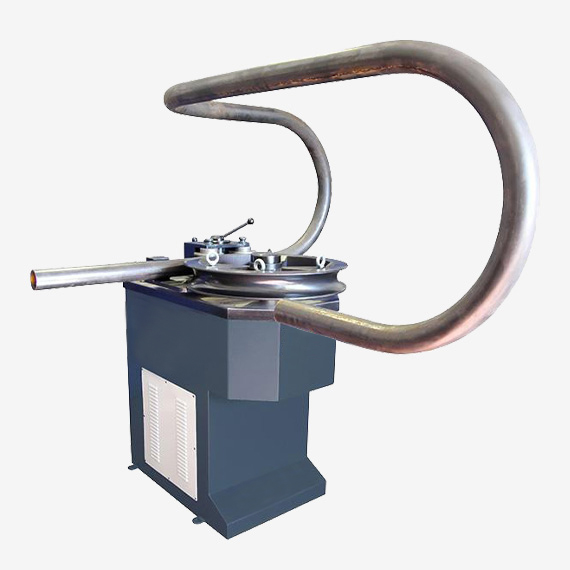
Curvadora de tubos metálicos: Una curvadora de tubos es una máquina o equipo utilizado para doblar tubos de manera controlada, permitiendo que adopten diversas formas y ángulos sin que se rompan o deformen de manera incontrolada. Este proceso se utiliza en diversas industrias, como la automotriz, la construcción, la ingeniería, y la fabricación de maquinaria y equipos.
Existen varios tipos de curvadoras de tubos, dependiendo de la tecnología utilizada y el tipo de tubo a curvar. Los métodos más comunes de curvado son:
- Curvado por rodillos: Utiliza rodillos para girar el tubo alrededor de un eje, doblándolo de forma gradual.
- Curvado por presión: Utiliza una prensa o matriz que aplica presión al tubo para doblarlo.
- Curvado por tracción: Un sistema de tracción estira el tubo mientras lo dobla para mantener una forma precisa.
- Curvado por inducción eléctrica: Un proceso más especializado en el que el tubo es calentado localmente con corriente eléctrica antes de ser doblado.
Cada tipo de curvadora es adecuado para diferentes diámetros, espesores de pared y materiales de los tubos.
Las curvadoras de tubos también se clasifican según la capacidad de control que ofrecen en el proceso de curvado, lo que es crucial para obtener curvas con precisión y evitar defectos como la deformación o el aplastamiento del tubo. Entre las características importantes a considerar en la elección de una curvadora de tubos están el rango de radios de curvado, la capacidad máxima de presión, la velocidad del proceso y la precisión del control del ángulo de curvado.
Algunas curvadoras de tubos también cuentan con sistemas de control numérico computarizado (CNC), que permiten programar y controlar con exactitud los parámetros de curvado, como el ángulo, la velocidad de avance y la dirección del curvado, mejorando la calidad y la repetibilidad en la producción de piezas. Estos sistemas son particularmente útiles en la fabricación de componentes complejos, como los usados en la industria automotriz y aeroespacial, donde las especificaciones son muy estrictas. Además, las curvadoras modernas también permiten trabajar con una amplia gama de materiales, como acero inoxidable, aluminio, cobre y materiales compuestos, lo que las hace versátiles y esenciales en muchas líneas de producción.
El mantenimiento adecuado de una curvadora de tubos es crucial para asegurar un rendimiento óptimo, lo que incluye la lubricación de las partes móviles, la revisión de las matrices y rodillos, y el ajuste regular de los sistemas hidráulicos o electrónicos para evitar fallas que puedan afectar la calidad de las piezas curvadas.
Además de los tipos y características de las curvadoras de tubos, es importante considerar los aspectos técnicos que influyen en la elección de una curvadora adecuada para un proceso específico. El material del tubo es uno de los factores más críticos, ya que distintos materiales tienen diferentes propiedades de resistencia, elasticidad y ductilidad, lo que influye en la cantidad de fuerza necesaria para curvarlos sin que se produzcan defectos. Por ejemplo, los tubos de acero inoxidable requieren más fuerza para ser curvados en comparación con los tubos de aluminio debido a su mayor resistencia. Además, los tubos con paredes gruesas pueden ser más difíciles de curvar sin que sufran deformaciones, lo que requiere una curvadora que ofrezca mayor capacidad de presión y precisión.
En términos de la tecnología de curvado, las curvadoras CNC (Control Numérico Computarizado) se han convertido en la opción preferida para muchas aplicaciones industriales debido a su capacidad para realizar curvados de alta precisión en lotes grandes o de producción continua. Estas máquinas permiten programar los ángulos de curvado, los radios y las velocidades con una exactitud impresionante, lo que garantiza que cada tubo curvado sea consistente con las especificaciones requeridas. La integración de la tecnología CNC también facilita la automatización del proceso, reduciendo la intervención manual y aumentando la eficiencia.
El radio de curvado es otro aspecto clave, ya que en muchos casos, los radios muy pequeños pueden causar que el tubo se deforme permanentemente o se rompa. Las curvadoras de tubos están diseñadas para manejar radios de curvado específicos, y la elección del radio adecuado depende de varios factores, como el material del tubo, el diámetro y el espesor de la pared. El proceso de curvado de un tubo con un radio demasiado pequeño puede generar reducción de la sección transversal del tubo, lo que puede comprometer la integridad estructural, especialmente si el tubo se utiliza para aplicaciones críticas, como sistemas de presión o conductos de fluidos.
Por otro lado, las curvadoras de tubos también se utilizan ampliamente en la industria automotriz, donde los tubos curvados se emplean en la fabricación de chasis, estructuras de vehículos, sistemas de escape y sistemas de refrigeración. En estos sectores, la precisión es esencial, ya que incluso una ligera variación en la forma del tubo puede afectar el rendimiento del vehículo o la seguridad del conductor. Las curvadoras de tubos automáticas y controladas por CNC se utilizan para garantizar que los tubos curvados sean exactos y se ajusten perfectamente a las especificaciones de diseño.
En la industria de la construcción, los tubos curvados se utilizan para una variedad de aplicaciones, como estructuras de soporte, sistemas de calefacción y ventilación, y sistemas de plomería. Aquí, los tubos a menudo necesitan ser curvados en ángulos específicos para adaptarse a las dimensiones y el diseño de un edificio o infraestructura. Las curvadoras de tubos en esta industria deben ser capaces de manejar grandes volúmenes de producción y ofrecer alta durabilidad, dado que los materiales utilizados en construcción suelen ser más robustos y pesados.
Además de los aspectos técnicos, el mantenimiento y la calibración de las curvadoras son fundamentales para garantizar la eficiencia y la calidad del proceso de curvado. Las partes móviles de la máquina, como los rodillos, las matrices y los sistemas hidráulicos, deben ser revisadas y mantenidas regularmente para prevenir el desgaste y garantizar un funcionamiento suave y preciso. Los sistemas CNC también requieren actualizaciones periódicas de software y ajustes de hardware para mantener la exactitud de los curvados. La capacitación de los operadores también es crucial, ya que una correcta comprensión de la máquina y los parámetros de curvado permite optimizar la producción y minimizar los errores.
El control de calidad durante el proceso de curvado es otra fase importante. Las máquinas curvadoras de tubos a menudo están equipadas con sistemas de inspección y medición que permiten verificar que cada tubo curvado cumple con las especificaciones exactas. Esto incluye la medición de la curvatura, el ángulo, el radio y la integridad estructural del tubo, asegurando que no haya defectos visibles como arrugas, grietas o deformaciones que puedan comprometer la función del tubo en su aplicación final.
En resumen, las curvadoras de tubos juegan un papel esencial en la fabricación de una amplia variedad de componentes industriales, desde vehículos hasta estructuras de edificios y maquinaria pesada. La tecnología avanzada, la precisión en el control del proceso, y el mantenimiento adecuado de estas máquinas son esenciales para asegurar una producción eficiente, de alta calidad y libre de defectos. La evolución hacia sistemas automatizados y controlados por CNC ha mejorado considerablemente la capacidad de producción y la versatilidad de las curvadoras, permitiendo su aplicación en una variedad aún mayor de industrias y procesos.
Además de los aspectos técnicos mencionados, la adaptabilidad de las curvadoras de tubos también juega un papel crucial en su utilización en distintos sectores industriales. La versatilidad de estas máquinas permite a los fabricantes manejar una amplia gama de tamaños de tubo, formas y ángulos, lo que es especialmente útil en sectores que requieren personalización o productos con especificaciones muy particulares. Por ejemplo, en la industria aeroespacial, los tubos curvados se utilizan para sistemas de combustible, oxígeno y otros fluidos esenciales en aeronaves. Estos sistemas requieren precisión absoluta, ya que cualquier fallo en el curvado del tubo puede llevar a fallos catastróficos. En este sector, las curvadoras de tubos de alta tecnología se utilizan para crear componentes que cumplen con los rigurosos estándares de seguridad.
La tecnología de simulación también ha hecho su entrada en el mundo del curvado de tubos. Los avances en el software de diseño y simulación permiten predecir cómo se comportará un tubo durante el proceso de curvado antes de realizar el trabajo físico. Esto minimiza el riesgo de fallos en el proceso y permite la optimización de los parámetros de curvado para obtener resultados más precisos. Los programas de simulación también pueden detectar posibles defectos, como el colapso de la pared del tubo o el desarrollo de arrugas, permitiendo que se realicen ajustes antes de que el proceso real se lleve a cabo, lo que reduce el desperdicio de material y los costos asociados.
En la industria energética, especialmente en la fabricación de componentes para turbinas de vapor o sistemas de tuberías de alta presión, las curvadoras de tubos se utilizan para crear secciones que deben resistir condiciones extremas de presión y temperatura. Estas curvadoras no solo deben ser capaces de manejar materiales altamente resistentes, como aleaciones de acero y titanio, sino que también deben hacerlo con una precisión que garantice que las juntas y los sellos entre las secciones curvadas no presenten fugas o puntos débiles. En aplicaciones críticas como estas, la calidad del curvado y la integridad estructural del tubo son esenciales para la eficiencia y la seguridad operativa.
En sectores como la industria naval, donde los tubos curvados se utilizan en sistemas de refrigeración, vapor y combustible, las curvadoras deben ser capaces de crear tubos con curvaturas complejas para adaptarse a los diseños de las embarcaciones. Estos sistemas de tuberías deben ser altamente confiables, ya que cualquier fallo podría afectar el rendimiento de la nave o incluso poner en riesgo la seguridad de la tripulación. Las curvadoras de tubos de última generación, a menudo equipadas con sistemas de control de calidad avanzados, permiten realizar inspecciones rigurosas en cada etapa del proceso para asegurarse de que las piezas cumplen con los estándares de calidad exigidos.
Una de las ventajas adicionales de las curvadoras de tubos modernas es su capacidad para trabajar con tuberías de materiales compuestos, que están ganando popularidad en industrias como la aeroespacial y la automotriz debido a sus propiedades de alta resistencia y bajo peso. Estos materiales compuestos, que pueden incluir fibras de carbono o materiales plásticos reforzados, requieren equipos especializados para ser curvados sin comprometer sus propiedades estructurales. Las curvadoras de tubos de materiales compuestos están diseñadas para manejar estas necesidades específicas, asegurando que los tubos curvados mantengan la integridad estructural y funcionalidad en aplicaciones que requieren altos estándares de rendimiento.
El costo de las curvadoras de tubos también varía considerablemente en función de su capacidad y características. Las curvadoras de tubos manuales, por ejemplo, son más accesibles y adecuadas para trabajos de curvado más simples o de menor volumen. Sin embargo, para producciones de mayor escala o aplicaciones más complejas, las curvadoras CNC, que son más caras pero altamente precisas y eficientes, son la opción preferida. El costo de estas máquinas no solo incluye la inversión inicial, sino también los gastos de mantenimiento, formación de personal y software de simulación que puede acompañar a las máquinas de control numérico.
El impacto ambiental del proceso de curvado de tubos también es un aspecto relevante en la actualidad. Las industrias buscan cada vez más métodos que reduzcan el desperdicio de material, la energía utilizada en el proceso y las emisiones derivadas de la producción. Las curvadoras de tubos más modernas están diseñadas para ser más eficientes energéticamente, y las técnicas de recubrimiento de tubos o de tratamiento térmico también han mejorado para asegurar que los productos finales no solo sean de alta calidad, sino también respetuosos con el medio ambiente. Además, los avances en la optimización de los procesos de fabricación han permitido a las empresas reducir el desperdicio de material, lo que contribuye tanto a la reducción de costos como a una menor huella de carbono.
Por último, la formación y capacitación de los operadores es esencial para el buen funcionamiento de las curvadoras de tubos. El proceso de curvado puede parecer sencillo, pero requiere un conocimiento profundo del material, la máquina y los parámetros del proceso para garantizar que se logren los mejores resultados posibles. Muchas empresas ofrecen programas de formación para operadores, donde se cubren desde los principios básicos del curvado hasta las técnicas avanzadas de control de calidad y mantenimiento. La experiencia del operador también es un factor importante en la reducción de errores y defectos en el proceso de curvado, ya que un operador bien entrenado puede anticipar y resolver problemas antes de que se conviertan en fallos graves.
En resumen, las curvadoras de tubos son herramientas clave en la fabricación de componentes de precisión para una amplia gama de industrias. Desde las aplicaciones más simples hasta las más complejas, estas máquinas son fundamentales para garantizar que los tubos curvados cumplan con los más altos estándares de calidad y fiabilidad. La tecnología avanzada, la automatización, la simulación y la mejora continua en el diseño y mantenimiento de estas máquinas aseguran que las curvadoras de tubos sigan siendo esenciales para los procesos de fabricación de hoy y del futuro.
Además de los aspectos técnicos y operativos de las curvadoras de tubos, se debe considerar también la evolución y tendencias futuras en esta tecnología, especialmente en lo que respecta a la integración de inteligencia artificial (IA), la automatización avanzada y la fabricación aditiva. Estas innovaciones están transformando la forma en que se diseñan, operan y mantienen las curvadoras de tubos, llevando el proceso de fabricación a nuevos niveles de eficiencia y precisión.
La inteligencia artificial está comenzando a ser integrada en las curvadoras de tubos, principalmente en la optimización del proceso de curvado. Los sistemas de IA pueden analizar grandes cantidades de datos de producción en tiempo real, lo que permite ajustar automáticamente los parámetros de la máquina para mantener la calidad del curvado, reducir el desperdicio y mejorar la eficiencia operativa. Por ejemplo, mediante el uso de sensores y algoritmos, una curvadora de tubos con IA podría detectar patrones de desgaste en las herramientas de curvado y predecir cuándo es necesario realizar mantenimiento preventivo, reduciendo tiempos de inactividad no planificados y mejorando la fiabilidad de la máquina.
Otro avance significativo es la automatización avanzada, que se está convirtiendo en un estándar en las fábricas de alto volumen. Las curvadoras de tubos automatizadas no solo realizan los procesos de curvado de manera más rápida, sino que también integran sistemas de monitorización remota, lo que permite a los operadores y técnicos supervisar las máquinas desde cualquier lugar del mundo. Esta conectividad permite un control más eficiente y facilita la detección temprana de problemas antes de que afecten la producción. Además, la interoperabilidad entre diferentes sistemas de fabricación, como la planificación de recursos empresariales (ERP) y el control de manufactura (MES), está mejorando la coordinación entre los procesos, reduciendo el tiempo de ciclo y mejorando la trazabilidad de los productos.
En cuanto a la fabricación aditiva, también conocida como impresión 3D, esta tecnología podría complementar el proceso de curvado de tubos en aplicaciones donde se necesiten geometrías complejas o piezas personalizadas. Aunque el curvado de tubos sigue siendo más efectivo para crear componentes largos y curvados, la fabricación aditiva está siendo explorada para la creación de herramientas de curvado personalizadas o componentes de diseño complejo que no pueden fabricarse de manera tradicional. Por ejemplo, las matrices de curvado o las piezas de fijación especializadas pueden ser producidas mediante impresión 3D, lo que reduce los tiempos de desarrollo y personalización de las herramientas.
Además, en sectores industriales como el automotriz y aeroespacial, se está experimentando con el uso de materiales avanzados como los compuestos de fibra de carbono y los materiales de aleaciones ligeras. Estos materiales requieren curvadoras de tubos que no solo sean capaces de manejar materiales más complejos, sino que también ofrezcan control de temperatura en el proceso de curvado. Algunas curvadoras de tubos avanzadas incluyen tecnologías de calentamiento local para asegurar que el material no pierda sus propiedades durante el curvado, lo que es especialmente importante para tubos curvados de materiales de alta resistencia utilizados en la industria aeronáutica, donde la integridad estructural es crucial.
Una tendencia clave en la industria es la creciente demanda de personalización. Las empresas están buscando soluciones más flexibles que les permitan adaptarse rápidamente a los cambios en los requisitos del cliente, como tamaños y formas de tubo personalizados. Las curvadoras de tubos de última generación, equipadas con sistemas CNC y programación avanzada, pueden responder a estas demandas al permitir una mayor flexibilidad en el diseño y la capacidad de cambiar rápidamente entre diferentes configuraciones de curvado sin la necesidad de herramientas costosas o configuraciones largas. Esto es particularmente útil en industrias que requieren lotes pequeños o producciones bajo demanda, como las de fabricación de prototipos o las que producen equipos médicos personalizados.
También se observa una mayor concentración en la reducción de costos operativos en el uso de curvadoras de tubos. Las tecnologías modernas están diseñadas para ser más energéticamente eficientes, lo que no solo reduce el impacto ambiental de la producción, sino que también ayuda a las empresas a reducir sus costos operativos. La automatización de la producción y la reducción del tiempo de ciclo también contribuyen significativamente a la optimización de costos, haciendo que las curvadoras de tubos sean una inversión más accesible para las empresas que desean mantener una producción eficiente sin comprometer la calidad.
Por otro lado, la adaptación de normas medioambientales más estrictas está llevando a muchas empresas a reconsiderar cómo gestionan el desperdicio de material durante el proceso de curvado. Los avances en el diseño de las curvadoras de tubos están permitiendo no solo la producción de tubos con menor desperdicio, sino también la reutilización de materiales reciclados, lo que es crucial en industrias que buscan cumplir con los estándares de sostenibilidad. Este cambio no solo beneficia al medio ambiente, sino que también mejora la competitividad de las empresas al reducir los costos asociados con la adquisición de materiales.
En términos de mantenimiento predictivo, una tendencia creciente es la integración de sensores inteligentes que monitorean continuamente el estado de la curvadora de tubos durante su operación. Estos sensores recopilan datos sobre parámetros clave, como la temperatura, la presión, el desgaste de los componentes y las vibraciones. Usando estos datos, los algoritmos de mantenimiento predictivo pueden anticipar cuándo es probable que una parte clave de la máquina necesite ser reemplazada o reparada, lo que permite a las empresas realizar mantenimiento en momentos óptimos para minimizar el tiempo de inactividad y evitar fallos costosos.
Finalmente, el futuro del curvado de tubos también estará influenciado por la convergencia de tecnologías. La combinación de curvado de tubos, robótica avanzada, análisis de datos en tiempo real y simulación computacional promete cambiar aún más la forma en que se fabrican y mantienen los tubos curvados. Las capacidades de automatización están creciendo de manera exponencial, lo que permite la creación de sistemas de producción más rápidos, flexibles y adaptables a las necesidades del mercado global. A medida que los avances en la industria 4.0 continúan, las curvadoras de tubos evolucionarán, ofreciendo aún más precisión, control y eficiencia a las industrias que dependen de ellas.
En resumen, el futuro de las curvadoras de tubos está marcado por la innovación tecnológica y una mayor integración de automatización, inteligencia artificial y tecnologías de simulación, lo que permitirá una mayor eficiencia, precisión y personalización en el proceso de fabricación. Estas máquinas no solo son fundamentales para la producción de componentes industriales de alta calidad, sino que seguirán evolucionando para satisfacer las demandas de una industria global cada vez más dinámica y exigente.
Máquina para doblar tubos
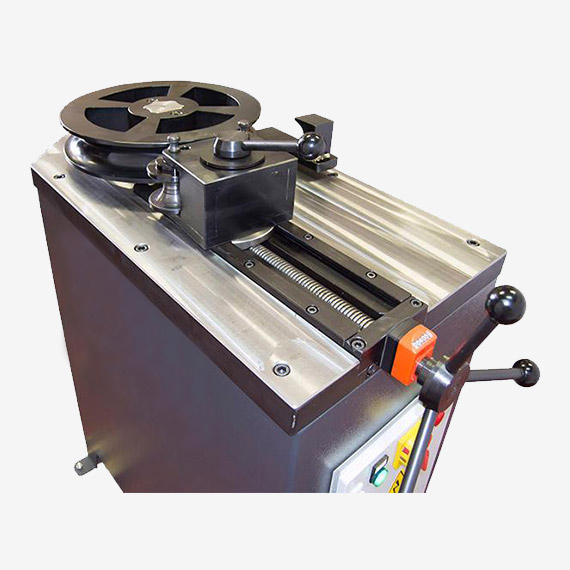
Una máquina para doblar tubos, también conocida como curvadora de tubos, es un dispositivo utilizado para doblar tubos de metal o plástico, dándoles la forma o el ángulo deseado sin que se rompan ni se deformen de manera indeseada. Estas máquinas se emplean en diversos sectores industriales, como la construcción, la automotriz, la aeronáutica, la energía y muchas más, donde los tubos curvados son esenciales para la fabricación de sistemas de tuberías, estructuras, chasis, sistemas de escape y más.
Existen diferentes tipos de máquinas para doblar tubos, que varían en su mecanismo, capacidad y aplicaciones. Algunos de los tipos más comunes son:
1. Curvadora de tubos manual
Estas máquinas son las más simples y generalmente se utilizan en trabajos pequeños o con poco volumen de producción. El operador utiliza palancas o manivelas para controlar el movimiento de los rodillos o el molde que dobla el tubo. Aunque son más económicas, las curvadoras manuales tienen limitaciones en cuanto a precisión y capacidad para manejar materiales de alta resistencia o tubos de gran diámetro.
2. Curvadora de tubos hidráulica
Este tipo de máquina utiliza un sistema hidráulico para aplicar presión y doblar el tubo. La curvadora hidráulica es ideal para aplicaciones que requieren una gran fuerza y precisión. Es capaz de manejar tubos con paredes gruesas y de materiales más resistentes, como acero inoxidable, aluminio y cobre. Estas máquinas son más costosas que las manuales, pero ofrecen una mayor capacidad de producción y calidad en el curvado.
3. Curvadora de tubos CNC (Control Numérico por Computadora)
Las curvadoras CNC son máquinas altamente precisas y automatizadas. El control numérico permite programar el proceso de curvado con gran exactitud, lo que resulta en tubos curvados de alta calidad y sin errores. Estas máquinas son adecuadas para lotes grandes y para curvar tubos con geometrías complejas. El operador solo necesita ingresar los parámetros necesarios (ángulos, radios, diámetros, etc.), y la máquina realiza el curvado automáticamente. Son particularmente útiles en la fabricación de componentes en la industria automotriz, aeronáutica y la construcción.
4. Curvadora de tubos por rodillos
Este tipo de máquina utiliza rodillos para doblar el tubo alrededor de un eje, aplicando presión gradual. Es especialmente útil para tubos con diámetros grandes o cuando se necesitan curvados en forma de espiral. Las curvadoras por rodillos también son populares en aplicaciones que requieren un curvado continuo sin necesidad de mantener el tubo en una posición fija durante el proceso.
5. Curvadora de tubos por inducción eléctrica
Este tipo de curvadora utiliza calor inducido mediante un campo magnético para calentar el tubo a una temperatura específica antes de doblarlo. Es particularmente útil cuando se necesitan curvados muy ajustados o cuando se trabaja con materiales que son sensibles a la deformación a temperaturas normales. El calor ayuda a ablandar el material, reduciendo el riesgo de agrietamientos o deformaciones durante el curvado.
6. Curvadora de tubos por tracción o estiramiento
En este proceso, el tubo se estira mientras se curva, lo que permite crear curvaturas de alta precisión sin causar la deformación de la sección transversal. Esta máquina es ideal para trabajar con materiales delgados o tubos que no se deben aplastar, como aquellos utilizados en la fabricación de componentes de precisión en la industria aeroespacial o médica.
Características importantes de las máquinas para doblar tubos:
- Capacidad de curvado: Varía según el diámetro, el espesor de las paredes y el material del tubo. Las máquinas de mayor capacidad permiten doblar tubos más gruesos y con mayor precisión.
- Radio de curvado: El radio de curvado se refiere a la curvatura mínima que se puede lograr sin dañar el tubo. Algunas máquinas permiten curvados con radios muy pequeños, lo que es necesario en aplicaciones donde el espacio es limitado o donde se requieren curvas agudas.
- Control de precisión: Las máquinas más avanzadas, como las CNC, ofrecen un control preciso sobre los ángulos y las formas de los tubos, garantizando la consistencia y la calidad en la producción.
- Automatización: Las curvadoras CNC y las máquinas hidráulicas de última generación están automatizadas para garantizar una producción eficiente y reducir la intervención manual, lo que mejora la velocidad de producción y reduce errores.
- Flexibilidad: Algunas máquinas para doblar tubos están diseñadas para ser versátiles, permitiendo la curvatura de una variedad de materiales y tamaños de tubos con un mínimo de ajustes.
Aplicaciones de las máquinas para doblar tubos:
- Industria automotriz: Para la fabricación de sistemas de escape, chasis, conductos de refrigeración y otras partes metálicas que requieren tubos curvados.
- Construcción: Para sistemas de plomería, estructuras de soporte, conductos de aire acondicionado y otras aplicaciones donde se necesitan tubos curvados para adaptarse a las dimensiones de un edificio.
- Industria aeroespacial: Para crear componentes de precisión como sistemas de combustible y estructuras internas de aeronaves que requieren tubos curvados con alta fiabilidad.
- Industria naval: Para sistemas de tuberías de refrigeración, combustible y otros sistemas que requieren tubos curvados en barcos y embarcaciones.
- Energía y petroquímica: En la fabricación de sistemas de tuberías que transportan fluidos a alta presión y temperatura, donde las curvas son necesarias para adaptar los tubos a los diseños de las plantas y sistemas de distribución.
En resumen, una máquina para doblar tubos es esencial para la creación de componentes curvados que se utilizan en una variedad de industrias. La elección del tipo de máquina depende de factores como la capacidad de producción, los materiales a trabajar y el nivel de precisión requerido en el proceso. Las máquinas más avanzadas, como las curvadoras CNC y las hidráulicas, permiten un mayor control y versatilidad, lo que las hace adecuadas para aplicaciones de alta precisión y volumen.
Las máquinas para doblar tubos no solo desempeñan un papel clave en la fabricación de componentes para diversas industrias, sino que también han evolucionado con el tiempo para adaptarse a las crecientes demandas de precisión, velocidad y eficiencia. La innovación tecnológica ha impulsado el desarrollo de equipos cada vez más sofisticados, que permiten realizar curvados de tubos con tolerancias mínimas y una flexibilidad sin precedentes. Con el uso de control numérico por computadora (CNC), las curvadoras de tubos modernas pueden ser programadas para realizar múltiples configuraciones sin la intervención manual, lo que permite realizar lotes de producción de alta calidad sin errores. Esto es especialmente útil en aplicaciones donde las especificaciones son estrictas, como en la fabricación de componentes de sistemas de escape de vehículos, componentes de aeronaves y en la construcción de sistemas de refrigeración en la industria automotriz y aeroespacial.
La precisión y la capacidad para trabajar con una variedad de materiales, como acero inoxidable, aleaciones de titanio y compuestos de fibra de carbono, han hecho que las máquinas para doblar tubos sean aún más relevantes en sectores que requieren tubos curvados con características específicas de resistencia, peso y durabilidad. En el sector energético, por ejemplo, se utilizan tubos curvados en sistemas de tuberías para transportar líquidos y gases a alta presión. Estos sistemas deben ser capaces de resistir condiciones extremas sin comprometer la seguridad ni la eficiencia del sistema, lo que pone de relieve la importancia de la precisión en el proceso de curvado.
Las máquinas para doblar tubos también han evolucionado en términos de eficiencia energética y reducción del desperdicio de material, lo que es una preocupación constante en la fabricación moderna. La capacidad para ajustar los parámetros del proceso de curvado en función de los materiales y el tipo de tubo está reduciendo la cantidad de material desperdiciado y la energía utilizada en el proceso, lo que se traduce en una producción más sostenible. Estas máquinas modernas pueden optimizar el proceso de curvado al realizar ajustes automáticos en tiempo real, basándose en datos proporcionados por sensores y sistemas de monitoreo, lo que permite obtener el máximo rendimiento de los materiales sin comprometer la calidad.
La tendencia hacia la automatización y la conectividad está transformando la forma en que se operan las curvadoras de tubos. El uso de tecnologías como la Industria 4.0 ha permitido que las máquinas sean más inteligentes y estén interconectadas con otros sistemas de producción. A través de plataformas basadas en la nube y sistemas de monitoreo remoto, los operadores pueden supervisar el rendimiento de las máquinas, realizar ajustes sobre la marcha y prevenir fallos antes de que ocurran, lo que contribuye a una reducción significativa del tiempo de inactividad y a una mayor eficiencia en la producción. La recopilación de datos en tiempo real también facilita el mantenimiento predictivo, lo que permite que los operadores reciban alertas sobre el desgaste de componentes o la necesidad de realizar ajustes en el proceso.
En términos de mantenimiento, las máquinas para doblar tubos de última generación están diseñadas con sensores inteligentes que no solo monitorean el estado de las máquinas, sino que también predicen cuándo es necesario realizar reparaciones o reemplazar componentes. Esto permite a los operadores planificar el mantenimiento de manera eficiente, evitando fallos costosos y tiempos de inactividad imprevistos. La tecnología de diagnóstico remoto también ha avanzado, permitiendo que los técnicos realicen diagnósticos y soluciones de problemas sin estar físicamente presentes, lo que agiliza la resolución de problemas y mejora la eficiencia operativa.
La flexibilidad es otra característica crucial en las curvadoras de tubos modernas. Las máquinas avanzadas permiten una mayor personalización y adaptabilidad a las demandas del mercado, lo que es especialmente valioso en sectores como la fabricación de prototipos, donde la capacidad de realizar ajustes rápidos y adaptarse a nuevas especificaciones es esencial. En industrias como la automotriz, donde los diseños de vehículos están en constante evolución, las curvadoras de tubos deben poder adaptarse a las especificaciones cambiantes sin necesidad de realizar cambios costosos en las herramientas o en los procesos.
Finalmente, a medida que las máquinas para doblar tubos continúan evolucionando, se espera que las soluciones integradas de diseño y fabricación jueguen un papel cada vez más importante. La capacidad de simular y optimizar el proceso de curvado mediante software avanzado antes de la producción física permite a las empresas prever posibles problemas y realizar ajustes en el diseño antes de que se realicen los trabajos, lo que reduce significativamente el riesgo de errores costosos. Esta integración de diseño y fabricación no solo mejora la calidad de los productos finales, sino que también acelera los ciclos de producción, permitiendo a las empresas responder más rápidamente a las demandas del mercado y mejorar su competitividad.
En resumen, las máquinas para doblar tubos son una parte fundamental de la infraestructura de fabricación moderna. Con avances tecnológicos que incluyen automatización, control preciso, monitoreo inteligente y optimización de procesos, estas máquinas están mejor equipadas que nunca para satisfacer las demandas de industrias altamente especializadas. Ya sea que se trate de aplicaciones simples o complejas, las máquinas para doblar tubos siguen siendo una herramienta indispensable en la creación de productos de calidad que son esenciales para una variedad de sectores industriales.
La continua evolución de las máquinas para doblar tubos también está impulsada por la creciente demanda de productos personalizados y lotes pequeños, lo que ha generado un cambio en la forma en que se gestionan los procesos de fabricación. Las industrias buscan mayor flexibilidad y adaptabilidad en la producción para cumplir con las necesidades específicas de los clientes, lo que hace que las curvadoras de tubos más avanzadas se adapten rápidamente a diferentes tipos de material y geometrías sin incurrir en altos costos adicionales.
Esta flexibilidad ha dado lugar a un aumento en el uso de software de simulación y diseño para optimizar los procesos de curvado antes de que se realicen físicamente. Estos programas permiten que los ingenieros y operadores ajusten las configuraciones de la máquina de manera virtual, probando diferentes configuraciones de curvado sin necesidad de realizar cambios físicos o incluso producir prototipos. Esto no solo mejora la precisión y eficiencia, sino que también reduce los costos asociados con la creación de prototipos y mejora los tiempos de respuesta al cliente.
La personalización del producto final también se ha visto impulsada por el uso de impresión 3D y la fabricación aditiva en combinación con las máquinas para doblar tubos. Aunque el curvado de tubos sigue siendo fundamental para muchas aplicaciones, la capacidad de crear componentes altamente personalizados a través de impresión 3D permite producir piezas más complejas que complementan los sistemas de tuberías curvadas. Esto es particularmente importante en sectores como la medicina, donde se requieren componentes de tubería curvados a medida para dispositivos médicos personalizados, o en la industria aeroespacial, donde cada componente necesita cumplir con estrictas especificaciones de diseño y tolerancias.
Otro de los avances en este ámbito es el mejoramiento de la tecnología de curvado para materiales compuestos. Los tubos de materiales compuestos, como los de fibra de carbono o plásticos reforzados con fibra, requieren un enfoque especial al ser doblados debido a su comportamiento más delicado en comparación con los metales tradicionales. Las curvadoras de tubos modernas están diseñadas con sistemas que permiten un control más preciso de la temperatura y la presión durante el curvado, lo que minimiza el riesgo de daños a la estructura del material compuesto y garantiza que el producto final mantenga sus propiedades físicas.
El curvado de tubos sin contacto físico directo, utilizando tecnologías como el curvado por láser o el curvado magnético, también está ganando popularidad en aplicaciones donde se requiere un alto grado de precisión sin la deformación o el contacto directo con el tubo. El curvado por láser, por ejemplo, utiliza un haz de láser para calentar localmente una sección del tubo, permitiendo que se curve con precisión sin necesidad de rodillos o moldes que puedan generar tensiones o marcas en el material.
En términos de sostenibilidad, el sector de la curvadora de tubos también está alineado con las iniciativas ecológicas globales. A medida que las regulaciones ambientales se vuelven más estrictas, las máquinas para doblar tubos están adoptando prácticas que minimizan el desperdicio de materiales y energía. Esto incluye el uso de energía renovable para operar las máquinas y la reciclabilidad de materiales utilizados en los procesos de curvado. Además, el diseño de las máquinas está incorporando materiales más eficientes y duraderos que prolongan la vida útil de los equipos, reduciendo la necesidad de reemplazos frecuentes y contribuyendo a un menor impacto ambiental.
La digitalización y la interconexión de las máquinas de curvado también son tendencias clave en la fabricación de tubos. A través de la implementación de sistemas IoT (Internet de las Cosas), las curvadoras de tubos están más conectadas que nunca, permitiendo el monitoreo remoto, la recopilación de datos en tiempo real y la optimización continua del proceso de producción. Los operadores pueden recibir alertas sobre cualquier desviación en el proceso, lo que les permite tomar decisiones rápidas y eficaces para garantizar la calidad y la eficiencia.
Finalmente, el aprendizaje automático y las técnicas de inteligencia artificial están comenzando a integrarse en las curvadoras de tubos más avanzadas. Estas tecnologías pueden analizar grandes volúmenes de datos de producción y predecir posibles fallos antes de que ocurran. También son capaces de ajustar automáticamente los parámetros de curvado basándose en los datos recopilados, lo que mejora aún más la precisión y eficiencia del proceso sin la intervención humana. Este enfoque no solo reduce el error humano, sino que también contribuye a una producción más ágil y flexible, adaptándose rápidamente a nuevas demandas del mercado.
A medida que las industrias se enfrentan a la necesidad de ser más ágiles y eficientes, las máquinas para doblar tubos seguirán desempeñando un papel crucial. La adopción de nuevas tecnologías permitirá una mayor personalización, precisión y eficiencia en el proceso de fabricación, lo que hace que estas máquinas sean una inversión aún más valiosa para las empresas que buscan mantenerse competitivas en un entorno industrial cada vez más exigente. Con el enfoque en la automatización, la sostenibilidad y la innovación tecnológica, las máquinas para doblar tubos están preparadas para afrontar los desafíos del futuro y seguir siendo una pieza clave en la fabricación moderna.
A medida que la tecnología continúa avanzando, las máquinas para doblar tubos también están adaptándose a nuevos paradigmas industriales, especialmente en áreas como la fabricación de componentes para vehículos eléctricos, energía renovable y la tecnología de la información. Estos sectores, que buscan optimizar el uso de recursos y materiales, están impulsando el desarrollo de nuevas técnicas de curvado que mejoren la resistencia, la ligereza y la eficiencia energética de los componentes fabricados.
Uno de los aspectos más importantes en este contexto es la fabricación aditiva en combinación con el curvado de tubos. En lugar de depender únicamente de técnicas de fabricación tradicionales, los fabricantes están utilizando la impresión 3D para crear estructuras complejas que incorporen tubos curvados. La capacidad de combinar el curvado de tubos con la fabricación aditiva ofrece una ventaja significativa en la creación de diseños complejos y geometrías optimizadas que no serían posibles con técnicas de fabricación convencionales. Esto es particularmente importante en sectores como el aeroespacial, donde las restricciones de peso son críticas y los componentes deben estar diseñados para ser extremadamente ligeros y fuertes.
En la industria de la energía renovable, las máquinas para doblar tubos están ganando relevancia debido a su aplicación en la fabricación de sistemas de energía solar térmica y geotérmica, donde los tubos deben curvarse de manera precisa para adaptarse a las estructuras de los sistemas de captación de energía. La creciente demanda de sistemas de energía más sostenibles ha impulsado la necesidad de mejorar la eficiencia de la fabricación de estos componentes, y las curvadoras de tubos juegan un papel fundamental en asegurar que los diseños se ajusten a las especificaciones exigidas.
El uso de materiales más sostenibles y ecológicos también ha impulsado cambios en la forma en que las máquinas para doblar tubos son diseñadas y operadas. Los plásticos biodegradables y los materiales compuestos a menudo requieren técnicas de curvado más delicadas para evitar la degradación o la deformación del material. En respuesta a esto, los fabricantes de máquinas de curvado están desarrollando tecnologías especializadas que permiten un control de temperatura más preciso, lo que minimiza los riesgos de daño a los materiales más sensibles.
En la industria automotriz, la creciente adopción de vehículos eléctricos y la reducción de emisiones han llevado a una mayor demanda de componentes más ligeros y eficientes. Los tubos curvados de materiales como el aluminio y el acero de alta resistencia se utilizan para construir estructuras más ligeras, mejorar la aerodinámica y reducir el peso total del vehículo, lo que a su vez mejora la eficiencia energética y la autonomía de los vehículos. Las máquinas para doblar tubos desempeñan un papel crucial en este proceso, permitiendo curvados precisos que se ajusten a los diseños más innovadores.
La personalización masiva es otro fenómeno que está cambiando la forma en que se producen los tubos curvados. La demanda de productos altamente personalizados está llevando a un aumento en la producción de componentes que deben cumplir con especificaciones exactas para cada cliente. Las máquinas para doblar tubos, particularmente aquellas equipadas con sistemas CNC avanzados, permiten la fabricación de componentes personalizados sin aumentar significativamente los costos de producción, lo que resulta en una mayor flexibilidad para los fabricantes. Esta personalización es esencial en sectores como el sector médico, donde las piezas personalizadas para dispositivos como prótesis o implantes requieren precisión en el curvado de tubos de materiales biocompatibles.
En términos de mantenimiento predictivo, la inteligencia artificial está desempeñando un papel clave en la mejora de la fiabilidad de las máquinas para doblar tubos. A través del análisis de grandes volúmenes de datos operacionales, los sistemas de inteligencia artificial pueden predecir cuándo ciertos componentes de la máquina están cerca de fallar. Este enfoque no solo reduce el tiempo de inactividad, sino que también mejora la eficiencia general de la producción al garantizar que las máquinas funcionen siempre a su máxima capacidad.
La realidad aumentada (RA) y la realidad virtual (RV) también están comenzando a ser utilizadas para mejorar la capacitación de los operadores y la programación de las máquinas de curvado de tubos. Estos avances permiten que los operadores entrenen de manera virtual y obtengan experiencia práctica sin los riesgos asociados con el trabajo en el entorno de producción real. Además, la RA puede ayudar a los operadores a visualizar en tiempo real los cambios en el proceso de curvado, facilitando ajustes más rápidos y precisos.
Además de la mejora en la eficiencia de las máquinas de curvado, la optimización de los procesos de corte y soldadura también juega un papel crucial en la fabricación de componentes curvados. Los avances en las tecnologías de corte, como el corte por láser y el corte por chorro de agua, permiten a las máquinas para doblar tubos trabajar de manera más eficiente y con menos desperdicio de material, lo que es especialmente relevante cuando se utilizan materiales costosos o difíciles de obtener.
Con el continuo desarrollo de nuevas tecnologías y materiales, las máquinas para doblar tubos seguirán evolucionando para satisfacer las demandas de una industria cada vez más dinámica y orientada hacia la innovación. A medida que los sectores industriales se enfrentan a desafíos cada vez mayores en términos de eficiencia energética, personalización y sostenibilidad, las máquinas de curvado se mantienen como un componente clave en la producción de productos de alta calidad que cumplen con los más altos estándares de rendimiento y diseño. Con un enfoque continuo en la mejora de la precisión, la flexibilidad y la automatización, las curvadoras de tubos seguirán desempeñando un papel fundamental en la industria de fabricación durante muchos años.
Dobladora de tubos
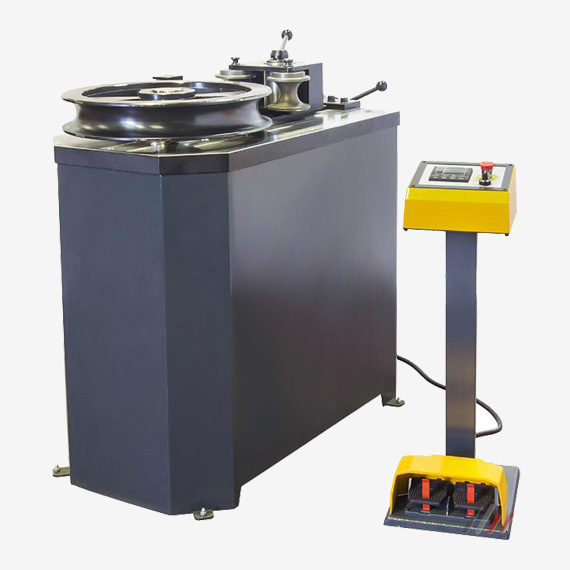
La dobladora de tubos es una máquina especializada diseñada para curvar tubos metálicos o de otros materiales, permitiendo la creación de formas específicas sin dañar la estructura del material. Estas máquinas son fundamentales en una variedad de industrias, como la automotriz, la aeroespacial, la de construcción, la energía y la fabricación de maquinaria industrial. Existen diferentes tipos de dobladoras de tubos, cada una adaptada para procesos específicos según el tipo de material, el diámetro del tubo, el radio de curvado y los requisitos de precisión.
Tipos de Dobladoras de Tubos
- Dobladora de tubos manual:
- Se utilizan principalmente en talleres pequeños o para trabajos de baja producción. Requieren intervención humana para ajustar los tubos y ejecutar el curvado.
- Son más simples, pero limitadas en cuanto a la cantidad de tubos que pueden doblar a la vez y la precisión del trabajo.
- Dobladora de tubos hidráulica:
- Utilizan presión hidráulica para realizar el curvado de tubos. Son capaces de aplicar una fuerza considerable y curvar tubos con precisión, incluso en tamaños grandes o materiales más gruesos.
- Son muy versátiles y se utilizan tanto en aplicaciones de producción en serie como en personalización.
- Dobladora de tubos CNC (Control Numérico por Computadora):
- Estas dobladoras están equipadas con sistemas CNC que permiten la programación de curvas complejas y curvados múltiples sin intervención manual.
- Son ideales para producciones grandes y proyectos que requieren alta precisión. Estas máquinas pueden realizar curvados automáticos, lo que reduce el error humano y mejora la eficiencia.
- Dobladora de tubos a rodillo:
- Usan rodillos para curvar el tubo, permitiendo un control preciso de la curva.
- Son especialmente útiles para tubos de gran diámetro y con un radio de curvado grande. Son más comunes en la fabricación de estructuras metálicas y en la industria de la construcción.
- Dobladora de tubos por mandril:
- Utiliza un mandril interno para mantener la forma del tubo durante el proceso de curvado y evitar que se colapse o deforme. Este tipo de dobladora es especialmente útil para tubos de materiales más delicados, como el aluminio o el cobre.
Principio de Funcionamiento
El principio básico de la dobladora de tubos radica en aplicar una fuerza controlada para modificar la forma del tubo sin alteraciones en su estructura interna. Dependiendo del tipo de dobladora, esta fuerza se genera mediante mecanismos hidráulicos, de rodillos o mediante un control computarizado de las herramientas de curvado. El proceso de doblado generalmente sigue estos pasos:
- Inserción del tubo: El tubo se coloca en la máquina y se asegura mediante un sistema de sujeción.
- Aplicación de la fuerza de curvado: La máquina aplica una fuerza controlada sobre el tubo a través de un rodillo, mandril o un mecanismo hidráulico, forzando al tubo a adoptar la curva deseada.
- Retiro del tubo curvado: Una vez completado el curvado, el tubo se retira de la máquina para continuar con el siguiente paso de la fabricación, como el corte o la soldadura.
Ventajas de las Dobladoras de Tubos
- Precisión y Repetibilidad: Las máquinas CNC, en particular, permiten realizar curvados con alta precisión, lo que es fundamental en sectores como la aeroespacial o la automotriz, donde las tolerancias son críticas.
- Versatilidad: Pueden doblar tubos de diferentes materiales, tamaños y diámetros. Esto las hace útiles en una amplia gama de aplicaciones industriales.
- Ahorro de tiempo: Las dobladoras de tubos automáticas y CNC son capaces de realizar trabajos de curvado con mayor rapidez y menos intervención humana, lo que optimiza los tiempos de producción.
- Mayor calidad en el producto final: Al evitar la distorsión, la deformación o el desgaste del material durante el proceso de curvado, se mejora la calidad del producto final.
Aplicaciones de las Dobladoras de Tubos
- Industria automotriz: Se utilizan para fabricar tubos de escape, estructuras metálicas del vehículo y componentes de los sistemas de refrigeración o aire acondicionado.
- Aeroespacial: Los tubos curvados son esenciales para sistemas de combustible, líneas hidráulicas y estructuras en aeronaves.
- Construcción: Se utilizan para fabricar estructuras de acero, barandillas, andamios y otros componentes metálicos.
- Energía: Las dobladoras de tubos se emplean en la fabricación de tuberías de alta presión en centrales térmicas, nucleares y sistemas de energía renovable.
- Mobiliario y decoración: También se utilizan en la fabricación de productos como mobiliario de acero, tuberías decorativas y estructuras de diseño.
Avances Tecnológicos
La automatización y el uso de tecnologías inteligentes están transformando las dobladoras de tubos. Con el auge de la Industria 4.0, muchas dobladoras de tubos ahora están equipadas con sensores inteligentes y sistemas de monitoreo en tiempo real que mejoran la eficiencia del proceso y permiten la optimización del rendimiento.
Por ejemplo, la tecnología de mantenimiento predictivo basada en datos puede predecir cuándo un componente de la máquina está cerca de fallar, lo que permite programar reparaciones antes de que se produzca un fallo. Esto contribuye a un menor tiempo de inactividad y mayores rendimientos en la producción.
Consideraciones en la Elección de una Dobladora de Tubos
- Tipo de material: Los diferentes materiales requieren diferentes enfoques. Los tubos de acero, por ejemplo, pueden necesitar una dobladora de alta presión, mientras que los tubos de materiales más blandos, como el cobre, pueden ser doblados con menos esfuerzo.
- Diámetro del tubo: El diámetro y el grosor de los tubos influirán en el tipo de máquina que se debe elegir.
- Tolerancia y precisión: Si el proyecto requiere una precisión extremadamente alta, se debe optar por dobladoras CNC que ofrezcan control preciso de la máquina.
- Radio de curvado: Algunos proyectos requieren curvados de tubos con radios muy pequeños, lo cual puede necesitar máquinas especializadas.
En resumen, las dobladoras de tubos son una herramienta esencial en la fabricación de componentes metálicos curvados. A medida que la tecnología sigue avanzando, las capacidades de estas máquinas también evolucionan, permitiendo una mayor precisión, velocidad y flexibilidad en el proceso de curvado. Estas máquinas seguirán siendo claves en una variedad de industrias, proporcionando soluciones eficientes y adaptables a las crecientes demandas del mercado.
Las dobladoras de tubos han experimentado una evolución constante, adaptándose a nuevas demandas y avances en materiales, diseño y producción. Una de las áreas en las que se ha observado un crecimiento significativo es la automatización, que ha transformado estas máquinas en herramientas mucho más sofisticadas. Los sistemas CNC (Control Numérico por Computadora) permiten una mayor precisión en la fabricación y son capaces de realizar curvados complejos sin intervención manual, lo que mejora tanto la eficiencia como la calidad del producto final. Estas máquinas, equipadas con sensores y tecnología avanzada, permiten programar una serie de curvados en función de las especificaciones exactas de cada proyecto. Esto es especialmente útil en sectores como el automotriz, donde la fabricación de componentes debe cumplir con tolerancias estrictas. La automatización también permite optimizar el uso de materiales, reduciendo los desperdicios y mejorando los tiempos de producción.
Además, las tecnologías de monitoreo en tiempo real se están incorporando cada vez más en las dobladoras de tubos. Estos sistemas permiten a los operadores supervisar el proceso de curvado mientras se está llevando a cabo, proporcionando alertas si algún parámetro de la máquina se desvía de las condiciones óptimas. Esto no solo mejora la eficiencia operativa, sino que también minimiza el riesgo de defectos en el producto final. Las máquinas modernas están conectadas a redes inteligentes que proporcionan datos valiosos sobre el estado de la máquina y el rendimiento del proceso. Esto se conoce como Industria 4.0, donde la interconexión de máquinas y la recopilación de datos en tiempo real permiten a las empresas ser más proactivas y menos reactivas.
Por otro lado, las máquinas de doblado están adoptando tecnologías de simulación que permiten a los ingenieros y operarios visualizar el proceso de curvado antes de ejecutarlo físicamente. Mediante software avanzado, es posible prever cómo se comportará el tubo durante el doblado, lo que permite hacer ajustes en los parámetros sin necesidad de realizar pruebas físicas. Esto es particularmente útil para proyectos que involucran tubos de materiales nuevos o complejos, como los de fibra de carbono o aleaciones de titanio, que requieren un manejo delicado durante el proceso de curvado para evitar daños.
El curvado de tubos de gran diámetro también ha visto avances importantes. Las máquinas de mayor capacidad ahora pueden curvar tubos de hasta varios metros de largo, lo que es esencial en sectores como la construcción de puentes o las plataformas petroleras, donde se requieren estructuras robustas y de gran tamaño. Además, se están desarrollando técnicas de curvado sin contacto físico, que utilizan métodos como el curvado por láser o el curvado magnético, lo que reduce las tensiones en el material y minimiza el riesgo de deformación no deseada.
La sostenibilidad también es un factor cada vez más relevante. En el mundo actual, donde las regulaciones ambientales son cada vez más estrictas, las empresas están buscando formas de reducir el impacto ambiental de sus operaciones. Las máquinas para doblar tubos no son ajenas a este movimiento. El uso de energía renovable para alimentar las máquinas y la implementación de prácticas que minimicen el desperdicio de materiales son pasos importantes hacia una fabricación más ecológica. Además, el reciclaje de materiales, como el acero o el aluminio, es más fácil cuando los tubos pueden ser doblados sin romperse ni deteriorarse, lo que contribuye a un ciclo de vida más largo y menos desechos en el proceso de fabricación.
Otro aspecto clave es el avance en los materiales. Los tubos de materiales compuestos, como fibra de carbono o plásticos reforzados con fibra, requieren una tecnología de doblado diferente debido a sus propiedades físicas. Estos materiales, que ofrecen una excelente relación resistencia-peso, deben ser manejados cuidadosamente durante el proceso de curvado para evitar que se rompan o se deformen. Las dobladoras de tubos de última generación están equipadas con sistemas especializados que controlan la temperatura y la presión de manera precisa para curvar estos materiales sin comprometer su integridad estructural.
La personalización también es un factor que está impulsando la evolución de las dobladoras de tubos. Los productos personalizados están ganando cada vez más demanda, ya sea en dispositivos médicos, donde los tubos deben ajustarse a medidas exactas para aplicaciones como implantes o prótesis, o en la industria del diseño, donde las formas complejas son esenciales para la creación de productos estéticamente atractivos. Las máquinas modernas pueden adaptarse a estas necesidades mediante programación avanzada y ajustes de precisión, lo que permite la fabricación de tubos curvados con formas y geometrías específicas sin la necesidad de moldes costosos.
Además de las capacidades técnicas, las dobladoras de tubos también están evolucionando en términos de seguridad. Con el aumento de la automatización, las máquinas están diseñadas con sistemas de seguridad avanzados que garantizan la protección de los operarios. Estos sistemas incluyen sensores de presencia, paradas automáticas en caso de falla y mecanismos para evitar la exposición a condiciones peligrosas durante el funcionamiento. La incorporación de estas medidas de seguridad no solo protege a los trabajadores, sino que también reduce el riesgo de daños a la máquina o al producto durante la producción.
En resumen, las dobladoras de tubos continúan siendo una herramienta esencial en una amplia gama de industrias, y su evolución tecnológica refleja la necesidad de adaptarse a las demandas de mayor precisión, eficiencia y flexibilidad en la fabricación moderna. Con la continua incorporación de automatización, tecnologías inteligentes y nuevos materiales, estas máquinas están preparadas para afrontar los retos de los sectores industriales más avanzados, contribuyendo al desarrollo de productos más innovadores y sostenibles.
El desarrollo de las dobladoras de tubos también ha sido impulsado por la globalización y el aumento de la demanda de productos con características técnicas más exigentes. Con mercados más competitivos, las fábricas están buscando maneras de optimizar no solo los procesos de curvado, sino también toda la cadena de producción. La integración de sistemas inteligentes en las dobladoras de tubos ha permitido la automatización de las líneas de producción, donde las máquinas se comunican entre sí, intercambiando información en tiempo real para ajustar las variables de la producción sin intervención humana directa.
El concepto de “producción personalizada a gran escala” está tomando más relevancia. Las empresas pueden fabricar productos personalizados con características únicas a través de dobladoras de tubos automatizadas que, sin sacrificar la eficiencia, permiten el cambio rápido de parámetros para adaptarse a las necesidades de cada cliente. Esto es particularmente importante en sectores como la construcción modular, donde se requieren tuberías curvadas a medida para proyectos que varían considerablemente en tamaño y forma, desde edificios hasta instalaciones industriales.
La conectividad y el Internet de las Cosas (IoT) están marcando otro punto de inflexión en la evolución de las dobladoras de tubos. Los sensores IoT instalados en estas máquinas pueden proporcionar datos detallados sobre su rendimiento, condición y eficiencia en tiempo real. Estos datos pueden ser monitoreados de manera remota, lo que permite una supervisión constante y facilita la toma de decisiones rápidas. Esta conectividad permite a los ingenieros identificar rápidamente cualquier anomalía o área de mejora, optimizando el mantenimiento de la máquina y reduciendo los tiempos de inactividad. Además, el análisis de estos datos a lo largo del tiempo puede proporcionar información valiosa para mejorar los procesos y aumentar la productividad de las fábricas.
En cuanto a la sostenibilidad, el enfoque está en la reducción de residuos y la reciclabilidad de los materiales. El reciclaje de metales y aleaciones, como el acero o el aluminio, está siendo cada vez más eficiente debido a las mejoras en las tecnologías de curvado. Las dobladoras modernas están diseñadas para minimizar el desperdicio material durante la fabricación. Los avances en la precisión de las máquinas y en los sistemas de control han permitido a los fabricantes reducir las sobras de material, lo que no solo disminuye los costos, sino que también contribuye a la preservación de recursos naturales. Además, muchos fabricantes están implementando prácticas ecológicas que abarcan desde el uso de energía renovable hasta el diseño de máquinas más eficientes energéticamente.
Los avances en la fabricación aditiva (impresión 3D) también están influyendo en el diseño de dobladoras de tubos. En lugar de depender exclusivamente de la fabricación tradicional, la combinación de la fabricación aditiva con el curvado de tubos ha permitido la creación de estructuras complejas y geometrías optimizadas. Esto es especialmente útil en aplicaciones donde el diseño debe ser ligero pero extremadamente resistente, como en la industria aeroespacial y en la fabricación de dispositivos médicos. Al combinar estas dos tecnologías, los fabricantes tienen la capacidad de crear productos altamente especializados que no serían viables solo con técnicas convencionales de doblado de tubos.
Por otro lado, la reducción del tamaño y la mejora en la ergonomía de las dobladoras de tubos son aspectos que también se están considerando para facilitar su uso en espacios más pequeños o en situaciones donde la movilidad es clave. Las máquinas están siendo diseñadas para ser más compactas sin perder rendimiento, permitiendo su uso en talleres con espacio limitado o en condiciones de trabajo más dinámicas. Estas innovaciones ayudan a las pequeñas y medianas empresas a acceder a tecnologías avanzadas sin tener que realizar grandes inversiones en maquinaria de gran tamaño.
Otro punto interesante es el desarrollo de máquinas con capacidad para doblar tubos de formas no convencionales. En la industria del diseño, por ejemplo, se requieren tubos con curvaturas que van más allá de los tradicionales círculos o ángulos rectos. Las máquinas de curvado avanzadas están siendo diseñadas para hacer posible el doblado de formas irregulares o de curvas complejas, lo que abre nuevas posibilidades en términos de diseño industrial y arquitectura. Estos avances están permitiendo a los diseñadores experimentar con nuevas formas y estructuras, sin tener que comprometer la integridad o la funcionalidad del material.
Las tecnologías de aprendizaje automático (machine learning) también están empezando a integrarse en las dobladoras de tubos. Con la capacidad de aprender y adaptarse a patrones de operación a lo largo del tiempo, estas máquinas pueden mejorar continuamente su rendimiento y ajustarse automáticamente a las variaciones del material o a los cambios en las especificaciones de producción. Esto no solo mejora la calidad de los productos terminados, sino que también optimiza el proceso, lo que resulta en una producción más eficiente y menos susceptible a errores humanos.
Por último, la capacidad de las dobladoras de tubos para adaptarse a una amplia gama de materiales es cada vez mayor. No solo las máquinas están evolucionando para trabajar con metales tradicionales, como el acero, aluminio o cobre, sino que también pueden trabajar con materiales compuestos, plásticos reforzados e incluso materiales no metálicos. Esto amplía enormemente el alcance de las aplicaciones de las dobladoras de tubos en sectores como la industria aeronáutica, donde se requieren materiales ligeros y resistentes, o en la tecnología médica, donde los tubos curvados deben ser precisos y fabricados a partir de materiales biocompatibles.
En resumen, el futuro de las dobladoras de tubos está marcado por un desarrollo continuo hacia máquinas más inteligentes, automatizadas, sostenibles y versátiles. Estas innovaciones están transformando industrias clave, permitiendo la producción de componentes más complejos, más eficientes y más respetuosos con el medio ambiente. A medida que la demanda de personalización, precisión y eficiencia aumenta, las dobladoras de tubos seguirán siendo una pieza fundamental en la manufactura moderna, adaptándose a las necesidades de los sectores más avanzados y cambiantes.
Equipos de curvado de tubos
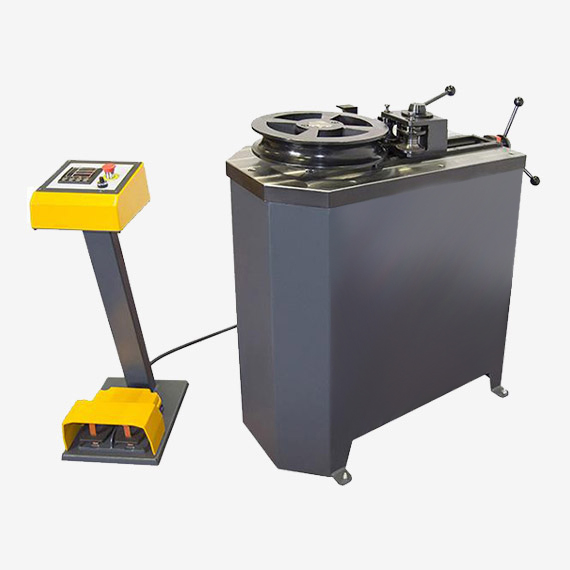
Los equipos de curvado de tubos son máquinas especializadas diseñadas para doblar tubos metálicos, plásticos o de otros materiales, siguiendo especificaciones de diseño que requieren curvaturas precisas y controladas. Estos equipos son esenciales en diversas industrias, como la automotriz, la aeroespacial, la construcción, la energética, entre otras, para producir componentes que cumplen con altos estándares de calidad y exactitud. A continuación se describen los principales tipos de equipos de curvado de tubos y sus aplicaciones:
Tipos de Equipos de Curvado de Tubos
- Dobladora de Tubos Manual
- Son máquinas más simples que requieren intervención manual en cada etapa del proceso. El operador inserta el tubo y aplica la fuerza necesaria para curvarlo. Aunque no son tan precisas ni rápidas como las opciones automatizadas, estas dobladoras son económicas y útiles para trabajos de bajo volumen o en talleres pequeños.
- Aplicaciones: Proyectos de bajo volumen, curvado de tubos pequeños o experimentación con diseños simples.
- Dobladora de Tubos Hidráulica
- Utiliza la fuerza generada por un sistema hidráulico para aplicar presión sobre el tubo y curvarlo. Estas máquinas son muy eficientes, capaces de curvar tubos con alta precisión y en una variedad de materiales, incluso tubos de mayor grosor o dureza.
- Aplicaciones: Fabricación de componentes automotrices, construcción de estructuras metálicas, sistemas de calefacción y refrigeración, fabricación de equipos industriales.
- Dobladora de Tubos CNC (Control Numérico por Computadora)
- Este tipo de dobladora utiliza sistemas de control computarizado para realizar curvados de alta precisión. Los tubos son curvados de acuerdo a un programa preestablecido, lo que permite una gran repetibilidad y la fabricación de componentes complejos sin intervención manual.
- Aplicaciones: Proyectos de alta producción, fabricación de componentes aeroespaciales, automotrices, tubos para sistemas hidráulicos, tuberías industriales y aplicaciones en las que se requiere una alta precisión en el curvado.
- Dobladora de Tubos a Rodillo
- En este tipo de máquina, los rodillos se utilizan para curvar los tubos. El tubo se introduce en la máquina y los rodillos aplican presión en puntos específicos para dar la curva deseada. Estas máquinas son más comunes para curvados en tubos de gran diámetro o cuando se necesitan radios de curvado más grandes.
- Aplicaciones: Curvado de tubos en la industria de la construcción, fabricación de estructuras grandes como andamios o cercas, y en el sector de fabricación de mobiliario metálico.
- Dobladora de Tubos por Mandril
- El mandril es un dispositivo que se introduce en el interior del tubo para mantener su forma durante el proceso de curvado. Esto es crucial para evitar que los tubos se colapsen o deformen durante el proceso. Se utiliza principalmente para materiales más delicados o tubos de mayor grosor.
- Aplicaciones: Curvado de tubos para aplicaciones aeroespaciales, automotrices y cualquier lugar donde la integridad interna del tubo sea crítica.
- Dobladora de Tubos por Inducción
- Este equipo utiliza un sistema de calentamiento por inducción para calentar localmente el tubo a la temperatura adecuada antes de realizar el curvado. El calentamiento permite que el material se flexione sin romperse ni agrietarse. Las máquinas de inducción son muy útiles cuando se trabaja con materiales que requieren calor para ser curvados con éxito.
- Aplicaciones: Curvado de tubos de acero inoxidable, acero al carbono y otros metales de alta resistencia, especialmente cuando el material es grueso o requiere alta temperatura para curvarse correctamente.
- Dobladora de Tubos a Calor (Técnica de Calentamiento por Resistencia)
- Este tipo de máquina calienta el tubo mediante una corriente eléctrica que pasa a través de los materiales para elevar su temperatura. Una vez caliente, el tubo se dobla a la forma deseada.
- Aplicaciones: Usada en la curvatura de materiales como el PVC, algunos plásticos y metales que requieren un calentamiento para evitar la rotura durante el curvado.
Principio de Funcionamiento
El principio básico de un equipo de curvado de tubos es aplicar una fuerza controlada para modificar la forma de un tubo sin dañar su estructura. Dependiendo del tipo de equipo, la fuerza puede ser hidráulica, mecánica o controlada por rodillos. En el proceso de curvado, los tubos generalmente se mantienen en su lugar con un sistema de sujeción mientras se les aplica presión de manera controlada para curvarlos.
El proceso de curvado en sí mismo suele involucrar varios pasos:
- Posicionamiento del tubo: El tubo se coloca en la máquina de curvado y se asegura con un sistema de sujeción.
- Aplicación de la fuerza de curvado: Dependiendo del tipo de máquina, la fuerza puede ser aplicada por presión hidráulica, rodillos, un mandril, etc.
- Curvado: La máquina curva el tubo de acuerdo a los parámetros predeterminados o el control manual del operador.
- Retiro del tubo: Una vez que se ha alcanzado la curvatura deseada, el tubo se retira de la máquina.
Ventajas de los Equipos de Curvado de Tubos
- Precisión: Los equipos modernos, especialmente los de tipo CNC, permiten curvar tubos con una alta precisión, lo que es esencial en sectores como la automotriz, aeroespacial o médico.
- Versatilidad: Los equipos de curvado de tubos pueden trabajar con una amplia variedad de materiales, incluidos diferentes tipos de metales y plásticos. Esto los hace útiles en una amplia gama de industrias.
- Velocidad: Las máquinas automatizadas y las de control numérico permiten realizar curvados rápidamente, lo que es esencial en aplicaciones de producción en serie.
- Flexibilidad de diseño: Muchas de las máquinas modernas permiten realizar curvados complejos y de formas irregulares, lo que da más libertad a los diseñadores y fabricantes en cuanto a la creación de productos.
- Eficiencia: Los sistemas hidráulicos y CNC optimizan el uso de los materiales, reduciendo el desperdicio de tubo y aumentando la eficiencia en la producción.
Aplicaciones de los Equipos de Curvado de Tubos
- Industria automotriz: Fabricación de tubos de escape, chasis de vehículos, sistemas de refrigeración, y otros componentes metálicos curvados.
- Industria aeroespacial: Fabricación de líneas de combustible, sistemas hidráulicos, y componentes estructurales de aeronaves.
- Construcción: Curvado de tubos para barandillas, andamios, estructuras metálicas, y otros elementos arquitectónicos.
- Energía: Producción de tuberías de alta presión para centrales eléctricas y plataformas petroleras.
- Electrodomésticos: Fabricación de intercambiadores de calor, sistemas de refrigeración y componentes metálicos curvados.
- Mobiliario y decoración: Diseño de muebles, estructuras decorativas, y otros productos que requieren tubos curvados con formas complejas.
Consideraciones para Elegir un Equipo de Curvado de Tubos
Al seleccionar un equipo de curvado de tubos, es importante tener en cuenta:
- Material del tubo: Algunos equipos son más adecuados para ciertos materiales, por lo que se debe elegir una máquina que pueda manejar el tipo de material con el que se trabajará (por ejemplo, acero inoxidable, cobre, aluminio, plástico, etc.).
- Diámetro y grosor del tubo: Las capacidades de curvado varían según el tamaño y grosor de los tubos. Asegúrese de que la máquina pueda manejar las especificaciones del tubo que necesita doblar.
- Precisión y tolerancias: Si el proyecto requiere alta precisión en los curvados, las máquinas CNC son la mejor opción.
- Radio de curvado: Algunos equipos permiten curvados con radios muy pequeños, mientras que otros son más adecuados para curvados con radios grandes.
- Producción y volumen: Dependiendo de si se necesita una producción masiva o trabajo personalizado, puede ser mejor elegir entre máquinas automáticas o manuales.
En resumen, los equipos de curvado de tubos son esenciales para la producción de una amplia gama de componentes en diversas industrias. La elección de la máquina adecuada dependerá de factores como el tipo de material, el diámetro del tubo, la precisión requerida y el volumen de producción. Con la evolución de la tecnología, estos equipos están mejorando continuamente en términos de eficiencia, precisión y versatilidad, lo que permite a las empresas ofrecer productos de alta calidad y cumplir con los requisitos del mercado.
Los equipos de curvado de tubos siguen avanzando en su capacidad de adaptarse a nuevas demandas tecnológicas y de mercado, lo que ha hecho que se vuelvan herramientas clave en múltiples sectores industriales. La automatización y el control numérico por computadora (CNC) han permitido que estos equipos sean más rápidos y precisos, lo que ha transformado el panorama de la fabricación. Los sistemas CNC, en particular, permiten que los operadores programen las máquinas para realizar curvados complejos de forma consistente y repetitiva sin intervención manual, lo que mejora la eficiencia y reduce el margen de error. Esto es fundamental en industrias como la automotriz, donde se requieren componentes de alta precisión en tiempos reducidos.
El aumento de la demanda de personalización también ha impulsado el desarrollo de equipos de curvado de tubos más versátiles. Las máquinas modernas permiten realizar curvados con múltiples radios y formas complejas, lo que resulta ideal para aplicaciones donde el diseño personalizado es esencial, como en la fabricación de estructuras metálicas decorativas, sistemas de tuberías para equipos industriales o componentes arquitectónicos. Además, la capacidad de realizar curvados sin dañar el material o producir defectos es crucial para industrias como la aeroespacial o la de dispositivos médicos, donde los estándares de calidad son extremadamente altos.
Con la creciente atención al medio ambiente y la sostenibilidad, los fabricantes están desarrollando equipos de curvado de tubos más eficientes desde el punto de vista energético y que generan menos desperdicios. La optimización del uso de materiales es una de las áreas en las que los avances tecnológicos están teniendo un impacto significativo. Gracias a los sistemas de control avanzados y a la monitorización en tiempo real, las máquinas pueden ajustar automáticamente los parámetros para minimizar el desperdicio de material, lo que no solo reduce los costos, sino que también contribuye a la reducción del impacto ambiental de los procesos industriales.
Por otro lado, la tendencia hacia la fabricación de productos más ligeros y resistentes también está llevando al uso de materiales nuevos y más avanzados en el curvado de tubos. El trabajo con materiales compuestos, como los plásticos reforzados con fibra de carbono, o con aleaciones de alta resistencia, requiere equipos de curvado especializados que pueden manejar las características particulares de estos materiales. Estos tubos, que son más frágiles o menos maleables que los metales tradicionales, deben ser tratados con precisión para evitar cualquier tipo de daño, lo que ha motivado el desarrollo de tecnologías de curvado más delicadas y controladas, como el curvado por inducción o el uso de mandriles internos.
Además de la tecnología de curvado en sí misma, el proceso de control de calidad ha mejorado enormemente gracias a la incorporación de tecnologías como la visión artificial, que permite a los equipos de curvado de tubos detectar posibles defectos durante el proceso de curvado. Los sistemas de inspección visual o sistemas de medición 3D permiten una verificación en tiempo real de las dimensiones y la forma de los tubos, asegurando que cumplan con las especificaciones exactas. Esta automatización del control de calidad contribuye a una mayor confiabilidad en la producción, reduciendo la probabilidad de defectos y fallos en los productos finales.
El mantenimiento predictivo también ha jugado un papel clave en la evolución de estos equipos. Con la integración de sensores IoT y sistemas de monitoreo, los fabricantes ahora pueden anticipar posibles fallos antes de que ocurran, optimizando el tiempo de funcionamiento de las máquinas y reduciendo los costos asociados al mantenimiento reactivo. Los datos recopilados por estos sistemas permiten a los ingenieros analizar patrones de uso, identificar posibles puntos de falla y programar el mantenimiento de manera más eficiente. Esto ha sido especialmente útil en la industria del petróleo y gas, donde las tuberías deben ser curvadas con alta precisión y estar en funcionamiento continuo.
En el ámbito de la industria aeronáutica, los equipos de curvado de tubos están adaptándose a la necesidad de producir componentes más ligeros y fuertes. La fabricación de tuberías de combustible y otros componentes críticos debe ser realizada con materiales de alta resistencia y precisión, sin comprometer la seguridad. Las máquinas de curvado con tecnología de control avanzado permiten crear estos componentes de forma eficiente y con la mínima desviación posible, algo esencial en sectores tan rigurosos.
El curvado de tubos a gran escala, como en la fabricación de sistemas de tuberías para la construcción de grandes plantas industriales, ha llevado al desarrollo de máquinas capaces de manejar tubos de mayor diámetro y mayor longitud. Estas máquinas no solo deben ser lo suficientemente potentes para manejar estos tubos, sino también lo suficientemente flexibles para adaptarse a diferentes radios de curvado y tipos de material, garantizando siempre la integridad del producto final.
Otro aspecto que está impulsando la innovación en estos equipos es el diseño modular. Algunas de las últimas máquinas de curvado de tubos permiten la incorporación de módulos adicionales o accesorios que pueden ajustarse según las necesidades específicas de cada proyecto. Esto proporciona a las empresas una mayor flexibilidad y permite que una sola máquina sea utilizada para una variedad de aplicaciones diferentes, reduciendo la necesidad de múltiples equipos especializados.
La conectividad también está siendo una característica destacada en los equipos de curvado de tubos. Las máquinas ahora pueden estar conectadas a redes industriales, facilitando la integración con otros equipos de producción y sistemas de gestión de fábricas. La recopilación de datos en tiempo real permite a las empresas monitorear el rendimiento y optimizar los procesos de fabricación en su totalidad, lo que a su vez contribuye a mejorar la eficiencia operativa y reducir los tiempos de ciclo.
En conclusión, los equipos de curvado de tubos están evolucionando para cumplir con las demandas de una industria cada vez más compleja y exigente. Con la integración de tecnologías avanzadas, la automatización y la mejora de la sostenibilidad, estas máquinas no solo están optimizando el proceso de fabricación, sino que están permitiendo la creación de productos con tolerancias más estrictas, diseños personalizados y una calidad más alta. La incorporación de inteligencia artificial, IoT y mantenimiento predictivo son tendencias que seguirán siendo claves en el futuro de los equipos de curvado de tubos, permitiendo a las empresas no solo mejorar su competitividad, sino también garantizar la seguridad, la eficiencia y la sostenibilidad de sus operaciones.
La evolución de los equipos de curvado de tubos también está estrechamente vinculada con los avances en materiales inteligentes y nano-tecnología. Con el auge de materiales como los metales de memoria de forma, que pueden regresar a su estado original después de ser deformados, se están abriendo nuevas posibilidades para el curvado de tubos. Estos materiales se utilizan en aplicaciones donde la flexibilidad y la recuperación son esenciales, como en dispositivos médicos, sistemas de control térmico y aeroespacial. Las máquinas de curvado de tubos deben ser capaces de adaptarse a las propiedades únicas de estos materiales, lo que plantea nuevos desafíos y oportunidades para la industria.
El papel de las impresoras 3D en la fabricación de componentes curvados también está comenzando a tener impacto en el proceso. Aunque la impresión 3D no es un reemplazo directo de los equipos tradicionales de curvado de tubos, se está utilizando para crear protótipos rápidos o componentes híbridos donde se combinan partes curvadas con otras fabricadas mediante aditivos. Esto es particularmente útil en sectores de diseño avanzado como la industria aeroespacial, la automotriz de alta gama y la fabricación de productos médicos, donde los componentes deben ser personalizados y fabricados con rapidez.
En términos de tecnología de control y software, los equipos de curvado de tubos modernos incorporan algoritmos avanzados que no solo controlan el curvado en tiempo real, sino que también optimizan el proceso al anticipar las reacciones del material bajo diferentes condiciones de temperatura, velocidad y presión. Esto significa que, incluso antes de comenzar a trabajar con un nuevo material o diseño, la máquina puede ajustar automáticamente sus parámetros para adaptarse a las propiedades específicas del tubo, lo que reduce significativamente la posibilidad de errores o defectos en el producto final.
El control de calidad avanzado es otra de las áreas que se está beneficiando enormemente de los avances tecnológicos. Los sistemas de visión artificial, escaneo 3D y sensores de deformación se integran en los equipos de curvado de tubos para realizar inspecciones en tiempo real, verificando tanto las dimensiones como la forma del tubo curvado. Estos sistemas pueden detectar incluso desviaciones mínimas que podrían pasar desapercibidas para un operador humano, lo que asegura que cada componente cumpla con las especificaciones exactas, sin necesidad de un control manual intensivo.
En cuanto a la mejora de la productividad, los avances en inteligencia artificial están permitiendo que los equipos de curvado de tubos aprendan de los procesos anteriores. Mediante el uso de machine learning, estas máquinas pueden detectar patrones en los datos generados durante el curvado y ajustar sus operaciones para lograr resultados más rápidos y precisos. Esto no solo optimiza los tiempos de producción, sino que también ayuda a reducir el desgaste de las máquinas y mejora la durabilidad del equipo.
El acceso remoto y el monitoreo en tiempo real también se están convirtiendo en características esenciales de los equipos de curvado de tubos, especialmente para grandes instalaciones de producción donde las máquinas trabajan durante largas horas sin interrupción. Los operadores pueden monitorear el rendimiento de las máquinas desde sus oficinas o incluso desde ubicaciones remotas, lo que permite realizar ajustes sin necesidad de estar físicamente presentes. Esto facilita la gestión centralizada de varias máquinas y la resolución rápida de problemas, reduciendo tiempos de inactividad y mejorando la eficiencia global de la planta.
En cuanto a sostenibilidad, la reducción de emisiones y consumo energético es otra área de enfoque. Los equipos de curvado de tubos están diseñados con sistemas más eficientes que requieren menos energía para operar, lo que no solo reduce los costos operativos, sino que también ayuda a las empresas a cumplir con normas medioambientales más estrictas. Además, el uso de materiales reciclables y la minimización de desperdicios durante el proceso de curvado contribuyen a que la fabricación sea más ecológica. Algunas máquinas también están equipadas con sistemas que permiten reciclar los restos de material, lo que mejora aún más la sostenibilidad del proceso.
La industria de la construcción también está siendo testigo de una evolución en los equipos de curvado de tubos. El diseño y la fabricación de estructuras metálicas complejas que requieren tubos curvados para encajar en formas personalizadas está llevando a la creación de máquinas de curvado más versátiles y especializadas. Esto es especialmente relevante para el diseño de edificaciones modulares, donde las estructuras prefabricadas requieren curvados exactos de tubos metálicos para encajar correctamente. Los diseños arquitectónicos contemporáneos que incorporan formas curvas y orgánicas también dependen de estas tecnologías para llevar sus ideas a la realidad.
A medida que los mercados emergentes crecen, también lo hace la demanda de equipos de curvado de tubos más asequibles pero igualmente eficientes. Los avances tecnológicos han permitido la fabricación de máquinas que ofrecen alto rendimiento a precios más competitivos, lo que permite a las pequeñas y medianas empresas acceder a tecnología de punta sin realizar grandes inversiones iniciales. Esta democratización de la tecnología es un motor clave para la innovación en muchas industrias, como la de los productos electrónicos, la fabricación de equipos de calefacción y refrigeración, y la construcción.
La automatización de procesos también está extendiéndose a la logística y almacenamiento de tubos curvados. El uso de robots de carga y descarga que mueven los tubos entre las estaciones de curvado y el almacenamiento permite reducir el tiempo de manipulación manual y minimizar los riesgos laborales. Los sistemas de almacenamiento automatizado y de gestión de inventarios optimizan el uso del espacio y mejoran la trazabilidad de los productos, lo que es fundamental en la fabricación a gran escala.
En el futuro cercano, se espera que los equipos de curvado de tubos sigan evolucionando hacia máquinas más autónomas, con inteligencia artificial que permita tomar decisiones en tiempo real, ajustes de diseño y predicción de fallos antes de que ocurran. Además, la capacidad de estos equipos de integrarse con sistemas de gestión de fábricas inteligentes ofrecerá un nivel de optimización sin precedentes, lo que permitirá a las empresas seguir mejorando su competitividad, productividad y sostenibilidad en el mercado global.
Con el avance de la tecnología digital y la Industria 4.0, el panorama de los equipos de curvado de tubos está experimentando una profunda transformación. La integración de sensores inteligentes, análisis de datos en tiempo real y plataformas basadas en la nube está permitiendo una mayor conectividad y control sobre los procesos de fabricación. Esto no solo facilita una producción más rápida y eficiente, sino que también mejora la calidad y la fiabilidad de los componentes fabricados, al permitir una supervisión continua y la intervención en caso de detectar anomalías.
Una de las áreas clave que se está beneficiando enormemente de estas tecnologías es la optimización de procesos. Los sistemas de gestión avanzada de la producción (MES) pueden estar conectados a los equipos de curvado, permitiendo un control de la producción en tiempo real. Esto significa que los operadores pueden recibir alertas si algún parámetro de curvado se desvía de los estándares, permitiendo correcciones inmediatas antes de que se produzcan defectos. Además, los sistemas de planificación de recursos empresariales (ERP) ahora se integran con estas máquinas, optimizando los tiempos de operación, el uso de materiales y la asignación de tareas.
El uso de simulación avanzada también se está convirtiendo en una herramienta crucial en el diseño y fabricación de productos curvados. Mediante el uso de software de simulación, los ingenieros pueden prever cómo se comportará un tubo bajo diferentes condiciones de curvado antes de que se lleve a cabo el proceso real. Esto permite realizar ajustes en los diseños sin necesidad de experimentar con materiales reales, lo que ahorra tiempo y reduce el riesgo de desperdiciar material.
La fabricación aditiva (impresión 3D) y las tecnologías de curvado híbrido están cambiando la forma en que se diseñan y producen componentes de tubo. La fabricación de prototipos rápidos de tubos curvados mediante impresión 3D ahora se combina con curvado tradicional para crear estructuras más complejas. Esto es especialmente relevante para la creación de piezas personalizadas y de bajo volumen, donde el curvado de tubos debe integrarse con otras tecnologías avanzadas para ofrecer la máxima flexibilidad en términos de diseño y producción.
Además, el mantenimiento predictivo juega un papel cada vez más importante en el prolongamiento de la vida útil de los equipos de curvado de tubos. Gracias a la inteligencia artificial y al uso de algoritmos predictivos, los sistemas pueden monitorear el desgaste de las piezas clave de la máquina, como los rodillos y las matrices, y prever cuándo será necesario realizar un mantenimiento preventivo. Esto no solo reduce el tiempo de inactividad no planificado, sino que también mejora la disponibilidad de las máquinas y reduce los costos asociados al mantenimiento correctivo.
En cuanto a la sostenibilidad, el curvado de tubos está evolucionando para alinearse con los principios de la economía circular. Las nuevas máquinas de curvado permiten reutilizar material sobrante, lo que ayuda a reducir los residuos de producción. Los avances en el reciclaje de materiales, combinados con técnicas de curvado más eficientes, están permitiendo a las empresas reducir su impacto ambiental. Algunas máquinas ahora incorporan sistemas que permiten el reciclaje interno de materiales de desecho, lo que contribuye a la reducción de residuos industriales.
Por otro lado, los materiales avanzados continúan siendo una fuente de innovación. A medida que los materiales compuestos y las aleaciones de alta resistencia se hacen más comunes en la fabricación de tubos, los equipos de curvado deben adaptarse a las características únicas de estos materiales. Por ejemplo, los tubos de fibra de carbono requieren tecnologías de curvado específicas debido a su fragilidad y composición. A medida que los fabricantes adoptan estos materiales más ligeros y fuertes, los equipos de curvado de tubos también deben evolucionar para garantizar que estos materiales sean procesados correctamente, sin comprometer sus propiedades estructurales.
El futuro del curvado de tubos también se está viendo influido por la impresión 3D de tubos curvados. Aunque no reemplaza completamente el curvado tradicional, la impresión 3D de tubos curvados o con características geométricas complejas está ganando terreno, especialmente en aplicaciones personalizadas y de baja producción. Esto permite la creación de geometrías que serían extremadamente difíciles o imposibles de lograr con curvado tradicional, como curvas extremadamente complejas o tuberías con cavidades internas que no pueden ser fabricadas con métodos convencionales.
Las máquinas de curvado de tubos más avanzadas también están mejorando en cuanto a la facilidad de uso y la ergonomía. Los controles intuitivos, las interfaces de usuario basadas en pantallas táctiles y las opciones de programación simplificadas están haciendo que los operadores puedan gestionar el proceso de curvado de manera más eficiente, incluso sin experiencia técnica previa. Esto es especialmente importante en plantas de producción de gran escala, donde la capacitación continua y la simplicidad operativa son claves para mantener la productividad sin errores.
El mercado global de los equipos de curvado de tubos está experimentando una creciente demanda debido a la expansión de las industrias de construcción y automotriz, particularmente en mercados emergentes. A medida que más países se industrializan y se desarrollan, la necesidad de infraestructura de tuberías (para calefacción, refrigeración, energía, agua potable, etc.) está en aumento. Esto está impulsando la adopción de máquinas de curvado de tubos más eficientes y económicas en diversas regiones del mundo, lo que contribuye a la expansión de la manufactura de componentes de tubos de alta calidad.
La seguridad en las operaciones de curvado de tubos también ha mejorado significativamente con los avances tecnológicos. Los sistemas de detención de fallos y los sensores de presión en tiempo real ayudan a prevenir accidentes y daños a la maquinaria, garantizando que los operadores trabajen en un entorno seguro. Las protecciones automáticas que detienen la máquina en caso de un fallo o sobrecarga también contribuyen a la reducción de riesgos laborales.
Finalmente, la personalización sigue siendo una de las tendencias más fuertes en el diseño de equipos de curvado de tubos. Con la creciente demanda de productos únicos o de bajo volumen, los equipos deben ser capaces de adaptarse a diferentes especificaciones de curvado con rapidez y precisión. Las máquinas modulares y ajustables están permitiendo que los fabricantes personalicen sus equipos de curvado para una variedad más amplia de aplicaciones sin la necesidad de comprar múltiples máquinas para diferentes tipos de trabajo.
En resumen, los equipos de curvado de tubos seguirán evolucionando con la incorporación de tecnologías digitales avanzadas, mayor sostenibilidad, y mayor conectividad para mejorar la producción y calidad de los productos. La capacidad de adaptarse a nuevos materiales, la mejora de la eficiencia operativa y el enfoque hacia la seguridad y la automatización son elementos clave para el futuro de la industria del curvado de tubos.
Máquina de curvado

Una máquina de curvado es un equipo utilizado en la industria para dar forma a materiales como tubos, varillas o perfiles metálicos, generando curvaturas específicas en estos. Estas máquinas son esenciales en sectores como la construcción, la automoción, la aeroespacial, la fabricación de mobiliario, y muchas más, donde las piezas curvadas se utilizan para formar estructuras complejas, sistemas de tuberías, y componentes de precisión.
Tipos de máquinas de curvado
- Curvadoras de tubos:
- Están diseñadas específicamente para doblar tubos metálicos u otros materiales sin dañar su estructura.
- Pueden doblar tubos de diferentes diámetros y espesores de pared. Dependiendo de la máquina, los tubos pueden ser curvados en una o varias direcciones.
- Curvadoras de varilla o barra:
- Se utilizan para dar forma a varillas, barras y perfiles, generalmente de acero u otros metales.
- Estas máquinas pueden ser manuales, semi-automáticas o totalmente automáticas, dependiendo de su complejidad.
- Curvadoras por rodillos:
- Se utilizan para curvar materiales más gruesos o de gran tamaño, como chapas metálicas o tubos de gran diámetro.
- Estas máquinas utilizan rodillos que presionan el material para darle forma. Son especialmente útiles cuando se necesita una curvatura más uniforme en materiales grandes.
- Curvadoras de mandril:
- Estas máquinas están diseñadas para realizar curvaturas de tubos sin que se aplasten o colapsen internamente. El mandril se inserta dentro del tubo, proporcionando soporte y evitando deformaciones no deseadas.
- Curvadoras hidráulicas:
- Las máquinas de curvado hidráulico utilizan el poder de los cilindros hidráulicos para aplicar fuerza al material y curvarlo. Son conocidas por su capacidad para curvar materiales más gruesos y duros con mayor precisión.
- Se emplean comúnmente en aplicaciones industriales donde se requiere mucha fuerza para trabajar con materiales de alta resistencia.
- Curvadoras CNC (Control Numérico Computarizado):
- Son máquinas de curvado de tubos y varillas que se controlan mediante programación computarizada, lo que permite curvados altamente precisos y repetitivos.
- La ventaja de las máquinas CNC es su capacidad para producir geometrías complejas con tolerancias muy estrictas y sin la necesidad de intervención manual.
Principio de funcionamiento
La máquina de curvado trabaja aplicando una fuerza controlada sobre el material que se desea doblar. Dependiendo del tipo de máquina, la forma y el método de curvado pueden variar:
- Curvado por flexión: El material se flexiona a lo largo de una matriz o por un conjunto de rodillos que lo presionan en un ángulo determinado.
- Curvado por torsión: El material se gira mientras se aplica una fuerza a lo largo de su longitud, creando una curva helicoidal.
- Curvado por tracción: En este proceso, el tubo o material se estira ligeramente mientras se curva, lo que ayuda a evitar fisuras o deformaciones.
Características y componentes clave
- Motor y sistema de accionamiento: Es el componente principal que impulsa la máquina y proporciona la fuerza necesaria para doblar el material. Puede ser eléctrico, hidráulico o neumático, dependiendo de la aplicación y el tipo de máquina.
- Rodillos: En muchas máquinas de curvado, los rodillos son esenciales para aplicar presión sobre el material y generar la curva. Pueden ser ajustables para variar el radio de la curva.
- Control numérico (CNC): En las máquinas de curvado más avanzadas, los controles CNC permiten a los operadores programar con precisión las especificaciones de la curva, ajustando la presión, la velocidad y el ángulo de curvado sin intervención manual.
- Matriz o moldes: Las matrices son utilizadas en algunas máquinas para dar forma al material durante el proceso de curvado. Son especialmente útiles en el curvado de materiales delgados o cuando se requieren formas más complejas.
- Sistemas de control: Muchos de los modelos modernos tienen sistemas de control avanzados que incluyen pantallas táctiles, interfaces gráficas de usuario (GUI) y diagnósticos en tiempo real para facilitar el uso y el mantenimiento.
Aplicaciones comunes
- Industria automotriz: Se utilizan para fabricar componentes como marcos de vehículos, tubos de escape, sistemas de calefacción y sistemas de dirección.
- Aeroespacial: El curvado de tubos es crucial para la fabricación de sistemas de combustibles, tuberías hidráulicas y estructuras internas de aviones y naves espaciales.
- Construcción: Las curvadoras son esenciales para producir tubos y barras curvadas utilizados en estructuras metálicas, sistemas de tuberías, y rejas de protección.
- Mobiliario y decoración: En la fabricación de muebles, revestimientos de acero inoxidable o estructuras decorativas, las máquinas de curvado permiten la creación de formas artísticas y funcionales.
- Electrónica: En el sector de los dispositivos electrónicos, el curvado de tubos se usa para fabricar carcasas metálicas, componentes de cables y dispositivos de soporte.
Ventajas de las máquinas de curvado
- Alta precisión: Las máquinas CNC pueden realizar curvados extremadamente precisos, lo que las hace ideales para componentes de alta tolerancia.
- Versatilidad: Muchas máquinas de curvado pueden ajustarse para trabajar con diferentes materiales, diámetros y radios de curvado.
- Reducción de desperdicios: Las máquinas modernas permiten una producción más eficiente, con menor cantidad de material desperdiciado durante el proceso de curvado.
- Automatización: El uso de controles automáticos y CNC facilita la producción en masa y la repetibilidad de procesos complejos.
En resumen, las máquinas de curvado son herramientas cruciales en muchas industrias, capaces de producir componentes de formas complejas con alta precisión. La continua evolución tecnológica ha permitido mejorar su eficiencia, versatilidad y capacidad de adaptación a nuevos materiales, lo que las convierte en piezas fundamentales para la producción moderna.
Las máquinas de curvado están cada vez más avanzadas, integrando tecnologías como la inteligencia artificial y la automatización para optimizar los procesos de producción. Con la incorporación de sistemas de monitoreo en tiempo real, las máquinas pueden ajustarse automáticamente a las condiciones del material o al desgaste de las herramientas, mejorando la precisión y reduciendo el tiempo de inactividad. Esto significa que las máquinas son capaces de aprender de cada ciclo de curvado y hacer ajustes en base a datos históricos, lo que lleva a un proceso de curvado más eficiente y con menor probabilidad de error. Además, la automoción de estas máquinas permite a las empresas de fabricación ahorrar en costos laborales y reducir la intervención humana, lo que no solo aumenta la productividad sino que también minimiza riesgos en el ambiente de trabajo.
Las máquinas de curvado también están incorporando tecnología de visión artificial y sensores para realizar inspecciones de calidad en tiempo real. Esto asegura que el producto final cumpla con los estándares requeridos sin la necesidad de intervención manual. La visibilidad avanzada de las piezas durante el proceso también ayuda a detectar problemas en la curvatura de los tubos antes de que se conviertan en defectos graves, lo que evita la producción de piezas defectuosas y reduce los costos de retrabajo. En aplicaciones que requieren precisión extrema, como la fabricación de componentes para la industria aeroespacial o medicamentos, esta capacidad de monitoreo es crucial para garantizar que las piezas sean exactamente como se especificaron en los planos de diseño.
Los avances en materiales también están influenciando el desarrollo de las máquinas de curvado. El uso de materiales compuestos o aleaciones especiales en la fabricación de tubos está llevando a la creación de máquinas de curvado más versátiles que pueden manejar estos materiales sin dañarlos. Los tubos de fibra de carbono, por ejemplo, tienen propiedades que requieren máquinas de curvado muy específicas, ya que son más frágiles y requieren un tratamiento especial para evitar el agrietamiento o la deformación. Las máquinas de curvado también deben ser capaces de ajustarse automáticamente a las propiedades del material para garantizar la integridad de la pieza final.
Otra tendencia clave es la personalización y la producción bajo demanda. A medida que las necesidades de los consumidores cambian y los productos cada vez son más específicos, las máquinas de curvado están mejorando en cuanto a su capacidad para adaptarse a diseños personalizados. Las tecnologías como la impresión 3D están ayudando a crear prototipos y modelos que se pueden probar rápidamente, lo que reduce los tiempos de desarrollo y permite que las máquinas de curvado se adapten a cambios rápidos en los diseños sin tener que modificar las configuraciones físicas de la máquina de forma extensa. La integración de software de simulación avanzada y modelado 3D también permite a los ingenieros predecir cómo se comportará un material bajo condiciones específicas antes de realizar el proceso de curvado, lo que reduce el riesgo de errores.
En términos de sostenibilidad, las máquinas de curvado están evolucionando para ser más ecoeficientes. El uso de energía renovable y la mejora de la eficiencia energética en los motores y sistemas de control está ayudando a reducir el consumo de electricidad. Las máquinas también están siendo diseñadas para minimizar el desperdicio de material, utilizando técnicas de curvado más precisas que permiten aprovechar mejor el material disponible y reducir los residuos generados durante el proceso. Esto no solo reduce los costos de producción, sino que también contribuye a la reducción del impacto ambiental de la industria.
El mantenimiento predictivo está jugando un papel cada vez más importante en la operación de las máquinas de curvado. Los sistemas de sensores conectados a plataformas IoT (Internet de las Cosas) permiten a los operadores recibir alertas sobre el desgaste o la falla inminente de componentes clave, como los rodillos o las matrices. Al identificar los problemas antes de que se produzcan fallos graves, se puede planificar el mantenimiento con antelación, evitando paradas no programadas y reduciendo los costos de mantenimiento correctivo.
En resumen, las máquinas de curvado están evolucionando rápidamente con la incorporación de tecnologías inteligentes, mejoras en la eficiencia energética, y un enfoque creciente hacia la sostenibilidad. La capacidad para personalizar la producción, adaptarse a nuevos materiales, y realizar inspecciones de calidad en tiempo real está cambiando la forma en que se utilizan estas máquinas en diferentes sectores industriales. A medida que estas tecnologías continúan avanzando, las máquinas de curvado se están convirtiendo en herramientas aún más precisas, eficientes y rentables, ayudando a las industrias a producir componentes de alta calidad de manera más rápida y económica.
A medida que las máquinas de curvado siguen evolucionando, la automatización avanzada y la inteligencia artificial están jugando un papel clave en la mejora de la eficiencia operativa. Los sistemas de control automatizado permiten a las máquinas ajustar sus parámetros en tiempo real para optimizar el proceso de curvado, lo que a su vez mejora la calidad del producto y reduce los tiempos de ciclo. Estos sistemas también pueden realizar ajustes basados en variables externas como la temperatura ambiente o la humedad, que pueden afectar las propiedades del material y la precisión del curvado. Este nivel de adaptabilidad reduce la intervención manual y minimiza el riesgo de errores humanos, lo que se traduce en una producción más rápida y precisa.
La conectividad es otro aspecto crucial del futuro de las máquinas de curvado. Muchas de las máquinas modernas ahora están integradas en sistemas de fabricación inteligente, donde todas las máquinas en la línea de producción están interconectadas y pueden comunicarse entre sí para coordinar las tareas y optimizar el flujo de trabajo. Esto permite a las empresas de manufactura monitorear y controlar el proceso de curvado desde una plataforma centralizada, asegurando que cada máquina esté funcionando de manera óptima. Además, al recopilar grandes cantidades de datos sobre el rendimiento de las máquinas, los fabricantes pueden utilizar herramientas de análisis de datos para identificar patrones y predecir problemas antes de que ocurran, lo que reduce aún más el tiempo de inactividad y mejora la confiabilidad general del sistema.
Con el crecimiento de las tendencias de personalización y producción a medida, las máquinas de curvado deben ser cada vez más flexibles para adaptarse a los requerimientos de diseño específicos de los clientes. Esto implica la capacidad de producir una amplia variedad de curvaturas, tamaños y formas en un solo ciclo de producción sin la necesidad de realizar ajustes significativos entre cada operación. Las máquinas que pueden cambiar entre diferentes tipos de curvado de forma rápida y eficiente están permitiendo a los fabricantes responder a la demanda de productos personalizados de forma más rápida y económica. Además, la fabricación aditiva y otras tecnologías de producción avanzada también están comenzando a integrarse en el proceso de curvado, lo que permite la creación de piezas complejas o de geometría especial que de otra forma sería difícil de producir utilizando métodos tradicionales.
La creciente demanda de materiales de alto rendimiento también está empujando a las máquinas de curvado a adaptarse a una gama más amplia de materiales. Los tubos de titanio, aluminio, fibra de carbono y otros materiales compuestos requieren tecnologías especializadas debido a sus propiedades únicas, como la alta resistencia, la ligereza o la fragilidad. Por ejemplo, los tubos de fibra de carbono son muy sensibles a las fuerzas externas y pueden fracturarse si no se manejan correctamente. Las máquinas de curvado de última generación están diseñadas para manejar estos materiales de manera que mantengan sus propiedades estructurales sin comprometer la integridad del producto final.
En términos de sostenibilidad, las máquinas de curvado están cada vez más alineadas con los objetivos de economía circular. Esto implica que las máquinas están optimizadas para reducir al máximo los residuos de material durante el proceso de curvado. Las tecnologías de curvado de precisión permiten usar solo la cantidad exacta de material necesaria para la producción, lo que minimiza los desechos y reduce el impacto ambiental. Además, las innovaciones en el reciclaje de materiales están permitiendo a las empresas recuperar los sobrantes de material y reutilizarlos en nuevas producciones, contribuyendo a la reducción de residuos y promoviendo prácticas más ecológicas en la manufactura.
El mantenimiento predictivo basado en inteligencia artificial es otro avance significativo en las máquinas de curvado. A través del análisis de datos en tiempo real recopilados de sensores y sistemas conectados, las máquinas pueden predecir cuándo es probable que se produzca un fallo mecánico o desgaste de componentes clave como los rodillos, matrices o sistemas de control. Esto permite a los operadores tomar medidas preventivas, como la sustitución de piezas antes de que se desgasten por completo, lo que no solo mejora la vida útil de la máquina, sino que también reduce los costos operativos a largo plazo.
La facilidad de uso de las máquinas de curvado también está mejorando. Con el uso de interfaces de usuario intuitivas, pantallas táctiles y programación basada en software, los operadores pueden controlar las máquinas de manera más sencilla, incluso sin una gran experiencia técnica. El diseño modular y las opciones de personalización de las máquinas también permiten que los fabricantes ajusten sus equipos de curvado para adaptarse a diferentes tipos de producción sin necesidad de realizar modificaciones costosas.
Por último, la seguridad sigue siendo una prioridad en el diseño de las máquinas de curvado. Las nuevas máquinas están equipadas con una variedad de sistemas de seguridad, como sensores de proximidad, barreras de seguridad automáticas y interruptores de emergencia que detienen la máquina si se detecta un problema o un riesgo para la seguridad del operador. Esto ayuda a crear un ambiente de trabajo más seguro, reduciendo la posibilidad de accidentes y mejorando la seguridad general en las instalaciones de fabricación.
En conclusión, el futuro de las máquinas de curvado está marcado por avances tecnológicos que mejoran su precisión, flexibilidad, eficiencia y sostenibilidad. La integración de la inteligencia artificial, la automatización avanzada, la conectividad y el mantenimiento predictivo están transformando las máquinas de curvado en herramientas aún más potentes y adaptables, capaces de enfrentar los desafíos de una producción más personalizada, eficiente y respetuosa con el medio ambiente.
Máquina de doblado de tubos
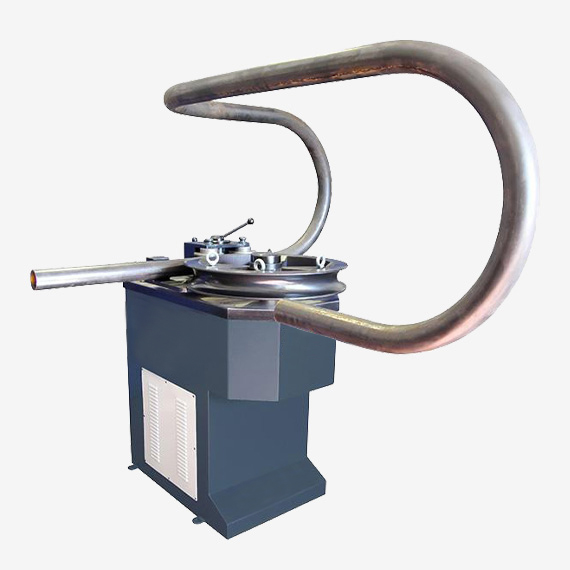
Una máquina de doblado de tubos es un equipo especializado en la curvatura de tubos metálicos y, en algunos casos, de otros materiales como plásticos o materiales compuestos. Estas máquinas son fundamentales en diversas industrias, como la automotriz, aeroespacial, de construcción, de calefacción y ventilación, entre otras. El objetivo principal de una máquina de doblado de tubos es dar forma a los tubos sin comprometer su integridad estructural, evitando daños como el colapso o la torsión.
Tipos de máquinas de doblado de tubos
- Máquina de doblado por rodillos:
- Utiliza un conjunto de rodillos que presionan el tubo mientras gira para crear la curva. Estas máquinas son muy eficientes cuando se trabajan tubos con diámetros grandes o cuando se requiere una curvatura suave y precisa. Existen versiones manuales y automáticas.
- Máquina de doblado por compresión:
- En este tipo de máquina, el tubo se coloca entre dos superficies que lo presionan para crear la curva. La presión se aplica en un área específica del tubo, doblándolo de manera controlada.
- Máquina de doblado hidráulico:
- Estas máquinas utilizan cilindros hidráulicos para aplicar la presión necesaria para doblar el tubo. Son especialmente útiles para tubos gruesos o con materiales de alta resistencia. La ventaja de las máquinas hidráulicas es que pueden trabajar con materiales más resistentes y de mayor espesor, y son conocidas por su capacidad de producir curvaturas muy precisas.
- Máquina de doblado por mandril:
- Esta máquina utiliza un mandril insertado en el interior del tubo, lo que previene que el tubo se colapse durante el proceso de curvado. Es especialmente útil para tubos de material delgado, como los de aluminio o acero inoxidable, y proporciona un doblado sin marcas internas o abolladuras.
- Máquina de doblado por tracción:
- Este tipo de máquina utiliza un sistema de tracción para estirar el tubo mientras lo dobla. El proceso de tracción es particularmente útil para tubos más largos o cuando se requiere un curvado con un radio más grande.
- Máquina de doblado CNC (Control Numérico Computarizado):
- Las máquinas CNC permiten programar el proceso de doblado con alta precisión y reproducibilidad. Estas máquinas son ideales para trabajos de curvado complejos y cuando se requieren múltiples doblados en un solo ciclo de trabajo. Los sistemas CNC pueden ajustar automáticamente el radio, el ángulo y la longitud del doblado.
Principio de funcionamiento
El principio básico detrás de las máquinas de doblado de tubos es aplicar una fuerza controlada para deformar el tubo de manera que adquiera la curvatura deseada sin comprometer su estructura. Dependiendo del tipo de máquina, el proceso puede incluir:
- Flexión simple: El tubo se coloca en una matriz que le aplica presión en una sola dirección, creando una curva.
- Flexión en varias etapas: En algunos casos, los tubos se doblan en múltiples pasos, aplicando diferentes fuerzas a diferentes puntos para obtener curvaturas más complejas.
- Curvado sin mandril: Este proceso se usa cuando no es necesario usar un mandril para evitar colapsos internos, lo cual es más común en tubos de mayor grosor.
- Curvado con mandril: Aquí, un mandril o herramienta interna es usado para evitar el colapso del tubo mientras se curva.
Componentes clave de una máquina de doblado de tubos
- Rodillos o matrices: Son las herramientas que dan forma al tubo mientras se aplica presión. Los rodillos pueden ser ajustables para controlar el radio de curvado.
- Sistema de accionamiento: Dependiendo del tipo de máquina, puede ser un sistema hidráulico, eléctrico o neumático que genera la fuerza necesaria para doblar el tubo.
- Control numérico (CNC): En las máquinas más avanzadas, el sistema CNC permite programar y automatizar el proceso de doblado. Este sistema también puede ajustar automáticamente las posiciones de las matrices, la fuerza aplicada y la velocidad de operación.
- Mandril: En algunas máquinas de doblado, el mandril es una pieza interna que se inserta dentro del tubo para darle soporte y evitar que el tubo se colapse o se deforme internamente mientras se curva.
- Sistemas de monitoreo: Muchas máquinas modernas tienen sensores para monitorear el proceso de curvado y detectar cualquier desviación o defecto. Esto ayuda a garantizar una mayor precisión y una mejor calidad del producto final.
Aplicaciones comunes
- Industria automotriz: Las máquinas de doblado de tubos son esenciales para la fabricación de componentes como marcos de vehículos, sistemas de escape, barras de dirección y sistemas de calefacción. En estos casos, la precisión y la fiabilidad del curvado son cruciales.
- Aeroespacial: Los componentes de tuberías de combustible y tuberías hidráulicas requieren ser doblados con precisión para asegurar que funcionen correctamente en entornos de alta presión y temperatura.
- Construcción: El doblado de tubos de acero es común para crear estructuras metálicas, soportes de tuberías y marcos de edificios. Las máquinas de doblado se utilizan también para crear rejas de protección o barandas de forma eficiente.
- Sistemas de calefacción y ventilación (HVAC): En esta área, se doblan tubos de cobre o aluminio para crear conductos de aire, sistemas de refrigeración y de distribución de agua.
- Electrónica y maquinaria: El curvado de tubos también se utiliza para componentes de maquinaria pesada, como sistemas hidráulicos o dispositivos de refrigeración en maquinaria industrial y equipos electrónicos.
Ventajas de las máquinas de doblado de tubos
- Precisión y repetibilidad: Las máquinas de doblado CNC permiten realizar curvados extremadamente precisos, garantizando que cada pieza producida sea idéntica a las demás.
- Eficiencia en la producción: Las máquinas automatizadas pueden realizar el trabajo mucho más rápido que el doblado manual, lo que permite una mayor producción en menos tiempo.
- Versatilidad: Estas máquinas pueden adaptarse para doblar una variedad de materiales, tamaños de tubos y tipos de curvados, lo que las hace muy útiles para diversas aplicaciones.
- Reducción de desperdicios: El proceso de doblado controlado minimiza los residuos de material, haciendo el proceso más económico y ecológico.
- Mejor calidad: La precisión de estas máquinas garantiza que los tubos doblados tengan una calidad constante, con menos defectos y mayor durabilidad.
Tendencias y avances
Las máquinas de doblado de tubos continúan evolucionando con la incorporación de tecnologías más avanzadas. Algunas de las tendencias y avances incluyen:
- Integración con sistemas de fabricación inteligente: Las máquinas de doblado están comenzando a integrarse con otros sistemas automatizados y robots en la línea de producción, lo que mejora aún más la eficiencia.
- Mejoras en el control de calidad: El uso de sensores y monitoreo en tiempo real permite detectar defectos durante el proceso de curvado, garantizando que solo las piezas de calidad superior lleguen al producto final.
- Mayor capacidad de personalización: Con la creciente demanda de productos personalizados, las máquinas de doblado están siendo diseñadas para manejar una mayor variedad de radios de curvado, espesores de material y longitudes de tubo.
En resumen, las máquinas de doblado de tubos son herramientas esenciales en la industria moderna, ofreciendo una alta precisión, eficiencia y versatilidad en el procesamiento de materiales. Con los avances tecnológicos, estas máquinas continúan mejorando en cuanto a capacidad, flexibilidad y sostenibilidad.
Las máquinas de doblado de tubos siguen evolucionando hacia soluciones más avanzadas, adaptándose a las necesidades de la industria moderna, que demanda mayor precisión, eficiencia y flexibilidad. Las máquinas CNC se han convertido en una herramienta esencial para la fabricación de componentes de tubos, ya que permiten realizar cortes y curvados con una precisión extremadamente alta, reduciendo el error humano y mejorando la producción en masa. Además, el uso de software de simulación está mejorando la capacidad de planificar y prever el resultado del doblado antes de ejecutar el proceso, lo que aumenta la eficiencia al evitar errores y retrabajos.
La automatización está tomando cada vez más protagonismo, con sistemas de control inteligentes que ajustan automáticamente las máquinas en función de las características del material y el tipo de curvado necesario. Esto es especialmente útil cuando se trabaja con materiales de diferentes resistencias, como el acero inoxidable, el aluminio o materiales compuestos, que requieren un enfoque distinto para evitar daños durante el curvado. El aprendizaje automático también se está incorporando en algunas máquinas para mejorar continuamente los procesos y ajustar parámetros basados en datos históricos y condiciones de trabajo en tiempo real.
Los avances en los materiales y en las técnicas de producción también están impactando directamente las máquinas de doblado de tubos. Por ejemplo, el uso de materiales más ligeros y resistentes está impulsando la necesidad de máquinas que no solo puedan doblar tubos de gran grosor, sino que también puedan adaptarse a materiales más delgados y flexibles sin dañarlos. Las máquinas están siendo diseñadas para ser más versátiles, permitiendo trabajar con una gama más amplia de materiales, tamaños de tubo y tipos de curvaturas, sin comprometer la calidad o la velocidad del proceso.
En términos de eficiencia energética, las máquinas de doblado de tubos también están experimentando avances significativos. Los sistemas hidráulicos tradicionales están siendo reemplazados en muchos casos por tecnologías más sostenibles que usan electricidad o incluso energía regenerativa para reducir el consumo. Las máquinas también están mejorando en cuanto a reducción de residuos, utilizando procesos de curvado de precisión que permiten aprovechar mejor el material, minimizando los desechos y contribuyendo a una mayor sostenibilidad en la fabricación.
En la industria moderna, la capacidad de las máquinas de doblado para integrarse con sistemas de Internet de las Cosas (IoT) está cambiando la forma en que se gestionan las operaciones de producción. La conectividad permite a los operadores monitorear el desempeño de la máquina y recibir datos en tiempo real sobre el estado del proceso, lo que facilita el mantenimiento predictivo y la resolución de problemas antes de que se conviertan en fallas importantes. La integración con sistemas de gestión de producción también ayuda a optimizar el flujo de trabajo, mejorando la coordinación entre las distintas fases de la fabricación.
Las aplicaciones de curvado personalizadas también están en auge, lo que significa que las máquinas de doblado de tubos necesitan ser cada vez más flexibles para satisfacer demandas específicas de los clientes. Esto es especialmente relevante en sectores como la automotriz y la aeroespacial, donde los tubos de precisión son esenciales para sistemas como los de combustible, los de escape o los de hidráulica. Las máquinas de doblado están evolucionando para permitir curvaturas complejas sin comprometer la integridad estructural del material.
Finalmente, las máquinas de doblado de tubos también están contribuyendo a mejorar la seguridad en las fábricas. Las protecciones automáticas, los sensores de seguridad y los sistemas de parada de emergencia están haciendo que estas máquinas sean más seguras para los operadores, reduciendo el riesgo de accidentes. La seguridad, combinada con la alta productividad y la precisión mejorada, está transformando el doblado de tubos en un proceso mucho más eficiente y fiable. Con todas estas innovaciones, las máquinas de doblado de tubos están configuradas para ser más inteligentes, sostenibles y adaptables, lo que facilita la producción de componentes de alta calidad en un tiempo más reducido y con un menor impacto ambiental.
A medida que las máquinas de doblado de tubos avanzan, una de las áreas clave de desarrollo es la flexibilidad en la configuración de la máquina. Las máquinas más modernas permiten realizar ajustes rápidos y sencillos, lo que optimiza los tiempos de cambio entre diferentes producciones sin necesidad de configuraciones complejas. Los sistemas de ajuste automático de parámetros basados en el tipo de material y el diseño del tubo son cada vez más comunes, permitiendo que una sola máquina pueda adaptarse a una variedad de tipos de curvados sin que se pierda precisión. Esto no solo mejora la versatilidad sino que también reduce los tiempos de inactividad y aumenta la eficiencia general de la producción.
Además, con el enfoque creciente en la fabricación personalizada, las máquinas de doblado de tubos están integrando funciones avanzadas de modelado 3D y simulación para prever el comportamiento de los materiales bajo diferentes condiciones de curvado. Los modelos virtuales permiten a los ingenieros realizar simulaciones detalladas antes de llevar a cabo el curvado físico, lo que les ayuda a identificar posibles problemas en las fases iniciales de diseño. Este tipo de simulación también ayuda a optimizar el uso del material, asegurando que las piezas no solo sean funcionales, sino también eficientes desde el punto de vista de los costos.
La capacidad de adaptarse a diferentes geometrías también está mejorando, permitiendo que las máquinas de doblado manejen no solo curvas simples, sino también curvados de formas complejas que requieren de un alto nivel de precisión, como las curvas en espiral o las que siguen trayectorias no lineales. Estos avances son cruciales en industrias como la aeroespacial, donde se requieren curvados en tubos que deben adaptarse a diseños extremadamente específicos y complejos.
En el ámbito de la producción masiva, las máquinas de doblado de tubos están incorporando tecnologías de integración robótica, lo que les permite operar de manera completamente autónoma en líneas de producción sin la intervención humana constante. Esto incluye el automanejo de materiales, donde los robots se encargan de cargar y descargar los tubos de la máquina de doblado, lo que mejora significativamente la velocidad y la seguridad. Los robots también pueden estar equipados con sistemas de visión artificial que detectan fallas o imperfecciones en el material antes de que entre en el proceso de curvado, garantizando que solo los tubos sin defectos sean procesados.
En términos de mantenimiento, las máquinas de doblado de tubos están adoptando el concepto de mantenimiento predictivo mediante el uso de sensores inteligentes que monitorizan continuamente el estado de los componentes clave, como los rodillos, las matrices y los sistemas hidráulicos. Estos sensores pueden predecir fallos antes de que ocurran y alertar a los operadores para que realicen un mantenimiento preventivo, evitando costosos tiempos de inactividad o fallos catastróficos. Esto no solo alarga la vida útil de la máquina, sino que también asegura que la producción se mantenga en niveles óptimos sin interrupciones.
Además, la automatización de las máquinas de doblado está permitiendo el uso de materiales reciclados o remanufacturados, lo que beneficia tanto a la economía de los fabricantes como a la sostenibilidad del proceso. El aumento en la demanda de productos ecológicos y la presión por reducir la huella de carbono están empujando a las empresas a adoptar máquinas capaces de trabajar con materiales reciclados sin comprometer la calidad del producto final.
El control de calidad también está experimentando un avance significativo, especialmente con la incorporación de tecnologías de inspección en línea que utilizan cámaras y sensores láser para verificar la precisión del curvado en tiempo real. Los sistemas de inspección detectan cualquier desviación del estándar establecido y permiten que la máquina ajuste automáticamente el proceso para corregir posibles errores sin la necesidad de intervención manual.
La tendencia hacia el trabajo colaborativo también está ganando terreno en la industria del doblado de tubos. Las máquinas colaborativas, o cobots (robots colaborativos), trabajan junto a los operadores humanos, asistiendo en tareas repetitivas o físicamente exigentes. Esto no solo mejora la eficiencia, sino que también permite a los trabajadores centrarse en actividades de mayor valor añadido, como el control de calidad o la programación de nuevas producciones.
El enfoque global también está influyendo en el desarrollo de estas máquinas. Las fábricas ahora están cada vez más orientadas hacia el comercio internacional, lo que requiere máquinas de doblado que puedan trabajar con materiales y especificaciones diversas de diferentes países y regiones. Esto exige que las máquinas sean altamente adaptables a normativas internacionales, lo que incluye variaciones en las normas de seguridad y los materiales utilizados.
Finalmente, las máquinas de doblado de tubos están jugando un papel crucial en la innovación en diseño. Los diseñadores y fabricantes pueden utilizar las capacidades avanzadas de estas máquinas para crear productos más innovadores y funcionales, optimizando tanto la forma como la resistencia de los tubos doblados. Esto es fundamental en sectores de alta tecnología como el automotriz y la aeroespacial, donde la ligereza y la resistencia de los tubos son factores esenciales para mejorar la eficiencia de los vehículos y la seguridad en los aviones. Las mejoras en el doblado de tubos también están permitiendo la fabricación de estructuras más complejas en campos como la ingeniería civil y la construcción, abriendo la puerta a nuevas posibilidades en la creación de componentes estructurales más ligeros, resistentes y fáciles de manejar.
En conclusión, las máquinas de doblado de tubos están pasando por una transformación considerable, influenciada por avances en automatización, sostenibilidad y precisión. Los cambios tecnológicos permiten que estas máquinas sean más flexibles, inteligentes y sostenibles, lo que les permite adaptarse a una mayor variedad de necesidades industriales y fabricar productos de más alta calidad de manera más eficiente.
Dobladora de caños
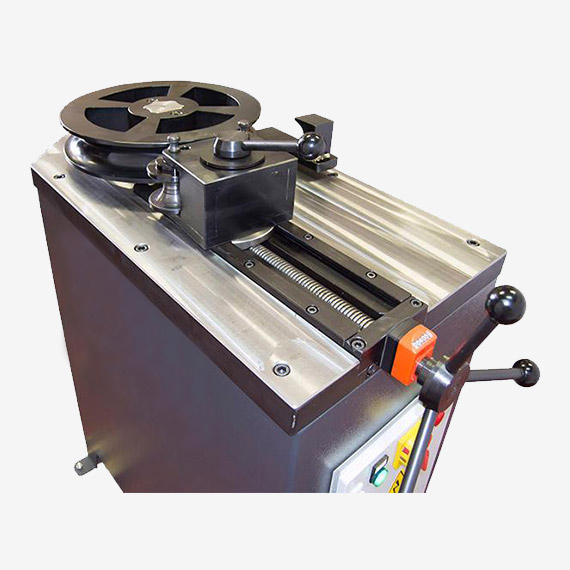
La dobladora de caños es una máquina fundamental en numerosos sectores industriales como la construcción, la automoción, la industria naval, la fabricación de muebles metálicos y la instalación de sistemas de conducción (agua, gas, aire). Su principal función es curvar o doblar caños —también llamados tubos— metálicos sin comprometer su integridad estructural ni su sección transversal. Esta operación, que podría parecer simple, requiere en realidad de un equipo diseñado con precisión para manejar diferentes diámetros, espesores de pared, radios de curvado y materiales, que pueden ir desde acero al carbono hasta aluminio, cobre o acero inoxidable.
Existen diferentes tipos de dobladoras de caños según el principio de funcionamiento: las manuales, las hidráulicas, las neumáticas y las CNC (controladas numéricamente por computadora). Las dobladoras manuales son comunes en trabajos pequeños o en campo, donde se requiere portabilidad y no se necesita alta precisión. Las hidráulicas y neumáticas permiten mayor fuerza y control en el doblado, y se usan en producciones de volumen medio. Las CNC, por su parte, son capaces de realizar curvas múltiples con precisión repetitiva y a alta velocidad, por lo que son esenciales en líneas de producción automatizadas.
El proceso de doblado puede realizarse por diferentes métodos: por compresión, por estiramiento o por inducción. En el doblado por compresión, un dado empuja el caño contra una forma fija para generar la curva. En el doblado por estiramiento, el tubo es traccionado mientras se dobla para evitar el aplastamiento de la sección. En el doblado por inducción, se calienta una zona específica del tubo mediante inducción electromagnética y luego se curva, siendo útil para caños de gran diámetro o paredes gruesas. Cada técnica tiene ventajas y limitaciones dependiendo del uso final del caño, la precisión deseada y el tipo de material.
Uno de los principales desafíos en el doblado de caños es evitar defectos como el aplanamiento del tubo en la zona curva, la formación de arrugas internas o la rotura por exceso de tensión. Para mitigar estos problemas, se emplean técnicas como el uso de mandriles o insertos internos que mantienen la forma durante el doblado, y soportes de presión o dados de sujeción que acompañan el movimiento. Las máquinas más modernas integran sensores de deformación, sistemas de retroalimentación y ajustes automáticos para asegurar que cada curva se produzca dentro de tolerancias estrictas.
Las dobladoras de caños también se diseñan para adaptarse a diversos requisitos industriales. Por ejemplo, en la industria automotriz, donde los tubos de escape, de freno o de aire acondicionado deben cumplir normas precisas, se requieren radios de curvatura exactos, sin deformaciones. En la construcción, los caños estructurales o de instalación requieren resistencia, por lo que se usan materiales más gruesos y métodos de doblado de alta potencia. La elección de la máquina depende tanto del material como del nivel de automatización y producción requerido.
Además de la funcionalidad técnica, el diseño ergonómico y la seguridad del operador son aspectos clave en las dobladoras actuales. La inclusión de barreras físicas, sensores de parada automática y sistemas de control por pantalla táctil facilita la operación y reduce riesgos. Las interfaces hombre-máquina en los modelos CNC permiten programar múltiples operaciones y almacenarlas para repetición futura, mejorando la trazabilidad y la eficiencia del proceso.
A medida que la industria demanda soluciones más rápidas, precisas y sostenibles, las dobladoras de caños seguirán evolucionando. La integración con software CAD/CAM permite traducir diseños digitales directamente en instrucciones de curvado, lo que reduce errores humanos y acelera la fabricación. También se observa una tendencia hacia máquinas más compactas y modulares, que puedan adaptarse fácilmente a distintos entornos de producción.
Las dobladoras de caños están en constante evolución, adaptándose a las demandas de precisión, velocidad y flexibilidad que requieren las industrias modernas. Además de las mejoras en los métodos de control y automatización, los avances en materiales y diseño también están permitiendo a estas máquinas ofrecer un mayor rendimiento y mayor durabilidad. Por ejemplo, las máquinas de doblado de caños CNC están equipadas con software avanzado que no solo controla el proceso de doblado con una precisión extremadamente alta, sino que también ofrece opciones de personalización para cada tipo de proyecto. Esto significa que se pueden crear curvas complejas y formas personalizadas para adaptarse a las necesidades específicas del cliente o del producto final.
Los sistemas de control numérico permiten ajustar y preprogramar diferentes configuraciones para cada tipo de material, diámetro y espesor del tubo, lo que optimiza tanto el tiempo de producción como la calidad del trabajo final. Esto es particularmente útil en industrias que requieren alta flexibilidad y rapidez, como la automotriz o la industria aeroespacial, donde los plazos de entrega son muy ajustados y la calidad es crítica.
Un aspecto importante de las dobladoras de caños es la capacidad de adaptarse a una variedad de materiales. Aunque el acero es el material más comúnmente doblado, cada vez se están utilizando más aleaciones especiales y materiales no ferrosos, como el aluminio y el cobre, que tienen propiedades de doblado diferentes. La adaptabilidad de las máquinas modernas a estos materiales también requiere innovaciones en los sistemas de control y en la tecnología de la máquina misma, para evitar deformaciones no deseadas, como el colapso de las paredes del tubo o el agrietamiento de materiales más frágiles.
El mantenimiento predictivo también es una tendencia creciente. Las máquinas de doblado modernas están equipadas con sensores que monitorean continuamente el estado de los componentes críticos, como los rodillos, las matrices y las cuchillas. Estos sensores pueden alertar a los operadores cuando es necesario realizar mantenimiento antes de que se produzca una falla grave. Esto no solo reduce el tiempo de inactividad, sino que también ayuda a prolongar la vida útil de la máquina, lo que representa una inversión a largo plazo más rentable.
En términos de eficiencia, las máquinas de doblado de caños están incorporando más funciones automatizadas, como la alimentación automática de tubos y el ajuste automático de parámetros, lo que elimina la necesidad de intervención manual constante y mejora la productividad. También se están desarrollando nuevas tecnologías que permiten el doblado en caliente o el doblado sin mandril para evitar daños en el tubo durante el proceso de curvado, especialmente cuando se trata de tubos de gran diámetro o paredes gruesas.
La industria está presionando por soluciones más ecológicas y sostenibles. Por lo tanto, las máquinas de doblado están adoptando tecnologías que permiten reducción de desechos y un menor consumo energético. Esto incluye el uso de sistemas hidráulicos de bajo consumo, el reciclaje de materiales y la implementación de procesos de doblado sin calor para eliminar la necesidad de calentamiento de los materiales, lo que reduce el impacto ambiental.
Finalmente, el diseño modular de las dobladoras de caños está haciendo posible que las máquinas se ajusten fácilmente a las necesidades cambiantes de los productores. Los componentes modulares permiten a los operadores actualizar o modificar sus equipos para adaptarse a nuevos requerimientos de producción, lo que hace que la inversión sea más rentable a largo plazo. Esto es especialmente útil en mercados donde la demanda puede fluctuar rápidamente o donde se requiere flexibilidad para realizar diferentes tipos de curvados sin necesidad de invertir en nuevos equipos costosos.
En resumen, las dobladoras de caños han avanzado significativamente, no solo en términos de capacidad de doblado, sino también en lo que respecta a la automatización, la precisión y la sostenibilidad. Estos avances están permitiendo a las industrias no solo mejorar la calidad y la eficiencia de su producción, sino también reducir costos y su impacto ambiental.
Las dobladoras de caños también están evolucionando en el área de integración de procesos. Hoy en día, muchas de estas máquinas pueden conectarse a sistemas de gestión de la producción y a plataformas IoT (Internet de las Cosas), lo que permite un flujo de trabajo completamente integrado. Esto significa que los datos generados por la máquina durante el proceso de doblado, como la velocidad, el torque, la temperatura y la deformación del material, pueden ser monitoreados en tiempo real a través de una interfaz centralizada. Esta integración permite no solo optimizar el proceso, sino también realizar ajustes dinámicos mientras la máquina está en operación, lo que mejora aún más la precisión y la eficiencia.
El uso de big data y análisis predictivo en las dobladoras de caños está permitiendo a los operadores prever comportamientos en los procesos y ajustar parámetros de la máquina de forma proactiva. Estos sistemas analizan patrones de datos de ciclos anteriores para anticipar problemas potenciales y optimizar los parámetros de doblado. Por ejemplo, los sensores pueden alertar al operador sobre posibles desviaciones en la alineación del caño, lo que evitaría fallas y defectos en las piezas.
En cuanto a la adaptación a los requisitos de diseño personalizado, las máquinas de doblado de caños de última generación tienen la capacidad de realizar curvas con múltiples radios y curvaturas complejas. Esto permite que los diseñadores de productos y los ingenieros estructurales creen geometrías innovadoras sin tener que comprometer la integridad estructural del tubo. Este tipo de flexibilidad es crucial en campos como la fabricación de componentes de alta precisión en la industria automotriz o la construcción de estructuras arquitectónicas que requieren tubos con formas no convencionales, como curvas angulares o curvas de gran radio.
La automatización avanzada está también desempeñando un papel importante en la reducción de errores humanos. Las dobladoras automatizadas eliminan la intervención manual en los procesos de ajuste de parámetros, programación de operaciones y control de calidad, lo que asegura que cada tubo doblado cumpla con los estándares de precisión preestablecidos. Con la capacidad de almacenar programas de doblado para diferentes tipos de caños, las máquinas pueden reproducir configuraciones y procesos específicos sin necesidad de reprogramación, lo que mejora la productividad y reduce el tiempo de inactividad.
Además, las máquinas de doblado más recientes están diseñadas para ser más compactas y versátiles, lo que permite su uso en espacios más reducidos sin sacrificar capacidad ni precisión. Las máquinas modulares son ahora comunes, permitiendo a las empresas personalizar sus equipos con los módulos adecuados según el tipo de trabajo que realicen, sin necesidad de comprar nuevas máquinas. Esto representa una inversión más flexible y rentable para las empresas que operan en múltiples sectores y requieren adaptarse rápidamente a diferentes tipos de trabajo.
Otro aspecto importante es la capacitación del personal. Con el avance de la automatización y las interfaces complejas de los sistemas de control, la formación de los operadores se ha vuelto aún más crucial. Las máquinas más avanzadas están siendo acompañadas por sistemas de aprendizaje integrados que pueden ayudar a los operadores a entender cómo optimizar el uso de la máquina y corregir posibles errores de operación. Además, algunos sistemas cuentan con interfaces visuales intuitivas que muestran en tiempo real la información del proceso y las condiciones operativas, permitiendo que los operadores no solo controlen la máquina de manera eficiente, sino que también intervengan rápidamente en caso de que algo no esté funcionando según lo previsto.
A medida que las industrias se vuelven más exigentes en cuanto a la eficiencia energética y la reducción de costos operativos, las máquinas de doblado de caños también están incorporando sistemas de recuperación de energía y optimizadores de consumo energético. Esto incluye tecnologías como motores eléctricos más eficientes, sistemas hidráulicos de bajo consumo, y el aprovechamiento de la energía regenerativa, lo que no solo reduce los costos operativos, sino que también contribuye a un proceso de fabricación más sostenible y respetuoso con el medio ambiente.
Finalmente, la evolución de la tecnología de curvado sin contacto está permitiendo nuevas posibilidades en el doblado de caños. Algunos procesos de curvado avanzados no requieren contacto directo entre las piezas y las herramientas, lo que minimiza el desgaste de los componentes de la máquina y reduce las imperfecciones en el material. Esta tecnología es especialmente útil en la fabricación de tubos extremadamente delgados o sensibles que requieren una manipulación muy cuidadosa para evitar daños durante el doblado.
En resumen, las dobladoras de caños no solo han mejorado en términos de precisión y velocidad, sino que ahora integran tecnologías de automatización, conectividad y sostenibilidad que permiten una mayor eficiencia y flexibilidad en la producción. Con avances en inteligencia artificial, aprendizaje automático y modelado 3D, estas máquinas están llevando la fabricación de tubos a nuevos niveles de precisión y personalización, adaptándose a las exigencias cada vez mayores de las industrias más innovadoras.
Formadora de tubos
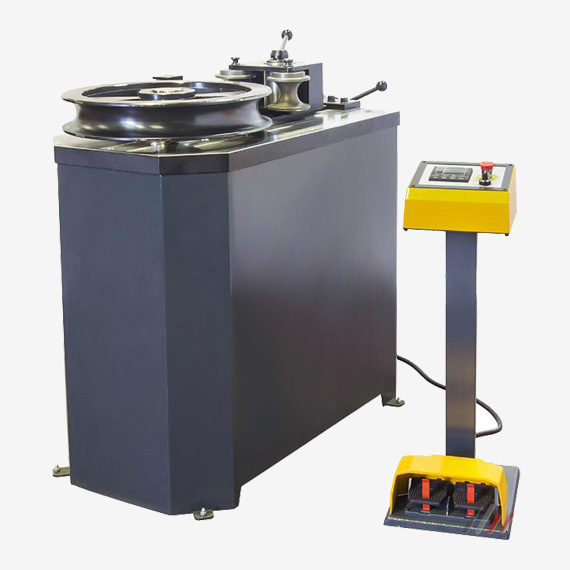
Una formadora de tubos es una máquina especializada en dar forma a los tubos metálicos mediante diversos procesos que permiten que los tubos adquieran la geometría y las características específicas requeridas para aplicaciones industriales. A diferencia de las dobladoras de tubos, que se enfocan en curvar tubos a lo largo de su eje, las formadoras de tubos suelen ser más versátiles en cuanto a la capacidad de modificar la forma transversal o estructural del tubo, como cambios en su diámetro, espesor de pared o incluso la creación de secciones transversales complejas.
Existen varios tipos de formadoras de tubos, cada una con un enfoque y proceso específico, según las necesidades de la industria. Los métodos de formación más comunes incluyen laminado, extrusión, embutición y soldadura. Estas máquinas son utilizadas en una amplia variedad de sectores como la industria automotriz, la industria de la construcción, la fabricación de mobiliario metálico, la fabricación de maquinaria, y la industria del transporte.
Las formadoras de tubos tienen como objetivo principal dar forma a los tubos de metal, pudiendo ser acero, aluminio, cobre, acero inoxidable, entre otros materiales. Dependiendo de la aplicación, se pueden usar para modificar el diámetro de un tubo, hacer transiciones de forma (como en el caso de tubos con cambios de sección), o crear diseños complejos como tubos con secciones cuadradas, rectangulares, ovaladas o de formas especiales.
El proceso de formación comienza con un tubo de material crudo que se introduce en la formadora. La máquina emplea una serie de rodillos o matrices que aplican presión al tubo para darle la forma deseada. En algunos procesos de formación, como el laminado, se utiliza un conjunto de rodillos que comprimen y estiran el material para reducir el diámetro del tubo o darle una forma más precisa. En otros casos, como la extrusión, el material es forzado a través de un molde para crear una forma continua.
En el caso de las formadoras de tubos de sección compleja, el proceso implica mandriles internos que se insertan dentro del tubo para mantener la forma mientras el exterior se moldea. Estas máquinas pueden ser de control manual, semiautomáticas o totalmente automáticas, dependiendo de los requisitos de producción y la complejidad de las formas que se deseen obtener.
Un aspecto crucial de la formación de tubos es el control de calidad. Las formadoras de tubos avanzadas incorporan sistemas de monitoreo y sensores que permiten ajustar en tiempo real las condiciones del proceso, asegurando que el tubo mantenga su forma y sus propiedades mecánicas. También es común que estas máquinas estén equipadas con sistemas de inspección visual o láser para verificar que el diámetro y el grosor de las paredes del tubo estén dentro de las tolerancias especificadas.
En términos de innovación, las formadoras de tubos más modernas están integrando la automatización y la robótica para realizar operaciones de manera más eficiente y precisa. Esto incluye robots de manipulación que cargan y descargan los tubos de la máquina, sistemas de visión artificial para identificar defectos en el material y algoritmos de control adaptativos que ajustan el proceso de formación según las variaciones en el material y las condiciones de operación. Además, muchas formadoras de tubos ahora permiten la integración con sistemas de diseño asistido por computadora (CAD) y manufactura asistida por computadora (CAM), lo que permite una mayor personalización de los productos y mejora la flexibilidad en la producción.
El mantenimiento también ha sido optimizado en las formadoras de tubos modernas, ya que los sensores y los sistemas de monitoreo continúan ayudando a identificar posibles fallos o desgastes antes de que afecten el rendimiento de la máquina. Esto contribuye a la fiabilidad de la producción, especialmente en líneas de fabricación de alta demanda.
En términos de sostenibilidad, las formadoras de tubos están adoptando prácticas que buscan minimizar el desperdicio de material. La recuperación de calor y la optimización energética son aspectos cada vez más importantes en la producción de tubos, y las máquinas actuales están diseñadas para funcionar con un consumo mínimo de energía, lo que no solo reduce los costos operativos, sino que también mejora el impacto ambiental del proceso.
En conclusión, las formadoras de tubos son herramientas clave en la producción de tubos metálicos con formas y características específicas. Con avances en automatización, precisión y sostenibilidad, estas máquinas están mejorando la eficiencia de la fabricación y adaptándose a las necesidades cambiantes de las industrias que dependen de los tubos como un componente esencial en sus productos.
Las formadoras de tubos también están evolucionando para incorporar tecnologías que permiten la producción de tubos complejos con mayor rapidez y precisión. Las nuevas generaciones de estas máquinas están diseñadas para manejar una variedad de formas y materiales, lo que las hace más versátiles para diferentes aplicaciones industriales. Por ejemplo, en la industria automotriz, donde se requieren tubos de formas especializadas para sistemas de escape, refrigeración o estructuras internas del vehículo, las formadoras de tubos deben ser capaces de crear perfiles irregulares sin comprometer la resistencia del material.
Además, las formadoras de tubos modernas están equipadas con sistemas de enfriamiento más eficientes para manejar materiales sensibles al calor. Algunos de estos sistemas emplean enfriamiento por aire o líquido que se aplican a las zonas críticas de la máquina y el tubo, asegurando que no se deformen por exceso de temperatura. Esto es crucial cuando se trabajan con metales como el aluminio o el cobre, que tienen puntos de fusión más bajos y son propensos a cambiar de forma si no se manejan adecuadamente.
El control de calidad es un aspecto esencial en las formadoras de tubos, especialmente cuando se producen grandes volúmenes de productos. Las máquinas más avanzadas integran inspección en línea que utiliza sensores ópticos o sistemas de visión artificial para detectar defectos en la superficie del tubo, tales como arrugas, abolladuras o grietas. Estos sistemas permiten a los operadores ajustar los parámetros de la máquina en tiempo real para corregir cualquier problema antes de que el tubo salga de la línea de producción. En algunos casos, los sistemas de inteligencia artificial pueden incluso anticipar problemas en el proceso y hacer recomendaciones automáticas para ajustes en las condiciones de operación.
Otro avance significativo es la mejora en los sistemas de manejo automatizado. Las formadoras de tubos pueden estar equipadas con robots industriales que cargan y descargan los tubos, eliminando la necesidad de intervención manual. Esto no solo reduce los riesgos para los trabajadores, sino que también aumenta la velocidad y la precisión de la operación. Los robots pueden seguir una secuencia programada de pasos que optimiza la producción y asegura que cada tubo se forme de acuerdo con las especificaciones exactas.
La flexibilidad también ha mejorado en las formadoras de tubos, lo que permite una producción más personalizada y adaptada a las demandas del cliente. Gracias a los avances en la tecnología CNC, las máquinas ahora pueden realizar una variedad de operaciones sin necesidad de realizar ajustes mecánicos significativos. Esto incluye desde el cambio de los diámetros de los tubos hasta la creación de formas más complejas o transiciones suaves entre diferentes diámetros en un solo tubo, lo que es común en aplicaciones de tuberías para fluidos o tuberías estructurales.
La sostenibilidad también juega un papel cada vez más importante en el diseño y la operación de las formadoras de tubos. Las máquinas están optimizando el uso de la energía y reduciendo el desperdicio de material. Algunos modelos emplean tecnologías de reciclaje de material para recuperar cualquier exceso de metal o desperdicio generado durante el proceso de formación. Además, el uso de motores eléctricos de alta eficiencia y sistemas hidráulicos que consumen menos energía contribuye a una reducción significativa del impacto ambiental en la producción de tubos.
En cuanto a la producción en masa, las formadoras de tubos de última generación permiten ciclos de trabajo más rápidos y mayor capacidad de procesamiento. Los tiempos de cambio entre diferentes tipos de tubos o perfiles se han reducido drásticamente, lo que permite una mayor flexibilidad en las líneas de producción y la capacidad de producir diferentes tipos de productos en un solo turno sin la necesidad de largos períodos de reconfiguración. Esto es especialmente útil en sectores donde las demandas de productos específicos pueden cambiar rápidamente, como en la industria electrónica o la industria de bienes de consumo, donde se necesitan tubos con características específicas en plazos de tiempo muy ajustados.
Finalmente, la innovación en software sigue siendo una parte clave en la mejora de las formadoras de tubos. Los programas de diseño asistido por computadora (CAD) y fabricación asistida por computadora (CAM) se integran de manera más estrecha con las máquinas para permitir un diseño más rápido y un ajuste preciso de las configuraciones de la máquina. Los modelos de simulación también son ahora más avanzados, lo que permite predecir el comportamiento de un tubo durante el proceso de formación antes de que se realice físicamente, reduciendo así el riesgo de defectos y mejorando la calidad general del producto final.
El avance continuo en estas áreas garantiza que las formadoras de tubos no solo sean más rápidas y eficientes, sino también más inteligentes y adaptables a las necesidades de las industrias modernas. Esto abre nuevas posibilidades en términos de diseño de productos, personalización y optimización de procesos, lo que permite que las empresas sean más competitivas en un mercado global que exige una alta calidad y tiempos de entrega reducidos.
A medida que la industria continúa evolucionando, las formadoras de tubos también están adoptando tecnologías emergentes para mantenerse a la vanguardia. Un área en particular que está ganando terreno es la inteligencia artificial (IA), que permite a estas máquinas no solo optimizar sus procesos, sino también adaptarse a cambios en tiempo real de manera autónoma. Gracias al aprendizaje automático, las formadoras pueden detectar patrones y predecir problemas antes de que ocurran, lo que permite realizar ajustes automáticamente para mantener la producción en curso sin necesidad de intervención humana constante.
Las máquinas de formación de tubos inteligentes pueden conectarse a plataformas de la nube, donde los datos generados por los sensores y los sistemas de monitoreo pueden ser analizados y utilizados para ajustes predictivos. Esto permite que las fábricas optimicen sus operaciones no solo dentro de una máquina individual, sino también a lo largo de toda la línea de producción. Además, esta conectividad abre la puerta a la gestión remota, lo que permite a los técnicos supervisar y ajustar las operaciones de la formadora de tubos desde cualquier lugar del mundo, mejorando la eficiencia y reduciendo los tiempos de inactividad.
Las tecnologías de simulación avanzada están jugando un papel cada vez más importante. Las simulaciones 3D y de análisis de elementos finitos (FEA) permiten prever cómo se comportará el material durante el proceso de formación antes de que este se lleve a cabo. Esto es crucial cuando se trabaja con materiales más difíciles de procesar, como acero inoxidable o aleaciones de alta resistencia. Al simular el proceso de formación, los ingenieros pueden ajustar los parámetros de la máquina para evitar defectos o deformaciones no deseadas, garantizando una producción más eficiente y menos costosa.
El avance en el control de calidad automatizado también está permitiendo que las máquinas de formación de tubos se deshagan de la inspección manual. Los sistemas de visión artificial pueden detectar imperfecciones en los tubos a medida que se producen, analizando incluso características microscópicas que pueden ser pasadas por alto por los operadores humanos. Estos sistemas pueden verificar la alineación, el diámetro, el espesor de pared y la forma del tubo en tiempo real, lo que asegura que los productos que salen de la máquina cumplen con los estándares de calidad más altos.
Además, la incorporación de tecnologías de fabricación aditiva (impresión 3D) está abriendo nuevas posibilidades para la producción de componentes personalizados de formación de tubos. Por ejemplo, los moldes y matrices que antes requerían largos plazos de fabricación pueden ahora ser creados con precisión mediante impresoras 3D, lo que reduce significativamente los tiempos de desarrollo y permite realizar ajustes rápidos a las especificaciones del cliente sin necesidad de fabricar nuevas piezas físicas.
Las máquinas de formación de tubos modulares continúan ganando popularidad, permitiendo a los fabricantes agregar o modificar módulos según las necesidades cambiantes de producción. Este diseño modular no solo mejora la flexibilidad de la producción, sino que también permite una personalización más rápida, lo que es especialmente valioso en industrias que requieren productos de tubos con especificaciones únicas, como en la industria aeroespacial o en la fabricación de equipos médicos, donde los requisitos precisos de cada tubo son esenciales para el funcionamiento del producto final.
En términos de eficiencia energética, las formadoras de tubos están implementando sistemas de recuperación de calor y optimización energética, lo que contribuye a reducir el consumo general de energía durante la operación. Al integrar tecnologías de variación de velocidad y motores de alta eficiencia, las máquinas no solo funcionan de manera más económica, sino que también tienen un menor impacto ambiental, alineándose con las tendencias globales hacia la sostenibilidad.
En cuanto a la seguridad, las máquinas modernas están incorporando más características automatizadas y remotas que ayudan a reducir el riesgo para los operadores. Las cámaras de seguridad y los sensores de proximidad aseguran que las máquinas detengan su operación si detectan una intervención humana no deseada en el área de trabajo. Esta mejora en la seguridad es particularmente valiosa en entornos de producción de alto ritmo, donde las máquinas están operando a altas velocidades y los márgenes de error son muy pequeños.
Finalmente, la adopción de métodos de producción más ecológicos está impulsando la evolución de las formadoras de tubos. Además de reducir el desperdicio de material, las formadoras de tubos están comenzando a integrar tecnologías de bajo consumo que permiten la producción de tubos reciclados y la utilización de materiales reciclados sin comprometer la calidad del producto final. La fabricación de tubos con materiales reciclados está siendo cada vez más demandada por sectores como la construcción y la automoción, que buscan mejorar su sostenibilidad sin sacrificar el rendimiento.
Con estos avances tecnológicos, las formadoras de tubos están mejor posicionadas para enfrentar los desafíos de una industria en constante cambio, mejorando la eficiencia, la flexibilidad y la calidad de los productos. A medida que la tecnología continúa avanzando, es probable que veamos aún más innovaciones en la forma en que se diseñan, fabrican y operan estas máquinas, haciendo que la producción de tubos sea más rápida, precisa y sostenible que nunca.
Equipos de doblado de tubos

Los equipos de doblado de tubos son máquinas diseñadas para curvar tubos metálicos y otros materiales en ángulos específicos sin comprometer la integridad estructural del material. Estos equipos son fundamentales en diversas industrias, como la automotriz, la construcción, la fabricación de maquinaria, la industria de las tuberías, y muchas más. Dependiendo de la aplicación, los equipos de doblado de tubos pueden ser de diferentes tipos y capacidades, con tecnologías que permiten lograr precisión, eficiencia y flexibilidad en los procesos de producción.
Tipos de Equipos de Doblado de Tubos
- Dobladoras de tubos manuales:
Son las más básicas y requieren que el operador aplique la fuerza necesaria para doblar el tubo. Están diseñadas principalmente para trabajos pequeños o donde se requiere menos volumen de producción. Estas máquinas tienen un conjunto de rodillos o matrices que guían el tubo para darle la forma deseada. A menudo son utilizadas para trabajos más sencillos o de menor escala. - Dobladoras de tubos hidráulicas:
Este tipo de máquina utiliza la presión hidráulica para doblar el tubo, lo que permite realizar curvas con mayor precisión y fuerza. Son más comunes en la fabricación de piezas más grandes y más complejas, ya que pueden manejar tubos de mayor diámetro y espesor. Las dobladoras hidráulicas permiten un control más fino del proceso de doblado y son aptas para trabajos de mayor volumen. - Dobladoras de tubos electrónicas o CNC:
Las máquinas de doblado de tubos con control numérico computarizado (CNC) son las más avanzadas. Permiten un control total sobre los ángulos de doblado, las longitudes y las velocidades de los procesos. Estas máquinas están equipadas con pantallas táctiles y software que permite al operador programar y ejecutar una serie de procesos de doblado sin intervención manual. Gracias a la automatización, pueden trabajar con precisión en procesos repetitivos, lo que mejora la consistencia y reduce el margen de error. - Dobladoras de tubos de radio corto:
Están diseñadas para realizar doblados de tubos con radios más pequeños. Este tipo de equipo es fundamental cuando se requiere que los tubos se curven en espacios reducidos, como en sistemas de tuberías complejas o en el diseño de estructuras donde el espacio es limitado. Aunque requieren un control más riguroso para evitar el aplastamiento del material, las dobladoras de radio corto son muy útiles en aplicaciones que demandan tuberías de alta precisión. - Dobladoras de tubos de mandril:
En este caso, se inserta un mandril o barra de soporte dentro del tubo durante el proceso de doblado. Este mandril mantiene la forma del tubo mientras se dobla, evitando deformaciones como arrugas o aplastamientos. Este tipo de máquina es ideal para tubos de materiales más frágiles, como el aluminio o el cobre, donde se requiere mantener la integridad del diámetro interno durante el doblado. - Dobladoras de tubos por presión rotativa:
Utilizan un sistema de presión rotativa en lugar de una matriz fija. Esta tecnología es útil cuando se requiere un doblado preciso y sin marcas visibles en la superficie del tubo. La presión rotativa genera menos tensión en el material, lo que es crucial cuando se trabajan con materiales delicados o de alta calidad, como los tubos utilizados en la industria aeroespacial.
Componentes Claves de los Equipos de Doblado de Tubos
- Rodillos o Mandriles:
Son las herramientas que guían el tubo durante el proceso de doblado. Los mandriles son especialmente importantes en los equipos de doblado de tubos de mandril, ya que ayudan a mantener la forma interna del tubo. - Matrices de Doblado:
Las matrices o moldes son las formas en las que el tubo se introduce para darle la curvatura deseada. Estas pueden ser intercambiables para crear diferentes tipos de curvas, como curvas de radio grande, radio corto o curvas de ángulo recto. - Sistema Hidráulico o Neumático:
Muchos de los equipos de doblado de tubos usan sistemas hidráulicos o neumáticos para proporcionar la presión necesaria para realizar el doblado. Los sistemas hidráulicos son más comunes en máquinas de mayor tamaño debido a su capacidad para generar gran fuerza. - Control Numérico (CNC):
Las máquinas de doblado más modernas vienen equipadas con tecnología CNC para programar de forma precisa los ángulos de doblado y las dimensiones de las piezas. Esto garantiza una mayor repetibilidad y control, lo que es crucial cuando se producen grandes volúmenes de tubos con formas complejas. - Sistema de Alimentación:
Algunas dobladoras de tubos tienen un sistema automatizado de alimentación de material, lo que facilita el proceso de introducción de tubos en la máquina. Esto es especialmente útil en las fábricas de alta producción, donde el tiempo de configuración y la eficiencia son clave.
Aplicaciones de los Equipos de Doblado de Tubos
Los equipos de doblado de tubos tienen aplicaciones en diversas industrias. Algunas de las más destacadas incluyen:
- Industria Automotriz:
Se utilizan para doblar tubos que forman parte de sistemas de escape, estructuras de chasis, y otras partes críticas del vehículo. - Industria Aeroespacial:
Los tubos que se utilizan en sistemas hidráulicos y sistemas de combustible a menudo requieren doblados de alta precisión sin afectar su resistencia o estructura interna. - Construcción:
En el sector de la construcción, los tubos doblados se utilizan para estructuras de soporte, sistemas de tuberías de agua, calefacción, y gas. - Fabricación de Mobiliario Metálico:
Los tubos doblados son comunes en la fabricación de muebles metálicos, como sillas, mesas, y estanterías, donde la estética y la funcionalidad son esenciales. - Industria de la Energía:
En las plantas de energía, los sistemas de tuberías para el transporte de fluidos y gases a menudo requieren doblados de tubos, tanto en el interior como en el exterior de las instalaciones. - Industria de Equipos Médicos:
Los tubos doblados también son fundamentales en la fabricación de equipos médicos, como catéteres, tubos para equipos de diálisis, y otros dispositivos que requieren curvas precisas y controladas.
Innovaciones y Tendencias
La automatización y la robotización están siendo cada vez más integradas en los equipos de doblado de tubos, lo que permite una mayor precisión, velocidad y flexibilidad en las líneas de producción. La conectividad también juega un papel crucial, ya que las máquinas modernas pueden estar conectadas a sistemas de monitoreo y control remoto, lo que facilita el diagnóstico y mantenimiento predictivo. Las tecnologías como el Internet de las Cosas (IoT) permiten a los fabricantes recopilar datos sobre el rendimiento de la máquina y optimizar los procesos de doblado en tiempo real.
Además, el uso de materiales más ligeros y tubos más delgados está llevando a un mayor enfoque en la mejora de la precisión en los procesos de doblado. Esto está impulsando el desarrollo de equipos de doblado más avanzados que pueden manejar estos materiales sin comprometer la calidad del producto final.
En resumen, los equipos de doblado de tubos son esenciales para una amplia gama de aplicaciones industriales, y su evolución continúa llevando la precisión, eficiencia y automatización a nuevos niveles. Con avances como el control CNC, la automatización y el monitoreo en tiempo real, estas máquinas están mejorando la calidad de los productos y reduciendo los tiempos de producción.
Los equipos de doblado de tubos están evolucionando rápidamente gracias a la adopción de nuevas tecnologías que mejoran su capacidad, precisión y eficiencia. Estos avances permiten que las máquinas manejen tubos de materiales más complejos y en aplicaciones más exigentes. Por ejemplo, el uso de inteligencia artificial (IA) está facilitando el diseño de programas de doblado más inteligentes que se ajustan automáticamente según el tipo de material y las especificaciones del tubo, mejorando la consistencia y la precisión en el proceso.
La capacidad de automonitorización también está aumentando, lo que significa que los equipos pueden realizar autodiagnósticos, enviando alertas cuando los componentes están cerca de fallar o necesitan mantenimiento. Esto no solo reduce el tiempo de inactividad, sino que también permite realizar mantenimiento preventivo antes de que los problemas afecten la producción. El monitoreo remoto también es cada vez más común, permitiendo que los técnicos y operadores supervisen el rendimiento de las máquinas en tiempo real desde cualquier lugar.
Además, las máquinas de doblado de tubos están integrando más tecnologías de visión artificial para el control de calidad en línea. Estos sistemas pueden identificar defectos como arrugas, pliegues o alteraciones en la geometría del tubo durante el proceso de doblado, lo que permite corregir problemas de inmediato, asegurando que los productos finales cumplan con los estándares de calidad más estrictos. La visualización en 3D de los resultados de doblado también está ayudando a los diseñadores a prever posibles problemas antes de que se inicie la producción, lo que ahorra tiempo y recursos.
La sostenibilidad es otro aspecto clave que está impulsando la evolución de los equipos de doblado de tubos. Los avances en los sistemas de reciclaje de material y reducción de residuos permiten una mayor eficiencia en la utilización de los recursos, minimizando el impacto ambiental de la producción. Muchas de las máquinas modernas están diseñadas para ser más eficientes en el uso de energía, utilizando motores de alta eficiencia y tecnologías de recuperación de calor, lo que ayuda a reducir el consumo general de electricidad.
Las mejoras en la automatización también están optimizando el uso del tiempo y los recursos. El robotizado de las líneas de producción facilita el manejo de los tubos y el ensamblaje de las piezas dobladas sin intervención manual. Esto no solo mejora la seguridad al reducir la exposición de los trabajadores a máquinas en movimiento, sino que también aumenta la capacidad de producción al eliminar los cuellos de botella en las fases de carga y descarga.
En términos de flexibilidad, los equipos de doblado de tubos actuales pueden manejar una gama mucho más amplia de materiales y tamaños de tubos. Esto permite a las fábricas adaptarse rápidamente a las necesidades del cliente sin necesidad de reconfiguraciones costosas o largas. Las máquinas también pueden ser fácilmente adaptadas para realizar doblados de tubos de formas no convencionales, lo que es crucial en industrias que requieren productos personalizados, como la automotriz o la aeroespacial.
El software avanzado sigue desempeñando un papel crucial en la optimización de los procesos de doblado de tubos. El uso de programas CAD/CAM permite a los diseñadores crear y modificar fácilmente los diseños de doblado, lo que se traduce en tiempos de respuesta más rápidos y una mayor capacidad para ajustarse a las especificaciones de cada cliente. La integración de estas plataformas con los sistemas de control CNC asegura que las máquinas realicen los movimientos necesarios con una precisión milimétrica.
Los avances en materiales también están impulsando el diseño de nuevos equipos de doblado. Los tubos fabricados con materiales compuestos o aleaciones avanzadas pueden requerir técnicas de doblado específicas que no eran necesarias para metales más comunes. Por ejemplo, los tubos de fibra de carbono o de titanio pueden ser más frágiles o sensibles al calor, por lo que se requieren máquinas con sistemas de control de temperatura más avanzados para evitar daños durante el proceso.
La adaptabilidad de los equipos de doblado de tubos ha mejorado con la introducción de módulos intercambiables que permiten a los usuarios modificar la máquina según sus necesidades. Esto facilita el cambio de tipo de trabajo entre lotes pequeños y grandes, sin perder eficiencia en ninguno de los dos casos. Los operadores pueden ajustar fácilmente las configuraciones para realizar trabajos más complejos o cambiar de material sin la necesidad de largas paradas en la producción.
El uso de tecnologías de visualización aumentada y realidad virtual (VR) también está siendo explorado como parte de la capacitación y la programación de máquinas. Los operadores pueden ahora ser entrenados en un entorno virtual, lo que les permite familiarizarse con la máquina y su funcionamiento antes de trabajar con la versión real. Esta forma de capacitación puede reducir significativamente los errores operativos y mejorar la eficiencia de los operadores.
A medida que las empresas buscan ser más competitivas y sostenibles, los equipos de doblado de tubos continúan siendo una parte fundamental de la producción en sectores industriales clave. La constante innovación en estas máquinas no solo permite procesos más rápidos y precisos, sino que también abre nuevas posibilidades para diseñar productos complejos y personalizados que son esenciales para diversas aplicaciones, desde la fabricación de automóviles hasta la construcción de sistemas de tuberías industriales.
El futuro de los equipos de doblado de tubos parece cada vez más centrado en la inteligencia artificial (IA) y el aprendizaje automático. Con la implementación de estos sistemas, los equipos no solo se optimizan en tiempo real para mejorar la eficiencia, sino que también pueden predecir fallos antes de que ocurran, lo que ayuda a reducir el tiempo de inactividad y mejora la fiabilidad general de las máquinas. La capacidad de los equipos de doblado para aprender de datos históricos y ajustarse automáticamente a las condiciones cambiantes de los materiales, como la temperatura o la humedad, está llevando la precisión y la flexibilidad a niveles sin precedentes. Esta capacidad adaptativa está también permitiendo a los sistemas realizar un análisis predictivo, anticipando la necesidad de mantenimiento y evitando reparaciones costosas.
Aparte de la automatización inteligente, la interconectividad de los equipos mediante plataformas de la nube está abriendo un abanico de posibilidades en la gestión y el monitoreo de la producción. Al integrar sistemas de Internet de las Cosas (IoT), los equipos de doblado de tubos pueden conectarse a una red que permite recopilar datos en tiempo real, como la presión, la temperatura y la velocidad de operación. Estos datos pueden ser procesados para optimizar el rendimiento y hacer ajustes sobre la marcha sin la intervención de los operadores. Además, esta interconexión facilita la supervisión remota de la producción, lo que aumenta la capacidad de los equipos para ser gestionados de manera centralizada desde una ubicación distinta a la fábrica.
Las máquinas de doblado de tubos también están siendo cada vez más eco-amigables, con un enfoque hacia la reducción de residuos y el uso eficiente de la energía. La presión sobre la sostenibilidad está impulsando el diseño de equipos más eficientes energéticamente, con sistemas mejorados de recuperación de calor y motores de bajo consumo. Esto no solo reduce los costos operativos, sino que también cumple con las normativas ambientales cada vez más estrictas. Además, algunas máquinas están incorporando técnicas de reciclaje de materiales para permitir la reutilización de desechos generados durante el proceso de doblado, minimizando los desperdicios y favoreciendo un ciclo de producción más limpio.
Los materiales inteligentes y composites también están influyendo en el diseño y la fabricación de equipos de doblado. Los tubos fabricados con materiales como acero de alta resistencia, aleaciones ligeras o materiales compuestos requieren enfoques más innovadores para garantizar que el proceso de doblado no los degrade. Para ello, las máquinas de doblado están siendo equipadas con sensores de alta precisión y tecnologías de control de temperatura que permiten adaptar la presión y la fuerza de doblado en tiempo real según el tipo de material. Esto no solo mejora la calidad del tubo doblado, sino que también permite que estos materiales más complejos sean procesados de manera eficiente.
Otra tendencia en el desarrollo de los equipos de doblado de tubos es la fabricación modular. Esta tendencia está permitiendo a las empresas personalizar sus equipos según las necesidades de producción específicas. Al tener equipos modulares, los usuarios pueden agregar o quitar componentes como rodillos, matrices y sistemas de control, permitiendo un ajuste más preciso para diferentes tipos de trabajos y materiales sin la necesidad de adquirir una nueva máquina completa. La capacidad de adaptación de estos sistemas permite que las fábricas mantengan una alta flexibilidad en su línea de producción, lo que es especialmente útil cuando se manejan volúmenes pequeños o productos con especificaciones únicas.
A medida que las exigencias del mercado aumentan, también lo hace la necesidad de precisión y calidad en la producción de tubos. Los sistemas de doblado de tubos de alta precisión se están beneficiando enormemente de avances en la tecnología de medición en tiempo real. Estas máquinas ahora cuentan con sensores de alta resolución que pueden medir el ángulo y la forma del tubo a medida que se dobla, lo que permite detectar y corregir desviaciones mínimas antes de que el producto final esté completo. Esto no solo mejora la calidad, sino que también reduce los costos al evitar la necesidad de realizar reprocesamientos o desechar productos defectuosos.
La virtualización y la simulación digital también están jugando un papel crucial en el diseño y la optimización de los procesos de doblado. A través de simulaciones de flujo de material y modelos 3D de los tubos, los diseñadores pueden prever cómo se comportará el material durante el proceso de doblado, lo que ayuda a planificar con precisión las configuraciones y a identificar posibles problemas antes de que ocurran en la producción real. Las simulaciones de la deformación y análisis de tensiones permiten realizar ajustes precisos para evitar defectos de material, como arrugas o pandeos, y garantizar que los tubos mantengan su resistencia estructural.
Además, los sistemas de gestión de la producción que integran estos equipos de doblado de tubos están convirtiéndose en herramientas poderosas para la planificación y control de la producción. Estos sistemas no solo optimizan el flujo de trabajo entre las diferentes máquinas, sino que también permiten gestionar inventarios, programar mantenimiento preventivo y gestionar las necesidades de los operarios, lo que mejora significativamente la productividad global.
En conclusión, los equipos de doblado de tubos están avanzando a pasos agigantados, impulsados por innovaciones tecnológicas como la automatización, el control remoto, el análisis de datos en tiempo real y el uso de materiales más complejos. La integración de inteligencia artificial, IoT, sostenibilidad y sistemas modulares está permitiendo a las fábricas ser más eficientes, precisas y flexibles. Estas tendencias no solo mejoran la calidad de los productos, sino que también optimizan los procesos de producción, reducen costos y permiten una mayor adaptabilidad a las demandas cambiantes del mercado. A medida que la tecnología continúa evolucionando, es probable que estos equipos sigan mejorando, abriendo nuevas posibilidades para la fabricación de productos cada vez más complejos y personalizados.
Herramienta de curvado de caños
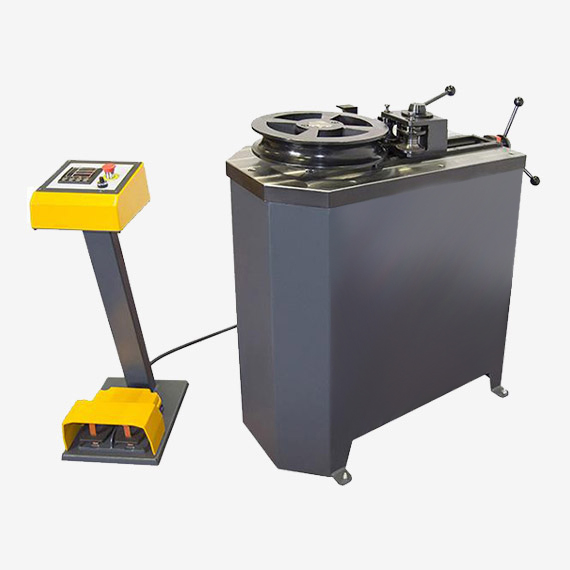
Una herramienta de curvado de caños es un dispositivo diseñado específicamente para doblar o curvar tubos o caños, generalmente fabricados en materiales como acero, aluminio, cobre, PVC o acero inoxidable. Estas herramientas permiten que los caños mantengan su integridad estructural durante el proceso de curvado, evitando deformaciones indeseadas como arrugas, aplastamientos o grietas. El curvado de caños se utiliza en diversas industrias, como la construcción, la automotriz, la de gas y petróleo, la energética y la fabricación de equipos, entre otras.
Existen varias herramientas de curvado que se utilizan dependiendo del tipo de material, el tamaño del caño y la aplicación específica. Estas herramientas varían en complejidad, desde herramientas manuales simples hasta sistemas automatizados de alta tecnología. Aquí se detallan algunos de los tipos más comunes de herramientas de curvado de caños:
Tipos de Herramientas de Curvado de Caños
- Curvadora manual de caños:
Son herramientas más simples que requieren de la intervención del operador para doblar el caño a mano. Estas herramientas suelen estar compuestas por un molde o rodillos que guían el caño mientras el operador aplica la fuerza necesaria para darle la curva deseada. Son adecuadas para trabajos de bajo volumen y cuando se necesitan solo un par de doblados. - Curvadora de caños hidráulica:
Utiliza la presión hidráulica para doblar el caño, lo que permite aplicar una fuerza mucho mayor que en las curvadoras manuales. Estas máquinas son capaces de doblar caños de mayor tamaño y de materiales más resistentes. Son más rápidas y precisas, lo que las hace ideales para producciones de mayor volumen. Además, el uso de un sistema hidráulico permite controlar con mayor precisión el ángulo y la forma del doblado, lo que es útil para piezas más complejas o de mayor tamaño. - Curvadora de caños por rodillos:
Esta herramienta utiliza un sistema de rodillos para guiar el caño a través de una serie de formas que lo curvan progresivamente. En lugar de aplicar una sola presión sobre el caño, los rodillos aplican una presión gradual, lo que reduce las posibilidades de que el caño se dañe. Las curvadoras por rodillos son bastante versátiles y se pueden ajustar para trabajar con diferentes tamaños de caños. - Curvadora de caños CNC (Control Numérico Computarizado):
Las curvadoras CNC son máquinas avanzadas que permiten a los operadores programar los parámetros de curvado, como el radio de curvatura, el ángulo y la longitud del caño, con una precisión extremadamente alta. Estas herramientas están equipadas con pantallas táctiles y software de programación, lo que permite realizar curvas complejas de manera automática y repetitiva. Son perfectas para trabajos de alta producción, donde se requiere un control preciso y una alta calidad de los productos. - Curvadora de caños de mandril:
En este tipo de curvadora se utiliza un mandril que se inserta en el interior del caño mientras se dobla. Esto evita que el caño se deforme o se aplaste durante el proceso de curvado. El mandril ayuda a mantener la forma del caño, especialmente cuando se trabaja con materiales más delicados, como el cobre o el aluminio. Este tipo de herramienta es muy útil cuando se necesitan curvas con un radio pequeño. - Curvadora de caños por presión rotativa:
Utiliza un sistema de presión rotativa que aplica una presión constante mientras el caño es girado. Esto reduce las tensiones en el material y permite obtener curvas suaves sin marcas. Las curvadoras de presión rotativa son especialmente útiles cuando se trabaja con materiales que pueden ser sensibles a las marcas o a las deformaciones, como los tubos de acero inoxidable.
Características y Componentes Comunes
- Rodillos de curvado:
La mayoría de las curvadoras de caños incluyen rodillos que guían el tubo durante el proceso de curvado. Los rodillos pueden ser ajustables para controlar la forma del doblado y permitir diferentes tipos de curvas. Los rodillos también pueden ser de diferentes materiales, dependiendo del tipo de caño que se está trabajando. - Molde o matriz:
Es el componente que define el radio y la forma de la curva. En las curvadoras manuales y en algunos modelos hidráulicos, la matriz es donde el caño se introduce para recibir la forma deseada. La matriz se adapta al tamaño y al tipo de tubo, y se puede cambiar para curvar diferentes diámetros de caños. - Mandril:
En las curvadoras de caños de mandril, este componente se inserta en el interior del caño durante el curvado. Su función es evitar que el tubo se deforme internamente y mantener su estructura interna intacta mientras se realiza el doblado. Los mandriles están disponibles en diferentes tamaños, dependiendo del diámetro del caño que se esté trabajando. - Sistema hidráulico o mecánico:
Dependiendo del tipo de curvadora, la máquina puede utilizar un sistema hidráulico, neumático o mecánico para generar la fuerza necesaria para doblar el caño. Los sistemas hidráulicos, en particular, ofrecen la ventaja de generar una fuerza considerable sin la necesidad de aplicar una gran cantidad de esfuerzo manual. - Control digital (en máquinas CNC):
Las curvadoras de caños más avanzadas están equipadas con sistemas de control numérico (CNC), que permiten al operador ingresar parámetros precisos de doblado, como el radio, el ángulo y el número de curvas. Los sistemas CNC también permiten la programación de procesos repetitivos, lo que mejora la eficiencia y reduce el margen de error.
Aplicaciones de las Herramientas de Curvado de Caños
Las herramientas de curvado de caños tienen múltiples aplicaciones en diferentes industrias. Algunos ejemplos incluyen:
- Industria de la construcción: Las curvadoras de caños se utilizan para crear estructuras metálicas, barandillas, columnas, sistemas de tuberías y conductos.
- Automotriz: En la fabricación de sistemas de escape y chasis, donde se requiere doblar caños de acero o aluminio.
- Sistemas de fontanería: Para doblar tubos de cobre o PVC que se usan en sistemas de agua y gas.
- Fabricación de maquinaria: En la producción de equipos y maquinaria que requieren tubos doblados para conexiones hidráulicas o estructuras.
- Industrias energética y petroquímica: Para la fabricación de sistemas de tuberías que transportan gas, agua o petróleo.
Conclusión
Las herramientas de curvado de caños son esenciales en la fabricación y construcción de una amplia variedad de productos y estructuras. Desde curvadoras manuales simples hasta máquinas CNC avanzadas, estas herramientas permiten un control preciso sobre el proceso de curvado, asegurando que los caños mantengan su integridad y cumplan con los estándares de calidad requeridos en diversas aplicaciones industriales. El avance hacia máquinas más automatizadas y eficientes está mejorando la productividad, reduciendo los costos de producción y ampliando las capacidades de diseño en muchas industrias.
Las herramientas de curvado de caños continúan evolucionando para adaptarse a las necesidades cada vez más complejas de las industrias modernas. Con la incorporación de tecnología avanzada, como sensores de precisión, controladores digitales y software inteligente, estos equipos permiten realizar curvados con una exactitud milimétrica y una repetibilidad excepcional. Los avances en tecnologías hidráulicas y neumáticas han permitido aumentar la fuerza disponible para doblar caños de mayor grosor y resistencia, mientras que los sistemas automáticos de carga y descarga optimizan el tiempo de producción, eliminando la intervención manual y mejorando la seguridad.
El uso de herramientas de curvado cada vez más personalizadas ha permitido que las empresas optimicen su producción al poder ajustar rápidamente las máquinas a diferentes tamaños de caños, materiales y formas de curvado. Esto es particularmente útil en aplicaciones que requieren caños doblados de manera no convencional, como en la fabricación de estructuras complejas o componentes automotrices donde las dimensiones precisas y las curvas exactas son fundamentales para el rendimiento del producto final.
Además, la integración de sistemas CNC (Control Numérico Computarizado) permite la programación avanzada de los procesos de curvado, lo que proporciona una mayor precisión, eficiencia y control sobre cada doblado. Los operarios pueden programar un conjunto de parámetros y luego dejar que la máquina ejecute las tareas de forma autónoma, lo que reduce significativamente el riesgo de errores humanos y mejora la calidad del producto final. La inteligencia artificial (IA), al estar integrada en estos sistemas, permite a las máquinas aprender y adaptarse a los cambios en los materiales, ajustando automáticamente los parámetros de doblado para optimizar el proceso y evitar posibles fallos.
Otro avance clave en la curvadora de caños es la reducción de residuos y mejora de la eficiencia. Las máquinas de curvado modernas están diseñadas para minimizar el desperdicio de material durante el proceso, lo que resulta en menores costos de producción y menos impacto ambiental. Las técnicas de curvado por mandril y las curvadoras de rodillos permiten que el material se deforme de manera más controlada, evitando que se produzcan arrugas o tensiones innecesarias en el tubo, lo que, a su vez, mejora la durabilidad y calidad de los tubos doblados. Además, la recuperación de energía en algunas máquinas, que convierte la energía generada durante el proceso de doblado en energía utilizable, está ayudando a reducir aún más el consumo energético.
Las herramientas de curvado de caños no solo se limitan a la producción de componentes estáticos. La tendencia hacia la personalización masiva y la fabricación a medida ha impulsado la demanda de sistemas capaces de producir tubos con curvas específicas adaptadas a necesidades individuales. Esto es crucial en sectores como la industria aeroespacial o la automotriz, donde los tubos deben cumplir con especificaciones rigurosas y cumplir con estándares de seguridad estrictos. Las máquinas de curvado también están cada vez más preparadas para manejar materiales compuestos avanzados, como fibra de carbono y aleaciones especiales, lo que amplía aún más las posibilidades de aplicación de estas herramientas en campos de alta tecnología.
El uso de sistemas de monitoreo y análisis de datos en tiempo real está permitiendo a los operadores ajustar los parámetros y controlar el proceso de curvado a distancia, asegurando que las máquinas operen de manera eficiente y sin problemas. Esta recopilación de datos también permite realizar un mantenimiento predictivo, lo que significa que los problemas pueden ser detectados antes de que afecten la producción, reduciendo el tiempo de inactividad y los costos operativos.
La combinación de tecnologías avanzadas, la mejora continua en automatización y la creciente demanda de personalización han convertido a las herramientas de curvado de caños en componentes fundamentales en muchos sectores industriales. Con un enfoque continuo en la sostenibilidad, la precisión y la eficiencia, estas máquinas seguirán desempeñando un papel crucial en la fabricación de productos que requieren tubos doblados, proporcionando soluciones más rápidas, precisas y económicas para una amplia variedad de aplicaciones.
El futuro del curvado de caños está marcado por una continua evolución tecnológica, donde la inteligencia artificial y el Internet de las Cosas (IoT) están desempeñando un papel crucial en la automatización y optimización de los procesos. Los sistemas de curvado de caños cada vez se integran más con plataformas smart factory, que permiten a las máquinas comunicarse entre sí y con los sistemas de gestión de la producción. Esta interconexión permite una supervisión y control en tiempo real, facilitando la detección de errores, el ajuste automático de parámetros y la predicción de fallos antes de que ocurran, lo que resulta en una mayor fiabilidad y una reducción de costos operativos.
Con el auge de la fabricación avanzada, las máquinas de curvado de caños se están volviendo más modulares y adaptables, lo que permite a los fabricantes configurar sus equipos según las necesidades específicas de la producción. La personalización no solo se limita a la geometría de los tubos, sino que también se extiende a las capacidades de las máquinas para adaptarse a diferentes tipos de materiales, tamaños y volúmenes de producción. Esto hace que las máquinas sean más versátiles, lo que resulta ideal en industrias que exigen productos con características únicas o pequeñas series de producción.
Además, el diseño de materiales está avanzando hacia nuevos compuestos que permiten una mayor flexibilidad y resistencia en los tubos. Materiales como los tubos de aleaciones especiales, fibra de carbono y plásticos de ingeniería son cada vez más comunes, lo que requiere que las herramientas de curvado se adapten a las propiedades particulares de estos materiales. Las máquinas de curvado de caños están siendo diseñadas para manejar estos nuevos materiales, utilizando sensores avanzados para ajustar dinámicamente la presión y la velocidad de curvado, lo que asegura la integridad estructural del tubo a lo largo de su vida útil.
La sostenibilidad también está tomando un rol más destacado en el diseño de estas herramientas. Las empresas están buscando maneras de reducir el impacto ambiental de la fabricación, y eso incluye el uso eficiente de los recursos. Los sistemas de curvado de caños están incorporando tecnologías como el reciclaje de materiales sobrantes, la reducción de emisiones y la optimización de la energía durante el proceso de producción. Además, el diseño eficiente de las máquinas permite disminuir el consumo de energía, lo que no solo reduce costos operativos, sino que también contribuye a alcanzar los objetivos ambientales de las empresas.
En términos de capacidad de procesamiento, las máquinas de curvado de caños están alcanzando nuevos límites. La incorporación de velocidades más altas y procesos más rápidos ha permitido a los fabricantes producir tubos curvados en menores tiempos, aumentando así la capacidad de producción sin sacrificar la calidad. Estos avances permiten a las empresas responder más rápidamente a las demandas del mercado, especialmente en sectores que requieren tiempos de entrega rápidos, como la industria automotriz o la fabricación de maquinaria de precisión.
El mantenimiento predictivo es otro de los avances clave en el futuro de las herramientas de curvado de caños. Utilizando sensores IoT y algoritmos de inteligencia artificial, las máquinas pueden predecir posibles fallos o necesidades de mantenimiento antes de que afecten la producción. Esto no solo reduce el tiempo de inactividad, sino que también mejora la longevidad de las máquinas, optimiza los costos de mantenimiento y asegura una producción continua y sin interrupciones. Los operarios pueden recibir notificaciones en tiempo real sobre el estado de la máquina, lo que les permite tomar medidas proactivas para evitar problemas.
Además, con el progreso en las tecnologías de simulación digital, las herramientas de curvado están integrando modelos 3D para predecir cómo se comportará el material durante el proceso de curvado. Esto no solo mejora la precisión de los resultados, sino que también permite a los fabricantes hacer ajustes en tiempo real, sin necesidad de detener la producción para realizar cambios en las configuraciones. Las simulaciones pueden tener en cuenta factores como la temperatura del material, la humedad y otros aspectos que podrían influir en la calidad del doblado.
A medida que avanzan estas tecnologías, también lo hace la capacidad de integración de los sistemas de curvado en el ciclo completo de producción. Estas máquinas ya no operan de manera aislada, sino que se integran en líneas de producción automatizadas, donde las decisiones de curvado se coordinan con otros procesos, como el corte, la soldadura o el ensamblaje. Esto da lugar a sistemas de producción más inteligentes, eficientes y conectados, que pueden ajustarse de manera autónoma a los cambios en la demanda, el tipo de material o los requisitos del cliente.
La incorporación de interfaces de usuario amigables, junto con pantallas táctiles y software intuitivo, también ha mejorado la facilidad de operación de estas máquinas. Los operadores ahora pueden configurar las máquinas de curvado con mayor rapidez y precisión, sin necesidad de tener una formación especializada en programación. Los sistemas de control son cada vez más accesibles, permitiendo a los operarios adaptar las máquinas para diferentes tareas sin necesidad de largos procesos de ajuste manual.
En resumen, el futuro de las herramientas de curvado de caños se perfila como una amalgama de automatización avanzada, inteligencia artificial, sostenibilidad y optimización en tiempo real. Con estos avances, las máquinas no solo se están volviendo más eficientes, sino también más inteligentes, adaptándose rápidamente a las necesidades de producción y mejorando los resultados en términos de calidad y reducción de costos. A medida que las industrias continúan evolucionando, las herramientas de curvado de caños jugarán un papel aún más importante en la creación de productos complejos, precisos y personalizados.
Dobladora industrial
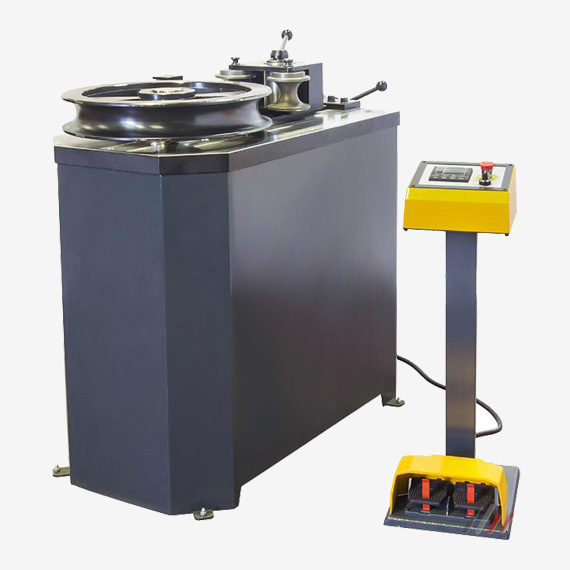
Una dobladora industrial es una máquina utilizada para doblar metales y otros materiales con precisión y eficiencia en ambientes de producción masiva. Estas máquinas son esenciales en una variedad de industrias, como la construcción, automotriz, electrodomésticos, aeroespacial, petróleo y gas, entre otras, donde se requieren piezas con curvaturas específicas, como caños, barras y perfiles metálicos.
Las dobladoras industriales están diseñadas para trabajar con materiales resistentes y de gran tamaño, lo que las hace fundamentales para tareas que involucran grandes volúmenes de producción o materiales pesados. A través de diversas tecnologías, como el control numérico computarizado (CNC) o sistemas hidráulicos, las dobladoras industriales ofrecen un alto grado de precisión, repetibilidad y velocidad, adaptándose a distintos tipos de curvados, radios de doblado y materiales.
Tipos de Dobladoras Industriales
- Dobladora de tubos:
Específicamente diseñada para doblar tubos metálicos de diferentes diámetros y grosores. Estas máquinas pueden ser manuales, hidráulicas o CNC, dependiendo de la capacidad de producción y los requerimientos de precisión. Son comúnmente usadas en la industria automotriz, para sistemas de escape, estructura de vehículos y en sistemas de conducción de fluidos. - Dobladora de barras y perfiles:
Estas máquinas están orientadas a doblar barras (de acero, aluminio, cobre, etc.) y perfiles (como ángulos, canales, vigas, etc.). Se utilizan para estructuras metálicas en la construcción de edificios, puentes, máquinas industriales y más. El sistema hidráulico o de rodillos se usa para controlar el proceso de doblado de acuerdo a la forma deseada. - Dobladora de láminas:
Se utilizan para curvar o doblar lámparas o chapas metálicas. Las dobladoras de láminas son fundamentales en la fabricación de componentes de carrocerías de vehículos, estructuras metálicas de edificios y electrodomésticos. Estas máquinas pueden ser operadas manualmente o mediante control automático, dependiendo de la producción. - Dobladora CNC:
Las dobladoras CNC (control numérico computarizado) ofrecen la máxima precisión y flexibilidad al permitir a los operadores programar de manera digital los ángulos, radios de curvatura, y otros parámetros de doblado. Estas máquinas son especialmente útiles para producciones de alta precisión, donde las tolerancias son estrictas, como en la industria aeroespacial o en la fabricación de componentes electrónicos.
Componentes Principales
- Rodillos y matrices: Son los elementos esenciales que guían y dan forma al material durante el proceso de doblado. Los rodillos son ajustables para adaptarse a diferentes diámetros y radios de curvatura.
- Sistema hidráulico: En muchas dobladoras industriales, especialmente las de alta capacidad, se utilizan sistemas hidráulicos para generar la fuerza necesaria para doblar materiales duros. El sistema hidráulico proporciona una presión constante y controlada para curvar el material sin deformarlo.
- Mandril: En algunas dobladoras, especialmente las de tubos, se utiliza un mandril para sostener el interior del tubo durante el proceso de doblado, evitando que se colapse o se deforme.
- Controladores y software: En las dobladoras CNC, el software permite la programación de la máquina, definiendo los parámetros exactos de curvado. Los sensores pueden usarse para monitorear el proceso en tiempo real y hacer ajustes automáticamente.
Características de las Dobladoras Industriales
- Alta capacidad de carga: Son capaces de doblar materiales de gran grosor y tamaños grandes sin comprometer la calidad del producto final.
- Precisión: Ofrecen altas tolerancias y repetibilidad, lo que permite producir piezas idénticas con mínima variación, clave en sectores que requieren altos estándares de calidad.
- Versatilidad: Son capaces de trabajar con una variedad de materiales, como acero, aluminio, cobre, titanio, plástico, entre otros. También permiten doblar diferentes tipos de perfiles y tubos, adaptándose a las necesidades específicas de cada industria.
- Automatización: Muchas dobladoras industriales están equipadas con sistemas automáticos que controlan el proceso de doblado, desde el inicio hasta el final, reduciendo la intervención humana y aumentando la eficiencia y seguridad.
Aplicaciones de las Dobladoras Industriales
- Industria Automotriz: La fabricación de chasis, sistemas de escape, estructuras internas del vehículo y otros componentes metálicos requiere dobladoras que puedan manejar tubos y perfiles metálicos con precisión.
- Construcción: Las dobladoras industriales se usan para curvar barras de acero que forman parte de la estructura metálica de puentes, edificios, y otras construcciones. También son fundamentales para fabricar elementos de soporte y estructuras metálicas ligeras y pesadas.
- Fabricación de Muebles y Equipos: Las dobladoras son fundamentales en la fabricación de muebles metálicos y en la producción de equipos industriales, donde se requiere doblar tubos y perfiles metálicos de acuerdo a diseños complejos.
- Sistemas de Tuberías: En las industrias de agua, gas y petroquímica, las dobladoras son necesarias para fabricar sistemas de tuberías curvadas que se ajusten a los sistemas de distribución de fluidos.
- Electrodomésticos: Muchas veces, las dobladoras se utilizan para curvar láminas metálicas y otros componentes que forman parte de la estructura interna o externa de electrodomésticos como refrigeradores, lavadoras y microondas.
- Aeroespacial: En la industria aeroespacial, las dobladoras CNC de alta precisión se usan para crear componentes de aviones, fuselajes y otras partes críticas que requieren tolerancias estrictas.
Ventajas de las Dobladoras Industriales
- Mejora la eficiencia de producción, ya que permiten realizar múltiples procesos de doblado de manera continua y rápida.
- Reducción de errores y defectos gracias a las máquinas automatizadas y controles de precisión.
- Mayor durabilidad de las piezas, ya que se utilizan para trabajar con materiales más fuertes y de mayor resistencia.
- Flexibilidad en la producción, ya que muchas de las máquinas pueden adaptarse a distintos materiales, tamaños y configuraciones de doblado.
Conclusión
Las dobladoras industriales son máquinas esenciales para la producción de componentes metálicos en una gran variedad de industrias. Gracias a sus capacidades de precisión, alta carga y versatilidad, se pueden adaptar a diferentes aplicaciones y materiales, desde tubos y perfiles metálicos hasta lámparas de acero o láminas de aluminio. La integración de tecnologías como CNC, automatización y mantenimiento predictivo ha elevado la eficiencia y la precisión de estas máquinas, convirtiéndolas en herramientas indispensables para la producción moderna.
Las dobladoras industriales están en constante evolución, adaptándose a las nuevas demandas del mercado. A medida que las industrias exigen productos más específicos y personalizados, las dobladoras también deben ofrecer una mayor flexibilidad. Las máquinas actuales no solo permiten realizar curvaturas con precisión, sino que también son capaces de realizar múltiples tipos de doblados en un solo proceso, lo que mejora la eficiencia y reduce los tiempos de producción. Además, la integración de la tecnología digital ha transformado la manera en que se operan estas máquinas. El uso de interfaces de pantalla táctil, sensores de alta precisión y sistemas de control avanzado hace que la operación de las dobladoras sea más intuitiva, reduciendo la necesidad de personal especializado y minimizando la posibilidad de errores. Esta digitalización no solo optimiza el proceso, sino que también facilita la planificación de producción al ofrecer a los operadores un acceso rápido a los parámetros de la máquina y a la información de mantenimiento.
La incorporación de inteligencia artificial también ha tenido un impacto importante en la operación de las dobladoras. Algunas máquinas ahora pueden analizar patrones en los procesos de producción y ajustar automáticamente los parámetros para mejorar la calidad del doblado o prevenir defectos. Esto hace que el proceso de doblado sea aún más eficiente, reduciendo el desperdicio de material y aumentando la vida útil de las máquinas, al detectar posibles fallos antes de que ocurran. Además, la automatización no solo acelera la producción, sino que también mejora la seguridad, ya que los operarios tienen menos contacto directo con las máquinas, reduciendo el riesgo de accidentes.
En términos de materiales, las dobladoras industriales son cada vez más capaces de trabajar con materiales complejos y compuestos. A medida que los fabricantes buscan utilizar materiales más ligeros pero fuertes, como el titanio o materiales compuestos, las dobladoras deben ser capaces de adaptarse a sus propiedades específicas. Algunas máquinas incluso están diseñadas para trabajar con materiales reciclados, lo que las convierte en una opción más ecológica para las industrias que buscan cumplir con las normativas medioambientales. La capacidad de manejar diferentes materiales también ha impulsado el desarrollo de dobladoras híbridas, que combinan diferentes tecnologías, como la hidráulica y la neumática, para adaptarse a una variedad de necesidades de curvado.
Por otro lado, el mantenimiento predictivo ha emergido como una herramienta crucial en la mejora de la eficiencia operativa de las dobladoras industriales. A través del uso de sensores IoT (Internet de las Cosas) y algoritmos de análisis de datos, las máquinas pueden monitorear su propio estado y alertar a los operadores sobre posibles fallos antes de que estos ocurran. Esta capacidad de realizar mantenimiento preventivo reduce el tiempo de inactividad y los costos asociados con reparaciones no planificadas, asegurando una producción continua y eficiente.
El uso de simulaciones digitales también está ganando terreno en el diseño y operación de dobladoras industriales. Las simulaciones permiten a los fabricantes modelar el proceso de doblado antes de que se realice físicamente, lo que ayuda a prever posibles problemas y ajustar los parámetros de la máquina para obtener el mejor resultado. Esto es particularmente útil cuando se trabajan con materiales nuevos o diseños complejos, ya que reduce la cantidad de pruebas físicas necesarias, lo que, a su vez, reduce los costos y el tiempo de producción.
En resumen, las dobladoras industriales están evolucionando rápidamente, integrando tecnologías avanzadas que aumentan su precisión, flexibilidad y eficiencia. Desde la automatización y la digitalización hasta el mantenimiento predictivo y la simulación digital, estas máquinas continúan siendo una parte fundamental en la fabricación de componentes metálicos, ofreciendo soluciones más rápidas, seguras y sostenibles para una variedad de aplicaciones industriales.
Las dobladoras industriales también están impulsando la innovación en la producción de componentes más complejos y de alto rendimiento. Con la creciente demanda de productos personalizados, especialmente en sectores como el automotriz y la aeroespacial, las dobladoras deben ser capaces de trabajar con geometrías y diseños más intrincados, garantizando al mismo tiempo que se mantenga la integridad estructural del material. El desarrollo de dobladoras de múltiples ejes es un ejemplo de cómo las máquinas están evolucionando para cumplir con estas exigencias. Estas máquinas permiten realizar curvaturas en diferentes direcciones en una sola operación, lo que abre la puerta a la fabricación de formas más complejas y a la optimización de procesos que anteriormente requerían múltiples etapas.
A la par de estos avances, la capacidad de las dobladoras para integrarse en sistemas más grandes y complejos de producción automatizada está transformando las cadenas de suministro. Las máquinas pueden conectarse a sistemas de gestión de producción inteligente que analizan los datos de la planta y ajustan las operaciones de las dobladoras en tiempo real para mejorar la eficiencia y reducir el consumo de energía. Estas capacidades de automatización total no solo mejoran la velocidad de producción, sino que también permiten a las empresas reaccionar de manera más ágil a cambios en las demandas del mercado o en los requerimientos de los clientes, aumentando la competitividad.
Por otro lado, los avances en la materialización de los equipos también están permitiendo que las dobladoras sean más compactas sin comprometer su capacidad de carga. Las mejoras en los materiales de construcción de las máquinas, como el uso de aleaciones de alta resistencia o composites, están haciendo posible que las dobladoras mantengan su robustez, pero con una huella espacial mucho más pequeña. Esto es especialmente valioso para las empresas que tienen espacio limitado en sus plantas de producción pero aún necesitan maquinaria de alta capacidad.
El futuro también apunta a mejoras en la sostenibilidad de las dobladoras industriales. Con las normativas ambientales cada vez más estrictas, los fabricantes están desarrollando máquinas que no solo son más eficientes en términos de consumo de energía, sino que también minimizan el desperdicio de materiales. Las dobladoras de próxima generación están siendo diseñadas para maximizar la utilización de materiales durante el proceso de doblado, reduciendo al mínimo los recortes y residuos. Esto no solo beneficia al medio ambiente, sino que también mejora la rentabilidad de las operaciones al reducir los costos de materia prima.
Además, la seguridad sigue siendo una prioridad en el diseño de dobladoras industriales. Las máquinas modernas están equipadas con sistemas de monitoreo en tiempo real, que permiten detectar condiciones de trabajo peligrosas o irregulares, lo que aumenta la seguridad del operador. También se están implementando tecnologías de bloqueo de seguridad que impiden el acceso a las partes móviles de la máquina mientras está en funcionamiento. Estas mejoras no solo protegen a los trabajadores, sino que también ayudan a cumplir con las normativas de seguridad industrial más estrictas.
Por último, la personalización del proceso de doblado es otro de los desarrollos que está tomando relevancia. Las dobladoras modernas pueden ser programadas de manera flexible para adaptarse a diferentes necesidades de producción sin tener que cambiar los componentes físicos de la máquina. Con la ayuda de sistemas de control avanzados, los operadores pueden ajustar rápidamente las máquinas para producir piezas con diferentes especificaciones de curvado o tamaños, lo que resulta en una mayor versatilidad y adaptabilidad para las fábricas.
En conclusión, las dobladoras industriales siguen siendo un pilar esencial en la fabricación moderna, con avances continuos en precisión, automatización, sostenibilidad y seguridad. Las innovaciones tecnológicas están permitiendo que las máquinas se adapten mejor a las exigencias de la producción actual y futura, brindando mayor flexibilidad, eficiencia y capacidad de respuesta ante los cambios del mercado. A medida que las industrias continúan evolucionando, las dobladoras seguirán siendo herramientas clave para cumplir con las expectativas de calidad, rapidez y sostenibilidad.
Curvadora automática
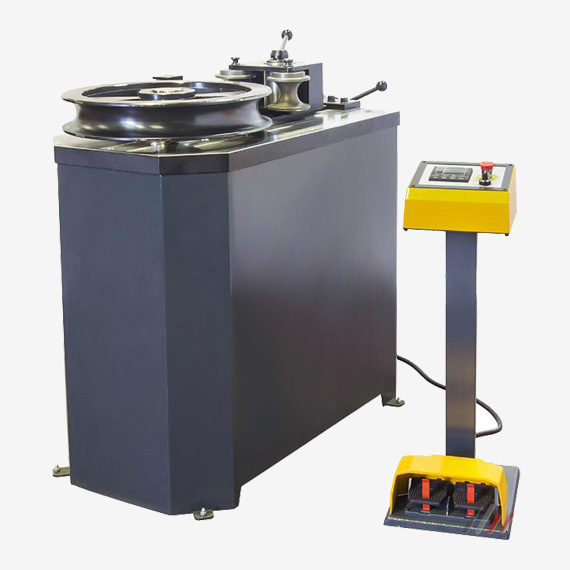
Una curvadora automática es una máquina especializada en realizar el proceso de curvado de materiales como tubos, barras y perfiles metálicos de forma automatizada, sin la necesidad de intervención manual constante. Estas máquinas son esenciales en la fabricación de componentes metálicos con precisión, eficiencia y consistencia, especialmente en entornos industriales de alta producción.
El funcionamiento de una curvadora automática se basa en la automatización del proceso de curvado, donde la máquina sigue un conjunto predefinido de instrucciones que pueden ser programadas mediante un sistema de control numérico computarizado (CNC) o a través de un sistema hidráulico o eléctrico automatizado. Estas máquinas son capaces de trabajar con varios tipos de materiales y tamaños, y son muy comunes en sectores como la industria automotriz, construcción, aeroespacial y fabricación de equipos industriales.
Características principales de la curvadora automática:
- Automatización del proceso de curvado: Gracias a los sistemas automáticos, las curvadoras automáticas permiten realizar curvados complejos con poca intervención humana. Esto no solo aumenta la precisión, sino que también mejora la eficiencia, ya que el proceso puede realizarse de manera continua sin detenerse por ajustes constantes.
- Control CNC: La mayoría de las curvadoras automáticas modernas cuentan con tecnología CNC, que permite programar de manera precisa los parámetros del proceso de curvado, como el radio de curvado, el ángulo y el número de repeticiones. Esta programación facilita la fabricación de piezas complejas sin la necesidad de configurar manualmente la máquina para cada tarea.
- Versatilidad: Las curvadoras automáticas pueden ser ajustadas para curvar una amplia variedad de materiales, como acero, aluminio, titanio, cobre y plástico. Además, pueden trabajar con una variedad de diámetros y grosores de tubos y perfiles, lo que las hace muy versátiles en la producción de diferentes tipos de componentes.
- Alta precisión y repetibilidad: Estas máquinas están diseñadas para garantizar un alto grado de precisión y repetibilidad, lo que significa que pueden realizar un número elevado de piezas idénticas con tolerancias mínimas, lo cual es crucial para industrias donde la calidad y la uniformidad son fundamentales.
- Reducción de tiempos de ciclo: Al estar automatizadas, las curvadoras automáticas pueden reducir significativamente los tiempos de ciclo. Esto se debe a que el proceso de curvado puede realizarse de manera más rápida y eficiente, sin la necesidad de múltiples ajustes o supervisión constante.
- Mantenimiento y monitoreo: Muchas curvadoras automáticas están equipadas con sistemas de monitoreo en tiempo real que permiten detectar posibles fallas antes de que afecten el proceso de producción. Esto es posible gracias al uso de sensores y tecnologías de mantenimiento predictivo, que aseguran una operación continua sin interrupciones inesperadas.
Aplicaciones de las curvadoras automáticas:
- Industria automotriz: Se utilizan para curvar tubos y perfiles metálicos que forman parte de la estructura de vehículos, los sistemas de escape, las suspensiones, y otros componentes. La capacidad de estas máquinas para manejar grandes volúmenes de producción con alta precisión es crucial para la industria.
- Construcción: En la construcción, se usan para fabricar componentes de acero curvado que forman parte de las estructuras metálicas de edificios, puentes, y otras infraestructuras. También se emplean para hacer tuberías curvadas que forman parte de sistemas de agua, gas y climatización.
- Fabricación de equipos industriales: Las curvadoras automáticas también son fundamentales en la producción de equipos industriales y muebles metálicos, donde se requieren curvas precisas en los perfiles de acero u otros metales.
- Industria aeroespacial: En este sector, las curvadoras automáticas se utilizan para fabricar componentes estructurales de aviones, cohetes y otras aeronaves, que requieren una precisión extrema en el curvado de materiales como el titanio y aluminio.
- Electrodomésticos: También son comúnmente usadas para producir componentes curvados en electrodomésticos como refrigeradores, lavadoras y microondas, donde se necesita una alta eficiencia en la fabricación de piezas metálicas complejas.
Ventajas de las curvadoras automáticas:
- Mayor productividad: Al eliminar la necesidad de intervención manual constante, las curvadoras automáticas pueden operar de manera continua y con mayor rapidez, lo que incrementa la producción.
- Calidad consistente: La precisión de las curvadoras automáticas garantiza una calidad constante de las piezas, lo que es esencial para la fabricación de productos en serie.
- Ahorro de costos: Aunque la inversión inicial en una curvadora automática puede ser alta, los ahorros en mano de obra, tiempos de ciclo más rápidos y reducción de desperdicio de material pueden generar un retorno sobre la inversión a largo plazo.
- Flexibilidad de producción: Las curvadoras automáticas son capaces de adaptarse a diferentes configuraciones y piezas personalizadas sin necesidad de grandes modificaciones, lo que las hace útiles en la producción de lotes pequeños o piezas especiales.
Desventajas y desafíos:
- Costo inicial elevado: Las curvadoras automáticas suelen ser más costosas en comparación con las máquinas manuales o semi-automáticas debido a la tecnología avanzada y la automatización que incorporan.
- Requiere capacitación: Aunque son más fáciles de operar que las máquinas manuales, las curvadoras automáticas requieren personal capacitado para configurar, programar y mantener las máquinas adecuadamente.
- Reparaciones y mantenimiento: Como con cualquier equipo automatizado, las curvadoras automáticas pueden ser complejas de reparar, y el mantenimiento preventivo puede ser costoso si no se lleva a cabo adecuadamente.
En resumen, las curvadoras automáticas son esenciales en la producción moderna, ofreciendo precisión, velocidad y eficiencia en una amplia gama de aplicaciones industriales. Su capacidad para realizar curvados complejos de manera repetible y de alta calidad las convierte en una inversión valiosa para sectores que requieren altos volúmenes de producción, precisión extrema y flexibilidad en sus procesos.
Las curvadoras automáticas continúan evolucionando con los avances tecnológicos, incorporando nuevas características para satisfacer las crecientes demandas de la industria. Un ejemplo de estas innovaciones es el uso de software avanzado que permite la simulación del proceso de curvado antes de realizarlo físicamente, lo que asegura que los resultados sean óptimos y permite ajustar los parámetros de forma más precisa. Estas máquinas también están mejorando su capacidad para ajustarse a materiales más diversos, como aleaciones especiales, compuestos y materiales con propiedades mecánicas complejas, que requieren tecnologías de curvado más avanzadas. El uso de sensores inteligentes para monitorear el proceso en tiempo real permite a las curvadoras automáticas ajustar de manera autónoma su operación para corregir cualquier desviación del proceso, lo que mejora aún más la precisión y la eficiencia.
Otra tendencia que está ganando terreno en las curvadoras automáticas es la integración con sistemas de fabricación inteligente o Industria 4.0. A través de la conexión en red y el intercambio de datos con otras máquinas y sistemas de control de la planta, estas curvadoras pueden optimizar el uso de materiales, reducir tiempos de inactividad y gestionar el mantenimiento predictivo. Con la ayuda de algoritmos de aprendizaje automático, las máquinas pueden identificar patrones en su funcionamiento y mejorar continuamente el proceso de curvado, detectando posibles fallos antes de que afecten la producción. Además, la interoperabilidad con otros sistemas de la planta permite la creación de líneas de producción completamente automatizadas, lo que reduce aún más la necesidad de intervención humana y mejora la eficiencia global de las fábricas.
Además de mejorar en términos de automatización y tecnología avanzada, las curvadoras automáticas también están haciendo esfuerzos para ser más energéticamente eficientes. A medida que las regulaciones ambientales se vuelven más estrictas y las empresas buscan reducir su huella de carbono, estas máquinas están siendo diseñadas para consumir menos energía durante su operación, mientras mantienen o incluso mejoran su rendimiento. Las mejoras en el diseño de los motores y los sistemas hidráulicos contribuyen a una mayor eficiencia energética, permitiendo que las curvadoras automáticas funcionen de manera más económica sin sacrificar la calidad o la productividad.
El control remoto y las interfaces intuitivas también son características que se están integrando en las curvadoras automáticas. Las pantallas táctiles permiten a los operadores monitorear y ajustar los parámetros de la máquina de forma sencilla y rápida. Además, algunas máquinas están equipadas con tecnología de control remoto que permite a los operadores supervisar las operaciones de la máquina desde una ubicación centralizada o incluso desde dispositivos móviles. Esto no solo mejora la comodidad, sino que también permite una mayor flexibilidad en la gestión de la producción y facilita la intervención rápida en caso de fallos o ajustes necesarios.
En cuanto a la personalización de las piezas, las curvadoras automáticas pueden ser configuradas para realizar una variedad de curvados, desde simples ángulos hasta curvas complejas con múltiples radios, adaptándose a la fabricación de productos más especializados y de baja producción. Esto es clave en industrias como la automotriz y la aeroespacial, donde los componentes curvados deben cumplir con requisitos específicos y, a menudo, deben fabricarse en pequeñas cantidades o lotes únicos. La capacidad de las curvadoras automáticas para manejar estas demandas personalizadas sin necesidad de reconfiguraciones costosas o prolongadas las convierte en una solución ideal para la fabricación flexible.
Al mismo tiempo, la adaptabilidad de estas máquinas se extiende a la integración de nuevas tecnologías como la realidad aumentada (AR) y la realidad virtual (VR) para la capacitación de operadores y la simulación de procesos. Estos enfoques permiten a los operadores familiarizarse con la máquina de forma interactiva, lo que puede acelerar el aprendizaje y reducir los errores en el proceso de producción. La integración de estas tecnologías en las curvadoras automáticas también permite la creación de entornos de trabajo virtuales donde los operarios pueden practicar la programación y operación de las máquinas en escenarios controlados, mejorando la seguridad y reduciendo la curva de aprendizaje.
Finalmente, la personalización y adaptabilidad de las curvadoras automáticas permiten a las empresas responder a las demandas del mercado con mayor agilidad, lo que resulta en una mayor competitividad. Al permitir la fabricación de productos más complejos, personalizables y con tiempos de producción más cortos, las curvadoras automáticas son esenciales para las industrias que buscan mantenerse a la vanguardia en términos de tecnología, productividad y sostenibilidad. Con su capacidad para integrar una amplia gama de tecnologías avanzadas, las curvadoras automáticas continúan siendo una herramienta vital en la fabricación moderna, ofreciendo soluciones flexibles y eficientes para una variedad de aplicaciones industriales.
Las curvadoras automáticas siguen siendo clave en el avance de la manufactura, especialmente cuando las industrias requieren alta precisión, velocidad y flexibilidad en la producción. A medida que las fábricas y las plantas de producción se modernizan, la integración de estas máquinas con sistemas de control avanzado y gestión de datos permite a las empresas optimizar todo el flujo de trabajo. En combinación con otros equipos automatizados y robots industriales, las curvadoras automáticas ayudan a formar parte de líneas de producción inteligentes, donde las decisiones sobre la programación, el control de calidad y la logística se realizan en tiempo real, ajustándose a las condiciones y demandas del mercado.
En términos de personalización del diseño, las curvadoras automáticas no solo mejoran la producción de piezas estándar, sino que también permiten crear componentes con geometrías altamente específicas que son comunes en la fabricación de productos industriales especializados. Esto es crucial para sectores como el de la automotriz, donde la demanda de piezas personalizadas de alta resistencia y adaptadas a modelos específicos de vehículos es cada vez mayor. Además, estas máquinas están diseñadas para aceptar distintos tipos de perfiles metálicos o incluso materiales compuestos que requieren procesos de curvado más sofisticados.
La gestión del ciclo de vida de la máquina también está mejorando, gracias a la implementación de sistemas de monitoreo continuo y mantenimiento predictivo. Estos sistemas permiten a los operadores de curvadoras automáticas monitorear las condiciones de la máquina en tiempo real, desde la presión hidráulica hasta el desgaste de las herramientas, lo que ayuda a prevenir fallos inesperados y optimizar el rendimiento de la máquina. Las alertas automáticas y las recomendaciones de mantenimiento programado basadas en el análisis de datos permiten a las empresas realizar mantenimiento proactivo, lo que reduce el tiempo de inactividad y mejora la vida útil de los equipos.
A nivel de conectividad, las curvadoras automáticas están cada vez más integradas en plataformas de Industria 4.0, lo que permite la comunicación bidireccional entre las máquinas y los sistemas de control central. Esto significa que las fábricas no solo pueden monitorear el estado de la producción, sino que también pueden ajustar parámetros en tiempo real desde un sistema centralizado, mejorando la eficiencia operativa. La capacidad de analizar grandes volúmenes de datos generados por las máquinas en tiempo real, combinada con tecnologías de inteligencia artificial, permite predecir y ajustar automáticamente los parámetros de curvado según las condiciones cambiantes de los materiales y las especificaciones del producto final.
A medida que la sostenibilidad se convierte en una prioridad en las operaciones industriales, las curvadoras automáticas también están siendo diseñadas para ser más eficientes en términos de consumo energético. Las mejoras en la eficiencia energética no solo están orientadas a la reducción del consumo durante el proceso de curvado, sino también a la optimización del uso de materiales. El diseño de estas máquinas busca minimizar el desperdicio de material durante el curvado, utilizando sistemas inteligentes que ajustan el proceso para aprovechar al máximo los recursos disponibles. Estas características permiten a las empresas cumplir con regulaciones más estrictas sobre la huella de carbono y las normas medioambientales.
En cuanto a la interfaz de usuario, las curvadoras automáticas se están tornando cada vez más intuitivas y fáciles de usar. Los sistemas de control mejorados, con pantallas táctiles y software fácil de navegar, permiten a los operadores ajustar configuraciones y solucionar problemas sin necesidad de formación técnica especializada. La visualización en tiempo real de parámetros como el ángulo de curvado, la presión y el radio de curvado no solo facilita la supervisión del proceso, sino que también ayuda a identificar y corregir rápidamente cualquier anomalía o desviación de las especificaciones.
El uso de tecnologías como realidad aumentada (AR) y realidad virtual (VR) para capacitación y diagnóstico está transformando la forma en que los operarios interactúan con las curvadoras automáticas. Estos avances permiten que los operarios sean entrenados de forma interactiva y segura, sin poner en riesgo la maquinaria. Además, la realidad aumentada permite a los técnicos realizar mantenimiento remoto o diagnósticos al superponer información útil sobre las piezas o componentes de la máquina, lo que mejora la eficiencia en la resolución de problemas y reduce el tiempo de inactividad.
En resumen, las curvadoras automáticas están en el corazón de la revolución industrial moderna. Con sus avances en automatización, inteligencia artificial, eficiencia energética y sostenibilidad, estas máquinas están diseñadas para satisfacer las demandas de las industrias actuales, proporcionando alta calidad, flexibilidad y productividad. A medida que las tecnologías continúan avanzando, las curvadoras automáticas seguirán desempeñando un papel crucial en la fabricación de componentes metálicos, facilitando la transición hacia fábricas más inteligentes, rápidas y sostenibles.
Curvadora hidráulica de tubos
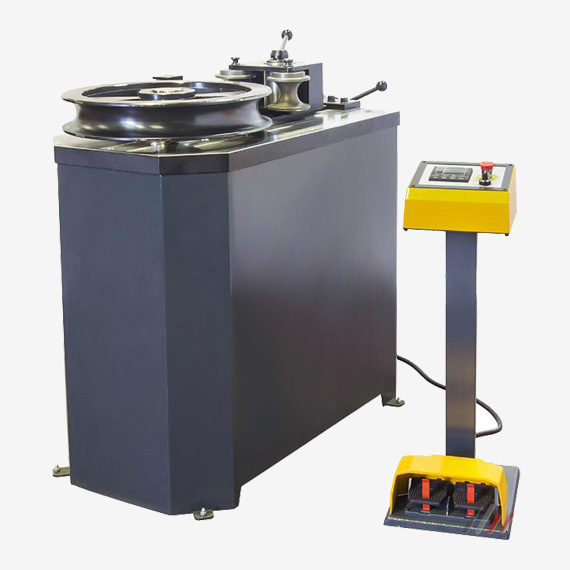
Una curvadora hidráulica de tubos es una máquina especializada en curvar tubos de diferentes materiales utilizando el principio de la presión hidráulica. Estas máquinas son muy comunes en la industria para la fabricación de componentes metálicos curvados, y son especialmente útiles cuando se necesita curvar tubos de gran diámetro o de materiales más duros que requieren una fuerza significativa para realizar el curvado de manera eficiente.
El principio básico de funcionamiento de una curvadora hidráulica de tubos se basa en la utilización de presión hidráulica para ejercer una fuerza sobre el tubo, lo que permite doblarlo o curvarlo sin romperlo ni dañar su estructura. Esto se logra utilizando una combinación de cilindros hidráulicos, moldes y rodillos que guían el tubo mientras se dobla.
Componentes principales de una curvadora hidráulica de tubos:
- Cilindros hidráulicos: Los cilindros son responsables de generar la fuerza necesaria para doblar el tubo. La presión del fluido hidráulico se controla de forma precisa, lo que permite ajustar la cantidad de curvado y la fuerza aplicada.
- Rodillos o mandriles: Los rodillos o mandriles son los elementos que guían el tubo mientras se va curvando. Estos componentes aseguran que el tubo siga la trayectoria correcta, evitando deformaciones no deseadas.
- Molde de curvado: El molde es la pieza sobre la cual el tubo se curvará. Dependiendo de la configuración de la máquina y el tipo de curvado deseado, el molde puede ser intercambiable o ajustable para adaptarse a diferentes diámetros y ángulos de curvado.
- Sistema de control hidráulico: Este sistema regula la presión y el flujo del fluido hidráulico, permitiendo un control preciso sobre la fuerza que se aplica al tubo, lo cual es fundamental para evitar la deformación excesiva o la ruptura del material.
- Panel de control o sistema CNC: Muchas curvadoras hidráulicas están equipadas con sistemas de control numérico computarizado (CNC), que permiten programar y ajustar automáticamente los parámetros del curvado, como el ángulo, el radio y la velocidad, para lograr una precisión constante en cada pieza producida.
Características y ventajas de las curvadoras hidráulicas de tubos:
- Gran capacidad de fuerza: Las curvadoras hidráulicas son capaces de generar fuerzas mucho mayores que las curvadoras mecánicas, lo que las hace ideales para tubos de mayor espesor o de materiales más resistentes, como acero inoxidable, titanio y aleaciones.
- Precisión: Gracias al control hidráulico, estas máquinas ofrecen una excelente precisión en el curvado de tubos, lo que permite producir componentes con tolerancias estrictas. Además, el uso de sistemas CNC facilita el proceso y permite realizar curvados complejos de forma repetitiva con alta exactitud.
- Curvados de gran diámetro: Las curvadoras hidráulicas son especialmente útiles para tubos de gran diámetro, ya que la presión hidráulica permite realizar curvados sin comprometer la integridad del material.
- Menor riesgo de dañar el material: A diferencia de otros tipos de curvadoras, como las curvadoras mecánicas, las curvadoras hidráulicas aplican una presión gradual y uniforme, lo que reduce el riesgo de deformaciones no deseadas o roturas del tubo durante el proceso de curvado.
- Versatilidad: Las curvadoras hidráulicas pueden manejar una amplia variedad de materiales, como acero, aluminio, cobre, acero inoxidable, titanio y plástico, lo que las convierte en herramientas versátiles para diversas aplicaciones industriales.
- Flexibilidad en los ángulos de curvado: Este tipo de curvadora puede realizar una variedad de ángulos de curvado, desde curvados suaves hasta ángulos agudos, dependiendo de las necesidades del proceso de fabricación.
Aplicaciones comunes de las curvadoras hidráulicas de tubos:
- Industria automotriz: En la fabricación de componentes como sistemas de escape, chasis, barras estabilizadoras y estructuras metálicas para vehículos, las curvadoras hidráulicas se utilizan para curvar tubos con alta precisión.
- Construcción: En la industria de la construcción, se utilizan para fabricar tubos curvados que forman parte de las estructuras metálicas de puentes, edificios y otras infraestructuras. También son útiles para crear sistemas de tuberías curvadas que transportan agua, gas o electricidad.
- Industria aeroespacial: Las curvadoras hidráulicas son cruciales en la fabricación de componentes aeronáuticos que requieren curvados precisos y resistentes a condiciones extremas, como el aluminio o titanio utilizados en la fabricación de aviones y naves espaciales.
- Fabricación de muebles metálicos: En la creación de muebles metálicos, como estantes, estructuras de sillas y mesas, las curvadoras hidráulicas permiten obtener tubos curvados con acabados uniformes y alta resistencia.
- Fabricación de equipos industriales: Las curvadoras hidráulicas son esenciales para fabricar estructuras metálicas y componentes de equipos industriales que requieren curvados precisos, como las tuberías de calderas, radiadores y tubos de refrigeración.
- Producción de sistemas de climatización: En la fabricación de conductos de aire y otros sistemas de climatización, las curvadoras hidráulicas permiten realizar curvados en tubos de cobre o aluminio de forma eficiente y precisa.
Ventajas adicionales de las curvadoras hidráulicas de tubos:
- Operación silenciosa: El sistema hidráulico tiende a ser más silencioso en comparación con las máquinas de curvado mecánicas, lo que mejora el ambiente laboral.
- Control de curvado sin contacto: Al usar presión hidráulica en lugar de una fuerza mecánica directa, se reduce el riesgo de dañar la superficie del tubo durante el curvado.
- Capacidad para realizar curvados en frío: Estas máquinas permiten curvar tubos sin necesidad de calentar el material, lo que es importante para ciertos materiales que no deben ser sometidos a calor excesivo.
En resumen, las curvadoras hidráulicas de tubos son herramientas esenciales en la fabricación de una amplia variedad de componentes curvados, ofreciendo gran precisión, fuerza y flexibilidad. Son especialmente útiles cuando se requiere curvar materiales difíciles o de gran diámetro, y su capacidad de automatización y control las convierte en una opción ideal para muchas industrias que necesitan una producción de alta calidad y en grandes volúmenes.
Las curvadoras hidráulicas de tubos han revolucionado la fabricación industrial, permitiendo procesos de curvado más eficientes y precisos. Con la capacidad de manejar una variedad de materiales y diámetros, son esenciales en sectores que requieren soluciones de curvado específicas y de alta calidad. El principio hidráulico de operación, basado en la aplicación de presión uniforme, no solo permite curvar tubos de gran tamaño y material resistente, sino que también asegura que no se produzcan daños en el material durante el proceso. Esto se traduce en una mayor durabilidad y menor desperdicio de material, lo que es fundamental para la optimización de costos en producción. La precisión en el curvado también es un factor clave, ya que asegura que las piezas finales cumplan con las estrictas especificaciones de diseño, lo cual es crucial en industrias como la automotriz, la aeroespacial y la de construcción, donde los componentes deben encajar con tolerancias muy estrictas.
La integración de sistemas de control CNC en las curvadoras hidráulicas mejora aún más la precisión y la repetibilidad de los procesos. Los operadores pueden programar con exactitud los parámetros del curvado, lo que permite realizar ajustes automáticos según las necesidades del proceso sin intervención manual. Esto no solo reduce el tiempo de configuración, sino que también aumenta la productividad y minimiza los errores humanos. Además, la capacidad de automatizar el proceso de curvado contribuye a un mayor rendimiento en líneas de producción a gran escala, facilitando la fabricación continua de piezas sin necesidad de parar para ajustes frecuentes.
Uno de los aspectos más destacados de las curvadoras hidráulicas es su versatilidad. Pueden trabajar con una amplia gama de materiales, incluyendo acero inoxidable, aluminio, cobre, y acero al carbono, lo que las hace aptas para múltiples aplicaciones en diversas industrias. Esto también se refleja en la adaptabilidad de la máquina a diferentes diámetros de tubo y radios de curvado, lo que les permite realizar curvados complejos que serían muy difíciles de ejecutar con métodos tradicionales. La posibilidad de curvar sin calentar los materiales también es una ventaja importante en muchas aplicaciones, ya que evita la alteración de las propiedades del material debido al calor.
Otra ventaja significativa de las curvadoras hidráulicas es su capacidad para producir piezas sin deformaciones. Esto se debe al control preciso que permite aplicar presión de manera constante y controlada, lo que minimiza el riesgo de distorsión o deformación no deseada en el tubo. Esto es especialmente crítico cuando se trabaja con materiales sensibles o de alta resistencia, como en la fabricación de componentes aeroespaciales o piezas de maquinaria pesada, donde las tolerancias de fabricación son extremadamente estrictas.
Además, las mejoras en la tecnología de monitoreo y en el uso de sensores inteligentes permiten una supervisión en tiempo real del proceso de curvado. Estos sensores detectan cualquier anomalía en la máquina o en el material, alertando a los operadores sobre posibles problemas antes de que ocurran, lo que mejora la seguridad y eficiencia operativa. El mantenimiento predictivo también se ha convertido en una función clave, ya que, mediante el análisis de datos, se pueden predecir fallos en los componentes y realizar intervenciones antes de que afecten la producción.
La incorporación de interfaces de usuario intuitivas ha mejorado la facilidad de uso de estas máquinas. Las pantallas táctiles y los sistemas de control avanzados permiten a los operadores ajustar los parámetros del curvado de manera rápida y sencilla, incluso sin tener una experiencia técnica profunda. Esta facilidad de uso es esencial en entornos de producción rápidos, donde se requiere una alta capacidad de respuesta y eficiencia para satisfacer las demandas del mercado.
En términos de sostenibilidad, las curvadoras hidráulicas también están evolucionando para ser más respetuosas con el medio ambiente. La optimización de los sistemas hidráulicos y la reducción del consumo energético son aspectos clave en el diseño de las máquinas modernas, lo que contribuye a una reducción en la huella de carbono de las fábricas. Además, la capacidad de utilizar materiales reciclables y la precisión en el curvado que minimiza el desperdicio de material son contribuciones importantes hacia prácticas de producción más sostenibles.
Finalmente, la capacidad de estas máquinas para realizar curvados de forma automática, con mínima intervención humana, las convierte en una herramienta vital en la fabricación moderna. Esto no solo reduce el riesgo de errores, sino que también aumenta la capacidad de las fábricas para producir grandes volúmenes de piezas de alta calidad con menos costos operativos. A medida que la tecnología continúa avanzando, las curvadoras hidráulicas seguirán desempeñando un papel crucial en la fabricación industrial, ofreciendo soluciones más eficientes, precisas y sostenibles para diversas industrias.
A medida que las curvadoras hidráulicas de tubos continúan evolucionando, la tendencia hacia la automatización y la integración con sistemas inteligentes está marcando un cambio significativo en la forma en que se gestionan los procesos de producción. La inteligencia artificial y el aprendizaje automático están comenzando a jugar un papel importante en la optimización de las máquinas, permitiendo no solo el ajuste automático de los parámetros de curvado, sino también la predicción de los comportamientos de los materiales durante el proceso. Esto permite a las curvadoras adaptar sus operaciones en tiempo real, mejorando aún más la precisión y reduciendo el desperdicio.
Además de la optimización de la producción, la interconexión de las máquinas dentro de la Industria 4.0 está permitiendo que las curvadoras hidráulicas de tubos se comuniquen de manera más efectiva con otros sistemas de la planta. Esto incluye la gestión de inventarios, el monitoreo de calidad en tiempo real y la optimización de recursos. Por ejemplo, los datos recopilados durante el proceso de curvado pueden integrarse con sistemas ERP (Enterprise Resource Planning) para mejorar la planificación de la producción y los tiempos de entrega.
Otra área donde las curvadoras hidráulicas están marcando una diferencia es en la personalización de la producción. La flexibilidad que ofrecen estas máquinas les permite adaptarse rápidamente a cambios en el diseño o en los requisitos del cliente, sin necesidad de largos períodos de configuración o reajustes. Esto es crucial en sectores como el automotriz o la fabricación de equipos industriales, donde las demandas de productos personalizados y diseños innovadores son cada vez más comunes.
Por otro lado, el avance hacia el uso de materiales compuestos también ha llevado a la necesidad de curvadoras hidráulicas especializadas que puedan manejar estos nuevos materiales. Los tubos hechos de materiales compuestos, como fibra de carbono o plásticos reforzados, requieren un enfoque diferente en el curvado, ya que son más sensibles a las deformaciones y requieren una presión más controlada y una manipulación más delicada durante el proceso. Las curvadoras hidráulicas están siendo diseñadas para adaptarse a estas nuevas demandas, lo que abre oportunidades para aplicaciones en sectores emergentes como la energía renovable y la aviación.
Las normas de calidad también están jugando un papel fundamental en el desarrollo de las curvadoras hidráulicas. La demanda de productos con tolerancias más estrictas y la necesidad de cumplir con certificaciones internacionales de calidad están impulsando mejoras en los sistemas de control y monitoreo de las máquinas. Muchas de las curvadoras hidráulicas modernas están equipadas con sensores de alta precisión que verifican la alineación y el radio de curvado en cada etapa del proceso, garantizando que las piezas curvadas cumplan con las especificaciones exactas requeridas.
La seguridad es otro factor que no puede pasarse por alto. Las curvadoras hidráulicas, debido a la alta fuerza que emplean, deben estar equipadas con sistemas de seguridad avanzados para proteger a los operadores y prevenir accidentes. Los sistemas de bloqueo automático, detención de emergencia y monitorización de presión ayudan a reducir el riesgo de fallos mecánicos o hidráulicos que podrían poner en peligro la seguridad del trabajador. Además, la ergonomía también juega un papel importante, con muchas de estas máquinas diseñadas para ser más fáciles de operar y mantener, reduciendo la carga física sobre los trabajadores.
El mantenimiento predictivo también ha sido optimizado gracias a la integración de tecnologías IoT (Internet of Things) que permiten monitorear en tiempo real el estado de cada componente de la curvadora. Esto proporciona información detallada sobre el desgaste de piezas, la presión hidráulica y el rendimiento general de la máquina, permitiendo una programación más eficiente del mantenimiento y evitando costosos tiempos de inactividad.
Además de los avances en la máquina misma, el software que acompaña a las curvadoras hidráulicas ha mejorado sustancialmente. Los programas de simulación de curvado permiten a los diseñadores prever los resultados de los curvados antes de realizar el proceso físico, lo que reduce los errores y la necesidad de pruebas físicas. Los sistemas de análisis de datos también están desempeñando un papel importante en la mejora continua de los procesos de curvado, proporcionando informes detallados que permiten realizar ajustes en tiempo real para mejorar la eficiencia de la producción.
En cuanto a la sostenibilidad, las curvadoras hidráulicas también están contribuyendo a una mayor eficiencia energética. Las mejoras en los sistemas hidráulicos, como el uso de bombeo variable y el control preciso del flujo de fluido, permiten reducir el consumo energético durante la operación. Esto no solo ayuda a las empresas a cumplir con las normativas medioambientales, sino que también contribuye a reducir los costos operativos.
Por último, el continuo desarrollo tecnológico está llevando a la creación de curvadoras hidráulicas con capacidades de curvado en 3D. Esto significa que, además de los curvados tradicionales de un solo eje, las máquinas podrán curvar tubos de manera más compleja, adaptándose a la geometría tridimensional de los diseños más avanzados. Esta capacidad permitirá a las empresas fabricar componentes más sofisticados y con diseños más complejos que antes solo podían ser realizados con múltiples procesos de curvado o moldeo.
En resumen, las curvadoras hidráulicas de tubos no solo están mejorando en términos de capacidad de producción y flexibilidad, sino que están avanzando en áreas clave como automatización, sostenibilidad, precisión y seguridad. Estos avances continúan posicionándolas como una herramienta esencial para la fabricación moderna, y su evolución futura promete abrir nuevas oportunidades en diversas industrias, desde la automotriz hasta la aeroespacial.
Curvadora de perfiles metálicos
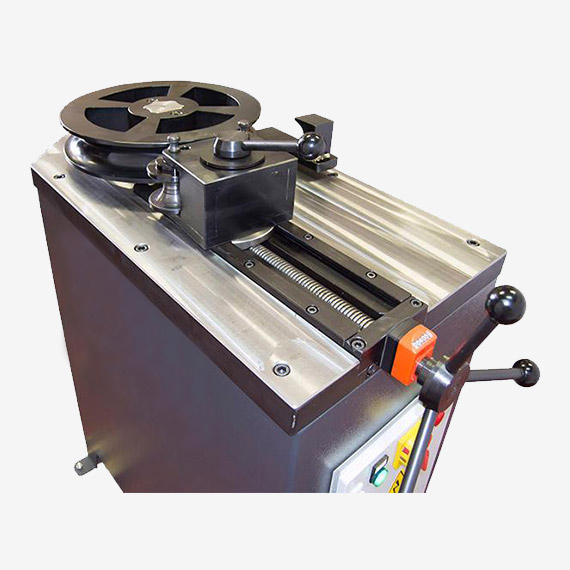
Una curvadora de perfiles metálicos es una máquina utilizada para doblar o curvar perfiles metálicos de diferentes formas, como perfiles en “L”, “U”, “C”, tubulares o en I, entre otros. Estas máquinas son esenciales en la fabricación de estructuras metálicas, componentes de construcción y otros productos industriales que requieren curvados precisos de materiales metálicos. A diferencia de las curvadoras de tubos, que se enfocan en doblar tubos y caños, las curvadoras de perfiles están diseñadas para trabajar con formas estructurales más complejas y a menudo más grandes.
Principio de funcionamiento
El funcionamiento de una curvadora de perfiles metálicos se basa en aplicar una fuerza de compresión controlada sobre el material metálico para cambiar su forma, sin causar roturas o deformaciones no deseadas. Las máquinas utilizan una combinación de rodillos o mandriles, y en algunos casos cilindros hidráulicos o motores eléctricos, para guiar el perfil a través de un proceso controlado de curvado.
Generalmente, el proceso de curvado de perfiles metálicos se lleva a cabo mediante la aplicación de presión gradual, utilizando una serie de rodillos dispuestos en diferentes posiciones alrededor del perfil. Este tipo de máquina permite realizar curvados de radio grande o curvados más agudos, según las necesidades del proyecto.
Tipos de curvadoras de perfiles metálicos
Existen varios tipos de curvadoras de perfiles metálicos que se distinguen por el sistema que emplean para curvar los perfiles y el tipo de material que pueden procesar. Algunos de los tipos más comunes son:
- Curvadoras manuales: Son las más básicas y, por lo general, se utilizan para curvar perfiles de tamaño pequeño o mediano. La máquina es operada a mano, lo que significa que el operador ajusta manualmente la presión aplicada al perfil. Son más adecuadas para producciones pequeñas o personalizadas.
- Curvadoras hidráulicas: Utilizan el principio de hidráulica para aplicar una mayor presión en el proceso de curvado. Son ideales para perfiles metálicos más grandes o de mayor espesor, y son capaces de realizar curvados precisos en una amplia gama de materiales, como acero, acero inoxidable y aluminio.
- Curvadoras CNC (Control Numérico por Computadora): Incorporan un sistema de control computarizado que permite programar el proceso de curvado. Este tipo de curvadora es ideal para producciones de grandes volúmenes o curvados complejos con alta precisión. Los sistemas CNC permiten realizar ajustes automáticos en el proceso de curvado y permiten la repetibilidad exacta de las formas.
- Curvadoras de rodillos: Estas máquinas emplean una serie de rodillos para guiar el perfil metálico a través de un proceso gradual de curvado. Son utilizadas para piezas más largas y para perfiles metálicos que requieren un radio de curvado mayor, como en la fabricación de estructuras de acero para la construcción.
- Curvadoras de doble rodillo: Son una variante de las curvadoras de rodillos y permiten curvar perfiles metálicos de una manera más controlada. Los perfiles se colocan entre dos rodillos que aplican presión en direcciones opuestas para doblar el material.
Características de una curvadora de perfiles metálicos
- Capacidad de curvado: Las curvadoras de perfiles metálicos tienen una capacidad limitada en cuanto al grosor y el tamaño del perfil que pueden curvar. Esto depende tanto del tipo de máquina como de la fuerza hidráulica o mecánica que puedan generar.
- Control de radio de curvado: Las curvadoras permiten controlar el radio de curvado para obtener una curvatura más suave o más aguda, según los requisitos del diseño. El control preciso de este parámetro es esencial, especialmente cuando se requiere que el perfil curvado mantenga ciertas especificaciones geométricas.
- Versatilidad de materiales: Las máquinas modernas son capaces de curvar no solo perfiles de acero, sino también materiales más ligeros como el aluminio, cobre, acero inoxidable y acero al carbono. Esto las hace muy versátiles para diversas aplicaciones industriales.
- Precisión: La precisión en el curvado es crítica en muchos sectores, especialmente en la fabricación de componentes que deben encajar perfectamente en un ensamblaje. Las curvadoras CNC permiten un nivel de precisión muy alto en el curvado de perfiles metálicos, asegurando que cada pieza tenga las dimensiones exactas que se necesitan.
- Velocidad de producción: Las curvadoras modernas están diseñadas para ofrecer una producción rápida, lo que permite curvar grandes volúmenes de perfiles metálicos sin comprometer la calidad del curvado. Las versiones CNC, en particular, optimizan la producción al permitir la automatización de procesos.
Aplicaciones de las curvadoras de perfiles metálicos
Las curvadoras de perfiles metálicos se utilizan ampliamente en diversas industrias. Algunos de los campos más comunes incluyen:
- Industria de la construcción: En la fabricación de estructuras metálicas para edificios, puentes, y otras infraestructuras, las curvadoras de perfiles metálicos son esenciales para crear vigas curvadas, columnas y marcos metálicos. También se utilizan en la producción de tuberías estructurales y sistemas de soporte.
- Industria automotriz: En la fabricación de chasis y componentes estructurales para vehículos, las curvadoras de perfiles metálicos permiten curvar acero y otros materiales para adaptarse a los diseños de los fabricantes de automóviles.
- Industria ferroviaria: En la fabricación de perfiles curvados para la infraestructura ferroviaria, las curvadoras se utilizan para curvar rieles y componentes de vías férreas.
- Fabricación de maquinaria: Las curvadoras de perfiles metálicos se emplean en la fabricación de estructuras y componentes de maquinaria pesada que requieren curvados precisos de perfiles metálicos de gran tamaño y resistencia.
- Industrias del metal y la energía: Las plantas de energía y las industrias del metal requieren la fabricación de estructuras metálicas curvadas para diversas aplicaciones, como soportes de tubos, componentes de calderas y sistemas de conductos.
- Decoración y diseño industrial: También se utilizan en aplicaciones más estéticas, como la fabricación de mobiliario metálico curvado, puertas y elementos decorativos.
Ventajas de las curvadoras de perfiles metálicos
- Alta precisión: Las curvadoras modernas permiten realizar curvados con alta precisión, lo que asegura que los componentes curvados encajen correctamente en su aplicación final.
- Versatilidad: Son capaces de trabajar con una amplia gama de materiales y tipos de perfiles, lo que las hace útiles para muchas industrias diferentes.
- Velocidad de producción: Gracias a la automatización y los sistemas CNC, las curvadoras de perfiles metálicos permiten una producción rápida y continua, optimizando el tiempo en la fabricación de componentes metálicos.
- Reducción de desperdicio: Los procesos de curvado controlados evitan la deformación y desperdicio del material, lo que ayuda a reducir costos y mejorar la eficiencia en la producción.
En resumen, las curvadoras de perfiles metálicos son esenciales en la fabricación de componentes curvados de materiales metálicos y tienen aplicaciones en una amplia gama de industrias. Gracias a su capacidad de trabajar con diversos materiales y perfiles, y a las mejoras tecnológicas como los sistemas CNC y hidráulicos, estas máquinas continúan siendo una herramienta clave para la fabricación de estructuras metálicas precisas y eficientes.
La evolución de las curvadoras de perfiles metálicos ha sido impulsada principalmente por las exigencias de precisión, velocidad y flexibilidad en los procesos de fabricación modernos. Estas máquinas no solo deben ser capaces de curvar una gran variedad de perfiles con distintos radios y ángulos, sino que también deben garantizar una repetibilidad exacta, especialmente en sectores donde las tolerancias geométricas son críticas. En este contexto, las curvadoras equipadas con controles numéricos por computadora han ganado protagonismo, ya que permiten automatizar por completo el proceso de curvado, reducir los errores humanos y aumentar significativamente la productividad.
A través de interfaces gráficas intuitivas, los operadores pueden cargar diseños, establecer parámetros de curvado específicos y monitorear el proceso en tiempo real, todo desde una misma estación. Esta integración digital permite además que la curvadora se conecte a sistemas de diseño asistido por computadora (CAD), facilitando así la transición directa del diseño a la fabricación sin pasos intermedios. Otro avance destacado en las curvadoras de perfiles metálicos es la incorporación de sistemas de compensación automática, los cuales ajustan la fuerza de curvado en función del retorno elástico del material, una característica especialmente útil al trabajar con aceros de alta resistencia o con perfiles de geometría irregular.
En paralelo, el desarrollo de tecnologías de monitoreo en tiempo real ha permitido implementar sistemas que detectan y corrigen desviaciones durante el proceso mismo, evitando defectos y desperdicio de material. Estos sistemas utilizan sensores que miden constantemente la posición, el ángulo y la curvatura del perfil en proceso, y en función de esos datos realizan ajustes automáticos a la máquina para mantener la calidad esperada. La precisión alcanzada por estos métodos ha hecho que las curvadoras de perfiles metálicos sean ampliamente utilizadas en la fabricación de componentes arquitectónicos personalizados, estructuras metálicas complejas, piezas para maquinaria pesada, y elementos decorativos de gran escala. Además, en entornos industriales donde la producción en serie es crucial, estas máquinas permiten programar y almacenar múltiples configuraciones de curvado, lo que reduce el tiempo de preparación entre distintos lotes de producción.
Otro aspecto importante es la robustez mecánica de las curvadoras de perfiles, ya que deben resistir fuerzas de curvado muy elevadas sin comprometer su estabilidad estructural. Los fabricantes han adoptado diseños de bastidor reforzado y sistemas de transmisión de gran eficiencia que garantizan un desempeño estable incluso bajo cargas exigentes. Algunos modelos de alta gama integran además sistemas de refrigeración y lubricación automáticos para prolongar la vida útil de los componentes críticos. En términos de seguridad, las curvadoras modernas están equipadas con barreras fotoeléctricas, botones de parada de emergencia y sistemas de diagnóstico que alertan al operador ante cualquier anomalía. Esto es especialmente relevante al trabajar con perfiles de gran tamaño, donde la manipulación manual puede implicar riesgos si no se dispone de los elementos de protección adecuados.
Desde el punto de vista operativo, una de las ventajas más valoradas por los usuarios es la capacidad de estas máquinas para adaptarse rápidamente a diferentes dimensiones y tipos de perfiles sin necesidad de cambiar completamente la configuración mecánica. Algunos modelos permiten intercambiar los rodillos o modificar sus posiciones de manera ágil, lo que favorece una producción más flexible. Esta capacidad de adaptación resulta clave en empresas que ofrecen soluciones a medida o que trabajan con proyectos que requieren cambios frecuentes en el diseño. Además, la compatibilidad de las curvadoras con materiales como aluminio, acero inoxidable, latón o acero al carbono amplía su rango de aplicación, permitiendo que una misma máquina pueda ser utilizada en diferentes áreas de producción dentro de una planta industrial.
En el ámbito del mantenimiento, las curvadoras de perfiles metálicos han incorporado sistemas inteligentes que monitorean el estado de componentes críticos como motores, cilindros hidráulicos y sistemas de control, alertando de forma anticipada sobre posibles desgastes o fallos. Esto permite planificar intervenciones de mantenimiento preventivo, evitando paradas inesperadas que podrían comprometer la producción. El uso de diagnósticos remotos también se ha vuelto común, permitiendo que el fabricante o servicio técnico acceda a los datos de la máquina para brindar soporte sin necesidad de presencia física. Esta funcionalidad es especialmente útil en entornos donde la disponibilidad de técnicos especializados es limitada o en ubicaciones remotas.
Por último, es importante mencionar que el mercado de las curvadoras de perfiles metálicos continúa creciendo impulsado por la demanda de estructuras metálicas complejas, soluciones arquitectónicas personalizadas y componentes industriales de alta precisión. La constante innovación en diseño mecánico, control electrónico y software de simulación asegura que estas máquinas seguirán siendo una herramienta fundamental en el desarrollo de proyectos modernos. A medida que las exigencias del mercado aumentan, se espera que las curvadoras evolucionen aún más en dirección a una integración completa con sistemas digitales de producción, mayor eficiencia energética y una personalización cada vez más precisa de los procesos de curvado.
Además de su papel fundamental en la industria pesada y en la construcción, las curvadoras de perfiles metálicos están adquiriendo relevancia en sectores más especializados como la aeronáutica, la fabricación de equipos médicos y la producción de mobiliario de diseño. En estos casos, la exigencia en cuanto a la calidad superficial del perfil curvado y la exactitud del ángulo de curvado es aún mayor, lo que ha llevado al desarrollo de tecnologías aún más refinadas. Algunas máquinas incorporan sistemas de servomotores de alta resolución que permiten realizar ajustes micrométricos en los rodillos o elementos de presión, garantizando así resultados repetibles en materiales delicados o altamente sensibles a la deformación. Asimismo, los controles avanzados permiten simular el curvado en entorno virtual antes de ejecutarlo, identificando posibles puntos de falla o tensiones no deseadas en el perfil, lo que reduce los costos de prueba y error.
Otro campo en expansión para las curvadoras de perfiles metálicos es la arquitectura moderna, especialmente en la creación de fachadas curvas, estructuras autoportantes, techos ondulados y elementos escultóricos de gran escala. En estos casos, las empresas diseñadoras y constructoras recurren a perfiles metálicos curvados con radios específicos que deben ser ejecutados con gran exactitud para garantizar tanto la estética como la integridad estructural del diseño. Las curvadoras utilizadas para este propósito suelen trabajar con perfiles de aluminio o acero inoxidable, y necesitan garantizar una perfecta conservación del acabado superficial, ya que el producto curvado no suele ser recubierto o pintado. Este nivel de exigencia ha llevado a la incorporación de recubrimientos especiales en los rodillos y soportes, que evitan marcas o deformaciones visibles durante el curvado.
También es notable el papel de las curvadoras en la industria de energías renovables, donde se utilizan para formar perfiles estructurales para torres eólicas, marcos de paneles solares y estructuras de soporte de instalaciones fotovoltaicas. En este ámbito, se valora especialmente la capacidad de estas máquinas para trabajar con perfiles largos y de alta resistencia, asegurando una producción rápida y estandarizada. De hecho, algunos modelos están preparados para trabajar en línea con otros equipos de corte y ensamblado, formando parte de celdas de producción automatizadas. La integración de estas curvadoras en líneas de producción de gran escala permite a los fabricantes aumentar significativamente su rendimiento sin sacrificar la calidad ni la precisión del producto final.
La flexibilidad de diseño de las curvadoras también ha hecho posible la ejecución de proyectos singulares que, sin estas tecnologías, habrían sido prácticamente imposibles de realizar. Por ejemplo, en obras de infraestructura como puentes con formas orgánicas, túneles metálicos curvos, pasarelas arquitectónicas o cubiertas de grandes luces, se utilizan perfiles curvados con precisión milimétrica. Cada uno de estos elementos debe cumplir con especificaciones geométricas y estructurales muy estrictas, por lo que el control de calidad durante el proceso de curvado es un aspecto crítico. Por ello, muchas curvadoras avanzadas incorporan no solo sensores de medición, sino también escáneres ópticos que permiten verificar en tiempo real la forma y dimensiones del perfil conforme va siendo trabajado.
La capacitación de los operadores es otro aspecto que ha evolucionado junto con la tecnología de las curvadoras. Si bien las primeras versiones requerían habilidades manuales significativas y experiencia práctica en el manejo de perfiles, las versiones modernas están orientadas a usuarios que dominan los entornos digitales. Esto ha llevado a la inclusión de interfaces más amigables, sistemas de ayuda interactivos y módulos de entrenamiento integrados en el software de la máquina. Además, muchos fabricantes ofrecen simuladores virtuales que permiten a los operarios entrenarse en el uso de la máquina sin riesgo de dañar material real, lo que facilita una curva de aprendizaje más rápida y segura.
La tendencia actual apunta hacia una mayor personalización de los equipos, permitiendo que cada empresa adquiera una curvadora configurada específicamente para el tipo de perfil, volumen de producción y nivel de automatización que requiere. Esto significa que, desde el diseño del bastidor hasta la disposición de los rodillos y el tipo de control, cada máquina puede adaptarse a las condiciones reales del entorno de trabajo. En consecuencia, la inversión en una curvadora de perfiles metálicos no solo representa una mejora tecnológica, sino también un elemento estratégico dentro del modelo de producción de la empresa, ya que afecta directamente la eficiencia operativa, la calidad del producto final y la capacidad de responder a demandas específicas del mercado.
Curvadora de caños metálicos
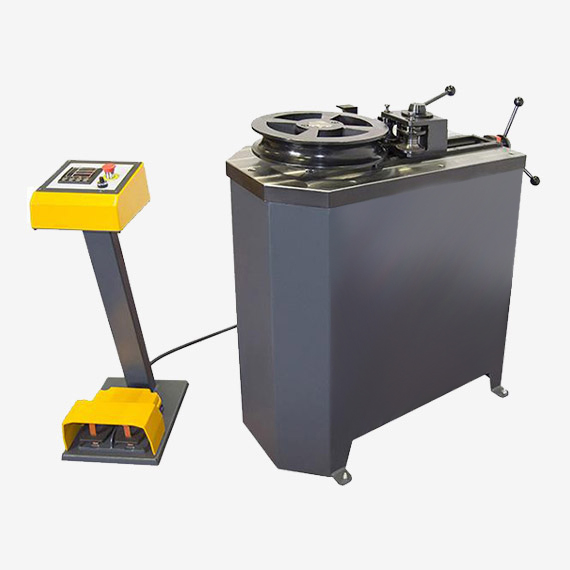
La curvadora de caños metálicos es una herramienta fundamental en numerosos sectores industriales donde se requiere modificar la trayectoria de tubos sin comprometer su sección transversal ni sus propiedades mecánicas. Estos equipos permiten realizar curvas con distintos radios, ángulos y formas, en materiales como acero al carbono, acero inoxidable, aluminio, cobre o aleaciones especiales. A diferencia de los tubos plásticos, los caños metálicos presentan mayor resistencia y dureza, lo que exige que la curvadora ejerza fuerzas significativas con una precisión milimétrica. Esto se logra mediante sistemas mecánicos, hidráulicos o eléctricos que aplican presión controlada sobre el tubo, obligándolo a adaptarse a la geometría deseada sin arrugarse, aplanarse ni romperse.
Las curvadoras modernas están diseñadas no solo para garantizar la calidad dimensional del caño doblado, sino también para minimizar el llamado “retorno elástico”, es decir, la tendencia natural del material a recuperar parcialmente su forma original después de ser curvado. Este fenómeno varía según el tipo de metal, su espesor y su tratamiento térmico, por lo que las máquinas de gama alta incorporan algoritmos de compensación automática que ajustan el ángulo final del curvado en función de esos factores. Estas funciones son controladas mediante pantallas digitales o sistemas CNC que permiten una programación precisa y repetible de las operaciones. Algunas curvadoras incluso permiten almacenar cientos de programas distintos, facilitando la producción en serie de piezas idénticas con mínimas intervenciones del operador.
En términos de diseño, las curvadoras de caños metálicos pueden clasificarse en varios tipos según el método de curvado que emplean. Las de curvado rotativo, por ejemplo, utilizan un mandril y una matriz que giran para arrastrar el tubo mientras lo doblan, lo que resulta ideal para curvaturas cerradas o radios pequeños sin deformar la sección. Las de empuje, en cambio, utilizan rodillos que aplican una presión progresiva a lo largo del tubo, siendo más apropiadas para curvas amplias y caños de gran longitud. También existen curvadoras por tracción-inducción, que calientan el tubo localmente mediante inducción electromagnética antes de doblarlo, técnica útil para tubos de gran espesor o de materiales difíciles de curvar en frío.
Estas máquinas encuentran aplicación en sectores tan diversos como la fabricación de sistemas de escape y chasis en la industria automotriz, instalaciones de gas y fluidos en la construcción, fabricación de mobiliario metálico, estructuras de soporte en arquitectura, y sistemas hidráulicos en maquinaria pesada. En cada uno de estos casos, la precisión del curvado es crítica no solo por razones estéticas, sino porque una mala curvatura puede comprometer el paso de fluidos, la resistencia estructural o la correcta instalación de un sistema completo. Por eso, la elección de la curvadora adecuada depende no solo del diámetro y espesor del caño, sino también del nivel de precisión requerido, el tipo de material, la frecuencia de uso y el entorno de trabajo.
El mantenimiento preventivo también es esencial en estos equipos, ya que los componentes mecánicos están sometidos a esfuerzos considerables. La lubricación de los elementos móviles, la verificación periódica de los rodillos, la limpieza de los sensores y la calibración del sistema de control son prácticas fundamentales para asegurar el buen funcionamiento a largo plazo. Además, en ambientes industriales exigentes, muchas curvadoras están equipadas con sistemas de protección contra polvo, vibración o altas temperaturas, lo que permite integrarlas a líneas de producción automatizadas sin riesgo de interrupciones frecuentes.
Con la creciente demanda de productos personalizados y soluciones flexibles, las curvadoras de caños metálicos se han convertido en herramientas estratégicas en talleres y fábricas. La posibilidad de adaptar una misma máquina a distintos diámetros, longitudes y configuraciones ha favorecido su adopción tanto en pequeñas empresas como en grandes industrias. Esta versatilidad, combinada con un control cada vez más intuitivo y preciso, asegura que las curvadoras sigan siendo una pieza clave en la transformación del metal a medida que los estándares técnicos y estéticos de los proyectos se vuelven cada vez más exigentes. ¿Quieres que profundice en algún tipo de curvadora en particular, como las hidráulicas, CNC o manuales?
La evolución de las curvadoras de caños metálicos ha estado estrechamente ligada a las necesidades crecientes de las industrias por obtener piezas más complejas, con curvas precisas y de calidad uniforme. En la actualidad, estas máquinas no solo deben cumplir con los requisitos técnicos del curvado, sino también integrarse a entornos de producción inteligentes, donde la eficiencia, la trazabilidad y la repetibilidad son fundamentales. Muchas curvadoras modernas permiten integrarse a redes de fabricación digital, conectándose a sistemas de gestión de producción que controlan no solo el proceso de doblado, sino también el inventario de materiales, el seguimiento de lotes y el análisis del rendimiento de cada ciclo de producción. Esto ha transformado la curvadora de caños metálicos en una herramienta conectada, capaz de intercambiar datos en tiempo real con otras estaciones de trabajo, y adaptarse dinámicamente a cambios en la línea de producción sin detenerse ni requerir ajustes manuales.
Desde el punto de vista mecánico, el diseño de las curvadoras ha mejorado significativamente gracias al uso de materiales de alta resistencia en sus componentes estructurales, lo que les permite trabajar con tubos de gran diámetro y espesor sin perder precisión. La estabilidad del bastidor, la rigidez de los ejes de curvado y la alineación perfecta de los rodillos son esenciales para evitar deformaciones en el tubo durante el proceso. En modelos más avanzados, se incorporan sensores de carga y desplazamiento que monitorean la fuerza ejercida en cada instante del curvado, y ajustan automáticamente los parámetros si detectan una variación inesperada en la resistencia del material, como podría ocurrir con caños soldados o con diferencias de espesor a lo largo del tramo. Esta retroalimentación continua es lo que permite mantener estándares de calidad muy altos, incluso cuando se trabaja con materiales de lotes diferentes o con perfiles no uniformes.
El aspecto energético también ha ganado protagonismo, ya que las industrias buscan reducir el consumo y operar de forma más sostenible. Por esa razón, muchas curvadoras han reemplazado los sistemas hidráulicos convencionales por actuadores eléctricos de alta eficiencia que no solo consumen menos energía, sino que permiten una mayor precisión de movimiento, un control más fino de la velocidad y una respuesta más rápida ante cambios de configuración. Al mismo tiempo, estos sistemas generan menos ruido, requieren menos mantenimiento y eliminan el riesgo de fugas de aceite, lo que los hace especialmente atractivos en sectores como el alimentario, el farmacéutico o el electrónico, donde la limpieza del entorno es una condición crítica. Algunos fabricantes incluso han comenzado a desarrollar curvadoras híbridas que combinan los beneficios de la hidráulica y la servoelectrónica, ofreciendo así un equilibrio entre fuerza, velocidad y eficiencia energética.
El desarrollo de herramientas de simulación también ha cambiado la forma en que se planifican los procesos de curvado. Hoy es posible cargar el diseño digital del tubo que se quiere fabricar en el sistema de control de la curvadora, y simular virtualmente todo el proceso antes de hacer el primer movimiento físico. Esta simulación permite detectar posibles colisiones, errores de trayectoria, interferencias entre el tubo y la máquina, o puntos críticos de tensión que puedan dañar la pieza. Al prevenir estos errores antes de la producción, se reducen los desperdicios de material, se acortan los tiempos de configuración y se incrementa el aprovechamiento de la máquina. Además, esta capacidad de previsualización ayuda a los operadores menos experimentados a familiarizarse con el comportamiento del equipo y del material sin incurrir en costos de prueba.
En sectores donde la trazabilidad es obligatoria, como el aeroespacial, el ferroviario o el nuclear, las curvadoras de caños metálicos incluyen funciones de registro de datos que permiten guardar toda la información del proceso, como las fechas, los parámetros aplicados, el lote del material y los resultados de control dimensional. Esta información se puede exportar en forma de informes certificados que acompañan a cada pieza, lo cual es fundamental para garantizar la conformidad con normativas estrictas. Incluso en aplicaciones más comunes, como la fabricación de barandillas, muebles metálicos, sistemas de climatización o estructuras de acero para construcción, la posibilidad de verificar y documentar la calidad del proceso aporta un valor añadido importante que los clientes valoran.
A medida que los caños metálicos se emplean en nuevas aplicaciones y materiales, las curvadoras también deben adaptarse a desafíos técnicos distintos. Por ejemplo, al trabajar con tubos de acero inoxidable, el control del retorno elástico y la fricción superficial se vuelve crítico, ya que este material tiende a recuperar su forma más que otros y puede marcarse fácilmente si no se usan herramientas adecuadas. En el caso del aluminio, el riesgo es el colapso de la sección si se usa un radio de curvatura demasiado pequeño. Por eso, muchas curvadoras incorporan accesorios como mandriles internos, soportes de guía y matrices especiales que permiten mantener la sección del tubo durante el doblado, incluso en geometrías exigentes. Estos accesorios, que pueden ser fijos o retráctiles, juegan un papel decisivo en el éxito del curvado, y su correcta selección depende de una comprensión profunda de las propiedades del material, la forma del tubo y el diseño final requerido.
Así, la curvadora de caños metálicos ha pasado de ser una herramienta mecánica tradicional a convertirse en una plataforma tecnológica avanzada, capaz de integrarse a la cadena de producción, ofrecer gran versatilidad, adaptarse a múltiples materiales y proporcionar resultados de alta calidad de manera confiable y eficiente. Esta transformación no solo mejora la competitividad de las empresas que las utilizan, sino que amplía el horizonte de lo que puede diseñarse y fabricarse con tubos metálicos, impulsando la innovación en múltiples sectores industriales. ¿Quieres que continúe con más detalles sobre algún aspecto técnico o aplicación específica?
El desarrollo continuo de las curvadoras de caños metálicos también ha permitido la aparición de soluciones portátiles y compactas, ideales para trabajos en campo o en talleres pequeños donde no se justifica la instalación de equipos de gran tamaño. Estas versiones más reducidas pueden ser operadas manualmente o mediante accionamientos eléctricos, y son utilizadas habitualmente en instalaciones de sistemas hidráulicos, montajes industriales, mantenimiento de maquinaria o fabricación de prototipos. Aunque no alcanzan el nivel de automatización ni la precisión de los modelos industriales, estas curvadoras portátiles ofrecen la ventaja de la movilidad, la facilidad de uso y la adaptabilidad a espacios reducidos, siendo muy valoradas por técnicos y operarios que requieren una herramienta práctica y confiable en el lugar de trabajo.
Por otro lado, en la fabricación en serie de componentes tubulares para automóviles, bicicletas, estructuras metálicas y maquinaria agrícola, las curvadoras se integran a estaciones robotizadas donde cada operación está sincronizada. Estas celdas de producción pueden incluir alimentación automática del tubo, corte previo, curvado, inspección por visión artificial y apilamiento o empaque final. El objetivo es reducir al mínimo la intervención humana y maximizar la repetibilidad, incluso cuando se trabaja con geometrías complejas o con múltiples curvas en distintas direcciones. En este contexto, las curvadoras deben ser extremadamente rápidas, precisas y resistentes al desgaste, ya que se espera que funcionen durante ciclos prolongados sin interrupciones. Es común que cuenten con sistemas de refrigeración para evitar sobrecalentamientos, y con ejes servoaccionados que permiten posicionamientos exactos en cuestión de milisegundos.
En cuanto al diseño de las herramientas de curvado, también se han producido avances significativos. Las matrices, los insertos de sujeción y los mandriles son fabricados con aleaciones especiales tratadas térmicamente o recubiertas con capas duras para resistir la fricción, el desgaste y las altas cargas de trabajo. Además, cada vez más se diseñan con métodos de ingeniería asistida por computadora (CAE), lo que permite optimizar su forma antes de su fabricación, garantizando una mejor distribución de fuerzas durante el curvado. Esta optimización no solo mejora la calidad del tubo curvado, sino que también alarga la vida útil de los componentes y reduce los costos de mantenimiento.
El entrenamiento del personal que opera estas máquinas también ha evolucionado. Las empresas fabricantes suelen ofrecer formación técnica especializada, que incluye no solo el uso de la máquina, sino también conceptos de resistencia de materiales, análisis de geometrías, prevención de fallos por pandeo o colapso, y mantenimiento básico. En muchos casos, el software de control de la curvadora incorpora manuales interactivos, sistemas de diagnóstico automático y simuladores integrados que permiten capacitar al usuario sin riesgo de dañar piezas reales. Este enfoque ha contribuido a profesionalizar el oficio del operario de curvado, que hoy debe combinar habilidades técnicas, conocimiento de materiales y dominio de entornos digitales.
Finalmente, las exigencias de seguridad en el uso de curvadoras de caños metálicos también han crecido, y los fabricantes han respondido incorporando barreras fotoeléctricas, sistemas de paro automático, protección de ejes móviles y monitoreo de condiciones anormales. Estas medidas son clave, especialmente en equipos de gran potencia, donde un error de operación puede provocar accidentes graves. Las normativas internacionales, como las europeas EN o las estadounidenses OSHA, exigen que las máquinas cumplan con estándares específicos, lo que ha impulsado la incorporación de certificaciones de calidad y pruebas rigurosas en la fase de diseño y fabricación.
En conjunto, el panorama actual de las curvadoras de caños metálicos es el de una tecnología madura, versátil y en constante perfeccionamiento, que responde a los desafíos industriales con soluciones cada vez más sofisticadas. Estas máquinas no solo facilitan el trabajo con tubos metálicos de distintas formas, tamaños y materiales, sino que además se adaptan a una amplia variedad de entornos productivos, desde el taller artesanal hasta la línea de producción automatizada de alta velocidad. Gracias a su capacidad de combinar fuerza, precisión y control, continúan siendo una herramienta indispensable en cualquier proceso que requiera transformar un tubo recto en una pieza funcional y estética que cumpla con exigencias técnicas rigurosas.
Máquina de curvado de caños

La máquina de curvado de caños es un dispositivo especializado diseñado para modificar la geometría lineal de tubos metálicos sin comprometer su integridad estructural. Su propósito principal es formar curvas o ángulos específicos en caños cilíndricos o perfiles huecos, permitiendo que estos se ajusten a las exigencias del diseño mecánico, arquitectónico o industrial en que se emplearán. Esta máquina emplea principios de fuerza controlada, ya sea mediante sistemas manuales, hidráulicos, neumáticos, eléctricos o mixtos, y se adapta a materiales diversos como acero al carbono, acero inoxidable, aluminio, cobre o aleaciones técnicas, según el tipo de industria.
En su funcionamiento más básico, la máquina posiciona el caño entre una serie de herramientas: un dado principal de curvado, una matriz de sujeción y, en muchos casos, un mandril interno o un soporte de arrastre. El dado principal se mueve rotativamente o linealmente según el diseño de la máquina, y de esta forma el tubo es forzado a seguir la forma de la herramienta. Esta acción controlada permite formar curvas con radios definidos, manteniendo la sección transversal del tubo lo más intacta posible. Cuando la curvatura es muy cerrada, o el caño es de pared delgada, es necesario emplear mandriles internos o lubricación específica para evitar que se aplaste, colapse o se arrugue durante el proceso.
Existen múltiples tipos de máquinas de curvado de caños, cada una con ventajas específicas. Las manuales son ideales para tareas ligeras, ajustes en obra o trabajos artesanales, ya que permiten control directo y no requieren alimentación eléctrica. Las hidráulicas, en cambio, ofrecen una gran fuerza y precisión para caños de mayor espesor o materiales duros, siendo comunes en talleres metálicos o industrias pesadas. Las eléctricas y CNC (control numérico computarizado) representan la forma más avanzada de curvado, ya que permiten programar curvas complejas, realizar secuencias múltiples y almacenar configuraciones para producción en serie. Estas últimas se usan frecuentemente en industrias automotrices, aeroespaciales, navales y de mobiliario metálico.
Uno de los aspectos más críticos en el diseño y operación de estas máquinas es el control del radio de curvatura y la minimización del retorno elástico, que es la tendencia del material a recuperar parte de su forma original tras ser curvado. Cada metal tiene un comportamiento distinto ante la deformación plástica, y la máquina debe poder compensar automáticamente esta característica para asegurar que el ángulo final sea el exacto que requiere el diseño. Por ello, en equipos de mayor sofisticación, se incluye retroalimentación mediante sensores de desplazamiento, presión y fuerza, permitiendo corregir errores en tiempo real y reducir el desperdicio.
También es importante considerar el sistema de fijación del tubo, especialmente cuando se trabaja con longitudes grandes o múltiples radios de curvatura. Algunas máquinas están equipadas con sistemas de arrastre automático que guían el tubo a lo largo de la secuencia programada, evitando desplazamientos o torsiones que podrían desviar el resultado final. Además, en sectores donde el acabado superficial del tubo es importante, como en el diseño de muebles o estructuras visibles, se utilizan rodillos y dados recubiertos con materiales que evitan marcas o rayaduras, o bien se aplican lubricantes específicos que reducen la fricción.
En resumen, la máquina de curvado de caños es una solución esencial en el procesamiento de tubos metálicos, permitiendo transformar una materia prima recta en un componente funcional, estético y preciso. Su versatilidad la convierte en una herramienta clave en industrias muy diversas, y su evolución tecnológica ha permitido que los procesos de curvado sean hoy más eficientes, seguros y precisos que nunca. ¿Te interesa que desarrolle un ejemplo de aplicación práctica en algún sector, como la construcción, automoción o hidráulica?
En la actualidad, el uso de máquinas de curvado de caños ha llegado a niveles de especialización que permiten fabricar geometrías sumamente complejas con tolerancias mínimas, lo cual ha abierto nuevas posibilidades de diseño y ha permitido a muchas industrias optimizar el uso de espacio, materiales y ensamblaje. Por ejemplo, en la fabricación de sistemas de escape para automóviles, donde los caños deben adaptarse a espacios muy limitados y sortear otros componentes del vehículo, la curvadora de caños trabaja con coordenadas tridimensionales muy precisas, permitiendo doblar el tubo en varias direcciones y con distintos radios dentro de un mismo ciclo. Este tipo de trabajo solo puede realizarse con máquinas CNC equipadas con cabezales de giro y empuje simultáneo, sensores de ángulo y sistemas de corrección automática. A su vez, este proceso permite eliminar empalmes, reduciendo puntos de fuga, disminuyendo peso y facilitando el ensamblaje en línea.
Otro campo donde estas máquinas juegan un rol crucial es en la fabricación de intercambiadores de calor, radiadores y serpentines para sistemas de calefacción, refrigeración y procesos industriales. En estos casos, el caño debe ser curvado en múltiples bucles o formas helicoidales sin que se deforme el diámetro interior, ya que una mínima obstrucción puede afectar el rendimiento térmico. Para lograrlo, se recurre a curvadoras especializadas que utilizan mandriles segmentados, control de tracción y lubricación interna a presión. Estos sistemas permiten mantener el flujo interno óptimo sin comprometer la forma externa del caño, lo que es vital tanto desde el punto de vista funcional como energético. De hecho, muchas veces el diseño de estos componentes se hace en función de las capacidades de la curvadora, lo que demuestra hasta qué punto estas máquinas están integradas en la ingeniería de producto.
En términos de materiales, cada tipo de caño plantea desafíos distintos durante el curvado. El acero al carbono, por ejemplo, tiene buena ductilidad pero tiende a endurecerse si se trabaja en frío sin control de velocidad, lo que puede generar grietas o fatiga prematura. En contraste, el acero inoxidable es más resistente a la deformación, pero su retorno elástico es alto, lo que obliga a aplicar correcciones de ángulo más pronunciadas para alcanzar el resultado deseado. El aluminio, por su parte, es más propenso a aplanarse o formar pliegues si no se cuenta con matrices de apoyo bien diseñadas. Por esta razón, en muchas curvadoras avanzadas se puede ajustar no solo la velocidad y el ángulo, sino también la secuencia y la presión de los dados, con el fin de adaptar cada operación al comportamiento específico del material.
Además de los aspectos técnicos, la curvadora de caños también ha mejorado significativamente en términos de facilidad de uso y mantenimiento. Los modelos modernos incluyen interfaces táctiles intuitivas, software multilingüe, sistemas de autodiagnóstico que alertan sobre desgaste o necesidad de lubricación, y hasta conexiones remotas que permiten recibir asistencia técnica a distancia o actualizaciones del sistema de control. Estos avances hacen que incluso operadores con poca experiencia puedan utilizar la máquina de manera efectiva luego de una capacitación breve, lo que reduce los costos de operación y mejora la productividad del taller. Las funciones de memoria para recetas de curvado también son muy útiles cuando se trabaja en lotes pequeños pero repetitivos, ya que se pueden recuperar configuraciones pasadas con un solo comando y comenzar la producción sin ajustes adicionales.
En lo que respecta a la eficiencia productiva, la automatización de procesos dentro de la misma curvadora ha permitido acortar los ciclos de producción. Por ejemplo, algunas máquinas combinan curvado con corte, marcación por láser o incluso prensado de extremos, eliminando la necesidad de trasladar el caño a otras estaciones de trabajo. Esto no solo ahorra tiempo, sino que también minimiza los errores de manipulación y reduce el espacio necesario en el taller. En muchas plantas modernas, las curvadoras forman parte de líneas completas de trabajo donde el tubo entra como una barra recta y sale como un conjunto terminado listo para su montaje. Estas líneas están sincronizadas con sistemas de control central que supervisan producción, rendimiento y calidad, lo que permite tener un control total del proceso desde una única estación de monitoreo.
También cabe destacar la influencia que ha tenido la sostenibilidad en el diseño reciente de curvadoras de caños. Se ha puesto énfasis en la reducción del consumo energético, la eliminación de residuos peligrosos (como aceites hidráulicos usados) y la posibilidad de trabajar con materiales reciclados. Muchas máquinas modernas operan con servomotores de bajo consumo, están fabricadas con componentes reciclables, y permiten utilizar tubos provenientes de procesos de recuperación sin comprometer la calidad del curvado. Esto ha facilitado su adopción en industrias comprometidas con prácticas ambientales responsables, como la fabricación de bicicletas, estructuras para energías renovables, o mobiliario urbano sustentable.
La versatilidad de la máquina de curvado de caños, su capacidad de adaptación a distintos entornos industriales, y su evolución técnica constante, la han convertido en una herramienta indispensable no solo para la transformación del tubo, sino también para la concepción de nuevas soluciones de diseño. Gracias a estas máquinas, es posible fabricar estructuras livianas, resistentes y estéticamente atractivas que antes hubieran requerido piezas soldadas o componentes adicionales. Esta capacidad de simplificar, aligerar y mejorar la calidad final del producto explica por qué la curvadora sigue siendo un punto clave en cualquier proceso de manufactura que involucre tubos metálicos. ¿Deseas que amplíe más sobre su integración en líneas automatizadas o sobre el mantenimiento preventivo de estas máquinas?
La integración de las máquinas de curvado de caños en líneas automatizadas representa uno de los avances más significativos en la fabricación moderna, ya que permite una producción continua y sin interrupciones, reduciendo notablemente los tiempos de ciclo y los errores humanos. En una línea automatizada, la curvadora no opera como una unidad aislada, sino que se comunica con alimentadores automáticos que cargan los tubos desde paquetes o cintas transportadoras, con sistemas de medición que verifican longitudes y tolerancias antes del curvado, y con dispositivos de descarga o clasificación que apilan o etiquetan las piezas curvadas. Todo este conjunto se orquesta mediante un controlador central que ajusta dinámicamente los parámetros de operación, monitoriza el rendimiento de cada etapa y detecta cualquier desviación o fallo en tiempo real.
Esta integración también facilita la trazabilidad completa de cada componente fabricado. Cada tubo puede ser identificado mediante códigos grabados o etiquetas que contienen información sobre su lote de origen, fecha de fabricación, parámetros de curvado aplicados y resultados de las pruebas de calidad. Esto es especialmente importante en industrias reguladas, como la aeronáutica, el sector ferroviario o la producción de equipamiento médico, donde cada componente debe cumplir con normativas estrictas y es necesario garantizar la repetibilidad exacta de los procesos.
Desde el punto de vista del mantenimiento, las curvadoras modernas están diseñadas para minimizar tiempos de parada mediante estrategias de mantenimiento preventivo y predictivo. Los sensores incorporados en los motores, cilindros hidráulicos, rodillos y sistemas de arrastre recopilan datos sobre vibración, temperatura, presión y consumo eléctrico. Esta información se analiza constantemente para detectar señales tempranas de desgaste o fallo. En algunos modelos, estos datos se envían a la nube o a servidores internos, donde algoritmos especializados generan alertas para que el personal técnico realice las tareas de mantenimiento antes de que ocurra una falla crítica. Esto no solo evita costosos tiempos muertos, sino que extiende la vida útil de la máquina y reduce los gastos asociados al mantenimiento correctivo.
Otra tendencia importante en el mantenimiento de curvadoras es la modularidad. Muchos fabricantes diseñan sus máquinas con componentes intercambiables, de modo que si una parte sufre desgaste o requiere reparación, puede ser reemplazada rápidamente sin necesidad de desarmar todo el sistema. Esto es posible gracias a conexiones estandarizadas, sistemas de alineación automática y herramientas de diagnóstico que indican exactamente qué módulo necesita intervención. Incluso los programas de control pueden ser actualizados o corregidos de forma remota por el fabricante, agilizando la solución de problemas y manteniendo el equipo en óptimas condiciones sin importar su ubicación geográfica.
En cuanto a la seguridad operativa, las curvadoras modernas han evolucionado para cumplir con normas internacionales cada vez más exigentes. Las barreras fotoeléctricas, los botones de paro de emergencia, los resguardos físicos transparentes y los sistemas de enclavamiento evitan que el operador pueda estar en contacto con partes móviles durante el ciclo de curvado. Además, muchos controles incorporan sistemas de verificación que impiden iniciar la operación si alguna de las condiciones de seguridad no se ha cumplido. Esto protege tanto a los operarios como a la maquinaria, y asegura una operación continua sin contratiempos. En equipos de gran porte, como las curvadoras de caños estructurales para construcción, también se emplean sistemas de guiado por láser para el posicionamiento de tubos de gran longitud, lo que reduce el esfuerzo físico del operador y aumenta la precisión.
Además, no debe pasarse por alto el rol de la ergonomía en el diseño de estas máquinas. Las estaciones de trabajo con altura ajustable, controles intuitivos, interfaces gráficas simples y pantallas táctiles han mejorado significativamente la experiencia del operador. Esta atención al diseño ergonómico reduce la fatiga, disminuye la probabilidad de errores y hace que el trabajo sea más seguro y productivo. En las plantas donde se utilizan curvadoras durante turnos prolongados, esta característica resulta especialmente valiosa.
En definitiva, las curvadoras de caños actuales son mucho más que herramientas de deformación: son unidades inteligentes, conectadas, seguras y altamente adaptables que permiten a las industrias avanzar hacia modelos de producción más ágiles, sostenibles y precisos. Su capacidad de integrarse a líneas completas, de ofrecer calidad constante, de requerir un mantenimiento mínimo y de operar con seguridad en entornos exigentes, las consolida como una inversión fundamental para cualquier organización que trabaje con tubos metálicos en forma intensiva. Si te interesa, también puedo profundizar en las diferencias entre los métodos de curvado como el por tracción rotativa, por compresión o por enrollado. ¿Te gustaría seguir por esa línea?
Dobladora de tuberías
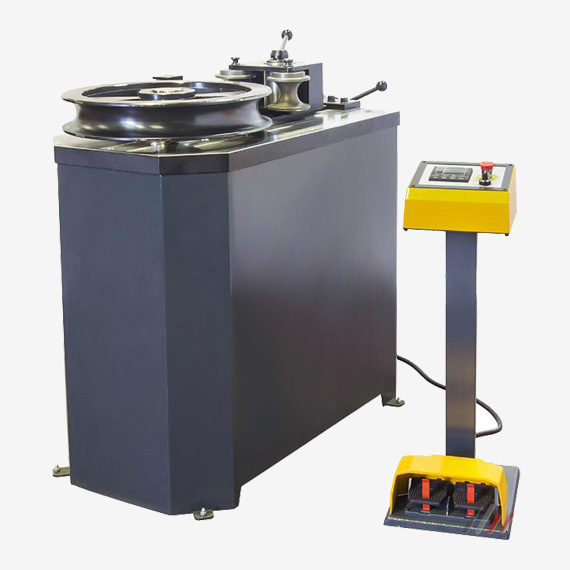
Una dobladora de tuberías es una máquina especializada en la operación de curvar tubos o caños, adaptándose a diversas formas y tamaños según el material y los requisitos del diseño. Estas máquinas son esenciales en diversas industrias, como la construcción, la automotriz, la hidráulica y la fabricación de estructuras metálicas. Las dobladoras de tuberías utilizan principios de fuerza controlada para cambiar la geometría de los tubos, permitiendo su incorporación en proyectos que requieren ángulos y curvas precisas. A continuación, te proporciono detalles sobre los diferentes aspectos y tipos de dobladoras de tuberías.
Tipos de dobladoras de tuberías
Existen varios tipos de dobladoras de tuberías, y cada una está diseñada para diferentes aplicaciones y capacidades:
- Dobladoras Manuales: Estas son las versiones más simples y económicas. Están diseñadas para trabajos ligeros y para tuberías de diámetro pequeño o mediano. Los operarios controlan la máquina de forma manual, y estas máquinas son comunes en talleres pequeños o en situaciones donde no se requieren grandes volúmenes de producción.
- Dobladoras Hidráulicas: Son muy utilizadas en talleres donde se necesita un alto rendimiento y fuerza. Utilizan la energía hidráulica para aplicar la presión necesaria para doblar tubos de mayor diámetro y espesor. Estas dobladoras permiten una mayor precisión y control en comparación con las manuales.
- Dobladoras Eléctricas: Estas dobladoras son automáticas y funcionan mediante motores eléctricos, lo que las hace ideales para trabajos de producción más rápida y precisa. Están equipadas con sistemas numéricos o controlados por computadora (CNC), lo que permite programar la máquina para doblar las tuberías con una precisión exacta y repetitiva. Este tipo de máquina es común en la industria automotriz y en la fabricación de equipos para sistemas de calefacción, ventilación y aire acondicionado (HVAC).
- Dobladoras CNC (Control Numérico Computarizado): Son las más avanzadas, con capacidad para programar de forma exacta los ángulos y radios de curvado. Estas máquinas permiten realizar trabajos de alta precisión, con tolerancias mínimas, y son ideales para aplicaciones en las que se requieren curvados complejos o en serie. Las dobladoras CNC permiten la programación de múltiples curvas, secuencias de curvado y la realización de proyectos a gran escala sin intervención humana.
Componentes y Funcionamiento
Las dobladoras de tuberías operan mediante una combinación de herramientas de sujeción y curvado, que trabajan en conjunto para aplicar presión de forma controlada. Los componentes principales de una dobladora de tuberías suelen incluir:
- Matriz o dado: Este es el componente que da forma a la tubería. El tubo es presionado contra la matriz, lo que obliga a la tubería a seguir la forma de la matriz mientras se curva.
- Mandril: En algunas dobladoras, se utiliza un mandril, especialmente en tuberías de paredes delgadas, para evitar que el tubo se colapse o se deforme internamente. El mandril se introduce en el interior de la tubería para proporcionar soporte durante el curvado.
- Rodillos de Sujeción: Estos rodillos mantienen la tubería en su lugar mientras la máquina aplica la presión necesaria para curvarla. A medida que el tubo es forzado a la forma deseada, estos rodillos ayudan a evitar que el tubo se deslice o se mueva de su posición.
- Motor y sistema de accionamiento: Dependiendo del tipo de dobladora, el motor puede ser hidráulico, eléctrico o neumático. El motor controla el movimiento de los rodillos, la matriz y otros componentes, aplicando la fuerza necesaria para el curvado.
- Controles y pantallas: Las máquinas de mayor tecnología suelen contar con pantallas digitales o interfaces de control donde el operario puede ingresar parámetros específicos de curvado, como el radio, el ángulo de la curva y la velocidad del proceso.
Materiales Usados
Las dobladoras de tuberías se utilizan en una variedad de materiales, cada uno con sus propias características. Los materiales más comunes incluyen:
- Acero al carbono: Es uno de los materiales más utilizados debido a su resistencia y versatilidad. Se emplea en aplicaciones generales de construcción y sistemas hidráulicos.
- Acero inoxidable: Su resistencia a la corrosión lo hace ideal para aplicaciones en entornos agresivos, como el sector químico o alimentario.
- Aluminio: Este material es más ligero que el acero y es utilizado en aplicaciones donde se requiere una menor carga y mayor resistencia a la fatiga, como en la industria automotriz.
- Cobre: Utilizado en sistemas de fontanería y HVAC, el cobre es flexible y resistente a la corrosión.
Aplicaciones
Las dobladoras de tuberías son utilizadas en diversas aplicaciones industriales, tales como:
- Construcción: Para la fabricación de estructuras metálicas, pasamanos, marcos y soportes.
- Automotriz: En la fabricación de sistemas de escape, chasis de vehículos, y componentes de vehículos de alto rendimiento.
- HVAC: En la fabricación de componentes de aire acondicionado, ventilación y sistemas de calefacción, como conductos de aire y tuberías de refrigerante.
- Sistemas hidráulicos y de gas: Fabricación de tuberías y conducciones que transportan fluidos a alta presión.
- Electrónica: En la fabricación de dispositivos electrónicos que requieren estructuras metálicas curvadas o tubos de precisión para cables y conexiones.
Ventajas de las Dobladoras de Tuberías
Las dobladoras de tuberías modernas ofrecen una serie de ventajas sobre métodos más tradicionales de curvado:
- Precisión: Permiten conseguir curvados exactos con tolerancias mínimas, lo que es crucial para aplicaciones donde la geometría es vital para el funcionamiento del sistema.
- Versatilidad: Son capaces de curvar una amplia gama de materiales y tamaños de tubo, adaptándose a diferentes industrias y necesidades.
- Automatización: Las versiones CNC permiten programar lotes de producción sin intervención manual, lo que mejora la eficiencia y reduce el riesgo de errores.
- Reducción de desperdicios: Gracias a la precisión en el curvado, se minimizan los residuos y se optimiza el uso de material, reduciendo costos y desperdicios.
- Mejora en la seguridad: Las modernas dobladoras incluyen sistemas de protección y controles de seguridad que minimizan los riesgos para los operadores.
En resumen, las dobladoras de tuberías son herramientas fundamentales en muchas industrias que trabajan con tubos metálicos. Su capacidad para curvar materiales con precisión, rapidez y eficiencia hace que sean esenciales para la fabricación de componentes metálicos complejos, ofreciendo una solución fiable y rentable para el procesamiento de tuberías en diversas aplicaciones industriales.
Las dobladoras de tuberías no solo mejoran la productividad, sino que también juegan un papel clave en la optimización de los procesos de fabricación. Estas máquinas permiten una mayor flexibilidad en términos de diseños, lo que facilita la creación de componentes complejos y personalizados. Además, la capacidad de automatizar el proceso de curvado con control numérico y la integración en líneas de producción automatizadas ha permitido reducir el tiempo de fabricación y aumentar la eficiencia operativa. En particular, las curvadoras de tubos automáticas y CNC permiten realizar varios curvados de alta precisión en un solo ciclo de producción, lo que ahorra tiempo y costos de mano de obra al eliminar la necesidad de cambiar configuraciones o ajustar la máquina para cada pieza.
Otra ventaja importante es la reducción de errores y defectos en el proceso de curvado. Las máquinas más avanzadas cuentan con sistemas de control de calidad integrados, que incluyen sensores y cámaras que monitorean el curvado en tiempo real, ajustando automáticamente los parámetros de curvado en caso de desviaciones. Esto garantiza que cada tubo curvado cumpla con las especificaciones exactas, minimizando la posibilidad de defectos que puedan afectar la integridad del producto final.
Además, las dobladoras de tuberías también están evolucionando en términos de sostenibilidad. Muchas de las máquinas más recientes están diseñadas para ser más eficientes en términos de consumo de energía, lo que ayuda a reducir los costos operativos y la huella de carbono. Además, al permitir una mayor precisión en el proceso de curvado, las máquinas modernas minimizan los desperdicios de material, lo que contribuye a un uso más eficiente de los recursos y una producción más ecológica.
El mantenimiento también ha mejorado con los avances tecnológicos. Las dobladoras de tubos de última generación están equipadas con sistemas de monitoreo que detectan desgaste, falta de lubricación o posibles fallas mecánicas antes de que se conviertan en problemas graves. Esto permite a los operadores realizar un mantenimiento preventivo, lo que reduce el riesgo de paradas imprevistas y prolonga la vida útil de la máquina. Las funciones de diagnóstico remoto también permiten a los fabricantes realizar reparaciones y actualizaciones a distancia, lo que ayuda a mantener la producción en marcha sin interrupciones.
En cuanto a la seguridad, las máquinas de curvado de tubos también han avanzado significativamente. Las nuevas tecnologías incluyen características como sensores de proximidad, sistemas de parada de emergencia, barreras de protección y pantallas de control que garantizan que los operadores no estén expuestos a riesgos durante el proceso de curvado. Estos avances no solo protegen a los trabajadores, sino que también contribuyen a crear un ambiente de trabajo más eficiente y seguro.
Por último, la versatilidad de las dobladoras de tubos también se refleja en su capacidad para adaptarse a una variedad de aplicaciones. Pueden curvar tubos de diferentes materiales, como acero inoxidable, aluminio, cobre, y otros metales, cada uno con sus propias propiedades y desafíos. Los operadores pueden ajustar la presión, la velocidad y los ángulos de curvado según el material, lo que permite trabajar con una amplia gama de especificaciones. Esto ha abierto nuevas oportunidades para la fabricación de productos que requieren curvados de alta precisión, como en la fabricación de intercambiadores de calor, componentes de sistemas de plomería y piezas estructurales para la industria automotriz y aeronáutica. La habilidad para trabajar con diversos materiales y tamaños de tubo, así como la capacidad de adaptarse a diferentes tipos de curvados, ha hecho que las dobladoras de tubos sean una inversión crucial para muchas industrias, asegurando que las empresas puedan producir productos de alta calidad, eficientes y rentables.
La capacidad de adaptarse a diferentes necesidades industriales también ha llevado a que las dobladoras de tuberías se vuelvan más especializadas en función de los tipos de trabajos que deben realizar. Por ejemplo, algunas máquinas están específicamente diseñadas para trabajar con tubos de gran diámetro o tubos de paredes gruesas, mientras que otras son más adecuadas para trabajos finos o detalles más precisos, como en la fabricación de componentes para la industria electrónica o la aviación. Esta especialización también ha sido posible gracias a avances en el diseño y la fabricación de las matrices y rodillos de curvado, que son intercambiables y personalizables según el tipo de tubo que se vaya a procesar.
El aspecto de la automatización ha revolucionado la forma en que se gestionan las líneas de producción. Las dobladoras modernas están equipadas con sistemas de gestión de datos que permiten la recolección y el análisis de información en tiempo real, lo que facilita la toma de decisiones rápidas y fundamentadas. Los operarios pueden acceder a información detallada sobre el rendimiento de la máquina, las tasas de producción, el estado de los materiales y los resultados de las pruebas de calidad, lo que les permite optimizar los procesos y mejorar la calidad del producto final. Este enfoque de “Industria 4.0” no solo mejora la eficiencia, sino que también facilita la trazabilidad completa de los productos, permitiendo que las empresas cumplan con los estándares de calidad y regulación.
En términos de aplicaciones más avanzadas, las dobladoras de tuberías están comenzando a integrarse con otras tecnologías como la robótica. Los robots industriales pueden cargar y descargar las tuberías de la máquina de curvado de manera autónoma, lo que aumenta la velocidad del proceso y minimiza el riesgo de error humano. Esta integración de robótica y automatización también permite la fabricación de componentes complejos con una mayor precisión y sin la necesidad de intervención manual, lo que se traduce en una mayor competitividad y reducción de costos operativos. Además, esta integración también permite que las máquinas se adapten a una producción más flexible y en lotes pequeños, lo cual es crucial para satisfacer las demandas del mercado actual, donde las personalizaciones y los cambios rápidos en el diseño son comunes.
Otro aspecto importante de las dobladoras modernas es su capacidad para trabajar de manera más eficiente con las condiciones de trabajo exigentes. En entornos industriales donde las condiciones de temperatura y humedad pueden variar, o donde se requieren velocidades de producción más altas, las dobladoras avanzadas están diseñadas para operar con fiabilidad en condiciones extremas. Esto se logra mediante el uso de materiales de alta calidad, sistemas de refrigeración mejorados y componentes de alto rendimiento que pueden resistir el desgaste y las condiciones de trabajo difíciles, garantizando un funcionamiento continuo y sin fallos.
La flexibilidad también se ha mejorado gracias a la posibilidad de personalizar las dobladoras para tareas específicas, como curvar tubos con formas no estándar o realizar curvados en ángulos complejos, lo que antes era un desafío. Esto es especialmente útil en sectores como la fabricación de equipos médicos, donde las especificaciones a menudo requieren curvas no convencionales, o en la industria de la energía, donde los sistemas de tuberías pueden tener geometrías complejas para adaptarse a las infraestructuras existentes.
Con el paso del tiempo, también ha habido un enfoque más consciente hacia la sostenibilidad en el diseño y operación de las dobladoras de tuberías. La reducción de residuos de material, la eficiencia energética y la reducción de emisiones en las plantas de producción han sido aspectos clave que los fabricantes de maquinaria han tenido en cuenta. Muchas dobladoras ahora incorporan tecnologías que mejoran la eficiencia energética, como motores de bajo consumo y sistemas de recuperación de energía, lo que ayuda a reducir tanto el costo operativo como el impacto ambiental. Esto es cada vez más importante a medida que las normativas ambientales se vuelven más estrictas y las empresas buscan alinear sus operaciones con prácticas de sostenibilidad.
La conectividad de estas máquinas también se está convirtiendo en una característica estándar. Las soluciones de Internet de las Cosas (IoT) están empezando a integrarse en las dobladoras de tubos, lo que permite la monitorización remota y el control del proceso de curvado a través de dispositivos móviles o computadoras. Los operadores pueden revisar el estado de la máquina, recibir alertas en tiempo real sobre el mantenimiento y optimizar los parámetros de la máquina para garantizar que el proceso de curvado se realice de manera eficiente y sin interrupciones. Esta conectividad abre la puerta a un monitoreo y mantenimiento más ágiles, lo que a su vez aumenta la disponibilidad de la máquina y reduce los tiempos de inactividad no programados.
Por último, la tendencia hacia la personalización de la maquinaria sigue creciendo. Las empresas que necesitan tuberías curvadas para proyectos específicos pueden ahora solicitar máquinas con características personalizadas que se adapten a las necesidades exactas de su producción. Esto va desde modificaciones en la configuración de las matrices hasta la creación de sistemas completamente adaptados que permitan una producción eficiente de tuberías para aplicaciones muy especializadas, como en la industria aeroespacial o la fabricación de estructuras de energía renovable. Este nivel de personalización está permitiendo a las empresas ofrecer soluciones más específicas y diferenciadas en el mercado.
En resumen, las dobladoras de tuberías han evolucionado desde máquinas simples para trabajos manuales hasta equipos avanzados que forman parte integral de líneas de producción automatizadas y altamente eficientes. La continua mejora de la precisión, la automatización, la sostenibilidad y la adaptabilidad de estas máquinas las convierte en piezas clave en la fabricación moderna de componentes metálicos, permitiendo a las empresas adaptarse a las demandas de la industria y ofrecer productos de alta calidad con mayor rapidez y eficiencia.
Curvadora de tubos metálicos
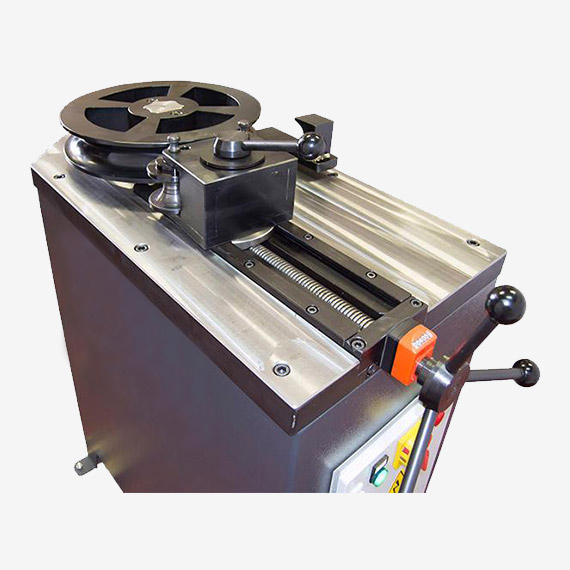
Una curvadora de tubos metálicos es una máquina especializada en la curvatura de tubos de diferentes materiales metálicos, como acero, acero inoxidable, aluminio y cobre, entre otros. Estas máquinas están diseñadas para aplicar una fuerza controlada para cambiar la forma de los tubos, permitiendo que se adapten a las especificaciones de diversos proyectos en diferentes industrias. Dependiendo de su tipo y características, las curvadoras de tubos metálicos se utilizan para crear componentes de sistemas hidráulicos, estructuras metálicas, conductos de aire, sistemas de refrigeración, y muchas otras aplicaciones.
Estas máquinas utilizan un proceso de curvado preciso para evitar deformaciones indeseadas en los tubos, manteniendo sus propiedades estructurales y estéticas. Las curvadoras de tubos metálicos tienen diversas configuraciones y tecnologías, y su elección depende de las necesidades específicas del trabajo y de los materiales que se vayan a curvar.
Tipos de curvadoras de tubos metálicos
- Curvadoras Manuales: Son las más simples y económicas, adecuadas para trabajos de menor escala o para tubos de diámetros pequeños y medianos. Estas máquinas permiten al operador controlar el proceso de curvado manualmente, generalmente a través de palancas o volantes. Aunque tienen limitaciones en cuanto a precisión y capacidad, siguen siendo útiles para tareas básicas o en talleres pequeños.
- Curvadoras Hidráulicas: Estas máquinas emplean energía hidráulica para proporcionar la fuerza necesaria para curvar tubos de mayor diámetro y espesor. Las curvadoras hidráulicas son más precisas y eficaces que las manuales, permitiendo realizar trabajos más complejos y de mayor volumen. Son muy comunes en industrias que requieren un alto nivel de precisión, como la automotriz, la construcción, y la manufactura de componentes para sistemas HVAC.
- Curvadoras Eléctricas o CNC (Control Numérico Computarizado): Las curvadoras de tubos CNC permiten programar el proceso de curvado con una precisión muy alta. Estas máquinas son capaces de curvar tubos en una variedad de formas y ángulos de manera completamente automática. Los operarios pueden ingresar las especificaciones en un sistema de control y la máquina realiza el proceso de manera exacta y repetitiva. Las curvadoras CNC son ideales para producciones en masa o para piezas que requieren altos estándares de precisión, como en la fabricación de tubos para la industria aeronáutica o electrónica.
- Curvadoras de Mandril: En algunas aplicaciones, especialmente cuando se curvan tubos de paredes finas, se utiliza un mandril para evitar que el tubo se deforme o colapse internamente. El mandril se inserta dentro del tubo durante el curvado para ofrecer soporte adicional, lo que permite curvados más estrictos sin comprometer la integridad del tubo.
Funcionamiento de una curvadora de tubos metálicos
Las curvadoras de tubos metálicos funcionan mediante un sistema de rodillos, matrices y, en algunos casos, mandriles, que aplican fuerza al tubo para darle la forma deseada. El tubo se coloca en una serie de rodillos o entre dos matraces que lo presionan para curvarlo. El tubo puede ser curvado a lo largo de su eje, creando una curva con un radio determinado, o puede ser doblado en diferentes ángulos, dependiendo de las especificaciones requeridas.
El proceso generalmente sigue estos pasos básicos:
- Sujeción: El tubo se coloca en la máquina, donde se fija con rodillos o pinzas para evitar que se deslice durante el curvado.
- Aplicación de Fuerza: A través de un sistema hidráulico, eléctrico o manual, se aplica la fuerza necesaria sobre el tubo para comenzar el proceso de curvado. Los rodillos o matrices guían el tubo mientras se curva.
- Curvado: A medida que la máquina aplica presión, el tubo comienza a adoptar la forma deseada, con la fuerza distribuida uniformemente para evitar deformaciones excesivas.
- Control y Precisión: En las curvadoras más avanzadas, los controles numéricos y sistemas automatizados permiten al operador ajustar la velocidad de curvado, los ángulos y el radio de la curva para garantizar que el producto final cumpla con las especificaciones exactas.
Aplicaciones comunes
Las curvadoras de tubos metálicos son herramientas esenciales en una variedad de industrias, tales como:
- Industria Automotriz: Se utilizan en la fabricación de sistemas de escape, chasis, estructuras metálicas y otros componentes que requieren curvado preciso de tubos de acero o aluminio.
- HVAC: En la fabricación de conductos de aire, sistemas de refrigeración y calefacción, donde se requieren tubos curvados para adaptarse a los diseños de edificios y sistemas industriales.
- Energía: Las curvadoras de tubos metálicos son cruciales en la fabricación de componentes para centrales eléctricas, intercambiadores de calor y sistemas de tuberías a gran escala.
- Construcción: Se utilizan para fabricar estructuras metálicas y marcos, donde los tubos curvados se usan en la creación de pasamanos, barandas, columnas y otras aplicaciones arquitectónicas.
- Aeronáutica: En la fabricación de aviones y componentes aeroespaciales, las curvadoras permiten trabajar con tubos y conductos complejos que deben cumplir con estrictos estándares de precisión.
- Gas y Petróleo: En la industria de extracción y distribución de gas y petróleo, las curvadoras de tubos se utilizan para crear tuberías de gran diámetro y espesor que se utilizan en sistemas de transporte de fluidos a presión.
Ventajas de las curvadoras de tubos metálicos
- Precisión: Las curvadoras de tubos modernas, especialmente las controladas por CNC, ofrecen una gran precisión en el curvado de tubos, lo que es crucial para aplicaciones en las que el ajuste exacto es vital.
- Versatilidad: Estas máquinas pueden trabajar con una amplia gama de materiales, diámetros y espesores, lo que las hace adecuadas para una gran variedad de aplicaciones industriales.
- Reducción de Desperdicios: Al realizar curvados precisos, se reduce la cantidad de material desperdiciado, lo que optimiza el uso de recursos y reduce los costos.
- Automatización: Las versiones CNC y automatizadas permiten producir lotes de piezas a gran escala con mínima intervención humana, mejorando la eficiencia y reduciendo los errores.
- Eficiencia: Las curvadoras hidráulicas y CNC permiten realizar curvados de alta calidad a alta velocidad, lo que aumenta la capacidad de producción sin sacrificar la precisión.
Desafíos y Consideraciones
Si bien las curvadoras de tubos metálicos son herramientas extremadamente útiles, también presentan algunos desafíos. El curvado de tubos metálicos es un proceso que depende de una correcta gestión de la presión y la temperatura para evitar la deformación del material o la pérdida de sus propiedades mecánicas. Además, los tubos de materiales como el acero inoxidable o el aluminio pueden requerir parámetros de curvado específicos para evitar problemas como el agrietamiento o la expansión excesiva de la pared del tubo.
El mantenimiento adecuado de las curvadoras es también fundamental para garantizar un rendimiento eficiente a largo plazo. Las piezas móviles deben ser lubricadas regularmente, y el sistema hidráulico o eléctrico debe ser monitoreado para evitar fallos que puedan interrumpir la producción.
En conclusión, las curvadoras de tubos metálicos son herramientas esenciales en la fabricación de componentes industriales, ofreciendo precisión, eficiencia y versatilidad en una amplia gama de aplicaciones. La elección de la máquina adecuada dependerá de factores como el tipo de material, el diámetro del tubo y las especificaciones del proyecto, lo que permite a las empresas producir componentes metálicos curvados con alta calidad y en menor tiempo.
Estas máquinas, además de su robustez y versatilidad, han evolucionado para satisfacer una demanda creciente de soluciones más precisas, eficientes y seguras en entornos industriales cada vez más exigentes. Las curvadoras de tubos metálicos no solo cumplen una función técnica, sino que también representan una inversión estratégica para las empresas que buscan optimizar sus procesos de fabricación. La confiabilidad en la repetitividad de los curvados permite reducir significativamente los errores en la producción y los costos asociados a reprocesos o desperdicio de material. Asimismo, las mejoras en la interfaz de usuario han simplificado el trabajo del operador, permitiendo que incluso quienes tienen poca experiencia puedan realizar curvados complejos con una curva de aprendizaje mucho menor que en décadas anteriores. Las pantallas táctiles, los sistemas de previsualización del curvado y los controles automatizados integrados permiten una interacción más fluida entre el operario y la máquina.
En muchas industrias, la implementación de curvadoras de tubos metálicos ha sido clave para mejorar el diseño de productos, ya que permite mayor libertad geométrica en la concepción de estructuras tubulares. Esto se traduce en productos más eficientes desde el punto de vista estructural, estético y funcional. Por ejemplo, en la industria del mobiliario metálico, estas máquinas permiten crear sillas, mesas y estanterías con formas curvas que no solo son visualmente atractivas, sino también más cómodas y resistentes. Del mismo modo, en el sector del transporte ferroviario, los tubos curvados con gran precisión son fundamentales para la seguridad y la aerodinámica de los vagones, lo que impacta directamente en el rendimiento energético y la experiencia del usuario.
Otro punto importante es la capacidad de adaptación de estas máquinas a diferentes entornos de producción. Hay curvadoras compactas diseñadas para talleres pequeños, donde el espacio es limitado pero se requiere una alta calidad de curvado, y también hay equipos industriales de gran escala con líneas de producción integradas, capaces de curvar varios tubos al mismo tiempo o realizar múltiples operaciones sin necesidad de cambiar el material de estación. Este nivel de adaptabilidad ha hecho que las curvadoras sean adoptadas no solo por grandes industrias, sino también por pymes y fabricantes independientes que necesitan flexibilidad para adaptarse a los cambios del mercado y a las necesidades de sus clientes.
La seguridad operativa también ha sido una prioridad en el diseño de curvadoras modernas. Equipadas con sensores, sistemas de parada automática y barreras físicas, estas máquinas reducen drásticamente el riesgo de accidentes laborales. Algunas versiones incluso incorporan sistemas de monitoreo continuo que detectan anomalías en la presión, la temperatura o el posicionamiento del tubo, y detienen el proceso si se detecta una condición insegura. Esto, junto con los sistemas de mantenimiento predictivo basados en datos de operación, prolonga la vida útil de la máquina y evita paradas imprevistas que puedan interrumpir el flujo de producción.
Además de su función principal, muchas curvadoras modernas ofrecen características adicionales como el corte, el abocardado o el estampado de tubos, lo que permite integrar varias operaciones en una sola estación de trabajo. Esta capacidad de realizar múltiples procesos en una única máquina mejora el flujo de producción y reduce los tiempos de manipulación del material, aumentando la eficiencia global de la planta. También es relevante mencionar que el software asociado a estas máquinas ha avanzado significativamente, permitiendo simular previamente el curvado, calcular los parámetros óptimos y almacenar configuraciones específicas para diferentes proyectos, lo cual es ideal para producciones seriadas.
Con la constante innovación tecnológica, el futuro de las curvadoras de tubos metálicos apunta hacia una mayor autonomía, una mayor capacidad de autoajuste y una integración más profunda en sistemas de fabricación inteligente. Se espera que el aprendizaje automático y la inteligencia de datos desempeñen un papel más importante en la optimización del proceso, identificando patrones en los errores de curvado o en el desgaste de los componentes, y ajustando los parámetros automáticamente para evitar fallos antes de que ocurran. Todo esto contribuirá a un entorno de producción más ágil, eficiente y sostenible, alineado con las exigencias del mercado global.
A medida que estas máquinas continúan perfeccionándose, también lo hacen los materiales que se curvan. La evolución en los tubos metálicos, como los aceros de alta resistencia, las aleaciones ligeras y los materiales con tratamientos térmicos específicos, plantea nuevos desafíos que exigen a las curvadoras una mayor capacidad de adaptación y control. Esto significa que los fabricantes de equipos de curvado no solo deben centrarse en la fuerza o la velocidad de la máquina, sino también en su sensibilidad para trabajar con materiales que pueden ser más frágiles o más exigentes en cuanto a parámetros de flexión, recuperación elástica y resistencia al colapso. Las curvadoras que integran retroalimentación automática sobre la fuerza aplicada y la forma obtenida permiten trabajar con estos materiales de forma segura y eficiente.
La trazabilidad también ha cobrado una importancia creciente en los procesos industriales modernos, y en este sentido, muchas curvadoras actuales incorporan sistemas que registran todos los datos relevantes de cada operación: ángulo, radio de curvatura, presión utilizada, lote de material, número de pieza, fecha y hora, entre otros. Esta información es esencial no solo para el control de calidad, sino también para cumplir con normativas internacionales o requerimientos específicos de sectores regulados, como el aeroespacial o el médico. Además, este nivel de trazabilidad facilita el diagnóstico de errores, la auditoría de procesos y la mejora continua dentro de un sistema de gestión de calidad.
En términos de mantenimiento, los avances tecnológicos han permitido desarrollar sistemas de diagnóstico a bordo que alertan al operario cuando se requiere una intervención, ya sea por desgaste de componentes, necesidad de lubricación o ajuste de piezas. Algunas máquinas incluso están preparadas para conectarse remotamente con el servicio técnico del fabricante, lo que permite una asistencia inmediata, análisis de fallos en tiempo real y actualizaciones de software sin necesidad de interrumpir el trabajo prolongadamente. Esto resulta especialmente útil en plantas donde las paradas no planificadas pueden tener un alto impacto económico.
En lo que respecta al diseño mecánico, las curvadoras modernas se han vuelto más ergonómicas y compactas. Esto no solo mejora la experiencia del usuario, reduciendo la fatiga y el esfuerzo físico, sino que también permite una mejor integración en entornos donde el espacio es limitado. Las mejoras en el aislamiento de vibraciones, la reducción del ruido y la eficiencia energética contribuyen a que estas máquinas sean más adecuadas para un uso intensivo sin comprometer la salud de los operarios ni el entorno de trabajo. La eficiencia energética, en particular, se ha vuelto una prioridad para muchas empresas que buscan reducir su huella de carbono sin perder competitividad.
Por último, es importante destacar que la formación del personal que opera estas máquinas ha ganado peso en la estrategia industrial. Una curvadora avanzada solo puede desplegar todo su potencial si está en manos de operadores capacitados, capaces de interpretar planos técnicos, ajustar parámetros con precisión y reconocer señales de alerta antes de que se conviertan en problemas. Por ello, muchos fabricantes ofrecen programas de formación y certificación, así como manuales interactivos y sistemas de asistencia en línea, que permiten acortar los tiempos de puesta en marcha y asegurar un uso óptimo desde el primer momento.
Así, la curvadora de tubos metálicos, lejos de ser una máquina aislada, se convierte en una pieza clave dentro del ecosistema de fabricación moderna, articulando precisión mecánica, control inteligente y adaptabilidad operativa. Su relevancia seguirá creciendo en la medida que los procesos industriales demanden mayor personalización, menores tiempos de respuesta y una calidad constante en todos los niveles de producción.
Máquinas Formadoras de Metales EMS
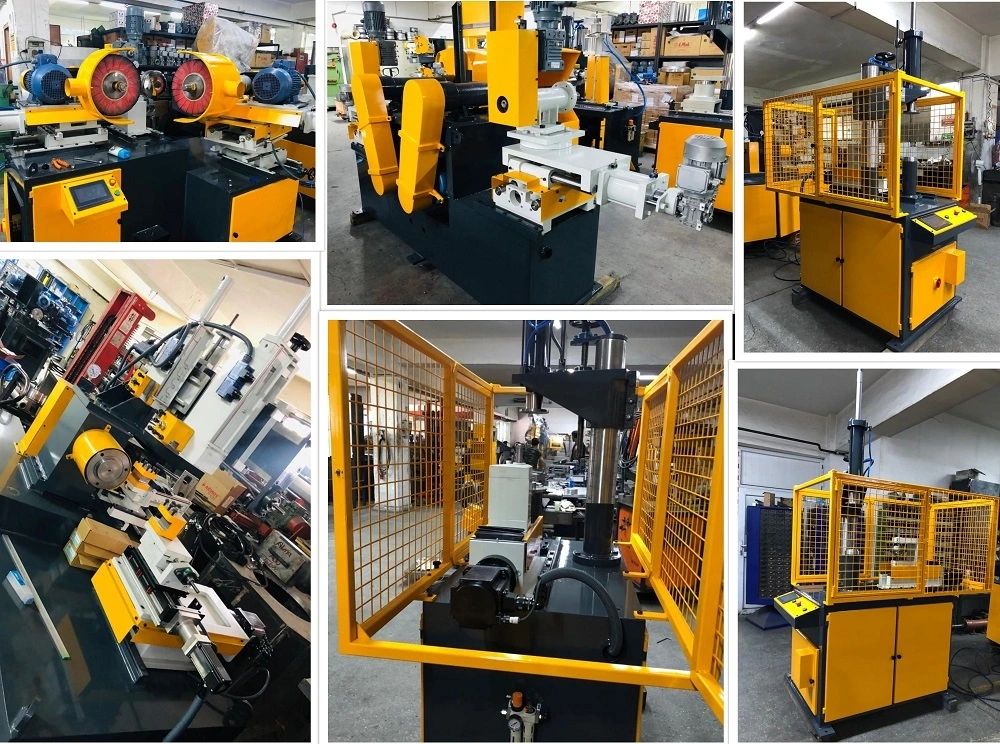
Diseñamos, fabricamos y montamos maquinaria metalmecánica como:
Prensa de transferencia hidráulica
Prensa para mosaicos de vidrio
Prensa hidráulica de embutición profunda
prensa de fundición
Prensa hidráulica de conformado en frío
Prensa de hidroformado
prensa compuesta
Prensa de moldeo de caucho de silicona
Prensa de pastillas de freno
Prensa de melamina
Prensa SMC y BMC
prensa labrotaroy
Máquina cortadora de bordes
Máquina rizadora de bordes
Máquina recortadora de abalorios
Máquina de recorte y jogging
Línea de producción de utensilios de cocina.
Máquina dobladora de tubos
Máquina dobladora de perfiles
Sierra de cinta para metal
Máquina de soldar cilíndrica
Prensas horizontales y utensilios de cocina.
Menaje de cocina, artículos de hotelería
Maquinaria para la producción de utensilios para hornear y cubiertos.
como una línea completa así como una máquina individual como:
Máquinas cortadoras de bordes y biseladoras
Pulidoras y rectificadoras de ollas y sartenes.
Prensas hidráulicas de trefilado
Máquinas troqueladoras circulares
remachadora
Punzonadoras
Máquina de alimentación de prensa
Puede consultar nuestra maquinaria en funcionamiento en: EMS Máquinas Formadoras de Metales EMS – YouTube
Aplicaciones:
Punzonado de bridas
Abalorios y nervaduras
Bridas
Guarnición
Curling
costura de bloqueo
Nervaduras