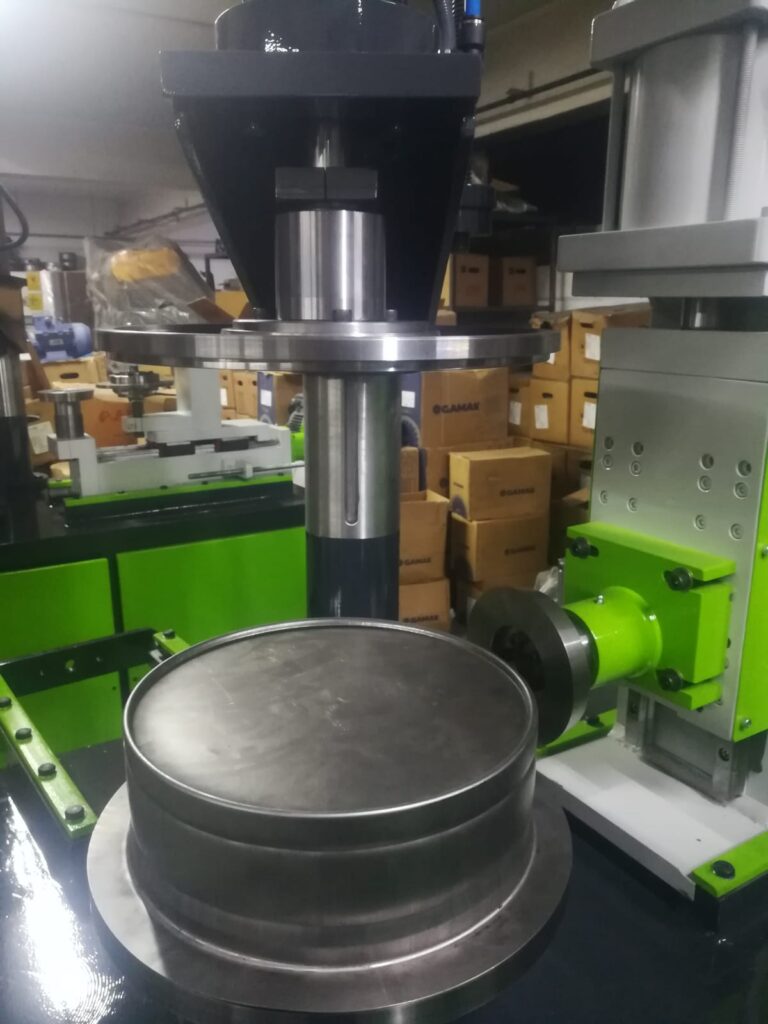
Cizallas Bordonadoras: Las máquinas de corte y bordó representan una solución versátil y eficiente para las industrias que trabajan con láminas metálicas y otros materiales similares. Este tipo de equipo combina dos funciones esenciales: el corte de materiales y el bordeado de sus extremos. El proceso de bordeado no solo garantiza un acabado estético, sino que también aumenta la resistencia y durabilidad de las piezas. Estas máquinas son utilizadas en una variedad de industrias, desde la automotriz hasta la construcción y la fabricación de electrodomésticos, donde la calidad y precisión en los acabados son esenciales.
Principios de funcionamiento
El funcionamiento de las máquinas de corte y bordó se basa en la integración de dos operaciones clave en un solo sistema. Por un lado, el proceso de corte se realiza mediante cuchillas afiladas que se desplazan a lo largo del material para separar la pieza deseada del resto de la lámina. Este corte puede ser recto o en formas específicas, dependiendo del tipo de máquina y sus configuraciones.
Después del corte, la máquina pasa al proceso de bordeado. Este se realiza generalmente con rodillos o herramientas especializadas que aplican presión en los bordes del material cortado. El bordeado puede tener diferentes formas según las especificaciones del diseño, incluyendo bordes planos, curvos o reforzados para aumentar la rigidez de la pieza. Este último proceso es crucial, ya que no solo mejora el aspecto de la pieza, sino que también elimina posibles aristas afiladas y minimiza el riesgo de deformaciones.
Tipos de máquinas de corte y bordó
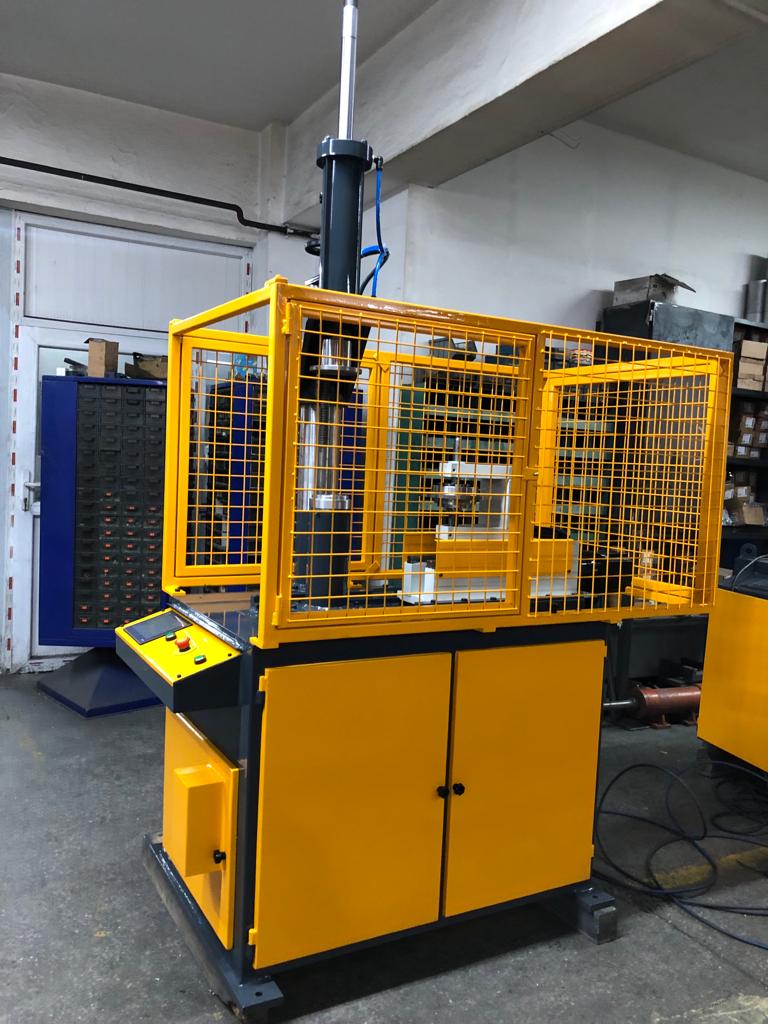
Existen varios tipos de máquinas de corte y bordó que varían en tamaño, capacidad y nivel de automatización. Entre las más comunes se incluyen:
- Máquinas manuales: Ideales para pequeñas producciones o talleres que requieren flexibilidad en los tipos de trabajos. Son manejadas directamente por el operario, lo que permite ajustes rápidos y precisos.
- Máquinas semiautomáticas: Estas máquinas requieren la intervención del operario para algunas operaciones, pero gran parte del proceso se automatiza, lo que aumenta la eficiencia.
- Máquinas automáticas: Equipos completamente automatizados que son utilizados en líneas de producción de gran volumen. Incorporan sistemas de alimentación automática de láminas y corte preciso mediante tecnología CNC (Control Numérico Computarizado).
- Máquinas con capacidad de procesamiento de múltiples materiales: Pueden manejar desde metales ligeros como el aluminio hasta materiales más gruesos y resistentes como el acero inoxidable.
Aplicaciones industriales
Las aplicaciones de las máquinas de corte y bordó son amplias y variadas. Algunas de las principales industrias que hacen uso de este tipo de tecnología incluyen:
- Industria automotriz: Se emplean para fabricar paneles de carrocería y otras piezas metálicas que requieren cortes precisos y bordes reforzados.
- Aeroespacial: Las piezas metálicas utilizadas en la construcción de aviones y componentes relacionados suelen requerir bordes precisos y acabados de alta calidad.
- Fabricación de electrodomésticos: Muchas partes de electrodomésticos, como las carcasas de lavadoras, secadoras y refrigeradores, se fabrican con máquinas de corte y bordó, lo que asegura bordes suaves y sin deformaciones.
- Construcción: En este sector, las máquinas se utilizan para la fabricación de paneles metálicos, vigas reforzadas y otros componentes estructurales que necesitan tanto corte como bordes precisos.
Ventajas de las máquinas de corte y bordó
El uso de máquinas de corte y bordó presenta numerosas ventajas en comparación con la realización de estos procesos por separado. Algunas de las principales ventajas son:
- Integración de procesos: Al combinar el corte y el bordeado en un solo paso, se reducen los tiempos de producción y se minimiza el uso de varios equipos.
- Ahorro de costos: Al realizar ambas operaciones en un solo equipo, las empresas pueden ahorrar en costos de mantenimiento y operación, además de reducir la necesidad de espacio en la planta.
- Mayor precisión: Estas máquinas permiten obtener acabados más precisos y uniformes en las piezas, lo que reduce el desperdicio de material y la necesidad de reprocesos.
- Versatilidad en materiales: Las máquinas de corte y bordó pueden trabajar con una amplia variedad de materiales, incluyendo acero, aluminio, cobre, entre otros, lo que las convierte en equipos altamente versátiles para diferentes tipos de producción.
- Mejora de la seguridad: Al suavizar los bordes de las piezas metálicas, se reduce el riesgo de accidentes laborales relacionados con bordes afilados.
Bordonadora Hidráulica
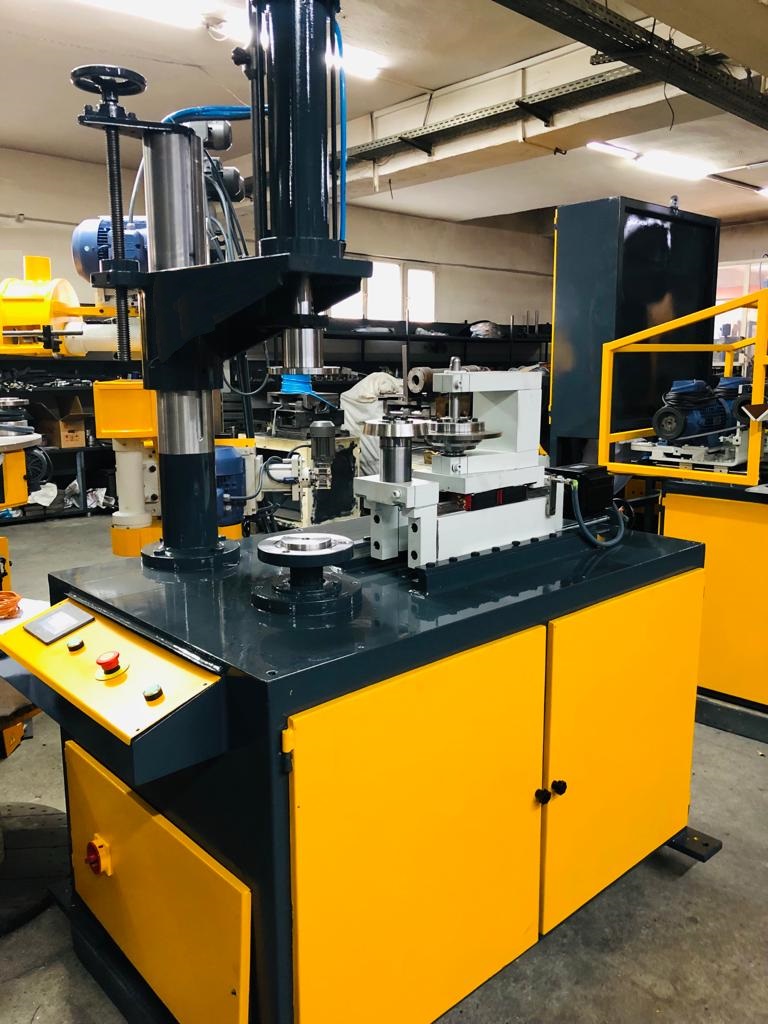
La bordonadora hidráulica es una máquina robusta y precisa que se utiliza para crear bordes o rebordes en chapas metálicas. Su principal característica es el uso de un sistema hidráulico para generar la fuerza necesaria para doblar o moldear el metal, permitiendo una mayor precisión y capacidad de manejo de materiales más gruesos o resistentes en comparación con bordonadoras manuales o mecánicas. Este tipo de equipo es común en sectores industriales donde se requiere un acabado reforzado y duradero, como en la fabricación de estructuras metálicas, electrodomésticos y automóviles.
Definición y funcionamiento
Las bordonadoras hidráulicas funcionan mediante la aplicación de presión hidráulica controlada que permite formar bordes en piezas de metal. El proceso se realiza de manera controlada y precisa, asegurando que el bordeado cumpla con las especificaciones técnicas del diseño. La presión hidráulica es proporcionada por un sistema de bombeo que impulsa el aceite hidráulico a través de cilindros, generando la fuerza suficiente para moldear el metal.
El operario ajusta los rodillos de la bordonadora según el grosor y tipo de material, así como el tipo de borde que se desea obtener. Una vez que la pieza de chapa metálica está en su posición, los rodillos aplican presión para crear un borde continuo a lo largo de la pieza, lo que añade resistencia y refuerza la integridad estructural del metal.
Componentes principales
Las bordonadoras hidráulicas están compuestas por varios elementos clave que aseguran su funcionamiento óptimo y su capacidad para manejar diferentes tipos de materiales y espesores. Algunos de estos componentes son:
- Sistema hidráulico: Es el núcleo de la máquina. Consiste en un motor hidráulico que acciona una bomba para generar la presión necesaria. El sistema incluye un depósito de aceite, válvulas de control de presión y cilindros hidráulicos que aplican la fuerza sobre los rodillos de la máquina.
- Rodillos de conformado: Son las herramientas que entran en contacto directo con la chapa metálica para moldear el borde. Están fabricados de materiales resistentes al desgaste y se ajustan de acuerdo con el diámetro y grosor de la chapa.
- Mesa de trabajo: Es la superficie sobre la que se posiciona la chapa metálica durante el proceso de bordeado. En algunos modelos, esta mesa puede incluir sistemas de sujeción para asegurar que la pieza no se desplace durante el proceso.
- Controladores: La presión aplicada y la velocidad del bordeado son controladas por un sistema de control que permite al operario ajustar los parámetros en función del tipo de material y el resultado deseado.
Características técnicas
Las bordonadoras hidráulicas ofrecen una serie de características técnicas que las hacen ideales para operaciones de bordeado en una variedad de entornos industriales:
- Fuerza hidráulica ajustable: La capacidad de ajustar la presión aplicada por los cilindros hidráulicos permite trabajar con una amplia gama de materiales, desde chapas delgadas de aluminio hasta acero de mayor grosor.
- Precisión en el conformado: Gracias a los rodillos ajustables y la fuerza hidráulica controlada, estas máquinas pueden crear bordes con tolerancias muy ajustadas, lo que resulta en productos de alta calidad y consistencia.
- Adaptabilidad a diferentes espesores y formas: La versatilidad de las bordonadoras hidráulicas les permite manejar tanto materiales planos como curvados, adaptándose a las necesidades de la producción.
- Control automático o manual: Algunas bordonadoras hidráulicas cuentan con sistemas de control numérico computarizado (CNC) que automatizan el proceso, lo que facilita la producción en masa y reduce el tiempo de inactividad. Otras máquinas permiten el ajuste manual, lo que las hace útiles para producciones personalizadas o de menor volumen.
Usos industriales
Las bordonadoras hidráulicas tienen una amplia gama de aplicaciones en varias industrias, especialmente en aquellas que requieren la fabricación de componentes metálicos con bordes reforzados. Algunos de los sectores que más se benefician del uso de estas máquinas incluyen:
- Fabricación de conductos: Se utilizan para formar bordes en conductos de ventilación, aire acondicionado y calefacción. Los bordes reforzados aumentan la durabilidad de los conductos y mejoran su resistencia al desgaste y la corrosión.
- Industria de electrodomésticos: En la producción de electrodomésticos como lavadoras, refrigeradores y estufas, las bordonadoras hidráulicas permiten crear bordes que refuerzan las estructuras de las carcasas y paneles metálicos.
- Fabricación de recipientes metálicos: Estas máquinas se emplean para fabricar recipientes y contenedores metálicos que requieren bordes reforzados para aumentar su resistencia estructural y su capacidad de soportar presión o peso.
- Sector automotriz: Se utilizan para la producción de paneles y componentes de automóviles que necesitan refuerzos en los bordes, como puertas, cofres y otros paneles estructurales.
Ventajas competitivas
Las bordonadoras hidráulicas ofrecen varias ventajas en comparación con otros tipos de bordonadoras, tales como las manuales o las mecánicas:
- Mayor precisión: El sistema hidráulico permite un control muy preciso sobre la presión aplicada, lo que resulta en bordes consistentes y de alta calidad en cada pieza, independientemente del grosor o tipo de metal.
- Capacidad de manejo de materiales más gruesos: A diferencia de las bordonadoras manuales o mecánicas, las versiones hidráulicas son capaces de manejar chapas metálicas más gruesas sin comprometer la calidad del borde o la eficiencia del proceso.
- Reducción de la fatiga del operario: Gracias a la automatización del sistema hidráulico, el esfuerzo físico requerido por el operario es mínimo, lo que aumenta la productividad y reduce el riesgo de errores.
- Versatilidad: Estas máquinas pueden ajustarse para trabajar con una variedad de metales y grosores, lo que las hace útiles para empresas que trabajan con diferentes tipos de materiales o productos.
- Durabilidad y menor mantenimiento: Las bordonadoras hidráulicas están diseñadas para soportar condiciones industriales exigentes, lo que les otorga una mayor durabilidad y reduce los tiempos de inactividad debido a reparaciones o mantenimiento.
Recortadora-Rebordeadora de Chapa Circular
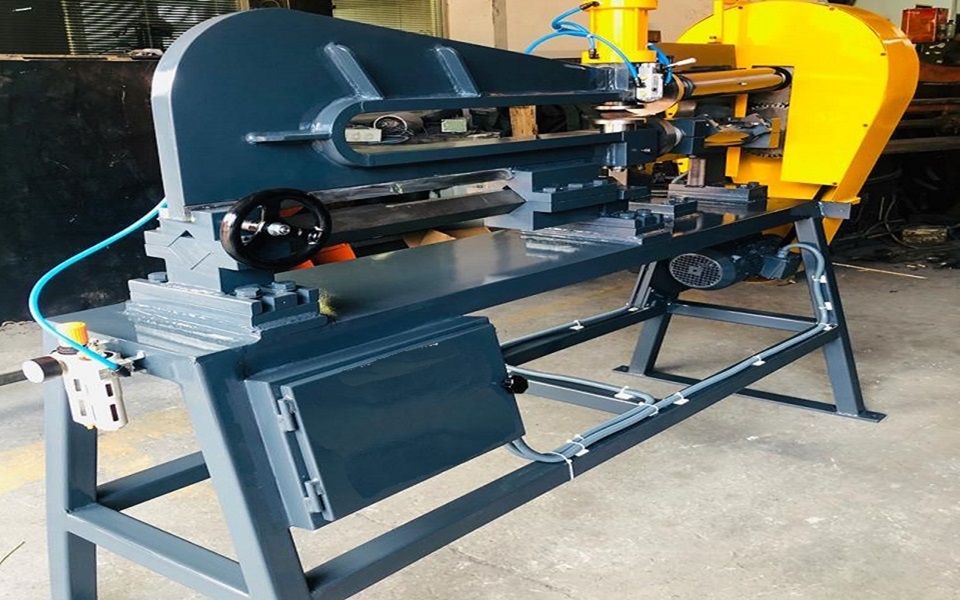
Las recortadoras-rebordeadoras de chapa circular son máquinas diseñadas específicamente para trabajar con piezas de chapa metálica de forma circular, cortando y perfilando sus bordes de manera precisa. Estas máquinas son esenciales en la fabricación de componentes circulares que requieren bordes uniformes y de alta calidad, como tapas metálicas, cubiertas de calderas y otras piezas redondas utilizadas en diferentes industrias. Su capacidad de combinar el recorte y el bordeado en un solo proceso las convierte en una opción eficiente para las líneas de producción que buscan maximizar la precisión y la productividad.
Descripción y propósito
El principal propósito de las recortadoras-rebordeadoras es realizar cortes circulares en chapas metálicas y, al mismo tiempo, aplicar un borde que refuerce y mejore el acabado de la pieza. Estas máquinas son ideales para producir piezas circulares perfectas, con bordes lisos y sin deformaciones, un aspecto crítico cuando se trabaja con componentes que deben ajustarse con precisión en ensamblajes o estructuras más grandes.
El funcionamiento de una recortadora-rebordeadora de chapa circular se basa en sujetar la pieza de chapa y hacer girar la herramienta de corte en torno al perímetro, eliminando el exceso de material de manera uniforme. Una vez realizado el corte, el proceso de bordeado comienza, perfilando el borde exterior de la chapa con herramientas específicas que aplican presión y moldean el metal para reforzarlo.
Mecanismos de operación
El proceso de operación de estas máquinas se basa en una combinación de cortes precisos y operaciones de rebordeado. Los componentes clave del mecanismo son:
- Sujeción de la chapa: El sistema de sujeción asegura la pieza circular en una posición fija mientras la máquina opera, permitiendo que el corte y el bordeado se realicen con precisión. Este mecanismo puede ajustarse para trabajar con chapas de diferentes tamaños y grosores.
- Cuchillas de corte: Las cuchillas afiladas y duraderas realizan el corte circular. La calidad y tipo de cuchilla pueden variar según el material que se esté trabajando, como acero, aluminio, cobre u otros metales.
- Rodillos de rebordeado: Después del corte, los rodillos se encargan de aplicar el borde a la chapa. Estos rodillos pueden configurarse para aplicar bordes simples o dobleces más complejos, dependiendo de los requerimientos del producto final.
El sistema de control, en muchos modelos de estas máquinas, es ajustable, lo que permite cambiar el diámetro de las chapas, la velocidad de corte y la presión aplicada durante el rebordeado. En máquinas más avanzadas, el proceso puede ser completamente automatizado mediante el uso de tecnología CNC, lo que garantiza una precisión extrema y permite la fabricación en masa.
Especificaciones técnicas
Las recortadoras-rebordeadoras de chapa circular varían en capacidad y características técnicas, lo que las hace adecuadas para diferentes tipos de industrias y aplicaciones. Algunas de las especificaciones más relevantes incluyen:
- Diámetro máximo y mínimo: Estas máquinas tienen la capacidad de manejar una amplia gama de diámetros de chapas circulares, desde piezas pequeñas hasta grandes discos metálicos utilizados en estructuras industriales.
- Materiales compatibles: Las cuchillas y rodillos están diseñados para trabajar con varios tipos de metales, incluidos el acero, aluminio, cobre y aleaciones especiales, lo que permite una gran versatilidad en su uso.
- Velocidad de operación: La velocidad de corte y rebordeado puede ajustarse en función de las necesidades de producción. En líneas de producción de gran volumen, las velocidades más altas permiten una mayor productividad sin comprometer la precisión.
- Automatización: Muchas recortadoras-rebordeadoras están equipadas con sistemas de control computarizado que permiten la programación de ciclos automáticos, asegurando una operación rápida y precisa sin intervención manual constante.
Industria y aplicaciones
Las recortadoras-rebordeadoras de chapa circular son ampliamente utilizadas en varias industrias que requieren componentes metálicos circulares. Algunas de las aplicaciones más comunes son:
- Fabricación de cubiertas metálicas: Estas máquinas son esenciales en la producción de tapas de calderas, válvulas y otros componentes que requieren bordes precisos para asegurar un ajuste perfecto en sistemas industriales. Los bordes reforzados proporcionan una mayor durabilidad y resistencia a la deformación bajo presión.
- Producción de tapas de contenedores: En la industria de contenedores y recipientes metálicos, las recortadoras-rebordeadoras son utilizadas para crear tapas con bordes que permitan un sellado adecuado y duradero. Esto es particularmente importante en recipientes que contienen líquidos o gases a presión.
- Componentes circulares en electrodomésticos: Los electrodomésticos como lavadoras, secadoras y ventiladores requieren piezas metálicas circulares que deben ajustarse de manera precisa en sus ensamblajes. Las recortadoras-rebordeadoras aseguran bordes suaves y consistentes en estos componentes.
- Industria automotriz y aeroespacial: En estos sectores, las piezas metálicas circulares, como discos y paneles, necesitan acabados de alta precisión para garantizar el rendimiento y la seguridad de los vehículos y aeronaves. Las máquinas de recorte y rebordeado permiten producir estos componentes con exactitud y eficiencia.
Beneficios para la industria
El uso de recortadoras-rebordeadoras de chapa circular presenta numerosos beneficios para las empresas que buscan aumentar la precisión y eficiencia en la fabricación de componentes circulares:
- Alta precisión: Estas máquinas ofrecen un nivel superior de precisión en el corte y rebordeado, lo que es fundamental en aplicaciones que requieren un ajuste perfecto y bordes suaves, como en sistemas de sellado y ensamblaje.
- Reducción de residuos: El proceso de corte circular controlado minimiza el desperdicio de material, optimizando el uso de la chapa metálica y reduciendo los costos de producción.
- Aumento en la productividad: Al combinar el recorte y el rebordeado en una sola operación, estas máquinas permiten que las líneas de producción funcionen más rápido y con menos interrupciones. Esto es especialmente útil en industrias donde la fabricación en masa es una prioridad.
- Durabilidad y mantenimiento sencillo: Las recortadoras-rebordeadoras están diseñadas para soportar un uso intensivo en entornos industriales exigentes, con componentes que requieren un mantenimiento mínimo, lo que reduce los tiempos de inactividad y los costos operativos.
Automatización en el proceso de rebordeado
Una de las tendencias recientes en el uso de recortadoras-rebordeadoras es la integración de sistemas automatizados que permiten controlar cada fase del proceso con precisión mediante software especializado. Estos sistemas CNC permiten la programación de parámetros específicos para cada pieza, lo que aumenta la flexibilidad de producción y reduce los tiempos de configuración entre lotes. Además, la automatización facilita el trabajo con chapas de mayor tamaño o espesor, que requieren una mayor precisión y control.
Cizallas Bordonadoras
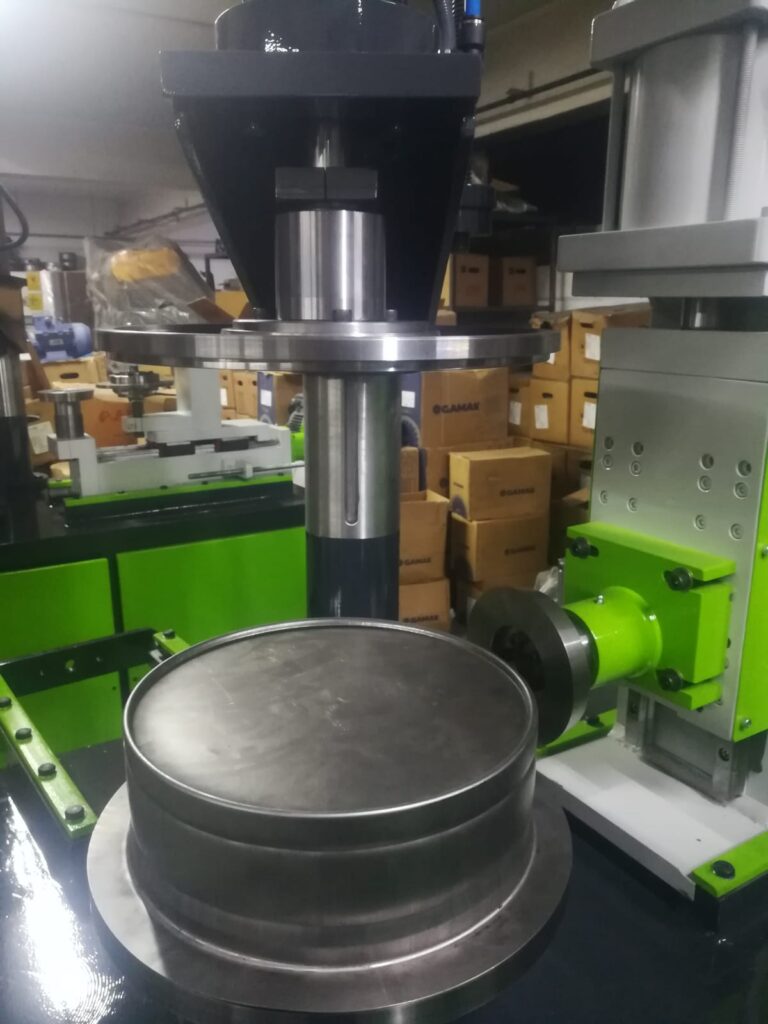
Las cizallas bordonadoras son máquinas industriales diseñadas para cortar y formar bordes o rebordes en chapas metálicas, combinando dos procesos esenciales en una sola operación. Estas máquinas son fundamentales en la producción de piezas metálicas de alta precisión, ya que permiten realizar cortes limpios y, al mismo tiempo, reforzar los bordes de las piezas mediante el proceso de bordonado. Su versatilidad y eficiencia las convierten en una opción popular en sectores industriales que requieren productos metálicos con acabados resistentes y duraderos, como la construcción, la automoción y la fabricación de electrodomésticos.
Definición y funciones
Las cizallas bordonadoras realizan dos funciones principales en el trabajo con chapas metálicas:
- Corte: Utilizan cuchillas afiladas para realizar cortes precisos y limpios en la chapa. Dependiendo del tipo de máquina, los cortes pueden ser rectos o curvados, lo que ofrece flexibilidad para fabricar una amplia gama de piezas.
- Bordeado: Después de cortar la pieza, los bordes son formados mediante rodillos o matrices que aplican presión para doblar y moldear los bordes. Este proceso aumenta la resistencia del metal, lo que es especialmente útil en piezas que deben soportar cargas o presiones significativas.
Estas máquinas están diseñadas para manejar diferentes tipos de metales, como acero, aluminio, cobre y sus aleaciones, lo que las convierte en una solución ideal para procesos de fabricación que involucran materiales de diferentes grosores y propiedades.
Cómo funcionan las cizallas bordonadoras
El proceso de operación de las cizallas bordonadoras se realiza en dos etapas. En la primera etapa, la chapa metálica se corta utilizando cuchillas controladas que separan la pieza deseada del resto del material. Este corte puede ser realizado de manera manual o automatizada, dependiendo del nivel de tecnología de la máquina.
En la segunda etapa, el borde recién cortado es doblado o perfilado para reforzar su estructura. Esto se hace mediante rodillos de bordeado, que aplican presión de forma controlada a lo largo de los bordes de la chapa. Los rodillos pueden ajustarse para formar diferentes tipos de bordes, desde simples dobleces hasta perfiles más complejos, dependiendo de las necesidades específicas de la pieza final.
Variantes de cizallas bordonadoras
Existen varios tipos de cizallas bordonadoras disponibles en el mercado, cada una diseñada para satisfacer diferentes necesidades industriales:
- Cizallas manuales: Son máquinas más simples y compactas, ideales para talleres pequeños o para trabajos que requieren flexibilidad y cambios frecuentes de configuración. Estas cizallas son operadas manualmente por el trabajador, lo que permite una mayor precisión en pequeños lotes de producción.
- Cizallas automáticas: Estas máquinas están diseñadas para líneas de producción de gran volumen. Cuentan con sistemas automáticos de alimentación de chapas y corte programado, lo que reduce la intervención del operario y aumenta la velocidad de producción.
- Cizallas CNC (Control Numérico Computarizado): Utilizan tecnología CNC para realizar cortes y bordeados con precisión extrema. Las cizallas CNC son ideales para producciones en masa que requieren una alta repetibilidad y precisión en cada pieza, ya que permiten programar cortes y rebordes con parámetros exactos.
Áreas de aplicación
Las cizallas bordonadoras se utilizan en una variedad de industrias que requieren piezas metálicas con bordes reforzados y acabados precisos. Algunas de las aplicaciones más comunes son:
- Industria automotriz: Las cizallas bordonadoras son fundamentales para la producción de paneles de carrocería, puertas y otras piezas que requieren cortes precisos y bordes reforzados para garantizar la seguridad y la durabilidad del vehículo.
- Construcción: Se emplean en la fabricación de piezas estructurales metálicas, como vigas, paneles y conductos. El proceso de bordeado refuerza los bordes de estas piezas, lo que aumenta su capacidad de carga y resistencia a la deformación.
- Electrodomésticos: En la fabricación de electrodomésticos como lavadoras, secadoras y refrigeradores, las cizallas bordonadoras se utilizan para crear paneles metálicos con bordes suaves que mejoran tanto la seguridad como la apariencia estética de los productos.
- Fabricación de envases metálicos: Las cizallas bordonadoras son esenciales en la producción de contenedores metálicos, ya que permiten cortar y bordear las láminas que se utilizarán en la fabricación de tapas y cuerpos de los recipientes.
Características principales y ventajas
El uso de cizallas bordonadoras ofrece una serie de ventajas en comparación con la utilización de máquinas independientes para cortar y bordear. Estas son algunas de sus principales características y beneficios:
- Cortes precisos sin deformar el material: Las cizallas bordonadoras están diseñadas para realizar cortes limpios que no alteran la forma o integridad del material. Esto es fundamental para piezas que deben mantener una alta precisión dimensional.
- Versatilidad para trabajar con diferentes tipos y grosores de chapa: Estas máquinas son capaces de manejar una amplia variedad de materiales, desde chapas delgadas de aluminio hasta acero de mayor grosor, lo que las hace ideales para diversas aplicaciones industriales.
- Integración de procesos: Al combinar el corte y el bordeado en una sola operación, las cizallas bordonadoras reducen el tiempo de producción y eliminan la necesidad de transferir las piezas entre diferentes máquinas. Esto mejora la eficiencia y disminuye los costos de producción.
- Ahorro de tiempo y costos: Al realizar dos procesos en un solo equipo, las cizallas bordonadoras no solo reducen el tiempo de producción, sino que también permiten un uso más eficiente de los recursos de la planta, como el espacio y la energía.
Automatización y control de calidad
Una de las características más importantes de las cizallas bordonadoras modernas es la incorporación de sistemas automatizados y tecnología CNC. Esto permite a los operadores controlar cada aspecto del proceso con precisión, desde el corte hasta el bordeado. El control automático garantiza una alta repetibilidad, lo que es esencial en líneas de producción de gran volumen.
Además, las máquinas automatizadas están equipadas con sistemas de control de calidad que pueden detectar cualquier variación en las dimensiones de las piezas o defectos en el borde, lo que asegura que cada pieza cumpla con los estándares de calidad requeridos. Esto no solo mejora la consistencia del producto, sino que también reduce los costos asociados con el desperdicio de material o la reelaboración de piezas defectuosas.
Mantenimiento y durabilidad
Las cizallas bordonadoras están diseñadas para soportar condiciones de trabajo intensivas y para ofrecer un rendimiento confiable a largo plazo. Los componentes críticos, como las cuchillas de corte y los rodillos de bordeado, están fabricados con materiales altamente resistentes al desgaste, lo que prolonga su vida útil y reduce la frecuencia de reemplazo.
El mantenimiento regular es esencial para garantizar el funcionamiento óptimo de estas máquinas. Sin embargo, las cizallas bordonadoras modernas están diseñadas para facilitar las tareas de mantenimiento, con sistemas de lubricación automáticos y accesibilidad a las partes críticas. Esto minimiza el tiempo de inactividad y permite mantener la producción en funcionamiento continuo.
Las prensas de cuatro columnas son máquinas industriales de gran relevancia en los procesos de conformado de metales. Este tipo de prensas destaca por su estructura robusta y la distribución equilibrada de la fuerza aplicada durante el prensado. Las prensas de cuatro columnas ofrecen una estabilidad excepcional, lo que las convierte en una opción confiable para tareas que requieren alta precisión y fuerza controlada, como el embutido, la estampación y el corte. Estas máquinas son utilizadas en múltiples industrias, incluyendo la automotriz, la aeroespacial, la fabricación de electrodomésticos y otros sectores industriales donde se requiere una manipulación exacta del metal.
Diseño y Funcionamiento
El diseño de las prensas de cuatro columnas se basa en una estructura compuesta por un marco rígido con cuatro columnas que conectan la base con la parte superior de la prensa. Este diseño distribuye uniformemente las cargas aplicadas durante el prensado, minimizando el desgaste y la deformación de las piezas. Las columnas ofrecen un soporte simétrico, lo que permite que el cabezal de la prensa se mueva de manera estable y uniforme, garantizando un prensado de alta calidad. Además, las prensas de cuatro columnas suelen incorporar un sistema hidráulico que controla el movimiento del pistón y la aplicación de la fuerza.
El sistema hidráulico es uno de los elementos más importantes de las prensas de cuatro columnas, ya que permite un control preciso de la fuerza y del desplazamiento. Mediante el uso de aceite a alta presión, se acciona el pistón, que se desplaza verticalmente dentro de la estructura de la prensa. La precisión en el control del flujo de aceite y la presión aplicada garantiza un proceso controlado y seguro, lo que es fundamental para la producción de piezas metálicas de alta calidad.
Ventajas de las Prensas de Cuatro Columnas
Uno de los principales beneficios de las prensas de cuatro columnas es su capacidad para manejar grandes cargas con una mínima deformación. A continuación, se detallan las principales ventajas de este tipo de prensas:
- Distribución Uniforme de la Fuerza: El diseño de cuatro columnas asegura que la fuerza aplicada se distribuya de manera homogénea sobre toda la superficie de trabajo, lo que reduce el riesgo de deformaciones indeseadas y mejora la calidad del producto final.
- Estabilidad Estructural: Gracias a su diseño robusto, las prensas de cuatro columnas ofrecen una gran estabilidad durante el proceso de prensado, lo que es esencial para operaciones que requieren alta precisión, como el embutido profundo y el corte.
- Versatilidad en Aplicaciones: Estas prensas son adecuadas para una amplia gama de procesos industriales, desde el estampado de metales hasta la fabricación de componentes complejos para sectores como el automotriz, aeroespacial y de electrodomésticos.
- Control Hidráulico Preciso: El sistema hidráulico integrado en estas prensas permite un control preciso de la presión, velocidad y desplazamiento del pistón, lo que se traduce en una mayor flexibilidad para adaptarse a diferentes tipos de procesos y materiales.
- Mayor Durabilidad: La distribución equilibrada de las cargas y la robustez de la estructura de las prensas de cuatro columnas contribuyen a una mayor vida útil de la máquina, reduciendo los costos de mantenimiento y garantizando una operación eficiente a largo plazo.
Aplicaciones Industriales
Las prensas de cuatro columnas son utilizadas en una variedad de industrias debido a su capacidad para manejar procesos complejos de conformado de metales. Algunas de las aplicaciones más comunes incluyen:
- Industria Automotriz: En la fabricación de componentes automotrices, como paneles de carrocería, chasis y piezas estructurales, las prensas de cuatro columnas son esenciales para garantizar un prensado preciso y uniforme.
- Industria Aeroespacial: La producción de componentes aeronáuticos requiere una alta precisión y control en el proceso de conformado de metales. Las prensas de cuatro columnas son utilizadas para la fabricación de piezas complejas, como fuselajes y componentes estructurales.
- Fabricación de Electrodomésticos: En la industria de los electrodomésticos, las prensas de cuatro columnas se emplean para la producción de carcasas, marcos y otros componentes metálicos utilizados en productos como refrigeradores, lavadoras y estufas.
- Industria de Envases Metálicos: Las prensas de cuatro columnas también son fundamentales en la fabricación de envases metálicos, como latas y contenedores, que requieren una conformación precisa y controlada.
Mantenimiento y Seguridad
El mantenimiento adecuado de las prensas de cuatro columnas es crucial para garantizar su funcionamiento continuo y evitar tiempos de inactividad costosos. Algunas de las mejores prácticas para el mantenimiento incluyen:
- Inspección Regular de los Sistemas Hidráulicos: Es fundamental revisar periódicamente los niveles de aceite, la presión del sistema y la integridad de los componentes hidráulicos para garantizar un funcionamiento seguro y eficiente.
- Lubricación de las Piezas Móviles: Las columnas y otras partes móviles de la prensa deben ser lubricadas de manera regular para reducir el desgaste y evitar la fricción excesiva.
- Revisión de los Componentes Estructurales: Dado que estas prensas manejan grandes cargas, es importante verificar la integridad estructural de las columnas y el marco para asegurarse de que no haya grietas o deformaciones que puedan comprometer la seguridad del equipo.
- Capacitación del Personal: El personal encargado de operar las prensas de cuatro columnas debe recibir capacitación adecuada en el manejo seguro de la máquina, así como en las pautas de mantenimiento y resolución de problemas.
En términos de seguridad, las prensas de cuatro columnas suelen estar equipadas con dispositivos de seguridad como sistemas de bloqueo hidráulico, barreras de protección y controles de emergencia para prevenir accidentes y garantizar un entorno de trabajo seguro.
Innovaciones Tecnológicas en Prensas de Cuatro Columnas
En los últimos años, la tecnología de las prensas de cuatro columnas ha evolucionado significativamente, incorporando avances en automatización, control numérico y monitoreo en tiempo real. Algunas de las innovaciones más destacadas incluyen:
- Automatización de Procesos: La integración de sistemas automatizados permite que las prensas de cuatro columnas realicen operaciones de prensado de manera autónoma, mejorando la eficiencia y reduciendo el tiempo de producción.
- Control Numérico Computarizado (CNC): El uso de CNC en las prensas de cuatro columnas permite un control extremadamente preciso de los parámetros del proceso, como la velocidad, presión y desplazamiento del pistón. Esto es especialmente útil en la fabricación de piezas de alta complejidad.
- Monitoreo en Tiempo Real: Los sistemas de monitoreo avanzados permiten a los operadores supervisar el estado de la prensa en tiempo real, detectando posibles fallos o problemas antes de que se conviertan en incidentes graves. Esto mejora la seguridad y la productividad al reducir los tiempos de inactividad.
Conclusión
Las prensas de cuatro columnas son máquinas esenciales en la industria moderna, proporcionando la fuerza, precisión y estabilidad necesarias para una amplia gama de aplicaciones de conformado de metales. Su diseño robusto y la capacidad de controlar de manera precisa la fuerza aplicada las convierten en una opción ideal para industrias que demandan altos niveles de calidad y durabilidad en sus productos. A medida que la tecnología continúa avanzando, las prensas de cuatro columnas seguirán siendo una herramienta clave en la fabricación industrial, ayudando a optimizar los procesos y mejorar la eficiencia en la producción.
Prensas de Bastidor en H
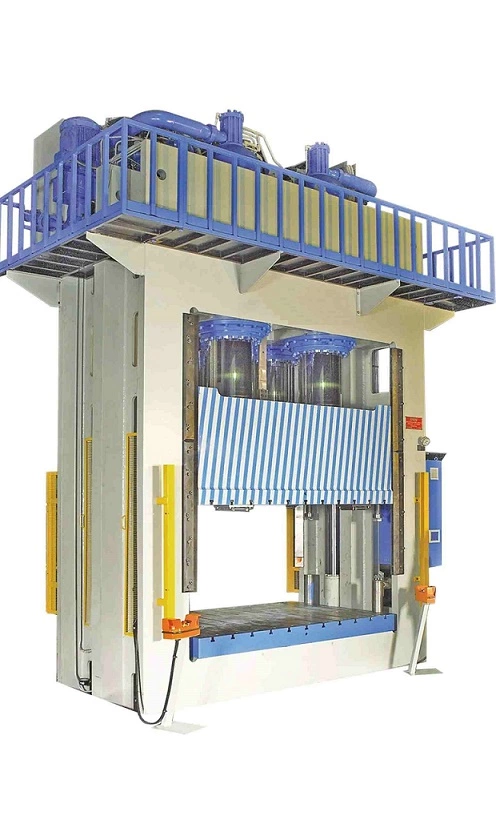
Las prensas de bastidor en H son máquinas esenciales en la industria del conformado de metales. Se caracterizan por tener un marco rígido en forma de “H”, lo que les otorga una estabilidad estructural superior y permite realizar operaciones de prensado con una fuerza controlada y precisa. Este tipo de prensas es altamente valorado en aplicaciones que requieren un alto nivel de precisión, como el estampado, embutido, corte y doblado de metales. Su diseño único no solo garantiza la distribución uniforme de la presión, sino que también facilita el acceso al área de trabajo desde todos los ángulos, lo que mejora la eficiencia operativa y la flexibilidad.
Diseño y Estructura de las Prensas de Bastidor en H
El diseño de las prensas de bastidor en H se distingue por su simplicidad y eficiencia. La estructura está compuesta por dos montantes verticales que forman las patas del marco en H, y una barra horizontal que conecta estos montantes, proporcionando un soporte rígido y equilibrado. Esta configuración permite que la prensa maneje grandes cargas sin comprometer la precisión o la estabilidad, características que son fundamentales en procesos de conformado de metales.
En las prensas de bastidor en H, la fuerza se aplica verticalmente, lo que reduce las tensiones no deseadas en la estructura de la máquina. Gracias a esta alineación, se puede garantizar un ciclo de trabajo más largo y con menos desgaste. Además, estas prensas suelen estar equipadas con un sistema hidráulico que permite el control preciso de la fuerza de prensado, la velocidad y el desplazamiento del pistón, lo que es crucial para adaptarse a diferentes tipos de operaciones.
Ventajas de las Prensas de Bastidor en H
- Estructura Robusta y Duradera: La rigidez estructural del diseño en H ofrece una alta resistencia a la flexión y la deformación, lo que permite que la prensa soporte grandes cargas sin comprometer su precisión ni su vida útil. Esta característica es especialmente útil en aplicaciones de prensado de alta intensidad y en procesos industriales que requieren una operación continua.
- Acceso Fácil al Área de Trabajo: Una de las ventajas más notables de las prensas de bastidor en H es su facilidad de acceso al área de trabajo. Gracias a la estructura abierta, los operadores pueden acceder a la pieza de trabajo desde tres lados, lo que facilita el ajuste de herramientas y la manipulación de materiales. Esto no solo mejora la eficiencia, sino que también permite una mayor versatilidad en términos de aplicaciones y configuraciones.
- Distribución Uniforme de la Fuerza: El diseño en H asegura una distribución equilibrada de las fuerzas durante el ciclo de prensado, lo que minimiza el riesgo de deformaciones no deseadas en las piezas de trabajo. Esta característica es crucial en aplicaciones que requieren una alta precisión, como el estampado y el embutido de piezas complejas.
- Versatilidad en Aplicaciones: Las prensas de bastidor en H son extremadamente versátiles y pueden ser utilizadas en una variedad de procesos industriales, incluyendo el conformado de metales, el doblado, el corte y el estampado. Esta versatilidad las convierte en una solución ideal para empresas que buscan maquinaria capaz de manejar diferentes tipos de tareas sin comprometer la calidad ni la eficiencia.
- Fuerza de Prensado Ajustable: Gracias al sistema hidráulico incorporado, las prensas de bastidor en H permiten ajustar la fuerza de prensado con precisión, lo que es esencial para adaptarse a diferentes tipos de materiales y procesos. Esto las convierte en una opción ideal para operaciones que requieren diferentes niveles de presión, como el embutido profundo y el corte de metales gruesos.
Aplicaciones de las Prensas de Bastidor en H
Las prensas de bastidor en H son ampliamente utilizadas en una variedad de industrias, gracias a su robustez y versatilidad. Algunas de las aplicaciones más comunes incluyen:
- Industria Automotriz: Las prensas de bastidor en H son esenciales en la fabricación de componentes automotrices, como paneles de carrocería, chasis y otras piezas estructurales. Gracias a su capacidad para manejar grandes cargas y ofrecer un prensado preciso, estas prensas son ideales para producir piezas de alta calidad y resistencia.
- Industria Aeroespacial: En la fabricación de componentes para la industria aeroespacial, donde la precisión y la resistencia son fundamentales, las prensas de bastidor en H juegan un papel crucial. Son utilizadas para conformar piezas complejas y ligeras que requieren una alta precisión en el proceso de estampado y embutido.
- Fabricación de Electrodomésticos: La industria de electrodomésticos también se beneficia del uso de prensas de bastidor en H para la fabricación de carcasas metálicas y otros componentes estructurales. Estas prensas permiten una producción eficiente y precisa de piezas que requieren una alta resistencia y durabilidad.
- Fabricación de Maquinaria Pesada: Las prensas de bastidor en H son utilizadas en la producción de piezas para maquinaria pesada, como excavadoras, tractores y otros equipos industriales. Su capacidad para manejar metales de gran espesor las convierte en una opción ideal para este tipo de aplicaciones.
Mantenimiento y Operación Segura
El mantenimiento adecuado de las prensas de bastidor en H es fundamental para garantizar su rendimiento a largo plazo y evitar paradas no planificadas. A continuación, se describen algunas de las mejores prácticas para el mantenimiento de estas prensas:
- Revisión Regular del Sistema Hidráulico: Dado que las prensas de bastidor en H dependen de un sistema hidráulico para controlar la fuerza de prensado, es crucial revisar periódicamente los niveles de aceite y la presión del sistema. Cualquier fuga o anomalía en el sistema hidráulico debe ser atendida de inmediato para evitar daños mayores.
- Inspección de los Componentes Estructurales: Los operadores deben inspeccionar regularmente la estructura de la prensa, incluyendo las columnas y las conexiones, para detectar cualquier signo de desgaste o deformación. Esto es especialmente importante en aplicaciones que involucran grandes cargas, ya que cualquier debilidad en la estructura podría comprometer la seguridad y el rendimiento de la máquina.
- Lubricación de Piezas Móviles: La lubricación adecuada de las piezas móviles, como el pistón y las guías, es esencial para reducir el desgaste y garantizar un funcionamiento suave y eficiente. Un programa de lubricación regular ayudará a prolongar la vida útil de la prensa y a minimizar los costos de mantenimiento.
- Capacitación del Personal: El personal que opera las prensas de bastidor en H debe recibir capacitación adecuada sobre el uso seguro y eficiente de la máquina. Esto incluye la comprensión de los controles hidráulicos, las configuraciones de seguridad y las pautas de mantenimiento.
Innovaciones Tecnológicas en Prensas de Bastidor en H
En los últimos años, las prensas de bastidor en H han experimentado importantes avances tecnológicos que han mejorado su rendimiento y eficiencia. Algunas de las innovaciones más destacadas incluyen:
- Automatización: La integración de sistemas automatizados en las prensas de bastidor en H ha permitido aumentar la productividad y reducir la necesidad de intervención humana en el proceso de prensado. Los sistemas de control automático pueden ajustar los parámetros de prensado en tiempo real, mejorando la precisión y la consistencia de las piezas producidas.
- Control Numérico Computarizado (CNC): El uso de CNC en las prensas de bastidor en H permite un control extremadamente preciso de los parámetros del proceso, como la velocidad, la fuerza y el desplazamiento del pistón. Esto es especialmente útil en la fabricación de piezas complejas que requieren un alto grado de precisión.
- Monitoreo en Tiempo Real: Las prensas de bastidor en H modernas están equipadas con sistemas de monitoreo en tiempo real que permiten a los operadores supervisar el estado de la máquina y detectar posibles fallos antes de que se conviertan en problemas graves. Esto no solo mejora la seguridad, sino que también ayuda a optimizar el mantenimiento y reducir los tiempos de inactividad.
Consideraciones Finales
Las prensas de bastidor en H son una opción confiable y eficiente para una amplia gama de aplicaciones industriales. Su diseño robusto y su capacidad para manejar grandes cargas las convierten en una herramienta indispensable en industrias como la automotriz, aeroespacial y de fabricación de maquinaria pesada. Con el mantenimiento adecuado y el uso de tecnologías avanzadas, estas prensas pueden ofrecer un rendimiento excepcional a largo plazo, ayudando a mejorar la productividad y la calidad de los productos fabricados.
Prensas Horizontales
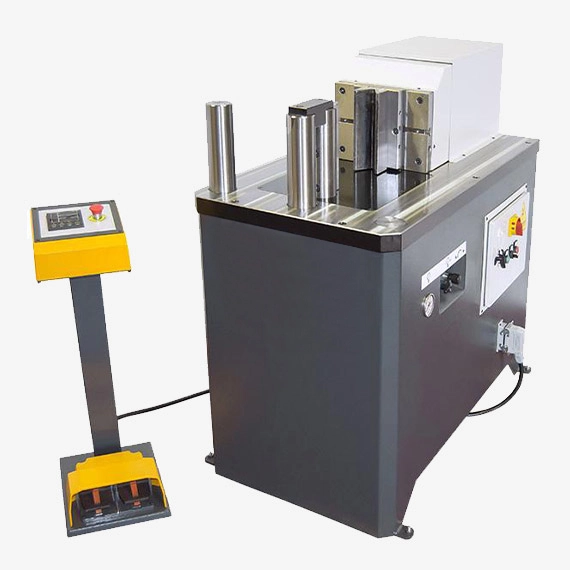
Las prensas horizontales son una variante especializada dentro del amplio espectro de máquinas de prensado utilizadas en la industria del conformado de metales. A diferencia de las prensas tradicionales que aplican la fuerza en dirección vertical, las prensas horizontales están diseñadas para ejercer la presión de manera horizontal. Este tipo de prensas es especialmente útil para aplicaciones de embutición, doblado, extrusión, corte y otras tareas que requieren una presión dirigida horizontalmente en lugar de verticalmente.
Las prensas horizontales son muy utilizadas en industrias como la automotriz, la fabricación de tuberías, la industria de electrodomésticos y otros sectores donde se requiere un control preciso de la presión en el eje horizontal. Debido a su diseño especializado, estas máquinas permiten procesar piezas largas y de gran tamaño que no podrían ser manejadas con facilidad en una prensa vertical tradicional.
Características de las Prensas Horizontales
El diseño de las prensas horizontales se basa en una estructura resistente que garantiza la aplicación de fuerza a lo largo de un eje horizontal. Esta disposición permite a las prensas horizontales procesar materiales de gran longitud, como barras, tubos y perfiles, de manera eficiente y con una gran precisión. A continuación, se detallan algunas de las principales características de estas prensas:
- Dirección de la Fuerza: La principal diferencia entre las prensas horizontales y las prensas convencionales es la dirección en la que se aplica la fuerza. En lugar de ejercer la presión hacia abajo, como lo haría una prensa vertical, las prensas horizontales aplican la fuerza de manera lateral. Esto facilita el trabajo con piezas largas y estrechas.
- Adaptabilidad a Procesos Especializados: Las prensas horizontales están diseñadas para aplicaciones específicas, como el doblado de tubos, la extrusión de perfiles metálicos y el corte de barras. Su diseño especializado les permite manejar procesos que serían complicados o ineficientes con una prensa vertical.
- Precisión en el Control de la Fuerza: Al igual que muchas prensas hidráulicas, las prensas horizontales están equipadas con sistemas de control hidráulico que permiten ajustar con precisión la cantidad de fuerza aplicada. Esto es fundamental para procesos que requieren un alto nivel de precisión, como el embutido y la extrusión.
- Versatilidad en Aplicaciones: Aunque las prensas horizontales se utilizan comúnmente en aplicaciones especializadas, son extremadamente versátiles y pueden adaptarse a una amplia gama de procesos industriales. Esto incluye el conformado de metales, el corte, la perforación y otras tareas que requieren una aplicación de fuerza en el eje horizontal.
Tipos de Prensas Horizontales
Existen varios tipos de prensas horizontales, cada una diseñada para cumplir con necesidades específicas dentro del proceso de manufactura. Los tipos más comunes incluyen:
- Prensas Horizontales Hidráulicas: Estas prensas funcionan mediante un sistema hidráulico que proporciona la fuerza necesaria para el prensado. Las prensas horizontales hidráulicas son populares debido a su capacidad para aplicar grandes cantidades de fuerza con precisión controlada. Se utilizan frecuentemente en procesos de doblado y corte de metales.
- Prensas Horizontales de Extrusión: Las prensas horizontales de extrusión están diseñadas específicamente para el proceso de extrusión de metales, en el que el material se empuja a través de una matriz para formar un perfil continuo. Este tipo de prensa es común en la fabricación de piezas largas y delgadas, como tuberías y perfiles metálicos.
- Prensas Horizontales de Doblado: Utilizadas en procesos de doblado de tubos y perfiles, las prensas horizontales de doblado aplican fuerza lateral para dar forma a los materiales sin comprometer su integridad estructural. Estas prensas son esenciales en la producción de componentes para la industria automotriz y de construcción.
- Prensas Horizontales de Corte: Estas prensas están diseñadas para cortar materiales largos, como barras y tubos, mediante la aplicación de fuerza en el eje horizontal. Son ampliamente utilizadas en la fabricación de componentes metálicos y plásticos.
Ventajas de las Prensas Horizontales
Las prensas horizontales ofrecen una serie de ventajas que las hacen ideales para aplicaciones industriales específicas. Algunas de las ventajas más destacadas incluyen:
- Capacidad para Procesar Piezas Largas: Una de las principales ventajas de las prensas horizontales es su capacidad para manejar piezas largas que serían difíciles o imposibles de procesar con una prensa vertical. Esto incluye materiales como barras, tubos y perfiles de metal o plástico.
- Distribución Equilibrada de la Fuerza: El diseño horizontal de estas prensas permite una distribución uniforme de la fuerza a lo largo de la pieza de trabajo, lo que minimiza las deformaciones y garantiza un acabado de alta calidad. Esta característica es particularmente útil en procesos de extrusión y doblado.
- Mayor Precisión en Aplicaciones Específicas: Las prensas horizontales están diseñadas para proporcionar un alto grado de precisión en procesos específicos, como el embutido y la extrusión. Esto las convierte en una herramienta invaluable para industrias que requieren un control exacto sobre el proceso de conformado.
- Versatilidad en la Configuración del Proceso: Las prensas horizontales pueden ser adaptadas a una amplia variedad de configuraciones de trabajo, lo que las hace extremadamente versátiles. Pueden ser utilizadas para doblar, cortar, embutir, y realizar otras tareas en diferentes tipos de materiales, desde metales hasta plásticos.
Aplicaciones Industriales de las Prensas Horizontales
Las prensas horizontales se utilizan en una amplia variedad de industrias debido a su capacidad para manejar piezas largas y su precisión en procesos especializados. Algunas de las aplicaciones más comunes incluyen:
- Industria Automotriz: En la fabricación de piezas automotrices, como ejes, marcos y componentes estructurales, las prensas horizontales son indispensables. Su capacidad para procesar piezas largas y su precisión en el doblado y corte de metales las convierten en una herramienta crucial en este sector.
- Fabricación de Tuberías: La industria de fabricación de tuberías y perfiles metálicos utiliza ampliamente prensas horizontales para conformar y cortar tubos de diferentes diámetros y grosores. Este tipo de prensa permite un procesamiento rápido y eficiente de materiales que requieren una conformación específica.
- Industria de la Construcción: Las prensas horizontales son utilizadas en la producción de componentes estructurales para la industria de la construcción, como vigas y perfiles de acero. Su capacidad para manejar piezas largas y aplicar fuerzas uniformes las convierte en una opción ideal para este tipo de aplicaciones.
- Fabricación de Electrodomésticos: En la producción de electrodomésticos, las prensas horizontales se utilizan para fabricar piezas largas, como conductos y marcos metálicos, que requieren una precisión y resistencia específicas.
Mantenimiento y Seguridad
El mantenimiento adecuado de las prensas horizontales es crucial para garantizar un funcionamiento eficiente y seguro. Algunas de las prácticas más importantes incluyen:
- Revisión Periódica del Sistema Hidráulico: Dado que muchas prensas horizontales dependen de sistemas hidráulicos, es esencial revisar periódicamente los niveles de aceite y la presión del sistema. Cualquier fuga o fallo en el sistema hidráulico debe ser reparado inmediatamente para evitar daños a la máquina.
- Lubricación de las Piezas Móviles: Al igual que con otras máquinas de prensado, es importante lubricar las piezas móviles de la prensa horizontal para reducir el desgaste y garantizar un funcionamiento suave. Esto incluye la lubricación del pistón, las guías y otras partes móviles.
- Inspección de Componentes Estructurales: Las piezas estructurales de la prensa, como el marco y las guías, deben ser inspeccionadas regularmente para detectar signos de desgaste o daño. Cualquier anomalía debe ser atendida de inmediato para evitar fallos en la máquina.
- Capacitación del Personal: El personal encargado de operar las prensas horizontales debe recibir capacitación adecuada para garantizar un manejo seguro y eficiente de la máquina. Esto incluye el conocimiento de los controles hidráulicos, las pautas de seguridad y los procedimientos de mantenimiento.
Innovaciones Tecnológicas en Prensas Horizontales
Las prensas horizontales han evolucionado significativamente con la incorporación de nuevas tecnologías que mejoran su precisión y eficiencia. Algunas de las innovaciones más importantes incluyen:
- Automatización: Las prensas horizontales modernas están cada vez más automatizadas, lo que permite un mayor control sobre el proceso de prensado y reduce la necesidad de intervención humana. La automatización mejora la productividad y reduce los errores humanos.
- Control Numérico Computarizado (CNC): La integración de sistemas CNC en las prensas horizontales ha permitido un control extremadamente preciso sobre los parámetros de operación, como la fuerza y el desplazamiento. Esto es especialmente útil en procesos que requieren alta precisión, como la extrusión y el embutido.
- Monitoreo en Tiempo Real: Los sistemas de monitoreo en tiempo real permiten a los operadores supervisar el estado de la máquina y ajustar los parámetros de operación en tiempo real. Esto ayuda a mejorar la eficiencia y reduce el tiempo de inactividad por fallos o ajustes incorrectos.
Conclusión
Las prensas horizontales son una herramienta esencial en la industria del conformado de metales, proporcionando la precisión y la capacidad necesarias para procesar piezas largas y realizar procesos especializados como el doblado, la extrusión y el embutido. Su diseño único y las ventajas que ofrecen en términos de distribución de la fuerza, precisión y versatilidad las convierten en una solución ideal para una amplia gama de aplicaciones industriales.
Prensas de Embutición Profunda
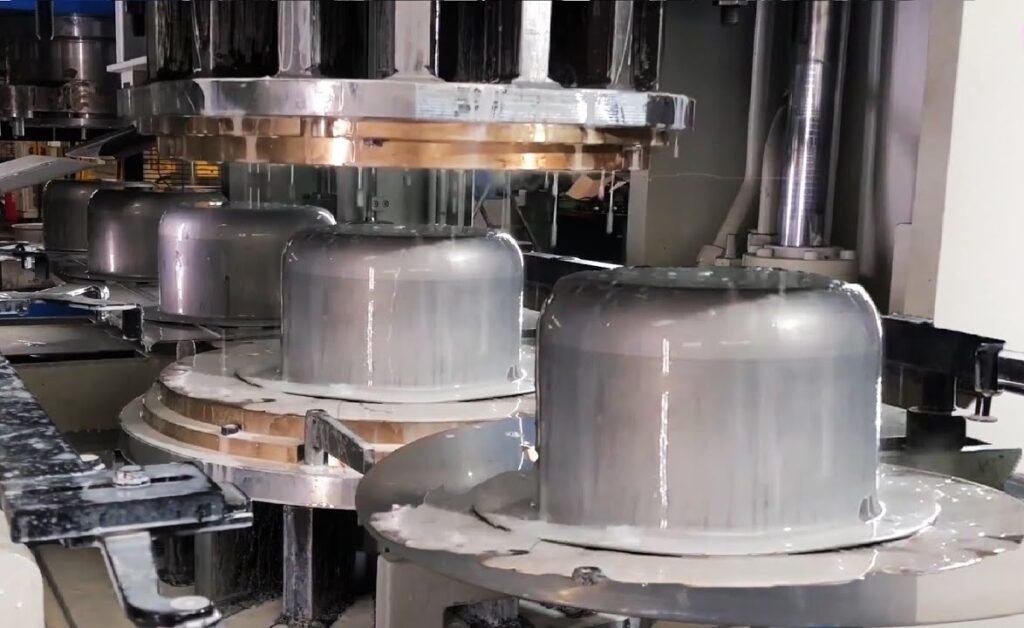
Las prensas de embutición profunda son máquinas especializadas utilizadas en la transformación de láminas metálicas para fabricar piezas con formas complejas, como componentes cóncavos o huecos. Este tipo de prensa es indispensable en la producción industrial moderna, ya que permite crear piezas de alta precisión y resistencia, optimizando el uso de material y reduciendo el tiempo de fabricación. La embutición profunda es un proceso altamente demandado en industrias como la automotriz, electrodoméstica, aeroespacial y de fabricación de recipientes metálicos.
El proceso de embutición profunda implica el uso de una prensa que aplica una gran fuerza sobre una lámina de metal, deformándola en un molde o matriz para darle forma. A diferencia de otros métodos de conformado, la embutición profunda permite crear piezas con una relación profundidad-diámetro elevada, lo que la hace ideal para fabricar componentes como cubiertas, carcasas, depósitos y envases metálicos.
Principio de Funcionamiento de la Embutición Profunda
El proceso de embutición profunda se basa en la aplicación de fuerza sobre una lámina de metal para deformarla plásticamente y darle una forma tridimensional. Este proceso implica varias fases:
- Preparación del Material: El proceso comienza con la selección de una lámina metálica, generalmente de acero, aluminio o cobre, dependiendo de la aplicación. La lámina se coloca sobre una matriz inferior que tiene la forma deseada.
- Acción de la Prensa: La prensa aplica una gran fuerza descendente a través de un punzón que empuja la lámina dentro de la matriz. Durante esta acción, la lámina de metal se deforma plásticamente, adaptándose a la forma de la matriz.
- Retención del Material: Para evitar que la lámina se rompa o arrugue durante el proceso, se utiliza un sujetador de presión o anillo de embutición que controla el flujo del material y asegura una distribución uniforme de la tensión.
- Desmoldeo de la Pieza: Una vez que la lámina ha sido conformada, la prensa se retira y la pieza embutida es extraída de la matriz. Este proceso puede repetirse varias veces para alcanzar la forma y profundidad deseadas, en lo que se conoce como embutición progresiva.
Características de las Prensas de Embutición Profunda
Las prensas de embutición profunda se destacan por su capacidad para aplicar grandes fuerzas de manera controlada y precisa, lo que es esencial para dar forma a láminas metálicas sin comprometer la calidad del material. Algunas de las características más importantes de estas prensas incluyen:
- Fuerza de Prensado Alta: Las prensas de embutición profunda deben generar grandes fuerzas para deformar los metales. Esta fuerza se mide en toneladas y varía según el tipo de material y el grosor de la lámina utilizada. Las prensas pueden variar desde máquinas de pequeña escala con unas pocas toneladas de fuerza hasta prensas industriales con miles de toneladas de capacidad.
- Control Preciso del Desplazamiento: El control preciso del desplazamiento del punzón es crucial para garantizar que el proceso de embutición se realice de manera eficiente y sin defectos. Las prensas de embutición profunda modernas están equipadas con sistemas hidráulicos o servoaccionados que permiten un control exacto del movimiento del punzón.
- Sistemas de Sujeción Ajustables: Para evitar que el material se rompa o arrugue durante el proceso, las prensas de embutición profunda suelen incorporar sistemas de sujeción ajustables que aplican una presión uniforme en los bordes de la lámina. Esto garantiza que el material fluya correctamente y se mantenga en su lugar durante el proceso de conformado.
- Capacidad para Procesar Diferentes Materiales: Las prensas de embutición profunda son altamente versátiles y pueden procesar una amplia gama de materiales, incluyendo acero inoxidable, aluminio, latón, cobre y materiales compuestos. Esto las convierte en una opción ideal para una variedad de aplicaciones industriales.
Ventajas de la Embutición Profunda
El uso de prensas de embutición profunda ofrece una serie de ventajas importantes en el proceso de fabricación de piezas metálicas. Algunas de las ventajas más destacadas son:
- Producción de Piezas Complejas: La embutición profunda permite la creación de piezas con formas complejas, como recipientes, carcasas y componentes huecos, que serían difíciles o imposibles de fabricar mediante otros procesos. Este método permite una mayor libertad de diseño, lo que es fundamental en industrias como la automotriz y la aeroespacial.
- Alta Precisión y Calidad: El proceso de embutición profunda garantiza una alta precisión en la forma final de las piezas, lo que reduce la necesidad de retrabajos o ajustes adicionales. Además, el control preciso de la fuerza y el desplazamiento asegura que las piezas fabricadas sean de alta calidad, con una excelente resistencia mecánica.
- Optimización del Material: La embutición profunda utiliza de manera eficiente el material, reduciendo el desperdicio de metal. Esto se traduce en un ahorro de costos y una mayor sostenibilidad en el proceso de fabricación.
- Reducción de Procesos Secundarios: A menudo, las piezas fabricadas mediante embutición profunda requieren menos procesos secundarios, como soldadura o ensamblaje, lo que acelera la producción y reduce los costos de fabricación.
Aplicaciones de las Prensas de Embutición Profunda
Las prensas de embutición profunda se utilizan en una amplia gama de industrias debido a su capacidad para fabricar piezas complejas y de alta precisión. Algunas de las aplicaciones más comunes incluyen:
- Industria Automotriz: En la fabricación de vehículos, las prensas de embutición profunda se utilizan para producir una variedad de componentes, como paneles de carrocería, chasis, depósitos de combustible y cubiertas. La alta precisión y resistencia de las piezas embutidas son cruciales para garantizar la seguridad y el rendimiento de los vehículos.
- Industria Aeroespacial: La industria aeroespacial requiere componentes ligeros pero resistentes, y las prensas de embutición profunda son ideales para fabricar carcasas, cubiertas y otros componentes estructurales. La capacidad de producir piezas complejas con alta precisión es fundamental en este sector.
- Fabricación de Electrodomésticos: Las prensas de embutición profunda son ampliamente utilizadas en la fabricación de electrodomésticos, donde se requieren carcasas y componentes metálicos de formas complejas y precisas. Ejemplos de piezas fabricadas mediante embutición profunda incluyen cubiertas de lavadoras, refrigeradores y cocinas.
- Industria de Envases Metálicos: La embutición profunda es el método preferido para la fabricación de envases metálicos, como latas de bebidas, recipientes de alimentos y depósitos a presión. La capacidad de producir recipientes metálicos ligeros y resistentes es una ventaja clave en esta industria.
Tecnologías Avanzadas en Prensas de Embutición Profunda
Las prensas de embutición profunda han evolucionado significativamente en las últimas décadas, gracias a la incorporación de nuevas tecnologías que han mejorado la precisión, la eficiencia y la seguridad del proceso. Algunas de las innovaciones más destacadas incluyen:
- Prensas con Control Numérico Computarizado (CNC): Las prensas de embutición profunda equipadas con sistemas CNC permiten un control extremadamente preciso de todos los parámetros del proceso, como la fuerza de prensado, la velocidad y el desplazamiento del punzón. Esto garantiza una repetibilidad exacta en la fabricación de piezas, lo que es crucial en aplicaciones industriales de gran volumen.
- Sistemas de Monitoreo en Tiempo Real: Muchas prensas de embutición profunda modernas están equipadas con sistemas de monitoreo en tiempo real que permiten a los operadores supervisar el estado de la máquina y ajustar los parámetros del proceso en tiempo real. Esto mejora la calidad de las piezas producidas y reduce el riesgo de fallos durante el proceso.
- Automatización del Proceso: La automatización ha permitido que las prensas de embutición profunda operen de manera más eficiente y con menor intervención humana. Los sistemas automáticos de carga y descarga de material, así como los controles automáticos de calidad, han mejorado significativamente la productividad y reducido el margen de error en la producción.
Mantenimiento y Seguridad en las Prensas de Embutición Profunda
El mantenimiento adecuado de las prensas de embutición profunda es crucial para garantizar un funcionamiento eficiente y prolongar la vida útil de la máquina. Algunas de las mejores prácticas de mantenimiento incluyen:
- Revisión del Sistema Hidráulico: La mayoría de las prensas de embutición profunda funcionan con sistemas hidráulicos, por lo que es esencial revisar periódicamente los niveles de aceite, la presión y los sellos para evitar fugas y garantizar un funcionamiento suave.
- Inspección de las Matrices y Punzones: Las matrices y punzones utilizados en el proceso de embutición profunda están sujetos a altos niveles de estrés, por lo que deben ser inspeccionados regularmente para detectar signos de desgaste o daño. El reemplazo o reparación oportuna de estos componentes es esencial para mantener la calidad del proceso.
- Lubricación de Piezas Móviles: La lubricación adecuada de las piezas móviles, como el pistón y las guías, es crucial para reducir el desgaste y garantizar un funcionamiento suave y eficiente de la prensa.
- Capacitación del Personal: El personal que opera las prensas de embutición profunda debe recibir una formación adecuada sobre los procedimientos de seguridad y las mejores prácticas de operación. Esto incluye el conocimiento de los controles de la máquina, los sistemas de seguridad y el mantenimiento preventivo.
Conclusión
Las prensas de embutición profunda son una herramienta esencial en la industria moderna, permitiendo la producción de piezas metálicas complejas y de alta precisión con una eficiencia y calidad excepcionales. Gracias a las innovaciones tecnológicas y las prácticas de mantenimiento adecuadas, estas máquinas continúan siendo una opción clave para la fabricación de componentes en una amplia gama de industrias, desde la automotriz hasta la aeroespacial.
Prensa de Embutición
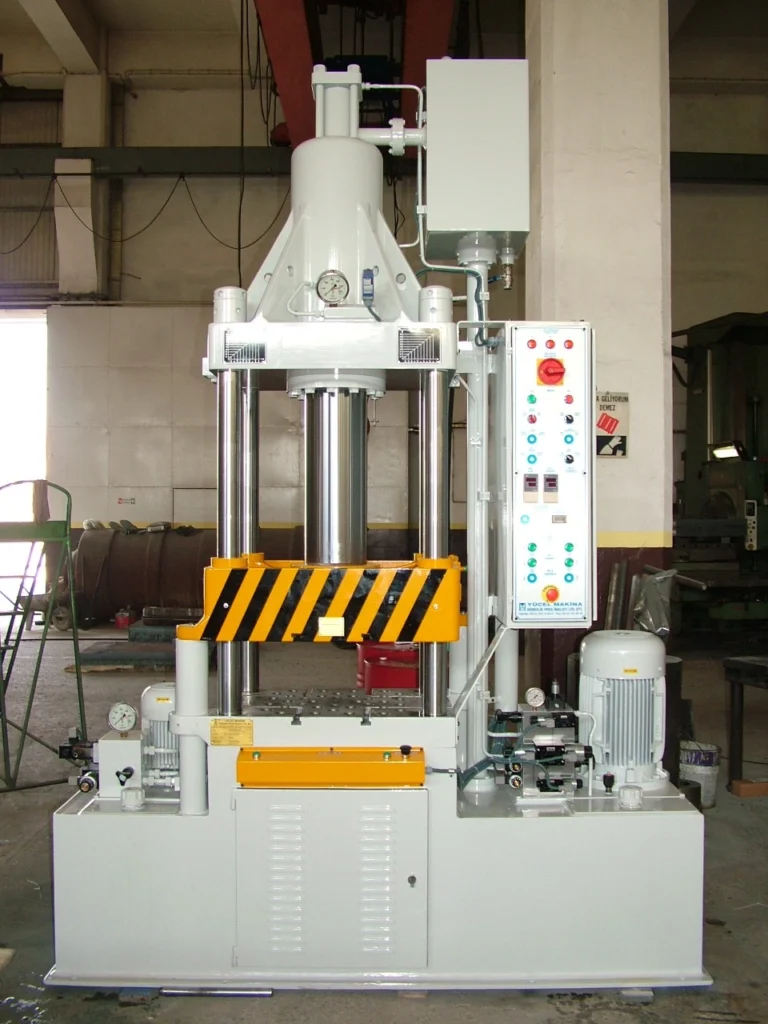
La prensa de embutición es una máquina fundamental en los procesos de transformación de metales, especialmente en la fabricación de piezas que requieren una forma tridimensional compleja, como recipientes, tapas, cubiertas y otros elementos industriales. A través de la embutición, una lámina metálica se conforma bajo una fuerza controlada, utilizando una matriz y un punzón, para obtener un producto final con características precisas y repetibles.
La embutición es un proceso altamente demandado en sectores industriales clave, como el automotriz, el de electrodomésticos, el aeroespacial y el de envases metálicos, ya que permite la producción eficiente de piezas de alta calidad. La prensa de embutición, como elemento central de este proceso, ofrece soluciones versátiles que optimizan tanto la forma como la resistencia de los productos finales.
Funcionamiento de una Prensa de Embutición
El funcionamiento de una prensa de embutición sigue un principio básico de deformación plástica del material. A través de la aplicación de una fuerza descendente, el punzón empuja una lámina metálica hacia una matriz que le da forma a la pieza. Dependiendo de la complejidad de la forma y la profundidad que se desee alcanzar, el proceso puede realizarse en una sola etapa o en varias etapas sucesivas, conocidas como embutición progresiva.
- Colocación de la Lámina: Se selecciona una lámina metálica del grosor y material adecuados, generalmente acero, aluminio, cobre o algún otro metal dúctil, que se coloca sobre la matriz de la prensa.
- Acción del Punzonado: El punzón de la prensa desciende con gran fuerza y presiona la lámina contra la matriz. Durante este proceso, la lámina se deforma plásticamente, adaptándose a la forma de la cavidad de la matriz.
- Control del Material: Para asegurar que la lámina se deforme de manera controlada y uniforme, se utiliza un sistema de sujeción que retiene el material en su lugar durante todo el proceso. Esto evita el deslizamiento y el arrugamiento de la lámina.
- Expulsión de la Pieza Conformada: Una vez que la pieza ha sido formada, el punzón se retira y la pieza es expulsada de la matriz. Este proceso puede repetirse para mejorar la precisión de la forma o aumentar la profundidad de la embutición.
Tipos de Prensas de Embutición
Existen varios tipos de prensas de embutición, cada una diseñada para satisfacer las necesidades específicas de diferentes aplicaciones industriales. Las más comunes incluyen:
- Prensas Hidráulicas: Las prensas hidráulicas son muy utilizadas en la embutición debido a su capacidad para generar grandes fuerzas de manera controlada. Estas prensas utilizan un sistema hidráulico para aplicar la presión necesaria en el proceso de conformado. Las prensas hidráulicas son ideales para procesos de embutición profunda, donde se requiere un control preciso de la fuerza y el desplazamiento.
- Prensas Mecánicas: Las prensas mecánicas utilizan energía cinética generada por un volante para aplicar la fuerza necesaria. Este tipo de prensa es adecuado para operaciones de embutición más rápidas y de menor complejidad, como la embutición de piezas poco profundas o de formas simples.
- Prensas Neumáticas: Las prensas neumáticas funcionan mediante aire comprimido y son utilizadas en aplicaciones donde se requiere menor fuerza que en las prensas hidráulicas o mecánicas. Estas prensas son comunes en la producción de piezas más pequeñas o de materiales más ligeros, como el aluminio o las láminas de cobre delgadas.
- Prensas de Embutición Progresiva: Estas prensas están diseñadas para realizar embuticiones en varias etapas, lo que permite la producción de piezas complejas con mayor precisión. Cada etapa de la prensa conforma el material un poco más, logrando formas que serían difíciles de obtener en una sola operación.
Aplicaciones de las Prensas de Embutición
Las prensas de embutición son ampliamente utilizadas en diversas industrias debido a su capacidad para producir piezas con formas complejas y precisas. A continuación, se describen algunas de las aplicaciones más comunes:
- Industria Automotriz: Las prensas de embutición juegan un papel clave en la fabricación de componentes automotrices, como paneles de carrocería, tapas de motor, chasis y otras piezas estructurales. La capacidad de conformar piezas ligeras pero resistentes es fundamental para la eficiencia y seguridad de los vehículos.
- Fabricación de Envases Metálicos: En la industria de envases, las prensas de embutición se utilizan para fabricar latas, botellas y otros recipientes metálicos, tanto para alimentos como para bebidas. La embutición permite crear envases herméticos con formas atractivas y funcionales, optimizando el uso del material.
- Electrodomésticos: Los componentes metálicos de electrodomésticos, como las cubiertas de lavadoras, refrigeradores y microondas, son fabricados mediante embutición. Este proceso permite crear piezas con alta resistencia y un acabado superficial uniforme, lo que mejora tanto la durabilidad como la estética de los electrodomésticos.
- Industria Aeroespacial: En el sector aeroespacial, la embutición se utiliza para fabricar componentes ligeros y de alta resistencia, como carcasas de motores y estructuras de fuselaje. La precisión y la capacidad de producir formas complejas hacen que la embutición sea ideal para cumplir con los exigentes estándares de calidad de la industria aeroespacial.
Ventajas de las Prensas de Embutición
El uso de prensas de embutición en los procesos de fabricación ofrece una serie de ventajas importantes, que contribuyen a mejorar la eficiencia, calidad y rentabilidad de la producción. Algunas de las principales ventajas incluyen:
- Reducción de Material Desperdiciado: El proceso de embutición permite utilizar la lámina metálica de manera eficiente, minimizando el desperdicio de material. Esto no solo reduce los costos de producción, sino que también contribuye a una mayor sostenibilidad en la fabricación.
- Alta Precisión y Repetibilidad: Las prensas de embutición están diseñadas para garantizar una alta precisión en la forma final de las piezas. Esto es esencial en aplicaciones industriales donde se requieren tolerancias estrictas y acabados de alta calidad. Además, las prensas pueden repetir el proceso con precisión, lo que garantiza uniformidad en la producción en masa.
- Versatilidad en Materiales y Formas: Las prensas de embutición pueden procesar una amplia variedad de materiales metálicos, desde aceros de alta resistencia hasta aleaciones ligeras como el aluminio. Además, permiten la fabricación de una gran diversidad de formas, desde recipientes cóncavos hasta componentes estructurales complejos.
- Mayor Resistencia de las Piezas: Durante el proceso de embutición, las piezas suelen experimentar un endurecimiento por deformación, lo que mejora su resistencia mecánica. Esto es especialmente importante en industrias como la automotriz y aeroespacial, donde la durabilidad y resistencia de los componentes son fundamentales.
Innovaciones Tecnológicas en Prensas de Embutición
Con el avance de la tecnología, las prensas de embutición han evolucionado para incorporar nuevas funcionalidades que mejoran tanto la precisión como la eficiencia del proceso de conformado. Algunas de las innovaciones más relevantes incluyen:
- Automatización del Proceso: Muchas prensas de embutición modernas están equipadas con sistemas de automatización que permiten un control más preciso del proceso y reducen la necesidad de intervención manual. Los robots y sistemas automáticos de alimentación de material mejoran la velocidad y eficiencia de producción.
- Control Numérico Computarizado (CNC): Las prensas con sistemas CNC ofrecen un control extremadamente preciso sobre los parámetros de operación, como la fuerza de prensado, la velocidad y la posición del punzón. Esto mejora la calidad de las piezas y permite la producción de formas más complejas.
- Monitoreo en Tiempo Real: Los sistemas de monitoreo en tiempo real permiten a los operadores supervisar el estado de la prensa y ajustar los parámetros de operación en respuesta a cualquier cambio en el proceso. Esto ayuda a reducir los errores y garantiza una mayor calidad en las piezas finales.
Mantenimiento y Seguridad en las Prensas de Embutición
El mantenimiento adecuado de las prensas de embutición es crucial para garantizar un funcionamiento eficiente y prolongar la vida útil de la máquina. Además, seguir las normas de seguridad es esencial para proteger tanto a los operadores como a la maquinaria. Algunas prácticas recomendadas incluyen:
- Inspección Regular de Matrices y Punzones: Las matrices y los punzones son las partes más críticas de una prensa de embutición. Deben ser inspeccionados regularmente para detectar signos de desgaste o daño que puedan afectar la calidad de las piezas o la seguridad del proceso.
- Revisión del Sistema Hidráulico: En las prensas hidráulicas, es fundamental revisar periódicamente los niveles de aceite y la presión del sistema para evitar fallos. Un sistema hidráulico bien mantenido garantiza un rendimiento óptimo y prolonga la vida útil de la prensa.
- Capacitación del Personal: El personal que opera las prensas de embutición debe estar debidamente capacitado para utilizar los controles de la máquina de manera segura y eficiente. Esto incluye el conocimiento de los procedimientos de seguridad y el mantenimiento preventivo.
Conclusión
Las prensas de embutición son una pieza clave en la industria de transformación de metales, permitiendo la fabricación de piezas complejas, precisas y resistentes. Gracias a su versatilidad, estas prensas son utilizadas en una amplia gama de sectores, desde la automoción hasta la fabricación de envases. A medida que la tecnología avanza, las prensas de embutición continúan mejorando en términos de eficiencia, precisión y seguridad, consolidándose como una herramienta esencial para la producción industrial moderna.
Máquinas de Corte y Bordó
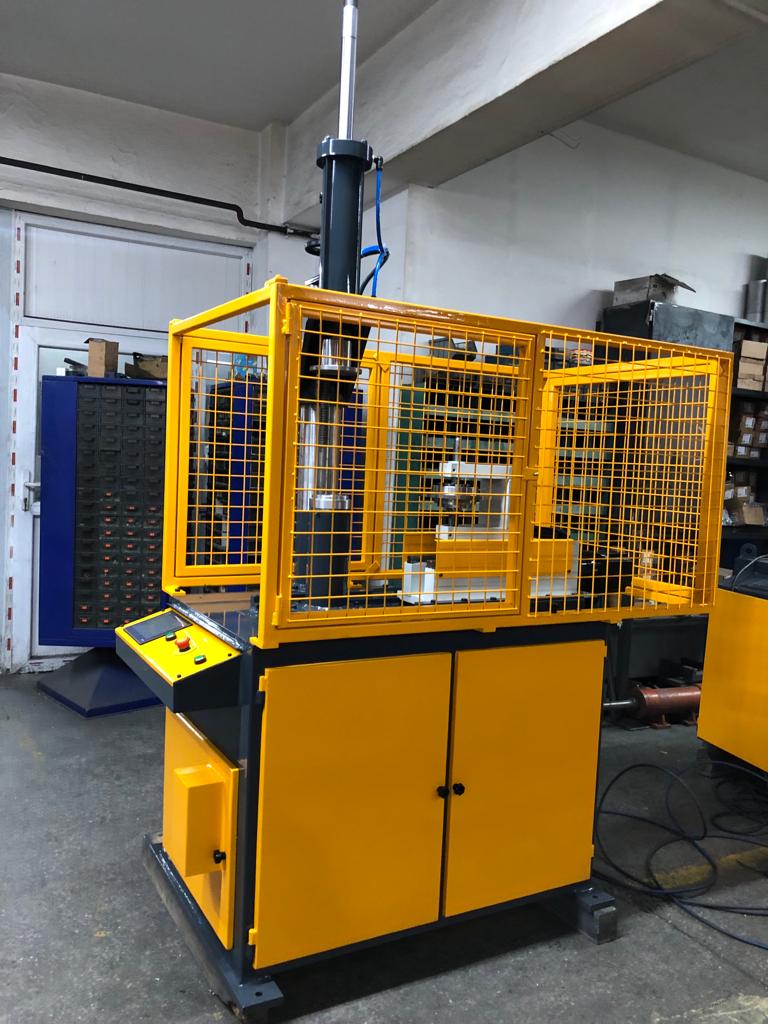
Las máquinas de corte y bordó desempeñan un papel fundamental en la industria de la fabricación de metales. Estas máquinas están diseñadas para realizar dos funciones clave: el corte de piezas de metal en formas específicas y el bordado, que implica la adición de bordes o contornos precisos para mejorar la funcionalidad o estética de los productos. Estas operaciones son esenciales en sectores como el automotriz, la fabricación de electrodomésticos, la industria de envases metálicos y muchas otras áreas industriales que requieren alta precisión en el procesamiento de metales.
El proceso de corte y bordó, cuando se realiza con equipos especializados, garantiza que los bordes de las piezas cortadas sean limpios y uniformes, lo que reduce la necesidad de procesos adicionales de acabado. Además, las máquinas modernas de corte y bordó están equipadas con tecnologías avanzadas, como el control numérico computarizado (CNC), lo que permite una mayor precisión, eficiencia y velocidad en la producción.
Funcionamiento de las Máquinas de Corte y Bordó
El principio básico de una máquina de corte y bordó combina dos operaciones: el corte y el conformado del borde. Dependiendo del diseño de la máquina, estas operaciones pueden realizarse de manera secuencial o simultánea, optimizando el proceso de producción.
- Corte de Material: El primer paso en el proceso es el corte del material. Utilizando una cuchilla o láser, la máquina corta la lámina de metal según la forma deseada. La precisión en el corte es fundamental para garantizar que el borde resultante sea uniforme y limpio. Este corte puede realizarse en diferentes ángulos o formas, dependiendo del diseño del producto final.
- Bordado de la Pieza: Después de cortar el material, la máquina procede al bordado, que consiste en la creación de un borde o contorno en la pieza. Este borde puede tener diferentes funciones, desde mejorar la resistencia estructural hasta proporcionar un acabado estético. El proceso de bordado se realiza mediante el prensado de los bordes de la pieza en una matriz que define su forma final.
- Ajuste de Parámetros: Las máquinas de corte y bordado modernas permiten ajustar varios parámetros de operación, como la velocidad de corte, la presión de bordado y la configuración del ángulo de las cuchillas. Esto garantiza una mayor versatilidad en el procesamiento de diferentes materiales y la producción de formas complejas.
Tipos de Máquinas de Corte y Bordó
Existen varios tipos de máquinas de corte y bordó, cada una diseñada para satisfacer necesidades específicas de la industria. Estas incluyen:
- Máquinas de Corte por Láser: Utilizan un rayo láser de alta potencia para cortar la lámina de metal con extrema precisión. Estas máquinas son ideales para cortes complejos y detallados en materiales como acero inoxidable, aluminio y otros metales. El corte por láser produce bordes extremadamente limpios, lo que reduce la necesidad de acabados posteriores.
- Máquinas de Corte por Cizalla: Las cizallas son una de las herramientas más comunes en el corte de metales. Estas máquinas utilizan cuchillas afiladas para cortar el material en línea recta. Son más adecuadas para cortes rápidos y de menor complejidad en materiales más gruesos.
- Máquinas de Bordado Hidráulicas: Estas máquinas utilizan un sistema hidráulico para aplicar presión a los bordes de las piezas de metal, conformándolos de acuerdo con las especificaciones del diseño. Son ampliamente utilizadas en la fabricación de piezas automotrices, envases metálicos y otros componentes donde el acabado del borde es crucial.
- Máquinas CNC: Las máquinas de corte y bordado controladas por CNC ofrecen un control preciso sobre el proceso. Gracias al uso de software avanzado, las máquinas CNC pueden realizar cortes y bordados complejos de manera automática y repetitiva, lo que es esencial en la producción en masa.
Ventajas del Uso de Máquinas de Corte y Bordó
Las máquinas de corte y bordó ofrecen numerosas ventajas para los procesos industriales de fabricación, especialmente en términos de precisión, eficiencia y calidad del producto final. Algunas de las principales ventajas incluyen:
- Alta Precisión: Las máquinas de corte y bordado modernas, especialmente las controladas por CNC, permiten realizar cortes y bordados con una precisión extrema. Esto es fundamental en la fabricación de piezas donde se requieren tolerancias estrechas y acabados perfectos.
- Mayor Velocidad de Producción: Al combinar las operaciones de corte y bordado en una sola máquina, se reduce el tiempo de producción y se aumenta la eficiencia general del proceso. Esto es particularmente importante en la fabricación en masa, donde los tiempos de ciclo son un factor crítico.
- Reducción de Desperdicio de Material: Las máquinas de corte y bordado están diseñadas para utilizar el material de manera eficiente, minimizando el desperdicio. El corte preciso reduce la cantidad de material sobrante, lo que se traduce en ahorro de costos y en un proceso de producción más sostenible.
- Versatilidad en el Procesamiento de Materiales: Estas máquinas pueden trabajar con una amplia gama de materiales metálicos, desde aceros de alta resistencia hasta aleaciones ligeras como el aluminio. Además, son capaces de producir una gran variedad de formas y diseños, lo que las hace extremadamente versátiles en diversas aplicaciones industriales.
- Acabado Limpio y Profesional: Una de las mayores ventajas de las máquinas de corte y bordado es la calidad del acabado final. El proceso de bordado asegura que los bordes de las piezas sean suaves, limpios y uniformes, lo que mejora tanto la estética como la funcionalidad de los productos.
Aplicaciones de las Máquinas de Corte y Bordó
Las máquinas de corte y bordado se utilizan en una variedad de industrias para la fabricación de componentes metálicos. Algunas de las aplicaciones más comunes incluyen:
- Industria Automotriz: En la fabricación de vehículos, las máquinas de corte y bordado son esenciales para producir paneles de carrocería, puertas, techos y otros componentes que requieren un corte preciso y un borde acabado de alta calidad. La resistencia y el acabado estético de las piezas son cruciales para la seguridad y el diseño del vehículo.
- Industria de Envases Metálicos: Las máquinas de corte y bordado juegan un papel clave en la producción de envases metálicos, como latas de bebidas y alimentos. El corte preciso y el bordado aseguran que los envases sean herméticos y que cumplan con los estándares de calidad y seguridad alimentaria.
- Electrodomésticos: En la fabricación de electrodomésticos, como lavadoras, refrigeradores y estufas, se utilizan máquinas de corte y bordado para producir las carcasas y paneles metálicos. El bordado de los bordes garantiza un acabado limpio y seguro, que mejora tanto la funcionalidad como la estética del producto.
- Industria Aeroespacial: En la industria aeroespacial, la precisión es de suma importancia. Las máquinas de corte y bordado son utilizadas para producir componentes ligeros pero resistentes, como paneles de alas y fuselajes, donde la calidad del corte y el acabado del borde son críticos para el rendimiento y la seguridad del avión.
Innovaciones en Máquinas de Corte y Bordó
Con los avances tecnológicos, las máquinas de corte y bordado han evolucionado significativamente en términos de precisión, eficiencia y automatización. Algunas de las innovaciones más destacadas incluyen:
- Tecnología Láser Avanzada: Las máquinas de corte por láser de última generación han mejorado en términos de potencia y precisión, lo que permite realizar cortes más rápidos y detallados, incluso en materiales más gruesos. Además, el láser produce bordes extremadamente limpios, lo que elimina la necesidad de procesos de acabado adicionales.
- Automatización y Robótica: La automatización ha transformado el uso de máquinas de corte y bordado en las líneas de producción. Los sistemas robóticos pueden cargar y descargar las piezas automáticamente, lo que reduce el tiempo de inactividad y mejora la eficiencia del proceso.
- Software de Diseño Avanzado: Las máquinas controladas por CNC están equipadas con software avanzado que permite a los diseñadores crear piezas complejas en el ordenador y luego enviarlas directamente a la máquina para su producción. Esto no solo reduce los errores, sino que también permite una mayor flexibilidad en el diseño de productos.
- Sistemas de Monitoreo en Tiempo Real: Muchas máquinas de corte y bordado modernas están equipadas con sistemas de monitoreo en tiempo real que permiten a los operadores supervisar el estado de la máquina y ajustar los parámetros de corte y bordado según sea necesario. Esto garantiza un nivel óptimo de calidad y reduce el riesgo de fallos en el proceso.
Mantenimiento y Seguridad en las Máquinas de Corte y Bordó
El mantenimiento adecuado y el cumplimiento de las normas de seguridad son fundamentales para garantizar un funcionamiento eficiente y seguro de las máquinas de corte y bordado. Algunas de las prácticas recomendadas incluyen:
- Inspección Regular de Cuchillas y Láser: En las máquinas de corte, es esencial revisar periódicamente el estado de las cuchillas o del láser para garantizar que estén en condiciones óptimas. Las cuchillas desgastadas o un láser mal calibrado pueden afectar la precisión del corte.
- Lubricación de Componentes Móviles: En las máquinas que operan con sistemas mecánicos, es importante mantener adecuadamente lubricadas las partes móviles para evitar el desgaste prematuro y garantizar un funcionamiento suave y eficiente.
- Capacitación del Personal: Los operadores de máquinas de corte y bordado deben recibir formación adecuada en el uso seguro y eficiente de las máquinas. Esto incluye la comprensión de los controles, el mantenimiento preventivo y las mejores prácticas de seguridad.
Conclusión
Las máquinas de corte y bordado son herramientas esenciales en la industria moderna de procesamiento de metales, permitiendo la producción de piezas con bordes limpios, precisos y funcionales. Gracias a los avances en tecnología láser, CNC y automatización, estas máquinas continúan mejorando en términos de velocidad, precisión y versatilidad. Desde la industria automotriz hasta la aeroespacial, las máquinas de corte y bordado juegan un papel clave en la fabricación de productos de alta calidad y resistencia.
Bordonadora Hidráulica
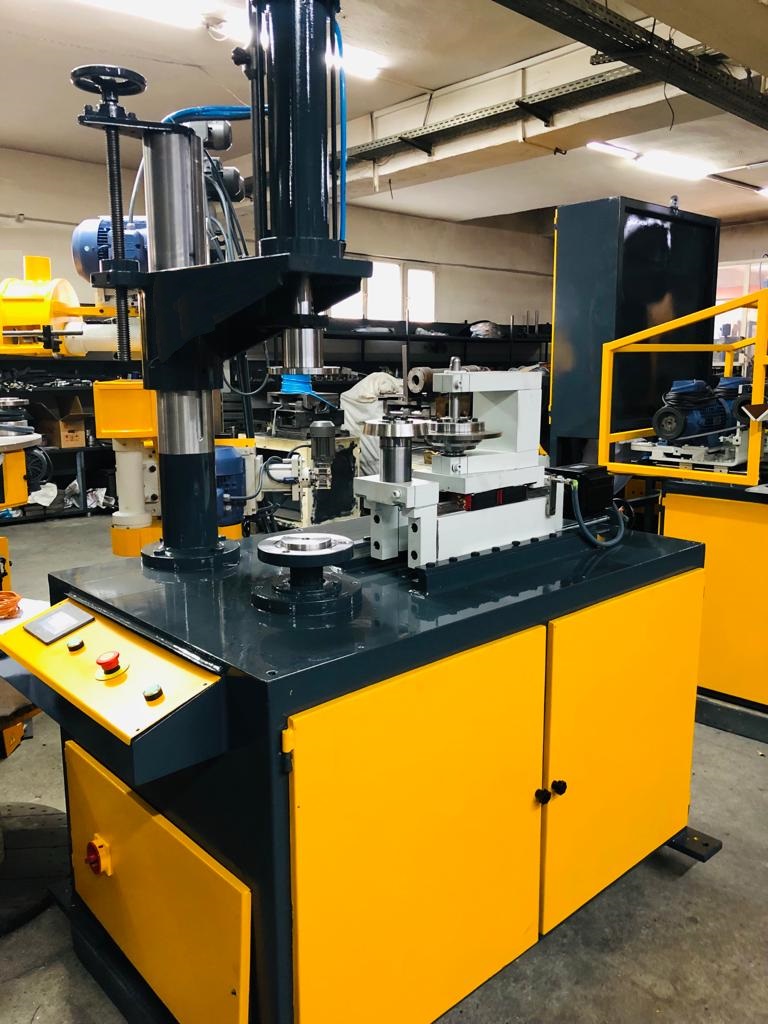
La bordonadora hidráulica es una máquina industrial esencial utilizada en la conformación de bordes en piezas metálicas, especialmente en láminas y chapas. Estas máquinas son fundamentales en sectores como la automoción, la fabricación de envases metálicos, la industria aeroespacial, y muchas otras áreas donde la precisión y el acabado de los bordes de las piezas de metal son cruciales para la funcionalidad y durabilidad del producto final.
El proceso de bordonado se refiere a la creación de un borde o reborde en una pieza de metal, que puede tener múltiples fines: desde reforzar la estructura de la pieza hasta mejorar su apariencia estética o facilitar su ensamblaje en otros componentes. La bordonadora hidráulica permite realizar este proceso de manera eficiente, aplicando la presión adecuada para lograr bordes uniformes y precisos sin comprometer la integridad del material.
Funcionamiento de una Bordonadora Hidráulica
El principio de funcionamiento de una bordonadora hidráulica se basa en el uso de un sistema hidráulico para generar la fuerza necesaria que deforma los bordes de la pieza metálica. A diferencia de otros tipos de bordonadoras, que pueden depender de mecanismos manuales o mecánicos, las bordonadoras hidráulicas ofrecen una mayor potencia y precisión, lo que las hace ideales para trabajar con materiales más gruesos o de alta resistencia.
El proceso de bordonado suele seguir los siguientes pasos:
- Preparación de la Pieza: La pieza de metal que va a ser bordonada se coloca en la máquina, asegurada mediante sujeciones especializadas para evitar el desplazamiento durante el proceso. Dependiendo de la configuración de la bordonadora, la pieza puede estar pre-cortada o ser procesada desde una lámina más grande.
- Aplicación de Presión Hidráulica: Una vez que la pieza está en posición, el sistema hidráulico se activa para aplicar presión a los bordes de la pieza. Esta presión es cuidadosamente controlada para evitar la deformación no deseada del material mientras se logra el borde preciso.
- Formación del Borde: A medida que se aplica la presión, la pieza se deforma de acuerdo con la forma de la matriz o molde que se utiliza en la bordonadora. Esta matriz puede ser personalizada según las especificaciones del producto final, permitiendo la creación de bordes de diversas formas y tamaños.
- Liberación de la Pieza: Una vez que el borde ha sido conformado, la presión hidráulica se reduce y la pieza se libera de las sujeciones, quedando lista para cualquier procesamiento adicional que sea necesario.
Componentes Clave de una Bordonadora Hidráulica
Una bordonadora hidráulica consta de varios componentes esenciales que trabajan en conjunto para garantizar un proceso de bordonado eficiente y preciso. Estos incluyen:
- Sistema Hidráulico: Este es el corazón de la bordonadora, ya que es el encargado de generar la fuerza necesaria para deformar el material. El sistema hidráulico está compuesto por una bomba hidráulica, cilindros y válvulas que controlan la presión aplicada a la pieza.
- Matriz o Molde: La matriz es el componente que define la forma del borde que se va a crear en la pieza de metal. Las matrices pueden ser intercambiables y personalizables para adaptarse a diferentes diseños y especificaciones.
- Controles Electrónicos: Las bordonadoras hidráulicas modernas están equipadas con controles electrónicos avanzados que permiten ajustar parámetros como la presión, la velocidad y la posición de la pieza. Esto garantiza un control preciso del proceso y minimiza el riesgo de errores o deformaciones no deseadas.
- Sistemas de Sujeción: Para asegurar que la pieza se mantenga en su lugar durante el proceso de bordonado, las bordonadoras hidráulicas están equipadas con sistemas de sujeción especializados. Estos sistemas pueden ajustarse para acomodar diferentes tamaños y formas de piezas.
- Estructura de la Máquina: La estructura o bastidor de la bordonadora está diseñada para soportar las fuerzas generadas durante el proceso de bordonado. Las bordonadoras hidráulicas suelen tener una construcción robusta y resistente, lo que les permite trabajar con materiales pesados o de alta resistencia.
Tipos de Bordonadoras Hidráulicas
Existen diferentes tipos de bordonadoras hidráulicas, diseñadas para satisfacer las necesidades específicas de diversos sectores industriales. Algunos de los tipos más comunes incluyen:
- Bordonadoras para Chapa: Estas máquinas están diseñadas específicamente para trabajar con láminas de metal, como acero, aluminio o latón. Son ampliamente utilizadas en la fabricación de componentes de automóviles, electrodomésticos y otros productos que requieren bordes precisos y bien acabados.
- Bordonadoras para Tubos: Estas máquinas están especializadas en la creación de bordes en piezas cilíndricas o tubulares. Se utilizan comúnmente en la industria de la fontanería, la construcción y la fabricación de conductos.
- Bordonadoras Automáticas: Equipadas con sistemas automatizados, estas bordonadoras permiten realizar el proceso de bordonado sin intervención humana directa. Son ideales para la producción en masa, donde la repetibilidad y la eficiencia son clave.
- Bordonadoras CNC: Estas bordonadoras están controladas por computadora, lo que permite una mayor precisión y flexibilidad en el diseño de los bordes. Las bordonadoras CNC son especialmente útiles para la producción de piezas complejas o de alta precisión.
Ventajas de las Bordonadoras Hidráulicas
Las bordonadoras hidráulicas ofrecen una serie de ventajas que las hacen una elección preferida en muchos sectores industriales:
- Alta Precisión: Gracias al control hidráulico y a los sistemas electrónicos avanzados, estas máquinas permiten crear bordes uniformes y precisos, lo que es crucial en aplicaciones donde la calidad del acabado es importante.
- Versatilidad en Materiales: Las bordonadoras hidráulicas pueden trabajar con una amplia gama de materiales, desde aceros de alta resistencia hasta aleaciones ligeras como el aluminio. Esto las convierte en una herramienta versátil para diversas aplicaciones.
- Capacidad para Procesar Materiales Gruesos: Una de las mayores ventajas de las bordonadoras hidráulicas es su capacidad para procesar materiales gruesos o de alta resistencia sin comprometer la calidad del borde.
- Automatización: Las bordonadoras hidráulicas modernas están equipadas con sistemas de automatización que reducen la necesidad de intervención manual, lo que mejora la eficiencia y reduce los costos laborales.
- Durabilidad y Resistencia: Dado que están diseñadas para manejar altas fuerzas y presiones, las bordonadoras hidráulicas tienen una construcción robusta que garantiza una larga vida útil, incluso en condiciones de trabajo intensivas.
Aplicaciones Industriales de las Bordonadoras Hidráulicas
Las bordonadoras hidráulicas se utilizan en una amplia gama de industrias debido a su capacidad para producir bordes precisos y uniformes en diferentes tipos de materiales. Algunas de las aplicaciones más comunes incluyen:
- Industria Automotriz: En la fabricación de vehículos, las bordonadoras hidráulicas son esenciales para la producción de paneles de carrocería, puertas, techos y otras piezas que requieren bordes reforzados. Estos bordes no solo mejoran la resistencia estructural de las piezas, sino que también facilitan su ensamblaje.
- Fabricación de Envases Metálicos: En la industria de envases metálicos, como la producción de latas y contenedores, las bordonadoras hidráulicas aseguran que los bordes de los envases sean uniformes y resistentes, lo que es crucial para garantizar la integridad del producto final.
- Industria Aeroespacial: La precisión es clave en la industria aeroespacial, y las bordonadoras hidráulicas juegan un papel importante en la fabricación de componentes metálicos ligeros pero resistentes, como paneles de alas y fuselajes. La capacidad de estas máquinas para crear bordes uniformes y precisos es crucial para garantizar la seguridad y el rendimiento de las aeronaves.
- Fabricación de Electrodomésticos: En la producción de electrodomésticos como refrigeradores, lavadoras y estufas, las bordonadoras hidráulicas son utilizadas para crear bordes acabados y seguros en las carcasas y paneles metálicos. Esto mejora tanto la durabilidad como la estética del producto final.
Innovaciones en Bordonadoras Hidráulicas
Con los avances tecnológicos, las bordonadoras hidráulicas han experimentado mejoras significativas en términos de eficiencia, precisión y automatización. Algunas de las innovaciones más destacadas incluyen:
- Control CNC: Las bordonadoras hidráulicas equipadas con sistemas de control numérico computarizado (CNC) permiten realizar operaciones de bordonado con una precisión milimétrica. Esto es especialmente útil en la producción de piezas complejas o en la fabricación en serie, donde la consistencia es crucial.
- Automatización Avanzada: La incorporación de sistemas de automatización ha permitido a las bordonadoras hidráulicas trabajar de manera continua y eficiente sin necesidad de intervención manual constante. Esto ha aumentado la productividad en fábricas de gran escala.
- Monitoreo y Diagnóstico en Tiempo Real: Muchas bordonadoras hidráulicas modernas están equipadas con sensores y sistemas de monitoreo que permiten a los operadores supervisar el rendimiento de la máquina en tiempo real. Esto no solo mejora la precisión del proceso, sino que también ayuda a identificar y corregir problemas antes de que afecten la calidad del producto final.
- Eficiencia Energética: Las bordonadoras hidráulicas más recientes están diseñadas para ser más eficientes en términos de consumo de energía. Esto es especialmente importante en la producción en masa, donde la reducción de los costos operativos es un factor clave.
Mantenimiento de una Bordonadora Hidráulica
Para garantizar que una bordonadora hidráulica funcione de manera óptima y tenga una larga vida útil, es esencial realizar un mantenimiento regular. Algunas de las prácticas de mantenimiento recomendadas incluyen:
- Revisión del Sistema Hidráulico: Es fundamental revisar regularmente los niveles de aceite hidráulico y asegurarse de que no haya fugas en el sistema. Un sistema hidráulico bien mantenido garantiza una operación suave y eficiente.
- Lubricación de Componentes: Los componentes móviles de la bordonadora, como las guías y los cilindros, deben ser lubricados regularmente para reducir el desgaste y prevenir fallos.
- Inspección de la Matriz: La matriz o molde utilizado para el bordonado debe ser inspeccionado regularmente para asegurarse de que no esté desgastado o dañado. Un molde en mal estado puede afectar la calidad del borde.
- Capacitación del Personal: Es importante que el personal encargado de operar la bordonadora esté debidamente capacitado en su uso y mantenimiento. Esto no solo garantiza la seguridad, sino que también ayuda a maximizar la eficiencia y productividad de la máquina.
Conclusión
Las bordonadoras hidráulicas son herramientas esenciales en la industria moderna del procesamiento de metales, ofreciendo una combinación de potencia, precisión y versatilidad que las hace indispensables en una amplia variedad de aplicaciones. Desde la industria automotriz hasta la fabricación de envases y la industria aeroespacial, estas máquinas juegan un papel crucial en la creación de bordes precisos y uniformes, mejorando tanto la funcionalidad como la estética de los productos finales. Con los continuos avances tecnológicos, las bordonadoras hidráulicas seguirán siendo una pieza clave en el futuro de la manufactura industrial.
Cizallas Bordonadoras
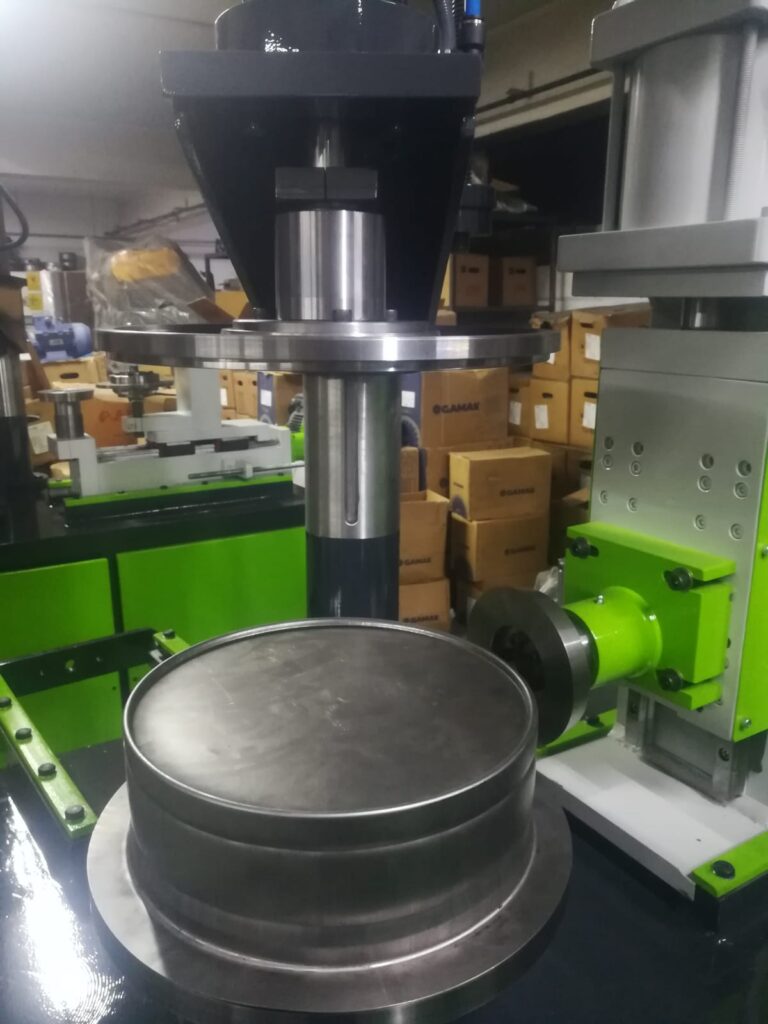
Las cizallas bordonadoras son herramientas clave en la industria del metal, diseñadas para combinar dos funciones esenciales: el corte preciso de láminas metálicas y la creación de bordes o rebordes. Este tipo de maquinaria se utiliza ampliamente en sectores como la fabricación de automóviles, la producción de electrodomésticos, la construcción, y la industria de envases metálicos. Su capacidad para cortar y bordonar en una sola operación las hace extremadamente eficientes, ahorrando tiempo y recursos.
La cizalla bordonadora no solo permite realizar cortes limpios y precisos en diversos materiales metálicos, sino que también proporciona la capacidad de reforzar los bordes de las piezas mediante el proceso de bordonado. Este refuerzo no solo mejora la resistencia estructural del material, sino que también contribuye a la seguridad y estética de la pieza final.
Funcionamiento de una Cizalla Bordonadora
El principio de funcionamiento de una cizalla bordonadora combina el corte de láminas de metal con el proceso de bordonado. Estas máquinas utilizan cuchillas afiladas y mecanismos especializados para realizar cortes precisos en el material, seguidos por un sistema de presión que crea el borde o reborde deseado.
El proceso generalmente sigue estos pasos:
- Colocación de la Lámina Metálica: El operador coloca la lámina o chapa metálica en la máquina, asegurándose de que esté alineada correctamente para el corte y bordonado. Dependiendo del tipo de cizalla, la lámina puede ser sujeta mediante sistemas de sujeción automáticos o manuales.
- Corte del Material: Las cuchillas de la cizalla se accionan para cortar el material. Estas cuchillas están diseñadas para realizar cortes limpios, minimizando las rebabas o imperfecciones en el borde cortado.
- Proceso de Bordonado: Tras el corte, la cizalla bordonadora aplica presión en los bordes de la pieza para crear un reborde. Este proceso puede realizarse simultáneamente con el corte o en una operación secundaria, dependiendo del diseño de la máquina.
- Liberación de la Pieza: Una vez completado el proceso, la pieza se libera de la máquina, lista para su inspección o para pasar a otros procesos de manufactura.
Componentes Clave de una Cizalla Bordonadora
Las cizallas bordonadoras están compuestas por una serie de componentes esenciales que permiten la ejecución precisa y eficiente de sus funciones. Entre los principales elementos, se incluyen:
- Cuchillas de Corte: Las cuchillas son uno de los componentes más importantes de una cizalla bordonadora. Están fabricadas con materiales de alta dureza, como el acero de herramientas, lo que les permite realizar cortes limpios incluso en materiales gruesos o duros. Las cuchillas deben ser afiladas regularmente para mantener su efectividad.
- Mecanismo de Bordonado: Este componente es responsable de la creación del reborde en la pieza cortada. Puede estar compuesto por rodillos o matrices que aplican presión a los bordes, moldeando el material de acuerdo con el diseño deseado.
- Sistemas de Sujeción: Estos sistemas aseguran que la lámina de metal permanezca en su lugar durante el proceso de corte y bordonado. Pueden ser manuales o automáticos, dependiendo de la complejidad de la máquina.
- Controles Electrónicos: Las cizallas bordonadoras modernas están equipadas con sistemas de control electrónico que permiten ajustar parámetros como la velocidad de corte, la presión de bordonado y la alineación de las piezas.
- Motor y Sistema de Accionamiento: El motor proporciona la potencia necesaria para accionar las cuchillas y el mecanismo de bordonado. Las cizallas bordonadoras pueden estar equipadas con motores eléctricos o hidráulicos, dependiendo del tamaño y la capacidad de la máquina.
Tipos de Cizallas Bordonadoras
Existen varios tipos de cizallas bordonadoras, cada uno diseñado para satisfacer necesidades específicas de la industria. Algunos de los más comunes incluyen:
- Cizallas Bordonadoras Manuales: Estas máquinas son ideales para trabajos pequeños o artesanales, donde la precisión y el control manual son esenciales. Son ampliamente utilizadas en talleres más pequeños y para la producción de prototipos.
- Cizallas Bordonadoras Automáticas: Diseñadas para operaciones de producción en masa, estas cizallas están equipadas con sistemas automatizados que permiten realizar cortes y bordonados de manera continua sin la intervención manual del operador.
- Cizallas Bordonadoras CNC: Estas máquinas están controladas por computadora, lo que permite una mayor precisión y repetibilidad en el corte y bordonado. Las cizallas CNC son ideales para la fabricación de piezas complejas que requieren tolerancias estrictas.
- Cizallas Hidráulicas: Utilizan sistemas hidráulicos para aplicar la fuerza necesaria tanto para cortar como para bordonar el material. Son especialmente útiles para trabajar con materiales gruesos o de alta resistencia.
Ventajas de las Cizallas Bordonadoras
Las cizallas bordonadoras ofrecen una serie de beneficios que las hacen indispensables en muchas aplicaciones industriales:
- Eficiencia en la Producción: Al combinar las funciones de corte y bordonado en una sola máquina, las cizallas bordonadoras permiten ahorrar tiempo y mejorar la eficiencia del proceso de fabricación.
- Precisión en el Corte: Las cuchillas de alta calidad garantizan cortes precisos y limpios, lo que es crucial en aplicaciones donde la calidad del borde es fundamental para la integridad del producto final.
- Refuerzo de los Bordes: El proceso de bordonado refuerza los bordes de las piezas cortadas, lo que mejora su resistencia estructural y durabilidad. Esto es particularmente importante en la fabricación de componentes metálicos que deben soportar cargas o tensiones.
- Versatilidad de Materiales: Las cizallas bordonadoras pueden trabajar con una amplia gama de materiales, desde metales ligeros como el aluminio hasta aceros más duros, lo que las convierte en una herramienta versátil para diferentes industrias.
- Automatización: Las versiones automáticas y CNC de las cizallas bordonadoras permiten una producción más rápida y precisa, reduciendo la intervención manual y los errores humanos.
Aplicaciones de las Cizallas Bordonadoras
Las cizallas bordonadoras se utilizan en una amplia variedad de industrias y aplicaciones, donde su capacidad para cortar y bordonar con precisión es esencial. Algunas de las aplicaciones más comunes incluyen:
- Industria Automotriz: En la fabricación de componentes de automóviles, como puertas, techos y paneles de carrocería, las cizallas bordonadoras juegan un papel clave en la producción de piezas con bordes limpios y reforzados, que son fundamentales para la seguridad y el rendimiento del vehículo.
- Fabricación de Electrodomésticos: Las cizallas bordonadoras se utilizan en la producción de electrodomésticos como lavadoras, refrigeradores y hornos, donde es importante que los bordes de las piezas metálicas sean seguros y estéticamente agradables.
- Industria de Envases Metálicos: En la producción de latas y otros envases metálicos, las cizallas bordonadoras garantizan que los bordes de los envases sean uniformes y seguros, lo que es crucial para la integridad y la funcionalidad del producto final.
- Construcción: En la construcción, las cizallas bordonadoras se utilizan para cortar y bordonar chapas metálicas que se utilizan en cubiertas, fachadas y otros componentes estructurales. Los bordes reforzados mejoran la resistencia de estos componentes y garantizan su durabilidad a largo plazo.
Mantenimiento de las Cizallas Bordonadoras
Para garantizar que una cizalla bordonadora funcione de manera óptima y tenga una larga vida útil, es esencial realizar un mantenimiento regular. Algunas de las prácticas de mantenimiento recomendadas incluyen:
- Afilado de las Cuchillas: Las cuchillas deben ser afiladas regularmente para garantizar cortes limpios y precisos. El uso de cuchillas desafiladas puede causar rebabas o imperfecciones en los bordes de las piezas.
- Lubricación de Componentes: Los componentes móviles de la cizalla, como los rodillos y guías, deben ser lubricados periódicamente para reducir el desgaste y prevenir fallos.
- Inspección del Sistema de Bordonado: El mecanismo de bordonado debe ser inspeccionado regularmente para asegurar que esté funcionando correctamente y no haya desgastes o daños en las matrices.
- Revisión del Sistema Hidráulico: En las cizallas bordonadoras hidráulicas, es importante revisar los niveles de aceite y asegurarse de que no haya fugas en el sistema. Un sistema hidráulico bien mantenido garantiza una operación suave y eficiente.
- Capacitación del Personal: Los operadores deben recibir formación adecuada en el uso seguro y eficiente de la cizalla bordonadora. Esto incluye la comprensión de los controles, el mantenimiento preventivo y las mejores prácticas de seguridad.
Innovaciones Tecnológicas en las Cizallas Bordonadoras
En los últimos años, las cizallas bordonadoras han experimentado una serie de innovaciones tecnológicas que han mejorado su rendimiento, precisión y eficiencia. Algunas de estas innovaciones incluyen:
- Control CNC: La incorporación de sistemas de control CNC permite a las cizallas bordonadoras realizar cortes y bordonados con una precisión sin precedentes, lo que es crucial en la fabricación de componentes complejos.
- Sistemas de Automatización: Las cizallas bordonadoras automáticas ahora pueden integrarse en líneas de producción totalmente automatizadas, lo que reduce el tiempo de inactividad y mejora la productividad.
- Mejoras en la Durabilidad de las Cuchillas: El desarrollo de nuevos materiales para las cuchillas ha aumentado su durabilidad y capacidad para cortar materiales más duros sin necesidad de afilado frecuente.
Conclusión
Las cizallas bordonadoras son herramientas indispensables en la industria del metal, ofreciendo una combinación única de corte preciso y bordonado que es fundamental para la fabricación de piezas metálicas de alta calidad. Con su capacidad para mejorar la resistencia estructural y la estética de los productos, estas máquinas seguirán siendo esenciales en una amplia gama de aplicaciones industriales.
Recortadora-Rebordeadora de Chapa Circular
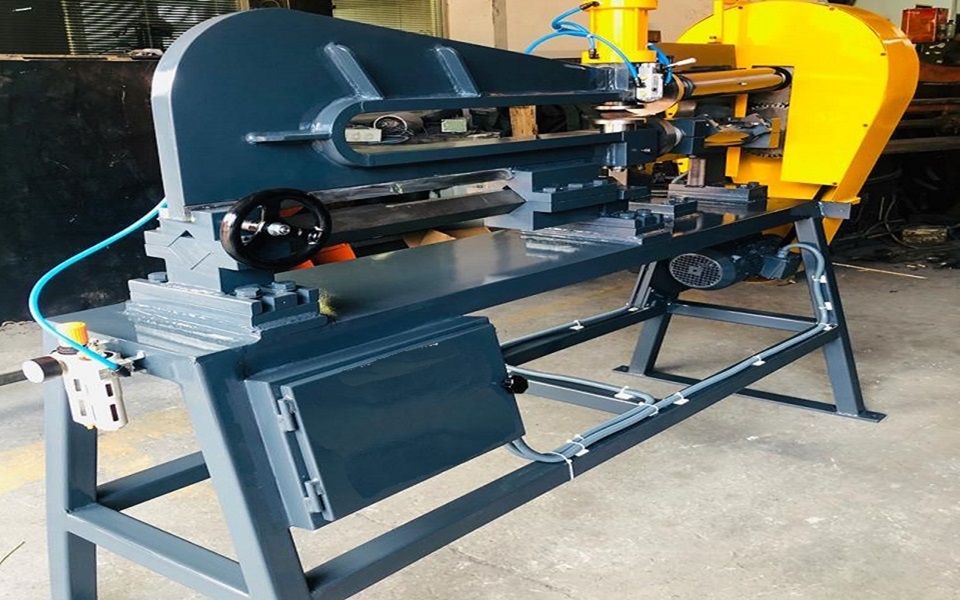
La recortadora-rebordeadora de chapa circular es una máquina especializada en el corte y conformado de bordes en chapas metálicas con forma circular. Este equipo es esencial en diversas industrias, como la fabricación de envases metálicos, componentes automotrices y electrodomésticos, donde se requieren piezas metálicas redondas con bordes bien definidos y resistentes.
Una recortadora-rebordeadora realiza dos funciones principales en un solo ciclo de operación: primero corta la chapa para darle una forma circular precisa y, posteriormente, realiza un reborde en los bordes de la pieza para mejorar su integridad estructural y apariencia estética. Estas máquinas son clave en la producción en masa de productos que requieren bordes reforzados, como tapas de envases metálicos, discos de freno y componentes de electrodomésticos.
Funcionamiento de una Recortadora-Rebordeadora de Chapa Circular
El proceso de recorte y rebordeado en una recortadora-rebordeadora de chapa circular implica varias etapas, todas diseñadas para maximizar la precisión y la eficiencia. A continuación, se describen los pasos típicos involucrados:
- Corte de la Chapa: La chapa metálica, que inicialmente puede tener una forma irregular o rectangular, se alimenta en la máquina. La recortadora utiliza cuchillas o un sistema de corte rotativo para cortar la chapa en una forma circular precisa.
- Rebordeado del Borde: Una vez que se ha cortado la chapa, la máquina aplica presión sobre los bordes de la pieza circular para formar un reborde. Este proceso de rebordeado no solo mejora la resistencia de la pieza, sino que también suaviza los bordes para hacerlos más seguros y estéticamente agradables.
- Control Automático o Manual: Dependiendo del tipo de recortadora-rebordeadora, el proceso puede ser completamente automático o requerir intervención manual para ajustar ciertos parámetros como la velocidad de corte, el grosor de la chapa o la presión aplicada para el rebordeado.
Componentes Clave de una Recortadora-Rebordeadora
Las recortadoras-rebordeadoras de chapa circular están compuestas por una serie de componentes esenciales que les permiten realizar cortes precisos y rebordear los bordes con alta eficiencia. Entre los principales componentes se incluyen:
- Cuchillas de Corte: Las cuchillas son las encargadas de realizar el corte inicial de la chapa en forma circular. Estas cuchillas están fabricadas con materiales altamente resistentes al desgaste, como acero de herramientas o carburo, y deben ser afiladas regularmente para mantener su eficacia.
- Matrices de Rebordeado: Las matrices o rodillos de rebordeado son los encargados de aplicar la presión necesaria para formar el borde en la chapa cortada. Estos componentes pueden ser ajustables para adaptarse a diferentes grosores de material y tamaños de pieza.
- Sistema de Sujeción: Este sistema asegura que la chapa se mantenga en su lugar durante el proceso de corte y rebordeado, garantizando una alineación precisa y reduciendo el riesgo de errores o imperfecciones en la pieza final.
- Control Electrónico: Muchas recortadoras-rebordeadoras modernas están equipadas con controles electrónicos o CNC que permiten programar y ajustar parámetros como la velocidad de corte, el tamaño de la pieza y la presión de rebordeado con gran precisión.
- Motor y Sistema de Accionamiento: El motor, ya sea eléctrico o hidráulico, proporciona la potencia necesaria para accionar tanto el sistema de corte como el de rebordeado. El tamaño y potencia del motor dependerán del grosor de la chapa y del nivel de automatización de la máquina.
Tipos de Recortadoras-Rebordeadoras de Chapa Circular
Existen varios tipos de recortadoras-rebordeadoras diseñadas para satisfacer diferentes necesidades industriales. Algunos de los tipos más comunes incluyen:
- Recortadoras-Rebordeadoras Manuales: Estas máquinas son más pequeñas y requieren una mayor intervención manual por parte del operador. Son ideales para trabajos de menor escala o para la producción de prototipos.
- Recortadoras-Rebordeadoras Automáticas: Estas máquinas están diseñadas para operaciones de mayor volumen y están equipadas con sistemas automáticos que permiten un corte y rebordeado continuo sin la intervención constante del operador.
- Recortadoras-Rebordeadoras CNC: Estas máquinas controladas por computadora ofrecen el más alto nivel de precisión y son capaces de producir piezas con tolerancias extremadamente ajustadas. Son ideales para la producción de piezas complejas y de alta precisión.
- Recortadoras-Rebordeadoras Hidráulicas: Estas máquinas utilizan sistemas hidráulicos para aplicar la fuerza necesaria en el proceso de rebordeado, lo que les permite trabajar con chapas más gruesas y materiales más resistentes.
Ventajas de Utilizar una Recortadora-Rebordeadora
Las recortadoras-rebordeadoras ofrecen una serie de beneficios que las hacen indispensables en muchas industrias. Algunas de las principales ventajas incluyen:
- Eficiencia en el Procesamiento: Al combinar las funciones de recorte y rebordeado en una sola operación, estas máquinas mejoran significativamente la eficiencia en la producción, reduciendo los tiempos de ciclo y eliminando la necesidad de realizar operaciones separadas.
- Cortes y Bordes Precisos: Gracias a sus cuchillas y sistemas de rebordeado de alta calidad, estas máquinas son capaces de producir piezas con cortes limpios y bordes uniformes, lo que es esencial en aplicaciones donde la precisión es crítica.
- Versatilidad en Materiales: Las recortadoras-rebordeadoras pueden trabajar con una amplia gama de materiales metálicos, incluidos el aluminio, acero, cobre y otros metales, lo que las convierte en herramientas versátiles para diversas industrias.
- Mejora de la Resistencia de la Pieza: El proceso de rebordeado refuerza los bordes de las piezas, aumentando su resistencia estructural y prolongando su vida útil, lo que es especialmente importante en aplicaciones que requieren piezas metálicas resistentes al desgaste o la deformación.
- Reducción de Desechos: Gracias a su capacidad para cortar con gran precisión, estas máquinas minimizan la cantidad de material desperdiciado, lo que contribuye a la reducción de costos y a un uso más eficiente de los recursos.
Aplicaciones Industriales de las Recortadoras-Rebordeadoras
Las recortadoras-rebordeadoras de chapa circular se utilizan en una amplia variedad de industrias debido a su capacidad para producir piezas con bordes precisos y reforzados. Algunas de las aplicaciones más comunes incluyen:
- Industria Automotriz: En la fabricación de discos de freno, tambores y otras piezas circulares utilizadas en los vehículos, las recortadoras-rebordeadoras son fundamentales para garantizar que los componentes tengan bordes precisos y resistentes.
- Industria de Envases Metálicos: En la producción de latas y tapas de envases metálicos, estas máquinas son cruciales para crear bordes seguros y uniformes que aseguren la integridad del envase y su funcionalidad en el almacenamiento y transporte de productos.
- Fabricación de Electrodomésticos: Los componentes metálicos circulares que se utilizan en electrodomésticos como lavadoras, secadoras y hornos suelen ser producidos con recortadoras-rebordeadoras, ya que los bordes suaves y reforzados son esenciales para la durabilidad y seguridad de estos productos.
- Industria Aeroespacial: En la fabricación de componentes metálicos circulares que deben soportar altas tensiones y condiciones extremas, como los utilizados en los motores de aviones, las recortadoras-rebordeadoras garantizan la resistencia y precisión necesarias para cumplir con los estrictos estándares de la industria.
- Sector de Energía: En la fabricación de componentes para generadores y otros equipos utilizados en la producción de energía, las recortadoras-rebordeadoras juegan un papel clave en la creación de piezas circulares que requieren bordes reforzados para soportar condiciones de trabajo exigentes.
Mantenimiento de las Recortadoras-Rebordeadoras
El mantenimiento adecuado de una recortadora-rebordeadora de chapa circular es esencial para garantizar su funcionamiento óptimo y prolongar su vida útil. Algunas prácticas de mantenimiento recomendadas incluyen:
- Afilado de Cuchillas: Las cuchillas deben ser afiladas regularmente para asegurar cortes limpios y precisos. El uso de cuchillas desafiladas puede resultar en cortes imperfectos o en un mayor desgaste de la máquina.
- Inspección de Matrices: Las matrices de rebordeado deben ser inspeccionadas regularmente para asegurarse de que no estén desgastadas o dañadas, ya que un reborde defectuoso puede comprometer la calidad de la pieza.
- Lubricación de Componentes: Los componentes móviles de la máquina, como las guías y los rodillos, deben ser lubricados periódicamente para reducir el desgaste y evitar fallos mecánicos.
- Revisión del Sistema Hidráulico: En las recortadoras-rebordeadoras hidráulicas, es importante revisar los niveles de aceite y asegurarse de que no haya fugas en el sistema hidráulico. Un sistema bien mantenido garantiza una operación suave y eficiente.
- Capacitación del Personal: Los operadores deben estar debidamente capacitados en el uso y mantenimiento de la máquina para garantizar su operación segura y eficiente. Esto incluye el conocimiento de los controles de la máquina, así como las mejores prácticas para ajustar y mantener los componentes.
Innovaciones Tecnológicas en las Recortadoras-Rebordeadoras
La tecnología de las recortadoras-rebordeadoras ha avanzado significativamente en los últimos años, lo que ha permitido mejoras en términos de precisión, eficiencia y automatización. Algunas de las innovaciones más destacadas incluyen:
- Control CNC: Las recortadoras-rebordeadoras equipadas con control CNC permiten una mayor precisión en el corte y rebordeado, lo que es esencial para la producción de piezas que requieren tolerancias estrictas y consistencia en grandes volúmenes.
- Automatización Completa: Las máquinas completamente automatizadas pueden integrar el proceso de recorte y rebordeado en líneas de producción, reduciendo la necesidad de intervención humana y mejorando la productividad.
- Mejora en los Materiales de las Cuchillas: Los avances en los materiales utilizados para fabricar las cuchillas han permitido que estas duren más tiempo y corten con mayor precisión, lo que reduce la necesidad de afilado frecuente y mejora la eficiencia del proceso.
- Sistemas de Visión Artificial: Algunos modelos avanzados de recortadoras-rebordeadoras están equipados con sistemas de visión artificial que permiten la inspección automática de las piezas para garantizar que cumplan con las especificaciones de calidad antes de ser liberadas para su uso o ensamblaje.
Conclusión
Las recortadoras-rebordeadoras de chapa circular son herramientas cruciales en la fabricación de piezas metálicas circulares, proporcionando un corte preciso y un rebordeado que mejora la resistencia y estética de las piezas. Su capacidad para trabajar con una amplia gama de materiales y su alta eficiencia las convierten en una inversión valiosa para cualquier industria que requiera productos metálicos redondos de alta calidad. A medida que la tecnología continúa avanzando, estas máquinas seguirán evolucionando, ofreciendo mayores niveles de precisión, automatización y versatilidad en la producción industrial.
Hilado de Cualquier Tipo de Metal
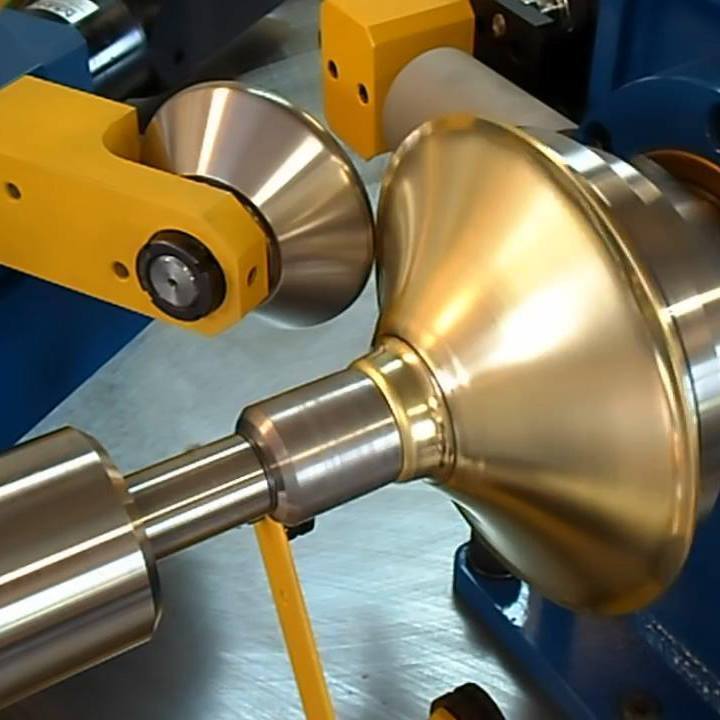
El hilado de metal, también conocido como “metal spinning”, es un proceso de fabricación que permite convertir discos metálicos en formas cilíndricas o cónicas mediante un método de deformación plástica. Este proceso se utiliza para crear piezas que van desde pequeños componentes decorativos hasta grandes estructuras industriales, y se caracteriza por su versatilidad para trabajar con una variedad de metales. El hilado de cualquier tipo de metal implica el uso de una amplia gama de materiales, como el acero, aluminio, cobre, latón y otros metales no ferrosos.
A lo largo de los años, el hilado de metal ha evolucionado desde un proceso manual hasta una técnica altamente mecanizada y automatizada, que hoy en día se aplica en industrias como la aeroespacial, automotriz, electrónica y fabricación de utensilios de cocina. El proceso permite fabricar piezas metálicas de manera eficiente, ofreciendo ventajas significativas en términos de coste y flexibilidad de diseño.
¿Qué es el Hilado de Metal?
El hilado de metal es una técnica de conformado en la que un disco plano de metal, conocido como preforma, se coloca en un torno. A medida que la preforma gira a alta velocidad, se aplica presión con herramientas especializadas (manuales o automáticas) para moldear el disco en una forma tridimensional, generalmente cilíndrica o cónica.
Este proceso se diferencia de otros métodos de conformado de metal, como el estampado o el embutido, en que el metal no se corta ni se extrae material; en lugar de eso, se deforma plásticamente. Gracias a esta característica, el hilado es un proceso más eficiente en cuanto al uso del material, minimizando el desperdicio.
Tipos de Hilado de Metal
Existen varios tipos de hilado de metal que se utilizan en función de las características del producto final y los requisitos del proceso. Estos incluyen:
- Hilado Convencional: En este proceso, la herramienta de hilado empuja el metal contra un mandril que da forma a la pieza. Este tipo de hilado es ideal para piezas simples con geometrías cilíndricas.
- Hilado de Compresión: Aquí, el disco metálico se comprime entre dos herramientas mientras gira, lo que permite crear piezas con paredes más delgadas y geometrías más complejas.
- Hilado por Corte: A diferencia de los otros métodos, en el hilado por corte, el material se estira y se corta durante el proceso, lo que permite la creación de piezas más delgadas con gran precisión.
- Hilado CNC: Con la automatización y el control por computadora (CNC), el hilado ha alcanzado nuevos niveles de precisión. Las máquinas de hilado CNC son capaces de producir piezas complejas con tolerancias estrictas, lo que es esencial en aplicaciones de alta exigencia como la aeroespacial o la automotriz.
Materiales Utilizados en el Hilado de Metal
El hilado de metal es un proceso sumamente flexible que puede utilizar una amplia gama de materiales metálicos, cada uno con sus propias características en términos de maleabilidad, resistencia y acabado. A continuación, se detallan algunos de los materiales más comúnmente utilizados:
- Aluminio: Es uno de los metales más utilizados debido a su ligereza, resistencia a la corrosión y excelente conductividad térmica. El hilado de aluminio es común en la fabricación de utensilios de cocina, lámparas y componentes de la industria automotriz.
- Acero Inoxidable: Este material se utiliza ampliamente en la fabricación de componentes de alta resistencia que requieren resistencia a la corrosión y durabilidad. Se emplea en sectores como la alimentación, medicina y aeroespacial.
- Cobre: Es un metal maleable y conductor que se utiliza en la fabricación de artículos decorativos, componentes eléctricos y equipos de calefacción y refrigeración.
- Latón: Este material se emplea en productos que requieren un acabado estético atractivo, como artículos decorativos, iluminación y componentes arquitectónicos.
- Titanio: En la industria aeroespacial y de defensa, el titanio se utiliza debido a su alta resistencia y ligereza, aunque su hilado es más complejo debido a su dureza.
Proceso de Hilado de Metal
El proceso de hilado de metal implica varias etapas, que pueden variar ligeramente según el tipo de hilado y el material utilizado. Sin embargo, los pasos básicos del proceso incluyen:
- Preparación del Disco: El proceso comienza con un disco plano de metal (preforma), que puede tener diferentes espesores y diámetros, dependiendo del diseño de la pieza final.
- Montaje en el Torno: El disco metálico se monta en un torno, donde se asegura contra un mandril. El mandril tiene la forma que la pieza final deberá adoptar.
- Aplicación de la Presión: A medida que el torno comienza a girar, el operario o la máquina CNC aplica presión con una herramienta especial, moldeando el disco de metal contra el mandril para que adopte la forma deseada.
- Formación de la Pieza: La herramienta se mueve a lo largo del disco de metal, deformándolo poco a poco hasta que adquiere la forma cilíndrica o cónica deseada.
- Acabado: En algunos casos, el proceso de hilado puede incluir pasos adicionales para mejorar el acabado de la pieza, como pulido o recubrimiento, dependiendo de los requisitos del cliente.
Ventajas del Hilado de Metal
El hilado de metal presenta una serie de ventajas en comparación con otros procesos de conformado de metal, lo que lo hace ideal para muchas aplicaciones industriales. Algunas de estas ventajas incluyen:
- Flexibilidad de Diseño: El hilado de metal permite la fabricación de una amplia gama de formas y tamaños, lo que ofrece una gran versatilidad en el diseño de las piezas.
- Menor Desperdicio de Material: Dado que el proceso de hilado implica la deformación del metal sin eliminar material, se minimiza el desperdicio, lo que resulta en una mayor eficiencia en el uso de los materiales.
- Costos Reducidos para Producciones Pequeñas y Medianas: A diferencia de otros métodos de conformado, como el estampado, el hilado no requiere costosos moldes o matrices, lo que reduce significativamente los costos de producción para series pequeñas y medianas.
- Mejora de las Propiedades Mecánicas: El proceso de deformación plástica durante el hilado puede mejorar la estructura del metal, aumentando la resistencia y durabilidad de la pieza final.
- Producción Rápida: El hilado de metal permite la producción rápida de prototipos y piezas personalizadas sin necesidad de largos tiempos de preparación.
Aplicaciones del Hilado de Metal
El hilado de metal se utiliza en una amplia variedad de industrias debido a su capacidad para producir piezas metálicas de alta calidad y con geometrías complejas. Algunas de las aplicaciones más comunes incluyen:
- Industria Aeroespacial: El hilado de metales como el titanio y el aluminio es esencial en la fabricación de componentes livianos y resistentes para aviones, como conos de nariz y carcasas de motores.
- Industria Automotriz: En este sector, el hilado se utiliza para fabricar piezas como cubiertas de ruedas, tanques de combustible y otros componentes metálicos que requieren una gran resistencia estructural.
- Fabricación de Utensilios de Cocina: Ollas, sartenes y otros utensilios de cocina de alta calidad se fabrican mediante hilado de aluminio y acero inoxidable, ya que este proceso permite la producción de piezas sin costuras con excelentes propiedades térmicas.
- Industria de la Iluminación: El hilado se utiliza para fabricar reflectores y pantallas metálicas para lámparas, aprovechando la capacidad de este proceso para crear formas cilíndricas con acabados lisos y precisos.
- Electrónica y Telecomunicaciones: En la fabricación de antenas y otros componentes electrónicos, el hilado de metales como el cobre y el aluminio permite la producción de piezas con geometrías específicas y alta conductividad.
- Arte y Decoración: El hilado de metal se utiliza también en la creación de piezas decorativas, esculturas y otros objetos de arte debido a su capacidad para moldear metales como el latón y el cobre en formas estéticamente atractivas.
Desafíos en el Hilado de Metal
A pesar de sus numerosas ventajas, el hilado de metal presenta ciertos desafíos que deben considerarse en el proceso de fabricación. Algunos de estos desafíos incluyen:
- Limitaciones en el Grosor del Material: El hilado de metales es más adecuado para chapas delgadas, ya que trabajar con materiales más gruesos puede resultar en defectos en la pieza o requerir una mayor cantidad de pasos.
- Precisión en Piezas Complejas: Aunque el hilado es un proceso flexible, crear piezas con geometrías extremadamente complejas puede ser difícil y requerir herramientas o procesos adicionales para lograr los resultados deseados.
- Variabilidad en la Calidad del Acabado: Dependiendo del tipo de metal y el proceso de hilado, la pieza final puede requerir tratamientos adicionales para mejorar el acabado de la superficie, como pulido o revestimiento.
Innovaciones en el Hilado de Metal
Las tecnologías en el hilado de metal han avanzado considerablemente en los últimos años, lo que ha permitido mejoras en la eficiencia, precisión y versatilidad del proceso. Algunas de las innovaciones más recientes incluyen:
- Hilado CNC: La integración de controles numéricos computarizados (CNC) ha permitido alcanzar niveles mucho mayores de precisión y repetibilidad, lo que es especialmente útil en aplicaciones que requieren tolerancias estrictas.
- Herramientas Avanzadas de Hilado: Las herramientas de hilado han mejorado en términos de durabilidad y precisión, lo que permite trabajar con materiales más duros y piezas más complejas sin comprometer la calidad.
- Automatización: Las líneas de producción completamente automatizadas para el hilado de metal han reducido los tiempos de ciclo y mejorado la eficiencia, permitiendo la producción en masa de piezas personalizadas.
Conclusión
El hilado de cualquier tipo de metal es un proceso esencial en muchas industrias debido a su flexibilidad, eficiencia y capacidad para trabajar con una amplia variedad de materiales metálicos. A medida que la tecnología continúa avanzando, el hilado de metal seguirá siendo una técnica clave para la producción de componentes metálicos de alta calidad, ofreciendo soluciones eficientes y económicas para una amplia gama de aplicaciones industriales y comerciales.
Prensa Rebordeadora
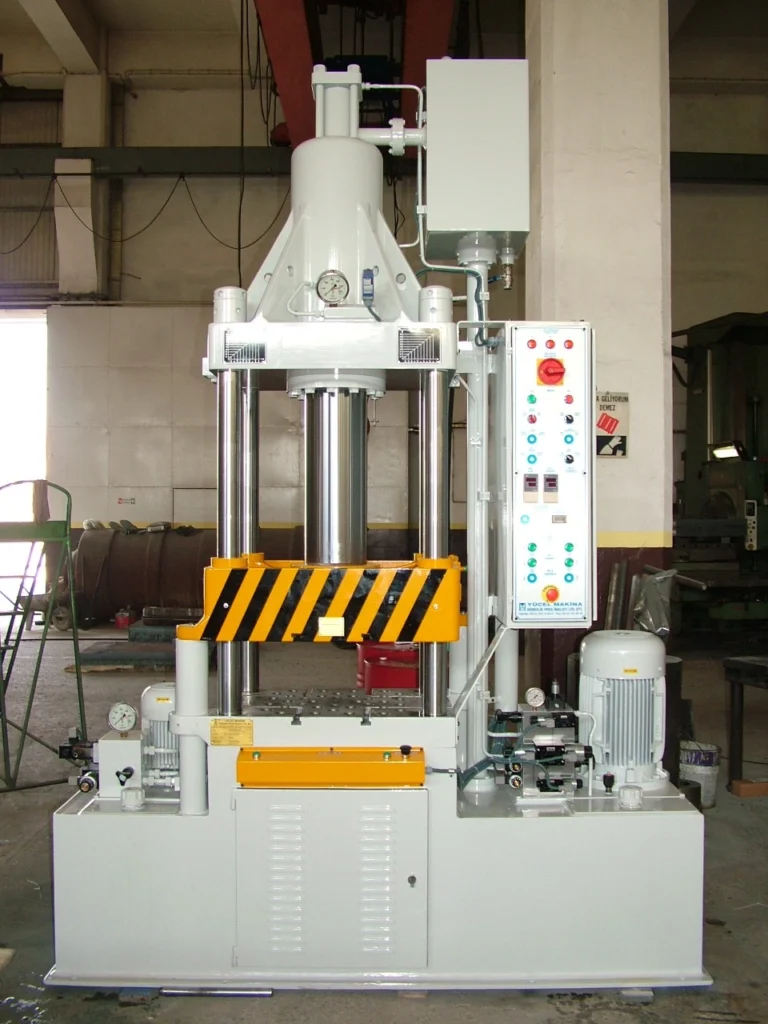
Las prensas rebordeadoras son un tipo especializado de equipo industrial utilizado principalmente para dar forma a los bordes de componentes metálicos. Este proceso es conocido como rebordeado y se utiliza en diversas industrias para crear bordes reforzados, mejorar la resistencia estructural y mejorar el acabado de los productos metálicos. Las prensas rebordeadoras son fundamentales en aplicaciones que requieren precisión, calidad en los acabados y consistencia en la producción.
En este contexto, es crucial comprender las características, los procesos, las aplicaciones y las ventajas que ofrecen las prensas rebordeadoras en la industria moderna. Desde las operaciones manuales hasta las máquinas completamente automatizadas, el rebordeado desempeña un papel central en la producción de una amplia gama de productos.
¿Qué es una Prensa Rebordeadora?
Una prensa rebordeadora es una máquina utilizada para formar bordes en piezas de chapa o productos metálicos. El proceso de rebordeado consiste en doblar o formar el borde exterior del metal hacia el interior o exterior para obtener una mayor rigidez estructural y mejorar el aspecto del producto. Dependiendo del diseño de la pieza y los requisitos del cliente, este proceso puede realizarse en diferentes ángulos y formas.
Existen diferentes tipos de prensas rebordeadoras, cada una diseñada para un propósito específico en función del tipo de material y las características del producto final. Estas prensas suelen ser controladas mediante sistemas hidráulicos, mecánicos o neumáticos que permiten un control preciso sobre el proceso de rebordeado.
Tipos de Prensas Rebordeadoras
Las prensas rebordeadoras se clasifican principalmente en función de la naturaleza del proceso de rebordeado y las especificaciones del material. Los tipos más comunes incluyen:
- Prensas Rebordeadoras Hidráulicas: Estas prensas funcionan mediante la aplicación de presión hidráulica, lo que les permite ejercer una fuerza constante y precisa. Son ideales para trabajar con materiales más gruesos y aplicaciones que requieren un rebordeado uniforme en toda la pieza.
- Prensas Rebordeadoras Neumáticas: En este tipo de prensa, se utiliza aire comprimido para accionar los mecanismos de la máquina. Aunque son menos potentes que las prensas hidráulicas, las prensas neumáticas son más rápidas y eficientes en términos de consumo de energía, lo que las hace ideales para aplicaciones en serie y trabajos de menor volumen.
- Prensas Rebordeadoras Automáticas: Estas máquinas están equipadas con sistemas de control automatizados, como el control numérico computarizado (CNC), que permiten un alto grado de precisión y repetibilidad en el proceso de rebordeado. Las prensas automáticas son ampliamente utilizadas en industrias que requieren grandes volúmenes de producción con altos estándares de calidad.
- Prensas Rebordeadoras Manuales: Aunque menos comunes en la industria moderna, las prensas manuales siguen siendo utilizadas en trabajos artesanales o en talleres donde el volumen de producción es bajo y se requiere una personalización más detallada de las piezas.
Proceso de Rebordeado
El proceso de rebordeado involucra una serie de pasos, que varían según el tipo de máquina y el material que se utilice. A continuación, se describen las fases generales del proceso:
- Preparación del Material: El primer paso consiste en seleccionar y preparar la pieza de chapa metálica que se va a rebordear. Este material puede variar desde acero, aluminio, cobre o latón, dependiendo de las necesidades del producto final.
- Colocación en la Prensa: El material se coloca en la prensa rebordeadora, donde se asegura para evitar que se mueva durante el proceso. El material debe estar correctamente alineado para garantizar que el reborde se realice de manera uniforme.
- Aplicación de la Fuerza: La prensa comienza a aplicar presión sobre el borde de la pieza. Dependiendo del diseño de la máquina y el tipo de material, esta presión se puede ajustar para obtener el ángulo y la forma de reborde deseados.
- Formación del Borde: A medida que la presión se aplica, el borde de la pieza se deforma gradualmente, doblándose hacia el interior o exterior según lo requiera el diseño. Este proceso puede repetirse varias veces para lograr un acabado preciso y uniforme.
- Inspección y Ajustes Finales: Una vez que el proceso de rebordeado ha finalizado, la pieza se inspecciona para verificar que cumpla con las especificaciones de calidad y que el reborde esté correctamente formado. Si es necesario, se pueden realizar ajustes adicionales para perfeccionar el acabado.
Ventajas de las Prensas Rebordeadoras
Las prensas rebordeadoras ofrecen una serie de ventajas significativas en la producción industrial, especialmente en comparación con otros métodos de conformado de bordes. Entre las principales ventajas se incluyen:
- Mejora de la Resistencia Estructural: El rebordeado aumenta la resistencia del borde de la pieza sin agregar material adicional, lo que resulta en productos más duraderos y resistentes sin aumentar su peso.
- Acabado de Alta Calidad: Las prensas rebordeadoras permiten obtener un acabado uniforme y suave en los bordes, lo que mejora tanto la apariencia estética como la funcionalidad del producto.
- Reducción del Desperdicio de Material: Dado que el proceso de rebordeado no implica la eliminación de material, se minimiza el desperdicio, lo que contribuye a una mayor eficiencia y reducción de costos en la producción.
- Flexibilidad en el Diseño: Las prensas rebordeadoras permiten realizar rebordes en una variedad de ángulos y formas, lo que ofrece una mayor flexibilidad en el diseño de piezas y productos personalizados.
- Mayor Seguridad: El proceso de rebordeado también puede mejorar la seguridad de los productos metálicos, ya que elimina bordes afilados que podrían representar un riesgo durante el manejo o ensamblaje.
Aplicaciones de las Prensas Rebordeadoras
Las prensas rebordeadoras son utilizadas en una amplia variedad de industrias y aplicaciones debido a su versatilidad y capacidad para trabajar con diferentes tipos de materiales y productos. Algunas de las aplicaciones más comunes incluyen:
- Industria Automotriz: En la fabricación de piezas de automóviles, como cubiertas de ruedas y componentes estructurales, el rebordeado es esencial para mejorar la resistencia de las piezas y garantizar su durabilidad bajo condiciones extremas.
- Industria Aeroespacial: En este sector, el rebordeado se utiliza para fabricar componentes livianos y resistentes que soporten las tensiones y cargas a las que están sometidos durante el vuelo.
- Industria de Electrodomésticos: Los electrodomésticos que contienen partes metálicas, como lavadoras, secadoras y refrigeradores, a menudo utilizan prensas rebordeadoras para mejorar la durabilidad y el aspecto de los bordes.
- Fabricación de Utensilios de Cocina: El rebordeado es crucial en la producción de utensilios de cocina, como ollas y sartenes, donde se requiere que los bordes sean resistentes y suaves al tacto.
- Contenedores Metálicos: Los bidones y contenedores metálicos utilizados para el almacenamiento de líquidos y productos químicos suelen ser rebordeados para mejorar su resistencia y evitar que los bordes se deterioren con el tiempo.
Mantenimiento y Operación de las Prensas Rebordeadoras
Para garantizar la longevidad y eficiencia de las prensas rebordeadoras, es esencial realizar un mantenimiento adecuado y operar las máquinas siguiendo las mejores prácticas. Entre los aspectos clave del mantenimiento se incluyen:
- Lubricación Regular: Las partes móviles de la prensa, como pistones y ejes, deben lubricarse periódicamente para evitar el desgaste prematuro y asegurar un funcionamiento suave.
- Inspección de Componentes: Las herramientas y moldes utilizados en el rebordeado deben inspeccionarse regularmente para detectar signos de desgaste o daño, lo que podría afectar la calidad del reborde.
- Limpieza: Mantener la máquina limpia es esencial para evitar la acumulación de polvo o residuos metálicos que podrían interferir con el proceso.
- Capacitación de los Operadores: Los operadores deben estar bien capacitados para manejar la máquina de manera segura y eficiente, incluyendo el conocimiento de los controles y ajustes necesarios para diferentes tipos de materiales.
Innovaciones Tecnológicas en las Prensas Rebordeadoras
Las prensas rebordeadoras han experimentado una serie de innovaciones tecnológicas que han mejorado su precisión, eficiencia y facilidad de uso. Algunas de estas innovaciones incluyen:
- Sistemas de Control CNC: La incorporación de sistemas de control numérico computarizado ha permitido automatizar gran parte del proceso de rebordeado, lo que ha resultado en una mayor precisión y repetibilidad en la producción.
- Sistemas de Visión Artificial: Algunas prensas avanzadas ahora están equipadas con cámaras y sensores que permiten monitorear el proceso en tiempo real, detectando cualquier irregularidad en el rebordeado y ajustando automáticamente los parámetros de la máquina.
- Mejora en los Materiales de Herramientas: Los avances en los materiales utilizados para las herramientas de rebordeado han aumentado su durabilidad y capacidad para trabajar con metales más duros sin comprometer la calidad del acabado.
- Automatización Completa: En entornos de producción en masa, las prensas rebordeadoras completamente automatizadas permiten realizar el proceso sin intervención humana, lo que aumenta significativamente la velocidad de producción y reduce los errores humanos.
Conclusión
Las prensas rebordeadoras son herramientas esenciales en la industria moderna, ofreciendo una combinación de precisión, eficiencia y flexibilidad. A medida que la tecnología continúa avanzando, es probable que el papel de estas prensas en la producción industrial siga creciendo, permitiendo a las empresas cumplir con los exigentes requisitos de calidad y diseño en una variedad de sectores.
Prensa Hidráulica Horizontal
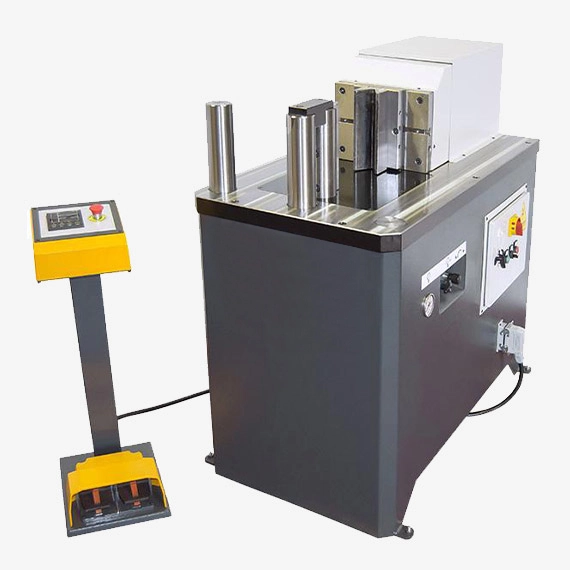
Las prensas hidráulicas horizontales son herramientas de gran relevancia en el ámbito de la conformación de metales y otros materiales. Este tipo de prensa se distingue por su capacidad para aplicar una fuerza controlada de manera horizontal, en lugar de vertical como las prensas tradicionales. Gracias a su diseño y funcionamiento, son ampliamente utilizadas en una variedad de aplicaciones industriales que requieren un control preciso y eficiente en el proceso de conformado o ensamblaje de piezas.
El funcionamiento de estas prensas se basa en el principio de Pascal, lo que les permite generar grandes cantidades de fuerza a través del uso de un fluido hidráulico, normalmente aceite, para accionar un pistón. La prensa hidráulica horizontal es ideal para operaciones como el doblado, enderezado, estampado, ensamblaje y corte de piezas de metal o plástico, entre otras aplicaciones.
A continuación, exploraremos en detalle el funcionamiento, las características, las aplicaciones y los beneficios de las prensas hidráulicas horizontales, así como las innovaciones tecnológicas que han permitido su evolución en la industria moderna.
Principio de Funcionamiento de una Prensa Hidráulica Horizontal
El principio básico de una prensa hidráulica se fundamenta en la ley de Pascal, que establece que la presión ejercida en un fluido en un recipiente cerrado se transmite de manera uniforme en todas las direcciones. En una prensa hidráulica, este principio se aprovecha para multiplicar la fuerza aplicada, permitiendo que una pequeña fuerza aplicada en un área pequeña se convierta en una gran fuerza en un área mayor.
En el caso de las prensas hidráulicas horizontales, el pistón de presión se desplaza horizontalmente, lo que les permite realizar una variedad de tareas industriales que requieren un movimiento lateral o de presión uniforme a lo largo de la longitud de la pieza. Este diseño es particularmente útil en aplicaciones que requieren la formación o manipulación de piezas largas y rectas, como barras de metal o tubos.
Los componentes principales de una prensa hidráulica horizontal incluyen:
- Cilindro Hidráulico: Es el componente encargado de generar la fuerza de presión mediante el desplazamiento de un pistón accionado por el fluido hidráulico.
- Bomba Hidráulica: Proporciona el fluido a presión necesario para mover el pistón dentro del cilindro.
- Válvulas de Control: Regulan el flujo del fluido hidráulico, permitiendo un control preciso sobre la cantidad de fuerza aplicada y la velocidad del pistón.
- Estructura o Bastidor Horizontal: Soporta las fuerzas generadas durante la operación y asegura que el movimiento de la prensa se realice de manera precisa y segura.
Tipos de Prensas Hidráulicas Horizontales
Existen diferentes configuraciones y tipos de prensas hidráulicas horizontales, cada una diseñada para cumplir con necesidades específicas en el proceso de fabricación. Entre los tipos más comunes se encuentran:
- Prensas Hidráulicas Horizontales de Doblado: Estas prensas están diseñadas específicamente para realizar operaciones de doblado en piezas largas, como tubos o barras de metal. La fuerza aplicada de manera horizontal facilita el doblado uniforme y controlado, sin necesidad de grandes esfuerzos manuales.
- Prensas Hidráulicas Horizontales de Ensamblaje: Utilizadas en procesos de ensamblaje de piezas, estas prensas aplican presión horizontal para unir componentes, como en el ensamblaje de estructuras metálicas o el encaje de componentes mecánicos.
- Prensas Hidráulicas Horizontales de Corte: Equipadas con herramientas de corte, estas prensas permiten realizar cortes precisos en materiales largos, como perfiles metálicos o plásticos. El movimiento horizontal facilita el corte a lo largo de piezas largas sin necesidad de realinearlas continuamente.
- Prensas Hidráulicas Horizontales de Enderezado: Se utilizan para enderezar piezas largas que han sufrido deformaciones, como barras o tubos metálicos, mediante la aplicación de presión horizontal controlada.
Aplicaciones de las Prensas Hidráulicas Horizontales
Las prensas hidráulicas horizontales son utilizadas en una amplia gama de sectores industriales debido a su capacidad para realizar diversas operaciones con precisión y control. Algunas de las aplicaciones más comunes incluyen:
- Industria Automotriz: En la fabricación de componentes automotrices, estas prensas son utilizadas para doblar y formar piezas metálicas largas, como ejes y marcos, así como para el ensamblaje de partes estructurales.
- Industria Aeroespacial: En este sector, las prensas hidráulicas horizontales juegan un papel clave en el conformado de piezas estructurales largas, como largueros y costillas de aeronaves, que requieren una gran precisión y consistencia en su fabricación.
- Industria de la Construcción: Son utilizadas para formar, cortar y ensamblar elementos estructurales metálicos, como vigas y columnas, que se emplean en la construcción de edificios y otras estructuras.
- Fabricación de Tuberías y Perfiles Metálicos: Las prensas hidráulicas horizontales se utilizan en el proceso de doblado y corte de tubos y perfiles metálicos de gran longitud, lo que es esencial para la producción de conductos y estructuras metálicas.
- Industria de Maquinaria Pesada: En la fabricación de componentes para maquinaria pesada, estas prensas se utilizan para formar y ensamblar piezas largas y robustas, como los chasis de máquinas industriales y agrícolas.
Ventajas de las Prensas Hidráulicas Horizontales
Las prensas hidráulicas horizontales ofrecen una serie de ventajas que las hacen ideales para una amplia variedad de aplicaciones industriales. Entre los beneficios más destacados se incluyen:
- Versatilidad: Estas prensas son extremadamente versátiles, ya que pueden ser utilizadas en una amplia gama de aplicaciones, desde el doblado y corte hasta el ensamblaje y enderezado de piezas metálicas.
- Fuerza y Precisión: Gracias al uso de sistemas hidráulicos, las prensas horizontales pueden generar grandes cantidades de fuerza con un control preciso, lo que garantiza la calidad y consistencia en el proceso de conformado.
- Capacidad para Trabajar con Piezas Largas: El diseño horizontal permite que estas prensas manejen piezas largas y rectas con mayor facilidad que las prensas verticales, lo que las hace ideales para la fabricación de componentes estructurales de gran tamaño.
- Automatización: Muchas prensas hidráulicas horizontales están equipadas con sistemas de control automatizados, como el control numérico computarizado (CNC), lo que permite realizar operaciones complejas con alta precisión y repetibilidad.
- Reducción del Esfuerzo Manual: El uso de una prensa hidráulica horizontal reduce significativamente el esfuerzo manual requerido para realizar operaciones como el doblado o el ensamblaje, lo que mejora la eficiencia y reduce la fatiga del operador.
Innovaciones Tecnológicas en las Prensas Hidráulicas Horizontales
El avance tecnológico ha jugado un papel fundamental en la evolución de las prensas hidráulicas horizontales, permitiendo mejoras significativas en su rendimiento y funcionalidad. Algunas de las innovaciones más notables incluyen:
- Integración de Sistemas CNC: La incorporación de sistemas CNC ha permitido automatizar el control de las prensas, mejorando la precisión y reduciendo los errores humanos. Esto es especialmente útil en aplicaciones que requieren conformado repetitivo y de alta precisión.
- Sensores de Presión y Control de Fuerza: Los sensores avanzados permiten monitorear la presión ejercida en tiempo real, lo que asegura que la fuerza aplicada sea la adecuada para cada tipo de material y operación.
- Sistemas de Seguridad Mejorados: La tecnología ha permitido el desarrollo de sistemas de seguridad avanzados, como barreras ópticas y controles de parada automática, que protegen a los operadores durante el funcionamiento de la prensa.
- Eficiencia Energética: Los nuevos sistemas hidráulicos están diseñados para ser más eficientes en términos de consumo de energía, lo que reduce el impacto ambiental y los costos operativos.
Mantenimiento de las Prensas Hidráulicas Horizontales
El mantenimiento regular de una prensa hidráulica horizontal es esencial para garantizar su funcionamiento óptimo y prolongar su vida útil. Entre los aspectos clave del mantenimiento se encuentran:
- Revisión de los Componentes Hidráulicos: Las bombas, cilindros y válvulas deben ser inspeccionados regularmente para detectar posibles fugas o fallos, lo que podría afectar el rendimiento de la prensa.
- Cambio de Fluido Hidráulico: El fluido hidráulico debe cambiarse periódicamente para asegurar que mantenga sus propiedades y evitar que la acumulación de impurezas afecte el rendimiento del sistema.
- Lubricación: Las partes móviles de la prensa, como guías y pistones, deben ser lubricadas adecuadamente para evitar el desgaste prematuro y garantizar un funcionamiento suave.
- Calibración y Ajuste de Controles: Los sistemas de control y sensores deben ser calibrados periódicamente para asegurar que la prensa funcione con precisión y que la fuerza aplicada sea la correcta.
Conclusión
Las prensas hidráulicas horizontales son herramientas fundamentales en muchas industrias debido a su capacidad para realizar operaciones de conformado de manera precisa, eficiente y versátil. Gracias a su diseño y los avances tecnológicos, estas prensas permiten trabajar con una gran variedad de materiales y realizar tareas que requieren un alto grado de precisión y control. Con el mantenimiento adecuado y el uso de tecnologías avanzadas, las prensas hidráulicas horizontales seguirán siendo una pieza clave en la fabricación industrial.
Prensas Horizontales Automáticas
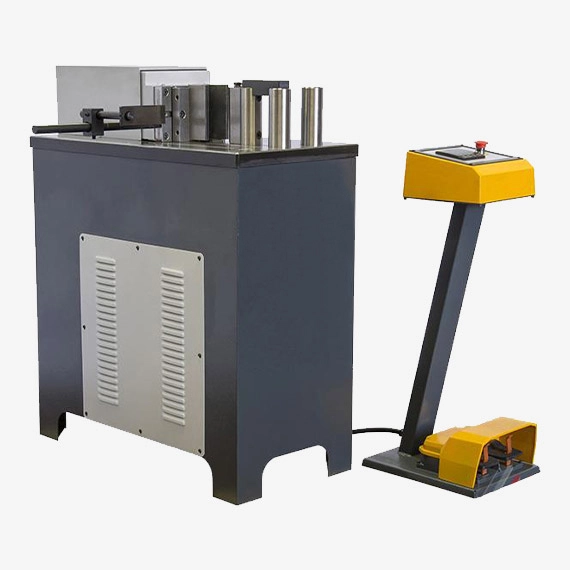
Las prensas horizontales automáticas representan una evolución avanzada en el mundo de las máquinas de conformado y manipulación de materiales, combinando la potencia de las prensas hidráulicas horizontales con tecnologías automatizadas para ofrecer un nivel superior de precisión, velocidad y eficiencia. Este tipo de prensas es fundamental en la producción en masa y en aplicaciones que requieren procesos repetitivos, como el estampado, doblado, corte, y ensamblaje de piezas metálicas y no metálicas.
Las prensas horizontales automáticas se destacan por su capacidad para operar de manera continua sin intervención humana, utilizando sistemas de control avanzados como el control numérico computarizado (CNC) para gestionar el proceso de conformado. Gracias a la automatización, estas máquinas pueden realizar operaciones complejas con una consistencia y velocidad que sería imposible alcanzar con prensas manuales o semi-automáticas.
En este análisis detallado, exploraremos las características, aplicaciones, beneficios y tecnologías asociadas con las prensas horizontales automáticas, además de su impacto en la industria moderna.
Características de las Prensas Horizontales Automáticas
Las prensas horizontales automáticas comparten muchas características con las prensas horizontales convencionales, pero con la adición de sistemas de automatización que permiten una mayor eficiencia y control. Algunas de las características más notables de estas prensas incluyen:
- Sistema de Control Automatizado: Utilizan un sistema de control CNC que permite programar y controlar con precisión cada aspecto del proceso, desde la cantidad de fuerza aplicada hasta el movimiento y posicionamiento de las piezas.
- Integración de Robots y Manipuladores: En muchas aplicaciones, las prensas automáticas están equipadas con robots o manipuladores que cargan y descargan las piezas automáticamente, lo que aumenta la velocidad de producción y reduce el tiempo de inactividad.
- Sensores de Monitoreo en Tiempo Real: Incorporan sensores que monitorean variables críticas como la presión, la posición y la temperatura, asegurando que la máquina opere de manera óptima y evitando errores o daños en las piezas.
- Configuración Modular: Algunas prensas horizontales automáticas están diseñadas de manera modular, lo que permite agregar o modificar componentes según las necesidades de producción, aumentando su flexibilidad.
- Capacidad de Personalización: Estas máquinas pueden ser configuradas y programadas para realizar múltiples tipos de operaciones, como corte, doblado o estampado, con diferentes tipos de materiales y formas, lo que las hace altamente versátiles.
Tipos de Prensas Horizontales Automáticas
Existen varios tipos de prensas horizontales automáticas, cada una diseñada para cumplir con diferentes requerimientos en la industria. Los tipos más comunes son:
- Prensas Automáticas de Doblado: Estas prensas están especializadas en doblar piezas metálicas, como láminas, tubos o perfiles, de manera precisa y rápida. La automatización permite realizar múltiples pliegues en una sola pasada, optimizando el tiempo de producción.
- Prensas Automáticas de Estampado: Utilizadas en la producción en masa, estas prensas aplican estampados en piezas metálicas, lo que es común en la fabricación de partes para la industria automotriz o electrodoméstica. El sistema automatizado asegura que cada pieza reciba un estampado uniforme y preciso.
- Prensas Automáticas de Corte: Estas prensas están equipadas con herramientas de corte que permiten realizar cortes precisos en piezas largas o en serie. Son utilizadas en la producción de perfiles metálicos, barras y otros componentes largos que requieren cortes exactos.
- Prensas Automáticas de Ensamblaje: En algunos sectores industriales, las prensas automáticas horizontales se utilizan para ensamblar componentes de manera precisa, aplicando presión en los puntos adecuados para unir piezas de metal o plástico.
Aplicaciones de las Prensas Horizontales Automáticas
Gracias a su capacidad para realizar una variedad de operaciones de manera automatizada y con alta precisión, las prensas horizontales automáticas son utilizadas en diversas industrias y para diferentes aplicaciones, como:
- Industria Automotriz: Estas prensas son esenciales en la fabricación de componentes automotrices, desde el estampado de partes del chasis hasta el ensamblaje de piezas estructurales. La automatización asegura que los componentes sean fabricados con alta precisión y uniformidad.
- Industria de Electrodomésticos: En la producción de electrodomésticos como lavadoras, secadoras y refrigeradores, estas prensas son utilizadas para conformar las carcasas y otras piezas metálicas que requieren ser cortadas o dobladas de manera uniforme.
- Aeroespacial: En este sector, las prensas horizontales automáticas son utilizadas para producir piezas estructurales que deben cumplir con estrictas tolerancias y altos estándares de calidad. La precisión de estas máquinas es clave para garantizar la seguridad y funcionalidad de los componentes aeroespaciales.
- Industria de la Construcción: Estas prensas son utilizadas para fabricar perfiles y componentes estructurales metálicos que se emplean en la construcción de edificios e infraestructuras. La automatización permite producir grandes volúmenes de piezas en un corto período de tiempo.
- Producción de Tuberías y Conductos: Las prensas horizontales automáticas son ideales para el doblado y corte de tuberías y conductos metálicos, lo que es esencial en la industria de la energía, la minería y la construcción.
Ventajas de las Prensas Horizontales Automáticas
Las prensas horizontales automáticas ofrecen una serie de ventajas significativas en comparación con las prensas manuales o semiautomáticas, entre las que destacan:
- Mayor Precisión y Consistencia: El uso de sistemas de control CNC y sensores avanzados permite realizar operaciones con un alto grado de precisión, lo que garantiza que cada pieza producida cumpla con los mismos estándares de calidad.
- Aumento de la Productividad: Al ser completamente automatizadas, estas prensas pueden operar durante largos períodos de tiempo sin intervención humana, lo que incrementa la velocidad de producción y reduce los tiempos de inactividad.
- Reducción de Errores Humanos: La automatización elimina el factor humano en tareas repetitivas, reduciendo la posibilidad de errores y mejorando la eficiencia general del proceso de fabricación.
- Mayor Seguridad: Las prensas automáticas están diseñadas con sistemas de seguridad avanzados que protegen a los operadores y evitan accidentes durante el proceso de conformado. Sensores y paradas de emergencia garantizan que la máquina se detenga automáticamente en caso de una falla.
- Flexibilidad en la Producción: Las prensas horizontales automáticas pueden ser programadas para realizar diferentes tipos de operaciones en función de las necesidades del cliente, lo que permite una mayor flexibilidad en la producción sin necesidad de cambiar de máquina.
Tecnologías Asociadas a las Prensas Horizontales Automáticas
La automatización de las prensas horizontales ha sido posible gracias a una serie de avances tecnológicos que han permitido mejorar su rendimiento, precisión y seguridad. Entre las principales tecnologías asociadas con estas prensas se incluyen:
- Control Numérico Computarizado (CNC): El CNC es una tecnología clave en las prensas automáticas, ya que permite programar y controlar cada movimiento de la máquina con una precisión milimétrica. Esto es esencial en operaciones que requieren conformado repetitivo y de alta precisión.
- Sistemas de Visión Artificial: Algunas prensas automáticas están equipadas con cámaras y sistemas de visión artificial que permiten monitorear el proceso en tiempo real. Esto asegura que la máquina pueda detectar y corregir cualquier irregularidad en el conformado sin detener el proceso.
- Robótica Industrial: La integración de brazos robóticos o manipuladores automatizados permite que las prensas horizontales automáticas realicen tareas adicionales, como la carga y descarga de piezas, sin intervención humana, lo que incrementa aún más la eficiencia.
- Sensores Inteligentes: Los sensores juegan un papel crucial en el monitoreo de variables críticas como la presión, temperatura y posición de las piezas, asegurando que la prensa opere bajo condiciones óptimas en todo momento.
- Sistemas de Seguridad Avanzados: Las prensas horizontales automáticas están equipadas con sistemas de seguridad como paradas de emergencia, barreras ópticas y enclavamientos que protegen a los operadores y garantizan un entorno de trabajo seguro.
Mantenimiento de las Prensas Horizontales Automáticas
El mantenimiento adecuado de las prensas horizontales automáticas es crucial para garantizar su correcto funcionamiento y prolongar su vida útil. Las operaciones de mantenimiento deben incluir:
- Inspección Regular de los Componentes: Los sistemas hidráulicos, eléctricos y mecánicos deben ser inspeccionados regularmente para detectar posibles fallos o desgastes que puedan afectar el rendimiento de la prensa.
- Cambio de Fluido Hidráulico: El fluido hidráulico debe ser reemplazado periódicamente para asegurar que mantenga sus propiedades y no cause fallos en los componentes del sistema.
- Actualización de Software: El sistema de control CNC y otros software asociados deben actualizarse con regularidad para garantizar que la máquina funcione con las últimas mejoras y correcciones de errores.
- Calibración de Sensores: Los sensores deben ser calibrados de manera periódica para asegurar que proporcionen lecturas precisas y que la máquina opere bajo los parámetros adecuados.
Innovaciones Futuras en las Prensas Horizontales Automáticas
La evolución tecnológica continúa mejorando las capacidades de las prensas horizontales automáticas. Algunas tendencias e innovaciones que se esperan en el futuro incluyen:
- Inteligencia Artificial (IA): La incorporación de sistemas de IA permitirá que las prensas automáticas sean aún más eficientes, capaces de aprender y optimizar sus operaciones de manera autónoma.
- Interconexión a la Industria 4.0: Las prensas horizontales automáticas podrán integrarse en sistemas de producción conectados, donde cada máquina se comunica entre sí y optimiza el proceso de producción en tiempo real.
- Mayor Eficiencia Energética: Las nuevas generaciones de prensas buscarán reducir el consumo energético mediante el uso de sistemas hidráulicos más eficientes y el aprovechamiento de energías renovables en el proceso de fabricación.
Conclusión
Las prensas horizontales automáticas representan un avance significativo en la fabricación industrial, ofreciendo una combinación de velocidad, precisión y eficiencia que es esencial en la producción moderna. Gracias a la integración de tecnologías avanzadas y la automatización, estas máquinas no solo mejoran la calidad de los productos, sino que también aumentan la productividad y reducen los costos operativos. A medida que las tecnologías continúan evolucionando, las prensas horizontales automáticas seguirán desempeñando un papel crucial en el futuro de la manufactura industrial.
Prensas para el Curvado
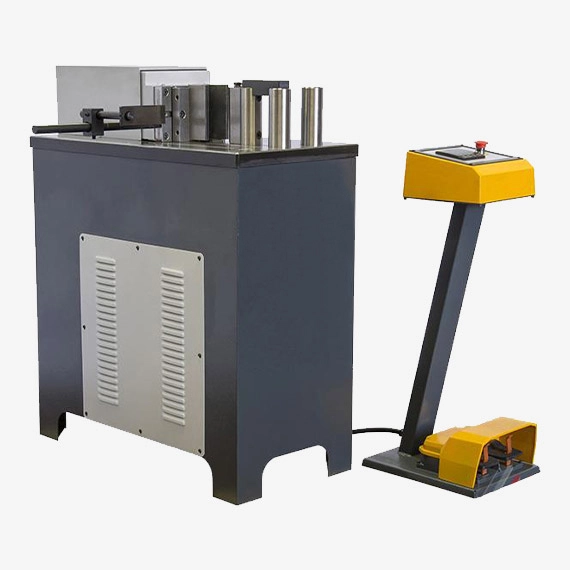
Las prensas para el curvado son máquinas industriales especializadas en la deformación controlada de materiales, particularmente de metales, para darles una forma curva o angular específica. Estas prensas son fundamentales en industrias como la automotriz, la construcción, la fabricación de tuberías, y la producción de estructuras metálicas, donde es necesario doblar y moldear piezas con alta precisión.
El proceso de curvado implica aplicar una fuerza considerable sobre el material, generalmente mediante un pistón hidráulico, que empuja el metal contra un dado o matriz para generar la curva deseada. Estas máquinas pueden curvar una variedad de materiales, como acero, aluminio, cobre y otros metales, en diferentes grosores y tamaños, lo que las hace versátiles y adaptables a múltiples aplicaciones.
Este análisis se centrará en las características, tipos, aplicaciones, beneficios y tecnologías asociadas con las prensas para el curvado, así como su impacto en la fabricación moderna.
Características de las Prensas para el Curvado
Las prensas para el curvado están diseñadas para realizar procesos de doblado de manera eficiente y precisa. Algunas de las características clave de estas prensas incluyen:
- Sistema de Fuerza Controlada: Las prensas de curvado aplican una fuerza ajustable sobre el material, permitiendo doblar metales de diferentes grosores sin comprometer su integridad estructural.
- Diseño Robusto: Están construidas con materiales altamente resistentes para soportar las enormes presiones generadas durante el proceso de curvado, lo que garantiza su durabilidad y rendimiento a largo plazo.
- Capacidad de Curvado en Múltiples Ángulos: Estas prensas pueden configurarse para realizar curvados en una amplia gama de ángulos, desde simples pliegues hasta formas más complejas, dependiendo de las necesidades de producción.
- Flexibilidad en el Uso de Diferentes Materiales: Estas máquinas están diseñadas para trabajar con una variedad de metales y aleaciones, lo que las hace versátiles en diferentes aplicaciones industriales.
- Automatización y Control Numérico: Muchas prensas de curvado modernas están equipadas con sistemas de control numérico computarizado (CNC), que permite automatizar el proceso y garantizar que cada curva sea realizada con precisión y consistencia.
Tipos de Prensas para el Curvado
Existen varios tipos de prensas para el curvado, cada una con características y aplicaciones específicas según el tipo de material y el tipo de curva que se desea realizar. Entre las más comunes se encuentran:
- Prensas de Curvado de Tubos: Especialmente diseñadas para doblar tubos de metal, estas prensas son ampliamente utilizadas en la fabricación de tuberías para industrias como la automotriz, la energética y la de construcción. Las prensas de curvado de tubos permiten crear curvas precisas sin aplastar o deformar el diámetro del tubo.
- Prensas de Curvado de Perfiles: Utilizadas para doblar perfiles metálicos como vigas, canales o ángulos, estas prensas son esenciales en la construcción y fabricación de estructuras metálicas. Las prensas de curvado de perfiles permiten formar componentes estructurales curvados sin afectar su resistencia.
- Prensas de Curvado de Láminas Metálicas: Estas prensas son ideales para doblar láminas de metal en diferentes ángulos y formas. Son comúnmente utilizadas en la producción de carcasas, paneles y otras piezas planas que requieren pliegues o curvas precisas.
- Prensas de Curvado Rotativo: Este tipo de prensas utiliza un rodillo que rota sobre el material para crear curvas suaves y continuas. Son ideales para aplicaciones donde se requieren grandes radios de curvatura y formas complejas.
- Prensas de Curvado de Tres Rodillos: Estas prensas son comúnmente utilizadas para curvar grandes placas y perfiles. Utilizan tres rodillos ajustables para aplicar presión gradual sobre el material, logrando una curvatura uniforme sin necesidad de aplicar una gran fuerza en un solo punto.
Aplicaciones de las Prensas para el Curvado
Las prensas para el curvado tienen un amplio rango de aplicaciones en múltiples sectores industriales, y su versatilidad las convierte en una herramienta esencial para cualquier tipo de fabricación que requiera la deformación de materiales metálicos. Algunas de las aplicaciones más comunes incluyen:
- Fabricación de Estructuras Metálicas: En la construcción de puentes, edificios y otras estructuras, las prensas para el curvado son utilizadas para moldear vigas, columnas y otros componentes estructurales metálicos que requieren formas curvadas para distribuir cargas y mejorar la resistencia.
- Industria Automotriz: En este sector, las prensas de curvado se utilizan para fabricar componentes como marcos de chasis, barras estabilizadoras, sistemas de escape y otras piezas que deben ser curvadas con alta precisión para cumplir con los estándares de seguridad y funcionalidad.
- Producción de Tuberías y Conductos: Las prensas de curvado son fundamentales en la fabricación de tuberías para aplicaciones industriales y comerciales, como los sistemas de calefacción, ventilación y aire acondicionado (HVAC), la distribución de agua y gas, y la conducción de fluidos en plantas industriales.
- Aeroespacial: En la industria aeroespacial, las prensas para el curvado se utilizan para dar forma a componentes estructurales ligeros pero resistentes, como los marcos de las alas, los fuselajes y otros elementos curvados que deben soportar fuerzas extremas sin comprometer la seguridad de la aeronave.
- Industria Energética: Las prensas de curvado son esenciales en la fabricación de conductos y estructuras utilizadas en la industria energética, como los soportes para paneles solares, las estructuras para turbinas eólicas y las tuberías de petróleo y gas.
Ventajas de las Prensas para el Curvado
Las prensas para el curvado ofrecen múltiples ventajas, que las hacen una herramienta indispensable en la manufactura moderna:
- Alta Precisión: El uso de sistemas de control CNC y otros mecanismos automatizados permite lograr curvas precisas y consistentes, reduciendo al mínimo los errores en la producción.
- Versatilidad: Estas prensas pueden trabajar con una amplia gama de materiales y realizar curvados en diferentes formas y ángulos, lo que las hace útiles para diversas aplicaciones industriales.
- Reducción de Desperdicio: Gracias a la precisión en el proceso de curvado, se minimiza la cantidad de material desperdiciado, lo que no solo reduce costos, sino que también mejora la sostenibilidad del proceso de producción.
- Mayor Eficiencia de Producción: Las prensas automáticas o semi-automáticas de curvado permiten realizar operaciones rápidas y repetitivas sin comprometer la calidad del producto final, lo que resulta en un aumento significativo de la productividad.
- Mejor Integridad Estructural: El proceso de curvado, cuando se realiza de manera controlada y precisa, no afecta la resistencia ni la integridad del material, lo que es esencial en aplicaciones donde la durabilidad es crítica.
Tecnologías Utilizadas en las Prensas para el Curvado
La evolución de las prensas para el curvado ha sido impulsada por el desarrollo de tecnologías que han mejorado tanto su rendimiento como su precisión. Entre las principales tecnologías utilizadas se incluyen:
- Control Numérico Computarizado (CNC): El CNC permite programar con precisión el proceso de curvado, asegurando que se cumplan las especificaciones exactas del diseño sin necesidad de intervención humana constante.
- Sistemas de Visión Artificial: Algunas prensas modernas utilizan cámaras y sistemas de visión artificial para monitorear el proceso en tiempo real y ajustar automáticamente el curvado si detectan desviaciones en la forma o el ángulo deseado.
- Sistemas Hidráulicos Avanzados: Los sistemas hidráulicos de alta precisión permiten aplicar la fuerza necesaria de manera controlada, asegurando un curvado uniforme y sin deformaciones no deseadas.
- Software de Simulación: Antes de realizar el proceso de curvado, algunas prensas permiten realizar simulaciones virtuales que muestran cómo se comportará el material bajo diferentes condiciones, lo que ayuda a evitar errores y optimizar el proceso.
Mantenimiento de las Prensas para el Curvado
El mantenimiento regular de las prensas para el curvado es esencial para asegurar su correcto funcionamiento y prolongar su vida útil. Entre las tareas de mantenimiento más comunes se incluyen:
- Lubricación de Componentes Móviles: Los componentes móviles, como los rodillos y pistones, deben ser lubricados regularmente para evitar el desgaste prematuro y asegurar un movimiento suave durante el proceso de curvado.
- Inspección de Herramientas y Matrices: Las matrices utilizadas para curvar el material deben ser inspeccionadas regularmente para asegurar que no presenten daños o desgaste, lo que podría afectar la precisión del curvado.
- Revisión de Sistemas Hidráulicos: Los sistemas hidráulicos deben ser revisados periódicamente para asegurar que no existan fugas y que la presión aplicada sea la adecuada para cada tipo de material.
- Calibración de Sensores y Sistemas de Control: Los sensores que monitorean el proceso de curvado, así como los sistemas de control CNC, deben ser calibrados regularmente para mantener su precisión y fiabilidad.
Conclusión
Las prensas para el curvado son una herramienta fundamental en la industria moderna, permitiendo realizar deformaciones precisas y controladas en una amplia variedad de materiales. Gracias a su versatilidad, eficiencia y capacidad de automatización, estas prensas continúan desempeñando un papel crucial en sectores industriales clave como la construcción, la automoción, la aeroespacial y la fabricación de tuberías. A medida que las tecnologías avanzan, se espera que las prensas para el curvado sigan mejorando en términos de precisión, velocidad y eficiencia, consolidándose como un pilar indispensable en la manufactura avanzada.
Bordonadora de Chapa
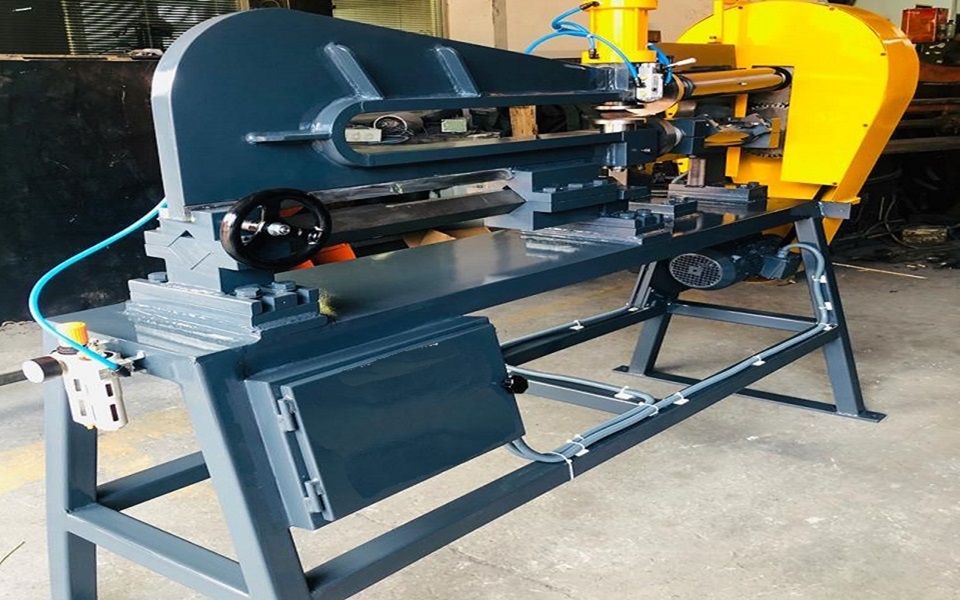
La bordonadora de chapa es una máquina especializada utilizada en la industria metalúrgica para crear bordes o refuerzos en láminas metálicas. Estos bordes son esenciales para aumentar la resistencia estructural de la pieza, mejorar su acabado estético y preparar las piezas para el ensamblaje o para otros procesos de manufactura. Este tipo de equipo es muy común en sectores como la fabricación de electrodomésticos, la industria automotriz, la construcción y la producción de equipos industriales, donde se requiere manipular láminas de metal con precisión y eficiencia.
El proceso de bordonado consiste en doblar o engrosar los bordes de una chapa metálica, lo que añade rigidez sin incrementar considerablemente el peso del componente. Además de mejorar las propiedades mecánicas de la pieza, este proceso también permite evitar bordes afilados, facilitando su manipulación y ensamblaje. A continuación, exploraremos en detalle las características, aplicaciones, tipos y beneficios de las bordonadoras de chapa.
Características de la Bordonadora de Chapa
Las bordonadoras de chapa están diseñadas para cumplir con los requisitos de precisión y durabilidad que demanda la industria. Entre las características más destacadas se encuentran:
- Diseño Robusto: Estas máquinas están fabricadas con materiales resistentes que soportan el desgaste continuo, lo que garantiza un rendimiento prolongado y confiable, incluso en ambientes industriales intensivos.
- Versatilidad: Las bordonadoras pueden trabajar con una variedad de metales, desde acero y aluminio hasta cobre y latón, en diferentes grosores y tamaños de chapa. Esto las hace adecuadas para una amplia gama de aplicaciones industriales.
- Control Preciso del Proceso: La capacidad de ajustar los parámetros de operación, como la presión y la velocidad, permite obtener bordes uniformes y precisos en la chapa metálica, evitando deformaciones no deseadas.
- Automatización y Control CNC: Muchas bordonadoras modernas están equipadas con sistemas de control numérico computarizado (CNC), lo que permite automatizar el proceso y lograr una alta precisión en las operaciones repetitivas. Esto es especialmente útil en la producción en masa.
- Diversos Tipos de Matrices: Estas máquinas pueden utilizar una variedad de matrices intercambiables, lo que facilita la creación de diferentes tipos de bordes según las necesidades específicas de cada proyecto.
Tipos de Bordonadoras de Chapa
Existen varios tipos de bordonadoras de chapa, diseñadas para adaptarse a las necesidades específicas de cada aplicación industrial. Entre los principales tipos se incluyen:
- Bordonadora Manual: Este tipo de bordonadora es operada manualmente, lo que la hace ideal para trabajos de pequeña escala o aplicaciones que no requieren una gran velocidad de producción. Son comunes en talleres artesanales y en trabajos personalizados donde la precisión es clave.
- Bordonadora Automática: Estas máquinas están equipadas con sistemas de automatización que permiten realizar el proceso de bordonado de manera rápida y precisa, sin la intervención constante del operario. Son ideales para líneas de producción que requieren alta eficiencia y consistencia.
- Bordonadora Hidráulica: Utilizan un sistema hidráulico para aplicar la presión necesaria en el proceso de bordonado. Esto permite manipular chapas metálicas más gruesas y duras, garantizando un borde limpio y preciso. Su uso es común en la fabricación de grandes componentes industriales.
- Bordonadora CNC: Controladas por computadora, estas bordonadoras permiten un control exacto de todos los parámetros del proceso, desde el ángulo y el espesor del borde hasta la velocidad de operación. Son esenciales para la producción en serie de componentes que requieren una precisión milimétrica.
- Bordonadora de Rodillo: Este tipo utiliza rodillos para aplicar la fuerza sobre la chapa metálica y crear el borde. Es ideal para trabajos que requieren bordes continuos y curvos, como en la fabricación de cilindros o componentes tubulares.
Aplicaciones de la Bordonadora de Chapa
La bordonadora de chapa se utiliza en una amplia variedad de aplicaciones industriales, donde se requiere reforzar bordes o mejorar el acabado de las piezas metálicas. Algunas de las aplicaciones más comunes incluyen:
- Fabricación de Electrodomésticos: En la producción de carcasas metálicas para electrodomésticos como lavadoras, refrigeradores y hornos, las bordonadoras de chapa son esenciales para crear bordes lisos y reforzados, lo que mejora tanto la seguridad como la durabilidad de los productos.
- Industria Automotriz: Las bordonadoras de chapa son utilizadas para fabricar piezas como paneles de carrocería, guardabarros y otras partes metálicas que requieren bordes reforzados para soportar las condiciones extremas a las que están sometidos los vehículos.
- Fabricación de Conductos: En la producción de sistemas de ventilación y conductos, las bordonadoras son esenciales para crear bordes que permitan el ensamblaje de las diferentes secciones de los conductos sin riesgo de fugas o deformaciones.
- Industria Aeroespacial: En la fabricación de componentes estructurales de aeronaves, las bordonadoras de chapa son utilizadas para reforzar piezas críticas, asegurando que los bordes no se debiliten bajo las tensiones mecánicas que experimentan durante el vuelo.
- Construcción: Las bordonadoras son esenciales en la fabricación de elementos estructurales como marcos de ventanas y puertas, así como en la producción de chapas metálicas para revestimientos y techos, donde los bordes reforzados mejoran la resistencia al impacto y a las condiciones climáticas adversas.
Beneficios de Utilizar una Bordonadora de Chapa
El uso de una bordonadora de chapa ofrece varios beneficios que la hacen una herramienta indispensable en la manufactura moderna. Estos incluyen:
- Mayor Resistencia Estructural: Al crear bordes reforzados en las láminas metálicas, las bordonadoras aumentan la resistencia del material sin necesidad de aumentar su grosor o peso, lo que es crucial en aplicaciones donde se requiere ligereza y durabilidad.
- Mejora Estética: El proceso de bordonado también contribuye a mejorar el acabado superficial de las piezas, eliminando bordes afilados y proporcionando un aspecto más pulido y profesional.
- Facilidad de Ensamblaje: Los bordes creados por una bordonadora permiten un mejor acoplamiento entre las diferentes piezas de un ensamblaje, facilitando el montaje y asegurando una unión más fuerte y duradera.
- Reducción de Costos: Al mejorar la resistencia de la chapa metálica sin la necesidad de usar materiales más gruesos, las bordonadoras ayudan a reducir los costos de producción. Además, el proceso automatizado minimiza los errores y el desperdicio de material.
- Versatilidad en los Procesos: Gracias a la posibilidad de cambiar las matrices y ajustar los parámetros de operación, las bordonadoras son extremadamente versátiles y pueden adaptarse a una amplia variedad de proyectos y tipos de chapa.
Tecnologías Utilizadas en las Bordonadoras de Chapa
Las bordonadoras han evolucionado significativamente gracias a los avances tecnológicos que han mejorado su precisión, velocidad y facilidad de uso. Entre las principales tecnologías implementadas en las bordonadoras modernas se incluyen:
- Control Numérico Computarizado (CNC): El CNC permite programar con precisión los movimientos y parámetros del proceso de bordonado, asegurando que las piezas producidas cumplan exactamente con las especificaciones deseadas. Esto es especialmente útil en la producción en masa.
- Sistemas Hidráulicos de Alta Precisión: Las bordonadoras hidráulicas son capaces de aplicar una presión uniforme y constante sobre la chapa, lo que garantiza un borde limpio y sin deformaciones, incluso en materiales más gruesos o duros.
- Sistemas de Medición por Láser: Algunas bordonadoras modernas están equipadas con sistemas de medición láser que controlan el proceso en tiempo real, asegurando que cada borde cumpla con los estándares de calidad establecidos.
- Software de Simulación: Antes de realizar el proceso de bordonado, el software de simulación permite prever cómo se comportará la chapa bajo la presión de la máquina, lo que ayuda a optimizar el proceso y reducir los errores.
Mantenimiento de las Bordonadoras de Chapa
Para garantizar el rendimiento y la longevidad de las bordonadoras de chapa, es esencial realizar un mantenimiento regular. Algunas de las tareas más comunes incluyen:
- Lubricación de Componentes Móviles: Los rodillos y otros componentes móviles deben ser lubricados regularmente para evitar el desgaste y asegurar un movimiento suave.
- Inspección de Herramientas y Matrices: Las matrices que se utilizan para formar los bordes deben ser inspeccionadas regularmente para detectar signos de desgaste que puedan afectar la calidad del bordonado.
- Calibración de Sensores y Sistemas de Control: Los sensores de medición y los sistemas CNC deben ser recalibrados periódicamente para garantizar que los bordes sean siempre precisos y uniformes.
- Revisión del Sistema Hidráulico: En las bordonadoras hidráulicas, es importante revisar los niveles de aceite y asegurarse de que no haya fugas en el sistema para mantener la presión correcta durante el proceso.
Conclusión
Las bordonadoras de chapa desempeñan un papel crucial en la manufactura moderna, permitiendo la producción de piezas metálicas con bordes reforzados que cumplen con altos estándares de resistencia y calidad. Su versatilidad, precisión y capacidad para trabajar con una variedad de materiales las convierten en herramientas esenciales en sectores industriales clave. Con el avance de la tecnología, estas máquinas continúan mejorando en términos de automatización, eficiencia y control, asegurando su lugar como un componente vital en la producción industrial.
Rebordeadora Hidráulica
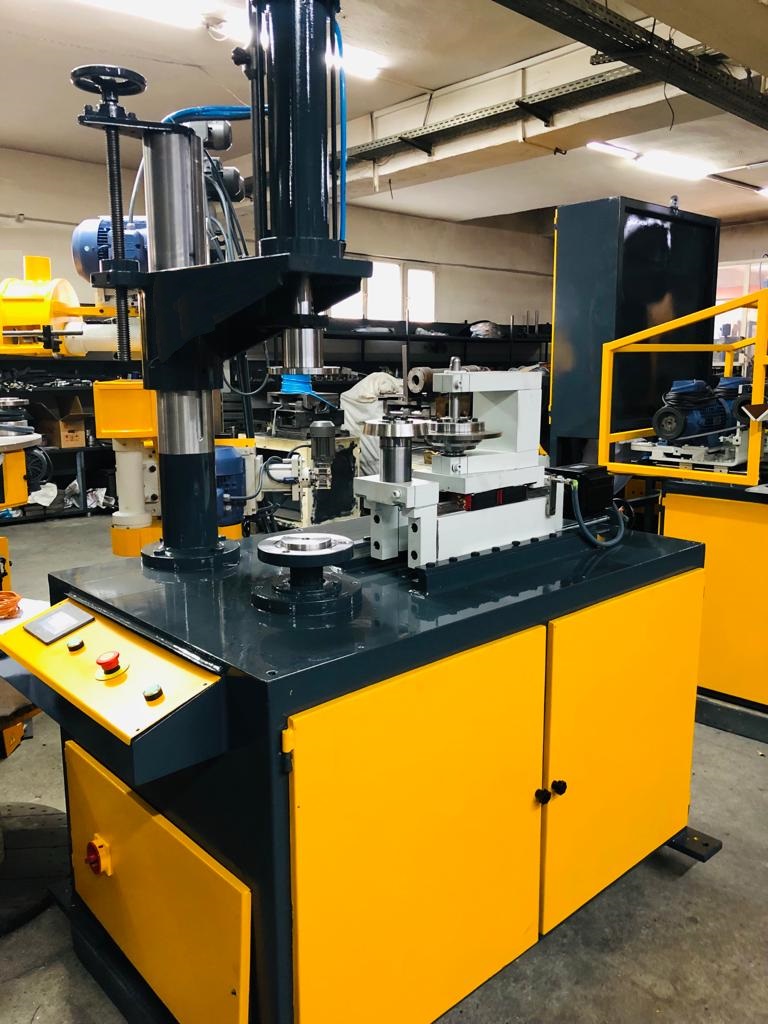
Las rebordeadoras hidráulicas son máquinas especializadas diseñadas para realizar el proceso de rebordear o formar un borde en láminas metálicas. Este proceso es esencial para fortalecer las piezas, mejorar su estética y facilitar el ensamblaje de componentes metálicos. Utilizan sistemas hidráulicos para aplicar la presión necesaria y moldear los bordes de la chapa metálica con precisión y consistencia. Las rebordeadoras hidráulicas son muy utilizadas en industrias como la automotriz, la fabricación de electrodomésticos, la construcción y la producción de componentes industriales.
El proceso de rebordeado es fundamental para otorgar mayor rigidez a las piezas metálicas, sin incrementar su peso de manera significativa. Además de sus beneficios estructurales, también permite un acabado más limpio y uniforme, eliminando bordes afilados que podrían ser peligrosos o difíciles de manipular.
A continuación, exploraremos en detalle las características, aplicaciones, tipos y ventajas de las rebordeadoras hidráulicas, así como su impacto en la eficiencia de la manufactura moderna.
Características de la Rebordeadora Hidráulica
Las rebordeadoras hidráulicas están equipadas con características avanzadas que les permiten cumplir con los exigentes estándares de la industria. Algunas de las principales características son:
- Sistema Hidráulico de Alta Potencia: El uso de un sistema hidráulico asegura que la máquina pueda aplicar una presión uniforme y controlada durante el proceso de rebordeado, lo que es fundamental para trabajar con materiales de diferentes grosores y durezas.
- Precisión y Control: Gracias a la incorporación de sistemas de control, muchas rebordeadoras hidráulicas permiten ajustar con precisión la presión aplicada, así como la velocidad del proceso, garantizando un acabado perfecto en cada borde.
- Capacidad para Trabajar con Diferentes Materiales: Las rebordeadoras hidráulicas pueden manipular una variedad de metales, como acero, aluminio, cobre, entre otros, lo que las convierte en herramientas extremadamente versátiles para múltiples industrias.
- Automatización y Sistemas CNC: En las versiones más avanzadas, estas máquinas pueden estar equipadas con control numérico computarizado (CNC), lo que permite la automatización del proceso, reduciendo la intervención humana y mejorando la precisión en operaciones repetitivas.
- Alta Durabilidad y Resistencia: Estas máquinas están diseñadas para soportar un uso continuo y exigente, gracias a su construcción robusta y a la calidad de los materiales con los que están fabricadas.
Tipos de Rebordeadora Hidráulica
Existen varios tipos de rebordeadoras hidráulicas en el mercado, diseñadas para satisfacer diferentes necesidades de producción y requerimientos técnicos. Entre los tipos más comunes se encuentran:
- Rebordeadora Hidráulica Manual: En estas máquinas, el operario controla el proceso de forma manual, ajustando los parámetros y operando la máquina según sea necesario. Son adecuadas para trabajos de menor escala o personalizados, donde se requiere un alto grado de control manual.
- Rebordeadora Hidráulica Automática: Estas rebordeadoras están automatizadas y permiten procesar grandes volúmenes de chapa con mínima intervención humana. Son ideales para líneas de producción que requieren alta eficiencia y consistencia en los resultados.
- Rebordeadora Hidráulica CNC: Equipadas con sistemas de control computarizado, estas máquinas permiten programar con precisión todos los aspectos del proceso, asegurando que las piezas sean rebordeadas con un alto grado de exactitud. Son esenciales en aplicaciones donde se requiere una precisión milimétrica.
- Rebordeadora Hidráulica de Rodillo: Este tipo de rebordeadoras utiliza rodillos para aplicar la presión sobre los bordes de la chapa, lo que resulta en un proceso continuo y eficiente, ideal para la fabricación de componentes cilíndricos o tubulares.
Aplicaciones de la Rebordeadora Hidráulica
Las rebordeadoras hidráulicas tienen una amplia variedad de aplicaciones industriales, especialmente en sectores que requieren precisión y eficiencia en el tratamiento de láminas metálicas. Entre las aplicaciones más comunes se encuentran:
- Industria Automotriz: Las rebordeadoras hidráulicas son utilizadas para fabricar componentes como paneles de carrocería, piezas estructurales y partes interiores, donde se necesita un acabado limpio y bordes reforzados para asegurar la integridad de las piezas.
- Fabricación de Electrodomésticos: En la producción de electrodomésticos, como refrigeradores, estufas y lavadoras, las rebordeadoras son esenciales para crear bordes uniformes y seguros en las carcasas metálicas.
- Fabricación de Conductos y Tubos: Las rebordeadoras son ampliamente utilizadas en la fabricación de conductos de ventilación, sistemas de escape y otros componentes tubulares, donde los bordes rebordeados mejoran la integridad estructural y la facilidad de ensamblaje.
- Construcción: En la industria de la construcción, las rebordeadoras hidráulicas son utilizadas para fabricar elementos estructurales, marcos de ventanas y puertas, y otros componentes metálicos que requieren bordes reforzados para mayor resistencia y seguridad.
- Industria Aeroespacial: En la fabricación de piezas para aeronaves, las rebordeadoras hidráulicas permiten crear componentes ligeros pero fuertes, asegurando que los bordes de las piezas cumplan con los estrictos requisitos de seguridad y resistencia.
Beneficios de Utilizar una Rebordeadora Hidráulica
El uso de una rebordeadora hidráulica en procesos industriales ofrece múltiples beneficios que van más allá de la simple creación de bordes en láminas metálicas. Entre los principales beneficios destacan:
- Mayor Precisión y Uniformidad: Gracias a su sistema hidráulico, estas máquinas garantizan que cada borde sea rebordeado de manera uniforme, lo que es crucial en aplicaciones donde se requiere una alta consistencia en la producción.
- Reducción del Tiempo de Producción: Al automatizar el proceso de rebordeado, las rebordeadoras hidráulicas permiten producir grandes volúmenes de piezas en un tiempo reducido, aumentando la eficiencia y reduciendo costos operativos.
- Aumento de la Resistencia Estructural: El rebordeado refuerza los bordes de las piezas metálicas, mejorando su resistencia a la deformación y al desgaste, lo que es esencial en aplicaciones donde las piezas están sometidas a altas tensiones.
- Mejora Estética: Además de sus beneficios estructurales, el proceso de rebordeado también mejora el acabado visual de las piezas, eliminando bordes afilados y proporcionando un aspecto más limpio y profesional.
- Versatilidad en el Manejo de Materiales: Las rebordeadoras hidráulicas pueden trabajar con una amplia variedad de materiales metálicos, desde acero y aluminio hasta cobre, lo que las hace adecuadas para diferentes sectores industriales.
Tecnología en las Rebordeadoras Hidráulicas
Las rebordeadoras hidráulicas han evolucionado con el tiempo, integrando tecnologías que mejoran su precisión, eficiencia y facilidad de uso. Algunas de las tecnologías más destacadas incluyen:
- Control Numérico Computarizado (CNC): La integración de sistemas CNC permite a las rebordeadoras programar con exactitud todos los parámetros del proceso, mejorando la precisión y la repetibilidad, especialmente en la producción en masa.
- Sistemas de Medición por Láser: Algunas máquinas están equipadas con sistemas de medición láser que monitorizan en tiempo real el proceso de rebordeado, asegurando que cada pieza cumpla con las especificaciones exactas.
- Software de Simulación: Antes de ejecutar el proceso, los operarios pueden simular el comportamiento de la chapa bajo presión, lo que ayuda a optimizar el proceso y minimizar errores.
- Sistemas Hidráulicos de Alta Precisión: Los sistemas hidráulicos modernos aplican una presión constante y controlada, lo que es esencial para obtener bordes uniformes y sin deformaciones.
Mantenimiento de las Rebordeadoras Hidráulicas
El mantenimiento adecuado de una rebordeadora hidráulica es crucial para garantizar su rendimiento y longevidad. Algunas de las tareas de mantenimiento más importantes incluyen:
- Lubricación de Componentes Móviles: Es esencial lubricar regularmente los rodillos y otras partes móviles para evitar el desgaste y asegurar un funcionamiento suave.
- Inspección de Herramientas y Matrices: Las matrices deben ser inspeccionadas periódicamente para asegurar que no haya desgaste que pueda comprometer la calidad del rebordeado.
- Revisión del Sistema Hidráulico: El sistema hidráulico debe ser revisado regularmente para asegurarse de que no haya fugas y de que la presión se mantenga constante durante el proceso.
- Calibración de los Sistemas de Control: Los sistemas CNC y los sensores de medición deben ser recalibrados periódicamente para garantizar la precisión en cada operación.
Conclusión
Las rebordeadoras hidráulicas son una pieza clave en la fabricación de componentes metálicos, ofreciendo precisión, eficiencia y versatilidad. Su capacidad para trabajar con una variedad de materiales y aplicaciones las convierte en una herramienta indispensable en sectores como la automoción, la construcción, la aeroespacial y la producción de electrodomésticos. A medida que la tecnología continúa avanzando, se espera que las rebordeadoras hidráulicas sigan evolucionando, proporcionando mayor automatización, precisión y eficiencia en los procesos de manufactura.
Prensa de Embutido
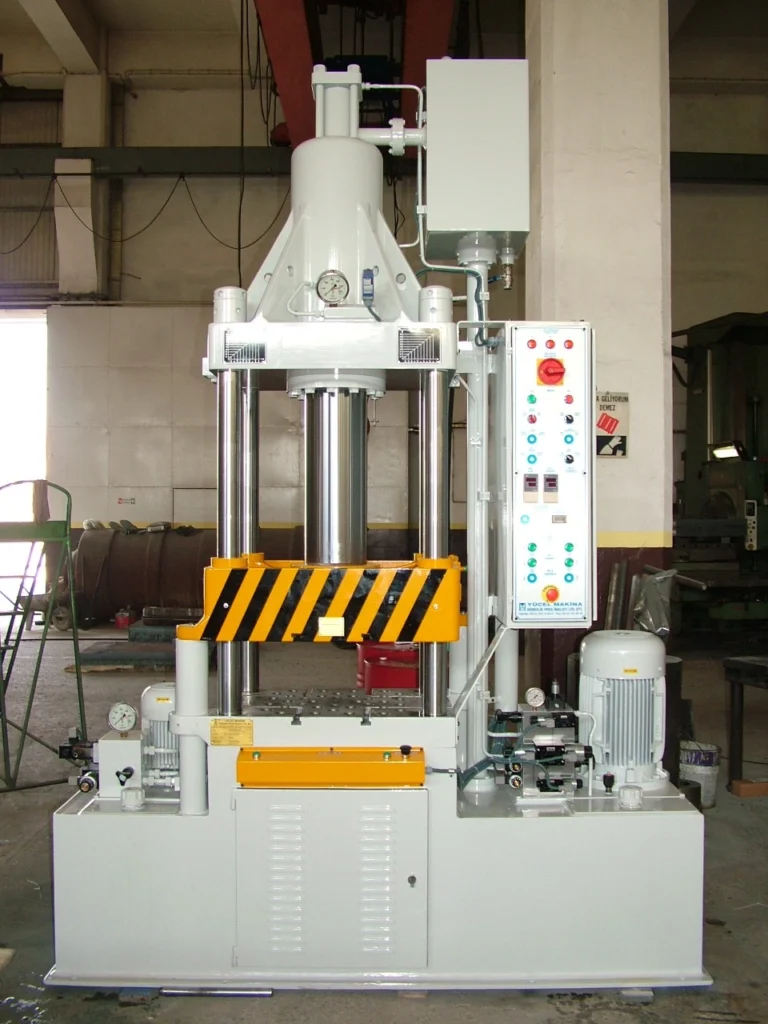
La prensa de embutido es una máquina fundamental en la industria metalúrgica, utilizada para realizar el proceso de embutición en piezas de metal. El embutido consiste en transformar una chapa metálica plana en una forma tridimensional mediante la aplicación de presión, sin romper el material. Este proceso es ampliamente utilizado en la fabricación de componentes que requieren formas profundas y complejas, como recipientes, carrocerías de vehículos, electrodomésticos, entre otros.
La prensa de embutido es especialmente útil cuando se necesita crear formas cilíndricas, cónicas o rectangulares con bordes profundos. Este equipo emplea una matriz y un punzón para aplicar una fuerza precisa sobre la chapa metálica, lo que permite darle forma sin comprometer la integridad del material.
En esta sección, exploraremos las características principales de las prensas de embutido, los tipos de prensas disponibles, sus aplicaciones, beneficios y los aspectos tecnológicos que hacen posible su uso en la industria moderna.
Características de la Prensa de Embutido
Las prensas de embutido están diseñadas para cumplir con los requisitos de precisión, durabilidad y eficiencia que demanda la industria. Entre sus características más importantes se encuentran:
- Fuerza de Prensado Controlada: Estas prensas están equipadas con sistemas hidráulicos o mecánicos que permiten aplicar la presión exacta necesaria para realizar el embutido sin dañar la chapa metálica.
- Capacidad de Formar Piezas Complejas: Las prensas de embutido son capaces de transformar chapas planas en formas tridimensionales de alta complejidad, lo que las hace ideales para la fabricación de componentes con formas geométricas complejas y profundas.
- Precisión en el Proceso: Gracias a sus sistemas de control, las prensas de embutido permiten un alto grado de precisión en la repetición de procesos, garantizando que cada pieza producida cumpla con las especificaciones exactas del diseño.
- Automatización y Control CNC: Muchas prensas de embutido modernas están equipadas con sistemas de control numérico computarizado (CNC), lo que facilita la automatización de procesos complejos y mejora la precisión en la producción en masa.
- Versatilidad en Materiales: Pueden trabajar con una amplia variedad de metales, desde acero y aluminio hasta cobre y bronce, lo que las convierte en herramientas muy versátiles.
- Diseño Robusto y Duradero: Las prensas de embutido están construidas para soportar un uso continuo en ambientes industriales intensivos, garantizando un rendimiento confiable y prolongado.
Tipos de Prensas de Embutido
Existen varios tipos de prensas de embutido que varían en su diseño y en el método de aplicación de la presión. Los principales tipos incluyen:
- Prensa Hidráulica de Embutido: Este tipo de prensa utiliza un sistema hidráulico para aplicar la fuerza necesaria durante el proceso de embutido. Son muy utilizadas cuando se requiere una fuerza de prensado elevada y constante, especialmente en aplicaciones que involucran metales gruesos o duros.
- Prensa Mecánica de Embutido: Las prensas mecánicas son más rápidas que las hidráulicas y están diseñadas para aplicaciones de embutido de alta velocidad. Estas prensas son ideales para operaciones en las que se producen grandes volúmenes de piezas en poco tiempo.
- Prensa de Embutido de Doble Acción: Estas prensas cuentan con dos sistemas de movimiento, uno para el punzón que realiza el embutido y otro para el troquel que sujeta la chapa metálica. Son especialmente útiles para procesos de embutido profundo, donde se necesita mayor control sobre la chapa durante el proceso.
- Prensa Neumática de Embutido: En estas prensas, la fuerza de prensado se genera mediante aire comprimido. Aunque no tienen la misma potencia que las prensas hidráulicas o mecánicas, son útiles en aplicaciones donde se trabaja con materiales más ligeros y en proyectos de menor escala.
- Prensa CNC de Embutido: Las prensas de embutido controladas por CNC permiten automatizar el proceso, lo que resulta en una mayor precisión y repetibilidad. Estas prensas son ideales para la producción en serie de piezas con tolerancias estrictas.
Aplicaciones de la Prensa de Embutido
Las prensas de embutido tienen una amplia variedad de aplicaciones en diferentes sectores industriales, donde se requiere transformar chapas planas en formas tridimensionales. Algunas de las principales aplicaciones incluyen:
- Industria Automotriz: Las prensas de embutido son ampliamente utilizadas en la fabricación de componentes para automóviles, como paneles de carrocería, cubiertas de motor, piezas de escape y otros elementos estructurales que requieren formas profundas y precisas.
- Fabricación de Electrodomésticos: En la producción de electrodomésticos como lavadoras, hornos y refrigeradores, las prensas de embutido permiten la fabricación de carcasas, recipientes y otras piezas que necesitan ser conformadas a partir de chapas metálicas.
- Industria Aeroespacial: En este sector, el embutido es utilizado para fabricar componentes ligeros y resistentes que forman parte de la estructura de aviones y cohetes, donde las formas tridimensionales juegan un papel crucial.
- Fabricación de Envases Metálicos: Las prensas de embutido son esenciales en la fabricación de envases metálicos, como latas de alimentos o bebidas, donde se requiere transformar una chapa plana en una forma cilíndrica o rectangular.
- Industria Electrónica: En la producción de dispositivos electrónicos, las prensas de embutido son utilizadas para crear carcasas y chasis metálicos que albergan los componentes electrónicos, asegurando tanto protección como estética.
Beneficios de Utilizar una Prensa de Embutido
El uso de prensas de embutido ofrece múltiples beneficios en el proceso de fabricación industrial. Entre los más importantes se destacan:
- Ahorro de Material: El proceso de embutido permite crear formas complejas sin necesidad de soldaduras o ensamblajes adicionales, lo que reduce el desperdicio de material y los costos asociados.
- Mayor Resistencia de las Piezas: Al formar la pieza de una sola chapa, el embutido mejora la resistencia estructural del componente final, reduciendo puntos débiles que podrían fallar bajo tensión o carga.
- Alta Precisión: Las prensas de embutido, especialmente aquellas equipadas con control CNC, permiten un alto grado de precisión en la conformación de las piezas, lo que es crucial en industrias donde se requieren tolerancias exactas.
- Versatilidad en el Diseño de Piezas: El embutido permite la creación de formas complejas y profundas que serían difíciles o imposibles de lograr mediante otros procesos de manufactura, lo que amplía las posibilidades de diseño.
- Aumento en la Productividad: Las prensas de embutido, especialmente las automáticas o controladas por CNC, permiten producir grandes volúmenes de piezas en un tiempo reducido, lo que mejora significativamente la eficiencia en la producción.
Tecnología en las Prensas de Embutido
Las prensas de embutido han evolucionado considerablemente con el tiempo, integrando tecnologías avanzadas que mejoran su precisión, eficiencia y seguridad. Algunas de las innovaciones tecnológicas más destacadas incluyen:
- Control Numérico Computarizado (CNC): Este sistema permite automatizar el proceso de embutido, garantizando que cada pieza cumpla con los requisitos exactos de diseño. El CNC también reduce la intervención humana y minimiza los errores.
- Sensores de Presión y Fuerza: Las prensas de embutido modernas están equipadas con sensores que monitorizan la fuerza y presión aplicada durante el proceso, asegurando que se mantengan dentro de los parámetros deseados para evitar deformaciones o rupturas en la chapa.
- Simulación de Procesos: Antes de realizar el embutido, los operadores pueden utilizar software de simulación para predecir cómo se comportará el material bajo presión, lo que permite optimizar el proceso y reducir la posibilidad de errores.
- Sistemas Hidráulicos de Alta Eficiencia: Los sistemas hidráulicos de las prensas modernas están diseñados para ser más eficientes en términos energéticos, reduciendo el consumo de energía y mejorando la sostenibilidad del proceso.
Mantenimiento de las Prensas de Embutido
El mantenimiento adecuado de las prensas de embutido es fundamental para garantizar su rendimiento óptimo y prolongar su vida útil. Algunas de las tareas de mantenimiento más importantes incluyen:
- Lubricación Regular: Es esencial lubricar las partes móviles de la prensa, como los pistones y las guías, para evitar el desgaste prematuro y asegurar un funcionamiento suave.
- Inspección de Herramientas y Matrices: Las herramientas y matrices que se utilizan en el embutido deben ser revisadas periódicamente para detectar cualquier signo de desgaste o daño que pueda afectar la calidad del proceso.
- Calibración de los Sistemas de Control: Los sistemas de control, como los sensores de presión y los controles CNC, deben ser recalibrados regularmente para garantizar que el proceso se realice con la precisión requerida.
- Revisión del Sistema Hidráulico: Es importante verificar que no haya fugas en el sistema hidráulico y que la presión se mantenga constante durante el embutido.
Conclusión
Las prensas de embutido son herramientas fundamentales en la industria moderna, permitiendo la creación de piezas metálicas complejas y profundas con un alto grado de precisión y eficiencia. Desde la fabricación de componentes automotrices hasta envases metálicos y piezas aeroespaciales, estas máquinas juegan un papel clave en diversos sectores industriales. A medida que la tecnología continúa avanzando, las prensas de embutido seguirán evolucionando, mejorando en términos de automatización, sostenibilidad y control, asegurando su lugar como una de las tecnologías más importantes en la fabricación de piezas metálicas.
Prensa de Embutir
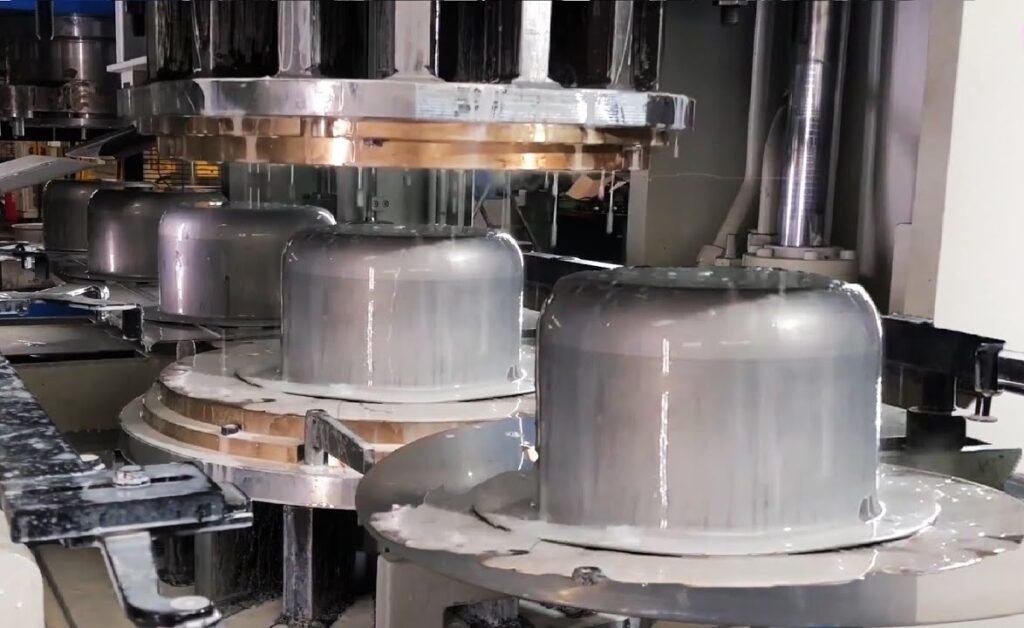
La prensa de embutir es una variante clave en el proceso de conformación de metales, diseñada específicamente para realizar operaciones de embutición de chapas metálicas. Similar a la prensa de embutido, esta máquina transforma láminas metálicas planas en piezas tridimensionales, con la diferencia de que está optimizada para embutidos profundos y complejos. Estas prensas son esenciales en sectores que demandan productos formados a partir de materiales como acero, aluminio y otros metales, con aplicaciones que van desde la fabricación automotriz hasta la industria de electrodomésticos y envases.
A continuación, exploraremos en detalle las características, tipos, aplicaciones y ventajas de las prensas de embutir, así como las innovaciones tecnológicas que las han llevado a ser una herramienta indispensable en la producción industrial moderna.
Características de la Prensa de Embutir
Las prensas de embutir poseen características avanzadas que permiten realizar procesos de embutición de alta complejidad. A continuación, se detallan algunas de las características más destacadas:
- Potencia y Precisión: Estas prensas están diseñadas para aplicar una presión controlada y uniforme, lo que permite realizar embuticiones precisas sin comprometer la calidad de la chapa metálica.
- Capacidad de Embutición Profunda: Las prensas de embutir son especialmente efectivas para operaciones de embutición profunda, permitiendo la creación de piezas con cavidades profundas y formas complejas.
- Sistemas Hidráulicos o Mecánicos: Al igual que otras prensas industriales, las prensas de embutir pueden ser hidráulicas o mecánicas. Las prensas hidráulicas ofrecen mayor control sobre la presión, mientras que las mecánicas son más rápidas y eficientes en operaciones repetitivas.
- Versatilidad en el Uso de Materiales: Estas prensas permiten trabajar con diferentes tipos de metales, incluidos acero, aluminio, cobre y sus aleaciones, lo que las hace muy versátiles en la industria manufacturera.
- Diseño Robusto y Duradero: Las prensas de embutir están fabricadas para soportar condiciones industriales exigentes, garantizando un rendimiento consistente y prolongado incluso bajo uso intensivo.
- Control de Precisión y Automatización: Muchas prensas de embutir modernas están equipadas con sistemas de control numérico computarizado (CNC), lo que permite la automatización del proceso y la producción de piezas con alta repetitividad y precisión.
Tipos de Prensas de Embutir
Las prensas de embutir se pueden clasificar en diferentes tipos según el mecanismo utilizado para aplicar la presión. Los principales tipos incluyen:
- Prensa Hidráulica de Embutir: Las prensas hidráulicas son ideales para embuticiones profundas, ya que ofrecen un control preciso sobre la velocidad y la presión, lo que evita la deformación no deseada de las piezas. Son ampliamente utilizadas en industrias que requieren piezas de gran tamaño o de alta resistencia.
- Prensa Mecánica de Embutir: Estas prensas utilizan un sistema de manivela para generar la fuerza necesaria. Aunque no ofrecen el mismo nivel de control que las hidráulicas, son mucho más rápidas, lo que las hace ideales para la producción en masa de piezas menos complejas.
- Prensa de Embutir de Doble Acción: Este tipo de prensa cuenta con dos movimientos simultáneos, uno para el punzón y otro para el troquel, lo que permite un mayor control sobre la lámina metálica durante el proceso de embutición. Son perfectas para embuticiones profundas y piezas que requieren un alto grado de precisión.
- Prensa Neumática de Embutir: En estas prensas, la presión se genera mediante aire comprimido. Aunque no tienen la misma potencia que las prensas hidráulicas o mecánicas, son útiles para procesos más ligeros y piezas de menor tamaño o en lotes pequeños.
Aplicaciones de las Prensas de Embutir
Las prensas de embutir son ampliamente utilizadas en una variedad de sectores industriales debido a su capacidad para crear piezas tridimensionales complejas. Algunas de sus principales aplicaciones incluyen:
- Industria Automotriz: Estas prensas son fundamentales en la fabricación de componentes automotrices como paneles de carrocería, guardabarros, cubiertas de motor y otros elementos estructurales que requieren embuticiones profundas.
- Fabricación de Electrodomésticos: En este sector, las prensas de embutir se utilizan para conformar carcasas metálicas, bandejas y otros componentes de electrodomésticos como lavadoras, refrigeradores y hornos.
- Industria Aeroespacial: En la fabricación de aviones y naves espaciales, las prensas de embutir permiten la creación de piezas ligeras y resistentes con formas aerodinámicas, indispensables para cumplir con los exigentes requisitos de este sector.
- Envases Metálicos: Las prensas de embutir son ampliamente utilizadas en la producción de envases metálicos, como latas de alimentos y bebidas, donde se necesita transformar una chapa plana en una forma cilíndrica o rectangular.
- Industria Electrónica: Las prensas de embutir permiten la fabricación de carcasas y chasis metálicos utilizados en productos electrónicos como computadoras, teléfonos móviles y otros dispositivos.
Beneficios de las Prensas de Embutir
El uso de prensas de embutir en los procesos de manufactura industrial ofrece múltiples beneficios, entre los que destacan:
- Reducción de Costos de Producción: Las prensas de embutir permiten fabricar piezas complejas en un solo paso, eliminando la necesidad de ensamblajes adicionales o procesos de soldadura, lo que reduce tanto los costos de material como de tiempo.
- Aumento en la Productividad: Estas prensas son capaces de producir grandes cantidades de piezas en poco tiempo, especialmente en aplicaciones automatizadas, lo que aumenta considerablemente la eficiencia en las líneas de producción.
- Mayor Resistencia de las Piezas: Al crear las piezas a partir de una sola chapa, se eliminan las juntas o puntos de soldadura que podrían debilitar la estructura, resultando en componentes más resistentes y duraderos.
- Flexibilidad en el Diseño de Piezas: El embutido permite la creación de formas complejas que serían difíciles o imposibles de lograr con otros métodos de fabricación, lo que da a los diseñadores mayor libertad para crear productos innovadores.
- Precisión y Repetibilidad: Gracias a la tecnología CNC, las prensas de embutir pueden producir piezas con un alto grado de precisión, garantizando que cada componente cumpla con las especificaciones exactas del diseño.
Tecnología en las Prensas de Embutir
El desarrollo tecnológico ha mejorado significativamente el rendimiento y las capacidades de las prensas de embutir. Algunas de las tecnologías más avanzadas incluyen:
- Control CNC: El control numérico computarizado permite programar la prensa para realizar embuticiones complejas con una precisión milimétrica, asegurando la consistencia en la producción de grandes volúmenes de piezas.
- Monitoreo de Fuerza en Tiempo Real: Muchas prensas modernas están equipadas con sensores que miden la fuerza aplicada durante el proceso de embutición, lo que ayuda a garantizar que se mantengan dentro de los parámetros óptimos.
- Sistemas de Seguridad Avanzados: Las prensas de embutir modernas cuentan con sistemas de seguridad que protegen al operador de accidentes, como barreras de luz, dispositivos de parada de emergencia y monitoreo constante de la maquinaria.
- Sistemas Hidráulicos Eficientes: Los avances en los sistemas hidráulicos han permitido que las prensas de embutir sean más eficientes en términos de consumo energético, lo que no solo reduce los costos operativos, sino que también minimiza el impacto ambiental.
Mantenimiento de las Prensas de Embutir
Un mantenimiento adecuado es crucial para garantizar el rendimiento y la durabilidad de las prensas de embutir. Algunas de las prácticas clave de mantenimiento incluyen:
- Revisión y Lubricación Regular: Es esencial mantener las partes móviles de la prensa bien lubricadas para evitar el desgaste prematuro y asegurar un funcionamiento suave.
- Inspección de Herramientas y Matrices: Las matrices y herramientas utilizadas en la prensa deben ser inspeccionadas regularmente para detectar desgaste o daños que puedan afectar la calidad del embutido.
- Verificación del Sistema Hidráulico: En las prensas hidráulicas, es importante comprobar que no haya fugas de aceite y que el sistema esté funcionando a la presión adecuada.
- Calibración del Sistema CNC: Las prensas con control CNC deben ser recalibradas periódicamente para asegurar que la precisión en la producción se mantenga dentro de los parámetros deseados.
Conclusión
Las prensas de embutir son herramientas clave en la industria moderna debido a su capacidad para transformar chapas metálicas planas en piezas tridimensionales complejas. Desde la industria automotriz hasta la aeroespacial, estas prensas juegan un papel fundamental en la fabricación de componentes que requieren alta precisión, resistencia y eficiencia en el proceso productivo. Con los avances tecnológicos, como la integración de sistemas CNC y sensores de monitoreo, las prensas de embutir continúan evolucionando para satisfacer las demandas de una industria en constante cambio, garantizando la producción de piezas de alta calidad a un menor costo
Máquinas de Corte y Bordó
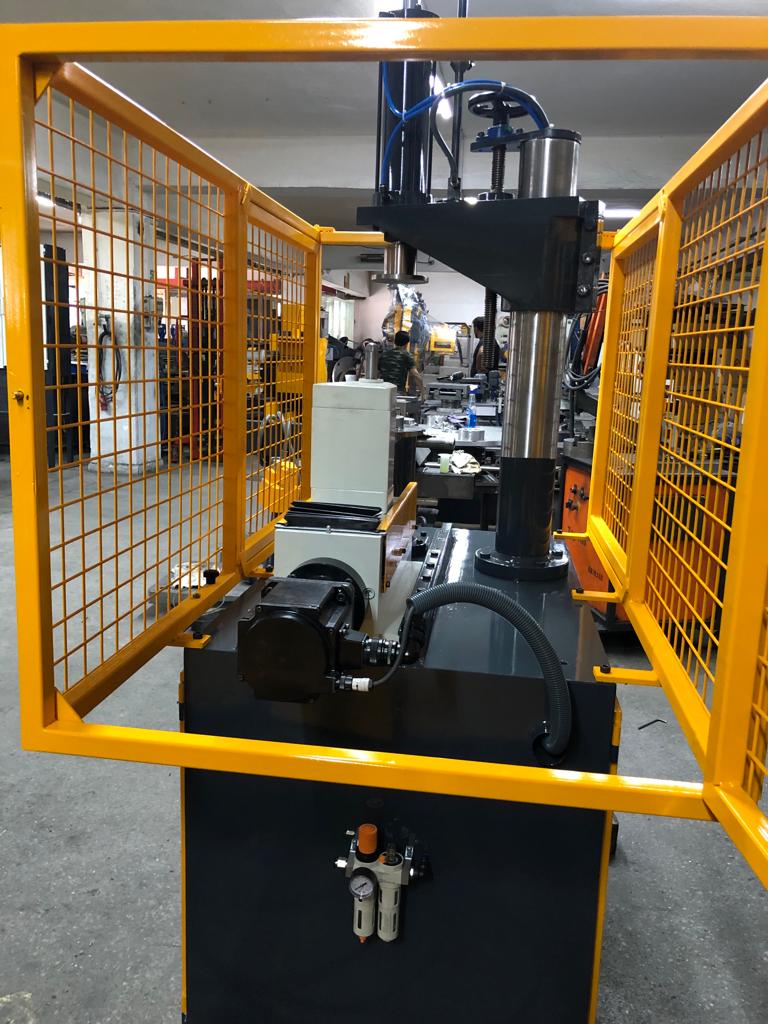
Las máquinas de corte y bordó son equipos esenciales en la industria metalúrgica y manufacturera, especialmente en procesos de conformado y acabado de piezas metálicas. Estas máquinas combinan dos funciones clave: el corte preciso de chapas metálicas y la formación de bordes o rebordes en dichas chapas, permitiendo la producción de piezas con formas y dimensiones específicas. Se utilizan en una amplia gama de sectores industriales, desde la fabricación de productos de consumo hasta componentes industriales más complejos.
Este tipo de máquinas son fundamentales en líneas de producción donde se requiere un alto grado de precisión en los cortes y una conformación adecuada de los bordes, especialmente en piezas que luego se ensamblarán o se usarán en aplicaciones estructurales o estéticas. A continuación, exploraremos en detalle las características, tipos, aplicaciones y beneficios de las máquinas de corte y bordó, así como las innovaciones tecnológicas que han mejorado su rendimiento.
Características de las Máquinas de Corte y Bordó
Las máquinas de corte y bordó están diseñadas para ofrecer precisión y eficiencia en los procesos de manufactura. Entre sus principales características, se destacan las siguientes:
- Capacidad de Corte de Alta Precisión: Estas máquinas están equipadas con herramientas de corte que permiten realizar cortes limpios y exactos en chapas metálicas de distintos espesores, minimizando el desperdicio de material.
- Formación de Bordes y Rebordes: Además del corte, estas máquinas también están diseñadas para conformar bordes en las chapas, creando perfiles que pueden ser utilizados para reforzar estructuras o darles una terminación estética.
- Versatilidad de Materiales: Las máquinas de corte y bordó son capaces de trabajar con una amplia variedad de metales, incluidos el acero, el aluminio, el cobre y sus aleaciones, lo que las hace adecuadas para diferentes aplicaciones industriales.
- Sistemas de Control Automatizado: Muchas de estas máquinas están equipadas con sistemas de control numérico computarizado (CNC) que permiten programar el corte y el conformado de bordes con una alta precisión, asegurando la repetitividad en la producción de grandes volúmenes de piezas.
- Diseño Robusto y Eficiente: Estas máquinas están diseñadas para operar en entornos industriales exigentes, garantizando un rendimiento constante y duradero, incluso en condiciones de alta demanda.
- Sistemas de Seguridad Integrados: Dado que el proceso de corte y conformado de bordes puede implicar riesgos para los operadores, las máquinas modernas incluyen múltiples sistemas de seguridad, como barreras de luz, paradas de emergencia y monitoreo constante de las herramientas.
Tipos de Máquinas de Corte y Bordó
Existen diversos tipos de máquinas de corte y bordó, cada una diseñada para satisfacer diferentes necesidades en la fabricación de piezas metálicas. Entre los tipos más comunes se encuentran:
- Máquinas de Corte y Bordó Hidráulicas: Utilizan la presión hidráulica para realizar tanto el corte como la formación de bordes. Son ideales para aplicaciones que requieren una fuerza considerable, como el trabajo con metales gruesos o duros.
- Máquinas de Corte y Bordó Mecánicas: Estas máquinas emplean un sistema de palanca o manivela para generar la fuerza necesaria. Aunque no tienen la misma versatilidad que las hidráulicas, son muy eficientes para trabajos de corte repetitivo y bordado en metales más finos.
- Máquinas de Corte y Bordó CNC: Incorporan tecnología de control numérico computarizado, lo que permite automatizar completamente el proceso de corte y conformado. Este tipo de máquinas es ideal para la producción en masa, donde se requiere un alto grado de precisión y uniformidad.
- Máquinas de Corte y Bordó Portátiles: Son más pequeñas y livianas, diseñadas para trabajos en campo o en entornos donde se requiere movilidad. Estas máquinas son utilizadas principalmente en trabajos de mantenimiento o reparaciones en sitio.
Aplicaciones de las Máquinas de Corte y Bordó
Las máquinas de corte y bordó se utilizan en una amplia variedad de industrias, debido a su capacidad para realizar cortes precisos y conformar bordes en piezas metálicas. Algunas de sus principales aplicaciones incluyen:
- Industria Automotriz: Estas máquinas son esenciales en la fabricación de componentes automotrices como paneles de carrocería, guardabarros y piezas estructurales, donde se requiere tanto el corte de chapas como la conformación de bordes para ensamblar los diferentes componentes del vehículo.
- Industria de Electrodomésticos: En este sector, las máquinas de corte y bordó se utilizan para fabricar carcasas y componentes de electrodomésticos como lavadoras, refrigeradores y hornos, que requieren cortes precisos y bordes bien definidos para un ensamblaje correcto.
- Industria Aeroespacial: Las máquinas de corte y bordó son utilizadas en la fabricación de componentes ligeros y resistentes, como paneles de fuselaje y otras piezas metálicas utilizadas en la construcción de aeronaves y naves espaciales.
- Fabricación de Envases Metálicos: En la industria del envasado, estas máquinas se utilizan para cortar y conformar bordes en envases metálicos como latas de alimentos y bebidas, donde la precisión en el corte y el acabado de los bordes es fundamental para garantizar un sellado adecuado.
- Construcción y Arquitectura: En la construcción, estas máquinas son utilizadas para cortar y dar forma a piezas metálicas que se emplean en la fabricación de estructuras, fachadas y elementos decorativos. La capacidad de bordar los bordes mejora tanto la seguridad como la apariencia de las piezas.
Ventajas de las Máquinas de Corte y Bordó
El uso de máquinas de corte y bordó en la fabricación de piezas metálicas ofrece múltiples beneficios, entre los que destacan:
- Precisión en los Procesos de Corte y Bordado: Estas máquinas permiten realizar cortes exactos y bordes precisos, lo que es fundamental en aplicaciones donde se requiere un ajuste perfecto entre las piezas.
- Ahorro de Material y Reducción de Desperdicio: Al realizar cortes limpios y precisos, se minimiza el desperdicio de material, lo que contribuye a una mayor eficiencia en la producción y una reducción en los costos.
- Flexibilidad para Trabajar con Diferentes Metales: La capacidad de trabajar con diversos tipos de metales permite a las máquinas de corte y bordó adaptarse a diferentes industrias y necesidades de producción.
- Mejora en la Estética y Funcionalidad de las Piezas: La capacidad de formar bordes en las piezas no solo mejora su resistencia estructural, sino que también contribuye a un acabado estético más profesional y atractivo.
- Eficiencia en la Producción en Masa: Las máquinas de corte y bordó CNC permiten automatizar el proceso de producción, aumentando la velocidad y la eficiencia en la fabricación de grandes volúmenes de piezas sin comprometer la calidad.
Innovaciones Tecnológicas en las Máquinas de Corte y Bordó
Con el avance de la tecnología, las máquinas de corte y bordó han experimentado importantes mejoras en términos de eficiencia, precisión y automatización. Algunas de las innovaciones más destacadas incluyen:
- Tecnología CNC: La implementación de sistemas CNC ha revolucionado la manera en que las máquinas de corte y bordó operan, permitiendo un control total sobre los cortes y la conformación de bordes con una precisión milimétrica. Además, estas máquinas pueden ser programadas para realizar operaciones complejas de manera automática, lo que mejora la eficiencia y reduce el margen de error.
- Sistemas de Corte por Láser y Plasma: Algunas máquinas de corte y bordó están equipadas con sistemas de corte por láser o plasma, que permiten realizar cortes aún más precisos y en materiales de mayor espesor, ofreciendo una mayor versatilidad en las aplicaciones industriales.
- Sensores de Monitoreo en Tiempo Real: Las máquinas más modernas están equipadas con sensores que monitorean en tiempo real el proceso de corte y conformado de bordes, lo que permite ajustar los parámetros de manera automática para asegurar la calidad del producto final.
- Mejoras en la Seguridad Operativa: Además de la eficiencia y la precisión, la seguridad de los operadores es una prioridad en el diseño de las máquinas de corte y bordó. Los sistemas de seguridad avanzados, como las barreras de luz y los sistemas de parada automática, ayudan a prevenir accidentes durante la operación.
Mantenimiento de las Máquinas de Corte y Bordó
Un mantenimiento adecuado es crucial para garantizar el buen funcionamiento y la durabilidad de las máquinas de corte y bordó. Algunas prácticas recomendadas incluyen:
- Revisión Periódica de las Cuchillas y Herramientas: Las cuchillas de corte y las herramientas utilizadas para el conformado de bordes deben ser inspeccionadas regularmente para detectar signos de desgaste o daño, y reemplazarlas cuando sea necesario.
- Lubricación de Partes Móviles: Es esencial mantener las partes móviles de la máquina bien lubricadas para evitar el desgaste prematuro y garantizar un funcionamiento suave y eficiente.
- Calibración del Sistema CNC: Las máquinas que operan con sistemas CNC deben ser recalibradas periódicamente para asegurar que los cortes y el bordado se realicen con la precisión deseada.
- Inspección de los Sistemas Hidráulicos o Mecánicos: En el caso de las máquinas hidráulicas, es importante verificar que no haya fugas de aceite y que los niveles de presión se mantengan dentro de los parámetros recomendados.
Conclusión
Las máquinas de corte y bordó son herramientas fundamentales en la industria moderna, permitiendo la fabricación de piezas metálicas con cortes precisos y bordes bien definidos. Su versatilidad y capacidad para trabajar con diferentes tipos de metales las hacen indispensables en una amplia gama de aplicaciones, desde la industria automotriz hasta la fabricación de electrodomésticos y la construcción. Con los avances tecnológicos, estas máquinas continúan mejorando en términos de precisión, eficiencia y seguridad, lo que garantiza su relevancia en los procesos de manufactura del futuro.
Bordonadora Hidráulica

Las bordonadoras hidráulicas son máquinas esenciales en la industria metalúrgica, especialmente en los procesos de conformado de chapas y metales. Su principal función es la de crear un reborde o borde en la pieza de metal, dándole mayor rigidez y resistencia, además de un acabado estético mejorado. Este tipo de máquinas se caracteriza por utilizar un sistema hidráulico para generar la fuerza necesaria para realizar el proceso de rebordado de manera eficiente y precisa.
La bordonadora hidráulica ha evolucionado para adaptarse a diversas aplicaciones industriales y ofrece una gran versatilidad en términos de los materiales con los que puede trabajar, desde chapas de acero hasta metales no ferrosos como el aluminio y el cobre. A continuación, se exploran en detalle las características, funcionamiento, aplicaciones, y ventajas de las bordonadoras hidráulicas.
Características de una Bordonadora Hidráulica
Una bordonadora hidráulica se distingue por una serie de características que la hacen eficiente y adecuada para su uso en la industria moderna. Entre ellas, destacan:
- Sistema de Potencia Hidráulica: La fuerza de estas máquinas proviene de un sistema hidráulico, que utiliza fluidos a alta presión para generar la energía necesaria para el conformado de los bordes. Este sistema permite aplicar una gran fuerza de manera controlada, lo que es esencial para trabajar con chapas metálicas gruesas o duras.
- Control de Precisión: Gracias al uso de tecnología avanzada, las bordonadoras hidráulicas pueden ofrecer un control preciso sobre el proceso de rebordado. Esto asegura que cada borde o reborde se forme con exactitud, manteniendo una uniformidad en toda la producción.
- Versatilidad en el Tipo de Material: Estas máquinas son capaces de trabajar con una amplia variedad de metales y chapas, incluyendo acero inoxidable, aluminio, latón, y otros metales no ferrosos. Esta versatilidad las convierte en una herramienta indispensable en diversas industrias.
- Diseño Robusto y Duradero: Las bordonadoras hidráulicas están diseñadas para operar en condiciones de trabajo intensivo. Su construcción robusta y los materiales de alta calidad con los que están fabricadas aseguran una larga vida útil y un rendimiento constante.
- Sistemas de Seguridad: Las máquinas modernas incluyen diversas medidas de seguridad, tales como paradas de emergencia y protección contra sobrecargas. Esto no solo protege al operario, sino que también asegura que la máquina no sufra daños por uso indebido.
Funcionamiento de una Bordonadora Hidráulica
El principio de funcionamiento de una bordonadora hidráulica es relativamente sencillo, pero altamente eficiente. A través del uso de presión hidráulica, la máquina empuja una herramienta de conformado contra la pieza metálica, creando un borde o reborde en la chapa. El proceso se realiza en varias etapas, aplicando presión de manera gradual para evitar dañar el material y asegurar un acabado preciso.
La presión hidráulica se controla mediante un sistema de válvulas que permite ajustar la cantidad de fuerza aplicada, dependiendo del tipo de metal y el grosor de la chapa. Este nivel de control es lo que hace que las bordonadoras hidráulicas sean tan apreciadas en la industria, ya que permite trabajar con una amplia gama de materiales y espesores sin comprometer la calidad del producto final.
Tipos de Bordonadoras Hidráulicas
Existen varios tipos de bordonadoras hidráulicas, cada una diseñada para aplicaciones específicas. Algunos de los tipos más comunes incluyen:
- Bordonadoras Hidráulicas Manuales: Estas máquinas son operadas manualmente, pero utilizan un sistema hidráulico para generar la fuerza necesaria. Son ideales para talleres pequeños o para aplicaciones donde no se requiere una alta tasa de producción.
- Bordonadoras Hidráulicas Automáticas: Estas máquinas están completamente automatizadas y pueden ser programadas para realizar operaciones de rebordado de manera continua. Son adecuadas para grandes fábricas y líneas de producción donde se requiere una alta eficiencia y uniformidad.
- Bordonadoras Hidráulicas CNC: Este tipo de máquina utiliza tecnología de control numérico computarizado (CNC) para ofrecer un control preciso y automatizado sobre el proceso de rebordado. Las bordonadoras CNC son especialmente útiles cuando se trabaja con piezas complejas o se requiere una gran precisión en el proceso de fabricación.
Aplicaciones de las Bordonadoras Hidráulicas
Las bordonadoras hidráulicas se utilizan en una amplia gama de industrias debido a su versatilidad y capacidad para trabajar con diferentes tipos de metales. Algunas de sus principales aplicaciones incluyen:
- Fabricación de Piezas Automotrices: Las bordonadoras son esenciales en la fabricación de componentes automotrices como paneles de puertas, capós, y otras piezas de carrocería que requieren bordes reforzados para mejorar su resistencia estructural.
- Industria Aeroespacial: En la fabricación de componentes aeronáuticos, las bordonadoras hidráulicas se utilizan para dar forma a los bordes de piezas de metal ligero, como paneles de fuselaje y otros componentes estructurales.
- Fabricación de Electrodomésticos: Las bordonadoras hidráulicas son comúnmente utilizadas en la producción de carcasas y componentes metálicos para electrodomésticos, donde es esencial tener bordes bien conformados para el ensamblaje.
- Fabricación de Envases Metálicos: En la industria de los envases, las bordonadoras se utilizan para crear bordes en latas y otros tipos de envases metálicos, asegurando un cierre hermético y un acabado limpio.
- Construcción y Arquitectura: Las bordonadoras también tienen aplicaciones en la fabricación de piezas metálicas para la construcción, como perfiles y chapas utilizadas en estructuras arquitectónicas y elementos decorativos.
Ventajas de las Bordonadoras Hidráulicas
El uso de bordonadoras hidráulicas ofrece una serie de ventajas significativas en comparación con otros métodos de conformado de bordes. Entre las principales ventajas, se encuentran:
- Mayor Precisión y Control: Gracias al sistema hidráulico, estas máquinas permiten un control exacto sobre el proceso de rebordado, lo que resulta en piezas con bordes perfectamente conformados y uniformes.
- Mayor Fuerza para Materiales Gruesos: Las bordonadoras hidráulicas son capaces de aplicar una gran cantidad de fuerza, lo que les permite trabajar con chapas metálicas más gruesas o metales más duros sin comprometer la calidad del producto final.
- Versatilidad en el Tipo de Material: Estas máquinas pueden trabajar con una amplia gama de metales, lo que las hace muy versátiles y útiles en diversas industrias.
- Mayor Durabilidad de la Máquina: Las bordonadoras hidráulicas están diseñadas para ser extremadamente robustas, lo que asegura que puedan operar durante largos periodos sin necesidad de reparaciones importantes.
- Ahorro de Tiempo y Costos en Producción: Al automatizar el proceso de rebordado, las bordonadoras hidráulicas pueden aumentar significativamente la eficiencia de la producción, reduciendo el tiempo de fabricación y los costos asociados.
Innovaciones Tecnológicas en las Bordonadoras Hidráulicas
En los últimos años, las bordonadoras hidráulicas han experimentado una serie de innovaciones tecnológicas que han mejorado su rendimiento y eficiencia. Algunas de estas innovaciones incluyen:
- Tecnología CNC: La integración de sistemas CNC ha permitido una mayor precisión en el proceso de rebordado, facilitando la producción de piezas complejas con un nivel de detalle mucho mayor.
- Sistemas de Monitoreo y Control Automático: Las bordonadoras modernas están equipadas con sensores y sistemas de monitoreo que permiten ajustar automáticamente los parámetros del proceso en tiempo real, mejorando la calidad y la eficiencia de la producción.
- Mejoras en la Seguridad Operativa: Los sistemas de seguridad avanzados, como las paradas de emergencia y las barreras de luz, han hecho que las bordonadoras hidráulicas sean más seguras para los operadores, reduciendo el riesgo de accidentes.
- Eficiencia Energética: Los nuevos diseños de sistemas hidráulicos han mejorado la eficiencia energética de estas máquinas, reduciendo el consumo de energía y haciendo que el proceso sea más sostenible.
Mantenimiento de una Bordonadora Hidráulica
Un buen mantenimiento es crucial para garantizar la larga vida útil de una bordonadora hidráulica. Algunas prácticas recomendadas para su mantenimiento incluyen:
- Revisión de los Niveles de Fluido Hidráulico: Es importante asegurarse de que los niveles de fluido hidráulico estén dentro de los parámetros recomendados, ya que un nivel bajo puede afectar el rendimiento de la máquina.
- Lubricación de Partes Móviles: Mantener bien lubricadas las partes móviles de la máquina es esencial para evitar el desgaste prematuro y garantizar un funcionamiento suave.
- Inspección de Herramientas: Las herramientas de rebordado deben ser inspeccionadas regularmente para detectar signos de desgaste o daño, y reemplazarlas cuando sea necesario.
- Calibración Regular del Sistema: Para asegurar la precisión en el proceso de rebordado, es recomendable realizar una calibración periódica de la máquina, especialmente en aquellas que utilizan sistemas CNC.
Máquinas Formadoras de Metales EMS
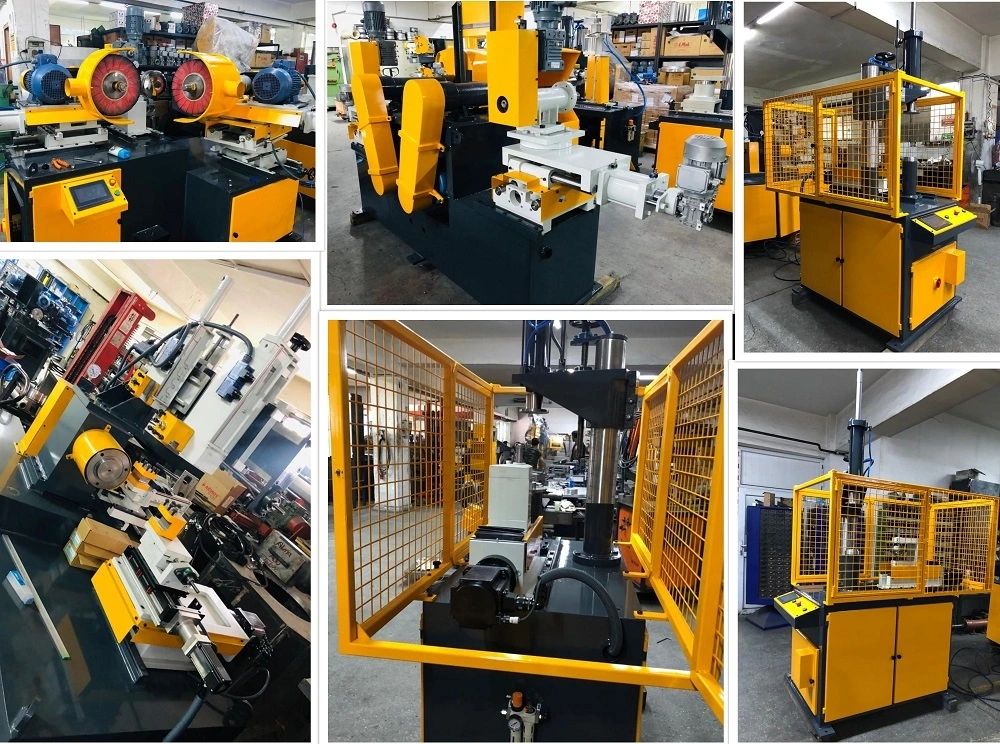
Diseñamos, fabricamos y montamos maquinaria metalmecánica como:
Prensa de transferencia hidráulica
Prensa para mosaicos de vidrio
Prensa hidráulica de embutición profunda
prensa de fundición
Prensa hidráulica de conformado en frío
Prensa de hidroformado
prensa compuesta
Prensa de moldeo de caucho de silicona
Prensa de pastillas de freno
Prensa de melamina
Prensa SMC y BMC
prensa labrotaroy
Máquina cortadora de bordes
Máquina rizadora de bordes
Máquina recortadora de abalorios
Máquina de recorte y jogging
Línea de producción de utensilios de cocina.
Máquina dobladora de tubos
Máquina dobladora de perfiles
Sierra de cinta para metal
Máquina de soldar cilíndrica
Prensas horizontales y utensilios de cocina.
Menaje de cocina, artículos de hotelería
Maquinaria para la producción de utensilios para hornear y cubiertos.
como una línea completa así como una máquina individual como:
Máquinas cortadoras de bordes y biseladoras
Pulidoras y rectificadoras de ollas y sartenes.
Prensas hidráulicas de trefilado
Máquinas troqueladoras circulares
remachadora
Punzonadoras
Máquina de alimentación de prensa
Puede consultar nuestra maquinaria en funcionamiento en: EMS Máquinas Formadoras de Metales EMS – YouTube
Aplicaciones:
Punzonado de bridas
Abalorios y nervaduras
Bridas
Guarnición
Curling
costura de bloqueo
Nervaduras