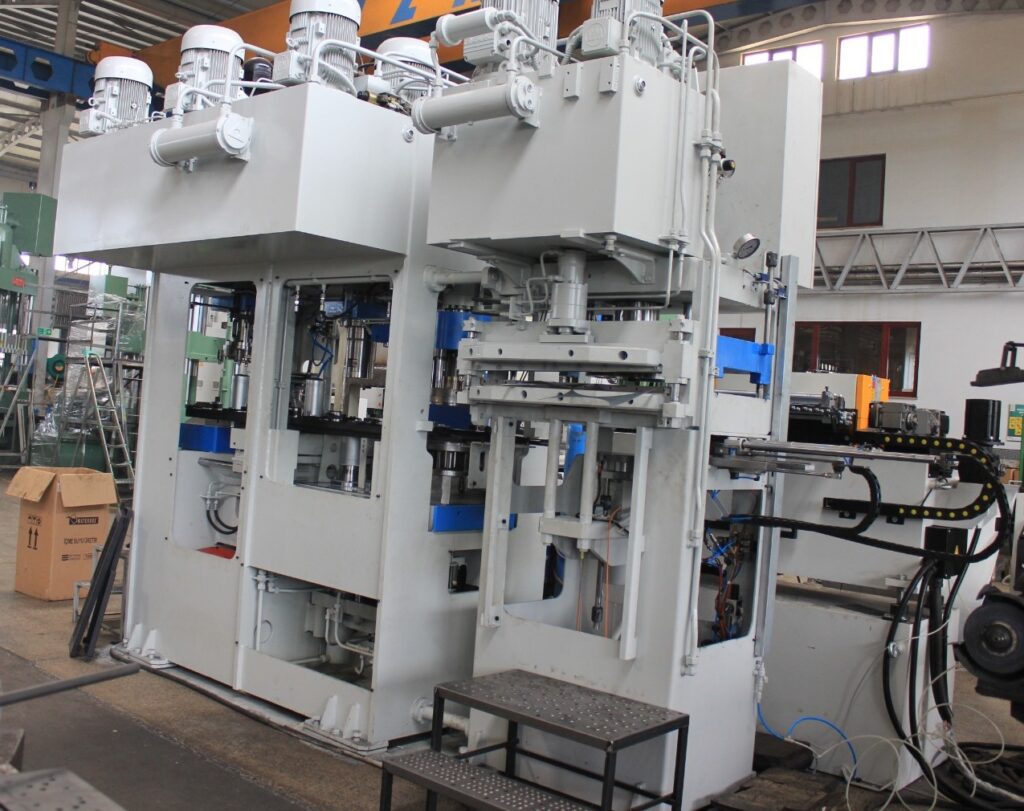
La prensa es una máquina diseñada especialmente para la embutición de piezas metálicas. La Prensa de Estirado y Embutición es una máquina industrial utilizada principalmente en procesos de conformado de chapa metálica, diseñada para realizar operaciones de estirado profundo y embutición en una sola línea de trabajo. Se trata de una prensa robusta, generalmente de tipo hidráulico o mecánico de doble efecto, equipada con un cojín o sistema de sujeción que mantiene la lámina en posición mientras el punzón da forma a la pieza.
Este tipo de prensa se emplea para producir componentes metálicos con formas complejas, de paredes altas y diámetros reducidos, como carcasas, recipientes cilíndricos, utensilios de cocina, piezas automotrices, envases metálicos, y elementos de electrodomésticos.
En el proceso de embutición, la chapa se deforma plásticamente y fluye dentro de la matriz hasta alcanzar la forma deseada. Cuando se trata de estirado, la chapa no solo fluye, sino que también se estira, logrando reducir su espesor en determinadas zonas para obtener piezas más resistentes y con mayor precisión dimensional.
Las características más destacadas de una prensa de estirado y embutición son:
- Cojín de embutición regulable, que controla la presión sobre la chapa y evita arrugas.
- Accionamiento hidráulico de alta precisión, que asegura una velocidad de trabajo uniforme y regulable.
- Capacidad de trabajar con diferentes espesores de chapa, adaptándose a diversas aplicaciones.
- Automatización opcional, con sistemas de alimentación, extracción y apilado de piezas.
La prensa de estirado y embutición es una de las máquinas más versátiles y complejas dentro del sector del conformado de chapa metálica, ya que combina en un mismo ciclo de trabajo operaciones de embutición profunda y de estirado controlado, lo que permite fabricar piezas de geometría exigente, con gran profundidad y al mismo tiempo con un acabado superficial impecable y tolerancias muy estrechas. El principio de funcionamiento se basa en la acción coordinada de un punzón que penetra en la chapa previamente colocada sobre la matriz, mientras un cojín de embutición o un sistema hidráulico de sujeción mantiene el material firmemente en su sitio para evitar el levantamiento de bordes, la formación de pliegues o la aparición de arrugas. Este control del flujo del material es fundamental, pues garantiza que la lámina se deforme plásticamente de manera uniforme, redistribuyendo tensiones y espesores sin llegar a provocar grietas o roturas en zonas críticas. A diferencia de las prensas convencionales de embutición simple, la prensa de estirado y embutición permite trabajar con mayores profundidades, con diámetros reducidos y con paredes más altas, lo cual es esencial en sectores como la automoción, donde se producen componentes estructurales, carcasas de transmisión o depósitos, en la industria de electrodomésticos para la fabricación de cubetas, paneles o envolventes, en utensilios de cocina como ollas, sartenes y cacerolas, o incluso en envases metálicos de precisión para alimentos y cosmética.
Una característica muy destacada de este tipo de prensas es la posibilidad de regular con alta precisión la presión del cojín de embutición. El control de esta fuerza resulta determinante, porque un exceso de presión puede impedir el correcto flujo del material y provocar roturas, mientras que una presión insuficiente genera arrugas y ondulaciones en las paredes de la pieza. Por este motivo, la tecnología hidráulica se ha consolidado como la más utilizada en este tipo de prensas, al ofrecer una regulación continua, progresiva y programable de los parámetros de presión, velocidad y carrera. Estas ventajas permiten adaptarse a una amplia variedad de materiales, desde aceros de alta resistencia hasta aceros inoxidables, aluminio, cobre y aleaciones especiales, siempre con espesores variables según las necesidades de la pieza final. Además, en los modelos modernos, el diseño estructural de la prensa suele ser de gran rigidez, con bastidores sobredimensionados y guiados lineales que garantizan una alineación perfecta entre punzón y matriz, lo que repercute en una mayor durabilidad de las herramientas y una calidad repetitiva en cada ciclo de producción.
En el ámbito de la automatización, la prensa de estirado y embutición puede integrarse con alimentadores automáticos de bobina o de chapa cortada, sistemas de centrado, robots de transferencia de piezas y apiladores automáticos, lo que transforma el proceso en una línea continua y de alta productividad. Esta integración no solo optimiza los tiempos de ciclo, sino que también reduce el error humano, mejora la seguridad del operario y permite mantener una producción estable y homogénea incluso en turnos de trabajo prolongados. La posibilidad de incluir control numérico o PLC en el sistema hace que el ajuste de parámetros sea más rápido y flexible, con memorias de programas que almacenan condiciones específicas para diferentes geometrías de piezas, facilitando los cambios de producción sin largos tiempos de preparación.
En cuanto al acabado de las piezas, la prensa de estirado y embutición ofrece superficies lisas y sin defectos visibles, lo cual es crucial en industrias donde el aspecto estético es tan importante como la precisión dimensional. Esto se debe a que el contacto entre la chapa y las superficies pulidas del punzón y la matriz se mantiene bajo condiciones de lubricación controlada, reduciendo la fricción y evitando marcas indeseadas. Con el uso de recubrimientos técnicos en las herramientas, como nitruración o revestimientos PVD, se consigue prolongar la vida útil de las matrices y mejorar el comportamiento tribológico del proceso. Todo este conjunto de tecnologías convierte a la prensa de estirado y embutición en una máquina altamente especializada que no solo cumple una función mecánica de deformación, sino que se convierte en el corazón de muchas plantas de producción donde se exige uniformidad, repetibilidad y una capacidad de fabricar piezas complejas con costos competitivos.
El diseño y la operación de una prensa de estirado y embutición requieren un equilibrio muy preciso entre los parámetros mecánicos, hidráulicos y materiales, ya que cualquier desviación en estos factores puede comprometer la calidad de la pieza final. El proceso comienza con la selección de la chapa, la cual debe presentar una homogeneidad en su microestructura y un límite elástico controlado, de manera que pueda deformarse plásticamente sin fracturarse. A medida que el punzón avanza hacia la matriz, la chapa es sometida a un estado complejo de tensiones combinadas de tracción y compresión, que provocan un flujo dirigido del material hacia el interior de la cavidad. En esta etapa, el comportamiento tribológico entre chapa, punzón y matriz resulta determinante, pues la fricción excesiva provoca desgarramientos, mientras que una lubricación inadecuada genera defectos superficiales y desgaste prematuro de las herramientas. Por eso, en la práctica industrial, se emplean aceites lubricantes con aditivos específicos para embutición profunda, emulsiones de alto rendimiento o recubrimientos sólidos que reducen la fricción y estabilizan el proceso.
La complejidad del estirado radica en que, además de lograr que el material fluya hacia la forma deseada, en muchos casos se busca reducir el espesor en determinadas zonas de la pieza para aumentar su resistencia o adaptarla a un diseño específico. Este fenómeno exige un control extremadamente fino del cojín de embutición, de la velocidad de desplazamiento del punzón y de la geometría de la matriz, ya que cualquier irregularidad puede provocar arrugas radiales, estrangulamientos o incluso fracturas por exceso de elongación. Los fabricantes de prensas modernas han incorporado sistemas de monitorización en tiempo real de la fuerza ejercida y del recorrido de cada componente, lo que permite corregir desviaciones durante el ciclo y garantizar piezas conformes con una repetibilidad absoluta. Además, la posibilidad de programar curvas de velocidad diferenciadas en el movimiento del punzón es clave para obtener un estirado controlado, donde la velocidad inicial puede ser más baja para permitir el asentamiento del material y posteriormente incrementarse en la fase de deformación estable.
En cuanto a las herramientas, el diseño de punzones y matrices es un campo de ingeniería altamente especializado que combina cálculos de resistencia de materiales, simulaciones por elementos finitos y experiencia acumulada en procesos reales. El ángulo de redondeo de la matriz, el radio del punzón y la rugosidad de las superficies de contacto influyen directamente en la calidad del flujo del material y en la ausencia de defectos. Para piezas de gran volumen de producción, se emplean aceros aleados de alta dureza, tratados térmicamente y con recubrimientos de alta resistencia al desgaste, que permiten mantener la estabilidad dimensional durante millones de ciclos de trabajo. En aplicaciones críticas, incluso se recurre a herramientas con insertos de carburo o materiales cerámicos para soportar condiciones extremas de presión y fricción. La inversión en el diseño y la fabricación de estas herramientas representa un coste elevado, pero resulta imprescindible para obtener piezas con tolerancias estrechas y acabados superficiales de alta calidad, lo que a su vez repercute en la reducción de rechazos y en una mayor rentabilidad global del proceso.
La prensa de estirado y embutición no solo es una máquina de deformación, sino también un sistema integrado que influye directamente en la eficiencia de toda una línea de producción. Por ello, los fabricantes han evolucionado hacia soluciones cada vez más automatizadas y conectadas, donde la integración con robots de alimentación, sistemas de visión para control de calidad en línea y softwares de simulación de procesos permite anticipar fallos y optimizar parámetros sin necesidad de largos ensayos físicos. Esto se traduce en una mayor productividad, reducción de costes operativos y capacidad de adaptación a lotes de producción tanto grandes como pequeños. El concepto de flexibilidad es cada vez más importante en este tipo de maquinaria, ya que la industria actual demanda cambios rápidos de formato, producción de series cortas y personalización de piezas sin sacrificar la eficiencia. Una prensa de estirado y embutición moderna es capaz de adaptarse a estas exigencias mediante sistemas modulares de matrices intercambiables, ajustes digitales de parámetros y monitorización continua de la calidad de las piezas fabricadas.
En el proceso de estirado y embutición se manifiestan fenómenos metalúrgicos y mecánicos de gran relevancia que determinan la viabilidad y el éxito de la operación. Uno de los factores más determinantes es la distribución de tensiones que se genera en la chapa cuando el punzón comienza a desplazar el material hacia el interior de la matriz. La zona central, en contacto directo con el punzón, está sometida a un estado de tracción biaxial que tiende a reducir su espesor, mientras que las zonas periféricas, sujetas por el cojín de embutición, experimentan una combinación de compresión circunferencial y tracción radial. Esta compleja interacción de tensiones es la que define si el material se deformará de manera controlada o si aparecerán defectos como arrugas, estricciones o incluso roturas por sobrecarga. En este sentido, cada material tiene un límite de conformabilidad distinto, que está directamente relacionado con su coeficiente de anisotropía plástica, conocido como valor r, y con el índice de endurecimiento por deformación, conocido como valor n. Materiales con valores r elevados presentan mejor capacidad de embutición, ya que resisten mejor la reducción de espesor, mientras que un valor n alto significa que el material tiene mayor resistencia al inicio de la estricción localizada, lo que permite deformaciones más uniformes.
Para garantizar que la chapa seleccionada pueda superar el proceso sin defectos se utilizan ensayos de embutición profunda, como la prueba de Erichsen o la prueba Swift, en las que se mide la profundidad máxima alcanzada por un punzón antes de que se produzca la rotura del material. Estos ensayos permiten establecer parámetros de seguridad en el diseño de matrices y definir los coeficientes de embutición admisibles, es decir, la relación entre el diámetro inicial de la chapa y el diámetro del punzón que puede alcanzarse sin que la pieza falle. En la práctica industrial, los coeficientes de embutición oscilan entre 1,8 y 2,2 dependiendo del material, pero con el empleo de lubricantes adecuados, geometrías optimizadas y prensas de alta precisión es posible llegar a valores aún más exigentes. De este modo, la investigación y el desarrollo en el campo de la embutición profunda se orientan cada vez más hacia el uso de simulaciones numéricas mediante métodos de elementos finitos, que permiten predecir con exactitud la distribución de tensiones, los posibles puntos de fallo y la formación de arrugas, evitando costosos ensayos físicos repetitivos.
Otro aspecto fundamental en las prensas de estirado y embutición es la gestión térmica durante el proceso. Aunque se trata de un conformado en frío, las altas presiones de contacto y la fricción entre chapa y herramienta generan un aumento localizado de la temperatura, lo que modifica temporalmente las propiedades del material y la lubricidad de la interfase. Un control inadecuado de este fenómeno puede dar lugar a una variación en el espesor de las paredes, desgaste irregular de los punzones y matrices, y una reducción en la vida útil de los recubrimientos protectores. Por esta razón, en aplicaciones críticas, se utilizan sistemas de refrigeración integrados en las herramientas, así como lubricantes de alto rendimiento con aditivos para mantener una película estable entre las superficies de contacto. En los últimos años, también se ha explorado el uso de conformado asistido térmicamente, donde se calienta controladamente la chapa antes del proceso para mejorar su ductilidad y permitir mayores profundidades de embutición, especialmente en aleaciones ligeras como el aluminio y el magnesio, que presentan menor conformabilidad en frío.
Desde la perspectiva de aplicaciones industriales, la prensa de estirado y embutición ocupa un lugar central en la producción de piezas para la industria automotriz, donde se requieren componentes estructurales de gran tamaño y alta precisión, tales como paneles de carrocería, cubetas de ruedas, depósitos de combustible y elementos de refuerzo. En el sector de los electrodomésticos, es indispensable para fabricar cubetas interiores de lavadoras, carcasas de motores, paneles exteriores y recipientes metálicos de gran capacidad. En la industria del menaje y utensilios de cocina, permite producir ollas, cacerolas, sartenes y tapas con formas uniformes, bordes lisos y superficies sin defectos, cualidades imprescindibles en productos destinados al consumidor final. Finalmente, en el ámbito de envases metálicos, desde latas para alimentos y bebidas hasta recipientes para productos químicos y cosméticos, el proceso de embutición profunda garantiza uniformidad en el espesor, resistencia mecánica adecuada y un acabado superficial apto para recubrimientos y decoraciones posteriores.
Máquina de Estampado de Piezas Metálicas
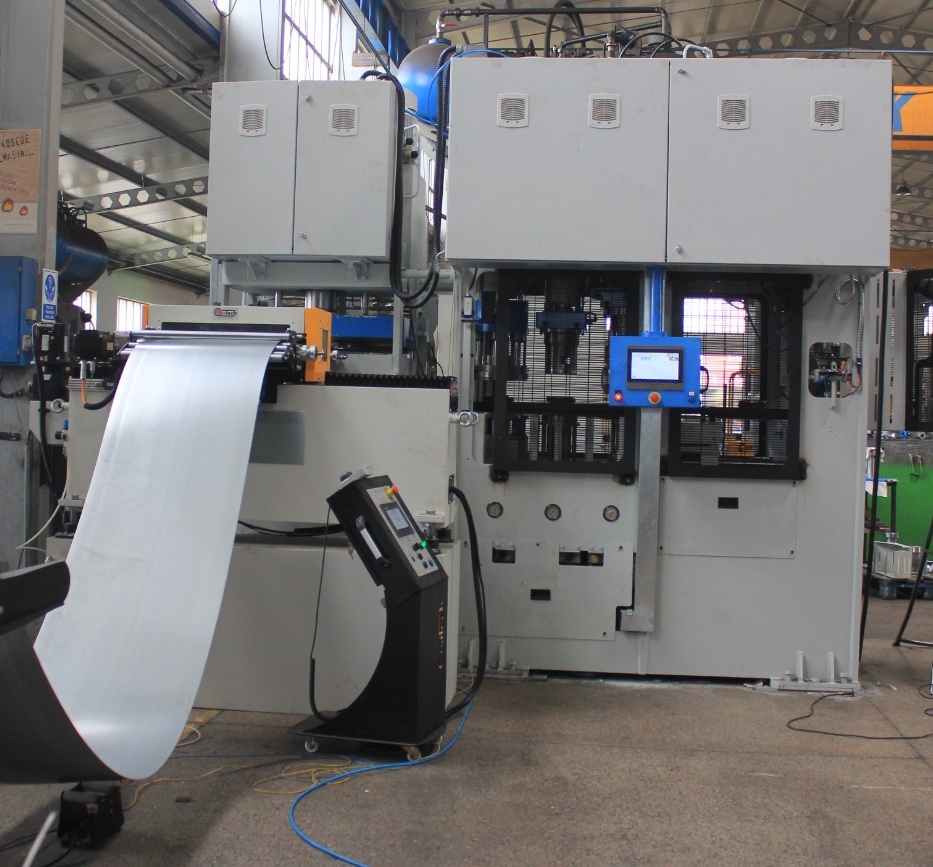
La máquina de estampado de piezas metálicas es un equipo industrial diseñado para transformar chapas metálicas planas en componentes con formas definidas mediante la aplicación de presión controlada sobre un troquel y una matriz. Se trata de una de las tecnologías más difundidas en la industria de transformación del metal, ya que permite producir piezas en grandes volúmenes, con gran precisión dimensional y con un costo unitario muy bajo una vez que la línea está en operación. Su principio de funcionamiento consiste en situar una lámina de metal entre el troquel y la matriz, y ejercer una fuerza a través de un sistema mecánico o hidráulico, generando así el corte, doblado o conformado de la pieza según la geometría diseñada en la herramienta.
Este tipo de máquina puede ser de diferentes configuraciones, siendo las más habituales las prensas mecánicas de volante de inercia, que trabajan a alta velocidad y son idóneas para procesos de estampado en serie con espesores moderados, y las prensas hidráulicas, que ofrecen mayor control sobre la fuerza de estampado y la velocidad de trabajo, lo que las hace adecuadas para piezas de mayor espesor o geometrías complejas. En muchas plantas de producción modernas, las máquinas de estampado se integran en líneas automatizadas con alimentadores de bobina, sistemas de enderezado, robots de transferencia y apiladores de piezas terminadas, logrando procesos continuos con mínima intervención humana.
La versatilidad de estas máquinas permite ejecutar operaciones muy variadas como el corte por punzonado, el doblado de pestañas, la embutición superficial, el repulsado y la acuñación de relieves, entre otras. Gracias a esta diversidad, son fundamentales en la fabricación de piezas automotrices como soportes, refuerzos y componentes de carrocería; en electrodomésticos, para producir paneles, chasis y tapas; en la industria eléctrica, para terminales, conectores y carcasas; y en el sector del menaje, para utensilios, tapas y recipientes metálicos. En función del diseño de los troqueles empleados, la misma máquina puede adaptarse a series cortas y prototipos o a grandes producciones con millones de piezas al año.
Uno de los aspectos más importantes en la operación de una máquina de estampado es la calidad y el diseño de las herramientas. Los troqueles y matrices determinan no solo la forma de la pieza final, sino también su acabado superficial, sus tolerancias y la vida útil del proceso. Por ello, se fabrican con aceros aleados de alta dureza, tratados térmicamente y, en muchos casos, recubiertos con capas de nitruro o revestimientos PVD que reducen el desgaste por fricción. La precisión de la máquina en cuanto a paralelismo, alineación de guías y control de carrera es igualmente crucial, ya que asegura una interacción perfecta entre troquel y matriz, evitando rebabas excesivas, deformaciones indeseadas o variaciones dimensionales.
En los últimos años, la evolución tecnológica ha llevado a que muchas máquinas de estampado incluyan sistemas de control numérico y monitorización en tiempo real. Esto permite registrar fuerzas de estampado, velocidad de ciclo, temperatura de herramientas y otros parámetros críticos, garantizando una producción estable y detectando anomalías antes de que se traduzcan en defectos de gran volumen. De esta manera, la máquina de estampado no solo es un equipo de conformado, sino un nodo clave dentro de la cadena de valor industrial, aportando productividad, repetibilidad y calidad en sectores donde la competitividad depende directamente de la eficiencia del proceso.
La máquina de estampado de piezas metálicas representa uno de los pilares fundamentales dentro de la manufactura moderna de componentes metálicos, no solo por su capacidad de producción masiva, sino también por la precisión y uniformidad que ofrece en cada ciclo de trabajo. El principio básico del estampado se remonta a las primeras prensas mecánicas, pero hoy en día estas máquinas han evolucionado hasta convertirse en sistemas altamente sofisticados, con estructuras rígidas, accionamientos de última generación y controles electrónicos que permiten alcanzar una repetitividad prácticamente perfecta. Cuando se coloca una lámina metálica entre el troquel y la matriz, el golpe controlado de la prensa hace que el material adopte la forma deseada, ya sea mediante corte, doblado, embutición o una combinación de operaciones. Lo fascinante de este proceso es que la transformación ocurre en fracciones de segundo, lo que convierte a la máquina de estampado en una herramienta indispensable para industrias que requieren volúmenes de producción enormes en plazos muy reducidos.
El tipo de máquina que se utilice depende de las necesidades de la aplicación. Las prensas mecánicas de volante son rápidas y eficaces para operaciones de corte y punzonado en chapas delgadas, mientras que las prensas hidráulicas se utilizan cuando se requieren fuerzas más elevadas, velocidades controladas y la posibilidad de realizar embuticiones más profundas o piezas con geometrías complejas. Existen además variantes como las prensas servoaccionadas, que combinan la potencia mecánica con la flexibilidad del control electrónico, lo que permite modificar en tiempo real la curva de velocidad y fuerza durante el ciclo, optimizando el flujo del material y reduciendo defectos. Esta adaptabilidad es especialmente valiosa cuando se trabaja con aceros de alta resistencia o aleaciones ligeras como el aluminio, que presentan un comportamiento de conformado muy distinto al de los aceros convencionales.
Otro elemento decisivo en la eficiencia de una máquina de estampado es la calidad de los troqueles y matrices, que son auténticas piezas de ingeniería de precisión. La geometría de corte, el pulido de las superficies, los radios de transición y los tratamientos aplicados determinan no solo la calidad de la pieza, sino también la durabilidad de la herramienta. En la producción de millones de piezas, una mínima desalineación entre troquel y matriz puede generar miles de unidades defectuosas, lo que repercute en costos muy elevados. Por esta razón, el diseño asistido por ordenador y la simulación por elementos finitos han adquirido una importancia esencial, ya que permiten prever el comportamiento del material bajo las cargas del estampado y ajustar las herramientas antes de su fabricación. Una vez en servicio, estas herramientas requieren un mantenimiento constante, que incluye afilado, limpieza y en algunos casos la aplicación de recubrimientos protectores para reducir el desgaste por fricción y mejorar la calidad superficial de las piezas estampadas.
La automatización ha transformado por completo la manera en que funcionan las máquinas de estampado. En las plantas modernas, rara vez se ve a un operario colocando manualmente una chapa en la matriz. En su lugar, se emplean alimentadores de bobina que desenrollan el material, lo enderezan y lo introducen en la prensa con precisión micrométrica. Robots de transferencia recogen las piezas estampadas y las colocan en estaciones posteriores para operaciones secundarias como rebordeado, soldadura o ensamblaje. Además, sistemas de visión artificial inspeccionan en tiempo real cada pieza, detectando rebabas, grietas o deformaciones que puedan comprometer la calidad del producto final. Todo este ecosistema convierte a la máquina de estampado en el corazón de una línea de producción completamente automatizada, en la que la intervención humana se limita a la supervisión, el mantenimiento y la programación de parámetros de operación.
El campo de aplicación de estas máquinas es inmenso. En la industria automotriz, por ejemplo, la mayor parte de la carrocería de un vehículo moderno está compuesta por piezas estampadas, desde paneles exteriores como puertas y techos, hasta componentes estructurales como largueros y refuerzos internos. En el sector de electrodomésticos, la máquina de estampado produce chasis de lavadoras, tapas de hornos, paneles de refrigeradores y multitud de piezas internas. En la electrónica y electricidad, se utilizan para fabricar conectores, bornes, carcazas y disipadores, donde la precisión dimensional es crítica para garantizar el correcto ensamblaje y funcionamiento. En el menaje de cocina, el estampado permite obtener tapas, bandejas, moldes y utensilios metálicos con bordes definidos y superficies lisas. Incluso en sectores como la aeronáutica o la energía, estas máquinas son esenciales para fabricar componentes metálicos de alta resistencia y tolerancias ajustadas.
Lo que hace verdaderamente valiosa a la máquina de estampado de piezas metálicas no es únicamente su capacidad de producir en serie, sino la combinación de velocidad, precisión y versatilidad que ofrece. Una misma prensa, con los troqueles adecuados, puede producir piezas completamente diferentes, pasando de cortes simples a embuticiones complejas sin necesidad de cambiar la máquina, lo que proporciona a los fabricantes una gran flexibilidad de producción. Esta adaptabilidad, junto con la posibilidad de integración con sistemas de control numérico y monitorización digital, convierte a las máquinas de estampado en herramientas estratégicas para la competitividad de cualquier planta industrial que trabaje con chapa metálica.
Durante el proceso de estampado de piezas metálicas se ponen en juego fenómenos físicos y mecánicos que son determinantes para el éxito de la operación y la calidad de la pieza final. Cuando el troquel entra en contacto con la chapa, el material sufre una combinación de tensiones de tracción y compresión que lo obligan a fluir hacia la geometría impuesta por la matriz. En el caso del corte, la chapa se somete a esfuerzos cortantes que generan una zona de cizalladura hasta que se produce la separación completa. La precisión de este corte depende en gran medida del paralelismo entre troquel y matriz, de la holgura entre ambos y de la calidad del material de la herramienta. Una holgura demasiado pequeña aumenta el desgaste de las matrices y puede provocar rebordes en la pieza, mientras que una holgura excesiva genera rebabas pronunciadas y una calidad deficiente de los bordes. En operaciones de doblado, el material se deforma plásticamente alrededor de un radio impuesto, y el comportamiento depende tanto del límite elástico del material como de su coeficiente de endurecimiento por deformación. Es aquí donde los cálculos de recuperación elástica se vuelven cruciales, ya que el metal tiende a volver parcialmente a su forma original tras la descarga de tensiones, lo que obliga a diseñar ángulos de doblado compensados para alcanzar las medidas finales deseadas.
Cuando se realizan procesos de embutición en máquinas de estampado, el flujo del material se vuelve aún más complejo porque, además del contacto directo con el punzón y la matriz, intervienen fenómenos de fricción y retención controlados por dispositivos como cojines neumáticos o hidráulicos. En esta etapa, el material debe redistribuirse de manera uniforme para evitar tanto el adelgazamiento excesivo que conduce a roturas como la acumulación de material que produce arrugas. El diseño del radio de la matriz, la velocidad de penetración del punzón y la presión del cojín son parámetros que deben armonizarse con gran precisión. Por esta razón, muchas máquinas modernas de estampado incorporan sistemas servoaccionados capaces de variar la velocidad del troquel en diferentes fases del ciclo, reduciéndola en la entrada inicial para permitir el correcto asentamiento del material y acelerándola posteriormente para mejorar la productividad sin sacrificar calidad.
Los materiales metálicos, al ser sometidos a estos procesos de alta velocidad y presión, presentan comportamientos que no siempre son lineales ni predecibles. La anisotropía de la chapa, que proviene del proceso de laminación durante su fabricación, influye de manera directa en cómo se distribuyen los esfuerzos y en la tendencia del material a arrugarse o a fracturarse en determinadas direcciones. Es por ello que, en el diseño de troqueles y matrices, se tienen en cuenta no solo las propiedades mecánicas nominales del material, sino también su dirección de laminación y sus valores de anisotropía plástica. Esto permite orientar la chapa en el sentido más favorable para el estampado, incrementando la profundidad alcanzable y reduciendo el riesgo de fallos. Además, con el avance de la simulación por elementos finitos, es posible predecir estos comportamientos antes de fabricar las herramientas, lo que supone un ahorro de tiempo y recursos muy significativo.
Desde el punto de vista productivo y económico, la máquina de estampado de piezas metálicas es insustituible porque permite transformar grandes cantidades de materia prima en productos terminados con un coste unitario extremadamente bajo. La inversión inicial en la prensa y en los troqueles puede ser elevada, pero una vez puesta en marcha, la capacidad de producir miles de piezas idénticas por hora hace que el coste de cada unidad se reduzca drásticamente. Esto es lo que explica que sectores como el automotriz o el de envases dependan de manera absoluta de estas tecnologías. Además, la integración con sistemas de alimentación automática de bobinas y la posibilidad de trabajar con líneas progresivas, en las que una tira de chapa avanza a través de varias estaciones de troquelado para obtener una pieza completamente terminada en una sola pasada, multiplican aún más la eficiencia del proceso. Esta filosofía de producción continua permite eliminar operaciones secundarias y reducir los tiempos de manipulación, lo que se traduce en mayores índices de productividad y en un mejor aprovechamiento de la materia prima.
El impacto de la máquina de estampado no solo se mide en términos de cantidad producida, sino también en calidad y consistencia. La posibilidad de fabricar piezas con tolerancias muy ajustadas, acabados superficiales limpios y geometrías repetitivas convierte al estampado en una técnica clave para la competitividad de cualquier industria. El avance hacia prensas servoaccionadas y sistemas de monitorización en tiempo real garantiza que cada golpe de la máquina se ejecute bajo parámetros controlados, registrando datos de fuerza, velocidad y desplazamiento que se utilizan para asegurar la trazabilidad de la producción y para implementar estrategias de mantenimiento predictivo. Con ello, la máquina de estampado deja de ser una simple prensa para convertirse en un centro de producción inteligente, capaz de adaptarse a distintos materiales, geometrías y volúmenes sin perder eficiencia ni fiabilidad.
En las líneas modernas de producción, la máquina de estampado de piezas metálicas ya no funciona como un equipo aislado, sino como parte de un sistema integrado conocido como línea de estampado progresiva. Este tipo de configuración consiste en una serie de estaciones de trabajo dispuestas dentro de un mismo troquel, donde la chapa metálica en forma de tira avanza paso a paso, sincronizada con cada golpe de la prensa, para ir recibiendo distintas operaciones hasta convertirse en una pieza terminada al final del recorrido. El proceso comienza con la alimentación de la bobina metálica, que se desenrolla y se endereza para eliminar tensiones internas y ondulaciones. Una vez alineada, la tira entra en la prensa y es sujeta con precisión mediante sistemas de guía que garantizan el avance exacto en cada ciclo. En la primera estación se realiza generalmente un punzonado inicial o un recorte de referencia, y a partir de ahí la chapa avanza a través de varias estaciones donde se van ejecutando operaciones como corte, doblado, embutición parcial, acuñado de detalles y finalmente el corte de separación de la pieza acabada.
La ventaja de este sistema radica en que, en lugar de tener que trasladar la pieza entre distintas prensas o máquinas para cada operación, todas las etapas se realizan en una sola línea y en un único ciclo de trabajo, lo que reduce enormemente los tiempos de producción y asegura una uniformidad absoluta. Además, al trabajar con tiras continuas, el aprovechamiento del material es más eficiente, pues se minimizan los recortes sobrantes y se pueden diseñar patrones de troquelado que optimicen la distribución de las piezas dentro de la banda metálica. Para que todo esto funcione con la máxima precisión, el sincronismo entre la prensa, el alimentador de bobina y los sistemas de guiado debe ser perfecto, y por ello las máquinas de estampado progresivo están equipadas con controles electrónicos avanzados, servomotores y sensores que supervisan en todo momento la posición de la tira y la correcta ejecución de cada operación.
En aplicaciones donde se requiere una mayor flexibilidad o series de producción más cortas, se emplean también sistemas de estampado transfer, en los cuales la pieza cortada se transfiere mediante brazos mecánicos o robots de una estación a otra, permitiendo operaciones más complejas y tridimensionales que no serían posibles en un troquel progresivo convencional. Este tipo de máquinas, aunque menos rápidas en comparación con las progresivas, ofrecen una adaptabilidad superior y son muy utilizadas en la industria automotriz y de electrodomésticos para piezas de gran tamaño o geometrías complicadas. En ambos casos, la tendencia actual es integrar la máquina de estampado en entornos completamente automatizados, donde desde la alimentación del material hasta la extracción y apilado de las piezas se realiza sin intervención humana directa, lo que incrementa no solo la productividad, sino también la seguridad en el lugar de trabajo al reducir el riesgo de accidentes.
La innovación tecnológica reciente ha transformado de manera radical las capacidades de estas máquinas. Las servoprensas, por ejemplo, han abierto un nuevo horizonte en el estampado al permitir un control total de la velocidad y posición del émbolo en cada fase del ciclo. A diferencia de las prensas mecánicas tradicionales, que trabajan con una curva de movimiento fija determinada por la geometría del cigüeñal, las servoprensas permiten programar perfiles de movimiento personalizados, adaptando la velocidad en tiempo real para optimizar el flujo del material y reducir los esfuerzos sobre las herramientas. Esto no solo mejora la calidad de las piezas, sino que también prolonga la vida útil de los troqueles y permite trabajar con materiales avanzados como aceros de ultra alta resistencia o aleaciones ligeras de aluminio y magnesio, que presentan mayores desafíos en el conformado. La posibilidad de programar ciclos lentos para embuticiones profundas y ciclos rápidos para cortes o doblados simples en una misma máquina multiplica la versatilidad y la eficiencia del proceso.
Por otro lado, la incorporación de sistemas de monitorización digital y de mantenimiento predictivo ha elevado la confiabilidad de las máquinas de estampado a niveles inéditos. Sensores distribuidos en la prensa miden en tiempo real parámetros como fuerza aplicada, vibraciones, temperatura de cojinetes, consumo de energía y desplazamiento del émbolo. Estos datos son procesados por algoritmos que detectan desviaciones con respecto a los valores nominales y anticipan posibles fallos antes de que se produzcan paradas no programadas. De esta forma, se pasa de un esquema de mantenimiento correctivo o preventivo tradicional a un enfoque predictivo, donde las intervenciones se realizan solo cuando son necesarias y con plena planificación, evitando tiempos muertos y maximizando la disponibilidad de la máquina. Además, esta digitalización facilita la trazabilidad completa de la producción, de modo que cada lote de piezas puede asociarse con los parámetros exactos bajo los cuales fue fabricado, garantizando un control de calidad exhaustivo que resulta vital en sectores como el automotriz y el aeronáutico.
La evolución de la máquina de estampado de piezas metálicas, desde las prensas mecánicas convencionales hasta las líneas progresivas automatizadas y las servoprensas inteligentes, refleja cómo la industria del conformado metálico se ha ido adaptando a las demandas de mayor productividad, precisión, flexibilidad y competitividad. Hoy en día, invertir en este tipo de equipos no solo significa adquirir una prensa, sino dotar a la planta de un sistema productivo integral capaz de responder a la diversidad de diseños y materiales que exige el mercado global. De esta manera, la máquina de estampado deja de ser vista como un simple equipo de taller para convertirse en un núcleo estratégico dentro de la cadena de valor industrial, donde cada golpe de troquel no solo da forma al metal, sino que marca la diferencia entre la eficiencia convencional y la manufactura de alto rendimiento.
¿Quieres que lo siga ampliando hacia una explicación más centrada en el impacto económico y estratégico de estas máquinas en la industria manufacturera, o prefieres que continúe profundizando en los aspectos físicos del material durante el estampado, como endurecimiento, recuperación elástica y límites de conformabilidad?
Prensa de Embutición Industrial
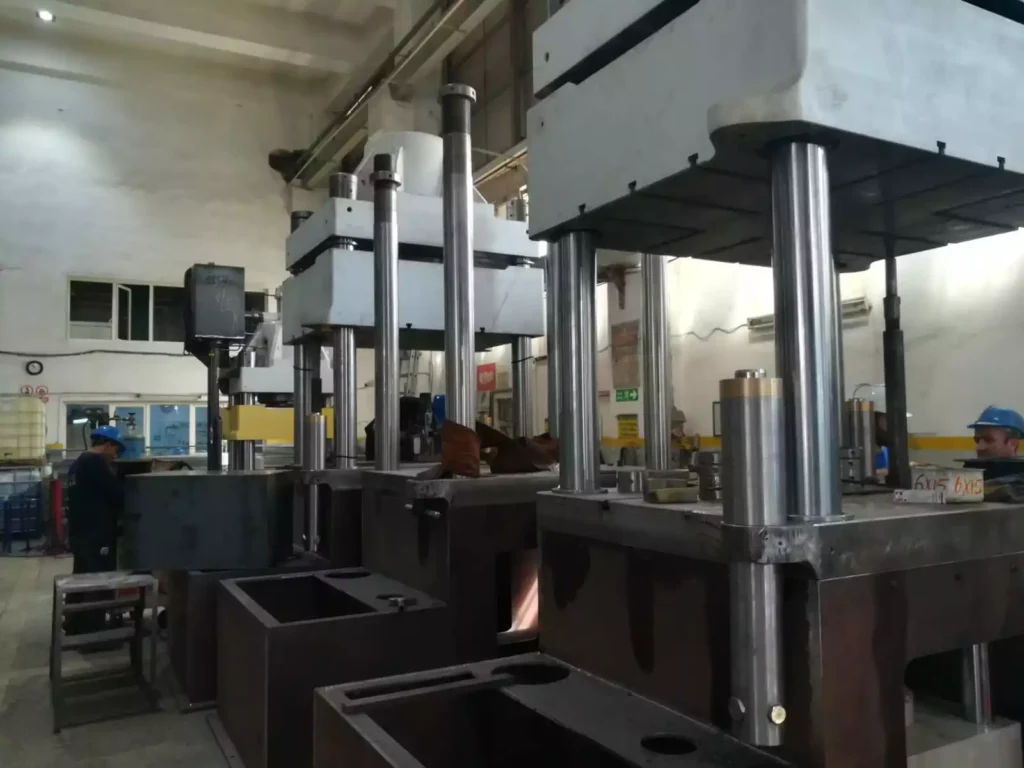
La prensa de embutición industrial es un equipo fundamental en la transformación de chapa metálica, diseñada para realizar operaciones de embutición profunda y conformado de piezas complejas mediante la aplicación de fuerzas controladas sobre un punzón y una matriz. Su funcionamiento se basa en la deformación plástica del material, donde la chapa se desplaza y adapta a la forma de la cavidad del troquel, produciendo piezas con geometrías tridimensionales precisas, paredes lisas y espesores controlados. Estas prensas se diferencian de otras por su capacidad de manejar embuticiones profundas, lo que significa que pueden conformar piezas con alturas superiores al diámetro inicial de la chapa, algo que es esencial en la fabricación de componentes automotrices, recipientes metálicos, electrodomésticos, utensilios de cocina y otros productos industriales de gran volumen.
Una característica clave de la prensa de embutición industrial es su sistema de control de presión, que puede ser hidráulico, mecánico o servoaccionado, dependiendo del modelo y de la complejidad de las piezas a producir. El control de la presión aplicada sobre la chapa mediante un cojín de embutición permite mantener un flujo uniforme del material y evita defectos como arrugas, estrangulamientos o roturas. Las prensas hidráulicas son especialmente valoradas por su capacidad de ejercer fuerzas precisas y constantes durante todo el ciclo de trabajo, mientras que las servoprensas permiten programar perfiles de velocidad y presión adaptables a cada fase de la operación, optimizando la calidad de la pieza y prolongando la vida útil de las herramientas.
El diseño de las herramientas, punzones y matrices es determinante en el rendimiento de la prensa de embutición industrial. La geometría de la matriz, el radio de transición, el pulido de las superficies y los tratamientos superficiales aplicados a los aceros de alta dureza utilizados en las herramientas garantizan un flujo controlado del material y reducen el desgaste por fricción. En piezas de alta precisión o producción masiva, los fabricantes recurren a recubrimientos avanzados y tratamientos térmicos que aseguran la estabilidad dimensional de la matriz durante millones de ciclos de trabajo, evitando la aparición de defectos y manteniendo la uniformidad de las piezas.
La automatización de la prensa de embutición industrial ha evolucionado significativamente, integrándose en líneas de producción completamente controladas, donde sistemas de alimentación de bobina, enderezado de chapa, robots de transferencia y apiladores automáticos permiten que el proceso sea continuo, seguro y eficiente. La monitorización digital de parámetros críticos, como fuerza aplicada, velocidad del punzón, posición y temperatura de la herramienta, permite ajustar el ciclo en tiempo real y detectar cualquier desviación que pueda afectar la calidad de la pieza, transformando a la prensa en un equipo inteligente dentro de la línea de producción.
Las aplicaciones de la prensa de embutición industrial son muy amplias. En la industria automotriz se utilizan para fabricar depósitos, carcasas, cubetas, paneles y componentes estructurales de alta resistencia; en electrodomésticos, para carcasas de motores, cubetas, tapas y paneles; en menaje de cocina, para ollas, cacerolas, tapas y utensilios metálicos; y en envases metálicos, para producir recipientes de alimentos, bebidas y cosmética, donde la uniformidad del espesor y la calidad superficial son esenciales. La capacidad de producir piezas complejas con tolerancias estrechas y gran repetitividad convierte a la prensa de embutición industrial en un elemento estratégico para cualquier planta de fabricación que busque productividad, eficiencia y calidad.
Si quieres, puedo continuar ampliando este texto en detalle técnico-extenso, explicando los fenómenos físicos que ocurren durante la embutición, como la distribución de tensiones, el flujo del material, la recuperación elástica y los límites de conformabilidad de los distintos metales. Esto daría un nivel de profundidad comparable al de un manual de ingeniería industrial.
La operación de una prensa de embutición industrial involucra fenómenos físicos y mecánicos complejos que determinan la calidad y la viabilidad de cada pieza fabricada. Cuando la chapa metálica se coloca sobre la matriz y el punzón desciende, el material experimenta un estado de tensiones combinado: tracción en las zonas que fluyen hacia el fondo de la cavidad y compresión en las áreas sujetas por el cojín de embutición. Esta interacción genera un flujo plástico del metal, que se adapta a la geometría de la matriz sin romperse ni arrugarse si los parámetros de presión, velocidad y lubricación están correctamente controlados. La fricción entre la chapa y las superficies de la herramienta es crítica; un exceso de fricción puede causar desgarramientos o estrangulamientos, mientras que una fricción insuficiente puede provocar arrugas o desplazamientos irregulares del material. Por esta razón, se utilizan lubricantes especializados y recubrimientos de alta resistencia en punzones y matrices, que permiten mantener un flujo de material uniforme y prolongar la vida útil de la prensa, especialmente en producciones de alto volumen.
El diseño de las herramientas es un aspecto fundamental en el desempeño de la prensa de embutición industrial. La geometría de la matriz, los radios de transición, la superficie del punzón y la alineación exacta entre ambos elementos determinan cómo se distribuyen las tensiones en la chapa durante el ciclo de embutición. Los radios demasiado pequeños concentran esfuerzos y pueden provocar fracturas, mientras que los radios demasiado grandes reducen la profundidad alcanzable y afectan la precisión dimensional de la pieza. Para garantizar resultados óptimos, se utilizan simulaciones por elementos finitos que permiten anticipar deformaciones, zonas de posible fallo y adelgazamientos críticos, optimizando tanto la geometría de la herramienta como los parámetros de operación antes de realizar ensayos físicos, lo que reduce costes y tiempos de desarrollo. Además, los tratamientos térmicos y recubrimientos aplicados a las matrices y punzones, como nitruración o recubrimientos PVD, aumentan la resistencia al desgaste y a la fricción, asegurando que la precisión y el acabado de las piezas se mantengan incluso después de millones de ciclos de producción.
La automatización en las prensas de embutición industriales ha alcanzado niveles muy avanzados, integrando sistemas de alimentación de bobina, enderezado de chapas, robots de manipulación y apiladores automáticos. En estas configuraciones, la intervención humana se limita a la supervisión y al mantenimiento, mientras que la producción se realiza de manera continua y controlada. Los sistemas de control electrónico permiten monitorizar en tiempo real parámetros como la fuerza aplicada, la velocidad del punzón, la posición de la chapa y la temperatura de las herramientas, ajustando el ciclo automáticamente para mantener la calidad de cada pieza. Esta monitorización digital no solo garantiza uniformidad, sino que también habilita estrategias de mantenimiento predictivo, anticipando desgastes o fallas antes de que provoquen paradas no programadas, aumentando la disponibilidad de la máquina y optimizando los tiempos de producción.
En cuanto a la aplicación industrial, la prensa de embutición industrial es imprescindible en sectores donde la precisión, la repetibilidad y la resistencia de las piezas son críticas. En la automoción, permite fabricar depósitos de combustible, cubetas, carcasas de transmisión y componentes estructurales que requieren espesores uniformes y geometrías complejas. En electrodomésticos, produce carcasas, paneles, cubetas y tapas con acabados lisos y tolerancias precisas. En menaje de cocina, se fabrican ollas, sartenes, tapas y utensilios metálicos con paredes uniformes y formas definidas, mientras que en envases metálicos permite obtener latas, recipientes de alimentos, cosméticos o químicos con espesores constantes y acabados superficiales aptos para recubrimientos decorativos o funcionales. La combinación de alta productividad, capacidad de embutición profunda y control dimensional convierte a esta máquina en un componente estratégico dentro de cualquier planta de fabricación de metal, asegurando eficiencia, competitividad y calidad constante en la producción.
Si quieres, puedo seguir desarrollando este tema explicando con aún más detalle los fenómenos metalúrgicos que ocurren durante la embutición, como el endurecimiento por deformación, la recuperación elástica, la anisotropía del material y los límites de conformabilidad según distintos tipos de acero y aleaciones ligeras, lo que daría un nivel de profundidad comparable al de un manual técnico especializado.
El proceso de embutición industrial no solo depende de la prensa y las herramientas, sino también de las propiedades intrínsecas del material, ya que la chapa metálica responde a la deformación de manera compleja. Durante la operación, el material experimenta un endurecimiento por deformación progresivo que incrementa su resistencia conforme se somete a tensiones plásticas, especialmente en zonas donde se produce un flujo concentrado hacia el fondo de la matriz. Este fenómeno, conocido como endurecimiento por trabajo, puede ser beneficioso al aumentar la rigidez de las paredes conformadas, pero también limita la capacidad de estiramiento del metal y puede provocar fracturas si no se controla adecuadamente. Por eso es fundamental conocer la composición del material, su límite elástico, el coeficiente de anisotropía plástica y el índice de endurecimiento por deformación, ya que estos factores determinan la profundidad máxima alcanzable en la embutición sin comprometer la integridad de la pieza.
La recuperación elástica del material es otro factor crítico que influye en la precisión dimensional de las piezas. Tras el retiro de la fuerza aplicada por el punzón, el metal tiende a recuperar parcialmente su forma original, lo que puede generar rebote o deformaciones residuales. Este efecto es especialmente notable en aceros de alta resistencia y aleaciones ligeras como aluminio y magnesio, que poseen mayores límites elásticos. Para compensar la recuperación elástica, los diseñadores de matrices calculan radios y formas ligeramente ajustadas, anticipando el comportamiento del metal y asegurando que la pieza final cumpla con las tolerancias requeridas. La comprensión de estos fenómenos permite, además, programar curvas de velocidad y presión en prensas servoaccionadas que minimicen el rebote, distribuyendo la carga de manera gradual y controlada.
La anisotropía de la chapa, resultante de su proceso de laminación, determina cómo fluye el material durante la embutición y afecta directamente la formación de defectos como arrugas o estrangulamientos. Una chapa con alto grado de anisotropía tenderá a fluir más fácilmente en una dirección que en otra, lo que exige orientar correctamente el material antes del proceso y ajustar los parámetros de presión y lubricación. Los lubricantes especializados y recubrimientos de matriz y punzón no solo reducen la fricción, sino que también favorecen un flujo uniforme del metal, permitiendo alcanzar mayores profundidades sin comprometer la superficie ni la geometría de la pieza. La selección del tipo de lubricante y su aplicación son cruciales, ya que cualquier fallo en este aspecto puede traducirse en arrugas, roturas o desgaste prematuro de las herramientas.
En términos de productividad, la prensa de embutición industrial permite integrar todo el proceso en líneas automatizadas de alta eficiencia. La alimentación de bobinas, enderezado de chapa, manipulación por robots, apilado y control de calidad se realizan de manera continua, garantizando uniformidad en cada pieza y reduciendo los tiempos muertos. La monitorización digital avanzada permite registrar fuerzas aplicadas, desplazamientos, velocidad y temperatura, generando información en tiempo real que se utiliza tanto para controlar la calidad como para implementar mantenimiento predictivo. Esto asegura la disponibilidad de la máquina y la consistencia de la producción incluso en series de millones de piezas.
La aplicación industrial de estas prensas es muy amplia y crítica para sectores donde la calidad y la repetibilidad son esenciales. En la automoción, las prensas de embutición producen depósitos de combustible, cubetas, carcasas de transmisión y componentes estructurales que requieren paredes uniformes y geometrías complejas. En electrodomésticos, fabrican carcasas, cubetas y tapas con acabados superficiales precisos y tolerancias estrictas. En menaje y utensilios de cocina, producen ollas, sartenes y recipientes metálicos de forma uniforme, mientras que en envases metálicos generan latas, contenedores y recipientes para alimentos, bebidas y productos cosméticos. La combinación de capacidad de embutición profunda, control dimensional preciso y producción continua convierte a la prensa de embutición industrial en un equipo estratégico para cualquier planta que busque eficiencia, alta productividad y calidad constante.
Si quieres, puedo seguir ampliando este tema con un nivel aún más técnico sobre cálculos de tensiones, deformaciones, radios de matriz y presión de cojín, explicando cómo se optimizan todos estos parámetros en ingeniería para lograr piezas complejas sin defectos y con alta repetibilidad.
La ingeniería detrás de la prensa de embutición industrial requiere un conocimiento profundo de la mecánica de materiales y de la metalurgia, ya que cada parámetro del proceso influye directamente en la calidad de la pieza final y en la vida útil de las herramientas. La fuerza aplicada por el punzón debe calcularse cuidadosamente en función del espesor de la chapa, su límite elástico, el coeficiente de fricción y la geometría de la pieza. Para embuticiones profundas, la presión del cojín se ajusta de manera que las zonas periféricas de la chapa fluyan suavemente hacia el fondo de la matriz, evitando arrugas en los bordes o estrangulamientos que podrían provocar fracturas. Este balance de fuerzas requiere precisión milimétrica y control en tiempo real, especialmente en materiales de alta resistencia, donde un error mínimo puede generar daños irreversibles en la pieza o en la matriz. Además, la velocidad de penetración del punzón influye directamente en el flujo del material: una velocidad demasiado alta puede inducir vibraciones o rebotes que afectan la uniformidad del espesor, mientras que una velocidad demasiado baja puede provocar un flujo desigual y concentraciones de tensión que reducen la profundidad alcanzable.
El cálculo de radios de transición en punzones y matrices es uno de los aspectos más críticos en el diseño de la prensa de embutición. Radios demasiado pequeños concentran esfuerzos y pueden inducir fisuras, mientras que radios demasiado grandes limitan la conformabilidad del metal y la precisión dimensional de la pieza. Para optimizar estos parámetros, se utilizan herramientas de simulación por elementos finitos que permiten modelar el flujo del material bajo distintas condiciones de presión, fricción y velocidad, anticipando zonas de posible adelgazamiento o arrugas antes de la fabricación física de la matriz. Esta metodología permite reducir costes y acelerar el desarrollo de nuevos productos, garantizando que cada ciclo de la prensa produzca piezas dentro de las tolerancias requeridas sin comprometer la integridad del material.
Otro fenómeno relevante es la anisotropía del material, que proviene del proceso de laminación y afecta la dirección preferencial de flujo de la chapa durante la embutición. La orientación correcta de la chapa respecto a la dirección de laminación es determinante para evitar defectos, y en algunos casos se realizan ensayos preliminares para determinar la mejor disposición de la banda metálica en la prensa. Además, la lubricación desempeña un papel esencial, ya que la fricción entre chapa y matriz regula el flujo del material: un coeficiente de fricción demasiado alto puede causar estrangulamiento, mientras que uno demasiado bajo puede inducir arrugas o movimientos irregulares. Por ello, se emplean lubricantes de alto rendimiento y recubrimientos especializados en punzones y matrices, combinando resistencia al desgaste con propiedades que favorecen un flujo uniforme y constante del metal.
En términos de productividad y eficiencia, la prensa de embutición industrial se integra cada vez más en líneas completamente automatizadas, donde la alimentación de bobina, el enderezado de la chapa, la manipulación mediante robots y el apilado de piezas se realizan de manera continua. La incorporación de sistemas de monitorización digital permite registrar fuerzas, desplazamientos, velocidades y temperaturas en tiempo real, facilitando ajustes inmediatos y garantizando uniformidad en cada pieza producida. Esta información también se utiliza para mantenimiento predictivo, anticipando desgastes y posibles fallas antes de que provoquen paradas no programadas, incrementando la disponibilidad de la máquina y reduciendo costes operativos.
El impacto industrial de estas prensas es muy amplio: en automoción permiten fabricar depósitos de combustible, cubetas, carcasas y componentes estructurales de gran complejidad; en electrodomésticos producen carcasas, tapas y paneles con acabados lisos y tolerancias estrictas; en menaje y utensilios de cocina generan ollas, sartenes y recipientes metálicos uniformes; y en envases metálicos permiten la producción masiva de latas y contenedores con espesores consistentes y superficies aptas para decoración o recubrimientos funcionales. La combinación de capacidad de embutición profunda, precisión dimensional, flujo controlado del material y producción automatizada convierte a la prensa de embutición industrial en un elemento estratégico para cualquier planta que busque competitividad, eficiencia y calidad sostenida.
Si quieres, puedo continuar desarrollando este tema en un nivel técnico todavía más avanzado, explicando cómo se calculan las tensiones máximas, los espesores mínimos, los radios de matriz óptimos, la presión de cojín y cómo se integran todos estos parámetros en la ingeniería de procesos para lograr piezas complejas de manera repetitiva y sin defectos.
Prensa de Estampación de Chapas Metálicas
La prensa de estampación de chapas metálicas es un equipo industrial diseñado para transformar láminas planas de metal en piezas con formas específicas mediante la aplicación de fuerzas controladas sobre un troquel y una matriz. Su función principal es conformar, cortar o punzonar chapas de distintos espesores, logrando piezas de geometría precisa y acabado superficial uniforme, lo que la hace indispensable en industrias como la automotriz, electrodomésticos, menaje de cocina, envases metálicos y componentes eléctricos. Estas prensas operan aplicando presión mecánica, hidráulica o servoaccionada, dependiendo del tipo de material y de la complejidad de la pieza, permitiendo desde operaciones de corte simples hasta embuticiones y repulsados más profundos y complejos. La prensa puede trabajar con chapas de acero, aluminio, cobre, latón y aleaciones especiales, adaptando su fuerza, velocidad y recorrido del émbolo a las características específicas de cada material.
El funcionamiento de la prensa de estampación se basa en la interacción precisa entre troquel, matriz y chapa metálica. Cuando la chapa se coloca entre estos elementos, el golpe del punzón provoca que el material fluya y adopte la forma del troquel, produciendo cortes, relieves o deformaciones según la operación deseada. Para lograr resultados óptimos, se deben considerar factores como el espesor de la chapa, su límite elástico, la fricción entre metal y herramienta, y la presión aplicada. El control de estos parámetros es esencial para evitar defectos como rebabas, arrugas, estrangulamientos o deformaciones indeseadas. En prensas modernas, los sistemas hidráulicos y servoaccionados permiten ajustar la velocidad de carrera, la fuerza aplicada y el tiempo de permanencia bajo presión, lo que mejora la precisión dimensional, protege las herramientas y optimiza la calidad superficial de la pieza.
El diseño de los troqueles y matrices es determinante en el desempeño de la prensa de estampación. Las herramientas se fabrican con aceros de alta dureza y tratamientos térmicos avanzados para resistir millones de ciclos de trabajo sin perder precisión. Además, los recubrimientos especiales reducen la fricción y aumentan la durabilidad, permitiendo mantener la calidad de corte y conformado incluso en series de producción masivas. La geometría de los troqueles, los radios de transición y el acabado de las superficies influyen directamente en cómo fluye la chapa, afectando tanto la profundidad alcanzable como la uniformidad del espesor y la superficie final. Para optimizar el diseño, se utilizan simulaciones por elementos finitos que anticipan el comportamiento del metal bajo carga, permitiendo corregir posibles zonas de fallo antes de fabricar la herramienta física.
La automatización ha transformado las prensas de estampación en centros de producción inteligentes. Las líneas modernas incorporan sistemas de alimentación de bobina, enderezado de chapa, robots de transferencia, inspección por visión artificial y apiladores automáticos, garantizando un flujo continuo de piezas con mínima intervención humana. Los sensores monitorizan fuerza, velocidad, desplazamiento y temperatura en tiempo real, permitiendo ajustes automáticos para mantener tolerancias estrictas y uniformidad en cada pieza. Esta integración de control y automatización no solo aumenta la productividad, sino que también mejora la seguridad en la planta, reduce tiempos muertos y permite implementar mantenimiento predictivo, anticipando desgastes y evitando paradas no planificadas.
En cuanto a su aplicación, la prensa de estampación de chapas metálicas es versátil y estratégica. En la industria automotriz produce paneles de carrocería, refuerzos estructurales, tapas y componentes interiores. En electrodomésticos, se utilizan para carcasas, cubetas, tapas y chasis de equipos. En menaje de cocina, fabrican ollas, sartenes, bandejas y utensilios metálicos con acabados precisos, mientras que en la industria de envases generan latas, recipientes y tapas con espesores uniformes y superficies listas para recubrimientos decorativos o funcionales. La combinación de velocidad, precisión y repetibilidad convierte a la prensa de estampación en un equipo indispensable para la fabricación moderna de piezas metálicas, donde la eficiencia y la calidad son factores críticos para la competitividad industrial.
Si quieres, puedo continuar desarrollando este tema en un nivel aún más técnico, explicando los fenómenos físicos que ocurren durante la estampación, como el flujo del material, concentración de tensiones, límites de deformación y optimización de troqueles para distintas aleaciones y espesores de chapa.
La prensa de estampación de chapas metálicas representa un elemento central en la fabricación industrial moderna debido a su capacidad de transformar láminas planas en piezas tridimensionales con alta precisión y repetibilidad. El proceso de estampación combina fenómenos de corte, tracción, compresión y fluido plástico del material, donde la chapa se deforma bajo fuerzas controladas para adoptar la geometría del troquel. Cada golpe del punzón genera un flujo de material que debe ser uniforme, evitando zonas de adelgazamiento excesivo, arrugas o fracturas. La distribución de tensiones en la chapa depende de la forma de la matriz, del radio de transición, del espesor del material, del coeficiente de fricción y de la velocidad de penetración del punzón, factores que se calibran cuidadosamente para garantizar que cada pieza cumpla con las tolerancias requeridas. El control de estos parámetros es particularmente crítico en operaciones de embutición profunda, donde la chapa debe estirarse considerablemente sin superar su límite de conformabilidad, y en piezas con geometrías complejas, donde los cambios abruptos de sección pueden generar concentraciones de tensiones que provoquen fallos prematuros.
El diseño de los troqueles y matrices es un aspecto estratégico, ya que determina la calidad superficial, la exactitud dimensional y la vida útil de la herramienta. Los troqueles se fabrican con aceros de alta dureza sometidos a tratamientos térmicos que aumentan su resistencia al desgaste y a la deformación. Las superficies de contacto se pulen y, en muchos casos, se recubren con materiales de baja fricción o con recubrimientos PVD, lo que permite un flujo del material más uniforme y reduce la fricción, prolongando la vida útil de la prensa y de la herramienta. Además, el uso de simulaciones por elementos finitos permite anticipar problemas como concentraciones de tensiones, arrugas o adelgazamientos excesivos antes de fabricar físicamente la herramienta, optimizando el diseño y evitando costosos errores en la producción. En la práctica, cada matriz se ajusta a las características específicas de la chapa, considerando no solo el tipo de metal, sino también la dirección de laminación, el grado de anisotropía y el comportamiento frente al endurecimiento por deformación.
Las prensas modernas de estampación están equipadas con sistemas de control avanzados que permiten ajustar la velocidad, la fuerza y la posición del punzón en tiempo real. En prensas servoaccionadas, estas variables se pueden programar de manera personalizada para cada fase del ciclo, lo que mejora el flujo del material, reduce el rebote y minimiza el riesgo de defectos. La automatización completa permite integrar alimentación de bobina, enderezado de chapa, manipulación por robots, inspección visual y apilado automático, creando líneas de producción altamente eficientes y seguras. Los sensores distribuidos en la prensa registran parámetros como fuerza aplicada, desplazamiento del punzón, velocidad de carrera y temperatura de la herramienta, permitiendo ajustes instantáneos y generando datos útiles para mantenimiento predictivo y trazabilidad de cada pieza producida. Esto asegura que la calidad se mantenga constante incluso en series de producción masiva y que se reduzcan las paradas no planificadas, incrementando la disponibilidad y eficiencia de la planta.
La aplicación industrial de la prensa de estampación de chapas metálicas es extremadamente amplia y crítica para sectores que requieren precisión y repetibilidad. En la industria automotriz, estas prensas producen paneles de carrocería, tapas, refuerzos estructurales y componentes internos que requieren espesores uniformes y geometrías complejas. En electrodomésticos, se fabrican carcasas, cubetas, tapas y chasis con acabados superficiales lisos y tolerancias estrictas. En menaje de cocina, la prensa permite obtener ollas, sartenes, bandejas y utensilios metálicos con paredes uniformes y formas definidas. En envases metálicos, la producción de latas, tapas y contenedores exige espesores consistentes, acabados de superficie impecables y geometrías exactas para permitir procesos posteriores de recubrimiento o impresión. La combinación de velocidad de producción, precisión dimensional, control del flujo del material y automatización convierte a la prensa de estampación en un equipo estratégico que asegura competitividad, eficiencia y calidad constante dentro de cualquier planta industrial moderna.
Si quieres, puedo continuar ampliando el tema explicando los aspectos más avanzados del flujo de material durante la estampación, incluyendo diagramas de distribución de tensiones, zonas de adelgazamiento, arrugas, recuperación elástica y cómo se optimizan los troqueles y la velocidad del punzón para distintos tipos de acero y aleaciones ligeras, con un nivel técnico comparable al de un manual de ingeniería especializada.
El comportamiento del material durante la estampación de chapas metálicas es un aspecto fundamental que determina la calidad final de la pieza y la eficiencia del proceso, ya que la chapa metálica no se deforma de manera uniforme sino que responde a un conjunto de tensiones combinadas que incluyen tracción, compresión y cizallamiento. Cuando el punzón desciende sobre la chapa, el metal fluye hacia la cavidad de la matriz siguiendo la trayectoria de menor resistencia, y este flujo está condicionado por la geometría del troquel, los radios de transición, la presión aplicada y la fricción en las superficies de contacto. Las zonas cercanas a los bordes del punzón o de la matriz suelen experimentar concentraciones de tensión que pueden provocar arrugas o adelgazamientos si no se controlan mediante el ajuste de la presión del cojín, la lubricación adecuada y el diseño preciso de los radios y ángulos de la matriz. En embuticiones profundas, por ejemplo, la chapa se estira considerablemente, y si el límite de conformabilidad del material se excede, se generan fisuras que comprometen la integridad de la pieza; por ello, el cálculo de la fuerza necesaria, el radio de transición y el flujo del material es crítico para asegurar que la pieza cumpla con las especificaciones dimensionales y estructurales.
Otro fenómeno importante es el endurecimiento por deformación, que ocurre a medida que la chapa se somete a esfuerzos plásticos. Este efecto incrementa la resistencia local del material, lo que puede ser favorable para mantener la rigidez de las paredes conformadas, pero también limita la capacidad de flujo en etapas posteriores del estampado. Por esta razón, en prensas modernas se pueden programar perfiles de velocidad y presión que modulan la fuerza aplicada durante el ciclo, reduciendo la posibilidad de concentraciones de tensión y permitiendo un flujo más uniforme del metal. La anisotropía del material, resultado del proceso de laminación, también influye directamente en la dirección preferencial del flujo; por ello, la orientación de la chapa con respecto a la dirección de laminación es esencial para minimizar defectos como arrugas o estrangulamientos. La lubricación es otro factor crítico, ya que la fricción entre chapa y herramientas regula la velocidad y uniformidad del flujo del metal; lubricantes de alta resistencia y recubrimientos de baja fricción en punzones y matrices permiten que la chapa fluya sin comprometer la superficie ni la geometría final de la pieza, al mismo tiempo que prolongan la vida útil de las herramientas.
En términos de automatización, las prensas de estampación modernas se integran en líneas completamente controladas donde la alimentación de bobinas, el enderezado de chapa, la manipulación mediante robots, la inspección visual y el apilado de piezas se realizan de manera continua y sincronizada. Los sistemas de monitorización digital permiten registrar fuerzas aplicadas, desplazamientos, velocidades, temperatura de herramientas y consumo energético en tiempo real, facilitando ajustes automáticos que garantizan uniformidad y consistencia en cada ciclo. Esta recopilación de datos no solo asegura la calidad de las piezas, sino que también permite implementar estrategias de mantenimiento predictivo, anticipando desgastes o fallas antes de que provoquen paradas no planificadas, aumentando la disponibilidad de la máquina y optimizando los tiempos de producción.
La prensa de estampación de chapas metálicas tiene aplicaciones estratégicas en diversos sectores industriales. En la automoción, produce paneles de carrocería, tapas, carcasas, refuerzos estructurales y componentes internos que requieren paredes uniformes y geometrías complejas. En electrodomésticos, permite fabricar carcasas, cubetas, chasis y tapas con acabados superficiales lisos y tolerancias estrictas. En menaje de cocina, produce ollas, sartenes, bandejas y utensilios metálicos con paredes consistentes y formas precisas. En envases metálicos, la producción de latas, contenedores y tapas requiere espesores uniformes, acabados impecables y geometrías exactas que permitan procesos posteriores de recubrimiento o impresión. La combinación de capacidad de producción masiva, precisión dimensional, control del flujo del material y automatización convierte a la prensa de estampación en un equipo indispensable para asegurar eficiencia, productividad y calidad constante en la fabricación industrial moderna.
Si quieres, puedo seguir ampliando este tema entrando en detalle aún más técnico sobre la física del metal durante la estampación, explicando cómo se calculan los espesores mínimos, las zonas críticas de adelgazamiento, la recuperación elástica, los diagramas de tensión y deformación, y cómo estos parámetros se ajustan en ingeniería para fabricar piezas complejas sin defectos y con alta repetibilidad.
Durante el proceso de estampación de chapas metálicas, la comprensión del comportamiento físico del material se vuelve absolutamente crítica, ya que cada pieza está sometida a una combinación de esfuerzos que incluyen tracción, compresión y cizallamiento, los cuales interactúan de manera compleja a lo largo de la geometría de la matriz y el punzón. Cuando la chapa recibe el golpe del punzón, el metal fluye hacia la cavidad de la matriz siguiendo rutas de menor resistencia, pero este flujo no es uniforme: las zonas cercanas a bordes, esquinas o radios de transición tienden a concentrar tensiones, lo que puede generar arrugas, estrangulamientos o fisuras si no se controla adecuadamente. En operaciones de embutición profunda o repulsado, el material debe estirarse considerablemente para alcanzar la forma deseada, y cualquier excedente del límite de conformabilidad provoca fallos prematuros que comprometen la integridad de la pieza y pueden dañar la matriz o el punzón. Por ello, cada variable del proceso —fuerza aplicada, velocidad de penetración, presión del cojín, lubricación, geometría de la herramienta y propiedades del material— se diseña y ajusta cuidadosamente para asegurar que el metal fluya de manera controlada y uniforme.
El endurecimiento por deformación es otro fenómeno clave que influye en la estampación industrial. A medida que la chapa se deforma, su resistencia aumenta de manera local, lo que puede ser positivo para mantener la rigidez de ciertas secciones, pero también limita el flujo del metal en etapas posteriores del ciclo, incrementando el riesgo de concentraciones de tensión y fisuras. Por ello, las prensas modernas, especialmente las servoaccionadas, permiten programar perfiles de velocidad y presión que modulan la fuerza del punzón en tiempo real, adaptando la carga a cada fase del ciclo y optimizando el flujo del material para evitar defectos. La anisotropía del material, originada en su laminación, determina la dirección preferencial de flujo, por lo que la correcta orientación de la chapa con respecto a esta dirección es fundamental para reducir arrugas y estrangulamientos. La lubricación, por su parte, regula la fricción entre la chapa y las herramientas: un coeficiente de fricción demasiado alto puede causar estrangulamiento y roturas, mientras que uno demasiado bajo puede provocar arrugas o desplazamientos irregulares del metal. Por ello, se emplean lubricantes especializados y recubrimientos de baja fricción en punzones y matrices, asegurando un flujo uniforme, prolongando la vida útil de las herramientas y mejorando la calidad superficial de la pieza.
La automatización de las prensas de estampación ha transformado radicalmente la eficiencia de la producción industrial. Las líneas modernas integran sistemas de alimentación de bobinas, enderezado de chapa, manipulación por robots, inspección visual automatizada y apilado de piezas, permitiendo que el proceso se realice de forma continua, segura y altamente repetible. Los sensores distribuidos en la prensa registran fuerzas, desplazamientos, velocidad del punzón y temperatura de las herramientas, generando datos en tiempo real que permiten ajustes automáticos y calibración constante del ciclo de estampación. Esto asegura que cada pieza cumpla con las tolerancias requeridas, facilita el mantenimiento predictivo al anticipar desgastes y fallas antes de que provoquen paradas no programadas y optimiza la disponibilidad de la planta, aumentando la productividad y reduciendo costes operativos.
La prensa de estampación de chapas metálicas tiene aplicaciones estratégicas en múltiples industrias. En la automoción produce paneles de carrocería, tapas, cubetas, carcasas y componentes estructurales que requieren espesores uniformes y geometrías complejas; en electrodomésticos fabrica carcasas, chasis, cubetas y tapas con acabados lisos y tolerancias estrictas; en menaje y utensilios de cocina permite producir ollas, sartenes, bandejas y utensilios metálicos con paredes consistentes y formas precisas; y en envases metálicos genera latas, tapas y contenedores con espesores uniformes, superficies listas para recubrimientos decorativos o funcionales y geometrías exactas que facilitan procesos posteriores de impresión o sellado. La combinación de velocidad, precisión dimensional, control del flujo del material y automatización convierte a la prensa de estampación en un elemento indispensable para asegurar competitividad, eficiencia y calidad constante en la fabricación industrial moderna, donde cualquier variación mínima puede traducirse en defectos que comprometan el producto final.
Si quieres, puedo continuar desarrollando el tema entrando en análisis técnico avanzado de las zonas de tensión y deformación, explicando cómo se calculan los espesores mínimos, las concentraciones de esfuerzo, la recuperación elástica y cómo se optimizan todos estos parámetros en ingeniería para producir piezas complejas con máxima repetibilidad y sin defectos.
Prensa de Embutido Hidráulico
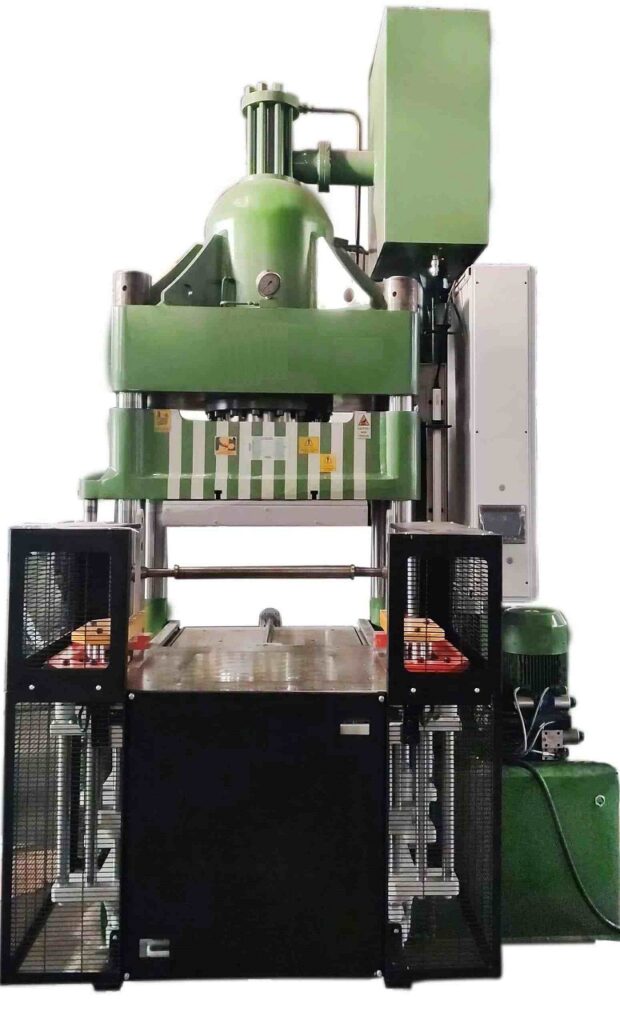
La prensa de embutido hidráulico es un equipo industrial especializado diseñado para conformar chapas metálicas mediante la aplicación de fuerza controlada a través de un sistema hidráulico, lo que permite realizar operaciones de embutición profunda, repulsado y conformado de piezas complejas que no podrían alcanzarse con prensas mecánicas tradicionales. Este tipo de prensa aprovecha la capacidad de los sistemas hidráulicos de generar fuerzas elevadas y regulables de manera precisa, distribuidas de forma uniforme durante todo el recorrido del pistón, lo que es esencial para evitar deformaciones indeseadas, arrugas, estrangulamientos o fisuras en la pieza. La embutición hidráulica se caracteriza por permitir un control exacto de la presión y la velocidad del punzón, adaptándose a distintos espesores de chapa y tipos de material, incluyendo acero, aluminio, cobre, latón y diversas aleaciones, lo que hace que estas prensas sean versátiles y adecuadas para sectores industriales muy diversos, como la automoción, electrodomésticos, menaje de cocina, envases metálicos y componentes electrónicos.
El funcionamiento de una prensa de embutido hidráulico se basa en un cilindro hidráulico que mueve un punzón hacia la matriz donde se encuentra la chapa metálica. La presión del sistema hidráulico puede regularse con gran precisión mediante válvulas y bombas de alto rendimiento, permitiendo que el punzón ejerza fuerza constante durante todo el ciclo de embutición, incluso en etapas donde el flujo del material es más crítico. La utilización de un cojín hidráulico complementario permite controlar la presión ejercida sobre la periferia de la chapa, asegurando que el material fluya de manera uniforme hacia el fondo de la matriz y evitando defectos en los bordes. Esta característica es especialmente importante en embuticiones profundas, donde la relación entre la altura de la pieza y el diámetro inicial de la chapa exige un flujo continuo y controlado del metal. Además, la velocidad de carrera del punzón puede ajustarse según la fase de trabajo, reduciendo el rebote y minimizando la aparición de arrugas o deformaciones residuales, algo que no es posible en prensas mecánicas convencionales.
El diseño de herramientas para prensas de embutido hidráulico es determinante para el éxito del proceso. Los punzones y matrices se fabrican con aceros de alta dureza y se someten a tratamientos térmicos y recubrimientos especializados que aumentan la resistencia al desgaste y a la fricción, prolongando la vida útil de la herramienta y garantizando la calidad superficial de las piezas. Los radios de transición, el acabado de la superficie y la geometría del troquel se diseñan considerando el comportamiento plástico del material, el flujo esperado de la chapa y la anisotropía derivada de su laminación. En la práctica, se utilizan simulaciones por elementos finitos para anticipar zonas de adelgazamiento, concentraciones de tensión y posibles arrugas antes de fabricar físicamente la herramienta, optimizando el diseño y reduciendo costes y tiempos de producción. La lubricación también es crítica, ya que regula la fricción entre la chapa y la herramienta; un lubricante adecuado permite un flujo uniforme del metal, protege las superficies y mejora la repetibilidad de las piezas en producciones de alto volumen.
La automatización de las prensas de embutido hidráulico ha alcanzado niveles avanzados, permitiendo integrar sistemas de alimentación de bobinas, enderezado de chapa, manipulación robotizada, inspección visual y apilado automático. Los sensores digitales monitorizan parámetros como fuerza aplicada, desplazamiento del punzón, velocidad de carrera y temperatura de las herramientas en tiempo real, lo que permite ajustes inmediatos para mantener tolerancias estrictas y uniformidad en cada pieza. Esta información también se utiliza para implementar mantenimiento predictivo, anticipando desgaste o posibles fallas antes de que provoquen paradas no planificadas, aumentando la disponibilidad de la máquina y optimizando la productividad.
En cuanto a su aplicación industrial, la prensa de embutido hidráulico es indispensable en sectores donde la precisión y la repetibilidad son críticas. En automoción, se utiliza para fabricar depósitos de combustible, cubetas, carcasas de transmisión y componentes estructurales de alta complejidad que requieren espesores uniformes y geometrías precisas. En electrodomésticos, permite producir carcasas, tapas y paneles con acabados lisos y tolerancias estrictas. En menaje de cocina, se fabrican ollas, sartenes, bandejas y utensilios metálicos de paredes uniformes y formas definidas. En envases metálicos, se producen latas, tapas y recipientes con espesores constantes y superficies listas para recubrimientos decorativos o funcionales. La combinación de fuerza precisa, control hidráulico, embutición profunda y automatización convierte a la prensa de embutido hidráulico en un equipo estratégico para garantizar productividad, eficiencia y calidad sostenida en la fabricación industrial.
Si quieres, puedo continuar desarrollando el tema en nivel técnico avanzado, explicando cómo se calculan fuerzas, presiones de cojín, velocidades del punzón, radios de matriz y distribución de tensiones para optimizar la embutición profunda sin generar defectos, con un enfoque de ingeniería industrial aplicado.
El proceso de embutido hidráulico implica una comprensión profunda del comportamiento mecánico y metalúrgico del material, ya que durante la operación la chapa metálica está sometida simultáneamente a tensiones de tracción, compresión y cizallamiento, las cuales interactúan a lo largo de toda la geometría de la matriz y el punzón. Cuando el punzón desciende, el metal fluye hacia la cavidad siguiendo las rutas de menor resistencia, pero este flujo no es uniforme; las zonas cercanas a bordes, esquinas y radios de transición tienden a concentrar tensiones, lo que puede generar arrugas, estrangulamientos o fisuras si no se controla adecuadamente. En embuticiones profundas, donde la relación entre la altura de la pieza y el diámetro de la chapa es elevada, el flujo del material debe mantenerse continuo y controlado para evitar que se exceda el límite de conformabilidad del metal, ya que cualquier fallo puede comprometer la integridad de la pieza y dañar la matriz o el punzón. La regulación de la presión hidráulica, la velocidad del punzón y la lubricación, junto con la geometría precisa del troquel, son factores críticos para asegurar que el material fluya de manera uniforme y que la pieza final cumpla con las especificaciones dimensionales y estructurales.
El endurecimiento por deformación es un fenómeno que influye significativamente en la embutición hidráulica. A medida que la chapa se deforma, su resistencia aumenta localmente, lo que puede ser beneficioso para mantener la rigidez de las paredes conformadas, pero también limita el flujo del material en etapas posteriores del ciclo y puede generar concentraciones de tensión peligrosas si no se ajusta correctamente la fuerza del punzón. Por esta razón, las prensas hidráulicas modernas permiten programar perfiles de presión y velocidad que modulan la carga durante todo el ciclo de embutición, adaptándola a cada fase y optimizando el flujo del material para evitar arrugas, estrangulamientos o fisuras. La anisotropía del material, derivada de su laminación, determina la dirección preferencial de flujo y afecta la formación de arrugas, por lo que la correcta orientación de la chapa es esencial para lograr resultados óptimos. La lubricación, que regula la fricción entre la chapa y las herramientas, es igualmente crítica: un exceso de fricción provoca estrangulamiento y riesgo de fisura, mientras que un coeficiente demasiado bajo puede inducir arrugas o desplazamientos irregulares del material. Por ello, se utilizan lubricantes especializados y recubrimientos de baja fricción en punzones y matrices, asegurando un flujo uniforme, protegiendo las superficies de la herramienta y mejorando la repetibilidad en producciones de alto volumen.
La automatización de las prensas de embutido hidráulico ha permitido integrarlas en líneas de producción altamente eficientes, donde la alimentación de bobinas, el enderezado de la chapa, la manipulación por robots, la inspección visual y el apilado automático se realizan de manera continua. Los sistemas de monitorización digital registran parámetros críticos como fuerza aplicada, desplazamiento del punzón, velocidad de carrera y temperatura de la herramienta en tiempo real, permitiendo ajustes automáticos que garantizan uniformidad y cumplimiento de tolerancias estrictas en cada pieza. Esta información también facilita la implementación de mantenimiento predictivo, anticipando desgaste o fallas antes de que provoquen paradas no planificadas, incrementando la disponibilidad de la máquina y optimizando la productividad de toda la línea de fabricación.
En cuanto a sus aplicaciones industriales, la prensa de embutido hidráulico es indispensable en sectores que requieren precisión, calidad y repetibilidad. En automoción, permite fabricar depósitos de combustible, cubetas, carcasas de transmisión y componentes estructurales complejos con paredes uniformes y geometrías precisas. En electrodomésticos, produce carcasas, tapas, chasis y paneles con acabados lisos y tolerancias estrictas. En menaje y utensilios de cocina, se utilizan para fabricar ollas, sartenes, bandejas y utensilios metálicos con paredes uniformes y formas definidas. En envases metálicos, permite la producción de latas, tapas y recipientes con espesores constantes, acabados superficiales aptos para recubrimientos decorativos o funcionales y geometrías exactas que facilitan procesos posteriores de impresión o sellado. La combinación de fuerza precisa, control hidráulico, embutición profunda y automatización convierte a la prensa de embutido hidráulico en un equipo estratégico para garantizar eficiencia, productividad y calidad sostenida en la fabricación industrial moderna.
Si quieres, puedo seguir desarrollando este tema entrando en un nivel técnico avanzado sobre la física del material, explicando cómo se calculan las tensiones máximas, la presión del cojín, los radios de matriz, la recuperación elástica, los espesores mínimos y cómo se optimizan todos estos parámetros en ingeniería para producir piezas complejas sin defectos y con alta repetibilidad.
El funcionamiento de una prensa de embutido hidráulico implica un análisis detallado de la interacción entre la chapa metálica y las herramientas, ya que el flujo del material depende de múltiples factores que deben ser cuidadosamente controlados para obtener piezas de alta calidad. Cuando el punzón desciende sobre la chapa, se generan esfuerzos de tracción en las zonas que se estiran y de compresión en aquellas que se pliegan o se encuentran en contacto directo con la matriz. La distribución de estas tensiones no es homogénea; los bordes, las esquinas y los radios de transición son puntos críticos donde se concentran mayores esfuerzos y donde es más probable que aparezcan arrugas, estrangulamientos o fisuras si no se regulan correctamente las fuerzas y la lubricación. La presión hidráulica, al ser regulable de manera precisa, permite mantener una fuerza constante a lo largo de todo el ciclo de embutición, incluso en los momentos de mayor resistencia del material, lo que garantiza un flujo uniforme y minimiza los riesgos de defectos. Esto es especialmente importante en embuticiones profundas, donde la relación entre la altura de la pieza y el diámetro inicial de la chapa exige un flujo controlado y continuo para evitar que el metal supere su límite de conformabilidad, ya que cualquier fallo puede comprometer tanto la pieza como la herramienta.
El endurecimiento por deformación es un fenómeno clave en la embutición hidráulica. A medida que la chapa se deforma, su resistencia aumenta localmente, lo que puede ser útil para mantener la rigidez de las paredes conformadas, pero también limita el flujo del material en etapas posteriores del ciclo, aumentando el riesgo de concentraciones de tensión que puedan inducir fisuras. Para manejar este efecto, las prensas hidráulicas modernas permiten programar perfiles de presión y velocidad que modulan la fuerza aplicada durante todo el ciclo, adaptándola a cada fase de la operación y optimizando el flujo del metal. La anisotropía de la chapa, derivada de su proceso de laminación, determina la dirección preferencial de flujo y afecta la aparición de arrugas, por lo que la correcta orientación del material es esencial. Además, la lubricación juega un papel determinante: un coeficiente de fricción demasiado alto genera estrangulamiento y fisuras, mientras que uno demasiado bajo provoca arrugas o desplazamientos irregulares del material. Por ello, se emplean lubricantes especializados y recubrimientos de baja fricción en punzones y matrices, garantizando un flujo uniforme, protegiendo la superficie de la herramienta y asegurando repetibilidad en producciones de alto volumen.
La automatización ha transformado las prensas hidráulicas en sistemas altamente eficientes e integrados, donde la alimentación de bobinas, el enderezado de la chapa, la manipulación mediante robots, la inspección visual y el apilado de piezas se realizan de manera continua y sincronizada. Los sensores digitales permiten registrar en tiempo real la fuerza aplicada, el desplazamiento del punzón, la velocidad de carrera y la temperatura de las herramientas, lo que posibilita ajustes automáticos inmediatos para mantener tolerancias estrictas y uniformidad en cada pieza. Esta monitorización también facilita el mantenimiento predictivo, anticipando desgaste o posibles fallas antes de que provoquen paradas no planificadas, incrementando la disponibilidad de la máquina y optimizando la productividad de la línea de fabricación.
En el ámbito industrial, la prensa de embutido hidráulico tiene aplicaciones estratégicas en múltiples sectores. En automoción, produce depósitos de combustible, cubetas, carcasas de transmisión y componentes estructurales complejos que requieren espesores uniformes y geometrías precisas. En electrodomésticos, se utiliza para fabricar carcasas, tapas, chasis y paneles con acabados lisos y tolerancias estrictas. En menaje de cocina, permite obtener ollas, sartenes, bandejas y utensilios metálicos con paredes uniformes y formas definidas. En envases metálicos, posibilita la producción de latas, tapas y recipientes con espesores consistentes, acabados superficiales aptos para recubrimientos y geometrías exactas que facilitan procesos posteriores de impresión o sellado. La combinación de fuerza regulable, control hidráulico, embutición profunda y automatización convierte a la prensa de embutido hidráulico en un equipo esencial para garantizar eficiencia, productividad y calidad sostenida en la fabricación industrial moderna, donde la precisión y la repetibilidad son factores determinantes para la competitividad de cualquier planta.
Si quieres, puedo continuar con un nivel técnico aún más avanzado, detallando cómo se calculan las tensiones máximas, la presión del cojín, los radios de matriz, los espesores mínimos, la recuperación elástica y cómo se integran todos estos parámetros en ingeniería para producir piezas complejas sin defectos y con alta repetibilidad.
El proceso de embutido hidráulico involucra un estudio meticuloso del comportamiento del material bajo cargas plásticas, ya que durante la operación la chapa metálica experimenta deformaciones complejas que incluyen tracción, compresión y cizallamiento simultáneamente, y estas se distribuyen de manera no uniforme a lo largo de la pieza. Las zonas cercanas a bordes, esquinas o radios de transición concentran esfuerzos máximos, lo que las hace más susceptibles a defectos como arrugas, estrangulamientos o fisuras si no se controlan correctamente la fuerza del punzón, la presión del cojín, la velocidad de carrera y la lubricación. En embuticiones profundas, donde la relación entre la altura de la pieza y el diámetro de la chapa es elevada, el flujo del metal debe mantenerse continuo y uniforme para evitar que se exceda el límite de deformación del material, ya que cualquier fallo puede comprometer la integridad de la pieza y provocar daños en la matriz o el punzón. Las prensas hidráulicas permiten regular con precisión la presión aplicada, manteniéndola constante incluso en fases críticas del ciclo, lo que asegura un flujo homogéneo del material y minimiza la aparición de defectos.
El endurecimiento por deformación es un factor determinante en la embutición, ya que a medida que la chapa se deforma, su resistencia aumenta localmente, lo que puede ser favorable para mantener la rigidez de las paredes formadas, pero también restringe el flujo del material en etapas posteriores, incrementando la posibilidad de concentraciones de tensión peligrosas. Para contrarrestar este efecto, las prensas modernas permiten programar perfiles de presión y velocidad que modulan la fuerza del punzón en cada fase del ciclo, adaptándose al comportamiento real del material y optimizando el flujo del metal para evitar arrugas, estrangulamientos o fisuras. La anisotropía de la chapa, derivada del proceso de laminación, determina la dirección preferencial de flujo y afecta la aparición de defectos, por lo que la orientación de la chapa respecto a la dirección de laminación es crítica. La lubricación, a su vez, regula la fricción entre la chapa y las herramientas; un coeficiente de fricción demasiado alto genera estrangulamiento y riesgo de fisuras, mientras que uno demasiado bajo puede provocar arrugas o desplazamientos irregulares del material. Por ello, se utilizan lubricantes especializados y recubrimientos de baja fricción en punzones y matrices, asegurando un flujo uniforme, protegiendo las herramientas y garantizando la repetibilidad en producciones de gran volumen.
La automatización ha transformado completamente el funcionamiento de las prensas de embutido hidráulico, permitiendo que se integren en líneas de producción completamente sincronizadas donde la alimentación de bobinas, el enderezado de chapa, la manipulación robotizada, la inspección visual y el apilado de piezas se realizan de manera continua y eficiente. Los sensores digitales registran en tiempo real la fuerza aplicada, el desplazamiento del punzón, la velocidad de carrera y la temperatura de las herramientas, permitiendo ajustes automáticos inmediatos para mantener tolerancias estrictas y uniformidad en cada pieza. Esta monitorización también facilita el mantenimiento predictivo, anticipando el desgaste de las herramientas y posibles fallas antes de que provoquen paradas no planificadas, aumentando la disponibilidad de la máquina y optimizando la productividad de toda la línea de fabricación.
En la industria, la prensa de embutido hidráulico tiene aplicaciones estratégicas que abarcan múltiples sectores. En automoción permite fabricar depósitos de combustible, cubetas, carcasas de transmisión y componentes estructurales complejos que requieren paredes uniformes y geometrías precisas. En electrodomésticos se utiliza para producir carcasas, tapas, chasis y paneles con acabados lisos y tolerancias estrictas. En menaje y utensilios de cocina permite fabricar ollas, sartenes, bandejas y utensilios metálicos con paredes uniformes y formas definidas. En envases metálicos se emplea para producir latas, tapas y recipientes con espesores consistentes, acabados superficiales aptos para recubrimientos decorativos o funcionales y geometrías exactas que facilitan procesos posteriores de impresión, sellado o recubrimiento. La combinación de fuerza precisa, control hidráulico, embutición profunda y automatización convierte a la prensa de embutido hidráulico en un equipo esencial para garantizar productividad, eficiencia y calidad sostenida en la fabricación industrial moderna, donde cualquier variación mínima puede afectar directamente la competitividad y la consistencia del producto final.
Si quieres, puedo continuar con un nivel aún más técnico, explicando con detalle cómo se calculan los espesores mínimos, la distribución de tensiones, la presión del cojín, los radios de matriz, la recuperación elástica y la optimización de todos estos parámetros para producir piezas complejas con máxima repetibilidad y sin defectos.
Prensa para Moldeo de Chapas
La prensa para moldeo de chapas es un equipo industrial diseñado para dar forma a láminas metálicas mediante la aplicación controlada de fuerza, transformando materiales planos en piezas tridimensionales con geometrías específicas y acabados precisos. A diferencia de las prensas de corte o embutición simples, las prensas de moldeo permiten realizar deformaciones complejas que incluyen curvado, repulsado, conformado y estampación profunda, adaptándose a distintos espesores y tipos de metal como acero, aluminio, cobre, latón y aleaciones especiales. Estas prensas son esenciales en industrias que requieren alta precisión y repetibilidad, como la automotriz, la fabricación de electrodomésticos, el menaje de cocina, envases metálicos y componentes electrónicos, ya que permiten producir piezas con geometrías complejas que cumplen estrictas tolerancias dimensionales y de acabado superficial.
El funcionamiento de la prensa para moldeo de chapas se basa en la interacción precisa entre el punzón, la matriz y la chapa metálica. La chapa se coloca sobre la matriz y el punzón aplica presión controlada para deformarla hasta que adopte la forma deseada. La fuerza aplicada puede ser mecánica, hidráulica o servoaccionada, dependiendo del tipo de prensa y de la complejidad de la pieza. La regulación de esta fuerza es fundamental para evitar defectos como arrugas, estrangulamientos, fisuras o deformaciones irregulares, ya que durante el moldeo la chapa experimenta tensiones combinadas de tracción, compresión y cizallamiento. Las prensas modernas permiten ajustar la velocidad del punzón, la presión aplicada y la duración de la fuerza para garantizar un flujo uniforme del material y mantener la integridad de la pieza incluso en operaciones de moldeo profundo o repulsado de gran complejidad.
El diseño de las herramientas, incluyendo punzones y matrices, es determinante para la calidad de la operación. Estas herramientas se fabrican con aceros de alta dureza y se someten a tratamientos térmicos y recubrimientos especializados que aumentan su resistencia al desgaste y reducen la fricción, prolongando su vida útil y asegurando que la superficie de la pieza quede libre de marcas o imperfecciones. Los radios de transición, la geometría de la matriz y el acabado superficial de la herramienta se diseñan considerando el comportamiento plástico del material y la dirección preferencial del flujo de la chapa, de modo que el metal se deforme de manera controlada y uniforme. La utilización de simulaciones por elementos finitos permite anticipar zonas de concentración de tensión, arrugas o adelgazamiento antes de fabricar físicamente la herramienta, optimizando su diseño y reduciendo costes y tiempos de producción.
La automatización de las prensas para moldeo de chapas ha mejorado significativamente la eficiencia y precisión del proceso. Las líneas modernas integran sistemas de alimentación de bobina, enderezado de chapa, manipulación robotizada, inspección visual y apilado automático, permitiendo una producción continua y de alta repetibilidad. Los sensores digitales monitorizan parámetros como fuerza aplicada, desplazamiento del punzón, velocidad de carrera y temperatura de la herramienta en tiempo real, posibilitando ajustes automáticos para mantener tolerancias estrictas y uniformidad en cada pieza. Esta monitorización también facilita el mantenimiento predictivo, anticipando desgaste o fallas antes de que provoquen paradas no planificadas y aumentando la disponibilidad de la máquina.
En la práctica industrial, la prensa para moldeo de chapas se utiliza para fabricar paneles y componentes de carrocería en automoción, carcasas y chasis de electrodomésticos, utensilios de cocina con formas precisas, envases metálicos de geometría exacta y diversos componentes industriales que requieren paredes uniformes y acabados superficiales impecables. La combinación de fuerza controlada, diseño de herramientas optimizado, control hidráulico o servoaccionado y automatización convierte a este tipo de prensa en un equipo estratégico para garantizar productividad, calidad y consistencia en la fabricación de piezas metálicas complejas.
Si quieres, puedo continuar desarrollando el tema en un nivel técnico avanzado, explicando con detalle cómo se calculan tensiones, espesores mínimos, radios de matriz, flujo del material, recuperación elástica y optimización de todos estos parámetros para producir piezas complejas sin defectos y con máxima repetibilidad.
El moldeo de chapas en una prensa industrial implica un control extremadamente preciso del comportamiento del material, ya que durante la operación la chapa metálica se somete simultáneamente a esfuerzos de tracción, compresión y cizallamiento que interactúan de manera compleja a lo largo de toda la geometría de la pieza. Cuando el punzón desciende sobre la chapa, el material fluye hacia la cavidad de la matriz siguiendo rutas de menor resistencia, pero este flujo no es uniforme: las zonas cercanas a bordes, esquinas o radios de transición concentran esfuerzos máximos que pueden causar arrugas, estrangulamientos o fisuras si no se controlan adecuadamente la fuerza aplicada, la presión del cojín, la velocidad del punzón y la lubricación. En operaciones de moldeo profundo, donde la relación entre la altura de la pieza y el diámetro inicial de la chapa es elevada, es esencial mantener un flujo continuo y uniforme del material para evitar que se exceda el límite de deformación del metal, ya que cualquier fallo puede comprometer la integridad de la pieza y provocar daños en la matriz o el punzón. Las prensas modernas, especialmente las hidráulicas y servoaccionadas, permiten regular con exactitud la presión, la velocidad y la duración del golpe, asegurando un flujo homogéneo del material y minimizando la aparición de defectos incluso en geometrías complejas o piezas de gran tamaño.
El endurecimiento por deformación del material es un fenómeno crítico en el moldeo de chapas, ya que a medida que la chapa se deforma, su resistencia aumenta localmente, lo que puede ser útil para mantener la rigidez de paredes y bordes, pero también limita el flujo del material en fases posteriores del ciclo, aumentando el riesgo de concentraciones de tensión que generen fisuras o fallas prematuras. Para contrarrestar este efecto, las prensas modernas permiten programar perfiles de fuerza y velocidad que modulan la presión del punzón durante todo el ciclo, adaptándose a las diferentes etapas de deformación y optimizando el flujo del metal. La anisotropía del material, originada por su laminación, determina la dirección preferencial del flujo y puede afectar la aparición de arrugas o estrangulamientos si la chapa no se orienta correctamente. La lubricación también juega un papel decisivo: un coeficiente de fricción demasiado alto provoca estrangulamiento y riesgo de fisuras, mientras que uno demasiado bajo puede generar arrugas o desplazamientos irregulares del material. Por ello, se utilizan lubricantes especializados y recubrimientos de baja fricción en punzones y matrices, lo que garantiza un flujo uniforme del metal, protege las herramientas y asegura repetibilidad en producciones de gran volumen.
La automatización de las prensas de moldeo de chapas permite integrarlas en líneas de producción completamente sincronizadas, donde la alimentación de bobinas, el enderezado de la chapa, la manipulación robotizada, la inspección visual y el apilado de piezas se realizan de forma continua. Los sistemas de monitorización digital registran en tiempo real parámetros críticos como la fuerza aplicada, el desplazamiento del punzón, la velocidad de carrera y la temperatura de las herramientas, lo que permite ajustes automáticos inmediatos para mantener tolerancias estrictas y uniformidad en cada pieza. Esta recopilación de datos también facilita la implementación de mantenimiento predictivo, anticipando desgastes o fallas antes de que provoquen paradas no planificadas, aumentando la disponibilidad de la máquina y optimizando la productividad de toda la línea de fabricación.
En la práctica industrial, la prensa para moldeo de chapas es indispensable en sectores que requieren alta precisión y repetibilidad. En la automoción, permite fabricar paneles de carrocería, cubetas, refuerzos estructurales y componentes complejos que exigen espesores uniformes y geometrías precisas. En electrodomésticos, produce carcasas, tapas, chasis y paneles con acabados lisos y tolerancias estrictas. En menaje y utensilios de cocina, se utiliza para fabricar ollas, sartenes, bandejas y utensilios metálicos con paredes uniformes y formas definidas. En envases metálicos, posibilita la producción de latas, tapas y contenedores con espesores constantes, superficies listas para recubrimientos decorativos o funcionales y geometrías exactas que facilitan procesos posteriores de impresión o sellado. La combinación de control preciso de fuerza, flujo de material optimizado, diseño de herramientas avanzado y automatización convierte a la prensa de moldeo de chapas en un equipo estratégico para garantizar productividad, calidad y consistencia en la fabricación industrial moderna, donde incluso pequeñas variaciones pueden afectar la competitividad y la uniformidad del producto final.
Si quieres, puedo continuar explicando detalles avanzados de ingeniería sobre el moldeo de chapas, incluyendo cómo se calculan tensiones máximas, espesores mínimos, radios de matriz, recuperación elástica, distribución de esfuerzos y cómo se ajustan todos estos parámetros para producir piezas complejas con alta repetibilidad y sin defectos.
El moldeo de chapas en una prensa industrial implica un análisis profundo de todos los factores que afectan la deformación del metal, ya que durante la operación la chapa se somete a un conjunto complejo de tensiones de tracción, compresión y cizallamiento que interactúan en distintas zonas de la pieza. Cuando el punzón presiona la chapa sobre la matriz, el material fluye hacia las áreas de menor resistencia, pero este flujo no es uniforme: los bordes, esquinas y radios de transición concentran los esfuerzos máximos, lo que puede generar arrugas, estrangulamientos o fisuras si no se controlan adecuadamente la presión, la velocidad del punzón, la lubricación y la geometría de la herramienta. En piezas de moldeo profundo, donde la relación entre la altura y el diámetro inicial de la chapa es elevada, mantener un flujo continuo y uniforme del material es crucial para evitar superar el límite de deformación del metal, ya que cualquier fallo puede comprometer la integridad de la pieza y causar daños en la matriz o el punzón. Las prensas modernas, sean hidráulicas, mecánicas de servocontrol o híbridas, permiten ajustar con precisión la fuerza aplicada, la velocidad de carrera y la duración del golpe, asegurando que el flujo del material sea homogéneo y que las piezas complejas se conformen sin defectos.
El endurecimiento por deformación es un fenómeno determinante en el moldeo de chapas, ya que a medida que la chapa se deforma, su resistencia aumenta localmente, lo que puede ser favorable para mantener la rigidez de las paredes y bordes, pero también restringe el flujo del material en fases posteriores, aumentando el riesgo de concentraciones de tensión que puedan inducir fisuras o fallas prematuras. Para contrarrestar este efecto, las prensas modernas permiten programar perfiles de presión y velocidad que modulan la fuerza del punzón durante todo el ciclo, adaptándose a cada etapa del proceso y optimizando el flujo del metal para evitar defectos. La anisotropía del material, consecuencia de su laminación, determina la dirección preferencial del flujo y afecta la aparición de arrugas, por lo que la orientación de la chapa es esencial para obtener piezas uniformes y libres de estrangulamientos. La lubricación, por su parte, regula la fricción entre la chapa y la herramienta; un coeficiente de fricción demasiado alto provoca estrangulamiento y riesgo de fisuras, mientras que uno demasiado bajo puede generar arrugas o desplazamientos irregulares del metal. Por ello, se utilizan lubricantes especializados y recubrimientos de baja fricción en punzones y matrices, asegurando un flujo uniforme, protegiendo las herramientas y garantizando repetibilidad en producciones de alto volumen.
La automatización ha transformado completamente la operación de las prensas para moldeo de chapas, integrándolas en líneas de producción donde la alimentación de bobinas, el enderezado de la chapa, la manipulación robotizada, la inspección visual y el apilado de piezas se realizan de manera continua y sincronizada. Los sistemas de monitorización digital permiten registrar en tiempo real la fuerza aplicada, el desplazamiento del punzón, la velocidad de carrera y la temperatura de las herramientas, lo que posibilita ajustes automáticos inmediatos para mantener tolerancias estrictas y uniformidad en cada pieza. Esta información también facilita el mantenimiento predictivo, anticipando el desgaste de las herramientas o posibles fallas antes de que provoquen paradas no planificadas, aumentando la disponibilidad de la máquina y optimizando la productividad de toda la línea de fabricación.
En el ámbito industrial, la prensa para moldeo de chapas es utilizada en sectores que requieren alta precisión, repetibilidad y calidad superficial constante. En la automoción, permite fabricar paneles de carrocería, cubetas, carcasas estructurales y componentes complejos que exigen espesores uniformes y geometrías precisas. En electrodomésticos, produce carcasas, tapas, chasis y paneles con acabados lisos y tolerancias estrictas. En menaje y utensilios de cocina, permite obtener ollas, sartenes, bandejas y utensilios metálicos con paredes uniformes y formas definidas. En envases metálicos, posibilita la fabricación de latas, tapas y recipientes con espesores consistentes, superficies aptas para recubrimientos decorativos o funcionales y geometrías exactas que facilitan procesos posteriores de impresión, sellado o recubrimiento. La combinación de fuerza regulable, flujo de material optimizado, diseño avanzado de herramientas y automatización convierte a la prensa para moldeo de chapas en un equipo estratégico que garantiza productividad, eficiencia y calidad constante, permitiendo a las industrias mantener competitividad y uniformidad en sus productos finales.
Si quieres, puedo continuar desarrollando un nivel técnico más avanzado, explicando cómo se calculan las tensiones máximas, la presión del cojín, los radios de matriz, los espesores mínimos, la recuperación elástica y cómo se optimizan todos estos parámetros para producir piezas complejas con alta repetibilidad y sin defectos.
El moldeo de chapas mediante una prensa industrial es un proceso que requiere un control extremadamente preciso de cada variable, ya que la chapa metálica se somete a deformaciones complejas en múltiples direcciones al mismo tiempo, incluyendo tracción, compresión y cizallamiento, que interactúan de manera diferente en cada zona de la pieza. Al descender el punzón sobre la chapa colocada en la matriz, el material fluye hacia las áreas de menor resistencia, pero este flujo no es homogéneo; los bordes, esquinas, radios de transición y zonas de cambio de espesor concentran los mayores esfuerzos, lo que aumenta la probabilidad de aparición de arrugas, estrangulamientos o fisuras si no se controlan correctamente la presión aplicada, la velocidad del punzón, la lubricación y la geometría de la herramienta. En piezas de moldeo profundo, donde la relación entre la altura final y el diámetro inicial de la chapa es elevada, es fundamental mantener un flujo continuo y uniforme del metal para evitar que se supere el límite de deformación del material, ya que cualquier fallo puede comprometer la integridad de la pieza y dañar la matriz o el punzón. Las prensas modernas, especialmente las hidráulicas o servoaccionadas, permiten ajustar de manera precisa la fuerza aplicada, la velocidad de carrera y el tiempo de presión, garantizando que el flujo del material sea uniforme y que las piezas complejas se conformen sin defectos ni deformaciones indeseadas.
El endurecimiento por deformación es un fenómeno crítico durante el moldeo de chapas. A medida que la chapa se deforma, su resistencia aumenta localmente, lo que ayuda a mantener la rigidez de paredes y bordes, pero también limita el flujo del material en etapas posteriores del ciclo, incrementando el riesgo de concentraciones de tensión que pueden inducir fisuras o fallas prematuras. Para contrarrestar este efecto, las prensas modernas permiten programar perfiles de presión y velocidad que modulan la fuerza del punzón a lo largo de todo el ciclo, adaptándose a cada fase del proceso y optimizando el flujo del metal para minimizar defectos. La anisotropía del material, originada por su laminación, determina la dirección preferencial del flujo y puede afectar la aparición de arrugas si la chapa no se orienta correctamente en la prensa. La lubricación es igualmente decisiva: un coeficiente de fricción demasiado alto genera estrangulamiento y riesgo de fisuras, mientras que uno demasiado bajo puede producir arrugas o desplazamientos irregulares del material. Por ello, se emplean lubricantes especializados y recubrimientos de baja fricción en punzones y matrices, asegurando un flujo uniforme del metal, protegiendo las herramientas y garantizando la repetibilidad en producciones de gran volumen.
La automatización ha transformado las prensas de moldeo de chapas en sistemas altamente eficientes y precisos, permitiendo integrarlas en líneas de producción completas donde la alimentación de bobinas, el enderezado de chapa, la manipulación por robots, la inspección visual y el apilado de piezas se realizan de manera continua y sincronizada. Los sensores digitales registran en tiempo real la fuerza aplicada, el desplazamiento del punzón, la velocidad de carrera y la temperatura de las herramientas, lo que permite realizar ajustes automáticos inmediatos para mantener tolerancias estrictas y uniformidad en cada pieza. Esta monitorización también facilita la implementación de mantenimiento predictivo, anticipando el desgaste de las herramientas o posibles fallas antes de que provoquen paradas no planificadas, aumentando la disponibilidad de la máquina y optimizando la productividad de toda la línea de fabricación.
En la industria, la prensa para moldeo de chapas es utilizada en sectores que requieren alta precisión, repetibilidad y calidad superficial constante. En automoción permite producir paneles de carrocería, cubetas, carcasas estructurales y componentes complejos que exigen espesores uniformes y geometrías precisas. En electrodomésticos fabrica carcasas, tapas, chasis y paneles con acabados lisos y tolerancias estrictas. En menaje y utensilios de cocina permite obtener ollas, sartenes, bandejas y utensilios metálicos con paredes uniformes y formas definidas. En envases metálicos posibilita la fabricación de latas, tapas y recipientes con espesores constantes, superficies listas para recubrimientos decorativos o funcionales y geometrías exactas que facilitan procesos posteriores de impresión, sellado o recubrimiento. La combinación de fuerza regulable, flujo de material optimizado, diseño avanzado de herramientas y automatización convierte a la prensa para moldeo de chapas en un equipo estratégico capaz de garantizar productividad, eficiencia y calidad constante, permitiendo a las industrias mantener la competitividad y la uniformidad en sus productos finales.
Si quieres, puedo continuar con un nivel técnico más detallado, explicando cómo se calculan las tensiones máximas, espesores mínimos, radios de matriz, recuperación elástica, distribución de esfuerzos y cómo se ajustan todos estos parámetros para producir piezas complejas con alta repetibilidad y sin defectos.
Prensa de Embutición con Troquel
La prensa de embutición con troquel es un equipo industrial especializado diseñado para conformar piezas metálicas mediante un proceso de deformación controlada en el que la chapa es estirada o embutida dentro de un troquel, adoptando la forma deseada de manera precisa y repetible. Este tipo de prensa se utiliza ampliamente en la fabricación de componentes que requieren geometrías complejas, paredes uniformes y tolerancias estrictas, siendo común en industrias como la automotriz, de electrodomésticos, envases metálicos, menaje de cocina y productos electrónicos. La característica distintiva de estas prensas es el uso de un troquel, que actúa como molde donde la chapa fluye y se conforma según la geometría deseada; el punzón, al descender sobre la chapa, ejerce fuerza controlada para empujar el material dentro de la cavidad del troquel, produciendo piezas de alta precisión y calidad superficial uniforme.
El funcionamiento de una prensa de embutición con troquel depende de la coordinación exacta entre la fuerza aplicada, la velocidad del punzón y la presión ejercida sobre la chapa. Durante la operación, la chapa metálica se somete a esfuerzos combinados de tracción, compresión y cizallamiento que varían a lo largo de la pieza. Las zonas cercanas a los bordes del troquel y los radios de transición concentran mayores tensiones, por lo que un control preciso de la fuerza y de la lubricación es esencial para evitar arrugas, estrangulamientos o fisuras. En embuticiones profundas, donde la relación entre la altura de la pieza y el diámetro inicial de la chapa es elevada, es fundamental mantener un flujo continuo y uniforme del metal para que no se exceda el límite de deformación del material, garantizando la integridad de la pieza y evitando daños en la matriz o el punzón. Las prensas modernas permiten ajustar la fuerza de manera progresiva a lo largo del ciclo de embutición, lo que asegura que el material fluya correctamente hacia las zonas más críticas del troquel y que las paredes de la pieza mantengan espesores uniformes.
El diseño del troquel es determinante para el éxito del proceso de embutición. Los punzones y matrices se fabrican con aceros de alta dureza y se someten a tratamientos térmicos y recubrimientos especiales que aumentan su resistencia al desgaste y reducen la fricción, prolongando su vida útil y garantizando que la superficie de la pieza quede libre de marcas o imperfecciones. La geometría del troquel, los radios de transición, el acabado superficial y la dureza del material se calculan considerando el comportamiento plástico de la chapa y la dirección de flujo del metal, asegurando que el material se deforme de manera uniforme y que se minimicen los riesgos de arrugas, estrangulamientos o fisuras. La simulación por elementos finitos permite prever zonas de concentración de tensión y adelgazamiento antes de fabricar la herramienta, optimizando el diseño y reduciendo costes y tiempos de producción.
La lubricación es otro factor crítico en las prensas de embutición con troquel, ya que regula la fricción entre la chapa y las herramientas. Un coeficiente de fricción demasiado alto puede generar estrangulamientos y riesgo de fisuras, mientras que uno demasiado bajo puede provocar arrugas o desplazamientos irregulares del material. Por ello, se utilizan lubricantes especializados y recubrimientos de baja fricción, asegurando un flujo uniforme del metal, protegiendo las superficies de las herramientas y mejorando la repetibilidad en producciones de gran volumen. La automatización también ha transformado estas prensas, permitiendo integrar alimentación automática de chapa, enderezado, manipulación robotizada, inspección visual y apilado de piezas, lo que aumenta significativamente la productividad y reduce errores humanos.
En cuanto a sus aplicaciones industriales, la prensa de embutición con troquel se utiliza para fabricar componentes automotrices como depósitos de combustible, cubetas y carcasas estructurales, carcasas y paneles de electrodomésticos, utensilios de cocina con paredes uniformes y formas definidas, así como envases metálicos como latas y tapas de alta precisión. La combinación de control de fuerza, geometría de troquel optimizada, flujo de material uniforme y automatización convierte a este tipo de prensa en un equipo estratégico para garantizar calidad, productividad y repetibilidad en la fabricación industrial moderna, permitiendo obtener piezas complejas sin defectos y con acabados superficiales impecables.
Si quieres, puedo continuar desarrollando el tema en un nivel técnico avanzado, explicando cómo se calculan las fuerzas de embutición, la presión del cojín, los espesores mínimos, los radios de matriz y la optimización de todos estos parámetros para producir piezas complejas con máxima repetibilidad y sin defectos.
El proceso de embutición con troquel es altamente dependiente del control de múltiples variables que afectan directamente el flujo del material y la calidad final de la pieza. Durante la operación, la chapa metálica se somete simultáneamente a tensiones de tracción, compresión y cizallamiento que se distribuyen de manera no uniforme a lo largo de toda la pieza, siendo las zonas cercanas a los bordes del troquel, los radios de transición y los cambios de espesor las áreas donde se concentran los esfuerzos máximos. Si la presión del punzón, la velocidad de carrera o la lubricación no se ajustan correctamente, pueden generarse defectos como arrugas, estrangulamientos o fisuras, comprometiendo la integridad de la pieza y dañando la matriz o el punzón. En embuticiones profundas, donde la relación entre la altura de la pieza y el diámetro inicial de la chapa es elevada, es imprescindible mantener un flujo continuo y uniforme del metal, evitando que se exceda el límite de deformación del material, lo que garantiza la precisión dimensional y la uniformidad del espesor en todas las paredes de la pieza. Las prensas modernas permiten regular la fuerza de manera progresiva a lo largo de todo el ciclo, aplicando cargas controladas que facilitan que el material fluya hacia las zonas más críticas del troquel sin generar concentraciones de tensión que puedan provocar fallas prematuras.
El endurecimiento por deformación es un fenómeno clave en la embutición, ya que a medida que la chapa se estira dentro del troquel, su resistencia aumenta localmente. Esto ayuda a mantener la rigidez de las paredes conformadas, pero también limita el flujo del material en fases posteriores, aumentando la necesidad de un control preciso de la presión y la velocidad del punzón para evitar defectos. La anisotropía del material, derivada de su laminación, determina la dirección preferencial del flujo del metal y puede influir en la aparición de arrugas si la chapa no está correctamente orientada dentro del troquel. La lubricación tiene un papel determinante en este proceso: un coeficiente de fricción excesivamente alto puede provocar estrangulamiento y riesgo de fisuras, mientras que un coeficiente demasiado bajo puede generar arrugas o desplazamientos irregulares del metal. Por ello, se utilizan lubricantes específicos y recubrimientos de baja fricción en punzones y matrices, asegurando un flujo uniforme del material, protegiendo las herramientas y garantizando la repetibilidad de piezas en producciones de alto volumen.
El diseño del troquel es determinante para la eficiencia y calidad del proceso. Los punzones y matrices se fabrican con aceros de alta dureza y se someten a tratamientos térmicos y recubrimientos especiales para aumentar su resistencia al desgaste y reducir la fricción. La geometría del troquel, los radios de transición, el acabado superficial y la dureza de los materiales se calculan considerando el comportamiento plástico de la chapa y la dirección preferencial de flujo del metal, asegurando que el material se deforme de manera uniforme y minimizando la posibilidad de arrugas, estrangulamientos o fisuras. La simulación por elementos finitos se utiliza para prever zonas de concentración de tensión, adelgazamiento y deformaciones críticas antes de fabricar las herramientas, optimizando el diseño y reduciendo costes y tiempos de producción.
La automatización de las prensas de embutición con troquel ha transformado la operación industrial, integrando procesos de alimentación de bobinas, enderezado de chapa, manipulación robotizada, inspección visual y apilado automático de piezas. Los sistemas de monitorización digital permiten registrar en tiempo real parámetros como la fuerza aplicada, el desplazamiento del punzón, la velocidad de carrera y la temperatura de las herramientas, posibilitando ajustes automáticos inmediatos para mantener tolerancias estrictas y uniformidad en cada pieza. Esta recopilación de datos también facilita la implementación de mantenimiento predictivo, anticipando desgaste o fallas antes de que provoquen paradas no planificadas, aumentando la disponibilidad de la máquina y optimizando la productividad de toda la línea de fabricación.
En cuanto a sus aplicaciones industriales, la prensa de embutición con troquel es utilizada para fabricar depósitos de combustible, cubetas, carcasas estructurales y componentes complejos en la automoción; carcasas, tapas, chasis y paneles en electrodomésticos; ollas, sartenes y utensilios metálicos con paredes uniformes en menaje de cocina; así como latas, tapas y recipientes metálicos de geometría exacta en envases. La combinación de control de fuerza progresivo, flujo de material optimizado, diseño avanzado de herramientas y automatización convierte a esta prensa en un equipo estratégico capaz de garantizar productividad, calidad constante y repetibilidad, permitiendo producir piezas complejas sin defectos y con acabados superficiales uniformes.
Si quieres, puedo seguir explicando un nivel técnico avanzado sobre ingeniería de embutición, detallando cómo se calculan las fuerzas de embutición, la presión del cojín, los espesores mínimos, los radios de matriz, la recuperación elástica del material y la optimización de todos estos parámetros para obtener piezas complejas de manera repetitiva y sin defectos.
La operación de una prensa de embutición con troquel se basa en la interacción precisa entre el punzón, la chapa y la matriz, donde cada parámetro influye directamente en la calidad de la pieza final. Al descender el punzón, la chapa se estira y fluye hacia la cavidad del troquel siguiendo rutas de menor resistencia, pero este flujo está condicionado por múltiples factores como el espesor inicial de la chapa, el límite elástico del material, la velocidad de carrera del punzón, la presión del cojín y la fricción entre las superficies de contacto. Las zonas críticas, como los bordes de la matriz, los radios de transición y los cambios de sección, concentran tensiones elevadas que pueden provocar arrugas, estrangulamientos o fisuras si no se aplican correctamente los controles de fuerza y lubricación. En embuticiones profundas o piezas de geometría compleja, mantener un flujo uniforme y continuo del material es indispensable para evitar que se exceda la capacidad de deformación del metal y garantizar la uniformidad del espesor en toda la pieza. Las prensas modernas, sean hidráulicas, mecánicas o servoaccionadas, permiten ajustar la fuerza progresivamente a lo largo del ciclo, aplicando presiones controladas que facilitan el flujo hacia las zonas más críticas del troquel y reducen al mínimo las concentraciones de tensión.
El endurecimiento por deformación del metal durante la embutición es un factor que debe ser considerado cuidadosamente, ya que a medida que la chapa se conforma, su resistencia aumenta localmente. Este fenómeno es útil para mantener la rigidez de paredes y bordes, pero limita el flujo del material en fases posteriores, incrementando el riesgo de fisuras si no se compensan con ajustes precisos de la presión y velocidad del punzón. La anisotropía de la chapa, derivada de su laminación, afecta la dirección preferencial del flujo y puede generar arrugas o estrangulamientos si no se orienta adecuadamente dentro de la prensa. La lubricación tiene un papel decisivo en el proceso; un coeficiente de fricción demasiado alto genera estrangulamiento y riesgo de fisuras, mientras que un coeficiente demasiado bajo provoca arrugas o desplazamientos irregulares del metal. Por ello, se emplean lubricantes especializados y recubrimientos de baja fricción en punzones y matrices, lo que garantiza un flujo uniforme del material, protege las herramientas y asegura repetibilidad en producciones de alto volumen.
El diseño de los troqueles es crítico para la eficiencia y la calidad de la operación. Los punzones y matrices se fabrican con aceros de alta dureza tratados térmicamente y recubiertos con materiales que reducen el desgaste y la fricción, prolongando su vida útil y garantizando superficies impecables en las piezas. La geometría del troquel, los radios de transición, el acabado superficial y la dureza del material se calculan considerando el comportamiento plástico de la chapa y la dirección de flujo del metal, asegurando deformaciones uniformes y minimizando defectos. La simulación mediante elementos finitos permite anticipar zonas de concentración de tensión, adelgazamiento o deformaciones críticas antes de la fabricación física del troquel, optimizando el diseño y reduciendo costes y tiempos de producción.
La automatización de las prensas de embutición con troquel permite integrar la alimentación de bobinas, el enderezado de la chapa, la manipulación robotizada, la inspección visual y el apilado automático en líneas de producción continuas, lo que incrementa la eficiencia y la consistencia de las piezas. Los sensores digitales registran en tiempo real parámetros como fuerza aplicada, desplazamiento del punzón, velocidad de carrera y temperatura de las herramientas, permitiendo ajustes automáticos inmediatos para mantener tolerancias estrictas y uniformidad en cada pieza. Esta monitorización también facilita el mantenimiento predictivo, anticipando el desgaste o posibles fallas antes de que provoquen paradas no planificadas, aumentando la disponibilidad de la máquina y optimizando la productividad de toda la línea de fabricación.
En la práctica industrial, la prensa de embutición con troquel es empleada para fabricar depósitos de combustible, cubetas, carcasas estructurales y componentes automotrices complejos; carcasas, tapas, chasis y paneles de electrodomésticos; ollas, sartenes y utensilios metálicos de menaje; así como envases metálicos como latas, tapas y recipientes de geometría exacta. La combinación de control progresivo de la fuerza, flujo de material optimizado, diseño avanzado de troqueles y automatización convierte a estas prensas en equipos estratégicos capaces de garantizar productividad, calidad constante y alta repetibilidad, permitiendo producir piezas complejas sin defectos y con acabados superficiales uniformes, manteniendo la competitividad y la consistencia en la industria moderna.
Si quieres, puedo continuar con un nivel aún más técnico, describiendo los cálculos exactos de fuerzas de embutición, presión del cojín, espesores mínimos, radios de matriz, recuperación elástica y la optimización de todos estos parámetros para lograr piezas complejas con máxima precisión y repetibilidad industrial.
El funcionamiento de la prensa de embutición con troquel requiere un conocimiento profundo de la mecánica de materiales y de la metalurgia, ya que la chapa metálica se comporta de manera diferente según su composición, espesor, dirección de laminación y tratamiento previo. Durante el ciclo de embutición, la chapa se deforma plásticamente siguiendo la geometría del troquel, pero al mismo tiempo experimenta tensiones residuales que pueden generar arrugas, estrangulamientos o fisuras si no se aplican correctamente los parámetros de presión, velocidad y lubricación. La coordinación entre la fuerza del punzón y la presión del cojín es fundamental: mientras que el punzón empuja la chapa hacia la cavidad del troquel, el cojín sostiene la parte de la chapa que no debe fluir inmediatamente, evitando deformaciones irregulares y concentraciones de esfuerzo que puedan comprometer la integridad de la pieza. En embuticiones profundas, la relación entre la altura de la pieza y el diámetro inicial de la chapa aumenta la complejidad, ya que el metal tiende a adelgazarse en las zonas críticas y a concentrar tensiones, por lo que la aplicación progresiva y controlada de la fuerza del punzón es esencial para mantener espesores uniformes y evitar defectos.
El endurecimiento por deformación es un fenómeno que influye directamente en la selección de los parámetros de embutición. A medida que la chapa se deforma dentro del troquel, su resistencia aumenta localmente, lo que es útil para mantener la rigidez de las paredes formadas, pero también limita el flujo del material en fases posteriores del ciclo, aumentando el riesgo de concentraciones de tensión y fisuras. La anisotropía de la chapa, derivada de su laminación, determina la dirección preferencial del flujo del material, por lo que la orientación de la chapa dentro de la prensa es crítica para evitar arrugas y estrangulamientos. La lubricación es igualmente determinante: un coeficiente de fricción demasiado alto provoca estrangulamientos y riesgo de fisuras, mientras que un coeficiente demasiado bajo puede causar arrugas o desplazamientos irregulares del material. Por ello, se utilizan lubricantes especializados y recubrimientos de baja fricción en punzones y matrices, asegurando un flujo uniforme del metal, protegiendo las herramientas y garantizando repetibilidad incluso en producciones de alto volumen.
El diseño del troquel y del punzón es fundamental para el éxito del proceso de embutición. Los punzones y matrices se fabrican con aceros de alta dureza tratados térmicamente y recubiertos con materiales que reducen el desgaste y la fricción, prolongando su vida útil y garantizando superficies de contacto que no marquen la pieza. La geometría del troquel, los radios de transición, el acabado superficial y la dureza del material se calculan considerando el comportamiento plástico de la chapa y la dirección de flujo del metal, asegurando deformaciones uniformes y minimizando la posibilidad de defectos. La simulación por elementos finitos permite prever zonas de concentración de tensión, adelgazamiento y deformaciones críticas antes de fabricar la herramienta, optimizando su diseño y reduciendo costes y tiempos de producción.
La automatización de estas prensas permite integrarlas en líneas de producción continuas donde la alimentación de bobinas, el enderezado de la chapa, la manipulación robotizada, la inspección visual y el apilado de piezas se realizan de forma sincronizada. Los sistemas de monitorización digital registran en tiempo real la fuerza aplicada, el desplazamiento del punzón, la velocidad de carrera y la temperatura de las herramientas, lo que permite realizar ajustes automáticos inmediatos para mantener tolerancias estrictas y uniformidad en cada pieza. Esta monitorización también facilita la implementación de mantenimiento predictivo, anticipando desgaste o posibles fallas antes de que provoquen paradas no planificadas, aumentando la disponibilidad de la máquina y optimizando la productividad de toda la línea de fabricación.
En la práctica industrial, la prensa de embutición con troquel se utiliza para producir componentes automotrices como depósitos de combustible, cubetas, carcasas estructurales y partes complejas; carcasas, tapas, chasis y paneles de electrodomésticos; utensilios de cocina como ollas, sartenes y bandejas con paredes uniformes y formas definidas; así como envases metálicos de alta precisión como latas, tapas y recipientes. La combinación de control progresivo de la fuerza, flujo de material optimizado, diseño avanzado de troqueles y automatización convierte a estas prensas en equipos estratégicos capaces de garantizar productividad, calidad constante y alta repetibilidad, permitiendo fabricar piezas complejas sin defectos y con acabados superficiales uniformes, manteniendo la competitividad y la consistencia en la industria moderna.
Si quieres, puedo continuar con un análisis aún más técnico, detallando cálculos exactos de fuerzas de embutición, presión del cojín, espesores mínimos, radios de matriz, recuperación elástica, distribución de esfuerzos y cómo se optimizan todos estos parámetros para lograr piezas complejas con máxima repetibilidad y sin defectos.
Prensa de Estampado y Corte
La prensa de estampado y corte es un equipo industrial diseñado para realizar operaciones combinadas sobre chapas metálicas, donde el material se conforma mediante estampado y, simultáneamente o en pasos sucesivos, se cortan secciones para obtener piezas con geometrías precisas y acabados exactos. Este tipo de prensa es fundamental en la industria manufacturera, especialmente en sectores como automoción, electrodomésticos, envases metálicos, menaje de cocina, electrónica y componentes industriales, donde se requiere alta precisión, repetibilidad y calidad superficial en grandes volúmenes de producción. La operación de la prensa combina dos procesos críticos: el estampado, que implica deformar la chapa para adoptar una forma tridimensional específica mediante un punzón y una matriz, y el corte, donde se separan porciones de chapa siguiendo líneas definidas, garantizando bordes limpios y sin rebabas. Esta combinación permite producir piezas complejas en un solo ciclo de trabajo, optimizando tiempos de producción y reduciendo la manipulación de materiales entre procesos.
El funcionamiento de la prensa de estampado y corte depende de la sincronización precisa entre el movimiento del punzón, la posición de la chapa y la geometría de la matriz y cuchillas. Durante el estampado, la chapa se somete a tensiones de tracción y compresión que deben controlarse para evitar arrugas, estrangulamientos o fisuras, especialmente en piezas de geometría compleja o en embuticiones profundas. La fase de corte requiere que la presión se distribuya uniformemente a lo largo de las cuchillas y que la chapa esté correctamente posicionada, evitando desplazamientos que puedan provocar bordes irregulares o marcas en la pieza. Las prensas modernas permiten regular con precisión la fuerza aplicada, la velocidad de carrera y la duración del golpe, asegurando que tanto el estampado como el corte se realicen de manera uniforme y controlada, incluso en operaciones de alta velocidad y producción masiva.
El diseño de las herramientas es determinante en la calidad de la operación. Los punzones, matrices y cuchillas se fabrican con aceros de alta dureza tratados térmicamente y recubiertos con materiales que reducen el desgaste y la fricción, prolongando la vida útil de la herramienta y asegurando un acabado superficial óptimo en las piezas. Los radios de transición, los ángulos de corte y la geometría de la matriz se calculan considerando el comportamiento plástico de la chapa y el flujo del material durante el estampado, garantizando que las deformaciones sean uniformes y minimizando defectos como arrugas, estrangulamientos o rebabas. La simulación por elementos finitos se utiliza frecuentemente para anticipar zonas de concentración de esfuerzo, deformaciones críticas y adelgazamientos antes de fabricar las herramientas, optimizando su diseño y reduciendo costos y tiempos de producción.
La lubricación y control de fricción son factores críticos, ya que un coeficiente de fricción excesivo puede provocar estrangulamiento y fisuras durante el estampado, mientras que un coeficiente demasiado bajo puede generar desplazamientos irregulares de la chapa y bordes irregulares durante el corte. Por ello, se emplean lubricantes especializados y recubrimientos de baja fricción, asegurando un flujo uniforme del material, protegiendo las herramientas y garantizando la repetibilidad en producciones de alto volumen. La automatización de estas prensas permite integrar alimentación de bobinas, enderezado de la chapa, manipulación robotizada, inspección visual y apilado automático de piezas, incrementando la eficiencia y consistencia en la producción y reduciendo errores humanos.
En la práctica industrial, la prensa de estampado y corte se utiliza para fabricar piezas de carrocería automotriz como paneles, refuerzos y tapas, componentes de electrodomésticos como carcasas, paneles y chasis, utensilios metálicos como tapas y bases de menaje de cocina, y envases metálicos de geometría precisa como latas, tapas y contenedores. La combinación de estampado y corte en un solo ciclo, junto con la regulación precisa de fuerza, geometría de herramientas optimizada, flujo de material uniforme y automatización avanzada, convierte a esta prensa en un equipo estratégico capaz de garantizar productividad, calidad constante y alta repetibilidad, permitiendo producir piezas complejas sin defectos y con acabados superficiales uniformes, asegurando competitividad y eficiencia en la industria moderna.
Si quieres, puedo continuar con un nivel técnico avanzado, explicando cómo se calculan las fuerzas de estampado y corte, la presión de contacto, los espesores mínimos, los radios de matriz y cuchilla, la recuperación elástica del material y la optimización de todos estos parámetros para producir piezas complejas de manera repetitiva y sin defectos.
La prensa de estampado y corte combina la deformación plástica controlada del metal con la separación precisa del material para producir piezas terminadas en un solo ciclo de trabajo, lo que la hace esencial en la fabricación industrial moderna. Durante el estampado, la chapa metálica se coloca sobre la matriz y es empujada por el punzón, lo que provoca que el material fluya hacia las cavidades y adopte la geometría deseada; este flujo de metal no es uniforme, ya que las zonas cercanas a bordes, radios de transición o cambios de sección concentran tensiones elevadas que pueden generar arrugas, estrangulamientos o fisuras si no se aplican correctamente la fuerza y la lubricación. En la fase de corte, las cuchillas separan secciones de la chapa siguiendo líneas definidas, y cualquier desplazamiento o deformación irregular de la pieza puede producir bordes ásperos o rebabas, por lo que la sincronización entre el movimiento del punzón, la posición de la chapa y la geometría de la matriz y cuchillas es crítica. Las prensas modernas permiten ajustar con precisión la fuerza aplicada, la velocidad de carrera y la duración del golpe, asegurando que tanto el estampado como el corte se realicen de manera controlada y uniforme, incluso en ciclos de alta velocidad y producción masiva, minimizando defectos y garantizando tolerancias estrictas.
El endurecimiento por deformación es un fenómeno que influye directamente en la calidad de la pieza, ya que a medida que la chapa se deforma dentro de la matriz, su resistencia aumenta localmente, manteniendo la rigidez de las paredes conformadas pero limitando el flujo del material en fases posteriores. Por ello, es necesario programar perfiles de fuerza que modulen la presión del punzón durante todo el ciclo, adaptándose a la deformación progresiva del metal y optimizando el flujo hacia las zonas críticas de la pieza. La anisotropía de la chapa, derivada de su laminación, determina la dirección preferencial del flujo del metal y puede afectar la aparición de arrugas o estrangulamientos si la chapa no está correctamente orientada dentro de la prensa. La lubricación juega un papel decisivo: un coeficiente de fricción demasiado alto puede generar estrangulamiento y riesgo de fisuras, mientras que un coeficiente demasiado bajo puede producir desplazamientos irregulares del material y bordes de corte defectuosos; por ello se emplean lubricantes especializados y recubrimientos de baja fricción que aseguran flujo uniforme, protegen las herramientas y permiten alta repetibilidad incluso en producciones de gran volumen.
El diseño de los punzones, matrices y cuchillas es fundamental para garantizar precisión, calidad superficial y durabilidad de las herramientas. Los componentes se fabrican con aceros de alta dureza tratados térmicamente y recubiertos con materiales que minimizan el desgaste y la fricción, prolongando su vida útil y asegurando superficies impecables en las piezas. Los radios de transición, ángulos de corte y geometría de las matrices se calculan considerando el comportamiento plástico de la chapa, el flujo del material y la distribución de tensiones, de manera que se minimicen arrugas, estrangulamientos, rebabas y deformaciones irregulares. La simulación por elementos finitos permite prever zonas críticas de adelgazamiento, concentración de esfuerzos y deformaciones antes de fabricar la herramienta, optimizando su diseño, reduciendo costes de prototipado y acortando los tiempos de producción.
La automatización integrada en estas prensas permite que la alimentación de bobinas, el enderezado de la chapa, la manipulación robotizada, la inspección visual y el apilado automático se realicen de manera continua y sincronizada, aumentando la productividad y la consistencia de cada pieza. Los sistemas de monitorización digital registran en tiempo real la fuerza aplicada, el desplazamiento del punzón, la velocidad de carrera y la temperatura de las herramientas, posibilitando ajustes automáticos inmediatos que aseguran tolerancias estrictas y uniformidad, mientras que los datos recopilados permiten implementar mantenimiento predictivo, anticipando desgaste o fallas antes de que generen paradas no planificadas y optimizando la disponibilidad de la máquina.
En la práctica industrial, las prensas de estampado y corte se utilizan para fabricar paneles de carrocería, refuerzos, cubetas y componentes automotrices; carcasas, chasis y paneles de electrodomésticos; utensilios metálicos como tapas, bandejas y ollas; y envases metálicos de geometría exacta como latas, tapas y contenedores. La combinación de estampado y corte en un solo ciclo de operación, junto con la regulación precisa de la fuerza, flujo de material optimizado, geometría de herramientas avanzada y automatización completa, convierte a estas prensas en equipos estratégicos capaces de garantizar productividad, calidad constante y alta repetibilidad, permitiendo fabricar piezas complejas sin defectos y con acabados superficiales uniformes, asegurando eficiencia y competitividad en la industria moderna.
Si quieres, puedo continuar con un nivel técnico aún más detallado, explicando cómo se calculan con precisión las fuerzas de estampado y corte, la presión de contacto, espesores mínimos, radios de matriz y cuchilla, recuperación elástica del material y la optimización de todos estos parámetros para producir piezas complejas de manera repetitiva y sin defectos.
La prensa de estampado y corte funciona como un sistema integral donde cada parámetro influye directamente en la calidad final de la pieza y en la eficiencia del proceso productivo. Durante el estampado, la chapa metálica se coloca sobre la matriz y el punzón desciende ejerciendo fuerza controlada, provocando que el material fluya hacia la cavidad definida por la herramienta. Este flujo no es homogéneo; las zonas cercanas a los bordes, radios de transición y cambios de espesor concentran mayores tensiones, por lo que un control preciso de la fuerza del punzón, la velocidad de carrera y la lubricación es esencial para evitar arrugas, estrangulamientos o fisuras que comprometan la integridad de la pieza y puedan dañar las herramientas. En la fase de corte, las cuchillas separan secciones de la chapa siguiendo líneas exactas, y cualquier desplazamiento o deformación irregular puede producir bordes ásperos, rebabas o marcas en la superficie de la pieza. Las prensas modernas permiten ajustar con exactitud la fuerza aplicada, la velocidad y el tiempo de contacto del punzón y las cuchillas, garantizando uniformidad y precisión incluso en producciones de alta velocidad y gran volumen, optimizando tiempos de ciclo y reduciendo la necesidad de operaciones secundarias.
El endurecimiento por deformación es un factor clave, ya que a medida que la chapa se conforma, su resistencia aumenta localmente. Esto contribuye a mantener la rigidez de las paredes conformadas durante el estampado, pero limita el flujo del material en etapas posteriores, por lo que es necesario programar perfiles de presión progresivos que modulen la fuerza del punzón de acuerdo con la deformación del metal, asegurando que el material fluya hacia las zonas críticas sin generar concentraciones de tensión que puedan producir fisuras o adelgazamientos excesivos. La anisotropía de la chapa, derivada de su laminación, determina la dirección preferencial del flujo del material, por lo que la orientación correcta de la chapa dentro de la prensa es fundamental para evitar arrugas y estrangulamientos. La lubricación juega un papel determinante: un coeficiente de fricción demasiado alto provoca estrangulamiento y riesgo de fisuras, mientras que uno demasiado bajo genera arrugas o desplazamientos irregulares durante el corte. Por ello, se utilizan lubricantes especializados y recubrimientos de baja fricción en punzones, matrices y cuchillas, asegurando un flujo uniforme del metal, protegiendo las herramientas y garantizando la repetibilidad incluso en producciones masivas.
El diseño de las herramientas, punzones, matrices y cuchillas es esencial para la precisión y durabilidad del proceso. Los componentes se fabrican con aceros de alta dureza tratados térmicamente y recubiertos con materiales que reducen el desgaste y la fricción, prolongando la vida útil de las herramientas y asegurando superficies de contacto que no marquen la pieza. La geometría de las matrices, los radios de transición, los ángulos de corte y el acabado superficial se calculan considerando el comportamiento plástico de la chapa, el flujo del metal y la distribución de tensiones, garantizando deformaciones uniformes y minimizando defectos. La simulación por elementos finitos permite anticipar zonas críticas de concentración de esfuerzo, adelgazamiento o deformaciones antes de fabricar las herramientas, optimizando su diseño y reduciendo costos de prototipado y tiempo de fabricación.
La automatización integrada en estas prensas permite que la alimentación de bobinas, el enderezado de la chapa, la manipulación robotizada, la inspección visual y el apilado automático se realicen de manera continua y sincronizada. Los sistemas de monitorización digital registran en tiempo real la fuerza aplicada, el desplazamiento del punzón, la velocidad de carrera y la temperatura de las herramientas, permitiendo ajustes automáticos inmediatos que aseguran tolerancias estrictas y uniformidad en cada pieza. Esta información también facilita la implementación de mantenimiento predictivo, anticipando desgaste o posibles fallas antes de que provoquen paradas no planificadas, aumentando la disponibilidad de la máquina y optimizando la productividad de toda la línea de producción.
En la práctica industrial, la prensa de estampado y corte se utiliza para fabricar paneles de carrocería, refuerzos, cubetas y componentes automotrices; carcasas, chasis y paneles de electrodomésticos; utensilios metálicos como tapas, bandejas y ollas; y envases metálicos de geometría exacta como latas, tapas y recipientes. La combinación de estampado y corte en un solo ciclo de operación, junto con la regulación precisa de la fuerza, flujo de material optimizado, geometría de herramientas avanzada y automatización completa, convierte a estas prensas en equipos estratégicos capaces de garantizar productividad, calidad constante y alta repetibilidad, permitiendo fabricar piezas complejas sin defectos y con acabados superficiales uniformes, asegurando eficiencia y competitividad en la industria moderna.
Si quieres, puedo continuar explicando un nivel aún más técnico y detallado, abordando cómo se calculan las fuerzas de estampado y corte, la presión de contacto, espesores mínimos, radios de matriz y cuchilla, recuperación elástica del material, distribución de esfuerzos y la optimización de todos estos parámetros para producir piezas complejas de manera repetitiva y sin defectos.
La prensa de estampado y corte representa un sistema complejo donde la interacción entre chapa, punzón, matriz y cuchillas determina la calidad de la pieza y la eficiencia del proceso productivo, siendo indispensable comprender en detalle cómo cada variable afecta el resultado final. Durante la fase de estampado, la chapa metálica es empujada por el punzón hacia la cavidad de la matriz, generando un flujo de material que debe ser controlado cuidadosamente, ya que las zonas cercanas a bordes, radios de transición y cambios de sección concentran las mayores tensiones y son las más susceptibles a arrugas, estrangulamientos o fisuras. Para evitar estos defectos, es necesario programar perfiles de fuerza progresivos y sincronizar perfectamente la velocidad de carrera del punzón con la presión del cojín, garantizando un flujo uniforme del metal hacia todas las zonas críticas de la pieza, incluso en embuticiones profundas o geometrías complejas. La fase de corte requiere precisión extrema: las cuchillas separan secciones de chapa siguiendo líneas exactas y cualquier desalineación o deformación puede generar bordes irregulares, rebabas o marcas superficiales; por ello, la sincronización entre el movimiento del punzón, la posición de la chapa y la geometría de las matrices y cuchillas es fundamental, y las prensas modernas permiten ajustar con exactitud la fuerza aplicada, el tiempo de contacto y la velocidad de carrera, asegurando uniformidad y calidad incluso en ciclos de producción de alta velocidad y gran volumen.
El endurecimiento por deformación y la anisotropía de la chapa son factores críticos en el proceso, ya que a medida que la chapa se conforma, su resistencia aumenta localmente, lo que contribuye a mantener la rigidez de las paredes y bordes, pero también limita el flujo del material en fases posteriores, incrementando el riesgo de fisuras si no se ajusta correctamente la presión del punzón. La dirección de laminación de la chapa determina la anisotropía y la orientación óptima para el flujo del material, siendo clave evitar arrugas y estrangulamientos. La lubricación tiene un papel decisivo: un coeficiente de fricción demasiado alto puede provocar estrangulamientos y fisuras, mientras que uno demasiado bajo puede generar arrugas o desplazamientos irregulares durante el corte; por ello, se emplean lubricantes especializados y recubrimientos de baja fricción que aseguran flujo uniforme, protegen las herramientas y garantizan la repetibilidad de las piezas incluso en producciones masivas.
El diseño de las herramientas, punzones, matrices y cuchillas es determinante para la precisión, durabilidad y calidad de las piezas. Los componentes se fabrican con aceros de alta dureza tratados térmicamente y recubiertos con materiales que minimizan el desgaste y la fricción, prolongando la vida útil de las herramientas y asegurando superficies de contacto que no marquen la pieza. Los radios de transición, ángulos de corte, geometría de matrices y acabado superficial se calculan considerando el comportamiento plástico de la chapa, el flujo del metal y la distribución de tensiones, garantizando deformaciones uniformes y minimizando defectos. La simulación por elementos finitos permite anticipar zonas críticas de concentración de esfuerzo, adelgazamiento o deformaciones antes de fabricar las herramientas, optimizando el diseño y reduciendo costes de prototipado y tiempos de producción.
La automatización de estas prensas permite integrar procesos como la alimentación de bobinas, enderezado de chapa, manipulación robotizada, inspección visual y apilado automático en una línea de producción continua y sincronizada, aumentando la eficiencia y consistencia de cada pieza. Los sistemas de monitorización digital registran en tiempo real la fuerza aplicada, el desplazamiento del punzón, la velocidad de carrera y la temperatura de las herramientas, permitiendo ajustes automáticos inmediatos para mantener tolerancias estrictas y uniformidad en cada pieza. La recopilación de estos datos también facilita la implementación de mantenimiento predictivo, anticipando desgaste o posibles fallas antes de que provoquen paradas no planificadas, aumentando la disponibilidad de la máquina y optimizando la productividad de toda la línea de fabricación.
En la práctica industrial, las prensas de estampado y corte se emplean para fabricar paneles de carrocería, refuerzos, cubetas y componentes automotrices complejos; carcasas, chasis y paneles de electrodomésticos; utensilios metálicos como tapas, bandejas y ollas; y envases metálicos de geometría exacta como latas, tapas y recipientes. La combinación de estampado y corte en un solo ciclo de operación, junto con la regulación precisa de fuerza, flujo de material optimizado, geometría de herramientas avanzada y automatización completa, convierte a estas prensas en equipos estratégicos capaces de garantizar productividad, calidad constante y alta repetibilidad, permitiendo producir piezas complejas sin defectos y con acabados superficiales uniformes, asegurando eficiencia y competitividad en la industria moderna.
Si deseas, puedo continuar con un análisis extremadamente técnico y detallado, abordando cómo se calculan las fuerzas exactas de estampado y corte, la presión de contacto, espesores mínimos, radios de matriz y cuchilla, recuperación elástica del material, distribución de esfuerzos y la optimización de todos estos parámetros para fabricar piezas complejas de manera completamente repetitiva y sin defectos.
Prensa de Conformado de Metales
La prensa de conformado de metales es una máquina industrial diseñada para modificar la geometría de láminas, chapas o perfiles metálicos mediante la aplicación controlada de fuerzas mecánicas, hidráulicas o servoaccionadas, logrando que el material adopte formas específicas sin comprometer su integridad estructural. Este tipo de prensa es fundamental en la industria manufacturera moderna, abarcando sectores como automoción, aeroespacial, electrodomésticos, menaje de cocina, envases metálicos y componentes industriales, donde se requiere precisión, repetibilidad y acabado superficial de alta calidad. El funcionamiento se basa en la interacción precisa entre el punzón, la matriz y la chapa metálica; al descender el punzón sobre la chapa colocada sobre la matriz, el material se deforma plásticamente y fluye hacia la geometría de la cavidad, adoptando la forma deseada. Este flujo de material no es uniforme: las zonas cercanas a bordes, cambios de espesor y radios de transición concentran tensiones elevadas, por lo que el control de la fuerza, la velocidad del punzón, la lubricación y la presión del cojín es crítico para evitar defectos como arrugas, estrangulamientos o fisuras.
En procesos de conformado complejos, como embuticiones profundas, dobleces o curvados de chapa, la chapa experimenta tensiones de tracción, compresión y cizallamiento que deben distribuirse de manera controlada. Las prensas modernas permiten aplicar fuerzas progresivas a lo largo de todo el ciclo, modulando la presión del punzón y del cojín para garantizar que el material fluya uniformemente hacia todas las zonas críticas sin generar concentraciones de tensión que puedan provocar fallas. La anisotropía del material, derivada de su laminación, determina la dirección preferencial del flujo del metal, por lo que la orientación de la chapa dentro de la prensa es determinante para evitar deformaciones irregulares. La lubricación es esencial: un coeficiente de fricción elevado puede causar estrangulamiento y fisuras, mientras que un coeficiente demasiado bajo genera arrugas o desplazamientos irregulares; por ello se utilizan lubricantes especializados y recubrimientos de baja fricción que optimizan el flujo del material, protegen las herramientas y aseguran alta repetibilidad en producciones de gran volumen.
El diseño de punzones, matrices y cojines es crucial para la precisión, durabilidad y calidad de las piezas. Las herramientas se fabrican con aceros de alta dureza tratados térmicamente y recubiertos con materiales resistentes al desgaste, garantizando superficies de contacto uniformes y prolongando la vida útil de la máquina. Los radios de transición, ángulos de doblado, geometría de la matriz y acabado superficial se calculan considerando el comportamiento plástico de la chapa y la distribución de esfuerzos, asegurando deformaciones uniformes y minimizando defectos. La simulación por elementos finitos permite anticipar zonas críticas de concentración de tensión, adelgazamiento o deformaciones irregulares antes de fabricar las herramientas, optimizando su diseño, reduciendo costos de prototipado y acortando tiempos de producción.
La automatización en las prensas de conformado permite integrar alimentación de bobinas, enderezado de chapa, manipulación robotizada, inspección visual y apilado automático de piezas en un flujo de producción continuo y sincronizado, incrementando la productividad y consistencia de cada pieza. Los sistemas de monitorización digital registran parámetros como fuerza aplicada, desplazamiento del punzón, velocidad de carrera y temperatura de las herramientas, posibilitando ajustes automáticos inmediatos para mantener tolerancias estrictas y uniformidad en cada operación. Esta información también permite implementar mantenimiento predictivo, anticipando desgaste o fallas antes de que provoquen paradas no planificadas, aumentando la disponibilidad de la máquina y optimizando la eficiencia de toda la línea de fabricación.
En la práctica industrial, las prensas de conformado de metales se utilizan para fabricar componentes automotrices como paneles, refuerzos, carcasas y cubetas; estructuras y paneles de electrodomésticos; utensilios metálicos como ollas, sartenes y bandejas; y envases metálicos de geometría precisa como latas, tapas y contenedores. La combinación de control progresivo de fuerza, flujo de material optimizado, geometría avanzada de herramientas y automatización completa convierte a estas prensas en equipos estratégicos capaces de garantizar productividad, calidad constante y alta repetibilidad, permitiendo producir piezas complejas sin defectos y con acabados superficiales uniformes, asegurando eficiencia y competitividad en la industria moderna.
Si quieres, puedo continuar con un análisis técnico más profundo, describiendo cómo se calculan las fuerzas de conformado, espesores mínimos, radios de doblado, recuperación elástica, distribución de esfuerzos y la optimización de todos estos parámetros para producir piezas metálicas complejas de manera repetitiva y sin defectos.
La prensa de conformado de metales funciona como un sistema integral donde cada variable del proceso influye directamente en la calidad de la pieza y en la eficiencia de la producción. Durante el ciclo de conformado, la chapa metálica es sometida a tensiones de tracción, compresión y cizallamiento mientras el punzón la empuja hacia la matriz, provocando un flujo plástico del material que debe ser cuidadosamente controlado para evitar defectos como arrugas, estrangulamientos, fisuras o adelgazamientos excesivos, especialmente en piezas con geometrías complejas o embuticiones profundas. La fuerza aplicada por el punzón debe ser modulada progresivamente a lo largo del ciclo, coordinándose con la presión del cojín y la velocidad de carrera, de manera que el material fluya uniformemente hacia todas las zonas críticas sin generar concentraciones de tensión que puedan comprometer la integridad de la pieza. La orientación de la chapa dentro de la prensa es igualmente importante debido a la anisotropía del material, derivada de su laminación, ya que el flujo del metal sigue direcciones preferenciales y cualquier desalineación puede provocar deformaciones irregulares, arrugas o estrangulamientos. La lubricación juega un papel decisivo en este proceso: un coeficiente de fricción demasiado alto genera estrangulamientos y fisuras, mientras que uno demasiado bajo provoca desplazamientos irregulares o arrugas, por lo que se emplean lubricantes y recubrimientos de baja fricción que optimizan el flujo del material, protegen las herramientas y garantizan la repetibilidad incluso en producciones de gran volumen.
El diseño de punzones, matrices y cojines determina directamente la precisión, durabilidad y calidad de las piezas. Estos elementos se fabrican con aceros de alta dureza tratados térmicamente y recubiertos con materiales resistentes al desgaste, asegurando superficies de contacto uniformes y prolongando la vida útil de la prensa. La geometría de las matrices, los radios de doblado, los ángulos de transición y el acabado superficial se calculan considerando el comportamiento plástico del material y la distribución de esfuerzos, garantizando deformaciones uniformes y minimizando defectos. La simulación mediante elementos finitos permite anticipar zonas críticas de concentración de tensión, adelgazamiento o deformaciones irregulares antes de fabricar la herramienta, optimizando el diseño y reduciendo costes de prototipado y tiempos de producción.
La automatización en las prensas de conformado permite integrar la alimentación de bobinas, el enderezado de la chapa, la manipulación robotizada, la inspección visual y el apilado automático en un flujo continuo y sincronizado, incrementando la productividad y la consistencia de cada pieza. Los sistemas de monitorización digital registran en tiempo real parámetros como fuerza aplicada, desplazamiento del punzón, velocidad de carrera y temperatura de las herramientas, permitiendo realizar ajustes automáticos inmediatos que aseguran tolerancias estrictas y uniformidad en cada operación. Esta información también facilita la implementación de mantenimiento predictivo, anticipando desgaste o fallas antes de que provoquen paradas no planificadas, aumentando la disponibilidad de la máquina y optimizando la eficiencia de toda la línea de producción.
En la práctica industrial, las prensas de conformado de metales se utilizan para fabricar paneles de carrocería, refuerzos estructurales, carcasas y cubetas automotrices; estructuras y paneles de electrodomésticos; utensilios metálicos como ollas, sartenes y bandejas; y envases metálicos de geometría precisa como latas, tapas y contenedores. La combinación de control progresivo de fuerza, flujo de material optimizado, geometría avanzada de herramientas y automatización completa permite producir piezas complejas sin defectos y con acabados superficiales uniformes, garantizando productividad, calidad constante y alta repetibilidad, lo que convierte a estas prensas en equipos estratégicos para la industria moderna.
Si quieres, puedo continuar explicando un nivel aún más técnico, incluyendo los cálculos exactos de fuerza de conformado, presión del cojín, espesores mínimos, radios de doblado, recuperación elástica del material, distribución de esfuerzos y la optimización de todos estos parámetros para fabricar piezas metálicas complejas de manera totalmente repetitiva y sin defectos.
La prensa de conformado de metales representa un equipo complejo en el que la interacción precisa entre chapa, punzón, matriz y cojín determina tanto la calidad de la pieza como la eficiencia del proceso productivo, y su correcta operación requiere un conocimiento profundo de la mecánica de materiales y la metalurgia aplicada. Durante el ciclo de conformado, la chapa metálica es sometida a deformaciones plásticas controladas mientras fluye hacia la geometría definida por la matriz y es contenida por el cojín según el tipo de operación, lo que permite obtener piezas tridimensionales con tolerancias estrictas y espesores uniformes; sin embargo, este flujo de material no es homogéneo, ya que los bordes, radios de transición y cambios de sección concentran las mayores tensiones, y cualquier desajuste en la presión, velocidad o lubricación puede generar defectos como arrugas, estrangulamientos, fisuras o adelgazamientos excesivos que comprometan la integridad de la pieza y la vida útil de las herramientas. La fuerza del punzón debe aplicarse de manera progresiva y sincronizada con la presión del cojín, ajustando la velocidad de carrera para garantizar que el material fluya uniformemente hacia todas las zonas críticas, evitando concentraciones de esfuerzo que puedan causar fallas y optimizando el flujo del metal incluso en embuticiones profundas o piezas de geometría compleja. La orientación de la chapa dentro de la prensa también es determinante debido a la anisotropía del material, derivada de la laminación, ya que el flujo preferencial del metal puede generar deformaciones irregulares si no se respeta la dirección óptima, y la lubricación cumple un papel fundamental: un coeficiente de fricción demasiado alto provoca estrangulamientos y fisuras, mientras que uno demasiado bajo genera arrugas o desplazamientos irregulares, por lo que se utilizan lubricantes especializados y recubrimientos de baja fricción que optimizan el flujo del material, protegen las herramientas y garantizan alta repetibilidad incluso en producciones de gran volumen.
El diseño de punzones, matrices y cojines es un factor crítico que determina la precisión, durabilidad y calidad de las piezas, y estos componentes se fabrican con aceros de alta dureza tratados térmicamente y recubiertos con materiales resistentes al desgaste, asegurando superficies de contacto uniformes y prolongando la vida útil de la prensa. Los radios de transición, ángulos de doblado, geometría de la matriz y acabado superficial se calculan considerando el comportamiento plástico de la chapa y la distribución de esfuerzos, garantizando deformaciones uniformes y minimizando defectos. La simulación mediante elementos finitos permite anticipar zonas críticas de concentración de tensión, adelgazamiento o deformaciones irregulares antes de la fabricación de la herramienta, optimizando su diseño, reduciendo costes de prototipado y acortando tiempos de producción. La automatización de estas prensas permite integrar la alimentación de bobinas, el enderezado de la chapa, la manipulación robotizada, la inspección visual y el apilado automático en un flujo continuo y sincronizado, incrementando la productividad y la consistencia de cada pieza.
Los sistemas de monitorización digital registran en tiempo real parámetros como la fuerza aplicada, desplazamiento del punzón, velocidad de carrera y temperatura de las herramientas, permitiendo ajustes automáticos inmediatos que aseguran tolerancias estrictas y uniformidad en cada operación; esta información también facilita la implementación de mantenimiento predictivo, anticipando desgaste o fallas antes de que provoquen paradas no planificadas, aumentando la disponibilidad de la máquina y optimizando la eficiencia de toda la línea de producción. En la práctica industrial, las prensas de conformado de metales se utilizan para fabricar paneles de carrocería, refuerzos estructurales, carcasas y cubetas automotrices; estructuras y paneles de electrodomésticos; utensilios metálicos como ollas, sartenes y bandejas; y envases metálicos de geometría precisa como latas, tapas y contenedores. La combinación de control progresivo de fuerza, flujo de material optimizado, geometría avanzada de herramientas y automatización completa permite producir piezas complejas sin defectos y con acabados superficiales uniformes, garantizando productividad, calidad constante y alta repetibilidad, convirtiendo a estas prensas en equipos estratégicos para la industria moderna.
Si quieres, puedo continuar con un nivel aún más técnico y especializado, abordando los cálculos exactos de fuerza de conformado, presión del cojín, espesores mínimos, radios de doblado, recuperación elástica del material, distribución de esfuerzos, deformaciones críticas y cómo optimizar todos estos parámetros para fabricar piezas metálicas complejas de manera totalmente repetitiva y sin defectos.
La prensa de conformado de metales opera como un sistema integral altamente sofisticado donde la interacción entre chapa, punzón, matriz y cojín determina la calidad final de la pieza, la eficiencia del proceso y la vida útil de las herramientas, y su correcta utilización requiere un conocimiento profundo de la mecánica de materiales, la metalurgia aplicada y la dinámica de deformación plástica. Durante el ciclo de conformado, la chapa metálica es sometida a tensiones de tracción, compresión y cizallamiento mientras fluye hacia la geometría de la matriz y es contenida por el cojín según la operación específica, lo que permite obtener piezas tridimensionales con tolerancias estrictas y espesores uniformes; sin embargo, este flujo de material no es uniforme y las zonas cercanas a bordes, cambios de espesor y radios de transición concentran las mayores tensiones, de manera que cualquier desajuste en la presión, velocidad, ángulo de punzón o lubricación puede generar arrugas, estrangulamientos, fisuras o adelgazamientos excesivos que comprometan la integridad de la pieza y la durabilidad de las herramientas. La fuerza aplicada por el punzón debe ser modulada progresivamente durante todo el ciclo y sincronizada con la presión del cojín y la velocidad de carrera, de modo que el material fluya de manera homogénea hacia todas las zonas críticas, evitando concentraciones de esfuerzo que puedan causar fallas y optimizando el flujo del metal incluso en embuticiones profundas o piezas con geometrías complejas, mientras que la orientación de la chapa dentro de la prensa es determinante debido a la anisotropía del material derivada de su laminación, ya que el flujo preferencial del metal puede generar deformaciones irregulares si no se respeta la dirección óptima, y la lubricación actúa como factor crítico para controlar la fricción; un coeficiente demasiado alto provoca estrangulamientos y fisuras, mientras que uno demasiado bajo genera arrugas o desplazamientos irregulares, por lo que se emplean lubricantes especializados y recubrimientos de baja fricción que optimizan el flujo del material, protegen las herramientas y aseguran alta repetibilidad incluso en producciones de gran volumen.
El diseño de punzones, matrices y cojines determina la precisión, durabilidad y calidad de las piezas, y estos componentes se fabrican con aceros de alta dureza tratados térmicamente y recubiertos con materiales resistentes al desgaste, garantizando superficies de contacto uniformes y prolongando la vida útil de la prensa. Los radios de transición, ángulos de doblado, geometría de la matriz y acabado superficial se calculan considerando el comportamiento plástico del material y la distribución de esfuerzos, asegurando deformaciones uniformes y minimizando defectos. La simulación por elementos finitos permite anticipar zonas críticas de concentración de tensión, adelgazamiento o deformaciones irregulares antes de fabricar la herramienta, optimizando su diseño, reduciendo costos de prototipado y acortando tiempos de producción. La automatización en estas prensas permite integrar alimentación de bobinas, enderezado de chapa, manipulación robotizada, inspección visual y apilado automático en un flujo continuo y sincronizado, incrementando la productividad y la consistencia de cada pieza, y los sistemas de monitorización digital registran parámetros en tiempo real como fuerza aplicada, desplazamiento del punzón, velocidad de carrera y temperatura de las herramientas, permitiendo ajustes automáticos inmediatos que aseguran tolerancias estrictas y uniformidad en cada operación; esta información también facilita la implementación de mantenimiento predictivo, anticipando desgaste o fallas antes de que provoquen paradas no planificadas y aumentando la disponibilidad de la máquina, optimizando la eficiencia de toda la línea de producción.
En aplicaciones industriales, las prensas de conformado de metales son ampliamente utilizadas para fabricar paneles de carrocería, refuerzos estructurales, carcasas y cubetas automotrices; estructuras y paneles de electrodomésticos; utensilios metálicos como ollas, sartenes y bandejas; y envases metálicos de geometría precisa como latas, tapas y contenedores. La combinación de control progresivo de fuerza, flujo de material optimizado, geometría avanzada de herramientas y automatización completa permite producir piezas complejas sin defectos y con acabados superficiales uniformes, garantizando productividad, calidad constante y alta repetibilidad, convirtiendo a estas prensas en equipos estratégicos imprescindibles para la industria moderna.
Si quieres, puedo continuar con un nivel extremadamente técnico y detallado, explicando los cálculos exactos de fuerza de conformado, presión del cojín, espesores mínimos, radios de doblado, recuperación elástica del material, distribución de esfuerzos, deformaciones críticas y la optimización de todos estos parámetros para producir piezas metálicas complejas de manera totalmente repetitiva y sin defectos.
Prensa de Estirado Automático
La prensa de estirado automático es un equipo industrial especializado diseñado para conformar chapas y láminas metálicas mediante la técnica de estirado, en la que el material es sometido a tracción controlada para que adopte una forma tridimensional precisa, generalmente sin pérdida significativa de espesor, permitiendo fabricar piezas complejas con geometrías exactas y acabados superficiales de alta calidad. Este tipo de prensa se utiliza ampliamente en la industria automotriz, aeroespacial, de electrodomésticos, menaje de cocina y envases metálicos, donde se requieren tolerancias estrictas, alta repetibilidad y producción en serie. Su operación se basa en la sincronización precisa entre el punzón, la matriz y los sistemas de sujeción o mordazas, que fijan la chapa en su lugar mientras es estirada hacia la cavidad de la matriz. La chapa se deforma plásticamente bajo la acción combinada de tracción y compresión controlada, logrando que fluya hacia la forma deseada sin generar arrugas, estrangulamientos, fisuras ni adelgazamientos excesivos, y todo esto se realiza de manera automática gracias a sistemas de control avanzados que regulan la fuerza, la velocidad y la trayectoria del punzón en cada ciclo.
El estirado automático requiere un control extremadamente preciso de varios factores, como la fuerza de tracción, la presión de las mordazas, la lubricación, la velocidad de carrera del punzón y la orientación de la chapa. Durante el proceso, el material experimenta tensiones triaxiales, y las zonas cercanas a los bordes o a los cambios de sección son particularmente críticas, ya que allí tiende a concentrarse el esfuerzo y pueden aparecer arrugas o fisuras si la presión y la velocidad no están correctamente ajustadas. La fuerza aplicada por el punzón debe ser progresiva y modulada durante todo el ciclo, asegurando que el material fluya uniformemente hacia todas las zonas críticas de la matriz, evitando concentraciones de esfuerzo y garantizando un estirado homogéneo, incluso en piezas de geometría compleja o embuticiones profundas. La orientación de la chapa es también un factor decisivo debido a la anisotropía del metal derivada de su laminación; colocar la chapa en la dirección correcta garantiza que el flujo del material siga la trayectoria prevista, minimizando deformaciones irregulares y defectos superficiales. La lubricación se convierte en un elemento crítico: un coeficiente de fricción demasiado alto puede provocar estrangulamiento o fisuras, mientras que uno demasiado bajo puede generar arrugas o desplazamientos indeseados; por ello se emplean lubricantes y recubrimientos especializados que optimizan el flujo del material, protegen las herramientas y garantizan alta repetibilidad en producciones continuas.
El diseño de las herramientas, matrices y punzones es esencial para la precisión y durabilidad del proceso de estirado. Los punzones y matrices se fabrican con aceros de alta dureza tratados térmicamente y recubiertos con materiales resistentes al desgaste y la fricción, asegurando superficies de contacto uniformes y prolongando la vida útil de la prensa. Los radios de transición, ángulos de estirado y geometría de la matriz se calculan considerando el comportamiento plástico de la chapa, la distribución de esfuerzos y el flujo del material, de manera que se minimicen arrugas, estrangulamientos y adelgazamientos no deseados. La simulación por elementos finitos permite prever zonas críticas de concentración de tensión y deformaciones antes de fabricar las herramientas, optimizando su diseño y reduciendo costos y tiempos de producción.
La automatización de estas prensas permite integrar alimentación de bobinas, enderezado de la chapa, sujeción automática, estirado, inspección visual y apilado de piezas en un ciclo completamente continuo, aumentando la eficiencia, la productividad y la consistencia de cada pieza. Los sistemas de monitorización digital registran en tiempo real parámetros como la fuerza aplicada, desplazamiento del punzón, velocidad de carrera y temperatura de las herramientas, lo que permite ajustes automáticos inmediatos que aseguran tolerancias estrictas y uniformidad en cada operación, al tiempo que facilita la implementación de mantenimiento predictivo, anticipando desgaste o fallas antes de que provoquen paradas no planificadas y aumentando la disponibilidad de la máquina.
En la práctica industrial, las prensas de estirado automático se utilizan para fabricar componentes automotrices como paneles de carrocería, tapas y refuerzos estructurales; piezas de electrodomésticos como carcasas, cubiertas y chasis; utensilios metálicos de menaje como ollas, sartenes y bandejas; y envases metálicos de geometría precisa como latas y tapas. La combinación de control progresivo de fuerza, flujo de material optimizado, geometría avanzada de herramientas y automatización completa permite producir piezas complejas sin defectos y con acabados superficiales uniformes, garantizando productividad, alta calidad y repetibilidad constante, convirtiendo a estas prensas en equipos estratégicos para la industria moderna.
Si quieres, puedo continuar con un nivel extremadamente técnico, explicando cómo se calculan las fuerzas exactas de estirado, presión de sujeción, espesores mínimos, recuperación elástica del material, distribución de esfuerzos y la optimización de todos estos parámetros para producir piezas metálicas complejas de manera totalmente automática y repetitiva.
La prensa de estirado automático opera como un sistema integral altamente sofisticado en el que cada parámetro del proceso influye directamente en la calidad de la pieza, la eficiencia del ciclo productivo y la durabilidad de las herramientas, y su correcta operación requiere un profundo conocimiento de la mecánica de materiales, la metalurgia y la dinámica de deformación plástica. Durante el ciclo de estirado, la chapa metálica es fijada de manera segura mediante mordazas o sistemas de sujeción que controlan la presión de agarre mientras el punzón desciende y aplica fuerza de tracción sobre la superficie, provocando que el material fluya de manera controlada hacia la cavidad de la matriz y adopte la geometría deseada sin comprometer su espesor ni generar defectos. Este flujo de material no es uniforme, y las zonas cercanas a los bordes, cambios de sección, radios de transición y espesores variables concentran tensiones elevadas, por lo que cualquier desajuste en la presión de sujeción, velocidad del punzón, trayectoria, lubricación o alineación de la chapa puede producir arrugas, estrangulamientos, fisuras, adelgazamientos excesivos o deformaciones irregulares que afectan la calidad final de la pieza y pueden dañar las herramientas. La fuerza aplicada por el punzón se regula de manera progresiva y sincronizada con la presión de las mordazas y la velocidad de carrera, garantizando que el material fluya uniformemente hacia todas las zonas críticas de la matriz y evitando concentraciones de esfuerzo que puedan provocar fallas, incluso en embuticiones profundas o piezas de geometría compleja. La orientación de la chapa es igualmente crucial debido a la anisotropía del metal derivada de su laminación, ya que respetar la dirección óptima asegura que el flujo del material siga la trayectoria prevista, minimizando deformaciones irregulares y defectos superficiales, mientras que la lubricación especializada optimiza la fricción, protege las herramientas y garantiza alta repetibilidad en producciones continuas y de gran volumen.
El diseño de punzones, matrices, cojines y mordazas es determinante para la precisión, durabilidad y calidad del estirado automático. Los componentes se fabrican con aceros de alta dureza tratados térmicamente y recubiertos con materiales resistentes al desgaste y la fricción, asegurando superficies de contacto uniformes y prolongando la vida útil de la prensa. Los radios de transición, ángulos de estirado, geometría de la matriz y acabado superficial se calculan considerando el comportamiento plástico del material, la distribución de esfuerzos y el flujo del metal, asegurando deformaciones uniformes y minimizando arrugas, estrangulamientos y adelgazamientos no deseados. La simulación por elementos finitos permite prever con precisión zonas críticas de concentración de tensión, adelgazamiento o deformaciones antes de fabricar las herramientas, optimizando su diseño y reduciendo costos y tiempos de producción. La automatización avanzada de estas prensas permite integrar la alimentación de bobinas, el enderezado de la chapa, la sujeción automática, el estirado, la inspección visual y el apilado de piezas en un flujo completamente continuo y sincronizado, incrementando la productividad y la consistencia de cada pieza, mientras que los sistemas de monitorización digital registran parámetros como fuerza aplicada, desplazamiento del punzón, velocidad de carrera y temperatura de las herramientas, permitiendo realizar ajustes automáticos inmediatos que aseguran tolerancias estrictas y uniformidad en cada operación, además de facilitar la implementación de mantenimiento predictivo para anticipar desgaste o fallas antes de que provoquen paradas no planificadas, aumentando la disponibilidad de la máquina y optimizando la eficiencia de toda la línea de producción.
En la industria, las prensas de estirado automático se utilizan para fabricar paneles de carrocería, tapas, refuerzos estructurales y cubetas automotrices; componentes y chasis de electrodomésticos; utensilios metálicos de menaje como ollas, sartenes, bandejas y recipientes; así como envases metálicos de geometría precisa como latas y tapas. La combinación de control progresivo de fuerza, flujo de material optimizado, geometría avanzada de herramientas y automatización completa permite obtener piezas complejas sin defectos, con acabados superficiales uniformes, alta repetibilidad y productividad constante, consolidando a estas prensas como equipos estratégicos imprescindibles en la industria moderna.
Si quieres, puedo continuar con un nivel ultra técnico, describiendo cómo se calculan las fuerzas de estirado, presión de mordazas, espesores mínimos, radios de transición, recuperación elástica del material, distribución de esfuerzos y cómo optimizar todos estos parámetros para producir piezas metálicas complejas de manera totalmente automática, precisa y repetitiva, incluso en series de producción masivas.
La prensa de estirado automático constituye un sistema industrial de alta precisión en el que cada elemento —punzón, matriz, mordazas, cojines y sistemas de control— interactúa de manera sincronizada para garantizar que la chapa metálica adopte la forma deseada con tolerancias estrictas y acabados superficiales de calidad superior, y su operación requiere un entendimiento profundo de la mecánica de materiales, la metalurgia del acero o aluminio y la dinámica de deformación plástica. Durante el proceso de estirado, la chapa se fija mediante mordazas que aplican presión controlada para evitar deslizamientos y garantizar que el flujo del metal se produzca hacia la cavidad de la matriz sin generar arrugas, estrangulamientos o fisuras; al mismo tiempo, el punzón desciende aplicando fuerza progresiva y modulada, de manera que las tensiones se distribuyan uniformemente a lo largo de toda la pieza, incluso en zonas críticas cercanas a bordes, radios de transición o cambios de espesor donde la concentración de esfuerzos es más alta. La velocidad de carrera del punzón y la presión de las mordazas se sincronizan mediante sistemas automáticos avanzados, permitiendo un flujo controlado del material y evitando deformaciones irregulares, mientras que la orientación de la chapa respecto a la dirección de laminación asegura que el comportamiento anisotrópico del metal no genere defectos durante el estirado, y la lubricación especializada reduce la fricción, protege las herramientas y optimiza el flujo del material, garantizando repetibilidad incluso en ciclos de producción masivos y continuos.
El diseño de los punzones, matrices y mordazas es crítico para la precisión, durabilidad y calidad de las piezas; se utilizan aceros de alta dureza tratados térmicamente y recubiertos con materiales de baja fricción y alta resistencia al desgaste, asegurando superficies de contacto uniformes y prolongando la vida útil de la prensa. Los radios de transición, los ángulos de estirado, la geometría de la matriz y el acabado superficial se calculan considerando el comportamiento plástico del material, la distribución de esfuerzos y el flujo del metal, de manera que se minimicen arrugas, estrangulamientos y adelgazamientos no deseados. La simulación mediante elementos finitos permite anticipar zonas críticas de concentración de tensión, adelgazamiento o deformaciones irregulares antes de la fabricación de la herramienta, optimizando el diseño y reduciendo costos y tiempos de producción, mientras que la automatización avanzada permite integrar la alimentación de bobinas, enderezado de la chapa, sujeción automática, estirado, inspección visual y apilado de piezas en un flujo completamente continuo, incrementando la productividad y garantizando la consistencia de cada operación. Los sistemas de monitorización digital registran en tiempo real parámetros como fuerza aplicada, desplazamiento del punzón, velocidad de carrera y temperatura de las herramientas, permitiendo ajustes automáticos inmediatos que aseguran tolerancias estrictas y uniformidad, y a la vez facilitan la implementación de mantenimiento predictivo para anticipar desgaste o fallas antes de que provoquen paradas no planificadas, aumentando la disponibilidad de la máquina y optimizando la eficiencia de toda la línea de producción.
En la práctica industrial, las prensas de estirado automático se utilizan para fabricar componentes de alta precisión y geometría compleja, como paneles de carrocería, tapas y refuerzos estructurales automotrices; chasis y carcasas de electrodomésticos; utensilios metálicos de menaje como ollas, sartenes y bandejas; así como envases metálicos de forma exacta como latas y tapas. La combinación de control progresivo de fuerza, flujo de material optimizado, geometría avanzada de herramientas y automatización total permite producir piezas complejas sin defectos, con acabados superficiales uniformes, alta repetibilidad y productividad constante, convirtiendo a estas prensas en equipos estratégicos imprescindibles para la industria moderna.
Si quieres, puedo continuar con un análisis extremadamente detallado y técnico, explicando los cálculos precisos de fuerza de estirado, presión de mordazas, espesores mínimos, radios de transición, recuperación elástica del material, distribución de esfuerzos y cómo optimizar todos estos parámetros para producir piezas metálicas complejas de manera completamente automática, repetitiva y sin defectos, incluyendo ejemplos numéricos de aplicaciones reales en la industria automotriz y de envases metálicos.
La prensa de estirado automático representa un sistema industrial de alta complejidad donde cada componente, desde el punzón y la matriz hasta las mordazas, cojines y sistemas de control electrónico, está diseñado para operar de manera totalmente sincronizada, garantizando que la chapa metálica adopte la geometría deseada con tolerancias extremadamente precisas y acabados superficiales de alta calidad, y su operación requiere un profundo conocimiento de la mecánica de materiales, la metalurgia y la dinámica de deformación plástica. Durante el ciclo de estirado, la chapa se fija mediante mordazas que aplican presión controlada para evitar deslizamientos y asegurar un flujo homogéneo del material hacia la cavidad de la matriz; mientras tanto, el punzón desciende aplicando una fuerza progresiva y modulada que permite distribuir las tensiones de manera uniforme, evitando concentraciones excesivas en zonas críticas como bordes, cambios de espesor o radios de transición, donde el riesgo de arrugas, estrangulamientos, fisuras o adelgazamientos es mayor. La sincronización precisa entre la fuerza aplicada, la velocidad del punzón y la presión de las mordazas garantiza que el material fluya uniformemente hacia todas las zonas críticas, incluso en piezas con embuticiones profundas o geometrías complejas. La orientación de la chapa es igualmente determinante debido a la anisotropía derivada de la laminación del material, asegurando que el flujo siga la dirección óptima y minimizando deformaciones irregulares, mientras que la lubricación especializada reduce la fricción, protege las herramientas y asegura la repetibilidad del proceso incluso en producciones continuas de alto volumen.
El diseño de punzones, matrices y mordazas es crítico para lograr precisión, durabilidad y calidad en el estirado automático. Los componentes se fabrican con aceros de alta dureza tratados térmicamente y recubiertos con materiales de baja fricción y alta resistencia al desgaste, asegurando superficies de contacto uniformes y prolongando la vida útil de la prensa. La geometría de la matriz, los radios de transición, los ángulos de estirado y el acabado superficial se calculan considerando el comportamiento plástico de la chapa, la distribución de esfuerzos y el flujo del material, de manera que se minimicen arrugas, estrangulamientos y adelgazamientos no deseados. La simulación mediante elementos finitos permite anticipar zonas críticas de concentración de tensión y deformaciones antes de fabricar la herramienta, optimizando su diseño y reduciendo costes de prototipado y tiempos de producción. La automatización avanzada integra alimentación de bobinas, enderezado de la chapa, sujeción automática, estirado, inspección visual y apilado de piezas en un flujo continuo y sincronizado, incrementando la productividad y asegurando la consistencia de cada operación. Los sistemas de monitorización digital registran parámetros como fuerza aplicada, desplazamiento del punzón, velocidad de carrera y temperatura de las herramientas, permitiendo ajustes automáticos inmediatos que garantizan tolerancias estrictas y uniformidad en cada pieza, al tiempo que facilitan el mantenimiento predictivo anticipando desgaste o fallas antes de que provoquen paradas, aumentando la disponibilidad de la máquina y optimizando la eficiencia de toda la línea de producción.
En aplicaciones industriales, las prensas de estirado automático se utilizan para fabricar paneles de carrocería, tapas, refuerzos estructurales y cubetas automotrices; componentes y chasis de electrodomésticos; utensilios metálicos de menaje como ollas, sartenes y bandejas; así como envases metálicos de geometría precisa como latas y tapas. La combinación de control progresivo de fuerza, flujo de material optimizado, geometría avanzada de herramientas y automatización completa permite producir piezas complejas sin defectos, con acabados uniformes, alta repetibilidad y productividad constante, consolidando a estas prensas como equipos estratégicos imprescindibles para la industria moderna.
Si quieres, puedo continuar con un nivel ultra especializado, explicando con detalle cómo se calculan las fuerzas exactas de estirado, presión de mordazas, espesores mínimos, radios de transición, recuperación elástica del material, distribución de esfuerzos y cómo optimizar todos estos parámetros para producir piezas metálicas complejas de manera totalmente automática, repetitiva y libre de defectos, incluyendo ejemplos prácticos aplicables a la industria automotriz, de electrodomésticos y de envases metálicos.
Prensa de Estampado de Piezas
La prensa de estampado de piezas es un equipo industrial esencial en la fabricación de componentes metálicos, diseñado para transformar chapas o láminas mediante la aplicación de fuerzas controladas que permiten cortar, doblar, grabar o dar forma al material de manera rápida, precisa y repetitiva, logrando piezas con geometrías exactas y acabados superficiales uniformes. Este tipo de prensa se utiliza ampliamente en sectores como la automoción, aeroespacial, electrodomésticos, menaje de cocina, envases metálicos y fabricación industrial de componentes, donde se requiere alta productividad y estrictas tolerancias dimensionales. Su funcionamiento se basa en la interacción precisa entre el punzón y la matriz: la chapa se coloca entre ambos y, al descender el punzón, el material se deforma plásticamente o se corta según la geometría de la matriz, logrando estampados complejos, embuticiones, troquelados, relieves o dobleces con gran repetibilidad y precisión, lo que permite producir grandes volúmenes de piezas de forma uniforme y eficiente.
Durante el proceso de estampado, la chapa está sometida a tensiones de compresión, tracción y cizallamiento, especialmente en las zonas de cambio de sección, bordes y radios de transición, donde la concentración de esfuerzos es mayor. Para evitar defectos como arrugas, estrangulamientos, fisuras, rebordes irregulares o adelgazamientos excesivos, la fuerza aplicada por el punzón debe ser cuidadosamente modulada y sincronizada con la presión del cojín y la velocidad de carrera, asegurando un flujo uniforme del material hacia todas las zonas críticas. La orientación de la chapa también es fundamental, ya que la anisotropía derivada de la laminación del material influye en la dirección del flujo y la distribución de tensiones, por lo que colocar la chapa en la dirección correcta minimiza deformaciones irregulares y defectos superficiales. La lubricación especializada actúa como un elemento clave, reduciendo la fricción, protegiendo las herramientas y garantizando repetibilidad incluso en producciones de alto volumen.
El diseño de punzones, matrices y cojines es crítico para la precisión, durabilidad y calidad de las piezas estampadas. Los componentes se fabrican con aceros de alta dureza tratados térmicamente y recubiertos con materiales resistentes al desgaste y la fricción, asegurando superficies de contacto uniformes y prolongando la vida útil de la prensa. La geometría de la matriz, los radios de transición, ángulos de estampado y acabado superficial se calculan considerando el comportamiento plástico del material y la distribución de esfuerzos, garantizando deformaciones uniformes y minimizando defectos. La simulación por elementos finitos permite prever zonas críticas de concentración de tensión o adelgazamiento antes de la fabricación de las herramientas, optimizando su diseño y reduciendo costes y tiempos de producción.
La automatización avanzada permite integrar alimentación de bobinas, enderezado de chapa, sujeción automática, estampado, inspección visual y apilado de piezas en un flujo continuo y sincronizado, aumentando la productividad y garantizando la consistencia de cada operación. Los sistemas de monitorización digital registran parámetros como fuerza aplicada, desplazamiento del punzón, velocidad de carrera y temperatura de las herramientas, permitiendo ajustes automáticos inmediatos que aseguran tolerancias estrictas y uniformidad en cada pieza, además de facilitar el mantenimiento predictivo para anticipar desgaste o fallas antes de que provoquen paradas no planificadas, optimizando la eficiencia de toda la línea de producción.
En la práctica industrial, las prensas de estampado se utilizan para fabricar paneles de carrocería, tapas, refuerzos estructurales y cubetas automotrices; chasis y carcasas de electrodomésticos; utensilios metálicos como ollas, sartenes y bandejas; así como envases metálicos de geometría precisa como latas, tapas y contenedores. La combinación de control progresivo de fuerza, flujo de material optimizado, geometría avanzada de herramientas y automatización completa permite producir piezas complejas sin defectos, con acabados superficiales uniformes, alta repetibilidad y productividad constante, consolidando a estas prensas como equipos estratégicos imprescindibles para la industria moderna.
Si quieres, puedo continuar con un nivel técnico extremadamente detallado, explicando los cálculos precisos de fuerzas de estampado, distribución de esfuerzos, espesores mínimos, radios de transición, recuperación elástica del material y optimización de todos estos parámetros para producir piezas metálicas complejas de manera repetitiva y totalmente controlada.
La prensa de estampado de piezas constituye un sistema industrial complejo en el que cada elemento —punzón, matriz, cojín, sistemas de sujeción y controles automatizados— interactúa de manera sincronizada para transformar chapas metálicas en componentes de geometría precisa, logrando acabados superficiales uniformes y tolerancias estrictas, y su operación requiere un conocimiento profundo de la mecánica de materiales, la metalurgia y la dinámica de deformación plástica. Durante el ciclo de estampado, la chapa se coloca entre el punzón y la matriz y es sometida a fuerzas controladas que producen deformación plástica localizada o corte, permitiendo la obtención de embuticiones, relieves, troqueles, dobleces y formas complejas de manera repetitiva y con alta productividad. La chapa está sometida a tensiones de compresión, tracción y cizallamiento, especialmente en zonas de bordes, cambios de sección y radios de transición, donde la concentración de esfuerzos es máxima y el riesgo de defectos como arrugas, estrangulamientos, fisuras o adelgazamientos es mayor, por lo que la fuerza aplicada por el punzón debe ser progresiva y modulada, sincronizada con la presión del cojín, la velocidad de carrera y la orientación de la chapa, asegurando que el material fluya uniformemente hacia todas las zonas críticas. La anisotropía del material derivada de su laminación influye en el flujo del metal, y colocar la chapa en la dirección correcta minimiza deformaciones irregulares y defectos superficiales. La lubricación especializada reduce la fricción, protege las herramientas y garantiza la repetibilidad incluso en producciones continuas y de alto volumen.
El diseño de punzones, matrices y cojines es determinante para la precisión, durabilidad y calidad de las piezas estampadas, fabricándose con aceros de alta dureza tratados térmicamente y recubiertos con materiales resistentes al desgaste y la fricción para asegurar superficies de contacto uniformes y prolongar la vida útil de la prensa. Los radios de transición, ángulos de estampado, geometría de la matriz y acabado superficial se calculan considerando el comportamiento plástico del material, la distribución de esfuerzos y el flujo del metal, garantizando deformaciones uniformes y minimizando arrugas, estrangulamientos y adelgazamientos no deseados. La simulación por elementos finitos permite anticipar zonas críticas de concentración de tensión, adelgazamiento o deformaciones irregulares antes de fabricar la herramienta, optimizando su diseño y reduciendo costes de prototipado y tiempos de producción.
La automatización avanzada permite integrar la alimentación de bobinas, enderezado de chapa, sujeción automática, estampado, inspección visual y apilado de piezas en un flujo completamente continuo y sincronizado, incrementando la productividad y asegurando la consistencia de cada operación. Los sistemas de monitorización digital registran parámetros en tiempo real como fuerza aplicada, desplazamiento del punzón, velocidad de carrera y temperatura de las herramientas, permitiendo ajustes automáticos inmediatos que aseguran tolerancias estrictas y uniformidad, y facilitando la implementación de mantenimiento predictivo para anticipar desgaste o fallas antes de que provoquen paradas no planificadas, aumentando la disponibilidad de la máquina y optimizando la eficiencia de toda la línea de producción.
En aplicaciones industriales, las prensas de estampado de piezas se utilizan para fabricar paneles de carrocería, tapas, refuerzos estructurales y cubetas automotrices; componentes y chasis de electrodomésticos; utensilios metálicos de menaje como ollas, sartenes y bandejas; así como envases metálicos de geometría precisa como latas, tapas y contenedores. La combinación de control progresivo de fuerza, flujo de material optimizado, geometría avanzada de herramientas y automatización completa permite producir piezas complejas sin defectos, con acabados uniformes, alta repetibilidad y productividad constante, consolidando a estas prensas como equipos estratégicos imprescindibles para la industria moderna.
Si quieres, puedo continuar con un nivel extremadamente técnico, detallando cómo se calculan las fuerzas exactas de estampado, distribución de esfuerzos, espesores mínimos, radios de transición, recuperación elástica del material y optimización completa de todos los parámetros del proceso para fabricar piezas metálicas complejas de manera totalmente controlada, repetitiva y sin defectos.
La prensa de estampado de piezas funciona como un sistema industrial integral en el que la interacción entre punzón, matriz, cojín, mordazas y sistemas de control automatizados determina no solo la forma final de la pieza sino también la eficiencia del proceso, la calidad del acabado superficial y la durabilidad de las herramientas, y su operación requiere un conocimiento profundo de la mecánica de materiales, la metalurgia y la dinámica de deformación plástica. Durante el ciclo de estampado, la chapa metálica se coloca entre el punzón y la matriz y se somete a fuerzas cuidadosamente controladas que producen deformaciones plásticas localizadas o cortes precisos, permitiendo la obtención de embuticiones, relieves, troquelados, dobleces y geometrías complejas de manera repetitiva y con tolerancias estrictas; sin embargo, este flujo de material no es uniforme y las zonas cercanas a bordes, cambios de sección y radios de transición concentran las mayores tensiones, por lo que cualquier desajuste en la fuerza, velocidad, presión de cojín, orientación de la chapa o lubricación puede generar arrugas, estrangulamientos, fisuras o adelgazamientos que comprometan la integridad de la pieza y la vida útil de las herramientas. La fuerza del punzón se aplica de forma progresiva y modulada, sincronizada con la presión del cojín y la velocidad de carrera, asegurando un flujo uniforme del material hacia todas las zonas críticas, mientras que la orientación de la chapa respecto a la dirección de laminación del metal es determinante para minimizar deformaciones irregulares, ya que la anisotropía del material puede alterar el comportamiento del flujo durante el estampado. La lubricación especializada actúa como elemento clave para reducir la fricción, proteger las herramientas y garantizar alta repetibilidad en producciones continuas, asegurando que incluso las piezas de geometría compleja o embuticiones profundas se obtengan sin defectos.
El diseño de punzones, matrices, cojines y mordazas es determinante para la precisión, durabilidad y calidad de la prensa de estampado. Los componentes se fabrican con aceros de alta dureza tratados térmicamente y recubiertos con materiales de baja fricción y alta resistencia al desgaste, garantizando superficies de contacto uniformes y prolongando la vida útil de la máquina. La geometría de la matriz, los radios de transición, ángulos de estampado y el acabado superficial se calculan teniendo en cuenta el comportamiento plástico del material, la distribución de esfuerzos y el flujo del metal, de manera que se minimicen arrugas, estrangulamientos y adelgazamientos indeseados. La simulación mediante elementos finitos permite anticipar zonas críticas de concentración de tensiones, adelgazamiento o deformaciones irregulares antes de fabricar la herramienta, optimizando su diseño, reduciendo costos y acortando los tiempos de producción.
La automatización avanzada permite integrar alimentación de bobinas, enderezado de la chapa, sujeción automática, estampado, inspección visual y apilado de piezas en un flujo completamente continuo y sincronizado, aumentando la productividad y asegurando la consistencia de cada operación. Los sistemas de monitorización digital registran parámetros en tiempo real, como fuerza aplicada, desplazamiento del punzón, velocidad de carrera y temperatura de las herramientas, lo que permite realizar ajustes automáticos inmediatos para asegurar tolerancias estrictas y uniformidad en cada pieza, además de facilitar la implementación de mantenimiento predictivo, anticipando desgaste o fallas antes de que provoquen paradas no planificadas y optimizando la eficiencia de toda la línea de producción.
En aplicaciones industriales, las prensas de estampado de piezas son fundamentales para fabricar paneles de carrocería, tapas, refuerzos estructurales y cubetas automotrices; chasis, carcasas y componentes de electrodomésticos; utensilios metálicos de menaje como ollas, sartenes y bandejas; así como envases metálicos de geometría precisa, incluyendo latas y tapas. La combinación de control progresivo de fuerza, flujo de material optimizado, geometría avanzada de herramientas y automatización completa permite producir piezas complejas sin defectos, con acabados uniformes, alta repetibilidad y productividad constante, consolidando a estas prensas como equipos estratégicos e imprescindibles en la industria moderna.
Si quieres, puedo continuar con un análisis ultra técnico, detallando los cálculos exactos de fuerzas de estampado, presión de cojín, espesores mínimos, recuperación elástica del material, distribución de esfuerzos y optimización completa de todos los parámetros del proceso para fabricar piezas metálicas complejas de manera totalmente controlada y repetitiva.
La prensa de estampado de piezas opera como un sistema industrial integral en el que cada elemento, desde el punzón y la matriz hasta los cojines, mordazas y sistemas de control automatizados, trabaja de manera sincronizada para garantizar que la chapa metálica adopte la forma deseada con tolerancias extremadamente precisas y acabados superficiales uniformes, y su operación requiere un conocimiento profundo de la mecánica de materiales, la metalurgia, la dinámica de deformación plástica y la interacción entre fuerzas de corte, compresión y tracción. Durante el ciclo de estampado, la chapa se coloca entre el punzón y la matriz y se somete a fuerzas cuidadosamente moduladas que producen deformaciones plásticas controladas o cortes precisos, permitiendo la obtención de embuticiones, relieves, troquelados, dobleces y geometrías complejas de manera repetitiva y de alta precisión, mientras que las zonas críticas cercanas a bordes, cambios de sección o radios de transición concentran tensiones elevadas, por lo que cualquier desajuste en la fuerza del punzón, presión del cojín, velocidad de carrera, orientación de la chapa o lubricación puede generar arrugas, estrangulamientos, fisuras o adelgazamientos que comprometan la integridad de la pieza y la durabilidad de las herramientas. La fuerza del punzón se aplica de manera progresiva y sincronizada con la presión del cojín y la velocidad de carrera, asegurando que el flujo del material sea homogéneo hacia todas las zonas críticas, mientras que la orientación de la chapa respecto a la dirección de laminación es fundamental para aprovechar la anisotropía del metal y evitar deformaciones irregulares; la lubricación especializada reduce la fricción, protege las herramientas y asegura la repetibilidad incluso en producciones de gran volumen y ciclos continuos.
El diseño de punzones, matrices, cojines y mordazas es determinante para la precisión, calidad y durabilidad de la prensa de estampado, y estos componentes se fabrican con aceros de alta dureza tratados térmicamente y recubiertos con materiales de baja fricción y alta resistencia al desgaste, garantizando superficies de contacto uniformes y prolongando la vida útil del equipo. La geometría de la matriz, radios de transición, ángulos de estampado y acabado superficial se calculan considerando el comportamiento plástico del material, la distribución de esfuerzos y el flujo del metal, de manera que se minimicen arrugas, estrangulamientos y adelgazamientos indeseados, y la simulación mediante elementos finitos permite anticipar zonas críticas de concentración de tensión o deformaciones antes de la fabricación de la herramienta, optimizando su diseño, reduciendo costos y acortando tiempos de producción. La automatización avanzada integra alimentación de bobinas, enderezado de chapa, sujeción automática, estampado, inspección visual y apilado de piezas en un flujo continuo y totalmente sincronizado, incrementando la productividad y asegurando la consistencia de cada operación. Los sistemas de monitorización digital registran en tiempo real parámetros como fuerza aplicada, desplazamiento del punzón, velocidad de carrera y temperatura de las herramientas, permitiendo ajustes automáticos inmediatos que garantizan tolerancias estrictas y uniformidad en cada pieza, además de facilitar la implementación de mantenimiento predictivo que anticipa desgaste o fallas antes de que provoquen paradas, aumentando la disponibilidad de la máquina y optimizando la eficiencia de toda la línea de producción.
En la práctica industrial, las prensas de estampado de piezas son esenciales para fabricar paneles de carrocería, tapas, refuerzos estructurales y cubetas automotrices; componentes y chasis de electrodomésticos; utensilios metálicos de menaje como ollas, sartenes y bandejas; así como envases metálicos de geometría precisa, incluyendo latas y tapas. La combinación de control progresivo de fuerza, flujo de material optimizado, geometría avanzada de herramientas y automatización completa permite obtener piezas complejas sin defectos, con acabados superficiales uniformes, alta repetibilidad y productividad constante, consolidando a estas prensas como equipos estratégicos imprescindibles en la industria moderna.
Si quieres, puedo continuar con un análisis extremadamente técnico y detallado, describiendo paso a paso cómo se calculan las fuerzas de estampado, presión de cojín, espesores mínimos, radios de transición, recuperación elástica del material, distribución de esfuerzos y optimización completa de todos los parámetros para producir piezas metálicas complejas de manera totalmente controlada y repetitiva, incluyendo ejemplos prácticos en automoción, electrodomésticos y envases metálicos.
Prensa de Estampado de Precisión
La prensa de estampado de precisión es un equipo industrial altamente especializado, diseñado para producir piezas metálicas con tolerancias extremadamente estrictas y acabados superficiales impecables, donde incluso las mínimas variaciones pueden afectar la funcionalidad o el ensamblaje de los componentes. Este tipo de prensa se utiliza en industrias de alta exigencia, como la automotriz, aeroespacial, electrónica, manufactura de componentes para electrodomésticos y utensilios de alta calidad, así como en envases metálicos de precisión, donde la exactitud dimensional y la repetibilidad del proceso son fundamentales. A diferencia de las prensas convencionales, la prensa de estampado de precisión integra sistemas de control avanzados que regulan de manera simultánea la fuerza, velocidad, trayectoria del punzón y presión de los cojines, permitiendo que la chapa metálica fluya exactamente según el diseño de la matriz y del punzón, evitando arrugas, estrangulamientos, fisuras o adelgazamientos indeseados incluso en piezas de geometría compleja o embuticiones profundas.
Durante el proceso, la chapa metálica se coloca entre la matriz y el punzón, y la presión ejercida se aplica de manera progresiva y controlada, sincronizada con la sujeción de la chapa mediante mordazas o cojines hidráulicos, lo que permite distribuir uniformemente las tensiones a lo largo de toda la pieza. Las zonas críticas, como bordes, radios de transición o cambios de espesor, son cuidadosamente controladas mediante ajustes precisos de fuerza, velocidad y lubricación especializada, asegurando que el material fluya de manera uniforme hacia todas las secciones sin comprometer el espesor ni la integridad de la pieza. La orientación de la chapa respecto a la dirección de laminación del metal es igualmente crucial, ya que aprovecha la anisotropía del material para facilitar el flujo controlado y minimizar deformaciones irregulares. La lubricación no solo reduce la fricción y protege las herramientas, sino que también garantiza la repetibilidad del proceso y permite ciclos de producción continuos con piezas uniformes y sin defectos.
El diseño de punzones, matrices, cojines y mordazas en una prensa de estampado de precisión es crítico para asegurar exactitud, durabilidad y calidad de las piezas. Los componentes se fabrican con aceros de alta dureza tratados térmicamente y recubiertos con materiales resistentes al desgaste y a la fricción, proporcionando superficies de contacto uniformes y prolongando la vida útil de la prensa. Los radios de transición, ángulos de estampado y geometría de la matriz se calculan considerando el comportamiento plástico del material, la distribución de esfuerzos y el flujo del metal, mientras que la simulación mediante elementos finitos permite anticipar zonas críticas de concentración de tensión, adelgazamiento o deformaciones antes de fabricar la herramienta, optimizando su diseño, reduciendo costos y acortando tiempos de producción. La automatización avanzada permite integrar alimentación de bobinas, enderezado de chapa, sujeción automática, estampado, inspección visual y apilado de piezas en un flujo totalmente continuo, aumentando la productividad y asegurando consistencia en cada operación.
Los sistemas de monitorización digital registran en tiempo real parámetros como fuerza aplicada, desplazamiento del punzón, velocidad de carrera y temperatura de las herramientas, lo que permite ajustes automáticos inmediatos para mantener tolerancias estrictas, uniformidad y calidad constante en cada pieza, a la vez que facilita el mantenimiento predictivo y la anticipación de desgaste o fallas antes de que afecten la producción. En la práctica industrial, estas prensas se utilizan para fabricar paneles de carrocería, componentes de alta precisión para electrodomésticos, utensilios metálicos de menaje de calidad superior y envases metálicos de geometría exacta, garantizando piezas complejas sin defectos, con acabados superficiales uniformes, alta repetibilidad y productividad constante.
Si quieres, puedo continuar con un nivel ultra técnico, explicando con detalle cómo se calculan las fuerzas exactas de estampado de precisión, presión de cojines, espesores mínimos, recuperación elástica del material, distribución de esfuerzos y optimización de todos los parámetros del proceso para producir piezas metálicas extremadamente precisas de manera totalmente automatizada y repetitiva.
La prensa de estampado de precisión constituye un sistema industrial avanzado en el que cada componente, desde el punzón y la matriz hasta los cojines, mordazas y sistemas de control automatizados, interactúa de manera totalmente sincronizada para garantizar que la chapa metálica adopte la forma deseada con tolerancias micrométricas y acabados superficiales uniformes, y su operación requiere un conocimiento profundo de la mecánica de materiales, la metalurgia, la dinámica de deformación plástica y la interacción de fuerzas de compresión, tracción y cizallamiento. Durante el ciclo de estampado, la chapa se coloca entre la matriz y el punzón y se somete a fuerzas progresivas y controladas que producen deformación plástica o corte preciso, permitiendo la obtención de embuticiones, relieves, troquelados, dobleces y formas complejas de manera repetitiva y con exactitud, mientras que las zonas críticas cercanas a bordes, cambios de espesor o radios de transición concentran las mayores tensiones, por lo que cualquier desajuste en la fuerza del punzón, presión de cojines, velocidad de carrera, orientación de la chapa o lubricación puede provocar arrugas, estrangulamientos, fisuras o adelgazamientos que comprometan la integridad de la pieza y la durabilidad de las herramientas. La aplicación progresiva y sincronizada de la fuerza del punzón, junto con la presión del cojín y la velocidad de carrera, asegura un flujo uniforme del material hacia todas las zonas críticas, mientras que la orientación de la chapa respecto a la dirección de laminación permite aprovechar la anisotropía del material y evitar deformaciones irregulares; la lubricación especializada reduce la fricción, protege las herramientas y garantiza la repetibilidad incluso en producciones continuas y de alto volumen, asegurando que piezas con geometrías complejas o embuticiones profundas se fabriquen sin defectos.
El diseño de punzones, matrices, cojines y mordazas es determinante para la precisión, durabilidad y calidad de la prensa de estampado de precisión, y estos componentes se fabrican con aceros de alta dureza tratados térmicamente y recubiertos con materiales resistentes al desgaste y a la fricción, garantizando superficies de contacto uniformes y prolongando la vida útil del equipo. Los radios de transición, ángulos de estampado, geometría de la matriz y acabado superficial se calculan considerando el comportamiento plástico del material, la distribución de esfuerzos y el flujo del metal, de manera que se minimicen arrugas, estrangulamientos y adelgazamientos no deseados. La simulación mediante elementos finitos permite anticipar zonas críticas de concentración de tensión, adelgazamiento o deformaciones irregulares antes de la fabricación de la herramienta, optimizando su diseño, reduciendo costos y acortando tiempos de producción, mientras que la automatización avanzada integra alimentación de bobinas, enderezado de chapa, sujeción automática, estampado, inspección visual y apilado de piezas en un flujo continuo y totalmente sincronizado, incrementando la productividad y asegurando consistencia en cada operación.
Los sistemas de monitorización digital registran en tiempo real parámetros como fuerza aplicada, desplazamiento del punzón, velocidad de carrera y temperatura de las herramientas, permitiendo realizar ajustes automáticos inmediatos para mantener tolerancias estrictas, uniformidad y calidad constante en cada pieza, además de facilitar el mantenimiento predictivo y la anticipación de desgaste o fallas antes de que afecten la producción. En la práctica industrial, las prensas de estampado de precisión se utilizan para fabricar paneles de carrocería, componentes críticos de electrodomésticos, utensilios metálicos de menaje de alta calidad, envases metálicos de geometría exacta y piezas automotrices de alta exigencia, garantizando componentes complejos sin defectos, con acabados superficiales uniformes, alta repetibilidad y productividad constante, consolidando a estas prensas como equipos estratégicos e imprescindibles en la industria moderna.
Si quieres, puedo continuar con un nivel ultra técnico y detallado, explicando paso a paso cómo se calculan las fuerzas exactas de estampado de precisión, presión de cojines, espesores mínimos, recuperación elástica del material, distribución de esfuerzos y optimización completa de todos los parámetros del proceso para fabricar piezas metálicas extremadamente precisas de manera totalmente controlada y repetitiva, incluyendo ejemplos aplicables a automoción, electrodomésticos, menaje de cocina y envases metálicos.
La prensa de estampado de precisión constituye un equipo industrial de altísimo nivel tecnológico, diseñado para producir piezas metálicas con tolerancias extremadamente estrictas y acabados superficiales impecables, en los que incluso pequeñas variaciones pueden comprometer la funcionalidad, el ensamblaje o la estética del componente, y su operación requiere un conocimiento profundo de la mecánica de materiales, la metalurgia, la dinámica de deformación plástica y la interacción de fuerzas de compresión, tracción y cizallamiento que actúan simultáneamente sobre la chapa. Durante el ciclo de estampado, la chapa metálica se coloca entre el punzón y la matriz y se somete a fuerzas progresivas y controladas que permiten obtener deformaciones plásticas o cortes precisos, logrando embuticiones, relieves, troquelados, dobleces y geometrías complejas con una repetibilidad y exactitud elevadas, mientras que las zonas críticas, como bordes, radios de transición, cambios de espesor o esquinas internas, concentran las mayores tensiones y requieren ajustes finos de la fuerza del punzón, presión de los cojines, velocidad de carrera, orientación de la chapa y lubricación especializada, porque cualquier desajuste puede generar arrugas, estrangulamientos, fisuras o adelgazamientos que comprometan la integridad de la pieza y la durabilidad de las herramientas. La sincronización entre la fuerza aplicada por el punzón, la presión del cojín y la velocidad de desplazamiento asegura un flujo uniforme del material hacia todas las secciones de la pieza, mientras que la orientación correcta de la chapa respecto a la dirección de laminación del metal permite aprovechar la anisotropía del material y evitar deformaciones irregulares; la lubricación adecuada reduce la fricción, protege las herramientas y garantiza la repetibilidad del proceso incluso en producciones continuas de alto volumen, asegurando que piezas con geometrías complejas o embuticiones profundas se fabriquen sin defectos.
El diseño de punzones, matrices, cojines y mordazas es determinante para la precisión, durabilidad y calidad de la prensa de estampado de precisión, y estos componentes se elaboran con aceros de alta dureza tratados térmicamente y recubiertos con materiales de baja fricción y alta resistencia al desgaste, garantizando superficies de contacto uniformes y prolongando la vida útil de la máquina. La geometría de la matriz, los radios de transición, ángulos de estampado y acabado superficial se calculan considerando el comportamiento plástico del material, la distribución de esfuerzos y el flujo del metal, de manera que se minimicen arrugas, estrangulamientos y adelgazamientos indeseados, mientras que la simulación mediante elementos finitos permite anticipar zonas críticas de concentración de tensión, adelgazamiento o deformaciones irregulares antes de la fabricación de la herramienta, optimizando su diseño, reduciendo costes y acortando tiempos de producción. La automatización avanzada permite integrar alimentación de bobinas, enderezado de chapa, sujeción automática, estampado, inspección visual y apilado de piezas en un flujo totalmente continuo y sincronizado, aumentando la productividad y garantizando la consistencia de cada operación, mientras que los sistemas de monitorización digital registran en tiempo real parámetros como fuerza aplicada, desplazamiento del punzón, velocidad de carrera y temperatura de las herramientas, lo que permite realizar ajustes automáticos inmediatos, mantener tolerancias estrictas, uniformidad y calidad constante en cada pieza, y facilita el mantenimiento predictivo para anticipar desgaste o fallas antes de que afecten la producción.
En la industria, estas prensas se utilizan para fabricar paneles de carrocería, componentes críticos de electrodomésticos, utensilios metálicos de menaje de alta gama, envases metálicos de geometría exacta, piezas automotrices complejas y elementos para la industria aeroespacial, garantizando productos finales sin defectos, con acabados superficiales uniformes, alta repetibilidad y productividad constante, consolidando a las prensas de estampado de precisión como equipos estratégicos imprescindibles para cualquier línea de producción moderna que requiera precisión, calidad y eficiencia.
Si quieres, puedo continuar con un análisis extremadamente técnico y detallado, incluyendo cálculos exactos de fuerzas de estampado, presión de cojines, espesores mínimos, recuperación elástica del material, distribución de esfuerzos, radios de transición óptimos, lubricación, control de velocidad y estrategias de automatización para fabricar piezas metálicas complejas de manera totalmente controlada, repetitiva y sin defectos.
La prensa de estampado de precisión representa la máxima expresión de la ingeniería aplicada al conformado de metales, funcionando como un sistema integral en el que cada componente, desde el punzón y la matriz hasta los cojines, mordazas, sistemas de sujeción y controles automatizados, está diseñado para operar de manera totalmente sincronizada con el fin de garantizar que la chapa metálica adopte la geometría deseada con tolerancias micrométricas y acabados superficiales impecables, y su operación requiere un conocimiento exhaustivo de la mecánica de materiales, la metalurgia, la dinámica de deformación plástica, la fricción, la anisotropía del material y la interacción simultánea de fuerzas de compresión, tracción y cizallamiento que se desarrollan durante el ciclo de estampado. Durante el proceso, la chapa se coloca entre el punzón y la matriz y se somete a fuerzas controladas de forma progresiva que permiten obtener deformaciones plásticas o cortes exactos, logrando embuticiones, relieves, troquelados, dobleces y geometrías complejas con alta repetibilidad y precisión, mientras que las zonas críticas como bordes, radios de transición, cambios de espesor o esquinas internas concentran las mayores tensiones y requieren un control extremadamente preciso de la fuerza del punzón, presión de cojines, velocidad de carrera, orientación de la chapa y lubricación especializada, porque cualquier desviación puede generar arrugas, estrangulamientos, fisuras o adelgazamientos que comprometan la integridad de la pieza y la durabilidad de las herramientas. La aplicación simultánea y sincronizada de la fuerza del punzón, la presión de los cojines y la velocidad de desplazamiento asegura que el flujo del material sea uniforme hacia todas las zonas críticas, mientras que la correcta orientación de la chapa respecto a la dirección de laminación permite aprovechar la anisotropía del metal y evitar deformaciones irregulares; la lubricación no solo reduce la fricción y protege las herramientas, sino que también garantiza la repetibilidad del proceso incluso en producciones continuas de gran volumen, asegurando que piezas con embuticiones profundas, relieves complejos o geometrías intrincadas se fabriquen sin defectos.
El diseño de punzones, matrices, cojines y mordazas es determinante para la precisión, durabilidad y calidad de la prensa de estampado de precisión, y estos elementos se fabrican con aceros de alta dureza tratados térmicamente y recubiertos con materiales resistentes al desgaste y la fricción, garantizando superficies de contacto uniformes y prolongando la vida útil de la máquina, mientras que los radios de transición, ángulos de estampado, geometría de la matriz y acabado superficial se calculan considerando el comportamiento plástico del material, la distribución de esfuerzos y el flujo del metal, de manera que se minimicen arrugas, estrangulamientos y adelgazamientos no deseados. La simulación mediante elementos finitos permite anticipar zonas críticas de concentración de tensión, adelgazamiento o deformaciones irregulares antes de fabricar la herramienta, optimizando su diseño, reduciendo costos y acortando tiempos de producción, mientras que la automatización avanzada integra alimentación de bobinas, enderezado de chapa, sujeción automática, estampado, inspección visual y apilado de piezas en un flujo totalmente continuo y sincronizado, aumentando la productividad y garantizando consistencia en cada operación.
Los sistemas de monitorización digital registran en tiempo real parámetros críticos como fuerza aplicada, desplazamiento del punzón, velocidad de carrera, temperatura de las herramientas y comportamiento del material, lo que permite realizar ajustes automáticos inmediatos que aseguran tolerancias estrictas, uniformidad y calidad constante en cada pieza, a la vez que facilita el mantenimiento predictivo y la anticipación de desgaste o fallas antes de que afecten la producción, aumentando la disponibilidad de la prensa y optimizando la eficiencia de toda la línea de fabricación. En la práctica industrial, estas prensas se utilizan para fabricar paneles de carrocería, componentes automotrices de alta exigencia, chasis y carcasas de electrodomésticos, utensilios metálicos de menaje de alta gama, envases metálicos de geometría exacta y piezas críticas para la industria aeroespacial, garantizando productos finales sin defectos, con acabados superficiales uniformes, alta repetibilidad y productividad constante, consolidando a las prensas de estampado de precisión como equipos estratégicos e indispensables en cualquier línea de producción moderna que requiera exactitud, calidad y eficiencia.
Si quieres, puedo continuar con un nivel técnico extremo, describiendo paso a paso los cálculos precisos de fuerzas de estampado, presión de cojines, espesores mínimos, radios de transición óptimos, recuperación elástica del material, distribución de esfuerzos, control de velocidad, lubricación avanzada y estrategias de automatización para producir piezas metálicas extremadamente precisas de manera totalmente controlada y repetitiva, incluyendo ejemplos aplicables a automoción, electrodomésticos, menaje de cocina y envases metálicos de alta exigencia.
La prensa de estampado de precisión es un sistema industrial de altísimo nivel, concebido para producir piezas metálicas con tolerancias extremadamente estrictas y acabados superficiales de calidad óptima, donde incluso la más mínima variación puede afectar la funcionalidad, el ensamblaje o la estética del componente final, y su operación requiere un conocimiento profundo de la mecánica de materiales, la metalurgia, la dinámica de deformación plástica y la interacción simultánea de fuerzas de compresión, tracción y cizallamiento que actúan sobre la chapa durante el ciclo de estampado. En su funcionamiento, la chapa metálica se coloca entre el punzón y la matriz y se somete a fuerzas progresivas y controladas que permiten obtener deformaciones plásticas precisas o cortes exactos, logrando embuticiones, relieves, troquelados, dobleces y formas complejas con alta repetibilidad y precisión, mientras que las zonas críticas, como bordes, radios de transición, cambios de espesor o esquinas internas, concentran las tensiones más elevadas, por lo que cualquier desajuste en la fuerza del punzón, presión de cojines, velocidad de carrera, orientación de la chapa o lubricación puede generar arrugas, estrangulamientos, fisuras o adelgazamientos que comprometan la integridad de la pieza y la vida útil de las herramientas. La sincronización precisa entre la fuerza del punzón, la presión de los cojines y la velocidad de desplazamiento asegura un flujo uniforme del material hacia todas las secciones críticas, mientras que la correcta orientación de la chapa respecto a la dirección de laminación permite aprovechar la anisotropía del material, evitando deformaciones irregulares y garantizando que incluso piezas con embuticiones profundas, relieves complejos o geometrías intrincadas se fabriquen sin defectos. La lubricación especializada reduce la fricción, protege las herramientas y asegura la repetibilidad del proceso incluso en producciones continuas de alto volumen, manteniendo uniformidad en el espesor y acabado superficial de cada pieza.
El diseño de punzones, matrices, cojines y mordazas es determinante para la precisión, durabilidad y calidad de la prensa de estampado de precisión, y estos componentes se fabrican con aceros de alta dureza tratados térmicamente y recubiertos con materiales resistentes al desgaste y a la fricción, garantizando superficies de contacto uniformes y prolongando la vida útil del equipo, mientras que los radios de transición, ángulos de estampado, geometría de la matriz y acabado superficial se calculan considerando el comportamiento plástico del material, la distribución de esfuerzos y el flujo del metal, de manera que se minimicen arrugas, estrangulamientos y adelgazamientos no deseados. La simulación mediante elementos finitos permite anticipar zonas críticas de concentración de tensión, adelgazamiento o deformaciones irregulares antes de fabricar la herramienta, optimizando su diseño, reduciendo costos y acortando tiempos de producción, mientras que la automatización avanzada integra alimentación de bobinas, enderezado de chapa, sujeción automática, estampado, inspección visual y apilado de piezas en un flujo completamente continuo y sincronizado, aumentando la productividad y asegurando consistencia en cada operación.
Los sistemas de monitorización digital registran en tiempo real parámetros críticos como fuerza aplicada, desplazamiento del punzón, velocidad de carrera, temperatura de las herramientas y comportamiento del material, permitiendo ajustes automáticos inmediatos que aseguran tolerancias estrictas, uniformidad y calidad constante en cada pieza, a la vez que facilitan el mantenimiento predictivo y la anticipación de desgaste o fallas antes de que afecten la producción, aumentando la disponibilidad de la prensa y optimizando la eficiencia de toda la línea de fabricación. En la práctica industrial, estas prensas se utilizan para producir paneles de carrocería, componentes automotrices de alta exigencia, chasis y carcasas de electrodomésticos, utensilios metálicos de menaje de alta gama, envases metálicos de geometría exacta y piezas críticas para la industria aeroespacial, garantizando productos finales sin defectos, con acabados superficiales uniformes, alta repetibilidad y productividad constante, consolidando a las prensas de estampado de precisión como equipos estratégicos e indispensables en cualquier línea de producción moderna que requiera exactitud, calidad y eficiencia.
Puedo continuar con un nivel técnico extremo, explicando cómo se calculan con precisión las fuerzas de estampado, presión de cojines, espesores mínimos, recuperación elástica del material, distribución de esfuerzos, radios de transición óptimos, lubricación avanzada, control de velocidad y estrategias de automatización para fabricar piezas metálicas extremadamente precisas de manera totalmente controlada, repetitiva y sin defectos, incluyendo aplicaciones concretas en automoción, electrodomésticos, menaje de cocina y envases metálicos de alta exigencia.
Prensa de Embutido en Frío
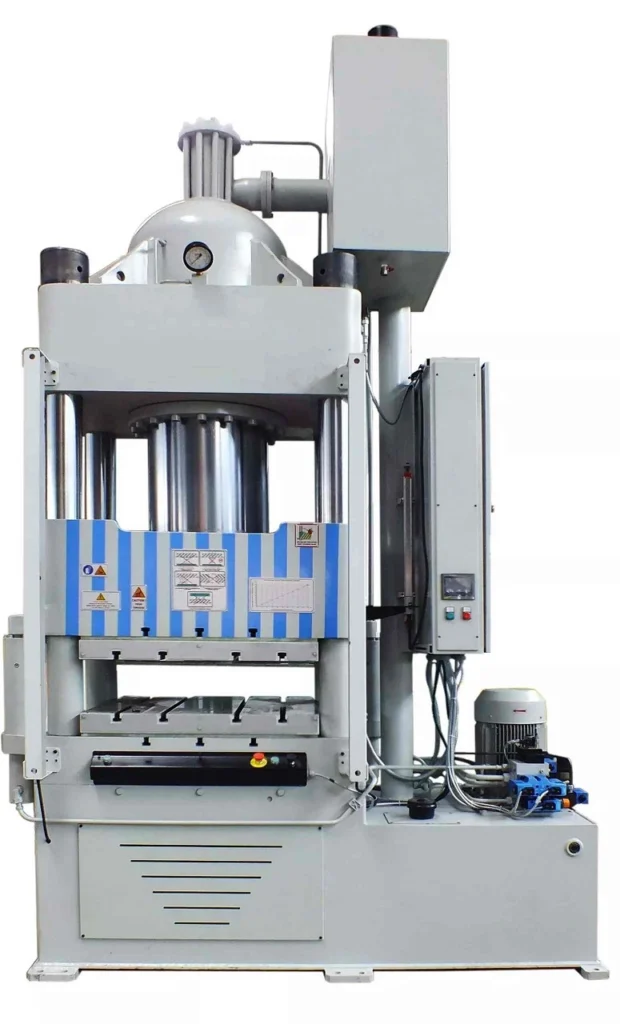
La prensa de embutido en frío es un equipo industrial especializado diseñado para conformar piezas metálicas a partir de chapas o láminas sin necesidad de aplicar calor, aprovechando únicamente la fuerza mecánica o hidráulica para provocar la deformación plástica del material, lo que permite obtener formas complejas como vasos, cubetas, tapas, carcasas y componentes estructurales con alta precisión dimensional y acabados superficiales de calidad, conservando las propiedades mecánicas y la resistencia del metal, ya que el proceso no altera su microestructura ni provoca recristalización. Este tipo de prensa se utiliza ampliamente en industrias automotriz, de electrodomésticos, menaje metálico, envases y componentes electrónicos, donde se requiere producción en serie de piezas uniformes, con geometrías precisas y tolerancias estrictas, manteniendo el espesor del material y evitando defectos como arrugas, estrangulamientos, fisuras o roturas durante el proceso de conformado.
En su funcionamiento, la chapa metálica se coloca entre el punzón y la matriz, y mediante la aplicación de fuerza progresiva y controlada se produce la deformación plástica del material, haciendo que la chapa fluya hacia la forma deseada. La sincronización entre la fuerza del punzón, la presión de los cojines y la velocidad de carrera es fundamental para garantizar que la chapa se deforme uniformemente, evitando concentraciones de tensión que puedan generar defectos. La orientación de la chapa respecto a la dirección de laminación y el control de la lubricación son igualmente cruciales, ya que la anisotropía del material influye en el flujo metálico y la fricción afecta tanto la calidad del acabado como la vida útil de las herramientas. La lubricación especializada reduce la fricción entre la chapa y las superficies de contacto, protege las herramientas y asegura la repetibilidad del proceso incluso en producciones continuas de alto volumen, permitiendo que piezas de geometría compleja se fabriquen sin fallas y con un acabado uniforme.
El diseño de punzones, matrices y cojines en una prensa de embutido en frío es crítico, fabricándose con aceros de alta dureza tratados térmicamente y recubiertos con materiales resistentes al desgaste y a la fricción, asegurando superficies de contacto homogéneas y prolongando la vida útil de la prensa. Los radios de transición, ángulos de embutido, geometría de la matriz y acabado superficial se calculan considerando la deformabilidad del material, la distribución de esfuerzos y el flujo metálico, para minimizar arrugas, estrangulamientos y adelgazamientos indeseados. La simulación mediante elementos finitos permite prever zonas de concentración de tensiones, adelgazamientos o deformaciones irregulares antes de fabricar la herramienta, optimizando su diseño, reduciendo costes y acortando tiempos de producción.
La automatización avanzada permite integrar alimentación de bobinas, enderezado de chapa, sujeción automática, embutido, inspección visual y apilado de piezas en un flujo continuo y completamente sincronizado, incrementando la productividad y garantizando consistencia en cada operación. Los sistemas de monitorización digital registran en tiempo real parámetros como fuerza aplicada, desplazamiento del punzón, velocidad de carrera y temperatura de las herramientas, lo que permite realizar ajustes automáticos inmediatos, mantener tolerancias estrictas, uniformidad y calidad constante en cada pieza, y facilita el mantenimiento predictivo al anticipar desgaste o fallas antes de que afecten la producción.
En la industria, las prensas de embutido en frío se utilizan para fabricar tapas, cubetas, paneles automotrices, carcasas de electrodomésticos, utensilios metálicos de menaje, envases metálicos y componentes estructurales de precisión, garantizando piezas complejas sin defectos, con acabados superficiales uniformes, alta repetibilidad y productividad constante, consolidando a estas prensas como equipos estratégicos e imprescindibles en líneas de producción modernas que requieren precisión, calidad y eficiencia.
Si quieres, puedo continuar con un análisis ultra técnico, detallando cómo se calculan las fuerzas exactas de embutido, la presión de los cojines, espesores mínimos, radios de transición, recuperación elástica del material, distribución de esfuerzos y optimización completa de todos los parámetros del proceso para producir piezas metálicas complejas de manera totalmente controlada y repetitiva.
La prensa de embutido en frío es un equipo industrial de alta especialización que permite conformar piezas metálicas a partir de chapas sin necesidad de aplicar calor, utilizando únicamente fuerzas mecánicas o hidráulicas para provocar la deformación plástica del material, lo que permite obtener piezas complejas como vasos, cubetas, tapas, carcasas y componentes estructurales con precisión dimensional y acabados superficiales de alta calidad, manteniendo las propiedades mecánicas originales del metal, ya que el proceso no altera su microestructura ni provoca recristalización, lo que asegura resistencia y durabilidad de la pieza final. Su uso es frecuente en industrias automotriz, de electrodomésticos, menaje metálico, envases y componentes electrónicos, donde se requiere producción en serie de piezas uniformes, con geometrías precisas y tolerancias estrictas, conservando el espesor del material y evitando defectos como arrugas, estrangulamientos, fisuras o roturas durante la deformación.
El funcionamiento de la prensa de embutido en frío implica la colocación de la chapa metálica entre el punzón y la matriz, y la aplicación de fuerzas controladas de forma progresiva que permiten que el material fluya hacia la forma deseada, logrando deformaciones plásticas uniformes y controladas. La sincronización entre la fuerza aplicada por el punzón, la presión de los cojines y la velocidad de carrera es fundamental para garantizar que la chapa se deforme de manera homogénea, evitando concentraciones de tensión que puedan generar defectos o comprometer la integridad de la pieza. La orientación de la chapa respecto a la dirección de laminación del metal es igualmente crítica, ya que la anisotropía del material influye directamente en el flujo metálico durante el embutido, y el control de la lubricación permite reducir la fricción, proteger las herramientas y garantizar la repetibilidad del proceso, incluso en producciones continuas de alto volumen, asegurando piezas complejas sin fallas y con acabados uniformes.
El diseño de punzones, matrices y cojines en una prensa de embutido en frío es determinante para la precisión, durabilidad y calidad de la operación, y estos elementos se fabrican con aceros de alta dureza tratados térmicamente y recubiertos con materiales resistentes al desgaste y a la fricción, asegurando superficies de contacto homogéneas y prolongando la vida útil de la máquina. Los radios de transición, ángulos de embutido, geometría de la matriz y acabado superficial se calculan considerando la deformabilidad del material, la distribución de esfuerzos y el flujo metálico, de manera que se minimicen arrugas, estrangulamientos, adelgazamientos o deformaciones indeseadas. La simulación mediante elementos finitos permite anticipar zonas críticas de concentración de tensiones, adelgazamiento o deformaciones irregulares antes de fabricar la herramienta, optimizando su diseño, reduciendo costes y acortando tiempos de producción, mientras que la automatización avanzada integra alimentación de bobinas, enderezado de chapa, sujeción automática, embutido, inspección visual y apilado de piezas en un flujo continuo y totalmente sincronizado, aumentando la productividad y asegurando la consistencia de cada operación.
Los sistemas de monitorización digital registran en tiempo real parámetros como fuerza aplicada, desplazamiento del punzón, velocidad de carrera, temperatura de las herramientas y comportamiento del material, permitiendo realizar ajustes automáticos inmediatos que garantizan tolerancias estrictas, uniformidad y calidad constante en cada pieza, además de facilitar el mantenimiento predictivo y la anticipación de desgaste o fallas antes de que afecten la producción, aumentando la disponibilidad de la prensa y optimizando la eficiencia de toda la línea de fabricación. En la práctica industrial, las prensas de embutido en frío se utilizan para producir tapas, cubetas, paneles automotrices, carcasas de electrodomésticos, utensilios metálicos de menaje, envases metálicos y componentes estructurales de precisión, asegurando piezas complejas sin defectos, con acabados superficiales uniformes, alta repetibilidad y productividad constante, consolidando a estas prensas como equipos estratégicos e imprescindibles en líneas de producción modernas que requieren precisión, calidad y eficiencia.
Si quieres, puedo continuar con un nivel técnico extremo, explicando cómo se calculan con exactitud las fuerzas de embutido en frío, la presión de los cojines, espesores mínimos, radios de transición, recuperación elástica del material, distribución de esfuerzos, lubricación, control de velocidad y estrategias de automatización para fabricar piezas metálicas complejas de manera totalmente controlada, repetitiva y sin defectos.
La prensa de embutido en frío constituye un sistema industrial de máxima precisión diseñado para conformar piezas metálicas mediante la aplicación exclusiva de fuerzas mecánicas o hidráulicas, evitando el uso de calor y preservando al máximo las propiedades mecánicas y estructurales del material, lo que permite obtener piezas complejas como vasos, cubetas, tapas, carcasas y componentes estructurales con tolerancias estrictas y acabados superficiales homogéneos, esenciales para industrias de alta exigencia como la automotriz, aeroespacial, de electrodomésticos, menaje metálico, envases y componentes electrónicos. El proceso comienza con la colocación de la chapa metálica entre el punzón y la matriz, donde se aplica una fuerza controlada y progresiva que induce deformación plástica uniforme, permitiendo que el material fluya hacia la geometría deseada, logrando embuticiones profundas, relieves, troquelados y dobleces con repetibilidad absoluta, mientras que las zonas críticas como bordes, esquinas internas, cambios de espesor y radios de transición concentran las tensiones más elevadas y requieren un control extremadamente preciso de la fuerza del punzón, presión de cojines, velocidad de carrera, orientación de la chapa y lubricación, porque cualquier desviación puede ocasionar arrugas, estrangulamientos, fisuras, adelgazamientos o fallas que comprometan la integridad de la pieza y la durabilidad de las herramientas. La correcta orientación de la chapa respecto a la dirección de laminación del metal es fundamental para aprovechar la anisotropía del material, optimizando el flujo y evitando deformaciones irregulares, mientras que la lubricación especializada reduce la fricción, protege las superficies de contacto y garantiza la repetibilidad del proceso en producciones continuas de alto volumen, asegurando que piezas de geometrías complejas se fabriquen sin defectos y con acabado uniforme.
El diseño de punzones, matrices y cojines es determinante para la precisión y la durabilidad de la prensa de embutido en frío, y estos componentes se elaboran con aceros de alta dureza tratados térmicamente y recubiertos con materiales de baja fricción y alta resistencia al desgaste, garantizando superficies de contacto homogéneas y prolongando la vida útil de la máquina. La geometría de la matriz, radios de transición, ángulos de embutido y acabado superficial se calculan considerando la deformabilidad del material, la distribución de esfuerzos y el flujo metálico, minimizando arrugas, estrangulamientos y adelgazamientos indeseados, mientras que la simulación mediante elementos finitos permite anticipar zonas críticas de concentración de tensiones o deformaciones antes de fabricar la herramienta, optimizando el diseño, reduciendo costes y acortando tiempos de producción. La automatización avanzada permite integrar alimentación de bobinas, enderezado de chapa, sujeción automática, embutido, inspección visual y apilado de piezas en un flujo completamente continuo y sincronizado, incrementando la productividad y asegurando la uniformidad de cada operación, mientras que los sistemas de monitorización digital registran parámetros en tiempo real como fuerza aplicada, desplazamiento del punzón, velocidad de carrera, temperatura de las herramientas y comportamiento del material, permitiendo ajustes automáticos inmediatos que garantizan tolerancias estrictas, calidad constante y uniformidad de espesor y acabado, y facilitando el mantenimiento predictivo al anticipar desgaste o fallas antes de que afecten la producción.
En la práctica industrial, las prensas de embutido en frío se utilizan para fabricar tapas, cubetas, paneles automotrices, carcasas de electrodomésticos, utensilios de menaje metálico de alta gama, envases metálicos de geometría precisa y componentes estructurales críticos, garantizando productos finales sin defectos, con acabados uniformes, alta repetibilidad y productividad constante, consolidando a estas prensas como equipos estratégicos e imprescindibles en cualquier línea de producción moderna que requiera precisión, calidad y eficiencia. Este proceso combina de manera integral mecánica, metalurgia, automatización, simulación y control digital avanzado para lograr piezas complejas de manera repetitiva, con tolerancias estrictas y con la máxima conservación de las propiedades físicas del material, asegurando que cada ciclo de producción mantenga los estándares más elevados de calidad y eficiencia industrial.
Puedo continuar describiendo un nivel técnico extremo, incluyendo todos los cálculos precisos de fuerzas de embutido, presión de cojines, espesores mínimos, radios de transición, recuperación elástica del material, distribución de esfuerzos, lubricación, control de velocidad y estrategias de automatización avanzada para producir piezas metálicas complejas en frío de manera completamente controlada, repetitiva y sin defectos.
La prensa de embutido en frío constituye un equipo industrial altamente especializado cuya función principal es transformar chapas metálicas en piezas tridimensionales complejas mediante la aplicación exclusiva de fuerzas mecánicas o hidráulicas, sin recurrir a la aplicación de calor, lo que permite preservar las propiedades mecánicas y la estructura interna del material, garantizando que la resistencia, dureza y ductilidad originales se mantengan intactas y que las piezas resultantes cumplan con estándares estrictos de precisión y calidad superficial. Este tipo de prensas se emplea en la fabricación de componentes automotrices como tapas de motor, cubetas, carcasas y paneles, así como en electrodomésticos, utensilios metálicos, envases de metal y partes críticas para la industria aeroespacial y electrónica, donde la exactitud dimensional, la repetibilidad y la integridad del material son imprescindibles. Durante el ciclo de embutido, la chapa se coloca entre el punzón y la matriz y se somete a fuerzas cuidadosamente controladas, progresivas y sincronizadas con la presión de los cojines y la velocidad de carrera, de manera que el material fluya uniformemente hacia la forma deseada, evitando concentraciones de tensión que puedan generar arrugas, estrangulamientos, fisuras, adelgazamientos o fracturas, especialmente en zonas críticas como bordes, radios de transición, cambios de espesor o esquinas internas. La orientación correcta de la chapa respecto a la dirección de laminación del metal es fundamental, ya que permite aprovechar la anisotropía del material para un flujo homogéneo y evita deformaciones irregulares; la lubricación especializada no solo reduce la fricción y protege las herramientas, sino que también asegura la repetibilidad del proceso incluso en producciones continuas de alto volumen, garantizando acabados uniformes y tolerancias estrictas en cada pieza fabricada.
El diseño de punzones, matrices y cojines en una prensa de embutido en frío es un aspecto crítico que determina la precisión, durabilidad y calidad de la producción; estos elementos se fabrican con aceros de alta dureza tratados térmicamente y recubiertos con materiales resistentes al desgaste y a la fricción, asegurando superficies de contacto homogéneas y prolongando la vida útil del equipo, mientras que la geometría de la matriz, los radios de transición, los ángulos de embutido y el acabado superficial se calculan considerando la deformabilidad del material, la distribución de esfuerzos y el flujo del metal, minimizando arrugas, estrangulamientos y adelgazamientos indeseados. La simulación mediante elementos finitos permite anticipar zonas críticas de concentración de tensiones, adelgazamiento o deformaciones irregulares antes de la fabricación de la herramienta, optimizando su diseño, reduciendo costos, acortando tiempos de producción y garantizando uniformidad en cada ciclo de embutido. La automatización avanzada permite integrar la alimentación de bobinas, enderezado de chapa, sujeción automática, embutido, inspección visual y apilado de piezas en un flujo continuo y totalmente sincronizado, aumentando la productividad y asegurando la consistencia de cada operación.
Los sistemas de monitorización digital registran en tiempo real parámetros como fuerza aplicada, desplazamiento del punzón, velocidad de carrera, temperatura de las herramientas y comportamiento del material, permitiendo ajustes automáticos inmediatos que aseguran tolerancias estrictas, uniformidad y calidad constante en cada pieza, al mismo tiempo que facilitan el mantenimiento predictivo y la anticipación de desgaste o fallas antes de que afecten la producción, aumentando la disponibilidad de la prensa y optimizando la eficiencia de toda la línea de fabricación. En la práctica industrial, las prensas de embutido en frío se utilizan para fabricar tapas, cubetas, paneles automotrices, carcasas de electrodomésticos, utensilios metálicos de menaje, envases metálicos y componentes estructurales críticos, garantizando piezas complejas sin defectos, con acabados superficiales uniformes, alta repetibilidad y productividad constante, consolidando a estas prensas como equipos estratégicos e imprescindibles en cualquier línea de producción moderna que requiera precisión, calidad y eficiencia.
Si quieres, puedo continuar con un nivel técnico extremadamente detallado, explicando paso a paso todos los cálculos de fuerza de embutido, presión de cojines, espesores mínimos, recuperación elástica del material, distribución de esfuerzos, lubricación, control de velocidad y estrategias de automatización avanzada para fabricar piezas metálicas complejas en frío de manera totalmente controlada, repetitiva y sin defectos, incluyendo ejemplos prácticos para la industria automotriz, electrodomésticos, menaje metálico y envases de alta precisión.
Prensa de Estampado de Láminas
La prensa de estampado de láminas es un equipo industrial de alta precisión diseñado para conformar, cortar, doblar o troquelar chapas metálicas delgadas mediante la aplicación de fuerzas mecánicas o hidráulicas controladas, permitiendo la obtención de piezas complejas con geometrías precisas y acabados superficiales uniformes, manteniendo la integridad del material y asegurando tolerancias estrictas requeridas por sectores industriales como la automoción, electrodomésticos, menaje metálico, envases y componentes electrónicos. Este tipo de prensa se utiliza para fabricar paneles, carcasas, tapas, cubetas, embuticiones y relieves, asegurando que cada pieza producida sea idéntica en dimensiones y calidad, lo que es fundamental para ensamblajes mecánicos y productos de alta exigencia. La operación de la prensa de estampado de láminas implica colocar la chapa entre el punzón y la matriz, donde se aplica fuerza progresiva y controlada para que el material fluya uniformemente hacia la forma deseada, logrando deformaciones plásticas precisas sin generar defectos como arrugas, estrangulamientos, fisuras o adelgazamientos, especialmente en zonas críticas como bordes, esquinas internas, cambios de espesor o radios de transición. La correcta orientación de la chapa respecto a la dirección de laminación es vital para aprovechar la anisotropía del material y garantizar un flujo homogéneo durante el estampado, mientras que la lubricación especializada reduce la fricción, protege las herramientas y asegura la repetibilidad del proceso incluso en producciones continuas de alto volumen, manteniendo uniformidad de espesor y acabado superficial en cada pieza.
El diseño de punzones, matrices y cojines es fundamental para la precisión, durabilidad y calidad de la prensa de estampado de láminas; estos componentes se fabrican con aceros de alta dureza tratados térmicamente y recubiertos con materiales resistentes al desgaste y a la fricción, asegurando superficies de contacto homogéneas y prolongando la vida útil de la prensa. Los radios de transición, ángulos de estampado, geometría de la matriz y acabado superficial se calculan considerando la deformabilidad del material, la distribución de esfuerzos y el flujo metálico, minimizando arrugas, estrangulamientos y adelgazamientos no deseados, mientras que la simulación mediante elementos finitos permite anticipar zonas críticas de concentración de tensiones o deformaciones antes de fabricar la herramienta, optimizando su diseño, reduciendo costos y acortando tiempos de producción. La automatización avanzada permite integrar alimentación de bobinas, enderezado de chapa, sujeción automática, estampado, inspección visual y apilado de piezas en un flujo totalmente continuo y sincronizado, aumentando la productividad y garantizando uniformidad y calidad en cada ciclo de estampado.
Los sistemas de monitorización digital registran en tiempo real parámetros como fuerza aplicada, desplazamiento del punzón, velocidad de carrera, temperatura de las herramientas y comportamiento del material, permitiendo ajustes automáticos inmediatos que aseguran tolerancias estrictas, uniformidad y calidad constante en cada pieza, al mismo tiempo que facilitan el mantenimiento predictivo y la detección anticipada de desgaste o fallas antes de que afecten la producción, aumentando la disponibilidad de la prensa y optimizando la eficiencia de toda la línea de fabricación. En la práctica industrial, las prensas de estampado de láminas se utilizan para producir paneles automotrices, carcasas de electrodomésticos, utensilios metálicos, envases, tapas, cubetas y componentes estructurales de precisión, garantizando piezas complejas sin defectos, con acabados superficiales uniformes, alta repetibilidad y productividad constante, consolidando a estas prensas como equipos estratégicos e imprescindibles en cualquier línea de producción moderna que requiera precisión, calidad y eficiencia.
Si quieres, puedo continuar con un nivel técnico extremadamente detallado, describiendo cómo se calculan con precisión fuerzas de estampado, presión de cojines, espesores mínimos, radios de transición, recuperación elástica del material, distribución de esfuerzos, lubricación, control de velocidad y estrategias de automatización avanzada para fabricar piezas metálicas complejas de manera totalmente controlada, repetitiva y sin defectos, incluyendo aplicaciones prácticas para la industria automotriz, electrodomésticos, menaje metálico y envases de alta precisión.
La prensa de estampado de láminas es un equipo industrial diseñado para transformar chapas metálicas delgadas en piezas tridimensionales con formas complejas mediante la aplicación de fuerzas mecánicas o hidráulicas controladas, sin alterar las propiedades mecánicas del material, lo que permite obtener productos con tolerancias estrictas, acabados superficiales uniformes y alta repetibilidad, esenciales para industrias de alta exigencia como la automotriz, aeroespacial, electrodomésticos, menaje metálico, envases y componentes electrónicos. Su funcionamiento implica colocar la chapa entre el punzón y la matriz, y aplicar fuerza progresiva para inducir la deformación plástica del material, logrando embuticiones, relieves, troquelados, dobleces y geometrías complejas con total uniformidad, mientras que las zonas críticas como bordes, radios de transición, cambios de espesor o esquinas internas concentran las tensiones más elevadas, requiriendo un control preciso de la fuerza aplicada, la presión de cojines, la velocidad de carrera, la orientación de la chapa y la lubricación, ya que cualquier desviación puede provocar arrugas, estrangulamientos, fisuras o adelgazamientos que comprometan la integridad de la pieza y la durabilidad de las herramientas. La orientación correcta de la chapa respecto a la dirección de laminación permite aprovechar la anisotropía del material y garantizar un flujo uniforme durante el estampado, mientras que la lubricación especializada reduce la fricción, protege las herramientas y asegura la repetibilidad del proceso incluso en producciones continuas de alto volumen, garantizando acabados homogéneos y tolerancias estrictas en cada pieza fabricada.
El diseño de punzones, matrices y cojines es fundamental para la precisión, durabilidad y calidad de la prensa de estampado de láminas; estos componentes se elaboran con aceros de alta dureza tratados térmicamente y recubiertos con materiales de baja fricción y alta resistencia al desgaste, garantizando superficies de contacto homogéneas y prolongando la vida útil del equipo. Los radios de transición, ángulos de estampado, geometría de la matriz y acabado superficial se calculan considerando la deformabilidad del material, la distribución de esfuerzos y el flujo metálico, minimizando arrugas, estrangulamientos y adelgazamientos no deseados, mientras que la simulación mediante elementos finitos permite anticipar zonas críticas de concentración de tensiones o deformaciones antes de fabricar la herramienta, optimizando su diseño, reduciendo costes y acortando tiempos de producción. La automatización avanzada permite integrar alimentación de bobinas, enderezado de chapa, sujeción automática, estampado, inspección visual y apilado de piezas en un flujo continuo y totalmente sincronizado, aumentando la productividad y asegurando uniformidad y calidad en cada ciclo de estampado.
Los sistemas de monitorización digital registran en tiempo real parámetros como fuerza aplicada, desplazamiento del punzón, velocidad de carrera, temperatura de las herramientas y comportamiento del material, permitiendo realizar ajustes automáticos inmediatos que aseguran tolerancias estrictas, uniformidad y calidad constante en cada pieza, mientras facilitan el mantenimiento predictivo y la detección anticipada de desgaste o fallas antes de que afecten la producción, aumentando la disponibilidad de la prensa y optimizando la eficiencia de toda la línea de fabricación. En la práctica industrial, las prensas de estampado de láminas se utilizan para producir paneles automotrices, carcasas de electrodomésticos, utensilios metálicos, envases, tapas, cubetas y componentes estructurales de precisión, garantizando piezas complejas sin defectos, con acabados superficiales uniformes, alta repetibilidad y productividad constante, consolidando a estas prensas como equipos estratégicos e imprescindibles en cualquier línea de producción moderna que requiera precisión, calidad y eficiencia.
Puedo continuar con un nivel técnico extremadamente detallado, incluyendo cálculos exactos de fuerzas de estampado, presión de cojines, espesores mínimos, recuperación elástica del material, distribución de esfuerzos, lubricación, control de velocidad y estrategias de automatización avanzada para producir piezas metálicas complejas con total control, repetibilidad y sin defectos, mostrando ejemplos prácticos aplicables a la automoción, electrodomésticos, menaje metálico y envases de alta precisión.
La prensa de estampado de láminas representa un equipo industrial de alta complejidad y precisión, diseñado para transformar chapas metálicas delgadas en piezas tridimensionales con geometrías complejas mediante la aplicación controlada de fuerzas mecánicas o hidráulicas, logrando deformaciones plásticas uniformes que permiten obtener embuticiones, relieves, cortes, dobleces y troquelados con tolerancias extremadamente estrictas y acabados superficiales homogéneos, manteniendo la integridad estructural del material y preservando sus propiedades mecánicas originales, lo que es esencial en industrias de alta exigencia como la automotriz, aeroespacial, electrodomésticos, menaje metálico, envases y componentes electrónicos. Su operación implica la colocación precisa de la chapa entre el punzón y la matriz, aplicando fuerzas progresivas y sincronizadas con la presión de los cojines y la velocidad de carrera para asegurar que el material fluya de manera uniforme hacia la forma deseada, evitando concentraciones de tensión que puedan provocar arrugas, estrangulamientos, fisuras o adelgazamientos, especialmente en zonas críticas como bordes, esquinas internas, cambios de espesor o radios de transición, donde cualquier desviación puede afectar la calidad de la pieza y la durabilidad de las herramientas. La orientación adecuada de la chapa respecto a la dirección de laminación permite optimizar el flujo del metal y aprovechar la anisotropía del material, mientras que la lubricación especializada reduce la fricción, protege las superficies de contacto y asegura la repetibilidad del proceso incluso en producciones continuas de alto volumen, garantizando que cada pieza se fabrique con acabados uniformes y tolerancias precisas, sin defectos ni variaciones entre ciclos.
El diseño de punzones, matrices y cojines es determinante para la eficiencia y calidad de la prensa de estampado de láminas; estos componentes se fabrican con aceros de alta dureza tratados térmicamente y recubiertos con materiales resistentes al desgaste y a la fricción, asegurando superficies de contacto homogéneas y prolongando la vida útil del equipo, mientras que la geometría de la matriz, los radios de transición, los ángulos de estampado y el acabado superficial se calculan considerando la deformabilidad del material, la distribución de esfuerzos y el flujo metálico, minimizando arrugas, estrangulamientos y adelgazamientos no deseados. La simulación mediante elementos finitos permite anticipar zonas críticas de concentración de tensiones, adelgazamiento o deformaciones irregulares antes de fabricar la herramienta, optimizando su diseño, reduciendo costes y acortando los tiempos de producción, mientras que la automatización avanzada integra la alimentación de bobinas, enderezado de chapa, sujeción automática, estampado, inspección visual y apilado de piezas en un flujo totalmente continuo y sincronizado, aumentando la productividad y garantizando uniformidad y calidad en cada operación.
Los sistemas de monitorización digital registran en tiempo real parámetros críticos como fuerza aplicada, desplazamiento del punzón, velocidad de carrera, temperatura de las herramientas y comportamiento del material, permitiendo ajustes automáticos inmediatos que aseguran tolerancias estrictas, uniformidad y calidad constante en cada pieza, además de facilitar el mantenimiento predictivo y la detección anticipada de desgaste o fallas antes de que afecten la producción, aumentando la disponibilidad de la prensa y optimizando la eficiencia de toda la línea de fabricación. En la práctica industrial, las prensas de estampado de láminas se utilizan para producir paneles automotrices, carcasas de electrodomésticos, utensilios metálicos, envases, tapas, cubetas y componentes estructurales de precisión, garantizando piezas complejas sin defectos, con acabados superficiales uniformes, alta repetibilidad y productividad constante, consolidando a estas prensas como equipos estratégicos e imprescindibles en cualquier línea de producción moderna que requiera precisión, calidad y eficiencia.
Si deseas, puedo continuar con un nivel técnico extremo, detallando paso a paso cómo se calculan fuerzas de estampado, presión de cojines, espesores mínimos, recuperación elástica del material, distribución de esfuerzos, lubricación avanzada, control de velocidad y estrategias de automatización avanzada para producir piezas metálicas complejas con total control, repetibilidad absoluta y sin defectos, incluyendo ejemplos prácticos aplicables a automoción, electrodomésticos, menaje metálico y envases de alta precisión.
La prensa de estampado de láminas es un equipo industrial diseñado para transformar chapas metálicas en piezas tridimensionales con geometrías complejas mediante la aplicación de fuerzas mecánicas o hidráulicas controladas, logrando deformaciones plásticas precisas que permiten la fabricación de embuticiones profundas, relieves, troquelados, dobleces y cortes con tolerancias extremadamente estrictas y acabados superficiales uniformes, preservando las propiedades mecánicas y la resistencia del material, lo que resulta esencial en sectores como la automoción, aeroespacial, electrodomésticos, menaje metálico, envases y componentes electrónicos de alta precisión. Su funcionamiento comienza con la colocación exacta de la chapa entre el punzón y la matriz, donde se aplica una fuerza progresiva y sincronizada con la presión de los cojines y la velocidad de carrera, lo que garantiza que el metal fluya de manera uniforme hacia la forma deseada, evitando concentraciones de esfuerzo que puedan provocar defectos como arrugas, estrangulamientos, fisuras o adelgazamientos, especialmente en zonas críticas como bordes, esquinas internas, cambios de espesor o radios de transición, donde cualquier desviación puede comprometer la calidad final de la pieza y la durabilidad de las herramientas. La orientación correcta de la chapa respecto a la dirección de laminación es vital para aprovechar la anisotropía del material y asegurar un flujo homogéneo durante el estampado, mientras que la lubricación especializada reduce la fricción, protege las superficies de contacto y garantiza la repetibilidad del proceso incluso en producciones continuas de alto volumen, manteniendo uniformidad de espesor y acabado superficial en todas las piezas.
El diseño de punzones, matrices y cojines es crítico para la precisión, durabilidad y rendimiento de la prensa de estampado de láminas; estos componentes se fabrican con aceros de alta dureza tratados térmicamente y recubiertos con materiales de alta resistencia al desgaste y baja fricción, asegurando superficies de contacto homogéneas y prolongando la vida útil del equipo, mientras que la geometría de la matriz, los radios de transición, los ángulos de estampado y el acabado superficial se calculan considerando la deformabilidad del material, la distribución de esfuerzos y el flujo del metal, minimizando arrugas, estrangulamientos y adelgazamientos indeseados. La simulación mediante elementos finitos permite anticipar zonas críticas de concentración de tensiones o deformaciones antes de la fabricación de la herramienta, optimizando su diseño, reduciendo costes y acortando los tiempos de producción, mientras que la automatización avanzada integra alimentación de bobinas, enderezado de chapa, sujeción automática, estampado, inspección visual y apilado de piezas en un flujo completamente continuo y sincronizado, aumentando la productividad y garantizando uniformidad y calidad en cada ciclo de estampado.
Los sistemas de monitorización digital registran parámetros en tiempo real como fuerza aplicada, desplazamiento del punzón, velocidad de carrera, temperatura de las herramientas y comportamiento del material, permitiendo realizar ajustes automáticos inmediatos que aseguran tolerancias estrictas, uniformidad y calidad constante en cada pieza, al tiempo que facilitan el mantenimiento predictivo y la detección anticipada de desgaste o fallas antes de que afecten la producción, aumentando la disponibilidad de la prensa y optimizando la eficiencia de toda la línea de fabricación. En la práctica industrial, las prensas de estampado de láminas se utilizan para producir paneles automotrices, carcasas de electrodomésticos, utensilios metálicos, envases, tapas, cubetas y componentes estructurales de precisión, asegurando piezas complejas sin defectos, con acabados uniformes, alta repetibilidad y productividad constante, consolidando a estas prensas como equipos estratégicos e imprescindibles en cualquier línea de producción moderna que requiera precisión, calidad y eficiencia.
Si quieres, puedo continuar con un análisis técnico extremadamente detallado, explicando cómo se calculan las fuerzas exactas de estampado, presión de cojines, espesores mínimos, radios de transición, recuperación elástica del material, distribución de esfuerzos, lubricación avanzada, control de velocidad y estrategias de automatización para producir piezas metálicas complejas en lámina de manera totalmente controlada, repetitiva y sin defectos, con ejemplos prácticos aplicables a automoción, electrodomésticos, menaje metálico y envases de alta precisión.
Prensa Automática de Embutición
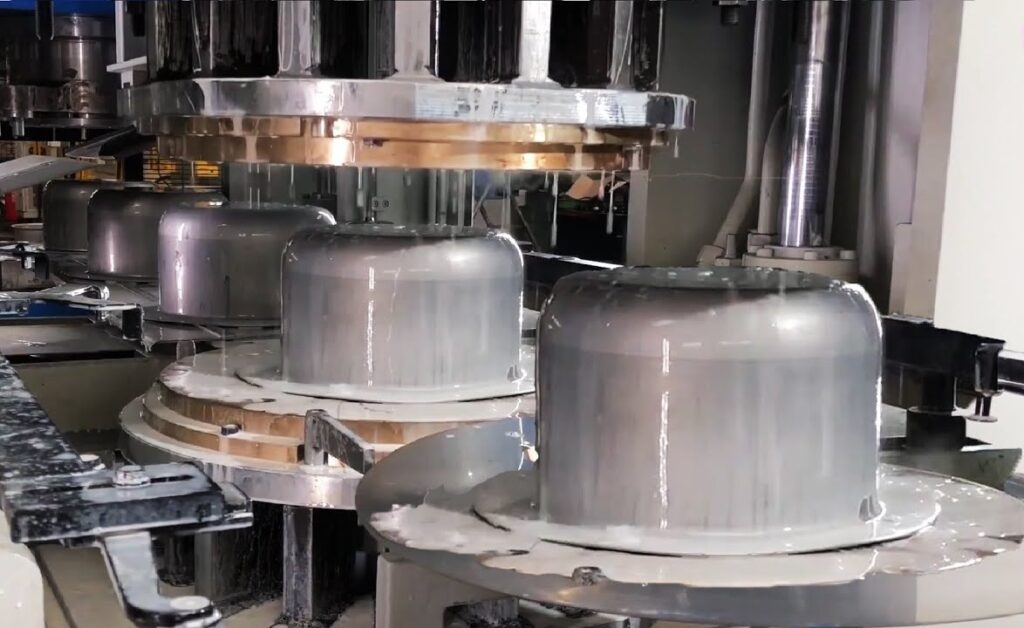
La prensa automática de embutición es un equipo industrial altamente especializado diseñado para conformar piezas metálicas a partir de chapas o láminas mediante la aplicación de fuerzas mecánicas o hidráulicas controladas, sin necesidad de calor, logrando deformaciones plásticas precisas que permiten producir embuticiones profundas, relieves, carcasas, cubetas, tapas y componentes estructurales complejos con tolerancias estrictas y acabados superficiales homogéneos, lo que resulta fundamental en industrias de alta exigencia como la automotriz, aeroespacial, electrodomésticos, menaje metálico, envases y componentes electrónicos. A diferencia de las prensas de embutición convencionales, este tipo de prensa integra sistemas automáticos de alimentación de chapa, posicionamiento, sujeción, embutición y expulsión de piezas, permitiendo un flujo continuo de producción con mínima intervención humana, lo que incrementa significativamente la productividad, reduce errores y garantiza la repetibilidad absoluta en cada ciclo de trabajo.
El funcionamiento de la prensa automática de embutición comienza con la alimentación de la chapa metálica desde bobinas o planchas, la cual es enderezada y alineada mediante sistemas automáticos antes de colocarse entre el punzón y la matriz. La fuerza de embutición se aplica de manera controlada, sincronizada con la presión de cojines y la velocidad de carrera, para asegurar que el material fluya uniformemente hacia la forma deseada, evitando concentraciones de tensiones que puedan provocar defectos como arrugas, estrangulamientos, fisuras o adelgazamientos, especialmente en zonas críticas como bordes, esquinas internas, cambios de espesor o radios de transición. La correcta orientación de la chapa respecto a la dirección de laminación y el control preciso de la lubricación permiten optimizar el flujo metálico, reducir la fricción, proteger las herramientas y garantizar la calidad superficial y dimensional de las piezas incluso en producciones de alto volumen.
El diseño de punzones, matrices y cojines es crítico en la prensa automática de embutición; estos componentes se fabrican con aceros de alta dureza tratados térmicamente y recubiertos con materiales de baja fricción y alta resistencia al desgaste, asegurando superficies de contacto homogéneas y prolongando la vida útil del equipo. La geometría de la matriz, los radios de transición, los ángulos de embutición y el acabado superficial se calculan considerando la deformabilidad del material, la distribución de esfuerzos y el flujo metálico, minimizando arrugas, estrangulamientos y adelgazamientos no deseados. La simulación mediante elementos finitos permite prever zonas críticas de concentración de tensiones o deformaciones antes de fabricar la herramienta, optimizando su diseño, reduciendo costes y acortando los tiempos de producción. La automatización avanzada integra alimentación de bobinas, enderezado de chapa, sujeción automática, embutición, inspección visual y apilado de piezas en un flujo totalmente continuo y sincronizado, asegurando consistencia, uniformidad y productividad máxima en cada ciclo de embutición.
Los sistemas de monitorización digital registran parámetros en tiempo real como fuerza aplicada, desplazamiento del punzón, velocidad de carrera, temperatura de las herramientas y comportamiento del material, permitiendo ajustes automáticos inmediatos que aseguran tolerancias estrictas, uniformidad y calidad constante en cada pieza, al tiempo que facilitan el mantenimiento predictivo y la detección anticipada de desgaste o fallas antes de que afecten la producción, aumentando la disponibilidad de la prensa y optimizando la eficiencia de toda la línea de fabricación. En la práctica industrial, las prensas automáticas de embutición se utilizan para producir tapas, cubetas, paneles automotrices, carcasas de electrodomésticos, utensilios metálicos de menaje, envases metálicos y componentes estructurales de precisión, garantizando piezas complejas sin defectos, con acabados superficiales uniformes, alta repetibilidad y productividad constante, consolidando a estas prensas como equipos estratégicos e imprescindibles en cualquier línea de producción moderna que requiera precisión, calidad y eficiencia.
Si deseas, puedo continuar con un análisis técnico extremadamente detallado, describiendo paso a paso cómo se calculan las fuerzas de embutición, la presión de los cojines, los espesores mínimos, los radios de transición, la recuperación elástica del material, la distribución de esfuerzos, la lubricación avanzada, el control de velocidad y las estrategias de automatización para producir piezas metálicas complejas en frío de manera completamente controlada, repetitiva y sin defectos, incluyendo ejemplos prácticos aplicables a la automoción, electrodomésticos, menaje metálico y envases de alta precisión.
La prensa automática de embutición es un equipo industrial de máxima precisión diseñado para conformar chapas metálicas en piezas tridimensionales complejas mediante la aplicación de fuerzas mecánicas o hidráulicas controladas, sin necesidad de aplicar calor, preservando completamente las propiedades mecánicas y estructurales del material, lo que permite fabricar embuticiones profundas, relieves, carcasas, tapas, cubetas y componentes estructurales con tolerancias estrictas y acabados superficiales homogéneos, esenciales en industrias como la automotriz, aeroespacial, electrodomésticos, menaje metálico, envases y componentes electrónicos de alta precisión. A diferencia de las prensas de embutición convencionales, la versión automática integra sistemas de alimentación de chapa desde bobinas o planchas, enderezado, posicionamiento, sujeción, embutición y expulsión de piezas de manera completamente sincronizada, lo que permite un flujo de producción continuo, reduce la intervención humana, aumenta la productividad, minimiza errores y garantiza la repetibilidad absoluta en cada ciclo de trabajo.
El funcionamiento de la prensa automática de embutición implica que la chapa, previamente alineada y enderezada automáticamente, se coloca entre el punzón y la matriz, donde se aplica una fuerza progresiva cuidadosamente controlada, sincronizada con la presión de los cojines y la velocidad de carrera, para que el material fluya uniformemente hacia la forma deseada, evitando concentraciones de tensión que puedan causar defectos como arrugas, estrangulamientos, fisuras o adelgazamientos, especialmente en zonas críticas como bordes, esquinas internas, cambios de espesor o radios de transición. La correcta orientación de la chapa respecto a la dirección de laminación permite optimizar el flujo metálico, aprovechar la anisotropía del material y garantizar un estampado homogéneo, mientras que la lubricación especializada reduce la fricción, protege las superficies de contacto, prolonga la vida útil de las herramientas y asegura la uniformidad de acabado superficial incluso en producciones continuas de alto volumen, manteniendo consistencia en todas las piezas fabricadas.
El diseño de punzones, matrices y cojines es determinante para la eficiencia y precisión de la prensa automática de embutición; estos elementos se fabrican con aceros de alta dureza tratados térmicamente y recubiertos con materiales de baja fricción y alta resistencia al desgaste, garantizando superficies de contacto homogéneas y prolongando la vida útil del equipo. La geometría de la matriz, los radios de transición, los ángulos de embutición y el acabado superficial se calculan considerando la deformabilidad del material, la distribución de esfuerzos y el flujo del metal, minimizando arrugas, estrangulamientos y adelgazamientos indeseados. La simulación mediante elementos finitos permite anticipar zonas críticas de concentración de tensiones o deformaciones antes de fabricar la herramienta, optimizando su diseño, reduciendo costes y acortando tiempos de producción. La automatización avanzada permite integrar todos los procesos, desde la alimentación de bobinas y enderezado de chapa, hasta la sujeción automática, embutición, inspección visual y apilado de piezas, en un flujo continuo y completamente sincronizado, aumentando la productividad y garantizando uniformidad y calidad en cada ciclo de trabajo.
Los sistemas de monitorización digital registran en tiempo real parámetros críticos como fuerza aplicada, desplazamiento del punzón, velocidad de carrera, temperatura de las herramientas y comportamiento del material, permitiendo ajustes automáticos inmediatos que aseguran tolerancias estrictas, uniformidad y calidad constante en cada pieza, además de facilitar el mantenimiento predictivo y la detección anticipada de desgaste o fallas antes de que afecten la producción, incrementando la disponibilidad de la prensa y optimizando la eficiencia de toda la línea de fabricación. En la práctica industrial, las prensas automáticas de embutición se utilizan para fabricar tapas, cubetas, paneles automotrices, carcasas de electrodomésticos, utensilios de menaje metálico, envases metálicos y componentes estructurales de precisión, asegurando piezas complejas sin defectos, con acabados homogéneos, alta repetibilidad y productividad constante, consolidando a estas prensas como equipos estratégicos e imprescindibles en cualquier línea de producción moderna que requiera precisión, calidad y eficiencia.
Puedo continuar con un análisis técnico extremadamente detallado, explicando los cálculos exactos de fuerza de embutición, presión de cojines, espesores mínimos, radios de transición, recuperación elástica del material, distribución de esfuerzos, lubricación avanzada, control de velocidad y estrategias de automatización para fabricar piezas metálicas complejas en frío con control absoluto, repetibilidad total y sin defectos, incluyendo ejemplos prácticos aplicables a automoción, electrodomésticos, menaje metálico y envases de alta precisión.
La prensa automática de embutición constituye un equipo industrial de máxima precisión y sofisticación, diseñado para transformar chapas metálicas en piezas tridimensionales complejas mediante la aplicación controlada de fuerzas mecánicas o hidráulicas, sin recurrir al calor, garantizando la preservación de las propiedades mecánicas y estructurales del material, lo que permite obtener embuticiones profundas, relieves, carcasas, tapas, cubetas y componentes estructurales con tolerancias extremadamente estrictas y acabados superficiales homogéneos, esenciales en sectores como la automoción, aeroespacial, electrodomésticos, menaje metálico, envases y componentes electrónicos de alta precisión. A diferencia de las prensas convencionales, la prensa automática integra sistemas de alimentación de chapa desde bobinas o planchas, enderezado, posicionamiento, sujeción, embutición y expulsión de piezas en un flujo completamente sincronizado, permitiendo un proceso continuo de producción que minimiza la intervención humana, incrementa la productividad, reduce errores y garantiza la repetibilidad absoluta en cada ciclo.
El funcionamiento de la prensa automática de embutición comienza con la alimentación de la chapa, que es enderezada y alineada automáticamente para luego colocarse entre el punzón y la matriz, donde se aplica una fuerza progresiva y controlada, sincronizada con la presión de los cojines y la velocidad de carrera, de manera que el material fluya uniformemente hacia la forma deseada, evitando concentraciones de esfuerzo que puedan causar defectos como arrugas, estrangulamientos, fisuras o adelgazamientos, especialmente en zonas críticas como bordes, esquinas internas, cambios de espesor o radios de transición, donde cualquier desviación podría comprometer la calidad de la pieza y la durabilidad de las herramientas. La correcta orientación de la chapa respecto a la dirección de laminación optimiza el flujo metálico y permite aprovechar la anisotropía del material, mientras que la lubricación especializada reduce la fricción, protege las herramientas y asegura uniformidad de acabado superficial incluso en producciones de alto volumen, garantizando piezas consistentes y sin defectos en cada ciclo de trabajo.
El diseño de punzones, matrices y cojines es determinante para la eficiencia y precisión de la prensa automática de embutición; estos elementos se fabrican con aceros de alta dureza tratados térmicamente y recubiertos con materiales de alta resistencia al desgaste y baja fricción, asegurando superficies de contacto homogéneas y prolongando la vida útil del equipo. La geometría de la matriz, los radios de transición, los ángulos de embutición y el acabado superficial se calculan considerando la deformabilidad del material, la distribución de esfuerzos y el flujo del metal, minimizando arrugas, estrangulamientos y adelgazamientos no deseados, mientras que la simulación mediante elementos finitos permite prever zonas críticas de concentración de tensiones o deformaciones antes de fabricar la herramienta, optimizando su diseño, reduciendo costos y acortando tiempos de producción. La automatización avanzada integra todos los procesos, desde la alimentación de bobinas y el enderezado de chapa, hasta la sujeción automática, embutición, inspección visual y apilado de piezas, en un flujo continuo y completamente sincronizado, aumentando la productividad y asegurando uniformidad y calidad en cada ciclo de trabajo.
Los sistemas de monitorización digital registran en tiempo real parámetros críticos como fuerza aplicada, desplazamiento del punzón, velocidad de carrera, temperatura de las herramientas y comportamiento del material, permitiendo ajustes automáticos inmediatos que garantizan tolerancias estrictas, uniformidad y calidad constante en cada pieza, además de facilitar el mantenimiento predictivo y la detección anticipada de desgaste o fallas antes de que afecten la producción, incrementando la disponibilidad de la prensa y optimizando la eficiencia de toda la línea de fabricación. En la práctica industrial, las prensas automáticas de embutición se utilizan para fabricar tapas, cubetas, paneles automotrices, carcasas de electrodomésticos, utensilios metálicos de menaje, envases metálicos y componentes estructurales de precisión, asegurando piezas complejas sin defectos, con acabados homogéneos, alta repetibilidad y productividad constante, consolidando a estas prensas como equipos estratégicos e imprescindibles en cualquier línea de producción moderna que requiera precisión, calidad y eficiencia.
Puedo continuar con un nivel técnico extremadamente detallado, incluyendo cálculos exactos de fuerza de embutición, presión de cojines, espesores mínimos, radios de transición, recuperación elástica del material, distribución de esfuerzos, lubricación avanzada, control de velocidad y estrategias de automatización para producir piezas metálicas complejas en frío de manera totalmente controlada, repetitiva y sin defectos, mostrando ejemplos prácticos aplicables a automoción, electrodomésticos, menaje metálico y envases de alta precisión.
La prensa automática de embutición es un equipo industrial de alta sofisticación diseñado para transformar chapas metálicas en piezas tridimensionales complejas mediante la aplicación de fuerzas mecánicas o hidráulicas controladas, sin necesidad de calor, preservando completamente las propiedades mecánicas, la resistencia y la ductilidad del material, lo que permite fabricar embuticiones profundas, relieves, carcasas, tapas, cubetas y componentes estructurales con tolerancias extremadamente estrictas y acabados superficiales homogéneos, fundamentales en industrias de alta exigencia como la automotriz, aeroespacial, electrodomésticos, menaje metálico, envases y componentes electrónicos de alta precisión. A diferencia de las prensas convencionales, las prensas automáticas integran sistemas completos de alimentación de chapa desde bobinas o planchas, enderezado, posicionamiento, sujeción, embutición y expulsión de piezas, permitiendo un flujo de producción continuo, minimizando la intervención humana, incrementando la productividad, reduciendo errores y garantizando la repetibilidad absoluta en cada ciclo.
El funcionamiento de la prensa automática de embutición implica que la chapa, previamente enderezada y alineada automáticamente, se coloque entre el punzón y la matriz, donde se aplica una fuerza progresiva y cuidadosamente controlada, sincronizada con la presión de los cojines y la velocidad de carrera, para que el material fluya uniformemente hacia la forma deseada, evitando concentraciones de tensión que puedan generar defectos como arrugas, estrangulamientos, fisuras o adelgazamientos, especialmente en zonas críticas como bordes, esquinas internas, cambios de espesor o radios de transición, donde cualquier desviación podría comprometer la calidad de la pieza y la durabilidad de las herramientas. La correcta orientación de la chapa respecto a la dirección de laminación optimiza el flujo metálico, permite aprovechar la anisotropía del material y garantiza un estampado homogéneo, mientras que la lubricación especializada reduce la fricción, protege las herramientas, prolonga su vida útil y asegura uniformidad de acabado incluso en producciones de alto volumen, manteniendo consistencia dimensional y superficial en todas las piezas fabricadas.
El diseño de punzones, matrices y cojines es determinante para la eficiencia, precisión y durabilidad de la prensa automática de embutición; estos elementos se fabrican con aceros de alta dureza tratados térmicamente y recubiertos con materiales de alta resistencia al desgaste y baja fricción, asegurando superficies de contacto homogéneas y prolongando la vida útil del equipo. La geometría de la matriz, los radios de transición, los ángulos de embutición y el acabado superficial se calculan considerando la deformabilidad del material, la distribución de esfuerzos y el flujo del metal, minimizando arrugas, estrangulamientos y adelgazamientos no deseados, mientras que la simulación mediante elementos finitos permite anticipar zonas críticas de concentración de tensiones, adelgazamiento o deformaciones irregulares antes de fabricar la herramienta, optimizando su diseño, reduciendo costos y acortando los tiempos de producción. La automatización avanzada integra todos los procesos, desde la alimentación de bobinas y enderezado de chapa hasta sujeción automática, embutición, inspección visual y apilado de piezas, en un flujo continuo y completamente sincronizado, aumentando la productividad y asegurando uniformidad y calidad en cada ciclo de trabajo.
Los sistemas de monitorización digital registran en tiempo real parámetros críticos como fuerza aplicada, desplazamiento del punzón, velocidad de carrera, temperatura de las herramientas y comportamiento del material, permitiendo ajustes automáticos inmediatos que aseguran tolerancias estrictas, uniformidad y calidad constante en cada pieza, al mismo tiempo que facilitan el mantenimiento predictivo y la detección anticipada de desgaste o fallas antes de que afecten la producción, incrementando la disponibilidad de la prensa y optimizando la eficiencia de toda la línea de fabricación. En la práctica industrial, las prensas automáticas de embutición se utilizan para producir tapas, cubetas, paneles automotrices, carcasas de electrodomésticos, utensilios metálicos de menaje, envases metálicos y componentes estructurales de precisión, garantizando piezas complejas sin defectos, con acabados homogéneos, alta repetibilidad y productividad constante, consolidando a estas prensas como equipos estratégicos e imprescindibles en cualquier línea de producción moderna que requiera precisión, calidad y eficiencia.
Puedo continuar con un análisis técnico extremadamente detallado, describiendo cómo se calculan las fuerzas de embutición, presión de cojines, espesores mínimos, radios de transición, recuperación elástica del material, distribución de esfuerzos, lubricación avanzada, control de velocidad y estrategias de automatización para fabricar piezas metálicas complejas en frío de manera totalmente controlada, repetitiva y sin defectos, incluyendo ejemplos prácticos aplicables a la automoción, electrodomésticos, menaje metálico y envases de alta precisión.
Prensa de Embutición de Metales
La prensa de embutición de metales es un equipo industrial de alta precisión diseñado para transformar chapas metálicas planas en piezas tridimensionales mediante la aplicación de fuerzas mecánicas o hidráulicas controladas, sin necesidad de aplicar calor, lo que permite mantener la resistencia, ductilidad y otras propiedades mecánicas del material, asegurando que las piezas resultantes cumplan con tolerancias estrictas y presenten acabados superficiales uniformes. Este tipo de prensa se utiliza ampliamente en industrias como la automotriz, aeroespacial, electrodomésticos, menaje metálico, envases y componentes electrónicos, donde la precisión, la calidad superficial y la repetibilidad del proceso son fundamentales. La prensa de embutición de metales permite la fabricación de embuticiones profundas, relieves, carcasas, tapas, cubetas y componentes estructurales complejos, adaptándose a piezas de formas irregulares y geometrías sofisticadas que serían imposibles de obtener mediante procesos de corte y doblado convencionales.
El funcionamiento de la prensa de embutición de metales se basa en colocar la chapa entre un punzón y una matriz, aplicando una fuerza progresiva y controlada que provoca la deformación plástica del material, de manera que fluya uniformemente hacia la forma deseada. Es fundamental controlar parámetros como la fuerza de embutición, la presión de los cojines, la velocidad de carrera y la orientación de la chapa respecto a la dirección de laminación, ya que cualquier desviación puede generar defectos como arrugas, estrangulamientos, fisuras o adelgazamientos, especialmente en zonas críticas como bordes, esquinas internas o cambios de espesor. La lubricación especializada reduce la fricción, protege las herramientas y asegura la uniformidad de las piezas, permitiendo producciones continuas de alto volumen sin comprometer la calidad superficial ni la precisión dimensional.
El diseño de los componentes de la prensa, como punzones, matrices y cojines, es determinante para la eficiencia, precisión y durabilidad del equipo. Estos elementos se fabrican con aceros de alta dureza tratados térmicamente y recubiertos con materiales resistentes al desgaste y a la fricción, garantizando superficies de contacto homogéneas y prolongando la vida útil del equipo. La geometría de la matriz, los radios de transición, los ángulos de embutición y el acabado superficial se calculan considerando la deformabilidad del material, la distribución de esfuerzos y el flujo del metal, minimizando arrugas, estrangulamientos y adelgazamientos indeseados. La simulación mediante elementos finitos permite anticipar zonas críticas de concentración de tensiones o deformaciones antes de fabricar la herramienta, optimizando su diseño, reduciendo costos y acortando tiempos de producción.
En la práctica industrial, la prensa de embutición de metales se utiliza para fabricar tapas, cubetas, paneles automotrices, carcasas de electrodomésticos, utensilios metálicos, envases metálicos y componentes estructurales de precisión, garantizando piezas complejas sin defectos, con acabados homogéneos, alta repetibilidad y productividad constante. La incorporación de sistemas automáticos de alimentación, sujeción y expulsión de piezas permite un flujo de producción continuo y sincronizado, reduciendo la intervención humana y aumentando la eficiencia general de la línea de fabricación. Los sistemas de monitorización digital registran en tiempo real parámetros como fuerza aplicada, desplazamiento del punzón, velocidad de carrera, temperatura de las herramientas y comportamiento del material, permitiendo ajustes automáticos inmediatos que aseguran tolerancias estrictas, uniformidad y calidad constante en cada pieza, al tiempo que facilitan el mantenimiento predictivo y la detección anticipada de desgaste o fallas antes de que afecten la producción.
Si deseas, puedo continuar con un análisis técnico extremadamente detallado, explicando paso a paso cómo se calculan las fuerzas de embutición, la presión de cojines, los espesores mínimos, la recuperación elástica del material, la distribución de esfuerzos, la lubricación avanzada, el control de velocidad y las estrategias de automatización para producir piezas metálicas complejas de manera totalmente controlada, repetitiva y sin defectos, con ejemplos prácticos aplicables a la automoción, electrodomésticos, menaje metálico y envases de alta precisión.
La prensa de embutición de metales se distingue de otros equipos de conformado porque está pensada para trabajar con chapas metálicas de distinto espesor, desde láminas muy delgadas utilizadas en envases y piezas de menaje hasta chapas de mayor espesor empleadas en el sector automotriz y en aplicaciones estructurales. El proceso de embutición profunda que permite este tipo de prensas hace posible transformar una lámina plana en una geometría tridimensional compleja sin cortes ni uniones adicionales, lo que garantiza piezas de una sola pieza con gran resistencia estructural, ausencia de fugas en el caso de envases y un acabado superficial uniforme que reduce o incluso elimina procesos posteriores de mecanizado o pulido. Al no depender de procesos de soldadura para unir distintas partes, la embutición asegura que la integridad mecánica de la pieza final sea mayor, además de ofrecer mayor productividad en grandes series de producción.
El principio fundamental de funcionamiento es relativamente sencillo en concepto, pero muy complejo en ejecución técnica. La chapa metálica se coloca sobre la matriz y el punzón desciende aplicando una fuerza que provoca el flujo del material hacia dentro de la cavidad, deformando la chapa plásticamente sin llegar a romperla. En ese punto entran en juego múltiples variables que deben estar cuidadosamente controladas: la fuerza del cojín que sujeta la chapa para evitar arrugas, la velocidad de carrera del punzón que influye en la distribución de esfuerzos, la lubricación que reduce la fricción y asegura el deslizamiento uniforme del material, así como la geometría de las herramientas, que debe estar optimizada para favorecer un flujo continuo del metal. Cada una de estas variables influye directamente en la calidad final de la pieza y en la eficiencia de la producción, y un desequilibrio en cualquiera de ellas puede provocar defectos como fisuras, estrangulamientos, adelgazamientos excesivos o deformaciones no deseadas.
El diseño de la prensa de embutición de metales está íntimamente ligado a las exigencias de la industria que la emplea. En sectores como la automoción se demandan piezas de gran tamaño y geometrías muy complejas, lo que implica prensas de gran tonelaje, sistemas de cojines hidráulicos de alta precisión y troqueles diseñados con radios de transición cuidadosamente calculados para evitar fallas en el estampado. En el caso de la industria de envases, donde se trabaja con materiales como aluminio o acero estañado, la prioridad está en la producción masiva de recipientes ligeros y resistentes, por lo que las prensas deben operar a gran velocidad y con sistemas de alimentación automática que garanticen continuidad en la línea. En cambio, en la industria de electrodomésticos y menaje metálico, la calidad superficial es un factor determinante, pues el acabado de la pieza suele ser visible para el usuario final, lo que exige lubricación controlada, matrices de pulido especial y procesos que minimicen marcas o rayaduras.
Las prensas modernas de embutición de metales incorporan sistemas de control electrónico y monitorización en tiempo real que permiten ajustar parámetros durante la operación, asegurando repetibilidad y reduciendo tiempos de parada. Estos sistemas pueden detectar desviaciones mínimas en la fuerza de embutición, en la presión de los cojines o en la velocidad del punzón, y realizar correcciones automáticas para evitar la generación de piezas defectuosas. Además, gracias al uso de sensores y algoritmos de mantenimiento predictivo, es posible anticipar el desgaste de los troqueles o cojines antes de que afecten a la producción, aumentando la vida útil de la maquinaria y reduciendo costes asociados a paradas no planificadas.
En términos de materiales, la prensa de embutición de metales trabaja con una gran variedad de aleaciones: aceros al carbono, aceros inoxidables, aluminio, cobre, latón e incluso aleaciones más avanzadas utilizadas en el sector aeroespacial. Cada material requiere un enfoque distinto debido a su ductilidad, límite elástico, espesor y comportamiento frente a la deformación plástica. El acero inoxidable, por ejemplo, presenta tendencia a endurecerse por deformación, lo que exige mayores fuerzas de embutición y una lubricación más eficiente. El aluminio, en cambio, aunque más blando, es muy sensible a arrugas y fisuras si no se controlan las presiones de sujeción de forma precisa. Todo esto obliga a que los fabricantes de prensas adapten sus diseños y tecnologías a las características específicas del material que se va a trabajar, asegurando que el proceso sea estable, eficiente y económicamente viable.
De esta manera, la prensa de embutición de metales no solo es un equipo para dar forma, sino un verdadero sistema de ingeniería de precisión que conjuga fuerza, control y tecnología de materiales para garantizar la producción de piezas complejas a gran escala con una calidad uniforme. Con la integración de simulación digital, sistemas automatizados de alimentación y expulsión, así como controles electrónicos avanzados, estas prensas representan hoy un pilar central en la producción industrial moderna, permitiendo a las empresas fabricar piezas con alta complejidad geométrica, reduciendo costos y tiempos, y respondiendo a las demandas cada vez más exigentes de sectores como la automoción, el menaje, la electrónica y la industria del envase metálico.
La prensa de embutición de metales, en su concepción más avanzada, es una síntesis de ingeniería mecánica, ciencia de materiales y control automatizado, ya que no se limita a la simple acción de transformar una lámina en una pieza con volumen, sino que abarca un conjunto complejo de fenómenos de deformación plástica que deben ser entendidos y controlados de forma precisa. Cuando se produce el contacto entre el punzón y la chapa, el metal empieza a fluir hacia la cavidad del troquel en un movimiento radial y axial que pone en juego tensiones de tracción y compresión distribuidas de manera heterogénea en toda la pieza. El éxito de la operación radica en lograr que ese flujo sea uniforme, sin que se produzcan arrugas en la zona de brida, sin que el material se fracture en las paredes y sin que se generen adelgazamientos que comprometan la resistencia final. Para lograrlo, los ingenieros calculan con antelación las fuerzas necesarias de embutición, que dependen del espesor inicial de la chapa, del diámetro de la pieza a obtener, de las propiedades mecánicas del material y de la geometría del punzón y la matriz. Estos cálculos no son aproximaciones simples, sino que se apoyan en modelos matemáticos, en simulaciones por elementos finitos y en pruebas experimentales que permiten ajustar las condiciones exactas antes de pasar a la producción en serie.
En la práctica, la fuerza de embutición suele expresarse en función del esfuerzo cortante del material multiplicado por el perímetro del contorno en contacto y por el espesor de la chapa, pero este valor inicial debe corregirse con factores de seguridad que consideran la fricción, la rigidez de la prensa, la presencia de radios en la matriz y el coeficiente de fricción entre la chapa y las herramientas. Una prensa diseñada para trabajar con chapas de acero inoxidable, por ejemplo, requiere potencias considerablemente mayores que una destinada al aluminio, debido a la resistencia mecánica superior del primero y a su tendencia al endurecimiento por deformación. El diseño del cojín neumático o hidráulico que sujeta la chapa es igualmente crítico, ya que su fuerza debe ser suficiente para impedir el deslizamiento incontrolado del material pero no tan alta como para impedir que fluya hacia el interior del troquel, pues esto generaría fracturas prematuras. Ese equilibrio dinámico se logra mediante controles hidráulicos de precisión, capaces de regular la presión en milisegundos, lo que garantiza la estabilidad del proceso incluso en operaciones de embutición profunda.
Otro aspecto clave es el diseño de los troqueles, que no son simples moldes metálicos, sino herramientas de alta ingeniería en las que los radios de entrada, las holguras entre punzón y matriz, las superficies de contacto y los tratamientos térmicos del acero con el que están fabricados desempeñan un papel determinante. Un radio demasiado pequeño en la matriz puede concentrar tensiones y provocar fisuras en la chapa, mientras que un radio demasiado grande puede favorecer la aparición de arrugas. Las holguras, que suelen estar en el rango de 7 a 15% del espesor de la chapa, se definen en función del material trabajado y determinan en gran medida la calidad del embutido. Además, los troqueles modernos incluyen recubrimientos especiales como nitruración o deposiciones PVD que mejoran la resistencia al desgaste y reducen la fricción, prolongando su vida útil y garantizando un comportamiento más estable durante ciclos prolongados de producción.
La lubricación en la embutición de metales es un factor muchas veces subestimado, pero absolutamente esencial. Sin un sistema adecuado de lubricación, la fricción entre chapa y troquel aumenta, lo que eleva las fuerzas requeridas, acelera el desgaste de las herramientas y provoca defectos como rayaduras o marcas superficiales. En aplicaciones críticas, como la producción de envases de aluminio o la fabricación de componentes automotrices, se emplean lubricantes especializados con aditivos de extrema presión, diseñados para soportar condiciones de contacto severas. En algunos casos se utilizan recubrimientos sólidos sobre la chapa, como películas poliméricas o grafito, que reducen la fricción de manera más controlada y permiten prescindir de aceites que luego serían costosos de eliminar en los procesos posteriores. La tendencia actual, motivada por razones medioambientales, es reducir el uso de lubricantes contaminantes y sustituirlos por soluciones ecológicas y reciclables, lo que añade un desafío adicional a los ingenieros que deben mantener la calidad del proceso con opciones más sostenibles.
El desarrollo tecnológico de las prensas de embutición de metales ha llevado a la integración de sistemas de monitorización en tiempo real, capaces de medir la fuerza aplicada en cada instante del ciclo, la velocidad de desplazamiento del punzón y la presión ejercida por el cojín. Gracias a estos sistemas, se obtiene un registro completo de cada operación y se pueden detectar variaciones mínimas que indiquen un inicio de desgaste en el troquel, un desajuste en la lubricación o un comportamiento anómalo del material. En las fábricas más avanzadas, estos datos se integran en plataformas de análisis que permiten optimizar los parámetros de manera continua, reduciendo el índice de piezas defectuosas y aumentando el rendimiento global. La embutición, que históricamente se concebía como un proceso de fuerza bruta, hoy se entiende como una disciplina de alta precisión, donde cada variable está cuantificada y controlada.
Por último, la relevancia de la prensa de embutición de metales se aprecia en la amplitud de aplicaciones que permite. Desde latas de bebidas, tapas metálicas y envases de alimentos que requieren geometrías uniformes y alta productividad, hasta grandes paneles automotrices, depósitos de combustible o carcasas de electrodomésticos, este tipo de prensa ofrece una versatilidad que difícilmente podría alcanzarse con otros métodos de conformado. Además, con el auge de nuevas aleaciones ligeras en la industria del transporte y la necesidad de piezas cada vez más complejas en la electrónica y la ingeniería médica, el papel de estas prensas seguirá creciendo, obligando a que su diseño incorpore innovaciones constantes en control, automatización y compatibilidad con nuevos materiales. De este modo, la prensa de embutición de metales no es solamente una máquina de taller, sino un componente esencial de la cadena de valor industrial moderna, donde precisión, resistencia, economía de escala y sostenibilidad se encuentran en un mismo proceso de transformación.
La embutición de metales realizada con prensas especializadas presenta una serie de fenómenos que, si bien son aprovechados por la ingeniería para moldear piezas con precisión, también conllevan riesgos de defectos que deben ser analizados y controlados con suma atención. Uno de los más comunes es la formación de arrugas, que aparecen generalmente en la zona de brida cuando el material no se mantiene bajo la presión adecuada del cojín o cuando la fricción es insuficiente para controlar el flujo de la chapa. Estas arrugas no solo deterioran el aspecto estético de la pieza, sino que también generan concentraciones de tensiones que, en procesos posteriores, pueden convertirse en puntos de fallo. Para evitarlas, los ingenieros ajustan de manera milimétrica la presión de sujeción y recurren a modificaciones en la geometría del troquel, como la incorporación de radios progresivos que suavizan el flujo del material. Otro defecto frecuente es la fisuración o rotura de la chapa, que suele originarse por un estiramiento excesivo en las zonas donde las tensiones de tracción superan el límite de resistencia del material. Este problema se enfrenta diseñando radios de punzón más amplios, optimizando la lubricación o variando la relación entre el diámetro inicial de la chapa y el diámetro de la pieza final, lo que se conoce como relación de embutición. Cuanto mayor es esta relación, más exigente se vuelve el proceso, y de allí la importancia de planificar embuticiones en varias etapas cuando se requieren profundidades extremas.
El adelgazamiento localizado del material es otro fenómeno crítico, especialmente en piezas que deben soportar presiones internas o esfuerzos mecánicos durante su vida útil, como depósitos, tuberías conformadas o componentes estructurales. En estas situaciones, un espesor reducido puede convertirse en un punto débil que comprometa la seguridad de toda la aplicación. Para controlar este adelgazamiento, se recurre a cálculos detallados de la distribución de tensiones, a la simulación por computadora y, en algunos casos, a la introducción de procesos auxiliares como el planchado, en el cual el punzón fuerza al material a fluir de manera uniforme contra la pared del troquel, corrigiendo variaciones de espesor. Sin embargo, el planchado aumenta considerablemente las fuerzas necesarias, lo que implica contar con prensas de mayor capacidad y troqueles preparados para resistir un desgaste acelerado. En este punto, la elección del material del troquel y sus recubrimientos se vuelve determinante, pues de ellos depende que la herramienta mantenga su precisión dimensional después de miles o millones de ciclos de producción.
La aparición de marcas superficiales o rayaduras también es un tema que preocupa en industrias como la automotriz o la de envases, donde el acabado superficial es un requisito esencial. Estas imperfecciones suelen originarse en la fricción inadecuada entre la chapa y las superficies del troquel, en partículas contaminantes atrapadas en el lubricante o en defectos microscópicos del propio acero del troquel. Para mitigarlas, se implementan protocolos estrictos de limpieza, filtración de lubricantes y pulido de las herramientas hasta alcanzar niveles de rugosidad extremadamente bajos. Incluso, en aplicaciones críticas, los troqueles se diseñan con geometrías específicas para reducir las zonas de contacto directo y favorecer un flujo más controlado del material. La superficie de la chapa en sí también juega un papel importante: pequeñas irregularidades, óxidos o contaminaciones superficiales pueden amplificarse durante la embutición y convertirse en defectos visibles en la pieza final. Por ello, los procesos previos de limpieza, decapado o recubrimiento protector de las chapas son esenciales para garantizar un comportamiento predecible durante la conformación.
Los avances recientes en la embutición de metales han permitido implementar sistemas de corrección automática que, mediante sensores de fuerza, desplazamiento y presión, ajustan en tiempo real los parámetros de la prensa para mantener la calidad constante. Estos sistemas no solo evitan defectos en la pieza actual, sino que aprenden del proceso acumulando datos que se utilizan para prever tendencias y programar mantenimientos preventivos en la maquinaria. Así, la prensa de embutición de metales ya no se percibe como una máquina rígida con parámetros fijos, sino como un sistema adaptable capaz de responder a variaciones en las propiedades del material, en la lubricación o en las condiciones ambientales de la planta de producción. El impacto de esta transformación es evidente: menores tasas de desperdicio, ahorro en energía al evitar ciclos defectuosos y mayor vida útil de los troqueles gracias a un uso más equilibrado de los esfuerzos.
La importancia estratégica de estas prensas en la industria contemporánea no puede subestimarse. La fabricación de automóviles, electrodomésticos, envases metálicos y dispositivos médicos depende en gran medida de piezas obtenidas por embutición. En el caso de la automoción, por ejemplo, la búsqueda de aligerar los vehículos para reducir emisiones ha impulsado el uso de chapas de alta resistencia y de aleaciones ligeras como el aluminio o el titanio. Estos materiales presentan desafíos adicionales en la embutición: el acero avanzado de alta resistencia tiende a fracturarse si no se controla el proceso con exactitud, mientras que el aluminio, aunque más dúctil, genera mayores problemas de arrugas y requiere lubricantes especiales. En el sector de los envases, la embutición es la técnica clave para producir latas a gran escala, donde la velocidad de ciclo se mide en cientos de piezas por minuto y la precisión debe garantizar que cada envase sea hermético y uniforme. En medicina, la embutición de aceros inoxidables de grado quirúrgico se utiliza para fabricar piezas como implantes, carcasas de instrumentos o contenedores estériles, donde las tolerancias dimensionales y la ausencia de defectos son absolutamente vitales.
La evolución futura de la prensa de embutición de metales apunta hacia sistemas aún más inteligentes, capaces de integrarse en líneas de producción totalmente digitalizadas en las que la trazabilidad de cada pieza queda registrada desde la lámina inicial hasta el producto acabado. La tendencia a la personalización masiva y a la fabricación flexible exige que estas máquinas sean versátiles, capaces de adaptarse rápidamente a diferentes geometrías sin perder eficiencia. Al mismo tiempo, la presión medioambiental obliga a desarrollar procesos más limpios, con lubricantes biodegradables, menor consumo energético y estrategias de reciclaje de materiales más efectivas. Todo ello convierte a la embutición en un campo donde la tradición centenaria de conformar metales con fuerza bruta se une a la ciencia de datos, la simulación avanzada y la sostenibilidad, consolidando a estas prensas como pilares indispensables de la industria moderna.
Prensa para Estampado Industrial
La prensa para estampado industrial es una de las máquinas más representativas en el ámbito de la transformación de metales, ya que permite convertir láminas planas de acero, aluminio, cobre u otras aleaciones en piezas con formas específicas mediante la aplicación de grandes fuerzas a través de troqueles diseñados con geometrías particulares. En esencia, su función consiste en transferir la energía de un sistema mecánico o hidráulico hacia la chapa metálica, que bajo condiciones controladas de presión y velocidad adopta la forma deseada con altos niveles de precisión y repetitividad. En un entorno industrial moderno, estas prensas trabajan integradas a líneas automatizadas de alimentación, corte, embutición y expulsión, lo que garantiza no solo una elevada productividad sino también una reducción significativa de errores humanos y desperdicios de material. El estampado industrial, gracias a estas máquinas, permite fabricar desde componentes pequeños como arandelas, clips y piezas electrónicas hasta partes de gran tamaño como paneles de carrocería, chasis estructurales o elementos de maquinaria pesada.
El funcionamiento de una prensa de estampado industrial se basa en la coordinación precisa entre tres elementos fundamentales: la fuente de energía (que puede ser un motor eléctrico acoplado a un sistema de volante en el caso de las prensas mecánicas, o un conjunto de cilindros en las hidráulicas), el bastidor que soporta los esfuerzos durante el ciclo de trabajo y los troqueles que definen la geometría de la pieza final. En la industria se utilizan distintos tipos de prensas dependiendo de las necesidades: las prensas excéntricas y de manivela se emplean en operaciones de alta velocidad y gran volumen de producción, mientras que las hidráulicas son más versátiles y adecuadas para procesos que requieren grandes recorridos del émbolo y control preciso de la fuerza aplicada en cada etapa. Esta diversidad permite que el estampado se adapte tanto a producciones masivas de piezas idénticas como a series más cortas de componentes complejos que exigen ajustes específicos.
Una de las características más destacadas de la prensa para estampado industrial es su capacidad para integrar operaciones múltiples en un solo ciclo, lo que se conoce como estampado progresivo. En este sistema, una tira de chapa avanza paso a paso a través de una matriz compuesta por varias estaciones, cada una de las cuales realiza una operación distinta: perforado, doblado, embutición parcial, recorte o conformado final. De esta manera, en un solo golpe de la prensa y con cada avance del material, se obtiene una pieza completamente terminada, lista para pasar a procesos de montaje o tratamiento superficial. Este método, muy utilizado en la fabricación de componentes automotrices y electrónicos, reduce drásticamente los tiempos de producción y asegura una uniformidad absoluta entre millones de piezas. Por otro lado, cuando se requiere producir componentes de mayor tamaño, como puertas, capós o electrodomésticos, las prensas transfer y las de gran tonelaje permiten manipular láminas enteras, realizando embuticiones profundas y estampados en varias etapas con gran estabilidad dimensional.
El impacto de las prensas de estampado en la industria contemporánea se refleja no solo en la capacidad de producción en masa, sino también en la calidad estructural de los productos resultantes. La resistencia mecánica, la precisión de las dimensiones y la repetibilidad en lotes de miles o millones de unidades son cualidades que estas máquinas aseguran, siempre que se mantengan en condiciones óptimas de calibración y mantenimiento. Asimismo, el uso de aceros de alta resistencia y aleaciones ligeras ha obligado a los fabricantes de prensas a desarrollar estructuras más robustas, controles electrónicos avanzados y sistemas de lubricación adaptados para reducir el desgaste prematuro de los troqueles. Estas innovaciones permiten enfrentar los desafíos de producir piezas cada vez más ligeras, delgadas y resistentes, manteniendo al mismo tiempo los costes bajo control y reduciendo el impacto ambiental gracias al mejor aprovechamiento del material.
La tendencia actual apunta hacia prensas de estampado industrial inteligentes, equipadas con sensores que monitorean en tiempo real parámetros como la fuerza de impacto, la temperatura, la vibración y el desgaste de los troqueles. Esta información se integra en sistemas de control digital que no solo corrigen desviaciones en el mismo instante en que se producen, sino que también generan bases de datos útiles para planificar mantenimientos predictivos y mejorar continuamente la eficiencia del proceso. En este sentido, la prensa de estampado deja de ser vista como un simple equipo mecánico para convertirse en una herramienta estratégica en la cadena de valor industrial, capaz de responder a las exigencias de calidad, sostenibilidad y flexibilidad que demandan los mercados globales.
La prensa para estampado industrial representa una pieza fundamental en la manufactura moderna porque concentra en su operación la posibilidad de transformar materiales metálicos de forma masiva, estandarizada y con un grado de precisión que difícilmente podría alcanzarse mediante procesos manuales o por otras técnicas de conformado. Su importancia se refleja en sectores como el automotriz, el electrodoméstico, la electrónica, la construcción y la fabricación de maquinaria, donde millones de piezas idénticas requieren fabricarse con tolerancias muy estrictas y en plazos de tiempo reducidos. Lo que distingue a una prensa de estampado industrial frente a otros equipos de conformado es la combinación de potencia, control y repetitividad, ya que en cada ciclo de trabajo se aplican fuerzas que pueden oscilar desde unas pocas toneladas hasta miles de toneladas en función de la complejidad de la pieza, del espesor de la lámina y de la geometría del troquel. Cada golpe de la prensa está calculado con exactitud para garantizar que el material fluya dentro del troquel sin fisuras ni deformaciones indeseadas, lo que permite producir piezas con bordes definidos, radios precisos y superficies libres de imperfecciones.
Cuando se analiza con mayor profundidad el funcionamiento de estas prensas, se observa que el proceso de estampado no consiste únicamente en el acto de presionar un metal entre dos superficies, sino que es un fenómeno de deformación plástica controlada en el cual intervienen múltiples variables físicas y mecánicas. La velocidad de trabajo es uno de los factores críticos, ya que influye directamente en el comportamiento del material durante la deformación. Una velocidad demasiado alta puede generar calentamiento localizado, fracturas o arrugas, mientras que una velocidad demasiado baja podría reducir la productividad y ocasionar un gasto energético innecesario. Por ello, los fabricantes de prensas diseñan sistemas que equilibran fuerza y velocidad, de manera que el ciclo sea lo suficientemente rápido para garantizar eficiencia pero también lo bastante controlado para evitar defectos en la pieza. Otro aspecto crucial es la rigidez estructural del bastidor, porque durante cada golpe se transmiten fuerzas inmensas que si no están adecuadamente absorbidas por la estructura de la máquina, pueden ocasionar desviaciones en el paralelismo del émbolo y el troquel, lo que compromete la precisión del producto final.
La tecnología de troqueles también desempeña un papel decisivo en el estampado industrial. Existen troqueles de una sola operación que ejecutan cortes, perforaciones o doblados simples, pero también troqueles compuestos y progresivos capaces de realizar múltiples tareas en un solo ciclo. En un troquel progresivo, por ejemplo, una lámina metálica se alimenta de forma continua y con cada avance queda posicionada en una estación distinta del troquel, donde se realiza una operación parcial hasta que finalmente se obtiene la pieza completa. Esto significa que en un mismo golpe de prensa, mientras una parte de la lámina recibe un punzonado, otra es doblada y otra se libera como pieza terminada. La precisión con la que se diseñan y fabrican estos troqueles es tan elevada que incluso una desviación de micras puede provocar que las piezas finales no cumplan con las tolerancias establecidas, lo que obliga a detener la producción y reajustar el proceso. La fabricación de troqueles, por tanto, es una disciplina altamente especializada que acompaña inseparablemente a la operación de las prensas de estampado.
En términos de cálculos técnicos, la determinación del tonelaje necesario para una prensa depende de parámetros como el espesor y la resistencia del material, el perímetro de corte o embutición y el grado de complejidad geométrica de la pieza. Por ejemplo, para calcular la fuerza de corte en una operación de punzonado se multiplica el perímetro de corte por el espesor de la lámina y por la resistencia al corte del material. Estos cálculos permiten definir si una prensa de 100 toneladas será suficiente o si se requiere una de 500 o incluso más, dependiendo de la aplicación. En embuticiones profundas, además de la fuerza máxima, se necesita controlar la presión ejercida sobre el material a través del pisador, que evita que la lámina forme pliegues mientras es empujada dentro de la cavidad del troquel. Este control de presiones múltiples es lo que diferencia a una prensa de alta gama de una prensa convencional, ya que el éxito de la operación no depende solo de la fuerza bruta, sino del equilibrio entre el punzonado, el pisador y los sistemas de guiado.
Las aplicaciones industriales de estas prensas son tan diversas que abarcan desde la producción de piezas estructurales en automóviles hasta la creación de componentes electrónicos diminutos. En la industria automotriz, por ejemplo, grandes prensas de estampado en tándem son capaces de dar forma a paneles completos de carrocerías con una velocidad de ciclo impresionante, asegurando al mismo tiempo que cada panel cumpla con estrictos estándares de calidad dimensional y superficial. En el sector electrónico, en cambio, prensas más pequeñas pero de alta velocidad producen miles de microcomponentes como conectores, resortes o terminales que requieren tolerancias extremadamente finas. En ambos casos, la capacidad de producir en serie piezas idénticas y con un costo unitario reducido convierte a la prensa de estampado industrial en un pilar de la manufactura global.
Al mismo tiempo, la digitalización y la automatización han llevado a que estas prensas evolucionen hacia sistemas inteligentes. Hoy en día, muchas están equipadas con sensores que miden en tiempo real la fuerza aplicada, el desgaste de los troqueles, la alineación de los componentes y hasta la temperatura en zonas críticas. La información recolectada se procesa mediante sistemas de control CNC que ajustan parámetros automáticamente, reduciendo la posibilidad de error humano y permitiendo un mantenimiento predictivo que evita paradas inesperadas. Esta integración de tecnología digital no solo optimiza el rendimiento de la prensa, sino que también extiende la vida útil de los troqueles y mejora la trazabilidad del proceso productivo, aspectos cada vez más valorados en una industria orientada a la calidad total y a la eficiencia energética.
Las prensas de estampado industrial pueden clasificarse principalmente en mecánicas, hidráulicas y servo-prensas, cada una con características que las hacen más adecuadas para determinadas aplicaciones dentro del vasto campo de la manufactura. La prensa mecánica es la más tradicional y se basa en un sistema de volante de inercia, embrague y biela que convierte el movimiento rotativo en un movimiento lineal alternativo del émbolo. Su gran ventaja es la alta velocidad de trabajo, lo que la hace ideal para operaciones repetitivas como punzonados, cortes o doblados simples de láminas metálicas en grandes volúmenes. Sin embargo, su limitación radica en que la fuerza máxima solo se alcanza en un punto específico del recorrido, normalmente cerca del punto muerto inferior, lo que puede dificultar procesos como la embutición profunda donde se requiere aplicar una fuerza constante a lo largo de un tramo mayor del recorrido. Además, las prensas mecánicas ofrecen menor flexibilidad para variar la velocidad de carrera y la posición de parada, lo que las hace menos versátiles en procesos que demandan precisión variable.
Por otra parte, la prensa hidráulica opera mediante cilindros hidráulicos que generan la fuerza de trabajo aplicando presión a través de un fluido. Este sistema permite controlar con mayor exactitud la presión ejercida durante todo el recorrido, lo que resulta esencial para embuticiones profundas, estampados complejos y conformados donde es necesario mantener fuerzas elevadas durante largos desplazamientos. A diferencia de la mecánica, la prensa hidráulica ofrece una curva de fuerza constante a lo largo de todo el recorrido, lo cual amplía enormemente las posibilidades de conformado de piezas de geometrías complicadas o de materiales de alta resistencia. También brinda mayor flexibilidad al operador porque puede ajustar fácilmente la carrera, la velocidad y la fuerza según la operación. Sin embargo, su desventaja principal es la velocidad relativamente más baja frente a las prensas mecánicas, lo que puede limitar la productividad en operaciones que requieren miles de piezas por hora. Asimismo, los sistemas hidráulicos necesitan un mantenimiento riguroso debido al desgaste de válvulas, sellos y al riesgo de fugas de aceite, que además pueden afectar la limpieza en la planta de producción.
Las servo-prensas representan la evolución tecnológica más avanzada al integrar un motor servoeléctrico de alta precisión que controla directamente el movimiento del émbolo sin necesidad de embragues ni sistemas hidráulicos. Este tipo de prensa combina lo mejor de ambos mundos: la velocidad de las mecánicas y la flexibilidad de las hidráulicas. Gracias a la programación del motor, es posible definir perfiles de movimiento específicos en los que la velocidad, la fuerza y la posición del émbolo se ajustan con una precisión extraordinaria. Esto permite realizar operaciones de estampado complejo con gran control sobre la deformación del material, reduciendo rebabas, arrugas o defectos superficiales. Además, las servo-prensas son mucho más eficientes energéticamente porque consumen energía solo cuando es necesario aplicar movimiento o fuerza, en contraste con los sistemas hidráulicos que mantienen una presión constante en el circuito. También destacan por su bajo nivel de ruido y por la posibilidad de integración total con sistemas de automatización y monitoreo digital en entornos de producción inteligente. La principal barrera de estas prensas sigue siendo su elevado costo inicial, aunque a largo plazo este se compensa por la reducción de desperdicios, el menor mantenimiento y el ahorro energético.
Si se comparan en el terreno práctico, la selección de un tipo de prensa u otro depende de la naturaleza del producto a fabricar y de los volúmenes de producción esperados. Una empresa automotriz que produce paneles de carrocería en millones de unidades anuales puede optar por grandes prensas mecánicas en línea tándem debido a su velocidad y robustez, complementadas con robots que alimentan y extraen las piezas a gran velocidad. Una empresa dedicada a la fabricación de utensilios de cocina embutidos, como ollas o fregaderos, suele preferir prensas hidráulicas porque necesitan controlar la presión en procesos de embutición profunda de láminas de acero inoxidable sin que se generen fisuras. En cambio, sectores de alta precisión como el electrónico o el aeroespacial encuentran en las servo-prensas la solución ideal para fabricar componentes con tolerancias extremadamente estrechas y con trazabilidad completa del proceso gracias a los sistemas de monitoreo integrados.
La tendencia actual de la industria es avanzar hacia sistemas híbridos en los que se aprovechen las virtudes de cada tecnología y se integren en líneas de producción inteligentes donde las prensas no operan como máquinas aisladas, sino como parte de una cadena automatizada que incluye alimentadores automáticos de bobinas, sistemas de centrado y alineación, robots de transferencia y células de inspección de calidad. En este contexto, las prensas modernas no solo cumplen la función de aplicar fuerza sobre una lámina, sino que se convierten en nodos dentro de un ecosistema de fabricación donde cada variable es medida, analizada y ajustada en tiempo real para garantizar eficiencia, calidad y sostenibilidad. Con ello, la prensa de estampado industrial se consolida como una máquina clave en la cuarta revolución industrial, manteniendo su esencia de transformar el metal, pero ahora potenciada por la inteligencia digital y el control absoluto sobre cada ciclo de trabajo.
En el ámbito técnico de las prensas de estampado industrial, uno de los aspectos más críticos es el cálculo correcto del tonelaje requerido para cada operación, ya que de ello depende no solo la calidad del producto final, sino también la vida útil de la máquina y la seguridad en el proceso. El tonelaje se define como la fuerza máxima que la prensa puede ejercer durante su carrera, y su cálculo está directamente relacionado con variables como el espesor del material, la resistencia del mismo, la longitud del corte o embutido y la geometría de la pieza. En una operación de corte o punzonado, por ejemplo, el tonelaje se determina multiplicando el perímetro de la pieza a cortar por el espesor de la lámina y por la resistencia al corte del material, obteniendo así un valor aproximado que permite seleccionar una prensa con la capacidad suficiente para llevar a cabo la operación sin riesgo de sobrecargarla. Sin embargo, en operaciones más complejas como la embutición profunda, este cálculo se vuelve más sofisticado, ya que entran en juego factores como el coeficiente de fricción entre la lámina y el troquel, el radio de embutición y la necesidad de aplicar fuerzas auxiliares mediante pisadores o cojines hidráulicos que eviten el arrugamiento del material durante la deformación.
El sistema de pisadores en una prensa de estampado cumple un papel fundamental, pues son los encargados de mantener la lámina en posición y de controlar el flujo del material hacia la cavidad del troquel. Una presión insuficiente del pisador puede ocasionar que la lámina se deforme de manera irregular, produciendo arrugas, pliegues o incluso la rotura de la pieza. Por el contrario, una presión excesiva puede impedir el correcto flujo del material y generar desgarramientos. Por esta razón, en prensas de gran capacidad, sobre todo las hidráulicas y servo-prensas, se emplean sistemas de cojines de presión ajustables que distribuyen la fuerza de manera uniforme y permiten controlar con gran precisión la presión ejercida en cada etapa del proceso. En el diseño del troquel también se debe considerar este factor, ya que una distribución incorrecta de los esfuerzos puede derivar en desgaste prematuro de las herramientas, fisuras en las matrices o incluso accidentes por fallas súbitas en los componentes.
La distribución de esfuerzos dentro de la prensa es otro aspecto clave que los ingenieros deben estudiar cuidadosamente. Cuando el esfuerzo no se aplica de manera equilibrada, se generan cargas excéntricas que afectan tanto al bastidor como a los mecanismos internos de la máquina, provocando desalineaciones en el émbolo y desgastes irregulares en las guías. Para evitar estos problemas, en la práctica se recomienda que la carga aplicada se mantenga dentro de los márgenes de capacidad de la prensa y, preferentemente, centrada en el área de trabajo. En prensas modernas, especialmente en las servo-prensas, se utilizan sensores y sistemas de monitoreo en tiempo real que registran la distribución de fuerzas durante cada golpe, lo que permite detectar desviaciones e implementar ajustes inmediatos para mantener la máquina trabajando dentro de parámetros seguros.
Además de los aspectos puramente mecánicos, el diseño del proceso de estampado también influye de manera decisiva en la eficiencia y durabilidad del sistema. Factores como la lubricación adecuada del material, la temperatura de trabajo en procesos especiales y la calidad superficial de la lámina influyen directamente en la fricción y en la fuerza necesaria para conformar o cortar el metal. Una lubricación insuficiente, por ejemplo, no solo incrementa la fricción y el esfuerzo requerido, sino que también acelera el desgaste de los troqueles y puede generar defectos en la superficie de la pieza. Por ello, en entornos de alta producción se aplican lubricantes específicos mediante sistemas automáticos de pulverización o rodillos, optimizando así el consumo y asegurando una cobertura uniforme en cada ciclo.
La tendencia en la industria es hacia la digitalización y la integración de estos cálculos y variables en sistemas de control avanzados que permiten predecir el comportamiento de la prensa en cada operación antes de llevarla a cabo. Mediante simulaciones de elementos finitos se pueden modelar las fuerzas, deformaciones y tensiones en la lámina y en los componentes del troquel, lo que reduce significativamente el tiempo de desarrollo de nuevos procesos y minimiza el riesgo de errores en la producción real. Esto se traduce en una mayor eficiencia, en una reducción de desperdicios y en la capacidad de producir piezas de geometrías cada vez más complejas con tolerancias mínimas. En este contexto, la prensa de estampado industrial deja de ser solo una máquina que aplica fuerza para transformarse en una plataforma tecnológica de precisión, donde la mecánica, la hidráulica, la electrónica y el software trabajan de manera conjunta para garantizar resultados óptimos y reproducibles en grandes volúmenes de producción.
Prensa de Dibujo Profundo
La prensa de dibujo profundo es una máquina especializada que ocupa un lugar esencial dentro de los procesos de transformación de metales, ya que permite fabricar piezas de geometrías complejas a partir de chapas planas mediante una deformación plástica controlada. A diferencia de otras prensas de estampado o corte que únicamente realizan operaciones de cizallado, punzonado o embutición superficial, la prensa de dibujo profundo está diseñada para desplazar grandes volúmenes de material hacia la cavidad de un troquel sin que se produzcan fisuras, desgarros o pliegues indeseados en la superficie de la pieza. Este tipo de prensas se utiliza ampliamente en la fabricación de componentes cilíndricos, cónicos o de geometrías mixtas como latas, envases metálicos, depósitos, carcasas automotrices, utensilios de cocina, fregaderos y tanques a presión, donde se requiere que el material conserve un espesor relativamente uniforme y propiedades mecánicas adecuadas después del proceso de conformado.
El principio de funcionamiento de la prensa de dibujo profundo se basa en el control preciso del flujo del material entre el punzón y la matriz, lo cual requiere la aplicación simultánea de varias fuerzas: la del punzón, que impulsa la chapa hacia el interior del troquel; la del pisador o cojín, que evita el arrugamiento de los bordes y controla la entrada del material; y en muchos casos, la de sistemas auxiliares hidráulicos que compensan tensiones o aseguran la distribución uniforme de esfuerzos. Una de las características técnicas más importantes en este tipo de prensas es la relación de embutición, que corresponde a la proporción entre el diámetro inicial del blank (disco metálico) y el diámetro final de la pieza. Cuando esta relación es demasiado elevada, el riesgo de que el material se fracture o se formen pliegues aumenta considerablemente, lo que obliga a realizar operaciones intermedias conocidas como redibujos, en las que la pieza se somete a nuevos ciclos de embutición con geometrías progresivamente más cercanas al diseño final.
La elección de una prensa de dibujo profundo depende de factores como el tipo de material a trabajar, su resistencia mecánica, el espesor de la chapa y la complejidad geométrica de la pieza. Los materiales más utilizados son el acero bajo en carbono, el aluminio, el cobre y algunas aleaciones inoxidables, los cuales presentan buena ductilidad y resistencia suficiente para soportar deformaciones significativas sin romperse. Para garantizar la calidad del producto, resulta imprescindible el uso de lubricantes adecuados que reduzcan la fricción entre el material y las superficies de contacto con el troquel, ya que un coeficiente de fricción elevado puede aumentar la fuerza necesaria, acelerar el desgaste de las herramientas y generar defectos visibles en la superficie de la pieza.
En cuanto a su construcción, las prensas de dibujo profundo pueden ser de tipo mecánico, hidráulico o servo-controlado. Las mecánicas son más rápidas y adecuadas para producciones masivas de piezas relativamente simples, mientras que las hidráulicas ofrecen mayor flexibilidad y control de la fuerza durante toda la carrera del punzón, lo cual resulta esencial para embuticiones complejas o de gran profundidad. Las servo-prensas, por su parte, representan la tecnología más avanzada, pues permiten programar perfiles de velocidad y fuerza personalizados, optimizando así tanto la calidad de la pieza como la eficiencia energética del proceso. Estas últimas son especialmente apreciadas en la industria automotriz y de electrodomésticos, donde se requieren piezas de precisión en grandes volúmenes de producción.
El mantenimiento y la precisión en el ajuste de una prensa de dibujo profundo también son determinantes para su rendimiento. Un desajuste en la alineación del punzón con respecto a la matriz puede provocar un desgaste irregular, un flujo asimétrico del material y defectos irreparables en las piezas producidas. De igual forma, la calibración de los cojines hidráulicos o neumáticos debe garantizar una presión uniforme, ya que de lo contrario se generan arrugas localizadas o fisuras por exceso de tensión. Gracias a los avances tecnológicos, muchas de estas prensas modernas incorporan sensores de carga, sistemas de monitoreo en tiempo real y software de simulación que permiten anticipar posibles fallos y optimizar cada etapa del proceso de embutición profunda.
La prensa de dibujo profundo no solo se distingue por su capacidad de transformar una simple lámina metálica en un cuerpo tridimensional con gran profundidad, sino también por la precisión con la que debe ejecutarse cada etapa del proceso. El éxito de una operación de embutición profunda depende de un conjunto complejo de variables que interactúan de manera dinámica: la geometría de los punzones y matrices, la presión ejercida por los cojines de sujeción, la fricción entre chapa y herramienta, la resistencia del material, el espesor inicial y su distribución durante la deformación. Por eso, estas prensas han evolucionado hacia sistemas sumamente sofisticados en los que la automatización, la simulación por software y los controles digitales son tan importantes como la robustez mecánica de la estructura. Cuando se embute una chapa, esta experimenta un flujo radial que va desde el borde hacia el interior del troquel, y en ese movimiento la superficie se encuentra sometida a esfuerzos de tracción y compresión que, si no se controlan, pueden provocar fracturas longitudinales o arrugas periféricas. De ahí que el diseño del radio de embutición en la matriz sea crítico, porque radios demasiado pequeños concentran tensiones y favorecen la aparición de grietas, mientras que radios excesivamente grandes facilitan el deslizamiento pero aumentan el riesgo de arrugas.
El control de la fricción constituye otro de los aspectos decisivos en el dibujo profundo. Una fricción alta eleva la fuerza de embutición requerida, desgasta las herramientas y puede causar marcas superficiales en la pieza, mientras que una fricción demasiado baja provoca un flujo descontrolado del material que genera pliegues. Por eso, la selección del lubricante no es un factor secundario sino una de las condiciones que determinan la viabilidad técnica del proceso. Lubricantes con aditivos sólidos, como el disulfuro de molibdeno, o emulsiones específicas para acero inoxidable y aluminio, se aplican de manera estratégica para mantener un equilibrio entre adherencia y deslizamiento. Al mismo tiempo, en prensas modernas, sensores integrados monitorean en tiempo real las cargas de embutición y las variaciones en la fuerza de retención, ajustando automáticamente los parámetros para compensar cambios en la lubricación, la temperatura o las propiedades del lote de material.
Un elemento igualmente crucial es la relación de embutición. En teoría, un blank de diámetro grande puede transformarse en un cilindro profundo, pero en la práctica la proporción entre el diámetro inicial y el diámetro final está limitada por la ductilidad del material y por la capacidad de la prensa de controlar la deformación. Cuando la relación es demasiado alta, la pieza no puede embutirse en una sola operación y se recurre al redibujo progresivo. Cada redibujo implica pasar la pieza por un nuevo conjunto de punzón y matriz, reduciendo gradualmente el diámetro y aumentando la altura sin comprometer la integridad estructural del material. Este método se observa claramente en la fabricación de latas de bebidas, envases de conservas o cartuchos metálicos, donde la calidad superficial, la uniformidad del espesor y la ausencia de tensiones residuales son requisitos innegociables.
Las industrias que más aprovechan la prensa de dibujo profundo son la automotriz, la aeronáutica, la de electrodomésticos, la de utensilios de cocina y la de envases metálicos. En el sector automotor, estas prensas permiten fabricar depósitos de combustible, carcasas para embragues, cubetas de aceite, componentes estructurales de carrocerías y piezas de sistemas de suspensión. En aeronáutica se emplean para conformar elementos de aleaciones ligeras que deben soportar grandes esfuerzos con bajo peso. En electrodomésticos y menaje, se producen fregaderos, sartenes, ollas y carcasas exteriores de electrodomésticos. En todos los casos, la durabilidad del troquel y la estabilidad dimensional de las piezas son factores de competitividad. Para lograrlo, los troqueles son fabricados en aceros especiales templados, a veces con recubrimientos de nitruro de titanio o carburo que prolongan su vida útil frente a la fricción y el desgaste.
La incorporación de sistemas servo-hidráulicos y servo-mecánicos ha transformado la prensa de dibujo profundo en una máquina inteligente capaz de ajustar automáticamente la velocidad de embutición en cada fase de la carrera, reduciendo aceleraciones bruscas que podrían dañar el material y optimizando el consumo de energía. Estas prensas modernas ofrecen perfiles de movimiento programables que permiten, por ejemplo, comenzar con un avance lento durante el contacto inicial para facilitar la adaptación del material, acelerar en la fase intermedia para aumentar la productividad y desacelerar nuevamente al final para evitar tensiones críticas. Además, los sistemas de control actuales registran cada ciclo de producción, almacenando datos que facilitan la trazabilidad de los lotes y el análisis predictivo de fallos.
En este contexto, la prensa de dibujo profundo deja de ser vista simplemente como un equipo de deformación y se convierte en el eje de una cadena tecnológica donde intervienen la ingeniería de materiales, la simulación por elementos finitos, la robótica de alimentación automática y el control digital avanzado. El resultado es un proceso que puede fabricar millones de piezas idénticas con tolerancias mínimas, un acabado impecable y un aprovechamiento máximo de la materia prima. Esto último es vital, ya que en industrias de gran volumen incluso una reducción marginal en el desperdicio de material se traduce en enormes ahorros económicos y en beneficios ambientales asociados a la reducción de chatarra.
En el estudio más detallado de la prensa de dibujo profundo resulta imprescindible analizar las diferencias tecnológicas entre los sistemas mecánicos, hidráulicos y servoaccionados, ya que cada uno de ellos responde de manera particular a las necesidades de la industria y a las características de los materiales procesados. Las prensas mecánicas de dibujo profundo, que fueron las primeras en masificarse durante la revolución industrial del siglo XX, se basan en un sistema de volante de inercia y biela-manivela que convierte el movimiento rotativo en lineal, proporcionando un ciclo rápido y repetitivo. Su principal ventaja es la velocidad, lo que las hace idóneas para producciones en masa con piezas de geometría relativamente sencilla y profundidades moderadas. Sin embargo, presentan limitaciones importantes, ya que la fuerza disponible no es constante durante toda la carrera, sino que alcanza su máximo en un punto específico del recorrido, lo que dificulta operaciones de gran complejidad en las que el material requiere un esfuerzo uniforme para fluir adecuadamente. Además, el control de parámetros es limitado y dependen en gran medida de la experiencia del operario y de la precisión en el diseño de matrices y punzones.
Las prensas hidráulicas, por el contrario, han aportado un salto cualitativo en el control del proceso. Su principio de funcionamiento se basa en la transmisión de energía mediante fluidos a presión, lo que permite aplicar fuerzas constantes en cualquier punto de la carrera y mantener una presión estable en el tiempo. Esta capacidad es fundamental para operaciones de embutición profunda, donde el material necesita un control minucioso del flujo para evitar roturas, arrugas o espesores desiguales. Otra ventaja crucial es la flexibilidad, ya que la misma prensa hidráulica puede adaptarse a una amplia gama de piezas mediante el ajuste de la presión, la velocidad y el recorrido, lo que resulta atractivo en industrias que manejan lotes más pequeños y productos con diseños complejos. Sin embargo, las prensas hidráulicas suelen ser más lentas que las mecánicas y requieren un mantenimiento cuidadoso de sus sistemas de bombas, válvulas y circuitos hidráulicos, además de un mayor consumo energético en comparación con los sistemas mecánicos tradicionales.
El desarrollo más reciente lo constituyen las prensas servoaccionadas o servo-prensas, que representan una convergencia entre la rapidez de las prensas mecánicas y la flexibilidad de las hidráulicas. Estas máquinas utilizan servomotores eléctricos controlados digitalmente para gestionar cada fase del movimiento del punzón y del cojín de sujeción. La programación de perfiles de movimiento permite, por ejemplo, iniciar la embutición con un descenso lento que favorece el acomodo inicial del material, continuar con una velocidad mayor para incrementar la productividad y finalizar con una desaceleración precisa que evita sobreesfuerzos en la pieza. Esta adaptabilidad convierte a la prensa servo en una herramienta de alto rendimiento especialmente en la fabricación de componentes automotrices de seguridad, como airbags y piezas estructurales, donde no se tolera ninguna imperfección. Además, su eficiencia energética es superior, ya que los servomotores consumen energía únicamente cuando ejecutan movimiento, a diferencia de los sistemas hidráulicos que mantienen la presión incluso en estado de reposo.
Desde el punto de vista económico y de sostenibilidad, la elección entre uno u otro tipo de prensa de dibujo profundo depende de múltiples factores. En producciones masivas de gran volumen, como la industria de envases metálicos para bebidas, todavía se emplean prensas mecánicas de alta velocidad con sistemas de redibujo en varias etapas, ya que el coste por unidad producida se reduce al mínimo gracias a la rapidez del ciclo. En la industria automotriz, donde la complejidad geométrica de las piezas y los requerimientos de calidad superficial son extremadamente exigentes, predominan las prensas hidráulicas y servo-prensas, capaces de garantizar tolerancias mínimas y reproducibilidad absoluta. Por otro lado, sectores como la aeronáutica o la fabricación de menaje de alta gama, donde los volúmenes de producción son menores pero la precisión y la integridad estructural resultan prioritarias, también optan por prensas hidráulicas que permiten realizar embuticiones profundas en aleaciones ligeras o en aceros inoxidables de gran dureza.
Es importante destacar que, más allá del tipo de prensa utilizada, el éxito del proceso de dibujo profundo descansa sobre la interacción entre máquina, herramienta y material. Las herramientas deben diseñarse con radios adecuados, acabados superficiales pulidos al máximo y tratamientos térmicos que les otorguen resistencia al desgaste. El material, por su parte, debe presentar una ductilidad uniforme, libre de tensiones internas y con un espesor homogéneo que garantice una deformación predecible. La prensa, finalmente, debe ser capaz de transmitir la fuerza necesaria de manera controlada y reproducible, evitando variaciones que puedan afectar la calidad de la pieza. En la actualidad, la integración de software de simulación por elementos finitos permite prever cómo se comportará la chapa durante la embutición, optimizando previamente el diseño de herramientas y parámetros de operación, lo que reduce el número de pruebas físicas y los costos de desarrollo.
De este modo, la prensa de dibujo profundo ha dejado de ser simplemente un equipo de transformación mecánica para convertirse en un centro tecnológico donde convergen la ingeniería de materiales, la mecatrónica, la simulación avanzada y la automatización inteligente. El resultado no solo son piezas metálicas con geometrías complejas, sino también un proceso de manufactura eficiente, sostenible y altamente competitivo en un mercado global que demanda calidad absoluta, reducción de tiempos y un aprovechamiento óptimo de los recursos.
Prensa de Estampado de Embutidos
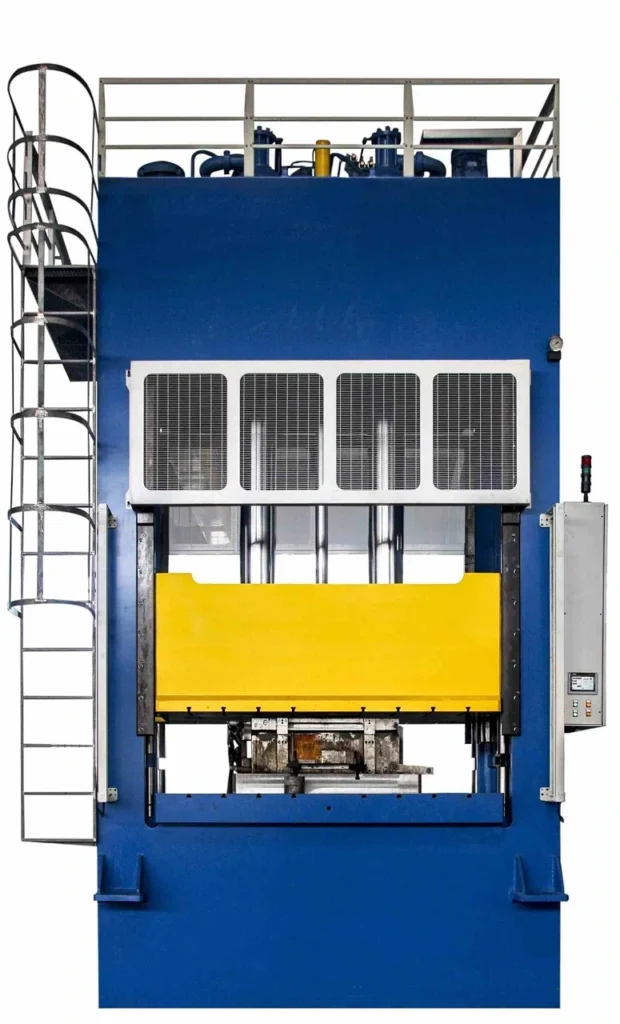
La prensa de estampado de embutidos es un equipo industrial especialmente diseñado para transformar masas de carne y otros ingredientes en productos con formas uniformes y precisas, como salchichas, chorizos, mortadelas o jamones cocidos. A diferencia de las prensas de metal, esta máquina no aplica fuerzas para deformar materiales sólidos rígidos, sino que utiliza presión controlada para compactar, llenar y dar forma a mezclas de carne picada, emulsiones y especias dentro de envoltorios naturales o sintéticos, garantizando densidad uniforme, textura homogénea y aspecto estético atractivo. El funcionamiento se basa en un sistema de tolva o embudo donde se deposita la mezcla de carne previamente molida y mezclada con aditivos, que es empujada mediante pistones, tornillos sin fin o sistemas hidráulicos hacia los moldes o tripas, dependiendo del tipo de embutido que se desee producir. La presión aplicada es ajustable, ya que debe ser suficiente para llenar completamente el molde o tripa sin generar vacíos, pero no excesiva para evitar la ruptura de la envoltura o la pérdida de jugosidad del producto.
En el diseño de estas prensas, la uniformidad de la presión y la precisión en la dosificación son fundamentales, porque afectan directamente la calidad final del embutido. Muchos modelos modernos incorporan sistemas automáticos de control que regulan la velocidad de llenado y la presión en tiempo real, adaptándose a cambios en la densidad de la mezcla o al diámetro de la tripa utilizada. Esto permite producir lotes consistentes, reducir desperdicios y mantener estándares higiénicos elevados, ya que los componentes que entran en contacto con la carne suelen ser de acero inoxidable y diseñados para facilitar la limpieza y evitar la proliferación de bacterias. Además, estas prensas se integran frecuentemente en líneas de producción automáticas que incluyen sistemas de llenado, atado, cocción y empaquetado, optimizando la eficiencia y reduciendo la intervención manual, lo que es crucial en plantas de gran volumen donde se producen miles de unidades diariamente.
La versatilidad de la prensa de estampado de embutidos también radica en la posibilidad de ajustar parámetros como la longitud, el diámetro y la forma final del producto. Algunos modelos permiten cambiar rápidamente los moldes o boquillas para alternar entre diferentes tipos de embutidos sin detener significativamente la línea de producción. Los sistemas de control modernos pueden incluso memorizar configuraciones de presión, velocidad y volumen de mezcla para cada tipo de embutido, facilitando la producción de diferentes recetas con consistencia absoluta. Este nivel de control no solo garantiza un producto uniforme y atractivo para el consumidor, sino que también contribuye a la eficiencia económica de la planta, minimizando el desperdicio de materia prima y el consumo energético asociado a operaciones repetitivas o mal calibradas.
En cuanto a su funcionamiento mecánico, la prensa de estampado de embutidos puede operar mediante sistemas hidráulicos, neumáticos o mecánicos, dependiendo de la capacidad requerida y del tipo de producto. Las prensas hidráulicas son particularmente eficaces para embutidos más compactos o densos, ya que permiten aplicar fuerzas constantes y uniformes durante el llenado, evitando que la carne se comprima de manera desigual. Las prensas neumáticas, más rápidas y ligeras, se utilizan en producciones medianas y en productos de menor densidad. Los modelos mecánicos, aunque menos frecuentes hoy en día, se utilizan en operaciones tradicionales donde se requiere un control manual más directo, como en pequeñas plantas artesanales o en producción limitada de especialidades regionales.
El mantenimiento y la higiene son aspectos críticos en estas prensas, ya que el contacto directo con alimentos exige cumplir estrictamente con normas sanitarias. Todos los componentes desmontables deben ser resistentes a la corrosión, fáciles de limpiar y desinfectar, y la máquina suele diseñarse para evitar rincones donde pueda acumularse la mezcla de carne. Asimismo, el monitoreo constante de la presión y la uniformidad del llenado ayuda a prevenir inconsistencias que podrían afectar la textura, el sabor o la seguridad microbiológica del embutido. En conjunto, la prensa de estampado de embutidos es una herramienta clave en la industria cárnica, capaz de combinar productividad, precisión y estándares sanitarios, y su evolución hacia sistemas automatizados ha permitido mejorar la calidad, reducir el desperdicio y aumentar la eficiencia en la fabricación de productos embutidos de manera industrial.
La prensa de estampado de embutidos, al ser un equipo fundamental en la industria cárnica, presenta un diseño y funcionamiento altamente adaptado a las necesidades de producción de distintos tipos de embutidos, desde los frescos hasta los curados o cocidos, permitiendo mantener uniformidad, textura y forma en grandes volúmenes de manera eficiente. En el caso de los embutidos frescos, la mezcla de carne molida, especias y aditivos se caracteriza por una mayor humedad y menor densidad, lo que exige que la prensa aplique una presión controlada que sea suficiente para llenar la tripa sin generar burbujas de aire ni vacíos, pero evitando comprimir excesivamente la mezcla para no alterar su textura ni provocar exudación de líquidos. Este tipo de prensas suele combinar sistemas hidráulicos con pistones ajustables que permiten regular la fuerza de empuje de manera continua, además de contar con boquillas intercambiables que se adaptan a diferentes diámetros de tripa, garantizando que cada unidad tenga longitud y volumen uniformes. La velocidad de llenado también es crítica; un flujo demasiado rápido podría romper la envoltura, mientras que un flujo demasiado lento reduce la eficiencia de la línea de producción.
En los embutidos cocidos, como mortadelas, jamones o salchichas precocidas, la densidad de la mezcla es mayor debido a la incorporación de gelatinas, proteínas y otros estabilizantes que aumentan la cohesión del producto. En estos casos, la prensa debe generar una presión más elevada y constante para asegurar que la mezcla penetre completamente en la envoltura y adopte la forma deseada sin crear huecos ni irregularidades. Los sistemas de control avanzados permiten ajustar la fuerza de manera progresiva, comenzando con un empuje moderado en la fase inicial y aumentando gradualmente para mantener la uniformidad en toda la longitud del embutido. Además, las prensas modernas para embutidos cocidos incorporan sensores que monitorean la densidad y la presión durante el llenado, asegurando que cada pieza cumpla con los estándares de textura y firmeza establecidos para la cocción posterior.
Los embutidos curados o secos, como salchichones, chorizos secos y fuets, presentan características particulares que requieren adaptaciones específicas en la prensa. Estos productos contienen menos humedad y su mezcla es más firme, lo que implica que la fuerza de estampado debe ser cuidadosamente calibrada para no dañar la envoltura y permitir un flujo controlado de la masa. Algunas prensas para embutidos secos incorporan sistemas de torsión o rodillos adicionales que ayudan a compactar la mezcla dentro de la tripa y a eliminar posibles bolsas de aire, contribuyendo a la consistencia final del producto. También se utilizan sistemas de alimentación más lentos y uniformes, y boquillas con recubrimientos especiales que reducen la fricción y evitan adherencias que podrían deformar la pieza.
La automatización ha transformado significativamente la eficiencia de estas prensas, integrando sistemas que combinan dosificación precisa, regulación de presión, control de longitud y velocidad de llenado en tiempo real. Los equipos modernos pueden almacenar perfiles de operación para cada tipo de embutido, lo que permite cambiar rápidamente de un producto a otro sin ajustes manuales extensivos. Por ejemplo, al pasar de una producción de salchichas frescas a salchichas cocidas, la máquina ajusta automáticamente la presión, la velocidad del pistón, el diámetro de la boquilla y el flujo de mezcla, asegurando que cada unidad producida cumpla con los parámetros de densidad, textura y apariencia establecidos por el fabricante. Este nivel de control no solo mejora la calidad y la consistencia, sino que también reduce el desperdicio de materia prima, minimiza el riesgo de defectos y optimiza el tiempo de producción.
Desde el punto de vista higiénico, la prensa de estampado de embutidos debe cumplir con estrictas normas sanitarias, ya que la carne es altamente perecedera y susceptible a contaminación. Todos los componentes en contacto con la mezcla se fabrican en acero inoxidable, son desmontables y fáciles de limpiar, y las superficies se diseñan para evitar rincones donde pueda acumularse producto. Los sistemas automáticos de limpieza, conocidos como CIP (Clean-in-Place), permiten lavar y desinfectar la máquina sin desarmarla completamente, lo que incrementa la seguridad alimentaria y reduce tiempos de parada en la producción. Asimismo, los controles electrónicos monitorean la presión y el flujo de la mezcla para detectar anomalías que puedan indicar atascos, sobrellenado o inconsistencias en la densidad, lo que previene defectos y garantiza uniformidad en todas las unidades.
En la práctica industrial, estas prensas forman parte de líneas de producción completamente automatizadas que incluyen sistemas de molienda, mezclado, enfriamiento, dosificación, embutido, atado, cocción y empaquetado, funcionando de manera coordinada para producir grandes volúmenes con alta eficiencia. La prensa de estampado de embutidos, por tanto, no es solo un equipo de llenado, sino un componente esencial en la cadena de manufactura industrial cárnica, capaz de combinar precisión, productividad, higiene y flexibilidad para satisfacer las exigencias del mercado moderno. La evolución tecnológica ha permitido que estas prensas, con sus sistemas hidráulicos, neumáticos o servoaccionados, se adapten a cualquier tipo de embutido, garantizando resultados uniformes, optimización de recursos y cumplimiento de estándares sanitarios y de calidad.
La evolución de la prensa de estampado de embutidos hacia sistemas automáticos y altamente tecnológicos ha permitido que la industria cárnica logre niveles de precisión y eficiencia antes inimaginables, transformando completamente la manera en que se producen salchichas, chorizos, jamones cocidos, mortadelas y embutidos especiales. Hoy en día, las prensas automáticas incorporan no solo sistemas hidráulicos o neumáticos de alta precisión para controlar la presión aplicada sobre la mezcla, sino también un conjunto de sensores y software de monitoreo que garantizan uniformidad en densidad, textura, tamaño y peso de cada unidad producida. Estos sistemas son capaces de detectar variaciones en la consistencia de la masa o en el flujo de la mezcla y ajustar automáticamente la fuerza del pistón, la velocidad de llenado o el diámetro de la boquilla para mantener estándares óptimos de calidad. En líneas de producción de gran volumen, esta capacidad de ajuste en tiempo real es esencial, ya que permite alternar rápidamente entre diferentes tipos de embutidos, ya sean frescos, cocidos o curados, sin comprometer la uniformidad ni detener la operación durante largos periodos.
Los sistemas de visión artificial son otra innovación clave, ya que permiten verificar de manera continua la integridad de la envoltura, detectar defectos superficiales, burbujas de aire, deformaciones o irregularidades en el tamaño de cada pieza y enviar señales al sistema de control para corregir cualquier desviación. Esta integración tecnológica garantiza que incluso en producciones masivas cada unidad cumpla con los estándares estéticos y funcionales requeridos por el mercado, reduciendo desperdicios y mejorando la eficiencia global de la planta. Al mismo tiempo, los algoritmos de control predicen el comportamiento de la mezcla en función de su composición, temperatura y humedad, ajustando parámetros de presión y velocidad de forma automática para evitar problemas como desbordes, compactación insuficiente o ruptura de la tripa.
En cuanto al diseño de las prensas, las innovaciones también han abarcado la ergonomía y la higiene, incorporando componentes de acero inoxidable con superficies pulidas, sistemas CIP (Clean-in-Place) que permiten lavar y desinfectar la máquina sin desmontarla completamente, y estructuras modulares que facilitan el mantenimiento y la sustitución rápida de piezas críticas. La combinación de estos avances no solo reduce el riesgo de contaminación bacteriana, sino que también minimiza los tiempos de parada, lo que resulta fundamental en plantas que producen decenas de miles de unidades diariamente. Los sistemas de dosificación automática aseguran que cada embutido tenga exactamente el mismo volumen y peso, mientras que los sistemas de atado, enrollado o sellado complementan la operación, garantizando productos consistentes listos para su cocción, curado o envasado.
Además, las prensas automáticas modernas permiten la integración con líneas completas de producción digitalmente conectadas, en las que cada etapa —mezclado, enfriado, embutido, cocción y empaquetado— se coordina a través de software centralizado. Esto posibilita la recopilación de datos en tiempo real sobre producción, rendimiento de la máquina, consumo energético y calidad del producto, lo que a su vez facilita la trazabilidad y la optimización continua del proceso. La información recolectada puede ser analizada para identificar tendencias, prever fallos y realizar ajustes preventivos, logrando un equilibrio entre productividad, calidad y sostenibilidad, y reduciendo el desperdicio de materia prima y energía.
Por otro lado, estas prensas automáticas son extremadamente versátiles y permiten adaptar la presión y velocidad de llenado según el tipo de tripa utilizada, ya sea natural, colágeno o sintética, así como el tipo de mezcla: carne fresca con alto contenido de agua, emulsiones cocidas densas o productos curados con menor humedad. Esta capacidad de ajuste dinámico es clave para mantener la uniformidad de los embutidos, evitando roturas de tripa, vacíos internos o deformaciones externas, lo que garantiza un producto final de alta calidad que cumpla con los estándares de los mercados locales e internacionales.
En síntesis, la prensa de estampado de embutidos ha evolucionado desde máquinas simples de empuje manual hasta sofisticadas unidades automatizadas que combinan sistemas hidráulicos, neumáticos y servoaccionados con sensores inteligentes, control por software, visión artificial y protocolos de limpieza avanzados. Esta evolución tecnológica ha permitido producir grandes volúmenes de embutidos con uniformidad de forma, peso y textura, optimizando el uso de materia prima, reduciendo el desperdicio, asegurando la higiene y la seguridad alimentaria, y aumentando la eficiencia energética y productiva de las plantas industriales. La prensa ya no es simplemente un instrumento de llenado; es el núcleo de un sistema integrado de manufactura inteligente que combina ingeniería de procesos, automatización y control de calidad en tiempo real, asegurando que cada embutido producido cumpla con los más altos estándares de calidad y presentación.
La prensa de estampado de embutidos en la industria moderna representa el punto de convergencia entre la ingeniería mecánica, la automatización y la gestión de procesos alimentarios, y su evolución tecnológica ha permitido superar los límites de producción tradicionales, garantizando uniformidad, eficiencia y seguridad alimentaria en grandes volúmenes de manufactura. Estas prensas no solo aplican presión para llenar tripas o moldes, sino que integran sistemas de control inteligentes que regulan con precisión cada variable del proceso, desde la fuerza aplicada por pistones o tornillos sin fin hasta la velocidad de llenado y la longitud final de cada embutido. La tecnología moderna incluye sensores de presión, caudal y densidad de la mezcla, que permiten monitorizar el comportamiento del producto en tiempo real, detectando variaciones en la consistencia de la carne o de la emulsión y ajustando automáticamente los parámetros de la máquina para mantener estándares de calidad estrictos, evitando defectos como vacíos, burbujas de aire, desbordes o roturas de tripa.
En la producción industrial, estas prensas se integran en líneas automatizadas completas que incluyen sistemas de molienda, mezclado, enfriado, embutido, atado, cocción y empaquetado, donde cada etapa se sincroniza digitalmente para optimizar tiempos, reducir desperdicios y asegurar consistencia en lotes de decenas de miles de unidades diarias. La automatización avanzada permite memorizar perfiles de operación específicos para cada tipo de embutido, ya sea fresco, cocido o curado, de modo que la máquina ajuste automáticamente la presión, la velocidad y el diámetro de la boquilla, evitando la intervención manual constante y garantizando uniformidad en densidad, peso y textura de cada producto. En paralelo, los sistemas de visión artificial verifican continuamente la integridad de la tripa, la presencia de burbujas o arrugas y el tamaño de cada unidad, enviando señales al sistema de control para corregir desviaciones de manera instantánea.
Los materiales y la construcción de la prensa son igualmente determinantes para su eficiencia y durabilidad. Los componentes en contacto con la mezcla, como pistones, tolvas, boquillas y moldes, se fabrican en acero inoxidable de alta calidad, con acabados pulidos que reducen la fricción, evitan adherencias y facilitan la limpieza. Los sistemas CIP (Clean-in-Place) permiten desinfectar automáticamente la máquina sin necesidad de desmontarla, asegurando que se cumplan estrictos estándares de higiene y reduciendo el riesgo de contaminación cruzada. Esta característica es especialmente relevante en la industria cárnica, donde los productos son altamente perecederos y las regulaciones sanitarias exigen trazabilidad y control absoluto sobre la manipulación de alimentos.
La versatilidad de las prensas modernas se refleja también en su capacidad para trabajar con distintos tipos de tripa y mezclas. Las tripas naturales, sintéticas o de colágeno requieren ajustes precisos de presión y velocidad para evitar roturas, mientras que las mezclas de carne con alto contenido de grasa, agua o aditivos gelificantes presentan distintos comportamientos durante el embutido. Las prensas automáticas adaptan en tiempo real estos parámetros, garantizando que la densidad y textura del producto sean uniformes a lo largo de toda la longitud del embutido, optimizando la eficiencia de producción y reduciendo desperdicio de materia prima. Además, la capacidad de programar perfiles de operación para distintos productos permite a las plantas alternar rápidamente entre líneas de salchichas, chorizos, mortadelas o embutidos especiales sin interrupciones significativas, mejorando la productividad y reduciendo costos operativos.
Desde el punto de vista económico y de competitividad, la implementación de prensas automáticas inteligentes genera beneficios significativos. La reducción del desperdicio, la mejora en la uniformidad y la optimización de la energía consumida por la máquina contribuyen a un menor costo por unidad producida, mientras que el control de calidad en tiempo real asegura que cada producto cumpla con los estándares requeridos por mercados locales e internacionales. Al mismo tiempo, la recopilación y análisis de datos de producción permiten realizar mantenimiento predictivo, anticipar fallos y optimizar los ciclos de trabajo, prolongando la vida útil de los componentes y aumentando la disponibilidad operativa de la línea de producción. La prensa de estampado de embutidos, por tanto, deja de ser simplemente un equipo de llenado para convertirse en un centro de control inteligente que integra ingeniería, automatización, higiene y gestión de procesos, garantizando que la producción industrial de embutidos sea eficiente, segura y de alta calidad, capaz de adaptarse rápidamente a cambios en la demanda, nuevas recetas o diferentes tipos de tripa y mezcla.
Prensa de Embutición Profunda
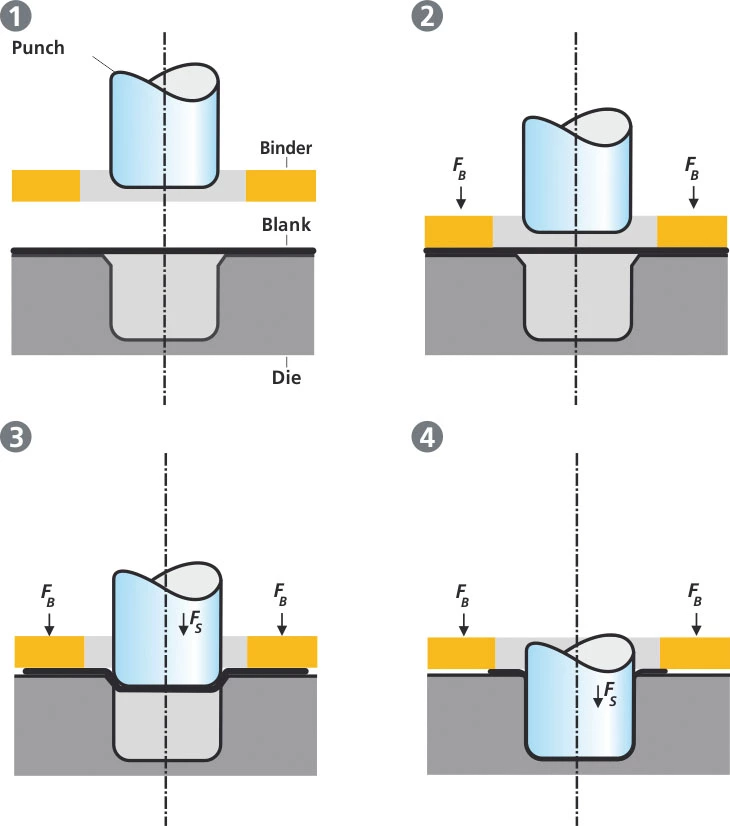
La prensa de embutición profunda es una máquina fundamental en la industria metalúrgica y de manufactura de piezas metálicas, diseñada específicamente para transformar chapas planas en componentes tridimensionales de gran profundidad mediante un proceso controlado de deformación plástica. A diferencia de la embutición superficial o de la estampación simple, la embutición profunda permite obtener piezas con relaciones de altura y diámetro que superan con creces los límites de la chapa inicial, como cilindros, depósitos, carcasas y otros cuerpos huecos con paredes relativamente uniformes. El funcionamiento de la prensa se basa en la interacción precisa entre punzón, matriz y pisador o cojín de sujeción: el punzón impulsa la chapa hacia el interior de la matriz, mientras el cojín controla el flujo del material desde los bordes para evitar arrugas o pliegues. La fuerza aplicada debe ser cuidadosamente calibrada para adaptarse al espesor de la chapa, su ductilidad, el radio de la matriz y la relación de embutición, evitando así fracturas o deformaciones irregulares en la pieza final.
El diseño de la prensa de embutición profunda puede variar según el tipo de accionamiento: mecánico, hidráulico o servo-hidráulico. Las prensas mecánicas, tradicionales y de alta velocidad, convierten el movimiento rotativo en lineal mediante bielas y volantes, permitiendo ciclos rápidos ideales para producción masiva de piezas de geometría sencilla y relaciones de embutición moderadas, aunque ofrecen un control limitado de la fuerza durante la carrera. Las prensas hidráulicas proporcionan fuerzas uniformes a lo largo de todo el recorrido del punzón, lo que resulta indispensable para embuticiones complejas y materiales más resistentes, aunque su velocidad de ciclo es menor y requieren mantenimiento regular de bombas, válvulas y circuitos hidráulicos. Las servo-prensas representan la tecnología más avanzada, combinando velocidad, control de fuerza y precisión, permitiendo programar perfiles de movimiento que ajustan la velocidad y presión durante todo el ciclo de embutición, lo que es esencial en la fabricación de piezas críticas para automoción, electrodomésticos y aplicaciones industriales de alta precisión.
Un aspecto crítico en la embutición profunda es la relación entre el diámetro inicial de la chapa y el diámetro final de la pieza, ya que exceder los límites de ductilidad del material puede provocar fisuras o arrugas. Cuando la relación de embutición es elevada, es necesario realizar redibujos sucesivos: la pieza se somete a nuevas etapas de embutición progresiva hasta alcanzar las dimensiones finales sin comprometer la integridad del material. Esto es frecuente en la producción de latas, depósitos de líquidos, componentes estructurales y utensilios de cocina metálicos. El radio de la matriz y del punzón, así como la fricción entre la chapa y las superficies de la herramienta, también influyen directamente en el flujo del material; radios demasiado pequeños concentran tensiones y generan fisuras, mientras que la fricción excesiva aumenta la fuerza requerida y puede producir arrugas. Por ello, se utilizan lubricantes especiales que reducen la fricción, protegen las superficies de las herramientas y facilitan un flujo uniforme de la chapa.
La prensa de embutición profunda moderna incorpora sistemas de monitoreo en tiempo real, sensores de fuerza, desplazamiento y temperatura, así como software de simulación que permite anticipar el comportamiento de la chapa antes de iniciar la producción. Esto optimiza el diseño de punzones y matrices, minimiza pruebas físicas costosas y reduce el riesgo de defectos en las piezas finales. Además, la trazabilidad de cada ciclo permite analizar el desempeño de la máquina, predecir mantenimiento y ajustar parámetros de manera preventiva. La integración de estos sistemas convierte a la prensa en un equipo inteligente, capaz de producir millones de piezas con tolerancias mínimas, acabados uniformes y aprovechamiento máximo de la materia prima.
En términos industriales, la prensa de embutición profunda es utilizada en sectores como automoción, aeronáutica, electrodomésticos, menaje y envases metálicos, donde se requiere fabricar piezas de geometría compleja y alta precisión. Su capacidad para realizar embuticiones profundas sin comprometer la resistencia estructural del material permite la producción de depósitos de combustible, carcasas, tanques a presión, fregaderos y componentes de acero o aluminio con espesores uniformes. La versatilidad de estas prensas, junto con los avances tecnológicos en control de fuerza, velocidad y flujo de material, hace posible adaptarlas a diferentes materiales y espesores, optimizando la eficiencia y reduciendo el desperdicio.
La prensa de embutición profunda, siendo un pilar fundamental en la manufactura de piezas metálicas de gran complejidad, opera bajo una serie de parámetros críticos que determinan la calidad, precisión y eficiencia del producto final. Uno de los factores más importantes es la velocidad de embutición, que debe ajustarse de manera que el flujo del material sea uniforme desde el borde de la chapa hacia el interior del troquel; velocidades excesivas pueden generar arrugas, fisuras o tensiones residuales que comprometen la integridad de la pieza, mientras que velocidades demasiado bajas reducen la productividad sin ofrecer mejoras significativas en la calidad. Paralelamente, la presión aplicada por el punzón y el cojín debe ser cuidadosamente calibrada en función del espesor de la chapa, la ductilidad del material y la profundidad de embutición, de manera que se garantice un flujo controlado y uniforme del metal. La combinación de velocidad y presión define no solo la forma final de la pieza, sino también la uniformidad del espesor de las paredes y la ausencia de defectos superficiales, factores esenciales en componentes que deben soportar cargas o presiones internas.
El redibujo progresivo constituye otro elemento crítico en la operación de la prensa de embutición profunda. Cuando la relación de embutición —la proporción entre el diámetro inicial de la chapa y el diámetro final de la pieza— excede los límites de ductilidad del material, es necesario realizar múltiples etapas de embutición sucesivas, conocidas como redibujos. Cada redibujo reduce gradualmente el diámetro y aumenta la altura de la pieza, distribuyendo las tensiones de manera controlada y evitando fisuras o arrugas. Este procedimiento es especialmente relevante en la fabricación de latas de bebidas, envases de alimentos, depósitos de líquidos, componentes automotrices y utensilios de cocina, donde la uniformidad del espesor y la integridad estructural son esenciales. Cada redibujo requiere ajustes específicos en la presión, el radio de la matriz y la lubricación, de manera que el flujo del metal se mantenga constante y el producto final cumpla con las tolerancias dimensionales requeridas.
La lubricación es otro aspecto determinante en el desempeño de la prensa. Un coeficiente de fricción adecuado entre la chapa y las superficies del punzón y la matriz facilita el flujo del material, protege la herramienta del desgaste prematuro y asegura un acabado superficial óptimo. Se emplean lubricantes sólidos, emulsiones o pastas especiales según el tipo de metal, su espesor y la complejidad de la pieza, y su aplicación puede ser uniforme o localizada en zonas críticas de deformación. La correcta elección y aplicación del lubricante no solo mejora la calidad del producto, sino que también reduce la fuerza requerida por la prensa y prolonga la vida útil de las herramientas, resultando en un proceso más eficiente y económico.
La selección del material de la chapa es igualmente esencial, ya que la ductilidad, resistencia, espesor y homogeneidad del metal determinan la viabilidad del proceso de embutición profunda. Aceros al carbono de bajo contenido, aceros inoxidables, aluminio, cobre y aleaciones ligeras son los materiales más utilizados, elegidos en función de su capacidad de deformación sin fractura y de las propiedades mecánicas requeridas para la aplicación final. La calidad del material influye directamente en el número de redibujos necesarios, la presión aplicada y el tipo de lubricación a utilizar, así como en la durabilidad de los punzones y matrices.
El control moderno de la prensa de embutición profunda ha incorporado sistemas electrónicos, sensores de fuerza, desplazamiento y temperatura, y software de simulación que permiten prever el comportamiento del material antes de iniciar la producción. Esta integración tecnológica facilita la optimización de parámetros, la reducción de pruebas físicas costosas y la anticipación de defectos, garantizando piezas con tolerancias mínimas y acabados uniformes. En paralelo, los sistemas de monitoreo en tiempo real registran cada ciclo de embutición, permitiendo análisis predictivos de mantenimiento, ajuste automático de fuerzas y velocidad, y trazabilidad completa del proceso, lo que resulta especialmente valioso en la producción industrial de componentes críticos.
En términos de aplicaciones, la prensa de embutición profunda es esencial en sectores como la automoción, aeronáutica, electrodomésticos, menaje y envases metálicos, donde la fabricación de piezas huecas de gran profundidad con paredes uniformes y acabados precisos es imprescindible. Componentes como depósitos de combustible, carcasas estructurales, tanques a presión, fregaderos, utensilios de cocina y latas metálicas son ejemplos típicos que requieren un control preciso de los parámetros de embutición, la aplicación correcta de lubricantes, la selección adecuada de materiales y, en muchos casos, la utilización de redibujos progresivos para alcanzar las dimensiones finales sin comprometer la integridad del material. La combinación de ingeniería de herramientas, automatización, control electrónico y selección de materiales convierte a la prensa de embutición profunda en un equipo versátil y altamente eficiente, capaz de producir piezas complejas en grandes volúmenes con calidad, uniformidad y optimización de recursos.
La prensa de embutición profunda ha alcanzado en la actualidad un nivel de sofisticación que va mucho más allá de la simple aplicación de fuerza sobre una chapa metálica, convirtiéndose en un sistema integral donde la precisión mecánica, la automatización, la instrumentación de control y el análisis de datos se combinan para garantizar la producción de piezas complejas con los más altos estándares de calidad. En esta maquinaria, cada ciclo de embutición se gestiona mediante parámetros cuidadosamente calibrados, incluyendo la fuerza aplicada por el punzón, la presión ejercida por el cojín, la velocidad de descenso, el radio de la matriz y el flujo del material, todos ajustables en función de la geometría, el espesor y las propiedades del metal empleado. El control de estas variables es crítico: una presión demasiado baja puede generar arrugas o pliegues en las paredes de la pieza, mientras que una presión excesiva puede provocar fisuras, estiramientos localizados o incluso el fallo de la herramienta. Del mismo modo, la velocidad de embutición debe adaptarse para permitir que el metal fluya uniformemente, evitando tensiones residuales y garantizando una superficie uniforme y sin defectos.
La incorporación de sensores de fuerza, desplazamiento y temperatura permite un monitoreo continuo del proceso, de manera que cualquier desviación de los parámetros predeterminados activa ajustes automáticos que corrigen el comportamiento del material en tiempo real. Esto es especialmente importante en la producción de componentes críticos en sectores como la automoción, aeronáutica y electrodomésticos, donde las piezas embutidas profundas deben cumplir tolerancias estrictas, soportar cargas dinámicas y mantener uniformidad en espesor y acabado superficial. Además, el software de simulación por elementos finitos permite predecir cómo se comportará la chapa durante la embutición, optimizando previamente el diseño de punzones y matrices, anticipando posibles zonas de concentración de tensiones y determinando la necesidad de redibujos sucesivos, todo ello antes de realizar la producción física. Esta combinación de simulación y control inteligente reduce significativamente el número de pruebas físicas, acorta los tiempos de desarrollo y minimiza el desperdicio de materia prima, incrementando la eficiencia global del proceso.
El redibujo progresivo es otro aspecto fundamental en la embutición profunda, especialmente cuando se requieren relaciones de altura a diámetro muy elevadas que exceden la ductilidad natural del material. Mediante varias etapas de embutición sucesivas, cada una con parámetros de presión, velocidad y radio de matriz específicos, se logra una distribución controlada de tensiones en el material, evitando fisuras, arrugas o deformaciones irregulares. Este procedimiento es habitual en la fabricación de envases metálicos, depósitos de líquidos, carcasas de electrodomésticos y componentes estructurales automotrices, donde la uniformidad del espesor y la integridad mecánica son determinantes. La correcta aplicación de lubricantes también es crucial, ya que reduce la fricción entre la chapa y las superficies de la herramienta, protege los punzones y matrices del desgaste prematuro y facilita un flujo de material más uniforme, garantizando un acabado superficial óptimo y la vida útil prolongada de la maquinaria.
Las prensas modernas de embutición profunda pueden ser mecánicas, hidráulicas o servo-hidráulicas, cada una con ventajas específicas según el tipo de producción. Las mecánicas ofrecen ciclos rápidos ideales para producciones masivas de piezas de geometría relativamente sencilla, aunque con un control limitado de la fuerza durante la carrera. Las hidráulicas permiten aplicar una presión constante a lo largo de todo el recorrido, esenciales para materiales más duros o piezas de geometría compleja, aunque con ciclos más lentos y requerimientos de mantenimiento mayores. Las servo-prensas combinan lo mejor de ambos mundos: velocidad, precisión y control total del perfil de fuerza y movimiento, adaptándose a cada fase de la embutición y permitiendo optimizar la calidad y la eficiencia energética simultáneamente. Además, su integración con sistemas de control digital permite almacenar configuraciones específicas para distintos materiales, espesores y geometrías, facilitando cambios rápidos de producción sin comprometer la uniformidad del producto.
La trazabilidad y la recopilación de datos en tiempo real constituyen otra ventaja estratégica de las prensas modernas. Cada ciclo de embutición puede registrar información sobre fuerza aplicada, velocidad, temperatura y comportamiento del material, permitiendo análisis posteriores que optimizan la operación, planifican el mantenimiento preventivo y aseguran la reproducibilidad de las piezas en grandes lotes de producción. Esta información es crítica en sectores donde la calidad del producto es regulada estrictamente, como la automoción y la aeronáutica, y también permite garantizar estándares sanitarios y de seguridad en la manipulación de materiales sensibles. La integración de sensores de visión y sistemas de inspección automatizados asegura la detección de defectos superficiales, arrugas, burbujas o variaciones dimensionales, lo que completa un ciclo de control total sobre el proceso de embutición profunda, desde la chapa inicial hasta la pieza final lista para su ensamblaje o venta.
En términos de aplicaciones industriales, la prensa de embutición profunda es indispensable para la fabricación de componentes huecos con paredes uniformes, incluyendo depósitos de combustible, tanques de presión, carcasas de electrodomésticos, utensilios de cocina metálicos, latas de alimentos y bebidas, y piezas estructurales de vehículos. Su capacidad para adaptarse a diferentes materiales —aceros, aceros inoxidables, aluminio, cobre y aleaciones ligeras—, espesores y complejidades geométricas, junto con el control preciso de fuerza, velocidad, lubricación y redibujo progresivo, asegura la producción de piezas consistentes, duraderas y de alta calidad, mientras se optimizan recursos, se minimiza el desperdicio y se incrementa la eficiencia de la planta industrial. La prensa de embutición profunda, por tanto, se ha convertido en un equipo estratégico, donde convergen ingeniería mecánica, control automatizado, análisis de materiales y gestión de procesos para garantizar la excelencia en la manufactura de piezas metálicas complejas.
La prensa de embutición profunda ha evolucionado hasta convertirse en un elemento central dentro de la manufactura industrial de piezas metálicas complejas, integrando no solo la mecánica y la fuerza aplicada sobre la chapa, sino también sofisticados sistemas de automatización, control de procesos y análisis de datos en tiempo real que permiten garantizar la calidad, uniformidad y eficiencia de cada pieza producida. En el funcionamiento de estas prensas, cada parámetro, desde la presión aplicada por el punzón hasta la velocidad de desplazamiento y el comportamiento del cojín de sujeción, debe ser cuidadosamente calibrado según el material, el espesor de la chapa, la geometría de la pieza y la relación de embutición requerida. La precisión en estos ajustes es determinante: si la presión es insuficiente, la chapa puede arrugarse o deformarse de manera irregular, mientras que una presión excesiva puede generar fisuras o concentraciones de tensión que comprometan la integridad de la pieza. Del mismo modo, la velocidad de embutición afecta directamente al flujo del material; velocidades demasiado rápidas incrementan el riesgo de arrugas o fracturas, mientras que velocidades demasiado bajas afectan la productividad sin mejorar la calidad de manera significativa.
El control moderno de estas prensas incorpora sensores de fuerza, desplazamiento, temperatura y fricción, conectados a sistemas de supervisión que permiten ajustar en tiempo real los parámetros de operación para corregir cualquier desviación de los estándares establecidos. Esto es crucial en la producción de piezas críticas en sectores como automoción, aeronáutica, electrodomésticos y envases metálicos, donde la uniformidad de espesor, la resistencia estructural y la precisión dimensional son esenciales. Adicionalmente, el software de simulación por elementos finitos se utiliza para prever el comportamiento de la chapa antes de la producción física, permitiendo optimizar el diseño de punzones y matrices, anticipar zonas de concentración de tensiones y definir la necesidad de redibujos sucesivos, reduciendo considerablemente las pruebas físicas y el desperdicio de materia prima.
El redibujo progresivo es un proceso clave cuando la relación de embutición excede los límites de ductilidad del material, ya que permite alcanzar alturas y formas complejas mediante varias etapas de embutición sucesivas. Cada redibujo requiere ajustes específicos de presión, velocidad, radio de matriz y lubricación, asegurando un flujo uniforme del material, evitando arrugas, pliegues o fisuras y garantizando uniformidad en el espesor de las paredes de la pieza. Este procedimiento es fundamental en la fabricación de latas, depósitos de líquidos, carcasas de electrodomésticos, tanques de presión y utensilios de cocina, donde la integridad estructural y la presentación estética son determinantes. La lubricación adecuada entre la chapa y las superficies de punzón y matriz es esencial para reducir la fricción, proteger las herramientas y garantizar un flujo de material uniforme, prolongando la vida útil de la maquinaria y mejorando la calidad superficial de las piezas.
Las prensas de embutición profunda modernas pueden ser mecánicas, hidráulicas o servo-hidráulicas, cada una adaptándose a necesidades específicas de producción. Las mecánicas ofrecen ciclos rápidos y son ideales para piezas de geometría relativamente simple, aunque su control de fuerza es limitado. Las hidráulicas permiten aplicar una presión constante durante todo el recorrido, indispensables para piezas de geometría compleja o materiales resistentes, aunque su velocidad de ciclo es menor y requieren un mantenimiento más frecuente. Las servo-prensas combinan velocidad, precisión y control total del perfil de fuerza y movimiento, permitiendo ajustar cada fase de la embutición de manera óptima y almacenar configuraciones para diferentes materiales, espesores y geometrías, facilitando cambios rápidos de producción sin comprometer la uniformidad ni la calidad de las piezas.
La recopilación de datos y la trazabilidad en tiempo real se han convertido en elementos estratégicos dentro de la producción industrial con prensas de embutición profunda. Cada ciclo de operación registra información sobre fuerza, velocidad, temperatura y desplazamiento, lo que permite un análisis detallado de desempeño, optimización de parámetros, mantenimiento predictivo y control de calidad integral. Los sistemas de visión artificial complementan este control, detectando arrugas, deformaciones, burbujas de aire y variaciones dimensionales, y ajustando automáticamente los parámetros de la prensa para garantizar que cada pieza cumpla con los estándares de precisión y acabado requeridos por industrias de alta exigencia.
En aplicaciones industriales, estas prensas son indispensables para la fabricación de componentes huecos y de geometría compleja, incluyendo depósitos de combustible, tanques de presión, carcasas de electrodomésticos, utensilios de cocina metálicos, envases de alimentos y bebidas, así como componentes estructurales automotrices y aeronáuticos. La capacidad de adaptarse a distintos materiales, espesores y complejidades geométricas, combinada con el control preciso de presión, velocidad, lubricación y redibujo progresivo, garantiza la producción de piezas consistentes, duraderas y de alta calidad, optimizando recursos y reduciendo el desperdicio. La prensa de embutición profunda moderna, por tanto, se ha convertido en un sistema integral donde convergen ingeniería mecánica, automatización, control de procesos y análisis de materiales, asegurando que cada pieza cumpla con los estándares más exigentes de precisión, resistencia y acabado superficial, y permitiendo a la industria manufacturera mantener eficiencia, productividad y competitividad en mercados altamente exigentes.
Si quieres, puedo continuar desarrollando un texto todavía más detallado sobre la integración de prensas de embutición profunda con automatización completa de plantas, monitoreo predictivo, mantenimiento inteligente y control de calidad avanzado para piezas de alta exigencia, explicando paso a paso cómo cada parámetro afecta la producción y la durabilidad de las piezas.
Equipo de Embutición Metálica
El equipo de embutición metálica constituye un conjunto de máquinas y dispositivos especialmente diseñados para transformar chapas planas en piezas tridimensionales de alta precisión mediante deformación plástica controlada, permitiendo la fabricación de componentes huecos o de geometrías complejas que serían imposibles de obtener por otros métodos de conformado. Este equipo no se limita a una sola máquina, sino que incluye prensas de embutición profunda, matrices, punzones, cojines de sujeción, sistemas de lubricación, controles automáticos y, en plantas industriales modernas, dispositivos de monitoreo en tiempo real que aseguran uniformidad, calidad y repetibilidad en la producción. Cada componente del equipo cumple un rol crítico: las prensas aplican la fuerza necesaria para inducir el flujo del metal hacia la forma deseada, las matrices determinan la geometría final y los punzones controlan la dirección y profundidad del material, mientras que los cojines o sistemas de presión regulan la tensión en los bordes de la chapa para evitar arrugas o pliegues.
El equipo de embutición metálica puede operar mediante accionamientos mecánicos, hidráulicos o servo-hidráulicos, dependiendo de la complejidad de las piezas y del volumen de producción requerido. Las prensas mecánicas son adecuadas para producciones rápidas de piezas simples, mientras que las hidráulicas ofrecen un control de fuerza constante durante todo el ciclo, esencial para materiales más resistentes o piezas de geometría compleja. Las servo-prensas, por su parte, permiten programar perfiles de movimiento que ajustan en tiempo real la velocidad, fuerza y trayectoria del punzón, optimizando la calidad de cada pieza y reduciendo el desgaste de las herramientas. La combinación de estos sistemas con matrices intercambiables y punzones diseñados específicamente para cada aplicación garantiza la flexibilidad del equipo, permitiendo la fabricación de una amplia variedad de productos desde latas y depósitos hasta carcasas de electrodomésticos y componentes automotrices.
La lubricación es un aspecto esencial dentro del equipo de embutición metálica, ya que reduce la fricción entre la chapa y las superficies de las herramientas, facilita el flujo uniforme del material y prolonga la vida útil de punzones y matrices. Se utilizan lubricantes sólidos, pastas o emulsiones, aplicados de manera localizada o en toda la superficie de contacto según el tipo de material, el espesor de la chapa y la complejidad de la pieza. La correcta elección y aplicación del lubricante contribuye a prevenir defectos como arrugas, pliegues, fisuras o deformaciones irregulares, asegurando piezas con acabados superficiales óptimos y uniformes.
El redibujo progresivo es otra función crítica dentro del equipo de embutición metálica, especialmente cuando se producen piezas con relaciones de altura y diámetro elevadas que exceden la ductilidad natural del material. En estos casos, la pieza se somete a múltiples etapas de embutición sucesivas, cada una con ajustes específicos de presión, velocidad, radio de matriz y lubricación, garantizando un flujo uniforme del metal y evitando daños en la chapa. Esta técnica permite fabricar envases metálicos, tanques, carcasas, depósitos y otros componentes que requieren alta precisión, paredes uniformes y resistencia estructural, cumpliendo con los estándares industriales más exigentes.
En las plantas industriales modernas, el equipo de embutición metálica se integra en líneas de producción automatizadas, donde cada máquina está conectada a sistemas de control centralizados que permiten monitorear fuerza, velocidad, desplazamiento y temperatura en tiempo real. Los sistemas de visión artificial y sensores complementan este control, detectando deformaciones, arrugas o irregularidades y ajustando automáticamente los parámetros de operación para garantizar uniformidad y calidad. Esta integración digital permite la trazabilidad completa de cada pieza producida, optimiza la eficiencia energética, reduce desperdicios y facilita el mantenimiento predictivo, prolongando la vida útil de los componentes del equipo y asegurando la producción continua sin interrupciones.
El equipo de embutición metálica es indispensable en sectores como automoción, aeronáutica, electrodomésticos, menaje, envases metálicos y utensilios de cocina, donde se requieren piezas huecas de geometría compleja, con paredes uniformes y acabados precisos. Su capacidad para trabajar con distintos materiales —acero, acero inoxidable, aluminio, cobre y aleaciones ligeras—, espesores variados y formas complejas, junto con el control preciso de presión, velocidad, lubricación y redibujo progresivo, asegura la fabricación de productos de alta calidad, consistentes y duraderos, optimizando recursos, reduciendo desperdicio y aumentando la eficiencia de producción.
El equipo de embutición metálica en la industria moderna ha alcanzado un nivel de sofisticación que permite combinar fuerza mecánica, control hidráulico o servo-hidráulico, automatización avanzada y análisis de datos en tiempo real, constituyendo un sistema integral que asegura la producción de piezas metálicas de alta precisión, consistencia y calidad en grandes volúmenes. Cada componente del equipo cumple un papel crítico: las prensas generan la fuerza necesaria para inducir el flujo plástico del material, las matrices y punzones definen la geometría final y controlan la profundidad y dirección del embutido, mientras que los cojines de sujeción regulan la presión en los bordes de la chapa para evitar arrugas, pliegues o fisuras. La precisión en el ajuste de estos parámetros determina no solo la calidad superficial y dimensional de la pieza, sino también la integridad estructural, especialmente en componentes que deben soportar cargas, presiones internas o esfuerzos mecánicos elevados, como depósitos, tanques de presión, carcasas de automoción o piezas de electrodomésticos.
La automatización integrada en los equipos de embutición metálica permite monitorizar en tiempo real variables como la fuerza aplicada, el desplazamiento del punzón, la velocidad de embutición, la temperatura del material y la fricción entre la chapa y las superficies de la herramienta. Estos datos son procesados por sistemas de control que ajustan automáticamente la presión, la velocidad y el flujo de material para mantener uniformidad y prevenir defectos. En plantas de producción masiva, esta capacidad de ajuste en tiempo real es fundamental, ya que permite alternar entre distintos tipos de piezas, espesores y materiales sin comprometer la calidad, garantizando que cada lote cumpla con los estándares industriales y de seguridad más exigentes. El software de simulación por elementos finitos complementa este control, prediciendo el comportamiento de la chapa antes de iniciar la producción, optimizando el diseño de punzones y matrices, identificando zonas de concentración de tensiones y determinando la necesidad de redibujos progresivos para alcanzar la geometría final sin defectos.
El redibujo progresivo es una técnica esencial en la embutición metálica cuando se producen piezas con relaciones altura-diámetro elevadas, que exceden la ductilidad natural del material. La pieza se somete a múltiples etapas de embutición, cada una ajustando parámetros específicos de fuerza, velocidad, radio de matriz y lubricación para permitir un flujo controlado del metal y mantener la uniformidad del espesor de las paredes. Esta técnica es particularmente utilizada en la fabricación de envases metálicos, tanques, carcasas de electrodomésticos, depósitos industriales y utensilios de cocina, donde la precisión dimensional y la integridad estructural son determinantes para el rendimiento y la seguridad del producto final. La correcta aplicación de lubricantes —ya sean sólidos, pastas o emulsiones— reduce la fricción, protege las superficies de punzones y matrices y facilita un flujo uniforme del material, garantizando un acabado superficial homogéneo y prolongando la vida útil de las herramientas.
Las prensas que forman parte del equipo de embutición metálica pueden ser mecánicas, hidráulicas o servo-hidráulicas. Las prensas mecánicas son ideales para ciclos rápidos y producción de piezas simples, aunque el control de fuerza es limitado durante el recorrido. Las hidráulicas aplican una presión constante y uniforme, esenciales para materiales más duros o piezas de geometría compleja, aunque presentan ciclos más lentos y requieren un mantenimiento regular de sus componentes. Las servo-prensas permiten un control total del perfil de fuerza, velocidad y trayectoria del punzón, ofreciendo máxima precisión y flexibilidad, además de la posibilidad de almacenar configuraciones específicas para distintos materiales, espesores y geometrías, lo que facilita cambios de producción sin afectar la uniformidad ni la calidad de las piezas.
La integración de sensores de visión artificial y monitoreo en tiempo real permite al equipo de embutición metálica detectar deformaciones, arrugas, burbujas o irregularidades dimensionales, ajustando automáticamente los parámetros de operación para garantizar piezas uniformes y de alta calidad. Esta trazabilidad completa es especialmente relevante en industrias con altos estándares de control, como la automotriz, aeronáutica, electrodomésticos y envases metálicos, donde cada pieza debe cumplir con tolerancias estrictas y resistir esfuerzos mecánicos, cargas o presiones internas. El registro de datos también permite mantenimiento predictivo, optimización de ciclos y reducción de desperdicio de material, mejorando la eficiencia energética y la rentabilidad de la planta industrial.
El equipo de embutición metálica, por tanto, no solo facilita la transformación de chapas planas en componentes tridimensionales de alta complejidad, sino que también integra ingeniería mecánica, automatización, control de procesos, simulación de flujo de material, lubricación controlada, redibujo progresivo y sistemas de inspección avanzada, garantizando la producción continua de piezas precisas, duraderas y consistentes. Su versatilidad permite trabajar con distintos materiales, como acero, acero inoxidable, aluminio, cobre y aleaciones ligeras, adaptándose a diferentes espesores, formas y aplicaciones, desde utensilios de cocina y envases hasta depósitos de líquidos y componentes estructurales de alta exigencia. La combinación de estas tecnologías convierte al equipo de embutición metálica en un sistema integral, capaz de optimizar recursos, reducir desperdicio, incrementar productividad y mantener altos estándares de calidad en la manufactura industrial.
El equipo de embutición metálica ha alcanzado un nivel de integración tecnológica que lo convierte en un sistema completo capaz de gestionar todo el proceso de conformado de piezas metálicas complejas, desde la alimentación de la chapa hasta la obtención de componentes terminados con tolerancias mínimas y acabados uniformes. En este tipo de equipos, cada elemento —prensas, punzones, matrices, cojines de sujeción, sistemas de lubricación y controles electrónicos— está diseñado para trabajar de manera sincronizada, asegurando que el flujo del material sea uniforme y que la deformación plástica se distribuya de manera homogénea en toda la pieza, evitando defectos como arrugas, fisuras, estiramientos localizados o cambios indeseados en el espesor de las paredes. La fuerza aplicada por el punzón y la presión del cojín deben ajustarse cuidadosamente según las propiedades del material, su espesor y la geometría de la pieza, mientras que la velocidad de embutición se regula para permitir un flujo controlado del metal, asegurando que las piezas resulten resistentes y precisas, incluso cuando se trata de geometrías con relaciones de altura y diámetro elevadas.
La automatización avanzada es un componente central del equipo de embutición metálica moderno, permitiendo el control en tiempo real de variables críticas como la fuerza, el desplazamiento, la velocidad, la temperatura y la fricción. Los sensores instalados en punzones, matrices y cojines recopilan datos continuos que son procesados por sistemas de control digital, ajustando automáticamente la presión y la velocidad durante todo el ciclo de embutición. Esto no solo mejora la calidad y uniformidad de las piezas, sino que también permite alternar rápidamente entre diferentes tipos de productos, espesores y materiales sin comprometer la precisión ni la integridad de las piezas. La simulación por elementos finitos se emplea para predecir el comportamiento del material antes de la producción, optimizando el diseño de punzones y matrices, identificando zonas de concentración de tensiones y determinando la necesidad de redibujos progresivos, lo que reduce considerablemente los ensayos físicos y el desperdicio de materia prima.
El redibujo progresivo es una técnica esencial en este tipo de equipos, especialmente cuando se requiere producir piezas con relaciones altura-diámetro elevadas que exceden la ductilidad natural del material. Cada redibujo implica una etapa adicional de embutición con ajustes específicos de fuerza, velocidad, radio de matriz y lubricación, garantizando un flujo uniforme del metal y evitando defectos. Esta técnica es fundamental en la fabricación de envases metálicos, depósitos industriales, carcasas de electrodomésticos, tanques de presión y utensilios de cocina, donde la precisión dimensional, la uniformidad de espesor y la integridad estructural son determinantes. La correcta aplicación de lubricantes, ya sean sólidos, pastas o emulsiones, reduce la fricción, protege los punzones y matrices y facilita un flujo uniforme del material, asegurando acabados superficiales homogéneos y prolongando la vida útil del equipo.
El equipo de embutición metálica puede estar compuesto por prensas mecánicas, hidráulicas o servo-hidráulicas, cada una adaptándose a necesidades específicas de producción. Las prensas mecánicas permiten ciclos rápidos y son ideales para piezas de geometría simple, aunque con control limitado de la fuerza durante el recorrido. Las prensas hidráulicas ofrecen una presión constante y uniforme, esenciales para piezas complejas o materiales más resistentes, aunque presentan ciclos más lentos y requieren mantenimiento regular. Las servo-prensas permiten ajustar con precisión cada fase del embutido, controlando fuerza, velocidad y trayectoria del punzón, almacenando perfiles específicos para diferentes materiales, espesores y geometrías, lo que facilita cambios de producción rápidos sin afectar la uniformidad ni la calidad de las piezas. La combinación de estas tecnologías convierte al equipo de embutición metálica en un sistema altamente flexible, capaz de producir grandes volúmenes de piezas complejas con estándares de precisión industrial.
La integración de sistemas de visión artificial y monitoreo en tiempo real permite al equipo detectar cualquier desviación dimensional, arruga, pliegue, burbuja o irregularidad superficial, ajustando automáticamente los parámetros de operación para garantizar piezas uniformes y de alta calidad. Esta trazabilidad completa es crucial en industrias de alta exigencia como automoción, aeronáutica, electrodomésticos y envases metálicos, donde cada pieza debe cumplir con tolerancias estrictas, soportar esfuerzos mecánicos y mantener resistencia estructural. La recopilación de datos también facilita el mantenimiento predictivo, optimiza los ciclos de producción, reduce el desperdicio de material y mejora la eficiencia energética de la planta, asegurando continuidad de producción y prolongando la vida útil de los componentes del equipo.
En su conjunto, el equipo de embutición metálica combina ingeniería mecánica, control de procesos, automatización, simulación de flujo de material, redibujo progresivo, lubricación controlada y sistemas de inspección avanzada, garantizando la producción de piezas tridimensionales de geometría compleja, paredes uniformes y acabados precisos. Su versatilidad permite trabajar con distintos materiales como acero, acero inoxidable, aluminio, cobre y aleaciones ligeras, adaptándose a diferentes espesores y formas según la aplicación industrial, desde utensilios de cocina y envases metálicos hasta depósitos de líquidos y componentes estructurales de alta exigencia. La combinación de estas tecnologías convierte al equipo de embutición metálica en un sistema integral capaz de optimizar recursos, reducir desperdicio, aumentar la productividad y mantener estándares de calidad elevados en la fabricación industrial.
El equipo de embutición metálica moderno ha evolucionado hasta convertirse en un sistema totalmente integrado en el que confluyen la ingeniería mecánica, la hidráulica, la automatización avanzada y el análisis de datos en tiempo real, permitiendo que la transformación de chapas planas en piezas tridimensionales complejas se realice con una precisión y uniformidad sin precedentes. Cada componente de este equipo, desde la prensa hasta los punzones, matrices, cojines de sujeción, sistemas de lubricación y controles electrónicos, está diseñado para trabajar de manera coordinada, asegurando que el flujo del material sea constante y homogéneo y que la deformación plástica se distribuya uniformemente en toda la pieza, evitando arrugas, pliegues, fisuras o cambios no deseados en el espesor de las paredes. La fuerza aplicada por el punzón, combinada con la presión del cojín y la velocidad de embutición, debe ajustarse con precisión en función de las propiedades mecánicas del material, su espesor, la geometría de la pieza y la relación de embutición, de modo que se garantice la integridad estructural, la uniformidad dimensional y la calidad superficial del componente, incluso cuando se trata de geometrías de alta complejidad o relaciones altura-diámetro elevadas.
El control automatizado de estas prensas permite monitorear y ajustar en tiempo real parámetros como la fuerza, el desplazamiento del punzón, la velocidad de embutición, la fricción y la temperatura del material. Sensores estratégicamente ubicados recopilan información continua, que es procesada por sistemas de control digital capaces de modificar instantáneamente la presión y la velocidad para mantener la uniformidad del flujo del metal y prevenir defectos. Esta capacidad de ajuste dinámico resulta crucial en la producción de piezas críticas para sectores como la automoción, la aeronáutica, los electrodomésticos y los envases metálicos, donde cada pieza debe cumplir con tolerancias estrictas, soportar esfuerzos mecánicos y mantener uniformidad de espesor y acabado superficial. Además, el uso de simulación por elementos finitos permite anticipar el comportamiento de la chapa antes de iniciar la producción, optimizando el diseño de punzones y matrices, identificando zonas de concentración de tensiones y determinando la necesidad de redibujos progresivos para alcanzar la geometría final sin defectos, reduciendo así pruebas físicas costosas y desperdicio de materia prima.
El redibujo progresivo es una técnica esencial en la embutición metálica cuando se requiere producir piezas con relaciones altura-diámetro elevadas que exceden la ductilidad natural del material. Cada etapa de redibujo aplica ajustes específicos de fuerza, velocidad, radio de matriz y lubricación para controlar el flujo del metal y garantizar uniformidad en el espesor de las paredes, evitando arrugas, pliegues o fisuras. Esta técnica es clave en la fabricación de envases metálicos, depósitos industriales, carcasas de electrodomésticos, tanques de presión y utensilios de cocina, donde la precisión dimensional, la uniformidad de espesor y la integridad estructural son determinantes. La lubricación, empleando pastas, emulsiones o lubricantes sólidos, reduce la fricción, protege las herramientas y facilita un flujo homogéneo del material, asegurando acabados superficiales de alta calidad y prolongando la vida útil de los componentes del equipo.
El equipo puede estar compuesto por prensas mecánicas, hidráulicas o servo-hidráulicas, adaptadas según las necesidades de producción. Las prensas mecánicas permiten ciclos rápidos y son adecuadas para piezas simples, aunque ofrecen control limitado de fuerza durante el recorrido. Las hidráulicas proporcionan presión constante y uniforme, necesarias para materiales más duros o piezas complejas, aunque con ciclos más lentos y mantenimiento más frecuente. Las servo-prensas permiten un control total del perfil de fuerza, velocidad y trayectoria del punzón, almacenando configuraciones específicas para distintos materiales y geometrías, lo que facilita cambios de producción rápidos sin afectar la calidad ni la uniformidad de las piezas. La combinación de estas tecnologías convierte al equipo de embutición metálica en un sistema flexible y eficiente, capaz de producir grandes volúmenes de piezas complejas con altos estándares de precisión industrial.
Los sistemas de visión artificial y monitoreo en tiempo real permiten detectar cualquier irregularidad en la pieza, como arrugas, pliegues, burbujas o desviaciones dimensionales, ajustando automáticamente los parámetros de operación para garantizar uniformidad y calidad en cada ciclo. Esta trazabilidad es fundamental en industrias de alta exigencia, asegurando que cada pieza cumpla con tolerancias estrictas, soportando esfuerzos mecánicos y manteniendo resistencia estructural. La recopilación de datos también permite implementar mantenimiento predictivo, optimizar ciclos de producción, reducir desperdicio de material y mejorar la eficiencia energética de la planta, garantizando continuidad operativa y prolongando la vida útil de los componentes del equipo.
En resumen, el equipo de embutición metálica no solo transforma chapas planas en componentes tridimensionales de geometría compleja, sino que integra ingeniería mecánica, control de procesos, automatización, simulación de flujo de material, redibujo progresivo, lubricación controlada y sistemas de inspección avanzada, asegurando la producción de piezas con paredes uniformes, acabados precisos y alta resistencia estructural. Su capacidad para trabajar con distintos materiales, espesores y formas lo hace indispensable en sectores como automoción, aeronáutica, electrodomésticos, envases metálicos y menaje, optimizando recursos, reduciendo desperdicio, aumentando la productividad y manteniendo los más altos estándares de calidad industrial.
Si quieres, puedo continuar desarrollando un texto aún más detallado sobre la implementación de líneas de producción completamente automatizadas con equipos de embutición metálica, incluyendo control inteligente de parámetros, mantenimiento predictivo y sistemas de inspección integrados para piezas críticas de gran volumen.
Prensa de Troquelado y Embutición
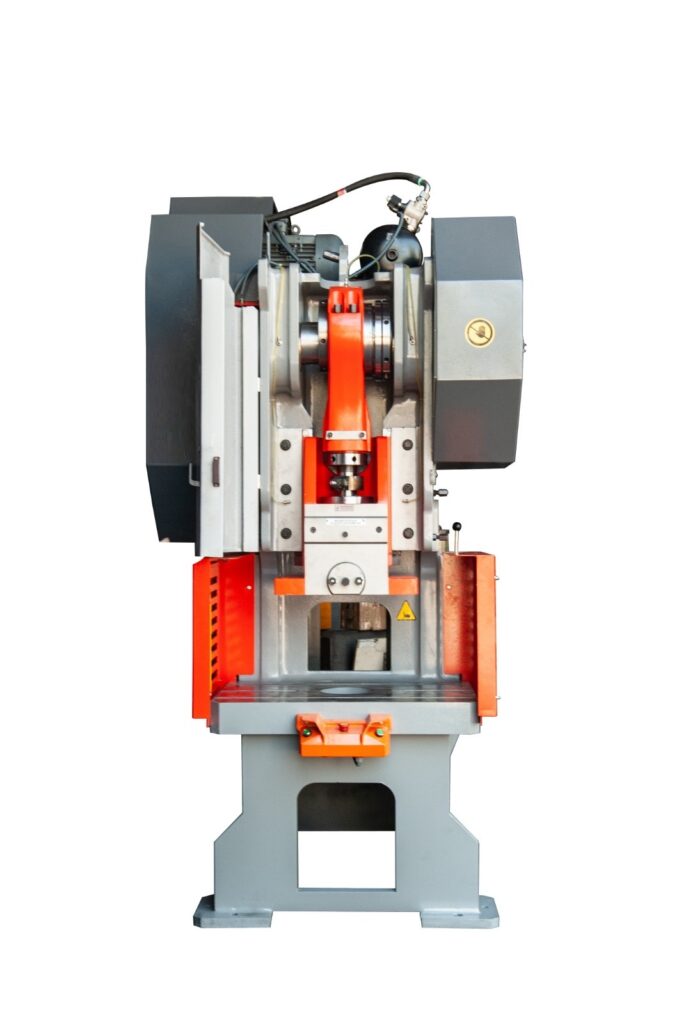
La prensa de troquelado y embutición es un equipo industrial diseñado para realizar dos funciones críticas en la transformación de chapas metálicas: el corte preciso mediante troquelado y la conformación tridimensional mediante embutición, combinando ambas operaciones en un solo ciclo de trabajo que optimiza tiempos de producción, reduce la manipulación de la chapa y asegura una mayor precisión en la geometría final de la pieza. Esta prensa se compone de un conjunto de elementos cuidadosamente coordinados: el troquel que permite cortar la chapa según el contorno deseado, el punzón que aplica la fuerza para deformar el material y darle forma, la matriz que guía y controla el flujo del metal, y los cojines o sistemas de sujeción que regulan la presión sobre los bordes de la chapa para evitar arrugas, pliegues o fisuras. La combinación de troquelado y embutición en un mismo equipo permite que la pieza obtenga dimensiones exactas y paredes uniformes en un solo ciclo, lo que es especialmente útil en la producción masiva de componentes huecos o piezas con geometrías complejas, como envases metálicos, carcasas de electrodomésticos, depósitos de líquidos y componentes automotrices.
El control de parámetros en la prensa de troquelado y embutición es fundamental para garantizar la calidad y consistencia de las piezas. La fuerza aplicada por el punzón debe ajustarse de acuerdo con el espesor y tipo de material, mientras que la presión del cojín regula la tensión en los bordes de la chapa para asegurar un flujo uniforme del metal. La velocidad de embutición y la sincronización del troquelado deben coordinarse cuidadosamente para que el corte y la deformación se realicen sin generar arrugas ni fisuras. En los modelos modernos, este control se realiza mediante sistemas electrónicos integrados que monitorizan la fuerza, el desplazamiento y la velocidad en tiempo real, ajustando automáticamente los parámetros del ciclo para optimizar la calidad de cada pieza. Además, el uso de software de simulación permite anticipar el comportamiento del material antes de iniciar la producción, optimizando el diseño de matrices y punzones y reduciendo la necesidad de ensayos físicos, lo que minimiza el desperdicio de material y mejora la eficiencia del proceso.
La prensa de troquelado y embutición puede ser mecánica, hidráulica o servo-hidráulica, cada una con ventajas específicas según la aplicación. Las prensas mecánicas son ideales para ciclos rápidos y piezas de geometría simple, aunque su control de fuerza es limitado. Las hidráulicas permiten aplicar una presión constante durante todo el recorrido del punzón, siendo especialmente útiles para materiales más duros o piezas de geometría compleja. Las servo-prensas permiten un control total del perfil de fuerza y velocidad, ajustando en tiempo real el movimiento del punzón para adaptarse a las distintas fases del embutido y del troquelado, optimizando la uniformidad de la pieza y prolongando la vida útil de las herramientas. Este nivel de control es esencial en la producción de piezas críticas que requieren alta precisión, resistencia estructural y acabados superficiales uniformes.
El sistema de lubricación en estas prensas también juega un papel fundamental, ya que reduce la fricción entre la chapa y las superficies de punzón y matriz, facilita un flujo uniforme del material y protege las herramientas del desgaste prematuro. Se utilizan lubricantes sólidos, pastas o emulsiones aplicados de manera localizada o en toda la superficie de contacto, dependiendo del tipo de material, espesor de la chapa y complejidad de la pieza. Una lubricación adecuada no solo asegura un acabado superficial óptimo, sino que también permite que la prensa funcione de manera más eficiente, reduciendo la fuerza requerida y prolongando la vida útil del equipo.
La integración de sensores de visión artificial y sistemas de monitoreo permite al equipo detectar deformaciones, arrugas, pliegues o irregularidades dimensionales, ajustando automáticamente los parámetros del ciclo para garantizar uniformidad y calidad en cada pieza. Esta trazabilidad completa es crucial en industrias con altos estándares de control, como la automoción, la aeronáutica, los electrodomésticos y los envases metálicos, donde cada pieza debe cumplir con tolerancias estrictas y mantener resistencia estructural. La recopilación de datos también permite realizar mantenimiento predictivo, optimizar ciclos de producción y reducir desperdicio de material, aumentando la eficiencia energética y la productividad de la planta industrial.
En conjunto, la prensa de troquelado y embutición es un equipo versátil y estratégico que permite transformar chapas metálicas en piezas tridimensionales complejas con paredes uniformes, acabados precisos y alta resistencia estructural, combinando ingeniería mecánica, control automatizado, simulación de flujo de material, redibujo progresivo, lubricación controlada y sistemas de inspección avanzada. Su capacidad para trabajar con distintos materiales, espesores y geometrías la hace indispensable en sectores como la automoción, aeronáutica, electrodomésticos, menaje y envases metálicos, optimizando recursos, reduciendo desperdicio y aumentando la productividad, manteniendo siempre los estándares más exigentes de calidad industrial.
La prensa de troquelado y embutición representa un avance significativo en la manufactura industrial, al combinar en un solo ciclo de operación el corte preciso de la chapa mediante troquelado con la conformación tridimensional de la pieza mediante embutición, lo que permite optimizar el tiempo de producción, reducir manipulación de materiales y garantizar una precisión dimensional y un acabado superficial superiores. Este tipo de prensa se compone de un conjunto coordinado de elementos donde cada uno cumple un rol específico: los troqueles definen el contorno y realizan el corte exacto de la chapa, los punzones aplican la fuerza necesaria para deformar el metal según la geometría requerida, las matrices guían y controlan el flujo del material, y los cojines o sistemas de sujeción regulan la presión en los bordes de la chapa, evitando arrugas, pliegues, fisuras o deformaciones irregulares. La sincronización de todas estas funciones permite que el material fluya de manera uniforme desde la etapa de troquelado hasta la embutición, asegurando que cada pieza mantenga un espesor uniforme, paredes lisas y una geometría precisa, incluso cuando se trata de piezas de gran complejidad o de relaciones altura-diámetro elevadas.
El control de parámetros en estas prensas es esencial para garantizar la calidad y la repetibilidad de las piezas. La fuerza aplicada por el punzón debe ajustarse según el tipo de material y su espesor, la presión del cojín debe regular la tensión en los bordes para evitar deformaciones no deseadas, y la velocidad de embutición debe sincronizarse con el troquelado para asegurar un flujo de material homogéneo y sin defectos. En las prensas modernas, estos parámetros se gestionan mediante sistemas de control electrónico que monitorean la fuerza, el desplazamiento, la velocidad y la fricción en tiempo real, realizando ajustes automáticos durante cada ciclo de operación. La incorporación de software de simulación permite anticipar el comportamiento del material, optimizar el diseño de matrices y punzones, detectar zonas de concentración de tensiones y definir la necesidad de redibujos progresivos, lo que reduce significativamente las pruebas físicas, minimiza el desperdicio de materia prima y aumenta la eficiencia de la producción.
El redibujo progresivo es una técnica crítica cuando la relación altura-diámetro de la pieza excede la ductilidad del material, permitiendo que la chapa alcance la forma final mediante varias etapas de embutición sucesivas. Cada etapa ajusta fuerza, velocidad, radio de matriz y lubricación para controlar el flujo del metal, evitando arrugas, pliegues o fisuras y asegurando paredes uniformes. Esta técnica es ampliamente utilizada en la fabricación de envases metálicos, depósitos industriales, carcasas de electrodomésticos, tanques de presión y utensilios de cocina, donde la precisión dimensional, la integridad estructural y el acabado superficial son factores determinantes para la funcionalidad y la estética del producto. La lubricación adecuada, ya sea mediante pastas, emulsiones o lubricantes sólidos, reduce la fricción, protege los punzones y matrices y facilita un flujo uniforme del material, garantizando no solo calidad superficial, sino también prolongando la vida útil de las herramientas y optimizando el rendimiento de la prensa.
La prensa de troquelado y embutición puede ser mecánica, hidráulica o servo-hidráulica, cada una adaptándose a diferentes necesidades de producción. Las prensas mecánicas permiten ciclos rápidos y son adecuadas para piezas simples, aunque ofrecen un control limitado de la fuerza durante el recorrido. Las prensas hidráulicas proporcionan presión constante y uniforme, esenciales para piezas complejas o materiales más resistentes, aunque sus ciclos son más lentos y requieren un mantenimiento más frecuente. Las servo-prensas permiten un control completo del perfil de fuerza y velocidad del punzón, ajustando cada fase del ciclo de manera dinámica, almacenando configuraciones específicas para distintos materiales, espesores y geometrías, y optimizando la uniformidad y precisión de las piezas mientras se prolonga la vida útil de las herramientas. Esta flexibilidad convierte al equipo en un sistema eficiente capaz de producir grandes volúmenes de piezas complejas manteniendo altos estándares de calidad industrial.
La integración de sensores de visión artificial y monitoreo en tiempo real añade una capa adicional de control, permitiendo detectar arrugas, pliegues, deformaciones, burbujas o desviaciones dimensionales, y ajustar automáticamente los parámetros de operación para garantizar piezas uniformes y de alta calidad. Esta trazabilidad es indispensable en industrias con estrictos estándares de control como automoción, aeronáutica, electrodomésticos y envases metálicos, donde cada componente debe cumplir con tolerancias exactas y mantener resistencia estructural. Además, la recopilación de datos permite implementar mantenimiento predictivo, optimizar ciclos de producción, reducir desperdicio de material y mejorar la eficiencia energética de la planta, asegurando continuidad operativa y prolongando la vida útil del equipo.
En resumen, la prensa de troquelado y embutición constituye un equipo integral, versátil y estratégico para la industria moderna, capaz de transformar chapas planas en piezas tridimensionales complejas con paredes uniformes, acabados precisos y alta resistencia estructural. Su capacidad para trabajar con distintos materiales como acero, acero inoxidable, aluminio, cobre y aleaciones ligeras, adaptándose a diferentes espesores y geometrías, lo hace indispensable en sectores como automoción, aeronáutica, electrodomésticos, envases metálicos y menaje, optimizando recursos, reduciendo desperdicio y aumentando la productividad, garantizando siempre los estándares más exigentes de calidad industrial.
La prensa de troquelado y embutición, considerada uno de los equipos más completos dentro de la manufactura industrial de piezas metálicas, combina en un solo sistema la capacidad de cortar, conformar y embutir chapas metálicas con un nivel de precisión, eficiencia y repetibilidad que permite satisfacer las demandas más exigentes de sectores como la automoción, la aeronáutica, la fabricación de electrodomésticos, envases metálicos, utensilios de cocina y componentes estructurales industriales. Este equipo integra múltiples elementos que funcionan de manera coordinada: los troqueles definen el contorno exacto del corte, los punzones aplican la fuerza necesaria para deformar la chapa hacia la forma final, las matrices guían el flujo del material, y los cojines o sistemas de sujeción regulan la presión sobre los bordes de la chapa para evitar arrugas, pliegues o fisuras. La sincronización de estas funciones permite que el material pase del corte a la embutición de manera fluida, logrando piezas con geometría precisa, paredes uniformes y acabados superficiales de alta calidad, incluso cuando se trata de piezas con relaciones altura-diámetro elevadas o geometrías complejas que requieren redibujo progresivo en varias etapas.
El control de parámetros en estas prensas es crítico para garantizar la uniformidad y la repetibilidad de cada pieza producida. La fuerza aplicada por el punzón debe ajustarse según el tipo de material, su espesor y la complejidad de la pieza, mientras que la presión del cojín asegura que los bordes de la chapa mantengan la tensión correcta para un flujo uniforme del material. La velocidad de embutición se sincroniza con el troquelado para que el metal fluya sin generar defectos, mientras que sensores instalados en punzones, matrices y cojines recopilan datos continuos de fuerza, desplazamiento, velocidad, fricción y temperatura. Estos datos son procesados por sistemas de control digital capaces de ajustar automáticamente los parámetros del ciclo de embutición y troquelado, optimizando la calidad de cada pieza y reduciendo la posibilidad de desperdicio de material. La simulación por elementos finitos complementa este control, permitiendo anticipar el comportamiento de la chapa, optimizar el diseño de matrices y punzones, identificar zonas de concentración de tensiones y determinar la necesidad de redibujos progresivos, lo que reduce ensayos físicos costosos y aumenta la eficiencia del proceso.
El redibujo progresivo es una técnica clave en la prensa de troquelado y embutición cuando las relaciones altura-diámetro de las piezas exceden la ductilidad del material. Cada etapa de redibujo ajusta de manera precisa la fuerza, la velocidad, el radio de matriz y la lubricación para controlar el flujo del metal, garantizando que las paredes de la pieza mantengan un espesor uniforme y que no aparezcan arrugas, pliegues o fisuras. Esta técnica es ampliamente utilizada en la producción de envases metálicos, depósitos industriales, carcasas de electrodomésticos, tanques de presión y utensilios de cocina, donde la precisión dimensional, la integridad estructural y la calidad del acabado superficial son factores determinantes para la funcionalidad, la seguridad y la estética del producto final. La lubricación adecuada mediante emulsiones, pastas o lubricantes sólidos es esencial para reducir la fricción, proteger las herramientas y garantizar un flujo homogéneo del material, prolongando la vida útil de la prensa y asegurando un rendimiento constante y fiable.
Las prensas de troquelado y embutición pueden ser mecánicas, hidráulicas o servo-hidráulicas, cada una adaptada a necesidades de producción específicas. Las prensas mecánicas son ideales para ciclos rápidos y piezas de geometría simple, aunque con control limitado de la fuerza durante el recorrido. Las hidráulicas aplican presión constante y uniforme, necesarias para piezas complejas o materiales más resistentes, aunque sus ciclos son más lentos y requieren un mantenimiento más frecuente. Las servo-prensas permiten un control total del perfil de fuerza y velocidad, ajustando dinámicamente cada fase del ciclo para adaptarse a la complejidad del material y la geometría de la pieza, almacenando configuraciones específicas para distintos tipos de chapas, espesores y formas, lo que permite cambios de producción rápidos sin comprometer la calidad ni la uniformidad de las piezas. Esta flexibilidad convierte al equipo en un sistema eficiente capaz de producir grandes volúmenes de piezas complejas con estándares industriales exigentes, garantizando uniformidad dimensional, resistencia estructural y acabados superficiales homogéneos.
Los sistemas de visión artificial y monitoreo en tiempo real son un complemento esencial en la prensa de troquelado y embutición, ya que permiten detectar cualquier irregularidad en la pieza, como arrugas, pliegues, burbujas, fisuras o desviaciones dimensionales, ajustando automáticamente los parámetros del ciclo para mantener la calidad y uniformidad de la producción. Esta trazabilidad es crucial en industrias de alta exigencia, asegurando que cada componente cumpla con tolerancias estrictas, soporte esfuerzos mecánicos y mantenga integridad estructural. Además, la recopilación y análisis de datos posibilitan implementar mantenimiento predictivo, optimizar ciclos de producción, reducir desperdicio de material y mejorar la eficiencia energética de la planta, asegurando continuidad operativa y prolongando la vida útil de los componentes de la prensa.
En definitiva, la prensa de troquelado y embutición constituye un equipo integral, versátil y estratégico para la industria moderna, combinando corte, conformado, redibujo progresivo, control de fuerza y velocidad, lubricación controlada, automatización avanzada y sistemas de inspección en tiempo real. Su capacidad para trabajar con distintos materiales como acero, acero inoxidable, aluminio, cobre y aleaciones ligeras, adaptándose a diferentes espesores y geometrías, la hace indispensable en sectores que requieren piezas tridimensionales de alta precisión, uniformidad y acabado superficial, optimizando recursos, reduciendo desperdicio y aumentando la productividad industrial. La combinación de estas tecnologías permite a la prensa de troquelado y embutición mantener estándares de calidad superiores, producir piezas complejas en grandes volúmenes y garantizar que cada componente cumpla con los requisitos más exigentes de la manufactura industrial moderna.
La prensa de troquelado y embutición, dentro de las líneas de producción industrial modernas, se ha convertido en un componente central que integra corte, conformado y embutición de manera simultánea, optimizando la eficiencia y asegurando la precisión en piezas metálicas de geometría compleja. Este equipo no funciona de manera aislada; forma parte de sistemas completos en los que la sincronización entre la alimentación de la chapa, el troquelado y la embutición es fundamental para garantizar que cada pieza cumpla con las especificaciones dimensionales, mantenga un espesor uniforme y presente un acabado superficial de alta calidad. Las prensas pueden estar equipadas con múltiples estaciones que realizan cortes preliminares, embuticiones parciales y redibujos progresivos, de manera que incluso las piezas con relaciones altura-diámetro elevadas o geometrías complicadas puedan fabricarse con seguridad, evitando defectos como arrugas, fisuras o pliegues que comprometan la integridad estructural. Cada fase del proceso requiere un control preciso de la fuerza del punzón, la presión del cojín y la velocidad de embutición, factores que interactúan con la fricción, la lubricación y las propiedades del material, elementos que se gestionan mediante sistemas de control electrónico de última generación capaces de ajustar dinámicamente cada parámetro durante el ciclo de producción.
La automatización avanzada y la integración de sensores son esenciales para maximizar la eficiencia y garantizar la calidad de cada pieza. Sensores de fuerza, desplazamiento, velocidad, temperatura y fricción recopilan datos en tiempo real que son procesados por sistemas de control digital, ajustando la presión del punzón y la velocidad de embutición según la respuesta del material. Este monitoreo continuo permite detectar cualquier desviación, como deformaciones no deseadas o variaciones en el espesor de las paredes, y realizar correcciones instantáneas, asegurando que todas las piezas producidas mantengan uniformidad y cumplan con estrictas tolerancias industriales. La simulación por elementos finitos complementa este proceso, permitiendo prever cómo se comportará la chapa antes de iniciar la producción, optimizando el diseño de matrices y punzones, definiendo la necesidad de etapas de redibujo progresivo y reduciendo desperdicio de material y tiempo en ensayos físicos.
El redibujo progresivo es una técnica indispensable para piezas de alta complejidad y materiales con ductilidad limitada. Cada etapa de redibujo aplica ajustes específicos de fuerza, velocidad, radio de matriz y lubricación, controlando de manera precisa el flujo del metal y asegurando que las paredes de la pieza mantengan un espesor uniforme y que la geometría final cumpla con los requerimientos estructurales. Esta técnica se aplica en la producción de envases metálicos, depósitos, carcasas de electrodomésticos, tanques de presión y componentes industriales, donde la precisión, la uniformidad y la integridad estructural son determinantes para la funcionalidad y seguridad del producto. La lubricación, ya sea mediante emulsiones, pastas o lubricantes sólidos, facilita un flujo de material uniforme, reduce la fricción, protege las herramientas y prolonga la vida útil del equipo, además de mejorar la eficiencia energética del proceso y la calidad superficial de cada pieza.
Las prensas pueden ser mecánicas, hidráulicas o servo-hidráulicas, seleccionadas según las necesidades específicas de producción y el tipo de material a trabajar. Las prensas mecánicas permiten ciclos rápidos, ideales para piezas simples, pero tienen control limitado de fuerza. Las hidráulicas proporcionan presión constante y uniforme, adecuadas para piezas más complejas o materiales más resistentes, aunque sus ciclos son más lentos y requieren mantenimiento frecuente. Las servo-prensas permiten un control total del perfil de fuerza y velocidad del punzón, ajustando de forma dinámica cada fase del ciclo de embutición y troquelado, almacenando perfiles específicos para distintos materiales y geometrías, optimizando la uniformidad y precisión de las piezas y prolongando la vida útil de los punzones y matrices. La combinación de estas tecnologías permite producir grandes volúmenes de piezas complejas manteniendo los más altos estándares de calidad industrial, garantizando uniformidad dimensional, resistencia estructural y acabados superficiales homogéneos.
Los sistemas de visión artificial y monitoreo en tiempo real representan un componente fundamental de estas prensas avanzadas. Permiten detectar arrugas, pliegues, fisuras, burbujas o desviaciones dimensionales durante cada ciclo de operación y ajustar automáticamente la presión, la velocidad o la trayectoria del punzón, asegurando que cada pieza cumpla con los requisitos de calidad. Esta trazabilidad es crítica en sectores como la automoción, la aeronáutica, los electrodomésticos y los envases metálicos, donde cada componente debe mantener tolerancias estrictas y soportar esfuerzos mecánicos importantes. La recopilación de datos también facilita el mantenimiento predictivo, la optimización de ciclos de producción y la reducción del desperdicio de material, aumentando la eficiencia energética y productiva de la planta y asegurando la continuidad operativa de las líneas de producción.
En conjunto, la prensa de troquelado y embutición es un equipo integral que combina corte, conformado, embutición, redibujo progresivo, control de fuerza y velocidad, lubricación controlada, automatización avanzada y sistemas de inspección en tiempo real, convirtiéndola en un elemento indispensable para la industria moderna. Su capacidad de trabajar con distintos materiales, espesores y geometrías, su flexibilidad para producir piezas tridimensionales de alta precisión, uniformidad y acabado superficial, y su integración con sistemas de control y monitoreo avanzados optimizan recursos, reducen desperdicio y aumentan la productividad industrial, manteniendo siempre los más altos estándares de calidad en la manufactura de piezas metálicas complejas.
Si quieres, puedo continuar desarrollando un texto aún más extenso sobre cómo se diseñan y sincronizan líneas completas de producción con múltiples prensas de troquelado y embutición, incluyendo control centralizado, ajuste dinámico de parámetros, integración de robótica para alimentación de chapas y sistemas automatizados de inspección de piezas críticas para garantizar eficiencia máxima y calidad constante en grandes volúmenes.
Prensa de Conformado en Profundidad
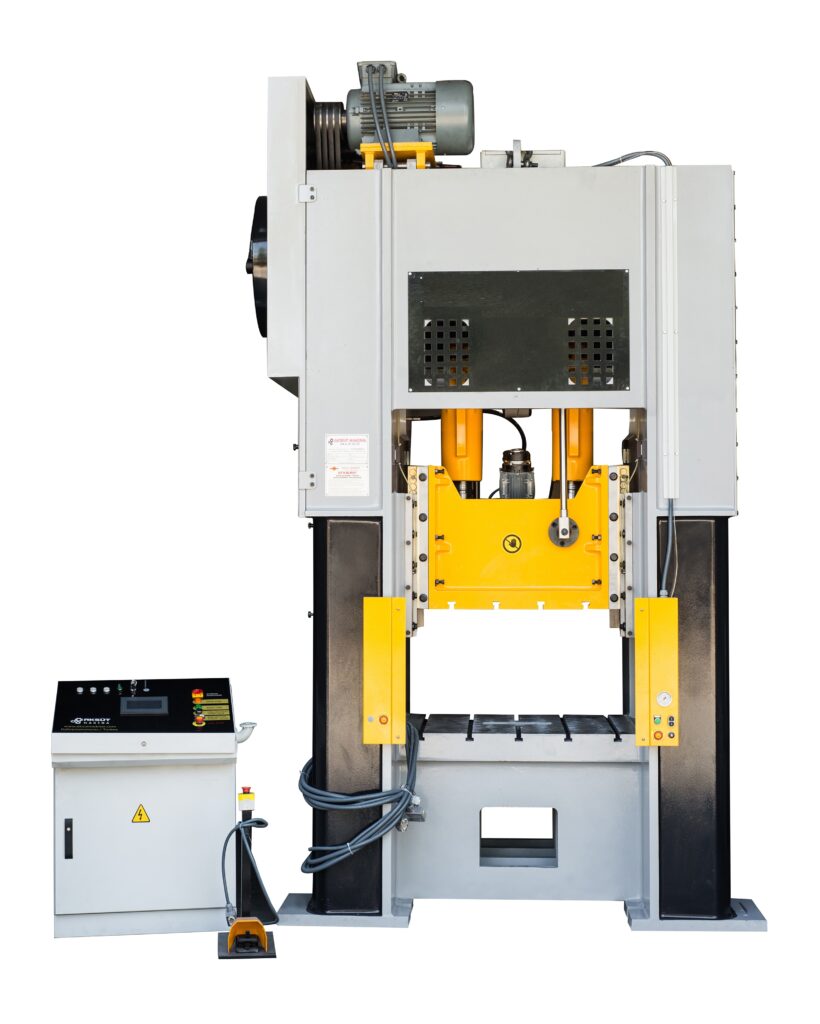
La prensa de conformado en profundidad es un equipo industrial especializado en transformar chapas metálicas planas en piezas tridimensionales de geometría compleja mediante la técnica de embutición profunda, un proceso en el cual la chapa es forzada a fluir dentro de una matriz mediante un punzón, logrando componentes con paredes uniformes, gran resistencia estructural y acabados superficiales de alta calidad. Este tipo de prensa está diseñada para manejar deformaciones significativas del material, permitiendo que piezas con relaciones altura-diámetro elevadas se fabriquen sin comprometer la integridad del metal ni generar defectos como arrugas, pliegues, fisuras o cambios irregulares en el espesor de las paredes. La prensa de conformado en profundidad integra múltiples sistemas que trabajan de manera coordinada: el punzón que aplica la fuerza controlada sobre la chapa, la matriz que guía el flujo del metal, los cojines de sujeción que regulan la presión en los bordes, y sistemas de lubricación que reducen la fricción y aseguran un flujo uniforme del material. La correcta sincronización de estos elementos permite que el proceso se realice de manera eficiente y reproducible, garantizando la calidad y precisión dimensional de cada pieza producida.
El control de parámetros es fundamental en este tipo de prensas, ya que la fuerza, la velocidad de embutición, la presión del cojín y la lubricación deben ajustarse en función de las propiedades del material, su espesor y la geometría de la pieza. Los modelos modernos incorporan sistemas electrónicos avanzados que monitorean estos parámetros en tiempo real y realizan ajustes automáticos durante el ciclo de conformado, optimizando el flujo del material y reduciendo la posibilidad de defectos. La simulación por elementos finitos permite anticipar el comportamiento de la chapa antes de la producción, optimizando el diseño de punzones y matrices, identificando posibles concentraciones de tensiones y determinando la necesidad de redibujo progresivo en piezas con geometrías complejas, lo que reduce ensayos físicos costosos y desperdicio de material.
El redibujo progresivo es una técnica clave dentro del conformado en profundidad, especialmente para piezas con gran altura relativa respecto al diámetro. Cada etapa de redibujo aplica ajustes precisos en fuerza, velocidad, radio de matriz y lubricación, controlando el flujo del metal y asegurando que las paredes mantengan un espesor uniforme y que la geometría final cumpla con los requisitos estructurales. Esta técnica es ampliamente utilizada en la fabricación de envases metálicos, depósitos industriales, carcasas de electrodomésticos, tanques de presión y utensilios de cocina, donde la precisión dimensional, la integridad estructural y el acabado superficial son esenciales para la funcionalidad y la seguridad del producto final. La lubricación, ya sea mediante pastas, emulsiones o lubricantes sólidos, protege las herramientas, facilita el flujo uniforme del material y prolonga la vida útil de la prensa, además de mejorar la eficiencia energética y la calidad de las piezas.
Las prensas de conformado en profundidad pueden ser mecánicas, hidráulicas o servo-hidráulicas, dependiendo de las necesidades de producción y del tipo de material a trabajar. Las prensas mecánicas permiten ciclos rápidos, ideales para piezas de geometría simple, aunque ofrecen un control limitado de la fuerza durante el recorrido. Las prensas hidráulicas proporcionan presión constante y uniforme, esenciales para materiales más resistentes o piezas complejas, aunque presentan ciclos más lentos y requieren mantenimiento frecuente. Las servo-prensas permiten un control total del perfil de fuerza, velocidad y trayectoria del punzón, ajustando dinámicamente cada fase del ciclo de conformado, almacenando configuraciones específicas para distintos materiales y geometrías, y optimizando la uniformidad y precisión de las piezas mientras se prolonga la vida útil de los punzones y matrices. Esta flexibilidad convierte al equipo en un sistema eficiente capaz de producir grandes volúmenes de piezas complejas con estándares industriales exigentes.
La integración de sistemas de visión artificial y monitoreo en tiempo real permite detectar cualquier irregularidad, como arrugas, pliegues, burbujas o desviaciones dimensionales, y ajustar automáticamente los parámetros de operación para garantizar uniformidad y calidad en cada pieza. Esta trazabilidad es crucial en sectores de alta exigencia, asegurando que cada componente cumpla con tolerancias estrictas y mantenga resistencia estructural. Además, la recopilación de datos permite implementar mantenimiento predictivo, optimizar ciclos de producción y reducir desperdicio de material, aumentando la eficiencia energética y productiva de la planta y asegurando continuidad operativa en líneas de producción de gran volumen.
En conjunto, la prensa de conformado en profundidad constituye un equipo integral, versátil y estratégico para la industria moderna, capaz de transformar chapas metálicas planas en piezas tridimensionales complejas con paredes uniformes, acabados precisos y alta resistencia estructural. Su capacidad para trabajar con distintos materiales como acero, acero inoxidable, aluminio, cobre y aleaciones ligeras, adaptándose a diferentes espesores y geometrías, la hace indispensable en sectores como automoción, aeronáutica, electrodomésticos, envases metálicos y menaje, optimizando recursos, reduciendo desperdicio y aumentando la productividad industrial, manteniendo siempre los estándares más exigentes de calidad y precisión en la manufactura de piezas metálicas complejas.
La prensa de conformado en profundidad, dentro de un entorno de producción industrial avanzado, representa un elemento clave para la fabricación de piezas metálicas tridimensionales con geometrías complejas, combinando precisión, eficiencia y repetibilidad en cada ciclo de operación. Este equipo permite que chapas metálicas planas se transformen en componentes huecos con paredes uniformes y acabados superficiales de alta calidad, mediante un proceso controlado de embutición profunda, en el que el material fluye dentro de la matriz bajo la acción de un punzón, mientras los cojines de sujeción regulan la presión sobre los bordes para evitar arrugas, pliegues, fisuras o variaciones irregulares del espesor. La prensa no solo realiza la deformación, sino que integra sistemas de control de fuerza, velocidad, lubricación y temperatura que permiten ajustar cada parámetro en tiempo real, asegurando que la pieza mantenga su integridad estructural y precisión dimensional, incluso cuando se trata de geometrías complejas o relaciones altura-diámetro elevadas que requieren redibujo progresivo en varias etapas. Cada componente de la prensa, desde los punzones hasta las matrices y los sistemas de lubricación, está diseñado para trabajar en perfecta sincronía, permitiendo un flujo uniforme del material y garantizando que cada pieza cumpla con los estándares más exigentes de calidad industrial, sin necesidad de procesos adicionales de corrección o acabado.
El control avanzado de parámetros es fundamental para el éxito del conformado en profundidad. La fuerza aplicada por el punzón, la presión de los cojines, la velocidad de desplazamiento y la lubricación deben calibrarse en función del tipo de material, su espesor y la complejidad de la pieza. Los modelos más modernos incorporan sistemas de control electrónico y sensores estratégicamente ubicados que monitorean en tiempo real la fuerza, el desplazamiento, la velocidad, la fricción y la temperatura de la chapa, ajustando automáticamente los parámetros del ciclo para optimizar el flujo del material y reducir la posibilidad de defectos. La simulación por elementos finitos permite anticipar el comportamiento de la chapa antes de iniciar la producción, optimizando el diseño de punzones y matrices, identificando zonas de concentración de tensiones y determinando la necesidad de redibujo progresivo, lo que reduce el desperdicio de material y la necesidad de ensayos físicos costosos, acelerando la puesta en marcha de la producción y mejorando la eficiencia global de la planta.
El redibujo progresivo es una técnica esencial en la embutición profunda cuando las piezas presentan relaciones altura-diámetro elevadas o materiales con ductilidad limitada. Cada etapa de redibujo aplica ajustes específicos de fuerza, velocidad, radio de matriz y lubricación, asegurando que las paredes mantengan un espesor uniforme y que la geometría final cumpla con los requisitos estructurales y funcionales. Esta técnica se utiliza en la producción de envases metálicos, depósitos industriales, carcasas de electrodomésticos, tanques de presión y utensilios de cocina, donde la precisión dimensional, la integridad estructural y la calidad del acabado superficial son determinantes para la funcionalidad, seguridad y estética del producto. La lubricación adecuada reduce la fricción, protege las herramientas, facilita el flujo homogéneo del material y prolonga la vida útil de la prensa, contribuyendo además a la eficiencia energética del proceso y a la calidad constante de cada pieza producida.
Las prensas de conformado en profundidad pueden ser mecánicas, hidráulicas o servo-hidráulicas, cada una con ventajas específicas según el tipo de producción y material. Las prensas mecánicas permiten ciclos rápidos y son ideales para piezas de geometría simple, aunque ofrecen un control limitado de la fuerza durante el recorrido. Las prensas hidráulicas proporcionan presión constante y uniforme, necesarias para piezas complejas o materiales más resistentes, aunque presentan ciclos más lentos y requieren un mantenimiento más frecuente. Las servo-prensas permiten un control completo del perfil de fuerza y velocidad, ajustando dinámicamente cada fase del ciclo de conformado y almacenando configuraciones específicas para distintos materiales y geometrías, optimizando uniformidad, precisión y vida útil de las herramientas. Esta flexibilidad convierte a la prensa de conformado en profundidad en un sistema eficiente capaz de producir grandes volúmenes de piezas complejas con estándares industriales exigentes, manteniendo uniformidad dimensional, resistencia estructural y acabados superficiales homogéneos.
La integración de sistemas de visión artificial y monitoreo en tiempo real amplifica la capacidad del equipo para garantizar calidad y uniformidad. Sensores avanzados detectan arrugas, pliegues, burbujas, fisuras o desviaciones dimensionales y ajustan automáticamente parámetros como la presión, la velocidad o la trayectoria del punzón, asegurando que cada pieza cumpla con tolerancias estrictas y mantenga integridad estructural. Esta trazabilidad es indispensable en sectores como automoción, aeronáutica, electrodomésticos y envases metálicos, donde la exactitud y resistencia de cada componente es crítica. La recopilación de datos permite además implementar mantenimiento predictivo, optimizar ciclos de producción, reducir desperdicio de material y mejorar la eficiencia energética y productiva de la planta, garantizando continuidad operativa y confiabilidad en la fabricación de piezas críticas de gran volumen.
En conjunto, la prensa de conformado en profundidad constituye un equipo integral y estratégico que combina embutición, redibujo progresivo, control de fuerza y velocidad, lubricación controlada, automatización avanzada y sistemas de inspección en tiempo real. Su capacidad para trabajar con distintos materiales, espesores y geometrías, producir piezas tridimensionales con paredes uniformes, acabados precisos y alta resistencia estructural, y su integración con sistemas de control y monitoreo avanzados optimizan recursos, reducen desperdicio y aumentan la productividad industrial, manteniendo los estándares más exigentes de calidad y precisión en la manufactura de piezas metálicas complejas.
La prensa de conformado en profundidad, en el marco de líneas de producción industrial avanzadas, se posiciona como un equipo indispensable para la transformación de chapas metálicas planas en piezas tridimensionales complejas, permitiendo obtener componentes huecos con paredes uniformes, alta resistencia estructural y acabados superficiales de máxima calidad. En estas líneas, la prensa no opera de manera aislada, sino como parte de un sistema integrado donde la alimentación de la chapa, el troquelado previo, la embutición y el redibujo progresivo se sincronizan para garantizar que cada pieza cumpla con las especificaciones dimensionales, mantenga la uniformidad de espesor y presente acabados homogéneos. El proceso de embutición profunda consiste en forzar el material dentro de una matriz mediante un punzón, mientras los cojines de sujeción regulan la presión sobre los bordes para controlar la tensión de la chapa, evitando arrugas, pliegues, fisuras o deformaciones irregulares. Cada elemento del equipo, desde punzones y matrices hasta sistemas de lubricación, está diseñado para funcionar de manera coordinada y precisa, asegurando que el flujo del material sea uniforme y que cada pieza mantenga integridad estructural y geometría exacta.
El control de parámetros en la prensa de conformado en profundidad es esencial para asegurar la calidad y repetibilidad de cada pieza. La fuerza ejercida por el punzón, la presión de los cojines, la velocidad de desplazamiento y la lubricación deben ajustarse en función del tipo de material, su espesor y la complejidad de la pieza. Los modelos modernos incorporan sistemas electrónicos avanzados y sensores que monitorean en tiempo real fuerza, desplazamiento, velocidad, fricción y temperatura, ajustando automáticamente los parámetros del ciclo para optimizar el flujo del material y reducir la posibilidad de defectos. La simulación por elementos finitos permite anticipar el comportamiento de la chapa, optimizando el diseño de punzones y matrices, identificando zonas de concentración de tensiones y determinando la necesidad de redibujo progresivo, minimizando el desperdicio de material y los ensayos físicos costosos y acelerando la puesta en marcha de la producción.
El redibujo progresivo es una técnica fundamental en la embutición profunda, especialmente para piezas con relaciones altura-diámetro elevadas o materiales con ductilidad limitada. Cada etapa de redibujo aplica ajustes específicos de fuerza, velocidad, radio de matriz y lubricación, asegurando que las paredes de la pieza mantengan un espesor uniforme y que la geometría final cumpla con los requisitos estructurales y funcionales. Esta técnica es utilizada en la fabricación de envases metálicos, depósitos industriales, carcasas de electrodomésticos, tanques de presión y utensilios de cocina, donde la precisión dimensional, la integridad estructural y el acabado superficial son determinantes para la funcionalidad y seguridad del producto. La lubricación adecuada mediante pastas, emulsiones o lubricantes sólidos reduce la fricción, protege las herramientas y facilita un flujo homogéneo del material, prolongando la vida útil de la prensa y asegurando un rendimiento constante y eficiente.
Las prensas de conformado en profundidad pueden ser mecánicas, hidráulicas o servo-hidráulicas, cada una adaptándose a necesidades de producción específicas. Las prensas mecánicas permiten ciclos rápidos, ideales para piezas de geometría simple, aunque ofrecen un control limitado de fuerza. Las prensas hidráulicas proporcionan presión constante y uniforme, necesarias para materiales más resistentes o piezas complejas, aunque presentan ciclos más lentos y requieren mantenimiento frecuente. Las servo-prensas permiten un control total del perfil de fuerza, velocidad y trayectoria del punzón, ajustando dinámicamente cada fase del ciclo de conformado y almacenando configuraciones específicas para distintos materiales y geometrías, optimizando uniformidad, precisión y prolongando la vida útil de punzones y matrices. Esta flexibilidad convierte al equipo en un sistema eficiente capaz de producir grandes volúmenes de piezas complejas manteniendo altos estándares de calidad industrial.
La integración de sistemas de visión artificial y monitoreo en tiempo real permite detectar cualquier irregularidad, como arrugas, pliegues, fisuras, burbujas o desviaciones dimensionales, y ajustar automáticamente parámetros como presión, velocidad o trayectoria del punzón para garantizar uniformidad y calidad en cada pieza. Esta trazabilidad es esencial en sectores de alta exigencia como automoción, aeronáutica, electrodomésticos y envases metálicos, donde la exactitud y resistencia de cada componente es crítica. La recopilación de datos también permite implementar mantenimiento predictivo, optimizar ciclos de producción, reducir desperdicio de material y mejorar la eficiencia energética de la planta, asegurando continuidad operativa y confiabilidad en la fabricación de piezas críticas de gran volumen.
En conjunto, la prensa de conformado en profundidad constituye un equipo integral, versátil y estratégico que combina embutición, redibujo progresivo, control de fuerza y velocidad, lubricación controlada, automatización avanzada y sistemas de inspección en tiempo real, optimizando recursos, reduciendo desperdicio y aumentando la productividad industrial, manteniendo los estándares más exigentes de calidad y precisión en la manufactura de piezas metálicas complejas. Su capacidad para trabajar con distintos materiales, espesores y geometrías y producir piezas tridimensionales con paredes uniformes, acabados precisos y alta resistencia estructural la hace indispensable en sectores industriales que requieren eficiencia máxima, control absoluto de calidad y alta productividad en piezas de gran complejidad y volumen.
La prensa de conformado en profundidad, cuando se integra dentro de líneas de producción industrial totalmente automatizadas, se convierte en un elemento central para la fabricación de piezas metálicas tridimensionales complejas, permitiendo transformar chapas planas en componentes huecos con paredes uniformes, alta resistencia estructural y acabados superficiales homogéneos, incluso en geometrías que requieren relaciones altura-diámetro elevadas o materiales de ductilidad limitada. En estas líneas, la prensa no actúa de manera aislada; forma parte de un sistema coordinado que incluye estaciones de alimentación automática de chapas, pre-troquelado, embutición, redibujo progresivo y extracción de piezas terminadas, con sincronización precisa entre cada fase del proceso para garantizar que el flujo del material sea constante y que cada pieza mantenga exactitud dimensional, espesor uniforme y acabados de alta calidad. Los punzones, matrices y cojines de sujeción trabajan en perfecta armonía, mientras los sistemas de lubricación controlada aseguran que el metal fluya sin fricción excesiva, evitando arrugas, pliegues, fisuras o deformaciones indeseadas, y prolongando la vida útil de las herramientas y de la prensa misma.
El control de parámetros en estas prensas es crítico para mantener la uniformidad y repetibilidad de las piezas producidas. La fuerza del punzón, la presión del cojín, la velocidad de embutición y la lubricación se ajustan en función de las propiedades del material, su espesor y la complejidad de la geometría, todo ello gestionado mediante sistemas de control digital que monitorean en tiempo real fuerza, desplazamiento, velocidad, fricción y temperatura, realizando ajustes automáticos durante cada ciclo. La simulación por elementos finitos permite anticipar el comportamiento de la chapa, optimizando el diseño de punzones y matrices, identificando zonas de concentración de tensiones y determinando la necesidad de redibujo progresivo en piezas complejas, reduciendo el desperdicio de material y minimizando ensayos físicos costosos, mientras se acelera la puesta en marcha de la producción.
El redibujo progresivo constituye una técnica esencial dentro del conformado en profundidad, permitiendo que piezas con grandes alturas relativas respecto a su diámetro se fabriquen sin comprometer la integridad del material. Cada etapa de redibujo ajusta de forma precisa fuerza, velocidad, radio de matriz y lubricación, controlando el flujo del metal y garantizando que las paredes mantengan espesor uniforme y que la pieza cumpla con los requisitos estructurales y funcionales. Esta técnica se aplica en la producción de envases metálicos, depósitos, carcasas de electrodomésticos, tanques de presión, utensilios de cocina y componentes industriales críticos, donde la precisión dimensional, la uniformidad y el acabado superficial son esenciales para la funcionalidad y seguridad del producto. La lubricación adecuada, ya sea mediante pastas, emulsiones o lubricantes sólidos, reduce la fricción, protege las herramientas y asegura un flujo homogéneo del material, optimizando la eficiencia energética y prolongando la vida útil de los componentes de la prensa.
Las prensas de conformado en profundidad pueden ser mecánicas, hidráulicas o servo-hidráulicas, adaptándose a distintos requerimientos de producción. Las prensas mecánicas permiten ciclos rápidos y son ideales para piezas simples, aunque ofrecen control limitado de la fuerza durante el recorrido. Las hidráulicas proporcionan presión constante y uniforme, adecuadas para piezas complejas o materiales más resistentes, aunque presentan ciclos más lentos y requieren mayor mantenimiento. Las servo-prensas permiten un control total del perfil de fuerza y velocidad del punzón, ajustando dinámicamente cada fase del ciclo, almacenando configuraciones específicas para distintos materiales, espesores y geometrías, y optimizando uniformidad, precisión y vida útil de punzones y matrices, garantizando piezas consistentes incluso en producciones de gran volumen.
La incorporación de sistemas de visión artificial y monitoreo en tiempo real añade una capa adicional de control, permitiendo detectar arrugas, pliegues, fisuras, burbujas o desviaciones dimensionales, y ajustar automáticamente parámetros como presión, velocidad o trayectoria del punzón, asegurando uniformidad y calidad de cada pieza. Esta trazabilidad es esencial en industrias de alta exigencia como automoción, aeronáutica, electrodomésticos y envases metálicos, donde cada componente debe cumplir tolerancias estrictas y mantener resistencia estructural. La recopilación y análisis de datos también facilitan la implementación de mantenimiento predictivo, la optimización de ciclos de producción, la reducción del desperdicio de material y la mejora de la eficiencia energética, garantizando continuidad operativa y confiabilidad en la fabricación de piezas críticas de gran volumen.
En conjunto, la prensa de conformado en profundidad constituye un equipo integral, estratégico y altamente versátil, que combina embutición, redibujo progresivo, control de fuerza y velocidad, lubricación controlada, automatización avanzada y sistemas de inspección en tiempo real. Su capacidad de trabajar con distintos materiales, espesores y geometrías, producir piezas tridimensionales con paredes uniformes, acabados precisos y alta resistencia estructural, y su integración con sistemas de control centralizado y robótica de alimentación y extracción, permite optimizar recursos, reducir desperdicio y aumentar la productividad industrial, manteniendo los más altos estándares de calidad y precisión en la manufactura de piezas metálicas complejas. La combinación de estas tecnologías permite que la prensa de conformado en profundidad se mantenga como un elemento indispensable en líneas de producción modernas, capaces de operar con eficiencia máxima, garantizar calidad constante y producir grandes volúmenes de piezas críticas sin comprometer la uniformidad, integridad estructural ni el acabado superficial.
Si quieres, puedo continuar con un desarrollo aún más amplio sobre la coordinación completa de múltiples prensas de conformado en profundidad en una línea de producción automatizada, incluyendo sincronización de robótica, control centralizado de parámetros, sistemas de inspección de calidad y optimización del flujo de materiales para máxima eficiencia y productividad industrial.
Máquina de Estampación y Embutido
La máquina de estampación y embutido es un equipo industrial diseñado para transformar chapas metálicas planas en piezas tridimensionales con formas complejas, combinando los procesos de corte, conformado y embutición en un solo sistema que permite alta precisión, repetibilidad y eficiencia en la producción. Este tipo de máquina se utiliza ampliamente en sectores como la automoción, la aeronáutica, los electrodomésticos, envases metálicos, menaje y componentes industriales, donde se requiere que las piezas mantengan uniformidad de espesor, integridad estructural y acabados superficiales de alta calidad. La máquina integra punzones, matrices, cojines de sujeción y sistemas de lubricación que trabajan de manera coordinada: los punzones aplican la fuerza necesaria para deformar la chapa y darle forma, las matrices guían el flujo del material evitando arrugas o pliegues, los cojines regulan la presión sobre los bordes para controlar la tensión de la chapa y los sistemas de lubricación facilitan el deslizamiento del metal, reduciendo fricción y prolongando la vida útil de las herramientas.
El control de parámetros es fundamental en estas máquinas para asegurar que cada pieza cumpla con las especificaciones dimensionales y mantenga la uniformidad del espesor. La fuerza del punzón, la presión del cojín, la velocidad de embutición y la lubricación se ajustan según el tipo de material, su espesor y la complejidad de la geometría de la pieza. Los modelos modernos incorporan sistemas de control digital que monitorean en tiempo real la fuerza, el desplazamiento, la velocidad, la fricción y la temperatura, ajustando automáticamente cada parámetro para optimizar el flujo del material y minimizar la posibilidad de defectos. La simulación por elementos finitos permite anticipar cómo se comportará la chapa antes de la producción, optimizando el diseño de punzones y matrices, identificando concentraciones de tensión y determinando la necesidad de redibujo progresivo, reduciendo desperdicio de material y ensayos físicos costosos.
El redibujo progresivo es una técnica esencial en el embutido de piezas con relaciones altura-diámetro elevadas o geometrías complejas. Cada etapa de redibujo aplica ajustes precisos en fuerza, velocidad, radio de matriz y lubricación, garantizando que las paredes mantengan espesor uniforme y que la pieza final cumpla con los requisitos estructurales y funcionales. Esta técnica se emplea en la producción de envases metálicos, depósitos, carcasas de electrodomésticos, tanques de presión y utensilios de cocina, donde la precisión dimensional y la calidad superficial son determinantes para la funcionalidad y seguridad del producto. La lubricación adecuada facilita un flujo homogéneo del metal, protege las herramientas y prolonga la vida útil de la máquina, además de mejorar la eficiencia energética del proceso y asegurar un rendimiento constante en cada ciclo de producción.
Las máquinas de estampación y embutido pueden ser mecánicas, hidráulicas o servo-hidráulicas. Las prensas mecánicas permiten ciclos rápidos y son ideales para piezas de geometría simple, pero ofrecen control limitado de fuerza. Las prensas hidráulicas proporcionan presión constante y uniforme, necesarias para piezas complejas o materiales más resistentes, aunque sus ciclos son más lentos y requieren mantenimiento frecuente. Las servo-prensas permiten un control completo del perfil de fuerza y velocidad, ajustando dinámicamente cada fase del ciclo y almacenando configuraciones específicas para distintos materiales y geometrías, optimizando uniformidad, precisión y prolongando la vida útil de punzones y matrices, permitiendo producir grandes volúmenes de piezas complejas cumpliendo con estándares industriales exigentes.
La integración de sistemas de visión artificial y monitoreo en tiempo real es un complemento clave para garantizar calidad y uniformidad. Sensores avanzados detectan arrugas, pliegues, fisuras, burbujas o desviaciones dimensionales, y ajustan automáticamente los parámetros de operación como presión, velocidad o trayectoria del punzón, asegurando que cada pieza cumpla con tolerancias estrictas y mantenga integridad estructural. Esta trazabilidad es fundamental en industrias como la automoción, aeronáutica y electrodomésticos, donde cada componente debe cumplir estrictos estándares de calidad. La recopilación de datos también permite implementar mantenimiento predictivo, optimizar ciclos de producción, reducir desperdicio de material y mejorar la eficiencia energética, asegurando continuidad operativa y confiabilidad en la fabricación de piezas críticas.
En conjunto, la máquina de estampación y embutido constituye un equipo integral y estratégico para la industria moderna, combinando corte, conformado, embutición, redibujo progresivo, control de fuerza y velocidad, lubricación controlada, automatización avanzada y sistemas de inspección en tiempo real. Su capacidad para trabajar con distintos materiales, espesores y geometrías, producir piezas tridimensionales con paredes uniformes, acabados precisos y alta resistencia estructural, y su integración con sistemas de control centralizado y robótica de alimentación y extracción, permite optimizar recursos, reducir desperdicio y aumentar la productividad industrial, manteniendo los más altos estándares de calidad y precisión en la manufactura de piezas metálicas complejas.
La máquina de estampación y embutido, al integrarse en líneas de producción industrial avanzadas, se convierte en un componente fundamental para la transformación de chapas metálicas planas en piezas tridimensionales complejas, capaces de cumplir con altos estándares de precisión, uniformidad y acabado superficial, incluso en geometrías de difícil manufactura o materiales de ductilidad limitada. En estas líneas, la máquina no opera de manera aislada, sino como parte de un sistema coordinado en el que la alimentación automática de chapas, el troquelado preliminar, la embutición profunda, el redibujo progresivo y la extracción de piezas terminadas se sincronizan de manera precisa para garantizar que cada componente mantenga exactitud dimensional, espesor uniforme y acabados homogéneos, eliminando defectos como arrugas, pliegues, fisuras o deformaciones irregulares que puedan comprometer la integridad estructural. Cada elemento de la máquina, desde punzones y matrices hasta los cojines de sujeción y los sistemas de lubricación, trabaja en perfecta armonía, controlando la presión, el flujo del material y la fricción para asegurar que el metal fluya de manera uniforme y que cada pieza cumpla con los requisitos de diseño y funcionalidad.
El control de parámetros es crítico para garantizar la repetibilidad y la calidad de cada pieza producida. La fuerza aplicada por el punzón, la presión de los cojines, la velocidad de embutición y la lubricación se ajustan según el tipo de material, su espesor y la complejidad de la geometría, todo gestionado mediante sistemas de control electrónico avanzados que monitorean en tiempo real fuerza, desplazamiento, velocidad, fricción y temperatura. Estos sistemas permiten realizar ajustes automáticos durante cada ciclo, optimizando el flujo del material y reduciendo la posibilidad de defectos. La simulación por elementos finitos complementa este proceso, anticipando el comportamiento de la chapa antes de la producción, optimizando el diseño de punzones y matrices, identificando posibles concentraciones de tensiones y determinando la necesidad de redibujo progresivo, lo que disminuye el desperdicio de material y minimiza ensayos físicos costosos, acelerando la puesta en marcha de la línea de producción.
El redibujo progresivo se convierte en una técnica indispensable en la fabricación de piezas con relaciones altura-diámetro elevadas o geometrías complejas. Cada etapa de redibujo aplica ajustes específicos de fuerza, velocidad, radio de matriz y lubricación, controlando el flujo del material y asegurando que las paredes mantengan un espesor uniforme y que la pieza final cumpla con los requisitos estructurales y funcionales. Esta técnica es ampliamente utilizada en la fabricación de envases metálicos, depósitos industriales, carcasas de electrodomésticos, tanques de presión, utensilios de cocina y componentes industriales críticos, donde la precisión dimensional, la uniformidad y la calidad superficial determinan la funcionalidad y seguridad del producto. La lubricación adecuada, ya sea mediante pastas, emulsiones o lubricantes sólidos, protege las herramientas, facilita el flujo homogéneo del metal y prolonga la vida útil de la máquina, contribuyendo a la eficiencia energética y asegurando un rendimiento constante en cada ciclo de producción.
Las máquinas de estampación y embutido pueden ser mecánicas, hidráulicas o servo-hidráulicas, cada una adaptándose a distintos requerimientos de producción y materiales. Las prensas mecánicas permiten ciclos rápidos, ideales para piezas simples, pero ofrecen un control limitado de la fuerza durante el recorrido. Las prensas hidráulicas proporcionan presión constante y uniforme, necesarias para piezas complejas o materiales más resistentes, aunque presentan ciclos más lentos y requieren mantenimiento frecuente. Las servo-prensas permiten un control total del perfil de fuerza y velocidad del punzón, ajustando dinámicamente cada fase del ciclo, almacenando configuraciones específicas para distintos materiales y geometrías, optimizando uniformidad, precisión y prolongando la vida útil de punzones y matrices, permitiendo la producción de grandes volúmenes de piezas complejas con estándares industriales exigentes.
La incorporación de sistemas de visión artificial y monitoreo en tiempo real añade una capa adicional de control y trazabilidad, permitiendo detectar arrugas, pliegues, fisuras, burbujas o desviaciones dimensionales y ajustar automáticamente parámetros como presión, velocidad o trayectoria del punzón, asegurando uniformidad y calidad de cada pieza. Este monitoreo es esencial en sectores de alta exigencia, como la automoción, la aeronáutica y la fabricación de electrodomésticos, donde la precisión y resistencia de cada componente son críticas. La recopilación y análisis de datos permite además implementar mantenimiento predictivo, optimizar ciclos de producción, reducir desperdicio de material y mejorar la eficiencia energética de la planta, garantizando continuidad operativa y confiabilidad en la fabricación de piezas críticas de gran volumen.
En conjunto, la máquina de estampación y embutido constituye un equipo integral y estratégico que combina corte, conformado, embutición, redibujo progresivo, control de fuerza y velocidad, lubricación controlada, automatización avanzada y sistemas de inspección en tiempo real. Su capacidad para trabajar con distintos materiales, espesores y geometrías, producir piezas tridimensionales con paredes uniformes, acabados precisos y alta resistencia estructural, y su integración con sistemas de control centralizado y robótica para alimentación y extracción de chapas, permite optimizar recursos, reducir desperdicio y aumentar la productividad industrial, manteniendo los más altos estándares de calidad y precisión en la manufactura de piezas metálicas complejas. Esta combinación de tecnologías y controles convierte a la máquina en un pilar fundamental de líneas de producción modernas, capaces de operar con eficiencia máxima, garantizar calidad constante y producir grandes volúmenes de piezas críticas sin comprometer la uniformidad, integridad estructural ni el acabado superficial.
La máquina de estampación y embutido, al formar parte de líneas de producción completamente automatizadas, se convierte en un eje central para la fabricación de piezas metálicas tridimensionales de gran complejidad, capaces de cumplir con los estándares más exigentes de precisión, uniformidad y acabado superficial. En este contexto, la máquina no opera de manera aislada, sino que se integra con sistemas de alimentación automática de chapas, estaciones de troquelado preliminar, procesos de embutición profunda, redibujo progresivo y extracción de piezas terminadas, todos sincronizados para garantizar que cada componente mantenga espesor uniforme, integridad estructural y acabados homogéneos, evitando defectos como arrugas, pliegues, fisuras o deformaciones irregulares que puedan comprometer la funcionalidad o estética de la pieza. Los punzones aplican la fuerza necesaria para deformar la chapa, las matrices guían el flujo del metal, los cojines de sujeción regulan la presión sobre los bordes y los sistemas de lubricación controlada facilitan el desplazamiento uniforme del material, protegiendo las herramientas y prolongando la vida útil de la máquina, mientras se asegura que cada pieza cumpla con los parámetros de diseño y las especificaciones industriales.
El control de parámetros es un aspecto crítico en estas máquinas para asegurar la repetibilidad y calidad de cada pieza producida. La fuerza del punzón, la presión de los cojines, la velocidad de embutición y la lubricación se ajustan de manera precisa según el tipo de material, su espesor y la complejidad geométrica de la pieza, todo gestionado mediante sistemas de control digital avanzado que monitorean en tiempo real fuerza, desplazamiento, velocidad, fricción y temperatura, permitiendo ajustes automáticos durante cada ciclo y optimizando el flujo del material para minimizar defectos. La simulación por elementos finitos complementa el proceso, anticipando el comportamiento de la chapa antes de la producción, optimizando el diseño de punzones y matrices, identificando posibles concentraciones de tensión y determinando la necesidad de redibujo progresivo, reduciendo desperdicio de material y ensayos físicos costosos, acelerando la puesta en marcha de la línea de producción y aumentando la eficiencia global.
El redibujo progresivo constituye una técnica indispensable en el embutido de piezas con relaciones altura-diámetro elevadas o geometrías complejas. Cada etapa de redibujo aplica ajustes específicos de fuerza, velocidad, radio de matriz y lubricación, controlando el flujo del material y asegurando que las paredes mantengan espesor uniforme y que la pieza final cumpla con los requisitos estructurales, funcionales y estéticos. Esta técnica se aplica en la fabricación de envases metálicos, depósitos industriales, carcasas de electrodomésticos, tanques de presión, utensilios de cocina y componentes industriales críticos, donde la precisión dimensional, la uniformidad y la calidad superficial determinan la funcionalidad y seguridad del producto. La lubricación adecuada, ya sea mediante pastas, emulsiones o lubricantes sólidos, protege las herramientas, facilita el flujo homogéneo del metal, prolonga la vida útil de la máquina y mejora la eficiencia energética del proceso, asegurando un rendimiento constante y estable en cada ciclo de producción.
Las máquinas de estampación y embutido pueden ser mecánicas, hidráulicas o servo-hidráulicas, adaptándose a diferentes necesidades de producción y materiales. Las prensas mecánicas permiten ciclos rápidos, ideales para piezas simples, pero ofrecen un control limitado de la fuerza durante el recorrido. Las prensas hidráulicas proporcionan presión constante y uniforme, necesarias para piezas complejas o materiales más resistentes, aunque presentan ciclos más lentos y requieren mayor mantenimiento. Las servo-prensas permiten un control total del perfil de fuerza y velocidad del punzón, ajustando dinámicamente cada fase del ciclo, almacenando configuraciones específicas para distintos materiales, espesores y geometrías, optimizando uniformidad, precisión y prolongando la vida útil de punzones y matrices, permitiendo la producción de grandes volúmenes de piezas complejas cumpliendo con los estándares más exigentes de la industria.
La incorporación de sistemas de visión artificial y monitoreo en tiempo real añade una capa de control y trazabilidad adicional, permitiendo detectar arrugas, pliegues, fisuras, burbujas o desviaciones dimensionales, y ajustar automáticamente parámetros como presión, velocidad o trayectoria del punzón, asegurando uniformidad y calidad de cada pieza. Esta trazabilidad es esencial en industrias de alta exigencia como automoción, aeronáutica, electrodomésticos y envases metálicos, donde cada componente debe cumplir estrictos estándares de calidad y resistencia estructural. La recopilación y análisis de datos permiten implementar mantenimiento predictivo, optimizar ciclos de producción, reducir desperdicio de material y mejorar la eficiencia energética de la planta, garantizando continuidad operativa y confiabilidad en la fabricación de piezas críticas de gran volumen.
En conjunto, la máquina de estampación y embutido constituye un equipo integral, versátil y estratégico que combina corte, conformado, embutición, redibujo progresivo, control de fuerza y velocidad, lubricación controlada, automatización avanzada y sistemas de inspección en tiempo real, optimizando recursos, reduciendo desperdicio y aumentando la productividad industrial. Su capacidad para trabajar con distintos materiales, espesores y geometrías, producir piezas tridimensionales con paredes uniformes, acabados precisos y alta resistencia estructural, y su integración con sistemas de control centralizado y robótica para alimentación y extracción de chapas, permite mantener los más altos estándares de calidad y precisión en la manufactura de piezas metálicas complejas. Esta combinación de tecnologías asegura que la máquina de estampación y embutido sea un pilar fundamental en líneas de producción modernas, capaces de operar con eficiencia máxima, garantizar calidad constante y producir grandes volúmenes de piezas críticas sin comprometer la uniformidad, integridad estructural ni el acabado superficial, convirtiéndose en un elemento esencial para la competitividad y sostenibilidad de la producción industrial.
La máquina de estampación y embutido, cuando se integra en líneas de producción completamente automatizadas, se convierte en un elemento central para la fabricación de piezas metálicas de gran complejidad, donde cada fase del proceso está diseñada para garantizar máxima precisión, uniformidad y acabado superficial en piezas tridimensionales. Estas líneas combinan alimentación automática de chapas, corte preliminar, embutición profunda, redibujo progresivo y extracción de piezas terminadas, todo coordinado mediante sistemas de control digital y robótica para asegurar que cada componente cumpla con tolerancias estrictas, mantenga espesor uniforme y presente acabados homogéneos sin arrugas, pliegues, fisuras o deformaciones que puedan comprometer su funcionalidad o estética. Los punzones aplican la fuerza necesaria para moldear la chapa, mientras que las matrices guían el flujo del material y los cojines de sujeción regulan la presión sobre los bordes, asegurando un desplazamiento uniforme del metal. La lubricación controlada reduce fricción, protege herramientas y prolonga la vida útil de la máquina, garantizando ciclos de producción eficientes y consistentes.
El control de parámetros es fundamental en estas máquinas, ya que la fuerza del punzón, la presión de los cojines, la velocidad de embutición y la lubricación deben ajustarse de forma precisa según el tipo de material, su espesor y la complejidad de la pieza. Los sistemas de control avanzados monitorean en tiempo real fuerza, desplazamiento, velocidad, fricción y temperatura, realizando ajustes automáticos durante cada ciclo para optimizar el flujo del material y minimizar defectos. La simulación por elementos finitos permite anticipar el comportamiento de la chapa antes de la producción, optimizando el diseño de punzones y matrices, identificando concentraciones de tensión y determinando la necesidad de redibujo progresivo, reduciendo desperdicio de material y costos de ensayo físico, acelerando la puesta en marcha de la producción y aumentando la eficiencia global.
El redibujo progresivo es esencial para piezas con relaciones altura-diámetro elevadas o geometrías complejas, aplicando en cada etapa ajustes específicos de fuerza, velocidad, radio de matriz y lubricación, asegurando que las paredes mantengan espesor uniforme y que la pieza final cumpla con los requisitos estructurales y funcionales. Esta técnica se aplica en la producción de envases metálicos, depósitos industriales, carcasas de electrodomésticos, tanques de presión, utensilios de cocina y componentes críticos, donde la precisión dimensional, la uniformidad y la calidad superficial son determinantes para la funcionalidad, seguridad y estética del producto. La lubricación adecuada facilita el flujo homogéneo del material, protege herramientas, prolonga la vida útil de la máquina y mejora la eficiencia energética del proceso, asegurando un rendimiento constante y estable en cada ciclo.
Las máquinas de estampación y embutido pueden ser mecánicas, hidráulicas o servo-hidráulicas, adaptándose a distintos requerimientos de producción y materiales. Las prensas mecánicas permiten ciclos rápidos, ideales para piezas simples, aunque ofrecen control limitado de fuerza. Las prensas hidráulicas proporcionan presión constante y uniforme, necesarias para piezas complejas o materiales resistentes, aunque requieren mayor mantenimiento y ciclos más lentos. Las servo-prensas permiten control total del perfil de fuerza y velocidad del punzón, ajustando dinámicamente cada fase del ciclo, almacenando configuraciones específicas para distintos materiales y geometrías, optimizando uniformidad, precisión y vida útil de punzones y matrices, permitiendo la producción de grandes volúmenes de piezas complejas con estándares industriales exigentes.
La incorporación de sistemas de visión artificial y monitoreo en tiempo real permite detectar cualquier irregularidad, como arrugas, pliegues, fisuras, burbujas o desviaciones dimensionales, y ajustar automáticamente parámetros como presión, velocidad o trayectoria del punzón, asegurando uniformidad y calidad en cada pieza. Esta trazabilidad es esencial en sectores de alta exigencia, como automoción, aeronáutica, electrodomésticos y envases metálicos, donde la precisión y resistencia de cada componente son críticas. La recopilación y análisis de datos facilita el mantenimiento predictivo, optimiza los ciclos de producción, reduce desperdicio de material y mejora la eficiencia energética de la planta, asegurando continuidad operativa y confiabilidad en la fabricación de piezas críticas de gran volumen.
En conjunto, la máquina de estampación y embutido constituye un equipo integral, estratégico y altamente versátil que combina corte, conformado, embutición, redibujo progresivo, control de fuerza y velocidad, lubricación controlada, automatización avanzada y sistemas de inspección en tiempo real, optimizando recursos, reduciendo desperdicio y aumentando la productividad industrial. Su capacidad para trabajar con distintos materiales, espesores y geometrías, producir piezas tridimensionales con paredes uniformes, acabados precisos y alta resistencia estructural, y su integración con sistemas de control centralizado y robótica para alimentación y extracción de chapas permite mantener los más altos estándares de calidad y precisión en la manufactura de piezas metálicas complejas. Estas tecnologías garantizan que la máquina sea un pilar fundamental en líneas de producción modernas, capaces de operar con eficiencia máxima, garantizar calidad constante y producir grandes volúmenes de piezas críticas sin comprometer uniformidad, integridad estructural ni acabado superficial, consolidándose como un elemento clave para la competitividad y sostenibilidad industrial.
Prensa para Estirado de Metales
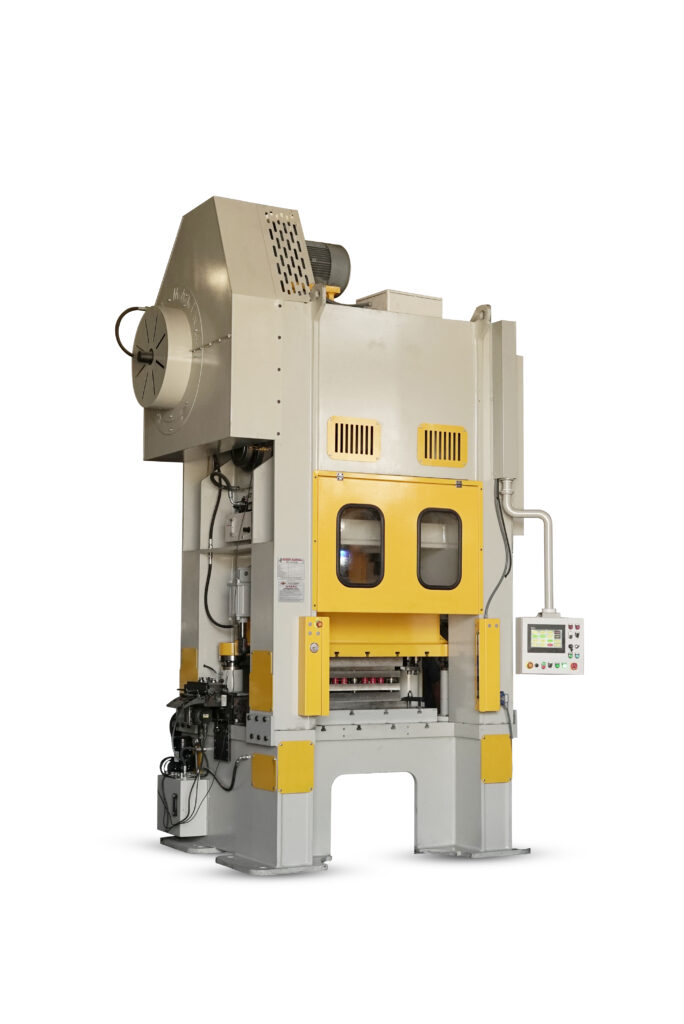
La prensa para estirado de metales es un equipo industrial diseñado específicamente para transformar láminas, chapas o planchas metálicas en piezas cilíndricas, cónicas o huecas con alta precisión dimensional y uniformidad de espesor mediante el proceso de estirado, que consiste en deformar el material forzándolo a adaptarse a la forma de un troquel mediante la acción de un punzón o matriz, controlando cuidadosamente el flujo del metal para evitar arrugas, pliegues, fisuras o variaciones de espesor. Este tipo de prensa se utiliza ampliamente en sectores como la automoción, la aeronáutica, la fabricación de envases metálicos, depósitos industriales, electrodomésticos, utensilios de cocina y componentes estructurales, donde la precisión, la integridad estructural y la calidad superficial de cada pieza son determinantes para la funcionalidad y la seguridad del producto. La prensa combina punzones, matrices, cojines de sujeción y sistemas de lubricación para asegurar un estirado controlado y uniforme; los punzones aplican la fuerza necesaria para deformar la chapa, las matrices guían el flujo del material y los cojines regulan la presión sobre los bordes, evitando concentraciones de tensión y permitiendo un estirado homogéneo a lo largo de toda la pieza, mientras que la lubricación facilita el deslizamiento del metal, protege las herramientas y prolonga la vida útil del equipo.
El control de parámetros en una prensa de estirado es fundamental para garantizar la repetibilidad y la calidad de cada pieza. La fuerza aplicada por el punzón, la presión de los cojines, la velocidad de estirado, el tipo y la cantidad de lubricante, así como la temperatura del material en algunos casos, se ajustan de forma precisa según el tipo de metal, su espesor y la geometría de la pieza. Las prensas modernas incorporan sistemas de control digital que monitorean en tiempo real fuerza, desplazamiento, velocidad, fricción y temperatura, permitiendo ajustes automáticos durante cada ciclo y optimizando el flujo del material para minimizar defectos y asegurar uniformidad dimensional. La simulación por elementos finitos y el modelado del flujo del metal permiten anticipar el comportamiento de la chapa durante el estirado, optimizando el diseño de punzones y matrices, identificando posibles concentraciones de tensión y determinando la necesidad de estirado en varias etapas o mediante redibujo progresivo, reduciendo desperdicio de material y costos asociados a ensayos físicos, y acelerando la puesta en marcha de la producción.
El estirado progresivo es una técnica que permite obtener piezas de gran altura relativa o geometrías complejas sin comprometer la integridad del material. Cada etapa del estirado ajusta parámetros como fuerza, velocidad, radio de matriz y lubricación, garantizando que las paredes de la pieza mantengan un espesor uniforme y que la geometría final cumpla con los requisitos funcionales y estructurales. Esta técnica se aplica en la fabricación de envases metálicos, depósitos de presión, componentes estructurales, utensilios de cocina y carcasas de electrodomésticos, donde la precisión dimensional, la uniformidad de espesor y la calidad superficial son esenciales para la funcionalidad, seguridad y estética del producto. La lubricación controlada reduce la fricción, protege las herramientas y prolonga la vida útil de la prensa, mejorando la eficiencia energética del proceso y asegurando un rendimiento constante en cada ciclo de producción.
Las prensas para estirado de metales pueden ser mecánicas, hidráulicas o servo-hidráulicas, adaptándose a distintos requerimientos de producción y materiales. Las prensas mecánicas permiten ciclos rápidos, ideales para piezas simples o de producción en masa, aunque ofrecen un control limitado de la fuerza aplicada durante el recorrido. Las prensas hidráulicas proporcionan presión constante y uniforme, necesarias para materiales más resistentes o piezas de geometría compleja, aunque sus ciclos son más lentos y requieren mantenimiento periódico. Las servo-prensas permiten un control total del perfil de fuerza y velocidad, ajustando dinámicamente cada fase del ciclo, almacenando configuraciones específicas para distintos materiales, espesores y geometrías, optimizando uniformidad, precisión y prolongando la vida útil de punzones y matrices, permitiendo la producción de grandes volúmenes de piezas complejas cumpliendo con los estándares más exigentes de la industria.
La incorporación de sistemas de visión artificial y monitoreo en tiempo real añade una capa adicional de control y trazabilidad, permitiendo detectar arrugas, pliegues, fisuras, burbujas o desviaciones dimensionales, y ajustar automáticamente parámetros como presión, velocidad o trayectoria del punzón, asegurando uniformidad y calidad de cada pieza. Esta trazabilidad es fundamental en sectores de alta exigencia como la automoción, aeronáutica, electrodomésticos y envases metálicos, donde cada componente debe cumplir estrictos estándares de calidad y resistencia estructural. La recopilación y análisis de datos también facilita implementar mantenimiento predictivo, optimizar ciclos de producción, reducir desperdicio de material y mejorar la eficiencia energética de la planta, asegurando continuidad operativa y confiabilidad en la fabricación de piezas críticas de gran volumen.
En conjunto, la prensa para estirado de metales constituye un equipo integral, estratégico y altamente versátil que combina estirado progresivo, control de fuerza y velocidad, lubricación controlada, automatización avanzada y sistemas de inspección en tiempo real. Su capacidad para trabajar con distintos materiales, espesores y geometrías, producir piezas tridimensionales con paredes uniformes, acabados precisos y alta resistencia estructural, y su integración con sistemas de control centralizado y robótica para alimentación y extracción de chapas permite optimizar recursos, reducir desperdicio y aumentar la productividad industrial, manteniendo los más altos estándares de calidad y precisión en la manufactura de piezas metálicas complejas. Esta combinación de tecnologías asegura que la prensa de estirado de metales sea un pilar fundamental en líneas de producción modernas, capaces de operar con eficiencia máxima, garantizar calidad constante y producir grandes volúmenes de piezas críticas sin comprometer uniformidad, integridad estructural ni acabado superficial.
La prensa para estirado de metales, cuando se integra en líneas de producción totalmente automatizadas, se convierte en un elemento central para la fabricación de piezas metálicas tridimensionales complejas con precisión extrema, uniformidad de espesor y acabados superficiales consistentes, incluso en geometrías difíciles o materiales con ductilidad limitada. Estas líneas combinan alimentación automática de chapas, troquelado preliminar, estirado progresivo, redibujo, lubricación controlada y extracción de piezas terminadas, todo coordinado mediante sistemas de control digital avanzado y robótica, garantizando que cada componente cumpla con tolerancias estrictas, mantenga espesor uniforme y presente acabados homogéneos sin defectos como arrugas, pliegues, fisuras o deformaciones irregulares. Los punzones aplican la fuerza necesaria para deformar la chapa y darle forma, las matrices guían el flujo del material para que se adapte perfectamente a la geometría deseada, los cojines de sujeción controlan la presión sobre los bordes evitando concentraciones de tensión, y los sistemas de lubricación aseguran un deslizamiento uniforme del metal, protegiendo las herramientas y prolongando la vida útil de la prensa mientras se mantiene la eficiencia del proceso y la constancia de calidad en cada ciclo de producción.
El control de parámetros en la prensa para estirado de metales es determinante para la calidad y repetibilidad de las piezas. La fuerza del punzón, la presión de los cojines, la velocidad de estirado, el tipo y cantidad de lubricante, así como la temperatura del material en algunos casos, se ajustan de manera precisa según el tipo de metal, su espesor y la complejidad geométrica de la pieza. Los sistemas de control avanzados monitorean en tiempo real fuerza, desplazamiento, velocidad, fricción y temperatura, realizando ajustes automáticos durante cada ciclo para optimizar el flujo del material, minimizar defectos y asegurar uniformidad dimensional en todas las piezas. La simulación por elementos finitos permite anticipar el comportamiento del metal durante el estirado, optimizando el diseño de punzones y matrices, detectando concentraciones de tensión y determinando la necesidad de múltiples etapas de estirado o redibujo progresivo, lo que reduce desperdicio de material y ensayos físicos costosos, agilizando la puesta en marcha de la línea de producción y aumentando la eficiencia general del proceso.
El estirado progresivo es fundamental para piezas con relaciones altura-diámetro elevadas o geometrías complejas. Cada etapa del estirado ajusta fuerza, velocidad, radio de matriz y lubricación, asegurando que las paredes de la pieza mantengan un espesor uniforme y que la pieza final cumpla con los requerimientos estructurales, funcionales y estéticos. Esta técnica se aplica en la fabricación de envases metálicos, depósitos industriales, carcasas de electrodomésticos, tanques de presión, utensilios de cocina y componentes críticos de maquinaria industrial, donde la precisión dimensional, la uniformidad y la calidad superficial determinan la funcionalidad, seguridad y estética del producto. La lubricación adecuada facilita un flujo homogéneo del metal, protege herramientas, prolonga la vida útil de la prensa y mejora la eficiencia energética del proceso, garantizando ciclos de producción estables y consistentes.
Las prensas para estirado de metales pueden ser mecánicas, hidráulicas o servo-hidráulicas, adaptándose a distintos requerimientos de producción y materiales. Las prensas mecánicas permiten ciclos rápidos y son ideales para piezas simples, aunque su control de fuerza es limitado. Las prensas hidráulicas proporcionan presión constante y uniforme, necesarias para piezas de geometría compleja o materiales más resistentes, aunque sus ciclos son más lentos y requieren mayor mantenimiento. Las servo-prensas permiten un control total del perfil de fuerza y velocidad del punzón, ajustando dinámicamente cada fase del ciclo, almacenando configuraciones específicas para distintos materiales, espesores y geometrías, optimizando uniformidad, precisión y prolongando la vida útil de punzones y matrices, permitiendo la producción de grandes volúmenes de piezas complejas con los estándares más exigentes de la industria.
La incorporación de sistemas de visión artificial y monitoreo en tiempo real añade control y trazabilidad adicionales, permitiendo detectar arrugas, pliegues, fisuras, burbujas o desviaciones dimensionales, y ajustar automáticamente parámetros como presión, velocidad o trayectoria del punzón, asegurando uniformidad y calidad en cada pieza. Esta trazabilidad es crucial en sectores de alta exigencia como automoción, aeronáutica, electrodomésticos y envases metálicos, donde cada componente debe cumplir estrictos estándares de calidad y resistencia estructural. La recopilación y análisis de datos permite implementar mantenimiento predictivo, optimizar ciclos de producción, reducir desperdicio de material y mejorar la eficiencia energética de la planta, asegurando continuidad operativa y confiabilidad en la fabricación de piezas críticas de gran volumen.
En conjunto, la prensa para estirado de metales constituye un equipo integral, estratégico y altamente versátil que combina estirado progresivo, control de fuerza y velocidad, lubricación controlada, automatización avanzada y sistemas de inspección en tiempo real, optimizando recursos, reduciendo desperdicio y aumentando la productividad industrial. Su capacidad para trabajar con distintos materiales, espesores y geometrías, producir piezas tridimensionales con paredes uniformes, acabados precisos y alta resistencia estructural, y su integración con sistemas de control centralizado y robótica para alimentación y extracción de chapas, permite mantener los más altos estándares de calidad y precisión en la manufactura de piezas metálicas complejas. Estas tecnologías aseguran que la prensa de estirado de metales sea un pilar fundamental en líneas de producción modernas, capaces de operar con eficiencia máxima, garantizar calidad constante y producir grandes volúmenes de piezas críticas sin comprometer uniformidad, integridad estructural ni acabado superficial, consolidándose como un elemento esencial para la competitividad y sostenibilidad de la producción industrial.
La prensa para estirado de metales, cuando se incorpora en líneas de producción automatizadas de alto rendimiento, se convierte en un componente central para la manufactura de piezas metálicas tridimensionales complejas, donde cada etapa del proceso está cuidadosamente diseñada para garantizar precisión dimensional, uniformidad de espesor y acabados superficiales consistentes, incluso en geometrías complicadas o en materiales de ductilidad limitada. Estas líneas integran alimentación automática de chapas, corte preliminar, estirado progresivo, redibujo, lubricación controlada y extracción de piezas terminadas, todo coordinado mediante sistemas de control digital avanzado y robótica, de modo que cada pieza cumpla con tolerancias estrictas, mantenga espesor uniforme y presente acabados homogéneos sin arrugas, pliegues, fisuras ni deformaciones. Los punzones aplican la fuerza exacta para deformar la chapa según la geometría requerida, las matrices guían el flujo del material evitando concentraciones de tensión, los cojines de sujeción regulan la presión sobre los bordes y los sistemas de lubricación permiten un deslizamiento uniforme del metal, protegiendo las herramientas y prolongando la vida útil de la prensa mientras se mantiene eficiencia y consistencia en cada ciclo de producción.
El control de parámetros es esencial para garantizar la calidad y repetibilidad de las piezas. La fuerza aplicada por el punzón, la presión de los cojines, la velocidad de estirado, la cantidad y tipo de lubricante, y en algunos casos la temperatura del material, se ajustan con precisión según el tipo de metal, su espesor y la complejidad geométrica de la pieza. Los sistemas de control avanzados monitorean en tiempo real fuerza, desplazamiento, velocidad, fricción y temperatura, permitiendo ajustes automáticos durante el ciclo, optimizando el flujo del material, minimizando defectos y asegurando uniformidad dimensional en todas las piezas producidas. La simulación por elementos finitos y el modelado del flujo del metal permiten anticipar el comportamiento de la chapa antes de la producción, optimizando punzones y matrices, detectando concentraciones de tensión y determinando la necesidad de múltiples etapas de estirado o redibujo progresivo, reduciendo desperdicio de material, costos de ensayo físico y tiempo de puesta en marcha de la línea de producción, aumentando así la eficiencia global del proceso.
El estirado progresivo es imprescindible para piezas con relaciones altura-diámetro elevadas o geometrías complejas. Cada etapa del estirado ajusta parámetros como fuerza, velocidad, radio de matriz y lubricación, asegurando que las paredes de la pieza mantengan espesor uniforme y que la pieza final cumpla con los requerimientos estructurales, funcionales y estéticos. Esta técnica se aplica en envases metálicos, depósitos industriales, carcasas de electrodomésticos, tanques de presión, utensilios de cocina y componentes críticos de maquinaria industrial, donde la precisión dimensional, la uniformidad y la calidad superficial determinan la funcionalidad, seguridad y estética del producto. La lubricación adecuada facilita el flujo homogéneo del metal, protege herramientas, prolonga la vida útil de la prensa y mejora la eficiencia energética del proceso, asegurando ciclos de producción estables y consistentes sin interrupciones ni defectos.
Las prensas para estirado de metales pueden ser mecánicas, hidráulicas o servo-hidráulicas, adaptándose a distintos requerimientos de producción y materiales. Las prensas mecánicas permiten ciclos rápidos, ideales para piezas simples o producción en masa, aunque con control limitado de fuerza. Las prensas hidráulicas proporcionan presión constante y uniforme, necesarias para piezas de geometría compleja o materiales resistentes, aunque sus ciclos son más lentos y requieren mantenimiento periódico. Las servo-prensas permiten control total del perfil de fuerza y velocidad del punzón, ajustando dinámicamente cada fase del ciclo, almacenando configuraciones específicas para distintos materiales, espesores y geometrías, optimizando uniformidad, precisión y prolongando la vida útil de punzones y matrices, permitiendo la producción de grandes volúmenes de piezas complejas cumpliendo los estándares más exigentes de la industria.
La incorporación de sistemas de visión artificial y monitoreo en tiempo real agrega control y trazabilidad adicionales, detectando arrugas, pliegues, fisuras, burbujas o desviaciones dimensionales, y ajustando automáticamente parámetros como presión, velocidad o trayectoria del punzón, asegurando uniformidad y calidad en cada pieza. Esta trazabilidad es crucial en sectores de alta exigencia como automoción, aeronáutica, electrodomésticos y envases metálicos, donde cada componente debe cumplir estrictos estándares de calidad y resistencia estructural. La recopilación y análisis de datos permiten implementar mantenimiento predictivo, optimizar ciclos de producción, reducir desperdicio de material y mejorar la eficiencia energética de la planta, asegurando continuidad operativa y confiabilidad en la fabricación de piezas críticas de gran volumen.
En conjunto, la prensa para estirado de metales constituye un equipo integral, estratégico y altamente versátil que combina estirado progresivo, control de fuerza y velocidad, lubricación controlada, automatización avanzada y sistemas de inspección en tiempo real, optimizando recursos, reduciendo desperdicio y aumentando la productividad industrial. Su capacidad para trabajar con distintos materiales, espesores y geometrías, producir piezas tridimensionales con paredes uniformes, acabados precisos y alta resistencia estructural, y su integración con sistemas de control centralizado y robótica para alimentación y extracción de chapas, permite mantener los más altos estándares de calidad y precisión en la manufactura de piezas metálicas complejas. Estas tecnologías garantizan que la prensa de estirado de metales sea un pilar fundamental en líneas de producción modernas, capaces de operar con eficiencia máxima, garantizar calidad constante y producir grandes volúmenes de piezas críticas sin comprometer uniformidad, integridad estructural ni acabado superficial, consolidándose como un elemento esencial para la competitividad, sostenibilidad y rentabilidad de la producción industrial.
La prensa para estirado de metales, cuando se incorpora en líneas de producción totalmente automatizadas, se convierte en un eje estratégico dentro de la manufactura industrial de piezas metálicas complejas, permitiendo transformar láminas, chapas o planchas en componentes tridimensionales con alta precisión dimensional, uniformidad de espesor y acabados superficiales impecables, incluso en piezas de geometría complicada o con materiales de ductilidad limitada. Estas líneas de producción integran sistemas de alimentación automática de chapas, corte preliminar, estirado progresivo, redibujo, lubricación controlada y extracción automatizada de piezas terminadas, todos sincronizados mediante control digital avanzado y robótica, garantizando que cada componente mantenga tolerancias estrictas, espesor uniforme y acabados homogéneos sin arrugas, pliegues, fisuras ni deformaciones. Los punzones aplican la fuerza necesaria para deformar el metal, las matrices guían el flujo del material asegurando que siga la forma deseada, los cojines de sujeción controlan la presión sobre los bordes evitando concentraciones de tensión, y los sistemas de lubricación facilitan el desplazamiento uniforme del metal, protegen las herramientas y prolongan la vida útil de la prensa, asegurando consistencia y eficiencia en cada ciclo de producción.
El control preciso de parámetros es determinante para la calidad y repetibilidad de cada pieza. La fuerza del punzón, la presión de los cojines, la velocidad de estirado, la cantidad y tipo de lubricante y, en algunos casos, la temperatura del material se ajustan de manera exacta según el tipo de metal, su espesor y la complejidad geométrica de la pieza. Los sistemas de control avanzado monitorean en tiempo real fuerza, desplazamiento, velocidad, fricción y temperatura, realizando ajustes automáticos durante cada ciclo para optimizar el flujo del metal, minimizar defectos y garantizar uniformidad dimensional. La simulación por elementos finitos permite anticipar el comportamiento del metal antes de la producción, optimizando el diseño de punzones y matrices, detectando concentraciones de tensión y determinando la necesidad de múltiples etapas de estirado o redibujo progresivo, reduciendo desperdicio de material, costos de ensayo físico y tiempo de puesta en marcha de la línea de producción, incrementando la eficiencia global del proceso.
El estirado progresivo resulta imprescindible para piezas con relaciones altura-diámetro elevadas o geometrías complejas, ya que cada etapa ajusta parámetros como fuerza, velocidad, radio de matriz y lubricación, garantizando que las paredes de la pieza mantengan espesor uniforme y que la geometría final cumpla con los requerimientos funcionales, estructurales y estéticos. Esta técnica se aplica en la fabricación de envases metálicos, depósitos industriales, carcasas de electrodomésticos, tanques de presión, utensilios de cocina y componentes críticos de maquinaria industrial, donde la precisión dimensional, la uniformidad de espesor y la calidad superficial determinan la funcionalidad, seguridad y apariencia del producto. La lubricación controlada facilita un flujo homogéneo del metal, protege las herramientas, prolonga la vida útil de la prensa y mejora la eficiencia energética del proceso, garantizando ciclos de producción estables y continuos sin interrupciones ni defectos.
Las prensas para estirado de metales pueden ser mecánicas, hidráulicas o servo-hidráulicas, cada una adaptándose a diferentes necesidades de producción y tipos de material. Las prensas mecánicas permiten ciclos rápidos, ideales para piezas simples o producción en masa, aunque ofrecen un control limitado de la fuerza aplicada. Las prensas hidráulicas proporcionan presión constante y uniforme, necesarias para piezas de geometría compleja o materiales más resistentes, aunque sus ciclos son más lentos y requieren mantenimiento frecuente. Las servo-prensas permiten un control total del perfil de fuerza y velocidad del punzón, ajustando dinámicamente cada fase del ciclo, almacenando configuraciones específicas para distintos materiales, espesores y geometrías, optimizando uniformidad, precisión y prolongando la vida útil de punzones y matrices, lo que permite producir grandes volúmenes de piezas complejas cumpliendo con los estándares más exigentes de la industria.
La incorporación de sistemas de visión artificial y monitoreo en tiempo real permite una trazabilidad completa, detectando arrugas, pliegues, fisuras, burbujas o desviaciones dimensionales, y ajustando automáticamente parámetros como presión, velocidad o trayectoria del punzón, asegurando uniformidad y calidad en cada pieza. Este control es vital en industrias de alta exigencia como automoción, aeronáutica, electrodomésticos y envases metálicos, donde la precisión y resistencia de cada componente son fundamentales. La recopilación y análisis de datos permite implementar mantenimiento predictivo, optimizar ciclos de producción, reducir desperdicio de material y mejorar la eficiencia energética de la planta, asegurando continuidad operativa y confiabilidad en la fabricación de piezas críticas de gran volumen.
En su conjunto, la prensa para estirado de metales es un equipo integral y estratégico que combina estirado progresivo, control de fuerza y velocidad, lubricación controlada, automatización avanzada y sistemas de inspección en tiempo real, optimizando recursos, reduciendo desperdicio y aumentando la productividad industrial. Su capacidad para trabajar con distintos materiales, espesores y geometrías, producir piezas tridimensionales con paredes uniformes, acabados precisos y alta resistencia estructural, y su integración con sistemas de control centralizado y robótica para alimentación y extracción de chapas, permite mantener los más altos estándares de calidad y precisión en la manufactura de piezas metálicas complejas. Estas tecnologías aseguran que la prensa de estirado de metales sea un pilar fundamental en líneas de producción modernas, capaces de operar con eficiencia máxima, garantizar calidad constante y producir grandes volúmenes de piezas críticas sin comprometer uniformidad, integridad estructural ni acabado superficial, consolidándose como un elemento esencial para la competitividad, sostenibilidad y rentabilidad de la producción industrial.
Si quieres, puedo continuar ampliando el texto para detallar cómo se sincronizan múltiples prensas de estirado en una línea automatizada completa, integrando robótica avanzada, control centralizado de parámetros, inspección automática de calidad, gestión de inventario de materias primas y optimización del flujo de materiales para máxima eficiencia y productividad industrial.
Prensa para Formado de Chapas
La prensa para formado de chapas es un equipo industrial fundamental diseñado para transformar láminas metálicas planas en piezas tridimensionales con geometrías complejas, manteniendo uniformidad de espesor, precisión dimensional y calidad superficial en cada componente. Este tipo de prensa aplica fuerza controlada mediante punzones y matrices, guiando el flujo del metal para conformar la chapa según la forma deseada, mientras los cojines de sujeción regulan la presión sobre los bordes, evitando arrugas, pliegues, fisuras o deformaciones irregulares que puedan comprometer la integridad del material o la funcionalidad de la pieza. La prensa puede operar con distintos tipos de metales, incluyendo acero, aluminio, cobre y aleaciones, y es ampliamente utilizada en sectores como automoción, aeronáutica, electrodomésticos, envases metálicos, utensilios de cocina y componentes industriales, donde la precisión, resistencia y acabado superficial son esenciales. La lubricación controlada facilita el flujo del material, protege herramientas y prolonga la vida útil de la máquina, asegurando ciclos de producción consistentes y de alta calidad.
El control de parámetros es crítico en una prensa de formado de chapas para garantizar la repetibilidad y la uniformidad de cada pieza. La fuerza del punzón, la presión de los cojines, la velocidad de conformado, el tipo y cantidad de lubricante y, en algunos casos, la temperatura de la chapa se ajustan según el material, el espesor y la complejidad de la pieza. Las prensas modernas incorporan sistemas de control digital que monitorean en tiempo real fuerza, desplazamiento, velocidad, fricción y temperatura, permitiendo ajustes automáticos durante cada ciclo y optimizando el flujo del material, minimizando defectos y asegurando uniformidad dimensional y acabado superficial en todas las piezas producidas. La simulación por elementos finitos y el modelado del flujo del metal permiten anticipar el comportamiento de la chapa, optimizar el diseño de punzones y matrices, detectar concentraciones de tensión y determinar la necesidad de conformado en varias etapas, reduciendo desperdicio de material y costos de ensayo físico y acelerando la puesta en marcha de la producción.
El conformado progresivo es una técnica esencial en la prensa de formado de chapas, especialmente para piezas con geometrías complejas o relaciones altura-diámetro elevadas, ya que permite controlar el flujo del material a lo largo de múltiples etapas, ajustando fuerza, velocidad, radios de matriz y lubricación en cada fase. Esto asegura que las paredes de la pieza mantengan un espesor uniforme y que la pieza final cumpla con los requisitos funcionales, estructurales y estéticos. La prensa puede producir envases metálicos, depósitos industriales, carcasas de electrodomésticos, tanques de presión, utensilios de cocina y componentes críticos, donde la precisión dimensional, la uniformidad y la calidad superficial determinan la funcionalidad, seguridad y apariencia del producto. La lubricación controlada facilita el desplazamiento homogéneo del metal, protege las herramientas, prolonga la vida útil de la prensa y mejora la eficiencia energética del proceso, garantizando ciclos de producción estables y consistentes.
Las prensas para formado de chapas pueden ser mecánicas, hidráulicas o servo-hidráulicas, adaptándose a distintos requerimientos de producción y materiales. Las prensas mecánicas permiten ciclos rápidos y son ideales para piezas simples o producción en masa, aunque el control de la fuerza aplicada es limitado. Las prensas hidráulicas proporcionan presión constante y uniforme, necesarias para piezas de geometría compleja o materiales resistentes, aunque sus ciclos son más lentos y requieren mantenimiento frecuente. Las servo-prensas permiten control total del perfil de fuerza y velocidad del punzón, ajustando dinámicamente cada fase del ciclo, almacenando configuraciones específicas para distintos materiales, espesores y geometrías, optimizando uniformidad, precisión y prolongando la vida útil de punzones y matrices, permitiendo la producción de grandes volúmenes de piezas complejas cumpliendo los estándares más exigentes de la industria.
La incorporación de sistemas de visión artificial y monitoreo en tiempo real permite detectar arrugas, pliegues, fisuras, burbujas o desviaciones dimensionales y ajustar automáticamente parámetros como presión, velocidad o trayectoria del punzón, asegurando uniformidad y calidad en cada pieza. Esta trazabilidad es fundamental en sectores de alta exigencia como automoción, aeronáutica, electrodomésticos y envases metálicos, donde la precisión y resistencia de cada componente son determinantes. La recopilación y análisis de datos permite implementar mantenimiento predictivo, optimizar ciclos de producción, reducir desperdicio de material y mejorar la eficiencia energética de la planta, garantizando continuidad operativa y confiabilidad en la fabricación de piezas críticas de gran volumen.
En conjunto, la prensa para formado de chapas constituye un equipo integral, estratégico y altamente versátil que combina conformado progresivo, control de fuerza y velocidad, lubricación controlada, automatización avanzada y sistemas de inspección en tiempo real, optimizando recursos, reduciendo desperdicio y aumentando la productividad industrial. Su capacidad para trabajar con distintos materiales, espesores y geometrías, producir piezas tridimensionales con paredes uniformes, acabados precisos y alta resistencia estructural, y su integración con sistemas de control centralizado y robótica para alimentación y extracción de chapas, permite mantener los más altos estándares de calidad y precisión en la manufactura de piezas metálicas complejas. Estas características aseguran que la prensa para formado de chapas sea un pilar fundamental en líneas de producción modernas, capaces de operar con eficiencia máxima, garantizar calidad constante y producir grandes volúmenes de piezas críticas sin comprometer uniformidad, integridad estructural ni acabado superficial, consolidándose como un elemento esencial para la competitividad y sostenibilidad industrial.
La prensa para formado de chapas, cuando se integra en una línea de producción completamente automatizada, se convierte en el núcleo estratégico de la manufactura de piezas metálicas tridimensionales complejas, permitiendo transformar láminas y chapas planas en componentes con geometrías sofisticadas, manteniendo uniformidad de espesor, precisión dimensional y acabados superficiales impecables en cada pieza. Estas líneas combinan alimentación automática de chapas, corte preliminar, conformado progresivo, estirado, redibujo, lubricación controlada y extracción automatizada de las piezas terminadas, todo sincronizado mediante sistemas de control digital avanzado y robótica, de manera que cada componente cumpla con tolerancias estrictas, conserve espesor uniforme y presente acabados homogéneos sin arrugas, pliegues, fisuras o deformaciones. Los punzones aplican la fuerza exacta para moldear el metal según la forma deseada, las matrices guían el flujo del material evitando concentraciones de tensión, los cojines de sujeción regulan la presión sobre los bordes y los sistemas de lubricación facilitan el desplazamiento uniforme del metal, protegiendo las herramientas y prolongando la vida útil de la prensa mientras se garantiza eficiencia y constancia en cada ciclo de producción.
El control de parámetros es crítico para asegurar la calidad y repetibilidad de cada pieza. La fuerza aplicada por el punzón, la presión de los cojines, la velocidad de conformado, el tipo y cantidad de lubricante y, en ocasiones, la temperatura de la chapa se ajustan de manera precisa según el material, el espesor y la complejidad de la geometría de la pieza. Los sistemas de control avanzado monitorean en tiempo real fuerza, desplazamiento, velocidad, fricción y temperatura, permitiendo ajustes automáticos durante cada ciclo para optimizar el flujo del material, minimizar defectos y asegurar uniformidad dimensional y acabado superficial en todas las piezas producidas. La simulación por elementos finitos permite anticipar el comportamiento del metal antes de la producción, optimizar el diseño de punzones y matrices, detectar concentraciones de tensión y determinar la necesidad de múltiples etapas de conformado o redibujo progresivo, reduciendo desperdicio de material, costos de ensayo físico y tiempo de puesta en marcha, incrementando así la eficiencia global del proceso y asegurando resultados consistentes en toda la línea de producción.
El conformado progresivo es esencial en la prensa para chapas, especialmente para piezas con relaciones altura-diámetro elevadas o geometrías complejas, ya que permite controlar el flujo del metal a lo largo de varias etapas, ajustando fuerza, velocidad, radios de matriz y lubricación en cada fase. Esto asegura que las paredes de la pieza mantengan espesor uniforme y que la geometría final cumpla con los requerimientos funcionales, estructurales y estéticos. Este método se aplica en la fabricación de envases metálicos, depósitos industriales, carcasas de electrodomésticos, tanques de presión, utensilios de cocina y componentes críticos de maquinaria industrial, donde la precisión dimensional, la uniformidad y la calidad superficial determinan la funcionalidad, seguridad y apariencia del producto. La lubricación controlada facilita un flujo homogéneo del metal, protege herramientas, prolonga la vida útil de la prensa y mejora la eficiencia energética del proceso, asegurando ciclos de producción estables, continuos y de alta calidad.
Las prensas para formado de chapas pueden ser mecánicas, hidráulicas o servo-hidráulicas, adaptándose a distintos requerimientos de producción y materiales. Las prensas mecánicas permiten ciclos rápidos, ideales para piezas simples o producción en masa, aunque su control de fuerza es limitado. Las prensas hidráulicas proporcionan presión constante y uniforme, necesarias para piezas de geometría compleja o materiales resistentes, aunque requieren ciclos más lentos y mantenimiento frecuente. Las servo-prensas permiten un control total del perfil de fuerza y velocidad del punzón, ajustando dinámicamente cada fase del ciclo, almacenando configuraciones específicas para distintos materiales, espesores y geometrías, optimizando uniformidad, precisión y prolongando la vida útil de punzones y matrices, lo que permite producir grandes volúmenes de piezas complejas cumpliendo los estándares más exigentes de la industria.
La incorporación de sistemas de visión artificial y monitoreo en tiempo real agrega control y trazabilidad adicionales, detectando arrugas, pliegues, fisuras, burbujas o desviaciones dimensionales y ajustando automáticamente parámetros como presión, velocidad o trayectoria del punzón, asegurando uniformidad y calidad en cada pieza. Esta trazabilidad es vital en industrias de alta exigencia como automoción, aeronáutica, electrodomésticos y envases metálicos, donde la precisión y resistencia de cada componente son determinantes. La recopilación y análisis de datos permite implementar mantenimiento predictivo, optimizar ciclos de producción, reducir desperdicio de material y mejorar la eficiencia energética de la planta, garantizando continuidad operativa y confiabilidad en la fabricación de piezas críticas de gran volumen.
En conjunto, la prensa para formado de chapas constituye un equipo integral, estratégico y altamente versátil que combina conformado progresivo, control de fuerza y velocidad, lubricación controlada, automatización avanzada y sistemas de inspección en tiempo real, optimizando recursos, reduciendo desperdicio y aumentando la productividad industrial. Su capacidad para trabajar con distintos materiales, espesores y geometrías, producir piezas tridimensionales con paredes uniformes, acabados precisos y alta resistencia estructural, y su integración con sistemas de control centralizado y robótica para alimentación y extracción de chapas, permite mantener los más altos estándares de calidad y precisión en la manufactura de piezas metálicas complejas. Estas características aseguran que la prensa para formado de chapas sea un pilar fundamental en líneas de producción modernas, capaces de operar con eficiencia máxima, garantizar calidad constante y producir grandes volúmenes de piezas críticas sin comprometer uniformidad, integridad estructural ni acabado superficial, consolidándose como un elemento esencial para la competitividad, sostenibilidad y rentabilidad de la producción industrial.
La prensa para formado de chapas, en el contexto de la industria moderna, se ha convertido en un equipo imprescindible para la fabricación de componentes metálicos que requieren no solo alta precisión geométrica sino también una resistencia estructural controlada y un acabado superficial impecable. Cuando este tipo de prensa se integra en plantas industriales que trabajan con grandes volúmenes de producción, su función no se limita simplemente a aplicar fuerza sobre una lámina metálica, sino que se convierte en un sistema complejo de transformación en el que intervienen múltiples variables físicas, mecánicas y de control digital, todas interconectadas y reguladas en tiempo real. El proceso comienza con la alimentación de chapas que son previamente seleccionadas y acondicionadas en función de su espesor, composición y tratamiento superficial, de manera que se garantice que cada pieza responda de forma uniforme durante el ciclo de conformado. A partir de ese punto, la prensa aplica un movimiento controlado del punzón sobre la chapa que es sostenida y guiada por la matriz, de modo que el material fluye hacia la cavidad siguiendo trayectorias cuidadosamente definidas para evitar zonas de acumulación de tensión, fisuras, pliegues o adelgazamientos irregulares que comprometerían la calidad de la pieza final.
El control de parámetros en este proceso es extremadamente sofisticado, pues no basta con aplicar una fuerza de manera continua, sino que cada etapa del ciclo exige ajustes dinámicos en la velocidad del punzón, la presión ejercida por los cojines de sujeción, la lubricación del contacto entre chapa, punzón y matriz, e incluso, en determinados casos, el control de la temperatura del material para facilitar el flujo plástico del metal. Este nivel de control solo es posible gracias a sistemas hidráulicos, servoaccionamientos eléctricos y sensores de alta precisión que capturan datos en tiempo real sobre carga, desplazamiento, fricción, vibración y temperatura, transmitiéndolos a unidades de control computarizado capaces de procesar la información y realizar ajustes instantáneos para mantener la estabilidad del proceso. Este tipo de retroalimentación inmediata asegura no solo la uniformidad entre piezas consecutivas, sino también la optimización del consumo energético, la reducción de desperdicio de materia prima y la prolongación de la vida útil de las herramientas de conformado, las cuales están sometidas a esfuerzos repetitivos de gran magnitud y requieren un mantenimiento preventivo altamente planificado.
La aplicación práctica de las prensas para formado de chapas abarca un espectro muy amplio de sectores industriales, desde la automoción, donde se producen paneles de carrocería, largueros estructurales y componentes de seguridad que deben combinar ligereza con máxima resistencia, hasta la fabricación de electrodomésticos en la que se demandan piezas con superficies impecables y tolerancias dimensionales muy estrictas. También se utilizan en la industria de envases metálicos, tanto para alimentos como para bebidas, donde la velocidad de producción es crítica y la precisión en el espesor y la uniformidad de la pared determina la resistencia del envase frente a la presión interna y a los procesos de esterilización. En el sector aeroespacial, la exigencia es todavía mayor, ya que se requiere conformar chapas de aleaciones especiales con alta resistencia mecánica y baja densidad, que deben conservar propiedades estructurales bajo condiciones extremas de temperatura, presión y vibración, lo cual obliga a emplear prensas servo-hidráulicas de última generación con control absoluto del ciclo de embutición y trazabilidad completa de cada lote de producción.
El diseño de las matrices y punzones empleados en estas prensas es otro factor determinante, ya que de ellos depende en gran medida la distribución del flujo del material y la calidad de la pieza obtenida. Estos componentes se fabrican con aceros de alta resistencia al desgaste o aleaciones especiales tratadas térmicamente, y en muchos casos reciben recubrimientos antifricción y de alta dureza que reducen el deterioro por contacto repetido con las chapas. Para optimizar este diseño se emplean programas de simulación por elementos finitos que permiten prever cómo se comportará el material en cada zona de la pieza, anticipando la aparición de defectos como adelgazamientos excesivos, arrugas o fisuras, y corrigiendo parámetros como el radio de curvatura de la matriz, el perfil del punzón o la secuencia de embuticiones progresivas antes de iniciar la fabricación real. De esta manera se reducen drásticamente los costos de ensayo y error, se acortan los plazos de desarrollo y se garantiza que la prensa pueda producir en serie piezas de geometría compleja con total consistencia.
En el plano operativo, la automatización de las prensas para formado de chapas juega un papel esencial para alcanzar la productividad que demanda la industria contemporánea. Los sistemas de alimentación automática introducen la chapa en la posición exacta de conformado, los cojines neumáticos o hidráulicos aseguran su correcta sujeción, y al finalizar el ciclo los extractores retiran la pieza conformada sin necesidad de intervención manual, minimizando tiempos muertos y riesgos de accidente. La integración de robots industriales permite además la manipulación de piezas intermedias, la transferencia entre distintas estaciones de conformado, el apilado y clasificación automática, e incluso la inspección dimensional mediante cámaras de visión artificial que verifican en línea la calidad de cada componente y descartan automáticamente aquellos que no cumplen con las especificaciones. Este nivel de automatización se combina con sistemas de control centralizado capaces de recopilar datos de toda la línea de producción, analizarlos en tiempo real e implementar estrategias de mantenimiento predictivo que evitan paradas no planificadas y maximizan la disponibilidad del equipo.
Todo este conjunto de factores convierte a la prensa para formado de chapas en mucho más que una simple máquina de aplicación de fuerza: se trata de un sistema de manufactura inteligente y altamente especializado, capaz de transformar materia prima metálica en productos terminados con el máximo nivel de precisión, repetibilidad y eficiencia, adaptándose a las exigencias de cada sector y a la evolución tecnológica de la industria. Su capacidad para trabajar con diferentes materiales, espesores y geometrías, junto con la posibilidad de integrarse en líneas totalmente automatizadas, asegura que seguirá siendo un pilar fundamental en la fabricación de componentes metálicos de alto valor añadido en los próximos años.
La evolución tecnológica de las prensas para formado de chapas ha seguido una trayectoria marcada por la búsqueda constante de mayor eficiencia, precisión y sostenibilidad, impulsada por la necesidad de reducir costos de producción, minimizar el impacto ambiental y responder a los estándares de calidad cada vez más estrictos que imponen los mercados globales. En este contexto, los fabricantes de maquinaria han integrado avances significativos en sistemas de control, accionamientos y materiales de construcción, logrando que las prensas actuales sean capaces de trabajar a ritmos de producción muy superiores a los de décadas anteriores y con un consumo energético optimizado. Una de las transformaciones más relevantes ha sido el paso de los sistemas puramente hidráulicos o mecánicos hacia prensas servoaccionadas, que combinan lo mejor de ambos mundos: la gran capacidad de carga y resistencia de las hidráulicas con la flexibilidad y precisión de las electrónicas. Estas prensas permiten programar perfiles de movimiento del punzón completamente personalizados, de manera que la velocidad, la aceleración y la presión ejercida se adapten de forma exacta a cada etapa del conformado, evitando esfuerzos innecesarios, reduciendo el desgaste de las herramientas y garantizando un uso mucho más racional de la energía.
En paralelo, se ha potenciado la incorporación de sistemas de monitorización en tiempo real que convierten a la prensa en un equipo inteligente capaz de registrar y analizar miles de variables durante cada ciclo de trabajo. Sensores de presión, temperatura, vibración y desplazamiento envían información de forma continua a plataformas digitales que no solo controlan el proceso en el momento, sino que además almacenan datos históricos que permiten identificar patrones de comportamiento y prever fallos antes de que se produzcan. Esta capacidad de diagnóstico y predicción se traduce en un mantenimiento mucho más planificado, evitando paradas inesperadas y extendiendo significativamente la vida útil de componentes críticos como los cojinetes, los sellos hidráulicos o los sistemas de guiado. Además, este enfoque de mantenimiento predictivo se vincula de manera natural con las filosofías de la Industria 4.0, donde la conectividad y la intercomunicación entre máquinas permiten a toda la línea de producción adaptarse de forma dinámica a la demanda del mercado y a las condiciones reales de operación.
Otra dimensión clave de la evolución de estas prensas es la sostenibilidad, tanto desde el punto de vista del consumo energético como del aprovechamiento de materiales. Los accionamientos servoeléctricos, además de proporcionar un control de altísima precisión, consumen únicamente la energía que realmente se necesita en cada fase del ciclo, lo que reduce drásticamente las pérdidas habituales de los sistemas hidráulicos convencionales. También se ha avanzado en sistemas de recuperación de energía, en los que parte de la energía generada en los movimientos de retorno o en las desaceleraciones del punzón se almacena y reutiliza en ciclos posteriores, disminuyendo así la huella energética global del proceso. Desde el punto de vista de los materiales, el empleo de softwares de simulación avanzada y algoritmos de optimización ha permitido reducir los márgenes de seguridad sobredimensionados que antes se aplicaban al diseño de piezas, de modo que ahora es posible trabajar con espesores de chapa más ajustados sin comprometer la resistencia final del componente. Esta reducción en el consumo de metal no solo implica un ahorro económico importante, sino también un impacto ambiental menor, ya que disminuye la cantidad de recursos naturales extraídos y procesados, así como la energía necesaria para transformar y transportar la materia prima.
La digitalización ha jugado igualmente un papel decisivo, ya que hoy en día las prensas para formado de chapas no operan como sistemas aislados, sino que están integradas en entornos de fabricación inteligentes donde la información fluye de manera transversal entre diferentes equipos y niveles de la planta. Esto permite, por ejemplo, que un cambio en las especificaciones de un producto se traduzca automáticamente en una modificación en los parámetros de la prensa, sin necesidad de largos ajustes manuales, reduciendo así los tiempos de preparación y aumentando la flexibilidad de la producción. Gracias a esta digitalización también es posible llevar un control de trazabilidad absoluto, registrando qué lote de material se ha utilizado en cada pieza, bajo qué condiciones de proceso se ha conformado y qué resultados de inspección dimensional y superficial ha obtenido. Esta información no solo es vital para garantizar la calidad en sectores como el automotriz o el aeroespacial, sino que también facilita la detección y resolución de problemas en caso de incidencias, reduciendo costos asociados a devoluciones, reclamaciones o fallos en servicio.
Por otro lado, la integración de las prensas con tecnologías de automatización avanzada y robótica colaborativa abre la puerta a entornos de producción mucho más versátiles, en los que el flujo de materiales se adapta en tiempo real a la disponibilidad de equipos y a la demanda de productos. Robots equipados con sistemas de visión pueden detectar de manera autónoma la posición y orientación de chapas o piezas, alimentando la prensa con total precisión y retirando las partes conformadas para su transferencia a operaciones posteriores de corte, soldadura, ensamblaje o pintura. En este escenario, los operarios humanos desempeñan funciones de supervisión, programación y control de calidad, reduciendo su exposición a riesgos físicos y aumentando la seguridad laboral. A medida que estas tecnologías evolucionan, se vislumbra un futuro en el que las prensas para formado de chapas serán nodos inteligentes dentro de fábricas completamente digitalizadas, donde cada máquina contribuye con datos a un sistema global de optimización capaz de ajustar la producción de manera automática a factores externos como fluctuaciones en la demanda del mercado, variaciones en el costo de la energía o cambios en la disponibilidad de materias primas.
Prensa de Estampación Profunda
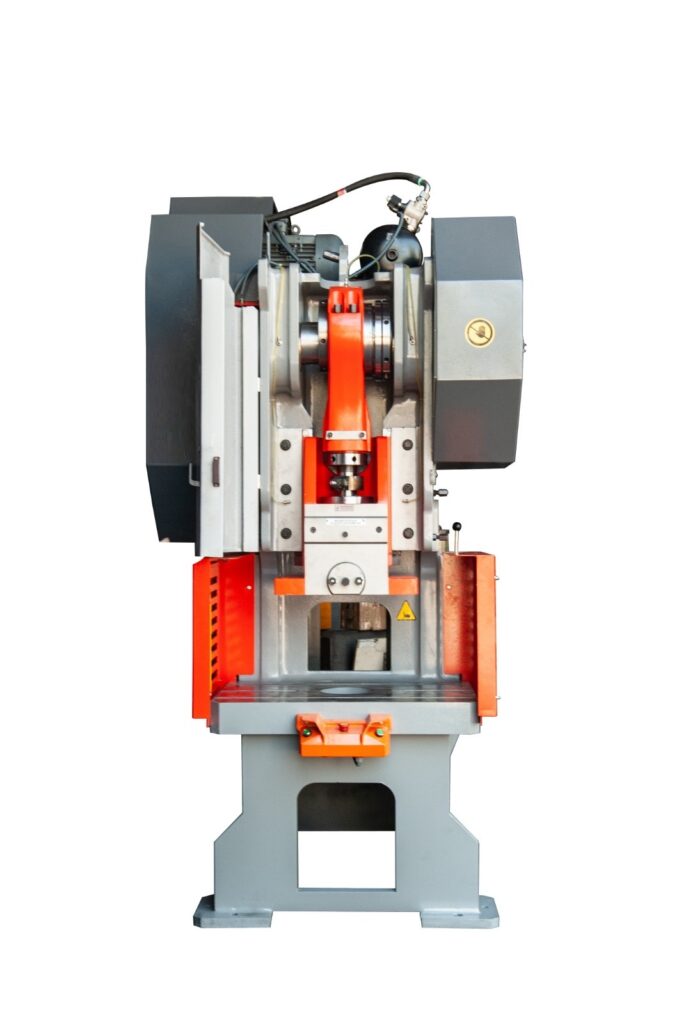
La prensa de estampación profunda representa una de las tecnologías más avanzadas dentro de los procesos de conformado de metales, ya que está diseñada específicamente para transformar chapas planas en piezas con geometrías complejas, de gran profundidad y con altos requerimientos de resistencia estructural y calidad superficial. Este tipo de prensa se diferencia de las máquinas convencionales de estampado porque no se limita únicamente a operaciones de corte, doblado o troquelado simple, sino que lleva el material más allá de sus límites plásticos de manera controlada, logrando configuraciones tridimensionales que serían imposibles con métodos tradicionales. La estampación profunda implica un movimiento progresivo del punzón que va empujando la chapa hacia el interior de una matriz, al mismo tiempo que se controla cuidadosamente el flujo del material para evitar defectos como arrugas, desgarros o adelgazamientos excesivos.
Las prensas de estampación profunda modernas pueden operar bajo distintos sistemas de accionamiento, siendo los más habituales los hidráulicos, los mecánicos y los servoaccionados. Las hidráulicas destacan por su gran capacidad de fuerza constante y su adaptabilidad, lo que resulta ideal cuando se trabaja con piezas grandes, chapas de gran espesor o materiales de alta resistencia como aceros especiales, aleaciones de titanio o aluminio de grado aeronáutico. Las mecánicas, por su parte, ofrecen ciclos más rápidos y mayor productividad en series largas, siendo más utilizadas en sectores como la automoción o la línea blanca, donde la repetitividad y el volumen son factores determinantes. En los últimos años, las servoaccionadas han ganado terreno gracias a su capacidad de personalizar los perfiles de movimiento del punzón y de los cojines de sujeción, lo que otorga una precisión sin precedentes en la distribución de esfuerzos y en el control del flujo del material durante el embutido.
Uno de los elementos más críticos en este tipo de prensas es el cojín de sujeción, dispositivo que aplica una presión controlada sobre la periferia de la chapa para regular el deslizamiento del material hacia la cavidad del troquel. Un control inadecuado en este punto puede provocar arrugas o fracturas, comprometiendo la calidad de la pieza final. Por eso, las prensas de estampación profunda actuales integran sistemas de cojín hidráulico o neumático con control electrónico que permiten ajustar la presión de forma dinámica durante todo el ciclo. Además, muchas incorporan sistemas de monitorización con sensores de fuerza y desplazamiento, de manera que se obtiene una retroalimentación en tiempo real que ayuda a garantizar que cada pieza se forme bajo condiciones óptimas. Esta digitalización no solo eleva la calidad del producto, sino que también mejora la trazabilidad y la repetibilidad de los procesos, lo cual es fundamental en industrias reguladas como la aeroespacial, la automotriz o la biomédica.
El ámbito de aplicación de la prensa de estampación profunda es vasto y abarca sectores industriales estratégicos. En la automoción, es indispensable para la fabricación de componentes estructurales y de carrocería como puertas, cofres, guardabarros y cubiertas de motor, que requieren gran resistencia y geometrías complejas con tolerancias mínimas. En el sector de electrodomésticos, se emplea en la producción de cubetas, paneles y carcasas metálicas que deben soportar esfuerzos mecánicos y térmicos durante largos periodos de uso. En la industria aeroespacial y de defensa, estas prensas se utilizan para fabricar piezas críticas que requieren una relación resistencia-peso optimizada, como depósitos de combustible, carcasas de turbinas o paneles estructurales. Incluso en el ámbito médico y de bienes de consumo, la estampación profunda es clave para producir elementos como recipientes estériles, bandejas quirúrgicas, cápsulas metálicas o utensilios de precisión.
Otro aspecto fundamental es la optimización del diseño de troqueles y matrices, ya que el éxito del proceso depende en gran medida de la calidad y precisión de estas herramientas. Actualmente se emplean softwares de simulación avanzada que permiten predecir el comportamiento del material durante el embutido, identificando posibles zonas de arrugas o rotura antes de realizar la producción real. Esto reduce de manera significativa los costos asociados a pruebas físicas, ajustes de troqueles y desperdicio de material. Al mismo tiempo, se optimiza el espesor y el flujo del metal, lo que permite trabajar con materiales más ligeros sin sacrificar resistencia, alineándose con las tendencias globales de aligeramiento estructural en automóviles eléctricos, aeronaves modernas y equipos industriales eficientes.
La sostenibilidad también ha encontrado un lugar importante en las prensas de estampación profunda de nueva generación. Gracias a los sistemas servoaccionados y de recuperación de energía, se consigue una reducción notable en el consumo eléctrico, al mismo tiempo que se minimizan las pérdidas energéticas propias de los sistemas hidráulicos tradicionales. Asimismo, la posibilidad de simular procesos y optimizar parámetros permite reducir el desperdicio de materia prima, generando una producción más eficiente y respetuosa con el medio ambiente. Esta combinación de eficiencia energética, reducción de desechos y mejora en la durabilidad de las herramientas convierte a estas prensas en un pilar fundamental para la fabricación sostenible del futuro.
Las prensas de estampación profunda, en su evolución más reciente, se han convertido en un pilar fundamental en la adaptación de la industria a los nuevos materiales avanzados que demandan los sectores de alta tecnología. El auge de los aceros de ultra alta resistencia, las aleaciones ligeras de aluminio y magnesio, así como los materiales híbridos y recubiertos, ha transformado las exigencias de los procesos de conformado, y las prensas modernas han debido integrar soluciones específicas para afrontar estos retos. Trabajar con aceros de ultra alta resistencia, por ejemplo, requiere una combinación de gran capacidad de fuerza, precisión en el control de la velocidad del punzón y una gestión optimizada de la fricción entre la chapa y el troquel, ya que estos materiales, aunque ofrecen excelentes propiedades mecánicas, presentan mayor riesgo de rotura o fisuración si no se controla adecuadamente la deformación. Para responder a ello, se han desarrollado prensas servoaccionadas con perfiles de movimiento personalizables que permiten reducir la velocidad en zonas críticas del embutido y aumentar la fuerza de forma progresiva, evitando fallas del material sin sacrificar productividad. En el caso de las aleaciones ligeras como el aluminio y el magnesio, la dificultad radica en su baja formabilidad en frío y en su tendencia a presentar retroceso elástico, lo que obliga a utilizar tecnologías que permitan un control aún más preciso del cojín de sujeción, así como troqueles con recubrimientos especiales y lubricantes avanzados que disminuyen la fricción y el desgaste.
El papel de la simulación computacional se vuelve cada vez más crucial en este escenario, ya que permite predecir el comportamiento del material bajo condiciones reales de carga, evaluando con antelación posibles fallos y optimizando el diseño de troqueles, punzones y cojines. Estas herramientas de ingeniería digital, combinadas con sistemas de monitoreo en tiempo real instalados en las prensas, generan un ecosistema productivo en el que cada ciclo de estampación se convierte en una fuente de datos valiosa para mejorar la eficiencia del siguiente. La tendencia de la industria hacia la manufactura inteligente se refleja en estas máquinas, que no solo forman piezas metálicas, sino que también recopilan, procesan y comunican información para la optimización continua del proceso. De esta manera, las prensas de estampación profunda dejan de ser simples equipos mecánicos para convertirse en nodos tecnológicos que integran la cadena de valor de la producción moderna.
La capacidad de estas prensas de adaptarse a los materiales más complejos abre el camino a nuevas aplicaciones industriales que hace unas décadas habrían sido inviables. La fabricación de carrocerías más livianas pero altamente resistentes en el sector automotriz es un ejemplo claro, ya que gracias a la estampación profunda con materiales avanzados se pueden producir estructuras que cumplen con estrictas normativas de seguridad al mismo tiempo que reducen el peso del vehículo, contribuyendo a la eficiencia energética y a la reducción de emisiones. En el sector aeroespacial, donde cada gramo de peso cuenta, la posibilidad de conformar piezas grandes y complejas en aleaciones de aluminio y titanio mediante procesos de embutido controlado representa una ventaja estratégica, ya que se disminuye la necesidad de uniones adicionales, se mejora la integridad estructural y se reducen los costos asociados a mecanizados intensivos. Incluso en sectores como la medicina o la electrónica, la estampación profunda permite fabricar cápsulas, carcasas, bandejas y componentes de precisión en materiales biocompatibles o conductores avanzados que cumplen con requisitos estrictos de calidad, seguridad y funcionalidad.
El diseño de estas prensas también ha evolucionado para responder a los nuevos escenarios industriales. La integración de sistemas de recuperación energética en los accionamientos hidráulicos, la implementación de servomotores de alta eficiencia y la automatización completa de los procesos de carga y descarga de chapas mediante robots colaborativos han permitido incrementar la velocidad de producción sin comprometer la precisión. Además, los sistemas de visión artificial y control por inteligencia digital permiten una detección instantánea de defectos, arrugas o microfisuras, lo que reduce significativamente la tasa de desperdicio y mejora la trazabilidad de cada componente fabricado. Esto es especialmente importante en industrias donde la calidad debe estar garantizada en un cien por ciento, ya que incluso un defecto mínimo puede tener consecuencias graves, como en la aviación o en la fabricación de dispositivos médicos.
En este contexto, la prensa de estampación profunda se convierte en un verdadero puente entre la tradición metalúrgica y la innovación tecnológica, uniendo la fuerza bruta necesaria para conformar materiales de gran resistencia con la delicadeza y precisión que solo los sistemas digitales de control pueden ofrecer. Este equilibrio entre potencia y sofisticación es lo que asegura que la estampación profunda continúe siendo una tecnología insustituible en la era de la manufactura avanzada. El futuro de estas máquinas apunta hacia una integración aún mayor con las plataformas digitales de gestión de producción, donde cada prensa estará conectada en red con otros equipos, intercambiando datos en tiempo real para coordinar el flujo de trabajo y optimizar los recursos de toda la planta.
Las prensas de estampación profunda en la actualidad ya no se limitan únicamente a ser vistas como máquinas destinadas a la transformación de chapas metálicas, sino que se han convertido en verdaderos sistemas productivos inteligentes capaces de interactuar con diferentes tecnologías de automatización y control. Una de las áreas donde esta evolución es más evidente es en la integración con la robótica aplicada, ya que en muchos procesos de embutición y estampación profunda la manipulación de las piezas, la alimentación de chapas y la retirada de componentes conformados solían ser tareas críticas, repetitivas y físicamente exigentes que requerían gran precisión para no afectar la calidad final del producto. Con la introducción de robots industriales, especialmente de robots colaborativos que pueden trabajar de manera sincronizada con las prensas, se ha conseguido un nivel de eficiencia y seguridad sin precedentes. Estos sistemas robóticos cargan las chapas en el troquel con una precisión milimétrica, retiran las piezas conformadas sin riesgos de deformaciones o daños, y al mismo tiempo se comunican con el sistema de control de la prensa para sincronizar cada ciclo de producción. Este tipo de automatización no solo incrementa la velocidad del proceso, sino que además garantiza una repetibilidad constante, reduciendo el margen de error humano que en procesos tan exigentes podía derivar en defectos de fabricación o en un desgaste prematuro de los troqueles.
La introducción de la automatización también ha transformado la seguridad laboral en torno a estas máquinas. En el pasado, el operario debía acercarse directamente a la zona de trabajo de la prensa, exponiéndose a riesgos de atrapamiento, cortes o accidentes derivados de movimientos inesperados del equipo. Hoy en día, gracias a los sistemas de alimentación automática, a los robots integrados y a los dispositivos de seguridad basados en sensores de presencia, barreras fotoeléctricas y sistemas de enclavamiento inteligentes, el operario ya no necesita entrar en contacto directo con las partes peligrosas de la máquina. Su papel ha evolucionado hacia un rol de supervisión, programación y mantenimiento, donde el trabajo manual repetitivo es reemplazado por tareas de control y optimización, mucho menos riesgosas y más cualificadas. Esto no solo eleva los estándares de seguridad en la planta, sino que además contribuye a una mejora significativa en la ergonomía laboral, ya que desaparecen las posturas forzadas, los levantamientos de peso constante y los movimientos repetitivos que históricamente han generado problemas de salud en los trabajadores de este sector.
Al mismo tiempo, la flexibilidad en la producción se ha visto reforzada por la incorporación de estos sistemas de automatización y control avanzado. Las prensas de estampación profunda actuales pueden adaptarse a lotes de producción más pequeños, con cambios rápidos de troqueles y ajustes automáticos en los parámetros de embutido según las características de cada pieza. Esto significa que una misma máquina puede pasar en poco tiempo de producir grandes series de componentes automotrices a fabricar piezas de menor escala para el sector electrónico o médico, sin perder eficiencia y manteniendo altos estándares de calidad. Los robots colaborativos facilitan este tipo de flexibilidad porque permiten programaciones rápidas y sencillas, adaptándose a distintas geometrías de chapas y piezas sin requerir largas paradas de producción. A esto se suma el uso de sistemas de visión artificial y control adaptativo que supervisan el proceso en tiempo real, corrigiendo desviaciones mínimas en la alineación, la presión de contacto o la posición de la chapa antes de que se produzca un error irreversible.
El impacto de esta combinación entre prensas de estampación profunda y automatización se refleja de manera directa en los índices de productividad de las plantas industriales modernas. Donde antes se necesitaba un grupo numeroso de operarios para atender varios procesos de alimentación y descarga de piezas, ahora un sistema automatizado con un solo supervisor puede manejar varias prensas en simultáneo, optimizando el espacio, reduciendo los costos de producción y aumentando de manera considerable la capacidad de respuesta frente a las demandas del mercado. Esto es crucial en un entorno económico donde la competitividad exige no solo producir con eficiencia, sino también reaccionar con rapidez a cambios en los diseños, en los materiales o en las cantidades de producción solicitadas por los clientes. Las prensas con automatización avanzada son capaces de implementar estas variaciones con un mínimo tiempo de adaptación, lo que representa una ventaja estratégica para las empresas que buscan posicionarse en mercados internacionales altamente competitivos.
En un horizonte futuro cercano, la tendencia apunta hacia una integración todavía más estrecha entre las prensas de estampación profunda, la automatización robótica y los sistemas digitales de gestión de la producción. Cada prensa será un nodo conectado en una red industrial inteligente, intercambiando información en tiempo real con otros equipos, con los sistemas de mantenimiento predictivo y con las plataformas de planificación de la producción. Esto permitirá no solo prevenir fallas antes de que ocurran, sino también programar los ciclos de trabajo en función de la disponibilidad de materiales, la demanda de los clientes y la optimización energética de toda la planta. El concepto de fábrica totalmente conectada encuentra en las prensas de estampación profunda un ejemplo claro de cómo la maquinaria tradicional puede reinventarse y convertirse en un actor clave de la manufactura avanzada del siglo XXI, combinando potencia, precisión, automatización y digitalización en un solo sistema de producción.
En el ámbito de la sostenibilidad y la eficiencia energética, las prensas de estampación profunda han evolucionado hacia configuraciones mucho más respetuosas con el entorno, integrando tecnologías que permiten no solo reducir el consumo de energía sino también optimizar el uso de materias primas y minimizar los residuos generados en cada ciclo de trabajo. Uno de los avances más destacados ha sido la sustitución progresiva de los sistemas hidráulicos tradicionales por sistemas híbridos o totalmente eléctricos, en los que los servomotores controlan con precisión la velocidad y la fuerza de embutición únicamente en el momento necesario, evitando el consumo constante de energía que caracterizaba a las prensas hidráulicas convencionales. Este cambio no solo ha reducido drásticamente el gasto energético, sino que también ha disminuido la generación de calor y la necesidad de sistemas de refrigeración, lo cual repercute en una reducción global de la huella de carbono de la planta productiva. Además, la recuperación de energía en los momentos de desaceleración o retroceso de los sistemas de prensado permite reintegrar parte de esa energía al circuito, aumentando todavía más la eficiencia del proceso.
Otro aspecto fundamental en esta transición hacia procesos más sostenibles es la optimización del material utilizado. Gracias a los sistemas de simulación digital y a la integración de software avanzado de diseño de procesos, es posible planificar cada operación de estampación profunda para aprovechar al máximo la chapa metálica, reduciendo recortes innecesarios y asegurando que cada pieza cumpla con los requerimientos dimensionales y estructurales con la mínima cantidad de material. Esta optimización no solo reduce los costos directos de producción, sino que también disminuye la cantidad de desperdicios metálicos que requieren reprocesamiento o reciclaje, lo cual supone un beneficio ambiental significativo. En paralelo, el uso de aceros de alta resistencia, aleaciones ligeras como el aluminio y metales reciclados se ha vuelto más común en combinación con estas prensas, ya que los avances tecnológicos permiten trabajar con materiales más complejos sin comprometer la calidad del producto final.
La sostenibilidad en el uso de prensas de estampación profunda también está estrechamente ligada a la durabilidad de los troqueles y componentes internos de la máquina. En épocas pasadas, el desgaste de los troqueles era una de las principales causas de desperdicio de material y de fallas en la calidad del producto, pero hoy en día gracias a los recubrimientos avanzados, a los sistemas de lubricación inteligente y al monitoreo constante del estado de cada componente mediante sensores, se logra extender la vida útil de los troqueles y reducir de manera considerable las paradas no planificadas por mantenimiento. Este enfoque no solo disminuye los costos operativos, sino que también contribuye a un ciclo de producción más sostenible, ya que evita la fabricación excesiva de repuestos y reduce los desechos generados por piezas defectuosas.
El aspecto energético y medioambiental se complementa con la capacidad de estas prensas de integrarse en sistemas de gestión global de la planta, donde cada máquina comunica en tiempo real sus parámetros de consumo, rendimiento y estado operativo. Esta interconexión permite tomar decisiones basadas en datos para programar la producción en momentos del día en que la energía es más barata o más limpia, ajustando la operación a estrategias de eficiencia energética que benefician tanto a la empresa como al entorno. Incluso existen sistemas que coordinan las prensas con instalaciones de energías renovables, como paneles solares o sistemas de cogeneración, para garantizar que la mayor parte de la energía utilizada provenga de fuentes sostenibles. Este tipo de innovación está marcando una diferencia notable en industrias que buscan no solo ser competitivas, sino también cumplir con normativas ambientales cada vez más estrictas en los mercados internacionales.
En definitiva, la prensa de estampación profunda moderna no puede entenderse únicamente como una máquina para dar forma a metales, sino como un sistema integral de producción que responde a las necesidades de eficiencia, seguridad, flexibilidad y sostenibilidad del mundo industrial actual. La transición hacia equipos con menor impacto ambiental no es una moda pasajera, sino una necesidad estratégica en un contexto donde las cadenas de suministro globales, la presión por reducir costos y la demanda de productos fabricados de manera responsable se entrelazan. Estas prensas, al incorporar tecnologías de automatización, digitalización y optimización energética, se han convertido en piezas clave de la manufactura avanzada, permitiendo que la industria metalúrgica continúe creciendo de manera competitiva pero también respetuosa con el medio ambiente.
Prensa de Estampado en Frío
La prensa de estampado en frío es una de las máquinas más utilizadas en la industria metalúrgica y de transformación de materiales, ya que permite dar forma a chapas, láminas y piezas metálicas a temperatura ambiente sin necesidad de calentar el material previamente. Este tipo de conformado aprovecha la alta presión ejercida por la prensa sobre el metal en bruto, normalmente mediante troqueles especialmente diseñados, para obtener piezas con geometrías definidas, con gran precisión dimensional y acabados superficiales de alta calidad. A diferencia de los procesos en caliente, donde el metal se ablanda con el calor y fluye con mayor facilidad, el estampado en frío exige mayores esfuerzos de prensado y el uso de materiales con buena ductilidad, pero ofrece ventajas como la mejora de las propiedades mecánicas por endurecimiento por deformación, la reducción de costes energéticos al no requerir hornos de calentamiento y la posibilidad de trabajar con altas velocidades de producción.
Este proceso es muy utilizado en la fabricación de piezas automotrices, electrodomésticos, equipos electrónicos, utensilios de cocina y un sinfín de productos de consumo e industriales. Piezas como tapas, carrocerías, conectores eléctricos, estructuras de soporte o componentes de precisión se producen con prensas de estampado en frío, gracias a la repetitividad y uniformidad que ofrece el método. La exactitud en las dimensiones obtenidas permite reducir operaciones posteriores de mecanizado o acabado, lo cual aumenta la eficiencia productiva. Además, el estampado en frío permite aprovechar al máximo la materia prima, ya que los troqueles optimizan la distribución del material, reduciendo desperdicios y generando un aprovechamiento económico más favorable.
La prensa de estampado en frío puede ser de diferentes configuraciones: mecánica, hidráulica o servoprensa. Las mecánicas suelen usarse para series de producción de gran volumen con geometrías menos complejas, gracias a su rapidez y bajo coste operativo. Las hidráulicas ofrecen mayor versatilidad y control de la fuerza a lo largo del recorrido del émbolo, lo cual es fundamental en piezas que requieren un embutido profundo o procesos más delicados. Las servoprensas representan una evolución tecnológica que integra motores eléctricos de control digital, capaces de ajustar en cada instante velocidad, fuerza y posición, lo que aporta mayor flexibilidad y ahorro energético, además de la posibilidad de programar perfiles de movimiento adaptados a cada tipo de pieza.
Desde el punto de vista metalúrgico, el estampado en frío incrementa la resistencia del material al provocar un endurecimiento estructural, aunque al mismo tiempo puede reducir su ductilidad si las deformaciones son muy intensas. Por ello, en muchos casos se aplican tratamientos térmicos posteriores, como el recocido, para recuperar propiedades de tenacidad o para facilitar procesos de embutición sucesivos. En la industria, esta combinación de operaciones permite crear piezas que no solo tienen la forma deseada, sino que además presentan un equilibrio óptimo entre resistencia, ligereza y durabilidad, algo especialmente valorado en sectores como el automotriz y la construcción metálica.
En cuanto a sostenibilidad y competitividad, el estampado en frío ha ganado protagonismo porque al eliminar la necesidad de calentar el material se reducen las emisiones y los costes energéticos, alineándose con las tendencias de manufactura más limpias y eficientes. Asimismo, la integración de sistemas de monitoreo en línea, control numérico de los parámetros de prensado y automatización de la alimentación de chapas y retirada de piezas terminadas permiten que estas prensas funcionen en líneas de producción totalmente automatizadas, aumentando la productividad y reduciendo riesgos para los operarios. De este modo, la prensa de estampado en frío no solo es una máquina de conformado, sino un elemento estratégico en los sistemas modernos de producción en serie, que combina precisión, velocidad, ahorro y sostenibilidad.
En la industria automotriz, la prensa de estampado en frío ocupa un papel absolutamente esencial porque permite transformar grandes volúmenes de chapa metálica en componentes estructurales y estéticos con una repetitividad milimétrica. Las carrocerías de los automóviles modernos, por ejemplo, se fabrican en su mayor parte mediante este proceso, ya que las láminas de acero o de aleaciones ligeras como el aluminio pueden ser embutidas, troqueladas y conformadas en distintas etapas hasta convertirse en puertas, capós, techos, paneles laterales y refuerzos internos. La razón principal por la que se emplea el estampado en frío en lugar de otros métodos es que ofrece una relación óptima entre costo, velocidad de producción y calidad del acabado, permitiendo a las plantas automotrices producir miles de piezas idénticas al día sin necesidad de mecanizados posteriores costosos. Además, el hecho de que el material no sea sometido a temperaturas elevadas ayuda a mantener tolerancias dimensionales más ajustadas y una superficie lista para tratamientos de pintura, galvanizado o recubrimientos especiales que protegen contra la corrosión.
La evolución de la tecnología de estampado en frío ha ido de la mano de las exigencias del mercado automotor. A medida que se demandan vehículos más ligeros y con mayor eficiencia energética, los fabricantes buscan materiales de alta resistencia como los aceros avanzados de alta resistencia (AHSS) o incluso aleaciones complejas de aluminio y magnesio. Estos materiales requieren una capacidad de prensado y un control del proceso mucho más precisos, pues son más difíciles de conformar sin que aparezcan grietas o defectos. Es aquí donde entran en juego las servoprensas y las prensas hidráulicas modernas con control numérico, capaces de aplicar fuerzas progresivas, variar la velocidad del émbolo en cada fase del proceso y sincronizarse con sistemas de lubricación avanzada que reducen el desgaste de los troqueles y facilitan la deformación del metal. Gracias a estos avances, piezas complejas como pilares de seguridad, refuerzos de impacto lateral o bastidores de asiento pueden producirse de manera eficiente y segura, cumpliendo con los estándares cada vez más estrictos de seguridad vehicular.
Un aspecto clave en la integración de prensas de estampado en frío dentro de la industria automotriz es la automatización completa de las líneas de producción. Robots especializados alimentan las chapas en las prensas, retiran las piezas conformadas y las trasladan a estaciones sucesivas donde se aplican operaciones adicionales como recorte, punzonado, taladrado o soldadura por puntos. Esta integración garantiza no solo un flujo continuo de producción, sino también una trazabilidad total de cada pieza, ya que los sistemas modernos incorporan sensores que miden en tiempo real las presiones aplicadas, la posición del émbolo y posibles desviaciones en las dimensiones de las piezas. Cuando se detecta alguna anomalía, la línea se detiene automáticamente para evitar la generación masiva de piezas defectuosas, lo que supone un gran ahorro económico y asegura una calidad consistente en todo el lote.
La prensa de estampado en frío también es crucial para lograr el equilibrio entre seguridad y peso en los automóviles. A medida que los fabricantes intentan reducir el peso total del vehículo para disminuir el consumo de combustible o ampliar la autonomía de los vehículos eléctricos, se emplean piezas estampadas de mayor complejidad geométrica que permiten usar menos material sin sacrificar resistencia. Por ejemplo, mediante el conformado en frío es posible crear piezas con nervaduras y refuerzos que aumentan la rigidez estructural de la carrocería, a pesar de estar fabricadas con chapas más delgadas. Este principio de diseño liviano con alta resistencia ha sido uno de los motores que ha impulsado la mejora continua en el campo de las prensas de estampado en frío, obligando a los fabricantes de maquinaria a innovar constantemente en precisión, velocidad y capacidad de carga.
En la actualidad, muchas plantas de estampado en frío trabajan bajo el concepto de manufactura flexible, donde una misma prensa puede adaptarse a producir diferentes piezas con solo cambiar el troquel y reprogramar el sistema de control. Esto resulta vital en la industria automotriz, donde conviven diferentes modelos de vehículos en una misma línea de producción y donde los ciclos de vida de los modelos son cada vez más cortos. La capacidad de adaptar rápidamente la maquinaria a nuevas geometrías y nuevos materiales se traduce en una ventaja competitiva decisiva. Además, los avances en simulación por computadora permiten prever el comportamiento de la chapa antes del estampado real, identificando posibles arrugas, pliegues o fallos de embutición, lo que reduce tiempos de ensayo, minimiza desperdicios y acelera el lanzamiento de nuevos modelos al mercado.
En el sector de electrodomésticos y equipos eléctricos, las prensas de estampado en frío han demostrado ser igualmente esenciales, ya que permiten fabricar piezas metálicas con tolerancias precisas y acabados superficiales de alta calidad que son fundamentales tanto para la funcionalidad como para la estética de los productos. Elementos como cubiertas, paneles, carcasas, bandejas internas, soportes estructurales y conductos se producen en grandes cantidades utilizando chapas de acero, aluminio o aleaciones ligeras, conformadas a temperatura ambiente mediante procesos controlados de embutición, corte y punzonado. La ventaja principal de emplear estampado en frío en estos sectores radica en la repetitividad y consistencia del proceso: cada pieza sale prácticamente idéntica a la anterior, lo que asegura un ensamble perfecto en líneas automatizadas de producción y evita problemas de montaje que podrían generar defectos funcionales o estéticos en los electrodomésticos, equipos de climatización o dispositivos electrónicos. Además, la capacidad de fabricar piezas complejas sin necesidad de mecanizado posterior permite reducir tiempos de producción y minimizar costos operativos, algo especialmente importante en productos de consumo masivo donde la eficiencia y la competitividad son decisivas.
En esta industria, la integración de prensas de estampado en frío con sistemas de automatización avanzada y robótica ha optimizado tanto la productividad como la seguridad laboral. Robots colaborativos alimentan chapas de manera precisa y las posicionan correctamente en los troqueles, mientras otros sistemas se encargan de retirar las piezas terminadas, realizar inspecciones dimensionales automáticas y trasladarlas a las etapas siguientes del proceso, como ensamblaje, pintura o recubrimiento. Esta coordinación entre prensas, robots y sistemas de visión artificial garantiza no solo la consistencia de la producción, sino también la trazabilidad completa de cada componente, registrando parámetros críticos de proceso y posibles desviaciones para su análisis posterior. Gracias a esta combinación de control digital y automatización, se pueden producir grandes lotes de manera eficiente, cumpliendo con estrictos estándares de calidad sin aumentar el riesgo de accidentes laborales o fatiga de los operarios.
La precisión de las prensas de estampado en frío también es crucial en la fabricación de equipos eléctricos, donde componentes como carcasas de motores, soportes de circuitos, paneles de control y conectores metálicos requieren tolerancias muy ajustadas para asegurar la correcta funcionalidad eléctrica y mecánica. En estos casos, cualquier variación mínima puede afectar el ensamblaje, la conductividad o la durabilidad del producto final. La posibilidad de programar perfiles de movimiento del punzón y de regular la presión del cojín de sujeción permite moldear piezas complejas sin generar arrugas, desgarros o deformaciones indeseadas, lo que se traduce en componentes más fiables y con una vida útil prolongada. Además, el uso de lubricantes avanzados y recubrimientos especiales en los troqueles contribuye a reducir el desgaste de las herramientas, permitiendo mantener la calidad de producción durante largos periodos y disminuyendo los costos asociados a mantenimiento y reemplazo de piezas críticas.
El aprovechamiento de la materia prima es otro factor donde el estampado en frío muestra ventajas claras en la fabricación de electrodomésticos y equipos eléctricos. Las prensas modernas permiten optimizar el posicionamiento de cada pieza sobre la chapa metálica, reduciendo los recortes innecesarios y aprovechando al máximo el material disponible. Esto no solo reduce el costo de producción, sino que también disminuye el impacto ambiental, al generar menos residuos y facilitar el reciclaje de los recortes sobrantes. Además, la combinación de materiales avanzados y prensas de alta precisión ha permitido fabricar piezas más ligeras y resistentes, contribuyendo a productos más eficientes energéticamente y con mejores prestaciones.
La digitalización de estas prensas también ha transformado la manera en que se gestionan las líneas de producción en el sector de electrodomésticos y equipos eléctricos. Cada prensa puede conectarse a sistemas de control centralizados que supervisan el rendimiento, el consumo de energía, la presión aplicada y la posición de los punzones en tiempo real, permitiendo ajustes automáticos y evitando fallos antes de que se produzcan. Esta integración no solo aumenta la eficiencia operativa, sino que también permite implementar estrategias de producción más sostenibles, reduciendo el consumo eléctrico y el desperdicio de material, alineándose con las demandas actuales de responsabilidad ambiental y eficiencia industrial.
En conclusión, la prensa de estampado en frío se ha convertido en un elemento estratégico para sectores que requieren alta precisión, productividad y sostenibilidad, desde la industria automotriz hasta la fabricación de electrodomésticos y equipos eléctricos. Su capacidad de transformar chapas metálicas en piezas complejas, repetibles y duraderas, combinada con la integración de automatización, robótica y control digital, ha redefinido la manera de producir en masa, elevando los estándares de calidad y eficiencia de manera significativa.
En el ámbito de la fabricación de productos de consumo y dispositivos electrónicos de nueva generación, las prensas de estampado en frío han demostrado ser herramientas imprescindibles para producir componentes metálicos de alta precisión y fiabilidad, que cumplen con los estrictos requisitos funcionales y estéticos de estos sectores. Cada smartphone, laptop, tablet o dispositivo doméstico inteligente contiene múltiples piezas metálicas que deben ajustarse con exactitud a tolerancias milimétricas para garantizar el correcto ensamblaje, la disipación térmica, la conectividad eléctrica y la durabilidad del producto. Componentes como carcasas, marcos, bandejas internas, disipadores de calor y conectores se fabrican mediante procesos de estampado en frío, aprovechando la capacidad de estas prensas para dar forma a metales delgados como acero inoxidable, aluminio y aleaciones ligeras, manteniendo superficies lisas, libres de deformaciones indeseadas y listas para recibir recubrimientos protectores, anodizados, pinturas o tratamientos conductivos.
La evolución tecnológica de estas prensas ha permitido abordar desafíos asociados a piezas de geometría muy compleja, paredes delgadas y embutidos profundos, que son comunes en dispositivos compactos y de diseño minimalista. Los sistemas servoaccionados y las prensas hidráulicas modernas permiten ajustar la velocidad y la fuerza de prensado en tiempo real, optimizando el flujo del material y evitando defectos como arrugas, desgarros o adelgazamiento excesivo. La incorporación de sensores y sistemas de visión artificial permite monitorear cada ciclo de estampación, detectando desviaciones mínimas en la posición o en la fuerza aplicada, lo que garantiza la uniformidad de cada pieza y asegura que los productos finales cumplan con los estándares de calidad más exigentes. Este nivel de control es esencial en la fabricación de dispositivos electrónicos, donde cualquier irregularidad puede afectar la funcionalidad, el rendimiento térmico o la integración de componentes electrónicos sensibles.
Además, la automatización y la robótica han transformado por completo la manera de operar estas prensas en líneas de producción modernas. Robots colaborativos se encargan de alimentar chapas metálicas, posicionarlas en los troqueles con precisión micrométrica, retirar las piezas conformadas y trasladarlas a estaciones de ensamblaje o acabado, mientras los sistemas de control digital registran cada parámetro de operación y generan trazabilidad completa de cada componente. Esto no solo incrementa la productividad, sino que también garantiza seguridad para los operarios, elimina riesgos asociados a la manipulación manual de piezas pequeñas y delicadas y permite ajustar rápidamente la producción a diferentes modelos o diseños sin necesidad de largos tiempos de reprogramación. La combinación de alta precisión, control digital y automatización convierte a estas prensas en elementos estratégicos para la fabricación de dispositivos electrónicos de consumo masivo, donde la calidad y la consistencia son determinantes para la reputación de la marca.
El impacto de las prensas de estampado en frío también se extiende al sector de energías renovables, donde la fabricación de componentes metálicos para paneles solares, sistemas de almacenamiento de energía, turbinas eólicas y otros dispositivos requiere piezas con geometrías complejas, alta resistencia mecánica y mínima tolerancia dimensional. La capacidad de conformar chapas metálicas sin necesidad de calentarlas permite mantener propiedades mecánicas óptimas, reducir el consumo energético durante la producción y minimizar la deformación de materiales críticos. En este sentido, las prensas de estampado en frío contribuyen directamente a la eficiencia y sostenibilidad de toda la cadena de producción de tecnologías limpias, al garantizar que las piezas metálicas cumplan con los estándares de resistencia, conductividad y durabilidad necesarios para aplicaciones energéticas de alto rendimiento.
La sostenibilidad es un eje central en la modernización de estas prensas. La reducción del consumo energético mediante sistemas servoeléctricos, la recuperación de energía en los movimientos del émbolo, la optimización del material y la reducción de desperdicios permiten que las plantas de producción sean más responsables con el medio ambiente y más competitivas económicamente. Además, la integración con sistemas de control y monitoreo digital permite programar las operaciones de manera eficiente, coordinar el uso de energía renovable y minimizar el impacto ambiental asociado a la producción masiva de componentes metálicos. Este enfoque holístico convierte al estampado en frío en un proceso industrial que no solo cumple con los objetivos productivos, sino que también contribuye a la sostenibilidad y a la economía circular, promoviendo el uso eficiente de materiales y energía.
En resumen, la prensa de estampado en frío ha trascendido su función tradicional de conformar metales para convertirse en un elemento central en la manufactura avanzada de dispositivos electrónicos, productos de consumo y componentes de energías renovables. Su combinación de precisión, repetitividad, flexibilidad, automatización y eficiencia energética permite producir piezas complejas de manera rápida, segura y sostenible, adaptándose a los requerimientos de materiales modernos y a la demanda de productos de alta calidad. Esta capacidad de transformación, integración tecnológica y optimización de recursos asegura que el estampado en frío siga siendo una tecnología clave para la industria del siglo XXI, alineando productividad, innovación y responsabilidad ambiental.
Máquina para Moldeado por Embutición
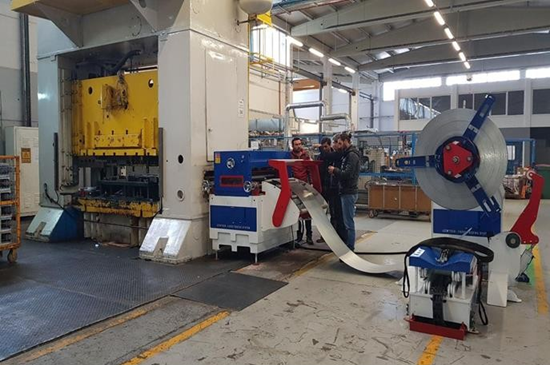
La máquina para moldeado por embutición es un equipo esencial en la industria metalúrgica y de fabricación de componentes, diseñada para conformar chapas metálicas mediante la aplicación controlada de fuerza, logrando dar forma a piezas complejas sin necesidad de cortes excesivos o procesos de unión adicionales. A través de un troquel específico y un punzón que ejercen presión sobre la chapa, la máquina de embutición permite transformar láminas planas en contenedores, carcasas, tapas, componentes estructurales y una amplia variedad de piezas con geometrías tridimensionales precisas. Este proceso, al realizarse a temperatura ambiente o ligeramente controlada según el material, aprovecha la ductilidad del metal y genera piezas con propiedades mecánicas mejoradas, como mayor resistencia y rigidez, debido al endurecimiento por deformación que ocurre durante el embutido. La versatilidad de la máquina para moldeado por embutición radica en su capacidad para trabajar con distintos tipos de metales, incluyendo acero, aluminio, cobre y aleaciones ligeras, así como con espesores variados de chapa, adaptándose a las necesidades específicas de sectores como el automotriz, electrodomésticos, aeroespacial, envases metálicos y equipos electrónicos.
El diseño de estas máquinas ha evolucionado considerablemente, pasando de prensas mecánicas tradicionales a sistemas hidráulicos y servoaccionados que permiten un control mucho más preciso de la velocidad, la presión y la trayectoria del punzón. En las prensas mecánicas, la velocidad de operación es elevada y está indicada para series largas de piezas estándar, mientras que en las hidráulicas se consigue una fuerza constante a lo largo de todo el recorrido, lo que resulta fundamental para piezas con embutidos profundos o formas complejas. Por su parte, las servoprensas combinan precisión, flexibilidad y eficiencia energética, ya que permiten programar perfiles de movimiento exactos, aplicar fuerza progresiva en zonas críticas y reducir el consumo eléctrico al accionar solo cuando es necesario. Esta evolución tecnológica no solo ha incrementado la calidad de las piezas producidas, sino que también ha ampliado la gama de aplicaciones posibles y reducido el desgaste de los troqueles y componentes internos de la máquina.
En el proceso de embutición, la lubricación y el diseño del troquel son fundamentales para asegurar que la chapa fluya correctamente sin generar arrugas, desgarros o adelgazamiento excesivo. Los troqueles modernos suelen contar con recubrimientos especiales y geometrías optimizadas, mientras que los sistemas de lubricación aplican aceites o películas lubricantes de manera uniforme para reducir la fricción y el calor generado durante el moldeado. La combinación de estos factores permite obtener piezas precisas, con superficies lisas y propiedades mecánicas uniformes, minimizando la necesidad de operaciones de rectificado o acabado posteriores. Además, el control digital integrado en las máquinas más avanzadas supervisa continuamente los parámetros de presión, desplazamiento y posición del punzón, detectando cualquier desviación en tiempo real y ajustando automáticamente el proceso para garantizar la calidad constante de cada pieza.
La automatización ha transformado radicalmente la operación de las máquinas para moldeado por embutición. En las plantas modernas, robots colaborativos se encargan de alimentar las chapas, posicionarlas con precisión en los troqueles y retirar las piezas conformadas, mientras sistemas de visión artificial y sensores de fuerza supervisan la correcta ejecución de cada ciclo. Esto no solo aumenta la productividad y la repetitividad del proceso, sino que también incrementa la seguridad laboral, eliminando la exposición directa del operario a las partes móviles de la prensa y reduciendo la fatiga derivada de la manipulación manual. Asimismo, la trazabilidad completa de cada pieza se garantiza mediante sistemas de registro digital que documentan los parámetros de operación, facilitando el control de calidad y la mejora continua del proceso.
En términos de eficiencia y sostenibilidad, las máquinas de embutición modernas incorporan soluciones que reducen el consumo energético y optimizan el uso del material. La aplicación de fuerzas progresivas, la recuperación de energía en los movimientos de retroceso del punzón, el uso de lubricantes de última generación y la optimización del aprovechamiento de la chapa permiten disminuir desperdicios, reducir emisiones y mejorar la competitividad industrial. Esto es especialmente relevante en industrias que producen grandes volúmenes de piezas, como la automotriz o la de envases metálicos, donde pequeñas mejoras en eficiencia y precisión se traducen en importantes ahorros de costo y energía a gran escala.
En resumen, la máquina para moldeado por embutición representa un elemento central de la manufactura moderna, capaz de transformar láminas planas en piezas tridimensionales complejas, con alta repetibilidad, precisión y resistencia mecánica. La integración de tecnologías de control digital, automatización robótica, troqueles avanzados y sistemas de lubricación optimizados convierte a estas máquinas en herramientas estratégicas para una amplia variedad de industrias, desde la automotriz y la aeroespacial hasta la fabricación de electrodomésticos, envases metálicos y componentes electrónicos. Su capacidad para combinar productividad, calidad, seguridad y sostenibilidad las posiciona como un componente indispensable en la producción industrial contemporánea.
En la industria automotriz, la máquina para moldeado por embutición se ha convertido en un elemento fundamental para la fabricación de componentes estructurales y estéticos que requieren alta precisión y resistencia mecánica. Piezas como puertas, capós, techos, guardabarros, refuerzos internos de la carrocería, pilares de seguridad y soportes de chasis se producen mediante procesos de embutición profunda, donde la chapa metálica fluye dentro del troquel hasta adquirir la forma deseada sin comprometer la integridad del material. La ventaja de utilizar embutición en frío para estas aplicaciones radica en la combinación de precisión dimensional y mejora de las propiedades mecánicas del metal por endurecimiento por deformación, lo que proporciona componentes más rígidos y duraderos con un mínimo de material, contribuyendo al ahorro de peso del vehículo, un factor clave en eficiencia energética y rendimiento de automóviles modernos.
La versatilidad de estas máquinas permite trabajar con distintos tipos de metales, incluyendo aceros de alta resistencia, aceros al carbono, aluminio y aleaciones ligeras que son cada vez más utilizadas para reducir el peso total del vehículo. El control preciso de la fuerza y el desplazamiento del punzón, ya sea mediante sistemas hidráulicos, mecánicos o servoaccionados, garantiza que incluso piezas con embutidos profundos, nervaduras o geometrías complejas se conformen correctamente sin arrugas, grietas o adelgazamiento excesivo del material. Además, los troqueles se diseñan con geometrías optimizadas y recubrimientos de alta durabilidad para soportar miles de ciclos de producción sin degradarse, lo que asegura consistencia y calidad durante la fabricación en serie. La incorporación de sensores de fuerza, posición y presión permite supervisar en tiempo real cada ciclo de embutición, detectando posibles desviaciones y ajustando automáticamente el proceso, lo que minimiza desperdicios y reduce la necesidad de reprocesos.
La automatización completa de las líneas de embutición ha transformado la producción automotriz, permitiendo que robots colaborativos alimenten las chapas, las coloquen con exactitud en los troqueles, retiren las piezas conformadas y las trasladen a estaciones de ensamblaje o pintura, mientras los sistemas de visión artificial verifican la calidad de cada componente. Esta integración aumenta la productividad, garantiza la uniformidad de cada pieza y reduce los riesgos laborales, evitando que los operarios manipulen manualmente piezas pesadas o zonas peligrosas de la prensa. Además, permite adaptar rápidamente la línea a diferentes modelos o versiones de vehículos, simplemente cambiando troqueles y reprogramando parámetros de prensa, lo que ofrece una flexibilidad indispensable en un sector donde los ciclos de vida de los modelos son cada vez más cortos y las demandas de personalización aumentan.
En el caso de la fabricación de envases metálicos, la máquina de embutición permite producir piezas como latas, tapas, botes, contenedores y recipientes de diversas formas y tamaños a partir de chapas de acero o aluminio. El proceso debe ser extremadamente preciso para asegurar que cada envase cumpla con las especificaciones de cierre, capacidad y resistencia mecánica, especialmente cuando se trata de alimentos, bebidas, productos químicos o farmacéuticos. La embutición profunda es esencial en este contexto, ya que permite crear envases de paredes delgadas y uniformes, maximizar el aprovechamiento del material y minimizar los residuos, lo que repercute en una producción más sostenible y económica. Los sistemas de control automatizado ajustan la fuerza y la velocidad del punzón según el diámetro y la altura del envase, evitando defectos como arrugas, pliegues o deformaciones que afectarían la funcionalidad y apariencia del producto final.
La combinación de embutición profunda con troqueles de alta precisión y automatización robótica permite que la producción de envases sea extremadamente rápida y constante, alcanzando velocidades de cientos o incluso miles de piezas por minuto sin comprometer la calidad. Los sistemas de inspección automática verifican cada envase para detectar irregularidades, asegurando que solo aquellos que cumplen los estándares pasen al empaquetado y distribución. Esta integración de tecnología avanzada ha hecho posible que la industria de envases metálicos responda a la demanda masiva de productos, manteniendo altos niveles de eficiencia, reducción de desperdicios y control de costos.
En términos de sostenibilidad, la embutición mediante estas máquinas ofrece ventajas significativas, ya que al producir piezas con mínima deformación térmica y máxima precisión se reduce el consumo de energía, se optimiza el uso del material y se disminuyen los desechos metálicos. La posibilidad de recuperación de energía en prensas servoaccionadas y la programación de perfiles de fuerza adaptativos contribuyen a una operación más eficiente y ecológica. Esto, sumado a la durabilidad de los troqueles y la reducción de reprocesos, hace que la producción de componentes automotrices y envases metálicos sea más competitiva y respetuosa con el medio ambiente, cumpliendo con los estándares industriales y las expectativas del mercado moderno.
La evolución de las máquinas para moldeado por embutición hacia sistemas inteligentes ha transformado la manera en que se gestionan las líneas de producción en industrias como la automotriz, la de envases metálicos, electrodomésticos y dispositivos electrónicos. Estas prensas modernas ya no funcionan de manera aislada, sino que están integradas en redes de control digital donde cada ciclo de embutición es monitoreado en tiempo real mediante sensores que registran fuerza aplicada, posición del punzón, velocidad de desplazamiento y temperatura del material. Esta información se procesa mediante software especializado que permite ajustar automáticamente los parámetros de operación, detectar anomalías antes de que se produzcan defectos y optimizar el consumo de energía. De esta manera, la prensa deja de ser un simple elemento mecánico para convertirse en un nodo inteligente dentro de un ecosistema de manufactura conectado que busca eficiencia, calidad y sostenibilidad simultáneamente.
La integración de estas máquinas con sistemas de automatización y robótica ha permitido que los procesos de embutición sean altamente repetitivos y consistentes, eliminando variaciones humanas y reduciendo riesgos laborales. Robots colaborativos alimentan las chapas metálicas con precisión micrométrica, posicionándolas en los troqueles y retirando las piezas conformadas para su traslado a estaciones de acabado, inspección o ensamblaje. Al mismo tiempo, sistemas de visión artificial verifican cada pieza, midiendo dimensiones, detectando arrugas, pliegues o deformaciones y asegurando que únicamente los productos conformes continúen en la línea de producción. Esta combinación de sensores, robótica y control digital permite alcanzar niveles de productividad impensables hace unas décadas, especialmente en la producción en serie de piezas complejas donde la precisión y la calidad son críticas.
El mantenimiento predictivo es otro de los grandes beneficios que aporta la digitalización de las prensas de embutición. Gracias al análisis constante de datos provenientes de los sensores, se pueden identificar patrones de desgaste en troqueles, cojinetes y sistemas hidráulicos o servoaccionados antes de que se produzca una falla. Esto permite programar intervenciones de mantenimiento de manera planificada, evitando paradas no programadas que generan pérdidas económicas y retrasos en la producción. Además, el monitoreo en tiempo real contribuye a prolongar la vida útil de los troqueles y a reducir el consumo de lubricantes y energía, optimizando la eficiencia global de la planta y disminuyendo el impacto ambiental asociado a la producción industrial.
La sostenibilidad es un componente central de estas tecnologías avanzadas. Las máquinas modernas de embutición permiten minimizar el desperdicio de material mediante el diseño optimizado de troqueles y la programación de perfiles de fuerza que ajustan la presión en función de la geometría de la pieza. La recuperación de energía en los movimientos de retroceso del punzón y la capacidad de operar únicamente cuando es necesario reducen el consumo eléctrico, lo que, combinado con la reducción de desperdicios, genera una operación industrial mucho más eficiente y ecológica. Esto es particularmente importante en industrias de alta demanda como la automotriz y la de envases metálicos, donde la producción masiva puede generar grandes cantidades de residuos y consumo energético si no se utilizan sistemas optimizados.
La flexibilidad de estas prensas inteligentes permite además adaptarse rápidamente a nuevos diseños y materiales. En la industria automotriz, por ejemplo, un mismo equipo puede producir diferentes piezas de carrocería, refuerzos o componentes estructurales simplemente cambiando el troquel y reprogramando los parámetros de prensado. En la fabricación de envases metálicos, la prensa puede ajustarse para producir distintas dimensiones y formas de latas, botes o tapas, optimizando cada ciclo para minimizar desperdicios y maximizar la velocidad de producción. Esta adaptabilidad es clave para mantener la competitividad en mercados donde los ciclos de vida de los productos son cada vez más cortos y la demanda de personalización y eficiencia es creciente.
En resumen, las máquinas para moldeado por embutición han evolucionado de ser simples prensas mecánicas a convertirse en sistemas inteligentes, conectados y automatizados que combinan precisión, flexibilidad, productividad, sostenibilidad y seguridad laboral. La incorporación de sensores, control digital, robótica y análisis de datos en tiempo real permite producir piezas metálicas complejas con alta repetitividad y calidad, optimizando materiales y energía, reduciendo desperdicios y asegurando que cada componente cumpla con las exigencias del mercado moderno. Esta integración tecnológica ha transformado la manera de producir en industrias clave, desde la automotriz y aeroespacial hasta electrodomésticos, dispositivos electrónicos y envases metálicos, consolidando al embutido como un proceso industrial estratégico del siglo XXI.
El diseño y la optimización de troqueles modernos para embutición representan uno de los aspectos más críticos y sofisticados dentro de la fabricación de piezas metálicas, ya que determinan directamente la calidad, la precisión, la durabilidad y la eficiencia energética del proceso. Un troquel bien diseñado no solo asegura que la chapa fluya correctamente durante el embutido profundo, sino que también minimiza defectos como arrugas, pliegues, adelgazamiento irregular o grietas, que podrían comprometer tanto la funcionalidad como la apariencia de la pieza final. La geometría del troquel se define cuidadosamente considerando la forma de la pieza, el tipo y espesor del material, el radio de los pliegues y las zonas críticas donde la chapa experimentará mayores tensiones. Cada curva, ángulo y relieve se calcula mediante software de simulación por elementos finitos, lo que permite prever el comportamiento del metal antes de la fabricación física del troquel y reducir significativamente el tiempo y los costos asociados a pruebas y ajustes.
El material del troquel es otro factor determinante. Para aplicaciones de alta producción y embutición profunda, se utilizan aceros especiales de alta dureza y resistencia al desgaste, a menudo tratados térmicamente y recubiertos con materiales como carburo de tungsteno, nitruro de titanio u otros recubrimientos avanzados que reducen la fricción, prolongan la vida útil del troquel y facilitan el flujo uniforme de la chapa. Este recubrimiento evita que la chapa se adhiera al troquel o que el metal se desgaste de manera prematura, garantizando la repetitividad de cada ciclo de producción y la uniformidad dimensional de todas las piezas fabricadas. La combinación de un material resistente con un recubrimiento de baja fricción es especialmente importante en aplicaciones donde se utilizan chapas delgadas o materiales de alta resistencia que son más propensos a arrugarse o agrietarse durante el embutido.
Los sistemas de lubricación también juegan un papel esencial en la eficiencia del troquel. La aplicación controlada de aceites, ceras o películas lubricantes reduce la fricción entre la chapa y la superficie del troquel, disminuye el calor generado durante el proceso y facilita el flujo del material hacia las áreas profundas del molde. En prensas modernas, la lubricación puede ser aplicada de manera automatizada y sincronizada con cada ciclo, garantizando que la cantidad y distribución del lubricante sean óptimas, evitando excesos que puedan generar residuos o problemas en etapas posteriores de acabado. Esta precisión en la lubricación no solo mejora la calidad de la pieza, sino que también prolonga la vida útil del troquel y reduce los costos de mantenimiento.
Además, el diseño del troquel se complementa con sistemas de amortiguación, cojines de presión y guías que aseguran que la chapa se mantenga correctamente posicionada durante todo el embutido, evitando desplazamientos indeseados que puedan generar deformaciones o fallos estructurales. Los troqueles modernos integran sensores que monitorean la presión, el desplazamiento y la temperatura en tiempo real, lo que permite ajustar dinámicamente el proceso, detectar anomalías antes de que se conviertan en defectos y mantener un control constante sobre cada pieza producida. La capacidad de simular, ajustar y monitorear el troquel en tiempo real convierte a este componente en un elemento estratégico, no solo para garantizar calidad, sino también para optimizar la eficiencia energética y la sostenibilidad del proceso de producción.
La interacción entre geometría, material, recubrimientos, lubricación y control digital permite que las prensas de embutición modernas produzcan piezas extremadamente complejas con alta precisión y repetitividad. Esto es fundamental en industrias donde los estándares de calidad son muy estrictos, como la automotriz, aeroespacial, de electrodomésticos, dispositivos electrónicos y envases metálicos. Cada troquel se diseña no solo para cumplir con las especificaciones de forma y dimensión, sino también para soportar ciclos de producción prolongados, minimizar desperdicios y permitir la fabricación de piezas que optimicen la resistencia mecánica del material sin incrementar innecesariamente su espesor.
En conclusión, el desarrollo de troqueles avanzados es un componente esencial dentro de la evolución de las máquinas de embutición, ya que integra consideraciones de ingeniería mecánica, metalurgia, tribología y control digital para garantizar que el proceso de conformado sea eficiente, preciso y sostenible. La combinación de materiales de alta resistencia, geometrías optimizadas, recubrimientos especializados, sistemas de lubricación y monitoreo en tiempo real permite que las prensas modernas produzcan piezas complejas, duraderas y de alta calidad, al mismo tiempo que reducen desperdicios, prolongan la vida útil de los componentes y minimizan el consumo energético. Esta integración tecnológica hace que la embutición continúe siendo un proceso estratégico y competitivo en la manufactura avanzada del siglo XXI, adaptándose a las demandas de precisión, velocidad, sostenibilidad y flexibilidad requeridas por los mercados más exigentes.
Prensa de Estirado de Láminas
La prensa de estirado de láminas es un equipo fundamental en la industria metalúrgica y de manufactura, especialmente en sectores como la automotriz, aeroespacial, electrodomésticos y envases metálicos, donde se requiere transformar láminas metálicas planas en piezas tridimensionales con formas complejas y tolerancias muy precisas. A diferencia de otros procesos de conformado, el estirado de láminas permite al metal fluir uniformemente sobre un troquel mediante la acción de un punzón, estirando el material sin romperlo y obteniendo paredes delgadas y uniformes, nervaduras estructurales y detalles geométricos complejos que serían imposibles de lograr con troquelado o corte simples. Este método es especialmente valioso cuando se necesitan piezas ligeras pero resistentes, ya que el estirado mejora las propiedades mecánicas del metal mediante el endurecimiento por deformación, aumentando su rigidez y durabilidad sin añadir grosor innecesario.
El funcionamiento de la prensa de estirado se basa en la coordinación precisa entre punzón, troquel y cojín de sujeción. La lámina metálica se coloca sobre el troquel y se asegura mediante un anillo o cojín que mantiene la chapa en posición, evitando desplazamientos indeseados. Luego, el punzón desciende aplicando fuerza progresiva, haciendo que el metal fluya y adopte la forma del molde. La presión del cojín y la velocidad de desplazamiento del punzón son parámetros críticos que se ajustan cuidadosamente según el tipo de metal, el espesor de la lámina y la complejidad de la pieza. La automatización de estos procesos, mediante sistemas hidráulicos o servoaccionados, permite un control extremadamente preciso de la fuerza y el desplazamiento, garantizando uniformidad y calidad en cada ciclo de producción.
La prensa de estirado de láminas moderna integra además sistemas de lubricación y sensores de monitoreo que optimizan el flujo del metal y prolongan la vida útil de los troqueles. La lubricación uniforme reduce la fricción, evita arrugas o desgarros y asegura un acabado superficial de alta calidad. Los sensores supervisan la presión aplicada, la posición del punzón y las posibles variaciones en la geometría de la pieza en tiempo real, permitiendo realizar ajustes automáticos durante el ciclo y manteniendo la producción dentro de tolerancias estrictas. Este nivel de control es crucial en aplicaciones donde la precisión es determinante, como en componentes estructurales de automóviles, carcasas de electrodomésticos o envases metálicos de alta calidad.
La automatización y la integración con líneas robóticas permiten que la prensa de estirado funcione de manera continua, alimentando chapas de forma automática, retirando las piezas conformadas y trasladándolas a estaciones de acabado o ensamblaje. Esta coordinación incrementa la productividad, reduce el riesgo laboral y garantiza la repetitividad de la producción. Además, la flexibilidad de las prensas modernas permite adaptarse rápidamente a distintos diseños o materiales, haciendo posible fabricar diferentes piezas en una misma línea simplemente cambiando el troquel y ajustando parámetros de presión y velocidad.
En términos de sostenibilidad, la prensa de estirado de láminas contribuye a la eficiencia de la producción al minimizar desperdicios de material y reducir el consumo energético. La optimización de troqueles, la recuperación de energía en sistemas servoaccionados y el uso controlado de lubricantes permiten reducir costos operativos y el impacto ambiental, cumpliendo con estándares modernos de producción responsable.
En resumen, la prensa de estirado de láminas es una herramienta estratégica en la manufactura avanzada, capaz de transformar láminas planas en piezas complejas y resistentes, combinando precisión, eficiencia, repetitividad y sostenibilidad. Su integración con sistemas digitales, robótica y control en tiempo real asegura la calidad constante de cada pieza, consolidándola como un equipo indispensable en industrias que requieren productos de alta calidad y gran volumen.
En la fabricación de piezas automotrices complejas, la prensa de estirado de láminas desempeña un papel crucial al permitir producir componentes que requieren formas tridimensionales complicadas, paredes uniformes y refuerzos estructurales integrados sin necesidad de ensamblajes adicionales. Piezas como paneles de carrocería, techos, puertas, guardabarros, cubiertas de motor y refuerzos de bastidor se obtienen mediante estirado profundo, un proceso en el que la lámina metálica fluye controladamente dentro del troquel mientras el punzón aplica fuerza progresiva. Este flujo uniforme del material permite mantener espesor constante, evitar arrugas o grietas y mejorar la resistencia mecánica gracias al endurecimiento por deformación, lo que resulta en componentes más rígidos y ligeros, cumpliendo con los requisitos de seguridad, eficiencia energética y rendimiento del vehículo. La precisión dimensional de estas prensas es fundamental, ya que incluso pequeñas variaciones pueden afectar el ensamblaje final, la alineación de paneles, la apertura de puertas y la integración de sistemas eléctricos o mecánicos, haciendo indispensable el uso de controles digitales avanzados, sensores de presión y desplazamiento, y sistemas de monitoreo en tiempo real para garantizar uniformidad y calidad en cada pieza.
El uso de prensas de estirado de láminas en la industria automotriz también permite optimizar el aprovechamiento del material, reduciendo desperdicios de chapa y mejorando la sostenibilidad del proceso. Los troqueles modernos están diseñados mediante simulación por elementos finitos para prever cómo fluirá el metal, minimizando zonas críticas que podrían generar arrugas o adelgazamiento excesivo. Los recubrimientos de alta durabilidad y los sistemas de lubricación controlada aseguran que cada pieza salga con acabado superficial uniforme y sin defectos, evitando la necesidad de operaciones de rectificado o acabado posteriores que incrementarían el costo y el tiempo de producción. Además, la automatización de la línea permite que robots alimenten las láminas, retiren las piezas estiradas y las transporten a estaciones de ensamblaje o pintura, manteniendo la repetitividad y reduciendo la intervención humana, lo que incrementa la seguridad laboral y la eficiencia global de la planta.
En el sector de envases metálicos, la prensa de estirado de láminas también ha demostrado ser indispensable, especialmente para la producción de latas, botes y recipientes con paredes delgadas y uniformes que requieren tolerancias estrictas para garantizar cierre hermético, resistencia mecánica y capacidad volumétrica exacta. Mediante embutición profunda combinada con estirado, es posible fabricar envases altos y de diámetro reducido sin arrugas ni desgarros, optimizando el uso del material y reduciendo el desperdicio. Los sistemas de control digital y los sensores permiten ajustar la presión, velocidad y lubricación de manera continua, adaptándose automáticamente a variaciones mínimas del material o cambios de diseño, lo que garantiza consistencia en series largas de producción masiva. La automatización robótica asegura que cada envase sea manipulado con precisión, alimentando chapas, retirando piezas conformadas y transportándolas a líneas de inspección, envasado y empaquetado sin intervención humana directa, manteniendo los estándares de higiene y seguridad requeridos en alimentos, bebidas y productos farmacéuticos.
Además, la prensa de estirado de láminas contribuye a la sostenibilidad industrial, no solo al optimizar el aprovechamiento del material y reducir desperdicios, sino también al disminuir el consumo energético mediante sistemas servoaccionados y recuperación de energía en movimientos de retorno del punzón. La combinación de eficiencia, precisión y automatización permite cumplir con los estándares modernos de producción responsable, reduciendo emisiones y costos operativos, y garantizando un ciclo de vida más largo de los troqueles y componentes de la máquina. Esta integración tecnológica convierte al estirado de láminas en un proceso clave para la manufactura avanzada, donde la calidad, la repetitividad, la velocidad y la sostenibilidad son factores esenciales para mantener la competitividad y cumplir con los requerimientos de los mercados más exigentes.
Las técnicas avanzadas de estirado profundo y la combinación de embutición con estirado representan un nivel superior en la conformación de láminas metálicas, permitiendo fabricar piezas con geometrías complejas, paredes delgadas y estructuras reforzadas que serían imposibles de lograr con métodos tradicionales de estampado o corte. En estas técnicas, el control preciso de la presión del punzón, la fuerza del cojín y la velocidad de desplazamiento es fundamental para garantizar que la chapa fluya de manera uniforme a lo largo del troquel sin generar arrugas, desgarros o adelgazamiento excesivo en zonas críticas. La simulación por elementos finitos y los programas de diseño asistido permiten anticipar el comportamiento del metal durante cada ciclo, identificando puntos de tensión máxima, zonas de flujo crítico y áreas susceptibles a defectos, lo que posibilita ajustar previamente la geometría del troquel y los parámetros de prensa para optimizar cada pieza antes de iniciar la producción.
En la industria automotriz, estas técnicas se aplican para producir componentes estructurales de gran complejidad, como techos, paneles laterales, cubiertas de motor y refuerzos de chasis. La capacidad de estirar profundamente la chapa permite integrar nervaduras, curvaturas y detalles funcionales en una sola pieza, eliminando la necesidad de ensamblajes múltiples y soldaduras que podrían debilitar la estructura o aumentar el peso. El resultado son piezas más ligeras pero con alta rigidez y resistencia mecánica, cumpliendo con los estrictos estándares de seguridad y eficiencia energética del sector. La automatización completa de estas prensas, combinada con robots para alimentación y extracción de piezas, asegura repetitividad, productividad y seguridad, mientras los sistemas de monitoreo en tiempo real ajustan la fuerza y la velocidad según el comportamiento del material en cada ciclo.
En el sector de envases metálicos, el estirado profundo combinado con embutición permite fabricar latas y recipientes de gran altura y diámetro reducido, con paredes uniformes y tolerancias precisas para garantizar cierre hermético, resistencia estructural y estética perfecta. La lubricación controlada y la geometría optimizada del troquel facilitan el flujo uniforme del metal, evitando arrugas o desgarros incluso en envases de paredes extremadamente finas. La precisión de estos sistemas es crítica para series masivas de producción, donde cualquier desviación puede generar defectos significativos, pérdidas de material y problemas en el envasado o transporte. Los sistemas de inspección automática detectan irregularidades en tiempo real, asegurando que solo los envases conformes continúen en la línea de producción, incrementando la eficiencia y reduciendo desperdicios.
La combinación de embutición y estirado también permite trabajar con una amplia variedad de materiales, incluyendo acero, aluminio, cobre y aleaciones ligeras, adaptando los parámetros de presión, velocidad y lubricación a cada tipo de metal. Esto resulta esencial en aplicaciones donde se busca reducir el peso del producto final sin comprometer la resistencia, como en componentes automotrices, aeroespaciales y electrodomésticos de alta calidad. La optimización del material y la precisión de los troqueles aseguran que cada pieza cumpla con las especificaciones dimensionales y mecánicas, mientras que la automatización y el control digital garantizan repetitividad y eficiencia en la producción.
En términos de sostenibilidad, estas técnicas avanzadas contribuyen a minimizar el consumo energético, reducir desperdicios de material y prolongar la vida útil de los troqueles y componentes de la prensa. Los sistemas servoaccionados y de recuperación de energía, junto con la lubricación eficiente y la planificación de ciclos de producción optimizados, permiten operar de manera responsable y económica, cumpliendo con estándares modernos de eficiencia y cuidado ambiental. Esto hace que el estirado profundo y la embutición combinada no solo sean procesos estratégicos para obtener piezas de alta calidad, sino también herramientas clave para una manufactura sostenible y competitiva en industrias de alto volumen y precisión.
Si quieres, puedo continuar detallando los diferentes tipos de prensas y troqueles especializados para estirado profundo, incluyendo sus configuraciones hidráulicas, mecánicas y servoaccionadas, y cómo cada tipo se adapta a distintas aplicaciones industriales para optimizar la producción y la calidad de las piezas.
Las prensas y troqueles especializados para estirado profundo están diseñados para adaptarse a distintas aplicaciones industriales, optimizando la producción y garantizando la calidad de las piezas metálicas con geometrías complejas y paredes delgadas. Las prensas pueden clasificarse principalmente en mecánicas, hidráulicas y servoaccionadas, cada una con ventajas específicas según el tipo de material, la profundidad del estirado y la complejidad de la pieza. Las prensas mecánicas se caracterizan por su rapidez en ciclos cortos y son ideales para producciones masivas de piezas de geometría relativamente sencilla, donde la velocidad de operación es más importante que la flexibilidad. Estas prensas utilizan un volante y un sistema de bielas para transformar el movimiento rotativo en un desplazamiento lineal del punzón, aplicando fuerza de manera repetitiva y constante. Sin embargo, su capacidad de ajuste dinámico es limitada en comparación con sistemas hidráulicos o servoaccionados, por lo que se utilizan principalmente en series largas y estandarizadas.
Las prensas hidráulicas, por su parte, permiten un control mucho más preciso de la fuerza aplicada durante todo el recorrido del punzón, lo que resulta esencial para piezas con embutidos profundos, formas complejas y materiales de alta resistencia. La presión hidráulica puede ajustarse gradualmente a lo largo de la trayectoria, evitando defectos como arrugas o adelgazamiento excesivo y garantizando un flujo uniforme de la chapa. Estas prensas son más lentas que las mecánicas en términos de ciclos por minuto, pero su versatilidad y capacidad para manejar diferentes espesores y tipos de metal las hace indispensables en aplicaciones donde la calidad y precisión son críticas, como componentes automotrices, aeroespaciales o envases metálicos de gran altura.
Por último, las prensas servoaccionadas combinan velocidad, precisión y eficiencia energética, utilizando motores eléctricos controlados por software para desplazar el punzón de manera exacta según perfiles programados. Esto permite aplicar fuerza progresiva en zonas específicas de la pieza, adaptar la velocidad en función de la complejidad geométrica y reducir el consumo eléctrico al accionar únicamente cuando es necesario. Las servoprensas ofrecen un alto grado de repetitividad y flexibilidad, lo que facilita cambiar de un diseño a otro sin necesidad de modificar físicamente la máquina, simplemente ajustando parámetros de control y reemplazando el troquel. Además, estas prensas son ideales para trabajos de estirado profundo combinados con embutición compleja, donde se requiere un control preciso del flujo del material para mantener espesor uniforme y evitar defectos.
Los troqueles especializados para estirado profundo también presentan gran diversidad según la aplicación. Se diseñan con geometrías optimizadas que guían la chapa a lo largo de la trayectoria de estirado, incorporando radios, nervaduras y relieve que permiten formar piezas tridimensionales complejas con paredes delgadas y resistentes. La elección del material del troquel, normalmente aceros de alta resistencia tratados térmicamente y recubiertos con materiales de baja fricción, es fundamental para soportar miles de ciclos de producción sin desgaste prematuro. La lubricación integrada y controlada, aplicada automáticamente, asegura un flujo uniforme del metal, reduce la fricción, evita arrugas y protege tanto la chapa como la herramienta. En troqueles avanzados, se incorporan sensores de presión, posición y temperatura para monitorear el estirado en tiempo real, detectar anomalías y ajustar parámetros automáticamente, garantizando la consistencia y calidad de cada pieza producida.
En aplicaciones industriales como la automotriz, la combinación de prensas servoaccionadas con troqueles de estirado profundo permite producir piezas integrales complejas, como paneles de carrocería, techos con nervaduras, cubiertas de motor y refuerzos de bastidor, eliminando la necesidad de ensamblajes adicionales y soldaduras que podrían debilitar la estructura o aumentar el peso del vehículo. En la industria de envases metálicos, este mismo enfoque permite fabricar latas y contenedores altos con paredes uniformes, logrando tolerancias precisas para garantizar cierre hermético, resistencia mecánica y estética impecable, incluso en series de producción masiva. La integración de robots para alimentación, extracción y traslado de piezas completa la automatización, incrementando productividad, seguridad y repetitividad, mientras los sistemas de inspección detectan cualquier defecto antes de que la pieza continúe en la línea.
En términos de sostenibilidad y eficiencia, estas prensas y troqueles avanzados permiten reducir desperdicio de material, optimizar el consumo energético y prolongar la vida útil de los componentes. La recuperación de energía en movimientos de retorno del punzón, el uso controlado de lubricantes y la programación de ciclos optimizados contribuyen a una operación más económica y ecológica. Esto convierte a las prensas de estirado profundo y sus troqueles especializados en herramientas estratégicas para la manufactura avanzada, capaces de cumplir con altos estándares de calidad, repetitividad y sostenibilidad en industrias exigentes como la automotriz, aeroespacial, de envases metálicos y electrodomésticos.
Si quieres, puedo continuar explicando las diferencias entre estirado simple, embutición profunda y combinaciones avanzadas, mostrando cómo cada técnica afecta el flujo del material, la resistencia final de la pieza y la eficiencia del proceso industrial.
Prensa de Conformado Metálico
La prensa de conformado metálico es un equipo esencial en la industria de manufactura de piezas metálicas, utilizada para transformar láminas o planchas de metal en componentes tridimensionales con formas complejas, mediante la aplicación de fuerza controlada sobre la chapa a través de troqueles específicos. Este tipo de prensa permite realizar múltiples operaciones de conformado, como estirado, embutición, doblado, corte y embutición profunda, logrando piezas con alta precisión dimensional, acabados superficiales uniformes y propiedades mecánicas mejoradas gracias al endurecimiento por deformación del metal. La versatilidad de la prensa de conformado metálico la hace indispensable en sectores como la automotriz, aeroespacial, electrodomésticos, envases metálicos y maquinaria industrial, donde los componentes requieren resistencia estructural, geometrías complejas y tolerancias estrictas para un ensamblaje perfecto.
El funcionamiento de la prensa de conformado se basa en la interacción precisa entre el punzón, el troquel y sistemas de sujeción o cojines que mantienen la chapa en la posición correcta durante todo el ciclo de trabajo. La lámina se coloca sobre el troquel y se aplica fuerza mediante el punzón, deformando el material hasta adoptar la forma deseada. La presión, velocidad de desplazamiento y trayectoria del punzón se ajustan según el tipo de metal, espesor de la chapa y complejidad de la pieza, asegurando que el metal fluya de manera uniforme y evitando defectos como arrugas, desgarros o adelgazamiento excesivo en zonas críticas. Las prensas modernas integran sistemas hidráulicos o servoaccionados que permiten un control preciso y repetitivo, garantizando la uniformidad y calidad de cada ciclo de producción, además de facilitar la adaptación a diferentes piezas sin necesidad de cambiar la estructura de la prensa, simplemente ajustando parámetros de control y cambiando el troquel.
La automatización de la prensa de conformado metálico ha revolucionado la producción industrial, incorporando sistemas robóticos para la alimentación de láminas, la extracción de piezas conformadas y su traslado a estaciones de acabado o ensamblaje. Estos sistemas permiten que la operación sea continua, segura y altamente eficiente, reduciendo la intervención humana en zonas de riesgo y aumentando la productividad. Además, la prensa puede integrarse con sistemas de visión artificial y sensores de monitoreo que verifican la calidad de cada pieza en tiempo real, midiendo dimensiones, detectando defectos superficiales y asegurando que cada componente cumpla con las especificaciones requeridas antes de pasar a la siguiente etapa del proceso productivo.
El diseño de los troqueles para conformado metálico es fundamental para garantizar la calidad y durabilidad del proceso. Se utilizan aceros especiales de alta resistencia, tratados térmicamente y recubiertos con materiales de baja fricción para soportar miles de ciclos de producción sin desgaste prematuro. La geometría del troquel se optimiza mediante software de simulación, calculando radios, relieves, nervaduras y zonas críticas donde la chapa experimentará mayor deformación, asegurando que el metal fluya correctamente y que la pieza final tenga paredes uniformes y dimensiones exactas. La lubricación controlada, aplicada de manera automática durante cada ciclo, reduce la fricción, evita arrugas y protege tanto la chapa como la herramienta, prolongando la vida útil de los troqueles y asegurando un acabado superficial de alta calidad.
En términos de sostenibilidad, la prensa de conformado metálico contribuye a la eficiencia de la producción al minimizar desperdicios de material, reducir el consumo de energía y prolongar la vida útil de los troqueles y componentes de la máquina. La recuperación de energía en sistemas servoaccionados, el uso controlado de lubricantes y la programación de ciclos optimizados permiten operar de manera más económica y ecológica, cumpliendo con estándares modernos de producción responsable. Esto hace que la prensa de conformado metálico sea una herramienta estratégica en la manufactura avanzada, capaz de producir piezas complejas, precisas, resistentes y sostenibles, esenciales en industrias que demandan alta calidad, repetitividad, productividad y adaptabilidad.
Las prensas de conformado metálico pueden clasificarse principalmente en tres tipos: mecánicas, hidráulicas y servoaccionadas, cada una adaptada a necesidades específicas de producción, complejidad de las piezas y tipo de material. Las prensas mecánicas son tradicionalmente utilizadas para producción en serie de piezas con geometrías más simples, ya que ofrecen ciclos rápidos y repetitivos, aplicando fuerza mediante un sistema de volante y bielas que transforma el movimiento rotativo en desplazamiento lineal del punzón. Su rapidez es ideal para manufacturas de alto volumen, aunque la flexibilidad en ajustes de presión y recorrido es limitada, lo que las hace más adecuadas para series largas y estandarizadas donde la consistencia de la pieza es más importante que la adaptación a distintos diseños.
Por su parte, las prensas hidráulicas proporcionan un control mucho más preciso de la fuerza durante todo el recorrido del punzón, permitiendo trabajar con piezas de geometría compleja, embutidos profundos y materiales de alta resistencia sin riesgo de arrugas, desgarros o adelgazamiento excesivo. La presión hidráulica puede ajustarse progresivamente a lo largo del ciclo, optimizando el flujo del metal y asegurando que la deformación sea uniforme, lo que resulta crucial en la producción de componentes automotrices, aeroespaciales y electrodomésticos donde la precisión y calidad dimensional son determinantes. Aunque estas prensas suelen ser más lentas que las mecánicas, su versatilidad y capacidad para adaptarse a diferentes espesores y materiales las hacen indispensables en procesos donde la repetitividad y la exactitud son críticas.
Las prensas servoaccionadas representan la combinación más avanzada de velocidad, precisión y eficiencia energética. Utilizan motores eléctricos controlados por software que permiten desplazar el punzón según perfiles programados, aplicando fuerza progresiva en áreas específicas de la pieza y adaptando la velocidad en función de la geometría y propiedades del material. Esto permite producir piezas con alta complejidad geométrica y tolerancias muy estrictas, optimizando el flujo del metal y evitando defectos incluso en embutición profunda combinada con estirado. Su flexibilidad permite cambiar de un diseño a otro sin necesidad de modificar la estructura de la máquina, simplemente ajustando parámetros de control y reemplazando el troquel, lo que es ideal para industrias que requieren producción de diferentes piezas en la misma línea sin detener la operación.
Los troqueles utilizados en prensas de conformado metálico son igualmente críticos para garantizar calidad y durabilidad. Se fabrican con aceros de alta resistencia, tratados térmicamente y recubiertos con materiales de baja fricción, lo que permite soportar miles de ciclos de producción sin desgaste prematuro. La geometría del troquel se optimiza mediante simulación por elementos finitos, incorporando radios, relieves, nervaduras y zonas críticas donde la chapa experimenta mayores tensiones. Esto asegura que la lámina fluya correctamente, evitando arrugas, adelgazamiento excesivo o deformaciones indeseadas, y que la pieza final cumpla con las dimensiones y tolerancias requeridas. Los sistemas de lubricación automática reducen la fricción y protegen tanto la chapa como el troquel, garantizando un acabado superficial uniforme y prolongando la vida útil de la herramienta.
La automatización completa de estas prensas permite integrar robots para alimentación de láminas, extracción de piezas y traslado a estaciones de ensamblaje o acabado, incrementando la productividad, seguridad y repetitividad del proceso. Sensores de presión, desplazamiento y temperatura monitorean cada ciclo en tiempo real, detectando cualquier anomalía y ajustando automáticamente los parámetros de operación, asegurando que cada pieza cumpla con estándares de calidad estrictos antes de continuar en la línea de producción. En industrias como la automotriz, aeroespacial, electrodomésticos y envases metálicos, esta integración tecnológica permite fabricar piezas complejas, ligeras y resistentes, optimizando material, energía y tiempo.
En términos de sostenibilidad, las prensas de conformado metálico avanzadas permiten minimizar desperdicios de material, reducir el consumo energético y prolongar la vida útil de los troqueles y componentes de la prensa. La recuperación de energía en movimientos de retorno, el uso controlado de lubricantes y la programación de ciclos optimizados contribuyen a una operación más eficiente y ecológica, cumpliendo con estándares modernos de producción responsable. Esto convierte a la prensa de conformado metálico en un elemento estratégico para la manufactura avanzada, capaz de producir piezas de alta calidad, precisas, resistentes y sostenibles, esenciales para mantener la competitividad en mercados exigentes y garantizar productos confiables en sectores que demandan precisión, repetitividad y eficiencia.
Los procesos combinados de estirado, embutición y doblado en prensas de conformado metálico representan el nivel más avanzado de fabricación de piezas de geometría compleja, permitiendo obtener componentes tridimensionales con paredes delgadas, nervaduras estructurales, curvas precisas y tolerancias estrictas en un solo ciclo o mediante ciclos secuenciales coordinados. En estos sistemas, la chapa metálica se somete a fuerzas controladas y progresivas que la hacen fluir sobre los troqueles de manera uniforme, evitando arrugas, desgarros o adelgazamientos irregulares, mientras que las diferentes etapas del proceso se combinan para formar detalles funcionales y estéticos sin necesidad de ensamblajes adicionales. Por ejemplo, en la industria automotriz, es posible producir paneles de carrocería, techos, puertas y cubiertas de motor con nervaduras integradas y curvaturas complejas que mejoran la rigidez estructural y reducen el peso total del vehículo, optimizando el rendimiento y la eficiencia energética.
La coordinación entre estirado, embutición y doblado requiere un control extremadamente preciso de la presión del punzón, el desplazamiento, la velocidad de la chapa y la fuerza de sujeción del cojín, ajustándose dinámicamente según las propiedades del metal, el espesor de la lámina y la complejidad de la pieza. Los sistemas modernos de control digital y servoaccionamiento permiten programar perfiles de presión y velocidad específicos para cada sección de la pieza, asegurando que el metal fluya correctamente y que cada detalle geométrico se reproduzca con exactitud. Además, los troqueles se diseñan mediante software de simulación avanzada, considerando radios de curvatura, relieves, nervaduras y zonas de tensión máxima, lo que permite prever cualquier comportamiento crítico del material antes de la fabricación física del troquel y reducir costos y tiempos de prueba.
La lubricación controlada es otro factor clave en estos procesos combinados, ya que reduce la fricción entre la chapa y las superficies del troquel, facilita el flujo del metal, evita marcas y defectos superficiales y protege tanto la lámina como el troquel de desgaste prematuro. La aplicación automática y sincronizada de lubricante en cada ciclo garantiza que todas las áreas críticas estén adecuadamente cubiertas, lo que resulta esencial en piezas de alta complejidad o de materiales delicados, como aluminio, cobre o aceros de alta resistencia. Los sistemas de monitoreo en tiempo real supervisan presión, desplazamiento, temperatura y lubricación, detectando cualquier desviación y ajustando automáticamente los parámetros del proceso, asegurando una producción homogénea y reduciendo el riesgo de desperdicio de material.
En líneas de producción completamente automatizadas, robots y sistemas de transporte integrados alimentan las láminas, extraen las piezas conformadas y las trasladan a estaciones de inspección, ensamblaje o acabado, permitiendo mantener ciclos de producción continuos, repetitivos y de alta velocidad sin comprometer la calidad. La integración de visión artificial y sensores de inspección dimensional asegura que cada componente cumpla con tolerancias estrictas, detectando defectos superficiales o desviaciones geométricas antes de que la pieza avance a la siguiente etapa, incrementando la eficiencia, reduciendo retrabajos y optimizando el uso de materiales.
Estos procesos combinados no solo mejoran la calidad y complejidad de las piezas, sino que también contribuyen significativamente a la sostenibilidad y eficiencia industrial. La optimización del flujo del material, la reducción de desperdicios, el uso eficiente de energía mediante sistemas servoaccionados y la prolongación de la vida útil de troqueles y componentes de la prensa permiten operaciones más económicas y ecológicas. Esto convierte a las prensas de conformado metálico con estirado, embutición y doblado combinados en herramientas estratégicas para la manufactura avanzada, capaces de producir piezas ligeras, resistentes y precisas en industrias como la automotriz, aeroespacial, de envases metálicos y electrodomésticos, donde la demanda de calidad, repetitividad, productividad y sostenibilidad es máxima.
El diseño y la optimización de líneas de producción que combinan estirado, embutición y doblado requieren una integración cuidadosa de múltiples elementos, incluyendo prensas de alta precisión, troqueles especializados, sistemas de automatización robótica, transporte de piezas y estaciones de inspección y control de calidad. Cada componente de la línea debe estar coordinado para garantizar que la chapa metálica fluya sin interrupciones desde la alimentación hasta la extracción de la pieza final, manteniendo un control constante sobre la presión, la velocidad y la trayectoria del punzón, así como sobre la fuerza del cojín y la lubricación aplicada. La sincronización de los ciclos de las prensas con los robots de carga y descarga permite un flujo continuo de producción, minimizando tiempos muertos y aumentando la productividad, mientras que los sistemas de transporte automatizados garantizan que cada pieza llegue a la estación correspondiente en el momento exacto, evitando golpes, deformaciones o errores de posicionamiento.
El diseño de troqueles en estas líneas de producción es igualmente crucial. Cada troquel se fabrica con aceros de alta resistencia tratados térmicamente y recubiertos con materiales de baja fricción, optimizando la durabilidad y reduciendo el desgaste durante miles de ciclos de producción. La geometría se calcula mediante simulaciones por elementos finitos, considerando radios, nervaduras, relieves y zonas de tensión máxima para asegurar un flujo uniforme del material y evitar defectos como arrugas, desgarros o adelgazamientos irregulares. En líneas avanzadas, se incorporan sensores de presión, desplazamiento y temperatura en cada troquel, lo que permite ajustar automáticamente la operación de la prensa en tiempo real y mantener la producción dentro de tolerancias estrictas, aumentando la calidad de cada pieza sin interrumpir la línea.
La automatización de la lubricación y la monitorización digital se integran para garantizar que la fricción entre la chapa y el troquel se mantenga dentro de niveles óptimos, facilitando el flujo uniforme del metal, protegiendo la herramienta y asegurando un acabado superficial uniforme. Esta integración permite que piezas extremadamente complejas, con paredes delgadas, nervaduras integradas y detalles geométricos precisos, sean producidas de manera repetitiva y confiable, sin necesidad de intervenciones manuales que podrían generar errores o retrasos. Los sistemas robóticos pueden alimentar láminas desde rollos o pallets, retirar las piezas conformadas y colocarlas en estaciones de inspección automática, donde cámaras y sensores verifican dimensiones, tolerancias y acabados, detectando cualquier anomalía antes de que la pieza continúe en la línea o se someta a procesos adicionales como pintura, ensamblaje o empaque.
En términos de eficiencia y sostenibilidad, estas líneas optimizadas permiten minimizar desperdicios de material, reducir el consumo energético y prolongar la vida útil de troqueles y componentes de la prensa. La recuperación de energía en sistemas servoaccionados, la programación de ciclos optimizados y la aplicación controlada de lubricantes contribuyen a operaciones más económicas y responsables con el medio ambiente. Esto resulta especialmente importante en industrias de alto volumen, como la automotriz y de envases metálicos, donde la reducción de desperdicios y la eficiencia energética impactan directamente en los costos de producción y en la competitividad del producto final.
La integración de estirado, embutición y doblado en una línea de producción también permite adaptar rápidamente la fabricación a nuevos diseños o modificaciones de piezas, simplemente cambiando troqueles y ajustando parámetros de control, lo que otorga flexibilidad sin sacrificar productividad ni calidad. Esta capacidad de adaptación es fundamental en sectores donde los ciclos de diseño y producción son cortos y la personalización de piezas es frecuente, garantizando que la manufactura pueda responder de manera ágil a cambios en la demanda del mercado, nuevos materiales o especificaciones técnicas más exigentes.
En conjunto, las líneas de producción de conformado metálico avanzado representan la máxima expresión de la manufactura industrial moderna, combinando precisión, repetitividad, productividad y sostenibilidad. Permiten producir piezas metálicas complejas, resistentes y precisas, con mínima intervención humana, optimizando el flujo de material y energía, reduciendo desperdicios y garantizando la calidad constante en cada ciclo. Su implementación es estratégica para industrias que requieren alto volumen, gran exactitud dimensional y control de calidad exhaustivo, asegurando que cada pieza cumpla con los estándares más exigentes y que la operación sea eficiente, segura y sostenible.
Los sistemas de control y monitoreo en tiempo real en las líneas de prensas de conformado metálico son fundamentales para garantizar la repetitividad, calidad y eficiencia en la producción de piezas complejas. Estos sistemas integran una red de sensores, actuadores y software de supervisión que permiten controlar cada aspecto del proceso, desde la presión aplicada por el punzón hasta la posición exacta de la chapa sobre el troquel. Los sensores de presión miden la fuerza ejercida en cada fase del estirado o embutición, asegurando que el metal fluya de manera uniforme y evitando arrugas, desgarros o adelgazamiento excesivo. Al mismo tiempo, los sensores de desplazamiento y posición registran la trayectoria del punzón y la ubicación de la lámina, garantizando que cada movimiento se ejecute con precisión milimétrica, mientras que los sensores de temperatura y fricción controlan las condiciones de lubricación y calor, fundamentales para proteger el material y prolongar la vida útil de los troqueles.
El software de control central coordina todos estos datos en tiempo real, comparando las mediciones con los parámetros preestablecidos y ajustando automáticamente la presión, la velocidad y el recorrido del punzón cuando se detectan desviaciones. Esto permite mantener la producción dentro de tolerancias estrictas sin necesidad de intervención humana constante, reduciendo errores, desperdicio de material y retrabajos. Además, el sistema registra toda la información del ciclo de producción, generando historiales de cada pieza, lo que facilita la trazabilidad, el análisis de fallas y la optimización continua del proceso. La capacidad de monitoreo en tiempo real también permite detectar problemas en troqueles o sistemas de sujeción antes de que provoquen daños mayores, evitando paradas no planificadas y asegurando la continuidad de la línea.
Los actuadores eléctricos, hidráulicos o servoaccionados reciben instrucciones del software de control para ejecutar movimientos precisos del punzón y los cojines de sujeción, aplicando fuerza y velocidad adaptadas a cada zona de la pieza. Esto es especialmente importante en procesos combinados de estirado, embutición y doblado, donde diferentes secciones de la chapa requieren diferentes intensidades de deformación. La coordinación de actuadores con sensores garantiza que cada sección de la pieza reciba la presión adecuada, evitando defectos y mejorando la uniformidad del material. En prensas servoaccionadas avanzadas, el software puede programar perfiles de fuerza y velocidad específicos para cada pieza, optimizando la producción de series diversas sin necesidad de reconfiguración física de la máquina, lo que aumenta la flexibilidad y reduce los tiempos de cambio de producción.
La integración de sistemas de visión artificial completa el monitoreo, permitiendo inspeccionar la geometría, los bordes y la superficie de la pieza al salir del troquel. Cámaras de alta resolución capturan imágenes en tiempo real, y el software analiza posibles irregularidades, desviaciones o marcas superficiales, enviando alertas al sistema de control para correcciones automáticas o separando piezas defectuosas. Esto garantiza que solo los componentes que cumplen con las especificaciones avanzadas continúen en la línea, incrementando la calidad final del producto y reduciendo el desperdicio de material. La combinación de sensores, actuadores, software de control y visión artificial hace que la línea funcione como un sistema completamente integrado, capaz de producir piezas complejas con repetitividad, precisión y eficiencia máximas.
Además, estos sistemas contribuyen a la eficiencia energética y sostenibilidad de la planta. La programación optimizada de movimientos reduce el consumo de energía, y los sistemas servoaccionados permiten aprovechar la recuperación de energía en los movimientos de retorno del punzón. La lubricación se aplica de manera controlada según el flujo de material y la presión registrada por los sensores, minimizando el uso excesivo de lubricantes y prolongando la vida útil de los troqueles y de la prensa. Esta integración tecnológica asegura que la operación sea segura, eficiente, económica y respetuosa con el medio ambiente, cumpliendo con estándares modernos de manufactura responsable.
En conjunto, los sistemas de control y monitoreo en tiempo real permiten que las líneas de prensas de conformado metálico produzcan piezas tridimensionales complejas con alta precisión, consistencia y velocidad, optimizando recursos y reduciendo riesgos. La coordinación de todos los elementos asegura que el metal fluya correctamente, que cada pieza cumpla con tolerancias estrictas y que la producción pueda adaptarse rápidamente a nuevos diseños o materiales. Esto hace que la prensa de conformado metálico moderna no solo sea una herramienta de transformación de material, sino un sistema integral de manufactura avanzada, capaz de satisfacer las exigencias de industrias como la automotriz, aeroespacial, de electrodomésticos y envases metálicos, donde la calidad, repetitividad, productividad y sostenibilidad son imprescindibles.
Si quieres, puedo continuar explicando los tipos de automatización avanzada en estas prensas, incluyendo líneas robóticas de alimentación, transporte y ensamblaje, y cómo se integran con el software de control y visión artificial para lograr producción completamente autónoma y altamente eficiente.
Prensa para Estampado de Chapa
La prensa para estampado de chapa es un equipo fundamental en la industria metalúrgica e industrial, diseñada para transformar láminas metálicas planas en piezas tridimensionales mediante la aplicación de fuerza controlada sobre la chapa a través de troqueles específicos. Este tipo de prensa permite realizar operaciones como estampado, corte, doblado, embutición y conformado, logrando componentes con alta precisión dimensional, acabados superficiales uniformes y propiedades mecánicas mejoradas gracias al endurecimiento por deformación del metal. Es utilizada en sectores como la automotriz, aeroespacial, electrodomésticos, envases metálicos, maquinaria industrial y construcción, donde las piezas requieren resistencia estructural, geometrías complejas y tolerancias estrictas para garantizar un ensamblaje perfecto y funcionamiento seguro.
El funcionamiento de la prensa para estampado de chapa se basa en la interacción precisa entre el punzón, el troquel y los sistemas de sujeción que mantienen la chapa en la posición correcta durante el ciclo de trabajo. La lámina se coloca sobre el troquel y el punzón aplica fuerza progresiva para deformar el metal hasta adoptar la forma deseada. La presión, la velocidad de desplazamiento y el recorrido del punzón se ajustan según el tipo de material, el espesor de la chapa y la complejidad de la pieza, asegurando que el metal fluya de manera uniforme y evitando defectos como arrugas, desgarros o adelgazamiento irregular. En prensas modernas, los sistemas hidráulicos o servoaccionados permiten un control preciso de cada ciclo, garantizando uniformidad y calidad constante en todas las piezas producidas, así como la posibilidad de adaptar rápidamente la máquina a diferentes diseños sin necesidad de modificar la estructura física, solo cambiando troqueles y ajustando parámetros de control.
Los troqueles son un elemento crítico en el estampado de chapa, ya que determinan la geometría final, la precisión dimensional y la durabilidad de la herramienta. Se fabrican con aceros de alta resistencia tratados térmicamente y recubiertos con materiales de baja fricción, capaces de soportar miles de ciclos de producción sin desgaste prematuro. La geometría del troquel se optimiza mediante simulaciones por elementos finitos, considerando radios, relieves, nervaduras y zonas de mayor tensión para asegurar que el metal fluya correctamente y que la pieza final tenga paredes uniformes y acabado superficial de alta calidad. La lubricación controlada reduce la fricción y protege tanto la chapa como el troquel, evitando marcas superficiales y aumentando la vida útil de la herramienta.
La automatización de la prensa para estampado de chapa ha permitido integrar robots para alimentación de láminas, extracción de piezas y transporte hacia estaciones de inspección, ensamblaje o acabado, incrementando la productividad, seguridad y repetitividad del proceso. Sensores de presión, desplazamiento y temperatura monitorean cada ciclo en tiempo real, detectando cualquier desviación y ajustando automáticamente los parámetros de la prensa para mantener la producción dentro de tolerancias estrictas. Sistemas de visión artificial verifican la geometría, acabados y dimensiones de cada pieza, separando automáticamente las que no cumplen con los estándares, lo que reduce desperdicios y garantiza consistencia en la producción.
En cuanto a eficiencia y sostenibilidad, las prensas de estampado de chapa modernas optimizan el uso de material, reducen desperdicios, disminuyen el consumo energético y prolongan la vida útil de troqueles y componentes de la prensa. La recuperación de energía en movimientos de retorno, el uso controlado de lubricantes y la programación de ciclos optimizados contribuyen a operaciones más económicas y responsables con el medio ambiente, cumpliendo con estándares de producción industrial moderna. Este nivel de integración tecnológica convierte a la prensa para estampado de chapa en un equipo estratégico para la fabricación de piezas metálicas complejas, precisas, resistentes y sostenibles, esenciales para industrias que demandan alta calidad, repetitividad, productividad y flexibilidad.
Las prensas para estampado de chapa se clasifican principalmente en mecánicas, hidráulicas y servoaccionadas, y cada tipo está diseñado para satisfacer necesidades específicas de producción, complejidad de las piezas y características del material. Las prensas mecánicas son ampliamente utilizadas en la producción en serie de piezas con geometrías más simples y repetitivas, gracias a su velocidad de operación y ciclos cortos. Funcionan mediante un volante y un sistema de bielas que transforma el movimiento rotativo en desplazamiento lineal del punzón, aplicando fuerza de manera constante en cada ciclo. Aunque ofrecen alta velocidad, su capacidad de ajuste dinámico es limitada, por lo que resultan más adecuadas para producciones estandarizadas donde la consistencia es prioritaria y la flexibilidad es secundaria. Son ideales para componentes de grandes volúmenes como paneles de carrocería, cubiertas y piezas de maquinaria industrial que no requieren cambios frecuentes en el diseño del troquel.
Las prensas hidráulicas, en cambio, proporcionan un control más preciso de la fuerza durante todo el recorrido del punzón, permitiendo trabajar con piezas de geometría compleja, embutidos profundos y metales de alta resistencia sin riesgo de defectos como arrugas, desgarros o adelgazamiento irregular. La presión hidráulica puede ajustarse progresivamente a lo largo del ciclo de trabajo, optimizando el flujo del metal y asegurando que la deformación sea uniforme, lo que resulta crucial en aplicaciones automotrices, aeroespaciales y de electrodomésticos de alta precisión. Aunque son más lentas que las mecánicas, su versatilidad y capacidad de adaptarse a distintos espesores y materiales las hacen indispensables en procesos donde la exactitud y la calidad de cada pieza son determinantes.
Las prensas servoaccionadas representan la máxima expresión de control, velocidad y eficiencia energética. Están equipadas con motores eléctricos controlados por software que permiten desplazar el punzón según perfiles programados, aplicando fuerza y velocidad adaptadas a cada zona de la pieza. Esto es fundamental en piezas con detalles complejos, nervaduras, curvaturas y embutición profunda combinada con estirado, donde diferentes secciones requieren distintas intensidades de deformación. Su flexibilidad permite cambiar de diseño rápidamente, simplemente ajustando parámetros de control y reemplazando el troquel, sin necesidad de modificar la estructura física de la máquina, lo que reduce tiempos de parada y aumenta la productividad en líneas que fabrican múltiples piezas distintas.
Los troqueles en estas prensas son igualmente determinantes para garantizar calidad, precisión y durabilidad. Se fabrican con aceros de alta resistencia tratados térmicamente y recubiertos con materiales de baja fricción, capaces de soportar miles de ciclos de producción. Su geometría se diseña mediante simulaciones por elementos finitos, optimizando radios, nervaduras, relieves y zonas críticas para asegurar que la chapa fluya uniformemente y que la pieza final cumpla con tolerancias estrictas. La lubricación controlada aplicada automáticamente reduce fricción, protege tanto la chapa como el troquel y evita defectos superficiales, asegurando acabados uniformes y prolongando la vida útil de la herramienta.
La integración de sistemas robóticos y automatización en estas prensas ha transformado completamente la producción industrial. Robots alimentan láminas desde rollos o pallets, extraen las piezas conformadas y las trasladan a estaciones de inspección, ensamblaje o acabado. Sensores de presión, desplazamiento y temperatura supervisan cada ciclo en tiempo real, ajustando automáticamente los parámetros de la prensa cuando se detectan desviaciones, mientras sistemas de visión artificial inspeccionan dimensiones, tolerancias y acabados, separando piezas defectuosas antes de continuar en la línea. Esto asegura producción continua, repetitiva, segura y de alta calidad, con mínima intervención humana y máxima eficiencia.
En términos de sostenibilidad, las prensas modernas optimizan el uso de material, reducen desperdicios y el consumo de energía, prolongando la vida útil de troqueles y componentes de la máquina. La recuperación de energía en movimientos de retorno, la lubricación controlada y la programación de ciclos optimizados permiten operaciones más económicas y responsables con el medio ambiente, cumpliendo con estándares industriales modernos. La combinación de precisión, velocidad, repetitividad y eficiencia convierte a la prensa para estampado de chapa en una herramienta estratégica para la fabricación de piezas metálicas complejas, resistentes, precisas y sostenibles, esenciales en industrias que demandan alta productividad, calidad constante y flexibilidad para adaptarse a cambios en diseños, materiales o demandas del mercado.
Los procesos avanzados de estampado progresivo y multietapa en prensas de chapa representan uno de los niveles más sofisticados de la manufactura metálica, permitiendo transformar láminas planas en piezas tridimensionales complejas mediante una secuencia controlada de operaciones integradas en un solo ciclo de línea. En el estampado progresivo, la chapa metálica se desplaza automáticamente a través de una serie de estaciones o troqueles sucesivos, cada uno de los cuales realiza una operación específica, como corte, embutición, estirado, doblado o punzonado. Este sistema asegura que cada sección de la pieza se forme de manera controlada y precisa, evitando deformaciones, arrugas o adelgazamientos irregulares, y optimizando el flujo del material desde la alimentación hasta la pieza final. La coordinación de estas operaciones permite reducir tiempos de producción y minimizar la intervención humana, aumentando la repetitividad y la calidad de las piezas producidas.
En el estampado multietapa, la hoja metálica puede someterse a diferentes tipos de deformación en una sola prensa equipada con múltiples punzones y cojines, aplicando fuerzas diferenciadas según la geometría de cada zona. Esto es especialmente útil en piezas de gran complejidad, donde las paredes pueden tener espesores variables, las curvaturas son pronunciadas y se requieren nervaduras o relieves funcionales integrados en el diseño. La presión, velocidad y recorrido de cada punzón se ajustan mediante sistemas hidráulicos o servoaccionados que permiten aplicar fuerza progresiva y controlada, adaptándose a las propiedades del material y asegurando que la deformación sea uniforme en todas las secciones. La sincronización precisa entre los diferentes elementos de la prensa garantiza que cada operación se ejecute en el momento exacto, evitando conflictos entre movimientos y asegurando la integridad de la pieza.
Los troqueles para estampado progresivo y multietapa son diseñados cuidadosamente mediante simulaciones por elementos finitos, considerando radios de curvatura, nervaduras, relieves y zonas de máxima tensión para garantizar que el metal fluya correctamente y que la pieza final cumpla con las tolerancias dimensionales requeridas. Se fabrican con aceros de alta resistencia tratados térmicamente y recubiertos con materiales de baja fricción, capaces de soportar miles de ciclos sin desgaste prematuro. La lubricación automática se aplica de manera sincronizada durante cada etapa, reduciendo fricción, evitando marcas superficiales y protegiendo tanto la chapa como el troquel. Esto asegura un acabado superficial uniforme, prolonga la vida útil de la herramienta y mantiene la consistencia de cada pieza producida.
La automatización y el monitoreo en tiempo real son componentes esenciales en estas líneas de estampado avanzado. Robots alimentan las láminas, extraen las piezas formadas y las trasladan a estaciones de inspección, ensamblaje o acabado, mientras sensores de presión, desplazamiento, temperatura y fricción supervisan cada ciclo, ajustando automáticamente los parámetros de la prensa cuando se detectan desviaciones. Sistemas de visión artificial verifican geometría, dimensiones, tolerancias y acabados, separando piezas defectuosas antes de continuar en la línea, lo que garantiza un flujo continuo de producción con calidad constante y mínima intervención humana.
Además, estas líneas optimizadas contribuyen significativamente a la eficiencia y sostenibilidad de la producción industrial. La programación de ciclos optimizados, el uso de prensas servoaccionadas que permiten recuperar energía en los movimientos de retorno, y la aplicación controlada de lubricantes minimizan el consumo de energía y recursos, reduciendo desperdicios y prolongando la vida útil de los componentes. La combinación de precisión, repetitividad, velocidad y eficiencia convierte al estampado progresivo y multietapa en una solución estratégica para la manufactura de piezas metálicas complejas, resistentes, precisas y sostenibles, especialmente en industrias automotriz, aeroespacial, de electrodomésticos y envases metálicos, donde la demanda de calidad, productividad y flexibilidad es máxima.
La integración de líneas completas de estampado progresivo con robots, sistemas de transporte y estaciones de control de calidad permite que la producción de piezas metálicas complejas se realice de manera totalmente automatizada, eficiente y confiable. En estas líneas, la chapa metálica se alimenta desde rollos o pallets mediante sistemas robóticos o transportadores automáticos, que garantizan posicionamiento exacto y continuidad en la alimentación, evitando interrupciones que puedan afectar la calidad de la pieza o generar desperdicio de material. A medida que la lámina avanza por la línea, pasa por cada estación de troqueles donde se ejecutan operaciones específicas, como corte inicial, embutición, estirado, doblado o punzonado, y en cada etapa los sensores supervisan la presión, el desplazamiento del punzón, la fuerza aplicada y la temperatura de la pieza, ajustando automáticamente los parámetros para mantener la deformación uniforme y dentro de tolerancias estrictas.
Los robots no solo alimentan la materia prima, sino que también extraen las piezas conformadas de cada estación y las trasladan hacia la siguiente fase de procesamiento o hacia estaciones de inspección. En estas estaciones, sistemas de visión artificial y escáneres tridimensionales verifican dimensiones, geometría, curvaturas, acabados superficiales y presencia de defectos como arrugas, adelgazamiento irregular o marcas de troquel, separando automáticamente las piezas que no cumplen los estándares de calidad. Esta combinación de automatización y control en tiempo real permite mantener un flujo continuo de producción con mínima intervención humana, asegurando que cada componente fabricado cumpla con las especificaciones requeridas y que la repetitividad sea máxima, incluso en producciones de alto volumen o en líneas con múltiples variantes de diseño.
Los sistemas de transporte integrados garantizan que cada pieza llegue a la estación correcta sin riesgo de deformación o daños, coordinando los movimientos de robots, cintas transportadoras y mesas giratorias según la programación de la línea. Además, los sistemas de monitoreo registran datos de cada ciclo, generando historiales completos de producción que permiten trazabilidad, análisis de eficiencia, detección temprana de fallas y optimización continua de procesos. Esto no solo mejora la calidad y la consistencia, sino que también facilita la planificación de mantenimiento preventivo, la gestión de troqueles y componentes, y la reducción de tiempos de parada no planificados.
La sincronización entre prensas, robots, transportadores y sistemas de inspección permite ejecutar operaciones combinadas de estirado, embutición, doblado y corte de manera secuencial y coordinada, logrando piezas con geometrías complejas, paredes delgadas, nervaduras integradas y detalles funcionales sin necesidad de ensamblaje adicional. Cada estación puede ajustarse de forma individual mediante software de control, adaptando presión, velocidad y trayectoria del punzón según el diseño de la pieza, el espesor y el tipo de material, lo que otorga gran flexibilidad a la línea de producción para cambios rápidos entre diferentes modelos sin comprometer la productividad ni la calidad.
En términos de eficiencia y sostenibilidad, estas líneas avanzadas optimizan el uso de materiales, reducen desperdicios, disminuyen el consumo energético y prolongan la vida útil de los troqueles y componentes de la prensa. La recuperación de energía en sistemas servoaccionados, la aplicación controlada de lubricantes y la programación de ciclos optimizados permiten operaciones más económicas y respetuosas con el medio ambiente, cumpliendo con estándares de manufactura moderna. Gracias a esta integración tecnológica, la línea completa se convierte en un sistema de producción estratégico, capaz de fabricar piezas metálicas complejas, resistentes, precisas y repetitivas, con mínima intervención humana y máxima eficiencia, especialmente en industrias automotriz, aeroespacial, de envases metálicos y electrodomésticos, donde la calidad, productividad, seguridad y sostenibilidad son fundamentales.
Prensa Mecánica de Embutición
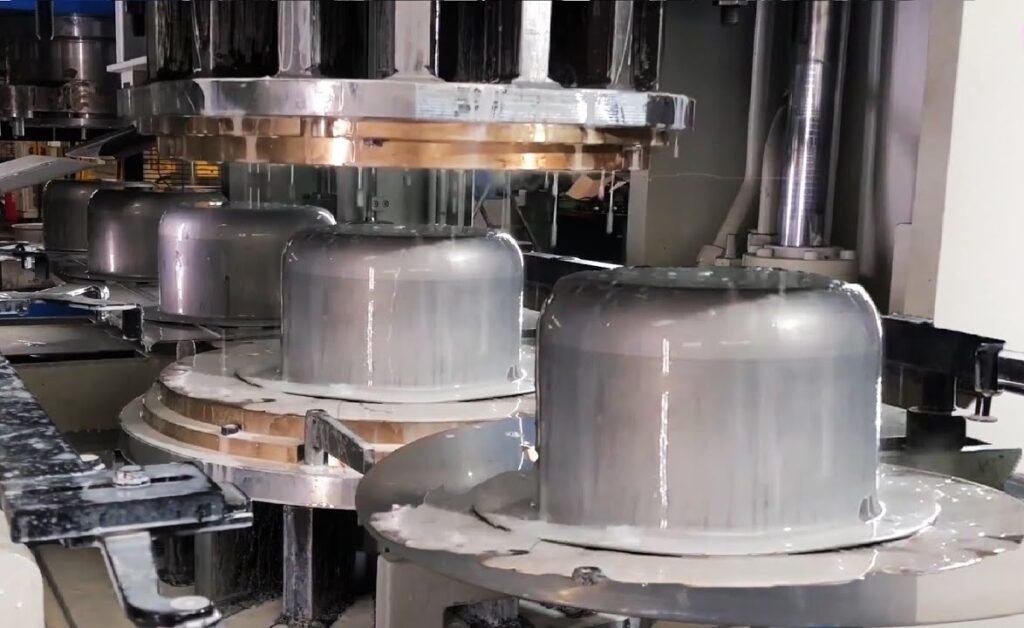
La prensa mecánica de embutición es un equipo fundamental en la industria metalúrgica e industrial, diseñado específicamente para dar forma a láminas metálicas mediante la aplicación de fuerza mecánica controlada a través de un punzón y un troquel. Este tipo de prensa se utiliza principalmente en procesos de embutición, estirado y conformado de piezas metálicas, permitiendo transformar láminas planas en componentes tridimensionales con paredes uniformes, curvaturas precisas y acabados superficiales de alta calidad. Su funcionamiento se basa en un sistema de volante, cigüeñal y bielas que convierte el movimiento rotativo del motor en un desplazamiento lineal del punzón, generando la fuerza necesaria para deformar el metal de manera controlada y repetitiva. Esta característica hace que las prensas mecánicas sean ideales para producciones en serie de piezas con geometrías estandarizadas, donde la consistencia, velocidad y repetitividad son prioritarias, como en la fabricación de envases metálicos, paneles automotrices, tapas, carcasas y piezas de maquinaria industrial.
El diseño de la prensa mecánica de embutición permite ajustar ciertos parámetros, como la velocidad del ciclo y la altura del golpe, lo que posibilita adaptar el equipo a distintos espesores y tipos de metal, aunque con menor flexibilidad que las prensas hidráulicas o servoaccionadas. La fuerza aplicada es constante durante el golpe, lo que resulta eficiente para deformaciones uniformes, pero requiere que el diseño del troquel esté cuidadosamente calculado para evitar arrugas, desgarros o adelgazamiento irregular de la chapa. Los troqueles utilizados en este tipo de prensa se fabrican con aceros de alta resistencia tratados térmicamente y recubiertos con materiales de baja fricción para prolongar su vida útil y garantizar un acabado uniforme. La geometría del troquel se optimiza mediante simulaciones y pruebas previas para asegurar que la chapa fluya correctamente y que la pieza final cumpla con las tolerancias dimensionales requeridas.
Aunque la prensa mecánica de embutición carece de la capacidad de aplicar fuerza progresiva controlada durante todo el ciclo como lo hacen las prensas hidráulicas, su velocidad de operación y capacidad para trabajar en ciclos cortos la hacen altamente productiva. Es especialmente adecuada para líneas de producción donde se requiere un alto volumen de piezas repetitivas con diseño estable, permitiendo integrar sistemas automáticos de alimentación de láminas, extracción de piezas y transporte hacia estaciones de inspección o ensamblaje. La automatización parcial o completa aumenta la seguridad operativa, reduce la intervención manual y asegura la consistencia en la producción, garantizando que cada pieza cumpla con los estándares de calidad.
El mantenimiento de las prensas mecánicas de embutición es un aspecto crítico para mantener su rendimiento y precisión. Se requiere lubricación regular de cojinetes, engranajes y guías, inspección de bielas y cigüeñales, y calibración periódica de la altura de golpe y la alineación del punzón con el troquel. Estas tareas aseguran que la fuerza se aplique de manera uniforme y que las piezas producidas mantengan tolerancias precisas a lo largo de miles de ciclos de producción. La durabilidad y confiabilidad de estas prensas, junto con su velocidad de operación, las hacen ideales para producciones continuas de piezas metálicas de geometría estándar donde la eficiencia y la repetitividad son clave.
Las prensas mecánicas de embutición permiten realizar procesos avanzados como embutición profunda, estirado progresivo y troquelado combinado, integrando varias operaciones en un solo ciclo o en ciclos secuenciales altamente coordinados. En la embutición profunda, la chapa metálica se transforma en recipientes, cubiertas o componentes con paredes altas en relación con su diámetro, manteniendo uniformidad en el espesor y evitando arrugas o desgarros mediante un control preciso de la posición del punzón y la presión aplicada, así como un diseño optimizado del troquel. Este proceso es ampliamente utilizado en la fabricación de envases metálicos, bombonas, carcasas automotrices y piezas industriales donde se requiere máxima rigidez estructural y acabado superficial de alta calidad. La chapa fluye gradualmente sobre las superficies del troquel gracias a la fuerza constante de la prensa mecánica y la lubricación controlada, asegurando un resultado uniforme y repetitivo en cada ciclo.
El estirado progresivo combina varias operaciones de conformado, corte y embutición, permitiendo que la lámina avance automáticamente a través de estaciones sucesivas dentro del troquel. Cada estación realiza una deformación específica, como alargar paredes, formar nervaduras, relieves o detalles funcionales integrados, mientras los cojines y punzones aplican fuerza controlada para guiar el metal sin generar tensiones excesivas que puedan producir fallas. Este enfoque permite producir piezas complejas en un solo ciclo de línea, reduciendo la necesidad de ensamblaje posterior y aumentando la productividad. Las prensas mecánicas se benefician de su alta velocidad de ciclo para este tipo de procesos, aunque requieren un diseño de troquel extremadamente preciso y un mantenimiento constante para asegurar que todos los componentes se alineen correctamente y funcionen de manera sincronizada.
El troquelado combinado en prensas mecánicas permite cortar, punzonar, embutir o estirar la pieza en un mismo golpe, lo que incrementa la eficiencia y reduce el tiempo de manipulación de la lámina. Cada troquel se fabrica con acero de alta resistencia tratado térmicamente y recubierto con materiales de baja fricción para soportar la presión constante y la fricción del metal durante miles de ciclos de producción. La geometría del troquel se calcula mediante simulaciones avanzadas para asegurar que el flujo del metal sea uniforme, evitando adelgazamientos irregulares o marcas superficiales, mientras que la lubricación automática reduce la fricción y prolonga la vida útil de la herramienta. Este tipo de troquelado es ideal para componentes automotrices, electrodomésticos, envases metálicos y piezas industriales donde se requiere repetitividad, alta precisión y acabados estéticos impecables.
La integración de sistemas automáticos de alimentación y extracción aumenta la eficiencia y seguridad en líneas que utilizan prensas mecánicas de embutición. Robots o transportadores colocan la lámina sobre el troquel, alineándola con precisión, mientras que otros sistemas retiran las piezas conformadas y las trasladan a estaciones de inspección, ensamblaje o acabado. Sensores de presión, desplazamiento y temperatura monitorean cada golpe en tiempo real, detectando cualquier desviación y permitiendo ajustes inmediatos para mantener tolerancias estrictas y consistencia en la producción. La combinación de automatización, monitoreo y control mecánico asegura que incluso en producciones de alto volumen, la calidad de cada pieza se mantenga constante, y que la línea funcione de manera continua con mínima intervención humana.
El mantenimiento preventivo y la calibración periódica son esenciales para maximizar la vida útil y la eficiencia de las prensas mecánicas de embutición. Esto incluye lubricación de cojinetes, engranajes y guías, verificación de bielas y cigüeñales, ajuste de la altura de golpe y alineación precisa del punzón con el troquel. Un mantenimiento adecuado garantiza que la fuerza se aplique uniformemente en cada ciclo, evitando deformaciones indeseadas y asegurando que las piezas cumplan con las especificaciones de diseño a lo largo de miles de ciclos de producción. La combinación de velocidad, repetitividad, control mecánico preciso y mantenimiento riguroso convierte a la prensa mecánica de embutición en una herramienta esencial para la producción industrial de piezas metálicas complejas, resistentes y precisas, especialmente en sectores donde la calidad, productividad y eficiencia son prioritarias.
La comparación entre prensas mecánicas, hidráulicas y servoaccionadas para embutición permite entender cómo cada tipo se adapta a distintas necesidades de producción, geometría de piezas y materiales, optimizando eficiencia, precisión y productividad según los requerimientos industriales. Las prensas mecánicas, como se explicó, se caracterizan por su velocidad de ciclo y fuerza constante, lo que las hace ideales para producciones en serie de piezas estandarizadas con geometrías simples o medianamente complejas. Su sistema de volante, bielas y cigüeñal transforma el movimiento rotativo en lineal, aplicando fuerza en cada golpe de manera repetitiva, garantizando uniformidad en las deformaciones, pero con menor flexibilidad para ajustar la fuerza durante el recorrido del punzón. Este tipo de prensa es eficiente en líneas donde la pieza y el troquel permanecen constantes, como en la fabricación de envases metálicos, tapas, carcasas o paneles automotrices, y se complementa con sistemas automáticos de alimentación y extracción para optimizar la productividad.
Por su parte, las prensas hidráulicas ofrecen un control más preciso de la fuerza durante todo el ciclo, lo que permite embutición profunda, estirado y conformado de piezas complejas con geometrías irregulares o paredes variables. La presión hidráulica puede ajustarse progresivamente, controlando la velocidad y la fuerza en cada fase del golpe, lo que reduce riesgos de arrugas, desgarros o adelgazamiento irregular. Este tipo de prensa es ideal para piezas que requieren deformaciones delicadas y uniformes, como componentes automotrices de alta complejidad, carcasas aeroespaciales o piezas industriales donde la calidad y precisión son críticas. Su velocidad de ciclo es menor que la mecánica, pero la flexibilidad y adaptabilidad permiten cambios rápidos de diseño sin modificar la estructura de la máquina, ajustando solo parámetros de presión, recorrido y velocidad.
Las prensas servoaccionadas combinan lo mejor de los sistemas mecánicos e hidráulicos, ofreciendo velocidad, control dinámico de la fuerza y eficiencia energética. Los motores eléctricos controlados por software permiten programar perfiles de fuerza y velocidad específicos para cada pieza, aplicando diferentes intensidades de deformación en distintas zonas de la chapa. Esto es crucial en piezas con detalles complejos, nervaduras, curvaturas pronunciadas o embutición profunda combinada con estirado, donde cada sección requiere un control preciso del flujo del metal. Las prensas servoaccionadas también permiten integrar fácilmente líneas automatizadas con robots, transportadores y sistemas de visión artificial, logrando producción totalmente autónoma, repetitiva y de alta calidad, mientras se optimiza el consumo energético mediante recuperación de energía en movimientos de retorno y control eficiente de los motores.
Cada tipo de prensa tiene ventajas y limitaciones que determinan su aplicación industrial. Las mecánicas destacan por velocidad y simplicidad, ideales para producción masiva de piezas repetitivas; las hidráulicas por precisión y control progresivo, recomendadas para piezas complejas o embutición profunda; y las servoaccionadas por flexibilidad, eficiencia energética y capacidad de integración en líneas totalmente automatizadas, siendo la opción más versátil para la manufactura moderna. La selección adecuada depende del tipo de pieza, volumen de producción, materiales y necesidades de calidad y tolerancia.
El mantenimiento, calibración y monitoreo son críticos en los tres tipos de prensa. Las mecánicas requieren lubricación y verificación de bielas, cigüeñales y alineación; las hidráulicas precisan control del sistema de presión, válvulas y fluido hidráulico; y las servoaccionadas, además de componentes mecánicos e hidráulicos, necesitan supervisión y actualización del software de control y motores eléctricos. Un mantenimiento adecuado garantiza fuerza uniforme, repetitividad y larga vida útil de troqueles y componentes, asegurando producción continua y consistente.
El diseño y fabricación de troqueles para prensas de embutición, ya sean mecánicas, hidráulicas o servoaccionadas, es un proceso crítico que determina la precisión, la durabilidad y la calidad de las piezas metálicas producidas. Los troqueles se elaboran con aceros de alta resistencia tratados térmicamente y, en muchos casos, recubiertos con materiales de baja fricción como nitruros o revestimientos PVD para soportar la presión constante, reducir desgaste y minimizar marcas superficiales sobre la chapa. La geometría del troquel se diseña cuidadosamente mediante simulaciones por elementos finitos, considerando radios de curvatura, ángulos de relieve, nervaduras, espesores de pared y zonas de tensión máxima para asegurar que el flujo del metal sea uniforme y que la pieza final cumpla con las tolerancias dimensionales y requisitos funcionales. Cada detalle del troquel es esencial: desde la forma de los bordes hasta la alineación de los punzones, ya que cualquier desviación puede generar defectos como arrugas, desgarros o adelgazamiento irregular.
Durante la fabricación de troqueles, se utilizan procesos de mecanizado de alta precisión como fresado CNC, electroerosión por hilo y rectificado, asegurando que cada superficie cumpla con tolerancias estrictas y un acabado óptimo. En troqueles complejos, se incorporan sistemas de cojines y guías para controlar la deformación del metal y permitir embutición profunda o estirado progresivo sin comprometer la integridad de la pieza. La lubricación es también un componente crítico del troquel: canales internos permiten aplicar lubricante de forma controlada en zonas de mayor fricción, reduciendo desgaste y evitando defectos superficiales en la pieza. El mantenimiento y ajuste de los troqueles son esenciales; se requiere inspección periódica para detectar desgaste, grietas o deformaciones, y rectificaciones precisas para mantener la producción dentro de tolerancias estrictas.
En troqueles para prensas mecánicas, la fuerza constante del golpe requiere que la geometría esté optimizada para el flujo uniforme del metal durante la embutición y el estirado, asegurando que la pieza no se deforme indebidamente durante el ciclo rápido. En prensas hidráulicas, los troqueles pueden diseñarse con geometrías más complejas, aprovechando la capacidad de aplicar fuerza progresiva y controlada a lo largo de todo el recorrido del punzón, lo que permite embutición profunda, nervaduras o relieves funcionales sin riesgo de arrugas o adelgazamiento excesivo. En prensas servoaccionadas, los troqueles se combinan con perfiles de fuerza programables, ajustando la presión y la velocidad según la sección de la pieza para lograr resultados de alta precisión y calidad, incluso en diseños extremadamente complejos o en materiales de alta resistencia.
La integración de troqueles con sistemas automáticos de alimentación, extracción y transporte permite líneas de producción totalmente coordinadas, donde la chapa avanza de manera precisa a través de cada estación de conformado. Sensores de presión, desplazamiento y temperatura monitorizan el comportamiento del metal en tiempo real, detectando cualquier desviación y ajustando los parámetros de la prensa o alertando a los operadores para intervenciones preventivas. Los sistemas de visión artificial inspeccionan cada pieza después del conformado, verificando dimensiones, geometría y acabados, asegurando que solo las piezas que cumplen con los estándares continúen en la línea. Esto reduce desperdicios, aumenta la eficiencia y garantiza una calidad constante en la producción de alto volumen.
Los troqueles modernos permiten, además, optimizar la eficiencia energética y sostenibilidad de la producción. El control preciso de fuerzas y desplazamientos reduce el consumo de energía, la lubricación controlada minimiza desperdicio de fluidos, y la durabilidad prolongada de los troqueles disminuye la necesidad de reemplazos frecuentes. En conjunto, el diseño, fabricación, mantenimiento y utilización de troqueles de alta calidad convierte a las prensas de embutición en sistemas completos de manufactura avanzada capaces de producir piezas metálicas complejas, precisas, resistentes y repetitivas, cumpliendo con los más altos estándares de la industria automotriz, aeroespacial, de electrodomésticos y de envases metálicos.
Prensa Hidráulica de Embutición
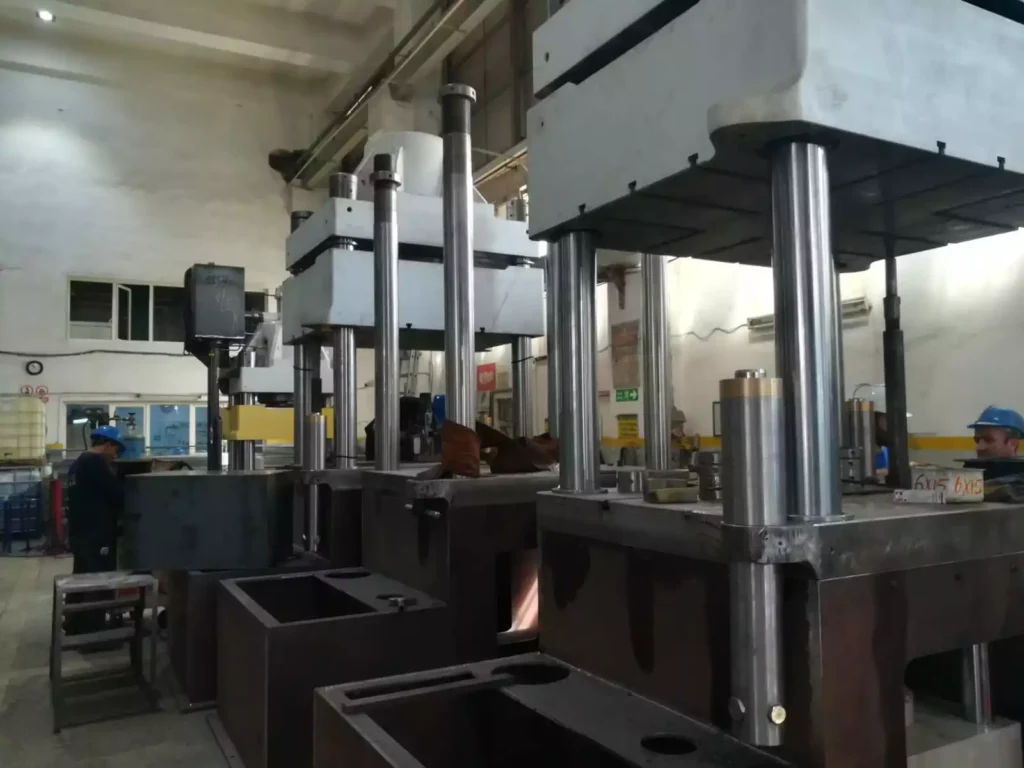
La prensa hidráulica de embutición es un equipo clave en la industria metalúrgica, diseñado para conformar láminas metálicas en piezas tridimensionales mediante la aplicación de fuerza controlada a través de un sistema hidráulico. A diferencia de las prensas mecánicas, donde la fuerza se mantiene constante durante el golpe, las prensas hidráulicas permiten regular la presión y la velocidad a lo largo de todo el recorrido del punzón, lo que posibilita deformaciones más precisas y controladas, especialmente en piezas de geometría compleja o en embutición profunda. Este tipo de prensa se utiliza ampliamente en la fabricación de componentes automotrices, aeroespaciales, electrodomésticos, envases metálicos y maquinaria industrial, donde se requiere alta calidad, tolerancias estrictas y acabados superficiales uniformes.
El funcionamiento de la prensa hidráulica de embutición se basa en un sistema de cilindros y válvulas que controlan el flujo del fluido hidráulico, generando fuerza lineal sobre el punzón de manera progresiva. Esta capacidad de ajuste permite aplicar distintas intensidades de presión en diferentes zonas de la pieza, optimizando el flujo del metal y evitando defectos como arrugas, desgarros o adelgazamiento irregular. La chapa se coloca sobre el troquel y, a medida que el punzón desciende, el metal fluye de manera controlada hacia las cavidades del troquel, tomando la forma deseada. La velocidad de desplazamiento del punzón y la presión aplicada se programan según el tipo de material, espesor de la lámina y complejidad de la pieza, garantizando uniformidad y repetitividad en cada ciclo de producción.
Los troqueles utilizados en prensas hidráulicas de embutición son esenciales para lograr piezas de alta precisión y durabilidad. Se fabrican con aceros tratados térmicamente y, en muchos casos, recubiertos con materiales de baja fricción para soportar la presión y el desgaste constante. La geometría de los troqueles se diseña mediante simulaciones por elementos finitos, considerando radios de curvatura, nervaduras, relieves y zonas de máxima tensión, asegurando que el flujo del metal sea uniforme y que la pieza final cumpla con las tolerancias dimensionales requeridas. La lubricación controlada aplicada durante el ciclo reduce la fricción, protege tanto la chapa como el troquel y garantiza un acabado superficial uniforme y de alta calidad.
Las prensas hidráulicas permiten realizar embutición profunda, estirado progresivo, troquelado combinado y conformado de piezas complejas en un solo ciclo de trabajo, lo que incrementa la eficiencia y reduce la necesidad de operaciones secundarias. Su capacidad de ajuste progresivo de fuerza es ideal para piezas con paredes delgadas, nervaduras pronunciadas o relieves funcionales, permitiendo deformaciones precisas sin comprometer la integridad del material. Esto las hace especialmente útiles en la fabricación de componentes automotrices, aeroespaciales, carcasas de electrodomésticos y envases metálicos donde la calidad y precisión son determinantes.
La integración de prensas hidráulicas con sistemas de automatización permite aumentar la productividad, seguridad y consistencia en la producción. Robots alimentan las láminas, extraen las piezas conformadas y las trasladan hacia estaciones de inspección o ensamblaje, mientras sensores de presión, desplazamiento y temperatura monitorean cada ciclo en tiempo real, ajustando automáticamente los parámetros de la prensa para mantener tolerancias estrictas. Sistemas de visión artificial verifican geometría, dimensiones y acabados superficiales, separando piezas defectuosas antes de continuar en la línea, lo que reduce desperdicios y asegura repetitividad en la producción.
El mantenimiento de prensas hidráulicas de embutición es crítico para garantizar eficiencia, seguridad y durabilidad. Requiere revisión periódica de cilindros, válvulas, bombas y fluido hidráulico, calibración de presión y recorrido del punzón, y verificación de la alineación de troqueles. Un mantenimiento adecuado asegura que la fuerza se aplique uniformemente, que las piezas cumplan con las especificaciones y que la producción continúe sin interrupciones, maximizando la vida útil de los componentes de la prensa y los troqueles.
Las prensas hidráulicas de embutición permiten realizar procesos avanzados como embutición profunda multietapa, estirado combinado y troquelado progresivo, integrando varias operaciones en un solo ciclo de manera controlada y precisa. En la embutición profunda multietapa, la lámina metálica se transforma gradualmente en piezas con paredes altas, relieves y detalles funcionales, asegurando que el espesor sea uniforme y que no se produzcan arrugas o desgarros. Cada etapa aplica fuerza controlada sobre diferentes zonas de la chapa, utilizando cilindros y cojines hidráulicos que ajustan la presión según la sección de la pieza. Este enfoque es fundamental en la fabricación de componentes automotrices complejos, carcasas de electrodomésticos, envases metálicos de alta resistencia y piezas industriales que requieren precisión y acabado superficial impecable.
El estirado combinado permite realizar deformaciones en diferentes direcciones, integrando operaciones de estirado y embutición en un mismo ciclo, lo que reduce la necesidad de operaciones secundarias y aumenta la eficiencia de producción. La chapa se guía mediante cojines, guías y sistemas de control de fuerza, asegurando que el metal fluya correctamente y que cada sección de la pieza alcance la forma deseada sin comprometer su integridad. Esta técnica es especialmente útil en piezas con geometrías complejas, nervaduras profundas, paredes delgadas o relieves funcionales que requieren precisión dimensional estricta. La capacidad de ajustar progresivamente la fuerza y la velocidad del punzón permite trabajar con distintos tipos de metales, espesores y aleaciones, adaptando el proceso a las necesidades específicas de cada pieza.
El troquelado progresivo en prensas hidráulicas integra múltiples operaciones de corte, punzonado, estirado y embutición en un solo ciclo, permitiendo que la pieza avance automáticamente entre estaciones sucesivas sin intervención manual. Cada troquel se fabrica con acero de alta resistencia tratado térmicamente, recubierto con materiales de baja fricción para soportar la presión constante y prolongar su vida útil. La geometría se diseña mediante simulaciones por elementos finitos, considerando radios de curvatura, nervaduras, relieves y zonas de máxima tensión para garantizar que el flujo del metal sea uniforme y que la pieza final cumpla con tolerancias estrictas. La lubricación controlada reduce la fricción, evita marcas superficiales y protege tanto la chapa como el troquel durante todo el proceso.
La automatización completa de estas líneas permite que robots alimenten láminas, extraigan piezas conformadas y las trasladen a estaciones de inspección, ensamblaje o acabado, mientras sensores de presión, desplazamiento y temperatura supervisan cada golpe en tiempo real. Sistemas de visión artificial verifican dimensiones, curvaturas, geometría y acabados superficiales, separando automáticamente piezas defectuosas antes de continuar en la línea. Esta coordinación garantiza producción continua, alta repetitividad, reducción de desperdicios y mantenimiento de estándares de calidad incluso en producciones de alto volumen o en piezas con geometrías complejas.
El mantenimiento y calibración de prensas hidráulicas avanzadas es crucial para mantener la eficiencia, seguridad y precisión. Incluye revisión de cilindros, válvulas, bombas, fluido hidráulico y alineación de punzón y troquel, así como ajustes de presión y recorrido según el tipo de pieza y material. Un mantenimiento adecuado prolonga la vida útil de los componentes, asegura fuerza uniforme en cada ciclo y mantiene la producción dentro de tolerancias estrictas. La combinación de fuerza progresiva, control preciso, troqueles optimizados y automatización convierte a la prensa hidráulica de embutición en una herramienta indispensable para la fabricación de piezas metálicas complejas, precisas, resistentes y repetitivas, especialmente en sectores que demandan máxima calidad, eficiencia y adaptabilidad, como la industria automotriz, aeroespacial, de envases metálicos y electrodomésticos.
La combinación de prensas hidráulicas de embutición con software de simulación de flujo de material y control digital ha transformado completamente la manufactura de piezas metálicas complejas, permitiendo anticipar y corregir problemas antes de que ocurran en la producción real. Mediante simulaciones por elementos finitos, los ingenieros pueden modelar la deformación de la chapa bajo diferentes condiciones de fuerza, velocidad y geometría de troquel, evaluando cómo fluye el metal durante la embutición profunda, el estirado progresivo o el troquelado combinado. Estas simulaciones permiten identificar zonas críticas donde podrían aparecer arrugas, adelgazamientos o tensiones excesivas, optimizando la forma del troquel, la presión aplicada y la trayectoria del punzón para garantizar uniformidad en el espesor y acabado superficial impecable. El resultado es un diseño de proceso más eficiente y seguro, que reduce desperdicio de material, tiempo de prueba y costos asociados con ajustes manuales o retrabajos.
El control digital integrado en las prensas hidráulicas permite aplicar fuerza progresiva y ajustar la velocidad del punzón de manera extremadamente precisa, adaptándose automáticamente a las características de cada pieza y del material utilizado. Sensores de presión, desplazamiento, temperatura y fricción recopilan datos en tiempo real, y el sistema de control ajusta instantáneamente los parámetros para mantener tolerancias estrictas, asegurando que cada ciclo produzca piezas idénticas sin necesidad de intervención humana constante. Esto es especialmente útil en piezas con geometrías complejas, paredes variables y relieves funcionales, donde incluso pequeñas desviaciones pueden afectar la funcionalidad o ensamblaje final. Además, los sistemas de monitoreo digital registran cada ciclo de producción, generando históricos que permiten trazabilidad completa, análisis de eficiencia, mantenimiento predictivo y optimización continua del proceso.
La automatización completa de la línea de producción combina prensas hidráulicas con robots para alimentación de láminas, extracción de piezas conformadas, transporte hacia estaciones de inspección y ensamblaje, así como sistemas de visión artificial que verifican dimensiones, curvaturas, relieves y acabados superficiales. Cada pieza es inspeccionada al momento, y cualquier defecto detectado provoca la separación automática de la pieza antes de continuar en la línea, reduciendo desperdicios y asegurando la repetitividad en producciones de alto volumen. La sincronización entre prensas, robots, transportadores y estaciones de inspección garantiza un flujo continuo, evitando colisiones, deformaciones accidentales o retrasos en la producción.
La integración de software de simulación, control digital y automatización permite también optimizar la eficiencia energética y sostenibilidad de la producción. Las prensas hidráulicas modernas pueden recuperar energía en los movimientos de retorno, aplicar fuerza únicamente cuando es necesaria y regular el consumo de fluido hidráulico, reduciendo el gasto energético y la contaminación ambiental. La planificación de ciclos optimizados, junto con lubricación controlada y materiales de troqueles duraderos, permite mantener producción continua de alta calidad mientras se minimizan costos operativos y mantenimiento. Esta combinación tecnológica convierte a las prensas hidráulicas en sistemas estratégicos de manufactura avanzada, capaces de producir piezas metálicas complejas, precisas, resistentes y repetitivas, con máxima eficiencia, trazabilidad y calidad, cumpliendo con los exigentes estándares de la industria automotriz, aeroespacial, de electrodomésticos y de envases metálicos.
En la industria automotriz, las prensas hidráulicas de embutición se utilizan para fabricar componentes críticos de carrocerías, chasis, paneles interiores y piezas estructurales, donde la precisión, repetitividad y resistencia del material son fundamentales. Por ejemplo, en la producción de puertas, techos o guardabarros, la chapa metálica debe conformarse con relieves, nervaduras y curvaturas precisas que aseguren ajuste perfecto, rigidez estructural y compatibilidad con otros componentes durante el ensamblaje. Las prensas hidráulicas permiten aplicar fuerza progresiva controlada en cada etapa del proceso, evitando arrugas y adelgazamientos que comprometan la integridad de la pieza. El uso de cojines hidráulicos y guías asegura que el flujo del metal sea uniforme, y los troqueles optimizados mediante simulaciones por elementos finitos garantizan que cada golpe se traduzca en una pieza exacta según las especificaciones de diseño.
En las líneas de producción automotriz, la integración de prensas hidráulicas con robots y sistemas automatizados permite un flujo continuo desde la alimentación de la chapa hasta la extracción y transporte de la pieza conformada hacia estaciones de inspección o ensamblaje. Robots colocan láminas de manera precisa sobre los troqueles, los sensores monitorean la presión, desplazamiento y temperatura del metal durante cada golpe, y sistemas de visión artificial verifican dimensiones, curvaturas y acabados superficiales. Las piezas defectuosas se separan automáticamente antes de continuar, reduciendo desperdicios y asegurando que solo componentes conformes lleguen al ensamblaje final. Esta coordinación de prensas, robots y sistemas de control digital garantiza producción de alta velocidad, repetitividad y consistencia en líneas de alto volumen, manteniendo la calidad requerida para la industria automotriz.
En la fabricación de envases metálicos, como latas de alimentos, bebidas o aerosoles, las prensas hidráulicas permiten embutición profunda de chapas finas sin comprometer su integridad. El proceso se realiza en múltiples etapas, donde cada golpe del punzón aumenta gradualmente la profundidad del envase mientras mantiene el espesor uniforme de las paredes. La fuerza progresiva y controlada evita arrugas o desgarros, mientras que la lubricación específica reduce fricción y protege la superficie. Los troqueles diseñados con precisión, junto con sensores y control digital, permiten producir millones de piezas con la misma geometría y acabado, cumpliendo estrictos estándares de volumen, peso y capacidad. La automatización asegura alimentación continua de la chapa, extracción de envases conformados y transporte hacia líneas de llenado o embalaje, optimizando productividad y minimizando intervención humana.
En ambos casos, automotriz y envases metálicos, las prensas hidráulicas se complementan con software de simulación de flujo de material y control digital avanzado. Antes de fabricar una sola pieza, los ingenieros simulan la deformación del metal, identificando zonas críticas de tensión, adelgazamiento o riesgo de arrugas, y ajustando diseño de troquel, recorrido del punzón y presión aplicada. Esto reduce tiempo de pruebas físicas, desperdicio de material y costos de ajustes manuales. Durante la producción, los sistemas de monitoreo registran cada ciclo, proporcionando trazabilidad completa y permitiendo mantenimiento predictivo para evitar paradas no planificadas. La combinación de fuerza controlada, troqueles optimizados, automatización y control digital convierte a las prensas hidráulicas en herramientas estratégicas de manufactura avanzada, capaces de producir piezas metálicas complejas, precisas y repetitivas, con alta eficiencia, calidad y seguridad.
Máquina Prensa de Estampación
La máquina prensa de estampación es un equipo fundamental en la industria metalúrgica y de fabricación de componentes metálicos, diseñada para dar forma a láminas mediante la aplicación de fuerza a través de un troquel y un punzón. Su objetivo principal es transformar chapas planas en piezas tridimensionales con geometrías precisas, relieves, cortes y detalles funcionales, manteniendo uniformidad en el espesor y acabados superficiales de alta calidad. Este tipo de prensa se utiliza ampliamente en sectores como la industria automotriz, aeroespacial, electrodomésticos, envases metálicos y maquinaria industrial, donde la precisión, repetitividad y resistencia del material son esenciales.
El funcionamiento de la máquina prensa de estampación puede ser mecánico, hidráulico o servoaccionado. En las prensas mecánicas, el movimiento rotativo de un motor se transforma mediante volante, cigüeñal y bielas en un desplazamiento lineal del punzón, generando fuerza constante durante cada golpe, lo que las hace ideales para producciones en serie de piezas estandarizadas con geometrías simples o medianamente complejas. Las prensas hidráulicas, por su parte, permiten regular la presión y velocidad a lo largo de todo el recorrido del punzón, logrando deformaciones controladas incluso en piezas con geometrías complejas o embutición profunda, mientras que las prensas servoaccionadas combinan velocidad, control progresivo de fuerza y flexibilidad de programación para adaptarse a diferentes diseños y materiales, integrándose fácilmente en líneas de producción automatizadas.
Los troqueles utilizados en estas prensas son elementos críticos para garantizar precisión y durabilidad. Fabricados con aceros de alta resistencia tratados térmicamente y, en muchos casos, recubiertos con materiales de baja fricción, los troqueles soportan la presión constante del proceso y protegen la chapa de marcas superficiales. Su geometría se diseña mediante simulaciones por elementos finitos, considerando radios de curvatura, relieves, nervaduras y zonas de máxima tensión, optimizando el flujo del metal y evitando defectos como arrugas, desgarros o adelgazamiento irregular. La lubricación controlada durante el ciclo de estampación reduce fricción, protege las superficies y asegura un acabado uniforme en cada pieza producida.
La estampación puede incluir múltiples operaciones como embutición, estirado, troquelado, repujado o corte, realizadas en un solo golpe o mediante estaciones progresivas. En embutición profunda, la chapa se transforma gradualmente en recipientes o carcasas con paredes altas y uniformes; en estirado, se alargan o conforman secciones de la pieza; y en troquelado combinado, se cortan, perforan o embuten detalles funcionales en un mismo ciclo. La combinación de estas operaciones permite producir piezas complejas en serie con alta repetitividad, reduciendo necesidad de ensamblajes adicionales o procesos secundarios.
La automatización de las líneas de estampación aumenta la eficiencia, seguridad y consistencia. Robots y transportadores alimentan las láminas, extraen las piezas conformadas y las trasladan a estaciones de inspección, ensamblaje o acabado, mientras sensores de presión, desplazamiento y temperatura monitorean cada golpe en tiempo real. Sistemas de visión artificial verifican dimensiones, curvaturas, relieves y acabados, separando automáticamente piezas defectuosas y asegurando que la producción cumpla con los estándares de calidad más exigentes. La trazabilidad completa de cada ciclo permite mantenimiento predictivo, análisis de eficiencia y optimización continua del proceso, garantizando que la producción sea constante, eficiente y de alta calidad.
El mantenimiento de la máquina prensa de estampación es esencial para prolongar la vida útil de los componentes y mantener la precisión. Incluye lubricación de cojinetes y guías, revisión de bielas, cigüeñales, cilindros o motores hidráulicos, calibración de recorrido y fuerza del punzón, y verificación de alineación de troqueles. Un mantenimiento adecuado asegura que la fuerza se aplique uniformemente, que las piezas mantengan tolerancias estrictas y que la línea de producción funcione de manera continua sin interrupciones, maximizando productividad, calidad y seguridad en la fabricación de piezas metálicas de todo tipo.
Las operaciones de estampación avanzadas en una máquina prensa incluyen embutición profunda, estirado progresivo, troquelado combinado, repujado y conformado de detalles funcionales, todas ellas diseñadas para transformar láminas metálicas planas en piezas tridimensionales complejas con alta precisión y repetitividad. En la embutición profunda, la chapa se deforma gradualmente mediante golpes controlados, tomando la forma de recipientes, carcasas o componentes con paredes altas y uniformes. Cada etapa del proceso puede regularse mediante presión, velocidad y trayectoria del punzón, asegurando que el metal fluya sin arrugas ni adelgazamientos irregulares. Este método es ampliamente utilizado en la industria automotriz para fabricar paneles de carrocería, techos y guardabarros, así como en la producción de envases metálicos para alimentos, bebidas y aerosoles, donde la uniformidad de espesor y acabado superficial es crítica.
El estirado progresivo consiste en someter la lámina a deformaciones en varias direcciones mediante estaciones sucesivas de troqueles, donde cada golpe alarga, estrecha o da forma a distintas secciones de la pieza. Esta técnica permite integrar relieves, nervaduras, refuerzos estructurales y detalles funcionales directamente en la pieza, reduciendo la necesidad de ensamblajes posteriores y aumentando la resistencia y rigidez del componente final. Los troqueles para estirado progresivo se diseñan mediante simulaciones por elementos finitos para optimizar el flujo del metal, evitando defectos como arrugas, desgarros o deformaciones no deseadas, y garantizando que cada pieza cumpla con tolerancias dimensionales estrictas y acabados de alta calidad.
El troquelado combinado permite realizar varias operaciones en un solo ciclo: cortar, perforar, embutir o estirar secciones específicas de la chapa. Esta combinación reduce tiempos de producción, aumenta la eficiencia y asegura que las piezas complejas se fabriquen de manera uniforme en grandes volúmenes. Cada troquel se fabrica con acero de alta resistencia, tratado térmicamente y recubierto con materiales de baja fricción para soportar la presión constante, minimizar desgaste y proteger la superficie de la chapa. Canales de lubricación incorporados en el troquel aseguran que la fricción se reduzca y que el acabado superficial se mantenga impecable en cada ciclo.
La automatización completa de la línea de estampación integra robots para alimentación de láminas, extracción de piezas conformadas y transporte hacia estaciones de inspección, ensamblaje o acabado. Sensores de presión, desplazamiento y temperatura supervisan cada golpe en tiempo real, mientras sistemas de visión artificial verifican dimensiones, curvaturas, relieves y acabados superficiales. Las piezas defectuosas se separan automáticamente antes de continuar en la línea, reduciendo desperdicios y asegurando repetitividad en la producción de alto volumen. El software de control digital permite ajustar la fuerza, velocidad y trayectoria del punzón según la geometría y el material de cada pieza, optimizando la eficiencia energética y la calidad final.
El mantenimiento de estas máquinas incluye lubricación de cojinetes y guías, revisión de bielas, cigüeñales, cilindros hidráulicos o motores eléctricos, calibración del recorrido y fuerza del punzón, y verificación de alineación de troqueles. Este cuidado asegura que la fuerza se aplique uniformemente, que la línea de producción funcione sin interrupciones y que las piezas cumplan con las tolerancias exigidas. La combinación de fuerza controlada, troqueles optimizados, automatización, control digital y mantenimiento preventivo convierte a la máquina prensa de estampación en un sistema de manufactura avanzada capaz de producir piezas metálicas complejas, precisas, resistentes y repetitivas, cumpliendo con los más altos estándares de la industria automotriz, aeroespacial, de envases metálicos y de electrodomésticos.
La selección de materiales de chapa y los parámetros del proceso en una máquina prensa de estampación son determinantes para garantizar la calidad, la precisión y la durabilidad de las piezas producidas. La elección del tipo de metal depende de la aplicación, las propiedades mecánicas requeridas y el tipo de operación de estampación a realizar. Por ejemplo, en la industria automotriz se utilizan aceros laminados en frío o en caliente con alta resistencia y ductilidad para paneles de carrocería, puertas, techos y componentes estructurales, mientras que en la fabricación de envases metálicos se emplean láminas de aluminio o acero con recubrimientos específicos para asegurar embutición profunda sin rupturas ni arrugas. La aleación, el espesor y la dureza de la chapa determinan la presión necesaria, la velocidad de desplazamiento del punzón y la lubricación adecuada, asegurando que el flujo del metal sea uniforme y que las piezas finales cumplan tolerancias estrictas y acabados superficiales de alta calidad.
En la estampación en frío, el metal se deforma a temperatura ambiente, aprovechando su ductilidad y resistencia, ideal para piezas que requieren precisión dimensional y acabado superficial uniforme. Este proceso es más económico y adecuado para alta repetitividad y volúmenes grandes, pero requiere chapas con propiedades mecánicas adecuadas y troqueles optimizados para evitar agrietamiento o arrugas. Por otro lado, la estampación en caliente eleva la temperatura de la chapa antes de conformarla, reduciendo su resistencia y aumentando la ductilidad, lo que permite deformaciones más profundas, estirado de piezas complejas y reducción de esfuerzos residuales. Este método se utiliza en aceros de alta resistencia o aleaciones difíciles de conformar en frío, como en componentes estructurales automotrices, piezas aeroespaciales y recipientes metálicos de gran profundidad. La selección de temperatura, tiempo de calentamiento y velocidad de prensado se calcula cuidadosamente para garantizar que el metal fluya correctamente y que la pieza final mantenga tolerancias y propiedades mecánicas requeridas.
El espesor de la chapa también influye en la elección de la prensa, la fuerza aplicada y el diseño del troquel. Chapas finas requieren fuerza controlada y lubricación adecuada para evitar arrugas y desgarros, mientras que chapas más gruesas demandan prensas con mayor capacidad y troqueles reforzados, así como ajustes precisos de velocidad y presión. La geometría de la pieza, incluyendo relieves, nervaduras, curvaturas y detalles funcionales, determina la necesidad de operaciones multietapa, estirado progresivo o troquelado combinado, integrando diferentes fases de deformación en una misma línea de producción para optimizar eficiencia, reducir desperdicio y garantizar repetitividad.
La lubricación es otro factor crítico, especialmente en embutición profunda o estirado, ya que reduce la fricción entre la chapa y el troquel, protege superficies, prolonga la vida útil de los troqueles y asegura acabados de alta calidad. Los sistemas de aplicación de lubricante pueden ser manuales o automatizados, con control preciso de cantidad y distribución, adaptándose al tipo de material, espesor de chapa y complejidad de la pieza. La combinación de selección de material, control de temperatura, espesor de chapa, geometría de la pieza, lubricación y parámetros de fuerza y velocidad convierte a la estampación en un proceso altamente especializado y optimizado, capaz de producir piezas metálicas complejas, precisas, resistentes y con acabados uniformes en grandes volúmenes.
El diseño de líneas de producción completas para estampación industrial implica la integración de múltiples elementos y procesos para garantizar eficiencia, precisión y calidad en la fabricación de piezas metálicas complejas. Todo comienza con la alimentación de chapas, donde sistemas automáticos transportan y posicionan la lámina sobre la prensa, asegurando alineación exacta con el troquel y minimizando errores de posicionamiento que podrían generar defectos. La automatización de esta etapa permite un flujo continuo de material, reduciendo tiempos muertos y aumentando la capacidad de producción, mientras sensores y sistemas de control digital supervisan la posición, grosor y propiedades del metal antes de cada ciclo de prensado.
Las prensas de estampación, ya sean mecánicas, hidráulicas o servoaccionadas, conforman las piezas aplicando fuerza controlada sobre la chapa mediante troqueles optimizados. Dependiendo de la complejidad de la pieza, el proceso puede incluir embutición profunda, estirado progresivo, troquelado combinado, repujado o corte, integrando varias operaciones en un solo ciclo o mediante estaciones sucesivas. Los troqueles se diseñan mediante simulaciones por elementos finitos para asegurar un flujo uniforme del metal, evitando arrugas, desgarros o adelgazamiento irregular, y se fabrican con aceros de alta resistencia tratados térmicamente, muchas veces recubiertos para reducir fricción y desgaste. Los cojines hidráulicos, guías y sistemas de control progresivo de fuerza garantizan que cada sección de la pieza se deforme correctamente, manteniendo tolerancias estrictas y acabados superficiales de alta calidad.
Tras cada ciclo de prensado, sistemas automáticos extraen las piezas conformadas y las transportan hacia estaciones de inspección, ensamblaje o acabado. Sensores de presión, desplazamiento y temperatura monitorean el proceso en tiempo real, y sistemas de visión artificial verifican dimensiones, curvaturas, relieves y acabados superficiales, separando automáticamente piezas defectuosas. Esta trazabilidad completa permite análisis de eficiencia, mantenimiento predictivo y optimización continua del proceso, asegurando que todas las piezas cumplan con los estándares más exigentes de la industria. La combinación de robots para alimentación y extracción, transportadores automatizados, control digital y visión artificial permite líneas de alta productividad con mínima intervención humana, reduciendo errores, desperdicios y costos operativos.
El software de simulación de flujo de material y control digital avanzado complementa la línea, permitiendo a los ingenieros modelar la deformación de la chapa antes de iniciar la producción física. Esto permite identificar zonas críticas de tensión, optimizar geometrías de troqueles y ajustar parámetros de fuerza, velocidad y lubricación, reduciendo retrabajos, desperdicio de material y tiempo de prueba. Durante la operación, el control digital ajusta automáticamente la presión y velocidad del punzón según el comportamiento del metal, adaptándose a variaciones de espesor, material o geometría de la pieza, asegurando uniformidad y calidad constante en producciones de alto volumen.
El mantenimiento de la línea completa incluye revisión de prensas, cilindros, motores hidráulicos o eléctricos, lubricación de cojinetes y guías, calibración de recorrido y fuerza del punzón, inspección y ajuste de troqueles, así como verificación de sistemas de automatización y sensores. Un mantenimiento adecuado asegura operación continua, fuerza uniforme en cada ciclo, precisión dimensional y prolonga la vida útil de todos los componentes. La combinación de alimentación automatizada de chapas, prensas de estampación avanzadas, troqueles optimizados, sistemas de control digital, visión artificial y mantenimiento preventivo convierte a estas líneas en sistemas de manufactura altamente eficientes, capaces de producir piezas metálicas complejas, precisas, resistentes y repetitivas, cumpliendo con los estándares de calidad más exigentes en industrias automotriz, aeroespacial, de envases metálicos, electrodomésticos y maquinaria industrial.
Prensa de Conformado por Embutición
La prensa de conformado por embutición es un equipo esencial en la industria metalúrgica, diseñado para transformar láminas metálicas planas en piezas tridimensionales mediante la aplicación controlada de fuerza sobre un troquel y un punzón. Su funcionamiento se basa en el principio de flujo plástico del metal: la chapa se desplaza gradualmente dentro de la cavidad del troquel, adoptando la forma deseada sin romperse ni arrugarse, lo que permite obtener piezas de paredes uniformes, relieves precisos y acabados superficiales de alta calidad. Este tipo de prensa se utiliza ampliamente en la fabricación de envases metálicos, componentes automotrices, electrodomésticos, carcasas de maquinaria y piezas industriales que requieren geometrías complejas y tolerancias estrictas.
El sistema de embutición puede ser mecánico, hidráulico o servoaccionado. Las prensas mecánicas transmiten la fuerza mediante cigüeñales y bielas, generando golpes rápidos y constantes, ideales para producciones en serie de piezas estandarizadas. Las prensas hidráulicas permiten un control progresivo de la fuerza y velocidad del punzón, adaptándose a piezas con geometrías complejas, embutición profunda o estirado progresivo. Las prensas servoaccionadas combinan velocidad, precisión y flexibilidad, integrándose fácilmente en líneas automatizadas y permitiendo ajustar la fuerza, velocidad y recorrido del punzón según la chapa, el espesor y la complejidad de la pieza.
Los troqueles son componentes críticos en la prensa de conformado por embutición. Se fabrican con aceros de alta resistencia tratados térmicamente y, en muchos casos, recubiertos para reducir fricción y desgaste. Su geometría se optimiza mediante simulaciones por elementos finitos, considerando radios de curvatura, relieves, nervaduras y zonas de máxima tensión, garantizando que el flujo del metal sea uniforme y evitando defectos como arrugas, desgarros o adelgazamiento irregular. Durante el proceso, la lubricación controlada reduce la fricción, protege la chapa y el troquel, y asegura acabados superficiales uniformes en cada pieza producida.
La embutición profunda permite fabricar recipientes, carcasas o componentes de paredes altas en varias etapas, aplicando fuerza progresiva y controlada para que la chapa fluya adecuadamente en todas las zonas del troquel. El estirado progresivo y el troquelado combinado se utilizan para integrar relieves, nervaduras, cortes y detalles funcionales en la pieza final, reduciendo operaciones secundarias y aumentando la eficiencia de producción. Cada operación se programa según el tipo de metal, espesor de la chapa y complejidad de la pieza, asegurando uniformidad, precisión y repetitividad en cada ciclo.
La automatización de la prensa de embutición permite integrar robots para alimentación de chapas, extracción de piezas conformadas y transporte hacia estaciones de inspección, ensamblaje o acabado. Sensores de presión, desplazamiento y temperatura supervisan cada ciclo en tiempo real, mientras sistemas de visión artificial verifican dimensiones, curvaturas, relieves y acabados superficiales, separando automáticamente piezas defectuosas. Esto garantiza producción continua, alta repetitividad, reducción de desperdicios y cumplimiento de estrictos estándares de calidad en industrias automotriz, aeroespacial, de envases metálicos y electrodomésticos.
El mantenimiento de la prensa de conformado por embutición es esencial para prolongar la vida útil de la máquina y los troqueles, asegurar fuerza uniforme, mantener tolerancias estrictas y garantizar producción sin interrupciones. Incluye lubricación de cojinetes y guías, revisión de cilindros y sistemas hidráulicos o mecánicos, calibración del recorrido y fuerza del punzón, y verificación de la alineación de los troqueles. La combinación de fuerza progresiva, troqueles optimizados, automatización, control digital y mantenimiento preventivo convierte a la prensa de embutición en un sistema de manufactura avanzada capaz de producir piezas metálicas complejas, precisas, resistentes y repetitivas con máxima eficiencia y calidad.
Los diferentes tipos de embutición se seleccionan según el material, el espesor de la chapa y la geometría de la pieza final, cada uno con características y aplicaciones específicas. La embutición en frío se realiza a temperatura ambiente y se aplica principalmente a chapas de acero, aluminio o cobre con buena ductilidad, permitiendo obtener piezas precisas, con acabados superficiales uniformes y tolerancias estrictas. Este método es ampliamente utilizado en la fabricación de componentes automotrices como paneles de carrocería, techos, puertas y guardabarros, así como en electrodomésticos y maquinaria industrial, donde la repetitividad y la calidad superficial son esenciales. La embutición en frío requiere control preciso de fuerza, velocidad y lubricación para evitar arrugas, desgarros o adelgazamientos irregulares en la chapa, especialmente cuando se trabaja con geometrías complejas o embutición profunda.
La embutición en caliente, por su parte, eleva la temperatura de la chapa antes de conformarla, reduciendo su resistencia y aumentando la ductilidad del metal. Este método permite deformaciones más profundas, estirado de piezas complejas y reducción de tensiones residuales, siendo ideal para aceros de alta resistencia, aleaciones difíciles de conformar en frío y componentes estructurales automotrices o aeroespaciales. La temperatura, el tiempo de calentamiento y la velocidad de prensado se calculan cuidadosamente para garantizar que el metal fluya correctamente, que la pieza final mantenga sus propiedades mecánicas y que se cumplan tolerancias dimensionales estrictas. La lubricación también es crítica en la embutición en caliente para reducir fricción y proteger tanto el troquel como la superficie de la chapa.
La embutición profunda permite producir piezas con paredes altas y uniformes en múltiples etapas, aplicando fuerza progresiva y controlada para que la chapa fluya adecuadamente en todas las zonas del troquel. Este tipo de embutición se utiliza para fabricar recipientes metálicos, carcasas complejas, envases de alimentos y bebidas, así como componentes estructurales automotrices que requieren resistencia y precisión dimensional. En este proceso, la chapa se guía mediante cojines hidráulicos y guías que aseguran un flujo uniforme, evitando arrugas, desgarros o adelgazamientos irregulares. El diseño de los troqueles se realiza mediante simulaciones por elementos finitos, considerando radios de curvatura, relieves, nervaduras y zonas de máxima tensión, optimizando el flujo del metal y garantizando piezas con acabados superficiales de alta calidad.
La embutición progresiva combina múltiples operaciones en un ciclo continuo, integrando estirado, corte, punzonado, relieves y embutición en una sola línea de producción. Esta técnica permite reducir tiempos de fabricación, minimizar operaciones secundarias y aumentar la eficiencia en producciones de alto volumen, asegurando que cada pieza cumpla con tolerancias estrictas y estándares de calidad uniformes. Las líneas de embutición progresiva suelen estar automatizadas, con robots que alimentan chapas, extraen piezas conformadas y las transportan a estaciones de inspección o ensamblaje. Sistemas de visión artificial y sensores monitorean dimensiones, curvaturas y acabados, separando automáticamente piezas defectuosas y garantizando repetitividad y calidad constante en cada ciclo de producción.
La elección del tipo de embutición también está ligada a la selección del material, considerando propiedades como ductilidad, resistencia, espesor y aleación. Chapas finas requieren control preciso de fuerza y lubricación adecuada, mientras que chapas más gruesas demandan prensas con mayor capacidad, troqueles reforzados y ajustes precisos de velocidad y presión. La combinación de embutición en frío, caliente, profunda y progresiva, junto con troqueles optimizados, prensas avanzadas y sistemas de automatización, permite producir piezas metálicas complejas, precisas, resistentes y repetitivas, cumpliendo con los más altos estándares de calidad en industrias como la automotriz, aeroespacial, de envases metálicos, electrodomésticos y maquinaria industrial.
La implementación de líneas completas de embutición industrial combina prensas avanzadas, control digital, simulación de flujo de material y automatización robótica para maximizar eficiencia, calidad y trazabilidad en la producción de piezas metálicas complejas. Estas líneas comienzan con la alimentación automática de chapas, donde robots y transportadores posicionan las láminas con precisión sobre el troquel, garantizando alineación perfecta y minimizando errores de posicionamiento que podrían generar defectos en la pieza final. Sensores de espesor, dureza y propiedades mecánicas verifican cada lámina antes del prensado, asegurando que solo materiales conformes entren al proceso y reduciendo desperdicios.
Las prensas de embutición, mecánicas, hidráulicas o servoaccionadas, transforman la chapa mediante golpes controlados, aplicando fuerza progresiva y ajustando velocidad y presión según la geometría de la pieza y las características del material. En operaciones complejas como embutición profunda, estirado progresivo o troquelado combinado, los troqueles se diseñan mediante simulaciones por elementos finitos que predicen el flujo del metal, zonas de máxima tensión y posibles puntos de arrugas o adelgazamiento, optimizando así la conformación de la pieza y reduciendo retrabajos. Los troqueles se fabrican con aceros de alta resistencia tratados térmicamente y, en muchos casos, recubiertos para minimizar fricción y desgaste, mientras que sistemas de lubricación controlada aseguran un flujo uniforme del metal y un acabado superficial impecable.
Una vez conformadas, las piezas se extraen automáticamente mediante robots y se transportan hacia estaciones de inspección, ensamblaje o acabado. Sistemas de visión artificial miden dimensiones, curvaturas, relieves y acabados superficiales en tiempo real, detectando cualquier desviación de tolerancia y separando automáticamente piezas defectuosas. Los sensores de presión, desplazamiento y temperatura monitorean cada ciclo del punzón, ajustando la fuerza y velocidad de manera inmediata para mantener la uniformidad en la producción, garantizando repetitividad y calidad en series de alto volumen. Esta trazabilidad completa permite registrar cada operación, analizar la eficiencia de la línea y realizar mantenimiento predictivo, evitando paradas no planificadas y asegurando continuidad en la producción.
La automatización de la línea también permite integrar operaciones complementarias como corte, punzonado, repujado, estampado de relieves y ensamblaje parcial de subcomponentes, reduciendo la necesidad de manipulaciones manuales y acelerando el flujo de producción. Los sistemas de control digital centralizan la operación de prensas, robots, transportadores y sensores, coordinando cada etapa para optimizar tiempos, minimizar desperdicios y garantizar que cada pieza cumpla con los estándares de calidad exigidos por industrias como la automotriz, aeroespacial, de envases metálicos, electrodomésticos y maquinaria industrial.
El mantenimiento de una línea de embutición completa abarca revisión de prensas, cilindros hidráulicos o motores servoaccionados, lubricación de cojinetes y guías, calibración de recorrido y fuerza del punzón, inspección y ajuste de troqueles, así como verificación de robots, sensores y sistemas de control. Un mantenimiento preventivo adecuado asegura que la fuerza se aplique uniformemente, que la producción se mantenga constante, que las piezas cumplan con tolerancias estrictas y que la línea funcione de manera segura y eficiente durante largos periodos de operación. La combinación de prensas avanzadas, troqueles optimizados, automatización robótica, control digital y mantenimiento preventivo convierte a las líneas de embutición en sistemas de manufactura industrial de alto nivel, capaces de producir piezas metálicas complejas, precisas, resistentes y repetitivas, cumpliendo con los estándares de calidad más exigentes y maximizando productividad, eficiencia y trazabilidad en la fabricación.
En la industria automotriz, las líneas de embutición se diseñan para producir componentes de carrocería como techos, puertas, guardabarros, tapas de motor y paneles estructurales con geometrías complejas, altos requerimientos de resistencia y tolerancias estrictas. La chapa metálica, generalmente acero laminado en frío o aleaciones de aluminio, se alimenta automáticamente desde rollos o láminas cortadas, pasando por sistemas de nivelado y limpieza para eliminar irregularidades superficiales que podrían afectar la conformación. Robots y transportadores posicionan la chapa sobre el troquel con precisión milimétrica, asegurando que cada golpe del punzón se realice exactamente en la posición requerida. Las prensas hidráulicas o servoaccionadas aplican fuerza controlada, ajustando presión, velocidad y recorrido del punzón según la complejidad del componente y el espesor de la chapa, permitiendo embutición profunda, estirado progresivo, troquelado combinado y estampado de relieves en un mismo ciclo o mediante estaciones sucesivas.
Los troqueles son diseñados utilizando software de simulación de flujo de material, prediciendo cómo se deformará la chapa, identificando zonas de tensión crítica y posibles puntos de arrugas o adelgazamiento. Esto permite optimizar radios de curvatura, relieves, nervaduras y guías de flujo de metal, garantizando piezas con paredes uniformes y acabados superficiales de alta calidad. La lubricación controlada entre la chapa y el troquel minimiza fricción, protege la superficie de la pieza y prolonga la vida útil de los troqueles, lo que es especialmente crítico en procesos de embutición profunda donde el metal experimenta grandes deformaciones. En componentes automotrices, la embutición progresiva permite integrar múltiples operaciones como corte, punzonado, relieves estructurales y perforaciones funcionales en un mismo ciclo, reduciendo la necesidad de ensamblajes posteriores y acelerando el flujo de producción.
Durante la producción, sistemas de visión artificial y sensores monitorean dimensiones, curvaturas, relieves, espesores y acabados superficiales en tiempo real, asegurando que cada pieza cumpla con los estándares de calidad más estrictos. Cualquier desviación se detecta automáticamente, separando piezas defectuosas antes de que continúen en la línea, reduciendo desperdicio y garantizando repetitividad en series de alto volumen. El control digital centralizado coordina prensas, robots, transportadores y sensores, ajustando parámetros de presión, velocidad y recorrido del punzón según el comportamiento del metal, optimizando eficiencia, uniformidad y seguridad en toda la línea.
En la producción de envases metálicos, las líneas de embutición permiten fabricar millones de recipientes de aluminio o acero con paredes finas y uniformes, como latas de bebidas, alimentos o aerosoles. La chapa se alimenta desde rollos, se limpia y se corta a la medida requerida, y luego se somete a embutición profunda mediante prensas hidráulicas o servoaccionadas que aplican fuerza progresiva. Cada golpe conforma la pieza gradualmente, evitando arrugas, desgarros y adelgazamientos irregulares. Troqueles optimizados y lubricación controlada aseguran flujo uniforme del metal y acabados superficiales perfectos, mientras que robots extraen las piezas conformadas y las transportan hacia estaciones de inspección, llenado o embalaje. Los sistemas de control digital y visión artificial supervisan cada operación, garantizando repetitividad y calidad constante en producciones de alto volumen.
El mantenimiento de estas líneas completas es fundamental para mantener productividad y precisión. Incluye lubricación de guías y cojinetes, calibración de recorrido y fuerza del punzón, revisión de cilindros hidráulicos o motores servoaccionados, inspección de troqueles, verificación de robots, sensores y sistemas de control. Un mantenimiento adecuado asegura fuerza uniforme, producción continua, tolerancias precisas y prolonga la vida útil de todos los componentes de la línea. La integración de prensas avanzadas, troqueles optimizados, automatización robótica, control digital, sistemas de inspección y mantenimiento preventivo convierte a estas líneas de embutición en sistemas de manufactura industrial de alto nivel, capaces de producir piezas metálicas complejas, resistentes, precisas y repetitivas, cumpliendo con los más altos estándares de calidad y eficiencia en sectores automotriz, aeroespacial, de envases metálicos, electrodomésticos y maquinaria industrial.
Prensa para Estirado Profundo
La prensa para estirado profundo es una máquina diseñada específicamente para realizar procesos de conformado en frío sobre chapas metálicas que requieren grandes deformaciones sin comprometer la integridad del material. En este tipo de operaciones, la chapa plana se transforma en un cuerpo hueco de gran profundidad en relación con su diámetro, lo cual demanda un control muy preciso de la presión, la velocidad y la lubricación, ya que el metal fluye progresivamente desde los bordes hacia el centro, estirándose de manera continua bajo la acción del punzón y el troquel. Este proceso se utiliza extensamente en la fabricación de componentes cilíndricos o de geometría compleja, como depósitos, recipientes a presión, envases metálicos, carcasas de motores eléctricos, piezas automotrices y aeroespaciales, así como en utensilios domésticos que requieren alta resistencia estructural y superficies uniformes.
La prensa de estirado profundo puede ser de tipo mecánico, hidráulico o servoaccionado, y su diseño incluye un sistema de cojín o pisador de chapa que sujeta firmemente el material durante la embutición para evitar la formación de arrugas en los bordes. Este cojín aplica una presión regulable que equilibra el flujo del metal, permitiendo que la chapa se estire de manera controlada y uniforme. En los modelos hidráulicos, la ventaja es la posibilidad de ajustar la fuerza y el recorrido con gran flexibilidad, lo que resulta esencial cuando se trabaja con piezas de diferentes espesores o materiales como aceros de alta resistencia y aleaciones ligeras de aluminio o titanio. En las versiones servoaccionadas, la precisión digital permite programar perfiles de movimiento complejos del punzón y del cojín, reduciendo esfuerzos internos en la pieza y aumentando la vida útil de los troqueles.
El diseño de los troqueles para estirado profundo es un factor crítico, ya que deben permitir un flujo continuo del material evitando zonas de adelgazamiento excesivo o concentración de tensiones. Se utilizan radios de curvatura cuidadosamente calculados, superficies pulidas y lubricación especializada para reducir la fricción entre chapa y herramienta. La simulación por computadora mediante software de elementos finitos se ha convertido en una práctica habitual, ya que permite prever defectos potenciales como desgarros, arrugas o falta de llenado antes de fabricar el troquel, optimizando así el diseño y reduciendo costos de prueba. Asimismo, la incorporación de sensores de fuerza, desplazamiento y temperatura en las prensas modernas permite recopilar datos en tiempo real que ayudan a ajustar parámetros de manera automática y garantizar piezas de alta calidad.
El estirado profundo exige un control estricto de la materia prima. La chapa debe presentar características homogéneas de resistencia, ductilidad y espesor, ya que cualquier variación puede afectar el comportamiento durante la deformación. Los fabricantes de prensas y de utillajes recomiendan el uso de chapas laminadas en frío, con acabados superficiales finos y libres de impurezas, lo que asegura un flujo más estable durante el proceso. En aplicaciones de envases y utensilios domésticos, donde las piezas suelen recibir acabados estéticos adicionales como pulido, anodizado o recubrimientos, la calidad superficial inicial obtenida en el estirado profundo resulta decisiva.
En las líneas de producción industrial, la prensa para estirado profundo suele integrarse con sistemas automáticos de alimentación de chapas, robots de carga y descarga, y equipos de inspección por visión artificial que verifican dimensiones, espesores y acabados de cada pieza. Esto permite mantener una producción continua de alto volumen con una calidad constante. En sectores como el automotriz o el aeroespacial, donde las exigencias de precisión son extremas, los sistemas de control digital integrados en las prensas garantizan la trazabilidad completa de cada lote, registrando los parámetros de presión, velocidad, lubricación y temperatura en cada ciclo de conformado.
El uso de la prensa para estirado profundo ha transformado profundamente la forma en que se diseñan y fabrican piezas metálicas en diversos sectores industriales, ya que permite obtener geometrías que serían imposibles de conseguir mediante simples procesos de estampado o doblado. En la industria automotriz, por ejemplo, el estirado profundo se emplea para la producción de componentes como tanques de combustible, cárteres de motor, cubiertas de embrague, carcasas de amortiguadores y numerosas piezas estructurales que requieren resistencia mecánica y dimensional estable. En este campo la exigencia de precisión es altísima porque incluso desviaciones mínimas en espesores o geometrías pueden generar problemas de ensamblaje, ruidos o fallas en la durabilidad del vehículo. Gracias a la capacidad de las prensas modernas, se pueden fabricar piezas de acero de alta resistencia que soportan grandes esfuerzos sin comprometer la seguridad, reduciendo además el peso total del vehículo en un contexto en el que la eficiencia energética es fundamental.
En el sector del envasado, el estirado profundo ha sido clave para la producción de latas y recipientes metálicos para bebidas, alimentos en conserva, aerosoles y envases farmacéuticos. Estos productos requieren no solo una gran precisión dimensional, sino también una superficie impecable que garantice hermeticidad y una estética adecuada para el consumidor final. El proceso de estirado profundo permite obtener paredes delgadas y uniformes, con gran resistencia a la presión interna y a los impactos externos, lo cual resulta esencial para mantener la seguridad del contenido. A su vez, el uso de aceros especiales, aluminio y aleaciones ligeras ha permitido reducir el espesor de las paredes de los envases sin comprometer su desempeño, lo que supone un ahorro significativo de materia prima y una contribución a la sostenibilidad, dado que el reciclaje de estos envases es más eficiente cuando el material es uniforme y homogéneo.
En el ámbito de los electrodomésticos y utensilios de cocina, las prensas para estirado profundo se utilizan en la fabricación de fregaderos de acero inoxidable, ollas, sartenes, teteras y otros recipientes que requieren una estética cuidada y resistencia al uso intensivo. Estos productos deben cumplir con altos estándares de higiene, lo que implica superficies lisas y libres de porosidades, algo que solo puede lograrse con procesos de embutición profunda controlada y herramientas de precisión. Además, la repetibilidad del proceso asegura que cada pieza sea idéntica, lo cual es vital en líneas de producción de gran volumen donde la uniformidad es un requisito indispensable para mantener la calidad percibida por el usuario final.
La industria aeroespacial es otro sector en el que el estirado profundo desempeña un papel determinante, ya que muchas de las piezas utilizadas en aeronaves, satélites y cohetes deben soportar condiciones extremas de presión, temperatura y vibración. Componentes como carcasas de sistemas hidráulicos, depósitos de combustible, cubiertas de motores o piezas estructurales se producen mediante este método, aprovechando su capacidad para conformar aleaciones ligeras como el titanio y el aluminio sin comprometer sus propiedades mecánicas. El control que ofrecen las prensas hidráulicas de alta precisión, junto con simulaciones avanzadas por elementos finitos, permite desarrollar piezas que cumplen con los estrictos requisitos de la industria aeroespacial en términos de tolerancias y confiabilidad.
Un aspecto fundamental del estirado profundo es la interacción entre la prensa, el material y el diseño del utillaje. Para garantizar la calidad de la pieza final, los ingenieros calculan de forma minuciosa la relación entre la profundidad a alcanzar y el diámetro de la chapa inicial, ya que este factor determina el límite de conformado antes de que se produzcan fallos por desgarro o adelgazamiento excesivo. También se controla cuidadosamente el coeficiente de fricción entre la chapa y las herramientas, que se reduce mediante lubricantes especiales diseñados para soportar altas presiones y temperaturas. Estos lubricantes no solo evitan defectos en la superficie de la pieza, sino que además prolongan la vida útil de los troqueles, lo cual resulta esencial en producciones de gran volumen donde el desgaste prematuro de las herramientas implicaría costos elevados y paradas no planificadas.
La evolución tecnológica ha llevado a que las prensas para estirado profundo se integren en líneas de producción totalmente automatizadas, en las que robots de carga y descarga, sistemas de alimentación de bobinas y controles electrónicos de última generación trabajan de forma sincronizada. Estos sistemas permiten un control total del proceso, con la posibilidad de ajustar parámetros en tiempo real según el comportamiento del material en cada ciclo. La incorporación de inteligencia en el monitoreo de la presión, la velocidad y la temperatura hace posible una producción más flexible, capaz de adaptarse a lotes variables sin necesidad de realizar cambios prolongados en la configuración. Esto responde a la demanda actual de la industria, donde la personalización de productos y la rapidez en la entrega son factores clave de competitividad.
En la actualidad, la innovación digital aplicada a las prensas para estirado profundo ha supuesto un cambio radical en la forma en que se conciben, operan y mantienen estas máquinas, ya que la introducción de servomotores, sistemas de control numérico y plataformas de monitoreo en tiempo real ha hecho posible un nivel de precisión y eficiencia que antes resultaba impensable. Mientras que las prensas hidráulicas tradicionales ofrecían un control basado principalmente en la presión ejercida sobre la chapa, las modernas prensas servoaccionadas permiten modular con exactitud no solo la fuerza sino también la velocidad y el recorrido de cada movimiento, adaptándose dinámicamente al comportamiento del material en cada etapa del ciclo. Esto significa que, si durante el estirado se detecta una variación mínima en la resistencia de la lámina metálica, el sistema ajusta automáticamente la presión y la velocidad para evitar desgarros, pliegues o adelgazamientos excesivos, garantizando que la pieza final cumpla con las especificaciones sin necesidad de detener el proceso para correcciones manuales.
El uso de sensores de alta resolución y algoritmos de análisis predictivo integrados en estas prensas ha permitido además una nueva forma de entender el mantenimiento y la gestión de la producción. A través del registro continuo de variables como presión, temperatura, vibración, consumo energético y desgaste de los útiles, se generan grandes volúmenes de datos que son analizados en tiempo real para identificar patrones de comportamiento anómalos. Gracias a ello, los fabricantes pueden anticiparse a posibles fallos antes de que se conviertan en problemas graves, programando intervenciones de mantenimiento preventivo en los momentos más adecuados para la línea de producción, lo que se traduce en una reducción significativa de paradas no planificadas y en una prolongación de la vida útil de la máquina y de los utillajes. Este enfoque, que en muchos casos se denomina mantenimiento predictivo, se ha convertido en un elemento esencial para empresas que dependen de la producción continua y de alta precisión, ya que la detención inesperada de una prensa puede significar pérdidas económicas muy elevadas y retrasos en la entrega de productos a clientes.
El impacto de estas innovaciones también se refleja en la sostenibilidad y en la eficiencia energética de los procesos de estirado profundo. Las prensas servoaccionadas consumen solo la energía necesaria en cada etapa del ciclo, evitando los picos de consumo característicos de los sistemas hidráulicos convencionales, lo que representa un ahorro considerable en el largo plazo y una reducción en la huella de carbono de la planta industrial. Asimismo, la optimización de parámetros como la presión y la velocidad de embutición reduce la cantidad de material desperdiciado en forma de piezas defectuosas o chatarra, lo que no solo supone un beneficio económico directo sino también una mejora ambiental. La posibilidad de fabricar piezas más ligeras y resistentes mediante un control avanzado de la deformación también contribuye a la eficiencia energética de sectores como el automotriz y el aeroespacial, donde cada gramo ahorrado en peso se traduce en menor consumo de combustible y menores emisiones contaminantes durante la vida útil del producto final.
Otro aspecto relevante de la digitalización en estas prensas es la capacidad de integración en entornos de producción inteligentes, donde todas las máquinas, robots y sistemas de logística interna están conectados en una red de comunicación que permite la trazabilidad completa del proceso. Esto significa que cada pieza fabricada puede ser registrada desde la materia prima hasta el producto terminado, con información detallada sobre los parámetros de conformado, los lotes de material utilizados y las condiciones de operación de la máquina en el momento de su producción. Esta trazabilidad no solo aporta confianza y seguridad a los clientes, especialmente en sectores críticos como el médico o el aeroespacial, sino que también facilita la certificación de calidad y el cumplimiento de normativas internacionales cada vez más estrictas.
La evolución tecnológica no se limita únicamente a las prensas en sí mismas, sino que también ha transformado el diseño de los troqueles y matrices utilizados en el estirado profundo. Gracias a herramientas avanzadas de simulación por computadora, es posible prever cómo se comportará una chapa bajo ciertas condiciones de estirado antes de fabricar físicamente la herramienta, lo que reduce drásticamente los tiempos de desarrollo y los costos asociados a pruebas y errores. Este enfoque de simulación virtual permite optimizar el flujo de material, identificar zonas críticas donde podrían producirse arrugas o roturas, y ajustar los radios de las matrices, las presiones de los pisadores y la geometría de los punzones de manera que el proceso sea lo más estable y eficiente posible. De este modo, cuando la prensa entra en producción real, los márgenes de error son mínimos y se asegura una transición rápida hacia la fabricación en serie.
En un contexto donde la competitividad industrial depende cada vez más de la capacidad de producir con rapidez, precisión y flexibilidad, las prensas de estirado profundo con integración digital se han consolidado como un pilar fundamental de la manufactura moderna. Estas máquinas no solo responden a las necesidades actuales de sectores exigentes como el automotriz, el aeroespacial, el médico o el de envases, sino que además se anticipan a las tendencias del futuro, donde la personalización masiva y la producción sostenible serán determinantes para el éxito.
La prensa para estirado profundo tiene una trayectoria histórica muy interesante que refleja de manera clara cómo la tecnología industrial se ha ido adaptando a las necesidades de cada época. En sus primeras aplicaciones, estas prensas eran básicamente máquinas mecánicas que funcionaban a través de grandes volantes de inercia y sistemas de biela-manivela que transformaban el movimiento rotativo en un movimiento lineal capaz de aplicar la fuerza necesaria sobre la chapa. Eran máquinas robustas y confiables, pero con limitaciones significativas en cuanto a control de velocidad, precisión y uniformidad de la presión aplicada durante todo el ciclo de embutición. El operario debía confiar en su experiencia y en ajustes manuales para lograr resultados aceptables, lo que hacía que el proceso dependiera mucho de la habilidad humana y estuviera sujeto a variaciones de calidad entre lotes. Estas prensas mecánicas, aunque revolucionarias en su momento, tenían el inconveniente de que no podían adaptarse fácilmente a geometrías complejas ni garantizar la repetibilidad absoluta que hoy se exige en la producción industrial moderna.
Con el tiempo, y en especial a lo largo del siglo XX, la introducción de la hidráulica supuso un salto cualitativo fundamental. Las prensas hidráulicas de estirado profundo permitieron aplicar una fuerza constante y controlada en todo el recorrido del pistón, lo que significaba que el material podía deformarse de forma mucho más uniforme, reduciendo la probabilidad de roturas, pliegues o defectos estructurales. Además, estas prensas ofrecieron la posibilidad de programar carreras más largas y de manipular chapas de mayor tamaño y espesor, lo que abrió la puerta a la fabricación de componentes de grandes dimensiones, como carrocerías de automóviles, piezas estructurales de maquinaria pesada y depósitos cilíndricos de diferentes usos. Sin embargo, a pesar de sus ventajas en términos de fuerza y control, las prensas hidráulicas tenían el problema de su elevado consumo energético, sus necesidades de mantenimiento relacionadas con fugas de aceite y la generación de calor, que obligaba a implementar sistemas de refrigeración costosos.
El avance siguiente vino de la mano de la electrificación avanzada y de la automatización mediante control numérico. Cuando se introdujeron los primeros sistemas CNC en prensas de estirado profundo, la capacidad de repetir un ciclo con parámetros idénticos transformó completamente la forma de concebir la producción. La máquina ya no dependía de los ajustes manuales ni de la intuición del operario, sino que podía ejecutar secuencias exactas con precisión micrométrica. La incorporación de servomotores eléctricos en lugar de sistemas puramente hidráulicos representó una verdadera revolución, ya que permitió un control dinámico de la velocidad y la fuerza en cada momento del recorrido. Esto trajo consigo la capacidad de realizar perfiles de movimiento personalizados: por ejemplo, iniciar con una aproximación rápida del punzón, disminuir la velocidad durante la etapa crítica de deformación para proteger el material, y aumentar nuevamente la velocidad en el retorno, optimizando así tanto la calidad de la pieza como el tiempo de ciclo.
Este nivel de control abrió también nuevas posibilidades de diseño de piezas más complejas y de materiales más sofisticados. Las aleaciones ligeras de aluminio y los aceros de alta resistencia, que eran muy difíciles de conformar con métodos tradicionales, comenzaron a ser utilizados con éxito gracias a la capacidad de las prensas servoaccionadas de modular la presión en función de la respuesta del material en tiempo real. Así, la industria automotriz pudo fabricar carrocerías más livianas y seguras, mientras que el sector aeroespacial encontró la forma de producir paneles y componentes estructurales que combinaban ligereza y resistencia, algo fundamental para reducir el peso total de los aviones y, con ello, el consumo de combustible.
En paralelo, la digitalización fue incorporando el concepto de “máquina inteligente”, donde la prensa no solo ejecuta una operación mecánica, sino que también recoge, procesa y transmite datos. Estos datos alimentan plataformas de monitoreo remoto que permiten a los ingenieros de planta conocer en todo momento el estado de la máquina, la calidad de las piezas que se están produciendo y los posibles desajustes antes de que se conviertan en problemas. De esta manera, la prensa para estirado profundo dejó de ser una máquina aislada para integrarse dentro de un ecosistema más amplio de manufactura conectada, conocido como Industria 4.0. Esta transición no solo aumentó la productividad y la calidad, sino que también permitió a las empresas adaptarse a un mercado más exigente, donde la trazabilidad, la personalización de productos y la sostenibilidad se han convertido en factores clave de competitividad.
Actualmente, las prensas de estirado profundo más avanzadas funcionan casi como un organismo inteligente que aprende y se optimiza con el tiempo. Gracias a la incorporación de algoritmos de inteligencia artificial, estas máquinas pueden reconocer patrones de deformación, comparar resultados de miles de ciclos anteriores y proponer ajustes automáticos para mejorar la calidad sin intervención humana. Por ejemplo, si la máquina detecta que una determinada combinación de presión y velocidad reduce el desgaste de la matriz y mejora la distribución del espesor de la pieza, es capaz de almacenar esa configuración y aplicarla en futuras producciones de forma autónoma. Esta capacidad de autoajuste lleva el concepto de automatización a un nivel superior, donde ya no se trata solo de seguir instrucciones predefinidas, sino de tomar decisiones basadas en experiencia acumulada y en análisis predictivo de datos.
Todo este recorrido histórico demuestra que la prensa para estirado profundo es un ejemplo perfecto de cómo la ingeniería mecánica y la innovación tecnológica han sabido evolucionar juntas, adaptándose a los desafíos de cada etapa industrial. Desde los grandes volantes mecánicos del siglo XIX hasta las sofisticadas plataformas servo-hidráulicas y digitales del siglo XXI, estas prensas han acompañado el desarrollo de la industria moderna, siendo responsables de la producción de millones de componentes que forman parte de la vida cotidiana y de sectores estratégicos. Lo que antes era visto como una máquina pesada y limitada, hoy es un sistema de alta precisión, eficiente y conectado que simboliza el futuro de la manufactura avanzada.
¿Quieres que continúe ampliando con ejemplos prácticos de industrias y productos específicos que se fabrican con prensas de estirado profundo modernas, explicando cómo cada sector aprovecha estas tecnologías?
Máquina de Embutición
La máquina de embutición es un equipo industrial diseñado para transformar láminas metálicas planas en piezas con geometrías tridimensionales mediante la aplicación controlada de fuerza y presión. Su principio de funcionamiento se basa en colocar una chapa sobre una matriz y presionar con un punzón, provocando que el material fluya y adopte la forma deseada sin perder continuidad ni sufrir cortes. Este proceso es fundamental dentro de la conformación de metales, ya que permite la fabricación de piezas huecas, resistentes y de gran precisión dimensional, que de otro modo requerirían métodos más costosos y menos eficientes. La máquina de embutición, en cualquiera de sus variantes mecánicas o hidráulicas, representa un pilar de la producción masiva moderna, especialmente en sectores como la automoción, los electrodomésticos, la aeronáutica o los envases metálicos.
Las primeras versiones de estas máquinas estaban basadas en sistemas mecánicos con volantes de inercia y levas que transmitían la energía necesaria para deformar el metal. Aunque eran eficaces en la producción en serie, tenían limitaciones en cuanto a flexibilidad y precisión, además de depender en gran medida de la habilidad del operario para realizar ajustes adecuados. Con la evolución de la hidráulica, surgieron las máquinas de embutición hidráulicas, que permitieron un control mucho más preciso de la fuerza durante todo el recorrido del punzón. Esto resultó crucial para el embutido profundo, donde la uniformidad en la aplicación de la presión evita defectos como grietas, pliegues o adelgazamientos excesivos del material. Hoy en día, con la incorporación de servomotores eléctricos, sistemas CNC y plataformas digitales, las máquinas de embutición se han convertido en sistemas inteligentes capaces de garantizar repetibilidad absoluta y trazabilidad en cada pieza producida.
En la práctica, estas máquinas hacen posible la fabricación de componentes muy variados. En la industria del automóvil, se utilizan para producir capós, puertas, guardabarros y paneles estructurales que deben cumplir requisitos estrictos de seguridad y ligereza. En el ámbito de los envases, las máquinas de embutición permiten la producción de latas de bebidas, aerosoles y contenedores metálicos, donde la uniformidad de espesor y la ausencia de defectos son esenciales para asegurar resistencia y hermeticidad. En la línea de los electrodomésticos, facilitan la creación de carcasas de lavadoras, hornos o microondas, combinando funcionalidad con un acabado estético de alta calidad. En sectores más especializados, como la aeronáutica o la energía, estas máquinas son indispensables para fabricar componentes que deben soportar esfuerzos mecánicos considerables manteniendo al mismo tiempo un peso reducido.
Una característica clave de la máquina de embutición moderna es la capacidad de integrar tecnologías digitales que optimizan su rendimiento. Sensores avanzados miden en tiempo real la fuerza aplicada, el desplazamiento del punzón y la resistencia del material, generando datos que pueden ser analizados para prevenir errores y mejorar continuamente el proceso. La integración de sistemas de mantenimiento predictivo ayuda a reducir tiempos de parada no planificada, ya que la máquina puede advertir de posibles desgastes en las matrices o desviaciones en los parámetros antes de que se conviertan en fallos críticos. Asimismo, la conectividad con plataformas de gestión industrial permite coordinar la producción de manera más eficiente, adaptándose rápidamente a cambios en la demanda sin perder productividad.
En definitiva, la máquina de embutición no es solo una herramienta de deformación del metal, sino una tecnología estratégica que combina ingeniería mecánica, hidráulica, electrónica y digitalización para responder a las exigencias de la industria contemporánea. Su evolución demuestra cómo un principio básico de transformación de materiales puede perfeccionarse hasta convertirse en una plataforma sofisticada, capaz de producir piezas complejas con la máxima eficiencia y calidad.
La máquina de embutición, en su evolución histórica, ha pasado de ser un equipo puramente mecánico a convertirse en un sistema altamente sofisticado que integra control electrónico, servomecanismos y soluciones digitales. En sus primeras décadas de uso, estas máquinas estaban diseñadas con mecanismos de biela-manivela, accionadas por grandes volantes de inercia que acumulaban energía y la liberaban en un solo golpe. Esta concepción, aunque muy útil para producciones repetitivas, no ofrecía la flexibilidad necesaria cuando se trataba de materiales más sensibles, geometrías complejas o necesidades de embutido profundo. Con el tiempo, la industria empezó a demandar piezas con tolerancias más estrictas, superficies libres de imperfecciones y una reducción considerable de los desperdicios de material, lo que obligó a que la tecnología de embutición se orientara hacia sistemas de control más precisos. De este modo surgieron las prensas hidráulicas, capaces de ejercer una presión continua y uniforme a lo largo de todo el recorrido del punzón, lo que resultó revolucionario para conseguir embutidos de mayor profundidad sin comprometer la integridad de la chapa metálica.
La introducción de la hidráulica permitió trabajar con una variedad más amplia de materiales, no solo aceros suaves sino también aceros inoxidables, aleaciones de aluminio y, más adelante, materiales avanzados como aleaciones de titanio o chapas de alta resistencia utilizadas en la automoción y la aeronáutica. Estas últimas presentaban retos importantes en términos de conformado, ya que su dureza y resistencia al estirado podían ocasionar grietas, arrugas o desgarros. Sin embargo, con la presión controlada y ajustable de las máquinas hidráulicas, fue posible alcanzar niveles de precisión que antes eran inalcanzables, lo cual abrió nuevas posibilidades para el diseño y la ingeniería de piezas. Con la llegada de la electrificación de las prensas, a través de servomotores de alta eficiencia, las máquinas de embutición lograron una combinación ideal: la potencia y la suavidad del control hidráulico junto con la velocidad, eficiencia energética y exactitud del control eléctrico.
Hoy en día, las máquinas de embutición forman parte integral de las cadenas de producción más avanzadas, especialmente en el sector del automóvil, donde el conformado de la chapa es un proceso crítico para la fabricación de carrocerías. El estampado de puertas, capós, techos o laterales completos requiere una coordinación precisa entre múltiples fases de embutición, corte, rebordeado y acabado, todo lo cual es posible gracias a la integración de la máquina de embutición en líneas robotizadas. Robots industriales alimentan las prensas con láminas de acero laminado, mientras sistemas de visión artificial supervisan la correcta colocación del material y el ajuste de parámetros, reduciendo la probabilidad de error humano. En estas aplicaciones, la máquina de embutición ya no es un equipo aislado, sino el corazón de un sistema automatizado que produce miles de piezas idénticas al día con una constancia casi absoluta en calidad y acabado.
Un aspecto particularmente interesante de la evolución de estas máquinas es el modo en que se han adaptado a los principios de la industria 4.0. Hoy no basta con producir piezas con precisión, sino que es imprescindible que cada proceso genere datos útiles que puedan ser analizados en tiempo real. Las máquinas de embutición actuales están equipadas con sensores que miden la presión, la velocidad, la temperatura y las deformaciones del material durante todo el ciclo. Esta información se transmite a sistemas centralizados que pueden detectar anomalías mínimas, anticipar el desgaste de una matriz o ajustar de forma automática los parámetros de la máquina para mantener la calidad sin necesidad de detener la producción. El mantenimiento predictivo, basado en estos datos, ha cambiado radicalmente la manera en que se gestionan las plantas industriales, ya que evita paradas costosas y maximiza la disponibilidad de los equipos.
Además, el papel de estas máquinas se ha visto reforzado por las nuevas exigencias de sostenibilidad. La industria busca reducir el consumo de energía y minimizar los desperdicios de material, lo que ha impulsado el desarrollo de prensas más eficientes, capaces de optimizar el flujo de material durante el embutido para reducir el recorte sobrante. Incluso se investigan combinaciones de procesos, como el embutido combinado con hidroformado, que permiten alcanzar formas aún más complejas utilizando menos etapas de producción. Este tipo de innovaciones están marcando el futuro de la embutición, ya que no solo se trata de producir más, sino de hacerlo de manera más limpia, con menor impacto ambiental y cumpliendo normativas internacionales cada vez más estrictas.
En conclusión, la máquina de embutición es mucho más que una prensa destinada a dar forma a chapas metálicas; es un reflejo del avance tecnológico en la ingeniería de manufactura. Desde los antiguos sistemas mecánicos con limitaciones de control hasta los modernos equipos híbridos y digitales, su desarrollo ha acompañado las transformaciones de la industria en general, adaptándose a nuevas demandas y a un entorno cada vez más competitivo. Su versatilidad, precisión y capacidad de evolución la convierten en un elemento esencial para la producción industrial moderna, y es previsible que siga desempeñando un papel estratégico en el futuro, sobre todo a medida que se integren nuevas tecnologías como la inteligencia artificial aplicada al control de procesos y el análisis predictivo basado en big data.
La embutición como proceso industrial no puede entenderse únicamente desde la perspectiva de una máquina que deforma una lámina metálica, sino como una interacción compleja entre material, geometría, parámetros de proceso y diseño de la propia prensa. Dentro de este amplio campo, la máquina de embutición ha debido evolucionar para dar respuesta a diferentes tipos de embutido, cada uno con características y desafíos particulares. El embutido profundo, por ejemplo, es aquel en el que la profundidad de la pieza formada es superior al diámetro de la abertura inicial, lo que exige una enorme capacidad de control en la fuerza ejercida sobre el punzón y el material. En este tipo de operación, el riesgo de roturas o de arrugas es elevado, por lo que las prensas hidráulicas con cojín de presión ajustable han resultado decisivas, ya que permiten aplicar una contrapresión regulada sobre la lámina mientras el punzón desciende, evitando que el material fluya de manera incontrolada. Gracias a este control, es posible fabricar piezas como depósitos de combustible, recipientes a presión, componentes cilíndricos para la industria química y farmacéutica, o incluso carcasas profundas para motores eléctricos.
Por otro lado, el embutido progresivo introduce una lógica distinta al proceso, ya que combina el troquelado y el conformado en varias etapas consecutivas dentro de un mismo utillaje. Aquí, la máquina de embutición no actúa de manera aislada, sino que se integra en una línea de troqueles progresivos que transforman gradualmente la lámina metálica desde una simple plancha hasta una pieza final altamente compleja. Este sistema resulta esencial en industrias que requieren grandes volúmenes de producción con precisión repetitiva, como la automotriz y la de electrodomésticos. Los troqueles progresivos, instalados en prensas mecánicas o servoprensas, permiten fabricar elementos como bisagras, cerraduras, clips metálicos y piezas estructurales de pequeño y mediano tamaño, todo en un ciclo continuo que reduce significativamente los tiempos de fabricación y el coste unitario de cada pieza.
Otra variante relevante es el embutido inverso, en el cual el material se desplaza en dirección contraria al movimiento del punzón. A diferencia del embutido convencional, donde la chapa fluye en el mismo sentido de la fuerza, en este caso se fuerza al material a moverse hacia arriba mientras el punzón se introduce, lo que permite obtener paredes más uniformes y un control mayor sobre el espesor de la pieza. Este procedimiento se emplea en componentes que requieren tolerancias geométricas muy estrictas y acabados superficiales de alta calidad, como envases metálicos para la industria farmacéutica o piezas técnicas de precisión en el ámbito aeroespacial. Las máquinas diseñadas para este tipo de embutido deben contar con mecanismos que aseguren un guiado perfecto del punzón y sistemas de lubricación avanzados que reduzcan la fricción y el desgaste de las herramientas, ya que las exigencias sobre el material y el troquel son significativamente mayores.
También se encuentra el embutido de pared delgada, que responde a la necesidad de fabricar piezas con espesores reducidos sin comprometer su resistencia estructural. Este tipo de embutido exige un control muy fino de la presión y la velocidad del punzón, así como de la calidad de la materia prima, ya que cualquier irregularidad puede traducirse en roturas o deformaciones indeseadas. Es común encontrar este procedimiento en la producción de latas, envases de bebidas, recipientes alimentarios y otros productos que combinan ligereza con capacidad de resistencia. En este campo, la máquina de embutición debe trabajar en conjunto con sistemas de lubricación y recubrimiento que faciliten el flujo del material, así como con matrices de alta precisión fabricadas con aceros especiales tratados térmicamente o incluso con recubrimientos de nitruro para prolongar la vida útil del utillaje.
Cada uno de estos tipos de embutición no solo determina el diseño de la máquina, sino también el de las matrices, el sistema de alimentación de la chapa y las estrategias de lubricación. Una máquina destinada a embutido profundo requiere robustez estructural y un sistema hidráulico potente y regulable, mientras que una destinada al embutido progresivo se beneficia más de la velocidad y repetitividad de una prensa mecánica o servoaccionada. En el embutido inverso y el de pared delgada, la precisión geométrica y el control de parámetros dinámicos resultan cruciales, lo que implica una inversión mayor en sistemas de monitorización en tiempo real y en componentes de alto rendimiento. La evolución de estas tecnologías ha sido posible gracias a décadas de investigación en ciencia de materiales, tribología y automatización industrial, campos que han permitido comprender mejor cómo se comporta una lámina metálica bajo condiciones de esfuerzo complejo.
Si bien la función principal de la máquina de embutición es transformar una plancha metálica en una pieza tridimensional, su impacto va mucho más allá de esa definición. Gracias a estas máquinas, industrias enteras han podido avanzar en términos de ligereza estructural, eficiencia en el uso de materiales y reducción de costes. Los automóviles modernos, por ejemplo, no podrían fabricarse sin el aporte de procesos de embutición, que permiten conformar desde piezas estructurales hasta elementos estéticos con exactitud milimétrica y repetitividad garantizada. Lo mismo ocurre con la producción de envases metálicos, un sector que depende casi en su totalidad de la embutición para garantizar la seguridad alimentaria y farmacéutica mediante recipientes herméticos, resistentes y de bajo coste.
El estudio de los materiales en la embutición resulta crucial para comprender el alcance y las posibilidades de las máquinas que realizan este proceso, ya que no todos los metales se comportan de la misma manera frente a las fuerzas de estirado y deformación. El acero, por ejemplo, es el material más utilizado en embutición debido a su resistencia, su relativa ductilidad y su bajo coste. Sin embargo, no todos los aceros son adecuados para este tipo de procesos; se requieren calidades especiales denominadas aceros de embutición profunda, caracterizados por un bajo contenido en carbono y un refinado controlado de su microestructura, lo que les otorga una mayor capacidad de estiramiento sin que aparezcan grietas ni roturas prematuras. Cuando se trabaja con acero, la máquina de embutición debe estar preparada para aplicar fuerzas relativamente altas y disponer de sistemas de guiado rígidos, puesto que el material tiende a ofrecer mayor resistencia al flujo. La precisión en la presión ejercida por el cojín de la prensa y la calidad de la lubricación también se vuelven determinantes para evitar problemas como el endurecimiento localizado o las arrugas en las zonas periféricas de la pieza.
El aluminio, en cambio, se comporta de manera muy distinta en la embutición. Es un metal ligero, con buena maleabilidad y una densidad mucho más baja que la del acero, lo que lo hace muy atractivo para industrias como la automotriz y la aeronáutica, donde la reducción de peso es un factor estratégico. No obstante, el aluminio presenta una tendencia mayor al agrietamiento por su menor coeficiente de endurecimiento, por lo que las prensas deben aplicar fuerzas más uniformes y controladas, con velocidades de embutición más ajustadas y sistemas de lubricación mejorados para reducir la fricción. Asimismo, las matrices que trabajan con aluminio suelen fabricarse con recubrimientos especiales que evitan la adhesión del material al utillaje, ya que este metal tiende a pegarse a las superficies de acero por fenómenos de adhesión en frío. El desarrollo de aleaciones de aluminio específicas para embutición ha permitido ampliar el rango de aplicaciones de este metal, como en paneles estructurales de automóviles, carcasas de dispositivos electrónicos y componentes ligeros para sistemas de climatización y refrigeración.
El titanio plantea otro conjunto de retos particulares, ya que es un material de altísima resistencia y excelente comportamiento frente a la corrosión, pero al mismo tiempo ofrece una ductilidad limitada y una tendencia al endurecimiento muy marcada durante el proceso de deformación. Embutir titanio requiere máquinas de gran robustez, equipadas con sistemas hidráulicos de precisión capaces de aplicar presiones muy elevadas con un control extremadamente fino. Además, se necesitan lubricantes de alto rendimiento y, en ocasiones, condiciones especiales de temperatura que reduzcan la resistencia al flujo del material, lo que introduce un nivel adicional de complejidad en el diseño de la prensa y de los troqueles. El titanio se utiliza en sectores altamente especializados, como la industria aeroespacial y la biomédica, donde la embutición se aplica para fabricar componentes como carcasas de turbinas, elementos de fijación quirúrgica y piezas estructurales que requieren ligereza, resistencia y durabilidad excepcionales.
Un caso más reciente y cada vez más importante es el de los materiales compuestos y los aceros de ultra alta resistencia, que han irrumpido en la industria automotriz y en otros sectores donde se busca una combinación de rigidez, ligereza y resistencia al impacto. Estos materiales plantean un gran desafío a las máquinas de embutición porque su comportamiento no es lineal ni predecible como en los metales convencionales. Los aceros de ultra alta resistencia, por ejemplo, requieren fuerzas mucho mayores para ser conformados, lo que implica que las prensas deban contar con bastidores reforzados, sistemas hidráulicos de gran potencia y utillajes fabricados con aceros de herramientas de altísima dureza y recubrimientos avanzados. En el caso de los compuestos, la embutición no siempre se realiza en frío, sino en combinación con procesos de calentamiento controlado que permiten reblandecer la matriz polimérica y facilitar el moldeo de las fibras. Esto obliga a rediseñar la máquina para incorporar sistemas de calentamiento, control de temperatura y herramientas específicas que no dañen las fibras de refuerzo durante el proceso de conformado.
La adaptación de la máquina de embutición al tipo de material que se está trabajando no solo se refleja en la potencia necesaria o en la precisión de los sistemas de control, sino también en el diseño de los troqueles, en la geometría de los punzones y en los sistemas auxiliares que acompañan al proceso. En el caso del acero, los troqueles suelen ser más robustos, con radios de curvatura relativamente amplios que permiten un flujo más estable del material. En el aluminio, los radios pueden reducirse, pero la calidad superficial del troquel debe ser impecable para evitar adherencias. En el titanio y en los materiales de alta resistencia, los troqueles deben estar fabricados con materiales de máxima dureza y tratados para resistir el desgaste acelerado que producen estos metales. La lubricación, que a menudo se considera un detalle secundario, se convierte en un elemento crítico en todos los casos, ya que influye directamente en la fricción, en la estabilidad del flujo del material y en la vida útil de las herramientas.
Así, la máquina de embutición se configura como un sistema flexible que debe adaptarse a una gran diversidad de escenarios industriales. No existe un único diseño válido para todas las aplicaciones, sino un abanico de configuraciones que responden a la naturaleza del material, a la geometría de la pieza, a los volúmenes de producción requeridos y al nivel de precisión exigido por el sector. La tendencia actual en el desarrollo de estas máquinas apunta hacia prensas inteligentes con capacidad de monitorización en tiempo real, que ajustan automáticamente parámetros como la presión del cojín, la velocidad del punzón o la cantidad de lubricante aplicado en función de las condiciones detectadas durante el ciclo. Esto no solo mejora la calidad de las piezas embutidas, sino que también prolonga la vida útil de los troqueles y optimiza el uso de materiales costosos.
Prensa de Estampado Profundo
La prensa de estampado profundo constituye una de las máquinas más avanzadas y exigentes en el ámbito de la conformación de metales, pues está diseñada específicamente para transformar láminas planas en piezas huecas de gran profundidad, manteniendo espesores relativamente uniformes y sin comprometer la resistencia estructural del material. El principio de funcionamiento de este tipo de prensas se basa en la aplicación de una fuerza controlada y progresiva a través de un punzón que empuja la chapa hacia una matriz, logrando que el material fluya plásticamente y adopte la forma deseada. La diferencia fundamental entre el estampado convencional y el estampado profundo radica en la magnitud de la deformación: en este último, la profundidad de la pieza supera con creces su diámetro, lo que obliga a la máquina a trabajar bajo condiciones de altísima precisión, con sistemas de guiado extremadamente rígidos y cojines hidráulicos que evitan arrugas, desgarramientos o fallos prematuros en la superficie de la pieza.
Las prensas de estampado profundo pueden ser de accionamiento mecánico, hidráulico o servoaccionado, dependiendo de las necesidades de producción. Las mecánicas son habituales en series grandes, pues ofrecen velocidad y repetitividad en ciclos continuos, aunque presentan limitaciones cuando se requieren ajustes finos de presión a lo largo de la carrera. Las hidráulicas, en cambio, brindan un control más exacto de la fuerza aplicada en todo el recorrido del punzón, lo que las hace más adecuadas para piezas de geometría compleja o materiales con un comportamiento difícil, como el titanio o los aceros de ultra alta resistencia. Las servo-prensas combinan lo mejor de ambos mundos, ya que mediante motores eléctricos y sistemas electrónicos de control permiten variar la velocidad, la fuerza y la posición en tiempo real, adaptándose a cada etapa del proceso de estampado con una flexibilidad sin precedentes.
El diseño de la prensa de estampado profundo debe responder no solo a la magnitud de las fuerzas requeridas, sino también a la necesidad de proteger la integridad del material. En este sentido, la presencia de cojines de presión es fundamental, ya que ejercen una fuerza opuesta sobre el material mientras el punzón avanza, manteniendo la chapa tensada y evitando que se formen arrugas en las zonas periféricas. La magnitud de esa fuerza de retención debe estar perfectamente calibrada: si es insuficiente, aparecen pliegues y defectos superficiales; si es excesiva, el material puede desgarrarse al no poder fluir hacia el interior de la matriz. Por ello, la prensa suele incorporar sistemas hidráulicos o neumáticos de regulación continua, a menudo asistidos por sensores que miden la presión en tiempo real y la ajustan automáticamente para garantizar un flujo estable del material.
El estampado profundo requiere además el uso de matrices de alta precisión, fabricadas con aceros especiales tratados térmicamente para resistir el desgaste, las cargas dinámicas y la fricción continua a la que son sometidas. En piezas de aluminio, es común emplear recubrimientos cerámicos o nitruración para evitar la adhesión del material, mientras que en aceros de alta resistencia se utilizan aceros rápidos o incluso materiales con insertos de carburo cementado para prolongar la vida útil de las herramientas. La geometría del punzón y de la matriz, el radio de transición en los bordes y el acabado superficial influyen de manera decisiva en la calidad del estampado, pues determinan cómo fluye el material y en qué medida se concentran los esfuerzos.
El papel de la lubricación en el estampado profundo no puede subestimarse. Dado que el material se desplaza bajo presiones extremadamente elevadas, la fricción entre la chapa y los utillajes es enorme, lo que genera calor y acelera el desgaste. Para contrarrestar estos efectos, se utilizan lubricantes específicos de base grasa, aceite mineral o sintética, a menudo reforzados con aditivos de alta presión que crean una película protectora entre las superficies. En procesos avanzados, se recurre incluso a sistemas de micro-lubricación o a recubrimientos sólidos, como el grafito o el disulfuro de molibdeno, que reducen la fricción y facilitan el deslizamiento del material. Una lubricación deficiente no solo compromete la vida de las herramientas, sino que aumenta drásticamente la probabilidad de defectos en la pieza final.
Las aplicaciones de las prensas de estampado profundo abarcan una amplia gama de sectores industriales. En la industria automotriz se utilizan para fabricar depósitos de combustible, componentes estructurales, carcasas de embrague y cubetas metálicas de gran resistencia. En el sector de electrodomésticos se aplican para producir cubetas de lavadoras, fregaderos de acero inoxidable y recipientes a presión. En la industria aeroespacial y de defensa, el estampado profundo es esencial para crear carcasas de motores, componentes de turbinas y piezas de titanio que requieren geometrías huecas y resistencia extrema sin comprometer el peso. Incluso en la industria alimentaria y de envases se emplea para producir latas y contenedores metálicos, donde se exige una alta velocidad de producción junto con una calidad superficial impecable.
Hoy en día, el desarrollo tecnológico ha llevado a que muchas prensas de estampado profundo estén equipadas con sistemas de monitorización digital que recopilan datos de cada ciclo, analizan parámetros críticos como la fuerza aplicada, la velocidad del punzón o la presión del cojín, y ajustan automáticamente las condiciones para garantizar una producción estable y de alta calidad. Estas prensas inteligentes permiten no solo mejorar la productividad, sino también optimizar el consumo de energía y prolongar la vida útil de las matrices, reduciendo costes operativos y aumentando la competitividad de la empresa.
La evolución de la prensa de estampado profundo ha estado marcada por la necesidad de responder a las crecientes exigencias de la industria en términos de precisión, flexibilidad y sostenibilidad, y en las últimas décadas este tipo de maquinaria ha experimentado transformaciones profundas que han ampliado sus capacidades y reducido sus limitaciones tradicionales. Una de las innovaciones más significativas ha sido la incorporación de sistemas servoaccionados, que reemplazan o complementan los tradicionales mecanismos de cigüeñal o hidráulicos con motores eléctricos de alta potencia y controladores digitales que permiten ajustar de manera independiente la velocidad, el par y la posición del punzón en cada fase del ciclo. Esto significa que, en lugar de un movimiento uniforme y predefinido, la máquina puede acelerar en las fases de aproximación, reducir la velocidad en el contacto con el material para evitar impactos bruscos, mantener una presión constante durante el conformado y volver a acelerar en la fase de retorno, lo que mejora no solo la calidad del estampado sino también la eficiencia energética al aprovechar mejor cada instante del ciclo. Además, la flexibilidad de los servoaccionamientos facilita la adaptación a diferentes materiales y geometrías sin necesidad de modificar mecánicamente la prensa, lo que reduce drásticamente los tiempos de preparación y aumenta la productividad en series cortas y variadas, algo cada vez más demandado en la industria moderna.
En paralelo, la digitalización ha llevado al estampado profundo a un nuevo nivel de control y trazabilidad, pues ahora las prensas incorporan sensores de presión, desplazamiento, vibración y temperatura que generan enormes volúmenes de datos durante cada operación. Estos datos son procesados en tiempo real por sistemas de control numérico que ajustan automáticamente parámetros como la fuerza del cojín, la velocidad del punzón o la sincronización entre diferentes etapas de la carrera. De esta manera, cada pieza fabricada no solo cumple con tolerancias estrictas, sino que además queda registrada con un historial de condiciones de producción que puede ser utilizado para fines de trazabilidad, auditoría de calidad o análisis de fallos. El uso de algoritmos de inteligencia predictiva permite detectar desviaciones mínimas en patrones de fuerza o vibración que podrían anticipar un desgaste irregular de la matriz o un fallo en el sistema hidráulico, y actuar de forma preventiva antes de que se produzca una parada de línea costosa. Este enfoque de mantenimiento predictivo no solo reduce los tiempos muertos, sino que incrementa la vida útil de los componentes críticos y asegura una producción más estable y confiable.
La sostenibilidad también ha influido en el desarrollo de estas prensas, ya que la presión regulatoria y el interés empresarial por reducir el consumo energético han impulsado la creación de sistemas de recuperación de energía en los ciclos de estampado. En muchas prensas modernas, la energía generada durante la desaceleración del punzón se recupera y se almacena en volantes de inercia eléctricos o en sistemas de baterías, de modo que puede reutilizarse en el siguiente ciclo. Este principio, similar al de la frenada regenerativa en los vehículos eléctricos, disminuye el consumo global de electricidad y reduce las emisiones indirectas de CO₂ asociadas a la producción. Asimismo, el uso de servomotores en lugar de sistemas hidráulicos en determinadas aplicaciones evita pérdidas de energía derivadas de la compresibilidad de los fluidos y la fricción interna, aumentando la eficiencia general de la máquina. En paralelo, se está desarrollando una nueva generación de lubricantes biodegradables y fluidos de estampado basados en aceites vegetales o polímeros solubles en agua, que reducen el impacto ambiental y facilitan el tratamiento de residuos, sin sacrificar la calidad de la superficie ni la durabilidad de las herramientas.
La interacción entre la prensa de estampado profundo y las cadenas de producción automatizadas es otro aspecto fundamental del desarrollo reciente, ya que en entornos industriales avanzados estas máquinas ya no operan de manera aislada, sino que forman parte de células de producción integradas con robots de alimentación, sistemas de transferencia entre estaciones y controles centralizados. Los robots colaborativos pueden alimentar la prensa con láminas, retirar piezas conformadas y trasladarlas directamente a procesos posteriores como el recorte, la soldadura o el ensamblaje, eliminando manipulaciones intermedias y reduciendo riesgos laborales. Todo este flujo se coordina mediante sistemas de comunicación estandarizados como OPC-UA o protocolos de la industria 4.0, lo que permite que la prensa se comunique con otras máquinas, con el software de planificación de la producción e incluso con plataformas en la nube que analizan los datos globales de la planta. De este modo, es posible optimizar la secuencia de producción en función de la demanda en tiempo real, asignar prioridades a ciertos lotes y ajustar automáticamente los parámetros de la prensa a las especificaciones de cada pedido, alcanzando una flexibilidad que hace unas décadas resultaba impensable en procesos de estampado profundo.
En cuanto al futuro inmediato de la prensa de estampado profundo, la tendencia apunta hacia una mayor personalización del proceso y una ampliación de las posibilidades de diseño de piezas, gracias al desarrollo de materiales avanzados como aceros de tercera generación, aleaciones de magnesio o compuestos híbridos que combinan metales con fibras poliméricas. La prensa del futuro deberá ser capaz de adaptarse a estos materiales exigentes sin perder velocidad ni precisión, lo que implica una combinación aún más sofisticada de servocontrol, monitorización digital y sistemas adaptativos de lubricación y refrigeración. Al mismo tiempo, la creciente demanda de piezas más ligeras y resistentes en sectores como el automotriz o el aeroespacial impulsará la investigación en geometrías de estampado más complejas, que requerirán prensas con mayor capacidad de carrera y una distribución de fuerzas más uniforme. El concepto de estampado profundo, que nació como una técnica puramente mecánica de conformación, se está transformando en un proceso inteligente, energéticamente optimizado y digitalmente interconectado, que no solo produce piezas, sino que también genera conocimiento sobre el comportamiento del material, el desgaste de las herramientas y la eficiencia global de la línea de producción.
Las prensas de estampado profundo modernas, gracias a la combinación de servoaccionamientos, control digital y automatización avanzada, han revolucionado la manera en que la industria automotriz y aeroespacial fabrican piezas complejas, permitiendo alcanzar niveles de precisión y productividad que antes eran impensables. En el sector automotriz, por ejemplo, las carrocerías de vehículos modernos están compuestas por cientos de piezas estampadas en acero de alta resistencia y aluminio, muchas de las cuales requieren profundidades de embutición significativas y geometrías complejas con radios precisos y espesores uniformes. Gracias a las prensas de estampado profundo, es posible conformar capós, techos, puertas, guardabarros y paneles estructurales que combinan ligereza, resistencia mecánica y exactitud dimensional, todo en ciclos controlados que aseguran repetitividad en cada pieza. La integración con robots de alimentación y extracción de piezas permite que la línea de estampado funcione de manera continua, minimizando la intervención humana y reduciendo riesgos laborales, mientras que los sistemas de monitorización digital ajustan en tiempo real la fuerza, la velocidad y la presión del cojín según las características del material, evitando defectos como arrugas, grietas o adelgazamiento excesivo de la chapa.
En la industria aeroespacial, las exigencias son aún mayores, porque los componentes deben cumplir estándares de seguridad extremadamente estrictos, soportar cargas elevadas y mantener la integridad estructural bajo condiciones extremas de temperatura, presión y vibración. Las prensas de estampado profundo se utilizan para fabricar carcasas de motores, revestimientos de turbinas, depósitos de combustible y componentes estructurales de titanio o aleaciones de alta resistencia. En estos casos, la precisión de la máquina no se limita a la forma de la pieza, sino también al control del espesor del material en todo el contorno, ya que pequeñas variaciones pueden afectar el rendimiento y la seguridad del componente. Los sistemas de servoaccionamiento permiten ajustar la velocidad y la fuerza del punzón de manera incremental durante todo el ciclo de estampado, asegurando que el material fluya de forma uniforme y que los radios y curvaturas críticos se formen correctamente. La digitalización añade una capa adicional de confiabilidad, al registrar cada parámetro del proceso, permitir el análisis de tendencias y anticipar posibles desgastes de las matrices antes de que afecten la producción, lo que es vital cuando cada pieza puede costar miles de euros o dólares en material y tiempo de fabricación.
El impacto de estas innovaciones también se refleja en la eficiencia de materiales y energía. La presión regulada y los sistemas de lubricación avanzada reducen la fricción y minimizan el desperdicio de material, mientras que los motores servoeléctricos y la recuperación de energía en ciertos ciclos permiten disminuir significativamente el consumo energético de la prensa. Esto no solo reduce los costes operativos, sino que también contribuye a cumplir con los requisitos medioambientales de la industria, algo cada vez más crítico en la automoción y la aeronáutica. Además, la trazabilidad digital que proporcionan estas prensas inteligentes asegura que cada pieza producida pueda ser auditada, garantizando el cumplimiento de normativas internacionales y facilitando la certificación de componentes críticos.
En la práctica, los fabricantes de automóviles pueden producir miles de piezas idénticas de alta calidad al día, con tolerancias milimétricas y acabados superficiales listos para el ensamblaje, mientras que en la industria aeroespacial se logran conformados complejos de titanio o aleaciones avanzadas que antes requerían múltiples operaciones de mecanizado y soldadura. La combinación de servoaccionamientos, control digital, sensores en tiempo real, lubricación avanzada y automatización robotizada ha convertido a la prensa de estampado profundo en un pilar estratégico de la manufactura moderna, capaz de satisfacer tanto los requerimientos de producción masiva como los desafíos de piezas críticas de alta tecnología.
El desarrollo de los troqueles y matrices en prensas de estampado profundo representa un componente fundamental dentro de la cadena de producción, ya que la calidad de la pieza final depende en gran medida de la precisión y resistencia de estas herramientas, así como de la capacidad de la máquina para mantener condiciones constantes de presión y alineación durante cada ciclo. Los troqueles modernos están diseñados para soportar fuerzas extremadamente altas y distribuidas de manera uniforme, evitando concentraciones de tensión que puedan generar roturas o arrugas en la chapa metálica. Para ello, se emplean aceros de alta dureza tratados térmicamente, con procesos de nitruración o recubrimientos superficiales de carburo que incrementan su resistencia al desgaste, prolongan la vida útil de la herramienta y minimizan la adherencia del material. Además, la geometría de los troqueles se calcula con precisión para permitir un flujo controlado del metal; los radios de curvatura, la inclinación de las paredes y los rebordes se diseñan según el tipo de material, el espesor de la chapa y la profundidad de embutición, de manera que cada pieza salga con espesores uniformes y sin deformaciones indeseadas.
Las matrices, por su parte, se integran con sistemas auxiliares que garantizan la correcta alimentación del material y el control de su comportamiento durante la deformación. Entre estos sistemas destacan los cojines hidráulicos regulables, que ejercen presión sobre la chapa en función de su fluencia, los sistemas de lubricación y enfriamiento que reducen la fricción y el calentamiento local, y los sensores de posición y fuerza que monitorean en tiempo real el proceso. En troqueles progresivos, donde el estampado y el troquelado ocurren en varias etapas consecutivas, la sincronización de cada matriz con la prensa es crucial para evitar desalineaciones, deformaciones parciales o daños en la herramienta. Los fabricantes modernos de prensas de estampado profundo invierten grandes recursos en la simulación digital de estas interacciones, utilizando software de análisis por elementos finitos para predecir cómo se comportará la chapa en cada fase del ciclo y ajustar los diseños de troqueles antes de fabricar la primera pieza física.
La evolución tecnológica también ha permitido desarrollar troqueles y matrices modulares, que pueden ser reemplazados o ajustados con facilidad para producir diferentes piezas en la misma prensa, aumentando la flexibilidad de la línea de producción. Esta modularidad es especialmente importante en industrias donde la variedad de componentes es elevada y los tiempos de cambio deben ser mínimos, como en la automoción, electrodomésticos o envases metálicos. Además, la introducción de sistemas inteligentes de monitorización permite registrar la temperatura, presión y desgaste de cada matriz, detectando de forma anticipada posibles fallos que podrían comprometer la calidad de la producción. Esto, combinado con la digitalización de los parámetros de proceso, posibilita un mantenimiento predictivo que reduce tiempos muertos y asegura una producción más estable y eficiente.
En la práctica, la correcta integración de troqueles, matrices y sistemas auxiliares se traduce en piezas metálicas con geometrías complejas y acabados superficiales de alta calidad. Por ejemplo, en la industria automotriz, los paneles de carrocería, puertas, techos y capós son estampados profundos que requieren mantener espesores uniformes, radios de curvatura precisos y superficies libres de defectos, todo mientras la producción debe cumplir con volúmenes elevados y estrictos estándares de repetibilidad. En la industria aeroespacial, las matrices permiten fabricar carcasas de motores, depósitos de combustible y piezas estructurales de titanio que soportan cargas extremas y deben cumplir con tolerancias milimétricas. El control digital de cada parámetro, la lubricación avanzada y la monitorización de fuerzas permiten que incluso los metales más difíciles, como aleaciones de alta resistencia o titanio, puedan conformarse sin defectos.
Los sistemas auxiliares también influyen directamente en la seguridad y ergonomía de la operación. La automatización de la alimentación de chapas, la extracción de piezas y la sincronización con robots y transportadores reduce la intervención humana en áreas de riesgo, minimizando accidentes y mejorando la eficiencia. Al mismo tiempo, la trazabilidad digital de cada pieza facilita la identificación de lotes defectuosos, la optimización del proceso y la gestión integral de la producción. Los desarrollos recientes apuntan a una integración aún mayor con la Industria 4.0, en la que la prensa, los troqueles, los sensores y los sistemas de control se comunican entre sí y con plataformas en la nube para permitir análisis avanzados de rendimiento, mantenimiento predictivo y ajustes automáticos de parámetros en tiempo real.
En definitiva, el conjunto formado por la prensa de estampado profundo, los troqueles, las matrices y los sistemas auxiliares configura un ecosistema de manufactura altamente sofisticado, en el que cada elemento está diseñado y optimizado para maximizar la calidad, la productividad y la durabilidad de la operación. Esta sinergia entre máquina, herramienta y proceso es lo que permite a la industria moderna fabricar piezas metálicas complejas con precisión, rapidez y bajo coste, respondiendo a la demanda de sectores como la automoción, aeroespacial, electrodomésticos, envases y aplicaciones técnicas especializadas. La tendencia hacia prensas inteligentes, troqueles modulares y sistemas de control digital continuará expandiendo las posibilidades de conformado de metales, permitiendo nuevas geometrías, materiales avanzados y procesos más eficientes y sostenibles.
Prensa para Embutición
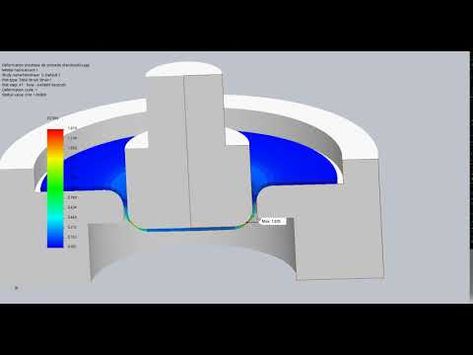
La prensa para embutición es una de las máquinas más importantes dentro de los procesos de conformado de metales, diseñada específicamente para transformar láminas planas en piezas huecas o con geometrías complejas mediante la aplicación controlada de presión sobre el material. Su funcionamiento básico consiste en colocar la chapa entre un punzón y una matriz, aplicando fuerza para que el metal fluya plásticamente y adopte la forma deseada, lo que requiere un equilibrio delicado entre la fuerza del punzón, la presión del cojín y la lubricación. A diferencia de otros procesos de estampado, la embutición permite alcanzar profundidades considerables, manteniendo espesores uniformes y evitando defectos como arrugas, grietas o adelgazamiento excesivo. La prensa puede ser de accionamiento mecánico, hidráulico o servoaccionado, y la elección depende del material, la geometría de la pieza y los volúmenes de producción requeridos.
En las prensas mecánicas, la fuerza se transmite mediante un sistema de cigüeñal y bielas, lo que garantiza velocidad y repetitividad en series largas, pero con menor flexibilidad para ajustar parámetros durante el ciclo. Las prensas hidráulicas permiten un control más preciso de la fuerza a lo largo de todo el recorrido del punzón, lo que es fundamental para materiales delicados o piezas con formas complejas, ya que pueden ejercer presión variable y mantener la chapa tensada uniformemente. Por su parte, las servo-prensas combinan la rapidez de las mecánicas con la precisión de las hidráulicas, mediante motores eléctricos y control digital, lo que permite ajustar en tiempo real la velocidad, la fuerza y la posición del punzón, adaptándose a cada fase del proceso y optimizando la calidad de la pieza final.
El diseño de la prensa para embutición también considera la integridad del material y la protección de los troqueles. Los cojines regulables son fundamentales para mantener la chapa bajo tensión, evitando la aparición de pliegues o arrugas, y la lubricación juega un papel crucial para reducir la fricción y el desgaste de las herramientas. La selección del material del troquel, su geometría y los recubrimientos superficiales influyen directamente en la durabilidad de la herramienta y en la calidad del estampado, permitiendo conformar metales como acero, aluminio, titanio y aceros de alta resistencia sin comprometer la superficie o el espesor de la pieza.
El uso de prensas para embutición se extiende a múltiples sectores industriales. En la automoción, se emplean para fabricar depósitos de combustible, cubiertas de motor, paneles de carrocería y piezas estructurales, donde se requiere combinación de ligereza, resistencia y precisión dimensional. En la industria aeroespacial, se utilizan para carcasas de motores, depósitos de titanio y componentes críticos que soportan cargas extremas y deben cumplir con tolerancias estrictas. También se aplican en electrodomésticos, envases metálicos y piezas técnicas para maquinaria industrial, donde se requiere reproducibilidad y calidad superficial consistente en cada ciclo de producción.
Las prensas modernas incorporan sistemas de monitorización digital y control en tiempo real que registran parámetros como fuerza aplicada, velocidad del punzón, presión del cojín y temperatura, ajustando automáticamente el proceso para asegurar la calidad y prolongar la vida útil de las matrices. La integración con robots y sistemas de transporte automatizado permite alimentar la chapa, retirar piezas y continuar con operaciones posteriores como recorte o ensamblaje, aumentando la productividad y reduciendo la intervención humana en áreas de riesgo. Asimismo, el mantenimiento predictivo basado en sensores y análisis de datos anticipa desgastes o posibles fallos, reduciendo tiempos muertos y optimizando la eficiencia de la planta.
La prensa para embutición, por tanto, no es solo una máquina para conformar metales, sino un sistema completo que combina potencia, precisión, control digital y automatización para satisfacer las demandas de la industria moderna, garantizando piezas de alta calidad, producción eficiente y flexibilidad frente a materiales y geometrías diversas. La tendencia actual apunta hacia prensas más inteligentes, capaces de adaptarse a nuevos materiales, geometrías complejas y procesos sostenibles, asegurando que la embutición siga siendo un proceso central en la manufactura avanzada de metales.
La embutición en frío y en caliente representan dos enfoques distintos dentro del proceso de conformado de metales, y cada uno de ellos tiene implicaciones directas sobre el diseño de la prensa, los troqueles, la selección de materiales y los parámetros de operación. La embutición en frío es la más utilizada en la industria, especialmente para aceros, aluminio y algunas aleaciones ligeras, debido a que permite obtener piezas con tolerancias dimensionales muy precisas y un acabado superficial uniforme sin necesidad de calentar el material previamente. En este proceso, la chapa se conforma a temperatura ambiente, lo que genera mayores esfuerzos internos y fricción, haciendo que la prensa deba ser capaz de ejercer fuerzas elevadas y contar con un sistema de cojines que distribuya uniformemente la presión sobre el material. La lubricación es esencial, ya que reduce la fricción entre la chapa y los troqueles, evita el desgaste prematuro de las herramientas y asegura que el metal fluya de manera uniforme hacia la matriz sin arrugas ni grietas. Los troqueles deben fabricarse con aceros de alta dureza y, en muchos casos, recubrirse con materiales resistentes a la adhesión, especialmente cuando se trabaja con aluminio o aceros de alta resistencia.
En la embutición en caliente, el material se calienta previamente a temperaturas específicas para aumentar su ductilidad y reducir la resistencia al flujo, permitiendo conformar piezas con geometrías más profundas o materiales más difíciles de estirar, como aceros de ultra alta resistencia, titanio o aleaciones de níquel. Este calentamiento reduce significativamente las fuerzas necesarias en la prensa, pero introduce nuevos desafíos: la máquina debe soportar variaciones térmicas, los troqueles deben resistir la expansión y contracción del material, y los sistemas de lubricación y refrigeración deben diseñarse para operar en condiciones de alta temperatura. Además, la sincronización entre el calentamiento del material y el ciclo de la prensa es crítica para evitar deformaciones irregulares o defectos superficiales. La prensa en caliente, por tanto, requiere un control más sofisticado, con sistemas digitales que ajusten la presión, la velocidad y el tiempo de permanencia del punzón en función de la temperatura del material y de la geometría de la pieza.
En ambos casos, frío o caliente, la selección del material de la chapa influye directamente en la configuración de la prensa y los troqueles. Los aceros de embutición profunda, por ejemplo, permiten obtener piezas con paredes uniformes y radios precisos sin comprometer la resistencia, mientras que los aceros de ultra alta resistencia requieren prensas con bastidores reforzados, sistemas hidráulicos de mayor potencia y matrices con insertos de carburo cementado para resistir la fricción y el desgaste. Las aleaciones de aluminio, debido a su menor resistencia y tendencia a pegarse, requieren matrices con superficies extremadamente pulidas y lubricantes de alto rendimiento que eviten defectos superficiales y aumenten la fluidez del material. En el titanio, la embutición solo es posible mediante prensas con control de fuerza muy preciso, lubricación especializada y, a menudo, preacondicionamiento térmico de la chapa para facilitar el flujo del material.
El proceso de embutición también se complementa con sistemas auxiliares que mejoran la productividad y la calidad de las piezas. Los sistemas de alimentación automatizada colocan la chapa de manera precisa en la prensa, mientras que los robots o transportadores extraen las piezas conformadas y las llevan a operaciones posteriores como recorte, soldadura o ensamblaje. La monitorización digital en tiempo real permite ajustar la presión, la velocidad del punzón y la fuerza del cojín en función de la respuesta del material, asegurando que cada pieza cumpla con los estándares de tolerancia, espesor y acabado superficial. Además, los datos registrados durante el proceso facilitan la trazabilidad, el mantenimiento predictivo y la optimización de los parámetros de operación, reduciendo tiempos muertos y aumentando la eficiencia energética.
En definitiva, la prensa para embutición, ya sea en frío o en caliente, constituye un sistema complejo donde la máquina, los troqueles, el material y los sistemas auxiliares trabajan de manera coordinada para producir piezas de alta calidad, con geometrías complejas y tolerancias estrictas. La diferencia entre ambos tipos de embutición radica principalmente en las condiciones de temperatura, la fluidez del material y los esfuerzos requeridos, lo que impacta directamente en el diseño de la prensa, la selección de materiales y los sistemas de control y lubricación. Con la integración de tecnologías modernas como servoaccionamientos, control digital y automatización avanzada, estas prensas son capaces de adaptarse a una gran variedad de materiales y piezas, optimizando la producción, reduciendo desperdicios y asegurando la durabilidad de las herramientas y la calidad constante de cada ciclo de fabricación.
La optimización de los parámetros de presión, velocidad y lubricación en prensas de embutición modernas es un factor determinante para lograr piezas de alta calidad, maximizar la vida útil de los troqueles y reducir desperdicios de material y energía. En el caso de la presión aplicada por el punzón, es fundamental calibrarla según la geometría de la pieza, el tipo de material y el espesor de la chapa. Una fuerza insuficiente puede provocar arrugas, pliegues o un flujo irregular del metal hacia la matriz, mientras que una fuerza excesiva puede causar grietas, adelgazamiento local o incluso el fallo del troquel. Para lograr este equilibrio, las prensas modernas emplean sistemas hidráulicos o servoaccionados que permiten ajustar la presión de manera continua durante todo el recorrido del punzón, adaptándose a cada fase del proceso: aproximación, conformado, embutición profunda y retorno. Además, la integración de sensores de fuerza y desplazamiento permite un control en tiempo real, detectando cualquier desviación y corrigiéndola automáticamente antes de que afecte la calidad de la pieza.
La velocidad del punzón es otro parámetro crítico que influye directamente en el comportamiento del material. Una velocidad demasiado alta puede generar impactos bruscos, inducir tensiones residuales y aumentar la fricción, mientras que una velocidad demasiado baja puede prolongar innecesariamente el ciclo de producción y generar calor localizado que afecte la superficie del metal. Las prensas con servoaccionamiento permiten variar la velocidad durante el ciclo, acelerando en la fase de aproximación para ganar tiempo, disminuyendo en el contacto inicial con la chapa para evitar impactos, y manteniendo una velocidad constante durante el flujo del material hacia la matriz para asegurar uniformidad. Esta regulación precisa de la velocidad, combinada con la presión controlada, facilita el conformado de materiales difíciles como aceros de alta resistencia, titanio o aleaciones de aluminio con espesores variables y formas complejas.
La lubricación juega un papel esencial en la optimización del proceso, ya que reduce la fricción entre la chapa y los troqueles, disminuye el desgaste de las herramientas y permite que el material fluya de manera uniforme. En aplicaciones industriales, se utilizan lubricantes sólidos, aceites especiales o grasas de alta presión, muchas veces reforzadas con aditivos que mejoran la adherencia y la resistencia a temperaturas elevadas. Para metales como el aluminio, se prefieren lubricantes con baja adherencia, mientras que para aceros de alta resistencia se emplean fluidos que soporten presiones extremas sin descomponerse. En prensas modernas, los sistemas de lubricación son automatizados, regulando la cantidad y distribución de manera precisa según el material, la geometría de la pieza y la etapa del ciclo, garantizando un flujo homogéneo del metal y reduciendo el riesgo de defectos superficiales o desgaste prematuro de los troqueles.
La combinación de presión, velocidad y lubricación debe ser ajustada según el tipo de embutición: en frío, se requiere mayor fuerza y lubricación eficiente para compensar la resistencia del material a temperatura ambiente, mientras que en caliente, la presión puede ser menor gracias a la ductilidad aumentada del metal, aunque los sistemas deben soportar las condiciones térmicas elevadas y controlar la expansión del material. En piezas profundas o con paredes delgadas, la sincronización precisa de estos parámetros es vital para evitar adelgazamiento excesivo, arrugas o fracturas, y garantizar que el espesor se mantenga uniforme en toda la pieza.
En la industria, la optimización de estos parámetros se traduce en resultados concretos y medibles: paneles de carrocería con superficies libres de defectos, depósitos de combustible sin arrugas, carcasas de motores con espesores precisos, y piezas críticas aeroespaciales que cumplen con estándares estrictos de seguridad y tolerancia. La integración de sistemas de control digital permite registrar todos los parámetros de cada ciclo, analizar tendencias de desgaste o variaciones en la presión y velocidad, y ajustar automáticamente la operación, garantizando una producción estable y eficiente. Al mismo tiempo, la trazabilidad digital facilita la auditoría de calidad, la planificación del mantenimiento y la optimización energética de la planta, lo que incrementa la competitividad y reduce costos.
En conclusión, la prensa para embutición moderna es un sistema complejo donde la correcta calibración de presión, velocidad y lubricación es esencial para maximizar la calidad de las piezas, prolongar la vida útil de los troqueles y optimizar la eficiencia del proceso. La combinación de servoaccionamientos, control digital, automatización de la lubricación y monitorización en tiempo real permite que estas prensas se adapten a diferentes materiales, espesores y geometrías, produciendo piezas de alta precisión de manera consistente y sostenible. Su aplicación abarca desde la industria automotriz y aeroespacial hasta electrodomésticos, envases y componentes industriales, consolidándose como un elemento central en la manufactura moderna de metales.
Las prensas de embutición se clasifican principalmente según su tipo de accionamiento, tamaño, capacidad de fuerza y complejidad de automatización, y cada categoría presenta ventajas específicas que la hacen adecuada para distintos tipos de piezas y volúmenes de producción. Entre las más comunes se encuentran las prensas mecánicas, hidráulicas y servoaccionadas, aunque dentro de cada categoría existen variaciones según la capacidad de tonaje y el diseño del bastidor. Las prensas mecánicas son tradicionales y funcionan mediante sistemas de cigüeñal, bielas y manivelas, transmitiendo fuerza de manera constante y repetitiva, lo que las hace ideales para series largas de piezas con geometrías relativamente simples y materiales de resistencia media. Su velocidad de ciclo es alta, lo que permite una producción continua y eficiente, pero ofrecen menor flexibilidad para ajustar presión o velocidad durante la carrera del punzón, y pueden requerir un tiempo considerable de ajuste cuando se cambia la geometría de la pieza. A pesar de ello, su simplicidad mecánica y bajo coste de mantenimiento las hace muy utilizadas en aplicaciones donde la repetitividad es más importante que la adaptabilidad, como el estampado de paneles de carrocería estándar, tapas de envases metálicos o piezas de electrodomésticos de gran volumen.
Las prensas hidráulicas, en cambio, permiten un control mucho más preciso de la fuerza aplicada durante todo el ciclo de embutición. La presión puede variarse continuamente desde el inicio hasta el final de la carrera del punzón, lo que facilita la conformación de materiales difíciles o piezas con geometrías complejas que requieren un flujo uniforme del metal. Este tipo de prensa es particularmente útil en la industria aeroespacial y automotriz para componentes de alta resistencia, depósitos profundos o piezas con paredes delgadas, donde incluso pequeñas variaciones en espesor o forma pueden comprometer la funcionalidad o la seguridad. Las prensas hidráulicas suelen operar a velocidades menores que las mecánicas, pero su adaptabilidad y capacidad para mantener presión constante hacen que sean más versátiles y adecuadas para embuticiones profundas o materiales sensibles a la deformación brusca, como aceros de ultra alta resistencia, titanio o aleaciones de aluminio.
Las prensas servoaccionadas combinan lo mejor de ambos mundos: la velocidad de las mecánicas y la precisión de las hidráulicas. Gracias a motores eléctricos controlados digitalmente, estas prensas permiten ajustar en tiempo real la velocidad, la posición y la fuerza del punzón, optimizando cada fase del ciclo según el comportamiento del material. Esto es particularmente valioso en producciones mixtas, donde se alternan piezas de diferentes geometrías o materiales, y en aplicaciones donde la eficiencia energética y la flexibilidad son prioridades. La capacidad de programar perfiles de fuerza y velocidad específicos para cada pieza reduce el desgaste de los troqueles, minimiza defectos y aumenta la vida útil de la máquina. Además, la integración con sistemas de automatización y monitoreo digital permite que la prensa se comunique con robots de alimentación, extracción y transporte, así como con plataformas de análisis de datos, lo que optimiza la producción, reduce errores y facilita el mantenimiento predictivo.
En cuanto al tamaño y la capacidad de fuerza, las prensas de embutición pueden variar desde pequeñas máquinas de mesa, utilizadas para prototipos, componentes electrónicos o envases metálicos, hasta grandes prensas industriales capaces de ejercer miles de toneladas de fuerza, necesarias para paneles de carrocería, depósitos de combustible, estructuras aeroespaciales o piezas de maquinaria pesada. La selección de la prensa adecuada depende de la profundidad de embutición, el espesor y tipo de material, la complejidad de la geometría y los volúmenes de producción. Las prensas grandes requieren bastidores reforzados, sistemas de cojín potentes y troqueles robustos, mientras que las pequeñas se enfocan en precisión, rapidez de cambio y ahorro energético.
El diseño de estas prensas también incorpora sistemas de seguridad avanzados, incluyendo protectores, sensores de presencia, paradas de emergencia automáticas y control de sobrecarga, para proteger tanto al operario como a la máquina. La trazabilidad digital, combinada con sensores de presión, desplazamiento y temperatura, permite registrar cada ciclo de producción, facilitando auditorías de calidad, mantenimiento predictivo y optimización continua de los parámetros de operación. La tendencia moderna apunta hacia la interconexión de la prensa con sistemas de la Industria 4.0, donde cada máquina actúa como un nodo dentro de una red inteligente que analiza datos globales de la planta, predice desgastes, ajusta parámetros automáticamente y optimiza la secuencia de producción en tiempo real.
En resumen, la elección de la prensa de embutición adecuada—mecánica, hidráulica o servoaccionada, pequeña o industrial, con mayor o menor tonelaje—depende del material, la geometría de la pieza, la profundidad de embutición y los objetivos de productividad y calidad. Cada tipo de prensa ofrece ventajas específicas: las mecánicas destacan por velocidad y repetitividad, las hidráulicas por precisión y adaptabilidad, y las servoaccionadas por flexibilidad, control y eficiencia energética. La combinación de un diseño robusto, troqueles y matrices optimizados, sistemas auxiliares de alimentación y extracción, lubricación avanzada y control digital permite producir piezas complejas con alta calidad, consistencia y sostenibilidad, consolidando a la prensa de embutición como un elemento clave en la manufactura moderna de metales.
Prensa de Embutidos
La prensa de embutidos, en el contexto industrial, es una máquina especializada diseñada para dar forma a productos cárnicos mediante un proceso de compresión controlada, extrusión y conformado, permitiendo obtener salchichas, chorizos, mortadelas, jamones y otros productos con forma y peso uniforme, consistencia adecuada y textura homogénea. Su funcionamiento se basa en la alimentación del producto cárnico previamente mezclado y condimentado en un embudo o tolva, desde donde un pistón, tornillo sinfín o sistema hidráulico empuja la masa hacia un tubo o molde, ajustando simultáneamente la presión y el flujo para que el embutido mantenga la densidad deseada y no presente burbujas de aire ni inconsistencias en la textura. La velocidad de extrusión y la fuerza aplicada son parámetros críticos, ya que determinan la uniformidad del producto y la integridad de la tripa, sea natural o artificial, evitando roturas o fugas durante el proceso.
Existen prensas de embutidos de distintos tipos y capacidades, desde modelos semiautomáticos para charcuterías y pequeñas plantas hasta sistemas completamente automáticos para la industria alimentaria de gran volumen. Las prensas semiautomáticas permiten al operario controlar manualmente la alimentación y la velocidad de extrusión, lo que ofrece flexibilidad en lotes pequeños o productos especiales, mientras que las automáticas cuentan con tolvas de gran capacidad, sistemas de alimentación continuos, sincronización de pistones o tornillos sinfín y control electrónico de presión y velocidad, garantizando consistencia en cada unidad y adaptabilidad para distintos calibres y tipos de tripa. En estos sistemas automáticos, los sensores de presión, flujo y nivel permiten ajustes en tiempo real, asegurando que cada embutido mantenga su forma, tamaño y densidad, y minimizando desperdicios o irregularidades.
Además de la conformación del embutido, muchas prensas industriales incorporan sistemas auxiliares que facilitan la producción y la higiene, como rodillos de corte, enrolladores, transportadores y dispositivos de pesaje, que permiten separar porciones uniformes, enrollar las salchichas o formar chorizos en longitudes estandarizadas y cumplir con los requerimientos de empaque y etiquetado. La limpieza y desinfección son aspectos esenciales; por ello, las prensas modernas están diseñadas con componentes desmontables, acero inoxidable de alta resistencia a la corrosión y superficies lisas que facilitan la higiene, evitando acumulaciones de grasa o residuos que puedan comprometer la seguridad alimentaria.
El control de temperatura también juega un papel relevante, especialmente cuando se trabaja con masas de carne frescas o mezcladas con especias. Mantener la carne a temperaturas adecuadas durante la embutición previene la proliferación bacteriana, asegura la consistencia de la masa y facilita el flujo uniforme dentro de la tripa. En algunas prensas avanzadas, se incorporan sistemas de enfriamiento del pistón o del embudo para mantener la carne en condiciones óptimas durante toda la producción, garantizando calidad y seguridad del producto final.
La prensa de embutidos es fundamental en la industria cárnica porque combina eficiencia, uniformidad y control higiénico en un solo proceso. La automatización permite producir grandes volúmenes sin sacrificar la calidad, mientras que los sistemas de control aseguran que cada embutido tenga peso, diámetro y textura uniformes, reduciendo mermas y mejorando la presentación final. Su aplicación abarca desde productos tradicionales hasta líneas modernas de producción industrial donde se requiere rapidez, precisión y cumplimiento de normativas sanitarias y de inocuidad alimentaria.
Las prensas de embutidos se presentan en una amplia variedad de diseños y capacidades, adaptándose a las necesidades de pequeñas charcuterías, plantas medianas y grandes instalaciones industriales. Entre los tipos más comunes se encuentran las prensas manuales, semiautomáticas, hidráulicas, neumáticas y completamente automáticas, cada una con ventajas específicas según la escala de producción, el tipo de producto y la uniformidad requerida. Las prensas manuales son ideales para talleres artesanales o producciones de bajo volumen; operadas por un pistón o manivela, permiten al usuario controlar directamente la presión y la velocidad de extrusión, proporcionando flexibilidad para distintos tipos de carne y tripa, aunque la producción por hora es limitada y depende de la destreza del operario. Estas prensas destacan por su simplicidad mecánica, bajo coste y facilidad de mantenimiento, y se utilizan principalmente en embutidos tradicionales donde la personalización del producto es importante.
Las prensas semiautomáticas incorporan sistemas de alimentación más eficientes, como tornillos sinfín o pistones accionados por motor eléctrico, que permiten una extrusión más uniforme y constante, manteniendo el control manual del operario para ajustes finos de presión y velocidad. Este tipo de prensa es ideal para medianas producciones donde se requiere un equilibrio entre flexibilidad, productividad y consistencia en el calibre de los embutidos. Los sensores de presión y flujo pueden integrarse para advertir sobre posibles bloqueos o irregularidades, asegurando que cada embutido cumpla con los estándares de calidad y evitando desperdicios de materia prima.
Las prensas hidráulicas y neumáticas representan el siguiente nivel de automatización, permitiendo controlar de manera precisa la fuerza aplicada sobre la masa cárnica, lo que es esencial para embutidos de gran tamaño, densidad uniforme o tripas delicadas. En las prensas hidráulicas, la fuerza se aplica mediante un pistón accionado por aceite a alta presión, lo que permite ejercer presión constante y ajustable durante todo el ciclo de embutición, incluso para productos largos o de embutición profunda. Las prensas neumáticas, por su parte, utilizan aire comprimido para mover el pistón, ofreciendo ciclos rápidos y repetitivos con menor inversión energética y menor complejidad mecánica, aunque con fuerza limitada comparada con las hidráulicas.
Las prensas completamente automáticas representan la máxima eficiencia para la producción industrial masiva. Estas máquinas integran tolvas de gran capacidad, sistemas de alimentación continua, pistones o tornillos sinfín controlados digitalmente, y mecanismos de corte y enrollado automáticos. Los sensores de presión, flujo y nivel de material permiten ajustar en tiempo real la extrusión, asegurando uniformidad de calibre, peso y densidad del embutido. Además, los sistemas automáticos se conectan con transportadores y líneas de envasado, lo que optimiza el flujo de producción y minimiza la intervención humana, reduciendo errores y garantizando condiciones higiénicas. En estas prensas, la programación de ciclos permite alternar entre distintos productos, calibres y tipos de tripa con ajustes mínimos, ofreciendo gran versatilidad para plantas que producen variedad de embutidos.
Otro aspecto fundamental en todas las prensas de embutidos es la higiene y la facilidad de limpieza. Las superficies en contacto con la carne deben ser de acero inoxidable, resistentes a la corrosión, y la máquina debe permitir desmontaje rápido de pistones, tornillos, tolvas y moldes para su limpieza y desinfección. La temperatura también es crítica; algunas prensas incluyen sistemas de enfriamiento de la masa o del pistón para mantener la carne a condiciones óptimas, evitando la proliferación bacteriana y asegurando la consistencia del producto durante todo el ciclo de producción. La correcta lubricación de partes móviles y juntas garantiza el funcionamiento eficiente de la prensa sin contaminar el producto.
En la industria, la elección de la prensa adecuada depende de factores como el tipo de embutido, el calibre de la tripa, el volumen de producción y el nivel de automatización requerido. Las prensas manuales y semiautomáticas son ideales para producción artesanal o mediana, ofreciendo control directo y flexibilidad; las hidráulicas y neumáticas permiten manejar embutidos más grandes y densos con mayor consistencia; y las automáticas facilitan la producción masiva con precisión, uniformidad y eficiencia. La combinación de fuerza controlada, velocidad adecuada, sistemas de alimentación y extracción, automatización y control digital asegura que cada embutido cumpla con estándares de tamaño, forma, densidad y textura, optimizando la producción y reduciendo desperdicios, tiempos muertos y riesgos de contaminación.
Las tecnologías modernas aplicadas en prensas de embutidos han transformado completamente la industria cárnica, permitiendo producir grandes volúmenes con alta uniformidad, control higiénico y eficiencia energética. Las prensas actuales cuentan con sistemas de control digital que regulan en tiempo real la presión del pistón o tornillo sinfín, la velocidad de extrusión y el flujo de masa cárnica, lo que garantiza que cada embutido mantenga el calibre, la densidad y la textura deseados. Estos controles digitales se complementan con sensores de nivel que supervisan la cantidad de carne en la tolva y evitan que se produzcan interrupciones o extrusiones irregulares, y con sensores de presión que ajustan automáticamente la fuerza del pistón para compensar variaciones en la densidad de la masa o en el calibre de la tripa. La integración de sistemas de retroalimentación permite que la máquina aprenda y optimice los parámetros de operación, adaptándose a distintos tipos de carne, aditivos, especias y tripas, reduciendo mermas y asegurando consistencia en toda la producción.
La automatización avanzada no solo regula la extrusión, sino que también coordina el corte, enrollado y transferencia de los embutidos hacia líneas de envasado o cocción. En plantas industriales de alta productividad, robots y transportadores se encargan de alimentar la máquina con la carne previamente mezclada, retirar los embutidos conformados y colocarlos en bandejas, empaquetadoras o hornos de cocción, lo que elimina la manipulación directa del producto y garantiza condiciones higiénicas estrictas. Los sistemas de pesaje integrados permiten cortar los embutidos en porciones exactas, evitando desperdicios y cumpliendo con los estándares de presentación y etiquetado. Todo el proceso puede supervisarse desde una interfaz digital centralizada, donde operadores y supervisores pueden ajustar parámetros, monitorear el estado de la producción y detectar fallos de manera inmediata.
Además, la modernización de las prensas incluye mejoras en la higiene y seguridad, esenciales en la industria alimentaria. Las prensas modernas están construidas en acero inoxidable, con superficies lisas que facilitan la limpieza, y cuentan con componentes desmontables que permiten un acceso rápido para lavado y desinfección. Sistemas de limpieza en lugar (CIP, por sus siglas en inglés) pueden integrarse en las prensas automáticas, garantizando que todas las partes en contacto con la carne se mantengan libres de contaminantes sin necesidad de desarmar completamente la máquina. La regulación de temperatura, mediante enfriamiento de la tolva o del pistón, asegura que la carne se mantenga en condiciones óptimas durante la extrusión, evitando proliferación bacteriana y preservando la textura y consistencia de los embutidos.
Los beneficios de estas tecnologías se reflejan en la eficiencia de producción, la calidad del producto y la trazabilidad. La capacidad de ajustar automáticamente la presión, la velocidad y el flujo permite producir embutidos uniformes incluso cuando se utilizan diferentes tipos de carne o tripas, mientras que la integración con sensores y sistemas de monitoreo digital permite registrar cada ciclo, generando datos útiles para mantenimiento predictivo, control de calidad y optimización del proceso. Esto es especialmente importante en industrias que requieren certificaciones de seguridad alimentaria y control de procesos, ya que facilita auditorías, seguimiento de lotes y cumplimiento normativo.
En plantas de alta productividad, estas prensas automáticas pueden producir miles de embutidos por hora, manteniendo uniformidad en diámetro, peso y densidad, mientras minimizan la intervención humana y reducen riesgos de contaminación o errores. La combinación de sistemas de alimentación automática, control digital, sensores de presión y flujo, robots para traslado y envasado, junto con soluciones de higiene avanzada, permite lograr una producción continua, eficiente y segura. Asimismo, estas prensas modernas contribuyen a la sostenibilidad, ya que optimizan el uso de materia prima, reducen energía desperdiciada y minimizan pérdidas de producto.
En definitiva, las prensas de embutidos modernas representan un sistema integral que combina precisión, control digital, automatización y soluciones de higiene avanzadas, adaptándose a una gran variedad de productos y volúmenes de producción. Estas tecnologías no solo mejoran la eficiencia y calidad, sino que también garantizan la seguridad alimentaria, la uniformidad del producto y la sostenibilidad de la producción, consolidándose como un elemento esencial en la industria cárnica contemporánea.
El diseño y la calibración de las prensas de embutidos para trabajar con tripas naturales o artificiales requieren una atención meticulosa a múltiples factores, ya que cada tipo de tripa tiene características físicas y mecánicas distintas que afectan directamente el flujo de la masa cárnica, la presión requerida y la uniformidad del producto final. Las tripas naturales, generalmente de intestino de cerdo, res o cordero, presentan variaciones en grosor, elasticidad y resistencia, lo que exige que la prensa cuente con sistemas de regulación de presión y velocidad muy precisos para evitar roturas, fugas o embutidos con paredes irregulares. En estos casos, el ajuste del pistón o del tornillo sinfín debe ser cuidadoso, y la máquina puede incorporar sensores de tensión en la tripa para monitorear la fuerza aplicada durante la extrusión, de modo que se mantenga la uniformidad en todo el lote. Además, la longitud del embutido y el calibre de la tripa determinan la velocidad de alimentación y el diámetro del tubo de extrusión; para tripas más finas se requieren ciclos más lentos y controlados, mientras que para calibres mayores se puede aumentar la velocidad, siempre dentro de los límites que garanticen integridad y textura.
Por otro lado, las tripas artificiales, fabricadas en colágeno, celulosa o plástico comestible, son más uniformes en diámetro y resistencia, lo que permite un control más consistente del calibre y la densidad del embutido. Sin embargo, estas tripas requieren adaptaciones en la prensa, como rodillos de alimentación ajustables y moldes de extrusión específicos que eviten arrugas o pliegues durante la formación. Los sistemas automáticos modernos permiten programar perfiles de presión y velocidad para cada tipo de tripa y producto, ajustando de manera precisa la fuerza aplicada por el pistón o el tornillo sinfín en función del material y la longitud del embutido. Esto asegura que el producto final tenga un espesor uniforme de la pared, densidad constante y la longitud exacta deseada, cumpliendo con los estándares de calidad y presentación.
La calibración también considera la densidad de la masa cárnica y la inclusión de aditivos, grasas o especias, ya que estas variables afectan la fluidez del material y la presión necesaria para mantener la integridad de la tripa. En prensas modernas, los sistemas de control digital registran la fuerza aplicada y el flujo de masa en tiempo real, realizando ajustes automáticos para compensar cualquier variación en la densidad o elasticidad de la tripa, asegurando que cada embutido tenga peso uniforme, sin burbujas de aire ni puntos de debilidad. Este nivel de control es especialmente importante en producciones industriales de gran escala, donde pequeños errores se multiplican y pueden generar desperdicio de producto o problemas de seguridad alimentaria.
Otro factor crítico en el diseño de la prensa es la longitud de los embutidos. Para productos cortos o medianos, el sistema de corte integrado permite porcionar de manera automática y rápida, manteniendo la uniformidad de peso y tamaño. En embutidos largos, como salchichas de gran calibre o chorizos de alta producción, la prensa puede incorporar enrolladores y sistemas de transporte continuo que guían la tripa mientras se llena, evitando estiramientos irregulares o torsiones que comprometan la uniformidad y la apariencia. La sincronización entre la extrusión, el corte y el enrollado es esencial para mantener un flujo constante y minimizar la intervención manual, aumentando la productividad y garantizando que cada pieza cumpla con los requisitos de presentación y densidad.
La higiene y seguridad también forman parte del diseño y calibración de las prensas para tripas naturales o artificiales. Todas las superficies en contacto con la carne deben ser de acero inoxidable, resistentes a la corrosión y fáciles de desmontar para limpieza y desinfección. Sistemas de limpieza en lugar (CIP) pueden integrarse en las prensas automáticas para mantener condiciones sanitarias óptimas sin detener la producción. Además, el control de temperatura de la masa y de la tripa durante la extrusión evita proliferación bacteriana y asegura que la carne fluya correctamente dentro de la tripa, preservando la textura, consistencia y sabor del producto final.
En plantas industriales modernas, la combinación de calibración precisa, control digital, automatización de alimentación y extracción, adaptación a tripas de distintos materiales y calibres, y sistemas de higiene avanzados permite producir embutidos de alta calidad con eficiencia máxima. Esto no solo asegura uniformidad en tamaño, peso y densidad, sino que también optimiza el uso de materia prima, minimiza desperdicios y reduce riesgos de contaminación, cumpliendo con los estándares de seguridad alimentaria y las expectativas del consumidor.
Máquinas Formadoras de Metales EMS
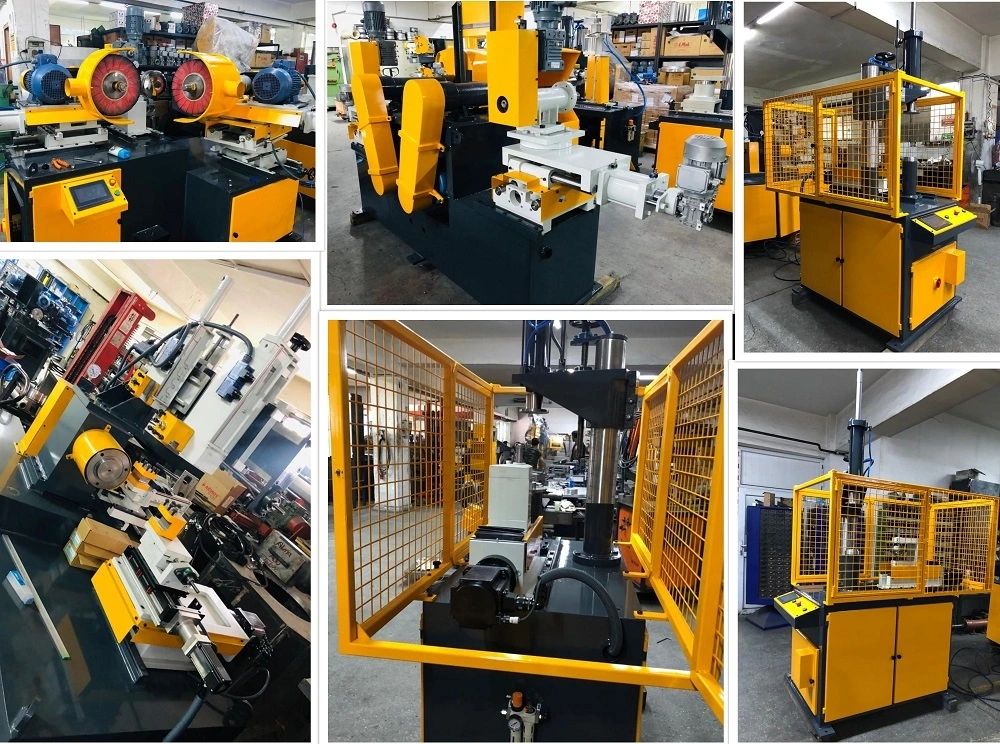
Diseñamos, fabricamos y montamos maquinaria metalmecánica como:
Prensa de transferencia hidráulica
Prensa para mosaicos de vidrio
Prensa hidráulica de embutición profunda
prensa de fundición
Prensa hidráulica de conformado en frío
Prensa de hidroformado
prensa compuesta
Prensa de moldeo de caucho de silicona
Prensa de pastillas de freno
Prensa de melamina
Prensa SMC y BMC
prensa labrotaroy
Máquina cortadora de bordes
Máquina rizadora de bordes
Máquina recortadora de abalorios
Máquina de recorte y jogging
Línea de producción de utensilios de cocina.
Máquina dobladora de tubos
Máquina dobladora de perfiles
Sierra de cinta para metal
Máquina de soldar cilíndrica
Prensas horizontales y utensilios de cocina.
Menaje de cocina, artículos de hotelería
Maquinaria para la producción de utensilios para hornear y cubiertos.
como una línea completa así como una máquina individual como:
Máquinas cortadoras de bordes y biseladoras
Pulidoras y rectificadoras de ollas y sartenes.
Prensas hidráulicas de trefilado
Máquinas troqueladoras circulares
remachadora
Punzonadoras
Máquina de alimentación de prensa
Puede consultar nuestra maquinaria en funcionamiento en: EMS Máquinas Formadoras de Metales EMS – YouTube
Aplicaciones:
Punzonado de bridas
Abalorios y nervaduras
Bridas
Guarnición
Curling
costura de bloqueo
Nervaduras