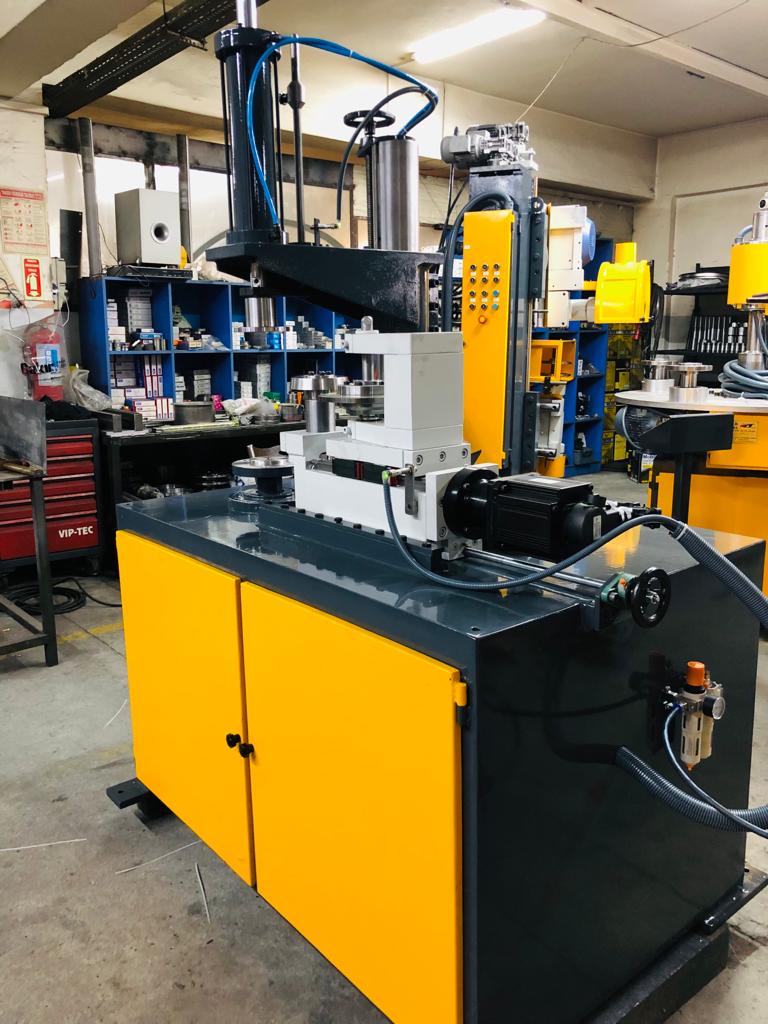
Bordonadora Biseladora de Lamina: La metalurgia es una de las industrias más antiguas y fundamentales en el desarrollo de la civilización humana. Desde la creación de herramientas simples hasta los complejos procesos industriales modernos, el trabajo con metales ha permitido a las sociedades construir infraestructuras, vehículos, maquinaria, y una infinidad de productos que forman parte integral de la vida diaria.
Cuando hablamos del trabajo con láminas metálicas, estamos refiriéndonos a un conjunto de procesos que permiten transformar, moldear y manipular el metal en formas y tamaños útiles para una amplia gama de aplicaciones industriales. Estos procesos incluyen desde el corte y doblado hasta la deformación profunda, el embutido y el rebordeado, utilizando máquinas y herramientas especializadas para lograr una alta precisión y acabados de calidad.
Importancia del trabajo con estructuras metálicas en la industria
En la actualidad, las estructuras metálicas son parte esencial en la construcción de edificios, puentes, maquinaria pesada, y vehículos. El acero, el aluminio y otras aleaciones metálicas son materiales que ofrecen una combinación única de resistencia, durabilidad y flexibilidad para soportar grandes cargas sin comprometer la estabilidad de la estructura. Esta versatilidad hace que el metal sea el material elegido para proyectos que requieren confiabilidad a largo plazo y resistencia a las condiciones ambientales.
En industrias como la automotriz, la aeronáutica, la construcción y la fabricación de electrodomésticos, la capacidad de manipular con precisión las láminas de metal es crucial. La creación de componentes ligeros pero resistentes, así como la necesidad de formas geométricas complejas, han impulsado la evolución de tecnologías de conformado y ensamblaje cada vez más sofisticadas.
Aplicaciones comunes del trabajo con metales
Las aplicaciones del trabajo con metales son amplias y variadas, y abarcan diversas industrias:
- Construcción y arquitectura: Desde vigas de acero hasta marcos y soportes, los metales forman la base de las estructuras modernas. Además, la manipulación de láminas permite crear fachadas, techos y otras estructuras decorativas.
- Industria automotriz: Las láminas metálicas son esenciales para la fabricación de carrocerías, paneles y componentes del motor. Procesos como el embutido profundo son esenciales para producir piezas que no solo sean ligeras, sino también resistentes a los impactos.
- Aeronáutica: En la fabricación de aviones, los materiales metálicos como el aluminio se trabajan en láminas para crear fuselajes, alas y otras partes críticas. La precisión en el trabajo es vital debido a las estrictas normativas de seguridad y rendimiento.
- Fabricación de electrodomésticos: Los productos cotidianos como refrigeradores, lavadoras y estufas dependen del trabajo con láminas metálicas para sus carcasas, paneles y componentes internos.
- Industrias de envases: El uso de metales en la creación de latas, recipientes de alimentos y envases de bebidas ha sido revolucionario, con procesos como el embutido profundo que permiten producir millones de unidades con un alto grado de eficiencia.
Principios básicos de la deformación y manipulación del metal
El trabajo con láminas metálicas implica un conocimiento profundo de las propiedades físicas del metal. Estos materiales pueden comportarse de manera diferente según la temperatura, la presión y las fuerzas aplicadas. Los principales procesos de manipulación y deformación del metal se basan en los siguientes principios:
- Ductilidad y maleabilidad: Estos son dos de los atributos más importantes de los metales cuando se trata de trabajarlos. La ductilidad se refiere a la capacidad de un metal de estirarse sin romperse, lo que es esencial en procesos como el estirado de alambres. La maleabilidad, por otro lado, es la capacidad del metal para ser comprimido o doblado sin fracturarse, lo cual es crucial en procesos como el embutido y el doblado de láminas.
- Elástico vs plástico: Los metales presentan tanto comportamiento elástico como plástico cuando se deforman. La deformación elástica es reversible: cuando se retira la fuerza aplicada, el metal vuelve a su forma original. La deformación plástica, sin embargo, es permanente. En el trabajo con láminas metálicas, se busca alcanzar una deformación plástica controlada, donde el metal adopte la forma deseada de manera permanente sin fracturarse.
- Tensiones y fuerzas: El proceso de deformación de una lámina metálica se basa en la aplicación de tensiones (fuerzas internas que resisten la deformación). El conocimiento de cómo se distribuyen estas tensiones en el material es fundamental para evitar fallas como fracturas o deformaciones no deseadas. Por ejemplo, en el proceso de embutido profundo, la distribución uniforme de la tensión es esencial para evitar defectos en la pieza.
- Técnicas de conformado: El conformado de láminas metálicas puede hacerse a través de diversos métodos, como el corte, el doblado, el estirado y el embutido. Estas técnicas permiten dar forma a una lámina para obtener piezas complejas con formas tridimensionales, manteniendo la integridad del material.
Herramientas fundamentales utilizadas en estos procesos
El trabajo con láminas y estructuras metálicas ha evolucionado con el tiempo, pasando de herramientas manuales a maquinaria altamente automatizada. Hoy en día, se utilizan una variedad de herramientas y equipos especializados para realizar las operaciones de corte, conformado y ensamblaje de metales. Entre las herramientas más comunes se incluyen:
- Prensas: Utilizadas para aplicar grandes fuerzas sobre las láminas metálicas, las prensas pueden ser mecánicas, hidráulicas o neumáticas. Las prensas profundas son esenciales para procesos como el embutido y la estampación.
- Máquinas rebordeadoras y bordonadoras: Estas máquinas son utilizadas para crear bordes en láminas de metal, lo que aumenta su resistencia y mejora su apariencia. La precisión en el rebordeado es fundamental para evitar defectos en las piezas finales.
- Cizallas y troqueladoras: Son herramientas de corte que permiten dividir una lámina en piezas más pequeñas. Las cizallas se utilizan principalmente para cortes rectos, mientras que las troqueladoras permiten cortes más complejos.
- Rodillos de enderezado: Estos dispositivos son esenciales para corregir deformaciones en las láminas metálicas. Aplican presión a través de varios rodillos para eliminar las ondulaciones o deformaciones en la lámina.
- Máquinas de embutido: Utilizadas en la producción de recipientes y piezas huecas a partir de láminas metálicas. Este proceso requiere prensas profundas y matrices especializadas para dar forma a la lámina sin que se rompa.
Futuro del trabajo con metales
El futuro del trabajo con metales sigue evolucionando con el desarrollo de nuevas tecnologías y procesos automatizados. Las prensas controladas por CNC (Control Numérico por Computadora) y los sistemas de fabricación robótica están permitiendo una mayor precisión y eficiencia en la producción en masa de componentes metálicos. Además, el uso de aleaciones avanzadas y el trabajo con nuevos materiales está abriendo las puertas a aplicaciones más innovadoras y sostenibles.
Cómo enderezar estructuras metálicas
El enderezado de estructuras metálicas es un proceso crucial en diversas industrias, especialmente en la construcción, fabricación y reparación de piezas. Las deformaciones pueden ocurrir durante la fabricación, el transporte o el uso, y es fundamental restaurar la alineación y la planitud del metal para asegurar su funcionalidad y resistencia estructural. Dependiendo de la magnitud de la deformación, las técnicas para enderezar metales varían, y se emplean diferentes herramientas y enfoques que van desde métodos manuales hasta el uso de maquinaria pesada.
Problemas comunes con las estructuras metálicas deformadas
Antes de profundizar en los métodos de enderezado, es importante entender las causas comunes de las deformaciones en estructuras metálicas. Estas deformaciones pueden ocurrir debido a una variedad de factores, tales como:
- Fuerzas externas: Golpes, presiones indebidas o fuerzas incontroladas durante el montaje o transporte pueden provocar dobleces, torsiones o aplastamientos en las piezas metálicas.
- Proceso de soldadura: El calor extremo durante la soldadura puede causar tensiones internas en el metal, lo que puede resultar en deformaciones no deseadas a medida que el metal se enfría y se contrae.
- Cargas excesivas: En estructuras como puentes o marcos de edificios, la sobrecarga o el uso incorrecto de los materiales pueden causar que las piezas se doblen bajo presión, debilitando la integridad estructural.
- Errores en el diseño o fabricación: Tolerancias mal calculadas o errores durante el proceso de fabricación pueden generar piezas deformadas o fuera de alineación.
Independientemente de la causa, es vital identificar el tipo y grado de deformación antes de proceder con el enderezado. Los tipos más comunes de deformaciones incluyen:
- Curvaturas: Piezas que han sido dobladas en una dirección.
- Torsiones: Partes que han sido torcidas a lo largo de su eje.
- Ondulaciones: Pequeñas deformaciones o pandeos en láminas delgadas.
- Abolladuras: Deformaciones locales causadas por impactos.
Métodos tradicionales para enderezar metales
El enderezado de estructuras metálicas puede realizarse mediante diversos métodos, dependiendo del tamaño de la pieza, el tipo de deformación y el equipo disponible. A continuación, se describen algunos de los métodos más comunes:
- Martillado manual:
- Uno de los métodos más tradicionales de enderezado de piezas pequeñas y medianas. Utilizando un martillo y un yunque o superficie sólida, se golpea la pieza en las áreas deformadas para devolverla a su forma original.
- Ventajas: Es un método simple y económico, que no requiere maquinaria compleja.
- Desventajas: Es un proceso lento, y el uso excesivo de fuerza puede causar fatiga o fracturas en el metal, especialmente en piezas más frágiles.
- Enderezado mediante calor:
- Este método consiste en aplicar calor localizado a las áreas deformadas. El metal, al calentarse, se expande y se vuelve más flexible, lo que permite manipularlo para corregir la deformación. Luego, se deja enfriar de manera controlada para que el metal recupere su forma sin tensiones.
- Ventajas: Es útil para deformaciones severas o en metales de mayor grosor, donde el uso de métodos manuales sería ineficaz.
- Desventajas: El calor excesivo puede afectar las propiedades del material, como la dureza o la resistencia, por lo que es importante controlar la temperatura y la distribución del calor.
- Enderezado con prensas manuales:
- Para piezas de metal más grandes o de mayor grosor, se utilizan prensas manuales o hidráulicas que aplican una fuerza controlada en las áreas deformadas. Estas prensas permiten ajustar con precisión la presión para evitar dañar la pieza.
- Ventajas: Mayor precisión que el martillado, especialmente en piezas más grandes.
- Desventajas: Requiere equipo especializado y entrenamiento adecuado para asegurar un enderezado eficiente y seguro.
- Rodillos de enderezado:
- En el caso de láminas metálicas, los rodillos de enderezado son herramientas esenciales. Estos dispositivos consisten en una serie de rodillos que comprimen y enderezan las láminas a medida que pasan entre ellos. Los rodillos pueden ajustarse para aplicar diferentes grados de presión en función del grosor y tipo de lámina.
- Ventajas: Es un método eficiente para corregir grandes cantidades de material rápidamente.
- Desventajas: El equipo puede ser costoso, y el proceso debe ser cuidadosamente calibrado para evitar nuevas deformaciones.
Uso de prensas y otros equipos de precisión para enderezado
El enderezado mediante prensas es uno de los métodos más utilizados en la industria moderna, especialmente para grandes piezas metálicas o cuando se requiere una precisión extrema. Las prensas, que pueden ser manuales, hidráulicas o mecánicas, permiten aplicar una fuerza significativa de manera controlada para restaurar la forma original de una pieza deformada.
Prensas hidráulicas
Las prensas hidráulicas son especialmente útiles para enderezar grandes piezas metálicas debido a su capacidad para generar una presión intensa y constante. Estas prensas funcionan mediante un sistema hidráulico que utiliza líquidos presurizados para aplicar fuerza. Una ventaja importante de las prensas hidráulicas es su capacidad de ajustar la presión con precisión, lo que las hace ideales para trabajar con diferentes tipos de metales y grosores.
El proceso de enderezado con una prensa hidráulica suele seguir estos pasos:
- Inspección de la pieza: Se examina la pieza deformada para determinar el grado y tipo de deformación. En algunos casos, se pueden realizar mediciones precisas con herramientas como calibres o comparadores.
- Preparación: Se colocan bloques de soporte en la prensa para evitar que la pieza sufra nuevas deformaciones durante el proceso. La pieza se posiciona de manera que la fuerza de la prensa actúe directamente sobre la zona deformada.
- Aplicación de presión: Se activa la prensa para aplicar presión gradual sobre la pieza. La presión se incrementa lentamente hasta que la deformación comienza a corregirse. Este proceso puede repetirse varias veces, aplicando presión en diferentes puntos según sea necesario.
- Liberación y comprobación: Una vez que la pieza ha sido enderezada, se libera la presión de la prensa y se comprueba que la deformación haya sido corregida de manera adecuada.
Prensas mecánicas
Las prensas mecánicas funcionan de manera similar a las hidráulicas, pero utilizan un sistema de engranajes y palancas para aplicar la fuerza. Aunque generalmente son más rápidas que las hidráulicas, las prensas mecánicas pueden ser menos precisas, por lo que son más adecuadas para trabajos en los que no se requiere tanta exactitud.
Consideraciones de seguridad al enderezar metales
El trabajo de enderezado de estructuras metálicas, especialmente cuando se utilizan prensas o calor, conlleva ciertos riesgos, tanto para el operario como para la integridad de la pieza. Algunas de las principales consideraciones de seguridad incluyen:
- Uso de equipo de protección personal (EPP): Los operarios deben usar guantes, gafas protectoras y ropa adecuada para protegerse de posibles proyecciones de metal, chispas o quemaduras.
- Manejo de herramientas y maquinaria: Las prensas y otras herramientas de enderezado deben manejarse con precaución. Es fundamental asegurar que la pieza esté bien sujeta antes de aplicar cualquier tipo de presión para evitar que se desplace bruscamente o cause accidentes.
- Control del calor: En los procesos que implican la aplicación de calor, es crucial controlar la temperatura para evitar sobrecalentamientos que puedan debilitar el metal o causar daños irreversibles.
Ejemplos de procesos de enderezado en la industria
El enderezado de estructuras metálicas es una operación común en varias industrias, especialmente en la construcción y automoción. A continuación se presentan algunos ejemplos:
- Enderezado de vigas de acero: En la construcción de edificios y puentes, las vigas de acero a menudo se deforman durante el transporte o la instalación. Se utilizan prensas hidráulicas de gran tamaño para enderezar estas vigas antes de ser ensambladas. Este proceso asegura que la estructura final sea segura y cumpla con los estándares de diseño.
- Enderezado de chasis de automóviles: En los talleres de reparación de automóviles, el enderezado de chasis es un proceso común después de accidentes. Utilizando prensas y marcos de enderezado, los técnicos restauran la forma original del vehículo para garantizar que sea seguro para su uso posterior.
- Restauración de piezas históricas: En el caso de la restauración de piezas metálicas antiguas, como puentes o monumentos, el enderezado de componentes deformados puede ser necesario para preservar la estructura original. Aquí, se emplean métodos tanto manuales como mecánicos, dependiendo de la fragilidad de las piezas.
Prensa profunda: Conceptos y uso en la industria
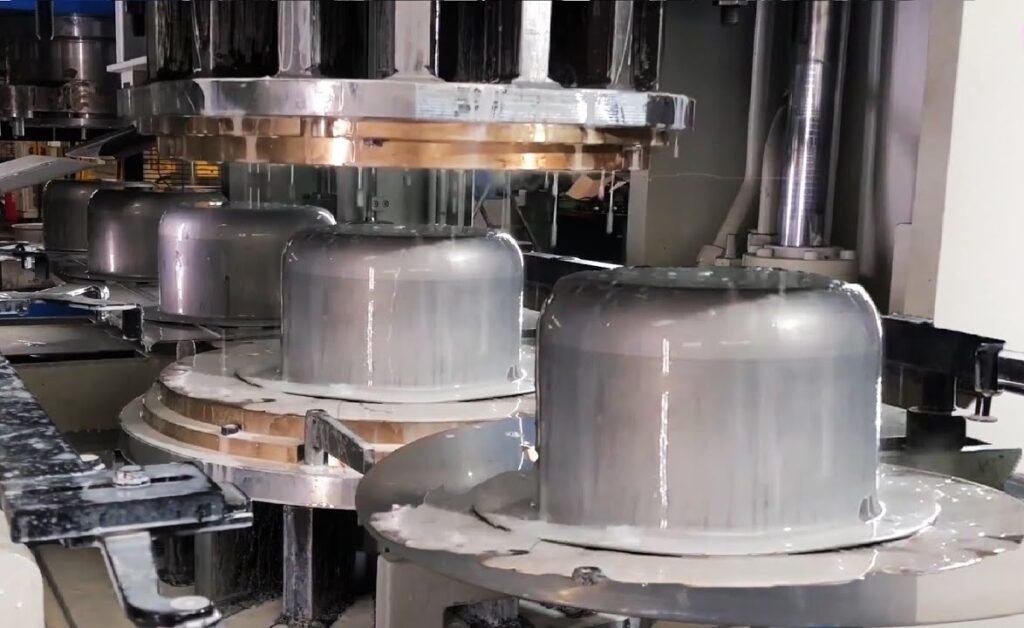
La prensa profunda es una herramienta esencial en la industria metalúrgica para procesos de conformado, particularmente en la producción de piezas complejas a partir de láminas metálicas. Este equipo permite aplicar grandes fuerzas de manera controlada para moldear el metal en formas tridimensionales, siendo especialmente útil en la fabricación de componentes automotrices, aeronáuticos y de electrodomésticos, donde se requiere precisión y resistencia.
¿Qué es una prensa profunda?
Una prensa profunda es una máquina diseñada para realizar operaciones de embutido, estampado y conformado profundo de metales. El proceso de embutición profunda, del que hablaremos con más detalle más adelante, implica el estiramiento de una lámina metálica para crear formas huecas, como tazas, cilindros o piezas con cavidades profundas.
El término “prensa profunda” se refiere a la capacidad de la máquina para realizar operaciones en las que la profundidad de la pieza final es mayor que su diámetro. Este proceso requiere de fuerzas extremadamente precisas para evitar la rotura o el agrietamiento del material mientras se moldea.
Tipos de prensas profundas
Existen varios tipos de prensas profundas, cada una con características específicas que las hacen adecuadas para diferentes aplicaciones industriales. Las más comunes son:
- Prensa hidráulica:
- Funciona mediante la aplicación de presión hidráulica para deformar el material. Este tipo de prensa es altamente eficiente para trabajos que requieren una presión constante y uniforme.
- Ventajas: Ofrece un control preciso sobre la fuerza aplicada y es ideal para trabajos de embutido profundo en los que se necesitan presiones altas pero controladas.
- Desventajas: Son más lentas en comparación con otros tipos de prensas debido a la naturaleza del sistema hidráulico.
- Prensa mecánica:
- Utiliza un sistema de engranajes y palancas para generar la fuerza de presión. Este tipo de prensa es más rápida que las prensas hidráulicas y es común en procesos de estampado y embutido menos profundos.
- Ventajas: Mayor velocidad de operación, lo que la hace ideal para la producción en masa.
- Desventajas: Menor control de la fuerza, lo que puede ser un problema en procesos que requieren alta precisión.
- Prensa neumática:
- Funciona mediante aire comprimido, lo que permite una operación más rápida y precisa. Se utiliza principalmente para operaciones de embutido de piezas pequeñas o de materiales más delgados.
- Ventajas: Rápida y fácil de controlar, ideal para trabajos de alta velocidad.
- Desventajas: Limitada en términos de la fuerza que puede generar, lo que la hace inadecuada para piezas más gruesas o embuticiones profundas.
Aplicaciones industriales de la prensa profunda
La prensa profunda es un equipo versátil que se utiliza en una amplia gama de industrias. Algunas de las aplicaciones más comunes incluyen:
- Industria automotriz:
- En la fabricación de automóviles, las prensas profundas se utilizan para crear piezas estructurales como paneles de carrocería, guardabarros y componentes del chasis. La embutición profunda permite obtener formas complejas que son esenciales para la aerodinámica y la seguridad del vehículo.
- También se utiliza para fabricar piezas más pequeñas, como cubiertas de motores, carcasas de frenos y componentes internos.
- Aeronáutica:
- En la industria aeroespacial, la capacidad de producir piezas ligeras pero resistentes es crucial. Las prensas profundas se utilizan para crear carcasas de motores, estructuras de fuselaje y piezas aerodinámicas. El embutido profundo permite la creación de piezas de una sola pieza, lo que reduce la necesidad de soldaduras o ensamblajes adicionales, mejorando así la resistencia y la integridad estructural.
- Electrodomésticos:
- La fabricación de electrodomésticos como lavadoras, secadoras, refrigeradores y estufas también se beneficia del uso de prensas profundas. Las cubiertas exteriores, los paneles internos y otros componentes estructurales suelen fabricarse mediante embutido profundo para garantizar acabados suaves y formas precisas.
- Industria de envases:
- La producción de envases metálicos, como latas de bebidas y contenedores de alimentos, es uno de los usos más comunes del embutido profundo. Las prensas profundas permiten crear envases delgados pero fuertes que son capaces de mantener la integridad del contenido y soportar la presión interna.
- Medicina:
- Las prensas profundas también se utilizan en la fabricación de equipos médicos, como implantes, instrumentos quirúrgicos y dispositivos protésicos, que requieren precisión y materiales que sean biocompatibles y resistentes.
El proceso de embutición profunda: cómo funciona y por qué es importante
La embutición profunda es el proceso principal que se realiza con una prensa profunda. Consiste en transformar una lámina plana de metal en una forma hueca mediante la aplicación de una fuerza de compresión. El embutido se realiza en una sola operación o en varias fases, dependiendo de la complejidad de la pieza.
Fases del proceso de embutido profundo:
- Preparación del material:
- El proceso comienza con la preparación de una lámina metálica, que se corta en discos o piezas del tamaño adecuado para el embutido. El material más comúnmente utilizado es el acero, aunque también se emplean otras aleaciones como el aluminio o el cobre, dependiendo de las necesidades de la pieza final.
- Colocación de la lámina en la prensa:
- La lámina metálica se coloca sobre un molde, llamado matriz, que tiene la forma de la pieza que se quiere obtener. Sobre la matriz se sitúa un punzón o prensa que aplicará la fuerza necesaria para deformar la lámina.
- Aplicación de presión:
- El punzón desciende lentamente sobre la lámina, forzándola a adoptar la forma de la matriz. Durante este proceso, la lámina experimenta una deformación plástica, lo que significa que cambia de forma de manera permanente sin romperse.
- Extracción de la pieza:
- Una vez que la lámina ha sido conformada, la prensa se levanta y la pieza formada se extrae del molde. En algunos casos, la pieza puede necesitar un proceso adicional de conformado para perfeccionar su forma o dimensiones.
Ventajas de la embutición profunda:
- Producción de piezas complejas: El embutido profundo permite la creación de formas tridimensionales complejas, que serían difíciles o imposibles de lograr con otros métodos de conformado.
- Reducción de piezas y ensamblajes: Al formar piezas en una sola operación, se reduce la necesidad de soldaduras o ensamblajes adicionales, lo que mejora la resistencia y la integridad estructural.
- Ahorro de material: En comparación con otros procesos de corte o mecanizado, el embutido profundo permite un uso más eficiente del material, ya que genera menos desperdicio.
- Mayor resistencia estructural: Las piezas formadas mediante embutido profundo suelen tener mayor resistencia, ya que el proceso compacta y refuerza la estructura del metal.
Desafíos del embutido profundo:
- Arrugas y roturas: Si no se controla adecuadamente el proceso, es posible que la lámina se arrugue o se rompa debido a las tensiones internas. El control preciso de la presión y la lubricación del material son fundamentales para evitar estos defectos.
- Limitaciones en materiales: Aunque el embutido profundo es adecuado para una variedad de metales, algunos materiales pueden ser demasiado frágiles o duros para deformarse sin romperse.
- Costos iniciales: La inversión en equipos de prensa profunda y en las matrices especializadas puede ser alta, aunque los beneficios en términos de producción en masa suelen justificar la inversión a largo plazo.
Consideraciones de diseño para el uso de prensas profundas
El diseño de las piezas que se van a fabricar mediante embutido profundo requiere una planificación cuidadosa para evitar problemas durante el proceso. Algunas de las consideraciones clave incluyen:
- Relación profundidad-diámetro:
- Uno de los factores más importantes es la relación entre la profundidad y el diámetro de la pieza. Si la profundidad es demasiado grande en relación con el diámetro, el material puede romperse durante el embutido. Generalmente, se recomienda que esta relación no exceda 2:1, aunque con materiales y lubricación adecuados, puede aumentarse ligeramente.
- Radio de las esquinas:
- Las esquinas agudas tienden a concentrar tensiones, lo que aumenta el riesgo de rotura durante el embutido. Por ello, es importante diseñar las piezas con radios suaves en las esquinas y bordes.
- Espesor de la lámina:
- El espesor del material influye directamente en la capacidad de embutido. Las láminas más delgadas son más fáciles de deformar, pero también son más propensas a arrugarse o romperse. El espesor debe seleccionarse en función del tamaño y la complejidad de la pieza.
- Uso de lubricantes:
- La fricción entre la lámina y las matrices puede causar desgaste y defectos en la pieza. Para evitarlo, es fundamental
Ventajas del uso de lubricantes en la embutición profunda:
- Reducción de la fricción: Esto no solo minimiza el desgaste de las herramientas, sino que también permite un mejor control del flujo del material a lo largo del proceso, disminuyendo las tensiones internas que podrían llevar a fracturas o fallos.
- Mejor acabado superficial: Al reducir el contacto directo entre el metal y las herramientas, los lubricantes ayudan a producir una pieza con un acabado superficial más suave y uniforme, lo cual es esencial en industrias como la automotriz y la aeronáutica, donde los acabados de alta calidad son indispensables.
- Prevención de sobrecalentamiento: La fricción genera calor, lo que podría comprometer las propiedades del metal durante el proceso. Los lubricantes ayudan a disipar el calor, manteniendo la temperatura del proceso bajo control y preservando las propiedades del material.
Ejemplos de procesos de embutición profunda en la industria
- Fabricación de latas de aluminio:
- Uno de los ejemplos más representativos del uso de prensas profundas es la fabricación de latas de aluminio para bebidas. El embutido profundo permite formar las paredes delgadas y precisas de las latas a partir de una pequeña pieza de aluminio plano, lo que resulta en un proceso eficiente y económico para la producción en masa.
- Producción de componentes automotrices:
- En la industria automotriz, el embutido profundo se utiliza para crear una variedad de componentes, desde partes de la carrocería hasta piezas estructurales del chasis. Las prensas profundas permiten crear formas complejas que ofrecen resistencia estructural con un peso mínimo, lo que es crucial para mejorar la eficiencia del combustible en los vehículos.
- Fabricación de fregaderos de acero inoxidable:
- Otro ejemplo común es la producción de fregaderos de acero inoxidable. Mediante el embutido profundo, se forma una pieza plana de acero en una forma profunda y hueca que es ideal para un fregadero. Este proceso permite obtener un fregadero sin costuras visibles y con una estructura sólida y resistente a la corrosión.
Innovaciones recientes en prensas profundas
Con los avances tecnológicos, las prensas profundas han experimentado una evolución significativa en términos de automatización y precisión. Algunas de las innovaciones recientes incluyen:
- Prensas CNC (Control Numérico por Computadora):
- Las prensas CNC permiten un control extremadamente preciso del proceso de embutido. A través de sistemas computarizados, se puede programar y ajustar la fuerza, velocidad y presión de la prensa con un nivel de detalle que sería imposible de lograr manualmente. Esto es especialmente útil en la producción de piezas complejas que requieren precisión milimétrica.
- Sistemas de monitoreo en tiempo real:
- Hoy en día, muchas prensas profundas están equipadas con sensores que monitorean en tiempo real el proceso de embutido. Estos sistemas pueden detectar irregularidades, como cambios en la presión o la velocidad, lo que permite a los operarios ajustar el proceso inmediatamente para evitar defectos en las piezas.
- Materiales avanzados:
- El desarrollo de nuevos materiales metálicos, como aleaciones ligeras y metales de alta resistencia, ha llevado a innovaciones en el diseño de las prensas. Las prensas modernas están diseñadas para manejar estos materiales avanzados, permitiendo que el embutido profundo sea más eficiente y versátil.
Consideraciones de mantenimiento y seguridad
Dado que las prensas profundas operan con fuerzas extremadamente altas, el mantenimiento regular es crucial para garantizar su correcto funcionamiento y prolongar la vida útil del equipo. Algunas consideraciones clave incluyen:
- Inspección de las herramientas: Las matrices y los punzones deben inspeccionarse regularmente para detectar signos de desgaste o daño. Las herramientas desgastadas pueden provocar defectos en las piezas y aumentar el riesgo de fallos en el proceso de embutido.
- Lubricación adecuada: Tanto el sistema hidráulico como las superficies de contacto deben mantenerse bien lubricados para minimizar el desgaste y garantizar un movimiento suave y controlado del equipo.
- Capacitación de los operarios: Los operarios deben estar capacitados no solo en el uso de la máquina, sino también en las medidas de seguridad necesarias. El uso de prensas profundas conlleva riesgos significativos si no se manejan adecuadamente, por lo que es esencial que los trabajadores sigan los protocolos de seguridad establecidos.
- Mantenimiento preventivo: Las prensas profundas requieren mantenimiento regular para asegurar que el sistema hidráulico, los controles electrónicos y las herramientas estén en condiciones óptimas. Esto no solo evita fallos imprevistos, sino que también garantiza que la calidad de las piezas producidas se mantenga constante.
Ventajas y desventajas del uso de prensas profundas
Ventajas:
- Alta precisión: Las prensas profundas permiten la producción de piezas complejas con una gran precisión, lo que es esencial en industrias como la automotriz y la aeroespacial.
- Reducción de desperdicio: A diferencia de otros métodos de fabricación, el embutido profundo utiliza el material de manera más eficiente, reduciendo el desperdicio y optimizando los costos de producción.
- Versatilidad: Pueden trabajar con una amplia gama de metales y materiales, desde acero y aluminio hasta cobre y latón, lo que las hace adecuadas para diversas aplicaciones industriales.
- Producción en masa eficiente: Las prensas profundas son ideales para la producción en masa, ya que pueden realizar múltiples operaciones de embutido en un solo ciclo, lo que aumenta la velocidad de producción y reduce el tiempo de fabricación.
Desventajas:
- Alto costo inicial: La inversión en una prensa profunda, especialmente en prensas hidráulicas de gran capacidad, puede ser significativa. Sin embargo, esta inversión se justifica con el tiempo en aplicaciones de producción en masa.
- Mantenimiento intensivo: Las prensas profundas requieren un mantenimiento regular para garantizar un rendimiento óptimo. Las matrices, punzones y otros componentes están sujetos a desgaste continuo y deben ser reemplazados o reparados periódicamente.
- Limitaciones en ciertos materiales: Aunque las prensas profundas son versátiles, algunos materiales extremadamente duros o frágiles pueden no ser adecuados para este proceso debido a la alta presión necesaria.
Máquina rebordeadora: Aplicaciones y funcionamiento
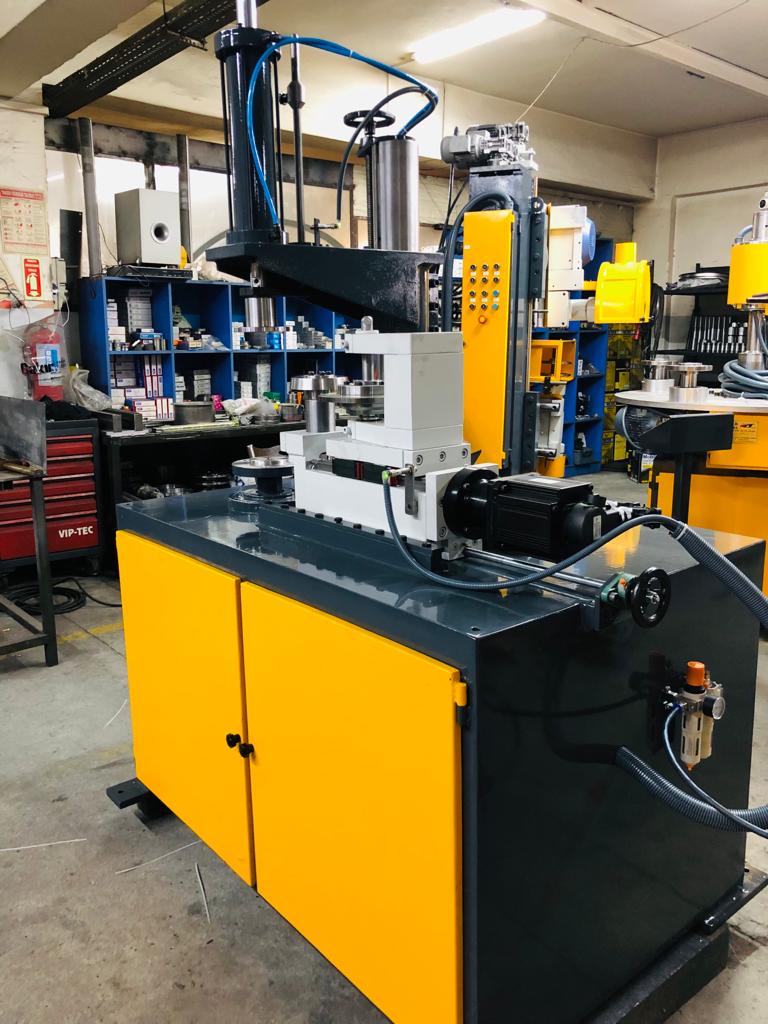
La máquina rebordeadora es una herramienta crucial en la conformación de bordes en láminas metálicas, utilizada ampliamente en la industria para fabricar componentes tubulares, cilíndricos o piezas que requieren bordes reforzados. Su capacidad para crear rebordes lisos, precisos y consistentes hace que este equipo sea indispensable en sectores como la automoción, la fabricación de electrodomésticos, la aeronáutica y la construcción. El proceso de rebordeado no solo mejora la estética de una pieza metálica, sino que también refuerza su estructura, aumentando la resistencia al desgaste y la durabilidad.
Descripción de la máquina rebordeadora: Partes y componentes
Una máquina rebordeadora se compone de varios elementos mecánicos clave que trabajan en conjunto para moldear los bordes de las piezas metálicas. Estos componentes incluyen:
- Rodillos de conformado:
- Los rodillos son las herramientas principales de la rebordeadora, responsables de aplicar presión y moldear los bordes de la lámina metálica. Los rodillos suelen estar hechos de acero endurecido para resistir el desgaste constante al trabajar con metales.
- Soportes ajustables:
- Estos soportes permiten posicionar y sujetar firmemente la pieza que se va a rebordear. La precisión en la sujeción es esencial para evitar movimientos durante el proceso, lo que podría generar bordes irregulares o defectuosos.
- Sistema de control de presión:
- La rebordeadora debe aplicar la cantidad justa de presión en el borde de la lámina metálica. Demasiada presión podría causar deformaciones o fracturas, mientras que una presión insuficiente no logrará formar un borde adecuado. El sistema de control de presión permite a los operarios ajustar la presión en función del tipo de material y del grosor de la lámina.
- Motor:
- El motor acciona los rodillos, proporcionando la energía necesaria para mover y deformar la lámina metálica. En muchas máquinas modernas, el motor está controlado electrónicamente para permitir ajustes de velocidad y precisión.
- Control de velocidad:
- En algunos modelos, especialmente aquellos utilizados en aplicaciones de alta precisión, se puede ajustar la velocidad a la que los rodillos giran para optimizar el proceso de rebordeado en diferentes materiales y espesores.
Diferentes tipos de rebordes en piezas metálicas
El rebordeado es un proceso versátil que puede aplicarse para crear diferentes tipos de bordes en una pieza metálica, dependiendo de la función que se busque. Algunos de los rebordes más comunes incluyen:
- Reborde simple:
- Este tipo de reborde consiste en doblar el borde de la lámina hacia afuera o hacia adentro, formando un borde liso y continuo. Es ideal para aplicaciones donde se busca mejorar la apariencia estética de la pieza o evitar bordes afilados que podrían representar un peligro para los usuarios.
- Reborde de refuerzo:
- Este tipo de reborde no solo mejora la apariencia de la pieza, sino que también refuerza su estructura. Al doblar el borde, se aumenta la rigidez de la lámina, lo que la hace más resistente a la deformación y al desgaste. Este tipo de reborde se utiliza comúnmente en la fabricación de recipientes metálicos y tuberías.
- Reborde acampanado:
- Se trata de un reborde que tiene una forma ligeramente cónica, lo que facilita el ensamblaje de piezas, especialmente en la unión de tubos o cilindros. Este tipo de reborde también puede mejorar el flujo de líquidos o gases cuando se utiliza en sistemas de tuberías.
- Reborde enrollado:
- En este caso, el borde de la lámina se enrolla sobre sí mismo, formando un borde redondeado y sin costuras. Este tipo de reborde es común en piezas que requieren una mayor seguridad y resistencia al desgaste, como en envases metálicos o componentes estructurales de aeronaves.
Proceso paso a paso del rebordeado de piezas metálicas
El proceso de rebordeado implica una serie de pasos que varían según la pieza y el tipo de reborde deseado. A continuación, se describe el flujo de trabajo típico en una máquina rebordeadora:
- Preparación de la pieza:
- Antes de iniciar el proceso, la pieza metálica debe estar correctamente preparada. Esto incluye asegurarse de que los bordes estén limpios y sin defectos. Dependiendo del tipo de reborde que se desee, la lámina puede necesitar corte o conformado previo para obtener la forma y el tamaño correctos.
- Colocación en la rebordeadora:
- La pieza se coloca en la máquina rebordeadora, asegurándose de que esté firmemente sujeta en los soportes ajustables para evitar movimientos durante el proceso. La alineación precisa es clave para evitar errores en el rebordeado.
- Ajuste de los rodillos y la presión:
- Se ajustan los rodillos de conformado para que estén en contacto con el borde de la lámina. La presión y la velocidad de los rodillos se configuran en función del tipo de metal, el grosor de la lámina y el tipo de reborde que se desee.
- Rebordeado:
- Una vez configurada la máquina, los rodillos empiezan a girar, aplicando presión sobre el borde de la lámina y dándole la forma deseada. El operario debe supervisar de cerca el proceso para asegurarse de que el borde se esté formando de manera uniforme y sin defectos.
- Revisión y ajustes:
- Después de completar el rebordeado, la pieza se retira de la máquina y se revisa para asegurarse de que el borde tenga la forma y el acabado adecuados. Si es necesario, se pueden realizar ajustes adicionales o se puede repetir el proceso para corregir cualquier imperfección.
Aplicaciones en la industria
El proceso de rebordeado tiene una gran variedad de aplicaciones industriales, debido a su capacidad para mejorar tanto la resistencia estructural como la estética de las piezas metálicas. Algunas de las industrias que más utilizan máquinas rebordeadoras incluyen:
- Industria automotriz:
- En la fabricación de vehículos, las máquinas rebordeadoras se utilizan para crear bordes lisos y resistentes en componentes como puertas, capós y parachoques. Estos bordes no solo mejoran la apariencia del vehículo, sino que también contribuyen a su resistencia estructural y seguridad, especialmente en caso de impacto.
- Aeronáutica:
- La industria aeroespacial requiere piezas de metal ligeras pero resistentes. Las máquinas rebordeadoras se utilizan para crear bordes reforzados en paneles de fuselaje, alas y componentes internos, lo que aumenta la durabilidad sin añadir peso innecesario.
- Fabricación de electrodomésticos:
- Muchos electrodomésticos, como lavadoras, secadoras y refrigeradores, utilizan partes metálicas con bordes rebordeados para mejorar su resistencia y apariencia. Los bordes rebordeados también ayudan a evitar que las piezas afiladas representen un peligro para los usuarios.
- Construcción y arquitectura:
- Las láminas de metal utilizadas en la construcción de fachadas, techos y otros elementos arquitectónicos suelen rebordearse para mejorar tanto la estética como la resistencia a las inclemencias del tiempo. El proceso de rebordeado también permite que las piezas metálicas encajen perfectamente en sistemas modulares de construcción.
- Envases metálicos:
- Las latas y otros envases metálicos dependen en gran medida de los bordes rebordeados para evitar fugas y mejorar la resistencia a la presión interna. El rebordeado crea un borde suave y continuo que es esencial para la seguridad y durabilidad del envase.
Ejemplos de uso de la rebordeadora en la fabricación de piezas cilíndricas y tubulares
Uno de los usos más comunes de las máquinas rebordeadoras es en la fabricación de piezas cilíndricas y tubulares, como tubos, recipientes y conductos. El rebordeado es esencial para mejorar la integridad estructural de estas piezas, especialmente en aplicaciones donde los bordes estarán sujetos a desgaste constante o donde es necesario evitar fugas o filtraciones.
- Tuberías y conductos:
- En la fabricación de sistemas de tuberías, el rebordeado de los extremos de los tubos facilita su conexión con otros componentes, garantizando una unión hermética y segura. El reborde acampanado, en particular, es común en sistemas de tuberías industriales y de fontanería, ya que permite una mejor alineación y flujo de líquidos o gases.
- Recipientes de presión:
- En la industria de los recipientes de presión, como tanques de gas y cilindros de aire comprimido, los bordes rebordeados ayudan a distribuir las tensiones de manera uniforme a lo largo de la estructura, evitando puntos de concentración de estrés que podrían llevar a fallos o rupturas.
- Cilindros metálicos en electrodomésticos:
- Los electrodomésticos como secadoras y lavadoras a menudo utilizan piezas cilíndricas rebordeadas en sus tambores y cubiertas internas. Esto proporciona resistencia adicional, lo que ayuda a soportar la presión del uso diario, al mismo tiempo que asegura que las piezas se ensamblen correctamente sin bordes afilados expuestos.
Recomendaciones de mantenimiento y operación eficiente
Para garantizar un rendimiento óptimo y prolongar la vida útil de una máquina rebordeadora, es fundamental seguir un programa de mantenimiento preventivo y asegurar una operación adecuada. Algunas recomendaciones clave incluyen:
- Inspección regular de los rodillos:
- Los rodillos de conformado están sujetos a un desgaste constante debido al contacto directo con el metal. Es importante revisar periódicamente estos rodillos para detectar signos de desgaste o daños. Los rodillos desgastados pueden causar defectos en los bordes y comprometer la calidad del producto final.
- Lubricación adecuada:
- Al igual que otros equipos industriales, las rebordeadoras deben mantenerse bien lubricadas para minimizar la fricción y el desgaste en sus partes móviles. Esto incluye tanto los rodillos como los sistemas de sujeción y motores.
- Ajustes periódicos:
- Con el tiempo, las rebordeadoras pueden desajustarse debido al uso continuo. Los operarios deben verificar regularmente que los rodillos y los soportes estén alineados correctamente y que la presión aplicada sea la adecuada para evitar daños en las piezas.
- Capacitación del personal:
- El personal debe estar capacitado para operar la máquina de manera segura y eficiente. Esto incluye no solo conocer cómo ajustar los rodillos y la presión, sino también cómo identificar posibles problemas en el equipo antes de que afecten la calidad de la producción.
Bordonadora biseladora de lámina: Herramienta clave para la precisión

La bordonadora biseladora de lámina es una herramienta especializada en el trabajo con metales, diseñada para crear bordes curvados o biselados en láminas metálicas, mejorando tanto la precisión como el acabado de las piezas. Este tipo de máquina es ampliamente utilizado en aplicaciones industriales que requieren bordes limpios, reforzados y uniformes, como la fabricación de piezas de maquinaria, tuberías, componentes automotrices y estructuras metálicas.
Introducción a la bordonadora biseladora de lámina
La bordonadora y la biseladora son máquinas que, aunque pueden parecer similares en términos de funcionalidad, tienen objetivos diferentes. Mientras que la bordonadora se utiliza para conformar un borde o un borde curvado (un borde “bordón” o rodado), la biseladora se encarga de crear un borde inclinado o biselado en el borde de la lámina metálica. Cuando una máquina combina estas dos funcionalidades, como en el caso de la bordonadora biseladora de lámina, permite tanto la formación de un borde reforzado como un borde inclinado, proporcionando una mayor versatilidad en los trabajos de fabricación.
Estas máquinas son especialmente importantes en la preparación de piezas que luego se van a ensamblar o soldar, ya que el bordón y el bisel ayudan a mejorar el ajuste y la alineación de las piezas, además de reforzar los bordes, haciéndolos más resistentes al desgaste y los impactos.
¿Cómo funciona una bordonadora biseladora?
La bordonadora biseladora de lámina utiliza un sistema de rodillos y cuchillas ajustables para doblar, curvar o biselar los bordes de una lámina metálica. Este proceso involucra la aplicación de presión controlada en los bordes de la lámina para crear la forma deseada.
El proceso de funcionamiento básico incluye los siguientes pasos:
- Colocación de la lámina:
- La lámina de metal se coloca en la máquina, asegurándose de que los bordes estén alineados con los rodillos o cuchillas de la bordonadora biseladora. El operador ajusta la máquina según el grosor y tipo de metal que se va a trabajar.
- Ajuste de la presión y el ángulo:
- Dependiendo de si se va a realizar un borde bordonado o biselado, el operario ajusta la presión de los rodillos (en el caso del bordonado) o el ángulo de las cuchillas (para el biselado). Los ajustes dependen del tipo de acabado que se desee y del grosor del material.
- Formación del borde:
- La máquina pone en movimiento los rodillos o cuchillas, que ejercen presión sobre el borde de la lámina para crear el bordón o bisel. A medida que la lámina avanza, la herramienta de conformado sigue la línea del borde para asegurar un acabado uniforme y preciso.
- Revisión del borde:
- Una vez completado el proceso, el operario revisa el borde para asegurarse de que cumple con las especificaciones. En caso de que se requiera mayor precisión o un ajuste adicional, la pieza puede volver a pasar por la máquina.
Comparación con otras máquinas de corte y conformado de metales
Las bordonadoras biseladoras de lámina se destacan frente a otras máquinas de corte y conformado debido a su precisión y capacidad para crear acabados específicos en los bordes. Algunas de las diferencias clave con otras herramientas de conformado incluyen:
- Cizallas y troqueladoras:
- Mientras que las cizallas y troqueladoras se utilizan principalmente para cortar o perforar el metal, la bordonadora biseladora se especializa en la preparación de los bordes, proporcionando un acabado que mejora la integridad estructural y la capacidad de ensamblaje.
- Prensas dobladoras:
- Las prensas dobladoras se utilizan para crear curvas grandes o ángulos en una lámina metálica, generalmente en el cuerpo de la lámina, no en los bordes. En contraste, la bordonadora biseladora está diseñada específicamente para trabajar en los bordes, lo que permite una mayor precisión en esas áreas críticas.
- Máquinas fresadoras:
- Las fresadoras son capaces de realizar biselados en láminas metálicas, pero la bordonadora biseladora es más eficiente para realizar biselados uniformes y consistentes a lo largo de los bordes de una lámina, sin necesidad de ajustes continuos de las herramientas de corte.
Ejemplos de su uso en la creación de bordes de precisión
El uso de la bordonadora biseladora es esencial en varias industrias, donde se requiere una alta precisión en los bordes para garantizar que las piezas metálicas se ajusten correctamente en los ensamblajes o se refuercen adecuadamente. Algunos ejemplos prácticos incluyen:
- Fabricación de tuberías y conductos:
- Las bordonadoras biseladoras se utilizan comúnmente en la industria de tuberías y conductos para crear bordes biselados que faciliten la soldadura de dos piezas de tubo. El bisel crea un ángulo que permite que las soldaduras penetren profundamente en la junta, asegurando una conexión fuerte y duradera.
- Carrocería automotriz:
- En la fabricación de carrocerías y componentes automotrices, se utilizan bordes biselados para mejorar el ajuste entre paneles de metal y piezas de ensamblaje. Además, el proceso de bordonado se utiliza para crear bordes redondeados que refuercen las piezas contra el desgaste por vibraciones y impactos.
- Aeronáutica:
- En la industria aeronáutica, las bordonadoras biseladoras son fundamentales para crear bordes biselados en paneles de fuselaje y otras piezas metálicas. Estos bordes permiten un ensamblaje preciso y ligero, al tiempo que aseguran una mayor resistencia estructural en las áreas donde se requiere la máxima integridad.
- Construcción de recipientes a presión:
- Los recipientes a presión, como tanques y contenedores metálicos, dependen de bordes biselados y bordonados para soportar las tensiones generadas por la presión interna. La bordonadora biseladora asegura que los bordes de estos recipientes sean lo suficientemente resistentes y estén bien alineados para evitar fugas o fallas en la estructura.
Recomendaciones de mantenimiento y operación eficiente
Para asegurar un funcionamiento óptimo y prolongar la vida útil de una bordonadora biseladora de lámina, es esencial llevar a cabo un mantenimiento regular y operar la máquina de manera eficiente. A continuación, se ofrecen algunas recomendaciones clave:
- Inspección de los rodillos y cuchillas:
- Los rodillos de la bordonadora y las cuchillas de la biseladora están sometidos a un uso intensivo, lo que puede generar desgaste con el tiempo. Es fundamental inspeccionar estos componentes regularmente y reemplazarlos cuando muestren signos de desgaste excesivo o daño, para mantener la precisión en el conformado de bordes.
- Lubricación:
- Al igual que otras máquinas de conformado, la bordonadora biseladora requiere una lubricación adecuada para minimizar la fricción entre las piezas móviles y reducir el desgaste. Los operadores deben asegurarse de seguir un plan de lubricación basado en las recomendaciones del fabricante.
- Calibración periódica:
- Es importante calibrar regularmente la máquina para asegurarse de que los rodillos y cuchillas estén aplicando la presión y el ángulo correctos durante el proceso. Una calibración incorrecta puede resultar en bordes defectuosos o dañados, lo que afecta negativamente la calidad de las piezas.
- Capacitación adecuada del personal:
- La operación de una bordonadora biseladora requiere una comprensión clara de los principios de conformado de metales y de las características específicas de la máquina. El personal debe estar bien capacitado en el uso adecuado de los controles, así como en los procedimientos de seguridad, para evitar accidentes y asegurar que el proceso se lleve a cabo con la máxima precisión.
- Limpieza de la máquina:
- Mantener la máquina limpia es vital para garantizar un funcionamiento sin problemas. Los restos de metal o polvo que se acumulen en los rodillos, cuchillas o mecanismos internos pueden afectar la precisión del proceso y aumentar el desgaste.
Ventajas del uso de la bordonadora biseladora
El uso de una bordonadora biseladora ofrece numerosas ventajas en términos de calidad de acabado y eficiencia en la producción:
- Alta precisión en los bordes: Estas máquinas permiten crear bordes perfectamente alineados y uniformes, lo cual es esencial para asegurar que las piezas metálicas se ensamblen correctamente y cumplan con los requisitos de calidad.
- Versatilidad en diferentes tipos de bordes: Al combinar las funciones de bordonado y biselado en una sola máquina, se obtiene mayor versatilidad en las aplicaciones, lo que permite realizar múltiples tipos de bordes con un solo equipo.
- Aumento de la resistencia estructural: El bordonado y el biselado no solo mejoran la apariencia de las piezas, sino que también refuerzan sus bordes, lo que aumenta la resistencia al desgaste, los impactos y las tensiones.
- Mejora en el proceso de ensamblaje: Los bordes biselados y bordonados facilitan el ensamblaje de las piezas, permitiendo que encajen mejor y ofreciendo un ajuste más seguro, especialmente en aplicaciones que involucran soldadura o uniones mecánicas.
Futuro e innovaciones en la tecnología de bordonado y biselado
El futuro de las máquinas bordonadoras biseladoras apunta hacia una mayor automatización y precisión gracias a la incorporación de tecnologías avanzadas, como los controles CNC (Control Numérico por Computadora) y el monitoreo en tiempo real. Estos avances permitirán una mayor eficiencia en la producción en masa, con una capacidad de ajuste aún más precisa y la posibilidad de integrar la máquina en líneas de producción completamente automatizadas.
Desarrollo de la primera sección: Introducción a la prensa profunda
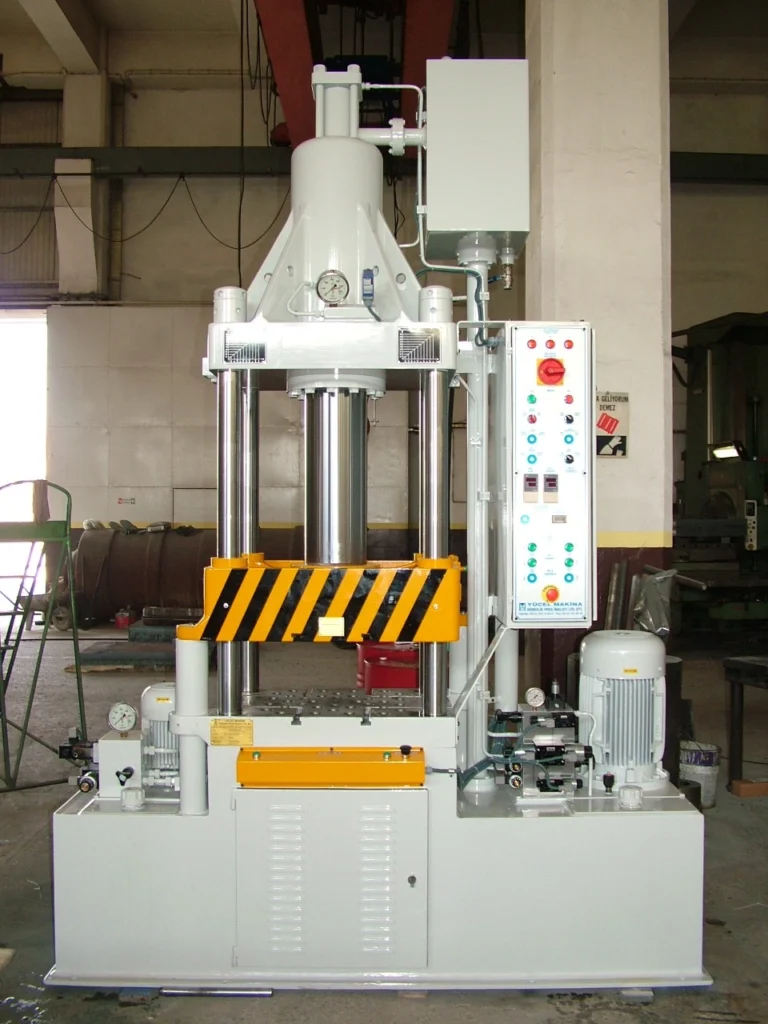
1. Introducción a la prensa profunda
La prensa profunda es un equipo esencial en la industria manufacturera, utilizada principalmente en el proceso de embutición profunda para formar piezas metálicas de formas complejas a partir de láminas planas. Este tipo de prensa permite producir componentes con cavidades profundas y perfiles tridimensionales en una sola operación o a través de varias etapas sucesivas.
El uso de prensas profundas ha revolucionado la forma en que se fabrican componentes metálicos en sectores como el automotriz, la industria aeroespacial y la fabricación de envases. La capacidad de estas máquinas para transformar una pieza plana de metal en una forma compleja, sin comprometer la integridad estructural del material, las convierte en herramientas indispensables en la producción en masa.
Las prensas profundas se basan en el principio de aplicar una fuerza controlada sobre una lámina metálica, forzando el material a fluir sobre una matriz para obtener la forma deseada. Este proceso se conoce como embutición profunda, y es utilizado principalmente para producir piezas como carcasas, latas, recipientes, tazas, y otros elementos huecos.
El origen de las prensas se remonta a la Revolución Industrial, cuando se desarrollaron las primeras máquinas para realizar operaciones de corte y estampado en metales. Sin embargo, fue a lo largo del siglo XX cuando las prensas profundas alcanzaron su madurez tecnológica, gracias al desarrollo de sistemas hidráulicos y mecánicos más avanzados, capaces de generar las fuerzas necesarias para procesos de embutido en piezas grandes y complejas.
Hoy en día, las prensas profundas están altamente automatizadas y cuentan con tecnologías de control avanzado, como sistemas CNC y sensores de monitoreo en tiempo real, que permiten una mayor precisión y eficiencia en la producción. Además, la evolución de los materiales utilizados en las matrices y punzones ha permitido mejorar la durabilidad y resistencia de las herramientas, optimizando así el ciclo de vida de la máquina y reduciendo los tiempos de mantenimiento.
La importancia de las prensas profundas en la industria actual no se limita solo a la capacidad de producir piezas complejas; también han contribuido a aumentar la eficiencia de los procesos de fabricación, reduciendo los costos y mejorando la calidad del producto final. Las empresas que emplean prensas profundas pueden producir grandes volúmenes de piezas en menor tiempo, lo que las hace competitivas en un mercado cada vez más globalizado.
En las siguientes secciones, exploraremos en detalle los distintos tipos de prensas profundas, los procesos relacionados con el embutido y su amplia gama de aplicaciones industriales.
Principios de funcionamiento de una prensa profunda
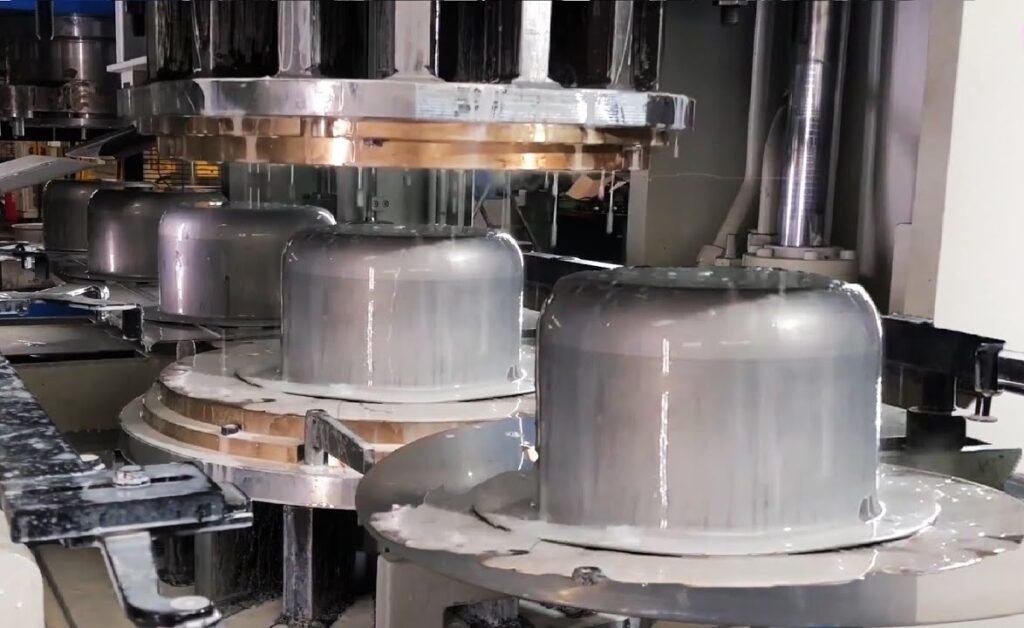
El funcionamiento de una prensa profunda se basa en la aplicación de una gran cantidad de fuerza sobre una lámina metálica, forzando el material a fluir dentro de una matriz y adoptando su forma. Este proceso, conocido como embutición profunda, permite obtener piezas tridimensionales con formas complejas y cavidades profundas, tales como recipientes, tazas, cilindros y otras piezas huecas. A lo largo del proceso, la lámina experimenta una deformación plástica, lo que significa que cambia de forma de manera permanente bajo la presión aplicada.
Conceptos básicos de la deformación y embutición profunda
El embutido profundo es un proceso de conformado de metales que utiliza una combinación de fuerza de compresión y estiramiento para moldear la lámina metálica. La fuerza se aplica a través de un punzón que presiona el material dentro de una matriz. A medida que la lámina se deforma, el metal fluye hacia abajo y adopta la forma de la cavidad de la matriz.
Este proceso es muy eficiente para crear formas huecas y cilíndricas con un nivel de precisión y acabado superficial que sería difícil de alcanzar con otros métodos de conformado de metales. Además, el embutido profundo reduce la necesidad de ensamblajes adicionales, ya que permite crear piezas completas en una sola operación o en unas pocas etapas.
Fases del embutido profundo:
- Colocación de la lámina metálica: El proceso comienza con la colocación de una lámina metálica sobre la matriz de la prensa profunda. El tamaño de la lámina y su grosor se seleccionan según las dimensiones y especificaciones de la pieza final.
- Inicio de la operación: La prensa profunda aplica una fuerza descendente a través del punzón, que comienza a empujar la lámina hacia la cavidad de la matriz.
- Deformación plástica: A medida que el punzón avanza, el metal se estira y se adapta a la forma de la matriz. Este proceso involucra la deformación plástica, es decir, la lámina cambia de forma de manera permanente, pero sin romperse, si el proceso está bien controlado.
- Extracción de la pieza: Una vez que el punzón ha completado su recorrido y la lámina ha sido embutida dentro de la matriz, la prensa se retrae y se extrae la pieza formada. Dependiendo de la complejidad de la pieza, esta puede requerir operaciones adicionales de conformado, pero en muchos casos, sale de la prensa con la forma final.
Diferencias entre prensa profunda y otras prensas
Aunque las prensas profundas son similares en algunos aspectos a otros tipos de prensas utilizadas en la industria metalúrgica, como las prensas mecánicas o hidráulicas convencionales, existen diferencias clave que hacen que las prensas profundas sean más adecuadas para el proceso de embutición profunda:
- Profundidad del embutido: Como su nombre lo indica, las prensas profundas están diseñadas para crear piezas con cavidades profundas, mientras que las prensas mecánicas estándar suelen realizar operaciones de estampado o doblado en superficies planas o con deformaciones menos profundas.
- Capacidad de deformación: Las prensas profundas aplican una presión constante y uniforme a lo largo del proceso, lo que es esencial para lograr la deformación plástica controlada que requiere el embutido profundo. Las prensas convencionales, por su parte, no están optimizadas para manejar las grandes fuerzas de compresión necesarias para deformar la lámina a profundidades significativas.
- Tamaño y precisión: Las prensas profundas suelen ser más grandes y robustas que otros tipos de prensas, ya que necesitan manejar materiales gruesos y aplicar grandes fuerzas sin comprometer la precisión.
Componentes clave de una prensa profunda
El diseño de una prensa profunda es complejo, y se compone de varios elementos que trabajan en conjunto para garantizar que el proceso de embutido sea eficiente y preciso. A continuación, se describen los principales componentes de una prensa profunda:
- Punzón:
- El punzón es la herramienta que aplica la presión sobre la lámina metálica para deformarla. Tiene la forma de la pieza que se desea obtener y está diseñado para entrar en la cavidad de la matriz, forzando a la lámina a adaptarse a esa forma.
- Los punzones están fabricados generalmente con acero de alta resistencia o materiales endurecidos, ya que deben soportar enormes fuerzas y resistir el desgaste.
- Matriz:
- La matriz es el molde que define la forma final de la pieza. Se coloca debajo de la lámina metálica y el punzón, y actúa como receptor de la lámina a medida que esta se deforma.
- Las matrices también están hechas de materiales muy resistentes, como aceros templados o carburo de tungsteno, para resistir el impacto y el desgaste continuo.
- Contrapunzón o sujeción del material:
- El contrapunzón, también conocido como sujeción de material, es una herramienta que sujeta firmemente la lámina metálica en su lugar durante el proceso de embutido. Esto evita que la lámina se arrugue o se desplace, lo que podría comprometer la calidad de la pieza final.
- Sistema hidráulico o mecánico:
- Las prensas profundas suelen ser hidráulicas o mecánicas. En las prensas hidráulicas, un sistema de pistones lleno de fluido genera la fuerza necesaria para realizar el embutido. En las prensas mecánicas, la fuerza proviene de un sistema de engranajes y levas.
- El sistema hidráulico es ideal para aplicaciones donde se requiere una gran fuerza constante y control preciso, mientras que el sistema mecánico es más rápido y adecuado para producciones en masa.
- Bandeja o sistema de extracción:
- Después del proceso de embutido, la pieza formada debe extraerse de la matriz. Las prensas profundas modernas están equipadas con sistemas automatizados que permiten la extracción rápida y segura de las piezas, lo que mejora la eficiencia del proceso.
El ciclo de operación en una prensa profunda
El ciclo de operación en una prensa profunda incluye varios pasos que, coordinados correctamente, aseguran que el proceso de embutido se realice sin problemas y con alta precisión. A continuación, se describe un ciclo típico:
- Alimentación de la lámina metálica: El proceso comienza cuando una lámina de metal se coloca sobre la matriz. En sistemas automatizados, esta etapa puede incluir la alimentación automática de láminas a la prensa.
- Sujeción de la lámina: El contrapunzón o el sistema de sujeción aseguran la lámina en su lugar, aplicando presión para evitar que el material se desplace o se deforme de manera no deseada.
- Movimiento del punzón: El punzón comienza a moverse hacia abajo, aplicando presión sobre la lámina y forzándola a adaptarse a la cavidad de la matriz. Este es el paso en el que ocurre la deformación plástica del material.
- Formación de la pieza: A medida que el punzón sigue avanzando, la lámina adopta la forma de la matriz, completando el proceso de embutido.
- Extracción de la pieza: Una vez que la pieza ha sido formada, el punzón se retrae y el sistema de extracción retira la pieza de la matriz. En algunos casos, se requieren operaciones adicionales para perfeccionar la forma o los detalles de la pieza.
Proceso físico: deformación plástica y tensiones internas
El embutido profundo se basa en la capacidad de los materiales metálicos para experimentar una deformación plástica sin fracturarse. Este comportamiento plástico permite que el metal fluya y adopte nuevas formas bajo presión, mientras mantiene su integridad estructural.
Sin embargo, durante el proceso de embutido, se generan tensiones internas en el material, que pueden afectar la calidad de la pieza final. El control de estas tensiones es fundamental para evitar defectos como arrugas, grietas o fallas en el material. Algunos factores clave que afectan las tensiones internas son:
- Espesor de la lámina: Las láminas más gruesas son más resistentes a la deformación, pero también son más propensas a generar tensiones internas más altas.
- Tipo de material: Los metales con mayor ductilidad (como el aluminio) tienden a deformarse más fácilmente sin generar tensiones excesivas, en comparación con metales más duros o frágiles.
- Velocidad de embutido: Un embutido demasiado rápido puede generar tensiones no deseadas, mientras que un embutido lento y controlado reduce la probabilidad de fallas.
Tipos de prensas profundas
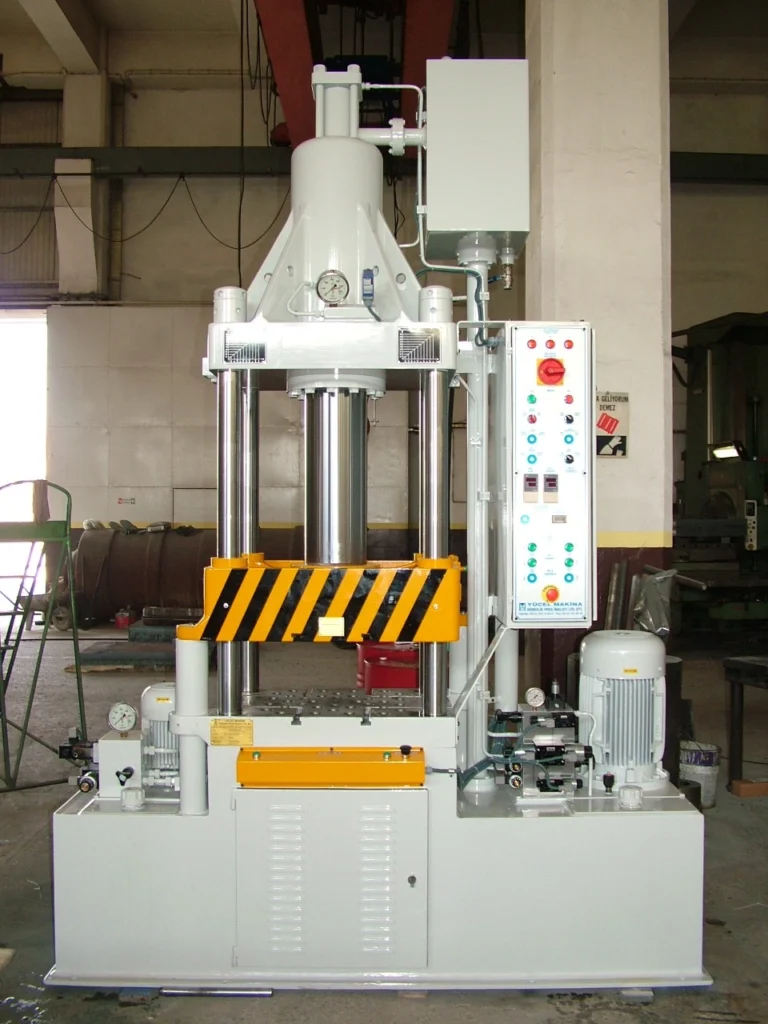
Existen varios tipos de prensas profundas, cada una diseñada para cumplir con distintos requerimientos de producción, dependiendo de factores como la cantidad de fuerza requerida, la velocidad del proceso, el tipo de material y el nivel de precisión. Las prensas profundas más comunes son las prensas hidráulicas, mecánicas, neumáticas y las servoaccionadas. Cada tipo tiene características específicas que lo hacen más adecuado para determinadas aplicaciones.
3.1 Prensa hidráulica
La prensa hidráulica es una de las más utilizadas en el proceso de embutición profunda, especialmente en aplicaciones que requieren grandes fuerzas de presión. Funciona mediante un sistema de cilindros hidráulicos llenos de un fluido que, cuando es presurizado, genera una fuerza constante y controlada. Este tipo de prensa es ideal para operaciones de conformado de metales donde se necesita una fuerza uniforme durante todo el proceso.
Funcionamiento de la prensa hidráulica:
- El sistema hidráulico se basa en el principio de Pascal, el cual establece que cuando se aplica una presión a un fluido en un sistema cerrado, esa presión se distribuye uniformemente en todas las direcciones.
- En una prensa hidráulica, un pistón presuriza un fluido (normalmente aceite) que, a su vez, impulsa el punzón hacia abajo, aplicando la fuerza necesaria para deformar la lámina metálica dentro de la matriz.
- Este proceso permite que la fuerza se aplique de manera controlada y constante, lo que es crucial para garantizar que la pieza metálica se deforme de manera uniforme sin fallos o defectos.
Ventajas de la prensa hidráulica:
- Gran capacidad de fuerza: Las prensas hidráulicas pueden generar una enorme cantidad de fuerza, lo que las hace ideales para embuticiones profundas y piezas metálicas de gran tamaño.
- Control preciso: El sistema hidráulico permite un control exacto sobre la cantidad de fuerza aplicada, lo que es esencial para trabajos que requieren alta precisión.
- Versatilidad: Estas prensas pueden manejar una variedad de materiales, desde metales blandos como el aluminio hasta aceros más duros.
- Uniformidad en la presión: La presión es constante durante todo el proceso, lo que reduce el riesgo de fracturas o defectos en la pieza.
Desventajas de la prensa hidráulica:
- Velocidad más lenta: En comparación con otros tipos de prensas, las prensas hidráulicas tienden a ser más lentas, lo que puede ser un inconveniente en procesos de producción en masa donde la velocidad es crucial.
- Mayor mantenimiento: El sistema hidráulico requiere un mantenimiento regular para evitar fugas de fluido y otros problemas relacionados con los cilindros hidráulicos.
- Consumo energético: Las prensas hidráulicas suelen tener un mayor consumo de energía debido a la operación del sistema de bombeo de fluido.
Aplicaciones de la prensa hidráulica:
- Industria automotriz: Se utilizan para fabricar grandes componentes de carrocería, como puertas, techos y paneles laterales.
- Fabricación de electrodomésticos: Para la producción de piezas como carcasas de lavadoras y secadoras.
- Industria aeroespacial: En la producción de piezas estructurales que requieren alta resistencia y formas complejas.
3.2 Prensa mecánica
La prensa mecánica funciona a través de un sistema de engranajes y levas que convierten el movimiento rotatorio en movimiento lineal, impulsando el punzón hacia abajo para deformar la lámina. A diferencia de la prensa hidráulica, la prensa mecánica ofrece una mayor velocidad en el proceso de embutición, lo que la hace ideal para producciones en masa.
Funcionamiento de la prensa mecánica:
- En una prensa mecánica, un motor hace girar un volante que almacena energía cinética. Esta energía se transfiere a un mecanismo de leva o excéntrico que convierte el movimiento rotatorio en un movimiento lineal.
- El movimiento lineal acciona el punzón, que se desplaza hacia abajo y realiza el proceso de embutición.
- A medida que el volante vuelve a su posición inicial, el punzón se retrae y el ciclo se repite rápidamente.
Ventajas de la prensa mecánica:
- Alta velocidad de operación: Las prensas mecánicas pueden realizar ciclos mucho más rápidos que las hidráulicas, lo que las hace ideales para aplicaciones de alta producción.
- Eficiencia energética: Debido al uso del volante para almacenar y transferir energía, las prensas mecánicas suelen ser más eficientes energéticamente que las prensas hidráulicas.
- Precisión en la repetición: La prensa mecánica es muy eficaz en procesos de producción repetitiva, donde se necesitan realizar muchas piezas idénticas.
Desventajas de la prensa mecánica:
- Menor control de la fuerza: A diferencia de las prensas hidráulicas, las prensas mecánicas no tienen un control tan preciso sobre la cantidad de fuerza aplicada, lo que puede ser una limitación en aplicaciones que requieren un embutido profundo o materiales más frágiles.
- Restricciones de tamaño: Las prensas mecánicas están limitadas por la cantidad de fuerza que pueden generar, lo que las hace menos adecuadas para piezas muy grandes o metales gruesos.
- Mayor desgaste: Los componentes mecánicos, como los engranajes y las levas, pueden desgastarse con el tiempo, lo que aumenta la necesidad de mantenimiento.
Aplicaciones de la prensa mecánica:
- Fabricación de piezas pequeñas y medianas: Como componentes de automóviles, electrodomésticos y piezas metálicas en serie.
- Estampado: Las prensas mecánicas son ampliamente utilizadas en procesos de estampado en la industria metalúrgica, donde se requiere alta velocidad y precisión.
3.3 Prensa neumática
La prensa neumática utiliza aire comprimido para generar la fuerza que impulsa el punzón hacia abajo. Aunque estas prensas no son tan potentes como las hidráulicas, ofrecen una excelente precisión y velocidad, lo que las hace ideales para piezas más pequeñas o procesos que requieren alta repetición.
Funcionamiento de la prensa neumática:
- El aire comprimido se utiliza para accionar un pistón que impulsa el punzón hacia abajo. Cuando se libera el aire, el pistón retorna a su posición original.
- Este tipo de prensa puede controlarse de manera muy precisa mediante válvulas de aire, lo que permite ajustar tanto la presión como la velocidad del proceso.
Ventajas de la prensa neumática:
- Velocidad y precisión: Las prensas neumáticas son rápidas y permiten un control preciso de la presión aplicada, lo que es ideal para procesos que requieren repetitividad y exactitud.
- Bajo costo operativo: El aire comprimido es un recurso relativamente barato y fácil de mantener, lo que reduce los costos operativos de la prensa.
- Mantenimiento simple: Las prensas neumáticas tienen menos componentes mecánicos que otras prensas, lo que simplifica el mantenimiento y reduce la probabilidad de fallos mecánicos.
Desventajas de la prensa neumática:
- Fuerza limitada: Las prensas neumáticas no pueden generar la misma cantidad de fuerza que las prensas hidráulicas o mecánicas, lo que las limita a aplicaciones más ligeras o de menor tamaño.
- Dependencia del aire comprimido: Estas prensas requieren un suministro constante de aire comprimido, lo que puede ser un inconveniente en instalaciones sin sistemas de aire adecuados.
Aplicaciones de la prensa neumática:
- Industria electrónica: En la producción de componentes electrónicos y ensamblajes pequeños.
- Procesos rápidos y repetitivos: Como el corte o el estampado de piezas pequeñas que requieren alta precisión.
- Industria de envases: Fabricación de piezas ligeras, como tapas de envases metálicos.
3.4 Prensas servoaccionadas
Las prensas servoaccionadas representan una innovación reciente en la industria del embutido profundo. Estas prensas utilizan servomotores para controlar con precisión el movimiento del punzón, lo que permite ajustar tanto la fuerza como la velocidad en tiempo real. Las prensas servoaccionadas ofrecen lo mejor de ambos mundos: la potencia de una prensa hidráulica combinada con la velocidad y eficiencia de una prensa mecánica.
Funcionamiento de la prensa servoaccionada:
- Los servomotores controlan el movimiento del punzón mediante una señal eléctrica, lo que permite un ajuste fino de los parámetros del proceso, como la velocidad, la posición y la fuerza.
- El sistema de control de la prensa puede programarse para realizar operaciones complejas, como embutidos múltiples o embutidos a diferentes velocidades, según las necesidades de la pieza.
Ventajas de la prensa servoaccionada:
- Control total: Las prensas servoaccionadas permiten un control total sobre los parámetros del proceso, lo que resulta en una mayor flexibilidad y precisión.
- Alta eficiencia: Al combinar fuerza y velocidad en una sola máquina, las prensas servoaccionadas optimizan el tiempo de ciclo sin comprometer la calidad del embutido.
- Menor desgaste: Al no depender de mecanismos mecánicos complejos, estas prensas tienen menos desgaste y requieren menos mantenimiento que las prensas tradicionales.
Desventajas de la prensa servoaccionada:
- Costo inicial elevado: Las prensas servoaccionadas son más costosas que las prensas hidráulicas o mecánicas tradicionales, lo que puede ser una barrera para algunas empresas.
- Requiere programación avanzada: La operación de una prensa servoaccionada requiere personal capacitado para programar y controlar el sistema, lo que puede aumentar los costos de capacitación.
Aplicaciones de la prensa servoaccionada:
- Producción de alta precisión: En industrias donde la calidad y la precisión son críticas, como la fabricación de componentes médicos o piezas aeroespaciales.
- Producción en masa de piezas complejas: Las prensas servoaccionadas son ideales para la producción en masa de piezas que requieren embutidos con diferentes niveles de complejidad.
Materiales utilizados en el proceso de embutición profunda
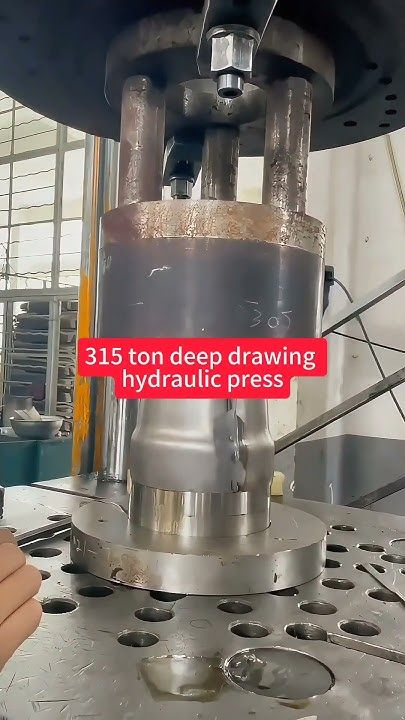
El embutido profundo es un proceso de conformado de metales que implica la deformación plástica de una lámina metálica mediante la aplicación de fuerza controlada. La elección de los materiales adecuados es fundamental para garantizar la calidad de las piezas producidas y el éxito del proceso. Los materiales utilizados en la embutición profunda deben tener ciertas propiedades que les permitan soportar el estiramiento y la compresión sin romperse ni generar defectos en la pieza.
A continuación, analizaremos los tipos de metales y aleaciones más comunes en este proceso, sus propiedades y cómo influyen en la calidad del producto final.
4.1 Tipos de metales y aleaciones comunes en la embutición profunda
- Acero:
- El acero es uno de los materiales más utilizados en la embutición profunda, debido a su combinación de resistencia y ductilidad. Existen varios tipos de acero que se emplean en este proceso, entre los que destacan el acero al carbono y el acero inoxidable.
- Acero al carbono: Este tipo de acero tiene un contenido de carbono que varía entre el 0,05 % y el 2,1 %, lo que le da una gran resistencia y dureza. Es ideal para piezas que requieren alta resistencia estructural, como paneles de carrocería de automóviles y piezas industriales.
- Acero inoxidable: Gracias a su resistencia a la corrosión y su durabilidad, el acero inoxidable es ampliamente utilizado en la fabricación de productos que estarán expuestos a ambientes agresivos o a líquidos, como en la industria alimentaria o de electrodomésticos. El acero inoxidable, sin embargo, es más difícil de embutir debido a su dureza en comparación con otros aceros, lo que requiere mayores fuerzas de presión.
- Aluminio:
- El aluminio es otro material popular en el proceso de embutición profunda, especialmente en la industria aeroespacial y automotriz, debido a su ligereza y resistencia a la corrosión. El aluminio es más maleable que el acero, lo que facilita su deformación sin generar grietas o fallos estructurales.
- La ligereza del aluminio lo hace ideal para aplicaciones donde se necesita reducir el peso sin comprometer la resistencia estructural, como en componentes de aviones o automóviles, donde la eficiencia energética es crucial. Además, su resistencia a la corrosión lo convierte en el material preferido en entornos donde la exposición a la humedad o agentes corrosivos es frecuente.
- Cobre:
- El cobre y sus aleaciones, como el latón y el bronce, también se utilizan en la embutición profunda, especialmente en aplicaciones donde se requiere buena conductividad térmica o eléctrica. El cobre es un material altamente maleable, lo que permite lograr embuticiones profundas con relativa facilidad.
- Los recipientes de cobre y las piezas eléctricas, como terminales y conectores, son ejemplos comunes de productos fabricados mediante embutido profundo. Sin embargo, el costo del cobre suele ser más alto que el de otros materiales, lo que limita su uso a aplicaciones específicas.
- Titanio:
- El titanio es un material utilizado principalmente en aplicaciones de alta tecnología, como la industria aeroespacial y la medicina, debido a su excelente relación resistencia-peso y su resistencia a la corrosión. Aunque es más costoso y más difícil de trabajar que otros materiales, el titanio es esencial para piezas que requieren resistencia a condiciones extremas.
- El titanio se emplea en la fabricación de componentes de aviones, turbinas, y prótesis médicas. El embutido de titanio requiere prensas capaces de generar grandes fuerzas de presión y matrices altamente resistentes al desgaste.
- Aleaciones ligeras:
- Además de los materiales mencionados, algunas aleaciones ligeras de magnesio o aluminio con otros elementos se emplean en aplicaciones que requieren una alta resistencia combinada con un bajo peso. Estas aleaciones son ideales para aplicaciones automotrices y aeroespaciales.
4.2 Propiedades de los materiales que influyen en el embutido
Para que un material sea adecuado para el proceso de embutición profunda, debe poseer una serie de propiedades que le permitan deformarse sin fallos durante el proceso. Algunas de las propiedades más importantes incluyen:
- Ductilidad:
- La ductilidad es la capacidad de un material para deformarse sin romperse cuando se le aplica una fuerza. Los materiales altamente dúctiles, como el aluminio y el cobre, pueden soportar grandes deformaciones plásticas, lo que los hace ideales para el embutido profundo.
- Los materiales menos dúctiles, como algunos tipos de acero de alta resistencia, pueden ser propensos a desarrollar grietas o fracturas si no se controlan adecuadamente las tensiones internas durante el proceso.
- Maleabilidad:
- La maleabilidad es la capacidad de un material para ser comprimido o moldeado sin romperse. Los materiales maleables pueden deformarse en grandes proporciones sin generar defectos, lo que es crucial en el embutido profundo, ya que implica una deformación considerable.
- Elasticidad:
- La elasticidad es la capacidad de un material de volver a su forma original después de ser deformado. Aunque en el embutido profundo buscamos una deformación plástica (permanente), los materiales más elásticos pueden presentar dificultades porque tienden a “rebotar” después de la deformación. Esto puede afectar la precisión del proceso si no se controla adecuadamente.
- Resistencia a la tracción:
- La resistencia a la tracción es la fuerza máxima que un material puede soportar antes de romperse. En el embutido profundo, los materiales con alta resistencia a la tracción pueden soportar grandes tensiones, lo que es crucial para mantener la integridad estructural durante el proceso.
- Espesor del material:
- El grosor de la lámina metálica juega un papel importante en el proceso de embutido. Las láminas más delgadas son más fáciles de deformar, pero son más susceptibles a arrugas y defectos. Las láminas más gruesas, por otro lado, requieren mayores fuerzas de presión, lo que puede aumentar la probabilidad de fallos si no se controla bien el proceso.
4.3 Comportamiento de los metales durante el embutido profundo
Durante el embutido profundo, los materiales metálicos experimentan una serie de cambios en su estructura interna. A medida que el punzón de la prensa aplica presión sobre la lámina metálica, el material pasa de un estado elástico (en el cual puede volver a su forma original) a un estado plástico (donde la deformación es permanente).
Este cambio ocurre debido a la redistribución de las tensiones internas en el material, lo que permite que el metal fluya y adopte la forma de la matriz sin fracturarse. Sin embargo, si las tensiones internas son demasiado altas o si el material no tiene suficiente ductilidad, pueden ocurrir defectos como:
- Grietas: Si el material no tiene suficiente ductilidad, puede fracturarse en las zonas donde las tensiones son más altas.
- Arrugas: Si la lámina no se sostiene correctamente durante el embutido, pueden formarse arrugas en los bordes de la pieza.
- Tensión en el reborde: Los bordes de la lámina metálica son especialmente susceptibles a las tensiones, lo que puede generar deformaciones no deseadas si no se controla adecuadamente el proceso.
4.4 Factores que afectan el rendimiento del material en el embutido profundo
- Calidad del material:
- La calidad del metal o aleación influye directamente en el éxito del proceso de embutido. Las impurezas o imperfecciones en el material pueden generar defectos durante el embutido, lo que afecta la resistencia y la apariencia de la pieza final.
- Temperatura del material:
- En algunos casos, los metales se calientan antes de ser embutidos para aumentar su ductilidad y reducir la probabilidad de fracturas. El embutido en caliente es común para materiales más duros, como el acero, que son difíciles de deformar a temperatura ambiente.
- Lubricación:
- La lubricación es crucial para reducir la fricción entre la lámina metálica y las herramientas de la prensa, lo que permite un flujo más suave del material y reduce el riesgo de defectos.
Procesos relacionados con la prensa profunda
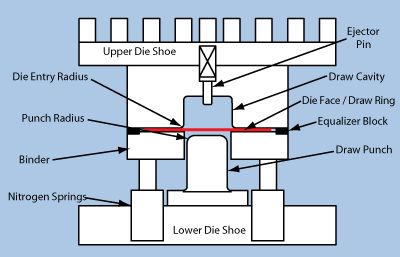
El proceso de embutición profunda es el principal método utilizado en la prensa profunda, pero no es el único. Existen otros procesos complementarios que se realizan en conjunto con la prensa profunda o como parte de un ciclo de operaciones, diseñados para mejorar la calidad del producto, optimizar la eficiencia y permitir la creación de piezas más complejas. A continuación, analizaremos el embutido profundo, embutición inversa, recalcado, planchado, y otros procesos relacionados.
5.1 Embutición profunda
El embutido profundo es el proceso clave en la prensa profunda y uno de los métodos más efectivos para la producción de piezas metálicas con formas huecas y cavidades profundas. Es ampliamente utilizado en la industria automotriz, aeroespacial, de envases y de electrodomésticos.
Proceso detallado del embutido profundo:
El embutido profundo comienza con una lámina metálica plana, que se coloca sobre una matriz con la forma deseada. Un punzón aplica presión sobre la lámina, forzando al material a deformarse y adaptarse a la forma de la matriz. Durante este proceso, el metal se estira y fluye hacia abajo, llenando completamente la cavidad de la matriz y adoptando una nueva forma tridimensional.
El embutido profundo permite obtener piezas de forma cilíndrica, rectangular, esférica, o cualquier otra forma compleja que requiera una cavidad profunda. Este proceso es ideal para la producción de piezas huecas como recipientes, latas, tazas y piezas automotrices.
Ventajas del embutido profundo:
- Reducción de ensamblajes: El embutido profundo permite fabricar piezas enteras en una sola operación o con pocas etapas, lo que reduce la necesidad de ensamblajes adicionales.
- Alta precisión: El proceso garantiza que las piezas finales tengan formas precisas y consistentes, con superficies lisas y acabados de alta calidad.
- Ahorro de material: En comparación con otros procesos, el embutido profundo genera menos desperdicio de material, ya que la lámina se deforma sin cortarse.
- Producción de grandes volúmenes: Es un proceso altamente eficiente para la fabricación en masa de componentes, lo que lo hace ideal para la industria automotriz y de envases.
Fases del embutido profundo:
- Corte de la lámina: Antes de iniciar el embutido, la lámina de metal se corta a un tamaño adecuado para el proceso.
- Sujeción: La lámina cortada se coloca en la prensa profunda, donde un sistema de sujeción la mantiene fija y previene arrugas o movimientos indeseados.
- Embutido: El punzón aplica presión sobre la lámina, empujándola hacia la matriz y deformándola de manera plástica para adoptar la forma deseada.
- Liberación: Una vez que la pieza ha sido embutida correctamente, el punzón se retrae y la pieza es extraída de la matriz.
- Acabado: Dependiendo de la aplicación, algunas piezas pueden requerir operaciones adicionales, como recortes o conformados adicionales, para obtener la forma final.
5.2 Embutición inversa
La embutición inversa es una variación del proceso de embutido profundo que se utiliza para crear piezas más complejas. En lugar de forzar la lámina hacia dentro de una matriz convencional, en la embutición inversa, el punzón empuja el material hacia una dirección opuesta o inversa, lo que permite que las paredes de la pieza se plieguen hacia el interior. Este proceso es útil para la fabricación de piezas que requieren diferentes secciones de diámetros o formas complejas.
Aplicaciones de la embutición inversa:
- Fabricación de recipientes y cilindros con múltiples diámetros: En algunos casos, es necesario que una pieza tenga secciones con diferentes diámetros o formas. La embutición inversa permite obtener estas formas en una sola operación.
- Piezas automotrices: En la industria automotriz, se utiliza para fabricar componentes de motor o piezas estructurales que requieren diferentes grosores o formas a lo largo de su longitud.
- Productos cilíndricos complejos: La embutición inversa se emplea comúnmente en la fabricación de cilindros metálicos con diferentes perfiles.
5.3 Recalcado
El recalcado es un proceso complementario que se utiliza para aumentar la densidad y resistencia de una pieza metálica en áreas específicas, como los extremos o las secciones donde se requiere una mayor resistencia estructural. En este proceso, la pieza ya formada (generalmente embutida) se somete a una compresión adicional, aumentando su grosor en ciertas áreas y mejorando su resistencia.
El recalcado se utiliza principalmente en la fabricación de piezas metálicas que deben soportar grandes tensiones o cargas, como los pistones de motores, pernos, y otros componentes de máquinas.
Ventajas del recalcado:
- Mejora de la resistencia: Al aumentar el grosor de la pieza en áreas clave, el recalcado mejora la resistencia de la pieza a la fatiga y al desgaste.
- Optimización del uso de material: El proceso permite aumentar el grosor solo en las áreas donde es necesario, lo que reduce el peso total de la pieza y optimiza el uso del material.
Aplicaciones del recalcado:
- Industria automotriz: Para aumentar la resistencia de componentes críticos del motor y otras piezas sometidas a grandes esfuerzos.
- Fabricación de herramientas: En la producción de herramientas de corte o impacto, el recalcado se utiliza para reforzar las secciones que están en contacto directo con las fuerzas más intensas.
5.4 Planchado
El planchado es otro proceso complementario que se realiza comúnmente después del embutido profundo para lograr una reducción del grosor de las paredes de una pieza embutida, con el objetivo de obtener una mayor uniformidad o mejorar el acabado superficial. El planchado es especialmente útil en la fabricación de piezas de metal que deben tener paredes delgadas y precisas, como latas de bebidas o contenedores de alimentos.
Proceso de planchado:
- La pieza embutida se pasa a través de una matriz de planchado, que aplica una presión controlada sobre las paredes de la pieza, comprimiendo el material y reduciendo su grosor.
- A medida que las paredes de la pieza se adelgazan, el material se estira y se alisa, lo que mejora el acabado superficial y garantiza una distribución uniforme del material.
Ventajas del planchado:
- Paredes más delgadas: El planchado permite obtener piezas con paredes finas pero resistentes, lo que es ideal para envases y recipientes ligeros.
- Mejoras en el acabado: El planchado mejora el acabado superficial de la pieza, eliminando imperfecciones y alisando la superficie.
Aplicaciones del planchado:
- Fabricación de envases metálicos: En la producción de latas de bebidas y alimentos, el planchado es esencial para obtener paredes delgadas y precisas.
- Componentes electrónicos: Se utiliza para fabricar piezas de metal con espesores reducidos y acabados de alta calidad para la industria electrónica.
5.5 Consideraciones técnicas en los procesos de embutido y planchado
El éxito de los procesos de embutido, recalcado y planchado depende de varios factores técnicos que deben controlarse cuidadosamente para evitar defectos y garantizar la calidad del producto final.
- Control de la fricción:
- La fricción entre la lámina metálica y las herramientas de la prensa (punzón, matriz y sujeciones) debe controlarse mediante el uso adecuado de lubricantes. Un nivel de fricción demasiado alto puede causar desgastes en las herramientas, arrugas en el material o incluso grietas.
- Lubricación:
- La lubricación es un aspecto crítico en todos los procesos relacionados con la prensa profunda. Los lubricantes ayudan a reducir la fricción entre el material y las herramientas, mejorando el flujo del metal y evitando defectos como arrugas, desgastes o fracturas. Además, la lubricación también protege las herramientas del desgaste, lo que prolonga su vida útil.
- Tipos de lubricantes: Dependiendo del material y el tipo de prensa utilizada, se emplean diferentes tipos de lubricantes, como aceites minerales, grafito, cera o emulsiones.
- Temperatura del material:
- La temperatura del material puede influir significativamente en su ductilidad. Algunos materiales, como el acero de alta resistencia, pueden requerir un proceso de embutido en caliente para mejorar su deformabilidad y evitar fracturas. Sin embargo, el embutido en caliente también implica mayores costos energéticos y un mayor desgaste de las herramientas.
- Velocidad de embutido:
- La velocidad a la que se realiza el embutido debe ajustarse adecuadamente. Un embutido demasiado rápido puede generar tensiones internas excesivas, lo que aumenta el riesgo de fracturas o arrugas en la pieza. Un proceso controlado y gradual mejora la calidad del producto final.
Diseño de matrices para prensa profunda
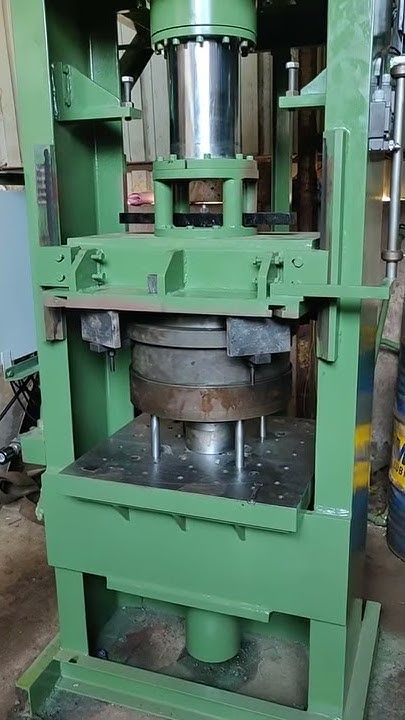
El éxito del proceso de embutición profunda depende en gran medida del diseño adecuado de las matrices. Las matrices son los moldes que le dan forma a la lámina metálica a medida que se deforma bajo la acción del punzón en la prensa profunda. Un diseño de matriz óptimo asegura que la pieza final tenga la forma y dimensiones correctas, evitando defectos como arrugas, fracturas o tensiones no deseadas.
6.1 El rol de las matrices en el proceso de embutición profunda
Las matrices son esenciales en la prensa profunda, ya que definen la geometría de la pieza que se va a fabricar. Durante el embutido profundo, la lámina de metal se deforma plásticamente y adopta la forma de la cavidad de la matriz. Las matrices deben estar diseñadas para soportar las enormes fuerzas que se generan durante el embutido, al mismo tiempo que garantizan que la lámina fluya de manera uniforme, sin que se produzcan fallos.
El diseño de una matriz depende del tipo de pieza que se va a fabricar, el grosor y las propiedades del material, y el tipo de proceso que se está utilizando. Las matrices de embutición profunda están diseñadas para trabajar en conjunto con otros componentes de la prensa, como el punzón y el contrapunzón, lo que permite una operación coordinada y precisa.
6.2 Materiales utilizados en la fabricación de matrices
Las matrices deben ser extremadamente resistentes para soportar el desgaste continuo y las tensiones aplicadas durante el proceso de embutido. Debido a la naturaleza del trabajo, las matrices se fabrican con materiales de alta resistencia que son capaces de mantener su forma y funcionalidad después de múltiples ciclos de embutido. Algunos de los materiales más comunes utilizados para fabricar matrices incluyen:
- Aceros endurecidos:
- Los aceros de alta resistencia son los materiales más comúnmente utilizados en la fabricación de matrices. Los aceros templados y aleaciones de acero son resistentes al desgaste y ofrecen una excelente capacidad para soportar la presión y el impacto.
- Los aceros de alta dureza, como el acero para herramientas, se seleccionan para matrices que estarán en contacto constante con metales duros, como el acero inoxidable o el acero al carbono.
- Carburo de tungsteno:
- En aplicaciones que requieren una durabilidad extrema, se utilizan matrices de carburo de tungsteno, un material extremadamente duro y resistente al desgaste. Aunque más costoso que los aceros, el carburo de tungsteno puede soportar mucho más desgaste, lo que lo hace ideal para prensas de alta producción o materiales muy duros.
- Este material es común en matrices que estarán sometidas a esfuerzos elevados y abrasión constante.
- Aleaciones especiales:
- En algunos casos, se utilizan aleaciones específicas con propiedades adicionales, como resistencia a la corrosión o alta dureza a temperaturas elevadas. Estas aleaciones son ideales para aplicaciones especializadas, como la industria aeroespacial o médica.
6.3 Tipos de matrices según el tipo de pieza y proceso
El diseño de las matrices varía según el tipo de pieza que se está fabricando y el proceso específico de embutido que se va a realizar. A continuación, se presentan algunos de los tipos de matrices más comunes utilizadas en el embutido profundo:
- Matriz de embutido simple:
- Este es el tipo de matriz más básico y se utiliza para crear piezas con cavidades simples y formas poco complejas. Consiste en una sola cavidad que define la forma de la pieza.
- Se utiliza en aplicaciones donde el embutido se realiza en una sola etapa, como en la producción de recipientes o tazas simples.
- Matriz de embutición múltiple:
- En piezas más complejas, que requieren varios pasos de embutido para obtener la forma final, se utiliza una matriz de embutición múltiple. Esta matriz permite realizar varios embutidos sucesivos en diferentes etapas del proceso.
- Es común en la fabricación de componentes automotrices y piezas que requieren formas complejas, como cilindros con múltiples diámetros.
- Matriz progresiva:
- Una matriz progresiva permite realizar múltiples operaciones de embutido y conformado en una sola máquina. Este tipo de matriz es ideal para la producción en masa, ya que reduce el tiempo de operación y la necesidad de reubicar la pieza entre diferentes máquinas.
- Es ampliamente utilizada en la producción de piezas pequeñas y medianas, como componentes electrónicos o piezas de precisión.
- Matriz compuesta:
- Las matrices compuestas están diseñadas para realizar operaciones de embutido y otras funciones, como troquelado o perforado, en una sola pasada. Este tipo de matriz es eficiente para producir piezas complejas en menos tiempo y con menos manipulaciones de la pieza.
- Se utilizan principalmente en la fabricación de piezas que requieren agujeros, recortes o cortes precisos durante el proceso de embutido.
6.4 Consideraciones en el diseño de matrices
El diseño de una matriz para embutido profundo es un proceso complejo que debe tener en cuenta varios factores para garantizar la calidad de la pieza final y la eficiencia del proceso. Algunas de las consideraciones más importantes en el diseño de matrices incluyen:
- Tolerancias dimensionales:
- Las tolerancias son las variaciones permitidas en las dimensiones de una pieza. En el diseño de matrices, es crucial asegurarse de que las tolerancias sean lo suficientemente estrictas para garantizar la calidad de la pieza, pero no tan ajustadas que dificulten la producción.
- Las matrices deben diseñarse con tolerancias que tengan en cuenta la expansión o contracción del material durante el embutido.
- Radio de las esquinas:
- Los radios de las esquinas de la matriz son críticos para evitar concentraciones de tensión que puedan provocar fracturas o deformaciones no deseadas. Un radio adecuado asegura que el material fluya suavemente durante el embutido, reduciendo el riesgo de fallos.
- Un radio de esquina más grande facilita el embutido, mientras que un radio más pequeño aumenta la precisión, pero también incrementa el riesgo de defectos.
- Superficie de contacto:
- La superficie de contacto entre la matriz y el material debe estar cuidadosamente diseñada para minimizar la fricción y evitar el desgaste prematuro de la matriz. La aplicación de lubricantes y el uso de materiales de alta dureza en las áreas de contacto pueden prolongar la vida útil de la matriz.
- Ángulo de desmoldeo:
- El ángulo de desmoldeo es la inclinación de las paredes de la matriz que permite que la pieza embutida se libere fácilmente después del proceso. Un ángulo adecuado asegura que la pieza no se quede atascada en la matriz, lo que podría dañar tanto la pieza como la herramienta.
- Este ángulo debe diseñarse de acuerdo con el tipo de material y la geometría de la pieza final.
- Desgaste y mantenimiento:
- Dado que las matrices están sometidas a un desgaste continuo, es importante considerar la facilidad de mantenimiento y reemplazo de las matrices. Diseñar matrices modulares, donde los componentes desgastables se puedan reemplazar fácilmente, reduce los tiempos de inactividad y mejora la eficiencia general del proceso.
6.5 Innovaciones en el diseño de matrices
En los últimos años, han surgido varias innovaciones en el diseño de matrices que han mejorado significativamente la calidad, precisión y eficiencia del proceso de embutición profunda. Algunas de estas innovaciones incluyen:
- Matrices controladas por CNC:
- Las matrices controladas por CNC (Control Numérico por Computadora) permiten realizar ajustes de forma automática y en tiempo real, lo que mejora la precisión del proceso. Estas matrices pueden adaptarse rápidamente a diferentes tolerancias y formas, reduciendo el tiempo de preparación y ajustando los parámetros según el material o la pieza.
- Esto es particularmente útil en la producción en masa de piezas que requieren variaciones de forma o tamaño.
- Matrices de alta precisión:
- Las tecnologías avanzadas de fabricación, como el mecanizado de precisión y la impresión 3D de metales, han permitido la creación de matrices con tolerancias extremadamente estrictas y formas complejas que antes no eran posibles con los métodos tradicionales.
- Estas matrices se utilizan en aplicaciones de alta tecnología, como la fabricación de piezas para la industria aeroespacial y la electrónica de precisión.
- Recubrimientos avanzados:
- Los recubrimientos de las matrices, como el recubrimiento de nitruro de titanio (TiN) o carburo de tungsteno, han mejorado significativamente la resistencia al desgaste y la durabilidad de las matrices. Estos recubrimientos permiten que las matrices trabajen con materiales más duros y prolongan su vida útil.
Aplicaciones industriales de la prensa profunda
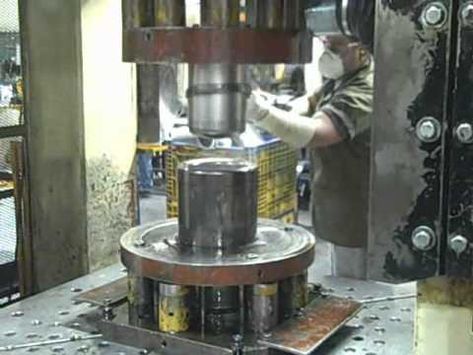
El uso de la prensa profunda se ha extendido a una variedad de sectores industriales debido a su capacidad para crear piezas de metal con formas complejas, cavidades profundas y altos niveles de precisión. Este proceso es ideal para la producción en masa de componentes que requieren resistencia, ligereza y uniformidad. A continuación, exploraremos algunas de las aplicaciones más comunes de la prensa profunda en diferentes industrias clave.
7.1 Industria automotriz
La industria automotriz es una de las principales beneficiarias del proceso de embutición profunda. Las prensas profundas se utilizan para fabricar una amplia gama de componentes metálicos esenciales en la construcción de automóviles. Los fabricantes de automóviles dependen de este proceso para producir piezas que cumplan con los estándares de calidad y seguridad, así como con los requisitos de peso y durabilidad.
Componentes fabricados mediante embutición profunda:
- Paneles de carrocería:
- Los paneles de las puertas, los techos y los capós de los automóviles se fabrican utilizando prensas profundas. Estos paneles deben tener un acabado suave y una forma precisa para que encajen perfectamente en el ensamblaje del vehículo.
- La embutición profunda permite crear paneles con cavidades, dobleces y formas tridimensionales sin comprometer la integridad estructural de la pieza.
- Estructuras del chasis:
- Componentes clave del chasis, como soportes y refuerzos, se producen mediante embutición profunda para garantizar la rigidez y resistencia del vehículo. Estos componentes deben soportar grandes cargas y tensiones, especialmente en caso de colisión, por lo que la calidad del proceso es crucial.
- Piezas del motor:
- Las prensas profundas también se utilizan para fabricar piezas internas del motor, como carcasas de motores, pistones y partes de sistemas de escape. Estas piezas requieren alta precisión y resistencia a temperaturas extremas.
Beneficios del uso de la prensa profunda en la industria automotriz:
- Reducción de peso: La embutición profunda permite producir piezas ligeras pero fuertes, lo que contribuye a mejorar la eficiencia del combustible de los vehículos.
- Mayor resistencia a impactos: Las piezas embutidas tienen una mayor resistencia a los impactos, lo que mejora la seguridad del vehículo.
- Producción en masa eficiente: La capacidad de producir grandes volúmenes de piezas en poco tiempo hace que el proceso sea ideal para la fabricación en masa en la industria automotriz.
7.2 Industria aeroespacial
La industria aeroespacial es otro sector que se beneficia enormemente del uso de prensas profundas. Los aviones y otros equipos aeroespaciales requieren componentes que sean extremadamente ligeros, pero también resistentes a condiciones extremas, como altas presiones, temperaturas y vibraciones. El embutido profundo permite producir piezas que cumplen con estos estrictos requisitos.
Aplicaciones en la industria aeroespacial:
- Carcasas de motores y turbinas:
- Las carcasas de los motores a reacción y las turbinas están sometidas a tensiones extremas durante el vuelo. Estas piezas se fabrican mediante embutición profunda para garantizar que tengan la resistencia necesaria sin agregar peso excesivo a la aeronave.
- Paneles estructurales:
- Los paneles que forman el fuselaje y las alas de un avión deben ser ligeros para mejorar la eficiencia del combustible, pero también lo suficientemente resistentes para soportar las tensiones del vuelo. La embutición profunda permite producir estos paneles con formas complejas que mejoran la aerodinámica y la resistencia estructural.
- Componentes internos:
- Partes más pequeñas, como refuerzos internos, soportes de cabina y piezas de sistemas hidráulicos, también se fabrican mediante embutición profunda. Estos componentes deben cumplir con tolerancias estrictas y ser extremadamente confiables.
Ventajas de la prensa profunda en la industria aeroespacial:
- Reducción del peso total: Las piezas embutidas son más ligeras, lo que mejora la eficiencia del combustible y reduce los costos operativos.
- Mayor resistencia estructural: Las piezas fabricadas mediante embutido profundo tienen una mayor capacidad para resistir tensiones y cargas sin fallar.
- Alta precisión: La industria aeroespacial exige un nivel de precisión extremo, y la embutición profunda permite cumplir con estas exigencias.
7.3 Fabricación de electrodomésticos
La industria de electrodomésticos utiliza ampliamente el proceso de embutición profunda para fabricar componentes metálicos como carcasas y piezas internas de productos como lavadoras, secadoras, refrigeradores y estufas. Este proceso garantiza que las piezas tengan un acabado suave y preciso, lo que es crucial tanto para la funcionalidad como para la estética de los electrodomésticos.
Aplicaciones en la fabricación de electrodomésticos:
- Carcasas exteriores:
- Las carcasas de electrodomésticos, como los paneles de lavadoras y refrigeradores, se fabrican mediante embutición profunda para garantizar un acabado liso y uniforme. Estas piezas también deben ser lo suficientemente robustas para soportar el uso diario y resistir la corrosión.
- Tambor de lavadora:
- El tambor de las lavadoras se fabrica mediante embutido profundo para crear una pieza cilíndrica con un acabado uniforme y resistente. Este componente debe ser resistente al desgaste y la corrosión, ya que está en contacto constante con agua y detergentes.
- Componentes internos:
- Además de las carcasas, muchos componentes internos de los electrodomésticos, como soportes y refuerzos, se producen mediante embutido profundo. Estos componentes requieren precisión para encajar correctamente en el ensamblaje del producto.
Ventajas del embutido profundo en la fabricación de electrodomésticos:
- Acabados suaves y precisos: La embutición profunda garantiza que las piezas tengan un acabado estético y funcional, lo que es crucial para los electrodomésticos.
- Resistencia al desgaste: Las piezas embutidas tienen una mayor resistencia a la corrosión y al desgaste, lo que prolonga la vida útil de los electrodomésticos.
- Producción en grandes volúmenes: El embutido profundo permite fabricar grandes cantidades de piezas de manera eficiente, lo que reduce los costos de producción en la industria de electrodomésticos.
7.4 Industria del envasado
La industria del envasado es una de las mayores usuarias de prensas profundas, especialmente en la producción de latas de bebidas, contenedores de alimentos, y otros tipos de envases metálicos. El embutido profundo permite crear envases metálicos con formas uniformes y ligeras, lo que es crucial para optimizar el transporte y almacenamiento de productos.
Aplicaciones en la industria del envasado:
- Latas de bebidas:
- Las latas de bebidas, como las utilizadas para refrescos y cervezas, se fabrican mediante embutido profundo a partir de láminas de aluminio o acero. El proceso de embutido asegura que las latas tengan paredes delgadas pero resistentes, lo que reduce el peso sin comprometer la durabilidad.
- Recipientes de alimentos:
- Los recipientes metálicos para alimentos, como las latas de conservas, también se producen mediante embutición profunda. Estas latas deben tener una forma precisa y un acabado uniforme para garantizar que se puedan sellar correctamente y mantener la integridad de los alimentos en su interior.
- Envases de aerosoles:
- Los envases de aerosoles, como los utilizados para productos de limpieza o cosméticos, se fabrican mediante embutición profunda para garantizar que tengan una estructura resistente capaz de soportar la presión interna.
Beneficios de la prensa profunda en la industria del envasado:
- Eficiencia en la producción en masa: La embutición profunda permite producir millones de envases idénticos de manera eficiente y rápida, lo que es esencial para la industria del envasado.
- Reducción de peso: Las latas y envases embutidos son ligeros, lo que reduce los costos de transporte y almacenamiento.
- Alta resistencia: A pesar de su ligereza, los envases embutidos son lo suficientemente resistentes como para soportar las presiones internas de los productos envasados.
7.5 Industria de equipos médicos
En la industria médica, la precisión y la calidad son fundamentales. El embutido profundo se utiliza en la fabricación de componentes metálicos para equipos médicos y dispositivos quirúrgicos, como prótesis, implantes y herramientas quirúrgicas. Estos productos deben cumplir con estrictos estándares de calidad y seguridad para garantizar que puedan utilizarse de manera confiable en entornos médicos.
Aplicaciones en la industria médica:
- Implantes y prótesis:
- Los implantes ortopédicos, como las caderas y las rodillas artificiales, se fabrican mediante embutición profunda para garantizar que tengan la forma correcta y la resistencia necesaria para soportar el uso a largo plazo.
- Instrumentos quirúrgicos:
- Las herramientas quirúrgicas, como pinzas, tijeras y bisturíes, se fabrican con prensas profundas para obtener piezas de metal precisas y duraderas. Estas herramientas deben ser fáciles de esterilizar y deben resistir la corrosión y el desgaste durante los procedimientos quirúrgicos.
- Componentes de dispositivos médicos:
- La embutición profunda también se utiliza para fabricar partes de dispositivos médicos más grandes, como marcos y estructuras para equipos de diagnóstico o tratamiento.
Ventajas del embutido profundo en la industria médica:
- Alta precisión: La embutición profunda permite fabricar piezas extremadamente precisas, lo que es crucial para dispositivos médicos y quirúrgicos.
- Resistencia a la corrosión: Las piezas embutidas en materiales como acero inoxidable o titanio son altamente resistentes a la corrosión, lo que es esencial para su uso en entornos médicos.
Avances tecnológicos en prensas profundas
El desarrollo tecnológico ha transformado el funcionamiento de las prensas profundas, permitiendo que este proceso de conformado de metales sea más eficiente, preciso y adaptable a los requerimientos modernos de la industria. Las innovaciones abarcan desde el control numérico por computadora (CNC) y la automatización, hasta la integración de sistemas inteligentes y el monitoreo en tiempo real. Estos avances han permitido que las prensas profundas se adapten mejor a la producción en masa, garantizando alta precisión y reduciendo el desperdicio de material.
A continuación, analizaremos algunos de los avances tecnológicos más importantes que han revolucionado el uso de las prensas profundas.
8.1 Automatización y control numérico (CNC)
Uno de los avances más significativos en las prensas profundas es la incorporación de sistemas CNC (Control Numérico por Computadora). Este tipo de tecnología permite un control preciso sobre los parámetros del proceso, como la velocidad, la presión y la posición del punzón, lo que mejora significativamente la calidad de las piezas producidas.
Ventajas del CNC en prensas profundas:
- Precisión y repetibilidad:
- El CNC permite que las prensas profundas mantengan niveles de precisión extremadamente altos, lo que es esencial en la producción de piezas complejas y con tolerancias estrictas. Este sistema controla cada aspecto del movimiento del punzón y asegura que las operaciones se repitan de manera exacta en cada ciclo de producción.
- Flexibilidad en el diseño:
- Los sistemas CNC permiten cambios rápidos en el diseño de la pieza sin necesidad de ajustar manualmente la prensa. Los operarios pueden introducir nuevos parámetros o cargar diferentes programas de producción con facilidad, lo que mejora la flexibilidad y reduce los tiempos de preparación de la máquina.
- Optimización de procesos:
- La tecnología CNC permite optimizar el proceso de embutido profundo en función del tipo de material, el grosor de la lámina y las características de la pieza final. El sistema ajusta automáticamente los parámetros para asegurar que el proceso sea lo más eficiente posible.
- Reducción de errores humanos:
- Al eliminar muchas de las operaciones manuales y depender del control computarizado, se reduce significativamente la probabilidad de errores humanos. Esto resulta en menos piezas defectuosas y mayor uniformidad en la producción.
8.2 Prensas inteligentes y sistemas de monitoreo en tiempo real
El avance de la industria 4.0 ha llevado a la introducción de prensas inteligentes que están equipadas con sensores avanzados y sistemas de monitoreo en tiempo real. Estos sistemas permiten recopilar y analizar datos de la prensa durante el proceso de embutido, lo que mejora la precisión y la eficiencia del proceso.
Características de las prensas inteligentes:
- Monitoreo de la presión y la fuerza:
- Las prensas inteligentes están equipadas con sensores de presión que monitorean la fuerza aplicada en tiempo real. Esto permite detectar cualquier desviación en los parámetros de la prensa y ajustar automáticamente la fuerza para asegurar que las piezas sean conformadas correctamente.
- Además, estos sensores pueden detectar picos de presión que podrían dañar la pieza o la máquina, lo que permite implementar medidas correctivas de inmediato.
- Control de calidad en tiempo real:
- Los sistemas de monitoreo en tiempo real permiten identificar defectos potenciales en las piezas durante el proceso, lo que ayuda a reducir el número de productos defectuosos. Si el sistema detecta una anomalía, puede detener el proceso automáticamente para evitar la producción de más piezas defectuosas.
- Optimización del ciclo de producción:
- Al recopilar datos en tiempo real, las prensas inteligentes pueden optimizar continuamente el ciclo de producción. Esto incluye ajustar la velocidad de embutido, la presión aplicada y la lubricación, lo que mejora la calidad del producto y aumenta la vida útil de las herramientas.
- Mantenimiento predictivo:
- Las prensas inteligentes también pueden utilizar los datos recopilados para predecir el desgaste de componentes críticos, como las matrices y los punzones. El mantenimiento predictivo permite realizar reparaciones o reemplazos antes de que ocurra una falla, lo que reduce el tiempo de inactividad y los costos de mantenimiento.
8.3 Uso de servomotores en prensas profundas
El uso de servomotores en las prensas profundas ha permitido un control más preciso y eficiente del proceso de embutido. Las prensas servoaccionadas ofrecen lo mejor de las prensas hidráulicas y mecánicas, ya que combinan la fuerza y la capacidad de las primeras con la velocidad y eficiencia de las segundas.
Beneficios de las prensas servoaccionadas:
- Control total sobre el movimiento del punzón:
- Los servomotores permiten un control preciso sobre la velocidad y posición del punzón, lo que es esencial para la producción de piezas complejas con múltiples fases de embutido. La velocidad del punzón puede ajustarse en tiempo real para garantizar un flujo uniforme del material y evitar defectos como grietas o arrugas.
- Ajustes en tiempo real:
- Las prensas servoaccionadas permiten realizar ajustes dinámicos durante el proceso de embutido. Por ejemplo, el sistema puede modificar la velocidad del embutido en función del material o la forma de la pieza, lo que optimiza el proceso para cada operación específica.
- Menor consumo de energía:
- Las prensas servoaccionadas consumen menos energía que las prensas hidráulicas tradicionales, ya que los servomotores solo consumen energía cuando están en movimiento. Esto reduce los costos operativos y mejora la sostenibilidad ambiental de las operaciones de producción.
- Reducción del ruido y las vibraciones:
- A diferencia de las prensas hidráulicas, que pueden ser ruidosas y generar vibraciones, las prensas servoaccionadas funcionan de manera más silenciosa y suave. Esto mejora las condiciones laborales en las plantas de producción y reduce el desgaste en los componentes de la máquina.
8.4 Integración con sistemas robóticos
Otra tendencia importante en las prensas profundas es la integración de sistemas robóticos para automatizar completamente el proceso de alimentación y extracción de las piezas. Los brazos robóticos pueden encargarse de colocar las láminas metálicas en la prensa y retirar las piezas embutidas de manera rápida y eficiente, lo que mejora significativamente la velocidad de producción y reduce los errores humanos.
Ventajas de la integración robótica:
- Aumento de la velocidad de producción:
- Los sistemas robóticos pueden realizar las operaciones de alimentación y extracción de manera más rápida que los operarios humanos, lo que aumenta el rendimiento de producción y reduce el tiempo de ciclo.
- Mayor consistencia y precisión:
- Los robots operan con un nivel de precisión extremadamente alto, lo que garantiza que cada lámina esté perfectamente alineada en la prensa. Esto reduce el riesgo de errores y mejora la uniformidad de las piezas producidas.
- Reducción del tiempo de inactividad:
- La automatización completa del proceso de alimentación y extracción reduce el tiempo de inactividad entre los ciclos de producción, lo que aumenta la eficiencia general de la prensa.
- Seguridad mejorada:
- Al automatizar las tareas de alimentación y extracción, se reduce la necesidad de intervención manual, lo que mejora la seguridad en el lugar de trabajo. Los operarios ya no tienen que acercarse a las partes móviles de la prensa, lo que minimiza el riesgo de accidentes.
8.5 Ejemplos de innovaciones recientes
Algunas de las innovaciones recientes en prensas profundas incluyen:
- Prensas híbridas:
- Las prensas híbridas combinan los beneficios de las prensas hidráulicas y servoaccionadas, permitiendo un control preciso y eficiente sobre el proceso de embutido profundo, mientras mantienen la capacidad de aplicar grandes fuerzas de manera controlada.
- Tecnología de realidad aumentada (AR):
- Algunas plantas están comenzando a utilizar realidad aumentada para asistir a los operarios en la configuración y el mantenimiento de las prensas profundas. A través de gafas o dispositivos AR, los operarios pueden visualizar instrucciones en tiempo real, lo que facilita las tareas complejas y reduce los errores.
- Uso de inteligencia artificial (IA):
- La IA se está integrando en sistemas de control avanzado para mejorar la eficiencia operativa. Los algoritmos de IA analizan los datos de producción en tiempo real y ajustan automáticamente los parámetros del proceso para mejorar la calidad de las piezas y reducir los desperdicios.
Mantenimiento y optimización de las prensas profundas
El mantenimiento de las prensas profundas es fundamental para asegurar su rendimiento óptimo a lo largo del tiempo y evitar costosos tiempos de inactividad en la producción. Debido a que estas máquinas están sometidas a grandes fuerzas y utilizan componentes de alta precisión, requieren un plan de mantenimiento integral que incluya tanto mantenimiento preventivo como mantenimiento predictivo. Además, la optimización del rendimiento de las prensas profundas es esencial para aumentar la eficiencia, reducir el desgaste de las herramientas y garantizar la calidad de las piezas fabricadas.
En esta sección, exploraremos las prácticas clave de mantenimiento, los procedimientos para optimizar el rendimiento de las prensas y las técnicas para prolongar la vida útil de sus componentes.
9.1 Mantenimiento preventivo y correctivo
El mantenimiento preventivo es esencial para evitar problemas mayores que puedan interrumpir la producción o causar daños permanentes a las prensas profundas. Este tipo de mantenimiento se enfoca en inspeccionar regularmente las máquinas y realizar tareas programadas de limpieza, ajuste y reemplazo de piezas que tienden a desgastarse con el uso.
Componentes clave a inspeccionar en el mantenimiento preventivo:
- Sistemas hidráulicos y neumáticos:
- En las prensas hidráulicas y neumáticas, es crucial revisar los sellos y válvulas para evitar fugas de fluido o aire. Las fugas pueden afectar el rendimiento de la prensa, reduciendo la fuerza aplicada durante el embutido y provocando un mal funcionamiento general.
- El fluido hidráulico debe cambiarse regularmente para evitar la acumulación de contaminantes que puedan dañar el sistema. Además, es importante verificar los niveles de presión y asegurarse de que los componentes neumáticos e hidráulicos estén funcionando correctamente.
- Matrices y punzones:
- Las matrices y los punzones están sometidos a un desgaste constante debido al contacto directo con el metal durante el embutido. Es importante inspeccionarlos regularmente en busca de signos de desgaste, deformación o grietas.
- Si se detecta algún daño, las matrices y punzones deben reemplazarse o repararse de inmediato para evitar defectos en las piezas fabricadas y daños mayores en la prensa.
- Lubricación:
- La lubricación adecuada de las partes móviles de la prensa profunda es esencial para reducir la fricción, prevenir el desgaste y mantener un funcionamiento suave. Los sistemas de lubricación automática, cuando están presentes, deben revisarse para asegurarse de que están suministrando el lubricante de manera uniforme y adecuada.
- Los rodillos, guías y cojinetes deben recibir lubricación de manera regular, según las recomendaciones del fabricante, para prevenir el desgaste prematuro.
- Sistema eléctrico:
- El sistema eléctrico que controla el movimiento de la prensa, especialmente en prensas servoaccionadas o CNC, debe mantenerse en buen estado. Es necesario verificar el correcto funcionamiento de los sensores, motores y paneles de control para evitar fallos inesperados.
- Componentes estructurales:
- La estructura de la prensa, incluidas las bases y columnas, debe revisarse para asegurarse de que no haya fisuras o deformaciones que puedan afectar la estabilidad y seguridad de la máquina. Un mal mantenimiento en este aspecto puede comprometer la alineación de la prensa, generando problemas en el proceso de embutido.
9.2 Mantenimiento predictivo y el uso de sensores
Con el avance de la tecnología, el mantenimiento predictivo se está convirtiendo en una parte fundamental del mantenimiento de prensas profundas. El uso de sensores inteligentes y tecnología de monitoreo en tiempo real permite predecir fallos antes de que ocurran, basándose en datos recopilados durante la operación de la prensa.
Ventajas del mantenimiento predictivo:
- Prevención de fallos:
- Los sensores instalados en las prensas profundas pueden monitorear constantemente el estado de componentes críticos, como las matrices, punzones, y sistemas hidráulicos. Al detectar cambios en la presión, vibraciones inusuales o temperaturas anormales, el sistema puede alertar a los operarios para que realicen un mantenimiento antes de que ocurra una falla.
- Aumento de la vida útil de las herramientas:
- El monitoreo en tiempo real del desgaste de herramientas, como matrices y punzones, permite reemplazarlas o repararlas en el momento oportuno, evitando daños más graves y aumentando su vida útil.
- Reducción del tiempo de inactividad:
- El mantenimiento predictivo minimiza los tiempos de inactividad inesperados al programar intervenciones antes de que ocurra un fallo grave. Esto optimiza la continuidad de la producción y evita costosos retrasos.
- Optimización de costos:
- Al predecir cuándo es necesario realizar reparaciones o reemplazos, las empresas pueden reducir los costos de mantenimiento y prolongar la vida útil de los equipos, mejorando la rentabilidad general.
9.3 Procedimientos de lubricación y limpieza
La lubricación y limpieza de las prensas profundas son cruciales para mantener su funcionamiento óptimo. La fricción entre las piezas móviles puede generar un desgaste excesivo, por lo que es fundamental asegurar que todas las partes estén adecuadamente lubricadas.
Prácticas recomendadas para la lubricación:
- Lubricación automática:
- Muchas prensas modernas están equipadas con sistemas de lubricación automática que distribuyen el lubricante de manera uniforme a las partes móviles. Estos sistemas deben revisarse regularmente para asegurarse de que funcionan correctamente y de que el nivel de lubricante es el adecuado.
- Selección del lubricante adecuado:
- La selección del tipo de lubricante es importante según el tipo de prensa, el material que se está embutiendo y las condiciones de operación. Se utilizan lubricantes con propiedades antidesgaste, anticorrosivas y de alta resistencia a la temperatura para garantizar el rendimiento a largo plazo.
- Limpieza regular:
- La limpieza de las herramientas es igual de importante que la lubricación. Durante el proceso de embutido, es posible que queden restos de metal o lubricante que, si no se eliminan, pueden interferir en las futuras operaciones y causar fallos en el sistema. Se recomienda limpiar las matrices, punzones y guías después de cada ciclo de producción.
9.4 Optimización del rendimiento de las prensas profundas
Optimizar el rendimiento de una prensa profunda no solo implica mantenerla en buen estado, sino también asegurar que el proceso de embutido se realice de la manera más eficiente posible. La optimización se centra en reducir el tiempo de ciclo, mejorar la calidad del producto y prolongar la vida útil de las herramientas.
Estrategias para optimizar el rendimiento:
- Ajuste de los parámetros de la prensa:
- Los operarios deben ajustar correctamente los parámetros de la prensa, como la velocidad de embutido, la presión aplicada y la lubricación. El ajuste incorrecto puede resultar en un proceso de embutido menos eficiente, con el riesgo de producir piezas defectuosas.
- Uso de prensas servoaccionadas:
- Las prensas servoaccionadas ofrecen un mejor control sobre el proceso, lo que permite ajustar la velocidad y fuerza en tiempo real para optimizar la calidad de las piezas y reducir el desgaste de las herramientas.
- Programación de ciclos de producción:
- Planificar ciclos de producción que equilibren la producción continua con los tiempos de mantenimiento preventivo es clave para evitar interrupciones innecesarias y maximizar la productividad.
- Revisión y reemplazo de herramientas:
- Las matrices y punzones deben revisarse regularmente para evitar que herramientas desgastadas o dañadas afecten la calidad de la pieza y el rendimiento de la prensa. Las piezas defectuosas no solo reducen la eficiencia de producción, sino que también aumentan el riesgo de dañar permanentemente las herramientas.
9.5 Solución de problemas comunes
A pesar del mantenimiento adecuado, pueden surgir problemas durante la operación de una prensa profunda. Algunas soluciones para los problemas más comunes incluyen:
- Arrugas en las piezas:
- Las arrugas suelen ocurrir cuando el material no está bien sujeto durante el embutido. Ajustar la sujeción del material o aumentar la presión del contrapunzón puede resolver este problema.
- Grietas en las piezas:
- Las grietas pueden ser el resultado de tensiones excesivas o un material demasiado frágil. La solución puede ser ajustar la velocidad de embutido o el tipo de material utilizado, además de verificar las condiciones de lubricación.
- Desgaste excesivo de matrices y punzones:
- Si las herramientas se desgastan demasiado rápido, es probable que el lubricante no sea adecuado o que los parámetros de la prensa no estén optimizados. Reemplazar las herramientas desgastadas y ajustar los parámetros puede mejorar la situación.
Máquina rebordeadora: Aplicaciones y funcionamiento
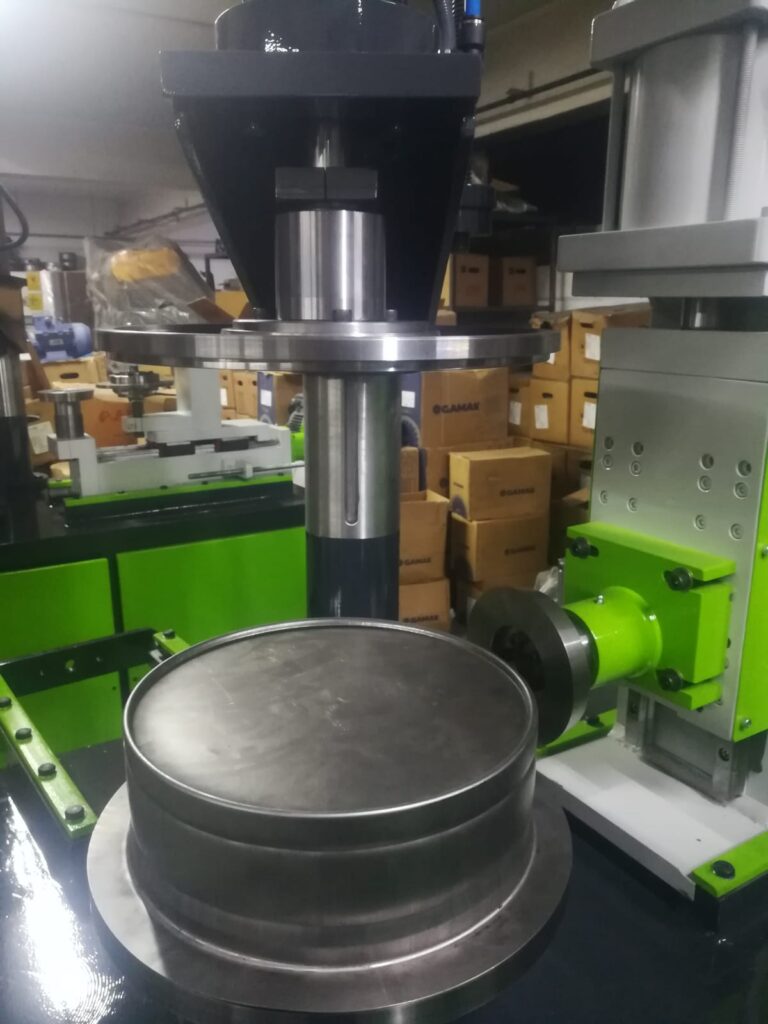
La máquina rebordeadora es un equipo industrial especializado que se utiliza para realizar el rebordeado de piezas metálicas, es decir, el conformado de los bordes de una lámina metálica para crear un reborde. Este proceso es crucial en la fabricación de componentes metálicos tubulares, cilíndricos o piezas que requieren bordes reforzados o lisos para un acabado estético o estructural. El rebordeado se utiliza ampliamente en industrias como la automotriz, aeroespacial, de electrodomésticos, y en la fabricación de envases.
1. ¿Qué es el rebordeado?
El rebordeado es una técnica de conformado de metales que implica doblar o rodar el borde de una lámina hacia el interior o exterior, creando un borde reforzado y suave. Este proceso sirve para mejorar tanto la resistencia estructural de la pieza como su estética. Además, ayuda a eliminar bordes afilados que podrían representar un peligro en las piezas finales.
2. Componentes principales de una máquina rebordeadora
Una máquina rebordeadora suele estar compuesta por los siguientes elementos clave:
- Rodillos de rebordeado:
- Son las herramientas principales que deforman el borde de la lámina metálica. Los rodillos aplican presión controlada para doblar el borde, formando el reborde según el diseño deseado. Generalmente, estos rodillos están fabricados con acero de alta resistencia o materiales endurecidos para soportar el desgaste constante.
- Sistema de sujeción:
- Mantiene la lámina metálica en su lugar mientras se aplica la presión de los rodillos. El sistema de sujeción garantiza que la lámina no se desplace o se deforme de manera incorrecta durante el proceso.
- Motor de accionamiento:
- Impulsa el movimiento de los rodillos de rebordeado. En las máquinas modernas, los motores pueden estar controlados electrónicamente, permitiendo ajustes precisos en la velocidad y presión para adaptarse a diferentes tipos de material.
- Panel de control:
- Permite a los operarios ajustar los parámetros del proceso, como la velocidad del rebordeado, la presión aplicada y el tipo de operación. En algunos modelos, los sistemas de control pueden incluir tecnología CNC para aumentar la precisión y la repetibilidad.
3. Tipos de máquinas rebordeadoras
Dependiendo de la aplicación y el tipo de rebordeado requerido, existen varios tipos de máquinas rebordeadoras:
- Máquinas manuales:
- Estas son más simples y son operadas manualmente por el usuario, girando los rodillos a través de una manivela o una palanca. Se utilizan para aplicaciones más pequeñas o cuando se requiere un control directo en el proceso.
- Máquinas automáticas:
- Estas máquinas utilizan motores eléctricos o neumáticos para automatizar el proceso de rebordeado. Permiten un rebordeado más rápido y consistente, siendo ideales para la producción en masa de piezas metálicas. Son comunes en industrias de gran volumen como la automotriz y de envases.
- Máquinas CNC rebordeadoras:
- Equipadas con sistemas de control numérico por computadora (CNC), estas máquinas permiten un control extremadamente preciso sobre el proceso de rebordeado. Pueden ajustarse automáticamente para realizar operaciones complejas y producir piezas con tolerancias muy estrictas.
4. Proceso de rebordeado: Paso a paso
El proceso de rebordeado sigue una secuencia de pasos estándar, dependiendo del tipo de máquina utilizada y la aplicación:
- Preparación de la pieza:
- La lámina metálica o pieza a trabajar se coloca en la máquina rebordeadora, asegurándose de que el borde que se desea rebordear esté correctamente alineado con los rodillos.
- Ajuste de los rodillos:
- Los rodillos de rebordeado se ajustan en función del grosor del material y del tipo de reborde que se desea formar. Dependiendo de la máquina, los rodillos pueden moverse automáticamente o requerir ajustes manuales.
- Inicio del proceso:
- Una vez que la pieza está correctamente colocada y los rodillos ajustados, el motor de la máquina activa el movimiento de los rodillos, que aplican presión al borde de la lámina, deformándola progresivamente para crear el reborde.
- Revisión y ajustes:
- A medida que se realiza el rebordeado, el operario puede monitorear el proceso para asegurarse de que el reborde se forme de manera uniforme y con el acabado deseado. En máquinas automáticas o CNC, los sistemas de control pueden ajustar automáticamente los parámetros para garantizar la consistencia.
5. Aplicaciones industriales de la máquina rebordeadora
El uso de máquinas rebordeadoras es esencial en varias industrias, debido a su capacidad para mejorar tanto la resistencia como la estética de las piezas metálicas. Algunas de las principales aplicaciones incluyen:
- Industria automotriz:
- Las piezas automotrices, como los paneles de carrocería y las puertas, requieren bordes lisos y resistentes para mejorar tanto la seguridad como la apariencia del vehículo. Las máquinas rebordeadoras se utilizan para crear bordes redondeados y reforzados en estas piezas.
- Fabricación de envases:
- Los envases metálicos, como latas de alimentos y bebidas, dependen del rebordeado para crear un borde resistente que garantice el sellado hermético. El rebordeado también mejora la seguridad al eliminar los bordes afilados.
- Aeronáutica:
- En la industria aeroespacial, se utiliza el rebordeado para reforzar componentes estructurales ligeros. Las piezas metálicas en aviones y helicópteros, como las cubiertas de los motores y las superficies de control, requieren bordes precisos que aumenten la resistencia sin agregar peso adicional.
- Fabricación de electrodomésticos:
- Las carcasas metálicas de electrodomésticos como lavadoras, secadoras y refrigeradores se rebordean para crear bordes lisos que eviten daños y mejoren la durabilidad del producto.
6. Ventajas del uso de máquinas rebordeadoras
El uso de máquinas rebordeadoras ofrece numerosas ventajas en términos de calidad del acabado y resistencia estructural de las piezas metálicas. Algunas de las principales ventajas incluyen:
- Aumento de la resistencia estructural:
- El rebordeado refuerza los bordes de las piezas, haciéndolas más resistentes a las tensiones y el desgaste. Esto es especialmente importante en piezas que estarán sometidas a fuerzas constantes o impactos.
- Mejora estética:
- El proceso de rebordeado crea bordes lisos y uniformes, mejorando la apariencia de las piezas y eliminando bordes afilados que podrían representar un riesgo.
- Versatilidad:
- Las máquinas rebordeadoras pueden trabajar con una amplia gama de materiales metálicos, desde aceros y aluminios hasta cobres y otros metales blandos. Esto las hace ideales para una variedad de industrias.
- Eficiencia en la producción en masa:
- Las máquinas automáticas y CNC rebordeadoras permiten realizar el proceso de rebordeado de manera rápida y consistente, lo que es ideal para la producción en masa. La automatización reduce los tiempos de ciclo y mejora la uniformidad de las piezas producidas.
7. Mantenimiento y optimización de máquinas rebordeadoras
El mantenimiento adecuado de una máquina rebordeadora es esencial para garantizar su funcionamiento eficiente a largo plazo. Algunas recomendaciones para mantener estas máquinas en óptimas condiciones incluyen:
- Lubricación regular:
- Los rodillos y sistemas de movimiento deben mantenerse bien lubricados para minimizar el desgaste y garantizar un movimiento suave durante el rebordeado.
- Revisión de rodillos:
- Los rodillos de rebordeado están en contacto constante con el metal, por lo que deben revisarse periódicamente en busca de desgaste o daños. Los rodillos desgastados pueden generar defectos en los bordes de las piezas.
- Ajuste adecuado:
- Asegurarse de que los rodillos estén alineados y ajustados correctamente para el material que se está trabajando es crucial para evitar defectos en el rebordeado.
- Limpieza de la máquina:
- Los restos de metal o lubricante acumulados en la máquina pueden interferir con el proceso de rebordeado. Se recomienda limpiar la máquina regularmente para mantener su rendimiento.
Máquinas automáticas: Aplicaciones y funcionamiento
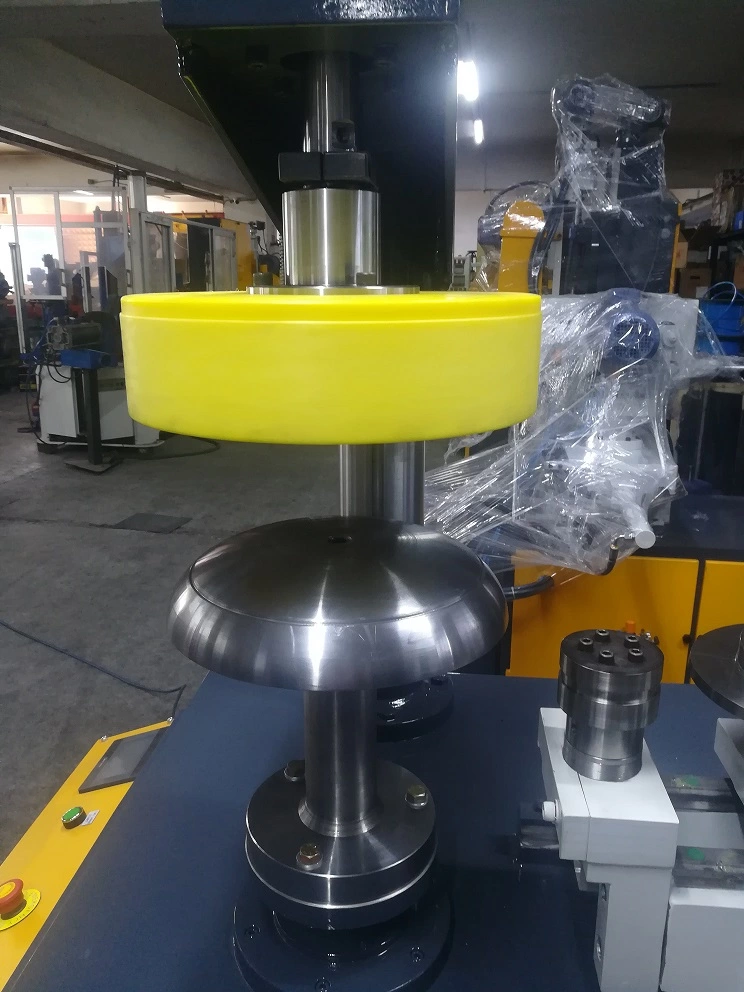
Las máquinas automáticas son equipos industriales diseñados para realizar tareas de manera autónoma o con mínima intervención humana, optimizando la producción y mejorando la precisión en diversas industrias. Estas máquinas juegan un papel crucial en la manufactura moderna, ya que permiten realizar procesos repetitivos y complejos con alta eficiencia, velocidad y consistencia. Las máquinas automáticas están presentes en una amplia gama de sectores industriales, como el automotriz, aeroespacial, fabricación de electrodomésticos, envasado y electrónica, entre otros.
1. ¿Qué es una máquina automática?
Una máquina automática es un dispositivo que está programado para realizar tareas específicas sin necesidad de intervención humana continua. Estas máquinas están equipadas con sistemas electrónicos o mecánicos avanzados que les permiten controlar, monitorear y ajustar su operación según las necesidades de la producción.
Las máquinas automáticas suelen estar conectadas a sistemas de control, como el Control Numérico por Computadora (CNC) o PLC (Controlador Lógico Programable), que permiten un control preciso y adaptable de los parámetros de producción, como la velocidad, presión, temperatura y movimiento. Dependiendo del tipo de máquina y su aplicación, pueden incluir componentes como motores eléctricos, sensores, actuadores, sistemas hidráulicos o neumáticos y interfaces de usuario avanzadas.
2. Componentes principales de una máquina automática
Una máquina automática puede variar en su diseño y características según la industria y la aplicación específica, pero generalmente incluye los siguientes componentes clave:
- Sistema de control:
- El sistema de control es el cerebro de la máquina automática, responsable de regular su funcionamiento. Los sistemas de control pueden incluir PLCs, CNC, o sistemas basados en microcontroladores. Estos dispositivos permiten la programación y el ajuste de los parámetros de operación, garantizando que la máquina funcione de manera eficiente y precisa.
- Sensores y actuadores:
- Los sensores monitorean el estado de la máquina y el proceso de producción, proporcionando datos en tiempo real al sistema de control. Los sensores pueden medir variables como la presión, temperatura, posición y velocidad.
- Los actuadores son los dispositivos que convierten la energía controlada por el sistema en movimiento físico o acción, como motores, cilindros hidráulicos o neumáticos que mueven piezas o realizan tareas específicas.
- Sistema de alimentación:
- En muchas máquinas automáticas, un sistema de alimentación automática suministra materia prima o componentes al proceso. Este sistema puede incluir cintas transportadoras, brazos robóticos, tolvas o alimentadores vibratorios, dependiendo del diseño de la máquina.
- Interfaz de usuario:
- La interfaz de usuario permite que los operarios configuren, controlen y monitoreen el proceso de producción. En las máquinas modernas, estas interfaces suelen ser pantallas táctiles que proporcionan información sobre el estado de la máquina y permiten ajustes en tiempo real.
- Motor de accionamiento:
- El motor impulsa el movimiento de las partes móviles de la máquina, ya sea directamente o a través de un sistema mecánico como engranajes, correas o cadenas. Dependiendo del tipo de operación, se pueden utilizar motores eléctricos, hidráulicos o neumáticos.
3. Tipos de máquinas automáticas
Existen diferentes tipos de máquinas automáticas, diseñadas para cumplir con tareas específicas en función de los requerimientos de producción. A continuación, se describen algunos de los tipos más comunes:
- Máquinas automáticas de ensamblaje:
- Estas máquinas están diseñadas para ensamblar componentes de manera automatizada. Se utilizan ampliamente en industrias como la automotriz y la electrónica, donde se necesita ensamblar grandes cantidades de piezas con alta precisión.
- Ejemplo: En la fabricación de automóviles, las máquinas automáticas de ensamblaje pueden unir paneles de carrocería, instalar sistemas eléctricos y ensamblar motores.
- Máquinas de corte y conformado:
- Estas máquinas realizan operaciones de corte, doblado o conformado de materiales, como metales, plásticos o madera. Las prensas automáticas, máquinas de corte por láser o cizallas automáticas son ejemplos de este tipo de máquina.
- Ejemplo: En la industria metalúrgica, las máquinas automáticas de corte por láser se utilizan para cortar láminas metálicas con alta precisión y a velocidades elevadas.
- Máquinas de envasado automático:
- Son esenciales en la industria del envasado de alimentos, bebidas, productos farmacéuticos y cosméticos. Estas máquinas realizan tareas como el llenado de envases, el sellado y el etiquetado.
- Ejemplo: En la industria de bebidas, las máquinas de envasado automático llenan, sellan y etiquetan botellas de manera continua y eficiente.
- Máquinas de inspección y control de calidad:
- Estas máquinas utilizan sensores, cámaras y sistemas avanzados para inspeccionar productos y garantizar que cumplan con los estándares de calidad. Pueden detectar defectos, medir dimensiones o verificar la integridad de las piezas.
- Ejemplo: En la producción de semiconductores, las máquinas automáticas de inspección verifican que los chips no tengan defectos microscópicos antes de su envío.
- Máquinas robóticas:
- Los robots industriales son un tipo de máquina automática que se utiliza para realizar tareas como soldadura, pintura, ensamblaje y manipulación de materiales. Están programados para realizar movimientos repetitivos con alta precisión.
- Ejemplo: En la industria automotriz, los robots realizan tareas de soldadura en las líneas de ensamblaje de vehículos, garantizando la precisión y consistencia en cada punto de soldadura.
4. Ventajas de las máquinas automáticas
El uso de máquinas automáticas en la industria ofrece numerosas ventajas que mejoran tanto la eficiencia de producción como la calidad del producto. Algunas de las principales ventajas incluyen:
- Aumento de la productividad:
- Las máquinas automáticas pueden trabajar durante largos períodos sin descanso, lo que aumenta significativamente la velocidad de producción. Pueden realizar tareas repetitivas de manera constante, lo que reduce los tiempos de ciclo y mejora la eficiencia general del proceso.
- Precisión y repetibilidad:
- Las máquinas automáticas están diseñadas para operar con alta precisión, lo que asegura que las piezas o productos sean consistentes y cumplan con los estándares de calidad. Esto es especialmente importante en industrias donde las tolerancias son críticas, como la automotriz, aeroespacial y electrónica.
- Reducción de errores humanos:
- Al automatizar procesos complejos y repetitivos, las máquinas automáticas reducen la dependencia de la intervención humana, lo que minimiza el riesgo de errores. Esto también mejora la seguridad en el lugar de trabajo, al eliminar tareas peligrosas o físicamente exigentes para los trabajadores.
- Flexibilidad:
- Muchas máquinas automáticas modernas pueden reprogramarse rápidamente para adaptarse a nuevos diseños o productos, lo que aumenta la flexibilidad de la producción. Esto es particularmente útil en industrias que deben responder rápidamente a cambios en la demanda o personalizar productos para diferentes mercados.
- Mejora de la calidad:
- Las máquinas automáticas pueden incluir sistemas de control de calidad en tiempo real, que permiten detectar y corregir defectos de manera inmediata. Esto asegura que los productos finales cumplan con los más altos estándares de calidad.
5. Aplicaciones industriales de las máquinas automáticas
Las máquinas automáticas son ampliamente utilizadas en diversas industrias debido a su capacidad para mejorar la eficiencia y calidad. A continuación, se describen algunas de las aplicaciones industriales más comunes:
- Industria automotriz:
- Las máquinas automáticas realizan una amplia gama de tareas en la fabricación de automóviles, desde la estampación de paneles de carrocería hasta el ensamblaje de motores. Los robots automatizados se encargan de la soldadura, el ensamblaje y la pintura en las líneas de producción.
- Industria aeroespacial:
- En la industria aeroespacial, las máquinas automáticas son esenciales para la fabricación de componentes de alta precisión, como fuselajes y sistemas de propulsión. Estas máquinas garantizan que los componentes cumplan con estrictas normas de calidad y seguridad.
- Industria de alimentos y bebidas:
- Las máquinas automáticas son fundamentales en la producción y envasado de alimentos y bebidas. Se utilizan para llenar botellas, sellar envases, etiquetar productos y garantizar que los productos se manipulen higiénicamente.
- Fabricación de productos electrónicos:
- En la industria de la electrónica, las máquinas automáticas ensamblan circuitos impresos, montan componentes y realizan pruebas de calidad en productos como teléfonos móviles, computadoras y dispositivos de consumo.
- Industria farmacéutica:
- Las máquinas automáticas se utilizan para el envasado de medicamentos, llenado de cápsulas, etiquetado de productos farmacéuticos y la inspección de calidad. Estos sistemas garantizan la exactitud y consistencia en la producción de medicamentos.
6. Mantenimiento y optimización de máquinas automáticas
Para garantizar el funcionamiento continuo y eficiente de una máquina automática, es esencial realizar un mantenimiento preventivo regular y aplicar estrategias de optimización.
Prácticas de mantenimiento:
- Inspección periódica de sensores, actuadores y motores para detectar fallos o desgastes.
- Lubricación de las partes móviles para reducir el desgaste y mejorar la eficiencia operativa.
- Actualización de software y sistemas de control para mejorar el rendimiento de la máquina.
- Monitoreo de datos de producción en tiempo real para identificar posibles problemas antes de que se conviertan en fallos.
Optimización del rendimiento:
- Ajustar los parámetros de producción según las especificaciones del material y el producto.
- Implementar sistemas de mantenimiento predictivo utilizando sensores avanzados para prevenir tiempos de inactividad inesperados.
- Reprogramar las máquinas para nuevas tareas o productos de manera eficiente, aprovechando su flexibilidad.
Máquinas CNC Rebordeadoras: Funcionamiento y Aplicaciones
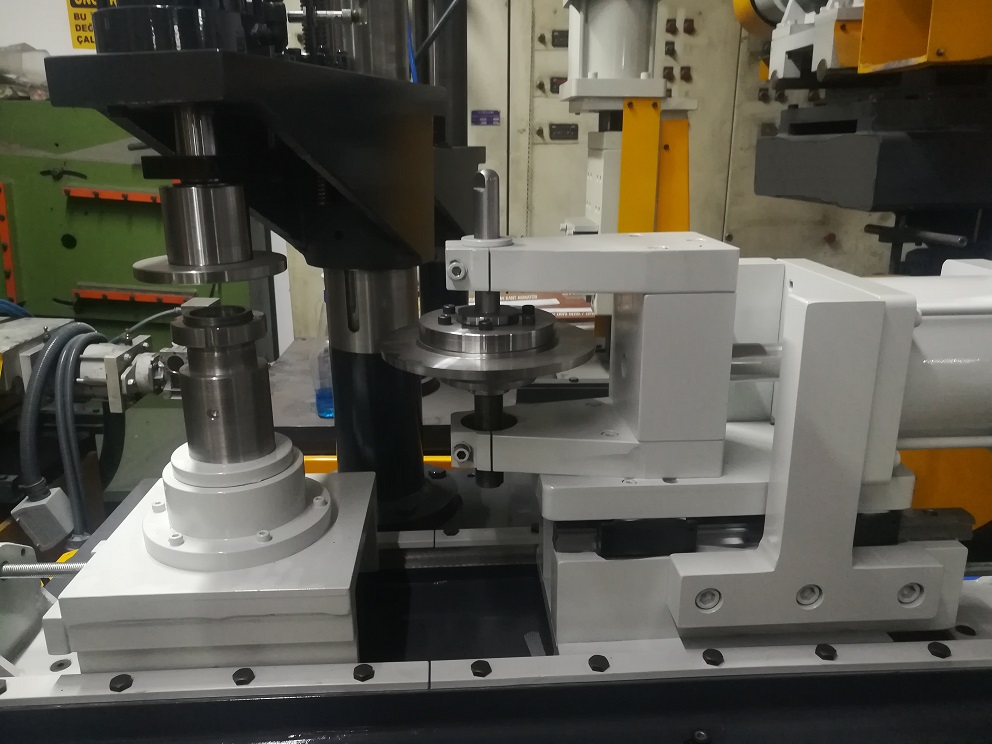
Las máquinas CNC rebordeadoras son herramientas industriales avanzadas que combinan las capacidades de una máquina rebordeadora convencional con la precisión y control del CNC (Control Numérico por Computadora). Estas máquinas se utilizan principalmente para realizar el rebordeado de piezas metálicas, creando bordes curvados, redondeados o reforzados en láminas o tubos de metal, con un alto grado de exactitud y consistencia. Al incorporar la tecnología CNC, las rebordeadoras automáticas pueden realizar procesos complejos con una precisión repetitiva, lo que es esencial en la producción de piezas de alta calidad en industrias como la automotriz, aeroespacial y de envases.
1. ¿Qué es una máquina CNC rebordeadora?
Una máquina CNC rebordeadora es un equipo especializado que realiza el proceso de rebordeado controlado por computadora. Esto significa que las operaciones de rebordeado (que incluyen el doblado o conformado de los bordes metálicos) se programan y controlan con gran precisión mediante software CNC, lo que permite realizar tareas de forma automática, con altas tolerancias y sin la necesidad de ajustes manuales frecuentes.
El rebordeado es esencial para reforzar los bordes de piezas metálicas, mejorar su resistencia estructural, y proporcionar acabados estéticos. En una máquina CNC rebordeadora, el proceso de conformado de los bordes se realiza de manera automatizada, con parámetros ajustados de manera precisa, lo que permite producir piezas uniformes y de alta calidad en grandes volúmenes.
2. Componentes principales de una máquina CNC rebordeadora
Las máquinas CNC rebordeadoras constan de varios componentes esenciales que les permiten realizar el proceso de rebordeado con alta precisión. A continuación, se describen los elementos clave:
- Sistema CNC:
- El sistema CNC es el cerebro de la máquina, permitiendo programar y controlar las operaciones de rebordeado con precisión. Este sistema utiliza software especializado para interpretar los comandos de diseño y ejecutar las instrucciones sobre la pieza a trabajar.
- El operador introduce el diseño, los parámetros de operación (como la velocidad y presión) y la secuencia de movimientos, y el sistema CNC se encarga de ejecutar el proceso con una precisión repetitiva.
- Rodillos de rebordeado:
- Los rodillos son las herramientas principales que se utilizan para doblar o conformar los bordes de la pieza metálica. Los rodillos aplican presión a lo largo del borde de la lámina o tubo metálico para crear el reborde deseado.
- En una máquina CNC rebordeadora, los rodillos son ajustables automáticamente para diferentes diámetros, grosores y formas de rebordes, lo que proporciona gran versatilidad.
- Servomotores:
- Las máquinas CNC rebordeadoras están equipadas con servomotores que controlan el movimiento de los rodillos de rebordeado. Estos motores permiten un control preciso sobre la velocidad y posición de los rodillos, lo que es esencial para obtener un acabado uniforme y sin defectos en el borde de la pieza.
- Los servomotores son controlados por el sistema CNC, que ajusta su operación en tiempo real para adaptarse a las variaciones en el material o las especificaciones del diseño.
- Contrapunzón o sistema de sujeción:
- El sistema de sujeción asegura la lámina o tubo en su lugar durante el proceso de rebordeado, evitando desplazamientos o movimientos que podrían afectar la calidad del reborde. Este sistema es ajustable y controlado electrónicamente en las máquinas CNC rebordeadoras, lo que garantiza un posicionamiento preciso y consistente de la pieza.
- Panel de control y pantalla:
- Las máquinas CNC rebordeadoras cuentan con un panel de control con una pantalla táctil o una interfaz de usuario, donde los operarios pueden introducir los parámetros del proceso y supervisar la operación en tiempo real. Este panel permite ajustar rápidamente la configuración de la máquina para diferentes piezas y aplicaciones, garantizando flexibilidad y control en la producción.
3. Funcionamiento de una máquina CNC rebordeadora
El funcionamiento de una máquina CNC rebordeadora sigue un flujo de trabajo bien definido que se lleva a cabo de manera automática. A continuación, se describe el proceso típico de operación:
- Programación del diseño:
- El operario introduce los parámetros del diseño en el software CNC. Esto incluye las dimensiones de la pieza, el tipo de reborde que se va a formar, la presión necesaria y la secuencia de movimientos de los rodillos.
- Preparación de la pieza:
- La lámina o tubo metálico se coloca en la máquina, asegurándose de que esté firmemente sujetada. En el caso de piezas complejas, la máquina puede ajustar automáticamente la posición de la pieza antes de comenzar el proceso de rebordeado.
- Ajuste de los rodillos y servomotores:
- El sistema CNC ajusta la posición y configuración de los rodillos de rebordeado de acuerdo con las instrucciones programadas. Los servomotores garantizan que los rodillos se muevan con la velocidad y presión precisas durante el proceso.
- Inicio del rebordeado:
- Una vez que la máquina está preparada, los rodillos comienzan a aplicar presión sobre el borde de la pieza, doblando o curvando el metal para crear el reborde. La máquina puede ejecutar múltiples pasadas según sea necesario para lograr el rebordeado final.
- Monitoreo y ajustes automáticos:
- A medida que avanza el proceso, el sistema CNC monitorea continuamente el progreso y realiza ajustes automáticos si es necesario, para corregir posibles desviaciones o variaciones en el material.
- Finalización y extracción de la pieza:
- Al finalizar el rebordeado, la pieza es liberada automáticamente y está lista para inspección o procesamiento adicional. La máquina puede continuar con el siguiente ciclo de manera automática si está en modo de producción en masa.
4. Tipos de rebordes que pueden realizarse con una máquina CNC rebordeadora
Las máquinas CNC rebordeadoras ofrecen una gran flexibilidad en el tipo de rebordes que pueden realizar. Algunos de los tipos de rebordes más comunes que se pueden fabricar incluyen:
- Reborde simple:
- Consiste en doblar el borde de la lámina hacia el exterior o interior. Este tipo de reborde es ideal para piezas que requieren un acabado simple y suave en los bordes.
- Reborde acampanado:
- El borde de la pieza se dobla formando una ligera inclinación o forma cónica, lo que facilita el ensamblaje de piezas o la unión de tubos.
- Reborde enrollado:
- En este tipo de reborde, el borde de la lámina se enrolla sobre sí mismo, creando un borde redondeado y sin costuras. Es ideal para piezas que requieren mayor seguridad y resistencia al desgaste, como envases metálicos.
- Reborde de refuerzo:
- Se utiliza para aumentar la resistencia estructural de la pieza. El borde se refuerza mediante un proceso de doblado más profundo, lo que incrementa la rigidez y resistencia de la pieza.
- Reborde decorativo:
- Las máquinas CNC rebordeadoras también pueden realizar rebordes con detalles decorativos, ideales para piezas donde la estética es un factor importante, como en la fabricación de electrodomésticos y productos de consumo.
5. Aplicaciones industriales de las máquinas CNC rebordeadoras
Las máquinas CNC rebordeadoras son ampliamente utilizadas en una variedad de sectores industriales donde la precisión y la consistencia son esenciales para la producción de piezas metálicas. Algunas de las principales aplicaciones incluyen:
- Industria automotriz:
- En la fabricación de carrocerías de automóviles, las máquinas CNC rebordeadoras se utilizan para crear bordes redondeados y reforzados en puertas, capós y otros componentes estructurales.
- Aeronáutica:
- En la industria aeroespacial, estas máquinas son esenciales para producir bordes precisos en componentes como paneles de fuselaje, que deben ser ligeros pero lo suficientemente resistentes para soportar las tensiones del vuelo.
- Fabricación de envases metálicos:
- Las latas de bebidas y otros envases metálicos dependen del rebordeado para crear bordes seguros y resistentes que no representen un peligro para los consumidores. El CNC permite ajustar rápidamente los parámetros para fabricar diferentes tamaños y formas de envases.
- Electrodomésticos:
- Las carcasas y componentes metálicos de lavadoras, secadoras y refrigeradores utilizan el rebordeado para mejorar tanto la estética como la durabilidad de las piezas.
6. Ventajas de las máquinas CNC rebordeadoras
Las máquinas CNC rebordeadoras ofrecen varias ventajas significativas sobre las máquinas rebordeadoras manuales o automáticas sin CNC:
- Alta precisión y repetibilidad:
- El sistema CNC garantiza que cada pieza sea rebordeada con las mismas especificaciones exactas, lo que reduce los defectos y mejora la calidad.
- Flexibilidad de producción:
- Las máquinas CNC permiten realizar cambios rápidos en los parámetros de operación, lo que facilita la producción de diferentes diseños y tamaños de piezas sin necesidad de ajustes manuales.
- Mayor eficiencia:
- Las máquinas CNC rebordeadoras pueden realizar procesos de rebordeado de manera continua y automática, reduciendo los tiempos de ciclo y aumentando la producción en masa.
- Reducción de errores humanos:
- Al eliminar la necesidad de ajustes manuales, las máquinas CNC reducen la posibilidad de errores, lo que se traduce en menos piezas defectuosas y una mayor uniformidad en la producción.
Bordonadora biseladora de lámina: Aplicaciones y funcionamiento
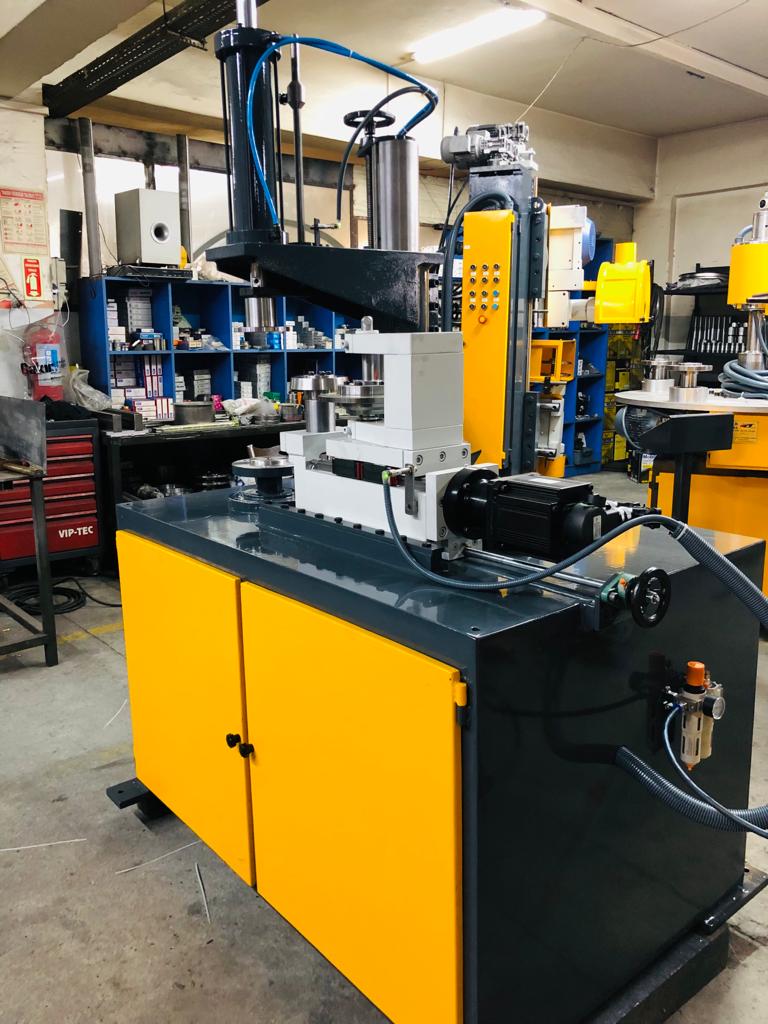
La bordonadora biseladora de lámina es una máquina especializada utilizada en el trabajo con láminas metálicas, diseñada para crear bordes curvados (bordonados) y bordes biselados. Este tipo de equipo es fundamental en la fabricación de componentes que requieren bordes reforzados o acabados inclinados, mejorando tanto la resistencia como el ajuste de las piezas en aplicaciones como la construcción, automoción, aeronáutica y la fabricación de envases metálicos. Las máquinas bordonadoras biseladoras combinan estas dos funcionalidades, ofreciendo una solución eficiente y versátil para múltiples procesos de conformado de láminas metálicas.
1. ¿Qué es una bordonadora biseladora de lámina?
Una bordonadora biseladora es una máquina industrial que combina dos procesos en una sola operación: el bordonado y el biselado de los bordes de láminas metálicas. El bordonado consiste en doblar o redondear los bordes para crear un borde curvado, mientras que el biselado implica cortar o inclinar el borde en un ángulo determinado.
- Bordonado: Se refiere a la creación de un borde curvado o enrollado en el borde de una lámina de metal. Esto mejora la resistencia estructural y la seguridad, eliminando bordes afilados que podrían representar un peligro o un defecto en el producto final.
- Biselado: Es el proceso de crear un borde inclinado o cortado en un ángulo específico. Los bordes biselados son necesarios en muchas aplicaciones industriales para mejorar el ensamblaje, facilitar la soldadura o mejorar la estética y el ajuste de las piezas.
2. Componentes principales de una bordonadora biseladora de lámina
Una bordonadora biseladora de lámina cuenta con varios componentes que permiten la realización de ambos procesos en una sola máquina. A continuación, se describen los componentes más importantes:
- Rodillos de bordonado:
- Los rodillos son las herramientas que aplican la presión necesaria para doblar el borde de la lámina, creando un borde redondeado o bordón. Estos rodillos están hechos de acero endurecido o materiales resistentes al desgaste, y pueden ajustarse para crear diferentes radios de curvatura dependiendo de las especificaciones del producto.
- Cuchillas de biselado:
- Las cuchillas de biselado están diseñadas para cortar el borde de la lámina en un ángulo determinado, creando el bisel. Estas cuchillas son ajustables para lograr diferentes ángulos de bisel, según las necesidades de la pieza.
- Sistema de sujeción:
- El sistema de sujeción asegura la lámina durante los procesos de bordonado y biselado, evitando que se mueva o se deforme de manera no deseada. Este sistema asegura que el borde se conforme correctamente según las especificaciones del proceso.
- Motor de accionamiento:
- El motor impulsa el movimiento de los rodillos y cuchillas, permitiendo que la máquina funcione de manera automática o semiautomática. Los motores modernos permiten ajustar la velocidad de operación y la presión aplicada, lo que garantiza que la máquina pueda adaptarse a diferentes tipos y grosores de lámina metálica.
- Panel de control:
- El panel de control permite a los operadores ajustar los parámetros de la máquina, como la velocidad de bordonado o el ángulo del bisel. En las máquinas modernas, este panel puede estar equipado con control CNC para ajustar automáticamente la posición de los rodillos y las cuchillas.
3. ¿Cómo funciona una bordonadora biseladora de lámina?
El proceso de bordonado y biselado se lleva a cabo en varias etapas dentro de la máquina. Dependiendo del diseño de la máquina, ambos procesos pueden realizarse de manera secuencial o simultánea. A continuación, se describe el funcionamiento típico de una bordonadora biseladora:
- Preparación de la lámina:
- La lámina metálica se coloca en la máquina, asegurándose de que los bordes estén alineados con los rodillos de bordonado y las cuchillas de biselado. El operario ajusta la máquina según el grosor y el tipo de material que se va a trabajar.
- Ajuste de la presión y el ángulo:
- Los rodillos de bordonado y las cuchillas de biselado se ajustan según el tipo de borde que se desea crear. El operario ajusta la presión que deben ejercer los rodillos y el ángulo de las cuchillas de biselado para obtener el acabado deseado.
- Inicio del proceso:
- Una vez que los ajustes están completos, la máquina comienza el proceso. Los rodillos de bordonado doblan el borde de la lámina para crear un borde curvado o enrollado, mientras que las cuchillas de biselado cortan el borde en el ángulo especificado.
- Revisión del borde:
- El borde de la lámina se inspecciona para asegurarse de que cumple con las especificaciones. Si es necesario, se pueden hacer ajustes adicionales en la máquina para perfeccionar el bordonado o biselado.
4. Aplicaciones industriales de la bordonadora biseladora de lámina
Las máquinas bordonadoras biseladoras son fundamentales en diversas industrias que requieren bordes reforzados o biselados para mejorar la integridad estructural y la funcionalidad de las piezas. A continuación, se presentan algunas aplicaciones clave:
- Industria automotriz:
- Los bordes de paneles de carrocería y componentes metálicos en vehículos se someten a bordonado para mejorar la resistencia estructural y eliminar bordes afilados. Además, el biselado facilita el ensamblaje de piezas y componentes, mejorando el ajuste y la eficiencia del ensamblaje.
- Fabricación de recipientes metálicos:
- Los recipientes de metal, como latas de alimentos o envases industriales, requieren bordes redondeados para evitar daños y garantizar la seguridad del usuario. Además, en algunas aplicaciones, el biselado es necesario para mejorar el sellado o facilitar el ensamblaje de las tapas y fondos de los recipientes.
- Industria aeronáutica:
- En la industria aeroespacial, el biselado es esencial para piezas metálicas que necesitan ensamblarse o soldarse con precisión. El bordonado, por otro lado, refuerza las piezas ligeras utilizadas en el fuselaje de aviones o componentes estructurales, proporcionando mayor resistencia sin agregar peso excesivo.
- Fabricación de electrodomésticos:
- Las carcasas metálicas de electrodomésticos, como refrigeradores, lavadoras y secadoras, utilizan el bordonado para mejorar tanto la estética como la resistencia. El biselado de las piezas facilita el ensamblaje de los diferentes componentes y mejora la alineación de las piezas durante la producción.
5. Ventajas del uso de una bordonadora biseladora de lámina
El uso de una bordonadora biseladora de lámina ofrece varias ventajas significativas, tanto en términos de calidad del producto como de eficiencia en la producción. Algunas de las principales ventajas incluyen:
- Alta precisión en los bordes:
- Al combinar las funciones de bordonado y biselado en una sola máquina, se logra una mayor precisión en el procesamiento de los bordes, lo que asegura que las piezas metálicas tengan bordes perfectamente formados y uniformes.
- Versatilidad:
- Las máquinas bordonadoras biseladoras son versátiles y pueden trabajar con una amplia variedad de metales y aleaciones, como acero, aluminio, cobre y otros. Esto las hace adecuadas para múltiples aplicaciones industriales.
- Mayor resistencia estructural:
- El bordonado refuerza los bordes de las piezas metálicas, aumentando su resistencia a la fatiga, el desgaste y los impactos. Esto es crucial en aplicaciones donde los bordes de las piezas están sometidos a grandes tensiones o son puntos críticos en la estructura.
- Mejora en el ensamblaje:
- Los bordes biselados facilitan el ensamblaje de las piezas, lo que reduce los tiempos de producción y mejora la calidad de las uniones, ya sea por soldadura o por otros métodos de ensamblaje.
- Acabados estéticos de alta calidad:
- Las bordonadoras biseladoras permiten obtener bordes suaves y estéticamente agradables, lo que es ideal para aplicaciones donde el acabado superficial es importante, como en electrodomésticos o productos de consumo.
6. Mantenimiento y optimización de las bordonadoras biseladoras
El mantenimiento adecuado de una bordonadora biseladora de lámina es crucial para garantizar su funcionamiento eficiente y prolongar su vida útil. Algunas recomendaciones clave incluyen:
- Lubricación de rodillos y cuchillas:
- Para reducir el desgaste y mantener un movimiento suave, los rodillos y cuchillas deben mantenerse bien lubricados.
- Revisión de cuchillas y rodillos:
- Los rodillos de bordonado y las cuchillas de biselado están sometidos a un desgaste constante. Se deben inspeccionar regularmente para detectar cualquier signo de deterioro o deformación y reemplazarse según sea necesario.
- Limpieza regular:
- Los residuos metálicos o lubricantes pueden acumularse en la máquina durante el proceso. Limpiar regularmente las áreas de trabajo y los componentes clave asegura un funcionamiento continuo y preciso.
La bordonadora biseladora de lámina es una herramienta indispensable para muchas industrias que requieren bordes reforzados y acabados precisos en láminas metálicas. Con su capacidad para realizar ambos procesos en una sola operación, estas máquinas ofrecen un alto nivel de eficiencia, versatilidad y precisión, haciendo posible la producción de piezas metálicas de alta calidad con bordes seguros, funcionales y estéticamente agradables.
¿Qué es una bordonadora biseladora de lámina?
Una bordonadora biseladora de lámina es una máquina industrial especializada que realiza dos procesos en los bordes de láminas metálicas: el bordonado y el biselado. Estos procesos permiten modificar los bordes de la lámina para reforzarlos, mejorar su resistencia estructural o facilitar su ensamblaje en otras piezas.
- Bordonado: Consiste en curvar o enrollar el borde de una lámina metálica, creando un borde redondeado o reforzado. Esto es útil para eliminar bordes afilados, mejorar la seguridad, aumentar la resistencia y darle un mejor acabado estético a la pieza.
- Biselado: Es el proceso de cortar o inclinar el borde de la lámina en un ángulo determinado, lo que facilita el ensamblaje de piezas o mejora la preparación para soldaduras.
Estas máquinas son comúnmente utilizadas en industrias como la automotriz, aeroespacial, fabricación de electrodomésticos, y envases metálicos. La combinación de estos dos procesos en una sola máquina permite realizar operaciones más eficientes, produciendo piezas con bordes reforzados y acabados precisos.
Los componentes principales de una bordonadora biseladora de lámina son los que permiten ejecutar los procesos de bordonado (curvado de los bordes) y biselado (corte en ángulo) de las láminas metálicas con precisión y eficiencia. A continuación se describen los componentes más importantes:
- Rodillos de bordonado:
- Son los elementos clave encargados de realizar el bordonado. Estos rodillos aplican presión sobre el borde de la lámina para curvarlo o enrollarlo, creando un borde redondeado. Están fabricados con materiales resistentes al desgaste, como acero endurecido, y pueden ajustarse para diferentes radios de curvatura dependiendo del tipo de bordón requerido.
- Cuchillas de biselado:
- Las cuchillas se encargan del proceso de biselado, que consiste en cortar o inclinar el borde de la lámina en un ángulo específico. Estas cuchillas son ajustables para crear biseles con distintos ángulos, según las necesidades del diseño de la pieza.
- Sistema de sujeción:
- Mantiene la lámina metálica firmemente en su lugar durante los procesos de bordonado y biselado. Esto es crucial para garantizar que los bordes se formen correctamente, sin desplazamientos ni deformaciones no deseadas.
- Motor de accionamiento:
- El motor impulsa el movimiento tanto de los rodillos de bordonado como de las cuchillas de biselado. Dependiendo de la máquina, este motor puede ser eléctrico, neumático o hidráulico, y permite controlar la velocidad y la presión aplicada durante el proceso.
- Panel de control:
- Es la interfaz que permite al operador ajustar los parámetros de la máquina, como la presión de los rodillos, el ángulo de biselado y la velocidad del proceso. En las máquinas más avanzadas, este panel puede estar conectado a un sistema CNC (Control Numérico por Computadora), que permite una mayor automatización y precisión.
- Sistemas de guía y ajuste:
- Estos sistemas aseguran que tanto los rodillos de bordonado como las cuchillas de biselado estén correctamente alineados con la lámina, permitiendo realizar ajustes según el grosor del material y la forma requerida.
- Estructura y bastidor:
- La estructura o bastidor de la máquina proporciona el soporte necesario para todos los componentes. Debe ser robusto y estable para soportar las fuerzas aplicadas durante el proceso sin sufrir deformaciones.
- Sistema de lubricación:
- Algunas máquinas cuentan con sistemas de lubricación automática para reducir la fricción entre los rodillos, cuchillas y la lámina metálica, lo que prolonga la vida útil de las herramientas y mejora el acabado del producto final.
Funcionamiento de una Bordonadora Biseladora de Lámina: Proceso Detallado
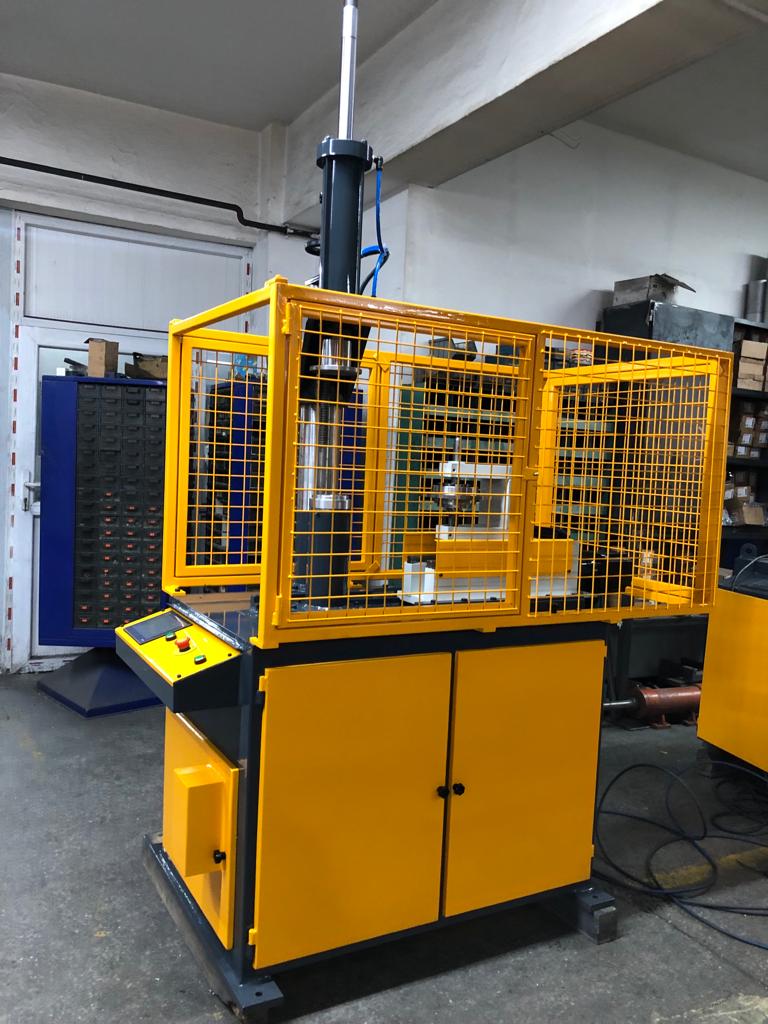
Una bordonadora biseladora de lámina es una máquina especializada en el procesamiento de bordes de láminas metálicas, diseñada para llevar a cabo dos funciones principales: bordonado y biselado. Estas máquinas son vitales en diversas industrias como la automotriz, aeroespacial, fabricación de envases, electrodomésticos, y otras donde es necesario reforzar los bordes de las láminas metálicas o darles un acabado inclinado para mejorar el ensamblaje o la estética. A lo largo de esta descripción, exploraremos el funcionamiento detallado de estas máquinas, sus procesos clave y cómo cada componente trabaja de forma integrada para lograr un acabado preciso y consistente.
2. Funcionamiento de la bordonadora biseladora de lámina: Paso a paso
El funcionamiento de una bordonadora biseladora implica varios pasos clave que deben llevarse a cabo de manera secuencial para lograr los resultados deseados en las láminas metálicas. A continuación, se describen en detalle estos pasos:
2.1. Preparación de la máquina
Antes de comenzar el proceso, es importante que la máquina esté configurada adecuadamente para la tarea específica que se va a realizar. Esto incluye la preparación de los rodillos de bordonado y las cuchillas de biselado según las especificaciones del producto.
- Selección del material: El primer paso es asegurarse de que la lámina metálica a procesar está lista. El tipo de material (acero, aluminio, cobre, etc.) y su grosor influyen en los ajustes que se deben realizar en la máquina.
- Ajuste de rodillos: Los rodillos de bordonado se ajustan según el grosor de la lámina y el radio de curvatura deseado. Algunas máquinas modernas cuentan con ajustes automáticos, mientras que otras requieren ajustes manuales.
- Configuración de las cuchillas de biselado: Las cuchillas se ajustan al ángulo de bisel necesario, que puede variar según la aplicación. Es importante asegurarse de que las cuchillas estén alineadas correctamente con la lámina para obtener un corte uniforme.
2.2. Colocación de la lámina metálica
Una vez que la máquina está configurada, se procede a colocar la lámina metálica en la zona de sujeción de la máquina. La sujeción es fundamental para asegurar que la lámina permanezca estable durante el proceso, evitando desplazamientos no deseados que podrían afectar la calidad del bordonado o biselado.
- Sujeción de la lámina: La lámina se asegura mediante un sistema de sujeción, que puede ser manual o automático. Este sistema fija la lámina en su lugar y la mantiene alineada con los rodillos y las cuchillas.
- Alineación precisa: Es importante que la lámina esté correctamente alineada con las herramientas de la máquina. Esto garantiza que los bordes se procesen de manera uniforme, evitando fallos o inconsistencias en los acabados.
2.3. Inicio del proceso de bordonado
Con la lámina firmemente colocada y la máquina configurada, el primer proceso a realizar es el bordonado. Los rodillos aplican presión al borde de la lámina, curvando o enrollando el material para formar un borde redondeado o reforzado.
- Activación del motor: El motor de accionamiento de la máquina impulsa los rodillos de bordonado. Dependiendo del diseño de la máquina, estos pueden estar controlados por servomotores o sistemas hidráulicos, lo que permite ajustar la presión y la velocidad de los rodillos.
- Curvado progresivo: Los rodillos comienzan a aplicar presión sobre el borde de la lámina, doblándola gradualmente hasta alcanzar el radio de curvatura deseado. La máquina puede realizar múltiples pasadas para garantizar que el borde se forme de manera uniforme y sin deformaciones.
- Monitoreo del proceso: Durante el bordonado, algunos modelos de máquinas bordonadoras cuentan con sensores que monitorizan la presión y el grosor del material en tiempo real, realizando ajustes automáticos si es necesario. Esto asegura que la curvatura sea consistente a lo largo de toda la longitud del borde.
2.4. Realización del biselado
Una vez completado el proceso de bordonado (si es necesario en la operación), se procede al biselado. Las cuchillas de biselado están diseñadas para cortar el borde de la lámina en un ángulo preciso, generando un borde inclinado.
- Ajuste de cuchillas: Las cuchillas de biselado deben estar configuradas según el ángulo de bisel especificado en el diseño de la pieza. Este ángulo puede variar, y en algunas aplicaciones industriales, se requieren biseles muy específicos para optimizar el ensamblaje o soldadura de las piezas.
- Corte preciso: Las cuchillas cortan el borde de la lámina en un ángulo definido. La precisión de este corte es crucial para garantizar que el borde se alinee correctamente en los procesos posteriores, como la soldadura o el ensamblaje.
- Control de la velocidad: La velocidad del proceso de biselado puede ajustarse en función del tipo de material y el espesor de la lámina. Los materiales más duros, como el acero, pueden requerir una velocidad más lenta y una mayor presión para realizar un biselado limpio.
2.5. Extracción y revisión de la pieza
Una vez completados ambos procesos (bordonado y biselado), la lámina procesada es liberada y extraída de la máquina para una inspección visual o mecánica.
- Liberación automática: En las máquinas bordonadoras biseladoras automáticas, el sistema de sujeción se libera automáticamente al finalizar el proceso, permitiendo que la lámina sea extraída de manera segura.
- Revisión de calidad: Después de la extracción, el operario o el sistema automatizado inspecciona la calidad de los bordes para asegurarse de que cumplen con las especificaciones del diseño. Se verifica que el bordonado sea uniforme y que el biselado haya sido realizado con el ángulo adecuado y sin defectos en el corte.
- Corrección de errores: Si se detecta alguna imperfección en el acabado del borde, se pueden hacer ajustes en los rodillos o cuchillas y repetir el proceso para corregir los errores.
3. Funciones avanzadas y automatización en bordonadoras biseladoras modernas
Con la evolución de la tecnología, las bordonadoras biseladoras han avanzado hacia un mayor nivel de automatización y control. Las máquinas modernas suelen estar equipadas con sistemas CNC (Control Numérico por Computadora) o PLC (Controlador Lógico Programable), lo que permite realizar operaciones con mayor precisión y control, y reducir al mínimo la intervención humana.
3.1. Control CNC en bordonadoras biseladoras
El uso de sistemas CNC en bordonadoras biseladoras permite un control más exacto sobre todos los aspectos del proceso. Los operarios pueden programar las secuencias de bordonado y biselado, definir ángulos específicos y ajustar parámetros como la velocidad y la presión, todo desde una interfaz de usuario.
- Programación avanzada: El operador puede introducir directamente las especificaciones del diseño a través de la interfaz CNC, lo que incluye los ángulos de biselado y el radio de curvatura del bordonado. Esto elimina la necesidad de ajustes manuales frecuentes.
- Ajustes automáticos: Los rodillos y las cuchillas pueden ajustarse automáticamente para diferentes grosores y tipos de material. La máquina CNC optimiza los parámetros en función de las propiedades del material, lo que garantiza un resultado óptimo sin necesidad de intervención humana.
- Producción en masa eficiente: Las máquinas CNC bordonadoras biseladoras son ideales para la producción en masa, ya que pueden ejecutar secuencias repetitivas con una precisión consistente. Esto es esencial en industrias como la automotriz y la aeronáutica, donde se deben fabricar grandes volúmenes de piezas con bordes precisos.
3.2. Sensores y monitoreo en tiempo real
Las máquinas modernas también están equipadas con sensores avanzados que permiten realizar un seguimiento en tiempo real de variables como la presión, la velocidad y el grosor del material. Esto mejora significativamente la calidad del proceso y reduce la posibilidad de errores.
- Sensores de presión: Controlan la cantidad de presión aplicada por los rodillos y las cuchillas, garantizando que no se ejerza una presión excesiva que pueda dañar el material.
- Monitoreo del grosor del material: Los sensores de grosor permiten ajustar los rodillos de bordonado y las cuchillas de biselado para adaptarse a pequeñas variaciones en el grosor de la lámina, asegurando que el proceso se realice de manera uniforme.
- Ajustes automáticos durante el proceso: Si los sensores detectan una variación en el material o un posible fallo en la operación, el sistema puede ajustar automáticamente los parámetros para corregir el error sin detener el proceso.
3.3. Automatización y brazos robóticos
En algunas líneas de producción, las máquinas bordonadoras biseladoras pueden estar integradas con brazos robóticos o sistemas de manipulación automatizada para cargar y descargar las láminas de manera eficiente.
- Carga y descarga automatizada: Los brazos robóticos pueden colocar las láminas en la máquina y retirarlas una vez que el proceso de bordonado y biselado ha finalizado, lo que reduce los tiempos de ciclo y mejora la eficiencia de la producción.
- Menor intervención humana: La automatización completa del proceso de carga y descarga reduce la intervención humana, minimizando los errores y mejorando la seguridad en el lugar de trabajo.
4. Aplicaciones industriales del bordonado y biselado de láminas
Las bordonadoras biseladoras tienen una amplia gama de aplicaciones en industrias que requieren bordes reforzados y acabados precisos en sus piezas metálicas. A continuación, se describen algunas de las principales aplicaciones industriales:
4.1. Industria automotriz
En la fabricación de automóviles, los bordes de paneles de carrocería y otras piezas metálicas deben ser redondeados (bordonados) para evitar bordes afilados que puedan causar daños o representar un peligro. Además, el biselado mejora el ensamblaje de componentes y la soldadura, facilitando un ajuste preciso y seguro.
4.2. Fabricación de recipientes metálicos
En la producción de envases metálicos, como latas de bebidas o recipientes de alimentos, el bordonado es esencial para crear bordes seguros y funcionales. Los bordes redondeados permiten un mejor sellado y aseguran que los consumidores no se lastimen al manipular los envases.
4.3. Industria aeroespacial
En la industria aeronáutica, se utiliza el biselado para preparar los bordes de los paneles metálicos para soldadura, asegurando una unión fuerte y precisa. El bordonado también se emplea en piezas estructurales para reforzar bordes ligeros sin añadir peso innecesario.
4.4. Fabricación de electrodomésticos
Los electrodomésticos como lavadoras, secadoras y refrigeradores requieren piezas con bordes bien acabados, tanto por razones estéticas como por seguridad. Las bordonadoras biseladoras garantizan que las carcasas metálicas tengan bordes lisos y precisos, lo que mejora la durabilidad y apariencia del producto final.
5. Ventajas y beneficios del uso de bordonadoras biseladoras
El uso de una bordonadora biseladora de lámina ofrece varias ventajas significativas:
- Eficiencia en la producción: Al combinar los procesos de bordonado y biselado en una sola máquina, se ahorra tiempo y se mejora la eficiencia operativa.
- Alta precisión: Gracias a los controles automatizados y la capacidad de ajustes finos, se logran bordes uniformes y precisos en todo el proceso.
- Versatilidad: Las máquinas bordonadoras biseladoras son adecuadas para trabajar con diferentes tipos de metales y grosores de láminas, lo que las hace útiles para una amplia gama de aplicaciones.
- Mejora en la seguridad: El bordonado elimina los bordes afilados, mejorando la seguridad en productos como envases y componentes automotrices.
- Reducción de errores humanos: La automatización y los controles CNC reducen la posibilidad de errores durante el proceso de producción, mejorando la consistencia y calidad del producto.
6. Mantenimiento y optimización de una bordonadora biseladora de lámina
El mantenimiento regular es clave para garantizar el buen funcionamiento de una bordonadora biseladora de lámina. Algunas prácticas recomendadas incluyen:
- Lubricación periódica: Mantener los rodillos y cuchillas bien lubricados reduce el desgaste y mejora el rendimiento de la máquina.
- Revisión de cuchillas y rodillos: Inspeccionar regularmente las herramientas para asegurarse de que no presenten desgaste o daño. El reemplazo a tiempo es esencial para evitar defectos en las piezas procesadas.
- Limpieza de residuos: Limpiar la máquina regularmente de restos de material o lubricantes acumulados mejora la precisión y evita interferencias en el proceso.
Embutido Profundo: Principios, Procesos y Aplicaciones Industriales
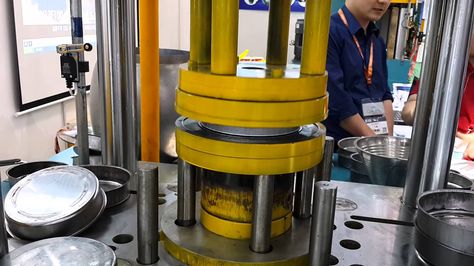
El embutido profundo es uno de los procesos de conformado de metales más utilizados en la industria. Permite transformar una lámina plana de metal en una pieza tridimensional con cavidades profundas y formas complejas, como recipientes, cubiertas y piezas estructurales. Este proceso es fundamental en sectores como la automoción, aeroespacial, electrodomésticos, envases metálicos y electrónica, donde se requiere fabricar componentes ligeros, resistentes y precisos.
El embutido profundo se lleva a cabo utilizando prensas y matrices especiales que aplican fuerzas controladas para deformar el material. Este proceso puede parecer simple, pero involucra numerosos factores técnicos que influyen en la calidad del producto final, como el tipo de material, las propiedades mecánicas, el diseño de la herramienta y los parámetros de operación.
En este documento, se explorará en profundidad el proceso de embutido profundo, sus principios fundamentales, los factores que influyen en su éxito y las diversas aplicaciones industriales donde se emplea.
Principios del embutido profundo
1.1. ¿Qué es el embutido profundo?
El embutido profundo es un proceso de conformado de metales que consiste en la deformación plástica de una lámina metálica mediante una matriz y un punzón, transformando la lámina en una pieza hueca tridimensional. El material se coloca sobre una matriz y el punzón empuja el centro de la lámina hacia el interior de la matriz, deformando el material sin cortarlo, hasta que adopta la forma de la cavidad de la matriz.
La profundidad de la pieza generada es mayor que su diámetro, de ahí el término “profundo”. A diferencia de otros procesos de conformado de metales, el embutido profundo es capaz de producir piezas de gran profundidad sin necesidad de cortar el material, lo que resulta en componentes con paredes finas, ligeros y de alta resistencia.
1.2. Proceso de embutido profundo
El embutido profundo se realiza en varias etapas, que pueden variar en complejidad dependiendo del diseño de la pieza y del tipo de material utilizado. A continuación, se describen los pasos básicos del proceso:
- Corte de la lámina: Se comienza cortando una lámina metálica plana, generalmente llamada “blanco”, con la forma y tamaño adecuados para el proceso.
- Colocación en la matriz: El blanco se coloca sobre la matriz, que contiene una cavidad con la forma deseada para la pieza final. La lámina se sostiene mediante un anillo de sujeción o un dispositivo similar para evitar que se mueva durante el embutido.
- Embutición: Un punzón desciende y presiona el centro del blanco, empujándolo hacia el interior de la cavidad de la matriz. A medida que el punzón avanza, el material se deforma plásticamente, estirándose y adaptándose a la forma de la cavidad sin romperse.
- Liberación de la pieza: Una vez que el punzón ha alcanzado la profundidad deseada, se retira y la pieza embutida es extraída de la matriz.
El embutido profundo se puede realizar en una o varias etapas, dependiendo de la complejidad de la pieza. En algunos casos, es necesario realizar varias pasadas para alcanzar la forma y profundidad finales sin causar fallos o defectos en el material.
1.3. Herramientas utilizadas en el embutido profundo
El embutido profundo requiere de herramientas especializadas para controlar la deformación del material y garantizar la precisión de la pieza final. Las herramientas clave incluyen:
- Matriz:
- Es el molde en el que se deforma la lámina metálica. Contiene una cavidad con la forma deseada para la pieza. Las matrices están hechas de materiales de alta resistencia, como acero endurecido o carburo de tungsteno, para soportar las fuerzas de embutido y el desgaste.
- Punzón:
- El punzón es la herramienta que aplica presión sobre el blanco, empujándolo hacia la matriz. Tiene una forma complementaria a la cavidad de la matriz y está diseñado para resistir la fricción y las altas presiones durante el proceso.
- Anillo de sujeción:
- Mantiene la lámina en su lugar y evita que se desplace durante el embutido. También ayuda a controlar el flujo del material para evitar arrugas o fallos.
- Contrapunzón (opcional):
- En algunos procesos de embutido profundo, se utiliza un contrapunzón para aplicar presión desde el lado opuesto del punzón. Esto ayuda a garantizar que el material fluya de manera uniforme hacia la cavidad de la matriz.
Factores que influyen en el proceso de embutido profundo
El éxito del embutido profundo depende de varios factores interrelacionados que deben controlarse cuidadosamente para evitar defectos y garantizar la calidad de la pieza. A continuación, se describen los factores más importantes:
2.1. Propiedades del material
El tipo de material utilizado para la lámina metálica juega un papel crucial en el proceso de embutido profundo. No todos los materiales son adecuados para este proceso, y aquellos que se utilicen deben tener ciertas propiedades para garantizar que puedan deformarse sin romperse. Las propiedades más importantes incluyen:
- Ductilidad:
- La ductilidad es la capacidad del material para deformarse plásticamente sin romperse. Los materiales altamente dúctiles, como el aluminio, el cobre o el acero de baja aleación, son ideales para el embutido profundo, ya que pueden estirarse sin fracturarse.
- Resistencia a la tracción:
- La resistencia a la tracción determina la cantidad de tensión que el material puede soportar antes de romperse. Un material con alta resistencia a la tracción es menos propenso a agrietarse o romperse durante el embutido profundo.
- Espesor de la lámina:
- El grosor de la lámina también afecta el proceso. Las láminas más delgadas son más fáciles de deformar, pero son más propensas a desarrollar arrugas o fallos. Las láminas más gruesas requieren mayores fuerzas de presión, pero son más resistentes.
- Coeficiente de endurecimiento:
- El coeficiente de endurecimiento se refiere a la capacidad del material para endurecerse a medida que se deforma. Un material con un alto coeficiente de endurecimiento puede resistir mejor las tensiones durante el embutido, lo que reduce la probabilidad de fallos.
2.2. Geometría de la pieza
El diseño de la pieza a embutir también influye en la complejidad del proceso. Las piezas con formas más complejas, profundidades mayores o radios de curvatura pequeños son más difíciles de embutir sin generar defectos. Algunos aspectos de la geometría que deben tenerse en cuenta incluyen:
- Relación entre la profundidad y el diámetro:
- En el embutido profundo, la relación entre la profundidad y el diámetro de la pieza es crucial. A medida que aumenta la profundidad en comparación con el diámetro, se incrementa la dificultad del proceso. Piezas muy profundas requieren múltiples etapas de embutido para evitar fallos.
- Radios de curvatura:
- Los radios de curvatura de la pieza también afectan el flujo del material. Radios pequeños aumentan la posibilidad de fracturas en el material, mientras que radios más grandes facilitan el proceso de deformación.
- Uniformidad de las paredes:
- En algunas aplicaciones, se requiere que las piezas tengan paredes de grosor uniforme. Esto puede ser difícil de lograr en piezas profundas, ya que el material tiende a estirarse de manera desigual durante el embutido. Un diseño adecuado de la matriz y el uso de lubricantes pueden ayudar a mitigar este problema.
2.3. Lubricación
La lubricación es fundamental en el embutido profundo para reducir la fricción entre la lámina y las herramientas (matriz y punzón). La fricción excesiva puede causar desgaste en las herramientas y defectos en la pieza, como arrugas, roturas o fracturas. La lubricación adecuada también mejora el flujo del material, permitiendo que se deforme de manera más uniforme.
Los lubricantes utilizados en el embutido profundo deben seleccionarse en función del tipo de material, el diseño de la pieza y los parámetros de operación. Los lubricantes más comunes incluyen aceites minerales, grasas, ceras o compuestos de base acuosa.
2.4. Parámetros del proceso
El éxito del embutido profundo depende de un control preciso de varios parámetros de operación, que deben ajustarse de acuerdo con el tipo de material, el diseño de la pieza y las herramientas utilizadas. Los parámetros más importantes incluyen:
- Velocidad de embutido:
- La velocidad a la que el punzón desciende sobre el material es crucial para evitar defectos. Una velocidad demasiado alta puede generar tensiones excesivas en el material, provocando fracturas, mientras que una velocidad demasiado baja puede aumentar la fricción y el desgaste de las herramientas.
- Fuerza de embutido:
- La fuerza de embutido debe ser suficiente para deformar el material sin exceder su límite de resistencia a la tracción. Si la fuerza es demasiado baja, la lámina no se deformará correctamente, mientras que una fuerza excesiva puede causar fallos en el material o en la herramienta.
- Presión de sujeción:
- La presión aplicada por el anillo de sujeción debe ajustarse cuidadosamente para evitar que el material se desplace o se arrugue durante el embutido. Una presión insuficiente puede provocar arrugas, mientras que una presión excesiva puede dificultar el flujo del material.
- Temperatura:
- En algunos casos, es beneficioso calentar el material antes del embutido para aumentar su ductilidad. El embutido en caliente se utiliza comúnmente para materiales más duros, como el acero inoxidable, que son difíciles de deformar a temperatura ambiente.
Defectos comunes en el embutido profundo y cómo evitarlos
A pesar de la precisión del proceso de embutido profundo, pueden surgir defectos en las piezas debido a una variedad de factores. Identificar las causas de estos defectos y aplicar las medidas correctivas adecuadas es crucial para asegurar la calidad del producto final. A continuación, se describen los defectos más comunes en el embutido profundo y las estrategias para evitarlos:
3.1. Arrugas
Las arrugas son uno de los defectos más comunes en el embutido profundo y se producen cuando la lámina no está adecuadamente sujeta o cuando el material se acumula en ciertos puntos, en lugar de fluir uniformemente hacia la matriz. Las arrugas suelen aparecer en las áreas cercanas a los bordes de la pieza, donde el material se somete a compresión.
Causas de las arrugas:
- Insuficiente presión del anillo de sujeción.
- Grosor inadecuado del material.
- Diseño inadecuado de la matriz, con radios demasiado pequeños.
- Velocidad de embutido demasiado alta.
Soluciones:
- Aumentar la presión del anillo de sujeción para controlar mejor el flujo del material.
- Usar materiales de mayor grosor o más resistentes a la compresión.
- Rediseñar la matriz para aumentar los radios de curvatura, facilitando el flujo del material.
- Ajustar la velocidad de embutido para reducir las tensiones en el material.
3.2. Grietas y fracturas
Las grietas y fracturas ocurren cuando el material no tiene suficiente ductilidad para soportar las tensiones generadas durante el embutido. Este defecto se suele observar en áreas donde el material está sometido a tensiones de estiramiento excesivas, como las esquinas o los radios de curvatura pequeños.
Causas de grietas y fracturas:
- Material con baja ductilidad o resistencia a la tracción insuficiente.
- Radios de curvatura demasiado pequeños en la matriz o el punzón.
- Fuerza de embutido demasiado alta.
- Falta de lubricación adecuada.
Soluciones:
- Seleccionar materiales más dúctiles o que soporten mayores tensiones.
- Aumentar los radios de curvatura en el diseño de la matriz y el punzón.
- Ajustar la fuerza de embutido para evitar tensiones excesivas en el material.
- Asegurarse de que la lubricación sea adecuada para reducir la fricción y mejorar el flujo del material.
3.3. Estiramiento excesivo y adelgazamiento de las paredes
El estiramiento excesivo del material puede causar una reducción en el grosor de las paredes de la pieza embutida, lo que puede afectar negativamente su resistencia y funcionalidad. Este defecto ocurre cuando el material es estirado más allá de su capacidad de deformación, lo que provoca un adelgazamiento desigual.
Causas del estiramiento excesivo:
- Material con bajo coeficiente de endurecimiento.
- Diseño de la matriz inadecuado, que no controla correctamente el flujo del material.
- Uso de láminas demasiado delgadas.
- Velocidad de embutido demasiado alta, que genera tensiones innecesarias.
Soluciones:
- Usar materiales con mayor coeficiente de endurecimiento, que sean más resistentes al estiramiento.
- Rediseñar la matriz para mejorar el control sobre el flujo del material.
- Seleccionar láminas de mayor grosor.
- Reducir la velocidad de embutido para permitir un estiramiento más controlado del material.
3.4. Roturas en el borde de la pieza
Las roturas en el borde ocurren cuando el borde de la lámina se estira demasiado o no se controla adecuadamente durante el embutido. Este defecto puede hacer que la pieza sea inservible, ya que un borde roto afecta la integridad estructural y la apariencia de la pieza.
Causas de las roturas en el borde:
- Estiramiento excesivo del material.
- Material demasiado frágil o con baja resistencia.
- Diseño de la matriz con bordes demasiado afilados.
- Lubricación insuficiente o inapropiada.
Soluciones:
- Ajustar la velocidad de embutido para reducir el estiramiento en el borde de la pieza.
- Usar materiales con mayor resistencia a la tracción o con mayor ductilidad.
- Redondear los bordes de la matriz para facilitar el flujo del material.
- Asegurarse de que la lubricación sea adecuada para reducir la fricción y el desgaste en el borde.
3.5. Desgarros
Los desgarros son defectos graves que ocurren cuando el material se rompe en áreas sometidas a tensiones excesivas. Este defecto puede hacer que la pieza embutida sea inservible y, en algunos casos, puede dañar las herramientas de embutido si no se detecta a tiempo.
Causas de los desgarros:
- Material de baja calidad o con inclusiones que generan puntos débiles.
- Velocidades de embutido demasiado altas, que someten al material a tensiones excesivas.
- Diseño inadecuado de la matriz o el punzón, que genera concentraciones de tensión en ciertos puntos.
- Fuerza de embutido mal ajustada.
Soluciones:
- Utilizar materiales de alta calidad, libres de inclusiones o impurezas.
- Reducir la velocidad de embutido para permitir que el material fluya de manera más uniforme.
- Rediseñar la matriz y el punzón para reducir las concentraciones de tensión.
- Ajustar la fuerza de embutido para evitar la sobrecarga del material.
3.6. Pliegues y dobleces
Los pliegues y dobleces son deformaciones no deseadas que pueden ocurrir en el material durante el embutido profundo. Estos defectos generalmente se presentan cuando el material no se estira de manera uniforme o cuando el flujo del material no está bien controlado.
Causas de pliegues y dobleces:
- Insuficiente presión del anillo de sujeción, lo que permite que el material se doble en lugar de estirarse.
- Velocidad de embutido demasiado alta.
- Falta de lubricación adecuada.
- Diseño de la matriz que no favorece un flujo uniforme del material.
Soluciones:
- Aumentar la presión del anillo de sujeción para controlar mejor el flujo del material.
- Reducir la velocidad de embutido para permitir un estiramiento más controlado.
- Asegurarse de que la lubricación sea suficiente y adecuada para el material.
- Rediseñar la matriz para mejorar el flujo del material y evitar zonas donde se puedan formar pliegues o dobleces.
Técnicas complementarias en el embutido profundo
En algunos casos, el embutido profundo se complementa con otras técnicas de conformado de metales para mejorar los resultados o permitir la fabricación de piezas más complejas. A continuación, se describen algunas de las técnicas más comunes utilizadas en combinación con el embutido profundo:
4.1. Recalcado
El recalcado es un proceso utilizado para aumentar el grosor o la resistencia de una pieza embutida en áreas específicas. Durante el recalcado, la pieza ya formada se somete a una compresión adicional en las zonas donde se requiere mayor resistencia o densidad. Este proceso es especialmente útil para componentes que estarán sometidos a grandes cargas o tensiones.
Aplicaciones del recalcado:
- Refuerzo de áreas críticas en pistones o piezas de motores.
- Aumento de la resistencia de componentes estructurales en la industria automotriz o aeroespacial.
4.2. Planchado
El planchado es una técnica utilizada para reducir el grosor de las paredes de una pieza embutida, mejorando la uniformidad y el acabado superficial. Durante el planchado, la pieza se pasa a través de una matriz que aplica presión controlada, comprimiendo el material y reduciendo su grosor. Esta técnica es especialmente útil en la fabricación de piezas con paredes delgadas y precisas, como latas de bebidas.
Aplicaciones del planchado:
- Producción de envases metálicos con paredes finas y uniformes.
- Fabricación de componentes ligeros en la industria aeroespacial o electrónica.
4.3. Embutición inversa
La embutición inversa es una variación del proceso de embutido profundo que se utiliza para fabricar piezas con geometrías más complejas o con diferentes secciones de diámetro. Durante la embutición inversa, el punzón empuja el material en la dirección opuesta al embutido tradicional, creando formas más elaboradas o permitiendo la fabricación de piezas con diferentes grosores en distintas secciones.
Aplicaciones de la embutición inversa:
- Producción de componentes automotrices o de maquinaria con perfiles complejos.
- Fabricación de cilindros o recipientes metálicos con múltiples diámetros o formas variadas.
4.4. Corte posterior al embutido
En algunos casos, las piezas embutidas requieren cortes adicionales para obtener la forma final. El proceso de corte se realiza después del embutido para eliminar material sobrante o crear agujeros o ranuras en la pieza. El corte puede realizarse mediante herramientas de corte mecánicas, como troqueles, o mediante tecnologías avanzadas, como el corte por láser o por chorro de agua.
Aplicaciones del corte posterior:
- Creación de aberturas o ranuras en componentes electrónicos o mecánicos.
- Eliminación de material sobrante en envases o piezas de precisión.
Aplicaciones industriales del embutido profundo
El embutido profundo es una técnica ampliamente utilizada en diversas industrias debido a su capacidad para producir piezas ligeras, resistentes y con formas complejas. A continuación, se describen algunas de las principales aplicaciones industriales del embutido profundo:
5.1. Industria automotriz
En la industria automotriz, el embutido profundo se utiliza para fabricar una amplia variedad de componentes esenciales para los vehículos. La capacidad de producir piezas ligeras pero resistentes es crucial para mejorar la eficiencia del combustible y cumplir con los estrictos requisitos de seguridad de la industria.
Aplicaciones en la industria automotriz:
- Producción de paneles de carrocería, puertas y capós.
- Fabricación de componentes estructurales, como refuerzos y soportes.
- Producción de pistones, carcasas de motores y otras piezas de precisión.
5.2. Industria aeroespacial
La industria aeroespacial requiere componentes que sean extremadamente ligeros pero capaces de soportar grandes tensiones y temperaturas extremas. El embutido profundo permite la fabricación de piezas con formas complejas y paredes delgadas, lo que es ideal para mejorar la eficiencia y el rendimiento de los aviones y naves espaciales.
Aplicaciones en la industria aeroespacial:
- Producción de componentes estructurales para fuselajes y alas.
- Fabricación de carcasas de motores y sistemas de escape.
- Producción de piezas de precisión para sistemas de control y propulsión.
5.3. Industria del envasado
El embutido profundo es ampliamente utilizado en la industria del envasado para la producción de latas y recipientes metálicos. Este proceso permite crear envases con paredes delgadas pero resistentes, lo que es esencial para garantizar la integridad del producto y la seguridad del consumidor.
Aplicaciones en la industria del envasado:
- Producción de latas de bebidas y alimentos.
- Fabricación de envases metálicos para productos químicos o industriales.
- Producción de envases de aerosol y contenedores presurizados.
5.4. Industria de electrodomésticos
En la industria de electrodomésticos, el embutido profundo se utiliza para fabricar carcasas y componentes metálicos que requieren resistencia, ligereza y un acabado estético de alta calidad. Este proceso es esencial para producir electrodomésticos duraderos y de alto rendimiento.
Aplicaciones en la industria de electrodomésticos:
- Fabricación de carcasas de lavadoras, secadoras y refrigeradores.
- Producción de componentes internos, como tambores de lavadora y cubiertas de motores.
- Fabricación de piezas estructurales y de ensamblaje para electrodomésticos.
5.5. Industria electrónica
En la industria electrónica, el embutido profundo se utiliza para producir componentes metálicos pequeños y precisos que son esenciales para el funcionamiento de dispositivos electrónicos. La capacidad de producir piezas con formas complejas y paredes delgadas es fundamental para optimizar el diseño y rendimiento de los dispositivos electrónicos.
Aplicaciones en la industria electrónica:
- Producción de carcasas y chasis metálicos para teléfonos móviles, computadoras y otros dispositivos.
- Fabricación de componentes de disipación de calor y protección electromagnética.
- Producción de piezas estructurales y de ensamblaje para dispositivos electrónicos.
Avances tecnológicos en el embutido profundo
El embutido profundo ha evolucionado con el tiempo gracias a los avances en materiales, herramientas y tecnologías de control. Estos avances han permitido mejorar la precisión, reducir los defectos y aumentar la eficiencia del proceso. A continuación, se describen algunos de los avances tecnológicos más importantes en el embutido profundo:
6.1. Control numérico por computadora (CNC)
El uso de tecnología CNC en el embutido profundo ha permitido un control más preciso sobre los parámetros del proceso, como la velocidad, la fuerza y la presión. Las máquinas CNC pueden ajustar automáticamente estos parámetros en función del material y el diseño de la pieza, lo que mejora la precisión y la repetibilidad del proceso.
Beneficios del CNC en el embutido profundo:
- Mayor precisión en la fabricación de piezas.
- Reducción de defectos y variaciones en las piezas producidas.
- Mayor flexibilidad para producir diferentes diseños y formas.
6.2. Sensores y monitoreo en tiempo real
El uso de sensores avanzados y sistemas de monitoreo en tiempo real ha permitido mejorar el control del proceso de embutido profundo. Estos sensores pueden detectar variaciones en la presión, la velocidad y el grosor del material, lo que permite realizar ajustes automáticos para garantizar un proceso más consistente y preciso.
Beneficios del monitoreo en tiempo real:
- Reducción de defectos y desperdicio de material.
- Mejora en la calidad y uniformidad de las piezas producidas.
- Mayor eficiencia en la producción en masa.
6.3. Lubricantes avanzados
Los nuevos desarrollos en lubricantes han permitido reducir la fricción y mejorar el flujo del material durante el embutido profundo. Los lubricantes modernos están diseñados para soportar altas presiones y temperaturas, lo que permite un mejor rendimiento y una mayor vida útil de las herramientas.
Beneficios de los lubricantes avanzados:
- Reducción del desgaste en las herramientas de embutido.
- Mejora en la calidad de las piezas, con menos defectos como arrugas o grietas.
- Mayor eficiencia en el proceso, con menos interrupciones por mantenimiento.
6.4. Materiales avanzados
El desarrollo de nuevos materiales más resistentes y dúctiles ha permitido ampliar las aplicaciones del embutido profundo a sectores que requieren piezas con propiedades mecánicas excepcionales. Los aceros avanzados de alta resistencia (AHSS) y las aleaciones ligeras, como el aluminio y el titanio, son algunos de los materiales que se utilizan en aplicaciones donde se requiere un rendimiento superior.
Beneficios de los materiales avanzados:
- Producción de piezas más ligeras y resistentes.
- Mayor durabilidad y resistencia a la fatiga en aplicaciones exigentes.
- Reducción del consumo de material, con piezas más delgadas pero igualmente resistentes.
6.5. Simulación y diseño asistido por computadora (CAD/CAM)
El uso de software de simulación y diseño asistido por computadora (CAD/CAM) ha mejorado significativamente la capacidad para diseñar y optimizar el proceso de embutido profundo. La simulación permite prever posibles defectos, como arrugas o fracturas, y ajustar el diseño de las herramientas y los parámetros del proceso antes de comenzar la producción.
Beneficios de la simulación y el diseño CAD/CAM:
- Reducción de los tiempos de desarrollo y puesta en marcha de nuevos productos.
- Optimización del proceso para minimizar defectos y mejorar la calidad.
- Mayor flexibilidad para producir piezas complejas con menos iteraciones de prueba y error.
Mantenimiento y optimización de herramientas de embutido profundo
El mantenimiento adecuado de las herramientas utilizadas en el embutido profundo es esencial para garantizar la calidad y la consistencia de las piezas producidas, así como para prolongar la vida útil de las herramientas. A continuación, se describen algunas prácticas clave para el mantenimiento y la optimización de herramientas en el embutido profundo:
7.1. Lubricación y limpieza
La lubricación adecuada de las herramientas es esencial para reducir la fricción y el desgaste durante el proceso de embutido. Los rodillos, punzones y matrices deben mantenerse bien lubricados para asegurar un flujo suave del material y evitar defectos como arrugas o fracturas.
Recomendaciones para la lubricación:
- Utilizar lubricantes de alta calidad, específicamente diseñados para el tipo de material y las condiciones de operación.
- Limpiar regularmente las herramientas para eliminar restos de material o lubricantes usados, lo que puede afectar el rendimiento de la máquina.
7.2. Revisión de herramientas
Las herramientas de embutido profundo están sometidas a un desgaste constante debido a las altas presiones y fricción durante el proceso. Es importante inspeccionar regularmente las matrices y los punzones para detectar cualquier signo de desgaste o deformación que pueda afectar la calidad de las piezas.
Recomendaciones para la revisión de herramientas:
- Inspeccionar regularmente las herramientas en busca de desgaste, grietas o deformaciones.
- Reemplazar las herramientas desgastadas antes de que comiencen a generar defectos en las piezas.
- Realizar un mantenimiento preventivo periódico para prolongar la vida útil de las herramientas.
7.3. Optimización de parámetros
Los parámetros de operación, como la velocidad, la fuerza y la presión de embutido, deben ajustarse cuidadosamente para optimizar el proceso y reducir el desgaste de las herramientas. Un mal ajuste de estos parámetros puede generar tensiones excesivas en las herramientas, lo que resulta en un desgaste prematuro o defectos en las piezas.
Recomendaciones para la optimización de parámetros:
- Utilizar simulaciones o software de diseño para optimizar los parámetros antes de comenzar la producción.
- Ajustar los parámetros de operación en función del tipo de material y el diseño de la pieza.
- Realizar pruebas periódicas para verificar que los parámetros estén optimizados para cada lote de producción.
7.4. Capacitación del personal
El personal que opera las máquinas de embutido profundo debe estar debidamente capacitado para ajustar los parámetros de operación, realizar inspecciones de herramientas y solucionar problemas durante el proceso. Una capacitación adecuada es esencial para garantizar que el proceso se realice de manera eficiente y segura.
Recomendaciones para la capacitación del personal:
- Proporcionar capacitación continua en el uso de máquinas y herramientas de embutido profundo.
- Enseñar a los operarios a identificar los signos de desgaste o fallos en las herramientas.
- Asegurarse de que los operarios comprendan cómo ajustar los parámetros de operación para optimizar el proceso.
Futuro del embutido profundo: Nuevas tendencias y desafíos
El embutido profundo sigue evolucionando a medida que surgen nuevos materiales, tecnologías y requisitos de la industria. En el futuro, se espera que el proceso continúe mejorando en términos de eficiencia, precisión y sostenibilidad. A continuación, se presentan algunas tendencias emergentes y desafíos que definirán el futuro del embutido profundo:
8.1. Materiales ligeros y avanzados
El uso de materiales ligeros y avanzados seguirá siendo una tendencia clave en el embutido profundo, especialmente en industrias como la automotriz y la aeroespacial, donde la reducción de peso es crítica para mejorar la eficiencia energética. Los materiales compuestos y las aleaciones avanzadas permitirán la producción de piezas más ligeras pero igualmente resistentes.
Desafíos:
- Adaptar el proceso de embutido profundo a los nuevos materiales, que pueden tener propiedades mecánicas diferentes a las de los metales tradicionales.
- Desarrollar herramientas y lubricantes que sean compatibles con estos materiales avanzados.
8.2. Sostenibilidad y reducción de residuos
La sostenibilidad será un factor cada vez más importante en la fabricación de piezas metálicas. El embutido profundo ya es un proceso eficiente en términos de material, pero en el futuro se espera que se desarrollen nuevas tecnologías para reducir aún más los residuos y mejorar la eficiencia energética.
Desafíos:
- Desarrollar procesos de embutido profundo que generen menos residuos y utilicen menos energía.
- Implementar prácticas de reciclaje y reutilización de materiales en las plantas de producción.
8.3. Automatización y robótica
El uso de robots y sistemas de automatización avanzada seguirá creciendo en las líneas de producción de embutido profundo. Los robots pueden mejorar la precisión, reducir los tiempos de ciclo y aumentar la eficiencia de la producción en masa.
Desafíos:
- Integrar robots y sistemas de automatización de manera efectiva en las líneas de producción.
- Desarrollar sistemas de monitoreo en tiempo real que puedan ajustar automáticamente los parámetros del proceso para optimizar la producción.
Conclusión
El embutido profundo es un proceso fundamental en la fabricación de piezas metálicas complejas y de alta precisión. Su capacidad para producir componentes ligeros, resistentes y con formas detalladas lo convierte en una opción ideal para una amplia gama de industrias. A medida que la tecnología avanza, el embutido profundo seguirá evolucionando, adaptándose a nuevos materiales, tecnologías y requisitos industriales, y ofreciendo soluciones innovadoras para la producción en masa de piezas metálicas de alta calidad.
Proceso de Embutido Profundo: Descripción Detallada
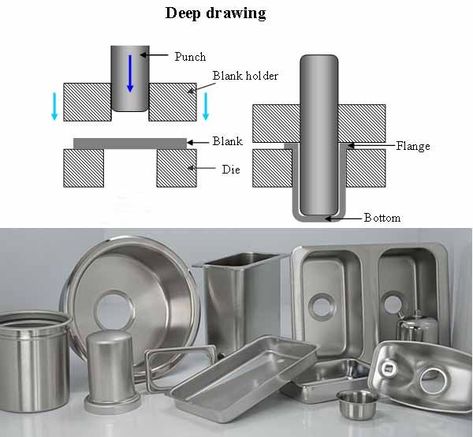
El embutido profundo es un proceso de conformado de metales que se utiliza para fabricar piezas huecas, de forma cilíndrica, rectangular, esférica o con geometrías complejas, a partir de una lámina plana de metal. Este proceso es ampliamente utilizado en la industria debido a su capacidad para producir piezas ligeras, resistentes y con tolerancias precisas, lo que lo convierte en una técnica clave en sectores como el automotriz, aeroespacial, electrodomésticos, envasado y muchos más.
En este documento, se presentará una descripción exhaustiva del proceso de embutido profundo, sus etapas clave, las herramientas utilizadas, las variables críticas que influyen en su éxito y los defectos comunes asociados con el proceso, junto con las técnicas para evitarlos.
1. Concepto del embutido profundo
El embutido profundo es una técnica de deformación plástica que implica el uso de una prensa hidráulica o mecánica para aplicar fuerza sobre una lámina metálica (blanco), que se coloca sobre una matriz. Un punzón presiona la lámina, forzando al material a entrar en la cavidad de la matriz, deformando el metal sin romperlo. El embutido profundo permite fabricar componentes de metal que tienen una profundidad mayor que su diámetro, como latas, cilindros, cubiertas o recipientes.
Este proceso permite estirar y deformar el metal para crear formas huecas o cóncavas sin alterar las propiedades mecánicas del material. Para conseguir piezas de alta calidad, es esencial que el proceso esté controlado de manera precisa, ya que la aplicación incorrecta de la fuerza o el uso de herramientas mal diseñadas puede generar defectos.
1.1. Diferencia entre embutido profundo y otros procesos de conformado
A diferencia de otros procesos de conformado, como el estampado o la embutición simple, en el embutido profundo, la profundidad de la pieza final es mayor que el diámetro del material original. El embutido profundo también se diferencia de otros métodos en su capacidad para producir formas complejas con paredes delgadas, lo que es crítico para la producción en masa de envases metálicos y componentes industriales.
2. Fases del proceso de embutido profundo
El proceso de embutido profundo se puede dividir en varias etapas críticas, que deben llevarse a cabo de manera precisa para obtener piezas de alta calidad sin defectos. A continuación, se describen las fases más importantes del proceso:
2.1. Preparación de la lámina
El primer paso en el proceso de embutido profundo es la preparación de la lámina metálica, también conocida como “blanco”. La lámina debe cortarse a las dimensiones adecuadas y asegurarse de que la superficie esté libre de impurezas, arañazos o defectos que podrían afectar el proceso.
- Material: Los materiales más comunes utilizados en el embutido profundo incluyen aluminio, acero inoxidable, cobre y latón. Estos materiales tienen una combinación de ductilidad y resistencia que les permite soportar las tensiones del proceso sin romperse.
- Espesor de la lámina: El grosor del material tiene un gran impacto en el éxito del embutido. Láminas demasiado delgadas son susceptibles de desgarrarse durante el proceso, mientras que láminas demasiado gruesas pueden ser difíciles de deformar. El grosor óptimo dependerá del tipo de material y de la geometría de la pieza que se desea producir.
2.2. Colocación en la matriz
Una vez que el blanco ha sido cortado y preparado, se coloca sobre la matriz. La matriz tiene una cavidad con la forma de la pieza final que se desea producir. Es importante que el blanco esté bien alineado y posicionado para evitar deformaciones asimétricas durante el proceso.
- Alineación: El blanco debe estar perfectamente centrado sobre la matriz para que la fuerza aplicada por el punzón sea uniforme. Si el blanco no está bien alineado, es posible que se produzcan fallos como arrugas o fracturas en la pieza.
- Sujeción: En algunos casos, se utiliza un anillo de sujeción o dispositivo de sujeción para mantener el blanco en su lugar y evitar que se desplace durante el proceso de embutido.
2.3. Acción del punzón
El punzón es el componente clave que ejerce la fuerza sobre el material, presionando el centro del blanco y empujándolo hacia la cavidad de la matriz. El punzón desciende lentamente, deformando el material y adaptándolo a la forma de la matriz.
- Fuerza aplicada: La cantidad de fuerza que aplica el punzón debe ser suficiente para deformar el material, pero no tan alta como para causar fallos o rupturas. Esta fuerza debe ajustarse según el tipo de material y el grosor del blanco.
- Velocidad de embutido: La velocidad a la que el punzón desciende también es importante. Si la velocidad es demasiado alta, puede provocar tensiones excesivas en el material, lo que aumenta el riesgo de fracturas. Si es demasiado lenta, el proceso se vuelve ineficiente y aumenta el desgaste de las herramientas.
2.4. Formación de la pieza
A medida que el punzón continúa descendiendo, el material se deforma progresivamente, estirándose y tomando la forma de la cavidad de la matriz. Es fundamental que el material fluya de manera uniforme para evitar la aparición de arrugas, grietas o adelgazamiento desigual en las paredes de la pieza.
- Estiramiento del material: El material se estira en varias direcciones a medida que el punzón lo empuja hacia la cavidad de la matriz. La distribución uniforme de este estiramiento es crítica para evitar defectos, especialmente en piezas con geometrías complejas o radios pequeños.
- Fricción: La fricción entre el material y las herramientas (matriz y punzón) puede afectar el flujo del material y generar puntos de tensión donde el material se adelgace o se rompa. La aplicación de lubricantes es esencial para reducir la fricción y garantizar un estiramiento suave.
2.5. Extracción de la pieza
Una vez que el punzón ha alcanzado la profundidad deseada, se retira y la pieza formada se extrae de la matriz. En algunos casos, se puede utilizar un contrapunzón para empujar la pieza hacia fuera de la matriz sin causar daños.
- Liberación de la pieza: La pieza debe liberarse cuidadosamente de la matriz para evitar que se deforme durante la extracción. Las fuerzas residuales en el material pueden provocar que la pieza se distorsione si no se maneja correctamente.
- Inspección de la pieza: Después de la extracción, la pieza debe inspeccionarse para garantizar que cumple con las especificaciones y está libre de defectos. Cualquier deformación o fallo detectado en esta etapa debe corregirse antes de continuar con los pasos posteriores de producción.
3. Herramientas utilizadas en el embutido profundo
El embutido profundo requiere el uso de herramientas especializadas que están diseñadas para soportar las fuerzas aplicadas durante el proceso y garantizar la precisión en la conformación del material. A continuación, se describen las herramientas clave utilizadas en este proceso:
3.1. Matriz
La matriz es la herramienta que contiene la cavidad con la forma de la pieza final. La precisión de la matriz es esencial para garantizar que la pieza embutida cumpla con las especificaciones de diseño.
- Diseño de la cavidad: La cavidad de la matriz se diseña según las dimensiones y la geometría de la pieza final. Las matrices pueden ser simples o complejas, dependiendo de la forma de la pieza. Para piezas más complejas, puede ser necesario utilizar varias matrices en diferentes etapas del proceso de embutido.
- Material de la matriz: Las matrices están fabricadas con materiales de alta resistencia, como acero endurecido o carburo de tungsteno, para resistir el desgaste causado por las altas presiones y la fricción durante el embutido.
3.2. Punzón
El punzón es la herramienta que aplica la fuerza necesaria para deformar la lámina y empujarla hacia la cavidad de la matriz. La precisión del punzón es tan importante como la de la matriz para garantizar una distribución uniforme de la fuerza.
- Forma del punzón: El punzón debe tener una forma complementaria a la de la cavidad de la matriz para asegurar un ajuste perfecto durante el proceso de embutido. En algunos casos, el punzón puede tener una forma más simple que la cavidad, dependiendo del diseño de la pieza.
- Material del punzón: Al igual que las matrices, los punzones están hechos de materiales de alta resistencia que pueden soportar las tensiones y el desgaste a largo plazo. El acero endurecido y el carburo de tungsteno son los materiales más comunes.
3.3. Anillo de sujeción
El anillo de sujeción se utiliza para mantener la lámina en su lugar y evitar que se desplace o se deforme durante el embutido. Este anillo ayuda a controlar el flujo del material hacia la cavidad de la matriz.
- Presión de sujeción: La cantidad de presión aplicada por el anillo de sujeción debe ajustarse cuidadosamente. Una presión insuficiente puede permitir que el material se arrugue, mientras que una presión excesiva puede impedir que el material fluya correctamente hacia la matriz.
3.4. Contrapunzón (opcional)
En algunos casos, se utiliza un contrapunzón para aplicar presión desde el lado opuesto del punzón. Esto es especialmente útil en piezas que requieren un control más preciso sobre el flujo del material o en piezas con geometrías complejas.
- Función del contrapunzón: El contrapunzón ayuda a equilibrar las fuerzas durante el proceso de embutido, lo que permite que el material fluya de manera más uniforme hacia la cavidad de la matriz.
4. Variables críticas en el proceso de embutido profundo
El éxito del embutido profundo depende del control preciso de varias variables críticas que pueden influir en la calidad de la pieza final. A continuación, se describen algunas de las variables más importantes que deben considerarse durante el proceso:
4.1. Material utilizado
El tipo de material utilizado para el blanco es una de las variables más importantes en el embutido profundo. No todos los materiales metálicos son adecuados para este proceso, y aquellos que se utilicen deben tener ciertas propiedades mecánicas, como la ductilidad y la resistencia a la tracción, para soportar la deformación sin romperse.
- Ductilidad: Los materiales con alta ductilidad, como el aluminio, el cobre y el acero de baja aleación, son los más adecuados para el embutido profundo, ya que pueden estirarse sin fracturarse.
- Resistencia a la tracción: La resistencia a la tracción del material debe ser lo suficientemente alta como para evitar que se rompa o agriete durante el proceso, pero también debe permitir una deformación suficiente.
4.2. Grosor de la lámina
El grosor de la lámina tiene un impacto directo en la cantidad de fuerza necesaria para realizar el embutido y en la calidad de la pieza final. Las láminas más delgadas son más fáciles de deformar, pero son más propensas a arrugarse o romperse. Las láminas más gruesas, en cambio, requieren más fuerza y pueden generar mayor desgaste en las herramientas.
- Optimización del grosor: El grosor de la lámina debe optimizarse en función de la geometría de la pieza y las propiedades del material. En algunos casos, puede ser necesario ajustar el grosor en diferentes etapas del proceso para evitar defectos.
4.3. Fuerza aplicada
La fuerza aplicada por el punzón debe ajustarse cuidadosamente para asegurar que el material se deforme sin romperse. Esta fuerza debe ser suficiente para que el material fluya hacia la cavidad de la matriz, pero no tan alta como para generar fracturas o deformaciones no deseadas.
- Distribución uniforme de la fuerza: La fuerza debe distribuirse de manera uniforme sobre el blanco para evitar tensiones localizadas que puedan causar defectos como grietas o arrugas.
- Ajuste de la fuerza según el material: Los materiales más duros, como el acero inoxidable, requieren una fuerza mayor para deformarse, mientras que los materiales más blandos, como el aluminio, necesitan menos fuerza.
4.4. Velocidad de embutido
La velocidad de embutido también influye en el éxito del proceso. Si el punzón se mueve demasiado rápido, puede generar tensiones excesivas en el material, lo que aumenta el riesgo de fracturas. Si el punzón se mueve demasiado lentamente, el proceso se vuelve ineficiente y aumenta el desgaste de las herramientas.
- Velocidad óptima: La velocidad de embutido debe ajustarse en función del tipo de material y la geometría de la pieza. La mayoría de las veces, se prefiere una velocidad moderada para permitir un estiramiento controlado del material sin generar defectos.
4.5. Lubricación
La lubricación es esencial para reducir la fricción entre el material y las herramientas durante el embutido profundo. Una lubricación inadecuada puede aumentar la fricción, lo que genera calor, desgaste de las herramientas y una deformación desigual del material.
- Tipos de lubricantes: Los lubricantes utilizados en el embutido profundo incluyen aceites minerales, grasas y ceras, dependiendo del material y los requisitos del proceso. Los lubricantes deben aplicarse de manera uniforme para garantizar que el material fluya sin problemas hacia la cavidad de la matriz.
- Efectos de la lubricación: Una lubricación adecuada ayuda a reducir el desgaste de las herramientas, evita la aparición de arrugas y fracturas en el material y mejora la calidad de la pieza final.
5. Defectos comunes en el embutido profundo y cómo evitarlos
El embutido profundo, aunque es un proceso altamente eficiente, puede generar varios defectos si las variables críticas no se controlan adecuadamente. A continuación, se describen algunos de los defectos más comunes en el embutido profundo y las estrategias para evitarlos:
5.1. Arrugas
Las arrugas se producen cuando el material no fluye de manera uniforme hacia la cavidad de la matriz y se acumula en ciertas áreas. Este es uno de los defectos más comunes en el embutido profundo y suele ocurrir cerca de los bordes de la pieza.
- Causas: Las arrugas pueden ser causadas por una presión insuficiente del anillo de sujeción, una velocidad de embutido demasiado alta o un grosor de la lámina inadecuado.
- Soluciones: Aumentar la presión del anillo de sujeción, reducir la velocidad de embutido o ajustar el grosor del material puede ayudar a reducir la aparición de arrugas.
5.2. Grietas y fracturas
Las grietas y fracturas ocurren cuando el material no puede soportar las tensiones generadas durante el embutido profundo. Este defecto suele aparecer en áreas donde el material se estira más allá de su límite de resistencia.
- Causas: Las grietas pueden ser causadas por una fuerza de embutido demasiado alta, un material con baja ductilidad o un diseño de matriz con radios de curvatura demasiado pequeños.
- Soluciones: Ajustar la fuerza de embutido, usar materiales más dúctiles o aumentar los radios de curvatura en el diseño de la matriz puede ayudar a reducir las grietas.
5.3. Adelgazamiento desigual de las paredes
El adelgazamiento desigual de las paredes ocurre cuando el material se estira de manera no uniforme durante el embutido. Esto puede afectar la resistencia y la funcionalidad de la pieza final.
- Causas: Este defecto puede ser causado por un mal diseño de la matriz o por un control inadecuado de la velocidad de embutido.
- Soluciones: Rediseñar la matriz para mejorar el control sobre el flujo del material o ajustar la velocidad de embutido puede ayudar a reducir el adelgazamiento desigual.
5.4. Desgarros
Los desgarros son fallos graves que ocurren cuando el material se rompe debido a tensiones excesivas. Este defecto puede hacer que la pieza sea inservible y, en algunos casos, puede dañar las herramientas de embutido si no se detecta a tiempo.
- Causas: Los desgarros pueden ser causados por una fuerza de embutido demasiado alta, un material de baja calidad o una fricción excesiva entre el material y las herramientas.
- Soluciones: Ajustar la fuerza de embutido, usar materiales de mayor calidad o mejorar la lubricación puede ayudar a reducir los desgarros.
6. Aplicaciones del embutido profundo en la industria
El embutido profundo es una técnica ampliamente utilizada en una variedad de industrias debido a su capacidad para producir piezas ligeras, resistentes y con formas complejas. A continuación, se describen algunas de las aplicaciones más comunes del embutido profundo:
6.1. Industria automotriz
En la industria automotriz, el embutido profundo se utiliza para fabricar una amplia variedad de componentes esenciales, como paneles de carrocería, puertas, capós y componentes estructurales. Estos componentes deben ser ligeros pero resistentes para mejorar la eficiencia del combustible y garantizar la seguridad del vehículo.
6.2. Industria aeroespacial
La industria aeroespacial depende del embutido profundo para la producción de piezas críticas que requieren una alta precisión y resistencia. Los componentes de fuselaje, cubiertas de motores y piezas estructurales son algunos ejemplos de piezas producidas mediante embutido profundo en este sector.
6.3. Envasado y recipientes metálicos
El embutido profundo es la técnica preferida en la industria del envasado para la producción de latas de bebidas, envases de alimentos y recipientes metálicos para productos químicos. Este proceso permite fabricar envases con paredes delgadas pero resistentes, lo que es esencial para garantizar la integridad del contenido y la seguridad del consumidor.
6.4. Electrodomésticos
En la industria de electrodomésticos, el embutido profundo se utiliza para fabricar carcasas metálicas, tambores de lavadora, cubiertas de motores y otros componentes estructurales que requieren alta resistencia y un acabado estético de calidad.
Conclusión
El embutido profundo es un proceso de conformado de metales altamente eficiente y versátil, que se utiliza para producir una amplia variedad de piezas en diversas industrias. A través del control preciso de las variables clave, como la fuerza aplicada, la velocidad de embutido y la lubricación, es posible obtener piezas de alta calidad con formas complejas y paredes delgadas. Aunque el proceso presenta desafíos, como la aparición de defectos y el desgaste de las herramientas, la optimización de los parámetros y el uso de materiales adecuados pueden garantizar el éxito del embutido profundo en aplicaciones industriales.
Factores que influyen en el proceso de embutido profundo
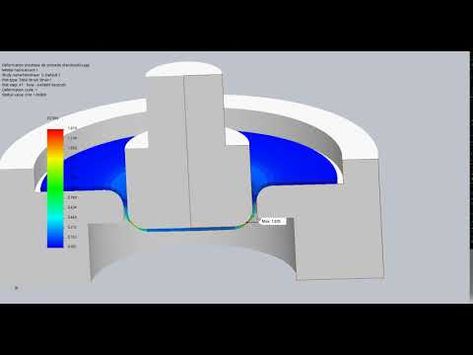
El embutido profundo es un proceso complejo que involucra una serie de factores interrelacionados que afectan directamente la calidad de las piezas producidas, la eficiencia del proceso y la durabilidad de las herramientas. Controlar y ajustar estos factores es esencial para evitar defectos como arrugas, grietas, fracturas, desgaste desigual, y para garantizar que las piezas finales cumplan con las especificaciones técnicas.
A continuación, se describen los principales factores que influyen en el éxito del proceso de embutido profundo:
1. Propiedades del material
El tipo de material utilizado para la lámina metálica (blanco) es uno de los factores más importantes en el embutido profundo, ya que afecta directamente la capacidad del material para deformarse plásticamente sin romperse. No todos los materiales metálicos son aptos para este proceso, y aquellos que se utilicen deben tener ciertas propiedades mecánicas clave, como la ductilidad y la resistencia a la tracción.
1.1. Ductilidad
La ductilidad se refiere a la capacidad del material para deformarse plásticamente sin fracturarse. Los materiales altamente dúctiles son más adecuados para el embutido profundo porque pueden soportar el estiramiento y la deformación a los que se someten durante el proceso sin agrietarse.
- Materiales recomendados: Entre los materiales más comúnmente utilizados en el embutido profundo se incluyen el aluminio, el acero de baja aleación, el acero inoxidable, el cobre y algunas aleaciones de latón. Estos materiales combinan alta ductilidad y resistencia, lo que permite que se deformen sin sufrir fracturas.
- Problemas relacionados con la ductilidad: Si se utiliza un material con baja ductilidad, es más probable que aparezcan defectos como grietas o fracturas. Además, es importante considerar la dirección del laminado del material, ya que la ductilidad puede variar dependiendo de la orientación de los granos en la lámina.
1.2. Resistencia a la tracción
La resistencia a la tracción es la cantidad de tensión que un material puede soportar antes de romperse. Un material con alta resistencia a la tracción es capaz de soportar las tensiones generadas durante el embutido profundo sin romperse.
- Elección del material: Para materiales como el acero inoxidable, que tienen una alta resistencia a la tracción, es necesario ajustar los parámetros del proceso para evitar que las tensiones excesivas causen desgarrones o grietas. La resistencia a la tracción del material también influye en la cantidad de fuerza de embutido necesaria.
- Compromiso entre resistencia y ductilidad: Existe un equilibrio entre la ductilidad y la resistencia a la tracción. Materiales con alta resistencia a la tracción pueden ser menos dúctiles, lo que limita su capacidad para deformarse sin sufrir fallos.
1.3. Espesor de la lámina
El grosor de la lámina influye significativamente en el comportamiento del material durante el embutido profundo. Las láminas más delgadas son más fáciles de deformar, pero también son más propensas a desarrollar arrugas o fracturas, mientras que las láminas más gruesas requieren mayor fuerza de embutido y pueden generar un mayor desgaste en las herramientas.
- Láminas delgadas: Son ideales para la producción de piezas ligeras y con paredes finas, pero requieren un control más preciso de la fuerza de embutido y la presión del anillo de sujeción para evitar arrugas o fallos durante el estiramiento.
- Láminas gruesas: Aumentan la resistencia de la pieza, pero el proceso de embutido se vuelve más exigente, requiriendo mayores fuerzas y un diseño cuidadoso de las herramientas para evitar fracturas o deformaciones no deseadas.
2. Geometría de la pieza
La geometría de la pieza que se está fabricando tiene un impacto directo en el proceso de embutido profundo. Piezas con formas complejas, radios pequeños o grandes profundidades son más difíciles de producir sin defectos. Por lo tanto, el diseño de la pieza influye en la elección de las herramientas, los materiales y los parámetros del proceso.
2.1. Relación profundidad/diámetro
En el embutido profundo, la relación entre la profundidad de la pieza y su diámetro es crítica. Cuando la profundidad es mayor que el diámetro, se requiere un control más preciso del proceso para evitar fallos.
- Mayor profundidad: Cuanto mayor sea la profundidad de la pieza, más complejo será el proceso. Las piezas con una gran relación de profundidad a diámetro pueden requerir varias etapas de embutido, utilizando matrices diferentes para deformar el material en pasos progresivos.
2.2. Radios de curvatura
Los radios de curvatura en el diseño de la pieza también influyen en la facilidad con la que el material puede fluir hacia la cavidad de la matriz. Radios muy pequeños son propensos a generar fracturas o grietas debido a la concentración de tensiones en esas áreas.
- Diseño de herramientas: Es importante diseñar las herramientas con radios de curvatura adecuados que permitan el flujo suave del material sin generar tensiones excesivas que puedan causar fallos. Radios más grandes facilitan el embutido y reducen el riesgo de defectos.
2.3. Grosor de las paredes
En muchas aplicaciones, se requiere que las piezas embutidas tengan paredes de grosor uniforme. Sin embargo, durante el proceso de embutido profundo, es común que el material se estire de manera desigual, lo que puede dar lugar a paredes con diferentes espesores.
- Control del estiramiento: El diseño de la pieza y las herramientas debe permitir que el material se estire de manera controlada para mantener un grosor uniforme de las paredes. En algunos casos, puede ser necesario utilizar procesos adicionales, como el planchado, para garantizar la uniformidad.
3. Lubricación
La lubricación juega un papel crucial en el embutido profundo, ya que reduce la fricción entre la lámina y las herramientas (matriz y punzón). La fricción excesiva puede dificultar el flujo del material, provocar desgaste de las herramientas y generar defectos como arrugas, desgarrones o incluso fracturas en el material.
3.1. Tipos de lubricantes
Existen varios tipos de lubricantes que pueden utilizarse en el embutido profundo, y la elección del lubricante adecuado depende del tipo de material, las condiciones de operación y los requisitos de la pieza final. Entre los lubricantes más comunes se incluyen:
- Aceites minerales: Son los lubricantes más utilizados debido a su capacidad para reducir la fricción y proteger las herramientas del desgaste.
- Grasas y ceras: Son útiles en aplicaciones donde se requiere una lubricación más intensa, especialmente en materiales más duros o en piezas con geometrías complejas.
- Lubricantes de base acuosa: Estos lubricantes son más respetuosos con el medio ambiente y pueden ser utilizados en procesos de embutido que requieran bajas temperaturas.
3.2. Aplicación de lubricantes
El método de aplicación del lubricante también es importante para garantizar una distribución uniforme y evitar problemas durante el proceso.
- Aplicación manual o automática: En la producción en masa, los lubricantes generalmente se aplican de manera automática para asegurar que todas las piezas reciban la misma cantidad de lubricante. En operaciones más pequeñas, la lubricación puede realizarse de forma manual, pero esto puede aumentar la variabilidad en la calidad de la pieza.
- Puntos críticos de lubricación: Los lubricantes deben aplicarse de manera uniforme en todas las áreas donde el material entra en contacto con las herramientas, especialmente en las zonas de mayor fricción, como los bordes del punzón y la matriz.
4. Parámetros del proceso
Los parámetros operativos como la fuerza de embutido, la velocidad de embutido y la presión de sujeción son críticos para garantizar que el embutido profundo se realice correctamente sin generar defectos. Estos parámetros deben ajustarse cuidadosamente en función del material, la geometría de la pieza y el diseño de las herramientas.
4.1. Fuerza de embutido
La fuerza de embutido es la cantidad de presión que el punzón ejerce sobre la lámina metálica para deformarla y hacerla entrar en la cavidad de la matriz. Esta fuerza debe ser suficiente para deformar el material, pero no tan alta como para generar fallos.
- Distribución de la fuerza: La fuerza debe distribuirse de manera uniforme para evitar tensiones localizadas que puedan provocar defectos como grietas o fracturas. Un punzón mal alineado o una matriz mal diseñada pueden generar concentraciones de tensiones en áreas específicas.
- Ajuste de la fuerza: La fuerza de embutido debe ajustarse de acuerdo con el grosor del material, la profundidad de la pieza y el tipo de material. Materiales más duros, como el acero inoxidable, requieren mayores fuerzas de embutido, mientras que materiales más blandos, como el aluminio, requieren menos.
4.2. Velocidad de embutido
La velocidad de embutido es la velocidad a la que el punzón desciende y deforma el material. Si el punzón se mueve demasiado rápido, puede generar tensiones excesivas en el material, lo que aumenta el riesgo de fracturas. Si el punzón se mueve demasiado lento, el proceso puede volverse ineficiente y aumentar el desgaste de las herramientas.
- Velocidad óptima: La velocidad óptima depende del material utilizado y la complejidad de la pieza. Generalmente, se prefiere una velocidad moderada que permita un flujo uniforme del material sin generar tensiones excesivas.
- Efectos de la velocidad: Una velocidad demasiado alta puede provocar fracturas o desgarrones en el material, mientras que una velocidad demasiado baja puede causar arrugas o adherencia del material a las herramientas.
4.3. Presión del anillo de sujeción
El anillo de sujeción se utiliza para mantener el material en su lugar y evitar que se desplace o se arrugue durante el proceso de embutido. La cantidad de presión aplicada por el anillo debe ajustarse cuidadosamente para controlar el flujo del material hacia la matriz.
- Insuficiente presión: Si la presión del anillo de sujeción es demasiado baja, el material puede moverse o arrugarse durante el proceso, lo que resulta en piezas defectuosas.
- Exceso de presión: Si la presión es demasiado alta, puede dificultar el flujo del material hacia la cavidad de la matriz, lo que genera tensiones excesivas y aumenta el riesgo de fracturas.
5. Condiciones de la herramienta
El diseño y el estado de las herramientas (matriz, punzón y anillo de sujeción) tienen un impacto directo en la calidad del embutido profundo. Las herramientas deben estar bien diseñadas, fabricadas con materiales de alta resistencia y bien mantenidas para garantizar un proceso de alta calidad.
5.1. Diseño de la matriz
El diseño de la matriz es fundamental para garantizar que el material fluya correctamente hacia la cavidad y tome la forma deseada sin generar defectos.
- Radios de curvatura: Los radios de curvatura en la matriz deben diseñarse adecuadamente para permitir que el material fluya sin generar tensiones excesivas que puedan causar fracturas.
- Acabado superficial: El acabado superficial de la matriz también es importante. Las superficies deben ser lisas y libres de imperfecciones para minimizar la fricción y permitir un estiramiento uniforme del material.
5.2. Desgaste de herramientas
El desgaste de las herramientas es inevitable en el embutido profundo debido a las altas fuerzas y fricción involucradas. Sin embargo, un mantenimiento regular y la sustitución oportuna de herramientas desgastadas es crucial para evitar problemas.
- Revisión periódica: Es necesario realizar inspecciones periódicas de las herramientas para detectar desgaste o daño. Las herramientas desgastadas pueden generar piezas con defectos, como arrugas o fracturas, y aumentar el riesgo de fallos en el proceso.
- Materiales de alta resistencia: Las herramientas deben fabricarse con materiales de alta resistencia, como acero endurecido o carburo de tungsteno, para prolongar su vida útil y resistir el desgaste causado por las altas presiones y la fricción.
6. Condiciones ambientales
Las condiciones ambientales durante el embutido profundo también pueden afectar el éxito del proceso, especialmente en aplicaciones que implican materiales sensibles a la temperatura o en ambientes donde las temperaturas fluctúan considerablemente.
6.1. Temperatura
En algunos casos, puede ser beneficioso realizar el embutido en caliente, especialmente cuando se trabaja con materiales duros o que son difíciles de deformar a temperatura ambiente. El calentamiento del material aumenta su ductilidad y facilita el proceso de deformación.
- Materiales que requieren embutido en caliente: Materiales como el acero inoxidable y algunas aleaciones de titanio pueden requerir calentamiento previo para facilitar el embutido y reducir el riesgo de fracturas.
- Control de temperatura: Es importante controlar la temperatura de manera precisa, ya que el exceso de calor puede debilitar el material, mientras que un calor insuficiente puede dificultar la deformación.
6.2. Humedad y limpieza
El control de la humedad y la limpieza en el entorno de trabajo es importante para evitar que los lubricantes o el material se contaminen. La presencia de contaminantes en la superficie del material o en las herramientas puede aumentar la fricción y afectar la calidad del embutido.
- Limpieza regular: Las superficies de las herramientas y las láminas deben mantenerse limpias y libres de polvo, residuos de lubricante o partículas metálicas para evitar defectos en la pieza final.
Conclusión
El embutido profundo es un proceso que involucra múltiples factores interrelacionados que deben controlarse con precisión para garantizar el éxito del proceso. Desde las propiedades del material y la geometría de la pieza, hasta la lubricación, los parámetros del proceso y el estado de las herramientas, cada uno de estos factores tiene un impacto significativo en la calidad de la pieza final y la eficiencia de la producción. Un control cuidadoso y un mantenimiento adecuado de todas las variables pueden ayudar a evitar defectos como arrugas, grietas y desgarrones, y garantizar un proceso de embutido profundo eficiente y de alta calidad.
Defectos comunes en el embutido profundo y cómo evitarlos
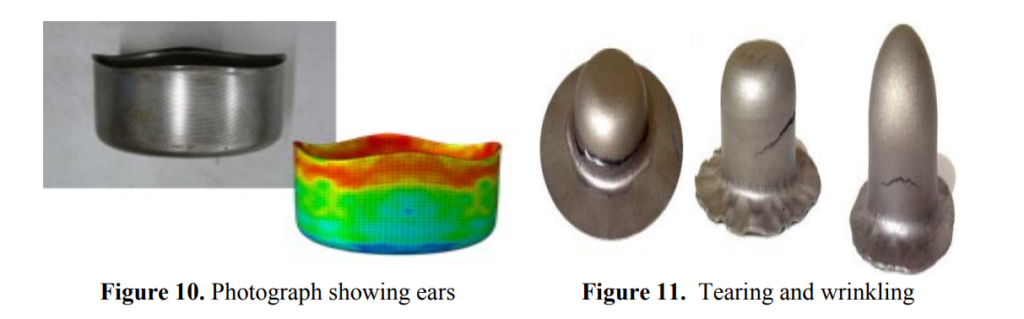
El embutido profundo es un proceso de conformado de metales altamente eficiente, pero debido a su complejidad, pueden surgir varios defectos que afectan la calidad de las piezas producidas. Estos defectos se originan por una combinación de factores como la selección inadecuada del material, un mal diseño de herramientas, parámetros de proceso incorrectos o una lubricación insuficiente.
A continuación, se describen los defectos más comunes que se presentan en el embutido profundo, junto con las causas principales y las estrategias para evitarlos.
1. Arrugas
Las arrugas son uno de los defectos más comunes en el embutido profundo, y aparecen cuando el material metálico se comprime y se acumula en zonas específicas, formando pliegues en la superficie. Las arrugas suelen formarse en las áreas donde el material se somete a compresión durante el embutido, particularmente cerca de los bordes o las esquinas de la pieza.
1.1. Causas de las arrugas
- Insuficiente presión del anillo de sujeción: Si el anillo de sujeción no aplica suficiente presión sobre la lámina, el material puede deslizarse hacia la cavidad de la matriz de manera no controlada, lo que genera acumulaciones de material que forman arrugas.
- Material demasiado delgado: Las láminas más delgadas tienen mayor tendencia a arrugarse, ya que el material se deforma más fácilmente bajo presión, especialmente cuando no hay suficiente sujeción.
- Diseño inadecuado de la matriz: Si el diseño de la matriz tiene radios de curvatura demasiado pequeños o formas que no permiten un estiramiento adecuado del material, las arrugas pueden formarse debido a la acumulación de material en ciertas áreas.
- Fricción excesiva: Si no se utiliza suficiente lubricación, la fricción entre el material y las herramientas puede impedir el flujo suave del metal, lo que provoca la formación de arrugas.
1.2. Cómo evitar las arrugas
- Ajustar la presión del anillo de sujeción: Aumentar la presión del anillo de sujeción ayuda a controlar mejor el flujo del material hacia la cavidad de la matriz. Es importante ajustar esta presión en función del grosor y las propiedades del material.
- Aumentar el grosor de la lámina: En algunos casos, seleccionar una lámina más gruesa puede reducir la tendencia a arrugarse, ya que el material más grueso es más resistente a las deformaciones indeseadas.
- Optimizar el diseño de la matriz: Rediseñar la matriz para proporcionar radios de curvatura más amplios y evitar zonas de acumulación de material puede prevenir la formación de arrugas.
- Utilizar lubricación adecuada: Asegurarse de que la fricción se minimiza mediante la aplicación uniforme de lubricantes ayudará a que el material fluya de manera suave y controlada.
2. Grietas y fracturas
Las grietas y fracturas son fallos graves que ocurren cuando el material no puede soportar las tensiones generadas durante el embutido profundo. Estos defectos suelen aparecer en áreas sometidas a estiramiento excesivo, como los radios pequeños o las esquinas de la pieza.
2.1. Causas de las grietas y fracturas
- Exceso de fuerza de embutido: Si la fuerza aplicada por el punzón es demasiado alta, el material puede estirarse más allá de su límite elástico, lo que genera grietas o fracturas.
- Material de baja ductilidad: Los materiales con baja ductilidad son más propensos a fracturarse durante el embutido profundo. Materiales frágiles o mal seleccionados no pueden deformarse plásticamente sin romperse.
- Radios de curvatura demasiado pequeños: Los radios de curvatura pequeños generan concentraciones de tensión que incrementan el riesgo de fracturas, ya que el material se estira de manera no uniforme en estas áreas.
- Fricción insuficiente: Una lubricación deficiente puede causar que el material se adhiera a las herramientas, lo que genera una tensión adicional que puede provocar grietas.
2.2. Cómo evitar las grietas y fracturas
- Reducir la fuerza de embutido: Ajustar la fuerza de embutido para que sea lo suficientemente alta como para deformar el material, pero no tan elevada que provoque tensiones excesivas, puede prevenir las fracturas.
- Seleccionar materiales adecuados: Utilizar materiales con alta ductilidad, como aceros de baja aleación, aluminio o cobre, puede reducir la probabilidad de grietas. Además, es importante verificar la dirección del laminado, ya que el comportamiento de deformación varía según la orientación de los granos.
- Aumentar los radios de curvatura: Rediseñar las herramientas para incluir radios más grandes reduce las concentraciones de tensiones en las esquinas y bordes, lo que previene fracturas.
- Aumentar la lubricación: Asegurarse de que el material esté bien lubricado permite un flujo más suave hacia la cavidad de la matriz, lo que reduce la fricción y las tensiones que pueden causar grietas.
3. Adelgazamiento excesivo de las paredes
El adelgazamiento de las paredes ocurre cuando el material se estira de manera desigual durante el embutido profundo, lo que provoca que las paredes de la pieza resultante sean más delgadas de lo especificado. Este defecto puede comprometer la resistencia estructural de la pieza y provocar fallos durante su uso.
3.1. Causas del adelgazamiento de las paredes
- Estiramiento excesivo del material: Durante el embutido, el material se estira para conformarse a la cavidad de la matriz. Si este estiramiento no está bien controlado, el material puede adelgazarse en ciertas áreas, especialmente en piezas profundas o con geometrías complejas.
- Velocidad de embutido demasiado alta: Cuando el punzón se mueve a una velocidad muy alta, el material puede estirarse de manera desigual, provocando adelgazamiento en las paredes.
- Diseño inadecuado de la matriz: Si la matriz no está diseñada correctamente para distribuir uniformemente las fuerzas de deformación, el material puede fluir de manera no uniforme, lo que genera adelgazamiento localizado en las paredes de la pieza.
3.2. Cómo evitar el adelgazamiento de las paredes
- Controlar el estiramiento: Ajustar la fuerza y velocidad del punzón puede ayudar a controlar el estiramiento del material y evitar que las paredes se adelgacen en exceso. En algunos casos, es necesario realizar el proceso en varias etapas para evitar un estiramiento excesivo.
- Reducir la velocidad de embutido: Una velocidad de embutido más baja permite que el material se estire de manera más controlada, evitando que se adelgace en áreas específicas.
- Optimizar el diseño de la matriz: El diseño de la matriz debe permitir que el material se deforme de manera uniforme, minimizando las áreas donde se pueda concentrar el estiramiento. En algunos casos, puede ser útil emplear matrices de planchado para garantizar un grosor uniforme de las paredes.
4. Arrastre de material (tirones)
El arrastre de material o los tirones ocurren cuando el material se adhiere a las herramientas, lo que genera marcas o rayas profundas en la superficie de la pieza. Este defecto es más común cuando hay fricción excesiva entre la lámina y las herramientas.
4.1. Causas del arrastre de material
- Fricción alta entre las herramientas y el material: La fricción excesiva puede hacer que el material se adhiera a las superficies de la matriz o el punzón, lo que provoca marcas en la superficie del material a medida que se deforma.
- Lubricación insuficiente o inadecuada: La falta de lubricación o el uso de un lubricante inapropiado puede aumentar la fricción y provocar arrastre de material.
- Desgaste de las herramientas: Las herramientas desgastadas o con superficies ásperas incrementan la fricción y causan tirones en el material.
4.2. Cómo evitar el arrastre de material
- Aplicar suficiente lubricante: Utilizar un lubricante adecuado y asegurarse de que se aplique de manera uniforme en todas las áreas de contacto entre la lámina y las herramientas puede reducir la fricción y prevenir el arrastre de material.
- Mejorar el acabado de las herramientas: Las herramientas deben tener un acabado superficial liso para minimizar la fricción. Es fundamental revisar regularmente las herramientas y pulirlas cuando sea necesario.
- Reducir la fricción: Ajustar los parámetros del proceso para reducir la fricción entre la lámina y las herramientas, como la velocidad de embutido o la presión del anillo de sujeción, puede ayudar a evitar los tirones.
5. Desgarros
Los desgarros son defectos graves que ocurren cuando el material se rompe debido a tensiones excesivas. Estos fallos pueden hacer que la pieza sea inservible, y en algunos casos, pueden dañar las herramientas si no se detectan a tiempo.
5.1. Causas de los desgarros
- Exceso de tensión en el material: Si el material se somete a tensiones demasiado altas durante el embutido, es probable que se desgarre, especialmente si el material no tiene suficiente ductilidad para soportar la deformación.
- Material de baja calidad o frágil: Los materiales con impurezas o baja ductilidad son más propensos a desgarrarse durante el embutido.
- Matriz o punzón defectuosos: Las herramientas mal diseñadas o dañadas pueden generar puntos de tensión que provocan desgarros en el material.
5.2. Cómo evitar los desgarros
- Reducir la fuerza de embutido: Ajustar la fuerza de embutido para evitar tensiones excesivas en el material puede reducir la probabilidad de desgarros. Es importante equilibrar la fuerza aplicada con las propiedades del material.
- Seleccionar materiales de mayor calidad: Utilizar materiales libres de impurezas y con alta ductilidad ayuda a prevenir desgarros. En algunos casos, puede ser necesario realizar tratamientos térmicos o seleccionar aleaciones más adecuadas.
- Revisar y optimizar las herramientas: Asegurarse de que las herramientas estén en buen estado, con un diseño adecuado que distribuya las tensiones de manera uniforme, es clave para evitar desgarros.
6. Muescas o marcas en los bordes
Las muescas o marcas en los bordes de la pieza suelen aparecer cuando el material se corta o daña durante la deformación. Estas imperfecciones pueden afectar tanto la estética como la funcionalidad de la pieza.
6.1. Causas de las muescas en los bordes
- Exceso de fuerza de embutido: Cuando el punzón aplica demasiada fuerza, los bordes del material pueden dañarse o cortarse, especialmente en piezas con radios de curvatura pequeños.
- Diseño de herramientas con bordes afilados: Los bordes afilados en las herramientas, especialmente en la matriz, pueden cortar el material durante el embutido.
- Desgaste de las herramientas: Las herramientas desgastadas o dañadas pueden dejar marcas en los bordes del material.
6.2. Cómo evitar las muescas en los bordes
- Reducir la fuerza de embutido: Ajustar la fuerza de embutido para evitar el exceso de presión en los bordes del material puede ayudar a prevenir muescas y cortes.
- Redondear los bordes de las herramientas: Rediseñar las herramientas para incluir bordes redondeados en lugar de afilados puede reducir el riesgo de dañar el material durante el proceso.
- Mantener las herramientas en buen estado: Revisar y mantener regularmente las herramientas para evitar que se desgasten o dañen ayudará a prevenir la formación de muescas.
Conclusión
El embutido profundo es un proceso altamente eficiente y versátil para fabricar piezas metálicas complejas, pero también puede ser susceptible a una variedad de defectos. Para lograr un proceso exitoso y producir piezas de alta calidad, es fundamental controlar cuidadosamente los parámetros de embutido, optimizar el diseño de las herramientas, utilizar materiales adecuados y mantener una lubricación adecuada. Con un enfoque preventivo y proactivo, es posible minimizar la aparición de defectos como arrugas, grietas, adelgazamiento desigual, tirones y desgarros, garantizando un proceso de embutido profundo más eficiente y confiable.
Técnicas complementarias en el embutido profundo
El embutido profundo es un proceso eficiente para la fabricación de piezas huecas y de formas complejas a partir de láminas metálicas, pero puede no ser suficiente por sí solo para lograr ciertas características o formas finales. Por esta razón, a menudo se utilizan técnicas complementarias para optimizar el proceso, mejorar la calidad de las piezas, corregir defectos y permitir la fabricación de geometrías más complejas.
A continuación, se describen algunas de las técnicas complementarias más comunes que se utilizan junto con el embutido profundo para mejorar los resultados y ampliar sus aplicaciones industriales.
1. Recalcado
El recalcado es una técnica que se utiliza para aumentar el grosor o la densidad de una pieza embutida en áreas específicas, mejorando así su resistencia mecánica y su capacidad para soportar cargas. Este proceso es particularmente útil cuando se necesitan refuerzos localizados en piezas embutidas que estarán sometidas a tensiones elevadas.
1.1. ¿Cómo funciona el recalcado?
El recalcado implica la compresión del material después del embutido, mediante la aplicación de una fuerza adicional en áreas seleccionadas de la pieza. Este proceso se realiza con el fin de aumentar el grosor en ciertas zonas, generalmente las más críticas desde el punto de vista estructural.
- Compresión localizada: En lugar de estirar o doblar el material, el recalcado aumenta la densidad del metal al comprimirlo, lo que incrementa su resistencia sin cambiar significativamente su forma exterior.
- Aplicaciones: Se utiliza principalmente para fabricar componentes como pistones, bridas, y partes de motores, donde se requiere mayor resistencia en ciertas zonas para soportar cargas o impactos repetitivos.
1.2. Beneficios del recalcado
- Mayor resistencia: Aumenta la capacidad de la pieza para soportar cargas o tensiones en áreas críticas.
- Refuerzo de zonas específicas: Permite mejorar la integridad estructural sin aumentar el grosor general de la pieza, lo que contribuye a reducir el peso total del componente.
2. Planchado
El planchado es una técnica utilizada para reducir el grosor de las paredes de una pieza embutida y, al mismo tiempo, mejorar la uniformidad y el acabado superficial. Es especialmente útil en la fabricación de envases metálicos con paredes delgadas y precisas, como las latas de bebidas.
2.1. ¿Cómo funciona el planchado?
El planchado implica pasar la pieza embutida a través de una matriz de reducción, donde se aplica presión controlada para comprimir y estirar el material, lo que reduce su grosor sin comprometer la forma de la pieza.
- Reducción de grosor: Durante el planchado, el material se comprime ligeramente, lo que permite reducir el grosor de las paredes mientras se mantiene o mejora la precisión dimensional.
- Mejora del acabado: El proceso también ayuda a mejorar el acabado superficial de la pieza, eliminando imperfecciones o rugosidades creadas durante el embutido.
2.2. Aplicaciones del planchado
- Producción de latas y envases metálicos: El planchado es esencial para la fabricación de latas de bebidas con paredes delgadas, lo que permite reducir el uso de material y, al mismo tiempo, mejorar la resistencia del envase.
- Componentes electrónicos: También se utiliza en la fabricación de piezas para la industria electrónica, donde se requieren componentes ligeros con paredes uniformes y de alta precisión.
2.3. Beneficios del planchado
- Reducción del peso: Permite reducir el peso de las piezas al disminuir el grosor de las paredes sin comprometer la resistencia.
- Mejora de la calidad: Proporciona un acabado más liso y uniforme, eliminando imperfecciones creadas durante el embutido.
- Consistencia dimensional: Ayuda a mantener una uniformidad en el grosor de las paredes, lo que es crucial para aplicaciones que requieren tolerancias estrictas.
3. Embutición inversa
La embutición inversa es una variación del proceso de embutido profundo que permite fabricar piezas con formas más complejas o con diferentes secciones de diámetro. A diferencia del embutido tradicional, en la embutición inversa, el material se empuja en la dirección opuesta al embutido inicial.
3.1. ¿Cómo funciona la embutición inversa?
En el proceso de embutición inversa, después de una primera etapa de embutido, el punzón o una segunda herramienta aplica fuerza en la dirección contraria para crear una forma compleja o modificar la pieza embutida inicial.
- Modificación de la forma: Permite ajustar el diámetro o la forma de la pieza sin necesidad de usar una nueva lámina de metal. El material que ha sido embutido en una dirección se empuja hacia atrás, creando geometrías más complejas y zonas de diferente diámetro.
- Control del grosor: También se utiliza para mejorar el control sobre el grosor de las paredes y evitar adelgazamientos excesivos.
3.2. Aplicaciones de la embutición inversa
- Producción de recipientes cilíndricos: La embutición inversa es ideal para fabricar recipientes con múltiples diámetros, como tubos de escape, cilindros de gas, o cápsulas.
- Componentes automotrices: Se utiliza en la fabricación de piezas de motores, sistemas de escape y otras partes del automóvil que requieren cambios de diámetro en diferentes zonas de la pieza.
3.3. Beneficios de la embutición inversa
- Mayor flexibilidad: Permite crear formas más complejas sin necesidad de utilizar nuevas láminas metálicas, lo que ahorra material y reduce los costes de producción.
- Control del grosor: La embutición inversa ayuda a mantener el grosor de las paredes y evita el estiramiento excesivo del material.
- Reducción de operaciones: Al permitir múltiples modificaciones en una misma pieza, se pueden reducir los tiempos de producción y los costos de herramientas.
4. Corte posterior al embutido
El corte posterior al embutido es una técnica utilizada para ajustar la forma final de la pieza después de haber completado el embutido. En muchos casos, las piezas embutidas requieren cortes adicionales para eliminar material sobrante o crear características específicas como aberturas, ranuras o orificios.
4.1. ¿Cómo funciona el corte posterior?
Después de que la pieza ha sido embutida, se utiliza una herramienta de corte, que puede ser un troquel, una cizalla o tecnologías avanzadas como el corte por láser o el corte por chorro de agua, para ajustar la forma de la pieza. Este proceso permite crear bordes lisos y precisos o generar agujeros en las áreas deseadas.
- Eliminación de material sobrante: En muchas aplicaciones, el embutido produce un exceso de material que debe eliminarse para dar la forma final. El corte posterior elimina ese material sin afectar la estructura de la pieza.
- Creación de orificios o ranuras: También se utiliza para perforar orificios o crear ranuras en la pieza embutida para cumplir con las especificaciones de diseño.
4.2. Aplicaciones del corte posterior
- Fabricación de componentes electrónicos: En dispositivos electrónicos, el corte posterior se utiliza para crear agujeros y ranuras que permitan la integración de piezas adicionales o cables.
- Automoción: En la fabricación de piezas automotrices, el corte posterior es necesario para dar forma final a componentes como paneles de carrocería, capós y piezas estructurales.
- Recipientes metálicos: Para envases metálicos, como latas de alimentos y bebidas, el corte posterior ajusta el borde del recipiente para mejorar el sellado y eliminar material sobrante.
4.3. Beneficios del corte posterior
- Mayor precisión: Permite ajustar las piezas a las especificaciones exactas después del embutido, lo que mejora la precisión y la calidad del producto final.
- Flexibilidad: Al combinar el embutido con técnicas de corte posterior, es posible producir piezas más complejas y con características detalladas sin necesidad de utilizar herramientas adicionales durante el embutido.
- Mejora del acabado: El corte posterior ayuda a eliminar los bordes ásperos o irregulares generados durante el embutido, mejorando el acabado de las piezas.
5. Recalentamiento o tratamiento térmico
El recalentamiento o tratamiento térmico es una técnica complementaria utilizada para modificar las propiedades mecánicas del material después del embutido profundo. Este proceso es particularmente útil en materiales que se endurecen durante el embutido, lo que puede generar tensiones residuales o deformaciones no deseadas.
5.1. ¿Cómo funciona el recalentamiento?
El recalentamiento implica aplicar calor controlado al material después de haber sido embutido, con el objetivo de relajar las tensiones internas generadas durante el proceso de deformación. También puede utilizarse para reblandecer el material, facilitando las operaciones posteriores, como el recalcado o el planchado.
- Alivio de tensiones: El tratamiento térmico ayuda a eliminar las tensiones residuales que pueden debilitar la pieza o causar deformaciones a largo plazo.
- Mejora de la ductilidad: El recalentamiento puede restaurar la ductilidad del material, permitiendo que se realicen operaciones adicionales sin riesgo de fracturas.
5.2. Aplicaciones del recalentamiento
- Industria automotriz: En la fabricación de componentes estructurales y piezas de carrocería, el recalentamiento es necesario para evitar tensiones que podrían causar grietas o deformaciones a largo plazo.
- Aeronáutica: Los componentes aeroespaciales suelen requerir un tratamiento térmico después del embutido profundo para garantizar que las piezas sean ligeras pero lo suficientemente fuertes para soportar las condiciones extremas de vuelo.
5.3. Beneficios del recalentamiento
- Reducción de tensiones internas: El recalentamiento ayuda a eliminar las tensiones acumuladas durante el embutido, lo que mejora la durabilidad y la estabilidad de la pieza.
- Facilidad para operaciones posteriores: Mejora la ductilidad del material, facilitando operaciones posteriores como el recalcado, corte o embutición inversa sin riesgo de fallos.
Conclusión
El embutido profundo es un proceso versátil y ampliamente utilizado, pero a menudo requiere de técnicas complementarias para lograr piezas de alta calidad con formas complejas o características especiales. Técnicas como el recalcado, el planchado, la embutición inversa, el corte posterior y el recalentamiento permiten optimizar el proceso de embutido profundo, mejorar las propiedades mecánicas de las piezas y garantizar su precisión y funcionalidad. Estas técnicas, cuando se aplican correctamente, amplían las posibilidades del embutido profundo y mejoran su eficiencia en diversas industrias.
Rebordeadora de lámina: Descripción, funcionamiento y aplicaciones
Una rebordeadora de lámina es una máquina especializada que se utiliza para crear bordes curvados o doblados en láminas de metal. Este proceso es esencial para una amplia gama de industrias, ya que permite mejorar la resistencia estructural de las piezas, eliminar bordes afilados, y facilitar el ensamblaje de componentes. Las rebordeadoras de lámina son utilizadas en sectores como el automotriz, aeroespacial, electrodomésticos, y envases metálicos, entre otros.
A continuación, se detalla cómo funcionan estas máquinas, sus componentes principales, las técnicas que emplean y las aplicaciones más comunes en la industria.
¿Qué es una rebordeadora de lámina?
Una rebordeadora de lámina es una máquina diseñada para curvar o doblar los bordes de una lámina metálica, formando un reborde que puede servir para reforzar la pieza, mejorar su apariencia o facilitar su ensamblaje con otras partes. El reborde puede ser simplemente un doblez, una curvatura o un enrollado del borde, dependiendo de la aplicación y el tipo de máquina utilizada.
El rebordear no solo refuerza los bordes de la pieza, sino que también mejora la seguridad, eliminando bordes afilados que podrían causar cortes durante el manejo. Asimismo, se utiliza para crear un borde estético o funcional, como en envases y recipientes metálicos.
1.1. Tipos de rebordeadoras de lámina
Existen varios tipos de rebordeadoras de lámina, que varían en cuanto a su diseño y método de operación. Los principales tipos incluyen:
- Rebordeadoras manuales:
- Son máquinas de operación manual, donde el operario ajusta y dobla los bordes de las láminas. Son más comunes en trabajos pequeños o en talleres donde no se requiere producción en masa.
- Rebordeadoras automáticas:
- Estas máquinas están equipadas con sistemas motorizados o hidráulicos para realizar el rebordeado automáticamente. Son más eficientes para la producción en serie y se utilizan en fábricas o plantas industriales.
- Rebordeadoras CNC:
- Las rebordeadoras controladas numéricamente (CNC) permiten realizar rebordes con un alto grado de precisión. Pueden programarse para realizar una amplia gama de bordes en diferentes tipos y grosores de láminas, lo que las hace ideales para producciones a gran escala que requieren alta precisión y consistencia.
2. Componentes principales de una rebordeadora de lámina
Una rebordeadora de lámina se compone de varios elementos clave que permiten ejecutar el proceso de manera eficiente. A continuación, se describen los componentes más importantes:
2.1. Rodillos de rebordeado
Los rodillos son la parte esencial de la máquina, ya que son los encargados de doblar o curvar el borde de la lámina. Los rodillos están diseñados con diferentes perfiles, según el tipo de reborde que se necesite (simple, enrollado, curvado, etc.).
- Rodillos ajustables: En muchas máquinas, los rodillos son ajustables para permitir la creación de diferentes tipos de rebordes en una amplia variedad de espesores y materiales.
- Material de los rodillos: Los rodillos suelen estar fabricados en acero endurecido o materiales de alta resistencia, ya que deben soportar altas fuerzas y resistir el desgaste.
2.2. Sistema de sujeción
El sistema de sujeción mantiene la lámina en su lugar durante el proceso de rebordeado, evitando que se mueva o se deforme de manera incontrolada.
- Sujeción ajustable: En muchas rebordeadoras, este sistema puede ajustarse según el tamaño y el grosor de la lámina, asegurando un rebordeado preciso y uniforme.
2.3. Motor o sistema de accionamiento
El motor es el responsable de accionar los rodillos para que realicen el proceso de rebordeado. En las máquinas automáticas y CNC, el motor controla la velocidad y la presión aplicada durante el proceso.
- Motores eléctricos o hidráulicos: Dependiendo del tipo de máquina, el motor puede ser eléctrico, hidráulico o neumático, y se ajusta según las necesidades de la producción.
2.4. Panel de control
El panel de control permite al operario ajustar los parámetros de operación de la máquina, como la velocidad de los rodillos, la presión aplicada y el tipo de reborde que se desea crear.
- Control CNC: En las máquinas avanzadas, el panel de control puede ser un sistema CNC que permite programar la máquina para realizar rebordes complejos de manera automática y precisa.
3. Proceso de funcionamiento de una rebordeadora de lámina
El funcionamiento de una rebordeadora de lámina varía según el tipo de máquina, pero los pasos básicos del proceso son los siguientes:
3.1. Colocación de la lámina
Primero, la lámina metálica se coloca en la máquina, asegurándola con el sistema de sujeción. La correcta colocación y sujeción de la lámina son esenciales para garantizar que el reborde sea uniforme y que no se produzcan deformaciones no deseadas.
3.2. Ajuste de los parámetros
El operario ajusta los parámetros de la máquina, como el tipo de reborde que se va a realizar, el grosor de la lámina y la presión que los rodillos aplicarán. En las máquinas automáticas o CNC, estos parámetros pueden preconfigurarse para optimizar el proceso.
3.3. Rebordeado de la lámina
Una vez ajustados los parámetros, la máquina inicia el proceso de rebordeado, en el cual los rodillos aplican presión sobre el borde de la lámina para doblarla o curvarla según sea necesario.
3.4. Verificación del reborde
Al finalizar el proceso, la lámina se inspecciona para verificar la calidad del reborde. En muchas industrias, la calidad del reborde es crucial, ya que debe cumplir con especificaciones precisas para asegurar que la pieza funcione correctamente.
4. Aplicaciones industriales de la rebordeadora de lámina
Las rebordeadoras de lámina tienen una amplia gama de aplicaciones industriales, ya que el rebordeado es un proceso crucial en la fabricación de componentes metálicos para diversas industrias.
4.1. Industria automotriz
En la industria automotriz, las rebordeadoras de lámina se utilizan para crear bordes en paneles de carrocería, puertas, capós y otras piezas metálicas. Estos bordes mejoran la resistencia estructural de las piezas, eliminan bordes afilados y permiten un mejor ensamblaje de las partes del vehículo.
4.2. Industria de envases metálicos
El sector de envases metálicos utiliza rebordeadoras para fabricar latas de alimentos, recipientes de bebidas y otros envases metálicos que requieren bordes redondeados para mejorar su resistencia, evitar el riesgo de cortes y facilitar el sellado.
4.3. Electrodomésticos
En la fabricación de electrodomésticos, como lavadoras, secadoras y refrigeradores, las rebordeadoras se utilizan para reforzar las carcasas metálicas y mejorar tanto la durabilidad como la seguridad de los productos.
4.4. Industria aeroespacial
En la industria aeroespacial, las rebordeadoras son esenciales para fabricar piezas estructurales ligeras pero resistentes, como componentes de fuselaje y paneles de avión, que deben soportar grandes tensiones sin añadir peso innecesario.
4.5. Fabricación de muebles metálicos
En la producción de muebles metálicos, las rebordeadoras se emplean para crear bordes estéticos y funcionales en piezas de metal que se ensamblan en sillas, mesas y estructuras.
5. Beneficios del uso de una rebordeadora de lámina
El uso de una rebordeadora de lámina ofrece numerosas ventajas en términos de calidad del producto, seguridad y eficiencia en la producción. A continuación, se destacan algunos de los principales beneficios:
5.1. Mejora de la resistencia estructural
El rebordeado refuerza los bordes de las piezas metálicas, lo que aumenta su resistencia a la deformación y a las tensiones mecánicas. Esto es crucial en aplicaciones industriales donde los componentes metálicos están sometidos a cargas o vibraciones constantes.
5.2. Eliminación de bordes afilados
Al curvar o redondear los bordes de la lámina, se eliminan los bordes afilados que podrían causar accidentes o cortes durante el manejo o el ensamblaje de las piezas.
5.3. Mejora del ensamblaje
Los bordes doblados o curvados facilitan el ensamblaje de las piezas metálicas con otras partes, ya que permiten una mejor alineación y un ajuste más preciso.
5.4. Estética mejorada
En muchas aplicaciones, como en la fabricación de muebles metálicos o electrodomésticos, el rebordeado mejora el acabado estético de las piezas, lo que es un factor importante para productos de consumo.
5.5. Eficiencia en la producción
Las máquinas automáticas y CNC aumentan la eficiencia en la producción, ya que permiten realizar el rebordeado de manera rápida y precisa, reduciendo la necesidad de intervención manual y el riesgo de errores.
Conclusión
Las rebordeadoras de lámina son herramientas indispensables en la fabricación de componentes metálicos en diversas industrias. Al permitir la creación de bordes curvados o doblados, mejoran la resistencia, la seguridad y la estética de las piezas, facilitando al mismo tiempo su ensamblaje en estructuras más grandes. Gracias a la versatilidad de estos equipos, las rebordeadoras pueden adaptarse a una amplia gama de aplicaciones, desde la fabricación de automóviles hasta la producción de envases metálicos o electrodomésticos.
Rebordeadora de lámina: Descripción, funcionamiento y aplicaciones
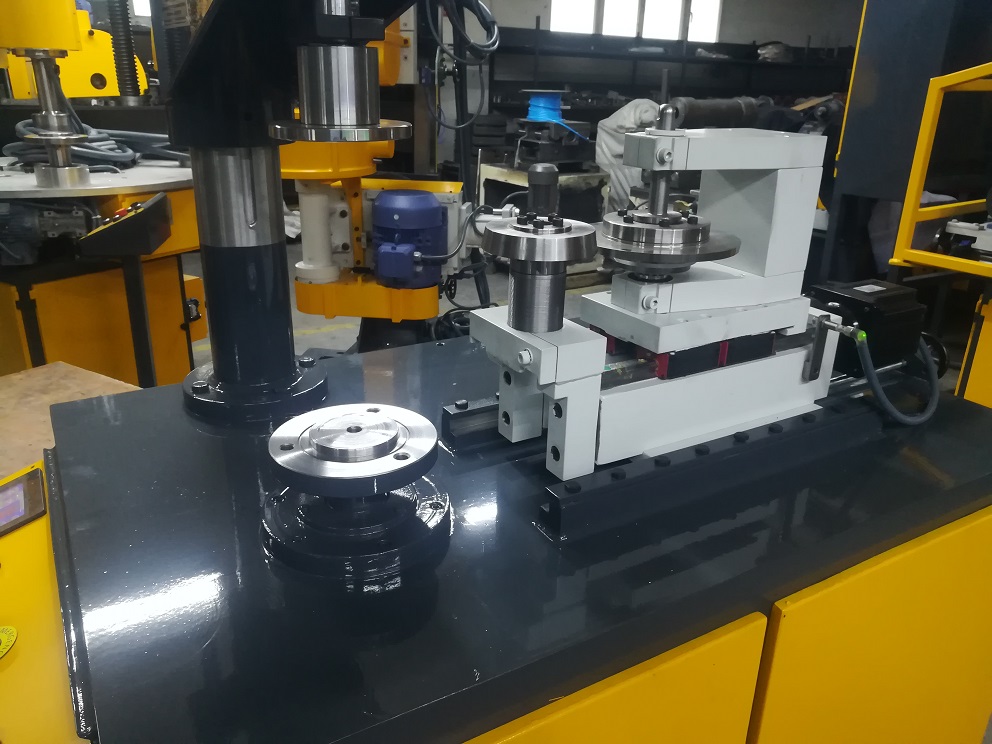
El procesamiento de láminas metálicas es un pilar fundamental en la fabricación de componentes en numerosas industrias, como la automotriz, aeroespacial, electrodomésticos, envases metálicos y muebles. Dentro de este procesamiento, el rebordeado es una técnica clave que se emplea para modificar los bordes de las láminas, mejorando su resistencia estructural, seguridad y funcionalidad. La rebordeadora de lámina es la máquina especializada para llevar a cabo este proceso, permitiendo curvar, doblar o enrollar los bordes de las láminas de metal de manera precisa.
En este documento, se abordará una descripción detallada de la rebordeadora de lámina, su funcionamiento, los componentes principales, las técnicas de operación y las aplicaciones más comunes. Este análisis permitirá comprender el impacto y las ventajas del rebordeado en la producción industrial.
1. Descripción de la rebordeadora de lámina
La rebordeadora de lámina es una máquina que se utiliza para doblar o curvar los bordes de una lámina metálica, generalmente con el fin de reforzar los bordes, eliminar irregularidades o preparar las piezas para su posterior ensamblaje. El rebordeado puede aplicarse a una amplia gama de materiales metálicos, incluyendo acero inoxidable, aluminio, latón, y otros tipos de metales, lo que convierte a la rebordeadora en una herramienta versátil para diversas aplicaciones industriales.
El proceso de rebordeado permite:
- Crear bordes redondeados o doblados que eliminan peligros asociados con bordes afilados, mejorando la seguridad tanto en el uso como en el manejo de las piezas.
- Refuerza la estructura de las piezas, ya que el material adicional en el borde proporciona resistencia adicional a las tensiones y deformaciones mecánicas.
- Facilita el ensamblaje con otras piezas, ya que los bordes doblados o curvados pueden mejorar el encaje y la alineación durante el proceso de montaje.
El uso de rebordeadoras de lámina está ampliamente extendido en sectores donde la seguridad, la precisión y la eficiencia en la producción son esenciales, tales como la industria automotriz, la fabricación de envases, electrodomésticos, y la industria aeroespacial.
2. Funcionamiento de una rebordeadora de lámina
El funcionamiento de una rebordeadora de lámina puede variar ligeramente dependiendo del tipo de máquina utilizada, ya sea manual, automática o CNC. Sin embargo, el principio básico es el mismo: la lámina metálica se coloca en la máquina, y a través de rodillos, fuerza controlada o movimientos mecanizados, el borde de la lámina es doblado o curvado para lograr el reborde deseado.
2.1. Proceso básico de rebordeado
El proceso de rebordeado de láminas metálicas sigue generalmente estos pasos:
- Colocación de la lámina: La lámina metálica se coloca sobre la mesa de trabajo o en el sistema de sujeción de la máquina. El borde que se va a trabajar debe estar alineado correctamente con los rodillos o herramientas de la rebordeadora.
- Ajuste de los parámetros: Dependiendo de la máquina, el operador puede ajustar varios parámetros, como la velocidad de los rodillos, la presión aplicada, el ángulo de curvatura y el tipo de reborde que se desea crear. En las rebordeadoras CNC, estos ajustes son automatizados y se introducen mediante un sistema de control numérico.
- Accionamiento de la máquina: Una vez ajustados los parámetros, la máquina comienza a operar, aplicando presión o movimiento rotacional mediante los rodillos sobre el borde de la lámina para doblarlo o curvarlo.
- Revisión de la pieza: Al final del proceso, la pieza es revisada para garantizar que el reborde cumple con las especificaciones necesarias en cuanto a ángulo, grosor y acabado superficial.
2.2. Tipos de rebordeadoras de lámina
Existen diferentes tipos de rebordeadoras de lámina diseñadas para satisfacer distintos niveles de producción y requerimientos de precisión:
- Rebordeadoras manuales: Estas máquinas son operadas de manera manual por un operario que controla directamente el movimiento y la presión de los rodillos. Son adecuadas para trabajos pequeños o en talleres donde no se requiere una gran capacidad de producción. A menudo se utilizan en aplicaciones personalizadas o en la reparación de piezas.
- Rebordeadoras automáticas: Equipadas con sistemas motorizados o hidráulicos, las rebordeadoras automáticas realizan el proceso de rebordeado sin intervención manual directa. Este tipo de máquina es ideal para producciones en serie donde la velocidad y la consistencia son esenciales. Las rebordeadoras automáticas están diseñadas para manejar grandes volúmenes de piezas de manera eficiente.
- Rebordeadoras CNC: Son las más avanzadas tecnológicamente, ya que están controladas por CNC (Control Numérico por Computadora), lo que permite programar las operaciones de manera precisa para obtener rebordes consistentes con tolerancias estrictas. Las rebordeadoras CNC son ampliamente utilizadas en la producción en masa de piezas complejas y en industrias que requieren precisión extrema, como la automotriz y la aeroespacial.
2.3. Componentes clave de una rebordeadora de lámina
Una rebordeadora de lámina cuenta con varios componentes que permiten el doblado y curvado del material de manera eficiente:
- Rodillos de rebordeado: Son los elementos clave de la máquina que aplican la presión necesaria para doblar el borde de la lámina. Los rodillos suelen ser ajustables y están diseñados con diferentes perfiles según el tipo de reborde que se quiera obtener.
- Sistema de sujeción: Asegura la lámina en su lugar durante el proceso de rebordeado para evitar que se desplace o deforme de manera incontrolada.
- Motor o accionamiento: El motor, que puede ser eléctrico, hidráulico o neumático, es responsable de accionar los rodillos y aplicar la fuerza necesaria para doblar la lámina.
- Panel de control: En las máquinas automáticas y CNC, el panel de control permite ajustar los parámetros de operación, como la velocidad de los rodillos, la presión aplicada y el tipo de reborde. En las rebordeadoras CNC, el panel de control se utiliza para introducir el programa que guiará la operación.
3. Aplicaciones industriales de la rebordeadora de lámina
El uso de rebordeadoras de lámina está ampliamente extendido en diversas industrias que requieren la producción de piezas metálicas con bordes precisos, seguros y reforzados. A continuación, se describen algunas de las aplicaciones más comunes:
3.1. Industria automotriz
En la industria automotriz, las rebordeadoras de lámina se utilizan para el procesamiento de componentes clave de los paneles de carrocería, puertas, capós, y otras piezas estructurales del vehículo. El rebordeado en estos componentes es esencial no solo para mejorar la resistencia estructural de las piezas, sino también para eliminar bordes afilados, lo que reduce el riesgo de accidentes durante la manipulación y el ensamblaje.
Además, los rebordes en las piezas automotrices permiten un mejor ajuste y alineación durante el ensamblaje del vehículo, lo que mejora la calidad y seguridad del producto final.
3.2. Industria de envases metálicos
El sector de envases metálicos utiliza rebordeadoras de lámina para fabricar recipientes como latas de alimentos y bebidas, entre otros envases. Los rebordes en las latas metálicas son cruciales para garantizar que los bordes no representen un peligro para los consumidores, además de mejorar el sellado y la durabilidad del envase.
En la fabricación de envases, el rebordeado también facilita los procesos de llenado y envasado, ya que los bordes redondeados permiten un ajuste más preciso de las tapas o cierres.
3.3. Electrodomésticos
En la producción de electrodomésticos, como lavadoras, secadoras y refrigeradores, las rebordeadoras se utilizan para reforzar las carcasas metálicas y mejorar la durabilidad de los productos. Los bordes rebordeados en las carcasas también eliminan bordes afilados, lo que mejora la seguridad tanto para los operarios durante la fabricación como para los consumidores.
Los bordes curvados o doblados permiten además un mejor acabado estético en los electrodomésticos, un factor clave para los productos de consumo masivo.
3.4. Industria aeroespacial
En la industria aeroespacial, las rebordeadoras son fundamentales para la fabricación de piezas ligeras pero resistentes, como paneles de fuselaje, cubiertas de motores y componentes estructurales de aeronaves. El rebordeado es una técnica eficaz para reducir el peso de las piezas sin comprometer su integridad estructural, lo que es esencial en las aeronaves para mejorar el rendimiento y la eficiencia del combustible.
Además, los bordes reforzados en piezas aeroespaciales ayudan a soportar las tensiones y vibraciones extremas a las que están sometidas durante el vuelo.
3.5. Fabricación de muebles metálicos
En la fabricación de muebles metálicos, como sillas, mesas y estructuras para oficinas o exteriores, las rebordeadoras de lámina permiten crear bordes suaves y estéticamente agradables. Estos bordes no solo mejoran el aspecto de los muebles, sino que también refuerzan la durabilidad y seguridad del producto, evitando que los usuarios sufran cortes o lesiones debido a bordes afilados.
4. Ventajas del uso de una rebordeadora de lámina
El uso de una rebordeadora de lámina ofrece diversas ventajas, tanto desde el punto de vista de la producción como de la calidad de las piezas. Entre las principales ventajas se destacan las siguientes:
4.1. Mejora de la resistencia estructural
El rebordeado aumenta la resistencia de las piezas al reforzar los bordes, lo que es crucial para componentes que estarán sometidos a tensiones mecánicas o vibraciones. Este aumento en la resistencia es especialmente importante en la fabricación de piezas automotrices, aeroespaciales y electrodomésticos.
4.2. Eliminación de bordes afilados
El proceso de rebordeado elimina los bordes afilados, lo que mejora la seguridad tanto en el manejo de las piezas durante la producción como en el uso del producto final. Este es un factor importante en industrias como la fabricación de envases y muebles, donde los bordes afilados pueden representar un riesgo para los usuarios.
4.3. Mejora del ensamblaje
Los bordes curvados o doblados creados por las rebordeadoras facilitan el ensamblaje de las piezas, ya que permiten una mejor alineación y ajuste con otras partes. Esto es especialmente importante en la producción de automóviles y electrodomésticos, donde el ajuste preciso de las piezas es esencial para garantizar la calidad del producto.
4.4. Eficiencia en la producción
Las máquinas automáticas y CNC permiten realizar el proceso de rebordeado de manera rápida y precisa, lo que reduce los tiempos de producción y aumenta la eficiencia en líneas de producción a gran escala. Además, la automatización minimiza la necesidad de intervención manual, lo que reduce los errores y garantiza una mayor consistencia en las piezas fabricadas.
4.5. Mejora estética
Además de mejorar la funcionalidad, el rebordeado también tiene un impacto positivo en la estética de las piezas. En productos de consumo como muebles metálicos y electrodomésticos, los bordes redondeados y suaves son preferidos tanto por su seguridad como por su aspecto visual.
Conclusión
La rebordeadora de lámina es una máquina clave en el procesamiento de metales, utilizada en diversas industrias para mejorar la resistencia, seguridad y funcionalidad de las piezas metálicas. Ya sea en la fabricación de componentes automotrices, envases metálicos, electrodomésticos, piezas aeroespaciales o muebles metálicos, las rebordeadoras desempeñan un papel crucial en la producción de piezas con bordes seguros, precisos y estéticamente agradables.
Gracias a las diferentes tecnologías disponibles (manuales, automáticas y CNC), las rebordeadoras pueden adaptarse a una amplia gama de aplicaciones industriales, desde trabajos personalizados hasta la producción en masa de piezas de alta precisión. Las ventajas de este proceso, como la mejora en la resistencia estructural, la eliminación de bordes afilados y la optimización del ensamblaje, lo convierten en un componente esencial en las líneas de producción modernas.
¿Qué es una rebordeadora de lámina?
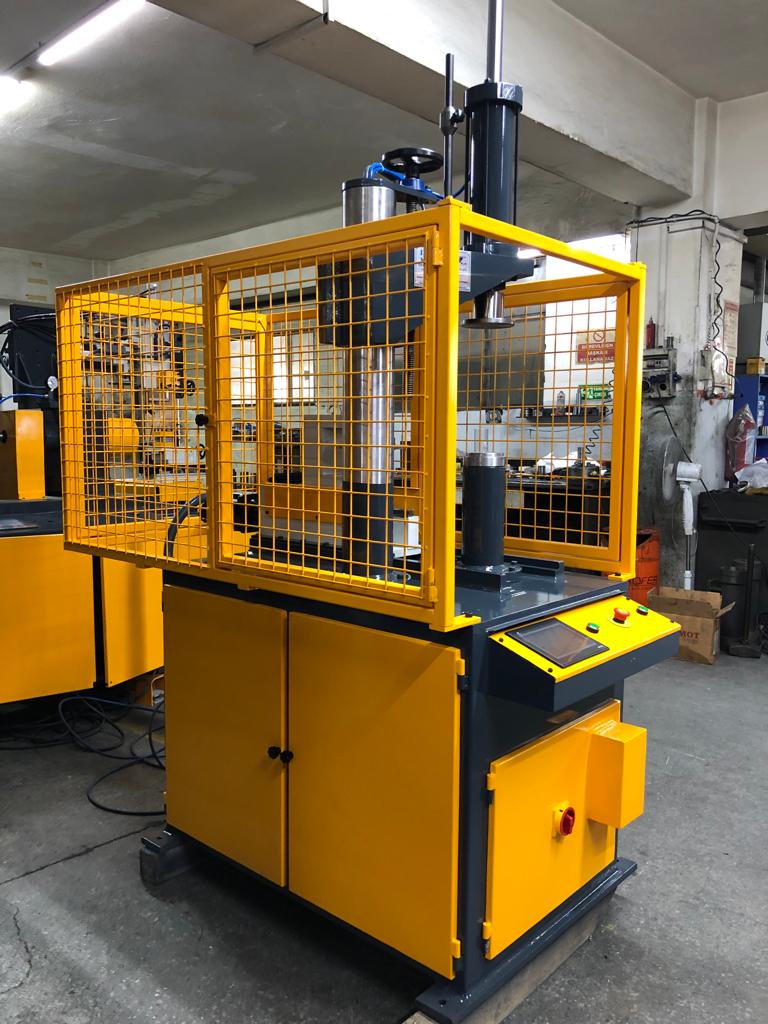
Una rebordeadora de lámina es una máquina industrial especializada en el procesamiento de láminas metálicas que permite crear bordes doblados, curvados o redondeados en los extremos de las piezas metálicas. Este proceso de rebordeado es esencial para mejorar la resistencia estructural de las piezas, eliminar bordes afilados y facilitar su ensamblaje. Las rebordeadoras de lámina se utilizan en una amplia gama de industrias, como la automotriz, aeroespacial, electrodomésticos, envases metálicos, y más.
El rebordeado no solo mejora las propiedades mecánicas de las piezas, sino que también contribuye a la seguridad de los productos, ya que elimina bordes cortantes que podrían causar accidentes durante el uso o el ensamblaje. Además, el proceso mejora la estética de las piezas al proporcionar un acabado más limpio y suave.
A continuación, se presentará una descripción detallada de qué es una rebordeadora de lámina, cómo funciona, los tipos de máquinas existentes, y sus aplicaciones industriales más comunes, así como las ventajas que ofrece este tipo de tecnología en los procesos de fabricación.
1. Descripción general de una rebordeadora de lámina
La rebordeadora de lámina es una máquina diseñada específicamente para realizar el rebordeado de los bordes de láminas metálicas. Las láminas pueden ser de diversos materiales, como acero inoxidable, aluminio, cobre, latón, y otras aleaciones, lo que hace de esta máquina una herramienta muy versátil en la fabricación de componentes metálicos.
El objetivo principal del rebordeado es mejorar las características estructurales y funcionales de las piezas metálicas, logrando que sean más resistentes y seguras para su uso en diversos productos y sistemas. Al aplicar un reborde, se logra que los bordes de las láminas sean menos propensos a desgastes, deformaciones o cortes accidentales, lo que es esencial en aplicaciones industriales y productos de consumo.
En términos simples, una rebordeadora toma una lámina metálica con bordes lisos o afilados y los dobla o enrolla hacia adentro para formar un borde más grueso y redondeado. Este borde puede ser utilizado para reforzar la pieza, mejorar su apariencia estética o para facilitar su ensamblaje con otras partes.
1.1. Funciones principales de la rebordeadora de lámina
Las rebordeadoras de lámina permiten realizar varias funciones clave en la fabricación de piezas metálicas:
- Curvado y doblado de bordes: El proceso principal es doblar o curvar los bordes de la lámina para crear un borde redondeado o enrollado, lo que refuerza la pieza y elimina bordes peligrosos.
- Ajuste de precisión: Algunas rebordeadoras permiten ajustes en los ángulos y la presión aplicada, lo que permite obtener bordes con la precisión exacta necesaria para aplicaciones industriales complejas.
- Mejora del acabado: El rebordeado también contribuye a mejorar el acabado superficial de las piezas, eliminando imperfecciones o irregularidades en los bordes.
1.2. Componentes básicos de una rebordeadora de lámina
Una rebordeadora de lámina está formada por varios componentes clave que permiten realizar el proceso de rebordeado de manera precisa y eficiente:
- Rodillos de rebordeado:
- Son los elementos principales encargados de doblar o curvar el borde de la lámina. Los rodillos están diseñados con perfiles específicos según el tipo de borde que se desea obtener, y pueden ajustarse según el grosor y el tipo de material.
- Sistema de sujeción:
- Mantiene la lámina en su lugar durante el proceso de rebordeado para evitar que se mueva o deforme. Es esencial para garantizar que el borde se forme de manera uniforme a lo largo de toda la pieza.
- Accionamiento:
- En las rebordeadoras automáticas o CNC, un motor, generalmente eléctrico o hidráulico, proporciona la fuerza necesaria para accionar los rodillos. En las versiones manuales, el operador es quien aplica la fuerza.
- Panel de control:
- En las máquinas más avanzadas, el panel de control permite ajustar los parámetros de operación, como la velocidad de los rodillos, la presión aplicada y el tipo de reborde que se desea crear.
2. Tipos de rebordeadoras de lámina
Existen varios tipos de rebordeadoras de lámina, cada uno diseñado para satisfacer diferentes necesidades de producción, desde operaciones pequeñas y manuales hasta procesos completamente automatizados que permiten la producción en masa con alta precisión.
2.1. Rebordeadoras manuales
Las rebordeadoras manuales son operadas directamente por un trabajador que controla los rodillos y el movimiento de la lámina a través de la máquina. Estas máquinas se utilizan principalmente en pequeños talleres o en trabajos personalizados donde no es necesaria una gran capacidad de producción o automatización.
- Ventajas: Ofrecen mayor flexibilidad en el ajuste de los ángulos de rebordeado y son adecuadas para trabajos a pequeña escala o producciones especiales.
- Desventajas: Requieren de un operario experimentado para garantizar la precisión y pueden ser lentas en comparación con las máquinas automáticas.
2.2. Rebordeadoras automáticas
Las rebordeadoras automáticas están equipadas con sistemas motorizados o hidráulicos que realizan el proceso de rebordeado sin intervención manual directa. Estas máquinas son ideales para producción en serie o procesos repetitivos, donde se requiere una mayor velocidad y consistencia.
- Ventajas: Aumentan la eficiencia y reducen el tiempo de ciclo, ya que permiten realizar el rebordeado de manera continua y sin la intervención constante de un operador.
- Desventajas: Requieren una inversión mayor en comparación con las manuales, y son menos flexibles para trabajos personalizados.
2.3. Rebordeadoras CNC (Control Numérico por Computadora)
Las rebordeadoras CNC son las más avanzadas, ya que permiten realizar el rebordeado con una precisión extrema mediante la programación de operaciones automatizadas. El sistema CNC permite ajustar y predefinir todos los parámetros de operación, lo que es ideal para trabajos que requieren alta precisión y consistencia.
- Ventajas: Altamente precisas, permiten realizar producciones en masa con tolerancias muy ajustadas. Son perfectas para industrias que requieren piezas complejas y de alta calidad, como la automotriz y la aeroespacial.
- Desventajas: Son más costosas y requieren de personal calificado para programar y operar la máquina.
3. Funcionamiento de una rebordeadora de lámina
El funcionamiento de una rebordeadora de lámina depende del tipo de máquina, pero en términos generales, el proceso sigue los mismos principios básicos. A continuación, se describe el proceso de rebordeado paso a paso:
3.1. Preparación de la lámina
Antes de iniciar el rebordeado, la lámina metálica debe estar preparada, limpia y libre de defectos que puedan interferir con el proceso. Dependiendo del tipo de lámina, se pueden realizar ajustes previos en el tamaño o grosor, de manera que se ajuste a las especificaciones requeridas para el proceso.
3.2. Colocación de la lámina en la máquina
La lámina se coloca en la zona de sujeción de la máquina, donde se asegura en su posición mediante un sistema de fijación. La sujeción es clave para garantizar que el material no se mueva ni se deforme de manera incontrolada durante el proceso de rebordeado.
3.3. Ajuste de los parámetros
En las rebordeadoras automáticas y CNC, el operario ajusta los parámetros de operación en el panel de control. Esto incluye la velocidad de los rodillos, el ángulo de curvatura, la presión aplicada y la velocidad de alimentación. En las máquinas manuales, el operador ajusta estos parámetros manualmente y los controla durante la operación.
3.4. Proceso de rebordeado
Una vez que la lámina está sujeta y los parámetros ajustados, el sistema de rodillos comienza a aplicar presión sobre el borde de la lámina para doblarlo, curvarlo o enrollarlo. Los rodillos aplican fuerza controlada para deformar el borde de la lámina según las especificaciones requeridas.
3.5. Inspección y acabado
Una vez completado el proceso de rebordeado, la pieza es inspeccionada para verificar la calidad del reborde, asegurándose de que cumple con las especificaciones de ángulo, curvatura y acabado superficial. Dependiendo de la aplicación, el borde puede requerir un procesamiento adicional, como el pulido o el corte para eliminar material sobrante.
4. Aplicaciones de la rebordeadora de lámina
El rebordeado de láminas metálicas es esencial en una variedad de industrias debido a los múltiples beneficios que ofrece, como el aumento de la resistencia estructural, la mejora de la seguridad y el mejor acabado estético de las piezas.
4.1. Industria automotriz
En la fabricación de vehículos, las rebordeadoras de lámina son cruciales para el procesamiento de componentes como los paneles de carrocería, puertas y capós. Los bordes rebordeados refuerzan estas piezas, mejoran la seguridad al eliminar bordes afilados y facilitan el ensamblaje en las líneas de producción.
4.2. Industria aeroespacial
En la industria aeroespacial, donde la ligereza y la resistencia son esenciales, las rebordeadoras se utilizan para fabricar componentes como paneles de fuselaje, estructuras internas y coberturas de motores. El rebordeado permite crear piezas que resisten las altas tensiones y vibraciones del vuelo sin añadir peso innecesario.
4.3. Industria de envases metálicos
En la producción de latas y recipientes metálicos, el rebordeado es esencial para garantizar que los bordes sean seguros para los consumidores y para mejorar el sellado y la durabilidad del envase. Las rebordeadoras permiten crear bordes redondeados en las latas de bebidas y alimentos, lo que asegura un mejor ajuste con las tapas o cierres.
4.4. Electrodomésticos
En la fabricación de electrodomésticos, como lavadoras, secadoras y refrigeradores, las rebordeadoras se utilizan para procesar los bordes de las carcasas metálicas, mejorando la resistencia y eliminando bordes peligrosos que podrían causar lesiones a los usuarios.
4.5. Fabricación de muebles metálicos
En la industria de muebles metálicos, las rebordeadoras se utilizan para crear bordes suaves y curvados en sillas, mesas y otros elementos metálicos, mejorando tanto la seguridad como la estética del producto.
5. Beneficios del uso de una rebordeadora de lámina
El uso de una rebordeadora de lámina ofrece varios beneficios importantes en el procesamiento de metales:
- Mayor resistencia estructural: El rebordeado refuerza los bordes de las piezas, lo que mejora su resistencia a la deformación y las tensiones mecánicas.
- Seguridad: Elimina los bordes afilados que podrían causar cortes o accidentes durante el manejo o el uso de las piezas.
- Mejora del ensamblaje: Los bordes rebordeados facilitan el ensamblaje de las piezas, mejorando el ajuste y la alineación de los componentes.
- Estética mejorada: Proporciona un acabado más suave y uniforme, lo que mejora la apariencia de las piezas en productos de consumo.
- Eficiencia en la producción: Las rebordeadoras automáticas y CNC aumentan la velocidad de producción y reducen el tiempo de ciclo, lo que resulta en una mayor eficiencia en la fabricación en masa.
Conclusión
La rebordeadora de lámina es una herramienta fundamental en la fabricación de piezas metálicas en una amplia variedad de industrias. Su capacidad para crear bordes curvados o doblados mejora la resistencia, la seguridad, y la estética de las piezas, haciéndolas más aptas para soportar tensiones mecánicas, evitar accidentes y facilitar su ensamblaje.
Desde la fabricación de automóviles y aeronaves hasta la producción de envases metálicos y electrodomésticos, las rebordeadoras de lámina son esenciales para garantizar productos de alta calidad, eficientes y seguros. Su versatilidad y capacidad para adaptarse a diferentes aplicaciones hacen que estas máquinas sean una inversión valiosa para cualquier industria que procese láminas metálicas.
Componentes principales de una rebordeadora de lámina
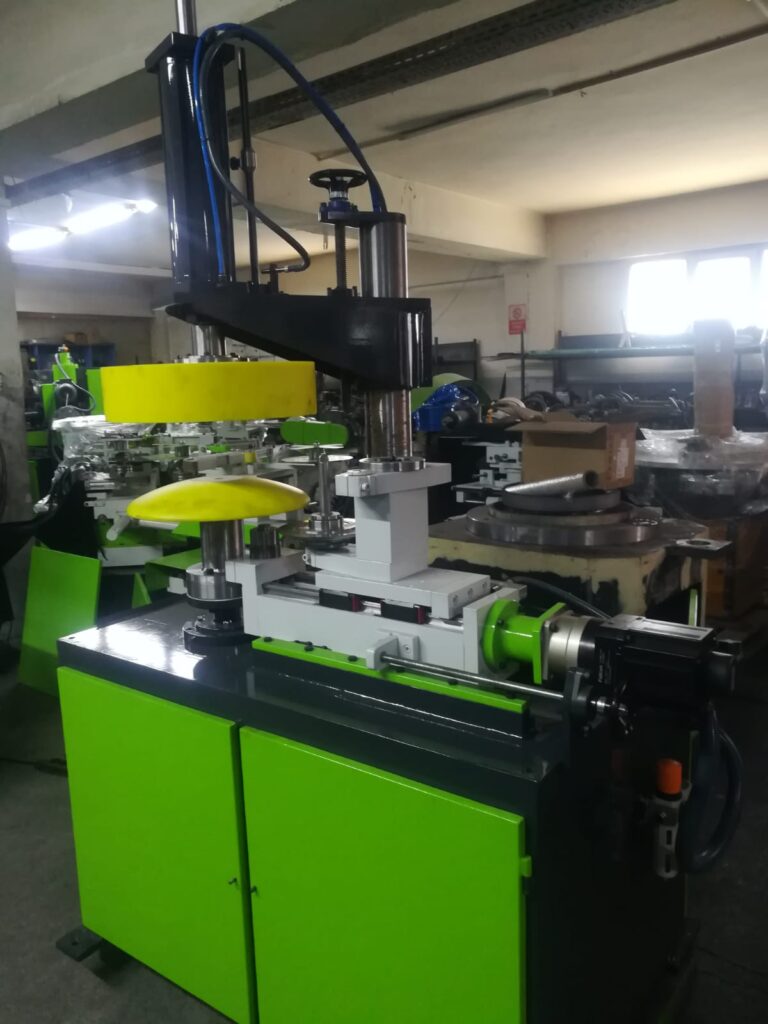
Una rebordeadora de lámina es una máquina clave en la industria del conformado de metales, utilizada para doblar, curvar o enrollar los bordes de láminas metálicas. La funcionalidad de una rebordeadora depende de su capacidad para controlar con precisión el proceso de rebordeado, y esta capacidad está determinada por los diferentes componentes que conforman la máquina. Estos componentes trabajan en conjunto para aplicar la presión necesaria, mover las piezas y garantizar la calidad del rebordeado, de modo que las piezas metálicas resultantes sean resistentes, seguras y cumplan con los requisitos específicos de cada aplicación.
A continuación, se describen en detalle los componentes principales de una rebordeadora de lámina, su función en el proceso de rebordeado y cómo contribuyen al rendimiento general de la máquina.
1. Rodillos de rebordeado
Los rodillos de rebordeado son el corazón de una rebordeadora de lámina, ya que son los componentes que efectúan el proceso de doblar, curvar o enrollar el borde de la lámina. Están diseñados con diferentes perfiles para permitir la creación de diversos tipos de rebordes, y su ajuste es fundamental para lograr un trabajo preciso y consistente.
1.1. Tipos de rodillos de rebordeado
- Rodillos simples: Utilizados para realizar doblados sencillos en los bordes de las láminas. Son adecuados para crear bordes de un ángulo específico y son fáciles de ajustar según el tipo de material.
- Rodillos de curvatura: Estos rodillos tienen un perfil diseñado para curvar el borde de la lámina, formando un reborde más suave o redondeado. Son comunes en la fabricación de recipientes metálicos, como latas o cilindros.
- Rodillos de enrollado: Permiten crear un borde enrollado en los extremos de las láminas, lo que aumenta la resistencia de la pieza y mejora su capacidad para soportar cargas mecánicas.
1.2. Material de los rodillos
Los rodillos están fabricados generalmente en acero endurecido o materiales de alta resistencia, como el carburo de tungsteno, que les permite soportar la fricción constante y la presión durante el proceso de rebordeado sin deformarse ni desgastarse fácilmente. La durabilidad de los rodillos es esencial para garantizar que la máquina mantenga su precisión durante largos periodos de uso.
1.3. Ajuste de los rodillos
La ajustabilidad de los rodillos es un factor crucial en las rebordeadoras de lámina. Los rodillos deben poder ajustarse para adaptarse a diferentes grosores de lámina y tipos de material. En las máquinas automáticas y CNC, este ajuste es controlado por un sistema motorizado o hidráulico, mientras que en las rebordeadoras manuales, el ajuste se realiza de manera mecánica por el operario.
2. Sistema de sujeción
El sistema de sujeción es el mecanismo encargado de mantener la lámina metálica en su lugar durante el proceso de rebordeado. Este sistema es crucial para garantizar que la lámina no se desplace o se deforme de manera incontrolada, lo que podría afectar la calidad del reborde final.
2.1. Tipos de sistemas de sujeción
- Sujeción mecánica: Utiliza abrazaderas o prensas manuales que se ajustan al borde de la lámina para mantenerla en su posición. Este sistema es común en rebordeadoras manuales o de pequeño tamaño.
- Sujeción hidráulica: Emplea cilindros hidráulicos para aplicar presión sobre la lámina y asegurarla durante el proceso. Este tipo de sujeción es más preciso y se utiliza en rebordeadoras automáticas e industriales de gran capacidad, donde la consistencia en la presión aplicada es fundamental para lograr resultados uniformes.
- Sujeción neumática: Similar a la sujeción hidráulica, pero utiliza aire comprimido en lugar de fluido hidráulico para sujetar la lámina. Este sistema es rápido y eficiente, lo que lo hace ideal para líneas de producción de alta velocidad.
2.2. Importancia del sistema de sujeción
Un sistema de sujeción bien diseñado es esencial para evitar el deslizamiento de la lámina durante el rebordeado. Si la lámina no está bien sujeta, puede moverse mientras los rodillos aplican presión, lo que resultará en bordes irregulares, deformaciones no deseadas o, incluso, en la ruptura de la pieza. Además, el sistema de sujeción también ayuda a mantener la alineación de la lámina, lo que es importante para garantizar un reborde uniforme a lo largo de toda la pieza.
3. Accionamiento o sistema motriz
El accionamiento de una rebordeadora de lámina es el componente que proporciona la energía necesaria para hacer girar los rodillos y mover las piezas a través de la máquina. Dependiendo del tipo de rebordeadora, el sistema de accionamiento puede ser manual, eléctrico, hidráulico o neumático.
3.1. Tipos de sistemas de accionamiento
- Accionamiento manual: En las rebordeadoras manuales, el operador controla el movimiento de los rodillos mediante una manivela o pedal, lo que permite aplicar la fuerza directamente. Este tipo de accionamiento es común en talleres de baja producción o para trabajos personalizados donde no se necesita una gran capacidad de producción.
- Accionamiento eléctrico: En las rebordeadoras automáticas, el movimiento de los rodillos es controlado por un motor eléctrico. El operador ajusta los parámetros de operación, como la velocidad y la presión, pero el motor realiza el trabajo de mover la lámina a través de los rodillos y aplicar la presión necesaria. Este tipo de accionamiento es eficiente y adecuado para producciones en masa.
- Accionamiento hidráulico: En algunas rebordeadoras industriales, los sistemas hidráulicos proporcionan la fuerza para accionar los rodillos y realizar el rebordeado. Los cilindros hidráulicos pueden generar grandes cantidades de fuerza, lo que es ideal para trabajar con láminas gruesas o materiales duros.
- Accionamiento neumático: Similar al sistema hidráulico, pero en lugar de fluido hidráulico, utiliza aire comprimido para generar la fuerza necesaria. Este sistema es rápido y eficiente, y se utiliza en líneas de producción de alta velocidad donde se requiere una alta tasa de producción.
3.2. Control de la velocidad y la presión
La velocidad de los rodillos y la presión aplicada durante el rebordeado son parámetros críticos que deben ser ajustados para cada aplicación. En las rebordeadoras automáticas y CNC, estos parámetros se controlan mediante el sistema de accionamiento, que permite ajustar la velocidad según el tipo de material y el grosor de la lámina. La presión aplicada también es importante para garantizar que el borde se forme de manera uniforme sin dañar el material.
4. Mesa de trabajo o plataforma
La mesa de trabajo es la superficie donde se coloca la lámina antes de comenzar el proceso de rebordeado. Es fundamental que la mesa de trabajo sea plana y estable, ya que cualquier irregularidad en la superficie podría afectar la precisión del rebordeado.
4.1. Material de la mesa de trabajo
La mesa de trabajo suele estar hecha de materiales resistentes como acero o aluminio, ya que debe soportar el peso de las láminas y resistir la presión aplicada durante el proceso de rebordeado. Además, el material de la mesa debe ser resistente a la corrosión para garantizar la durabilidad de la máquina.
4.2. Tamaño y capacidad de la mesa de trabajo
El tamaño de la mesa de trabajo depende de la capacidad de la rebordeadora y del tamaño de las láminas que se van a procesar. En máquinas industriales grandes, la mesa de trabajo puede tener suficiente espacio para procesar láminas de gran tamaño, mientras que en rebordeadoras manuales o pequeñas, la mesa está diseñada para piezas más compactas.
4.3. Soportes y guías
Algunas mesas de trabajo están equipadas con soportes ajustables o guías que ayudan a mantener la lámina en su posición durante el proceso. Estas guías permiten ajustar la posición de la lámina para asegurarse de que el reborde se realice de manera uniforme a lo largo de toda la pieza.
5. Sistema de control
El sistema de control es la parte de la rebordeadora que permite al operador ajustar los parámetros de operación, como la velocidad de los rodillos, la presión aplicada y el tipo de reborde que se desea realizar. El sistema de control puede variar en complejidad dependiendo del tipo de rebordeadora.
5.1. Sistema de control manual
En las rebordeadoras manuales, el control del proceso se realiza de forma manual por el operador, que ajusta directamente la máquina mediante palancas, pedales o manivelas. Este tipo de control es adecuado para trabajos personalizados o de baja producción, donde se requiere flexibilidad en el proceso.
5.2. Sistema de control automático
En las rebordeadoras automáticas, el sistema de control está motorizado y permite ajustar los parámetros a través de botones o interruptores. El operador establece la velocidad y la presión, y la máquina ejecuta el proceso de forma automática. Este sistema es ideal para producciones en serie donde se requiere consistencia y rapidez.
5.3. Control numérico por computadora (CNC)
En las rebordeadoras CNC, el sistema de control es mucho más avanzado y permite la programación de operaciones a través de un software. El operador puede predefinir los parámetros de operación, como el ángulo de reborde, la velocidad de los rodillos, y la presión, lo que garantiza que cada pieza sea procesada con un alto grado de precisión. Además, el sistema CNC permite realizar rebordes complejos y repetitivos de manera eficiente.
6. Dispositivos de seguridad
Como en todas las máquinas industriales, la seguridad es un aspecto fundamental en las rebordeadoras de lámina. Los dispositivos de seguridad están diseñados para proteger al operador y garantizar que la máquina funcione de manera segura durante todo el proceso de rebordeado.
6.1. Barreras de seguridad
Muchas rebordeadoras están equipadas con barreras de seguridad o protectores que evitan que el operador tenga acceso directo a las partes móviles de la máquina, como los rodillos o el sistema de accionamiento. Estas barreras están diseñadas para minimizar el riesgo de accidentes, especialmente cuando se trabaja con máquinas automáticas de alta velocidad.
6.2. Sensores de seguridad
Las máquinas automáticas y CNC pueden estar equipadas con sensores de seguridad que detectan la posición de las manos del operador o la presencia de objetos extraños en el área de trabajo. Si se detecta algo fuera de lo normal, la máquina se detiene automáticamente para evitar accidentes.
6.3. Sistemas de parada de emergencia
Todas las rebordeadoras deben tener un sistema de parada de emergencia que permita al operador detener la máquina inmediatamente en caso de que ocurra un problema durante el proceso. Este sistema de emergencia generalmente está ubicado en un lugar accesible y fácil de activar, para garantizar una respuesta rápida.
7. Sistema de lubricación
El sistema de lubricación es esencial en las rebordeadoras, ya que reduce la fricción entre los rodillos y la lámina, lo que mejora el flujo del material y ayuda a prolongar la vida útil de los componentes de la máquina.
7.1. Tipos de lubricantes
Los aceites minerales, grasas y ceras son los lubricantes más comunes utilizados en las rebordeadoras. Dependiendo del tipo de material que se está procesando, puede ser necesario utilizar un lubricante específico para reducir la fricción y evitar que el material se desgaste o se adhiera a los rodillos.
7.2. Sistemas de aplicación de lubricante
Los lubricantes pueden aplicarse manualmente en máquinas pequeñas o mediante sistemas automáticos de lubricación en las rebordeadoras industriales. Los sistemas automáticos aseguran que el lubricante se distribuya de manera uniforme a lo largo de los rodillos y las láminas, lo que mejora la eficiencia del proceso y reduce el desgaste de las herramientas.
Conclusión
Los componentes principales de una rebordeadora de lámina son fundamentales para su funcionamiento eficiente y seguro. Desde los rodillos de rebordeado, que son los encargados de doblar y curvar el material, hasta los sistemas de sujeción, que aseguran que la lámina se mantenga en su lugar, cada componente desempeña un papel crucial en la calidad del rebordeado final. El accionamiento, la mesa de trabajo, el sistema de control y los dispositivos de seguridad completan el conjunto de elementos que hacen posible la creación de bordes resistentes, precisos y seguros en una amplia variedad de aplicaciones industriales.
Las rebordeadoras de lámina, ya sean manuales, automáticas o CNC, son máquinas versátiles y esenciales en la producción moderna de componentes metálicos. Gracias a su diseño y funcionalidad, permiten realizar trabajos de rebordeado de alta calidad, lo que garantiza que las piezas metálicas resultantes sean adecuadas para cumplir con los estrictos estándares de calidad y seguridad requeridos en industrias como la automotriz, aeroespacial, envases metálicos y electrodomésticos.
Proceso de funcionamiento de una rebordeadora de lámina
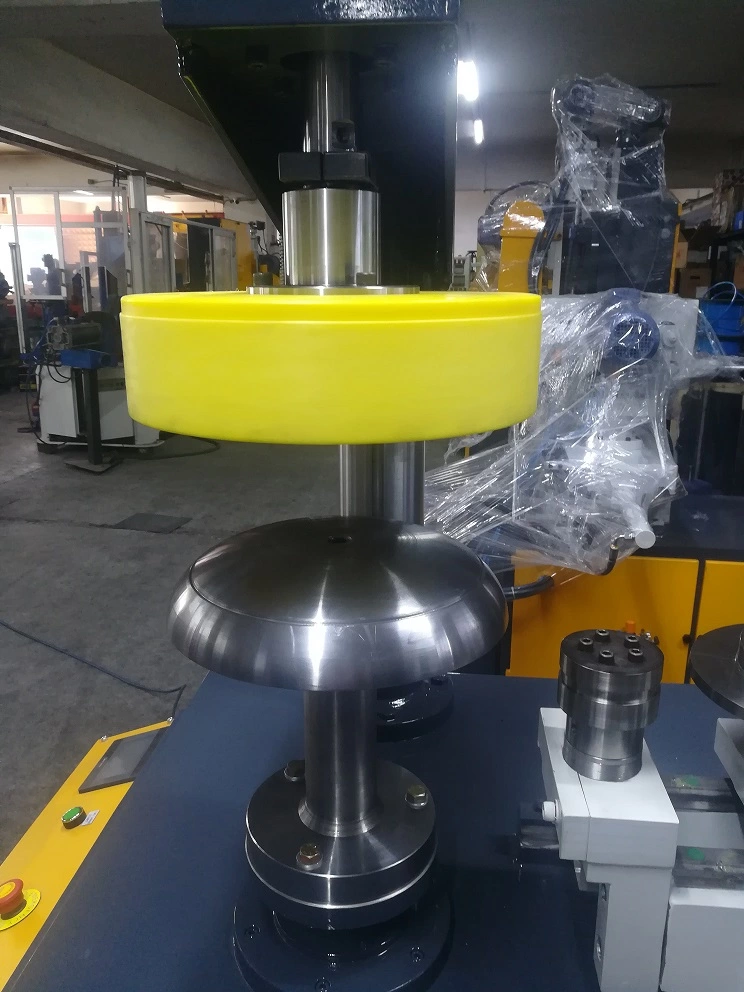
Las rebordeadoras de lámina son máquinas esenciales en el procesamiento de metales que se utilizan para doblar, curvar o enrollar los bordes de láminas metálicas. El proceso de rebordeado no solo mejora la resistencia estructural de las piezas, sino que también elimina bordes afilados y permite obtener acabados más estéticos y seguros, fundamentales para productos como envases metálicos, piezas automotrices, componentes aeronáuticos y electrodomésticos. Para garantizar un rebordeado eficiente y de alta calidad, es importante comprender el proceso de funcionamiento de una rebordeadora de lámina, los pasos involucrados, los parámetros que se deben controlar y los factores que afectan el resultado final.
Este artículo detalla el proceso completo de funcionamiento de una rebordeadora de lámina, abarcando desde la preparación del material hasta el acabado del reborde, y proporciona una descripción detallada de los ajustes y procedimientos que se deben realizar para optimizar la operación.
1. Preparación de la lámina metálica
El primer paso en el proceso de rebordeado es la preparación de la lámina metálica. Este es un paso crucial, ya que las condiciones iniciales de la lámina pueden influir directamente en la calidad del reborde final.
1.1. Selección del material
Las láminas metálicas pueden estar hechas de diferentes materiales, como acero inoxidable, aluminio, cobre, latón, entre otros. La selección del material es importante, ya que cada tipo de metal tiene diferentes propiedades de deformación y resistencia, lo que influye en la cantidad de fuerza que debe aplicarse durante el proceso de rebordeado.
- Acero inoxidable: Material duro y resistente, utilizado principalmente en aplicaciones automotrices y aeronáuticas donde se requiere alta durabilidad.
- Aluminio: Es más blando y ligero, utilizado comúnmente en envases metálicos y componentes aeroespaciales por su alta resistencia a la corrosión y su ligereza.
1.2. Inspección de la lámina
Antes de iniciar el proceso de rebordeado, es esencial inspeccionar la lámina para garantizar que esté libre de defectos como abolladuras, grietas o irregularidades superficiales que puedan afectar la calidad del reborde. Las láminas que presenten defectos pueden generar rebordes deformados o inconsistentes.
1.3. Limpieza de la lámina
La lámina debe estar completamente limpia y libre de impurezas, polvo, óxidos o partículas que puedan interferir con el contacto entre los rodillos de la máquina y la lámina metálica. La limpieza puede realizarse con solventes o detergentes específicos para eliminar residuos grasos o contaminantes de la superficie.
2. Colocación de la lámina en la rebordeadora
Una vez que la lámina ha sido preparada, se procede a colocar la lámina en la zona de trabajo de la rebordeadora. La forma en que la lámina se coloca y se asegura en la máquina es fundamental para obtener un reborde uniforme y sin defectos.
2.1. Alineación de la lámina
El primer paso en esta etapa es alinear la lámina correctamente con los rodillos de rebordeado. La alineación adecuada asegura que el borde de la lámina quede perfectamente perpendicular a los rodillos, lo que resulta en un reborde consistente a lo largo de todo el borde.
- Alineación manual: En las rebordeadoras manuales, el operador es responsable de posicionar la lámina de manera adecuada antes de iniciar el proceso. Esto requiere precisión para evitar desviaciones.
- Alineación automática: En las rebordeadoras CNC o automáticas, la alineación se realiza mediante sensores o guias automatizadas, que posicionan la lámina con gran exactitud y reducen la posibilidad de error humano.
2.2. Sujeción de la lámina
Después de alinear la lámina, es necesario sujetarla en su lugar para evitar que se desplace durante el proceso de rebordeado. Este paso es crucial para asegurar un reborde uniforme y sin imperfecciones.
- Sujeción mecánica: En las rebordeadoras manuales, la lámina se asegura mediante sistemas de fijación o abrazaderas ajustables que mantienen la lámina firme contra la mesa de trabajo.
- Sujeción hidráulica o neumática: En las rebordeadoras automáticas o industriales, la sujeción se realiza mediante cilindros hidráulicos o neumáticos que aplican una presión uniforme sobre la lámina para mantenerla en su posición mientras los rodillos realizan el rebordeado.
2.3. Ajustes previos de los rodillos
Antes de iniciar el rebordeado, los rodillos de la máquina deben ajustarse según el tipo de reborde que se va a realizar y el grosor del material. Los rodillos pueden ajustarse manualmente o a través de controles automáticos en las máquinas CNC.
- Distancia entre rodillos: La distancia entre los rodillos debe ajustarse según el grosor de la lámina. En materiales más gruesos, es necesario aplicar más fuerza para lograr el doblado adecuado, mientras que en materiales más delgados se requiere menos presión.
- Perfil de los rodillos: Dependiendo del tipo de reborde que se desea crear (simple, curvado o enrollado), los rodillos deben ajustarse para adoptar el perfil adecuado. En las máquinas CNC, estos perfiles pueden programarse previamente.
3. Proceso de rebordeado
El proceso de rebordeado es el momento en el que la máquina dobla o curva el borde de la lámina para crear el reborde deseado. Este es el paso clave en el funcionamiento de la rebordeadora, ya que define la forma final del borde y la calidad de la pieza.
3.1. Aplicación de presión sobre el borde
Una vez que la lámina está colocada y sujeta, los rodillos comienzan a aplicar presión sobre el borde de la lámina. Esta presión es lo que provoca que el borde de la lámina se doble o curve.
- Presión controlada: En las rebordeadoras CNC y automáticas, la presión aplicada por los rodillos está controlada de manera precisa, lo que permite un rebordeado uniforme sin causar fracturas o deformaciones en el material.
- Fuerza manual: En las rebordeadoras manuales, la presión aplicada depende de la habilidad y experiencia del operario, quien controla los rodillos a través de manivelas o pedales.
3.2. Control de la velocidad de rebordeado
La velocidad a la que los rodillos doblan o curvan el borde es otro parámetro crucial que debe controlarse cuidadosamente. Si los rodillos se mueven demasiado rápido, pueden provocar tensiones excesivas en la lámina, lo que resulta en arrugas o grietas. Si los rodillos se mueven demasiado lentamente, el proceso se vuelve ineficiente y puede generar irregularidades en el borde.
- Velocidad ajustable: En las rebordeadoras automáticas, la velocidad se ajusta automáticamente según el tipo de material y la geometría del borde. Esto permite que el proceso sea lo más eficiente posible sin comprometer la calidad del reborde.
3.3. Formación del reborde
A medida que los rodillos aplican presión y la lámina se deforma, se forma el reborde en el borde de la pieza. El tipo de reborde formado depende del diseño de los rodillos y de los parámetros de operación establecidos previamente.
- Reborde simple: Se dobla el borde de la lámina en un ángulo específico, generalmente de 90 grados o menos.
- Reborde curvado: Se aplica una curvatura suave al borde, creando un reborde redondeado.
- Reborde enrollado: Se enrolla el borde de la lámina sobre sí mismo, lo que crea un borde más grueso y resistente.
3.4. Lubricación durante el rebordeado
Durante el proceso de rebordeado, es común utilizar lubricantes para reducir la fricción entre los rodillos y la lámina. La lubricación no solo ayuda a prolongar la vida útil de los rodillos, sino que también mejora el flujo del material, lo que reduce el riesgo de que se formen arrugas o defectos en el reborde.
- Aplicación de lubricante: El lubricante puede aplicarse de manera manual o automática en las rebordeadoras industriales. Los aceites minerales y las grasas especializadas son los lubricantes más utilizados en este tipo de operaciones.
4. Ajuste y verificación de calidad
Una vez que se ha completado el rebordeado, es necesario realizar un ajuste y verificación del trabajo realizado para asegurarse de que cumple con los estándares de calidad requeridos.
4.1. Verificación del grosor del reborde
Es esencial medir el grosor del reborde para asegurarse de que cumple con las especificaciones necesarias. En algunos casos, el reborde puede requerir un planchado adicional para asegurar que el grosor sea uniforme a lo largo de todo el borde de la pieza.
4.2. Inspección visual del reborde
La inspección visual es otro paso importante en la verificación de la calidad. Durante esta inspección, el operario verifica que no haya arrugas, grietas, fracturas o deformaciones en el reborde. Cualquier defecto visual debe corregirse antes de que la pieza avance a la siguiente etapa del proceso de fabricación.
4.3. Ajustes finales
Si se detectan imperfecciones en el reborde, el operador puede realizar ajustes finales a la presión de los rodillos o a la velocidad del rebordeado para corregir el problema. En las rebordeadoras CNC, estos ajustes se realizan automáticamente al detectar un error, lo que garantiza una mayor consistencia.
5. Retiro de la lámina y acabado final
Una vez completado el rebordeado y verificada la calidad de la pieza, la lámina rebordeada se retira de la máquina para su procesamiento adicional, si es necesario.
5.1. Desbloqueo de la sujeción
El primer paso para retirar la pieza es desbloquear el sistema de sujeción que mantuvo la lámina en su lugar durante el proceso. En las rebordeadoras automáticas, este paso se realiza mediante controles hidráulicos o neumáticos, mientras que en las manuales es un proceso mecánico.
5.2. Retiro de la pieza
La pieza rebordeada se retira con cuidado para evitar deformaciones en el borde recién formado. El manejo adecuado de la pieza es fundamental para evitar daños que puedan comprometer la calidad del producto final.
5.3. Acabado superficial
En algunas aplicaciones, es necesario realizar un acabado adicional después del rebordeado. Este acabado puede incluir el pulido de los bordes para mejorar la suavidad o la aplicación de tratamientos superficiales para proteger el metal de la corrosión.
Conclusión
El proceso de funcionamiento de una rebordeadora de lámina implica varios pasos clave, desde la preparación del material hasta la verificación final del reborde. Cada etapa del proceso debe realizarse con precisión para garantizar que el rebordeado se realice de manera eficiente y con alta calidad.
La alineación adecuada, el ajuste de los rodillos, el control de la velocidad y la aplicación de lubricantes son factores fundamentales que influyen directamente en el éxito del rebordeado. Además, la correcta inspección y el ajuste final aseguran que el producto terminado cumpla con los estándares requeridos en términos de resistencia, seguridad y apariencia.
El uso de rebordeadoras automáticas y CNC ha mejorado significativamente la precisión y la eficiencia de este proceso, permitiendo una mayor consistencia y reduciendo el riesgo de errores humanos. Sin embargo, la habilidad del operario sigue siendo esencial en rebordeadoras manuales o en ajustes personalizados en la fabricación de piezas metálicas de alta calidad.
Máquinas Formadoras de Metales EMS
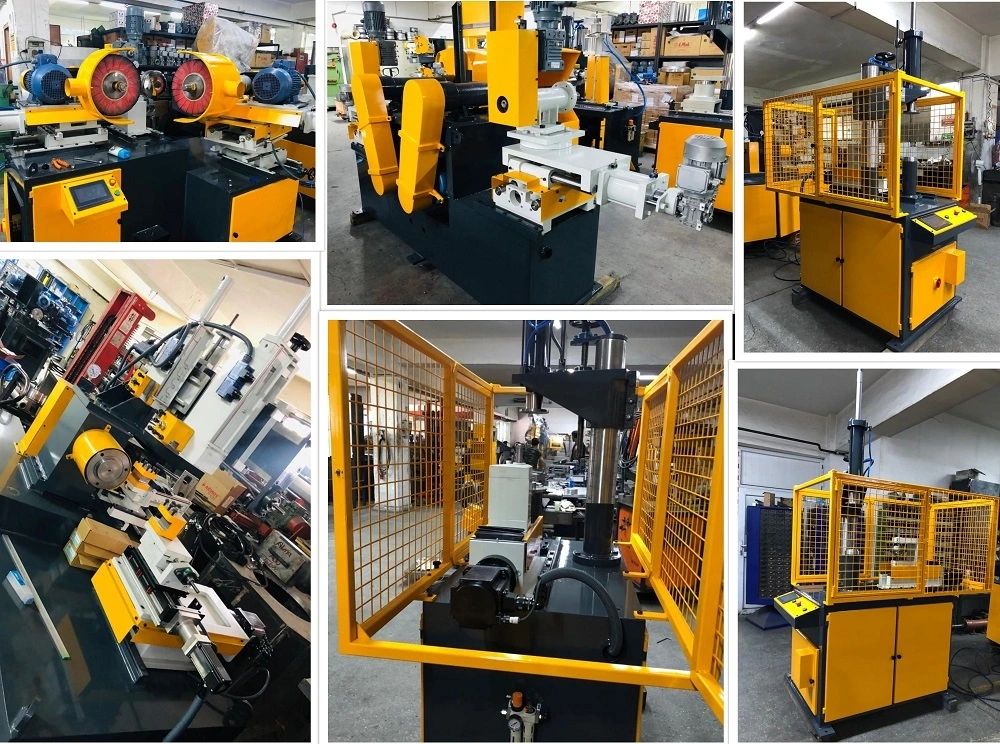
Diseñamos, fabricamos y montamos maquinaria metalmecánica como:
Prensa de transferencia hidráulica
Prensa para mosaicos de vidrio
Prensa hidráulica de embutición profunda
prensa de fundición
Prensa hidráulica de conformado en frío
Prensa de hidroformado
prensa compuesta
Prensa de moldeo de caucho de silicona
Prensa de pastillas de freno
Prensa de melamina
Prensa SMC y BMC
prensa labrotaroy
Máquina cortadora de bordes
Máquina rizadora de bordes
Máquina recortadora de abalorios
Máquina de recorte y jogging
Línea de producción de utensilios de cocina.
Máquina dobladora de tubos
Máquina dobladora de perfiles
Sierra de cinta para metal
Máquina de soldar cilíndrica
Prensas horizontales y utensilios de cocina.
Menaje de cocina, artículos de hotelería
Maquinaria para la producción de utensilios para hornear y cubiertos.
como una línea completa así como una máquina individual como:
Máquinas cortadoras de bordes y biseladoras
Pulidoras y rectificadoras de ollas y sartenes.
Prensas hidráulicas de trefilado
Máquinas troqueladoras circulares
remachadora
Punzonadoras
Máquina de alimentación de prensa
Puede consultar nuestra maquinaria en funcionamiento en: EMS Máquinas Formadoras de Metales EMS – YouTube
Aplicaciones:
Punzonado de bridas
Abalorios y nervaduras
Bridas
Guarnición
Curling
costura de bloqueo
Nervaduras