almohadillas especiales. La elección de la herramienta depende del material de la pieza, la geometría y el nivel de acabado requerido.
Los sistemas automáticos pueden ser de tipo estacionario, donde la pieza se fija y la herramienta realiza el movimiento, o de tipo robotizado, en los que un robot manipula la pieza frente a herramientas fijas o viceversa, para alcanzar superficies complejas y garantizar un acabado uniforme en todas las áreas. La programación de movimientos y parámetros es clave para asegurar la repetibilidad y calidad del proceso.
Muchas máquinas automáticas para acabado y pulido incorporan controles electrónicos que regulan la velocidad, la presión aplicada, la duración del ciclo y otros parámetros, además de sensores que monitorean el desgaste de las herramientas o detectan irregularidades en la superficie. Esto permite ajustes en tiempo real y evita defectos o daños en las piezas.
Estas máquinas se utilizan ampliamente en sectores como el automotriz, aeroespacial, metalúrgico, fabricación de electrodomésticos, utensilios de cocina, joyería, y dispositivos médicos, entre otros. Su implementación contribuye a mejorar la productividad, la consistencia del acabado y la seguridad laboral al reducir la exposición a procesos manuales repetitivos y potencialmente riesgosos.
Además, algunas máquinas automáticas están diseñadas para integrarse en líneas de producción continua o células robotizadas, permitiendo la automatización completa del proceso desde la carga hasta la descarga de piezas, lo que reduce tiempos muertos y aumenta la capacidad productiva.
Por último, el mantenimiento de estas máquinas es esencial para conservar su precisión y eficiencia, por lo que suelen contar con sistemas de autodiagnóstico y fácil acceso a componentes críticos. La formación del personal en operación y mantenimiento garantiza un rendimiento óptimo y una larga vida útil del equipo.
En conclusión, las máquinas automáticas para acabado y pulido son herramientas clave para la industria moderna, que combinan tecnología, precisión y flexibilidad para ofrecer acabados de alta calidad de manera eficiente y segura.
Además, estas máquinas automáticas para acabado y pulido suelen ofrecer gran versatilidad para trabajar con diferentes materiales, desde metales ferrosos y no ferrosos, hasta plásticos, vidrios y materiales compuestos. Esto es posible gracias a la amplia variedad de abrasivos y accesorios intercambiables que permiten adaptar el proceso a las características específicas de cada pieza, logrando acabados desde un pulido mate hasta un brillo espejo.
El avance tecnológico ha permitido que muchos de estos sistemas incorporen inteligencia artificial y aprendizaje automático para optimizar los parámetros de pulido según la geometría y estado superficial de cada pieza. Esto reduce el desgaste de las herramientas, minimiza el consumo de abrasivos y mejora la calidad final, al ajustar automáticamente variables como la presión, velocidad y tiempo en función de datos recogidos durante el proceso.
La integración de sensores de fuerza, vibración y visión artificial también contribuye a detectar a tiempo posibles fallos o desviaciones, como una pieza mal posicionada o un desgaste irregular del abrasivo. Esta retroalimentación en tiempo real ayuda a evitar defectos y reduce el desperdicio de material, mejorando la eficiencia global de la línea de producción.
Por otro lado, la modularidad y escalabilidad de estas máquinas permite adaptarlas a diferentes volúmenes de producción, desde lotes pequeños con alta variedad de piezas hasta grandes series con procesos altamente estandarizados. Esto facilita la inversión y amortización de los equipos en función de las necesidades y crecimiento de la planta industrial.
Además, muchas máquinas automáticas de pulido cuentan con sistemas de extracción y filtrado para eliminar polvo y partículas generadas durante el proceso, garantizando un ambiente de trabajo limpio y seguro para los operarios. Esto también protege la maquinaria y contribuye a cumplir con normativas ambientales y de seguridad laboral vigentes.
El mantenimiento predictivo y preventivo se ha vuelto una práctica común, apoyado por tecnologías IoT que monitorizan el estado de los componentes clave y alertan sobre posibles fallas antes de que ocurran. Esto reduce paradas imprevistas y prolonga la vida útil del equipo, optimizando los costos operativos.
Finalmente, la incorporación de estas máquinas automáticas para acabado y pulido en las líneas productivas representa un salto importante en la calidad, consistencia y productividad industrial, respondiendo a las exigencias actuales de mercados competitivos y clientes que demandan productos con acabados perfectos y tiempos de entrega cortos.
Asimismo, la evolución en los dispositivos automáticos para abrillantar ha permitido desarrollar sistemas cada vez más compactos y especializados para tareas concretas, facilitando su integración incluso en espacios reducidos o en líneas de producción ya establecidas sin necesidad de grandes modificaciones. Estos equipos pueden configurarse para trabajos específicos, como abrillantar bordes, superficies planas, contornos o piezas con geometrías complejas, aumentando la precisión y calidad del acabado final.
La capacidad de estos dispositivos para operar en modo continuo o por ciclos programados los hace ideales para una amplia gama de aplicaciones industriales, desde la producción en masa hasta lotes pequeños con requerimientos específicos. Además, la posibilidad de programar diferentes parámetros para distintos tipos de piezas permite la rápida adaptación a cambios en la producción, favoreciendo la flexibilidad sin comprometer la calidad.
El desarrollo de tecnologías de control avanzado, como servomotores de alta precisión y sistemas de retroalimentación en tiempo real, ha incrementado notablemente la exactitud en la aplicación de presión y velocidad durante el abrillantado. Esto evita daños o desgaste excesivo en las piezas, optimizando el uso de consumibles y prolongando la vida útil tanto de las herramientas como de las piezas mismas.
Estos sistemas también se benefician de avances en materiales abrasivos y compuestos de pulido, que ofrecen mayor durabilidad, mejores resultados estéticos y menor impacto ambiental. La combinación de estas mejoras con la automatización reduce la necesidad de re-trabajos y mejora la consistencia del acabado, dos factores clave para la competitividad industrial.
En términos de seguridad, los dispositivos automáticos para abrillantar están diseñados con protecciones integradas para evitar accidentes, tales como coberturas, sensores de presencia y sistemas de parada de emergencia. Esto es fundamental para proteger a los operarios y cumplir con las normativas vigentes en cada región.
Finalmente, la implementación de estos dispositivos en los procesos productivos contribuye a un entorno de trabajo más ergonómico y saludable, al eliminar tareas repetitivas y fatigantes, reduciendo la exposición a polvo y sustancias químicas, y permitiendo al personal enfocarse en tareas de supervisión, control de calidad y mantenimiento predictivo.
En conjunto, los dispositivos automáticos para abrillantar representan una inversión estratégica para las empresas que buscan mejorar la calidad de sus productos, aumentar la eficiencia operativa y garantizar la seguridad y bienestar de sus colaboradores, alineándose con las tendencias actuales de la industria 4.0 y la manufactura sostenible.
Equipos automáticos para pulido de superficies
Los equipos automáticos para pulido de superficies son sistemas diseñados para realizar el proceso de pulido de manera eficiente, repetitiva y con alta precisión, minimizando la intervención manual y asegurando acabados uniformes y de calidad superior. Estos equipos se utilizan ampliamente en industrias donde el acabado superficial es crítico, como la metalurgia, automotriz, aeroespacial, fabricación de electrodomésticos, utensilios de cocina, joyería, y dispositivos médicos.
Estos equipos suelen integrar mecanismos que permiten variar parámetros clave como la velocidad de rotación, presión aplicada y tiempo de ciclo, adaptándose a diferentes tipos de materiales (acero inoxidable, aluminio, latón, plásticos, etc.) y a diversas geometrías de piezas. El control preciso de estas variables garantiza la obtención de acabados que van desde un pulido mate hasta un brillo espejo.
Existen diferentes configuraciones de equipos automáticos para pulido, incluyendo máquinas estacionarias con mesas giratorias o fijas, sistemas robotizados que manipulan la pieza o la herramienta, y estaciones modulares que permiten la combinación de diferentes procesos de pulido y acabado en línea. La automatización facilita la producción en serie, reduce los tiempos de procesamiento y mejora la repetibilidad del proceso.
Estos equipos emplean herramientas abrasivas como discos de tela, cepillos, ruedas de fieltro o almohadillas especiales, junto con compuestos pulidores que varían según el nivel de acabado deseado y el material de la pieza. Además, cuentan con sistemas de extracción de polvo y filtración para mantener un ambiente de trabajo seguro y limpio.
La incorporación de sensores y sistemas de control permite la supervisión en tiempo real del proceso, detectando variables como la presión aplicada, desgaste de las herramientas y calidad del acabado, lo que posibilita ajustes automáticos y mantenimiento predictivo para optimizar el rendimiento y evitar defectos.
La automatización del pulido contribuye a mejorar la ergonomía y seguridad laboral, al reducir la exposición de los operarios a trabajos repetitivos, vibraciones y agentes contaminantes. Además, reduce el consumo de materiales abrasivos y energía, favoreciendo prácticas más sostenibles y eficientes.
En resumen, los equipos automáticos para pulido de superficies son una solución tecnológica avanzada que aporta calidad, eficiencia y seguridad a los procesos de acabado industrial, respondiendo a las demandas actuales
Además, los equipos automáticos para pulido de superficies permiten una alta flexibilidad operativa, ya que pueden programarse para diferentes tipos de piezas y acabados, adaptándose rápidamente a cambios en la producción o a requerimientos específicos de clientes. Esto se logra mediante la configuración de parámetros ajustables como la velocidad, la presión, la duración del proceso y el tipo de abrasivo utilizado, lo que facilita la estandarización y reproducibilidad de los resultados.
Estos sistemas suelen integrarse fácilmente en líneas de producción automatizadas o células robotizadas, donde la manipulación y el transporte de las piezas también se automatizan, logrando un flujo continuo que incrementa la productividad y reduce los tiempos muertos. La modularidad de algunos equipos permite combinar varias etapas de pulido y acabado en una sola línea, optimizando espacio y recursos.
Los avances tecnológicos han impulsado la incorporación de inteligencia artificial y sensores inteligentes que monitorean constantemente el estado de la pieza y de las herramientas, ajustando automáticamente los parámetros para mantener la calidad y evitar daños. Esto también facilita el mantenimiento predictivo, al alertar sobre el desgaste o la necesidad de reemplazo de componentes antes de que se produzca una falla.
En cuanto a la seguridad y el impacto ambiental, estos equipos están diseñados para minimizar la generación de polvo y residuos, mediante sistemas de extracción y filtración eficientes que protegen la salud de los operadores y cumplen con normativas ambientales. La reducción en el consumo de abrasivos y energía también contribuye a un proceso más sostenible.
Por último, la implementación de equipos automáticos para pulido de superficies representa una inversión estratégica para las empresas que buscan mejorar la calidad de sus productos, optimizar sus procesos y mantenerse competitivas en mercados cada vez más exigentes, donde la precisión y el acabado son factores diferenciadores clave.
Estos equipos automáticos también ofrecen la ventaja de reducir significativamente la variabilidad humana en los procesos de pulido, asegurando que cada pieza cumpla con los estándares establecidos sin desviaciones. Esto es particularmente importante en industrias donde la consistencia del acabado influye directamente en la funcionalidad, durabilidad y apariencia del producto final.
Además, la automatización permite procesar piezas con geometrías complejas o superficies difíciles de alcanzar manualmente, utilizando herramientas especializadas y movimientos controlados con alta precisión. Esto amplía el rango de aplicaciones y mejora la calidad en piezas que antes requerían trabajos manuales prolongados y costosos.
La adaptabilidad de estos sistemas facilita la integración con tecnologías complementarias, como sistemas de inspección óptica automática que verifican en línea la calidad del acabado y detectan defectos, permitiendo realizar correcciones inmediatas o apartar piezas fuera de especificación. Esto contribuye a un control de calidad más riguroso y eficiente.
El uso de materiales abrasivos y compuestos pulidores avanzados, combinados con tecnologías de control automatizado, permite obtener acabados superiores con menor desgaste de herramientas y menor generación de residuos, lo que impacta positivamente en los costos operativos y en el impacto ambiental.
Finalmente, la capacitación especializada para operadores y técnicos es esencial para maximizar los beneficios de estos equipos, garantizando un manejo adecuado, una programación precisa y un mantenimiento oportuno que prolongue la vida útil del sistema y mantenga su rendimiento óptimo.
En conjunto, los equipos automáticos para pulido de superficies representan una solución integral que combina tecnología, eficiencia y calidad, adaptándose a las necesidades actuales de la industria y contribuyendo a la excelencia en la fabricación.
Máquinas automáticas para tratamiento superficial
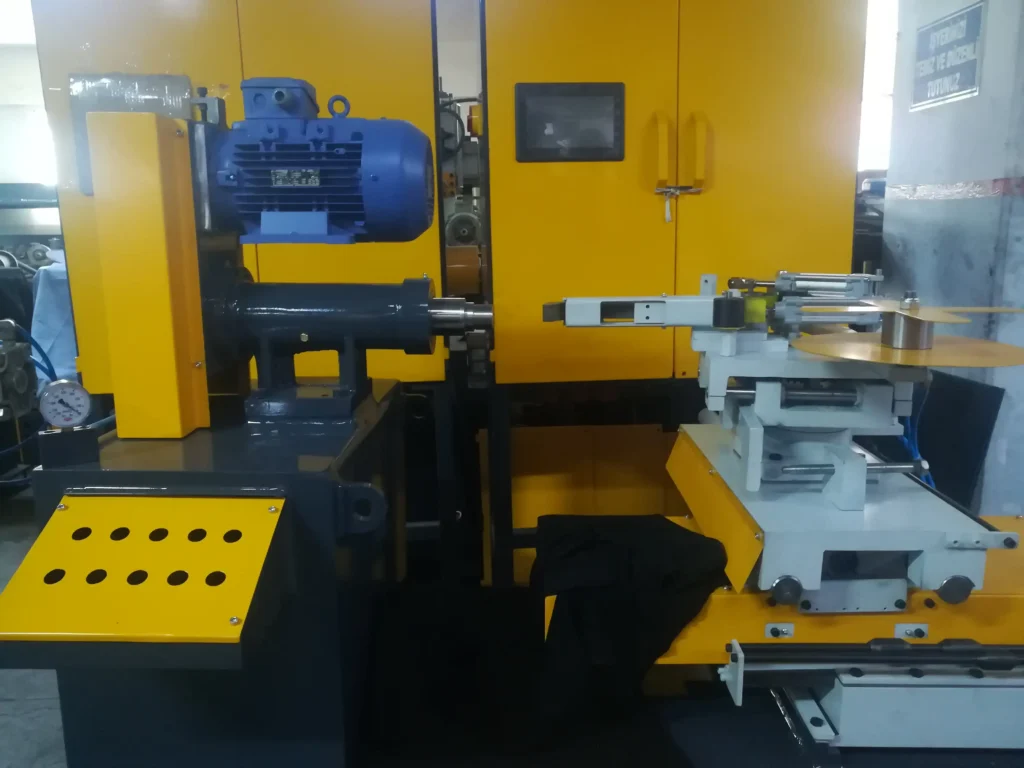
Las máquinas automáticas para tratamiento superficial son equipos diseñados para realizar de manera eficiente y precisa procesos que mejoran las propiedades funcionales, estéticas o protectoras de la superficie de piezas y componentes. Estos tratamientos incluyen pulido, abrillantado, decapado, granallado, limpieza, pasivado, anodizado, recubrimientos y otros procesos que preparan o modifican la superficie para cumplir con especificaciones técnicas o estéticas.
Estas máquinas automatizan operaciones que tradicionalmente se hacían de forma manual, incrementando la uniformidad, velocidad y repetibilidad del tratamiento, además de reducir riesgos laborales y costos operativos. Se utilizan ampliamente en industrias como la automotriz, aeroespacial, metalúrgica, electrónica, médica, y fabricación de bienes de consumo.
Entre las tecnologías más comunes incorporadas en estas máquinas están los sistemas de pulido y abrillantado automáticos con control de presión y velocidad, estaciones de granallado para mejorar la resistencia mecánica o preparar superficies para pintado, equipos de limpieza por ultrasonido o con productos químicos controlados, y sistemas de recubrimiento con aplicación uniforme de pinturas, barnices o tratamientos superficiales especiales.
Estas máquinas pueden ser configurables y modulares, permitiendo integrar varias etapas de tratamiento en una línea continua o células robotizadas. La programación de los parámetros del proceso asegura que cada pieza reciba el tratamiento adecuado según su material, forma y función.
La incorporación de sensores y controles inteligentes permite monitorear en tiempo real variables como temperatura, presión, abrasión o calidad superficial, garantizando un control exhaustivo y evitando defectos. Esto contribuye a optimizar el consumo de materiales y energía, a la vez que asegura la calidad y la trazabilidad del proceso.
Además, estos sistemas cuentan con dispositivos para la gestión ambiental, como filtros, sistemas de reciclaje y manejo de residuos, que aseguran el cumplimiento de normativas y minimizan el impacto ambiental de las operaciones.
En resumen, las máquinas automáticas para tratamiento superficial representan una solución tecnológica avanzada que potencia la calidad, eficiencia y sostenibilidad en los procesos industriales, adaptándose a las necesidades cambiantes del mercado y los estándares de producción modernos.
Estas máquinas automáticas para tratamiento superficial ofrecen una gran versatilidad al poder adaptarse a diferentes materiales, desde metales ferrosos y no ferrosos hasta plásticos, cerámicas y composites. Esta capacidad permite que una misma línea de tratamiento pueda atender múltiples tipos de piezas, facilitando la producción diversificada sin necesidad de múltiples equipos especializados.
El diseño modular de muchos de estos sistemas facilita la integración de diversas tecnologías en un solo proceso continuo, como combinar etapas de limpieza, granallado, pulido y recubrimiento, optimizando tiempos y recursos. Esto también permite una fácil ampliación o reconfiguración de la línea según cambien las necesidades productivas o se introduzcan nuevos procesos.
La automatización avanzada con sistemas de control digital y sensores inteligentes permite ajustar parámetros en tiempo real según las condiciones de la pieza o del ambiente, asegurando la consistencia y calidad del tratamiento en todas las piezas producidas. Estos sistemas suelen contar con capacidades de autodiagnóstico y mantenimiento predictivo, lo que reduce tiempos de inactividad y mejora la vida útil del equipo.
En cuanto a la seguridad y el medio ambiente, estas máquinas están equipadas con sistemas de extracción y filtrado que minimizan la emisión de partículas, gases o residuos, garantizando un entorno de trabajo seguro y cumpliendo con las regulaciones ambientales. Además, la automatización reduce la exposición directa de los operarios a sustancias químicas o procesos peligrosos, mejorando las condiciones laborales.
La capacidad para programar tratamientos específicos para cada tipo de pieza o lote también facilita la trazabilidad y el control de calidad, aspectos críticos en sectores donde la certificación y los estándares normativos son estrictos, como la industria aeroespacial o médica.
Finalmente, la implementación de máquinas automáticas para tratamiento superficial contribuye a mejorar la productividad, la calidad del producto final y la sostenibilidad del proceso, posicionando a las empresas que las utilizan en una ventaja competitiva significativa dentro de sus mercados.
Además, estas máquinas automáticas para tratamiento superficial permiten una reducción considerable en los tiempos de ciclo, ya que optimizan la secuencia y sincronización de los procesos involucrados. Esto se traduce en una mayor capacidad productiva sin sacrificar la calidad, aspecto fundamental en industrias con alta demanda y exigencias de entrega rápidas.
La precisión y uniformidad que ofrecen estas máquinas son especialmente importantes en aplicaciones donde la funcionalidad depende directamente del acabado superficial, como en piezas sometidas a esfuerzos mecánicos, resistencia a la corrosión o contacto con fluidos. Un tratamiento superficial homogéneo mejora la durabilidad y el desempeño del producto final.
Los avances en tecnologías de sensores y automatización han hecho posible que estos equipos registren y almacenen datos de cada ciclo de tratamiento, facilitando el análisis estadístico y la mejora continua del proceso. Esto contribuye a la implementación de sistemas de gestión de calidad y trazabilidad que son esenciales para cumplir con certificaciones internacionales y normativas específicas del sector.
Otra ventaja es la reducción del consumo de materiales y energía, gracias a procesos optimizados y controlados con alta precisión. Esto no solo disminuye costos operativos, sino que también responde a la creciente demanda de producción sostenible y responsable con el medio ambiente.
La flexibilidad de estos sistemas permite adaptarse rápidamente a cambios en la producción, ya sea por variación en los diseños, materiales o requisitos técnicos, sin necesidad de largos tiempos de ajuste o reconfiguración, lo que reduce tiempos muertos y mejora la rentabilidad.
Finalmente, la integración de estas máquinas automáticas para tratamiento superficial dentro de un entorno industrial moderno representa un paso estratégico hacia la digitalización y automatización completa de la producción, alineándose con las tendencias de la industria 4.0 y preparando a las empresas para enfrentar los retos futuros con mayor eficiencia y competitividad.
Los sistemas automáticos de acabado son soluciones integrales diseñadas para realizar procesos de terminación y mejora superficial de piezas y componentes de forma automatizada, eficiente y con alta precisión. Estos sistemas abarcan una amplia variedad de técnicas y tecnologías que incluyen pulido, abrillantado, lijado, desbarbado, granallado, limpieza, recubrimientos y tratamientos superficiales específicos, entre otros.
Estos sistemas están diseñados para optimizar la calidad del acabado final, asegurando uniformidad y repetibilidad, lo que es fundamental en sectores industriales donde la presentación, funcionalidad y durabilidad del producto son cruciales. La automatización permite reducir la intervención manual, minimizando errores y variaciones propias del trabajo manual, a la vez que mejora la productividad y la seguridad laboral.
Los sistemas automáticos de acabado pueden configurarse según el tipo de piezas, materiales y requisitos de producción, integrando dispositivos como mesas giratorias indexadas, robots manipuladores, unidades de pulido con control de presión y velocidad, sensores de monitoreo en tiempo real y sistemas de extracción de polvo y residuos. Esto posibilita la adaptación a distintos procesos y niveles de acabado, desde un pulido básico hasta un brillo espejo o tratamientos funcionales avanzados.
La incorporación de tecnologías de control digital y software especializado facilita la programación, supervisión y ajuste de los parámetros del proceso, permitiendo una alta flexibilidad para cambios rápidos en la producción o en las especificaciones del cliente. Además, los sistemas pueden integrarse en líneas de producción automatizadas o células robotizadas para un flujo continuo y eficiente.
En cuanto a la seguridad y el medio ambiente, estos sistemas cuentan con protecciones integradas para los operarios y sistemas de gestión ambiental que minimizan la emisión de contaminantes y el consumo de recursos, alineándose con las normativas vigentes y las prácticas de manufactura sostenible.
En resumen, los sistemas automáticos de acabado representan una evolución tecnológica que combina eficiencia, calidad y seguridad, brindando a las empresas industriales una herramienta clave para mejorar sus procesos productivos, cumplir con estándares exigentes y mantenerse competitivas en mercados globales.
Estos sistemas automáticos de acabado también contribuyen a la reducción significativa de los tiempos de procesamiento, al optimizar y sincronizar las distintas etapas del tratamiento superficial sin necesidad de intervenciones manuales que puedan generar retrasos o inconsistencias. Esta eficiencia permite aumentar la capacidad productiva y disminuir los costos operativos, lo que resulta en una mejor rentabilidad para las empresas.
La capacidad de manejar piezas con geometrías complejas y materiales diversos es otra ventaja importante, ya que los sistemas cuentan con herramientas especializadas y movimientos programados que garantizan un acabado uniforme incluso en zonas difíciles de alcanzar con métodos tradicionales. Esto amplía el rango de aplicación y mejora la calidad final del producto.
La incorporación de sensores y sistemas de monitoreo en tiempo real permite ajustar parámetros automáticamente durante el proceso, manteniendo la calidad constante y detectando cualquier desviación que pudiera afectar el acabado. Además, facilita el mantenimiento predictivo, alertando sobre el desgaste de componentes para evitar paradas no planificadas.
Desde el punto de vista ambiental y de seguridad, estos sistemas están diseñados para minimizar la generación de polvo, residuos y emisiones nocivas, incorporando sistemas de extracción y filtrado efectivos que protegen tanto a los operarios como al entorno. La automatización reduce la exposición humana a agentes químicos o físicos potencialmente peligrosos, mejorando las condiciones laborales.
Finalmente, la implementación de sistemas automáticos de acabado representa una inversión estratégica que permite a las empresas adaptarse rápidamente a las demandas cambiantes del mercado, mejorar la calidad de sus productos, optimizar sus procesos y cumplir con los estándares internacionales de fabricación, posicionándose así como líderes en innovación y eficiencia industrial.
Además, estos sistemas automáticos facilitan la integración con otras tecnologías de fabricación avanzada, como la robótica colaborativa, el control numérico computarizado (CNC) y la inteligencia artificial, potenciando aún más la precisión, la flexibilidad y la autonomía de los procesos de acabado. Esta sinergia tecnológica permite diseñar líneas de producción altamente personalizadas y adaptativas, capaces de responder en tiempo real a variaciones en la producción o especificaciones del producto.
La recopilación y análisis de datos generados durante el proceso de acabado permiten implementar estrategias de mejora continua y optimización, basadas en evidencia concreta. Esto favorece la toma de decisiones informadas para ajustar parámetros, reducir desperdicios y maximizar la eficiencia energética.
El diseño ergonómico y modular de estos sistemas también contribuye a facilitar su mantenimiento y actualización, asegurando una larga vida útil y la posibilidad de incorporar nuevas tecnologías sin necesidad de reemplazar completamente la infraestructura existente.
Finalmente, al automatizar procesos tradicionalmente laboriosos y repetitivos, las empresas pueden reasignar recursos humanos a tareas de mayor valor añadido, como el diseño, la supervisión de calidad y la innovación, impulsando así su competitividad y crecimiento sostenible en un mercado cada vez más exigente y globalizado.
Equipos automáticos para pulido industrial
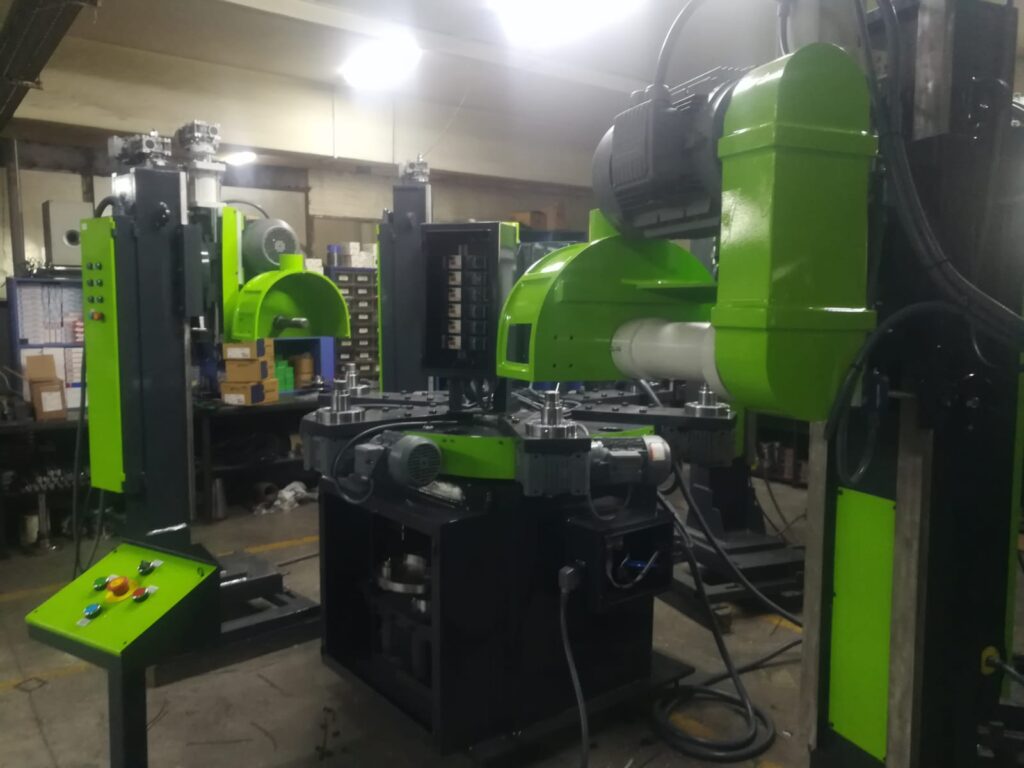
Los equipos automáticos para pulido industrial son sistemas diseñados para realizar procesos de pulido y acabado superficial en piezas y componentes de manera automatizada, garantizando alta calidad, uniformidad y eficiencia en la producción. Estos equipos se emplean en múltiples sectores industriales como el automotriz, metalúrgico, aeroespacial, fabricación de electrodomésticos, utensilios de cocina y componentes médicos, donde el acabado superficial es un factor clave para la funcionalidad y estética del producto.
Estos equipos incorporan tecnologías avanzadas que permiten controlar con precisión parámetros como velocidad, presión, tiempo de pulido y tipo de abrasivo o compuesto pulidor, adaptándose a diferentes materiales y geometrías de las piezas. Pueden incluir mesas giratorias indexadas, sistemas robotizados, unidades de pulido con motores de alta potencia y sistemas de sujeción automáticos para garantizar una manipulación segura y repetible.
La automatización reduce la variabilidad humana, optimiza el uso de materiales abrasivos y disminuye el tiempo de ciclo, mejorando la productividad y reduciendo costos. Además, suelen contar con sistemas de extracción de polvo y control ambiental para mantener condiciones seguras y limpias en el área de trabajo.
La flexibilidad de estos equipos permite integrarlos en líneas de producción automatizadas o células robotizadas, donde combinan el pulido con otros procesos de acabado o tratamiento superficial, creando flujos continuos y eficientes. También incorporan sensores y sistemas de monitoreo en tiempo real para ajustar parámetros y garantizar la calidad constante del acabado.
En resumen, los equipos automáticos para pulido industrial son una solución tecnológica que aporta precisión, velocidad y seguridad a los procesos de acabado, ayudando a las empresas a cumplir con altos estándares de calidad y a mantenerse competitivas en mercados exigentes.
Los equipos automáticos para pulido industrial permiten realizar acabados uniformes y de alta calidad en diferentes tipos de materiales y formas, desde piezas planas hasta geometrías complejas. Su precisión y repetibilidad aseguran que cada pieza cumpla con los requisitos técnicos y estéticos sin variaciones, lo que es esencial para sectores con altos estándares.
Estos sistemas reducen el esfuerzo manual, disminuyen el riesgo de errores y aceleran el proceso productivo. Gracias a su programación, pueden ajustarse rápidamente para distintos lotes o productos, facilitando la producción flexible y personalizada.
Incorporan sistemas de sujeción seguros y mecanismos automáticos que garantizan la correcta posición de las piezas durante el pulido, evitando daños y aumentando la eficiencia. Además, los sistemas de control supervisan continuamente variables como presión y velocidad para optimizar el proceso y prolongar la vida útil de los abrasivos.
El manejo de residuos y polvo generado se realiza mediante dispositivos de extracción y filtración integrados, mejorando la seguridad laboral y minimizando el impacto ambiental. Estos equipos también permiten un mantenimiento predictivo, gracias a sensores que detectan desgaste o fallas antes de que afecten la producción.
En conjunto, los equipos automáticos para pulido industrial combinan tecnología avanzada con diseño ergonómico y funcional, ofreciendo soluciones eficientes y sostenibles que responden a las necesidades actuales de la industria moderna.
Además, estos equipos pueden integrarse con sistemas robotizados para automatizar completamente la manipulación de las piezas, desde su carga hasta la descarga, lo que reduce aún más la intervención humana y los tiempos muertos. La conectividad con sistemas de gestión de producción permite un seguimiento detallado y análisis de datos para mejorar continuamente el proceso.
La versatilidad de los equipos automáticos para pulido permite trabajar con distintos abrasivos y compuestos, adaptándose a acabados desde un pulido mate hasta un brillo espejo, según los requerimientos del producto final. Esta adaptabilidad es clave para industrias que manejan productos variados o que requieren acabados específicos por cliente o aplicación.
Gracias a su diseño modular, los equipos pueden ampliarse o modificarse fácilmente, facilitando la incorporación de nuevas tecnologías o la adaptación a cambios en la línea productiva. Esto garantiza una inversión a largo plazo con alta rentabilidad.
En resumen, los equipos automáticos para pulido industrial no solo mejoran la calidad y consistencia del acabado, sino que también optimizan la productividad, seguridad y sostenibilidad, posicionando a las empresas que los emplean en una ventaja competitiva significativa.
Máquinas automáticas para acabado espejo
Las máquinas automáticas para acabado espejo están diseñadas para proporcionar superficies con un brillo intenso y uniforme, similar al de un espejo, en piezas metálicas u otros materiales que requieren un acabado estético y funcional de alta calidad. Estos sistemas combinan tecnologías de pulido, abrillantado y limpieza controladas con precisión para lograr un acabado superficial libre de imperfecciones, arañazos o marcas.
Estas máquinas emplean movimientos sincronizados, abrasivos específicos y compuestos pulidores que, junto con controles automáticos de presión y velocidad, garantizan un pulido homogéneo en toda la pieza, incluso en geometrías complejas. Pueden integrar mesas giratorias, robots o sistemas de sujeción que aseguran la correcta posición y manipulación durante el proceso.
La automatización reduce la variabilidad del acabado, mejora la productividad y permite trabajar con lotes grandes o pequeños manteniendo la misma calidad. Además, cuentan con sistemas de extracción de polvo y residuos para mantener condiciones seguras y limpias.
Estas máquinas son ideales para industrias como la automotriz, joyería, electrodomésticos, aeroespacial y médica, donde el acabado espejo no solo mejora la estética sino que también puede aportar beneficios funcionales, como la reducción de fricción o la protección contra la corrosión.
En conjunto, las máquinas automáticas para acabado espejo ofrecen una solución eficiente, precisa y sostenible para obtener superficies brillantes y perfectas, contribuyendo a elevar el valor y la calidad final del producto.
Las máquinas automáticas para acabado espejo permiten alcanzar superficies con un brillo profundo y uniforme gracias a la combinación de abrasivos finos y compuestos pulidores especializados, aplicados con movimientos controlados y repetitivos que eliminan microdefectos y generan un acabado liso y reflectante. Estos sistemas ajustan automáticamente la presión y velocidad para evitar daños o sobrecalentamiento de la pieza, garantizando resultados consistentes.
Incorporan sistemas de sujeción y posicionamiento que facilitan el tratamiento de piezas con formas complejas, asegurando que todas las áreas reciban un pulido homogéneo. La integración de mesas giratorias o robots mejora la precisión y reduce la intervención manual, lo que incrementa la productividad y disminuye errores.
Además, cuentan con sistemas de extracción y filtrado que eliminan residuos y polvo generados durante el proceso, manteniendo un ambiente seguro y limpio para los operarios y el equipo. Estos sistemas también contribuyen a la sostenibilidad al minimizar la contaminación y facilitar la gestión de desechos.
El uso de estas máquinas es especialmente valioso en sectores donde el acabado espejo es crucial, como en componentes decorativos, piezas para vehículos de lujo, dispositivos médicos o instrumentos de precisión. Su capacidad para producir acabados de alta calidad con rapidez y uniformidad les convierte en una inversión clave para mejorar la competitividad y eficiencia industrial.
Además, estas máquinas suelen incorporar tecnologías de monitoreo en tiempo real que permiten ajustar automáticamente parámetros como presión, velocidad y tiempo de pulido según las condiciones específicas de cada pieza, asegurando un acabado óptimo y reduciendo el desperdicio de materiales. Esto también facilita la detección temprana de anomalías o desgaste en las herramientas, permitiendo un mantenimiento predictivo que minimiza paradas no planificadas.
Su diseño modular y flexible facilita la adaptación a diferentes tamaños y tipos de piezas, así como la integración con otras etapas del proceso productivo, como limpieza previa o inspección final, creando líneas automatizadas de acabado espejo. Esta integración mejora el flujo de trabajo y reduce los tiempos totales de producción.
La ergonomía y seguridad son aspectos clave en estas máquinas, con protecciones y sistemas que limitan la exposición de los operarios a partículas, ruido o movimientos peligrosos, mejorando las condiciones laborales. También se optimiza el consumo energético y de materiales para hacer el proceso más sostenible y rentable.
En resumen, las máquinas automáticas para acabado espejo ofrecen una solución avanzada y completa para obtener superficies con alta calidad estética y funcional, combinando precisión, eficiencia y seguridad, y contribuyendo a la excelencia productiva en diversos sectores industriales.
Las máquinas automáticas para acabado espejo representan una evolución tecnológica fundamental en los procesos de manufactura y acabado superficial, ya que combinan precisión, eficiencia y repetibilidad para lograr superficies con un brillo intenso y uniforme, características esenciales en múltiples industrias. Estas máquinas están diseñadas para manejar desde piezas pequeñas y delicadas hasta componentes de grandes dimensiones y geometrías complejas, adaptándose a las necesidades específicas de producción con una flexibilidad que supera ampliamente los métodos tradicionales manuales.
El principio de funcionamiento se basa en la aplicación controlada de abrasivos finos, compuestos pulidores especializados y movimientos coordinados que eliminan las microimperfecciones de la superficie. Mediante el ajuste automático de parámetros como presión, velocidad de rotación o desplazamiento y tiempo de proceso, estos sistemas garantizan un pulido homogéneo sin riesgo de sobrecalentamiento o daños en el material, manteniendo la integridad estructural y las propiedades mecánicas de la pieza.
Los equipos suelen estar equipados con sistemas avanzados de sujeción y posicionamiento que aseguran que la pieza permanezca estable durante todo el proceso, incluso en áreas de difícil acceso, lo que permite que el acabado espejo se extienda de manera uniforme a toda la superficie. La integración de mesas giratorias indexadas, brazos robotizados o sistemas de manipulación automatizados facilita la repetibilidad y reduce la intervención humana, minimizando errores y variaciones propias del trabajo manual.
Además, estas máquinas incorporan sistemas de extracción y filtrado para eliminar el polvo, residuos de abrasivos y compuestos pulidores, creando un entorno de trabajo limpio y seguro para los operarios y evitando la contaminación ambiental. Este enfoque contribuye también a la sostenibilidad del proceso, optimizando el consumo de recursos y facilitando el manejo adecuado de los desechos generados.
El monitoreo en tiempo real mediante sensores y software de control avanzado permite ajustar automáticamente los parámetros operativos durante el ciclo de pulido, adaptándose a las características específicas de cada pieza y detectando cualquier anomalía que pudiera afectar la calidad del acabado. Esta capacidad de autoadaptación asegura resultados consistentes, reduce el desperdicio de materiales y facilita el mantenimiento predictivo, aumentando la disponibilidad y vida útil de la maquinaria.
Desde el punto de vista industrial, la implementación de máquinas automáticas para acabado espejo se traduce en importantes ventajas competitivas. La posibilidad de producir acabados de alta calidad con mayor rapidez y menor variabilidad mejora la satisfacción del cliente y abre oportunidades en mercados que demandan productos con exigencias estéticas y funcionales elevadas, como la industria automotriz de lujo, aeroespacial, dispositivos médicos, joyería y electrodomésticos premium.
Además, la automatización de estos procesos libera a los operadores de tareas repetitivas y físicamente exigentes, permitiéndoles enfocarse en actividades de supervisión, control de calidad e innovación, lo que contribuye a un mejor ambiente laboral y a la optimización del talento humano dentro de la empresa.
La modularidad y escalabilidad de estas máquinas permiten su integración en líneas de producción más amplias, facilitando la incorporación de nuevas tecnologías o la adaptación a cambios en los requerimientos productivos sin necesidad de inversiones completas en nuevos equipos. Esto garantiza una mayor flexibilidad y retorno de inversión a largo plazo.
En conclusión, las máquinas automáticas para acabado espejo no solo proporcionan un acabado estético superior, sino que también optimizan la productividad, calidad, seguridad y sostenibilidad de los procesos industriales. Su adopción representa una apuesta estratégica para empresas que buscan posicionarse a la vanguardia de la manufactura avanzada, maximizando la eficiencia operativa y la competitividad en un mercado global cada vez más exigente.
Equipos automáticos para acabado brillante
Los equipos automáticos para acabado brillante están diseñados para proporcionar a las superficies metálicas y otros materiales un acabado liso, uniforme y altamente reflectante que resalte la estética y funcionalidad del producto final. Este tipo de acabado es esencial en industrias donde la apariencia visual y la resistencia a la corrosión o al desgaste juegan un papel importante, como en la fabricación de utensilios de cocina, componentes automotrices, electrodomésticos, joyería y productos de consumo premium.
Estos sistemas combinan tecnologías avanzadas de pulido y abrillantado automatizado que controlan con precisión variables críticas como la presión aplicada, la velocidad de pulido, el tipo y la granulometría de los abrasivos, así como el uso de compuestos químicos específicos para obtener un brillo intenso y duradero. La automatización permite que estos parámetros se ajusten dinámicamente durante el proceso, optimizando el resultado y asegurando la repetibilidad entre lotes de producción.
Los equipos cuentan con dispositivos de sujeción y manipulación que garantizan la correcta fijación y posicionamiento de las piezas, evitando daños o movimientos indeseados durante el proceso. Además, pueden incluir mesas giratorias indexadas, brazos robóticos o sistemas de transporte integrados que facilitan el flujo continuo y sincronizado dentro de líneas de producción automatizadas.
La integración de sensores y sistemas de monitoreo en tiempo real permite supervisar el estado de la pieza y la maquinaria, detectando cualquier desviación en el proceso para corregirla de inmediato. Esto no solo mejora la calidad del acabado, sino que también reduce el desperdicio de materiales y prolonga la vida útil de los consumibles y componentes del equipo.
Los sistemas de extracción y filtración incorporados aseguran un ambiente de trabajo limpio y seguro, minimizando la exposición de los operarios a polvo, partículas abrasivas o compuestos químicos, al mismo tiempo que cumplen con normativas ambientales y de seguridad industrial.
En conjunto, los equipos automáticos para acabado brillante representan una solución tecnológica eficiente y sostenible que permite a las empresas aumentar su productividad, mejorar la calidad de sus productos y mantener la competitividad en mercados cada vez más exigentes, ofreciendo acabados que combinan estética, funcionalidad y durabilidad.
Los equipos automáticos para acabado brillante operan mediante procesos controlados que eliminan irregularidades y microdefectos de la superficie, logrando un nivel de pulido que refleja la luz de manera homogénea y con alta intensidad. Estos sistemas utilizan abrasivos de diferentes granulometrías, compuestos químicos y movimientos sincronizados que se ajustan según el material y la forma de la pieza, garantizando resultados consistentes en cada ciclo.
La automatización de estos procesos permite una reducción significativa del tiempo de acabado en comparación con métodos manuales, además de minimizar la variabilidad y los errores humanos. Gracias a sus sistemas de sujeción y manipulación automatizados, las piezas se mantienen estables durante el proceso, lo que evita marcas o daños accidentales, aumentando la calidad y reduciendo el retrabajo.
Los sensores integrados en los equipos supervisan parámetros clave como la presión, la velocidad y el desgaste de las herramientas abrasivas, ajustando el proceso en tiempo real para optimizar el pulido y prolongar la vida útil de los consumibles. Esto también facilita el mantenimiento predictivo, reduciendo paradas no planificadas y mejorando la disponibilidad del equipo.
Los sistemas de extracción y filtrado eliminan eficientemente los residuos generados durante el acabado, manteniendo un ambiente limpio y seguro, y cumpliendo con las normativas ambientales. Además, la reducción en la exposición de los operarios a partículas y compuestos químicos mejora las condiciones laborales y la seguridad.
Estos equipos pueden integrarse fácilmente en líneas de producción automatizadas, combinándose con otras etapas de fabricación y permitiendo un flujo continuo que incrementa la productividad general. La flexibilidad para adaptarse a diferentes tipos de piezas y acabados hace que sean ideales para industrias que demandan acabados brillantes de alta calidad y uniformidad.
En definitiva, los equipos automáticos para acabado brillante ofrecen una solución avanzada que optimiza tanto la calidad como la eficiencia del proceso, ayudando a las empresas a cumplir con los estándares más exigentes y a posicionarse competitivamente en mercados que valoran la excelencia en el acabado superficial.
Estos equipos automáticos para acabado brillante también permiten una gran adaptabilidad a distintos materiales, como acero inoxidable, aluminio, cobre, latón, entre otros, ajustando los parámetros para respetar las propiedades físicas y químicas de cada uno, evitando daños o alteraciones indeseadas. Esto los hace especialmente valiosos en sectores donde la diversidad de productos y acabados es amplia, como en la fabricación de electrodomésticos, automoción, arquitectura o diseño industrial.
La capacidad de programar diferentes ciclos de trabajo y secuencias de pulido facilita la producción de lotes variados sin perder tiempo en ajustes manuales o reconfiguraciones complejas, lo que favorece la flexibilidad productiva y reduce costos operativos. Además, el software de control suele incluir interfaces intuitivas que permiten a los operadores supervisar y modificar fácilmente los parámetros, facilitando la capacitación y el manejo diario.
Algunos modelos avanzados incorporan también tecnologías de visión artificial o escaneo 3D que evalúan la superficie en tiempo real, detectando imperfecciones o variaciones para corregir automáticamente el proceso y asegurar un acabado brillante perfecto y homogéneo en toda la pieza. Esto representa un salto importante hacia la fabricación inteligente y la calidad garantizada.
La integración con sistemas robotizados para la carga y descarga de piezas completa el ciclo automatizado, eliminando prácticamente la intervención humana en el proceso de acabado, lo que no solo mejora la seguridad laboral sino que también incrementa la velocidad y constancia de la producción.
En resumen, los equipos automáticos para acabado brillante combinan innovación tecnológica, eficiencia operativa y calidad superior, convirtiéndose en una herramienta indispensable para las industrias que buscan optimizar sus procesos de acabado y ofrecer productos con acabados excepcionales que cumplen con las expectativas más exigentes del mercado actual.
Máquinas automáticas para lustrado
Las máquinas automáticas para lustrado son equipos diseñados para proporcionar un acabado fino y brillante a las superficies de diversos materiales, principalmente metales, a través de procesos controlados y repetitivos que eliminan imperfecciones superficiales y mejoran la estética del producto final. Estas máquinas son fundamentales en sectores donde la presentación visual y la calidad superficial son decisivas, tales como la industria automotriz, fabricación de utensilios de cocina, productos de decoración, joyería y componentes industriales de alta precisión.
El lustrado automático combina movimientos coordinados de abrasivos suaves o pastas pulidoras aplicadas con presión y velocidad reguladas, lo que permite obtener un brillo intenso y homogéneo sin dañar el material. Gracias a la automatización, se elimina la variabilidad propia del trabajo manual, logrando una mayor uniformidad en el acabado y una producción más rápida y eficiente.
Estos equipos suelen incorporar sistemas de sujeción y posicionamiento que garantizan la estabilidad de las piezas durante el proceso, permitiendo el tratamiento de geometrías complejas o delicadas sin riesgos de daños. La inclusión de mesas giratorias, brazos robotizados o mecanismos de desplazamiento automatizado facilita la optimización del flujo productivo y la integración en líneas de fabricación automatizadas.
Además, las máquinas para lustrado cuentan con sistemas de monitoreo y control que ajustan parámetros clave en tiempo real, como presión, velocidad y duración del proceso, adaptándose a las características específicas de cada pieza y asegurando un acabado consistente. Esto también contribuye a la reducción de desperdicios y al mantenimiento preventivo de los equipos, incrementando su vida útil.
Los sistemas de extracción y filtración integrados garantizan un ambiente de trabajo limpio y seguro, eliminando polvo, partículas y residuos generados durante el lustrado, lo que protege la salud de los operarios y cumple con las normativas ambientales vigentes.
En conjunto, las máquinas automáticas para lustrado representan una solución avanzada y eficiente que mejora la calidad del acabado, reduce costos y tiempos de producción, y contribuye a la competitividad de las empresas al ofrecer productos con acabados superiores y estables, adaptándose a las demandas de mercados cada vez más exigentes.
Las máquinas automáticas para lustrado operan mediante procesos precisos que aplican compuestos pulidores y abrasivos suaves de manera controlada sobre la superficie de las piezas, eliminando rayones finos, marcas y pequeñas imperfecciones que afectan la apariencia y el tacto del material. A diferencia del pulido grueso o el abrillantado, el lustrado busca un acabado más delicado y uniforme que realce el brillo natural del material sin alterar su estructura.
Estos equipos están diseñados para manejar diferentes tipos de materiales, desde metales como acero inoxidable, aluminio, cobre y latón, hasta ciertos plásticos o superficies recubiertas. Los parámetros de trabajo, como la presión ejercida, la velocidad de rotación y el tipo de compuesto utilizado, se ajustan automáticamente según las características específicas de cada pieza y el nivel de acabado requerido, garantizando resultados repetibles y de alta calidad.
La incorporación de sistemas de sujeción automatizados asegura que la pieza permanezca estable durante todo el proceso, evitando movimientos que puedan generar marcas o daños. Asimismo, la integración de mesas giratorias indexadas o brazos robotizados permite alcanzar todas las áreas de la superficie, incluso en geometrías complejas, optimizando el tiempo y la eficiencia del proceso.
La automatización reduce significativamente la intervención manual, disminuyendo la fatiga y el riesgo de errores humanos, al mismo tiempo que mejora la seguridad laboral al limitar la exposición directa a compuestos químicos y polvo generado durante el lustrado. Los sistemas de extracción y filtración incorporados en estas máquinas mantienen un ambiente limpio y saludable, contribuyendo al cumplimiento de normativas de seguridad y medio ambiente.
Otra ventaja importante es la posibilidad de integración de sensores y software de control que supervisan en tiempo real parámetros críticos del proceso, como la presión aplicada, la velocidad o el desgaste de los consumibles, permitiendo ajustes automáticos para mantener la consistencia del acabado y prevenir daños en las piezas o en la máquina.
Además, estas máquinas se pueden incorporar en líneas de producción automatizadas, trabajando en conjunto con otros procesos como limpieza previa, inspección óptica o embalaje, lo que favorece un flujo continuo y eficiente que maximiza la productividad y reduce costos operativos.
En definitiva, las máquinas automáticas para lustrado ofrecen una solución avanzada que combina precisión, eficiencia y seguridad, permitiendo a las empresas mejorar la calidad estética y funcional de sus productos, incrementar la velocidad de producción y garantizar la uniformidad del acabado, aspectos cruciales para competir en mercados donde la excelencia superficial es un factor diferenciador clave.
Estas máquinas automáticas para lustrado también aportan una notable flexibilidad en la fabricación, ya que pueden programarse para diferentes ciclos y tipos de acabado según el producto o lote, lo que es especialmente útil en industrias donde la variedad de piezas y materiales es amplia. Esto permite adaptar el proceso sin necesidad de realizar cambios mecánicos complejos o paradas prolongadas, facilitando la personalización y respuesta rápida a demandas específicas del mercado.
El mantenimiento y la operatividad de estos equipos se benefician de sistemas inteligentes de diagnóstico que alertan sobre el desgaste de componentes, la necesidad de recarga de compuestos o ajustes de parámetros, lo que reduce el tiempo de inactividad y mejora la eficiencia general de la planta. Esta capacidad de autogestión es fundamental para garantizar la continuidad productiva y optimizar el uso de recursos.
Por otro lado, la mejora en las condiciones laborales es un aspecto importante, ya que el lustrado manual suele ser una tarea física y repetitiva que puede causar fatiga y riesgos ergonómicos. La automatización de este proceso no solo disminuye estos riesgos, sino que también permite a los operadores enfocarse en labores de supervisión, control de calidad y optimización, incrementando el valor agregado dentro de la cadena productiva.
Además, la precisión y uniformidad que ofrecen las máquinas automáticas para lustrado contribuyen a mejorar la resistencia superficial de las piezas, ya que un acabado correcto puede disminuir la adherencia de contaminantes, reducir la corrosión y facilitar la limpieza, extendiendo la vida útil del producto final y mejorando su desempeño en aplicaciones exigentes.
La integración con sistemas de robótica y automatización avanzada abre la puerta a la fabricación inteligente, donde los procesos de lustrado pueden comunicarse y sincronizarse con otras etapas productivas, generando líneas de fabricación más ágiles, controladas y eficientes. Esto es clave para empresas que buscan optimizar sus operaciones y mantenerse competitivas en un entorno globalizado y en constante evolución tecnológica.
En suma, las máquinas automáticas para lustrado son una herramienta estratégica que, al combinar tecnología de punta, eficiencia operativa y mejora en la calidad del producto, permiten a las empresas alcanzar altos estándares industriales, satisfacer demandas estéticas y funcionales exigentes, y consolidar su posición en mercados competitivos y dinámicos.
Dispositivos automáticos de pulido
Los dispositivos automáticos de pulido son sistemas diseñados para realizar el proceso de pulido de superficies de manera completamente automatizada, asegurando uniformidad, rapidez y precisión en la eliminación de imperfecciones, arañazos y marcas superficiales. Estos dispositivos se utilizan ampliamente en diversas industrias como la metalurgia, automotriz, aeroespacial, fabricación de utensilios, y en cualquier sector donde la calidad superficial y el acabado sean fundamentales.
Estos equipos funcionan mediante la combinación de movimientos mecánicos precisos, aplicación controlada de abrasivos y compuestos pulidores, y sistemas de sujeción que mantienen las piezas firmemente en posición durante todo el proceso. La automatización permite controlar parámetros clave como presión, velocidad, recorrido y tiempo de pulido, lo que asegura una repetibilidad alta y resultados consistentes en cada ciclo, algo difícil de lograr con procesos manuales.
Los dispositivos automáticos de pulido pueden variar en diseño y complejidad, desde mesas giratorias indexadas con sistemas de pulido integrados, hasta células robotizadas que manipulan las piezas con precisión en múltiples ejes para alcanzar superficies con geometrías complejas. La flexibilidad de estos dispositivos facilita su adaptación a diferentes tamaños, formas y materiales, incluyendo metales, plásticos y composites.
La incorporación de sensores y sistemas de monitoreo permite realizar ajustes en tiempo real, optimizando el proceso según el desgaste de las herramientas, la respuesta del material o la calidad superficial obtenida. Esto no solo mejora la eficiencia y la calidad, sino que también contribuye a la reducción de desperdicios y al mantenimiento predictivo del equipo, aumentando su vida útil y disponibilidad operativa.
Los dispositivos automáticos de pulido suelen contar con sistemas de extracción y filtración para controlar el polvo y residuos generados durante el proceso, garantizando un ambiente de trabajo limpio y seguro. Además, su integración en líneas de producción automatizadas contribuye a aumentar la productividad y reducir costos operativos, al minimizar la intervención manual y acelerar los tiempos de procesamiento.
En resumen, los dispositivos automáticos de pulido representan una solución tecnológica avanzada que permite a las empresas optimizar sus procesos de acabado superficial, mejorar la calidad de sus productos, aumentar la eficiencia productiva y asegurar un entorno laboral más seguro y sostenible, aspectos clave para mantenerse competitivos en el mercado actual.
Los dispositivos automáticos de pulido están diseñados para operar de manera continua y eficiente, adaptándose a diferentes requerimientos de producción y tipos de materiales. Su capacidad para ejecutar ciclos de pulido programados con precisión permite una alta uniformidad en el acabado superficial, lo que es fundamental para productos que deben cumplir con estrictos estándares de calidad estética y funcional.
Estos sistemas incorporan mecanismos avanzados de sujeción que mantienen la pieza fija durante todo el proceso, evitando movimientos indeseados que puedan causar marcas o daños. Además, los movimientos coordinados de las herramientas de pulido, que pueden incluir discos, bandas abrasivas o cepillos especiales, se controlan electrónicamente para ajustar la presión y velocidad según la respuesta del material, logrando un acabado óptimo sin comprometer la integridad de la pieza.
La automatización también permite la integración de tecnologías de inspección visual o sensorial, que supervisan en tiempo real la calidad del pulido y detectan posibles defectos o desviaciones. Esto facilita la corrección inmediata y asegura que solo las piezas que cumplen con los requisitos avanzan en la línea de producción, reduciendo retrabajos y desperdicios.
Los dispositivos automáticos de pulido suelen estar equipados con sistemas de extracción y filtrado que eliminan partículas, polvo y residuos generados durante el proceso, lo que mejora la calidad del ambiente de trabajo y protege la salud de los operarios. Esta característica también contribuye a cumplir con normativas ambientales y de seguridad industrial vigentes.
Además, la modularidad de muchos de estos dispositivos permite su fácil integración en líneas de fabricación existentes, optimizando el flujo productivo y permitiendo la combinación con otras operaciones como limpieza, inspección o embalaje. Esto maximiza la eficiencia global y reduce los costos operativos.
El uso de software avanzado para la programación y control de estos dispositivos facilita la adaptación rápida a nuevos productos o cambios en los requerimientos de acabado, brindando flexibilidad y agilidad en la producción. Asimismo, permite registrar datos y generar informes que ayudan en la gestión de calidad y el mantenimiento preventivo.
En definitiva, los dispositivos automáticos de pulido ofrecen una solución integral que combina precisión, eficiencia y seguridad, contribuyendo a que las empresas mejoren la calidad de sus productos, aumenten su productividad y mantengan altos estándares en sus procesos industriales, indispensables para competir exitosamente en mercados exigentes y en constante evolución.
Estos dispositivos automáticos de pulido también contribuyen significativamente a la reducción de costos operativos al minimizar la necesidad de intervención manual y disminuir el tiempo de ciclo por pieza. Al automatizar el proceso, se reduce la dependencia de operarios especializados, lo que permite una mejor asignación de recursos humanos hacia tareas de supervisión, control de calidad y mantenimiento, incrementando el valor agregado en la producción.
La precisión con la que estos equipos aplican la acción de pulido permite un uso más eficiente de los materiales consumibles, como abrasivos y compuestos pulidores, optimizando su duración y reduciendo desperdicios. Esta eficiencia en el uso de insumos no solo representa un ahorro económico, sino que también disminuye el impacto ambiental asociado al proceso.
Además, muchos dispositivos automáticos modernos cuentan con sistemas de autodiagnóstico y mantenimiento predictivo que alertan sobre el desgaste de componentes o la necesidad de ajustes, evitando fallas inesperadas y prolongando la vida útil del equipo. Esto mejora la continuidad operativa y reduce los costos relacionados con reparaciones y paradas no planificadas.
En cuanto a la versatilidad, estos dispositivos pueden ser configurados para atender diferentes niveles de acabado, desde un pulido básico para preparar la superficie hasta acabados de alta calidad que cumplen con estándares estéticos y funcionales específicos. Esta capacidad los hace aptos para una amplia variedad de aplicaciones industriales, desde la fabricación de piezas mecánicas hasta productos de consumo masivo con requerimientos estéticos exigentes.
La implementación de estos sistemas también favorece la trazabilidad del proceso, ya que mediante la integración con sistemas de gestión y control, es posible registrar y monitorear cada etapa del pulido, facilitando el control de calidad y la certificación de los productos finales.
Finalmente, el avance tecnológico continuo en este tipo de dispositivos, incluyendo la incorporación de inteligencia artificial y aprendizaje automático, abre nuevas posibilidades para la optimización dinámica de los procesos, adaptándose automáticamente a variaciones en las piezas o materiales y mejorando constantemente la eficiencia y calidad del pulido. Esto posiciona a los dispositivos automáticos de pulido como una inversión estratégica clave para empresas que buscan innovación, competitividad y excelencia en sus productos.
Sistemas automatizados para pulido
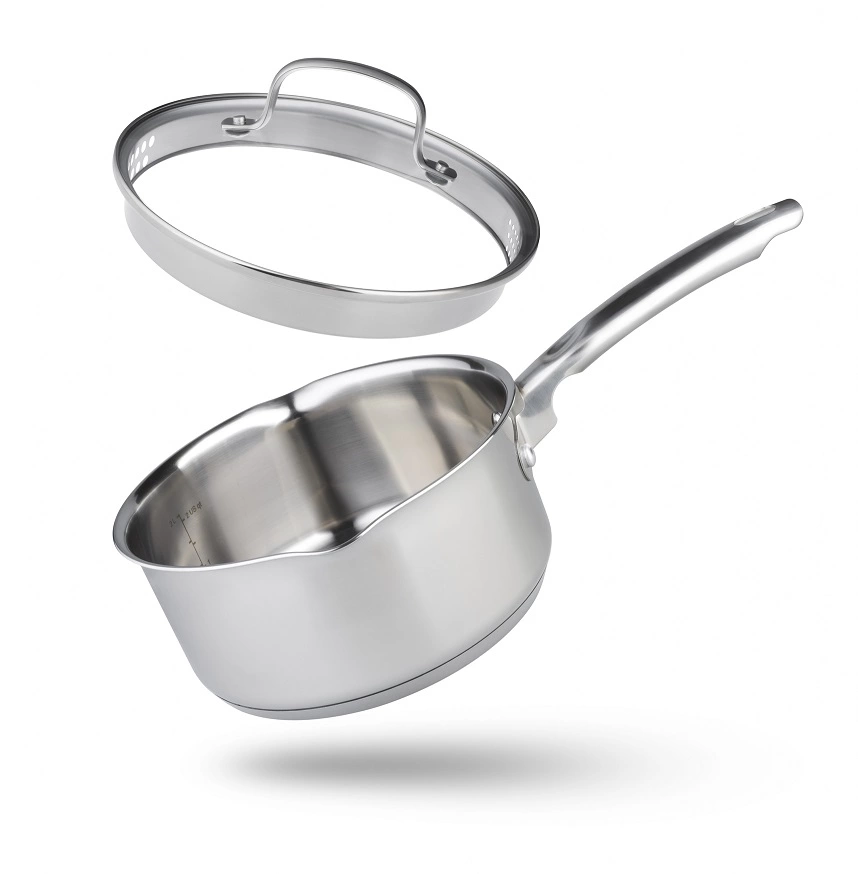
Los sistemas automatizados para pulido representan una evolución avanzada dentro del proceso de acabado superficial, integrando diversas tecnologías para llevar a cabo el pulido de manera eficiente, precisa y consistente. Estos sistemas combinan maquinaria especializada, control computarizado, sensores y, en muchos casos, robótica, para optimizar cada etapa del proceso, desde la sujeción de la pieza hasta el acabado final.
El principal beneficio de estos sistemas es la capacidad de realizar procesos complejos de pulido en piezas con geometrías variadas y exigencias específicas, manteniendo una alta repetibilidad y calidad en cada ciclo. La automatización reduce significativamente la intervención humana, lo que minimiza errores y variabilidad, y mejora la seguridad del entorno laboral al limitar la exposición a polvo y compuestos químicos.
Estos sistemas suelen incluir estaciones de trabajo con mesas giratorias, brazos robotizados o plataformas móviles que permiten abordar todas las superficies de la pieza con movimientos controlados en múltiples ejes. La programación avanzada permite adaptar los parámetros de presión, velocidad y recorrido de las herramientas abrasivas según el tipo de material y el nivel de acabado requerido, ofreciendo gran flexibilidad y personalización.
La integración de sensores de fuerza, visión artificial y sistemas de monitoreo en tiempo real permite ajustar el proceso de manera dinámica, detectando desviaciones o defectos y corrigiendo automáticamente los parámetros para asegurar un acabado óptimo. Esta capacidad de feedback continuo mejora la eficiencia y reduce el desperdicio de material y tiempo.
Además, estos sistemas incorporan dispositivos de extracción y filtración para mantener la limpieza ambiental y proteger la salud de los operarios, cumpliendo con normativas de seguridad y medio ambiente. La modularidad de los sistemas facilita su incorporación en líneas de producción ya existentes, permitiendo una mayor productividad y una mejor sincronización con otros procesos como limpieza, inspección o embalaje.
El uso de software especializado permite la programación sencilla de diferentes ciclos de trabajo, almacenamiento de recetas de pulido y recopilación de datos para análisis de producción y mantenimiento predictivo. Esto facilita la trazabilidad y el control de calidad, aspectos fundamentales para industrias que requieren certificaciones y estándares rigurosos.
En definitiva, los sistemas automatizados para pulido ofrecen una solución integral que mejora la calidad superficial, optimiza recursos, incrementa la productividad y asegura condiciones de trabajo más seguras, constituyendo una inversión estratégica para empresas que buscan mantenerse competitivas y a la vanguardia tecnológica en sus procesos industriales.
Los sistemas automatizados para pulido operan mediante la coordinación precisa de componentes mecánicos, electrónicos y de software que trabajan en conjunto para llevar a cabo procesos de acabado con alta eficiencia y repetibilidad. Estos sistemas pueden incluir mesas giratorias, actuadores lineales, robots articulados y herramientas abrasivas controladas, que se ajustan automáticamente para adaptarse a las características de cada pieza, garantizando resultados uniformes y de alta calidad.
La capacidad de programar múltiples parámetros como la presión aplicada, la velocidad de rotación, la trayectoria del pulidor y la duración del ciclo permite una gran versatilidad para procesar una amplia variedad de materiales, desde metales hasta plásticos y compuestos, así como piezas con geometrías simples o complejas. Esto facilita la producción de lotes variados sin la necesidad de cambios mecánicos extensos o tiempos muertos prolongados.
Además, la integración de sensores y sistemas de visión artificial posibilita la inspección continua durante el proceso, detectando imperfecciones, variaciones en la superficie o desgaste de las herramientas, y realizando ajustes en tiempo real para mantener la calidad del acabado. Esto no solo mejora la precisión, sino que también reduce el desperdicio y la necesidad de retrabajos, optimizando los costos de producción.
Los sistemas automatizados para pulido también contribuyen a mejorar las condiciones laborales al minimizar la exposición de los operarios a polvo, partículas y compuestos químicos, gracias a la incorporación de sistemas de extracción y filtración eficientes. Asimismo, la reducción de la intervención manual disminuye la fatiga y el riesgo de lesiones por movimientos repetitivos o posturas incómodas.
Otra ventaja importante es la posibilidad de integrar estos sistemas dentro de líneas de producción más amplias, permitiendo la automatización completa del proceso productivo, desde la carga y sujeción de las piezas hasta el pulido, inspección y descarga, lo que incrementa significativamente la productividad y reduce los tiempos de ciclo.
El software de control avanzado facilita la programación de diferentes recetas de pulido, el almacenamiento de datos históricos y la generación de informes que permiten un seguimiento detallado del desempeño del sistema y la calidad de los productos. Esto resulta esencial para industrias que deben cumplir con estrictos estándares de calidad y regulaciones.
En resumen, los sistemas automatizados para pulido representan una solución tecnológica que combina eficiencia, precisión, seguridad y flexibilidad, permitiendo a las empresas optimizar sus procesos de acabado superficial, mejorar la calidad de sus productos y aumentar su competitividad en mercados cada vez más exigentes y dinámicos.
Estos sistemas avanzados no solo mejoran la calidad y consistencia del pulido, sino que también posibilitan una significativa reducción en los tiempos de producción. La automatización elimina la variabilidad inherente al trabajo manual y asegura que cada pieza reciba un tratamiento uniforme, lo cual es crucial en industrias donde la estética y el desempeño superficial son factores determinantes, como en la fabricación de componentes automotrices, piezas aeroespaciales, electrodomésticos y utensilios de alta gama.
El diseño modular y escalable de muchos sistemas automatizados permite a las empresas implementar soluciones adaptadas a sus necesidades específicas, desde instalaciones pequeñas con ciclos de producción moderados hasta grandes plantas industriales con volúmenes elevados y diversidad de productos. Esta flexibilidad es vital para responder rápidamente a cambios en la demanda o en las especificaciones del cliente sin necesidad de realizar inversiones adicionales significativas.
La incorporación de tecnologías de inteligencia artificial y aprendizaje automático comienza a jugar un papel relevante en la optimización de estos sistemas, permitiendo que los equipos ajusten de manera autónoma sus parámetros operativos basándose en datos históricos y condiciones en tiempo real, anticipándose a posibles fallos o desviaciones en la calidad. Esto mejora la eficiencia operativa y facilita el mantenimiento predictivo, evitando paros inesperados y extendiendo la vida útil de los componentes.
Asimismo, la digitalización y conectividad que ofrecen estos sistemas favorecen su integración en entornos de fabricación inteligente (Industria 4.0), donde la comunicación entre máquinas, la recopilación de datos y el análisis en tiempo real permiten una gestión integral y optimizada de la producción. Esto incluye la posibilidad de realizar ajustes remotos, monitorización continua y análisis detallados para la mejora continua de procesos.
Por último, la adopción de sistemas automatizados para pulido contribuye a la sostenibilidad ambiental y económica de las operaciones industriales. Al optimizar el uso de materiales abrasivos y compuestos, minimizar el desperdicio, reducir el consumo energético y mejorar las condiciones laborales, estos sistemas se alinean con las políticas y objetivos de producción responsable y ecoeficiente que cada vez más empresas buscan implementar para cumplir con normativas y mejorar su imagen corporativa.
En definitiva, los sistemas automatizados para pulido no solo representan una herramienta clave para elevar la calidad y productividad, sino también un componente esencial en la transformación digital y sostenible de la industria moderna.
Máquinas automáticas para abrillantado
Las máquinas automáticas para abrillantado son equipos diseñados para mejorar el acabado superficial de piezas y productos mediante un proceso controlado que realza el brillo, la uniformidad y la estética del material. Estas máquinas automatizan el proceso tradicional de abrillantado, que normalmente se realiza manualmente, logrando resultados más rápidos, consistentes y de alta calidad.
El funcionamiento de estas máquinas se basa en la aplicación de movimientos mecánicos precisos, combinados con compuestos abrillantadores y abrasivos especiales, que eliminan imperfecciones superficiales, rayaduras finas y residuos, dejando un acabado brillante y uniforme. Pueden estar equipadas con sistemas de mesas giratorias, brazos robóticos o mecanismos de pulido rotativo que aseguran la cobertura completa y homogénea de las superficies a tratar.
La automatización permite ajustar con exactitud parámetros como la presión aplicada, velocidad de pulido, tiempo de tratamiento y cantidad de producto abrillantador, adaptándose a distintos materiales como metales, plásticos, vidrios o cerámicos. Esto garantiza que el proceso sea eficiente y adecuado a las características específicas de cada pieza, evitando daños o excesos en el tratamiento.
Estas máquinas también suelen incorporar sistemas de extracción y filtración para controlar el polvo y partículas generadas durante el proceso, lo que mejora las condiciones de trabajo y reduce el impacto ambiental. Además, muchas de ellas cuentan con programas preestablecidos o configurables, facilitando su uso y adaptabilidad a diferentes tipos de productos o requerimientos de producción.
En sectores industriales como el metalúrgico, automotriz, electrodomésticos, fabricación de utensilios de cocina o componentes electrónicos, las máquinas automáticas para abrillantado juegan un papel clave para asegurar que los productos cumplan con altos estándares de presentación y calidad superficial, contribuyendo a la satisfacción del cliente y a la competitividad en el mercado.
En resumen, estas máquinas representan una solución tecnológica avanzada que optimiza el proceso de abrillantado, aumentando la productividad, garantizando acabados de alta calidad y mejorando la seguridad y sostenibilidad de las operaciones industriales.
Las máquinas automáticas para abrillantado están diseñadas para integrarse fácilmente en líneas de producción modernas, permitiendo un flujo continuo y eficiente de piezas a tratar. Gracias a su programación flexible, pueden adaptarse rápidamente a diferentes tamaños, formas y materiales, lo que las hace ideales para empresas con diversidad de productos o que requieren cambios frecuentes en sus procesos.
El control preciso de variables como la presión de contacto, velocidad de rotación y tiempo de exposición asegura que el abrillantado se realice de manera uniforme, evitando problemas como el desgaste excesivo o el daño superficial. Esto es especialmente importante en materiales delicados o piezas con acabados sensibles, donde la calidad del brillo puede afectar tanto la estética como la funcionalidad del producto final.
Además, estas máquinas incorporan sistemas automáticos de dosificación y distribución de compuestos abrillantadores, optimizando el consumo de materiales y evitando desperdicios. Esto no solo reduce costos operativos, sino que también contribuye a una producción más sostenible y respetuosa con el medio ambiente.
El mantenimiento y operación de las máquinas automáticas para abrillantado suelen ser simples gracias a interfaces intuitivas y sistemas de autodiagnóstico que alertan sobre el estado del equipo y la necesidad de intervenciones preventivas. Esto minimiza tiempos de parada y mejora la disponibilidad del sistema, factores clave para mantener altos niveles de productividad.
Asimismo, la reducción de la intervención manual disminuye la exposición de los operarios a agentes abrasivos y polvo, mejorando la seguridad y condiciones laborales en las plantas de producción. La incorporación de sistemas de extracción y filtración complementa este aspecto, manteniendo un ambiente limpio y saludable.
En sectores donde la apariencia y calidad superficial son diferenciadores competitivos, las máquinas automáticas para abrillantado aportan un valor significativo al garantizar acabados homogéneos y de alta calidad en cada lote producido. Esto favorece la reputación de la marca y la fidelización de clientes.
Finalmente, la combinación de tecnología, eficiencia y versatilidad que ofrecen estas máquinas las posiciona como una inversión estratégica para cualquier empresa que busque optimizar sus procesos de acabado superficial, incrementar su capacidad productiva y mantener altos estándares de calidad en un mercado cada vez más exigente y competitivo.
Estas máquinas automáticas para abrillantado también permiten una integración completa con otros procesos productivos, facilitando la automatización total de la cadena de fabricación. Por ejemplo, pueden sincronizarse con sistemas de carga y descarga automatizados, estaciones de inspección visual y procesos posteriores como el embalaje, contribuyendo a la creación de líneas de producción altamente eficientes y con mínima intervención humana.
La capacidad de registrar y analizar datos operativos en tiempo real ofrece a los responsables de producción una visión detallada del desempeño del proceso, permitiendo identificar áreas de mejora, optimizar parámetros y reducir desperdicios. Esta trazabilidad es especialmente valiosa para cumplir con normativas de calidad y certificaciones industriales, además de favorecer una gestión más transparente y controlada.
Asimismo, el diseño ergonómico y compacto de muchas máquinas automáticas para abrillantado facilita su instalación en espacios reducidos, maximizando el uso del área productiva. La flexibilidad para adaptarse a diferentes configuraciones de planta permite que tanto pequeñas como grandes empresas puedan beneficiarse de estas tecnologías.
La evolución tecnológica constante impulsa la incorporación de nuevas funcionalidades, como sensores avanzados que monitorean la superficie en tiempo real, sistemas de inteligencia artificial para la optimización automática del proceso y conectividad IoT que permite la supervisión remota y el mantenimiento predictivo. Estas innovaciones aseguran que las máquinas de abrillantado mantengan su relevancia y efectividad en un mercado industrial en constante cambio.
En definitiva, las máquinas automáticas para abrillantado no solo mejoran la calidad y velocidad del proceso de acabado, sino que también contribuyen a la modernización, eficiencia y sostenibilidad de las operaciones industriales, consolidándose como una herramienta fundamental para empresas que buscan excelencia productiva y competitividad global.
Equipos automáticos para abrillantar
Los equipos automáticos para abrillantar son sistemas diseñados para mejorar la apariencia y el acabado superficial de diversos materiales mediante procesos controlados que realzan el brillo y la uniformidad de las piezas. Estos equipos automatizan lo que tradicionalmente era un proceso manual, optimizando la velocidad, precisión y consistencia del abrillantado en entornos industriales.
El principio de funcionamiento de estos equipos combina movimientos mecánicos repetitivos y precisos con la aplicación de compuestos abrasivos y abrillantadores específicos, permitiendo eliminar microimperfecciones, rayaduras superficiales y otros defectos menores. La acción controlada sobre la superficie consigue un acabado brillante y homogéneo, adecuado para piezas metálicas, plásticas, cerámicas, entre otros materiales.
Los equipos automáticos suelen contar con mesas giratorias, sistemas de brazo robotizado o mecanismos de pulido rotatorio que aseguran una cobertura uniforme de toda la superficie de la pieza. Además, la programación avanzada permite ajustar parámetros como la presión aplicada, la velocidad de rotación, el tiempo de abrillantado y la dosificación del compuesto, adaptándose a las necesidades específicas de cada producto y material.
Uno de los beneficios clave de estos equipos es la reducción significativa de la variabilidad en el acabado, garantizando que cada pieza cumpla con estándares de calidad rigurosos. Esto resulta esencial para sectores industriales donde la presentación y calidad superficial influyen directamente en la percepción del producto final, como en la fabricación de utensilios de cocina, componentes automotrices, electrodomésticos y artículos de consumo masivo.
Además, la automatización mejora las condiciones laborales al minimizar la exposición de los operarios a polvo, partículas y agentes químicos, aumentando la seguridad en el ambiente de trabajo. La integración de sistemas de extracción y filtración contribuye a mantener un entorno limpio y saludable.
La eficiencia en el consumo de materiales abrillantadores y la reducción de tiempos de proceso también representan ventajas económicas importantes, permitiendo a las empresas optimizar sus recursos y aumentar su capacidad productiva sin sacrificar la calidad.
Finalmente, muchos equipos automáticos para abrillantar están diseñados para integrarse fácilmente en líneas de producción existentes, ofreciendo flexibilidad y escalabilidad. Esto permite a las empresas adaptarse rápidamente a cambios en la demanda o en las especificaciones del producto, manteniendo una producción ágil y competitiva en mercados cada vez más exigentes.
Los equipos automáticos para abrillantar se caracterizan por su capacidad para realizar procesos repetitivos con alta precisión, lo que garantiza uniformidad en el acabado y reduce el margen de error asociado al trabajo manual. Esto es particularmente importante en piezas donde la estética es un factor determinante para el valor percibido del producto final.
La tecnología incorporada en estos equipos permite el ajuste dinámico de parámetros clave como la velocidad, presión y tiempo de abrillantado, lo que se traduce en una mayor flexibilidad para tratar distintos materiales y formas sin necesidad de realizar cambios mecánicos complejos. Esta adaptabilidad facilita la producción de lotes variados y la respuesta rápida a requerimientos específicos del cliente.
Además, estos sistemas cuentan con dispositivos integrados para la aplicación controlada de compuestos abrillantadores, lo que optimiza su uso y reduce desperdicios, contribuyendo así a una operación más sostenible y económica. La dosificación precisa evita el exceso de producto, que puede generar residuos difíciles de eliminar y afectar negativamente el proceso.
La integración de sensores y sistemas de monitoreo en tiempo real permite supervisar el estado del proceso, detectar posibles anomalías y ajustar parámetros de manera automática para mantener la calidad del acabado. Esta retroalimentación continua mejora la eficiencia y ayuda a prevenir defectos, reduciendo la necesidad de retrabajos o descartes.
En términos de seguridad, la automatización reduce la exposición directa de los operadores a partículas abrasivas y químicos, mejorando las condiciones laborales y cumpliendo con normativas de salud industrial. Los sistemas de extracción y filtración incorporados capturan los residuos generados durante el proceso, manteniendo el ambiente de trabajo limpio y seguro.
Estos equipos también pueden integrarse en sistemas de fabricación más amplios, formando parte de líneas automatizadas que incluyen procesos de limpieza, inspección y embalaje. Esta integración mejora la productividad global y permite un control más riguroso de la trazabilidad y calidad en cada etapa de la producción.
Finalmente, la inversión en equipos automáticos para abrillantar representa un avance tecnológico que no solo mejora la calidad estética de los productos, sino que también optimiza recursos, reduce costos operativos y aumenta la competitividad de las empresas en un mercado global donde la eficiencia y la excelencia en acabados son factores diferenciadores clave.
La implementación de equipos automáticos para abrillantar también contribuye a la reducción de tiempos de ciclo en los procesos de producción, lo que se traduce en una mayor capacidad para atender demandas elevadas sin comprometer la calidad. Al minimizar la intervención manual, se eliminan errores humanos y se agilizan las operaciones, favoreciendo entregas más rápidas y eficientes.
Estos sistemas permiten la programación de múltiples recetas o perfiles de abrillantado, lo que facilita el cambio rápido entre distintos tipos de productos o materiales sin necesidad de ajustes físicos complejos. Esta característica es esencial en plantas con producción diversificada o donde se requieren cambios frecuentes en las especificaciones del cliente.
La robustez y durabilidad de estos equipos aseguran una operación continua y confiable, incluso en ambientes industriales exigentes. Además, el mantenimiento preventivo y predictivo se ve facilitado por los sistemas de autodiagnóstico integrados, que alertan sobre el estado de componentes clave y permiten planificar intervenciones antes de que ocurran fallas mayores.
En sectores como el automotriz, electrodomésticos, joyería, artículos deportivos y utensilios de cocina, el acabado brillante es un factor crítico que impacta la percepción de calidad y valor. Por ello, el uso de equipos automáticos para abrillantar se ha convertido en un estándar para garantizar resultados homogéneos y que cumplan con los requisitos estéticos y funcionales de los productos.
La sostenibilidad también es un aspecto cada vez más valorado, y estos sistemas ayudan a disminuir el consumo de recursos y la generación de residuos, alineándose con prácticas responsables y normativas ambientales. La eficiencia energética y la reducción de desechos contribuyen a que las operaciones sean más amigables con el medio ambiente y económicamente viables.
En conclusión, los equipos automáticos para abrillantar representan una tecnología clave para la modernización y optimización de procesos industriales, combinando calidad, eficiencia, seguridad y sostenibilidad para satisfacer las demandas actuales y futuras del mercado.
Equipos de pulido automáticos
Los equipos de pulido automáticos son sistemas industriales diseñados para optimizar el proceso de acabado superficial de materiales y piezas mediante la automatización de las tareas de pulido. Estos equipos permiten obtener superficies uniformes, libres de imperfecciones y con acabados de alta calidad, reduciendo el esfuerzo manual y aumentando la productividad en la fabricación.
El pulido automático utiliza mecanismos precisos que controlan variables como la presión, velocidad, tiempo y tipo de abrasivo aplicado, garantizando que cada pieza reciba un tratamiento homogéneo y ajustado a sus características específicas. Esto es especialmente importante para materiales delicados o con formas complejas, donde el control del proceso evita daños y mejora el resultado final.
Los equipos pueden incluir mesas giratorias, robots industriales, brazos articulados o sistemas de pulido rotativos, que trabajan en combinación con compuestos abrasivos y pulidores especiales. La automatización de estos movimientos asegura una cobertura completa de la superficie, eliminando defectos como rayones, marcas o irregularidades superficiales.
Además, la incorporación de sensores y sistemas de control permite monitorear en tiempo real parámetros críticos del proceso, ajustar automáticamente las condiciones de trabajo y detectar posibles desviaciones. Esto no solo mejora la calidad del pulido, sino que también optimiza el uso de recursos y prolonga la vida útil de los consumibles.
En términos de seguridad, los equipos automáticos reducen la exposición de los operarios a polvo, partículas y agentes químicos, mejorando el ambiente laboral y cumpliendo con las normativas de seguridad industrial. La integración de sistemas de extracción y filtración de residuos contribuye a mantener el entorno limpio y saludable.
Estos equipos son ampliamente utilizados en industrias como la automotriz, aeroespacial, metalúrgica, fabricación de utensilios de cocina, electrónica y otras donde el acabado superficial es un factor crítico para la funcionalidad y la estética del producto final.
La versatilidad y adaptabilidad de los equipos de pulido automáticos permiten su implementación en líneas de producción diversas, desde pequeños lotes hasta grandes volúmenes, con la capacidad de ajustarse a distintos tamaños, formas y materiales. Esto representa una ventaja competitiva significativa para las empresas que buscan mejorar la calidad, reducir costos y aumentar la eficiencia operativa.
En resumen, los equipos de pulido automáticos constituyen una solución tecnológica avanzada que impulsa la modernización de los procesos industriales, ofreciendo acabados superiores, mayor productividad y condiciones de trabajo más seguras y sostenibles.
Los equipos de pulido automáticos destacan por su capacidad para ejecutar procesos repetitivos con una precisión constante, lo que resulta fundamental para garantizar la uniformidad y calidad del acabado en series de producción grandes o variadas. Al eliminar la variabilidad inherente al trabajo manual, estos sistemas aseguran que cada pieza cumpla con los estándares de acabado establecidos, minimizando defectos y retrabajos.
La flexibilidad es otra característica clave de estos equipos, ya que pueden ser programados para adaptarse a diferentes geometrías, materiales y requerimientos específicos del pulido. Esto permite a las empresas atender una amplia gama de productos sin la necesidad de realizar modificaciones complejas en la maquinaria, lo que se traduce en una mayor agilidad y reducción de tiempos de cambio entre lotes.
La integración de tecnologías como la robótica, la automatización avanzada y el control digital permite ajustar en tiempo real parámetros críticos como presión, velocidad y duración del pulido, optimizando el proceso según las condiciones detectadas. Esta capacidad de adaptación contribuye a maximizar la eficiencia, prolongar la vida útil de los abrasivos y reducir el consumo de recursos.
Además, los equipos automáticos suelen contar con sistemas incorporados para la aplicación dosificada de compuestos abrasivos y lubricantes, garantizando un uso racional de estos insumos y minimizando desperdicios. Esto no solo impacta positivamente en la reducción de costos operativos, sino que también ayuda a cumplir con estándares medioambientales cada vez más exigentes.
En cuanto a la seguridad y ergonomía, estos sistemas reducen significativamente la exposición de los operarios a condiciones potencialmente nocivas, como polvo, vibraciones o agentes químicos. La incorporación de dispositivos de extracción de polvo y filtración, así como la reducción de tareas manuales repetitivas, contribuye a mejorar las condiciones laborales y cumplir con normativas de salud ocupacional.
La capacidad para integrarse en líneas de producción automatizadas amplía las posibilidades de uso de los equipos de pulido automáticos, permitiendo su combinación con otros procesos como limpieza, inspección y embalaje. Esta integración favorece un flujo productivo continuo y eficiente, esencial para la competitividad en industrias donde la rapidez y calidad son claves.
En definitiva, los equipos de pulido automáticos representan una inversión estratégica para empresas que buscan optimizar sus procesos productivos, mejorar la calidad del producto final y garantizar un entorno de trabajo más seguro y sostenible, alineándose con las demandas actuales de la industria moderna.
Además de sus ventajas en precisión y eficiencia, los equipos de pulido automáticos permiten una trazabilidad completa del proceso gracias a la capacidad de registrar y almacenar datos operativos en tiempo real. Esto facilita el control de calidad, la identificación rápida de desviaciones y la implementación de mejoras continuas, aspectos fundamentales en industrias con altos estándares y certificaciones internacionales.
La reducción de tiempos muertos y paradas no planificadas es otra ventaja relevante, ya que muchos sistemas incluyen funciones de autodiagnóstico y mantenimiento predictivo. Estos mecanismos alertan sobre el desgaste o mal funcionamiento de componentes antes de que se produzcan fallas críticas, permitiendo una planificación proactiva de las intervenciones y asegurando una alta disponibilidad del equipo.
El diseño compacto y modular de muchos equipos automáticos de pulido facilita su instalación en distintos tipos de plantas industriales, optimizando el espacio y permitiendo la escalabilidad según las necesidades productivas. Además, la facilidad para reconfigurar y adaptar los equipos a nuevos productos o cambios en el proceso aporta una gran flexibilidad operativa.
En cuanto al impacto ambiental, el uso eficiente de abrasivos y compuestos, junto con sistemas de filtración y reciclaje, contribuye a minimizar la generación de residuos y emisiones contaminantes. Esto no solo responde a normativas cada vez más estrictas, sino que también forma parte de un compromiso empresarial hacia la sostenibilidad y la responsabilidad social.
En sectores donde la calidad estética y funcional es crítica —como en la fabricación de componentes electrónicos, piezas metálicas de precisión, o artículos de consumo premium—, los equipos automáticos de pulido aseguran resultados consistentes y repetibles que potencian la satisfacción del cliente y la reputación de la marca.
Por último, la continua evolución tecnológica impulsa la incorporación de innovaciones como inteligencia artificial, aprendizaje automático y conectividad IoT, que permiten optimizar aún más los procesos, anticipar necesidades de mantenimiento y adaptar el pulido en función de análisis avanzados. Estas tendencias aseguran que los equipos automáticos de pulido seguirán siendo una pieza clave en la transformación digital y la modernización de la industria.
Máquinas pulidoras automáticas
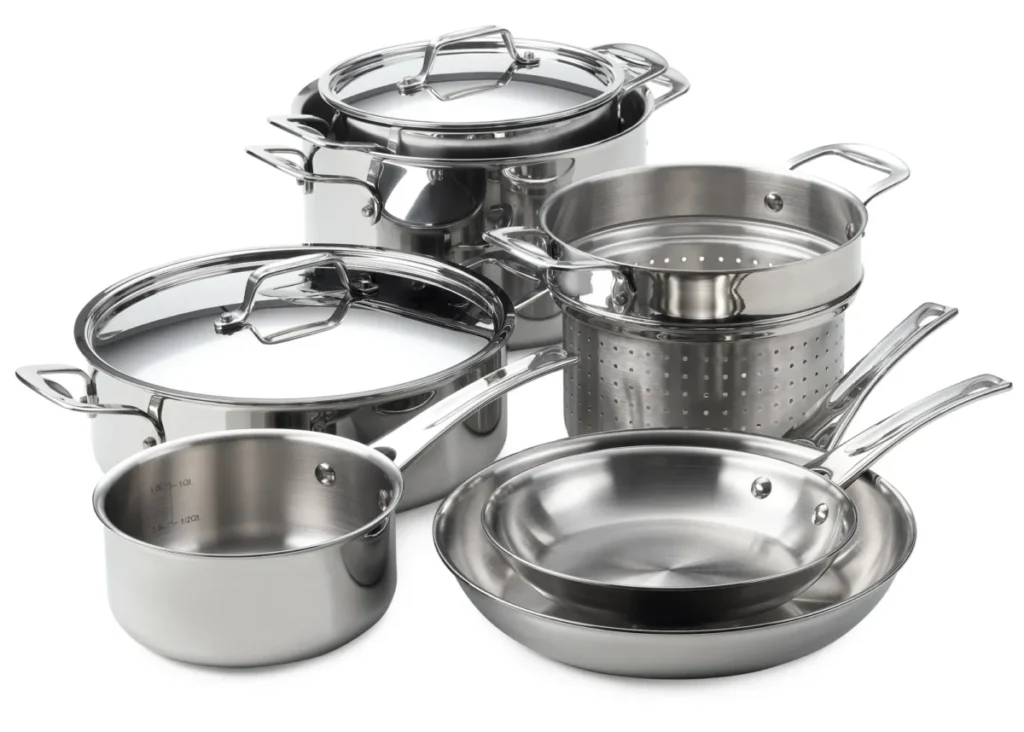
Las máquinas pulidoras automáticas son equipos industriales diseñados para realizar procesos de pulido de superficies de manera continua, precisa y eficiente, minimizando la intervención manual y mejorando la calidad del acabado final. Estas máquinas están especialmente desarrolladas para tratar una amplia variedad de materiales, incluyendo metales, plásticos, vidrios y cerámicas, adaptándose a diferentes formas y tamaños de piezas.
El funcionamiento de las máquinas pulidoras automáticas se basa en la combinación de movimientos controlados, como rotación, oscilación o traslación, junto con la aplicación de materiales abrasivos o compuestos especiales que permiten eliminar imperfecciones superficiales, rayaduras y asperezas, logrando un acabado liso, brillante y homogéneo. La programación avanzada y la automatización de los ciclos permiten ajustar parámetros clave como velocidad, presión, tiempo y tipo de abrasivo, optimizando el proceso para cada tipo de pieza.
Estas máquinas pueden estar equipadas con diferentes mecanismos, como mesas giratorias, cabezales rotativos, brazos robóticos o sistemas de pulido múltiple, que garantizan una cobertura completa y uniforme de la superficie a tratar. Además, la incorporación de sensores y sistemas de control digital permite monitorear el proceso en tiempo real, asegurando la consistencia y calidad del acabado.
Entre las ventajas principales de las máquinas pulidoras automáticas se destacan la mejora significativa en la productividad, ya que reducen el tiempo necesario para obtener acabados de alta calidad, y la disminución de la variabilidad que suele presentarse en procesos manuales. Esto es crucial para industrias que requieren acabados precisos y repetibles, como la automotriz, aeroespacial, fabricación de utensilios de cocina, joyería y electrónica.
Estas máquinas también contribuyen a mejorar la seguridad laboral, ya que minimizan la exposición de los operarios a polvo, partículas y agentes químicos presentes en los compuestos de pulido. Los sistemas integrados de extracción y filtración aseguran un ambiente de trabajo limpio y saludable, cumpliendo con las normativas vigentes en salud ocupacional.
Además, su diseño modular y adaptable facilita la integración en líneas de producción automatizadas, permitiendo combinarlas con otros procesos como lavado, inspección y embalaje, lo que optimiza el flujo productivo y reduce costos operativos. La capacidad para programar diferentes ciclos de pulido también proporciona flexibilidad para atender una amplia variedad de productos y lotes.
En conclusión, las máquinas pulidoras automáticas representan una tecnología clave para la modernización de los procesos industriales de acabado superficial, ofreciendo soluciones eficientes, seguras y de alta calidad que satisfacen las exigencias actuales del mercado y contribuyen a la competitividad de las empresas.
Las máquinas pulidoras automáticas son elementos esenciales en la industria moderna debido a su capacidad para combinar velocidad, precisión y repetibilidad en el proceso de acabado superficial. Al automatizar el pulido, se eliminan las variaciones propias del trabajo manual, lo que resulta en una producción más uniforme y con menor tasa de defectos. Esto es especialmente relevante en sectores donde la estética y funcionalidad de la pieza son críticas para su desempeño o aceptación en el mercado.
Estos equipos están diseñados para adaptarse a diferentes tipos de materiales y geometrías, permitiendo trabajar desde superficies planas hasta contornos complejos, gracias a la diversidad de cabezales y sistemas de movimiento que incorporan. La posibilidad de programar diferentes parámetros, como la presión ejercida, velocidad de rotación y duración del ciclo, facilita la optimización del proceso según las características particulares de cada pieza o lote.
La integración de sensores y sistemas de control digital permite un monitoreo constante del proceso, ajustando automáticamente las condiciones para mantener la calidad y eficiencia. Esto reduce el desperdicio de materiales abrasivos y compuestos, además de prolongar la vida útil de los consumibles, lo que representa un ahorro económico importante para la producción.
En términos de seguridad, la automatización del pulido reduce la exposición de los operarios a riesgos asociados, como la inhalación de polvo o el contacto directo con compuestos químicos. Los sistemas de extracción y filtración integrados en las máquinas ayudan a mantener un ambiente de trabajo limpio y seguro, cumpliendo con normativas de salud y seguridad industrial.
Las máquinas pulidoras automáticas también se benefician de un diseño modular y compacto, lo que facilita su instalación en diferentes entornos productivos y permite su integración con otras etapas del proceso industrial, como el lavado previo o la inspección posterior al pulido. Esta capacidad de integración contribuye a la creación de líneas de producción más eficientes y con mayor control sobre la calidad final del producto.
La adopción de estas máquinas se traduce en una mejora significativa en la productividad, ya que se reducen los tiempos de procesamiento y se incrementa la capacidad de producción sin comprometer la calidad. Además, permiten a las empresas responder con mayor agilidad a cambios en la demanda o requerimientos específicos de los clientes, gracias a la flexibilidad en la programación y configuración de los equipos.
En resumen, las máquinas pulidoras automáticas constituyen una inversión estratégica para cualquier industria que busque optimizar sus procesos de acabado, garantizar la uniformidad y calidad de sus productos, mejorar las condiciones laborales y avanzar hacia una producción más sostenible y competitiva.
Además, las máquinas pulidoras automáticas incorporan avances tecnológicos que permiten su conexión con sistemas de gestión y monitoreo centralizados, facilitando la supervisión remota y el análisis de datos para la toma de decisiones informadas. Esta conectividad contribuye a la implementación de estrategias de mantenimiento predictivo, evitando paradas no planificadas y extendiendo la vida útil de los equipos.
La precisión en los movimientos y la repetibilidad que ofrecen estas máquinas aseguran que incluso piezas con tolerancias muy estrictas puedan ser procesadas sin riesgo de sobrepulido o daños superficiales. Esto es vital en sectores como el aeroespacial o la fabricación de componentes médicos, donde los estándares de calidad son sumamente rigurosos.
Otro aspecto relevante es la reducción del impacto ambiental, ya que la automatización permite un uso más eficiente de los materiales abrasivos y los compuestos utilizados, minimizando residuos y emisiones contaminantes. Los sistemas modernos también incluyen mecanismos para la recolección y tratamiento de polvo y partículas, promoviendo prácticas industriales más limpias y responsables.
El diseño ergonómico de estas máquinas reduce la carga física sobre los operarios, quienes pueden centrarse en la supervisión y control del proceso, mejorando así la productividad y disminuyendo el riesgo de lesiones laborales. Además, la capacitación requerida para operar estos sistemas es más accesible, facilitando la incorporación de personal y mejorando la flexibilidad operativa.
En cuanto a la versatilidad, las máquinas pulidoras automáticas permiten el procesamiento de una amplia variedad de piezas, desde componentes pequeños y delicados hasta grandes estructuras metálicas, adaptándose a las necesidades específicas de cada industria. Esta adaptabilidad representa una ventaja competitiva importante, ya que posibilita atender distintos mercados y requerimientos sin la necesidad de múltiples equipos especializados.
Finalmente, el constante desarrollo tecnológico impulsa la incorporación de inteligencia artificial y aprendizaje automático en estos sistemas, abriendo nuevas posibilidades para la optimización continua del proceso de pulido, la detección temprana de fallas y la mejora de la calidad del producto final. Así, las máquinas pulidoras automáticas no solo responden a las demandas actuales, sino que también están preparadas para los retos futuros de la industria.
Equipos automatizados de pulido
Los equipos automatizados de pulido representan una evolución significativa en los procesos de acabado superficial industrial, combinando tecnología avanzada y precisión para lograr resultados consistentes y de alta calidad. Estos sistemas están diseñados para realizar tareas de pulido de manera autónoma o semiautónoma, integrando mecanismos mecánicos, eléctricos y de control que optimizan cada etapa del proceso.
Una de las principales ventajas de los equipos automatizados es la capacidad de manejar grandes volúmenes de producción con uniformidad y rapidez, superando las limitaciones del trabajo manual y minimizando errores humanos. Esto se traduce en una mejora notable en la eficiencia productiva y en la reducción de costos asociados a retrabajos o desperdicios.
Estos equipos suelen contar con componentes como mesas giratorias, cabezales de pulido múltiples, sistemas robotizados y actuadores programables que permiten abordar piezas con diferentes formas, tamaños y materiales. La flexibilidad de programación es fundamental para adaptar el proceso a las especificaciones técnicas y estéticas requeridas, así como para cambiar rápidamente entre diferentes tipos de piezas o lotes.
Además, la incorporación de sensores y sistemas de retroalimentación en tiempo real permite monitorear variables críticas como presión, velocidad, temperatura y desgaste de abrasivos, ajustando automáticamente las condiciones de trabajo para mantener la calidad y prolongar la vida útil de los consumibles. Esta capacidad de adaptación contribuye a optimizar recursos y a asegurar un acabado homogéneo en cada pieza.
Los equipos automatizados de pulido también mejoran las condiciones de trabajo, reduciendo la exposición de los operarios a polvo, vibraciones y productos químicos, gracias a sistemas integrados de extracción y filtración. Esto contribuye a cumplir con normativas de seguridad y salud ocupacional, además de fomentar un ambiente laboral más seguro y confortable.
La integración de estos equipos en líneas de producción automatizadas permite una mayor sincronización con otros procesos, como limpieza, inspección y embalaje, facilitando un flujo continuo y eficiente. Asimismo, la capacidad para recopilar y analizar datos operativos favorece la implementación de estrategias de mejora continua y mantenimiento predictivo.
En definitiva, los equipos automatizados de pulido son una solución tecnológica que impulsa la modernización industrial, ofreciendo beneficios tangibles en términos de calidad, productividad, seguridad y sostenibilidad, y posicionando a las empresas para afrontar con éxito los desafíos del mercado actual y futuro.
Los equipos automatizados de pulido se caracterizan por su precisión y capacidad para operar de manera ininterrumpida, lo que incrementa la productividad y reduce significativamente los tiempos de ciclo en comparación con los métodos manuales tradicionales. Esta automatización permite mantener un nivel constante de calidad en el acabado superficial, fundamental para sectores que demandan alta repetibilidad y estándares rigurosos, como la fabricación de componentes metálicos, automotrices, aeroespaciales y electrónicos.
El diseño modular y configurable de estos sistemas facilita su adaptación a diferentes procesos y tipos de productos, desde piezas pequeñas con detalles complejos hasta grandes componentes planos o curvos. La implementación de tecnología robótica en algunos equipos permite realizar movimientos precisos y complejos, alcanzando zonas difíciles y asegurando una cobertura total sin dañar la pieza.
La capacidad de integrar sensores inteligentes y sistemas de control digital permite una supervisión constante del proceso, detectando posibles desviaciones o fallas y ajustando automáticamente parámetros como velocidad, presión o tiempo de pulido. Esto no solo optimiza el uso de consumibles, sino que también mejora la eficiencia energética y reduce el impacto ambiental al minimizar el desperdicio de materiales y la generación de residuos.
Desde el punto de vista operativo, los equipos automatizados mejoran la seguridad laboral al reducir la necesidad de intervención directa en tareas que pueden ser riesgosas por la exposición a polvo, agentes químicos o vibraciones. Los sistemas incorporados de extracción de polvo y filtración garantizan un ambiente de trabajo limpio y conforme a las normativas de salud ocupacional, mientras que la reducción de tareas repetitivas disminuye el riesgo de lesiones musculoesqueléticas.
La posibilidad de integrar estos equipos en sistemas de manufactura más amplios, incluyendo líneas de producción completamente automatizadas, facilita la coordinación y sincronización con otros procesos industriales. Esto permite un flujo productivo continuo, mejor control de calidad y una respuesta más ágil ante cambios en la demanda o en las especificaciones del producto.
Adicionalmente, la recolección y análisis de datos operativos proporcionan información valiosa para la toma de decisiones estratégicas, desde el mantenimiento predictivo hasta la optimización de procesos y la mejora continua. La digitalización y conexión en red de estos equipos forman parte de la transformación hacia fábricas inteligentes y más sostenibles.
En resumen, los equipos automatizados de pulido son una herramienta indispensable para la industria moderna, permitiendo alcanzar altos niveles de calidad, eficiencia y seguridad, al tiempo que responden a las crecientes exigencias del mercado y las normativas ambientales y laborales vigentes. Su implementación representa una inversión que potencia la competitividad y sostenibilidad de las empresas en un entorno industrial cada vez más exigente y dinámico.
Estos equipos automatizados de pulido también facilitan la estandarización de los procesos productivos, lo cual es fundamental para garantizar la uniformidad en series grandes de producción. La eliminación de la variabilidad inherente al trabajo manual contribuye a reducir rechazos y retrabajos, lo que se traduce en ahorros significativos y una mejora en la rentabilidad.
Otra ventaja importante radica en la flexibilidad que ofrecen estos sistemas para adaptarse rápidamente a nuevos diseños o cambios en las especificaciones del producto. A través de software de control avanzado, es posible modificar los parámetros de pulido, configurar nuevos ciclos y ajustar movimientos con rapidez, sin necesidad de cambios físicos complejos en el equipo, lo que agiliza la respuesta ante requerimientos variables del mercado.
La automatización también permite una mejor gestión del consumo de materiales abrasivos y pulidores, optimizando su uso para minimizar desperdicios y costos. Esta eficiencia contribuye además a reducir la generación de residuos sólidos y líquidos, alineándose con políticas de producción más limpias y responsables desde el punto de vista ambiental.
En términos de mantenimiento, la incorporación de tecnologías de autodiagnóstico y monitoreo continuo facilita la identificación temprana de desgastes o fallos, permitiendo programar intervenciones de manera oportuna y evitando paradas inesperadas que pueden afectar la productividad. Esto mejora la disponibilidad y confiabilidad de los equipos, aspectos clave en entornos industriales exigentes.
Desde la perspectiva del capital humano, la automatización del pulido libera a los operarios de tareas repetitivas y físicamente demandantes, permitiendo que se enfoquen en actividades de supervisión, control de calidad y mejora continua. Esto puede incrementar la satisfacción laboral y reducir la rotación de personal, generando un impacto positivo en la organización.
Finalmente, la inversión en equipos automatizados de pulido representa una estrategia integral que contribuye no solo a mejorar la calidad y productividad, sino también a fortalecer la competitividad de las empresas en mercados globalizados, donde la eficiencia, la innovación tecnológica y el compromiso con la sostenibilidad son factores decisivos para el éxito a largo plazo.
Dispositivos automáticos para pulido
Los dispositivos automáticos para pulido son sistemas diseñados para realizar procesos de acabado superficial con mínima intervención manual, garantizando uniformidad, rapidez y alta calidad en el resultado final. Estos dispositivos pueden variar desde unidades compactas y específicas para tareas puntuales hasta sistemas integrados en líneas de producción automatizadas que manejan grandes volúmenes de piezas.
Estos dispositivos funcionan combinando movimientos controlados —ya sean rotativos, oscilatorios o lineales— con la aplicación de abrasivos o compuestos de pulido adecuados para el material y acabado deseado. La automatización permite ajustar parámetros clave como la presión aplicada, la velocidad y el tiempo de pulido, adaptándose a las características específicas de cada pieza y optimizando el proceso para obtener acabados precisos y homogéneos.
La incorporación de tecnología avanzada, como sensores de fuerza y posición, sistemas de control digital y retroalimentación en tiempo real, permite monitorizar y corregir automáticamente las condiciones de trabajo, mejorando la eficiencia y evitando daños o defectos en las superficies pulidas. Esto resulta especialmente importante en la fabricación de componentes delicados o con requerimientos estrictos de calidad.
Además, los dispositivos automáticos para pulido mejoran notablemente las condiciones de seguridad y salud en el ambiente laboral, al minimizar la exposición directa de los operarios a polvo, vibraciones y productos químicos. Muchos dispositivos cuentan con sistemas integrados de extracción y filtración, garantizando un entorno de trabajo limpio y conforme a las normativas vigentes.
Estos dispositivos se utilizan en diversos sectores industriales, desde la producción de piezas metálicas, plásticas y vidrios hasta la fabricación de productos electrónicos, joyería, automoción y aeroespacial, adaptándose a una amplia gama de geometrías y materiales. Su versatilidad y eficiencia hacen que sean una herramienta fundamental para mejorar la productividad y la calidad en procesos industriales modernos.
En resumen, los dispositivos automáticos para pulido constituyen una solución tecnológica esencial que optimiza el proceso de acabado superficial, ofreciendo ventajas significativas en términos de precisión, velocidad, seguridad y sostenibilidad, y posicionando a las empresas para competir eficazmente en mercados exigentes.
Estos dispositivos automáticos para pulido destacan por su capacidad para integrarse en diferentes etapas del proceso productivo, lo que permite una sincronización eficiente con otras operaciones como el lavado, secado o inspección de las piezas. Esta integración contribuye a la creación de líneas de producción continuas y altamente automatizadas, donde el pulido se realiza de forma fluida y sin interrupciones, aumentando así la capacidad y consistencia del proceso.
El uso de sistemas robotizados dentro de estos dispositivos permite una gran flexibilidad y precisión en la manipulación y pulido de piezas con geometrías complejas o delicadas. Los robots pueden programarse para realizar movimientos específicos y repetitivos con alta exactitud, asegurando que cada superficie reciba el tratamiento adecuado sin riesgo de daños ni variaciones en la calidad.
Además, la aplicación de software avanzado y sistemas de control inteligentes posibilita el monitoreo constante y la adaptación dinámica de los parámetros de pulido. Esto significa que los dispositivos pueden ajustarse automáticamente ante cambios en la condición de la pieza o el desgaste de los abrasivos, optimizando recursos y manteniendo estándares elevados de acabado sin necesidad de intervención constante.
Desde una perspectiva ambiental, estos dispositivos promueven un uso más eficiente de materiales y energía, contribuyendo a la reducción de residuos y emisiones contaminantes. La optimización del consumo de abrasivos y compuestos de pulido, junto con sistemas de recolección y filtración integrados, minimiza el impacto ambiental del proceso, alineándose con políticas industriales sostenibles.
En el ámbito de la seguridad laboral, la automatización del pulido reduce la exposición de los trabajadores a riesgos físicos y químicos asociados a estas tareas, como el contacto con partículas finas, vibraciones y movimientos repetitivos. Esto mejora las condiciones de trabajo y cumple con regulaciones estrictas de salud y seguridad, favoreciendo un entorno más saludable y productivo.
Por último, la implementación de dispositivos automáticos para pulido representa una inversión estratégica para las empresas que buscan aumentar su competitividad mediante la mejora continua de sus procesos productivos. La combinación de mayor calidad, eficiencia, seguridad y sostenibilidad posiciona a estas tecnologías como pilares fundamentales en la modernización y digitalización de la industria manufacturera actual y futura.
La evolución constante de los dispositivos automáticos para pulido también ha impulsado la incorporación de tecnologías emergentes como la inteligencia artificial y el aprendizaje automático. Estas innovaciones permiten que los sistemas analicen grandes cantidades de datos operativos para identificar patrones, predecir posibles fallos y ajustar los parámetros de pulido en tiempo real, mejorando la precisión y eficiencia del proceso sin necesidad de intervención humana directa.
Asimismo, la conectividad a través de redes industriales y plataformas de Internet de las cosas (IoT) facilita la integración de estos dispositivos dentro de entornos de fabricación inteligentes o “fábricas 4.0”. Esto permite no solo el control remoto y la supervisión en tiempo real, sino también la recopilación de datos históricos para optimizar el mantenimiento, planificar la producción y mejorar la trazabilidad de los productos.
En términos de aplicación, los dispositivos automáticos de pulido son cada vez más versátiles, capaces de adaptarse a distintos materiales, desde metales duros y aleaciones complejas hasta plásticos, vidrios y composites. Esta capacidad multipropósito amplía su alcance en sectores tan diversos como la industria automotriz, aeroespacial, electrónica, médica y de bienes de consumo.
Además, el diseño ergonómico y modular de muchos dispositivos permite una fácil instalación y mantenimiento, reduciendo los tiempos de parada y facilitando su actualización tecnológica. Esto es clave para mantener la competitividad en un mercado donde las demandas de calidad y eficiencia están en constante crecimiento.
Finalmente, el desarrollo sostenible es un factor cada vez más central en la industria, y los dispositivos automáticos para pulido responden a esta necesidad mediante la reducción del consumo energético, la minimización de residuos y la optimización del uso de materiales abrasivos y pulidores. Esto no solo beneficia al medio ambiente, sino que también representa un ahorro económico importante para las empresas.
En resumen, la continua innovación y adaptación de los dispositivos automáticos para pulido consolidan su papel como elementos indispensables en la modernización industrial, mejorando la calidad del producto final, la eficiencia operativa y la sostenibilidad, aspectos fundamentales para afrontar los retos y oportunidades del mercado global actual.
Sistemas automáticos para pulir
Los sistemas automáticos para pulir son soluciones tecnológicas diseñadas para optimizar y estandarizar los procesos de acabado superficial en la industria manufacturera. Estos sistemas integran componentes mecánicos, electrónicos y de control para ejecutar de manera autónoma las operaciones de pulido, garantizando resultados uniformes y de alta calidad en una amplia variedad de materiales y formas.
Estos sistemas están compuestos generalmente por estaciones de trabajo automatizadas que pueden incluir mesas giratorias, robots articulados, cabezales de pulido múltiples y dispositivos de sujeción específicos para cada tipo de pieza. La programación avanzada permite ajustar parámetros como velocidad, presión, trayectoria y tiempo de pulido para adaptarse a los requerimientos técnicos y estéticos de cada producto.
Una característica fundamental de los sistemas automáticos para pulir es su capacidad para monitorear y ajustar en tiempo real las condiciones del proceso mediante sensores y software especializado. Esto asegura la correcta aplicación del pulido, previniendo defectos como sobrepulido, marcas o desgaste irregular, y prolongando la vida útil de los consumibles.
Además, estos sistemas permiten la integración con otras etapas del proceso productivo, facilitando la creación de líneas de producción totalmente automatizadas que incluyen limpieza, inspección y embalaje, lo que mejora la eficiencia global y reduce los tiempos de ciclo.
La automatización del pulido también impacta positivamente en la seguridad y salud laboral, ya que minimiza la exposición de los operarios a riesgos asociados al manejo manual, como el contacto con abrasivos, polvo y vibraciones. Los sistemas suelen incorporar mecanismos de extracción de polvo y filtros para mantener un ambiente de trabajo limpio y seguro.
Desde el punto de vista económico, la implementación de sistemas automáticos para pulir reduce costos operativos mediante la optimización del uso de materiales y la reducción de rechazos y retrabajos. Su flexibilidad y capacidad para adaptarse a diferentes lotes y diseños facilitan la respuesta ágil a las demandas del mercado.
En conclusión, los sistemas automáticos para pulir representan una solución avanzada y eficiente que contribuye a elevar los estándares de calidad, productividad y sostenibilidad en la industria, posicionando a las empresas para competir con éxito en un entorno cada vez más exigente y tecnificado.
Estos sistemas automáticos para pulir se destacan por su versatilidad y capacidad de adaptación a diversas aplicaciones industriales, desde piezas pequeñas y delicadas hasta componentes grandes y complejos. La incorporación de tecnologías robóticas permite realizar movimientos precisos y repetitivos, alcanzando áreas difíciles de acceder mediante métodos convencionales, lo que asegura un acabado uniforme y de alta calidad en toda la superficie.
El uso de sensores inteligentes y software avanzado posibilita la supervisión constante del proceso, ajustando automáticamente variables como la presión aplicada, la velocidad de rotación o el tiempo de contacto del abrasivo con la pieza. Esto no solo optimiza el rendimiento, sino que también previene daños o excesos en el pulido, lo que a su vez prolonga la vida útil de los consumibles y reduce costos.
Estos sistemas facilitan la integración en líneas de producción más amplias, permitiendo la sincronización con procesos complementarios como el lavado, el secado o la inspección automatizada. Esta capacidad de integración contribuye a crear flujos productivos continuos y eficientes, mejorando la productividad y reduciendo tiempos muertos o cuellos de botella.
En términos de seguridad y medio ambiente, los sistemas automáticos para pulir incorporan dispositivos de extracción y filtración de polvo y partículas, lo que protege la salud de los operarios y cumple con normativas ambientales. Además, al minimizar la intervención manual en procesos que pueden ser físicamente demandantes o peligrosos, se mejora significativamente el entorno laboral.
La implementación de estos sistemas también representa una inversión estratégica para las empresas, ya que incrementa la competitividad al mejorar la calidad del producto final y la eficiencia operativa. La capacidad para adaptarse rápidamente a cambios en el diseño o en los requisitos de acabado permite responder con agilidad a las demandas del mercado, manteniendo la flexibilidad necesaria en entornos industriales dinámicos.
Finalmente, la recopilación de datos y el análisis de rendimiento mediante tecnologías digitales facilitan la mejora continua y el mantenimiento predictivo, asegurando que los sistemas operen siempre en condiciones óptimas. Esto reduce paradas no planificadas, optimiza costos y maximiza la rentabilidad, consolidando a los sistemas automáticos para pulir como una herramienta clave en la modernización y sostenibilidad de la manufactura contemporánea.
Además, los sistemas automáticos para pulir suelen diseñarse con modularidad, lo que permite adaptarlos y expandirlos según las necesidades específicas de producción. Esta característica facilita la incorporación de nuevas estaciones o la actualización tecnológica sin necesidad de reemplazar todo el sistema, ofreciendo una solución escalable y adaptable al crecimiento o diversificación de la empresa.
El control digital avanzado posibilita la creación de programas personalizados para distintos tipos de piezas, materiales y acabados, brindando una gran flexibilidad operativa. Esto resulta especialmente útil en industrias donde los productos cambian frecuentemente o donde se requieren lotes pequeños con alta precisión, optimizando recursos y tiempos de preparación.
La ergonomía y seguridad también son prioridades en el diseño de estos sistemas, ya que reducen la exposición de los operadores a movimientos repetitivos y riesgos asociados al pulido manual. El uso de cabinas cerradas, sistemas automáticos de carga y descarga, y sensores de presencia garantizan un entorno de trabajo seguro y confortable, mejorando al mismo tiempo la productividad.
Desde la perspectiva de sostenibilidad, los sistemas automáticos para pulir contribuyen a la reducción del consumo energético y de materiales abrasivos, gracias a su precisión y control. La posibilidad de reciclar o reutilizar compuestos y de manejar residuos de forma controlada disminuye el impacto ambiental, alineándose con los estándares y políticas globales de producción limpia y responsable.
Por último, la integración con sistemas de gestión y análisis de datos permite un seguimiento exhaustivo del rendimiento y calidad del proceso, facilitando la toma de decisiones basadas en información precisa y actualizada. Esto potencia la eficiencia operativa y la competitividad, haciendo que los sistemas automáticos para pulir sean una inversión clave
Las máquinas automáticas de pulido son equipos diseñados para llevar a cabo procesos de acabado superficial con un alto grado de precisión y repetibilidad, minimizando la intervención manual y optimizando la productividad en diferentes sectores industriales. Estas máquinas combinan elementos mecánicos, eléctricos y de control para realizar movimientos coordinados que permiten pulir, abrillantar o alisar superficies de manera uniforme y eficiente.
Estas máquinas están equipadas con sistemas de accionamiento que pueden incluir motores eléctricos, servomotores o actuadores neumáticos, los cuales controlan cabezales de pulido que se desplazan siguiendo trayectorias programadas. Además, cuentan con dispositivos de sujeción y posicionamiento que aseguran la correcta fijación y orientación de las piezas durante el proceso, lo que resulta fundamental para lograr acabados consistentes.
Un aspecto clave de las máquinas automáticas de pulido es la capacidad de ajustar parámetros como la presión aplicada, la velocidad de pulido y el tiempo de contacto según el tipo de material y acabado requerido. Esto se logra mediante sistemas de control electrónico y software especializado, que permiten programar ciclos específicos adaptados a diferentes productos o lotes.
La incorporación de sensores y sistemas de monitoreo en tiempo real posibilita la detección de anomalías, el control de desgaste de los abrasivos y la regulación dinámica del proceso, garantizando resultados de alta calidad y reduciendo desperdicios. Esto también contribuye a prolongar la vida útil de los consumibles y a optimizar los costos operativos.
Las máquinas automáticas de pulido se utilizan en industrias tan variadas como la metalúrgica, automotriz, electrónica, aeroespacial, y de fabricación de bienes de consumo, donde la calidad del acabado superficial es un factor determinante para el desempeño y la estética de los productos. Su capacidad para trabajar con diferentes materiales —metales, plásticos, vidrios, entre otros— y geometrías complejas las hace altamente versátiles.
Además, estas máquinas mejoran las condiciones de trabajo al reducir la exposición directa de los operarios a riesgos físicos y químicos, tales como polvo, vibraciones y manipulación repetitiva. Muchos modelos incluyen sistemas integrados de extracción y filtración para mantener un ambiente limpio y seguro, cumpliendo con normativas de salud y seguridad industrial.
En resumen, las máquinas automáticas de pulido representan una solución tecnológica avanzada que incrementa la eficiencia, calidad y seguridad en los procesos de acabado superficial, contribuyendo significativamente a la competitividad y sostenibilidad de las operaciones industriales modernas.
Las máquinas automáticas de pulido han evolucionado considerablemente gracias a la integración de tecnologías de control digital y robótica avanzada, lo que les permite ejecutar movimientos precisos y adaptarse rápidamente a diferentes tipos de piezas y acabados. Esto es especialmente útil en la producción en serie, donde la repetibilidad y la uniformidad del acabado son cruciales para mantener altos estándares de calidad. La programación flexible de estos equipos permite configurar parámetros específicos para cada lote o modelo, garantizando resultados consistentes sin necesidad de ajustes manuales frecuentes.
La automatización en el pulido también ofrece ventajas significativas en términos de ahorro de tiempo y costos operativos. Al reducir la dependencia de la intervención humana, se minimizan errores y variaciones en el proceso, al mismo tiempo que se acelera el ritmo productivo. Esto es vital en sectores donde los plazos de entrega son estrictos y la demanda de productos con acabados impecables es alta, como en la industria automotriz, aeroespacial o médica.
En cuanto al diseño, muchas máquinas automáticas de pulido están concebidas con estructuras modulares que facilitan su integración en líneas de producción existentes o futuras. Esta modularidad permite agregar o modificar componentes, como sistemas de carga y descarga automática, estaciones de inspección o dispositivos de limpieza, adaptándose a las necesidades específicas de cada planta. Además, el mantenimiento preventivo y predictivo se optimiza mediante sensores que monitorean el estado de los componentes críticos, evitando paradas inesperadas y prolongando la vida útil del equipo.
La ergonomía y seguridad son elementos prioritarios en estas máquinas. Al automatizar tareas que pueden ser físicamente exigentes o peligrosas, como la manipulación de piezas pesadas o el contacto con abrasivos y productos químicos, se reduce el riesgo de lesiones laborales. La incorporación de sistemas de protección, alarmas y controles de acceso asegura un entorno de trabajo seguro y conforme a normativas vigentes.
Otra ventaja destacada es el impacto ambiental positivo que generan estas máquinas automáticas. Su precisión y control permiten optimizar el consumo de materiales abrasivos y productos auxiliares, reduciendo residuos y emisiones contaminantes. Asimismo, muchas cuentan con sistemas integrados de extracción y filtración de polvo que contribuyen a mantener la calidad del aire en el entorno laboral y a cumplir con regulaciones ambientales cada vez más estrictas.
Finalmente, la digitalización y conectividad de estas máquinas abren nuevas posibilidades para la gestión y mejora continua del proceso. La recopilación y análisis de datos en tiempo real permiten identificar oportunidades de optimización, ajustar parámetros de manera proactiva y realizar mantenimientos más eficientes. Esto se traduce en una mayor competitividad para las empresas que las implementan, al combinar calidad superior, eficiencia operativa y sostenibilidad en sus procesos de pulido.
Equipos automáticos de pulido
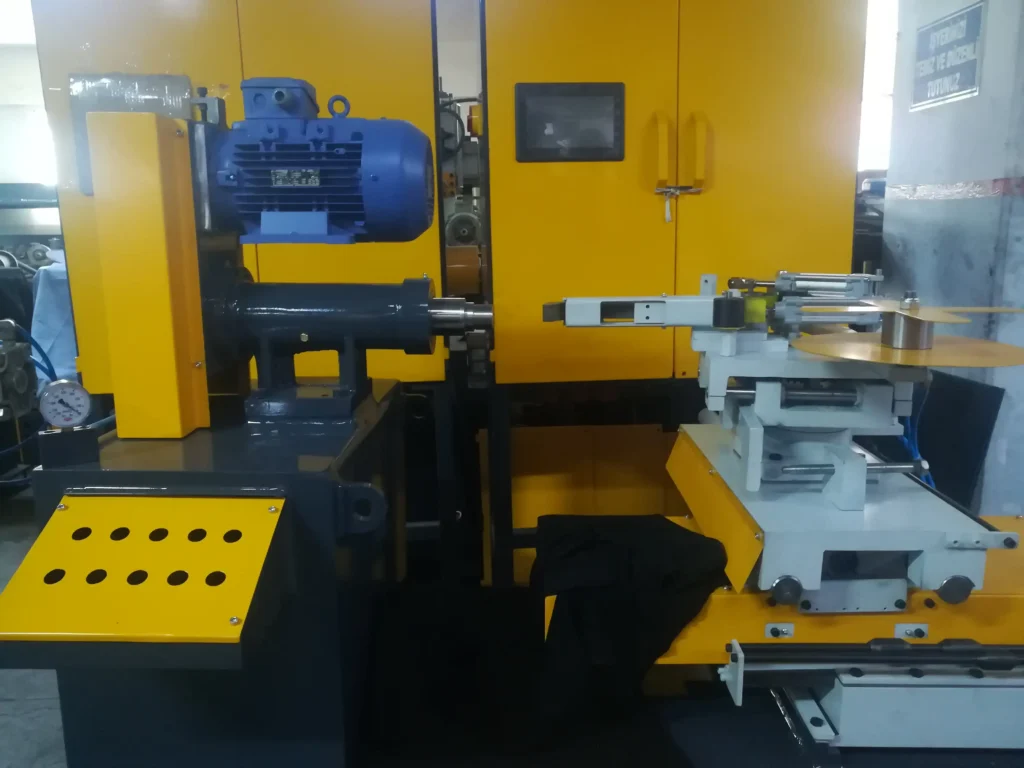
Los equipos automáticos de pulido están diseñados para optimizar y automatizar el proceso de acabado superficial en diferentes industrias, ofreciendo soluciones eficientes, precisas y consistentes. Estos equipos combinan tecnología mecánica, electrónica y de control para realizar tareas de pulido, abrillantado y lijado con mínima intervención humana, lo que mejora la calidad del producto y reduce tiempos de producción.
Los sistemas automáticos de pulido incluyen componentes como mesas giratorias indexadas, robots articulados, cabezales de pulido múltiples y dispositivos de sujeción adaptados a diferentes tipos y tamaños de piezas. La programación avanzada permite ajustar parámetros críticos como velocidad, presión, trayectoria y tiempo de contacto, adaptándose a las necesidades específicas de cada material y acabado deseado.
La integración de sensores inteligentes y software especializado posibilita la monitorización en tiempo real del proceso, ajustando automáticamente las variables para evitar defectos, controlar el desgaste de los abrasivos y optimizar el consumo de materiales. Esto resulta en una mayor uniformidad del acabado y prolonga la vida útil de los consumibles.
Estos equipos facilitan la incorporación en líneas de producción automatizadas, integrándose con procesos complementarios como limpieza, inspección y embalaje, aumentando la eficiencia global y reduciendo los tiempos muertos. Además, mejoran las condiciones laborales al reducir la exposición de los operarios a riesgos físicos y químicos.
En términos de sostenibilidad, los equipos automáticos de pulido contribuyen a disminuir el consumo energético y de recursos, y cuentan con sistemas de extracción y filtración de polvo que protegen el medio ambiente y cumplen con normativas vigentes.
En resumen, los equipos automáticos de pulido representan una solución avanzada que mejora la calidad, productividad y seguridad en los procesos industriales de acabado superficial, permitiendo a las empresas mantenerse competitivas en un mercado cada vez más exigente.
Los equipos automáticos de pulido incorporan tecnologías modernas que permiten una gran precisión y repetibilidad en el proceso de acabado, adaptándose a diferentes formas, tamaños y materiales. Su diseño modular facilita la personalización y expansión según las necesidades específicas de producción, permitiendo integrar estaciones adicionales o actualizar componentes sin interrumpir el flujo productivo. La programación flexible de estos sistemas posibilita la ejecución de ciclos de pulido específicos para cada tipo de pieza, optimizando tiempos y recursos, lo que resulta esencial en industrias con productos variados o en lotes pequeños.
La automatización reduce considerablemente la dependencia del trabajo manual, lo que no solo acelera el ritmo de producción sino que también minimiza errores y variaciones en la calidad del acabado. Esto es especialmente importante en sectores donde la estética y el rendimiento del producto final son críticos, como en la fabricación de componentes automotrices, electrónicos o de dispositivos médicos. Además, al limitar la intervención humana en tareas repetitivas o físicamente exigentes, estos equipos contribuyen a mejorar la seguridad y bienestar de los operarios, reduciendo riesgos asociados a la manipulación directa de herramientas abrasivas, exposición a polvo o vibraciones prolongadas.
Otra ventaja destacable es el impacto ambiental positivo derivado del uso eficiente de abrasivos y consumibles, así como la implementación de sistemas de extracción y filtración que mantienen el aire limpio en las instalaciones y cumplen con regulaciones ambientales. Esto refleja un compromiso creciente con la sostenibilidad en los procesos industriales modernos. La incorporación de sensores y sistemas de monitoreo en tiempo real permite ajustar dinámicamente los parámetros del proceso, lo que ayuda a prevenir defectos, alargar la vida útil de los componentes y optimizar el uso de energía y materiales.
Finalmente, la conectividad y digitalización de estos equipos facilitan la recopilación y análisis de datos, apoyando la toma de decisiones basada en información precisa para la mejora continua y el mantenimiento predictivo. Esto no solo reduce tiempos de inactividad y costos asociados, sino que también fortalece la capacidad competitiva de las empresas al ofrecer productos con acabados superiores, fabricados de manera eficiente y sostenible. En conjunto, los equipos automáticos de pulido se consolidan como una herramienta esencial para la modernización y optimización de los procesos industriales de acabado superficial.
Además, los equipos automáticos de pulido suelen estar diseñados para operar en entornos industriales exigentes, soportando largas jornadas de trabajo con alta precisión y fiabilidad. Esto se logra gracias a la utilización de materiales resistentes y componentes de calidad, así como a sistemas de enfriamiento y lubricación que garantizan un funcionamiento óptimo y prolongan la vida útil de las máquinas. La robustez del equipo permite mantener la consistencia del acabado incluso en procesos de producción intensivos, lo cual es fundamental para cumplir con los estándares de calidad más estrictos.
La implementación de interfaces intuitivas y sistemas de control avanzados facilita la programación y operación de los equipos, permitiendo a los operadores configurar y supervisar los procesos de manera sencilla y eficiente. Muchas máquinas cuentan con pantallas táctiles, controles remotos y acceso a plataformas digitales para el monitoreo y ajuste en tiempo real, lo que mejora la flexibilidad y rapidez en la adaptación a nuevos requerimientos o cambios en la producción.
El enfoque en la ergonomía y seguridad no solo protege a los trabajadores, sino que también contribuye a reducir el desgaste físico y mental asociado con tareas repetitivas y exigentes. La automatización del pulido minimiza la exposición a agentes nocivos, vibraciones y movimientos forzados, creando un ambiente de trabajo más saludable y productivo. Además, los sistemas automáticos pueden incluir funciones de autodiagnóstico y alertas que anticipan fallas o mantenimiento necesario, lo que mejora la confiabilidad y reduce tiempos de paro.
Por último, la integración de tecnologías emergentes como la inteligencia artificial y el aprendizaje automático comienza a transformar estos equipos, permitiendo optimizar aún más los procesos mediante análisis predictivos y ajustes automáticos basados en datos históricos y condiciones actuales. Esto abre nuevas posibilidades para la mejora continua, la personalización del acabado y la eficiencia operativa, posicionando a los equipos automáticos de pulido como una inversión estratégica para la industria del futuro, que busca combinar calidad, productividad y sostenibilidad en sus procesos productivos.
Producción de máquinas automáticas para el pulido
La producción de máquinas automáticas para el pulido implica un proceso complejo que abarca desde el diseño y desarrollo hasta la fabricación, ensamblaje, pruebas y puesta en marcha de equipos especializados para el acabado superficial industrial. Este proceso requiere la integración de múltiples disciplinas, incluyendo ingeniería mecánica, electrónica, automatización y software, con el fin de crear soluciones eficientes, precisas y adaptables a las diversas necesidades del mercado.
En la fase inicial, el diseño de la máquina se basa en un análisis detallado de los requerimientos del cliente, el tipo de piezas a pulir, materiales involucrados y el acabado final deseado. Se elaboran planos y modelos 3D que permiten visualizar y simular el funcionamiento del equipo, optimizando aspectos como la ergonomía, accesibilidad para mantenimiento y seguridad operativa. El diseño modular es una característica frecuente para facilitar futuras modificaciones o ampliaciones.
La selección de componentes es un paso crítico en la producción. Se eligen motores, sensores, sistemas de control, estructuras metálicas y elementos de sujeción que aseguren robustez, precisión y durabilidad. La calidad de los materiales y la compatibilidad entre partes influyen directamente en el rendimiento y vida útil de la máquina, así como en su capacidad para operar en entornos industriales exigentes.
El proceso de fabricación involucra técnicas avanzadas como mecanizado CNC, corte láser, soldadura robotizada y tratamientos superficiales para garantizar tolerancias estrictas y acabados óptimos en las piezas que componen el equipo. Posteriormente, se realiza el ensamblaje cuidadoso de todos los componentes, integrando sistemas eléctricos y electrónicos con el conjunto mecánico, asegurando que cada módulo funcione en armonía dentro del sistema global.
Una etapa fundamental es la programación y configuración del sistema de control, donde se desarrollan los algoritmos y software necesarios para la operación automática de la máquina. Esto incluye la definición de trayectorias de pulido, parámetros de presión y velocidad, y la implementación de sistemas de monitoreo y seguridad. Las pruebas funcionales y de calidad se realizan para validar que la máquina cumple con las especificaciones y estándares requeridos, detectando y corrigiendo posibles fallos antes de su entrega.
Finalmente, la puesta en marcha y capacitación al cliente forman parte del servicio integral que garantiza una correcta instalación y operación del equipo. La formación incluye el manejo del sistema, mantenimiento preventivo y resolución de problemas básicos, asegurando que la inversión realizada en la máquina automática de pulido se traduzca en beneficios reales para la producción.
En conjunto, la producción de máquinas automáticas para el pulido representa un proceso multidisciplinario y altamente especializado que combina innovación tecnológica, precisión industrial y atención personalizada para ofrecer soluciones que optimizan el acabado superficial, incrementan la productividad y mejoran la calidad de los productos finales en diversos sectores industriales.
La producción de máquinas automáticas para el pulido requiere además una constante innovación y actualización tecnológica para responder a las demandas cambiantes del mercado y a la evolución de los materiales y procesos productivos. Los fabricantes invierten en investigación y desarrollo para incorporar nuevas funcionalidades, mejorar la eficiencia energética, reducir el impacto ambiental y aumentar la versatilidad de sus equipos. Esto incluye el diseño de sistemas más compactos, el uso de materiales ligeros y resistentes, así como la integración de tecnologías digitales como la inteligencia artificial, el aprendizaje automático y la conectividad en red.
Otro aspecto importante es la personalización de las máquinas según las especificaciones y procesos particulares de cada cliente. Aunque existen modelos estándar, muchas veces se desarrollan soluciones a medida que se adaptan a la geometría, tamaño, volumen de producción y características del producto a pulir. Esta flexibilidad es clave para atender sectores diversos como la automoción, la aeroespacial, la electrónica, la fabricación de bienes de consumo o la industria médica, donde los requisitos de acabado pueden variar significativamente.
Durante el proceso de producción, se implementan estrictos controles de calidad en todas las etapas, desde la recepción de materias primas hasta la entrega final del equipo. Se realizan inspecciones dimensionales, pruebas funcionales, ensayos de seguridad y certificaciones que garantizan que las máquinas cumplen con normativas nacionales e internacionales. Este enfoque asegura la confiabilidad, durabilidad y desempeño óptimo de los equipos en condiciones reales de trabajo.
Además, la producción está acompañada por un soporte postventa que incluye servicios de mantenimiento, actualización de software, suministro de repuestos y asesoría técnica. Este respaldo es fundamental para maximizar la vida útil de las máquinas y mantener su rendimiento constante a lo largo del tiempo. Las empresas proveedoras también pueden ofrecer formación continua para los operarios y técnicos, facilitando la adopción de nuevas tecnologías y mejores prácticas.
Por último, la globalización y la competencia creciente en el sector industrial impulsan a los fabricantes a optimizar sus procesos productivos mediante la automatización interna, la gestión eficiente de la cadena de suministro y la reducción de costos sin sacrificar calidad. Esto se traduce en máquinas automáticas para el pulido más accesibles, con mayor valor agregado y capaces de satisfacer las exigencias de una producción cada vez más rápida, flexible y sostenible. En definitiva, la producción de estas máquinas es un reflejo de la convergencia entre ingeniería avanzada, innovación tecnológica y orientación al cliente, claves para el éxito en el mercado actual.
La producción de máquinas automáticas para el pulido también se beneficia de la colaboración estrecha entre distintos actores del sector industrial, como proveedores de componentes, centros de investigación, universidades y usuarios finales. Estas alianzas fomentan la innovación abierta y el desarrollo conjunto de tecnologías que responden mejor a las necesidades reales del mercado, acelerando la incorporación de avances y facilitando la transferencia de conocimiento.
Además, la adopción de metodologías de fabricación modernas, como la industria 4.0 y la fabricación inteligente, permite optimizar la planificación, el control y la trazabilidad en cada fase del proceso productivo. A través del uso de sistemas de gestión integrados, sensores conectados y análisis de datos en tiempo real, los fabricantes pueden anticipar problemas, reducir desperdicios y mejorar la eficiencia general, logrando así equipos con mayor calidad y tiempos de entrega más cortos.
La sostenibilidad es otro factor que ha cobrado relevancia en la producción de estas máquinas. Se priorizan diseños que minimizan el consumo energético y utilizan materiales reciclables o con menor impacto ambiental. Asimismo, se desarrollan tecnologías para disminuir la generación de residuos y facilitar el reciclaje de componentes al final de la vida útil del equipo. Este enfoque no solo responde a demandas regulatorias, sino también a una creciente conciencia social y empresarial sobre la responsabilidad ambiental.
En el contexto global, la competencia internacional impulsa a los fabricantes a mantener altos estándares de calidad y a diferenciarse a través de la innovación tecnológica y el servicio al cliente. La capacidad de ofrecer soluciones integrales, que incluyen desde el diseño hasta la instalación, capacitación y soporte técnico, es fundamental para consolidar relaciones comerciales duraderas y expandir mercados.
Finalmente, la producción de máquinas automáticas para el pulido se configura como un proceso dinámico y en constante evolución, que combina la precisión de la ingeniería, la eficiencia industrial y la adaptabilidad a las tendencias tecnológicas y ambientales. Esta sinergia permite desarrollar equipos cada vez más avanzados, capaces de optimizar los procesos de acabado superficial, mejorar la competitividad de las empresas y contribuir a un desarrollo industrial más sostenible y responsable.
Mesa giratoria indexada
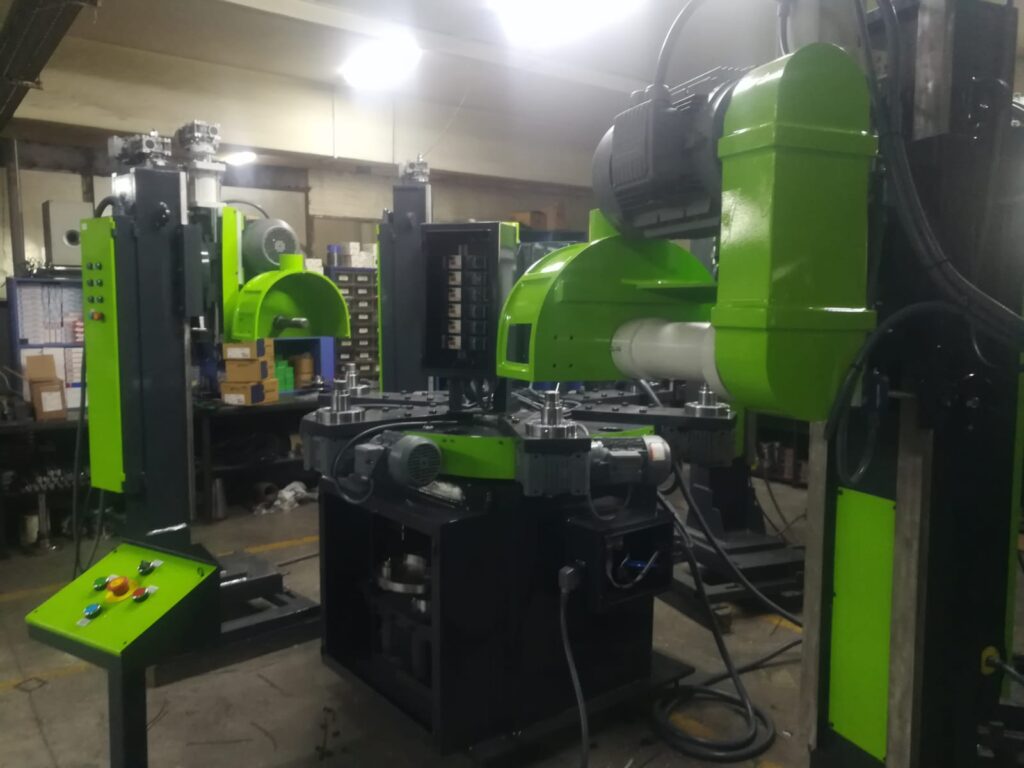
Una mesa giratoria indexada es un dispositivo mecánico utilizado en procesos industriales para posicionar y rotar piezas de trabajo de forma precisa y controlada. Este sistema permite que la mesa gire en pasos exactos o “indexados”, deteniéndose en posiciones predeterminadas que facilitan la ejecución de operaciones repetitivas y secuenciales como el pulido, montaje, inspección, soldadura o mecanizado.
El funcionamiento de una mesa giratoria indexada se basa en mecanismos de precisión que aseguran un posicionamiento exacto, generalmente mediante engranajes, levas o sistemas electromecánicos controlados por motores paso a paso o servomotores. Esto garantiza que cada pieza se detenga en el lugar correcto para ser procesada con alta repetibilidad y sin errores de alineación.
Las mesas giratorias indexadas pueden ser integradas en líneas de producción automatizadas, donde sincronizan el movimiento rotatorio con otras máquinas o robots, aumentando la eficiencia y reduciendo los tiempos de ciclo. Su diseño puede variar desde modelos simples con pocas posiciones hasta sistemas complejos con múltiples estaciones de trabajo, adaptándose a las necesidades específicas de cada proceso industrial.
Además, estas mesas pueden incorporar sistemas de sujeción y fijación automáticos, sensores de posición y controladores electrónicos que permiten programar y monitorear los movimientos en tiempo real. Esto facilita la adaptación a diferentes tipos de piezas y procesos, y asegura la calidad y precisión en cada etapa del trabajo.
En resumen, la mesa giratoria indexada es un componente clave en la automatización industrial, que ofrece precisión, flexibilidad y eficiencia para procesos que requieren movimientos rotatorios controlados y repetitivos.
La mesa giratoria indexada mejora significativamente la productividad y la precisión en los procesos industriales al permitir la manipulación automática y secuencial de piezas. Al eliminar la necesidad de ajustes manuales para cada posición, se reducen los tiempos muertos y se minimizan errores humanos, lo que contribuye a una mayor consistencia en la calidad del producto final. Esto resulta especialmente valioso en industrias donde la repetibilidad y la exactitud son críticas, como en la fabricación de componentes electrónicos, automotrices, dispositivos médicos y piezas de alta precisión.
Además, la capacidad de integrar la mesa giratoria indexada con sistemas de control automatizados y robots facilita la creación de células de trabajo completamente automatizadas. Esto permite la realización de múltiples operaciones en una sola línea de producción sin intervención humana directa, optimizando el uso del espacio y recursos. La coordinación entre la mesa y otros equipos asegura que cada etapa del proceso se ejecute en el momento preciso, mejorando el flujo de trabajo y reduciendo el riesgo de fallos o daños en las piezas.
El diseño robusto y la construcción precisa de estas mesas permiten su uso continuo en ambientes industriales exigentes, soportando cargas pesadas y ciclos de trabajo intensivos sin perder precisión. Muchos modelos incluyen materiales y tratamientos especiales que aumentan la resistencia al desgaste, la corrosión y otros factores ambientales, garantizando una larga vida útil y bajo mantenimiento.
La versatilidad de las mesas giratorias indexadas también radica en su capacidad para adaptarse a diferentes configuraciones y tamaños de piezas. Gracias a sistemas modulares y ajustables, es posible modificar la cantidad de posiciones, la velocidad de rotación y los mecanismos de sujeción para cumplir con los requisitos específicos de cada aplicación. Esto las convierte en una solución flexible para procesos de producción que requieren variedad o cambios frecuentes en la línea.
En definitiva, la mesa giratoria indexada es una herramienta fundamental para optimizar procesos industriales, aportando precisión, eficiencia y automatización que se traducen en productos de alta calidad y mayor competitividad en el mercado. Su implementación contribuye a la modernización de las plantas productivas y al aprovechamiento de tecnologías avanzadas en la manufactura contemporánea.
Además, la mesa giratoria indexada puede integrarse con sistemas de control avanzado que permiten la programación personalizada de ciclos y posiciones, lo que facilita la adaptación a procesos complejos y variados. Por ejemplo, en líneas de producción donde se requieren diferentes tiempos de trabajo para distintas estaciones, el sistema puede configurarse para detenerse en cada posición el tiempo necesario, garantizando la calidad y eficiencia del proceso sin necesidad de intervención manual.
La precisión en el posicionamiento se logra mediante el uso de sensores y codificadores que monitorean constantemente la posición angular de la mesa, permitiendo correcciones automáticas en tiempo real. Esto es crucial en operaciones donde un pequeño desalineamiento puede generar defectos o rechazos, como en la aplicación de recubrimientos, ensamblajes mecánicos o inspecciones ópticas.
El mantenimiento de una mesa giratoria indexada es relativamente sencillo gracias a su diseño modular y accesible. La lubricación adecuada, la revisión periódica de componentes mecánicos como engranajes y rodamientos, y la actualización del software de control, aseguran un funcionamiento estable y prolongado. Asimismo, la disponibilidad de repuestos estándar facilita las reparaciones rápidas y reduce los tiempos de inactividad en la producción.
Otra ventaja relevante es la capacidad de estas mesas para operar en combinación con otros sistemas automatizados, como robots industriales, sistemas de visión artificial y manipuladores. Esta sinergia permite la creación de estaciones de trabajo altamente especializadas y flexibles, capaces de realizar tareas complejas con mínima intervención humana, lo que reduce costos operativos y mejora la seguridad laboral.
Finalmente, la implementación de mesas giratorias indexadas contribuye a la estandarización de procesos y a la trazabilidad en la producción. Al contar con posiciones definidas y controladas electrónicamente, es posible registrar con exactitud cada etapa del proceso, facilitando el control de calidad, la identificación de fallos y la mejora continua. Esto es especialmente valioso en industrias reguladas donde la documentación y certificación de los procesos son requisitos indispensables.
En suma, la mesa giratoria indexada representa un componente esencial en la automatización industrial moderna, aportando precisión, flexibilidad y confiabilidad para optimizar una amplia variedad de procesos productivos. Su uso creciente refleja la tendencia hacia sistemas integrados y eficientes que responden a las exigencias de un mercado cada vez más competitivo y dinámico.
Mesa giratoria indexada
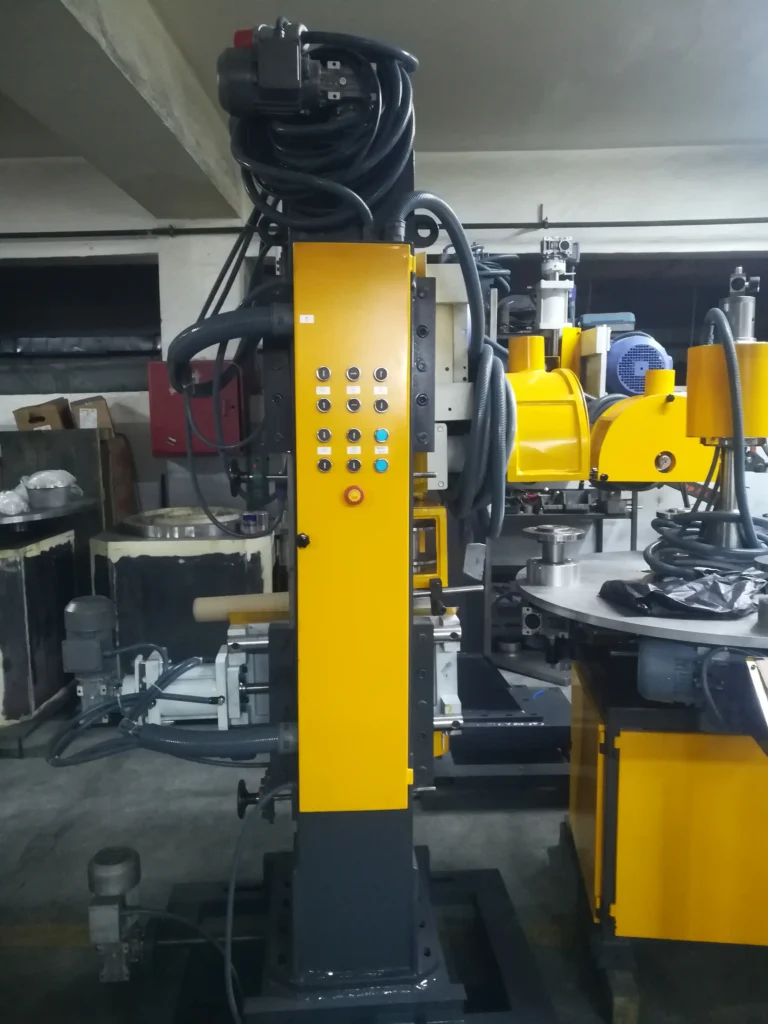
Una mesa giratoria indexada es un dispositivo mecánico diseñado para rotar una plataforma en pasos o posiciones específicas y repetibles. Este mecanismo permite que la mesa se detenga con precisión en ángulos determinados, facilitando la realización de operaciones industriales secuenciales, tales como ensamblaje, pulido, soldadura o inspección. La indexación garantiza que cada posición sea exacta y estable, asegurando la calidad y repetibilidad en los procesos automatizados.
El sistema de indexación puede ser mecánico, mediante levas o piñones que controlan el movimiento, o electrónico, usando motores paso a paso o servomotores junto con sensores y controladores digitales. Esta combinación permite un posicionamiento rápido y confiable, adaptable a diferentes velocidades y tamaños de mesa.
La mesa giratoria indexada es ampliamente utilizada en líneas de producción automatizadas, donde coordina su movimiento con otras máquinas o robots para optimizar la eficiencia y reducir tiempos de ciclo. Su diseño robusto y modular facilita la integración en distintos sistemas productivos, además de permitir ajustes para piezas de variados tamaños y pesos.
Este tipo de mesa puede incluir sistemas de sujeción automáticos y sensores para asegurar la correcta fijación y monitoreo de la posición, lo que minimiza errores y aumenta la seguridad operativa. En resumen, la mesa giratoria indexada es fundamental para procesos industriales que requieren movimientos rotativos precisos, repetitivos y coordinados, contribuyendo a mejorar la productividad y la calidad en la manufactura.
La mesa giratoria indexada juega un papel esencial en la automatización industrial al ofrecer un método eficiente para posicionar piezas de trabajo de manera precisa y repetitiva. Gracias a su capacidad para dividir una rotación completa en segmentos exactos, permite que las operaciones se realicen en múltiples estaciones de trabajo sin la necesidad de reposicionamiento manual, lo que incrementa notablemente la productividad y reduce los errores humanos.
Su diseño está pensado para soportar cargas variables, desde piezas pequeñas y ligeras hasta componentes grandes y pesados, adaptándose a distintos sectores como la industria automotriz, electrónica, aeroespacial y fabricación de maquinaria. Además, las mesas giratorias indexadas pueden fabricarse en diversos tamaños y configuraciones, lo que facilita su integración en líneas de producción tanto compactas como extensas.
La precisión en el posicionamiento se logra mediante mecanismos de alta calidad, como engranajes rectificados, piñones y discos de freno que garantizan la estabilidad en cada posición. En los sistemas más avanzados, se incorporan sensores ópticos o magnéticos que monitorizan la posición y permiten ajustes en tiempo real, asegurando una repetibilidad óptima y reduciendo el desgaste mecánico.
Otra ventaja importante es la facilidad para sincronizar la mesa giratoria indexada con sistemas de control centralizados, lo que permite coordinar su movimiento con otras máquinas y robots en la línea de producción. Esto posibilita la implementación de procesos complejos donde distintas operaciones se ejecutan de manera consecutiva y sin interrupciones, mejorando el flujo de trabajo y optimizando los tiempos de ciclo.
Además, estas mesas suelen estar diseñadas para facilitar el mantenimiento, con componentes modulares y accesibles que permiten realizar revisiones y reparaciones rápidas, minimizando los tiempos de inactividad. La durabilidad y confiabilidad de los materiales utilizados garantizan un funcionamiento estable incluso en ambientes industriales exigentes, con exposición a polvo, humedad o altas temperaturas.
Finalmente, la mesa giratoria indexada contribuye a la mejora continua de los procesos productivos, ya que su precisión y repetibilidad facilitan el control de calidad y la trazabilidad de cada pieza trabajada. Esto es fundamental en sectores donde las tolerancias son estrictas y los estándares de fabricación muy elevados. En conjunto, su uso representa una inversión que potencia la eficiencia, calidad y competitividad de la producción industrial.
Además de su función principal de posicionamiento preciso, la mesa giratoria indexada puede ser parte integral de sistemas flexibles de manufactura (FMS) y células robotizadas, donde la versatilidad y la adaptabilidad son cruciales. En estos entornos, la capacidad de cambiar rápidamente las configuraciones y adaptar las posiciones indexadas permite la producción de lotes pequeños o variados sin sacrificar la eficiencia.
La incorporación de tecnologías de sensores avanzados y controladores programables ha llevado a la evolución de las mesas giratorias indexadas hacia sistemas inteligentes. Estos sistemas pueden comunicarse con otros dispositivos mediante protocolos industriales (como Profinet, EtherCAT o Modbus), facilitando la integración en redes de automatización y el monitoreo en tiempo real del estado operativo. Esto permite implementar estrategias de mantenimiento predictivo, reduciendo fallas inesperadas y optimizando los recursos.
En términos de diseño, las mesas pueden equiparse con sistemas de frenado electromagnético o neumático, que aseguran un bloqueo firme en cada posición y facilitan paradas rápidas y seguras. También es común que incorporen sistemas de sujeción adaptativos para diferentes tipos de piezas, aumentando la flexibilidad y reduciendo tiempos de cambio entre productos.
El avance en materiales y procesos de fabricación ha permitido desarrollar mesas giratorias más ligeras pero resistentes, con estructuras que reducen vibraciones y mejoran la estabilidad durante la operación. Esto es especialmente importante en procesos de alta precisión, como el mecanizado de componentes delicados o el ensamblaje de dispositivos electrónicos.
Por último, la mesa giratoria indexada no solo optimiza procesos industriales sino que también contribuye a la seguridad laboral. Al automatizar movimientos repetitivos y de carga, reduce la exposición de los operadores a riesgos físicos y mejora las condiciones de trabajo en la planta.
En conclusión, la mesa giratoria indexada es un componente versátil y clave en la modernización de la manufactura, combinando precisión, flexibilidad y capacidad de integración para responder a las demandas actuales de eficiencia y calidad en la producción industrial.
Célula robotizada IR
Una célula robotizada IR (Infrared) es un sistema automatizado que integra uno o varios robots industriales equipados con sensores y tecnologías de detección por infrarrojos para realizar tareas específicas en procesos de manufactura. Estos sistemas utilizan la tecnología infrarroja para captar información sobre la posición, temperatura, presencia o características de las piezas, lo que permite una interacción más precisa y segura entre el robot, el entorno y los objetos a manipular.
La principal ventaja de incorporar sensores IR en una célula robotizada es la capacidad de realizar mediciones y detecciones sin contacto físico, lo que es especialmente útil en aplicaciones donde las piezas son delicadas, calientes o donde se requiere evitar contaminaciones. Por ejemplo, la tecnología infrarroja puede detectar la temperatura superficial de un objeto para controlar procesos térmicos, o identificar la presencia y posición de una pieza en la estación de trabajo con gran rapidez y fiabilidad.
Estas células suelen configurarse para realizar operaciones repetitivas como soldadura, pulido, pintura, ensamblaje o inspección de calidad. La integración de sensores IR facilita la automatización de procesos complejos, pues permite que el robot ajuste sus movimientos en tiempo real según la información recibida, aumentando la precisión y reduciendo errores o defectos en la producción.
Además, las células robotizadas IR pueden incluir sistemas de visión artificial que combinan imágenes térmicas y ópticas para mejorar la capacidad de análisis y control. Esto es especialmente útil en aplicaciones de control de calidad, donde se requieren evaluaciones detalladas de las piezas para detectar fallos superficiales, variaciones térmicas o defectos invisibles al ojo humano.
La programación y control de estas células se realiza mediante software especializado que coordina las señales de los sensores IR con los movimientos y acciones del robot. Esto permite una operación sincronizada y adaptable a diferentes tipos de productos y procesos, incrementando la flexibilidad y eficiencia en la línea de producción.
En resumen, una célula robotizada IR representa una solución avanzada para automatizar procesos industriales, combinando la precisión y versatilidad de los robots con la capacidad de detección no invasiva de la tecnología infrarroja, mejorando la calidad, productividad y seguridad en las operaciones de manufactura.
Las células robotizadas IR representan un paso significativo hacia la automatización inteligente de los procesos industriales, ya que permiten una interacción dinámica entre los robots y su entorno. La capacidad de detectar variaciones mínimas de temperatura, presencia o movimiento sin necesidad de contacto físico ofrece una ventaja importante en términos de velocidad, precisión y control. Estas células pueden operar de manera autónoma durante largos periodos, minimizando la intervención humana y reduciendo los errores por fatiga o distracción. Además, el uso de sensores infrarrojos mejora la seguridad operativa, ya que permite a los robots identificar obstáculos o personas en su entorno inmediato, activando protocolos de seguridad sin detener completamente la producción. En entornos de producción exigentes, como fundiciones, líneas de pintura, pulido o soldadura, donde la temperatura, la suciedad o los humos dificultan la visión óptica tradicional, los sensores IR siguen funcionando con fiabilidad.
Esto asegura una continuidad operacional que sería difícil de mantener con sistemas convencionales. Al integrarse con software de supervisión industrial, estas células pueden generar informes en tiempo real sobre el estado de la producción, el rendimiento de los robots y la trazabilidad de las piezas, facilitando el mantenimiento predictivo y la mejora continua. En plantas modernas, las células robotizadas IR se pueden reconfigurar con facilidad para adaptarse a diferentes tipos de piezas o cambios en la producción, lo que las convierte en una inversión flexible y escalable. Gracias a su diseño modular y a la posibilidad de incorporar diferentes herramientas o cabezales, estas células se adaptan a tareas que requieren precisión constante en ambientes de alta variabilidad. En suma, las células robotizadas IR no solo automatizan tareas, sino que elevan el nivel de inteligencia y adaptabilidad de los sistemas de manufactura, respondiendo a las exigencias de calidad, velocidad y personalización que demanda la industria actual.
Estas células robotizadas IR también tienen un papel clave en el avance hacia fábricas más sostenibles y eficientes energéticamente. Al incorporar sensores infrarrojos, no solo se optimiza la calidad del producto, sino también el uso de recursos. Por ejemplo, al detectar la temperatura exacta de una pieza metálica durante un proceso de enfriamiento o soldadura, se puede ajustar en tiempo real la aplicación de calor o el tiempo de espera, evitando consumos innecesarios de energía. Esta capacidad de corrección instantánea también reduce el desperdicio de materiales al minimizar defectos que en otros casos obligarían a repetir operaciones o desechar piezas.
Otra aplicación destacada es la inspección térmica en línea, que permite detectar anomalías en la estructura interna de un producto a través de diferencias de temperatura sutiles que no serían visibles a través de cámaras convencionales. Este tipo de control de calidad automatizado es muy utilizado en sectores como la automoción, la electrónica y la fabricación de componentes críticos para aeronáutica o medicina.
En cuanto a su arquitectura física, estas células pueden estar construidas dentro de cabinas protegidas que aíslan el proceso tanto para evitar riesgos como para controlar mejor el ambiente de trabajo. Esto es especialmente útil cuando se trabaja con polvo, vapores, radiación o calor excesivo. La instalación puede incluir además sistemas de extracción, iluminación IR complementaria, y una interfaz hombre-máquina (HMI) para facilitar su operación por parte del personal de planta.
El robot industrial dentro de la célula, generalmente de seis ejes, puede trabajar con una precisión de décimas de milímetro, y si se combina con visión artificial y sensores IR, puede incluso corregir su trayectoria en tiempo real si detecta una posición incorrecta, una pieza defectuosa o condiciones térmicas anómalas. Esto significa que incluso en producciones con variabilidad —como piezas fundidas con ligeras diferencias de forma— el sistema puede adaptarse sin necesidad de parar ni recalibrar manualmente.
Con la conectividad digital moderna, estas células pueden formar parte de redes de producción más amplias, integrándose en sistemas MES o ERP para una trazabilidad completa de cada unidad fabricada. Se pueden registrar datos como la temperatura durante cada fase, los tiempos de ciclo exactos, y la identificación única de cada pieza procesada, lo que es esencial para certificaciones de calidad o análisis de rendimiento.
En resumen, las células robotizadas IR no solo automatizan, sino que transforman los procesos industriales en operaciones inteligentes, adaptativas y conectadas. Representan una solución avanzada para quienes buscan precisión, control térmico, eficiencia energética y trazabilidad sin comprometer la velocidad ni la flexibilidad del sistema productivo.
Mesa giratoria indexada con unidad de pulido CPL
Una mesa giratoria indexada con unidad de pulido CPL (Continuous Polishing Line) es una solución altamente especializada en la automatización del acabado superficial, diseñada para ofrecer máxima precisión y productividad en procesos de pulido industrial. Este sistema combina el posicionamiento exacto y secuencial de una mesa indexada con una unidad de pulido avanzada, permitiendo trabajar de forma continua y repetitiva sobre piezas metálicas, plásticas o compuestas, garantizando resultados homogéneos y de alta calidad.
El corazón de este sistema es la mesa giratoria indexada, que rota en intervalos fijos y controlados, permitiendo que múltiples piezas se coloquen en diferentes estaciones alrededor de su circunferencia. Cada estación puede alojar una unidad de trabajo o ser parte del ciclo de carga y descarga. La indexación garantiza que cada pieza se alinee de manera precisa con la unidad de pulido, lo que es fundamental para mantener la consistencia del acabado, sobre todo en operaciones críticas como el abrillantado espejo o el pulido decorativo.
La unidad de pulido CPL montada en una de las estaciones está equipada con cabezales motorizados, sistemas de compensación automática de presión, y control de velocidad variable, lo que le permite adaptarse a distintos tipos de materiales y geometrías de piezas. Gracias a sus cepillos, discos o bandas abrasivas intercambiables, puede ejecutar desde un desbaste inicial hasta un acabado final brillante en un solo ciclo continuo. Esta unidad también puede estar asistida por sensores de presión o visión que optimizan el contacto entre la herramienta de pulido y la superficie de la pieza.
Además, el conjunto está pensado para trabajar en sincronía, de modo que mientras una pieza está siendo pulida, otras están entrando o saliendo de la mesa, lo que reduce al mínimo los tiempos muertos y maximiza el rendimiento. Esta simultaneidad convierte a este tipo de instalación en una solución muy atractiva para la producción en masa o de piezas con alta exigencia estética y dimensional, como grifería, herrajes, carcasas metálicas, electrodomésticos o componentes automotrices.
El diseño modular de la mesa permite integrar otras unidades funcionales, como soplado, limpieza, inspección por visión o estaciones de cambio automático de herramientas. Incluso puede conectarse con robots colaborativos para carga y descarga automatizada, mejorando la ergonomía y reduciendo la intervención humana directa.
En términos de control, todo el sistema puede gestionarse mediante una interfaz HMI centralizada, que permite la programación de parámetros específicos para cada tipo de pieza, el monitoreo del estado del equipo, y el registro de datos para trazabilidad o mantenimiento predictivo.
Una mesa giratoria indexada con unidad de pulido CPL representa por tanto una solución técnica de alto nivel para industrias que requieren acabados consistentes, ciclos de trabajo rápidos y una integración sencilla en líneas de producción automatizadas, con ventajas claras en calidad, productividad y eficiencia operativa.
La mesa giratoria indexada con unidad de pulido CPL no solo representa una solución mecánicamente robusta, sino también una plataforma ideal para la producción en serie donde el acabado superficial es determinante para el valor final del producto. Al operar de forma continua con una lógica secuencial y perfectamente sincronizada, permite ejecutar múltiples etapas de trabajo sin interrupciones, minimizando el tiempo de manipulación y optimizando cada segundo del ciclo productivo. Esta eficiencia se traduce en un mayor número de piezas por hora, lo cual es esencial en sectores como la automoción, los electrodomésticos o la industria sanitaria, donde los estándares de brillo, uniformidad y presentación visual son sumamente estrictos.
La versatilidad del sistema CPL permite ajustar automáticamente parámetros como la presión de contacto, la velocidad de rotación de los discos o bandas, la cantidad de compuesto abrasivo aplicado e incluso la dirección del pulido en función de la forma o el material de la pieza. Esto posibilita trabajar desde piezas planas hasta geometrías complejas como curvas, biseles o superficies con relieve. Además, algunos modelos incluyen sistemas de detección por visión artificial o sensores de fuerza que permiten al equipo corregir en tiempo real desviaciones en el proceso, asegurando una calidad constante incluso cuando hay ligeras diferencias entre las piezas entrantes.
Por su parte, la mesa indexada actúa como un distribuidor mecánico de alta precisión que posiciona cada pieza justo en el punto exacto donde la herramienta de pulido puede trabajar de manera óptima. Cada estación está calculada para evitar interferencias entre etapas, y su accionamiento suele ser servoaccionado o neumático con controles de alta repetibilidad. La estructura general está diseñada para resistir el estrés de un trabajo continuo, y puede incorporar cubiertas de protección, sistemas de aspiración de polvo o neblina y depósitos automáticos de pasta abrasiva para reducir el mantenimiento y aumentar la seguridad operativa.
La automatización de carga y descarga, ya sea mediante robots o sistemas neumáticos, no solo mejora la productividad sino que también reduce errores de manipulación y daños superficiales, factores críticos cuando se trabaja con acabados tipo espejo o superficies de alta estética. En configuraciones más avanzadas, la célula entera puede integrarse con sistemas de trazabilidad que registran cada pieza pulida, su programa de trabajo, parámetros usados y tiempos de ciclo, generando así un histórico de calidad accesible desde el sistema MES o SCADA de planta.
En definitiva, este tipo de solución proporciona un equilibrio perfecto entre precisión mecánica, flexibilidad operativa y control inteligente del proceso. La mesa giratoria indexada con unidad de pulido CPL no es simplemente una herramienta para mejorar la productividad, sino un nodo clave en una línea de fabricación moderna que exige acabados impecables, repetibilidad garantizada y adaptabilidad inmediata a nuevos diseños o especificaciones. Su adopción marca un paso firme hacia una producción más eficiente, estandarizada y técnicamente avanzada.
Además, la integración de una mesa giratoria indexada con unidad de pulido CPL ofrece beneficios logísticos y de mantenimiento que no deben subestimarse. Su diseño compacto y modular permite que se instale en espacios relativamente reducidos dentro de una línea de producción existente, sin necesidad de rediseñar completamente el layout de planta. Esto facilita la modernización de procesos tradicionales con una inversión contenida, pero con un retorno medible gracias a la mejora de la eficiencia operativa, la reducción de desperdicio de materiales y la disminución de intervenciones humanas.
Desde el punto de vista del mantenimiento, muchos de estos sistemas incorporan funciones de autodiagnóstico que alertan al operador sobre desgastes en los componentes clave como discos, bandas, cepillos o motores, permitiendo programar reemplazos sin necesidad de detener inesperadamente la producción. Los sistemas de cambio rápido de herramientas (quick-change) hacen posible sustituir consumibles en minutos, lo cual mantiene la línea en funcionamiento continuo. Asimismo, los sensores distribuidos en toda la célula permiten detectar desajustes o desalineaciones que, si se corrigen a tiempo, evitan defectos de acabado o roturas de piezas costosas.
En cuanto al impacto sobre la calidad del producto final, este tipo de sistema asegura una homogeneidad que difícilmente puede lograrse con trabajo manual o semiautomático. Cada pieza pasa por el mismo ciclo, con la misma presión, velocidad y tipo de herramienta, lo que resulta en superficies uniformes, sin marcas o variaciones. Este nivel de calidad es esencial cuando el acabado no es solo estético sino también funcional, como en superficies que requieren baja fricción, protección anticorrosiva mejorada o preparación para recubrimientos adicionales como anodizado o pintura.
La capacidad de adaptar fácilmente el programa de pulido a distintas piezas también la convierte en una solución útil para fábricas que manejan series cortas o personalizadas. Basta con cambiar el utillaje o ajustar el software para modificar completamente la configuración, lo que ofrece una agilidad de respuesta crucial en mercados donde los ciclos de producto son cada vez más cortos y la personalización es una exigencia constante. Incluso en industrias con requisitos normativos estrictos —como la farmacéutica, alimentaria o aeroespacial—, estas máquinas pueden trabajar bajo entornos controlados, garantizando trazabilidad total y validación de procesos.
Por todas estas razones, una mesa giratoria indexada con unidad de pulido CPL no solo automatiza una tarea específica, sino que mejora integralmente la capacidad productiva, la calidad del acabado, la trazabilidad del proceso y la flexibilidad de respuesta de la planta. Se trata de una tecnología madura y altamente eficaz, diseñada para satisfacer las demandas de una industria moderna que exige velocidad, precisión y adaptabilidad sin concesiones.
Mesas giratorias indexadas
Las mesas giratorias indexadas son dispositivos mecánicos diseñados para posicionar con precisión piezas o conjuntos en estaciones de trabajo fijas dentro de una línea de producción o un proceso industrial. Su función principal es permitir que una mesa o plataforma gire en pasos controlados y repetibles, deteniéndose exactamente en posiciones predeterminadas para facilitar operaciones como montaje, inspección, mecanizado, pulido o ensamblaje. La indexación asegura que cada pieza esté alineada correctamente con las herramientas o sistemas que intervienen en cada estación, lo cual es fundamental para mantener la calidad, la precisión y la eficiencia en la producción.
Estas mesas pueden ser accionadas por diferentes mecanismos, incluyendo motores eléctricos servoaccionados, motores paso a paso, sistemas neumáticos o hidráulicos, cada uno con sus ventajas dependiendo de la aplicación específica. Los sistemas servoeléctricos son especialmente populares debido a su alta precisión, control dinámico y capacidad para integrar sistemas de retroalimentación que garantizan la repetibilidad del posicionamiento en décimas o incluso centésimas de grado.
El diseño de las mesas giratorias indexadas suele ser modular, permitiendo adaptar el número de estaciones según las necesidades productivas. Esto facilita la personalización para distintos tamaños de lotes o tipos de piezas, ofreciendo flexibilidad para ampliaciones futuras o cambios en el proceso. Además, su construcción robusta garantiza la estabilidad y resistencia a cargas variables, vibraciones y condiciones de operación exigentes.
Las mesas pueden incorporar sistemas adicionales como sensores de posición, dispositivos de bloqueo para evitar movimientos no deseados durante la operación, y sistemas de seguridad para proteger al personal y los equipos. La integración con controles lógicos programables (PLC) permite coordinar la rotación y las operaciones en cada estación, facilitando la automatización y sincronización con otras máquinas o robots en la línea de producción.
En la práctica, las mesas giratorias indexadas se utilizan en numerosos sectores industriales, incluyendo la automoción, electrónica, fabricación de electrodomésticos, farmacéutica y metalurgia. Son ideales para procesos donde es necesario realizar múltiples operaciones secuenciales en una pieza, optimizando el flujo de trabajo y minimizando tiempos de ciclo. Su uso contribuye a aumentar la productividad, reducir errores humanos y mejorar la calidad final del producto.
En resumen, las mesas giratorias indexadas son componentes clave en la automatización industrial, proporcionando posicionamiento preciso y confiable para procesos repetitivos y de alta demanda, mejorando la eficiencia y la capacidad productiva de las líneas de fabricación.
Las mesas giratorias indexadas permiten una sincronización perfecta con otras etapas del proceso productivo, ya que su movimiento controlado posibilita que cada estación realice su tarea en un tiempo optimizado, evitando esperas innecesarias o solapamientos que podrían generar errores o daños en las piezas. Esto es especialmente importante en sistemas automatizados donde varias operaciones deben realizarse en paralelo o en secuencia estricta, como en líneas de montaje, pulido, soldadura o inspección. La capacidad de detener la mesa en posiciones exactas y con alta repetibilidad reduce la variabilidad en la producción, garantizando que cada pieza reciba el mismo tratamiento, lo cual impacta directamente en la uniformidad y calidad del producto final.
Además, estas mesas pueden integrarse con sistemas de alimentación y descarga automatizados, ya sea mediante robots, transportadores o sistemas neumáticos, facilitando la manipulación sin intervención manual y aumentando la seguridad del operador al reducir la exposición directa a áreas de trabajo con maquinaria en movimiento. La modularidad de su diseño también permite configurar diferentes tamaños y capacidades de carga, adaptándose a piezas desde componentes pequeños y delicados hasta conjuntos voluminosos y pesados.
En términos de control, las mesas giratorias indexadas suelen estar equipadas con sensores ópticos, magnéticos o inductivos que detectan la posición exacta y aseguran la correcta indexación antes de activar la siguiente operación. Esto permite que el sistema implemente lógicas de control avanzadas, detectando fallas, bloqueos o desviaciones que pueden ser corregidas automáticamente o generar alertas para el personal de mantenimiento, minimizando tiempos de paro y pérdidas de producción.
El mantenimiento de estas mesas es relativamente sencillo, dado que sus componentes suelen estar diseñados para soportar condiciones industriales severas, incluyendo cargas repetidas, ciclos continuos y presencia de polvo o líquidos. Las piezas móviles están lubricadas y protegidas, y su construcción facilita el acceso para inspecciones periódicas y sustitución de partes desgastadas. Además, muchos fabricantes ofrecen configuraciones con monitoreo remoto o diagnóstico predictivo, anticipando posibles fallos antes de que impacten en la producción.
En definitiva, las mesas giratorias indexadas constituyen una tecnología versátil, confiable y eficiente que aporta precisión y continuidad a múltiples procesos industriales. Su capacidad para integrarse en sistemas automatizados, adaptarse a diferentes requerimientos productivos y mantener un alto nivel de calidad las hace indispensables en fábricas modernas que buscan optimizar recursos, mejorar tiempos de ciclo y garantizar productos homogéneos con estándares rigurosos. Su papel es fundamental en la transición hacia la Industria 4.0, donde la interconectividad, el control inteligente y la flexibilidad son claves para la competitividad y la innovación.
Además, las mesas giratorias indexadas facilitan la implementación de sistemas de producción lean y just-in-time al optimizar el flujo de materiales y reducir tiempos muertos. Al permitir una distribución ordenada y sincronizada de las piezas en las distintas estaciones de trabajo, contribuyen a minimizar inventarios en proceso y a mejorar la trazabilidad en la línea. Esto es especialmente valioso en industrias con alta rotación de productos o con requisitos estrictos de calidad y cumplimiento normativo, donde la gestión precisa de cada componente y su historial es esencial.
La integración de estas mesas con tecnologías avanzadas como la visión artificial o sensores inteligentes potencia aún más su funcionalidad. Por ejemplo, la inspección automática de las piezas puede realizarse en una estación específica, verificando dimensiones, acabados o defectos antes de continuar al siguiente proceso. Si se detecta alguna irregularidad, el sistema puede redirigir o separar automáticamente la pieza, evitando que llegue a etapas posteriores y garantizando un control de calidad en tiempo real sin necesidad de intervención manual.
En términos de flexibilidad, las mesas giratorias indexadas se pueden programar para manejar distintos ciclos de trabajo, ajustando la duración de paradas, la velocidad de rotación o el número de posiciones activas según las necesidades de producción. Esta adaptabilidad es crucial en plantas donde se manejan diferentes modelos o lotes de productos, permitiendo cambios rápidos sin afectar significativamente la eficiencia global.
La combinación de robustez mecánica, precisión electrónica y facilidad de integración convierte a estas mesas en elementos estratégicos dentro de sistemas de automatización industrial. Además, la posibilidad de incorporar interfaces hombre-máquina (HMI) facilita la operación y supervisión por parte del personal, proporcionando información en tiempo real sobre el estado de la máquina, parámetros de proceso y alertas de mantenimiento.
Finalmente, la creciente demanda de soluciones sostenibles y eficientes energéticamente también ha impulsado el desarrollo de mesas giratorias indexadas con motores de bajo consumo, sistemas de recuperación de energía y diseños optimizados para reducir el impacto ambiental. Esta evolución responde a la necesidad de que la industria no solo sea competitiva y productiva, sino también responsable y alineada con las tendencias globales hacia la sostenibilidad y la reducción de la huella ecológica.
Dispositivos automáticos para abrillantar
Los dispositivos automáticos para abrillantar son sistemas diseñados para proporcionar acabados de alta calidad y brillo en superficies metálicas, plásticas u otros materiales, de manera rápida, precisa y homogénea, sin la necesidad de intervención manual constante. Estos equipos se utilizan ampliamente en industrias como la automotriz, la fabricación de electrodomésticos, la joyería, la metalurgia y la electrónica, donde la estética y la presentación del producto final son aspectos fundamentales.
Estos dispositivos combinan movimientos controlados, presión constante y aplicación adecuada de compuestos abrasivos o pulidores para lograr superficies lisas, uniformes y con un acabado espejo o brillante. Utilizan diferentes tecnologías, como cepillos rotativos, discos de pulido, bandas abrasivas o incluso sistemas de vibración y ultrasonido, dependiendo del tipo de material y el acabado requerido.
La automatización en estos equipos permite ajustar parámetros clave como la velocidad de rotación, la presión aplicada, el tiempo de pulido y la cantidad de abrasivo usado, lo que garantiza resultados consistentes y evita errores humanos. Además, muchos dispositivos cuentan con sensores y sistemas de control que monitorizan en tiempo real el proceso, ajustando automáticamente las variables para optimizar el acabado según las características específicas de cada pieza.
La integración de dispositivos automáticos para abrillantar en líneas de producción modernas contribuye significativamente a aumentar la productividad y la calidad del producto, reduciendo además el tiempo de ciclo y los costos asociados a la mano de obra. Estos sistemas pueden funcionar de manera continua o en ciclos programados, y a menudo se combinan con otros procesos de tratamiento superficial para ofrecer soluciones completas y eficientes.
En resumen, los dispositivos automáticos para abrillantar representan una herramienta clave en la industria actual para obtener acabados brillantes, uniformes y de alta calidad, optimizando recursos y asegurando la repetibilidad en la producción.
Estos dispositivos automáticos para abrillantar están diseñados para adaptarse a diferentes tipos y tamaños de piezas, desde componentes pequeños y delicados hasta objetos voluminosos que requieren un acabado uniforme en toda su superficie. La versatilidad de estos sistemas permite utilizarlos en una amplia variedad de materiales, como acero inoxidable, aluminio, cobre, latón, plásticos técnicos e incluso materiales compuestos, ajustando los parámetros de pulido según la dureza, la textura inicial y el acabado final deseado.
La precisión en el control de los procesos es fundamental para evitar defectos como sobrecalentamiento, marcas, rayaduras o eliminación excesiva de material, problemas que podrían afectar tanto la estética como las propiedades funcionales de la pieza. Para ello, muchos dispositivos incorporan tecnología avanzada, como sistemas de control por retroalimentación que regulan la presión y la velocidad en función del desgaste del abrasivo y la respuesta de la pieza durante el proceso. Esto garantiza una mayor uniformidad y protege las piezas sensibles.
Además, la automatización reduce significativamente la exposición de los operarios a ambientes con polvo, partículas abrasivas o vapores, mejorando la seguridad laboral y reduciendo riesgos asociados al pulido manual tradicional. Los dispositivos automáticos suelen integrarse con sistemas de extracción de polvo y filtración, manteniendo un entorno de trabajo limpio y cumpliendo con normativas ambientales y de seguridad industrial.
La incorporación de dispositivos automáticos para abrillantar también facilita la integración en líneas de producción inteligentes, donde pueden sincronizarse con otras máquinas y sistemas de control para lograr un flujo continuo y eficiente. Esto permite una mayor capacidad de producción sin sacrificar calidad, y la posibilidad de implementar sistemas de trazabilidad que registran cada ciclo de trabajo, facilitando el control de calidad y la certificación de los procesos.
Finalmente, el desarrollo tecnológico constante ha llevado a la aparición de dispositivos que incorporan inteligencia artificial y aprendizaje automático para optimizar automáticamente los parámetros de pulido en función del análisis de resultados en tiempo real, lo que abre nuevas posibilidades para mejorar la calidad, reducir el consumo de materiales y aumentar la vida útil de los equipos y consumibles. En conjunto, estos avances convierten a los dispositivos automáticos para abrillantar en soluciones indispensables para la manufactura moderna y competitiva.
Además, estos dispositivos automáticos para abrillantar están diseñados con una alta capacidad de personalización para adaptarse a los requerimientos específicos de cada cliente y producto. Por ejemplo, pueden configurarse con distintos tipos de herramientas de pulido, como rodillos, cepillos, discos o almohadillas abrasivas, según el tipo de acabado deseado y las características del material. Esta flexibilidad permite aplicar acabados desde un pulido mate hasta un brillo espejo intenso, cubriendo un amplio espectro de necesidades industriales y estéticas.
La implementación de sistemas modulares facilita la integración de estos dispositivos en líneas de producción ya existentes, minimizando el tiempo y costo de instalación, y permitiendo una fácil ampliación o actualización conforme cambian las demandas de producción. Asimismo, la mayoría de estos equipos cuentan con interfaces intuitivas y paneles de control amigables que permiten a los operadores programar y monitorear el proceso con facilidad, reduciendo la necesidad de capacitación especializada y minimizando errores operativos.
En términos de mantenimiento, los dispositivos automáticos para abrillantar están construidos con componentes de alta durabilidad y accesibilidad, lo que simplifica las tareas de limpieza, ajuste y reemplazo de partes. Esto se traduce en menores tiempos de parada y una mayor disponibilidad operativa, aspectos cruciales en entornos productivos donde la continuidad del proceso es vital para cumplir con los volúmenes y tiempos de entrega establecidos.
Desde el punto de vista económico, la inversión en estos dispositivos se ve rápidamente compensada por el aumento en la calidad del acabado, la reducción del desperdicio de materiales abrasivos y la disminución de costos asociados a la mano de obra manual. Además, al automatizar el proceso, se consigue una mayor uniformidad y repetibilidad, lo que reduce la tasa de rechazos y retrabajos, mejorando la rentabilidad global de la producción.
Finalmente, el compromiso con la sostenibilidad también se refleja en el diseño de estos dispositivos, ya que muchos incorporan sistemas para la reutilización o reciclaje de compuestos abrasivos, la reducción del consumo energético y la minimización del impacto ambiental. Esto permite a las empresas no solo optimizar sus procesos productivos sino también alinearse con las normativas ambientales y responder a las crecientes exigencias del mercado en materia de responsabilidad social corporativa y producción limpia.
Máquinas automáticas para acabado y pulido
Las máquinas automáticas para acabado y pulido son equipos industriales diseñados para realizar procesos de superficie que mejoran la apariencia, funcionalidad y durabilidad de las piezas manufacturadas. Estos sistemas combinan precisión mecánica, control electrónico y tecnologías avanzadas para lograr acabados uniformes, libres de imperfecciones y con características específicas como brillo, suavidad o textura.
Estos equipos son ampliamente utilizados en industrias como la automotriz, aeroespacial, metalmecánica, fabricación de muebles, electrónica y joyería, donde el acabado superficial es un factor clave para la calidad del producto final y su aceptación en el mercado. Las máquinas automáticas permiten realizar procesos como el desbarbado, pulido, bruñido, abrillantado, mateado o texturizado, adaptándose a diferentes materiales, desde metales ferrosos y no ferrosos hasta plásticos y composites.
El diseño de estas máquinas incluye sistemas de accionamiento por motores eléctricos con variadores de velocidad, sensores para monitoreo en tiempo real, dispositivos de seguridad y sistemas de control programables que permiten configurar ciclos de trabajo personalizados. La automatización de estos procesos reduce la intervención manual, disminuyendo el riesgo de errores, lesiones laborales y garantizando la repetibilidad en los resultados.
Además, las máquinas automáticas para acabado y pulido incorporan diferentes tipos de herramientas, como discos abrasivos, cepillos, bandas, rodillos y pastas pulidoras, que se seleccionan según el tipo de material y el acabado requerido. La presión, velocidad y tiempo de operación se ajustan con precisión para evitar daños en las piezas y optimizar el consumo de consumibles.
En términos de integración, estos equipos pueden formar parte de líneas automatizadas más amplias, comunicándose con otros sistemas mediante protocolos industriales para coordinar la producción, mejorar la eficiencia y facilitar la trazabilidad de cada lote o pieza. También suelen contar con interfaces hombre-máquina intuitivas que permiten un manejo sencillo y supervisión constante.
En resumen, las máquinas automáticas para acabado y pulido son soluciones tecnológicas esenciales para la manufactura moderna, aportando calidad, eficiencia y seguridad, y permitiendo a las empresas competir en mercados que demandan altos estándares de acabado superficial.
Estas máquinas automáticas para acabado y pulido están diseñadas para adaptarse a una amplia variedad de piezas y geometrías, desde componentes pequeños y delicados hasta estructuras grandes y complejas. Su flexibilidad se logra mediante sistemas de sujeción ajustables y herramientas intercambiables que permiten trabajar diferentes tamaños y formas con un alto grado de precisión. Esto las hace ideales para industrias que requieren múltiples configuraciones de producción o cambios rápidos entre diferentes productos.
La capacidad de controlar con exactitud parámetros como la velocidad de rotación, la presión aplicada, el tiempo de operación y la cantidad de abrasivo utilizado permite optimizar cada proceso según las características específicas del material y el acabado deseado. Este control preciso contribuye a reducir el desgaste de las herramientas y minimiza el consumo de consumibles, generando un impacto positivo en los costos operativos y en la sostenibilidad del proceso.
Además, muchas de estas máquinas cuentan con sistemas de retroalimentación en tiempo real que monitorizan el estado del proceso y realizan ajustes automáticos para mantener la calidad constante. Por ejemplo, sensores pueden detectar variaciones en la resistencia o vibración que indican desgaste o cambio en la condición de la pieza, permitiendo adaptar el ciclo para evitar defectos o daños. Esto garantiza resultados uniformes y mejora la confiabilidad del proceso, incluso en producciones continuas o de alto volumen.
La automatización también mejora significativamente la seguridad laboral al reducir la necesidad de intervención directa en tareas que suelen ser físicamente demandantes y potencialmente riesgosas, como el manejo de abrasivos o la exposición a partículas y polvo. Las máquinas están equipadas con sistemas de protección, extracción de polvo y mecanismos de parada automática ante detección de anomalías, contribuyendo a un ambiente de trabajo más seguro y saludable.
En cuanto a la integración industrial, estas máquinas se diseñan para ser compatibles con sistemas de manufactura inteligente y automatizada. Pueden conectarse a redes industriales y sistemas de supervisión para coordinar su funcionamiento dentro de líneas de producción complejas, permitiendo una gestión eficiente de recursos y tiempos, así como la recopilación de datos para análisis y mejora continua. Esto facilita la implementación de estrategias de mantenimiento predictivo y el seguimiento detallado de la calidad.
Finalmente, el avance tecnológico ha impulsado la incorporación de nuevas funcionalidades como el uso de inteligencia artificial y algoritmos de aprendizaje automático para optimizar los procesos de acabado y pulido. Estas capacidades permiten que las máquinas ajusten de manera autónoma sus parámetros en función de la experiencia acumulada y de las condiciones específicas de cada lote, mejorando la eficiencia, prolongando la vida útil de los componentes y asegurando un nivel de acabado superior, con una reducción significativa de rechazos y retrabajos.
Las máquinas automáticas para acabado y pulido también se benefician de innovaciones en materiales y herramientas abrasivas, que permiten alcanzar niveles superiores de calidad en menos tiempo y con menor desgaste. Por ejemplo, la utilización de abrasivos de alta tecnología, como discos con recubrimientos de diamante o microabrasivos cerámicos, proporciona una mayor eficiencia en el proceso, menor generación de calor y un acabado más fino, especialmente en materiales difíciles de trabajar como aceros inoxidables o aleaciones especiales.
Otra tendencia importante en este tipo de maquinaria es la implementación de sistemas multifuncionales que combinan diferentes técnicas de acabado en un solo equipo. Esto incluye la posibilidad de alternar entre procesos de pulido, abrillantado, desbarbado o limpieza superficial sin necesidad de cambiar la máquina o realizar ajustes complejos, lo que incrementa la flexibilidad y reduce tiempos muertos en la producción. Este enfoque modular permite a las empresas adaptarse rápidamente a las demandas del mercado y ofrecer productos con acabados personalizados.
El diseño ergonómico y compacto de muchas máquinas automáticas actuales facilita su integración en espacios de producción con limitaciones físicas, además de simplificar las tareas de mantenimiento y operación. Esto contribuye a una mayor eficiencia operativa y a la reducción de costos asociados a la instalación y el uso diario. Asimismo, la reducción de ruido y vibraciones generadas durante el proceso mejora las condiciones ambientales dentro de las plantas industriales.
Desde la perspectiva medioambiental, estas máquinas incorporan tecnologías para minimizar el impacto ecológico, como sistemas de recuperación y reciclaje de líquidos y compuestos abrasivos, reducción en el consumo energético mediante motores eficientes y automatización inteligente que optimiza los ciclos de trabajo para evitar consumos innecesarios. Estas características no solo cumplen con normativas cada vez más estrictas, sino que también permiten a las empresas posicionarse como responsables y sostenibles frente a sus clientes y sociedad.
Por último, el soporte técnico y la capacitación son elementos clave para maximizar el rendimiento de las máquinas automáticas para acabado y pulido. Los fabricantes suelen ofrecer programas de formación para los operarios, mantenimiento preventivo y soporte remoto, garantizando así un funcionamiento óptimo y prolongado de los equipos. La disponibilidad de piezas de repuesto y actualizaciones de software también contribuyen a mantener la competitividad y adaptabilidad de las máquinas en un entorno industrial en constante evolución.
Equipos automáticos para pulido de superficies
Los equipos automáticos para pulido de superficies representan una solución avanzada y eficiente para la mejora y acabado de piezas en diversos sectores industriales. Estos sistemas están diseñados para optimizar el proceso de pulido, garantizando uniformidad, alta calidad y reducción significativa del tiempo y esfuerzo manual. Su automatización permite un control preciso sobre parámetros clave como presión, velocidad, trayectoria y duración del pulido, adaptándose a diferentes tipos de materiales y geometrías complejas.
Estos equipos son ampliamente utilizados en la fabricación de componentes metálicos, plásticos, cerámicos y compuestos, brindando acabados que pueden ir desde un pulido básico para eliminar imperfecciones superficiales hasta un acabado espejo o brillante, requerido en aplicaciones que demandan alta estética o funcionalidad, como en la industria automotriz, aeroespacial, médica y electrónica.
La estructura típica de un equipo automático de pulido incluye sistemas de sujeción para posicionar y mantener la pieza estable durante el proceso, unidades motrices que accionan herramientas abrasivas (discos, cepillos, bandas, rodillos), sensores para monitoreo en tiempo real y sistemas de control programables que permiten definir y replicar ciclos de trabajo específicos. Esta integración tecnológica facilita la operación continua y garantiza resultados homogéneos, incluso en producciones a gran escala.
Además, los equipos incorporan sistemas de extracción y filtración de polvo y partículas generadas durante el pulido, contribuyendo a un ambiente de trabajo más seguro y limpio, y cumpliendo con normativas ambientales y de seguridad industrial. Algunos modelos avanzados incluyen tecnología de retroalimentación que ajusta automáticamente los parámetros para compensar el desgaste de los abrasivos o las variaciones en las piezas, asegurando la calidad constante del acabado.
La modularidad y flexibilidad de estos equipos permiten su integración en líneas de producción automatizadas, donde pueden sincronizarse con otras máquinas para lograr un flujo continuo y eficiente. Esto contribuye a mejorar la productividad y reducir costos operativos, además de facilitar la trazabilidad y control de calidad mediante sistemas de monitoreo digital.
Finalmente, el desarrollo constante en materiales abrasivos, control electrónico y software especializado impulsa la evolución de estos equipos, ofreciendo soluciones cada vez más precisas, rápidas y sostenibles. La adopción de equipos automáticos para pulido de superficies se traduce en ventajas competitivas para las empresas, al garantizar acabados de alta calidad, aumentar la eficiencia y minimizar impactos ambientales.
Estos equipos automáticos para pulido de superficies también destacan por su capacidad para adaptarse a diferentes configuraciones productivas, ya sea en lotes pequeños o en producción masiva. Su diseño versátil permite trabajar piezas de variados tamaños y formas, desde pequeñas carcasas electrónicas hasta grandes componentes metálicos, mediante sistemas ajustables de sujeción y herramientas intercambiables. Esto facilita la rápida adaptación a nuevas órdenes de producción sin necesidad de largos periodos de ajuste o reconfiguración.
La precisión en el control de variables como la presión aplicada, la velocidad de rotación y el tiempo de pulido es fundamental para evitar daños en las piezas y garantizar un acabado homogéneo. Para ello, estos equipos integran sensores y sistemas de monitoreo en tiempo real que detectan desviaciones o desgaste en las herramientas abrasivas, realizando ajustes automáticos que mantienen la calidad constante durante toda la operación. Esto reduce el desperdicio de material y prolonga la vida útil de los consumibles, impactando positivamente en los costos y la sostenibilidad del proceso.
Además, la automatización disminuye considerablemente la dependencia de la mano de obra directa, lo que no solo reduce riesgos laborales asociados al contacto con polvos, partículas abrasivas o movimientos mecánicos peligrosos, sino que también libera recursos humanos para tareas de supervisión, mantenimiento y optimización de procesos. Los sistemas de seguridad integrados, como barreras ópticas y paradas de emergencia automáticas, contribuyen a crear un entorno de trabajo más seguro.
La integración de estos equipos en líneas de producción inteligentes permite una coordinación eficiente con otras etapas del proceso productivo, optimizando tiempos y recursos. A través de protocolos de comunicación industrial, los equipos pueden enviar datos a sistemas de gestión y supervisión, facilitando el análisis de rendimiento, la detección temprana de fallas y la planificación de mantenimiento predictivo. Esto mejora la continuidad operativa y la calidad final del producto.
En cuanto al impacto ambiental, muchos equipos automáticos para pulido cuentan con sistemas de recuperación y filtración de polvo y residuos, así como tecnologías que minimizan el consumo energético y la generación de desechos abrasivos. Esta orientación hacia la producción limpia responde a las crecientes exigencias normativas y sociales, permitiendo a las empresas posicionarse como responsables y sostenibles.
Por último, el avance tecnológico continúa impulsando mejoras en estos equipos, incorporando inteligencia artificial y aprendizaje automático para optimizar procesos, adaptarse dinámicamente a variaciones en las piezas y anticipar necesidades de mantenimiento. Estas innovaciones contribuyen a aumentar la eficiencia, reducir costos y garantizar la excelencia en el acabado de superficies, fortaleciendo la competitividad de las empresas en mercados exigentes y en constante evolución.
Además, los equipos automáticos para pulido de superficies están diseñados para facilitar el mantenimiento y la actualización tecnológica, lo cual es esencial para asegurar su longevidad y adaptación a nuevas demandas productivas. Muchas máquinas cuentan con módulos intercambiables y software actualizado, lo que permite incorporar nuevas funciones o mejorar las existentes sin necesidad de reemplazar el equipo completo. Esta capacidad modular contribuye a optimizar la inversión y mantener la competitividad tecnológica a lo largo del tiempo.
El desarrollo de interfaces hombre-máquina (HMI) intuitivas y accesibles simplifica la programación y operación diaria de estos equipos, incluso para operadores con poca experiencia técnica. A través de pantallas táctiles, gráficos claros y menús configurables, se facilita la selección de ciclos de pulido, el ajuste de parámetros y el monitoreo en tiempo real de las condiciones de trabajo, lo que reduce errores y aumenta la productividad.
Otra característica importante es la posibilidad de personalizar los procesos de pulido para cumplir con requisitos específicos del cliente o normativas particulares del sector. Por ejemplo, en la industria médica o aeroespacial, donde la calidad superficial puede afectar la funcionalidad o seguridad del producto, los equipos automáticos permiten cumplir con estándares estrictos mediante controles precisos y documentación detallada del proceso, facilitando la trazabilidad y auditoría.
La integración con tecnologías complementarias como la robótica también ha abierto nuevas posibilidades para el pulido automatizado. Robots equipados con herramientas de pulido pueden trabajar en áreas difíciles de alcanzar o en piezas con geometrías complejas, incrementando la flexibilidad y reduciendo la necesidad de adaptadores específicos. Esta combinación de automatización y robótica contribuye a mejorar la calidad y eficiencia en procesos que tradicionalmente requerían un alto grado de trabajo manual.
Finalmente, la adopción de equipos automáticos para pulido de superficies representa una inversión estratégica que aporta beneficios tanto en la calidad del producto como en la optimización de recursos. Al reducir tiempos de ciclo, minimizar rechazos y retrabajos, y mejorar la seguridad laboral, estas tecnologías permiten a las empresas responder con mayor agilidad a las demandas del mercado y mantener altos estándares competitivos, convirtiéndose en un pilar fundamental dentro de la industria manufacturera moderna.
Las máquinas automáticas para tratamiento superficial son equipos diseñados para mejorar, proteger y preparar las superficies de diversos materiales mediante procesos controlados y repetibles. Estas máquinas abarcan una amplia gama de tecnologías que incluyen pulido, abrillantado, desbarbado, granallado, limpieza química, revestimientos y otras técnicas que buscan modificar las propiedades superficiales para incrementar la durabilidad, estética, resistencia a la corrosión o funcionalidad de las piezas.
Estas máquinas están desarrolladas para operar con alta precisión y eficiencia, reduciendo la intervención manual y garantizando resultados uniformes incluso en grandes volúmenes de producción. Incorporan sistemas automatizados de sujeción, posicionamiento y manipulación de las piezas, lo que permite adaptar el proceso a diferentes tamaños y geometrías con un mínimo tiempo de ajuste. Además, cuentan con controles programables que facilitan la replicación exacta de ciclos de tratamiento según las especificaciones técnicas requeridas.
En el ámbito industrial, el tratamiento superficial automático es crucial para optimizar la vida útil de componentes metálicos, plásticos y otros materiales, mejorando su rendimiento en aplicaciones exigentes. Por ejemplo, en la industria automotriz y aeroespacial, el acabado superficial puede afectar significativamente la resistencia al desgaste y la fatiga, mientras que en la fabricación de dispositivos médicos o electrónicos, la limpieza y el acabado son determinantes para el correcto funcionamiento y la seguridad.
Estas máquinas suelen integrar tecnologías avanzadas de monitoreo y control en tiempo real, que permiten ajustar parámetros como temperatura, presión, velocidad, composición química o intensidad del tratamiento para mantener una calidad constante y evitar daños en las piezas. Asimismo, incluyen sistemas de filtración, extracción y reciclaje de residuos generados durante el proceso, contribuyendo a un ambiente de trabajo seguro y al cumplimiento de normativas ambientales.
La flexibilidad y modularidad son características esenciales en estas máquinas, facilitando su incorporación en líneas de producción automatizadas y su adaptación a nuevos procesos o materiales. Esto resulta especialmente valioso en sectores donde las exigencias cambian rápidamente o donde se requiere personalización de los productos. Además, el uso de software especializado y la conexión a redes industriales permiten una gestión integrada, optimización del rendimiento y mantenimiento predictivo.
Finalmente, la evolución constante en materiales, tecnología de control y automatización impulsa el desarrollo de máquinas automáticas para tratamiento superficial cada vez más sofisticadas, que no solo mejoran la calidad y productividad sino que también promueven prácticas industriales más sostenibles y seguras. La adopción de estas tecnologías se traduce en ventajas competitivas para las empresas, al garantizar productos de alta calidad, reducir costos operativos y minimizar impactos ambientales.
Estas máquinas automáticas para tratamiento superficial también ofrecen una notable reducción en los tiempos de ciclo, lo cual incrementa significativamente la capacidad productiva y la eficiencia operativa. Gracias a la automatización y a los sistemas de control avanzado, se puede realizar un tratamiento preciso y repetible que evita errores comunes en procesos manuales, tales como un pulido desigual o la aplicación inadecuada de recubrimientos. Esto resulta en un menor porcentaje de piezas rechazadas y una disminución de retrabajos, lo que se traduce en ahorro de tiempo y recursos.
La implementación de tecnologías como la robótica y los sistemas de visión artificial permite una mayor adaptabilidad y precisión en la manipulación y tratamiento de las piezas, incluso en geometrías complejas o piezas con características variables. Los robots pueden ajustar dinámicamente la trayectoria y la fuerza aplicada según el análisis en tiempo real, asegurando que cada superficie reciba el tratamiento adecuado sin dañarla. Esto es especialmente valioso en sectores como la industria médica, aeroespacial o electrónica, donde los requisitos de acabado son extremadamente rigurosos.
Los sistemas de automatización integrados en estas máquinas facilitan la monitorización y control remoto de los procesos, posibilitando la recopilación de datos en tiempo real que pueden analizarse para mejorar la calidad y predecir necesidades de mantenimiento. Esto reduce el tiempo de inactividad no planificado y aumenta la vida útil de los equipos. Además, la conectividad con sistemas de gestión empresarial (ERP, MES) permite una planificación más eficiente y una trazabilidad completa del proceso, desde la materia prima hasta el producto final.
En términos de sostenibilidad, estas máquinas incorporan soluciones para minimizar el impacto ambiental, tales como sistemas de recuperación y reciclaje de abrasivos y líquidos de proceso, así como tecnologías que optimizan el consumo energético. Estas características contribuyen a cumplir con normativas ambientales cada vez más estrictas y a reducir la huella ecológica de la producción, alineándose con las demandas del mercado y las expectativas sociales.
Finalmente, la formación especializada y el soporte técnico que ofrecen los fabricantes aseguran que los operadores puedan maximizar el rendimiento de las máquinas y adaptarlas a las cambiantes necesidades del mercado. La evolución tecnológica continúa impulsando mejoras en estas soluciones automáticas para tratamiento superficial, integrando inteligencia artificial y aprendizaje automático que permiten optimizar procesos, adaptarse a variaciones en tiempo real y anticipar posibles fallas. Esto posiciona a estas máquinas como elementos clave para la competitividad y eficiencia de la industria manufacturera moderna.
Las máquinas automáticas para tratamiento superficial también se caracterizan por su capacidad de integración en sistemas productivos más amplios, donde actúan como eslabones fundamentales dentro de cadenas de fabricación totalmente automatizadas. Gracias a su diseño modular y a la compatibilidad con protocolos de comunicación industrial, estos equipos pueden sincronizarse con estaciones de ensamblaje, inspección y embalaje, lo que permite un flujo continuo de producción con mínima intervención humana. Esta integración favorece no solo la optimización de tiempos y recursos, sino también una mayor trazabilidad y control de calidad en toda la cadena.
Otro aspecto relevante es la personalización de los procesos que estas máquinas permiten. Los parámetros de tratamiento pueden ajustarse para cumplir con requisitos específicos de diferentes industrias o clientes, desde acabados rugosos para mejorar la adhesión de pinturas o recubrimientos, hasta superficies ultra lisas y pulidas para aplicaciones médicas o electrónicas. Esta flexibilidad posibilita que un mismo equipo pueda atender múltiples líneas de productos o cambios en el diseño sin necesidad de adquirir maquinaria adicional, optimizando la inversión y facilitando la respuesta rápida a las demandas del mercado.
En cuanto a la tecnología incorporada, el uso de sensores avanzados para la medición y control en tiempo real es cada vez más frecuente. Estos sensores permiten detectar irregularidades, desgastes de herramientas o cambios en las condiciones del proceso, activando ajustes automáticos o alertas para mantenimiento preventivo. La incorporación de inteligencia artificial y análisis de datos históricos posibilita la mejora continua del proceso, identificando patrones que ayudan a optimizar parámetros y reducir costos.
Asimismo, la seguridad laboral es un componente esencial en el diseño de estas máquinas. Los sistemas automáticos minimizan la exposición de los operarios a agentes nocivos, movimientos mecánicos peligrosos y partículas generadas durante el tratamiento superficial. Además, incorporan mecanismos de protección, como paradas de emergencia, sensores de presencia y enclavamientos, que garantizan un ambiente de trabajo seguro y conforme a las normativas vigentes.
Finalmente, la evolución constante en materiales abrasivos, tecnologías de control y automatización está impulsando el desarrollo de máquinas automáticas para tratamiento superficial cada vez más sofisticadas, que contribuyen a mejorar la calidad, reducir costos, aumentar la productividad y minimizar el impacto ambiental. La adopción de estas soluciones representa una ventaja competitiva para las empresas, permitiéndoles satisfacer las crecientes exigencias del mercado con productos de alta calidad y procesos eficientes y sostenibles.
Sistemas automáticos de acabado
Los sistemas automáticos de acabado representan una evolución tecnológica clave en la manufactura moderna, orientados a optimizar la calidad superficial de piezas y componentes mediante procesos controlados, repetibles y de alta precisión. Estos sistemas engloban diversas tecnologías y métodos que permiten lograr acabados superficiales uniformes, desde pulidos y abrillantados hasta texturizados o tratamientos específicos para mejorar la funcionalidad y estética del producto final.
Estos sistemas están diseñados para integrarse fácilmente en líneas de producción automatizadas, ofreciendo un control riguroso sobre parámetros como velocidad, presión, abrasividad, y tiempo de exposición, lo que garantiza resultados consistentes incluso en lotes grandes o con piezas de geometrías complejas. La automatización elimina gran parte de la variabilidad que puede introducir el trabajo manual, disminuyendo el porcentaje de defectos y aumentando la productividad global.
Entre las tecnologías más comunes en los sistemas automáticos de acabado se encuentran el pulido mecánico con abrasivos controlados, el desbarbado automático, el granallado, el rectificado y la aplicación de recubrimientos superficiales mediante pulverización o deposición física. Estos procesos pueden combinarse o ajustarse para obtener acabados específicos, como superficies espejo, texturas mate o patrones decorativos, según los requerimientos técnicos y estéticos.
La incorporación de sensores y sistemas de visión artificial permite el monitoreo en tiempo real de la calidad superficial, detectando irregularidades o desviaciones para corregir parámetros de forma automática. Esto se traduce en una reducción de desperdicios y mejora continua del proceso. Además, muchos sistemas cuentan con interfaces de usuario intuitivas y software avanzado que facilita la programación, supervisión y mantenimiento predictivo, reduciendo la necesidad de intervención directa y mejorando la seguridad operativa.
La versatilidad y modularidad de estos sistemas automáticos permiten su aplicación en sectores muy diversos, como la automoción, aeroespacial, electrónica, fabricación de dispositivos médicos, joyería, y otros, donde la calidad del acabado puede impactar directamente en el desempeño, durabilidad o aceptación comercial del producto. La capacidad de adaptarse a diferentes materiales, tamaños y formas los convierte en herramientas imprescindibles para la competitividad industrial actual.
Finalmente, el desarrollo continuo en tecnologías de automatización, inteligencia artificial y materiales abrasivos está impulsando la evolución de estos sistemas automáticos de acabado, promoviendo procesos más eficientes, sostenibles y con menor impacto ambiental. La implementación de estos sistemas no solo mejora la calidad y consistencia del producto final, sino que también contribuye a optimizar recursos, reducir costos y asegurar un entorno de trabajo más seguro para los operarios.
Los sistemas automáticos de acabado incorporan tecnologías avanzadas que permiten un control exhaustivo del proceso y una gran repetibilidad en los resultados. Gracias a la integración de sensores de presión, velocidad, temperatura y vibración, estos sistemas pueden ajustar de manera dinámica las condiciones de trabajo para adaptarse a variaciones en las piezas o en el material, garantizando un acabado uniforme y de alta calidad. La automatización reduce también el desgaste prematuro de herramientas y abrasivos, optimizando su vida útil y disminuyendo costos operativos.
La robotización juega un papel fundamental en estos sistemas, especialmente en aplicaciones que requieren gran precisión o en piezas con geometrías complejas. Los robots equipados con cabezales de pulido o herramientas específicas pueden seguir trayectorias programadas y realizar movimientos suaves y repetitivos que superan la capacidad manual, además de poder trabajar durante largos periodos sin fatiga ni pérdida de calidad. Esto aumenta la productividad y permite atender mayores volúmenes de producción con estándares elevados.
Además, estos sistemas suelen estar diseñados con un enfoque modular, facilitando la integración de diferentes etapas de acabado en un mismo flujo productivo. Por ejemplo, una línea automática puede incluir estaciones sucesivas para desbarbado, pulido grueso, pulido fino y abrillantado, todas sincronizadas para optimizar tiempos y evitar manipulación manual intermedia. Esta configuración reduce tiempos muertos y mejora la consistencia del producto final.
En cuanto a la sostenibilidad, los sistemas automáticos de acabado incorporan cada vez más soluciones para minimizar el consumo energético, reducir el uso de abrasivos y líquidos, y gestionar adecuadamente los residuos generados. Tecnologías como la recuperación y reciclaje de abrasivos o sistemas de filtración avanzada para líquidos de proceso contribuyen a disminuir el impacto ambiental, además de cumplir con normativas cada vez más exigentes en materia de seguridad y medio ambiente.
La evolución constante de estas tecnologías también se refleja en la incorporación de inteligencia artificial y análisis de datos, que permiten anticipar posibles fallas, optimizar parámetros de operación y mejorar la calidad a través del aprendizaje automático. Estos avances impulsan un mantenimiento predictivo eficiente y una mayor autonomía en los procesos, reduciendo intervenciones humanas y aumentando la fiabilidad de la producción.
Finalmente, la implementación de sistemas automáticos de acabado aporta beneficios tangibles en términos de reducción de costos, aumento de productividad, mejora en la calidad del producto y mayor seguridad para los operarios. La inversión en estas tecnologías se traduce en una ventaja competitiva significativa, especialmente en mercados donde la calidad del acabado y la eficiencia productiva son factores determinantes para el éxito comercial.
Los sistemas automáticos de acabado también facilitan la estandarización de procesos, lo que es fundamental para empresas que buscan certificaciones de calidad o que operan en mercados con altos requerimientos técnicos. Al eliminar la variabilidad inherente al trabajo manual, se asegura que cada pieza cumpla con especificaciones exactas, lo que reduce reclamos y mejora la satisfacción del cliente. Además, la trazabilidad que ofrecen estos sistemas permite registrar parámetros de cada ciclo, lo que es útil para auditorías internas y externas.
En la práctica, la implementación de sistemas automáticos puede transformar líneas de producción tradicionales, al permitir una mayor flexibilidad para la fabricación de lotes pequeños o productos personalizados sin sacrificar eficiencia. Los cambios de configuración son rápidos y pueden ser gestionados desde interfaces digitales, lo que reduce tiempos de setup y facilita la adaptación ante nuevas demandas del mercado o cambios en el diseño del producto.
Otra ventaja relevante es la mejora en las condiciones laborales, ya que los operarios quedan liberados de tareas repetitivas, físicamente exigentes o que implican exposición a polvo, ruido o productos químicos. Esto no solo incrementa la seguridad y bienestar de los trabajadores, sino que también contribuye a reducir accidentes y bajas laborales, aspectos que impactan directamente en la productividad y costos de la empresa.
El futuro de los sistemas automáticos de acabado apunta hacia una mayor integración con tecnologías de la Industria 4.0, donde la conectividad, el análisis en la nube y la inteligencia artificial permitirán procesos aún más inteligentes y autónomos. Se espera que estas innovaciones habiliten sistemas capaces de autodiagnosticarse, optimizarse y adaptarse en tiempo real, maximizando la eficiencia y calidad con un mínimo de intervención humana.
En resumen, la adopción de sistemas automáticos de acabado representa una inversión estratégica para cualquier empresa que busque mantenerse competitiva en un mercado global cada vez más exigente, permitiendo mejorar la calidad, reducir costos, optimizar tiempos y promover un ambiente de trabajo más seguro y sostenible.
Equipos automáticos para pulido industrial
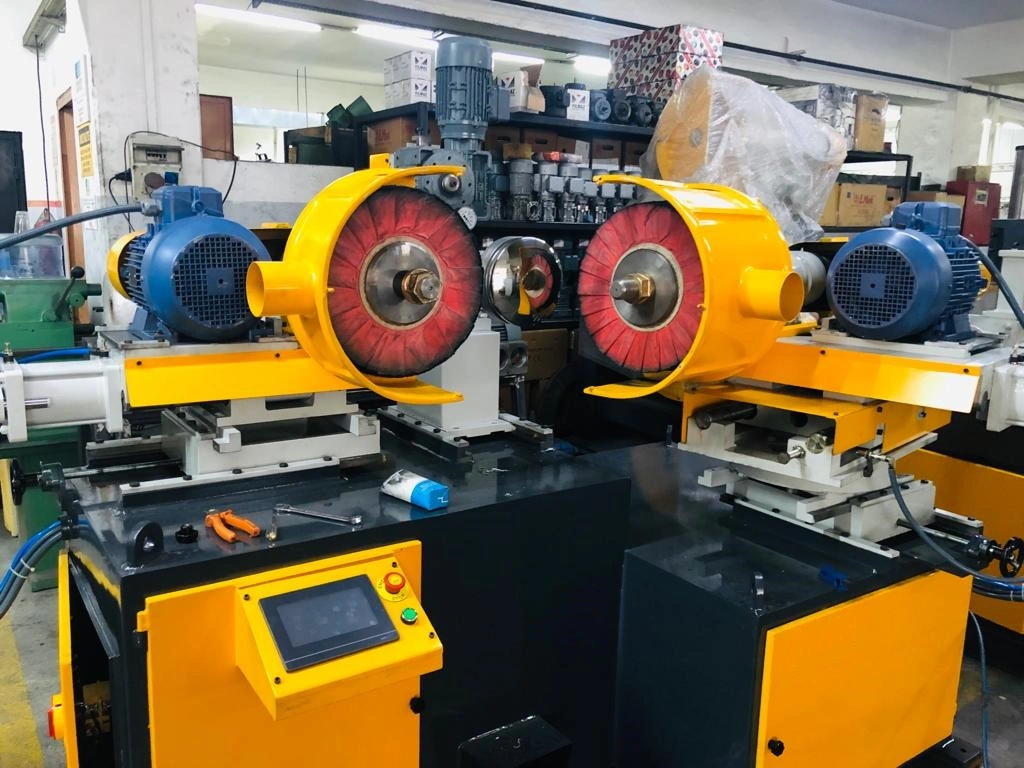
Los equipos automáticos para pulido industrial son máquinas diseñadas para realizar procesos de acabado superficial con alta precisión, eficiencia y consistencia, especialmente en entornos de producción a gran escala. Estos equipos eliminan la variabilidad del trabajo manual, garantizando que cada pieza alcance el nivel de pulido deseado, ya sea para eliminar imperfecciones, preparar superficies para recubrimientos o lograr acabados estéticos como el brillo espejo.
Estos sistemas están equipados con mecanismos automatizados que pueden incluir mesas giratorias indexadas, brazos robotizados, cabezales de pulido con control de presión y velocidad, así como sensores para monitorear el proceso en tiempo real. Esto permite ajustar parámetros dinámicamente y asegurar un pulido homogéneo incluso en piezas con geometrías complejas o materiales variados, desde metales hasta plásticos o compuestos.
Los equipos automáticos para pulido industrial suelen formar parte de líneas de producción integradas, donde se sincronizan con etapas previas y posteriores, como limpieza, desbarbado, inspección y embalaje. Esta integración reduce tiempos muertos y mejora la productividad global. Además, muchos cuentan con interfaces de control intuitivas que facilitan la programación y supervisión remota, así como la recopilación de datos para análisis y mantenimiento predictivo.
Otra ventaja fundamental es la reducción de riesgos laborales, ya que al automatizar procesos que pueden ser físicamente demandantes o peligrosos, se mejora la seguridad de los operarios y se minimiza la exposición a partículas o agentes abrasivos. Además, la precisión de estos equipos contribuye a disminuir el desperdicio de materiales y prolongar la vida útil de herramientas y abrasivos, impactando positivamente en los costos operativos.
En el contexto actual, donde la sostenibilidad y eficiencia energética son prioridades, los equipos automáticos para pulido industrial incorporan tecnologías para optimizar el consumo de energía, reciclar abrasivos y gestionar residuos de forma responsable, alineándose con normativas ambientales y expectativas del mercado.
La evolución constante de estos sistemas, impulsada por avances en automatización, robótica e inteligencia artificial, está permitiendo el desarrollo de soluciones cada vez más inteligentes, capaces de adaptarse en tiempo real a las condiciones del proceso y anticipar necesidades de mantenimiento, lo que incrementa la confiabilidad y calidad del acabado final.
En conclusión, la adopción de equipos automáticos para pulido industrial representa una inversión estratégica para las industrias que buscan mejorar su competitividad, calidad de producto y eficiencia operativa, al mismo tiempo que promueven un ambiente de trabajo más seguro y sostenible.
Los equipos automáticos para pulido industrial están diseñados para satisfacer las exigencias de distintos sectores productivos, tales como la automoción, aeroespacial, electrodomésticos, fabricación de herramientas, metalurgia y fabricación de dispositivos médicos, entre otros. La capacidad para trabajar con diferentes tipos de materiales, desde aceros inoxidables, aluminio, cobre, hasta aleaciones especiales, hace que estos equipos sean altamente versátiles y adaptables a diversos procesos industriales.
Uno de los componentes clave en estos sistemas es la mesa giratoria indexada, que permite posicionar la pieza con precisión y rotarla en ángulos específicos para un pulido uniforme en todas sus superficies. Esto es especialmente útil en piezas con geometrías complejas o múltiples caras que requieren atención detallada sin necesidad de reubicarlas manualmente, lo que reduce tiempos y errores.
La incorporación de células robotizadas en el proceso de pulido ha revolucionado la automatización, ya que los robots pueden ejecutar movimientos precisos y repetitivos con herramientas de pulido, eliminando la fatiga humana y aumentando la productividad. Estos robots están equipados con sensores de fuerza y retroalimentación que les permiten adaptar la presión aplicada según las características de la pieza, evitando daños y asegurando acabados consistentes.
Además, los equipos automáticos para pulido industrial suelen integrar sistemas de control avanzados que monitorean variables críticas como velocidad, presión, temperatura y desgaste de las herramientas. Estos sistemas pueden generar alertas o realizar ajustes automáticos para mantener la calidad y evitar paradas inesperadas, contribuyendo a una operación más eficiente y confiable.
La modularidad es otra ventaja significativa de estos equipos, ya que permite agregar o combinar diferentes estaciones de trabajo para procesos consecutivos de desbarbado, pulido grueso, pulido fino y abrillantado. Esta configuración optimiza el flujo de trabajo y reduce la manipulación manual, disminuyendo el riesgo de daños y contaminación de las piezas.
Desde una perspectiva ambiental, los equipos automáticos están diseñados para minimizar el consumo de recursos y la generación de residuos. Se implementan sistemas de filtración y recirculación de líquidos de pulido, así como técnicas que reducen el uso de abrasivos o sustituyen materiales tradicionales por opciones más sostenibles. Esto no solo contribuye a la protección ambiental, sino que también mejora la eficiencia económica al reducir costos asociados con materiales y disposición de residuos.
La implementación de software especializado permite una gestión integral del proceso de pulido, desde la programación inicial hasta el seguimiento en tiempo real y la recopilación de datos históricos para análisis y mejora continua. Esto facilita la trazabilidad del producto y el cumplimiento de normativas de calidad, además de permitir una rápida adaptación a nuevos diseños o requerimientos del mercado.
En resumen, los equipos automáticos para pulido industrial representan una solución integral que combina tecnología avanzada, eficiencia operativa y sostenibilidad, aportando beneficios clave en la calidad del producto, la reducción de costos y la mejora de las condiciones laborales. Su adopción es cada vez más común en industrias que buscan mantenerse competitivas en un entorno globalizado y exigente.
Estos equipos automáticos para pulido industrial también contribuyen a la optimización de los tiempos de producción, ya que permiten un ciclo de trabajo continuo y repetible, sin la necesidad de intervenciones frecuentes por parte del operador. Esto se traduce en una mayor capacidad productiva y en la posibilidad de cumplir con plazos ajustados sin comprometer la calidad del acabado final. Asimismo, la automatización reduce la probabilidad de errores humanos y garantiza la uniformidad en cada lote de producción.
La integración con sistemas de visión artificial es otro avance relevante en esta área, ya que permite la inspección automática de las piezas antes, durante y después del proceso de pulido. Los sensores ópticos detectan imperfecciones, variaciones en el brillo o inconsistencias en la superficie, y pueden enviar información en tiempo real para ajustar parámetros o descartar piezas que no cumplen con los estándares. Esto mejora el control de calidad y minimiza reprocesos costosos.
En cuanto al mantenimiento, los equipos automáticos para pulido están diseñados para facilitar tareas de limpieza y reemplazo de componentes, con accesos y estructuras modulares que reducen los tiempos de parada y simplifican la gestión del equipo. Además, gracias a sistemas de monitoreo continuo, es posible anticipar el desgaste de herramientas y programar intervenciones preventivas que evitan fallos imprevistos y prolongan la vida útil de la maquinaria.
La seguridad es otro aspecto crítico contemplado en estos equipos, incorporando protecciones físicas, sensores de presencia y sistemas de parada automática ante situaciones de riesgo. Esto asegura que los operarios puedan trabajar en un entorno protegido, incluso cuando la máquina está en funcionamiento, cumpliendo con las normativas vigentes de salud y seguridad industrial.
Por último, el desarrollo de tecnologías complementarias, como la utilización de abrasivos ecológicos, pulidos en seco o sistemas de pulido ultrasónico, está ampliando las capacidades y aplicaciones de los equipos automáticos para pulido industrial. Estas innovaciones permiten abordar materiales y acabados más delicados o exigentes, ampliando el espectro de industrias y productos que pueden beneficiarse de la automatización en el pulido.
En conclusión, la combinación de precisión, eficiencia, seguridad y sostenibilidad convierte a los equipos automáticos para pulido industrial en una pieza fundamental para la modernización de los procesos de fabricación, respondiendo a las demandas actuales de calidad, productividad y responsabilidad ambiental.
Máquinas automáticas para acabado espejo
Las máquinas automáticas para acabado espejo son equipos especializados diseñados para conseguir superficies con un brillo y reflejo casi perfectos, similares a un espejo, mediante procesos controlados y repetibles. Estas máquinas se emplean principalmente en industrias donde la estética y la calidad superficial son críticas, como la fabricación de componentes para automóviles, dispositivos electrónicos, utensilios de cocina, instrumentos médicos y piezas decorativas, entre otros.
El proceso de acabado espejo implica una serie de etapas de pulido y abrillantado que eliminan microimperfecciones, rayas y marcas superficiales, logrando una superficie extremadamente lisa y reflectante. Las máquinas automáticas integran sistemas mecánicos y electrónicos que permiten controlar con gran precisión la velocidad, presión y trayectoria de las herramientas de pulido, asegurando uniformidad en toda la pieza y evitando daños o sobrecalentamiento.
Entre las tecnologías más comunes en estas máquinas se encuentran los sistemas con mesas giratorias indexadas, que permiten posicionar la pieza en ángulos específicos para un pulido homogéneo, y las células robotizadas equipadas con sensores de fuerza y retroalimentación que ajustan automáticamente la presión aplicada durante el proceso. Esto es esencial para adaptarse a diferentes geometrías y materiales, desde metales blandos como el aluminio hasta aceros inoxidables o aleaciones especiales.
Además, estas máquinas suelen incorporar abrasivos y compuestos pulidores de alta calidad, optimizados para conseguir un acabado espejo en menor tiempo y con menos desgaste. Los sistemas automáticos permiten cambiar parámetros según el tipo de material o el acabado requerido, facilitando la producción de lotes variados sin perder eficiencia.
El control digital avanzado, mediante software específico, facilita la programación de ciclos personalizados, el monitoreo en tiempo real y la documentación de cada proceso para garantizar la trazabilidad y cumplimiento de estándares de calidad. Esto resulta especialmente valioso en sectores regulados donde la consistencia del acabado es un requisito fundamental.
La automatización de este proceso no solo mejora la calidad del acabado, sino que también reduce considerablemente el tiempo de producción y la intervención manual, disminuyendo riesgos laborales relacionados con el manejo de herramientas abrasivas o la exposición a polvo y partículas finas. Esto contribuye a un ambiente de trabajo más seguro y ergonómico.
Finalmente, las máquinas automáticas para acabado espejo están evolucionando hacia la integración con tecnologías de inteligencia artificial y aprendizaje automático, lo que permitirá en el futuro ajustar y optimizar los parámetros del proceso en tiempo real, anticipando y corrigiendo desviaciones para lograr acabados cada vez más perfectos con mínima supervisión.
En resumen, estas máquinas representan una solución avanzada para industrias que requieren acabados superficiales de máxima calidad, combinando precisión, eficiencia y seguridad para mejorar la competitividad y valor agregado de sus productos.
Las máquinas automáticas para acabado espejo incorporan una serie de innovaciones tecnológicas que potencian la calidad y eficiencia del proceso. Por ejemplo, la utilización de sensores táctiles y sistemas de retroalimentación permite ajustar la presión y velocidad de pulido en tiempo real, adaptándose a las irregularidades y características específicas de cada pieza. Esto asegura un resultado homogéneo y evita defectos como quemaduras o deformaciones superficiales.
Otra característica relevante es la integración de sistemas de refrigeración y lubricación controlada, que reducen la fricción y el calentamiento durante el pulido, prolongando la vida útil de las herramientas y evitando daños en el material. Estas funciones son automatizadas y sincronizadas con el ciclo de trabajo, optimizando el uso de recursos y manteniendo condiciones óptimas durante todo el proceso.
Las máquinas suelen contar con módulos intercambiables que permiten adaptar el equipo a diferentes tamaños y formas de piezas, así como variar los tipos de abrasivos y discos de pulido. Esta flexibilidad facilita la producción de lotes diversos y mejora la capacidad de respuesta ante cambios en las demandas del mercado o en los requerimientos técnicos.
En términos de programación y control, el software especializado permite definir múltiples programas con parámetros personalizados, que pueden ser guardados y reutilizados para garantizar la repetibilidad del proceso. Además, mediante interfaces gráficas intuitivas, los operarios pueden supervisar el estado de la máquina, recibir alertas preventivas y realizar ajustes rápidos sin necesidad de conocimientos técnicos avanzados.
El acabado espejo obtenido con estas máquinas no solo aporta valor estético, sino que también mejora propiedades funcionales de la superficie, como la resistencia a la corrosión, la facilidad de limpieza y la reducción de adherencia de contaminantes. Esto es especialmente importante en aplicaciones médicas, alimentarias y electrónicas, donde la calidad superficial impacta directamente en la seguridad y desempeño del producto final.
En el ámbito de la sostenibilidad, las máquinas automáticas para acabado espejo están diseñadas para minimizar el consumo de abrasivos y energía, así como para facilitar la gestión y reciclaje de residuos generados durante el proceso. Estas características contribuyen a reducir el impacto ambiental y a cumplir con normativas cada vez más estrictas en materia de producción responsable.
El avance constante en tecnologías complementarias, como el pulido asistido por ultrasonido, la integración de visión artificial para inspección automática y la incorporación de inteligencia artificial para optimización continua, están ampliando las capacidades de estas máquinas, posicionándolas como herramientas clave para la industria 4.0.
En conclusión, las máquinas automáticas para acabado espejo representan una combinación avanzada de mecánica de precisión, automatización inteligente y diseño ergonómico, que permite a las empresas obtener productos con acabados superiores, mayor productividad y menor impacto ambiental, asegurando su competitividad en mercados exigentes y dinámicos.
Además de las funciones ya mencionadas, muchas máquinas automáticas para acabado espejo están equipadas con sistemas de aprendizaje adaptativo que mejoran su rendimiento con cada ciclo de producción. Estos sistemas recopilan datos durante el pulido —como la velocidad de desgaste del abrasivo, las fluctuaciones en la presión, la duración de cada etapa— y ajustan automáticamente los parámetros para mejorar los resultados sin intervención humana. Este enfoque de autooptimización es especialmente útil en entornos de fabricación donde se requieren altos volúmenes con una calidad constante.
El acabado espejo también exige condiciones controladas en el entorno de trabajo. Por ello, algunas de estas máquinas se integran en celdas cerradas que incorporan extracción de polvo, ventilación filtrada y sistemas de insonorización. Esto no solo protege la salud del operador, sino que también garantiza que las partículas en suspensión no afecten negativamente el resultado final del pulido. En sectores como el médico, aeroespacial o de artículos de lujo, donde el más mínimo defecto superficial puede ser inaceptable, este control ambiental es esencial.
En cuanto a la interfaz hombre-máquina (HMI), los fabricantes de equipos de pulido espejo invierten en pantallas táctiles interactivas con menús simplificados y modos de ayuda integrados. Esto facilita la formación del personal y reduce el riesgo de errores operativos. Además, muchas máquinas incluyen conectividad remota que permite diagnóstico técnico a distancia, actualizaciones de software o asistencia en línea, disminuyendo los tiempos de parada en caso de fallos.
Desde el punto de vista del diseño mecánico, los sistemas de sujeción de piezas se han vuelto cada vez más sofisticados. Algunos equipos usan fijación por vacío o mandriles automáticos que centran y posicionan la pieza con máxima precisión. Esto permite lograr un contacto óptimo con las herramientas de pulido, especialmente en formas irregulares o superficies curvas, manteniendo una presión constante durante todo el proceso.
En cuanto al mantenimiento, muchas de estas máquinas automáticas están equipadas con sistemas de autodiagnóstico que verifican periódicamente el estado de componentes clave, como motores, correas, sensores, y consumibles. Esto permite realizar mantenimiento preventivo de manera eficiente, evitando paradas no planificadas que pueden afectar la producción en serie.
Un punto importante a destacar es que el acabado espejo no es únicamente decorativo. En algunos casos, como en moldes para inyección de plástico o en componentes ópticos, un pulido espejo mejora el rendimiento funcional del producto, disminuyendo la fricción, aumentando la resistencia al desgaste o mejorando la transmisión de luz. Por ello, las máquinas dedicadas a este tipo de acabado no solo aportan estética, sino también una mejora funcional del componente tratado.
En definitiva, estas máquinas representan una evolución técnica clave en los procesos de acabado de superficies, al permitir no solo una elevada calidad estética, sino también una producción más rápida, controlada, trazable y eficiente. Su integración en plantas industriales modernas es una inversión estratégica que responde tanto a las exigencias técnicas como a los desafíos de competitividad y sostenibilidad de la industria actual.
Equipos automáticos para acabado brillante
Los equipos automáticos para acabado brillante están diseñados para proporcionar superficies lisas, reflectantes y uniformemente pulidas en una amplia gama de materiales, especialmente metales como acero inoxidable, aluminio, latón o cobre. Su funcionamiento se basa en procesos de abrasión fina, pulido y abrillantado, ejecutados por sistemas controlados electrónicamente que garantizan precisión, repetibilidad y eficiencia, incluso en producciones de gran escala.
Estos equipos son fundamentales en industrias donde la estética y la calidad visual de las piezas son determinantes, como la fabricación de electrodomésticos, automoción, grifería, utensilios de cocina, mobiliario metálico, herrajes de lujo y componentes arquitectónicos. El acabado brillante no solo mejora el aspecto visual del producto final, sino que también proporciona una mayor resistencia a la corrosión, facilita la limpieza y puede servir como base para recubrimientos o tratamientos adicionales.
Los equipos automáticos para este tipo de acabado suelen incluir brazos robotizados o unidades lineales con herramientas de pulido giratorias, bandas abrasivas de grano fino y ruedas de paño con compuestos pulidores. Estas herramientas se aplican con presión controlada y movimientos precisos sobre la superficie de la pieza, eliminando microimperfecciones y generando el brillo deseado sin dañar el material.
El control de velocidad, presión, tiempo de contacto y secuencia de pasos se realiza mediante un software industrial que permite programar y guardar recetas específicas según el tipo de pieza, material y acabado requerido. Esto no solo acelera el cambio de producción, sino que garantiza una calidad constante y reduce la dependencia de operadores especializados. Además, los sensores integrados pueden monitorear el desgaste de las herramientas y compensar automáticamente las variaciones, asegurando resultados homogéneos a lo largo de todo el ciclo productivo.
Algunos modelos incorporan estaciones múltiples para realizar varios pasos de acabado en una sola pasada, como desbaste, pulido intermedio y abrillantado final. Esto reduce los tiempos de ciclo y minimiza la manipulación de las piezas. Las mesas giratorias indexadas, los transportadores automatizados y los dispositivos de sujeción inteligentes permiten posicionar cada pieza con precisión en cada estación, incluso si tienen geometrías complejas o irregulares.
En términos de sostenibilidad, los equipos modernos están diseñados para minimizar el uso de pastas abrasivas, reducir el consumo energético y facilitar la recolección de residuos metálicos o de polvo generado durante el proceso. También pueden estar equipados con sistemas de filtración y reciclaje de fluidos, lo que disminuye el impacto ambiental y mejora la eficiencia del sistema.
La seguridad del operador también es una prioridad en estos sistemas automáticos. Están equipados con protecciones físicas, sensores de emergencia, sistemas de enclavamiento y diagnósticos integrados que garantizan un entorno de trabajo seguro y reducen al mínimo la exposición directa a agentes abrasivos o piezas en movimiento.
En resumen, los equipos automáticos para acabado brillante representan una solución avanzada que combina estética, eficiencia y control de calidad. Su implementación permite a los fabricantes mejorar el valor percibido de sus productos, reducir tiempos de producción, minimizar errores y mantenerse competitivos en sectores donde la presentación superficial es clave.
Estos equipos automáticos para acabado brillante operan de manera continua y sincronizada gracias a sistemas de control CNC o PLC que gestionan todos los parámetros críticos del proceso. Desde el tipo y velocidad de rotación de las ruedas pulidoras, hasta la presión aplicada sobre la pieza y la dosificación de los compuestos abrillantadores, cada variable es supervisada con extrema precisión. Esta automatización elimina variaciones entre ciclos y reduce el margen de error humano, lo que resulta especialmente valioso en producciones de gran volumen donde la homogeneidad del brillo es indispensable. La posibilidad de almacenar programas preconfigurados para distintas piezas permite que un mismo equipo pueda alternar rápidamente entre diferentes lotes de producción con mínimos ajustes mecánicos. Muchos de estos equipos están preparados para trabajar en sincronía con líneas de montaje o células robotizadas, integrándose perfectamente en procesos industriales automatizados.
La flexibilidad es otra característica clave, ya que pueden adaptarse a productos planos, curvos, tubulares o con geometrías complejas, utilizando cabezales móviles, herramientas intercambiables y mesas indexadas que colocan la pieza en múltiples ángulos sin necesidad de intervención manual. El acabado brillante logrado con estas máquinas no solo tiene un propósito estético, sino que mejora la percepción del producto final, transmitiendo calidad y sofisticación, factores determinantes en sectores donde el diseño es una ventaja competitiva. Además, una superficie bien abrillantada es más resistente al desgaste superficial y a la acumulación de suciedad, lo que prolonga la vida útil del componente y reduce los costos de mantenimiento.
A nivel de sostenibilidad, estos equipos pueden operar con compuestos pulidores formulados para ser menos agresivos con el medio ambiente y con sistemas de reciclaje de materiales de pulido, contribuyendo a procesos de producción más limpios. La inversión en equipos automáticos de acabado brillante también implica una mejora en la trazabilidad y documentación del proceso, ya que muchas máquinas pueden registrar datos de producción, ciclos realizados, parámetros usados y estadísticas de eficiencia, facilitando el control de calidad y las auditorías. En última instancia, estos equipos representan una solución de alto rendimiento que responde tanto a las exigencias del mercado moderno como a la necesidad de eficiencia, precisión y repetibilidad en la fabricación avanzada.
La implementación de equipos automáticos para acabado brillante también permite optimizar significativamente los recursos humanos dentro de la planta de producción. Al reducir la necesidad de operadores especializados en tareas manuales de pulido, se libera personal para otras funciones de mayor valor agregado, y se minimizan los riesgos laborales asociados a la exposición prolongada a vibraciones, ruido, polvo metálico y productos químicos. Este tipo de automatización no reemplaza la supervisión técnica, pero sí transforma el rol del operador en uno más enfocado al monitoreo, ajuste fino y mantenimiento preventivo del sistema.
Otro aspecto relevante es la consistencia visual que estos equipos proporcionan. A diferencia del acabado manual, donde pequeñas diferencias en técnica pueden generar variaciones de brillo o textura, el sistema automático aplica los mismos parámetros con absoluta regularidad, garantizando que cada unidad de producto cumpla con los mismos estándares estéticos. Esto es especialmente importante cuando se producen componentes que estarán juntos en un ensamblaje visible, como electrodomésticos, manijas, perfiles decorativos o herrajes, donde la uniformidad en el acabado es crucial para la percepción de calidad.
Con la ayuda de sensores láser, ópticos o de contacto, algunos equipos son capaces de detectar defectos menores como arañazos, microfisuras o zonas mal abrillantadas durante o después del proceso, permitiendo ajustes automáticos o incluso activando un sistema de rechazo de piezas que no cumplen con el umbral de calidad. Este nivel de control asegura que solo las piezas con el acabado brillante correcto avancen en la cadena productiva, reduciendo desperdicios y evitando retrabajos costosos.
En cuanto a la ingeniería de diseño de estos equipos, suelen fabricarse con estructuras rígidas y materiales resistentes al desgaste, ya que deben operar con alta precisión y soportar condiciones intensivas de trabajo. Los motores de accionamiento son controlados por variadores de frecuencia que optimizan la velocidad de cada herramienta según el punto de contacto con la superficie, evitando marcas o zonas sobrecalentadas. En líneas de producción que trabajan a tres turnos, la confiabilidad mecánica de estas máquinas se convierte en un factor estratégico para mantener los ritmos de entrega.
En industrias que trabajan con normativas estrictas, como la alimentaria o la médica, el acabado brillante cumple además funciones higiénicas, ya que una superficie perfectamente lisa y sin porosidades impide la acumulación de bacterias, residuos o contaminantes. En estos casos, el equipo debe trabajar con un control aún más fino, asegurando que la calidad superficial no comprometa los requisitos sanitarios del producto final.
La evolución de estos sistemas también se orienta hacia la conectividad industrial. Muchos modelos modernos están preparados para integrarse con sistemas de gestión de planta (MES) o plataformas IIoT, lo que permite recopilar en tiempo real datos de rendimiento, consumos, desgaste de herramientas, eficiencia energética y productividad. Esta visibilidad completa facilita la toma de decisiones basadas en datos y la mejora continua del proceso.
Así, los equipos automáticos para acabado brillante no solo responden a una necesidad estética o funcional, sino que se convierten en un componente clave dentro de un ecosistema industrial moderno, orientado a la calidad, la eficiencia operativa, la seguridad del trabajo y la sostenibilidad del proceso productivo.
Máquinas automáticas para lustrado
Las máquinas automáticas para lustrado están diseñadas para ofrecer un acabado final de alta calidad en piezas metálicas y otros materiales, proporcionando superficies suaves, brillantes y libres de imperfecciones visibles. Este tipo de maquinaria se utiliza comúnmente en sectores industriales que requieren un acabado estético superior, como la fabricación de componentes para automóviles, electrodomésticos, artículos de lujo, joyería, y elementos decorativos.
Estas máquinas integran sistemas automatizados que combinan movimientos controlados de herramientas abrasivas o de pulido con la aplicación precisa de compuestos lubricantes o pulidores. Gracias a la automatización, se puede alcanzar un nivel de repetibilidad y uniformidad difícil de lograr con procesos manuales, asegurando que cada pieza lustrada cumpla con los estándares de calidad establecidos.
En general, una máquina automática para lustrado consta de varios componentes clave: un sistema de sujeción o fijación que mantiene la pieza en posición estable, mecanismos motorizados que controlan el movimiento y la velocidad de las herramientas de pulido, y un sistema de dosificación que aplica compuestos abrasivos o lubricantes de forma controlada. Estos elementos trabajan en conjunto bajo la supervisión de un controlador programable que regula tiempos, presiones y secuencias para optimizar el proceso según las características de la pieza y el acabado deseado.
La precisión en la aplicación del lustrado es fundamental para evitar daños en la superficie, como marcas o sobrecalentamiento, y para lograr un brillo homogéneo que realce las propiedades estéticas del material. Por ello, estas máquinas suelen estar equipadas con sensores que monitorean la fuerza aplicada, la velocidad de giro y la temperatura, permitiendo ajustes automáticos durante el ciclo de trabajo para mantener condiciones óptimas.
Otra ventaja de las máquinas automáticas para lustrado es su capacidad para trabajar con diferentes geometrías, desde superficies planas hasta formas complejas y contornos difíciles. Esto se logra mediante cabezales articulados, mesas giratorias indexadas o sistemas robotizados que posicionan las herramientas en ángulos específicos para asegurar una cobertura completa y uniforme del área a tratar.
Además, el uso de estas máquinas contribuye a mejorar la productividad y reducir los costos operativos. La automatización minimiza la intervención humana directa, disminuye el tiempo de ciclo y reduce la variabilidad en el resultado final, lo que implica menos retrabajo y desperdicio de materiales. Al mismo tiempo, la ergonomía del puesto de trabajo mejora, ya que se evitan las tareas repetitivas y físicamente exigentes para los operarios.
En términos de mantenimiento, estas máquinas están diseñadas para facilitar el acceso a las partes móviles y de desgaste, permitiendo realizar reemplazos y ajustes con rapidez y seguridad. La durabilidad de los componentes y la calidad de los sistemas de control electrónico también juegan un papel importante para garantizar la continuidad de la producción sin interrupciones inesperadas.
Finalmente, la integración de máquinas automáticas para lustrado dentro de líneas de producción más amplias, combinadas con otros procesos automáticos de acabado, contribuye a optimizar el flujo de trabajo industrial, mejorar la calidad del producto final y cumplir con los estándares cada vez más exigentes del mercado actual.
Las máquinas automáticas para lustrado representan una evolución significativa en los procesos industriales de acabado superficial, ya que permiten combinar alta precisión con una capacidad productiva elevada, aspectos fundamentales para industrias que demandan acabados estéticos de primer nivel y consistentes en cada lote fabricado. Estos sistemas automáticos están equipados con controles inteligentes que regulan de forma dinámica parámetros esenciales como la velocidad de rotación de las herramientas, la presión ejercida sobre la pieza y el tiempo de exposición, garantizando así que el lustrado sea óptimo y homogéneo.
El diseño modular de muchas máquinas automáticas para lustrado permite adaptarlas fácilmente a distintos tamaños y tipos de piezas, así como integrar diferentes tipos de herramientas abrasivas o de pulido según el material y el acabado deseado. Por ejemplo, algunas están preparadas para intercambiar automáticamente discos o rodillos abrasivos, lo que facilita la adaptación rápida a distintos procesos sin necesidad de detener la producción por largos períodos. Esta flexibilidad también es clave para mantener bajos los costos operativos y aumentar la versatilidad de la planta.
Además, estas máquinas suelen incorporar sistemas avanzados de detección y monitoreo, como sensores de fuerza y vibración, que detectan cualquier anomalía durante el proceso de lustrado y permiten realizar correcciones en tiempo real o detener el ciclo para evitar daños en la pieza. Esto contribuye a reducir el porcentaje de productos defectuosos y garantiza una mayor confiabilidad en la calidad del acabado final.
En muchos casos, las máquinas automáticas para lustrado forman parte de líneas integradas de acabado, donde se combinan etapas como el desbarbado, pulido, abrillantado y finalmente el lustrado, todo coordinado por un sistema central de control que optimiza la secuencia de procesos para maximizar la eficiencia y minimizar tiempos muertos. Estas líneas automatizadas no solo mejoran la calidad superficial, sino que también permiten una trazabilidad completa del producto a través del registro de parámetros y condiciones de cada ciclo de trabajo.
El impacto de estas tecnologías se observa no solo en la mejora estética del producto, sino también en su funcionalidad y durabilidad. Un lustrado bien realizado contribuye a reducir la adhesión de suciedad, facilita la limpieza y puede mejorar la resistencia a la corrosión en ciertos materiales. En sectores donde la apariencia y el desempeño son cruciales, como en la fabricación de dispositivos médicos, productos electrónicos o piezas decorativas, este nivel de acabado representa una ventaja competitiva clara.
Desde el punto de vista medioambiental, muchas máquinas automáticas para lustrado están diseñadas para optimizar el uso de consumibles, reduciendo el desperdicio de compuestos pulidores y el consumo energético mediante sistemas de recuperación y reutilización de materiales y energía. Además, su diseño ergonómico y seguro minimiza la exposición de los operarios a polvo, químicos o vibraciones, contribuyendo a ambientes de trabajo más saludables.
En definitiva, las máquinas automáticas para lustrado constituyen una solución tecnológica avanzada que responde a las demandas actuales de la industria manufacturera, combinando precisión, eficiencia, calidad y sostenibilidad para entregar productos terminados que cumplen con los estándares más exigentes en apariencia y funcionalidad. Su implementación representa una inversión estratégica que impulsa la competitividad y la innovación en diversos sectores industriales.
El avance tecnológico en máquinas automáticas para lustrado continúa su desarrollo hacia sistemas cada vez más inteligentes y conectados, incorporando capacidades de monitoreo en tiempo real y análisis predictivo mediante inteligencia artificial y aprendizaje automático. Estas innovaciones permiten anticipar el desgaste de componentes, optimizar los parámetros de operación y programar mantenimientos preventivos con mayor precisión, evitando paradas no planificadas y prolongando la vida útil de la maquinaria.
Asimismo, la integración con sistemas de manufactura digital y fábricas inteligentes posibilita que las máquinas de lustrado formen parte de ecosistemas productivos donde la información fluye de manera continua entre diferentes etapas del proceso. Esto facilita la trazabilidad completa del producto, el control de calidad automatizado y la toma de decisiones basadas en datos, lo que se traduce en una mayor eficiencia y reducción de costos operativos.
Por otro lado, la creciente demanda por acabados especializados y personalizados ha llevado a que las máquinas automáticas para lustrado incorporen tecnologías que permiten variar parámetros en función de características específicas de cada lote o pieza, adaptándose a diferentes tipos de materiales, texturas o requerimientos estéticos sin necesidad de una intervención manual prolongada. Esto se logra a través de programas flexibles y sistemas de cambio rápido de herramientas o accesorios, incrementando la versatilidad y agilidad de la producción.
Además, la sostenibilidad se vuelve un factor clave en el diseño de estas máquinas, impulsando el desarrollo de procesos que minimizan el consumo de agua, energía y productos químicos, así como la generación de residuos. Tecnologías como la recuperación y reciclaje de abrasivos o la optimización del uso de pulimentos contribuyen a que el proceso de lustrado sea más amigable con el medio ambiente, alineándose con las políticas corporativas y regulaciones ambientales vigentes.
En cuanto a la ergonomía y seguridad, las máquinas modernas incorporan sistemas de protección avanzada que incluyen detección de presencia, paradas automáticas ante situaciones de riesgo y interfaces intuitivas para facilitar la operación y reducir errores humanos. Esto no solo protege a los trabajadores, sino que también garantiza la continuidad del proceso y la calidad del acabado.
En síntesis, las máquinas automáticas para lustrado representan un componente fundamental en la transformación digital y sostenible de la industria del acabado superficial, combinando tecnología avanzada, eficiencia operativa y respeto ambiental para ofrecer soluciones integrales que satisfacen las exigencias del mercado actual y futuro.
Dispositivos automáticos de pulido
Los dispositivos automáticos de pulido son equipos diseñados para realizar el proceso de pulido de superficies de manera eficiente, precisa y repetible, reduciendo la intervención manual y mejorando la calidad del acabado final. Estos sistemas están concebidos para trabajar con una amplia variedad de materiales, incluyendo metales, plásticos, vidrio y otros, y se utilizan en múltiples industrias como la automotriz, aeroespacial, médica, de electrodomésticos y joyería.
Estos dispositivos integran mecanismos motorizados que accionan herramientas abrasivas, tales como discos, cepillos o rodillos de pulido, aplicando fuerzas controladas sobre la superficie a tratar. La automatización permite regular parámetros como velocidad, presión, trayectoria y duración del proceso, asegurando uniformidad y minimizando defectos como marcas, rayaduras o sobrecalentamiento.
Los dispositivos automáticos de pulido pueden ser de diferentes tipos, desde máquinas simples con movimientos lineales o rotativos, hasta sistemas complejos con brazos robotizados que permiten abordar geometrías complicadas y realizar movimientos en múltiples ejes. Esta flexibilidad posibilita adaptarse a distintas formas y tamaños de piezas, mejorando la cobertura del área y la calidad del pulido.
Además, muchos dispositivos incorporan sistemas de control y monitoreo en tiempo real, que utilizan sensores para medir variables como la fuerza aplicada, temperatura y velocidad, facilitando ajustes automáticos durante el proceso. Esto reduce la necesidad de supervisión constante y previene daños tanto en la pieza como en el equipo.
La integración de dispositivos automáticos de pulido en líneas de producción contribuye a aumentar la productividad, ya que permiten ciclos más cortos y mayor consistencia en los resultados, al tiempo que disminuyen la fatiga y riesgos para los operadores. También facilitan la trazabilidad del proceso, registrando datos que permiten garantizar la calidad y cumplir con normativas específicas del sector.
Por otro lado, la incorporación de tecnologías ecoeficientes en estos dispositivos, como sistemas de recuperación de abrasivos o reducción en el uso de compuestos químicos, responde a la creciente demanda por procesos más sostenibles y respetuosos con el medio ambiente.
En resumen, los dispositivos automáticos de pulido representan una solución tecnológica avanzada que optimiza el acabado superficial, mejora la eficiencia productiva y garantiza la calidad requerida por las industrias modernas, siendo una herramienta clave para la competitividad y la innovación en los procesos de manufactura.
Los dispositivos automáticos de pulido han revolucionado los procesos industriales al permitir una estandarización y optimización del acabado superficial que difícilmente se logra con métodos manuales tradicionales. Gracias a la automatización, se puede controlar con gran precisión la presión ejercida sobre la pieza, el ángulo de contacto y la velocidad del movimiento, aspectos que influyen directamente en la uniformidad y el brillo final. Esta precisión también reduce la probabilidad de errores o imperfecciones, lo que minimiza el desperdicio de material y la necesidad de retrabajos, generando ahorros significativos en tiempo y costos.
La adaptabilidad de estos dispositivos es uno de sus mayores beneficios. Por medio de sistemas programables y configurables, es posible ajustar los parámetros para distintos tipos de materiales, desde metales duros como acero inoxidable hasta superficies delicadas como aluminio o plásticos. Esto es especialmente valioso en sectores donde se requiere un acabado estético y funcional específico, como en la fabricación de componentes para la industria médica, electrónica o automotriz. Además, muchos dispositivos cuentan con accesorios intercambiables y módulos que permiten alternar entre procesos de desbaste, pulido fino y abrillantado sin necesidad de cambiar de máquina o interrumpir la producción.
En cuanto a la integración con otras tecnologías, los dispositivos automáticos de pulido suelen formar parte de sistemas de manufactura avanzada que incluyen robótica, visión artificial y control numérico computarizado (CNC). Esta integración permite que el proceso de pulido se adapte en tiempo real a variaciones en la pieza o en las condiciones del proceso, garantizando resultados consistentes incluso en producciones complejas o con alta variabilidad. La incorporación de inteligencia artificial y análisis de datos también está comenzando a implementarse para predecir el desgaste de herramientas y optimizar los ciclos de mantenimiento, contribuyendo a una mayor eficiencia operativa.
Además de la mejora en la calidad y productividad, estos dispositivos ofrecen importantes ventajas en términos de seguridad laboral y ergonomía. Al automatizar tareas que tradicionalmente implicaban esfuerzos repetitivos, exposición a polvo o vibraciones, se reduce significativamente el riesgo de lesiones y enfermedades profesionales. Los sistemas modernos incluyen también protecciones y sensores que detienen automáticamente la operación ante condiciones inseguras, protegiendo tanto al operador como al equipo.
La sostenibilidad es otro aspecto crucial en el diseño y operación de dispositivos automáticos de pulido. Se implementan tecnologías para minimizar el consumo de abrasivos, agua y productos químicos, así como para la captura y filtración de partículas generadas durante el proceso, lo que reduce el impacto ambiental y cumple con las normativas vigentes. Algunos sistemas incorporan circuitos cerrados que reutilizan líquidos de pulido o capturan el polvo para su posterior reciclaje, alineándose con prácticas de producción más limpias y responsables.
En definitiva, los dispositivos automáticos de pulido representan un avance tecnológico fundamental para la industria moderna, permitiendo alcanzar niveles superiores de calidad, eficiencia y sostenibilidad en los procesos de acabado superficial. Su implementación no solo mejora la competitividad de las empresas, sino que también contribuye a crear ambientes de trabajo más seguros y procesos productivos más respetuosos con el medio ambiente, respondiendo así a las demandas actuales del mercado y la sociedad.
La evolución constante de los dispositivos automáticos de pulido también ha impulsado el desarrollo de soluciones específicas para aplicaciones altamente especializadas, donde los requisitos de acabado son extremadamente rigurosos. Por ejemplo, en la industria aeroespacial, donde las piezas deben cumplir con estrictos estándares de precisión y resistencia, estos dispositivos permiten obtener superficies lisas que reducen la fricción y mejoran el rendimiento aerodinámico, al tiempo que garantizan la integridad estructural del componente. De manera similar, en la fabricación de dispositivos médicos implantables, el pulido automático asegura acabados libres de irregularidades que podrían afectar la biocompatibilidad o favorecer la acumulación de bacterias, aumentando así la seguridad para el paciente.
Los avances en materiales abrasivos y tecnologías de pulido también han complementado el desarrollo de estos dispositivos, ampliando las posibilidades de tratamiento superficial. El uso de abrasivos de alta tecnología, como microdiamantes o cerámicas avanzadas, permite un pulido más rápido y efectivo incluso en materiales extremadamente duros o sensibles al calor. Estos avances, combinados con el control automatizado, posibilitan procesos más cortos, menos invasivos y con resultados más consistentes.
Además, la flexibilidad en el diseño de dispositivos automáticos ha permitido la creación de sistemas modulares que pueden ser fácilmente integrados o reconfigurados según las necesidades productivas. Esto es especialmente valioso en plantas donde se manejan múltiples tipos de productos o donde se requiere cambiar frecuentemente el tipo de acabado, ya que se reducen los tiempos de preparación y se mejora la adaptabilidad del proceso.
La digitalización y conectividad de estos dispositivos se han convertido en un factor decisivo para su adopción en entornos industriales modernos. Gracias a la capacidad de conectarse a redes industriales y sistemas de gestión de la producción, es posible monitorizar el estado y desempeño en tiempo real, facilitando la toma de decisiones informadas para optimizar recursos y planificar mantenimientos. Esto se traduce en una mayor disponibilidad operativa y un mejor control de calidad, aspectos esenciales para mantener la competitividad en mercados cada vez más exigentes.
Por último, el impacto social y ambiental de los dispositivos automáticos de pulido no debe subestimarse. Al reducir la necesidad de intervención manual en procesos laboriosos y a menudo peligrosos, se contribuye a mejorar las condiciones laborales y a disminuir la exposición a riesgos físicos y químicos. Al mismo tiempo, la eficiencia energética y el menor consumo de materiales que ofrecen estos sistemas colaboran con la reducción de la huella ambiental de la producción industrial.
En resumen, los dispositivos automáticos de pulido representan una convergencia de innovación tecnológica, eficiencia productiva y compromiso ambiental, posicionándose como una herramienta indispensable para la industria actual y futura. Su continua evolución y adaptación a nuevas exigencias aseguran que seguirán siendo protagonistas en la optimización y mejora de los procesos de acabado superficial en diversos sectores industriales.
Sistemas automatizados para pulido
Los sistemas automatizados para pulido constituyen soluciones integrales que combinan maquinaria especializada, software de control avanzado y tecnologías de sensorización para ejecutar procesos de pulido con alta precisión, repetibilidad y eficiencia. Estos sistemas están diseñados para manejar desde piezas simples hasta geometrías complejas, adaptándose a diferentes tipos de materiales y requisitos de acabado, y permiten optimizar la producción industrial al reducir tiempos de ciclo y mejorar la calidad final.
Un sistema automatizado típico para pulido integra uno o varios mecanismos motorizados que accionan herramientas abrasivas o de pulido, como discos giratorios, cepillos o cintas, controlados mediante programas que regulan parámetros clave como velocidad, presión, recorrido y tiempo de operación. La incorporación de sensores de fuerza, temperatura y vibración permite un monitoreo constante del proceso, facilitando ajustes automáticos en tiempo real para evitar daños a las piezas o al equipo, y garantizar un acabado homogéneo.
La integración con tecnologías robóticas es uno de los aspectos más innovadores en estos sistemas, ya que los brazos robotizados con múltiples grados de libertad pueden acceder a áreas difíciles o realizar movimientos complejos que superan la capacidad de máquinas tradicionales. Esto es especialmente relevante para el pulido de piezas con formas irregulares o detalles delicados, donde la precisión y delicadeza son esenciales para cumplir con estándares estrictos, como los requeridos en la industria aeroespacial, médica o de componentes electrónicos.
Además, los sistemas automatizados para pulido suelen estar conectados a plataformas de manufactura digital o Industria 4.0, permitiendo la recopilación y análisis de grandes volúmenes de datos operativos. Esta conectividad facilita la optimización continua del proceso mediante algoritmos de inteligencia artificial, que pueden predecir el desgaste de herramientas, anticipar fallos o recomendar parámetros óptimos según el tipo de pieza o material. La trazabilidad digital también asegura el cumplimiento de normativas y estándares de calidad, un requisito cada vez más demandado en mercados globalizados.
Desde el punto de vista medioambiental, estos sistemas incorporan tecnologías que minimizan el consumo de abrasivos y productos químicos, así como la generación de residuos y emisiones contaminantes. Por ejemplo, algunos sistemas cuentan con circuitos cerrados para la reutilización de líquidos de pulido o filtros avanzados para capturar partículas en suspensión, contribuyendo a procesos de fabricación más limpios y sostenibles.
En el ámbito de la seguridad laboral, la automatización del pulido reduce la exposición de los operarios a riesgos asociados con la manipulación manual de herramientas abrasivas, polvo y vibraciones. Los sistemas cuentan con dispositivos de protección y detección automática de anomalías, lo que garantiza un entorno de trabajo más seguro y eficiente.
En definitiva, los sistemas automatizados para pulido representan una evolución tecnológica clave para la industria moderna, al combinar precisión, productividad, seguridad y sostenibilidad. Su implementación permite a las empresas enfrentar los desafíos de calidad y competitividad en un mercado cada vez más exigente, facilitando la producción de acabados superficiales de alta calidad con menores costos y un impacto ambiental reducido.
Los sistemas automatizados para pulido han transformado radicalmente los procesos de acabado en múltiples sectores industriales, permitiendo alcanzar niveles de precisión y uniformidad que resultan prácticamente inalcanzables mediante métodos manuales. Estos sistemas no solo optimizan la calidad del producto final, sino que también reducen significativamente los tiempos de producción y los costos asociados, gracias a la estandarización de los ciclos de trabajo y la disminución de errores humanos. Además, al integrar tecnologías avanzadas de control y monitoreo, es posible mantener la consistencia en cada pieza, incluso cuando se trabaja con grandes volúmenes o lotes variados.
La versatilidad de estos sistemas es otro aspecto que ha contribuido a su creciente adopción. Pueden configurarse para atender desde piezas pequeñas y delicadas hasta componentes voluminosos con geometrías complejas, adaptando automáticamente las variables del proceso como presión, velocidad y trayectoria de las herramientas abrasivas. Esto se logra mediante el uso de algoritmos de control que permiten ajustar los parámetros en tiempo real, reaccionando a las condiciones específicas de cada pieza o lote. Esta capacidad de adaptación no solo mejora la eficiencia, sino que también prolonga la vida útil de las herramientas y reduce el consumo de materiales abrasivos.
La integración con robótica avanzada es un factor determinante para ampliar las capacidades de los sistemas automatizados de pulido. Los brazos robóticos con alta flexibilidad y precisión pueden acceder a zonas de difícil alcance, realizar movimientos complejos y reproducir secuencias específicas de pulido que serían imposibles o muy lentas con métodos tradicionales. Esto es fundamental en industrias que demandan acabados impecables, como la aeroespacial, automotriz, médica y electrónica, donde la calidad superficial tiene un impacto directo en la funcionalidad y durabilidad del producto final.
Además, estos sistemas están cada vez más conectados a plataformas de manufactura digital e Industria 4.0, lo que facilita la supervisión remota, la recopilación de datos y el análisis predictivo. Gracias a esto, se pueden anticipar fallos, optimizar mantenimientos y ajustar procesos para maximizar la productividad y minimizar paradas no programadas. La trazabilidad y documentación automática también contribuyen a cumplir con estrictas normativas de calidad y auditorías industriales, lo que es especialmente relevante en sectores regulados.
En cuanto a la sostenibilidad, los sistemas automatizados para pulido incorporan tecnologías que reducen el impacto ambiental del proceso. La optimización en el uso de abrasivos, líquidos y energía, junto con sistemas de reciclaje y filtración, permiten minimizar residuos y emisiones. Esto no solo contribuye a cuidar el medio ambiente, sino que también reduce los costos operativos y mejora la imagen corporativa de las empresas, cada vez más comprometidas con prácticas responsables.
Por último, la seguridad y el bienestar de los operadores se ven significativamente beneficiados con la automatización del pulido. Al eliminar tareas repetitivas y extenuantes, y reducir la exposición a partículas, ruido y vibraciones, se crean ambientes laborales más saludables y seguros. Los sistemas incluyen múltiples dispositivos de protección y protocolos automáticos para detener operaciones ante condiciones anómalas, garantizando la integridad tanto del personal como de las máquinas.
En suma, los sistemas automatizados para pulido representan una convergencia de avances tecnológicos que mejoran la calidad, eficiencia, seguridad y sostenibilidad de los procesos industriales. Su implementación no solo responde a las demandas actuales del mercado, sino que también prepara a las empresas para afrontar los desafíos futuros, posicionándolas en la vanguardia de la manufactura moderna y competitiva.
Además de las ventajas mencionadas, los sistemas automatizados para pulido están evolucionando hacia configuraciones más inteligentes y autónomas, donde la inteligencia artificial y el aprendizaje automático juegan un papel cada vez más importante. Estas tecnologías permiten que los sistemas “aprendan” de cada ciclo de trabajo, identificando patrones en el desgaste de herramientas, variaciones en las características de las piezas y condiciones ambientales, para ajustar de manera proactiva los parámetros del proceso. Esto no solo mejora la calidad y uniformidad del pulido, sino que también reduce la intervención humana, disminuyendo la posibilidad de errores y optimizando el uso de recursos.
La incorporación de visión artificial es otra tendencia relevante, ya que facilita la inspección en línea de las superficies pulidas mediante cámaras y sensores ópticos de alta resolución. Esta capacidad permite detectar defectos o irregularidades en tiempo real, activando mecanismos correctivos inmediatos o descartando piezas fuera de especificación antes de continuar con etapas posteriores. De esta forma, se asegura un control de calidad exhaustivo y se minimizan desperdicios, lo cual es fundamental en sectores donde la precisión es crítica.
En términos de diseño y fabricación, los sistemas automatizados para pulido se están adaptando para ser más modulares y escalables, facilitando su integración en líneas de producción existentes y permitiendo la expansión progresiva según las necesidades del negocio. Esta flexibilidad también implica que pueden configurarse para trabajar con diferentes tipos de abrasivos, velocidades y técnicas de pulido, incluyendo desde procesos convencionales hasta pulidos ultrasónicos o por láser, ampliando así el rango de aplicaciones y materiales compatibles.
El mantenimiento predictivo es otro aspecto que mejora gracias a la automatización y digitalización de estos sistemas. Mediante el análisis de datos recopilados en tiempo real sobre el estado de motores, sensores y herramientas, es posible programar intervenciones antes de que ocurran fallos, evitando paradas inesperadas y extendiendo la vida útil del equipo. Esto contribuye a una mayor disponibilidad y rentabilidad operativa, factores clave en entornos industriales altamente competitivos.
Finalmente, la creciente demanda de personalización en la fabricación está impulsando el desarrollo de sistemas automatizados capaces de manejar lotes pequeños y producciones bajo demanda sin perder eficiencia ni calidad. Esto se logra gracias a la combinación de programación flexible, robótica avanzada y análisis de datos, que permiten adaptar rápidamente los procesos a diferentes diseños y especificaciones, respondiendo a las necesidades del mercado actual de manera ágil y rentable.
En definitiva, los sistemas automatizados para pulido no solo optimizan los procesos tradicionales, sino que están en constante transformación para incorporar nuevas tecnologías y responder a los desafíos de la industria moderna. Su evolución continúa siendo un motor clave para la innovación, eficiencia y sostenibilidad en la fabricación de productos con acabados superficiales de alta calidad.
Máquinas automáticas para abrillantado
Las máquinas automáticas para abrillantado representan una evolución significativa en los procesos industriales de acabado superficial, ofreciendo soluciones eficientes y consistentes para lograr superficies lisas, brillantes y estéticamente superiores en una amplia variedad de materiales y productos. Estas máquinas están diseñadas para automatizar y optimizar la etapa final del pulido, conocida como abrillantado, que realza el brillo y la uniformidad de la pieza, mejorando tanto su apariencia como su resistencia a la corrosión y al desgaste.
Estas máquinas operan combinando movimientos precisos y controlados de herramientas abrasivas finas, como paños, discos de pulido o rodillos especiales, con parámetros ajustables que incluyen velocidad, presión y tiempo de operación. Gracias a la automatización, se garantiza una aplicación homogénea y repetible del proceso, lo que reduce las variaciones propias del trabajo manual y asegura que cada pieza alcance un nivel de brillo uniforme conforme a los estándares requeridos.
Una característica fundamental de las máquinas automáticas para abrillantado es su capacidad para adaptarse a diferentes tipos y tamaños de piezas, desde componentes pequeños y delicados hasta superficies amplias y complejas. Esto se logra mediante sistemas de sujeción flexibles y mesas giratorias o móviles que posicionan la pieza con precisión, facilitando el acceso de las herramientas a todas las áreas necesarias para un acabado perfecto. Además, muchas máquinas integran sensores y sistemas de control que monitorean el proceso en tiempo real, ajustando parámetros para optimizar resultados y evitar daños.
En la actualidad, estas máquinas suelen estar integradas en líneas de producción automatizadas, donde se combinan con sistemas de limpieza, inspección y embalaje para maximizar la eficiencia operativa. La integración con sistemas robóticos permite incluso la manipulación automática de las piezas, desde la carga hasta la descarga, minimizando la intervención humana y aumentando la productividad, especialmente en producciones a gran escala o con altos requerimientos de calidad.
Desde la perspectiva de sostenibilidad, las máquinas automáticas para abrillantado incorporan tecnologías que reducen el consumo de materiales abrasivos y productos químicos, así como la generación de residuos. Sistemas de recuperación y filtración de líquidos de pulido, junto con controles precisos que evitan el uso excesivo de abrasivos, contribuyen a procesos más limpios y responsables con el medio ambiente, alineándose con las tendencias actuales de manufactura verde.
Finalmente, el uso de máquinas automáticas para abrillantado mejora significativamente la seguridad laboral al reducir la exposición de los operarios a polvo, ruidos y vibraciones, además de minimizar el riesgo asociado al manejo manual de herramientas abrasivas. Los sistemas incluyen protecciones integradas y protocolos de seguridad que garantizan un entorno de trabajo seguro y eficiente.
En resumen, las máquinas automáticas para abrillantado son herramientas esenciales para la industria moderna, permitiendo obtener acabados de alta calidad de manera rápida, precisa y sostenible, respondiendo a las exigencias de mercados cada vez más competitivos y exigentes en cuanto a la estética y funcionalidad de sus productos.
Las máquinas automáticas para abrillantado continúan evolucionando gracias a la incorporación de tecnologías avanzadas como la inteligencia artificial, la robótica y el control digital, que les permiten mejorar la precisión y adaptabilidad en sus procesos. Estas innovaciones facilitan la programación de ciclos personalizados para diferentes materiales y geometrías, lo que es fundamental para atender a sectores industriales diversos, desde la joyería y electrónica hasta la automotriz y aeroespacial, donde las exigencias de acabado son extremadamente rigurosas.
Uno de los avances más significativos en estas máquinas es la integración de sensores y sistemas de visión artificial que permiten supervisar en tiempo real la calidad del acabado, detectando imperfecciones, variaciones en el brillo o defectos superficiales que podrían comprometer la funcionalidad o estética del producto. Al contar con esta retroalimentación instantánea, el sistema puede ajustar automáticamente parámetros como la presión de pulido, la velocidad o la duración del proceso, garantizando resultados óptimos y consistentes en cada ciclo.
La modularidad y escalabilidad de las máquinas automáticas para abrillantado permiten a las empresas configurar líneas de producción flexibles que se adapten a cambios en la demanda o a nuevos productos sin necesidad de realizar inversiones significativas en equipos adicionales. Esta característica es especialmente valiosa en industrias que manejan producciones personalizadas o en lotes pequeños, donde la agilidad y eficiencia son clave para mantener la competitividad.
En cuanto a la sostenibilidad, estas máquinas incorporan sistemas de gestión y reciclaje de consumibles, así como tecnologías que optimizan el uso de energía y reducen la emisión de contaminantes. La reducción del desperdicio y el consumo eficiente de recursos no solo ayudan a cumplir con normativas ambientales cada vez más estrictas, sino que también contribuyen a reducir los costos operativos, haciendo que el proceso de abrillantado automático sea una opción económicamente viable y ecológicamente responsable.
Además, la seguridad y ergonomía son aspectos prioritarios en el diseño de estas máquinas. La automatización minimiza la exposición de los operarios a agentes nocivos como polvo, ruido y vibraciones, y los sistemas de protección integrados previenen accidentes y daños a la maquinaria. Esto mejora el ambiente laboral y reduce los tiempos de inactividad por lesiones o fallas, aumentando la productividad y el bienestar del personal.
La capacidad para integrarse con otras tecnologías de manufactura digital, como sistemas de gestión de producción (MES) y plataformas de análisis de datos, posiciona a estas máquinas dentro del paradigma de la Industria 4.0. Esto permite no solo la optimización continua del proceso de abrillantado, sino también la planificación predictiva, mantenimiento anticipado y trazabilidad completa de cada pieza, elementos que aportan un valor añadido en términos de calidad, eficiencia y cumplimiento normativo.
En definitiva, las máquinas automáticas para abrillantado constituyen un componente fundamental en la transformación digital y tecnológica de los procesos industriales de acabado. Su evolución constante y la incorporación de tecnologías innovadoras aseguran que seguirán siendo una solución clave para alcanzar altos estándares de calidad, productividad y sostenibilidad en múltiples sectores productivos a nivel global.
Además de los avances tecnológicos, la versatilidad de las máquinas automáticas para abrillantado se ha incrementado notablemente, permitiendo trabajar con una amplia gama de materiales, incluyendo metales ferrosos y no ferrosos, plásticos, vidrios, cerámicos y materiales compuestos. Esto abre la puerta a su aplicación en sectores muy variados, desde la fabricación de componentes electrónicos y piezas médicas hasta la producción de elementos decorativos y mobiliario de alta gama, donde el acabado superficial es un factor determinante para la funcionalidad y la percepción de calidad.
Los fabricantes de estas máquinas han puesto especial énfasis en el desarrollo de interfaces de usuario intuitivas, que facilitan la programación y el monitoreo del proceso incluso para operarios con poca experiencia técnica. Pantallas táctiles, software amigable y sistemas de diagnóstico integrados permiten una configuración rápida y una supervisión continua, reduciendo el tiempo de entrenamiento y mejorando la eficiencia operativa. Esto también facilita la implementación en plantas que requieren alta rotación de personal o donde la estandarización de procesos es crucial.
Otra característica relevante es la integración de sistemas de autoajuste y calibración automática, que aseguran que la máquina mantenga condiciones óptimas de trabajo sin necesidad de intervenciones manuales frecuentes. Esto no solo mejora la calidad del abrillantado, sino que también alarga la vida útil de las herramientas y reduce los costos de mantenimiento, dos factores críticos en la gestión eficiente de cualquier línea de producción industrial.
La capacidad de realizar procesos multietapa en una sola máquina o línea integrada representa otra ventaja competitiva importante. Por ejemplo, algunas máquinas combinan abrillantado con limpieza, desengrase o aplicación de recubrimientos protectores, creando soluciones completas que simplifican la cadena de valor y reducen tiempos de producción. Esta integración favorece la optimización del espacio en planta y disminuye la manipulación manual, lo que se traduce en una mayor productividad y menor riesgo de daños a las piezas.
En el contexto actual, donde la personalización y la rapidez en la entrega son demandadas por los clientes, las máquinas automáticas para abrillantado permiten responder eficazmente a estas exigencias gracias a su flexibilidad y capacidad para cambiar rápidamente entre distintos programas de trabajo. Esto las convierte en herramientas esenciales para fabricantes que operan bajo modelos de producción ajustada (lean manufacturing) y fabricación aditiva, donde la rapidez y la calidad son pilares fundamentales.
Finalmente, la combinación de estas características convierte a las máquinas automáticas para abrillantado en un elemento estratégico para las empresas que buscan mejorar su competitividad, optimizar recursos y ofrecer productos de alta calidad con acabados impecables. Su evolución tecnológica y funcional continuará siendo un motor clave para la innovación en la industria del acabado superficial, consolidándose como una inversión indispensable para el futuro de la manufactura avanzada.
Estas máquinas automáticas para abrillantado también juegan un papel crucial en la reducción de tiempos de producción y en la mejora de la consistencia del acabado, aspectos esenciales para la competitividad en mercados globalizados. La automatización del proceso permite realizar ciclos de trabajo mucho más rápidos que los métodos manuales, lo que no solo incrementa el volumen de producción sino que también reduce los costos asociados al trabajo intensivo en mano de obra.
La precisión en el control de variables como presión, velocidad y temperatura durante el abrillantado es fundamental para obtener acabados uniformes y libres de defectos. Las máquinas automáticas cuentan con sistemas avanzados de control que permiten ajustar estos parámetros con gran exactitud, evitando problemas comunes como el sobrecalentamiento, marcas de herramienta o desgaste irregular del material. Esto es particularmente importante en piezas con geometrías complejas o superficies delicadas, donde un tratamiento inadecuado puede comprometer la funcionalidad o integridad del componente.
En términos de mantenimiento, estas máquinas están diseñadas para facilitar las tareas preventivas y correctivas mediante accesos rápidos a los componentes, sistemas de autodiagnóstico y alertas tempranas de fallas. Esta capacidad reduce los tiempos muertos de producción y los costos derivados de reparaciones imprevistas, contribuyendo a una mayor disponibilidad operativa y a la optimización de los recursos técnicos y humanos.
La incorporación de soluciones modulares en el diseño de las máquinas permite que los usuarios puedan actualizar o adaptar sus equipos conforme evolucionan las necesidades productivas o aparecen nuevos materiales y tecnologías de acabado. Esto representa una ventaja económica considerable, ya que prolonga la vida útil de la inversión y asegura la compatibilidad con futuras innovaciones tecnológicas.
Asimismo, la creciente demanda por acabados con altos estándares de higiene, especialmente en sectores como el alimentario, farmacéutico y médico, ha impulsado el desarrollo de máquinas automáticas con características específicas, tales como superficies sanitarias, materiales anticorrosivos y sistemas de limpieza automática (CIP – Cleaning In Place). Estas innovaciones aseguran que el proceso de abrillantado cumpla con normativas estrictas y facilite la trazabilidad, elementos fundamentales para la certificación y aceptación en mercados regulados.
Finalmente, el impacto positivo que estas máquinas tienen en la calidad del producto final no solo se refleja en la estética, sino también en la durabilidad y rendimiento funcional. Un acabado bien ejecutado mejora la resistencia al desgaste, la corrosión y facilita posteriores procesos de ensamblaje o recubrimiento, aportando valor añadido a la cadena de producción y posicionando a las empresas que las emplean como líderes en calidad y eficiencia dentro de sus respectivos mercados.
Equipos automáticos para abrillantar
Los equipos automáticos para abrillantar son sistemas diseñados para proporcionar un acabado superficial brillante y uniforme en una amplia variedad de materiales y piezas, optimizando los procesos industriales de pulido y acabado. Estos equipos combinan tecnología avanzada, como robótica, sensores de control y software inteligente, para realizar de manera precisa y eficiente operaciones que tradicionalmente requerían trabajo manual intensivo y especializado.
Estos sistemas automáticos permiten manejar distintas formas y tamaños de piezas, desde componentes pequeños y delicados hasta grandes superficies industriales, garantizando la repetibilidad y calidad del acabado en cada ciclo de producción. Gracias a su programación adaptable, pueden ajustarse para diferentes grados de brillo, niveles de rugosidad y requerimientos específicos según el material a tratar, incluyendo metales, plásticos, vidrios y cerámicos.
Además, los equipos automáticos para abrillantar incorporan mecanismos para controlar variables críticas como la presión aplicada, la velocidad de rotación o movimiento, el tipo de abrasivo y la duración del proceso. Este control preciso minimiza el riesgo de daños o desgastes irregulares, asegurando un acabado homogéneo y de alta calidad que cumple con las exigencias estéticas y funcionales de sectores como el automotriz, aeroespacial, electrónico, médico y de bienes de consumo.
La automatización en estos equipos no solo mejora la productividad al reducir tiempos y costos de operación, sino que también incrementa la seguridad al limitar la exposición directa de los operarios a polvo, ruido y vibraciones. Además, su diseño modular y flexible facilita la integración en líneas de producción existentes y permite su adaptación a futuras necesidades, convirtiéndolos en una inversión rentable y sostenible para las empresas.
Finalmente, la implementación de equipos automáticos para abrillantar contribuye a la optimización de recursos y a la reducción de residuos mediante sistemas de reciclaje de abrasivos y control del consumo energético, alineándose con las tendencias globales hacia procesos industriales más limpios y responsables ambientalmente. Esto convierte a estos equipos en piezas clave para la modernización y competitividad de la manufactura avanzada.
Los equipos automáticos para abrillantar representan una evolución significativa en los procesos industriales de acabado superficial, ya que permiten alcanzar niveles de calidad y consistencia que resultan difíciles de lograr mediante métodos manuales. Gracias a la integración de tecnologías como la robótica y la inteligencia artificial, estos sistemas pueden realizar tareas repetitivas con alta precisión, reduciendo errores y variaciones entre piezas, lo que es esencial para cumplir con los estrictos estándares de calidad de la industria moderna.
Además, estos equipos ofrecen una gran flexibilidad operativa. Pueden programarse para trabajar con diferentes tipos de materiales y geometrías, adaptándose rápidamente a los cambios en la producción sin necesidad de largos tiempos de preparación o ajustes manuales. Esta capacidad es especialmente valiosa en entornos de fabricación donde se manejan lotes pequeños o personalizados, así como en líneas de producción masiva que requieren alta velocidad y eficiencia.
El control automático de parámetros como la presión, velocidad y tiempo de abrillantado no solo optimiza el acabado sino que también prolonga la vida útil de las herramientas y consumibles utilizados, generando ahorros importantes en costos de mantenimiento y reemplazo. Asimismo, el monitoreo en tiempo real mediante sensores y sistemas de diagnóstico facilita la detección temprana de posibles fallas o desviaciones en el proceso, permitiendo intervenciones rápidas que evitan pérdidas productivas y garantizan la calidad constante del producto final.
Estos equipos suelen estar diseñados con un enfoque ergonómico y de seguridad, minimizando la interacción directa del operador con los elementos de pulido y reduciendo la exposición a agentes contaminantes o peligrosos. Esto no solo mejora las condiciones laborales sino que también contribuye a cumplir con las normativas de salud y seguridad industrial vigentes.
En cuanto a su implementación, los equipos automáticos para abrillantar pueden integrarse fácilmente en líneas de producción existentes o funcionar como sistemas autónomos, dependiendo de las necesidades específicas de la planta. Su modularidad permite además la incorporación progresiva de nuevas funciones o tecnologías, facilitando la actualización tecnológica y la adaptación a futuras demandas del mercado.
Por último, la adopción de estos sistemas automáticos no solo incrementa la productividad y calidad, sino que también posiciona a las empresas como líderes en innovación y eficiencia, capaces de responder ágilmente a las exigencias cambiantes del mercado global y de ofrecer productos con acabados superiores que añaden valor tangible a sus clientes.
La evolución de los equipos automáticos para abrillantar ha ido acompañada de una creciente integración con sistemas de manufactura inteligente y automatización industrial, lo que ha potenciado aún más su rendimiento y capacidades. Actualmente, estos equipos no solo ejecutan el proceso de abrillantado, sino que también se comunican con otros elementos de la línea de producción para sincronizar tareas, optimizar tiempos y garantizar un flujo constante y eficiente.
Esta conectividad permite recopilar datos en tiempo real sobre el estado de la máquina, la calidad del acabado y el consumo de recursos, información que es vital para implementar estrategias de mantenimiento predictivo y mejora continua. Así, las empresas pueden anticipar posibles fallas antes de que ocurran, reducir paradas no planificadas y maximizar la disponibilidad operativa, traduciéndose en un aumento significativo de la rentabilidad.
Por otra parte, la capacidad de personalización de estos equipos ha mejorado notablemente, ofreciendo opciones que permiten adaptar el proceso de abrillantado a las características específicas de cada pieza, como su tamaño, forma, material y nivel de acabado deseado. Esto es especialmente importante en industrias donde la diversidad de productos y la precisión en los acabados son esenciales, como en la fabricación de componentes electrónicos, piezas médicas o productos de lujo.
Asimismo, la eficiencia energética ha sido un foco clave en el desarrollo de estas máquinas. El diseño de motores de bajo consumo, la optimización de movimientos y la incorporación de sistemas de recuperación y reutilización de materiales abrasivos contribuyen a reducir el impacto ambiental y los costos operativos. Esta conciencia ecológica responde a las demandas crecientes de sostenibilidad por parte de clientes, reguladores y la sociedad en general.
En cuanto a la seguridad, los equipos automáticos para abrillantar están equipados con múltiples dispositivos de protección, como sensores de proximidad, paradas de emergencia y sistemas de control que evitan situaciones de riesgo, protegiendo tanto a los operarios como a las propias máquinas. Esto facilita su uso en entornos industriales exigentes, donde la prevención de accidentes es una prioridad.
Finalmente, la continua innovación en materiales abrasivos, tecnologías de pulido y sistemas de control asegura que los equipos automáticos para abrillantar sigan mejorando en precisión, rapidez y calidad, consolidándose como herramientas indispensables para la manufactura avanzada. Su implementación representa una inversión estratégica para cualquier empresa que busque destacarse en mercados competitivos, ofreciendo productos con acabados superiores, eficiencia operativa y compromiso con la sostenibilidad.
Además, los avances en inteligencia artificial y aprendizaje automático están comenzando a transformar los equipos automáticos para abrillantar, permitiendo que las máquinas “aprendan” de cada ciclo de trabajo y ajusten automáticamente sus parámetros para optimizar el proceso. Esto significa que, con el tiempo, el equipo puede identificar patrones que afectan la calidad del acabado y corregir desviaciones sin intervención humana, mejorando la consistencia y reduciendo el desperdicio.
Otra tendencia importante es la integración de tecnologías de visión artificial y escaneo 3D que permiten inspeccionar la superficie de las piezas antes, durante y después del proceso de abrillantado. Estas herramientas facilitan la detección temprana de defectos o irregularidades, permitiendo que el sistema ajuste en tiempo real la presión o el tiempo de pulido para corregir imperfecciones, elevando significativamente la calidad del producto final.
La modularidad y escalabilidad de los equipos automáticos para abrillantar facilitan su adaptación a distintas escalas productivas, desde talleres pequeños hasta grandes plantas industriales. Esto amplía su accesibilidad y permite que empresas de diversos tamaños puedan beneficiarse de las ventajas de la automatización, mejorando su competitividad y capacidad de respuesta en mercados cada vez más exigentes.
En cuanto al mantenimiento, la incorporación de sistemas de monitoreo continuo y análisis predictivo no solo ayuda a prevenir fallas, sino que también optimiza los ciclos de mantenimiento, evitando intervenciones innecesarias y reduciendo costos. Esto aumenta la vida útil de los equipos y asegura que operen siempre en condiciones óptimas.
Por último, el enfoque en la sostenibilidad y el respeto al medio ambiente sigue ganando protagonismo en el diseño de estos equipos. Se implementan sistemas para minimizar el consumo de agua y productos químicos, gestionar residuos y reducir la emisión de contaminantes durante el proceso de abrillantado, alineándose con las políticas globales de producción limpia y responsabilidad ambiental.
En resumen, los equipos automáticos para abrillantar representan una convergencia de tecnología avanzada, eficiencia operativa, seguridad y sostenibilidad, configurándose como una pieza clave para la industria moderna que busca no solo optimizar sus procesos, sino también ofrecer productos de alta calidad y cumplir con los estándares ambientales y sociales actuales.
Equipos de pulido automáticos
Los equipos de pulido automáticos son sistemas diseñados para realizar procesos de pulido de manera mecanizada y controlada, garantizando acabados superficiales de alta calidad y uniformidad en diversos materiales y piezas. Estos equipos se utilizan ampliamente en industrias como la automotriz, aeroespacial, electrónica, metalúrgica y manufacturera, donde el acabado superficial es fundamental tanto por razones estéticas como funcionales.
La automatización de estos equipos permite programar y controlar parámetros clave del proceso, como la presión aplicada, la velocidad de rotación o desplazamiento, el tipo de abrasivo y el tiempo de pulido. Esto asegura resultados repetibles, disminuye el margen de error humano y mejora la productividad al reducir los tiempos de operación.
Entre las ventajas principales de los equipos de pulido automáticos se encuentran la reducción del esfuerzo físico para los operarios, una mayor seguridad al minimizar la exposición a polvo, ruido y vibraciones, y la posibilidad de integrar estos sistemas en líneas de producción continuas y automatizadas. Además, su diseño modular y adaptable facilita el pulido de piezas con geometrías complejas o tamaños variados, ajustándose a diferentes necesidades de producción.
Estos equipos pueden estar equipados con tecnologías adicionales como sensores de control, sistemas de visión artificial para inspección del acabado en tiempo real, y software avanzado que permite optimizar los procesos y realizar mantenimiento predictivo. La incorporación de robots o células robotizadas en los sistemas de pulido automático también permite manejar piezas delicadas o realizar operaciones complejas con alta precisión.
En términos de sostenibilidad, los equipos automáticos para pulido incorporan sistemas para la reutilización de abrasivos, control del consumo energético y reducción de residuos, contribuyendo a procesos más responsables con el medio ambiente.
En definitiva, los equipos de pulido automáticos representan una solución eficiente y moderna para mejorar la calidad del acabado superficial en la manufactura, optimizando recursos, tiempos y costos, mientras garantizan un entorno de trabajo más seguro y limpio.
Los equipos de pulido automáticos han revolucionado la industria del acabado superficial al combinar precisión, velocidad y repetibilidad en un solo sistema. Gracias a la integración de tecnologías avanzadas, estos equipos pueden adaptarse a diferentes tipos de materiales, desde metales como acero inoxidable, aluminio y cobre, hasta plásticos y composites, lo que los hace extremadamente versátiles. La capacidad para programar secuencias de pulido específicas permite abordar distintos grados de rugosidad y lograr acabados que van desde un pulido básico hasta un acabado espejo o de alta brillantez.
En la operación de estos equipos, la automatización elimina gran parte de la variabilidad que suele introducir el factor humano, garantizando que cada pieza reciba el mismo tratamiento con precisión constante. Esto es especialmente importante en sectores donde la calidad del acabado afecta directamente al desempeño o la estética del producto final, como en la fabricación de componentes médicos, piezas aeroespaciales o productos electrónicos de alta gama.
Además, el uso de equipos automáticos para pulido permite optimizar el consumo de materiales abrasivos y lubricantes, gracias a sistemas inteligentes que regulan su aplicación en función de la necesidad real durante el proceso. Esta eficiencia reduce no solo los costos operativos sino también el impacto ambiental, contribuyendo a prácticas de manufactura más sostenibles.
La integración de sistemas de monitoreo en tiempo real y análisis de datos permite detectar cualquier desviación en el proceso y ajustar automáticamente los parámetros para mantener la calidad constante. Estos avances también facilitan la implementación de mantenimiento predictivo, minimizando tiempos de paro y aumentando la disponibilidad de los equipos.
En cuanto al diseño, muchos equipos cuentan con configuraciones modulares y compactas, que permiten su instalación en líneas de producción existentes sin requerir grandes modificaciones en el layout de la planta. Esta flexibilidad favorece su adopción tanto en empresas con producción masiva como en talleres que manejan lotes pequeños o personalizados.
Finalmente, la seguridad y ergonomía son aspectos prioritarios en el desarrollo de estos sistemas. La automatización reduce la exposición de los operarios a riesgos asociados al pulido manual, como polvo fino, ruido, vibraciones y contacto con herramientas abrasivas. Los equipos incorporan protecciones, sistemas de extracción de polvo y controles que aseguran un ambiente de trabajo más seguro y saludable.
En conjunto, los equipos de pulido automáticos ofrecen una solución integral para lograr acabados de alta calidad de forma eficiente, segura y sostenible, convirtiéndose en un pilar fundamental para la competitividad y modernización de la industria manufacturera.
Además, los equipos de pulido automáticos permiten una gran adaptabilidad para trabajar con piezas de diferentes formas y tamaños, gracias a sistemas de sujeción y posicionamiento precisos, como mesas giratorias indexadas o células robotizadas. Estas tecnologías permiten que las piezas sean orientadas y expuestas de manera óptima al proceso de pulido, garantizando una cobertura uniforme y evitando áreas sin tratar o excesivamente pulidas.
La incorporación de robots industriales en las células de pulido automático ha ampliado aún más las posibilidades, permitiendo manejar piezas delicadas o complejas que requieren movimientos precisos y repetitivos. Estos robots pueden ser programados para realizar múltiples operaciones en una misma pieza, desde un pulido inicial hasta el acabado final, lo que incrementa la eficiencia y reduce la necesidad de manipulación manual.
Otro aspecto relevante es la integración de tecnologías de control y supervisión digital, que incluyen sensores de fuerza, temperatura y desgaste de herramientas, lo que permite monitorear constantemente el estado del proceso. Esta retroalimentación en tiempo real facilita ajustes inmediatos y mejora la calidad del acabado, evitando defectos y reduciendo desperdicios.
En términos de materiales abrasivos, los equipos automáticos trabajan con una amplia gama de productos, desde discos y cintas abrasivas hasta pastas y compuestos específicos, seleccionados según el tipo de material a pulir y el acabado requerido. La automatización permite controlar la aplicación y dosificación de estos materiales con alta precisión, optimizando su uso y extendiendo su vida útil.
Asimismo, el desarrollo de software especializado para la programación y control de los equipos facilita la adaptación rápida a nuevas piezas o procesos, disminuyendo el tiempo de configuración y aumentando la flexibilidad productiva. Esto es fundamental en industrias que requieren alta variedad de productos o ciclos cortos de fabricación.
Por último, la sostenibilidad continúa siendo un eje central en la evolución de estos equipos. Se implementan sistemas para la recuperación y reciclaje de abrasivos y lubricantes, además de tecnologías para minimizar el consumo energético durante el proceso. Estos esfuerzos contribuyen a reducir la huella ambiental y a cumplir con normativas cada vez más estrictas en materia de responsabilidad ambiental.
En resumen, los equipos de pulido automáticos representan una convergencia entre tecnología avanzada, eficiencia operativa, flexibilidad y sostenibilidad, posicionándose como herramientas clave para la industria moderna que busca maximizar la calidad y productividad en sus procesos de acabado superficial.
La implementación de equipos de pulido automáticos también impacta positivamente en la reducción de costos operativos a largo plazo. Aunque la inversión inicial puede ser significativa, los beneficios derivados de la reducción en tiempos de ciclo, menor consumo de materiales y menor necesidad de retrabajo generan ahorros considerables. Además, al disminuir la dependencia de la mano de obra directa para tareas repetitivas y físicamente exigentes, las empresas pueden optimizar sus recursos humanos hacia actividades de mayor valor agregado, como el control de calidad, mantenimiento predictivo y mejora continua de procesos.
El aumento en la precisión y repetibilidad del pulido automático contribuye a mejorar la calidad general del producto final, reduciendo defectos superficiales que pueden afectar tanto la funcionalidad como la apariencia estética. Esto es crucial en sectores como el médico, automotriz y aeroespacial, donde las especificaciones de acabado son estrictas y pueden influir en el desempeño o seguridad del componente.
En términos de integración industrial, los equipos automáticos de pulido se pueden incorporar dentro de sistemas de manufactura inteligente o Industria 4.0. La comunicación entre máquinas, el análisis de datos y la conectividad permiten la sincronización con otras etapas del proceso productivo, facilitando una operación más fluida y controlada. Esto también permite realizar diagnósticos remotos, actualizaciones de software y ajustes de parámetros sin necesidad de presencia física constante, optimizando la gestión operativa.
Otra ventaja significativa es la reducción del impacto ambiental. Los equipos modernos están diseñados para minimizar el consumo de agua, energía y productos químicos, así como para gestionar adecuadamente los residuos generados durante el proceso. Esto ayuda a las empresas a cumplir con las normativas ambientales y a promover prácticas de producción más sostenibles, aspecto cada vez más valorado por clientes, reguladores y la sociedad en general.
En cuanto al desarrollo tecnológico futuro, se espera que la inteligencia artificial y el aprendizaje automático jueguen un papel cada vez más relevante en la optimización de los equipos de pulido automáticos. Estas tecnologías permitirán anticipar fallas, mejorar la programación de tareas, adaptar procesos en tiempo real y personalizar acabados según especificaciones detalladas, elevando aún más los estándares de calidad y eficiencia.
Finalmente, la formación y capacitación especializada de los operadores y técnicos es fundamental para aprovechar al máximo el potencial de estos equipos. Aunque automatizados, requieren conocimientos para programación, mantenimiento y supervisión, asegurando que la tecnología se utilice de manera adecuada y segura, y que se mantenga en condiciones óptimas para prolongar su vida útil y rendimiento.
En síntesis, los equipos de pulido automáticos constituyen una solución integral que combina innovación tecnológica, eficiencia económica, calidad superior y responsabilidad ambiental, consolidándose como un pilar esencial para la modernización y competitividad de la industria manufacturera en la actualidad y en el futuro cercano.
Máquinas pulidoras automáticas
Las máquinas pulidoras automáticas son dispositivos diseñados para llevar a cabo procesos de pulido y acabado superficial de forma totalmente mecanizada, con el fin de obtener superficies lisas, brillantes y libres de imperfecciones en una amplia variedad de materiales. Estas máquinas se utilizan en sectores industriales donde la calidad del acabado es crucial, como la fabricación de componentes metálicos, piezas automotrices, utensilios de cocina, dispositivos electrónicos, y productos de alta precisión.
El funcionamiento de las máquinas pulidoras automáticas se basa en la combinación controlada de movimientos rotativos, oscilatorios o lineales, aplicados a las piezas junto con medios abrasivos específicos, como discos, cintas o pastas abrasivas. La automatización permite programar con exactitud variables como la velocidad, la presión de contacto, el tiempo de pulido y la cantidad de abrasivo utilizado, lo que asegura una uniformidad constante y repetible en cada ciclo de trabajo.
Una ventaja clave de estas máquinas es la capacidad para trabajar con grandes volúmenes de piezas, incrementando la productividad y reduciendo los tiempos de producción en comparación con el pulido manual. Además, minimizan la fatiga y el riesgo de lesiones en los operarios al eliminar la necesidad de realizar trabajos manuales repetitivos y físicamente exigentes.
Las máquinas pulidoras automáticas pueden integrar sistemas avanzados como mesas giratorias indexadas, que permiten posicionar las piezas con precisión para un pulido uniforme en todas sus caras, o células robotizadas que ofrecen flexibilidad para manejar piezas con geometrías complejas y realizar múltiples operaciones sin intervención humana.
En términos de mantenimiento y operación, estas máquinas están equipadas con sistemas de monitoreo y control que facilitan la detección temprana de desgastes o fallas, optimizando los tiempos de parada y asegurando una mayor vida útil del equipo. Además, el uso eficiente de materiales abrasivos y lubricantes contribuye a reducir costos y el impacto ambiental.
En definitiva, las máquinas pulidoras automáticas representan una solución tecnológica avanzada para obtener acabados superficiales de alta calidad con eficiencia, seguridad y sostenibilidad, adaptándose a las exigencias de la industria moderna y mejorando la competitividad de los procesos productivos.
Estas máquinas han evolucionado significativamente con el tiempo, incorporando tecnologías que permiten mayor precisión y adaptabilidad. Una característica destacada es la programación digital que ofrece la posibilidad de definir parámetros específicos para diferentes tipos de materiales y acabados, lo que facilita el cambio rápido entre productos sin necesidad de ajustes manuales extensos. Esto es especialmente útil en líneas de producción flexibles o en entornos donde la diversidad de piezas es alta y se requiere eficiencia sin sacrificar calidad.
El diseño modular de muchas máquinas pulidoras automáticas también permite incorporar distintos tipos de cabezales de pulido o estaciones múltiples, lo que amplía su versatilidad. Por ejemplo, una misma máquina puede incluir estaciones para desbaste, lijado intermedio y acabado brillante, todo en un solo ciclo automatizado. Esto reduce la manipulación de las piezas y garantiza transiciones suaves entre las etapas del proceso, disminuyendo el riesgo de contaminación cruzada o defectos por mal manejo.
Además, muchas máquinas modernas cuentan con sistemas de aspiración y filtrado integrados para capturar el polvo y los residuos generados durante el pulido, lo que mejora las condiciones de trabajo y protege tanto el ambiente como los componentes electrónicos del equipo. Algunos modelos avanzados también permiten la integración de sensores de presión, temperatura y vibración, que actúan en conjunto con algoritmos de control para ajustar el proceso en tiempo real, asegurando una calidad constante y una protección efectiva de la superficie tratada.
Otro aspecto fundamental es la eficiencia energética. Las nuevas generaciones de pulidoras automáticas están diseñadas para consumir menos energía por ciclo sin reducir la potencia de trabajo, y para gestionar de forma inteligente el uso de sus motores y sistemas auxiliares. Esto responde a las exigencias actuales de sostenibilidad y reducción de costes operativos.
El aspecto estético del acabado también ha cobrado cada vez más importancia. En sectores como el mobiliario metálico, la grifería, los electrodomésticos o la industria de la moda, un pulido espejo o un satinado fino pueden determinar el valor percibido del producto final. Las máquinas automáticas permiten reproducir estos acabados con exactitud en grandes volúmenes, cumpliendo con estándares estéticos exigentes y ofreciendo al mismo tiempo una excelente protección contra la corrosión y el desgaste.
En contextos donde la trazabilidad del proceso es crucial, como en la industria médica o aeronáutica, estas máquinas permiten registrar datos de cada ciclo de pulido, lo que facilita auditorías de calidad y certificaciones. Esto se logra gracias a la conectividad con sistemas de control centralizado y plataformas de gestión de producción, permitiendo una supervisión remota y la integración con cadenas de suministro inteligentes.
Por todo ello, las máquinas pulidoras automáticas no solo representan una mejora en la productividad y calidad de los procesos de acabado, sino que también se convierten en herramientas estratégicas para industrias que buscan innovación, competitividad y sostenibilidad en un entorno de fabricación cada vez más exigente y dinámico.
El diseño ergonómico y compacto de muchas máquinas pulidoras automáticas facilita su incorporación en líneas de producción ya existentes, incluso en plantas con espacio limitado. Esta adaptabilidad estructural permite que tanto pequeñas como grandes empresas puedan beneficiarse de la automatización del pulido sin necesidad de rediseñar toda su infraestructura. Algunas versiones incluso son móviles o modulares, lo que permite su traslado entre diferentes estaciones de trabajo o su ampliación futura conforme aumenten las necesidades de producción.
La reducción en la variabilidad del resultado es uno de los beneficios más valorados. A diferencia del pulido manual, donde la habilidad del operario puede afectar el acabado, las máquinas automáticas garantizan que cada pieza reciba exactamente el mismo tratamiento. Esto es vital en la producción en serie de artículos de consumo, componentes mecánicos o estructuras decorativas, donde cualquier inconsistencia puede generar devoluciones, reclamos o fallos funcionales.
La seguridad también es un aspecto reforzado en las máquinas pulidoras automáticas. Con carcasas protectoras, sensores de parada de emergencia, barreras ópticas y zonas de exclusión, se eliminan muchos de los riesgos tradicionales asociados al trabajo manual de pulido, como cortes, atrapamientos o exposición prolongada al polvo fino de abrasión. Estos sistemas no solo protegen a los operadores, sino que también permiten que las máquinas trabajen de forma continua sin supervisión constante, aumentando la productividad en turnos extendidos o nocturnos.
El desarrollo de nuevas herramientas abrasivas específicamente diseñadas para máquinas automáticas también ha impulsado el rendimiento de estos sistemas. Discos con formulaciones híbridas, cepillos abrasivos de alto rendimiento y pastas optimizadas para automatización han mejorado la capacidad de estas máquinas para trabajar sobre una gama muy amplia de materiales, desde metales ferrosos y no ferrosos hasta plásticos técnicos, vidrio o compuestos avanzados.
En aplicaciones específicas como la industria sanitaria, alimentaria o farmacéutica, donde la limpieza extrema de las superficies es obligatoria, las máquinas automáticas permiten lograr acabados sanitarios con rugosidades controladas, eliminando poros o fisuras donde podrían alojarse contaminantes. Este tipo de acabado solo es viable mediante sistemas automáticos que aseguren homogeneidad total y cumplimiento con normativas internacionales de higiene y seguridad.
La capacidad de estas máquinas para registrar métricas de funcionamiento, detectar desgaste de herramientas y predecir la necesidad de mantenimiento contribuye a mantener la producción activa sin interrupciones inesperadas. Este enfoque predictivo reduce los costos de mantenimiento correctivo y aumenta la disponibilidad operativa del equipo.
Finalmente, cabe destacar que el retorno de inversión (ROI) de una máquina pulidora automática se alcanza en muchos casos en pocos meses, especialmente en industrias con alta rotación de productos o volúmenes importantes. La reducción del trabajo manual, la mejora en la calidad del producto final, la aceleración del tiempo de entrega y la minimización de desperdicios son factores que se traducen en beneficios tangibles y sostenidos en el tiempo. Por estas razones, la incorporación de máquinas pulidoras automáticas ya no es vista como un lujo tecnológico, sino como una necesidad competitiva dentro de los entornos industriales modernos.
Además, estas máquinas se integran cada vez más dentro de células de manufactura inteligentes, donde no operan de forma aislada, sino como parte de un sistema colaborativo con robots manipuladores, estaciones de inspección óptica y software de control de producción. Esta interconexión permite una automatización completa del proceso, desde la alimentación de piezas en bruto hasta su entrega con acabado final, pulido y validado. Los sistemas robotizados, por ejemplo, cargan las piezas en la máquina pulidora, supervisan el progreso del trabajo e incluso pueden sustituir los medios abrasivos cuando es necesario, sin intervención humana.
En sectores como la automoción, la aeronáutica y la electrónica de consumo, donde el diseño y la estética son fundamentales, estas máquinas permiten ofrecer una calidad visual superior en grandes volúmenes de producción. El uso de algoritmos de control adaptativo les permite responder a irregularidades superficiales mínimas y corregirlas en tiempo real, garantizando que el acabado sea uniforme incluso en piezas con geometrías complejas o materiales mixtos. Esto ha abierto nuevas posibilidades en el diseño de producto, ya que los ingenieros pueden contar con procesos que aseguran la viabilidad técnica de acabados exigentes sin comprometer los tiempos de producción.
También hay una creciente tendencia a aplicar estas tecnologías en procesos de repulido o reacondicionamiento de piezas usadas o defectuosas. Las máquinas automáticas pueden recuperar el brillo y la textura original de productos que, de otro modo, serían desechados, contribuyendo así a la economía circular y a prácticas de manufactura sostenible. Esto es especialmente útil en sectores como la joyería, la óptica, o el equipamiento médico, donde el valor del producto es alto y su renovación tiene sentido económico.
La posibilidad de integrar inteligencia artificial o sistemas de autoaprendizaje también está empezando a ser explorada. Estos sistemas permitirán que la máquina ajuste automáticamente sus parámetros según el comportamiento real de las piezas y el estado de desgaste de sus componentes, reduciendo el error humano en la configuración y mejorando el rendimiento global del proceso.
En cuanto a los operadores, su rol se transforma: dejan de ser pulidores manuales para convertirse en técnicos supervisores de sistemas automatizados. Esto mejora las condiciones laborales, reduce la exposición a tareas repetitivas y peligrosas, y eleva el perfil técnico de la mano de obra industrial. Para muchas empresas, esto representa también una oportunidad de reconversión profesional y de desarrollo de nuevas competencias dentro de sus equipos de producción.
En resumen, las máquinas pulidoras automáticas representan un paso clave hacia una manufactura más limpia, rápida, precisa y escalable. A medida que los requisitos de calidad aumentan y las líneas de producción se automatizan, estas máquinas se convierten en piezas centrales en la estrategia de producción de cualquier empresa que aspire a competir en mercados globales exigentes. Con el tiempo, su adopción será tan estándar como lo fueron en su día las fresadoras CNC o las líneas de ensamblaje automatizadas.
Equipos automatizados de pulido
Los equipos automatizados de pulido representan una evolución fundamental en los procesos industriales de acabado superficial, combinando tecnología avanzada con eficiencia y precisión para lograr resultados consistentes y de alta calidad en distintos materiales y aplicaciones. Estos sistemas integran mecanismos de control computarizado, sensores inteligentes y una amplia variedad de herramientas abrasivas adaptadas para funcionar en ciclos programados y repetitivos, lo que reduce significativamente la intervención manual y los errores asociados.
En el núcleo de estos equipos, el control automatizado permite la configuración detallada de parámetros como velocidad de rotación, presión aplicada, trayectoria del cabezal pulidor y duración del proceso. Esta programación flexible facilita el tratamiento de piezas con geometrías complejas y superficies diversas, desde metales hasta plásticos técnicos, vidrios y compuestos especiales. Además, la posibilidad de almacenar y reproducir programas específicos contribuye a mantener la uniformidad de los acabados en lotes grandes y variados, aumentando la productividad y disminuyendo los tiempos muertos.
La integración de sistemas de robotización en los equipos de pulido automatizado potencia aún más su capacidad operativa. Los brazos robóticos pueden manipular piezas delicadas o pesadas con precisión, cargarlas y descargarlas de las estaciones de pulido, y realizar inspecciones visuales o con sensores para garantizar la calidad del proceso. Esta automatización extendida permite operaciones 24/7 con mínima supervisión humana, optimizando la utilización de los recursos y reduciendo los costos laborales y de mantenimiento.
En términos de diseño, los equipos automatizados se caracterizan por estructuras robustas y compactas que facilitan su instalación en líneas de producción ya existentes, con sistemas modulares que permiten ampliar o adaptar la capacidad según las necesidades específicas de la empresa. Además, incorporan sistemas de extracción y filtración de polvo y partículas generadas durante el pulido, asegurando un ambiente de trabajo limpio y seguro para los operarios y protegiendo los componentes electrónicos del equipo contra contaminaciones.
El desarrollo de abrasivos y consumibles específicos para automatización ha mejorado notablemente la eficiencia y calidad del pulido. Materiales abrasivos de última generación, combinados con pastas y líquidos especiales, permiten obtener acabados espejo, satinados o mate con niveles muy bajos de rugosidad superficial, cumpliendo con estándares internacionales en sectores como el automotriz, aeronáutico, médico, y de electrodomésticos.
La conectividad y digitalización de los equipos automatizados de pulido también son un aspecto destacado, ya que posibilitan la integración con sistemas de gestión de producción y mantenimiento predictivo. La recopilación de datos en tiempo real sobre el desempeño de la máquina, desgaste de herramientas y calidad del acabado facilita la toma de decisiones informadas, la reducción de tiempos de parada y la mejora continua del proceso productivo.
En definitiva, los equipos automatizados de pulido no solo aumentan la eficiencia y la calidad en los procesos de acabado, sino que también contribuyen a mejorar la seguridad laboral, reducir el impacto ambiental y optimizar los costos operativos, consolidándose como una inversión estratégica para cualquier empresa que busque mantenerse competitiva y sostenible en la industria moderna.
Los equipos automatizados de pulido continúan evolucionando rápidamente gracias a la incorporación de tecnologías avanzadas que potencian su precisión, versatilidad y facilidad de uso. Entre estas innovaciones destacan los sistemas de control adaptativo, que mediante sensores y algoritmos ajustan automáticamente la presión, velocidad y trayectoria del pulido según las características específicas de cada pieza, compensando posibles variaciones en el material o desgaste de las herramientas abrasivas. Esto garantiza acabados uniformes y reduce la necesidad de reajustes manuales, optimizando tiempos y costos.
Asimismo, la robotización integrada ha alcanzado niveles de sofisticación que permiten realizar operaciones complejas en espacios reducidos y con geometrías muy diversas, desde piezas planas hasta formas tridimensionales intrincadas. Los robots equipados con sistemas de visión y escaneo 3D pueden mapear la superficie de la pieza en tiempo real, detectar imperfecciones y modificar el proceso de pulido en consecuencia, asegurando una calidad superior y menor tasa de rechazo.
La modularidad es otro aspecto clave en el diseño de estos equipos, facilitando su adaptación a distintas líneas productivas y la posibilidad de escalabilidad. Las empresas pueden configurar estaciones de pulido automatizadas a medida, combinando múltiples módulos que realizan diferentes etapas del acabado, como desbarbado, pulido grueso, fino y abrillantado, todo controlado de manera centralizada. Esto permite optimizar el flujo de producción y reducir el espacio requerido en planta.
En términos de sostenibilidad, los equipos automatizados de pulido han incorporado sistemas de recuperación y reciclaje de abrasivos y líquidos de pulido, minimizando el consumo de recursos y la generación de residuos contaminantes. Además, la reducción del trabajo manual disminuye la exposición de los operarios a partículas y químicos, mejorando las condiciones de seguridad e higiene en el entorno laboral.
El acceso a datos en tiempo real mediante la conectividad IoT permite monitorear continuamente el estado del equipo, facilitando el mantenimiento predictivo y evitando paradas inesperadas. Esta recopilación de información también alimenta sistemas de análisis que ayudan a optimizar los parámetros del proceso y a detectar oportunidades de mejora en la eficiencia productiva.
Finalmente, la integración de inteligencia artificial en algunos sistemas avanzados abre nuevas fronteras en el pulido automatizado, con máquinas capaces de aprender y mejorar sus operaciones a partir de la experiencia, anticipando fallos y ajustándose a nuevas demandas sin necesidad de reprogramación manual. Esta evolución tecnológica posiciona a los equipos automatizados de pulido como herramientas esenciales para la industria 4.0, capaces de satisfacer los exigentes requisitos de calidad, rapidez y sostenibilidad que demandan los mercados actuales y futuros.
Además, la tendencia hacia la personalización masiva y la producción en lotes pequeños está impulsando el desarrollo de equipos automatizados de pulido que sean altamente flexibles y reconfigurables. Esto significa que las máquinas no solo deben manejar volúmenes grandes con eficiencia, sino también adaptarse rápidamente a cambios en el diseño, tipo de material o acabado requerido sin necesidad de largas paradas para ajustes. Para ello, se están implementando interfaces intuitivas de programación y sistemas de cambio rápido de herramientas, que facilitan la transición entre diferentes trabajos con mínima intervención humana.
Otra área donde los equipos automatizados están ganando terreno es en el pulido de materiales avanzados y compuestos, como aleaciones ligeras, cerámicos y materiales con recubrimientos funcionales o estéticos delicados. Estos materiales requieren procesos más controlados y específicos para evitar daños o alteraciones no deseadas, y los sistemas automatizados con sensores de fuerza, temperatura y vibración permiten un control preciso para proteger la integridad del producto mientras se logra el acabado deseado.
En paralelo, la integración de tecnologías complementarias como el láser para el acabado superficial, combinado con procesos tradicionales de pulido automático, abre posibilidades inéditas en la mejora de texturas, resistencia al desgaste o propiedades ópticas. Estos procesos híbridos permiten, por ejemplo, realizar microestructuras sobre la superficie que mejoran la funcionalidad sin comprometer la estética, aportando valor añadido a los productos finales.
Desde la perspectiva de la economía circular y sostenibilidad, los equipos automatizados también facilitan la implementación de procesos de reacondicionamiento y reciclaje, permitiendo recuperar piezas usadas o reprocesar componentes que requieren reacondicionamiento estético. Esto no solo reduce costos de materiales, sino que también contribuye a la reducción del impacto ambiental asociado con la fabricación de nuevos productos.
En resumen, la evolución constante de los equipos automatizados de pulido está redefiniendo la manera en que se entienden los procesos de acabado superficial. Su capacidad para combinar precisión, rapidez, adaptabilidad y sostenibilidad los convierte en un pilar fundamental para la industria moderna, capaz de responder a los desafíos técnicos y ambientales del presente y anticiparse a las necesidades futuras del mercado global.
Complementando lo anterior, la ergonomía y la seguridad en el diseño de los equipos automatizados de pulido han cobrado especial relevancia. Los fabricantes integran sistemas de protección física como carcasas de seguridad, sensores de presencia y paradas de emergencia automáticas para prevenir accidentes durante el funcionamiento. Además, el diseño busca minimizar la exposición de los operarios a ruidos, vibraciones y agentes contaminantes, contribuyendo a un entorno laboral más saludable y cumpliendo con normativas internacionales de seguridad industrial.
El mantenimiento predictivo y la monitorización continua son también elementos clave para maximizar la disponibilidad y vida útil de los equipos. Los sistemas integrados pueden detectar señales tempranas de desgaste en componentes mecánicos o eléctricos, programando intervenciones antes de que se produzcan fallos graves. Esto reduce costes operativos y evita interrupciones inesperadas en la producción, garantizando un flujo constante y fiable.
Por otro lado, la formación y capacitación de los operadores para manejar estos sistemas automatizados es fundamental. Aunque muchas tareas son controladas por software y robótica, el personal debe contar con conocimientos técnicos para supervisar el proceso, interpretar datos y realizar ajustes cuando sea necesario. Las interfaces de usuario amigables, con pantallas táctiles y sistemas gráficos intuitivos, facilitan esta interacción y reducen la curva de aprendizaje.
Finalmente, la evolución tecnológica permite que los equipos de pulido automático se integren en ecosistemas digitales más amplios, donde la comunicación con otras máquinas y sistemas de gestión contribuye a la optimización global de la planta productiva. La conectividad permite no solo mejorar la calidad del acabado, sino también reducir desperdicios, optimizar el consumo energético y adaptar dinámicamente la producción a las demandas del mercado, todo en tiempo real.
Esta convergencia de tecnología, seguridad, eficiencia y sostenibilidad posiciona a los equipos automatizados de pulido como herramientas indispensables para las empresas que buscan excelencia operativa y competitividad en un entorno industrial cada vez más exigente y dinámico.
Dispositivos automáticos para pulido
Los dispositivos automáticos para pulido representan una categoría avanzada de maquinaria diseñada para mejorar la eficiencia, calidad y consistencia en los procesos de acabado superficial. Estos dispositivos integran tecnologías de automatización, robótica y control inteligente para realizar operaciones de pulido que, tradicionalmente, requerían intervención manual especializada y tiempos prolongados.
En su funcionamiento básico, un dispositivo automático para pulido combina sistemas motorizados que controlan la velocidad y presión de las herramientas abrasivas con mecanismos de posicionamiento y guía precisos. Esto permite que la superficie de la pieza a tratar reciba un contacto uniforme y controlado, asegurando un acabado homogéneo y reduciendo el riesgo de defectos como marcas, rayas o desgaste irregular.
Una de las ventajas principales de estos dispositivos es su capacidad para trabajar de manera continua y repetitiva, lo que se traduce en un incremento notable en la productividad. Además, al reducir la dependencia del operario para realizar movimientos precisos, disminuye la variabilidad entre piezas y aumenta la reproducibilidad de los resultados, cruciales para industrias que exigen altos estándares de calidad, como la automotriz, aeroespacial, electrónica y manufactura de bienes de consumo.
Los dispositivos automáticos de pulido modernos suelen incluir sistemas de sensores y feedback que monitorean en tiempo real parámetros como la fuerza aplicada, la temperatura de la superficie y el desgaste de las herramientas abrasivas. Esta información se procesa mediante algoritmos que ajustan automáticamente las condiciones del proceso para optimizar el rendimiento y prolongar la vida útil de los consumibles.
Además, muchos dispositivos están diseñados con modularidad y flexibilidad, lo que permite adaptarlos fácilmente a diferentes tipos y tamaños de piezas, materiales y requisitos de acabado. Esto se logra mediante sistemas intercambiables de herramientas, ajustes de recorrido y programación personalizada, facilitando su integración en líneas de producción automatizadas o células robotizadas.
En términos de sostenibilidad, los dispositivos automáticos para pulido contribuyen a la reducción de desperdicios y consumo energético, ya que optimizan el uso de abrasivos y evitan procesos innecesarios o repetitivos. También mejoran las condiciones de trabajo al minimizar la exposición de los operarios a partículas y agentes químicos, fortaleciendo la seguridad y salud laboral.
Finalmente, la incorporación de tecnologías emergentes como la inteligencia artificial, aprendizaje automático y conectividad IoT está impulsando una nueva generación de dispositivos automáticos para pulido que pueden autoajustarse, prever mantenimientos y comunicarse con otros equipos para crear procesos más inteligentes, eficientes y confiables, alineados con los principios de la industria 4.0.
Estos dispositivos automáticos para pulido se caracterizan por su versatilidad y capacidad para adaptarse a una amplia gama de aplicaciones industriales. Desde la fabricación de componentes metálicos hasta productos plásticos o cerámicos, el pulido automático ofrece soluciones precisas que mejoran significativamente el acabado superficial y la apariencia estética de las piezas. Su uso es especialmente valioso en sectores donde la calidad superficial impacta directamente en la funcionalidad o la percepción del producto final, como en la industria médica, electrónica y de bienes de lujo.
La integración de sistemas robóticos permite que estos dispositivos alcancen geometrías complejas y zonas de difícil acceso, garantizando una cobertura total sin comprometer la uniformidad del acabado. Los robots pueden programarse para replicar patrones de movimiento específicos, aplicar fuerzas variables y adaptar la velocidad de pulido según las características particulares de cada pieza. Esto no solo reduce el tiempo de ciclo, sino que también evita errores humanos y minimiza el desgaste innecesario de materiales y herramientas.
En el ámbito del control y monitoreo, la incorporación de tecnologías avanzadas permite la supervisión continua de parámetros críticos durante el proceso. Sensores ópticos, de presión y de temperatura recopilan datos que son analizados en tiempo real para ajustar variables como la velocidad de rotación, la presión de contacto y la duración del pulido. Esta retroalimentación dinámica mejora la calidad del acabado y permite detectar a tiempo cualquier anomalía que pudiera afectar el proceso, optimizando la eficiencia y reduciendo desperdicios.
Además, la modularidad y escalabilidad de estos dispositivos facilitan su implementación en diferentes configuraciones productivas. Desde sistemas autónomos para lotes pequeños hasta líneas completamente automatizadas para producción masiva, los dispositivos automáticos de pulido pueden integrarse con otras tecnologías complementarias como lavado, secado y inspección óptica, creando células de trabajo completas y altamente eficientes.
El impacto ambiental también es un aspecto cada vez más considerado en el diseño y operación de estos equipos. La optimización del consumo de abrasivos, la reducción de residuos y la eficiencia energética forman parte de las mejoras constantes implementadas por los fabricantes. Asimismo, la automatización reduce la exposición del personal a sustancias químicas o partículas generadas durante el pulido, promoviendo un ambiente de trabajo más seguro y saludable.
Finalmente, la evolución tecnológica continúa impulsando innovaciones en dispositivos automáticos para pulido, con la adopción de inteligencia artificial para el análisis predictivo y optimización del proceso, así como la integración con sistemas de manufactura digital. Esto permite no solo mejorar la calidad y productividad, sino también ofrecer mayor flexibilidad y personalización en la producción, respondiendo a las demandas crecientes de mercados cada vez más exigentes y dinámicos.
Estos avances tecnológicos también facilitan la implementación de sistemas de mantenimiento predictivo, donde los dispositivos automáticos para pulido están equipados con sensores y software que monitorean continuamente el estado de sus componentes clave, como motores, ejes y herramientas abrasivas. Al analizar datos en tiempo real, es posible anticipar fallas o desgastes antes de que ocurran, programando intervenciones de mantenimiento en momentos óptimos para evitar paros inesperados y prolongar la vida útil del equipo. Esta estrategia no solo reduce costos operativos, sino que también mejora la confiabilidad y disponibilidad de la maquinaria, elementos fundamentales para mantener altos niveles de producción en entornos industriales competitivos.
Asimismo, la conectividad de estos sistemas con plataformas digitales permite la recopilación y análisis masivo de datos, facilitando la toma de decisiones informadas para la mejora continua del proceso. A través de interfaces intuitivas y dashboards personalizados, los operarios y técnicos pueden visualizar indicadores clave de rendimiento, ajustar parámetros y documentar resultados con mayor precisión y rapidez. Esta digitalización del pulido contribuye a una gestión más eficiente de recursos y a la optimización del flujo productivo, alineándose con los principios de la industria 4.0 y la manufactura inteligente.
El desarrollo de materiales abrasivos y herramientas especializadas también ha evolucionado en paralelo con los dispositivos automáticos para pulido. Se emplean abrasivos de alta durabilidad y eficiencia, que permiten alcanzar acabados superficiales de calidad superior en menor tiempo, además de reducir el consumo de materiales y residuos generados. Estas innovaciones, combinadas con movimientos controlados y precisos de las máquinas, garantizan resultados consistentes y repetibles, indispensables para cumplir con especificaciones técnicas rigurosas.
Además, la ergonomía y la seguridad siguen siendo prioridades en el diseño de estos dispositivos. La automatización de tareas repetitivas y físicamente exigentes minimiza la exposición de los trabajadores a riesgos laborales asociados con el pulido manual, como la fatiga, vibraciones y contacto con partículas abrasivas o químicos. Los sistemas incluyen protecciones, sensores de seguridad y paradas automáticas ante condiciones anómalas, creando un entorno de trabajo más seguro y saludable.
En resumen, los dispositivos automáticos para pulido representan una convergencia de avances tecnológicos, eficiencia operativa y seguridad, permitiendo a las industrias mejorar la calidad de sus productos, reducir costos y adaptarse rápidamente a las demandas cambiantes del mercado. Su desarrollo continuo impulsa una transformación profunda en los procesos de acabado, marcando un camino hacia una manufactura más inteligente, sostenible y competitiva.
La evolución constante de los dispositivos automáticos para pulido también ha impulsado la incorporación de tecnologías de visión artificial y sistemas de inspección automatizada. Estos sistemas permiten evaluar en tiempo real la calidad del acabado, detectando imperfecciones, irregularidades o variaciones en la textura superficial sin necesidad de intervención manual. Al integrar cámaras de alta resolución y software de análisis de imagen, las máquinas pueden ajustar automáticamente parámetros del proceso o separar piezas que no cumplen con los estándares de calidad, mejorando la trazabilidad y reduciendo el retrabajo o desperdicio.
Además, la personalización del proceso de pulido mediante programación avanzada facilita la adaptación a productos con geometrías complejas, diferentes tipos de materiales o acabados específicos requeridos por clientes. Esto es posible gracias a controladores numéricos y software que permiten diseñar secuencias y movimientos precisos, así como ajustar variables como presión, velocidad y tiempo de pulido en función de cada pieza. Esta flexibilidad es especialmente valiosa en sectores que demandan alta variedad de productos o lotes pequeños, donde la eficiencia y calidad no deben sacrificarse.
La integración de robots colaborativos, o “cobots”, ha abierto nuevas posibilidades en el uso de dispositivos automáticos para pulido. Estos robots pueden trabajar de forma segura junto a operadores humanos, complementando tareas donde la automatización completa no es viable o requiere supervisión. Los cobots pueden encargarse de operaciones repetitivas o de alta precisión, mientras que los operarios se concentran en tareas de control y ajuste, aumentando la productividad y la calidad general del proceso.
En el plano ambiental, la implementación de tecnologías para la gestión y reciclaje de residuos generados en el pulido automático es otro aspecto que cobra relevancia. Sistemas de extracción y filtración de partículas, recuperación de abrasivos y uso eficiente de líquidos de pulido contribuyen a minimizar el impacto ambiental, al mismo tiempo que optimizan el consumo de insumos y facilitan el cumplimiento de normativas ambientales cada vez más estrictas.
Finalmente, la capacitación y formación del personal en el manejo de estos equipos automáticos es fundamental para maximizar sus beneficios. El conocimiento en programación, mantenimiento, interpretación de datos y resolución de problemas permite aprovechar al máximo las capacidades tecnológicas de los dispositivos y asegurar procesos estables y de alta calidad. La colaboración entre fabricantes, integradores y usuarios finales es clave para el desarrollo de soluciones a medida, adaptadas a las necesidades específicas de cada industria y proceso productivo.
En definitiva, los dispositivos automáticos para pulido constituyen una pieza esencial en la modernización y optimización de los procesos industriales de acabado, combinando tecnología avanzada, eficiencia operativa, sostenibilidad y seguridad para responder a los retos actuales y futuros de la manufactura global.
Sistemas automáticos para pulir
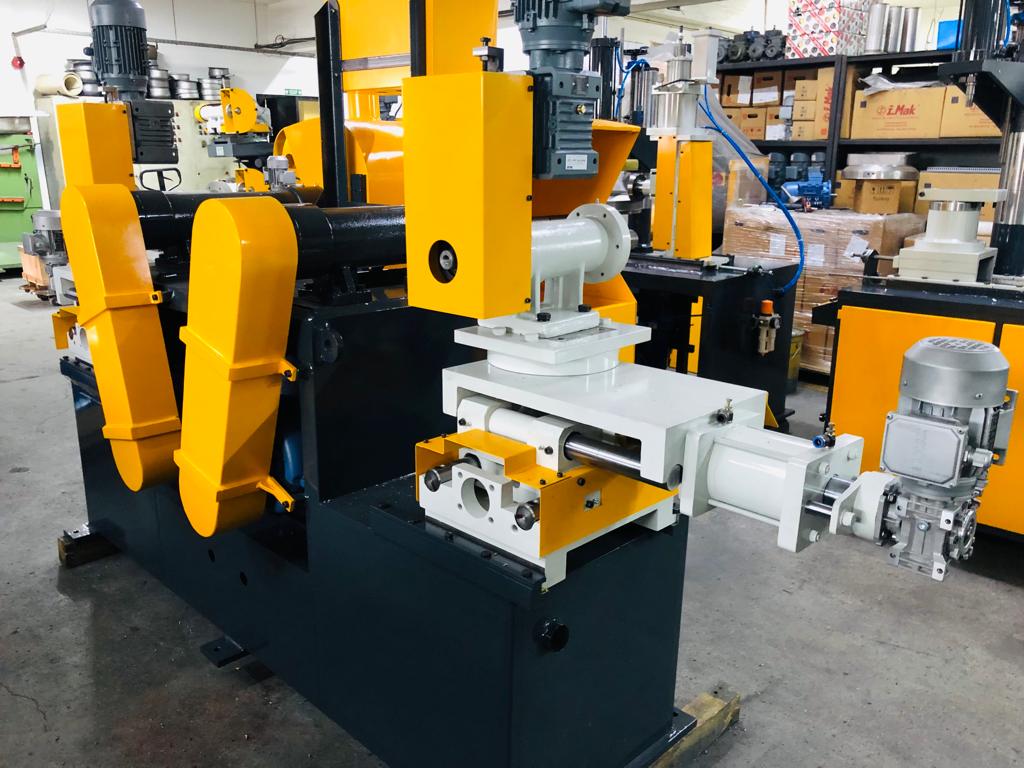
Los sistemas automáticos para pulir representan una evolución significativa en los procesos de acabado industrial, ofreciendo soluciones altamente eficientes y precisas para mejorar la calidad superficial de una amplia variedad de materiales y productos. Estos sistemas están diseñados para realizar tareas de pulido con mínima intervención humana, lo que no solo reduce costos operativos sino que también incrementa la uniformidad y reproducibilidad del acabado final.
En su estructura básica, un sistema automático de pulido suele integrar una combinación de componentes mecánicos, electrónicos y de software que permiten controlar con exactitud parámetros como la velocidad, presión, trayectoria y tiempo de pulido. La configuración típica incluye mesas giratorias o indexadas, robots articulados, unidades de pulido con abrasivos o discos de lustrado, así como sensores para monitorear la calidad y condiciones del proceso. Esta integración facilita la adaptación del sistema a distintos tipos de piezas, tamaños y geometrías, desde componentes planos hasta superficies complejas o tridimensionales.
Uno de los grandes beneficios de estos sistemas es la capacidad de operar en ciclos continuos y repetitivos con alta precisión, eliminando la variabilidad inherente al trabajo manual. La programación avanzada permite definir secuencias específicas y personalizadas para cada lote de producción, ajustando automáticamente las condiciones de trabajo para maximizar la eficiencia y minimizar el desgaste de las herramientas. Además, muchos sistemas modernos incorporan algoritmos de aprendizaje automático que optimizan el proceso con base en los datos recogidos durante la operación, lo que representa un avance hacia la manufactura inteligente.
En cuanto a la calidad del acabado, los sistemas automáticos para pulir garantizan resultados consistentes, con superficies libres de rayaduras, manchas o imperfecciones. Esto es crucial en industrias donde la presentación estética y la funcionalidad están estrechamente ligadas, como la fabricación de productos electrónicos, automotrices, muebles metálicos y artículos de lujo. Asimismo, la automatización permite realizar procesos delicados y precisos, como el pulido de materiales blandos o sensibles, evitando daños que podrían ocurrir con técnicas manuales.
El diseño modular de estos sistemas facilita su integración en líneas de producción existentes, permitiendo que se combinen con otras etapas de acabado o tratamiento superficial, como limpieza, secado, inspección óptica y embalaje. Esto contribuye a crear células de trabajo compactas y eficientes, que optimizan el uso del espacio y reducen tiempos de ciclo. La flexibilidad en la configuración también permite ajustar la capacidad productiva en función de la demanda, adaptándose tanto a producción masiva como a lotes personalizados.
Desde la perspectiva de seguridad y ergonomía, los sistemas automáticos para pulir disminuyen la exposición del operario a riesgos asociados con el pulido manual, tales como vibraciones, polvo, ruido y contacto con productos químicos. La automatización de estas tareas no solo protege la salud del personal, sino que también mejora las condiciones laborales, liberando a los trabajadores para actividades de supervisión, mantenimiento y control de calidad.
Por último, los avances tecnológicos continúan ampliando las capacidades de estos sistemas, con la incorporación de sensores inteligentes, conectividad IoT, análisis de big data y mantenimiento predictivo. Estas innovaciones permiten un monitoreo detallado del proceso, anticipación de fallas, optimización de recursos y mayor trazabilidad, alineándose con las tendencias de la industria 4.0 y la sostenibilidad. Así, los sistemas automáticos para pulir no solo mejoran la eficiencia y calidad, sino que también contribuyen a una producción más flexible, responsable y competitiva en el contexto global actual.
Los sistemas automáticos para pulir han transformado la manera en que las industrias abordan el acabado superficial, brindando una combinación de precisión, velocidad y control que difícilmente se logra con procesos manuales tradicionales. Estos sistemas permiten manejar grandes volúmenes de producción con estándares uniformes, asegurando que cada pieza cumpla con las especificaciones requeridas, lo que es especialmente importante en sectores donde la calidad del acabado influye directamente en el rendimiento o valor del producto final.
La implementación de tecnologías avanzadas en estos sistemas abarca desde motores con control de velocidad variable hasta sensores de fuerza y presión que regulan la intensidad del pulido en tiempo real. Esta regulación dinámica contribuye a evitar daños en las piezas y prolonga la vida útil de los abrasivos y herramientas, optimizando el consumo de materiales y reduciendo costos operativos. Además, el uso de actuadores y sistemas hidráulicos o neumáticos controlados electrónicamente mejora la repetibilidad y precisión de los movimientos, factores cruciales para obtener acabados homogéneos.
Un aspecto fundamental en la evolución de estos sistemas es la integración de interfaces de usuario amigables, que facilitan la programación y ajustes de los parámetros de trabajo sin necesidad de conocimientos profundos en automatización. Gracias a estos avances, los operarios pueden configurar rápidamente ciclos de pulido para diferentes tipos de piezas, con opciones para almacenar programas y consultar históricos de producción, lo que mejora la trazabilidad y el control del proceso. La facilidad de uso también acelera la capacitación y disminuye la dependencia de personal altamente especializado.
La versatilidad de los sistemas automáticos para pulir se manifiesta en su capacidad para trabajar con distintos materiales, tales como metales, plásticos, vidrios y composites, adaptando las técnicas y herramientas según las características específicas de cada superficie. Por ejemplo, en metales se pueden utilizar discos abrasivos o almohadillas de lustrado con compuestos especiales, mientras que en plásticos se emplean técnicas menos agresivas para evitar deformaciones o daños térmicos. Esta adaptabilidad amplía el rango de aplicaciones y sectores industriales que pueden beneficiarse de la automatización del pulido.
En términos de mantenimiento, estos sistemas están diseñados para facilitar la limpieza, reemplazo de componentes y ajustes periódicos, incorporando accesos rápidos y diagnósticos integrados que alertan sobre posibles fallas o desgastes. La planificación del mantenimiento basada en datos reales de operación contribuye a minimizar tiempos muertos y costos asociados, garantizando un funcionamiento confiable y prolongado de la maquinaria. Esto es especialmente valioso en plantas donde la continuidad productiva es crítica para cumplir con plazos y volúmenes de entrega.
Finalmente, el compromiso con la sostenibilidad y la reducción del impacto ambiental también influye en el diseño y operación de los sistemas automáticos para pulir. Se implementan soluciones para el manejo responsable de residuos, reciclaje de abrasivos y líquidos de proceso, así como tecnologías que minimizan el consumo energético y emisiones. Estas prácticas no solo cumplen con regulaciones ambientales, sino que además mejoran la imagen corporativa y la aceptación en mercados que valoran la responsabilidad ambiental.
En conjunto, los sistemas automáticos para pulir representan una pieza clave en la modernización industrial, aportando beneficios tangibles en calidad, eficiencia, seguridad y sostenibilidad. Su continua evolución abre nuevas oportunidades para innovar en procesos de acabado, responder a demandas cada vez más exigentes y consolidar la competitividad de las empresas en un mercado global en constante transformación.
La creciente demanda de acabados superficiales de alta calidad ha impulsado la adopción generalizada de sistemas automáticos para pulir en diversas industrias, desde la automotriz y aeroespacial hasta la fabricación de dispositivos médicos y electrónicos. En estos sectores, la precisión y consistencia del acabado no solo impactan en la estética, sino también en la funcionalidad y durabilidad de los componentes, haciendo que el pulido automático sea un elemento esencial para garantizar la excelencia del producto final.
Estos sistemas incorporan tecnologías de control avanzado que permiten la monitorización en tiempo real de variables críticas como la temperatura, presión de contacto, velocidad de rotación y desgaste de las herramientas abrasivas. Gracias a esta información, el sistema puede realizar ajustes automáticos para mantener condiciones óptimas durante todo el ciclo de pulido, evitando defectos superficiales y prolongando la vida útil de las piezas. Además, la recopilación de datos posibilita el análisis estadístico para identificar tendencias y mejorar continuamente los procesos.
La integración con sistemas de visión artificial y sensores ópticos ha llevado los sistemas automáticos de pulido a un nuevo nivel de precisión. Estos dispositivos permiten inspeccionar la superficie antes, durante y después del proceso, detectando imperfecciones, variaciones de textura o color, y asegurando que se cumplan los estándares establecidos. La retroalimentación inmediata facilita la corrección rápida de desviaciones y reduce el porcentaje de rechazos o retrabajos, mejorando la eficiencia productiva y reduciendo costos.
En cuanto a la configuración física, los sistemas automáticos para pulir pueden variar desde estaciones de trabajo independientes hasta células robotizadas completas que combinan pulido con otras operaciones de acabado. Estas células modulares y flexibles permiten adaptarse a diferentes líneas de producción, optimizando el flujo de materiales y reduciendo tiempos muertos. Además, la automatización contribuye a la estandarización de procesos, fundamental para cumplir con normativas internacionales de calidad y certificaciones específicas del sector.
El impacto en la fuerza laboral también es significativo, ya que la automatización de tareas repetitivas y físicamente demandantes libera a los operadores para enfocarse en actividades de supervisión, mantenimiento, programación y mejora continua. Esto eleva el nivel de especialización requerido y promueve un entorno laboral más seguro y motivador. La formación continua en el manejo y optimización de estos sistemas es clave para maximizar sus beneficios y mantener la competitividad en mercados exigentes.
La evolución tecnológica continúa abriendo nuevas posibilidades, como la incorporación de inteligencia artificial y aprendizaje automático para predecir el comportamiento de los materiales y ajustar el proceso de pulido en consecuencia. Asimismo, la conectividad en red y la integración con plataformas de gestión empresarial facilitan la trazabilidad completa y la toma de decisiones basada en datos, promoviendo una manufactura inteligente y sostenible.
En conclusión, los sistemas automáticos para pulir representan una inversión estratégica que combina innovación tecnológica, eficiencia operativa y calidad superior. Su adopción creciente refleja la necesidad de responder a desafíos productivos modernos, donde la rapidez, precisión y sostenibilidad son requisitos indispensables para el éxito industrial a largo plazo.
Los avances recientes en materiales abrasivos y tecnologías de pulido han complementado y potenciado la eficacia de los sistemas automáticos, permitiendo abordar superficies cada vez más complejas y exigentes. Por ejemplo, la incorporación de abrasivos de alta tecnología, como los compuestos diamantados o cerámicos, ha mejorado la capacidad de eliminar imperfecciones con mayor rapidez y menor desgaste, lo que se traduce en procesos más cortos y menor consumo de insumos. Esto es especialmente relevante en sectores como el aeroespacial, donde las tolerancias superficiales son extremadamente estrictas.
Además, la miniaturización y sofisticación de componentes en industrias como la electrónica han llevado al desarrollo de sistemas automáticos con una precisión micrométrica, capaces de trabajar en piezas muy pequeñas o delicadas sin comprometer su integridad. En estos casos, el control preciso de parámetros como la presión de contacto y la velocidad de pulido es fundamental para evitar daños y asegurar resultados homogéneos, evidenciando la versatilidad y adaptabilidad de estas tecnologías.
En cuanto a la ergonomía y seguridad, los equipos automáticos para pulido han incorporado soluciones que minimizan la exposición del personal a riesgos físicos, como vibraciones, ruido y polvo, mediante recintos cerrados, sistemas de extracción y controles remotos. Esto mejora las condiciones laborales y cumple con normativas de seguridad ocupacional, contribuyendo a un entorno de trabajo más saludable y productivo.
Por otro lado, la integración de estas máquinas en líneas de producción automatizadas facilita la sincronización con otras etapas del proceso productivo, optimizando el flujo y reduciendo tiempos muertos. La comunicación entre sistemas mediante protocolos industriales estándares permite un monitoreo centralizado y una gestión eficiente de recursos, promoviendo la Industria 4.0 y la digitalización de las fábricas.
La capacidad de personalización de los sistemas automáticos para pulido también es notable, con configuraciones ajustables para diferentes formas, tamaños y materiales, así como opciones modulares que permiten añadir funciones complementarias como limpieza, inspección o embalaje. Esta flexibilidad ayuda a las empresas a adaptarse rápidamente a cambios en la demanda o a nuevos productos sin necesidad de grandes inversiones adicionales.
Finalmente, el soporte técnico especializado y la disponibilidad de servicios postventa son componentes clave para el éxito y la longevidad de estos sistemas en la industria. La asistencia en la puesta en marcha, la capacitación continua y el mantenimiento preventivo garantizan que las máquinas funcionen de manera óptima, evitando paradas imprevistas y maximizando la rentabilidad de la inversión.
En resumen, los sistemas automáticos para pulido representan una sinergia entre tecnología avanzada, innovación en materiales y gestión eficiente, que transforma la producción industrial hacia procesos más rápidos, seguros y sostenibles, permitiendo a las empresas alcanzar estándares elevados de calidad y competitividad global.
Máquinas automáticas de pulido
Las máquinas automáticas de pulido son equipos diseñados para realizar procesos de acabado superficial de manera precisa, eficiente y repetitiva, sin la necesidad de intervención manual constante. Estas máquinas son fundamentales en industrias donde la calidad del acabado, la uniformidad y la productividad son esenciales, como en la fabricación de componentes metálicos, plásticos, vidrios, y productos electrónicos, entre otros.
El diseño de estas máquinas incluye diversos sistemas mecánicos y electrónicos que permiten controlar parámetros críticos del proceso de pulido, tales como la velocidad de la herramienta abrasiva, la presión aplicada sobre la pieza, el tiempo de contacto y el tipo de abrasivo utilizado. Gracias a estos controles, las máquinas automáticas pueden adaptarse a diferentes materiales y formas, asegurando un acabado homogéneo y reduciendo el riesgo de errores o daños.
Una característica importante de estas máquinas es su capacidad para integrar tecnologías de automatización, como robots y mesas giratorias indexadas, que permiten manipular las piezas con precisión y repetir el proceso en lotes grandes. Esto aumenta considerablemente la productividad y garantiza la consistencia en la calidad del acabado. Además, muchas máquinas cuentan con sensores y sistemas de monitoreo que supervisan el desgaste de las herramientas y las condiciones del proceso en tiempo real, facilitando el mantenimiento predictivo y evitando paradas inesperadas.
En cuanto a aplicaciones, las máquinas automáticas de pulido se utilizan en la fabricación de piezas para la industria automotriz, aeroespacial, médica, de joyería y electrónica, donde el acabado superficial puede influir directamente en el rendimiento, la resistencia a la corrosión y la apariencia estética del producto final. También son comunes en la producción de utensilios de cocina y artículos decorativos, donde se busca obtener superficies brillantes y libres de imperfecciones.
La versatilidad de estas máquinas permite trabajar sobre una amplia variedad de geometrías, desde superficies planas hasta formas complejas, utilizando diferentes métodos de pulido como el pulido por contacto directo, el pulido orbital o rotativo, e incluso técnicas combinadas. Además, algunas máquinas están diseñadas para operar en ambientes controlados, donde se minimiza la contaminación y se asegura la calidad requerida en industrias altamente reguladas.
Finalmente, la implementación de máquinas automáticas de pulido contribuye a mejorar la seguridad laboral, al reducir la exposición de los operarios a polvos, vibraciones y agentes químicos asociados con el pulido manual. Esto, junto con la mejora en la calidad del producto y la reducción de tiempos de producción, convierte a estas máquinas en una inversión estratégica para empresas que buscan optimizar sus procesos productivos y mantenerse competitivas en mercados exigentes.
Las máquinas automáticas de pulido representan un avance significativo en los procesos industriales al combinar precisión, velocidad y repetitividad. Su capacidad para adaptarse a diferentes tipos de materiales y geometrías ha permitido su integración en múltiples sectores productivos, donde la calidad del acabado superficial es un factor crítico para la funcionalidad y estética del producto final. Al eliminar en gran medida la intervención manual, estas máquinas no solo aumentan la eficiencia, sino que también aseguran una uniformidad que difícilmente se logra con métodos tradicionales.
El desarrollo tecnológico ha impulsado la incorporación de sistemas inteligentes en estas máquinas, como el control numérico computarizado (CNC), que permite programar con exactitud las trayectorias de pulido, tiempos y fuerzas aplicadas. Esto posibilita realizar acabados altamente complejos y personalizados, adaptándose a los requerimientos específicos de cada pieza. Además, la integración de sensores para la detección de la presión de contacto y el desgaste de abrasivos garantiza un monitoreo constante que evita daños y asegura la calidad del proceso.
Otra ventaja destacable es la capacidad de estas máquinas para operar en configuraciones modulares o en líneas de producción automatizadas, donde pueden sincronizarse con otros procesos como el mecanizado, limpieza o inspección visual. Esta integración mejora el flujo productivo y reduce los tiempos de ciclo, permitiendo una mayor capacidad de producción sin sacrificar la calidad. En muchos casos, estas máquinas cuentan con interfaces amigables que facilitan su programación y permiten ajustes rápidos para cambiar de producto o lote.
En términos de mantenimiento, las máquinas automáticas de pulido están diseñadas para facilitar las tareas preventivas y correctivas, contando con componentes de fácil acceso y sistemas de diagnóstico que anticipan posibles fallas. Esto reduce las paradas no planificadas y prolonga la vida útil del equipo, lo que se traduce en una mejor rentabilidad para las empresas que las utilizan. Además, la capacitación especializada del personal en el manejo y mantenimiento de estas máquinas es un factor clave para maximizar su desempeño.
El impacto ambiental también es un aspecto relevante en la evolución de estas máquinas, ya que muchas incorporan sistemas de reciclaje y gestión eficiente de residuos, como polvo y líquidos utilizados durante el pulido. Esto contribuye a cumplir con normativas ambientales y a promover prácticas sostenibles en la industria, alineándose con las tendencias globales de producción responsable.
En definitiva, las máquinas automáticas de pulido constituyen una herramienta indispensable en la manufactura moderna, al permitir alcanzar niveles de acabado superiores con mayor rapidez, seguridad y consistencia. Su continua evolución tecnológica y su integración con sistemas digitales auguran un futuro donde la automatización y la precisión serán la norma en los procesos de acabado superficial.
El avance constante en las máquinas automáticas de pulido está estrechamente vinculado a la evolución de tecnologías complementarias como la inteligencia artificial y el aprendizaje automático. Estas herramientas permiten analizar grandes volúmenes de datos generados durante el proceso de pulido para optimizar parámetros en tiempo real, ajustando automáticamente variables como la presión, velocidad y duración del pulido según las características específicas de cada pieza y el desgaste de las herramientas. Esta capacidad de autoajuste no solo mejora la calidad del acabado, sino que también prolonga la vida útil de los consumibles, reduce costos operativos y minimiza desperdicios.
Asimismo, la incorporación de sistemas de visión artificial ha revolucionado la inspección automática de las superficies pulidas. Cámaras de alta resolución y algoritmos de procesamiento de imagen permiten detectar imperfecciones, variaciones en el brillo y otras anomalías con gran precisión, habilitando una retroalimentación inmediata para corregir el proceso sin intervención humana. Esto asegura que cada pieza cumpla con los estándares de calidad exigidos y reduce significativamente la tasa de rechazos.
En la práctica industrial, estas máquinas se diseñan con estructuras robustas y sistemas de seguridad avanzados, tales como barreras ópticas, sensores de proximidad y dispositivos de emergencia que garantizan la protección del personal y evitan accidentes. Esto es especialmente importante en entornos donde se manejan piezas pesadas o se trabajan con velocidades elevadas, asegurando un ambiente de trabajo seguro y eficiente.
El diseño ergonómico también juega un papel crucial en la interacción entre operadores y máquinas, facilitando tareas de carga y descarga de piezas, ajustes y mantenimiento, lo que contribuye a reducir la fatiga laboral y aumentar la productividad. Los fabricantes suelen ofrecer soluciones personalizadas que consideran las necesidades específicas de cada industria y cliente, desde sistemas compactos para talleres pequeños hasta instalaciones complejas para grandes plantas de producción.
Por último, la tendencia hacia la digitalización y conectividad ha llevado a que muchas máquinas automáticas de pulido se integren en redes industriales y plataformas de gestión centralizada. Esto permite el monitoreo remoto, la recopilación de datos históricos para análisis de desempeño y la implementación de estrategias de mantenimiento predictivo basadas en inteligencia artificial, mejorando la toma de decisiones y la eficiencia operativa a nivel global.
En conclusión, las máquinas automáticas de pulido están en constante evolución, impulsadas por innovaciones tecnológicas que optimizan la calidad, eficiencia y seguridad del proceso. Su adopción creciente en diversas industrias refleja la importancia de estos sistemas para mantenerse competitivos en un mercado cada vez más exigente y orientado hacia la excelencia en el acabado superficial.
Además, la sostenibilidad y la eficiencia energética se han convertido en aspectos fundamentales en el diseño y operación de las máquinas automáticas de pulido. Los fabricantes están incorporando motores de alta eficiencia, sistemas de recuperación de energía y componentes optimizados para reducir el consumo eléctrico, lo que no solo disminuye los costos operativos, sino que también contribuye a la reducción de la huella ambiental de los procesos industriales. La implementación de tecnologías de bajo consumo y materiales reciclables en la fabricación de estas máquinas responde a una demanda creciente de prácticas más responsables y alineadas con los objetivos globales de desarrollo sostenible.
Otra dimensión relevante es la personalización y flexibilidad que estas máquinas ofrecen en el proceso de pulido. Gracias a las configuraciones modulares y la posibilidad de programar múltiples ciclos y estrategias de acabado, es posible adaptar rápidamente la máquina a distintos productos y lotes, lo que es especialmente valioso en industrias donde la diversidad de piezas es alta o los tiempos de producción deben ser cortos. Esta capacidad permite a las empresas responder con agilidad a cambios en la demanda y optimizar sus líneas productivas sin grandes inversiones adicionales.
El desarrollo de nuevas tecnologías abrasivas y consumibles también ha influido positivamente en el rendimiento de las máquinas automáticas de pulido. Materiales avanzados como abrasivos cerámicos, compuestos diamantados o pastas pulidoras de última generación ofrecen mayor durabilidad y efectividad, permitiendo alcanzar acabados más finos y precisos en menos tiempo. La combinación de estas innovaciones con el control automatizado garantiza resultados superiores y reduce el desgaste general de los sistemas.
En cuanto a la capacitación y formación del personal, es vital que los operadores y técnicos cuenten con conocimientos especializados para manejar, programar y mantener estas máquinas. La complejidad creciente de los sistemas y la integración con tecnologías digitales requieren programas de formación continua, que permitan maximizar el aprovechamiento de las capacidades de las máquinas y asegurar un funcionamiento óptimo a lo largo del tiempo. Muchas empresas fabricantes ofrecen soporte técnico y formación adaptada a las necesidades específicas de cada cliente, facilitando la adopción y el correcto uso de estas soluciones.
Finalmente, la evolución de las máquinas automáticas de pulido está estrechamente ligada a las demandas del mercado por productos con acabados cada vez más exigentes, rápidos y consistentes. Las mejoras en automatización, control, sostenibilidad y personalización convierten a estas máquinas en herramientas clave para la competitividad y el éxito industrial en un contexto globalizado y altamente competitivo. La innovación continúa siendo el motor que impulsa el desarrollo de tecnologías que optimizan el pulido y acabado superficial, contribuyendo al progreso y eficiencia de múltiples sectores productivos.
Equipos automáticos de pulido
Los equipos automáticos de pulido son sistemas diseñados para realizar el acabado superficial de piezas y componentes de manera eficiente, precisa y repetitiva, minimizando la intervención manual. Estos equipos están compuestos por una combinación de elementos mecánicos, eléctricos y de control que permiten llevar a cabo procesos de pulido, abrillantado y acabado espejo sobre materiales como metales, plásticos, vidrios y otros sustratos.
La principal ventaja de los equipos automáticos de pulido radica en su capacidad para estandarizar el proceso, asegurando uniformidad en el acabado y reduciendo errores humanos. Además, incrementan la productividad al acelerar los tiempos de procesamiento y permiten trabajar en serie con altos volúmenes de piezas. Su diseño puede variar desde máquinas compactas para operaciones específicas hasta sistemas modulares y células robotizadas integradas en líneas de producción automatizadas.
Entre los componentes más comunes se encuentran mesas giratorias indexadas, que facilitan la rotación precisa de las piezas para su pulido en múltiples ángulos; unidades de pulido con abrasivos y pastas especiales; sistemas de control numérico para programar ciclos específicos; y sensores que monitorean parámetros como la presión y velocidad para optimizar el proceso y evitar daños. En algunos casos, estos equipos están equipados con robots industriales que manipulan las piezas, lo que permite una automatización completa y una mayor flexibilidad.
Estos sistemas son ampliamente utilizados en industrias como la automotriz, aeroespacial, médica, joyería y manufactura de componentes electrónicos, donde la calidad del acabado superficial es crucial para la funcionalidad, durabilidad y estética del producto final. La implementación de equipos automáticos de pulido contribuye también a mejorar las condiciones de trabajo al reducir la exposición del personal a polvos y agentes abrasivos, y disminuye la fatiga derivada de tareas repetitivas.
En resumen, los equipos automáticos de pulido representan una solución tecnológica avanzada que combina precisión, eficiencia y seguridad, contribuyendo a la optimización de los procesos productivos y a la obtención de productos con altos estándares de calidad superficial. Su evolución continúa impulsada por innovaciones en automatización, control inteligente y materiales abrasivos, que amplían sus capacidades y aplicaciones industriales.
Los equipos automáticos de pulido han experimentado una evolución significativa con la integración de tecnologías digitales que permiten un control más preciso y adaptable del proceso. Gracias a la implementación de software avanzado y sistemas de sensores, es posible monitorizar en tiempo real variables como la presión aplicada, la velocidad de rotación, la temperatura y el desgaste de las herramientas abrasivas. Esta información se utiliza para ajustar automáticamente los parámetros operativos, asegurando que cada pieza reciba el tratamiento adecuado según sus características específicas y el tipo de acabado requerido.
Además, la incorporación de robots colaborativos en los sistemas de pulido ha abierto nuevas posibilidades para la manipulación segura y eficiente de piezas complejas o delicadas. Estos robots trabajan junto al personal humano, adaptándose a diferentes tareas y optimizando el flujo de trabajo en las líneas de producción. La flexibilidad que ofrecen permite cambiar rápidamente entre distintos tipos de pulido y acabados, lo que es especialmente útil en entornos donde la variedad de productos es amplia o los volúmenes de producción varían constantemente.
En términos de diseño mecánico, los equipos automáticos cuentan con sistemas modulares que facilitan la instalación, mantenimiento y actualización de sus componentes. Esto incluye mesas giratorias indexadas que permiten posicionar las piezas en ángulos específicos para un pulido uniforme, cabezales de pulido intercambiables según el tipo de abrasivo o acabado, y sistemas de extracción de polvo y residuos para mantener un ambiente limpio y seguro. Estas características contribuyen a minimizar los tiempos de paro y a maximizar la disponibilidad operativa de las máquinas.
Por otro lado, la sostenibilidad se ha convertido en un factor clave en el desarrollo de estos equipos. Se busca reducir el consumo de energía mediante motores eficientes y sistemas de recuperación, así como minimizar el uso de productos químicos o abrasivos contaminantes mediante procesos optimizados y recirculación de materiales. Esta orientación no solo responde a normativas ambientales cada vez más estrictas, sino también a una demanda creciente por parte de clientes y mercados que valoran las prácticas responsables.
En el contexto industrial actual, la integración de equipos automáticos de pulido con sistemas de manufactura inteligente y conectividad IoT permite la recopilación de datos que facilitan el análisis de rendimiento, la detección temprana de fallas y la planificación de mantenimiento predictivo. Esto reduce costos operativos y mejora la calidad del producto final, creando una ventaja competitiva para las empresas que adoptan estas tecnologías.
En definitiva, los equipos automáticos de pulido constituyen una solución avanzada y versátil que responde a las exigencias de precisión, eficiencia y sostenibilidad en el acabado superficial. Su constante innovación tecnológica y adaptación a las necesidades del mercado los posicionan como herramientas indispensables para la fabricación moderna en múltiples sectores industriales.
Estos equipos automáticos de pulido también incorporan innovaciones en los sistemas de abrasión y herramientas de acabado, que mejoran significativamente la calidad y la velocidad del proceso. Por ejemplo, el uso de abrasivos de alta tecnología, como discos con microestructuras especiales o pastas pulidoras con nanopartículas, permite lograr superficies con niveles de brillo y suavidad antes impensables, con menor desgaste de los consumibles y mayor durabilidad de las máquinas.
Asimismo, la ergonomía y seguridad han sido prioridades en el diseño de estos sistemas automáticos. La reducción de la intervención humana no solo aumenta la consistencia del pulido, sino que también disminuye la exposición a agentes peligrosos, como partículas en suspensión, vibraciones y ruido. Los sistemas cuentan con protecciones, cerramientos automáticos y dispositivos de parada de emergencia, garantizando un entorno de trabajo seguro y conforme a las normativas vigentes.
Otro aspecto clave es la capacidad de integración de estos equipos en líneas de producción totalmente automatizadas. Las máquinas pueden conectarse con sistemas de transporte, estaciones de lavado, inspección visual y embalaje, formando células de manufactura donde el proceso de pulido es una etapa más dentro de una cadena productiva optimizada. Esta integración reduce tiempos muertos, facilita la trazabilidad de las piezas y permite la producción en masa con altos estándares de calidad.
La personalización del acabado es también una característica destacada, ya que mediante la programación y selección de parámetros, es posible adaptar el proceso para obtener distintos tipos de superficies, desde acabados mate hasta acabados espejo, pasando por texturas específicas o perfiles definidos. Esta flexibilidad es fundamental para atender las demandas de sectores tan variados como el automotriz, el aeroespacial, la electrónica o la fabricación de bienes de consumo.
Por último, la innovación continúa en la incorporación de inteligencia artificial y análisis de datos para optimizar los procesos de pulido automático. Mediante el aprendizaje automático, los sistemas pueden predecir el mejor ciclo de trabajo para cada tipo de pieza, ajustando en tiempo real variables para maximizar la eficiencia y minimizar el desgaste. Esto representa un salto cualitativo hacia la manufactura inteligente, donde la automatización no solo ejecuta tareas, sino que también aprende y mejora continuamente, asegurando resultados de alta calidad con el menor costo posible.
En suma, los equipos automáticos de pulido constituyen una convergencia entre ingeniería mecánica avanzada, control inteligente y diseño industrial, que redefine los estándares de acabado superficial en la industria moderna. Su desarrollo y adopción permiten a las empresas mantenerse competitivas, responder ágilmente a los cambios del mercado y cumplir con exigencias cada vez mayores en términos de calidad, productividad y sostenibilidad.
Además de las mejoras en precisión y automatización, los equipos automáticos de pulido han incorporado tecnologías para optimizar la gestión del mantenimiento y la durabilidad de los sistemas. Los sensores integrados permiten un monitoreo constante de las condiciones operativas, detectando posibles desgastes o fallas antes de que ocurran interrupciones graves en la producción. Esta capacidad de mantenimiento predictivo no solo reduce los tiempos de inactividad, sino que también prolonga la vida útil de los componentes críticos, disminuyendo costos y mejorando la eficiencia global.
Los sistemas de control y software de última generación facilitan la programación intuitiva y la supervisión remota de las operaciones de pulido. Los operadores pueden ajustar parámetros, supervisar el avance y recibir alertas mediante interfaces gráficas amigables, e incluso acceder a los sistemas desde dispositivos móviles. Esto permite una gestión más flexible y adaptativa, ideal para ambientes productivos que requieren cambios rápidos entre lotes o modificaciones en los procesos según las especificaciones del cliente.
Otro avance relevante es la modularidad y escalabilidad de los equipos automáticos de pulido. Las máquinas están diseñadas para adaptarse a diferentes tamaños y formas de piezas, y para integrarse en líneas con capacidad de producción variable, desde pequeños lotes hasta grandes volúmenes industriales. Esta adaptabilidad permite a las empresas crecer y evolucionar sus procesos sin necesidad de inversiones completas en nueva maquinaria, simplemente añadiendo o modificando módulos existentes.
El compromiso con la sostenibilidad también se manifiesta en el desarrollo de procesos que minimizan el consumo de recursos, como agua y energía, y en el uso de materiales reciclables o biodegradables para abrasivos y pastas de pulido. Los sistemas modernos incluyen tecnologías de filtración y recuperación que reducen el impacto ambiental y cumplen con estándares internacionales para producción limpia.
Finalmente, la capacitación y formación del personal en el manejo de estos equipos es un componente esencial para maximizar su rendimiento. Los fabricantes suelen ofrecer programas especializados que abarcan desde la operación básica hasta el mantenimiento avanzado y la optimización del proceso. Este enfoque integral asegura que la inversión en equipos automáticos de pulido se traduzca en beneficios reales y sostenidos para las empresas.
En conclusión, los equipos automáticos de pulido representan una convergencia de avances tecnológicos y buenas prácticas industriales, proporcionando soluciones robustas, flexibles y sostenibles para el acabado superficial. Su continua evolución y perfeccionamiento posicionan a estos sistemas como elementos clave en la competitividad y eficiencia de los procesos productivos modernos.
Producción de máquinas automáticas para el pulido
La producción de máquinas automáticas para el pulido es un proceso altamente especializado que combina ingeniería mecánica, electrónica, software de control y diseño industrial para crear equipos capaces de ofrecer acabados superficiales de alta calidad con eficiencia y precisión. Este tipo de maquinaria se fabrica pensando en atender las demandas específicas de diferentes sectores industriales, tales como la automoción, la aeroespacial, la fabricación de electrodomésticos, la industria del mueble y la metalurgia, entre otros.
El proceso productivo comienza con la definición de los requerimientos técnicos y funcionales que deben cumplir las máquinas, incluyendo aspectos como el tipo de piezas a pulir, los acabados requeridos, la capacidad de producción, y las normativas de seguridad y medio ambiente aplicables. A partir de estos requisitos, se diseñan los componentes mecánicos principales, como motores, sistemas de transmisión, mesas giratorias indexadas, unidades de pulido y cabezales intercambiables, asegurando una estructura robusta y modular que facilite el mantenimiento y futuras ampliaciones.
Paralelamente, se desarrolla el sistema electrónico y de control, que incluye sensores, actuadores, controladores lógicos programables (PLC), y sistemas de interfaz hombre-máquina (HMI). Estos elementos son fundamentales para automatizar el proceso, permitiendo la programación precisa de ciclos de trabajo, ajustes dinámicos durante la operación, y la integración con otros equipos o líneas de producción a través de protocolos industriales estándar.
La fabricación y montaje de las máquinas se lleva a cabo en instalaciones equipadas con tecnología avanzada para el mecanizado de precisión, soldadura robotizada, ensamblaje automatizado y pruebas funcionales. Durante el montaje, se realizan rigurosos controles de calidad para garantizar la correcta alineación de componentes, el funcionamiento óptimo de los sistemas de pulido, y la seguridad operativa. Las pruebas incluyen simulaciones de carga, ciclos de pulido en condiciones reales y verificaciones de respuesta de sensores y controles.
Una vez completada la fabricación, las máquinas se someten a procesos de calibración y ajuste fino, que aseguran que cada unidad cumpla con las especificaciones técnicas y los estándares de rendimiento establecidos. También se ofrecen servicios de instalación, puesta en marcha y capacitación para los operadores, asegurando una transición eficiente hacia la producción con los nuevos equipos.
Finalmente, la producción de máquinas automáticas para el pulido incorpora una estrategia de mejora continua basada en la retroalimentación de los clientes y avances tecnológicos. Esto implica la actualización periódica de software, el desarrollo de nuevos accesorios y herramientas de pulido, y la adaptación a nuevas normativas ambientales y de seguridad, garantizando que las máquinas mantengan su competitividad y relevancia en un mercado dinámico.
En resumen, la producción de estos equipos requiere una combinación de diseño innovador, tecnología avanzada, calidad en la fabricación y un enfoque orientado al cliente, para ofrecer soluciones que optimicen los procesos de acabado superficial y contribuyan al éxito industrial.
La producción de máquinas automáticas para el pulido continúa evolucionando a medida que las demandas del mercado exigen mayores niveles de precisión, velocidad y personalización en los acabados superficiales. Las empresas fabricantes están invirtiendo en investigación y desarrollo para incorporar tecnologías emergentes, como la inteligencia artificial, el aprendizaje automático y el análisis predictivo, que permiten optimizar cada etapa del proceso de pulido y reducir al mínimo los desperdicios y los tiempos muertos.
Uno de los enfoques más innovadores en la producción es la implementación de sistemas modulares que facilitan la personalización y la adaptación rápida a diferentes tipos de piezas y materiales. Estos sistemas permiten ensamblar configuraciones específicas según las necesidades del cliente, desde máquinas compactas para pequeños talleres hasta instalaciones completas para producción en serie en grandes industrias. Esta flexibilidad es clave para atender sectores tan diversos como la joyería, la automoción o la fabricación de componentes electrónicos.
Además, la integración de sensores avanzados y sistemas de visión artificial en las máquinas automáticas de pulido está revolucionando la forma en que se controla la calidad del acabado. Estos dispositivos pueden detectar imperfecciones, variaciones en el brillo o irregularidades en tiempo real, permitiendo realizar ajustes automáticos durante el proceso y garantizando que cada pieza cumpla con los estándares establecidos sin necesidad de intervención manual. Esta capacidad reduce significativamente el retrabajo y los rechazos, mejorando la eficiencia global y la rentabilidad.
En el ámbito de la fabricación, el uso de técnicas de fabricación aditiva y componentes impresos en 3D está comenzando a influir en el diseño y producción de piezas específicas para estas máquinas. Esto facilita la creación de geometrías complejas, la reducción del peso de los componentes y la disminución de los tiempos de producción y entrega. Asimismo, la fabricación local y la personalización se ven favorecidas por estas tecnologías, contribuyendo a una cadena de suministro más ágil y sostenible.
La automatización del proceso no se limita únicamente a la máquina de pulido en sí, sino que se extiende a la línea completa de producción, incorporando sistemas de transporte automatizado, robótica para manipulación de piezas y estaciones de inspección y embalaje. Esta integración crea células de trabajo inteligentes que optimizan el flujo productivo, permiten la trazabilidad completa de las piezas y facilitan la gestión de lotes y órdenes de producción complejas.
La formación del personal sigue siendo un pilar fundamental en la producción y operación de máquinas automáticas para pulido. Las empresas invierten en programas de capacitación que combinan teoría y práctica, asegurando que los operadores y técnicos comprendan no solo el manejo básico, sino también el mantenimiento preventivo, la programación avanzada y la resolución de problemas. Esta preparación es vital para maximizar el rendimiento de las máquinas y prolongar su vida útil.
Finalmente, la sostenibilidad y el respeto al medio ambiente se han convertido en factores clave en el desarrollo y producción de estas máquinas. La eficiencia energética, la reducción de consumibles contaminantes, la gestión adecuada de residuos y la minimización del consumo de agua son aspectos incorporados desde el diseño. Las empresas que producen máquinas automáticas para pulido están comprometidas con ofrecer soluciones que no solo mejoren la productividad, sino que también contribuyan a una industria más limpia y responsable.
En conclusión, la producción de máquinas automáticas para el pulido representa un sector dinámico y en constante innovación, donde la combinación de tecnología avanzada, flexibilidad de diseño, control de calidad y compromiso ambiental permite ofrecer equipos que responden a las exigencias de un mercado cada vez más competitivo y orientado a la excelencia en el acabado superficial.
El avance continuo en la producción de máquinas automáticas para el pulido también está impulsado por la digitalización de los procesos industriales. La incorporación de tecnologías de Industria 4.0 permite la conexión en red de los equipos, facilitando el monitoreo remoto, el análisis de datos en tiempo real y la optimización predictiva del mantenimiento. Estas capacidades no solo mejoran la eficiencia operativa, sino que también reducen los costos asociados a paradas inesperadas y prolongan la vida útil de las máquinas.
La personalización y la adaptabilidad son factores clave en el diseño de nuevas generaciones de máquinas automáticas para pulido. Gracias a la programación flexible y a los sistemas de control avanzados, estas máquinas pueden ajustarse rápidamente a diferentes tipos de materiales —como metales, plásticos o compuestos— y a variadas geometrías de piezas, lo que permite atender tanto producciones masivas como series pequeñas o prototipos. Este nivel de versatilidad es especialmente valorado en industrias donde la innovación y la rapidez de respuesta al mercado son críticas.
El desarrollo de abrasivos y materiales de pulido más eficientes y sostenibles complementa la evolución de las máquinas automáticas. Nuevos compuestos, recubrimientos y técnicas de pulido químico o electroquímico se integran en los procesos para mejorar la calidad del acabado, reducir el desgaste de los componentes y disminuir el impacto ambiental. La sinergia entre la máquina y los consumibles optimizados permite lograr resultados superiores en menos tiempo y con menor consumo energético.
Además, la ergonomía y la seguridad en el diseño de estas máquinas han cobrado especial importancia. Los fabricantes implementan sistemas que minimizan la interacción directa del operador con las partes móviles, utilizando barreras físicas, sensores de presencia y protocolos de parada de emergencia automatizados. Estas medidas aseguran un ambiente de trabajo seguro y cumplen con las normativas internacionales más estrictas en materia de seguridad industrial.
La integración de sistemas robóticos para la carga y descarga de piezas dentro de las células de pulido automatizadas ha facilitado la creación de líneas de producción completamente autónomas. Estos sistemas robóticos pueden manipular piezas con precisión, cambiar herramientas y realizar inspecciones básicas, reduciendo la necesidad de mano de obra directa y permitiendo operar las máquinas durante turnos extendidos o incluso en horarios nocturnos sin supervisión constante.
Por último, la retroalimentación constante entre los usuarios finales y los fabricantes impulsa la innovación y mejora continua de los equipos. Las experiencias de operación, las sugerencias de optimización y los reportes de mantenimiento contribuyen a diseñar máquinas cada vez más robustas, eficientes y adaptadas a las necesidades reales de la industria. Este ciclo de colaboración asegura que las máquinas automáticas para pulido no solo respondan a las tendencias actuales, sino que también anticipen los desafíos futuros, consolidándose como herramientas indispensables para la producción moderna.
En definitiva, la producción y desarrollo de máquinas automáticas para el pulido es un área que combina ingeniería avanzada, innovación tecnológica y un enfoque centrado en el cliente, con el objetivo de ofrecer soluciones integrales que mejoren la calidad, eficiencia y sostenibilidad de los procesos de acabado superficial en múltiples sectores industriales.
Además de las mejoras tecnológicas y de diseño, la sostenibilidad se está posicionando como un aspecto fundamental en la producción de máquinas automáticas para pulido. Los fabricantes están adoptando estrategias para minimizar el consumo energético y reducir la huella ecológica de sus equipos. Esto incluye el uso de motores de alta eficiencia, sistemas de recuperación de energía y la implementación de tecnologías que disminuyen el uso de agua y productos químicos durante el proceso de pulido.
La gestión responsable de los residuos generados durante el pulido también es un foco importante. Se desarrollan sistemas de filtración y reciclaje de abrasivos y partículas para evitar la contaminación ambiental, contribuyendo a que el proceso sea más limpio y respetuoso con el entorno. Además, la tendencia hacia el diseño para la reciclabilidad facilita que las máquinas tengan un ciclo de vida más sostenible, pudiendo ser desmontadas y sus componentes reutilizados o reciclados al final de su vida útil.
El avance en el control digital ha facilitado la creación de interfaces de usuario más intuitivas y accesibles, que permiten a operadores de distintos niveles de experiencia manejar las máquinas con mayor facilidad. La incorporación de pantallas táctiles, menús personalizables y asistentes virtuales integrados optimizan la interacción hombre-máquina, reduciendo errores y mejorando la productividad. Estas interfaces también permiten la integración con sistemas ERP y software de gestión, facilitando la planificación y el seguimiento en tiempo real de la producción.
En el ámbito industrial, la integración de la inteligencia artificial en los sistemas de pulido automático está comenzando a marcar una diferencia significativa. Algoritmos avanzados pueden analizar patrones de desgaste, calidad del acabado y comportamiento de la máquina para ajustar parámetros en tiempo real y anticipar mantenimientos, lo que se traduce en mayor precisión y menor tiempo de inactividad. Esta capacidad de autoajuste y diagnóstico predictivo contribuye a optimizar recursos y maximizar la eficiencia operativa.
Asimismo, la evolución en los sistemas de automatización ha favorecido la combinación de procesos de pulido con otras etapas de acabado, como el lavado, secado o inspección superficial dentro de la misma línea automatizada. Esto permite una producción más compacta, eficiente y con menor manipulación manual, lo que reduce riesgos de daños y mejora la consistencia del producto final.
Finalmente, la capacitación y el soporte técnico son componentes esenciales para garantizar el éxito en la implementación y operación de máquinas automáticas de pulido. Los fabricantes suelen ofrecer programas de formación personalizados, asistencia remota y mantenimiento preventivo, asegurando que los clientes puedan aprovechar al máximo las capacidades de sus equipos. Este acompañamiento fortalece la relación entre productor y usuario, fomentando la innovación continua y la mejora constante en los procesos industriales.
En resumen, la producción de máquinas automáticas para pulido avanza no solo en aspectos tecnológicos, sino también en sostenibilidad, usabilidad y servicio al cliente, consolidándose como un pilar clave para la modernización y eficiencia de la industria del acabado superficial.
Máquinas Formadoras de Metales EMS
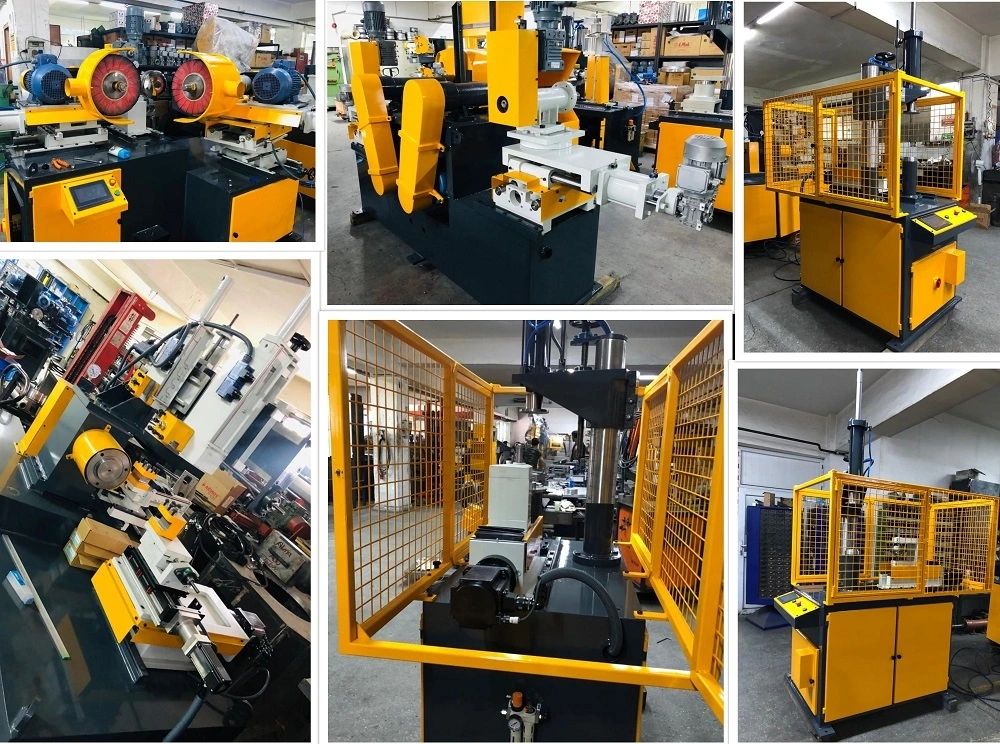
Diseñamos, fabricamos y montamos maquinaria metalmecánica como:
Prensa de transferencia hidráulica
Prensa para mosaicos de vidrio
Prensa hidráulica de embutición profunda
prensa de fundición
Prensa hidráulica de conformado en frío
Prensa de hidroformado
prensa compuesta
Prensa de moldeo de caucho de silicona
Prensa de pastillas de freno
Prensa de melamina
Prensa SMC y BMC
prensa labrotaroy
Máquina cortadora de bordes
Máquina rizadora de bordes
Máquina recortadora de abalorios
Máquina de recorte y jogging
Línea de producción de utensilios de cocina.
Máquina dobladora de tubos
Máquina dobladora de perfiles
Sierra de cinta para metal
Máquina de soldar cilíndrica
Prensas horizontales y utensilios de cocina.
Menaje de cocina, artículos de hotelería
Maquinaria para la producción de utensilios para hornear y cubiertos.
como una línea completa así como una máquina individual como:
Máquinas cortadoras de bordes y biseladoras
Pulidoras y rectificadoras de ollas y sartenes.
Prensas hidráulicas de trefilado
Máquinas troqueladoras circulares
remachadora
Punzonadoras
Máquina de alimentación de prensa
Puede consultar nuestra maquinaria en funcionamiento en: EMS Máquinas Formadoras de Metales EMS – YouTube
Aplicaciones:
Punzonado de bridas
Abalorios y nervaduras
Bridas
Guarnición
Curling
costura de bloqueo
Nervaduras