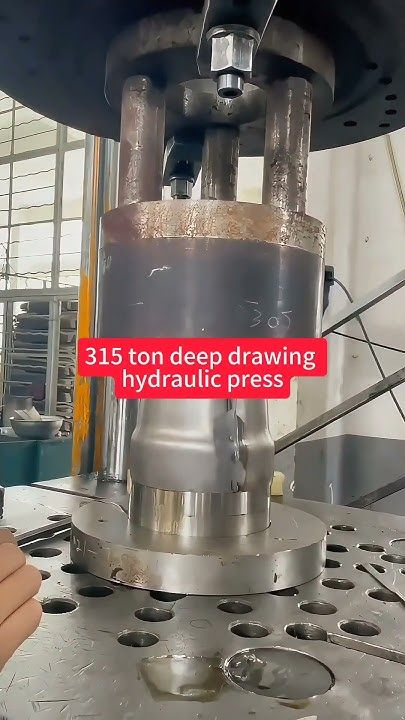
Prensas hidráulicas de conformado de metales: Prensa de embutido y embutición usada en máquinas, equipos, maquinaria y sistemas de conformado industrial: Una prensa dobladora es una máquina industrial diseñada para doblar y conformar láminas metálicas con alta precisión. Su función principal es aplicar fuerza mediante un punzón y una matriz para generar pliegues en chapas metálicas, usualmente en forma de “V”, “U” u otras configuraciones personalizadas según la geometría de la herramienta y el ángulo deseado.
Características clave:
- Accionamiento: puede ser hidráulico, mecánico, neumático o servoeléctrico.
- Control: en versiones modernas, incluye CNC (control numérico computarizado) para programar ángulos de doblado, posiciones y repeticiones automáticas.
- Capacidad: varía según la fuerza de prensado (toneladas) y el largo útil de trabajo (longitud de la bancada).
- Herramientas: intercambiables para diferentes perfiles de doblado.
- Precisión: muchas cuentan con sistemas de corrección de deflexión (crowning) y tope trasero (backgauge) para posicionar la pieza con exactitud.
Aplicaciones típicas:
- Fabricación de gabinetes eléctricos, carcasas metálicas, mobiliario metálico.
- Producción de perfiles estructurales y componentes para maquinaria.
- Industria automotriz, HVAC, construcción y electrodomésticos.
Si necesitas información sobre tipos específicos (como prensa plegadora hidráulica, eléctrica o CNC), o modelos para ciertos grosores o materiales, dime y te amplío.
Las prensas dobladoras funcionan mediante la aplicación de una fuerza vertical que empuja un punzón hacia una matriz, haciendo que una chapa colocada entre ambas se doble con el ángulo y la forma deseada. El espesor del material, la longitud de doblado y el tipo de material son factores críticos para definir la capacidad necesaria de la máquina. Las más comunes en la industria son las hidráulicas, por su potencia, fiabilidad y capacidad de doblar chapas gruesas, aunque las prensas eléctricas están ganando popularidad por su eficiencia energética, velocidad y bajo mantenimiento. Las versiones modernas incluyen sistemas CNC que permiten programar múltiples secuencias de doblado, corregir desviaciones automáticas y lograr una repetibilidad muy alta, lo cual es clave en producciones en serie. Estas máquinas también incorporan sensores, topes traseros motorizados y sistemas de compensación que permiten mantener una calidad constante en todas las piezas. En la fabricación, una prensa dobladora es esencial cuando se requiere transformar una simple lámina plana en una estructura tridimensional con precisión, ya sea para formar cajas, perfiles, soportes o carcasas. También se utilizan matrices especiales para lograr formas no convencionales o radios amplios de doblado. El operador juega un papel importante en la preparación, alineación y aseguramiento de la correcta colocación de la pieza, aunque los sistemas automatizados reducen cada vez más la intervención manual. Las soluciones robóticas integradas permiten incluso alimentar la máquina, doblar múltiples veces y retirar la pieza terminada sin intervención humana, incrementando así la productividad y la seguridad.
Además del aspecto operativo, el diseño estructural de una prensa dobladora influye directamente en su rendimiento. La rigidez del bastidor asegura que las deformaciones durante el proceso de doblado sean mínimas, lo cual es vital para mantener la precisión dimensional. En modelos de gran tonelaje, el sistema de compensación por flexión de bancada (crowning) es indispensable, ya que corrige las desviaciones causadas por la presión central que tiende a abrir ligeramente los extremos del pliegue. En cuanto al sistema hidráulico, se utilizan cilindros sincronizados que garantizan un movimiento uniforme del eje móvil (generalmente el eje Y1-Y2), mientras que los topes traseros programables pueden tener múltiples ejes (X, R, Z1, Z2, etc.) para posicionar la chapa con total exactitud en cada operación. La selección de herramientas (punzones y matrices) también es crítica. Existen herramientas estándar para ángulos de 90°, pero también configuraciones especiales para radios grandes, dobleces cerrados, materiales sensibles a la marca o para procesos de doblado por aire o por fondo. El doblado por aire es más versátil y rápido, permitiendo cambiar el ángulo de doblado sin cambiar de herramienta, mientras que el doblado en fondo proporciona una mayor precisión y repetibilidad, aunque requiere más fuerza y herramienta específica para cada ángulo. En los entornos productivos modernos, las prensas dobladoras pueden integrarse en líneas de fabricación con alimentación automática, estaciones de control de calidad por visión artificial y sistemas de trazabilidad de piezas. Esto las convierte en parte esencial de la industria 4.0 y de las celdas de producción inteligentes, donde se busca una fabricación flexible, rápida y precisa, con menor intervención humana y mayor control de calidad en tiempo real.
Embutición de metales
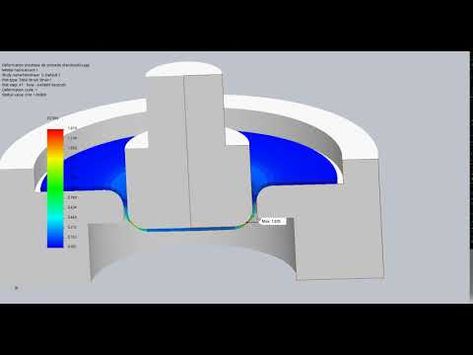
La embutición de metales es un proceso de conformado en frío mediante el cual una lámina metálica plana se transforma en una pieza hueca de forma generalmente cilíndrica, cónica o prismática, sin rupturas ni cortes en el material. Este proceso se realiza aplicando presión sobre la lámina con un punzón que la empuja dentro de una matriz, obligándola a adaptarse a la forma interna de esta última. La embutición es fundamental en la fabricación de piezas como latas, ollas, envases, carcasas, filtros, componentes automotrices, electrodomésticos y muchas otras aplicaciones industriales.
La operación comienza colocando un disco metálico (llamado “blanco”) sobre una matriz. El punzón, al descender, presiona el material hacia el interior de la matriz, mientras un aro de sujeción o prensachapa evita que se formen arrugas en los bordes. A medida que el punzón continúa avanzando, el material se deforma plásticamente, fluyendo hacia abajo y tomando la forma de la cavidad. En embuticiones profundas, donde la altura de la pieza es considerable respecto al diámetro inicial, pueden requerirse varias etapas, llamadas embuticiones sucesivas o reembuticiones, para evitar roturas y controlar el espesor final.
El éxito del proceso depende de múltiples factores: el tipo y espesor del material, el coeficiente de fricción, la velocidad de prensado, el diseño del punzón y la matriz, el diámetro inicial del blanco, y el uso de lubricantes adecuados. Materiales como acero inoxidable, aluminio, cobre y sus aleaciones son comúnmente embutidos debido a su buena ductilidad.
En la industria moderna, la embutición puede realizarse con prensas mecánicas, hidráulicas o servoaccionadas, y puede formar parte de una línea automatizada donde las piezas se alimentan, embuten, inspeccionan y descargan sin intervención humana. Este proceso destaca por su capacidad de producir piezas sin soldaduras ni uniones, con gran precisión dimensional, excelente acabado superficial y ahorro de material.
En embutición profunda, uno de los mayores desafíos es controlar la distribución del espesor del material. Durante el proceso, el material tiende a adelgazarse en ciertas zonas, especialmente en las paredes de la pieza, y a engrosarse o arrugarse en otras, como en la brida, si no se controla adecuadamente. Para evitar defectos como desgarros, arrugas o roturas, es fundamental calcular con precisión el coeficiente de embutición y, en muchos casos, recurrir a operaciones de alisado o calibrado posteriores. En diseños complejos o piezas de gran profundidad, también se pueden emplear matrices progresivas, donde cada estación va transformando el blanco de forma gradual y controlada. Otra técnica común es el uso de embutición inversa o redibujo, en la cual el punzón saca el material en sentido opuesto al inicial, permitiendo obtener mayores profundidades sin comprometer la integridad estructural de la pieza. El diseño del utillaje (punzón, matriz, prensachapa) es esencial y suele fabricarse con aceros especiales tratados térmicamente para resistir el desgaste y las presiones elevadas del proceso. Además, se aplican lubricantes específicos, tanto en base aceite como en emulsiones, para reducir la fricción y facilitar el flujo del material. Las simulaciones computacionales, mediante software de elementos finitos, permiten prever cómo se comportará el metal durante el embutido, detectando zonas críticas y optimizando el diseño antes de fabricar los moldes. Esto ahorra tiempo y costos de prueba. En sectores como la automoción, la embutición permite fabricar componentes estructurales ligeros y resistentes, como puertas, techos, paneles laterales y cubiertas, mientras que en la industria del envase se emplea para producir latas, tapas y envases presurizados de forma masiva y con extrema uniformidad. El avance de la automatización y la sensorización ha permitido monitorear en tiempo real variables como presión, fuerza de embutido, alineación del punzón, o desgaste del útil, asegurando que cada pieza cumpla con tolerancias exactas y reduciendo el riesgo de desperdicio o paradas no programadas.
Además, la embutición de metales ha evolucionado incorporando tecnologías avanzas para mejorar la eficiencia y la calidad del proceso. Por ejemplo, la embutición por hidroformado utiliza un fluido a alta presión para conformar la lámina contra un molde, lo que permite obtener formas más complejas y con menos esfuerzo mecánico, además de mejorar el acabado superficial y la uniformidad del espesor. Este método es especialmente útil en la fabricación de piezas automotrices y aeroespaciales donde la precisión y la ligereza son críticas. Otra innovación es la embutición incremental o progresiva, donde el material se deforma poco a poco mediante herramientas especiales que se mueven de forma secuencial, lo que reduce las tensiones internas y permite trabajar materiales con menor ductilidad o mayor espesor sin dañarlos. En cuanto a materiales, la expansión hacia aleaciones ligeras como el aluminio y el titanio ha impulsado la adaptación de las técnicas de embutición, debido a sus propiedades mecánicas particulares. Por último, la sostenibilidad también ha ganado relevancia; se optimizan los procesos para minimizar el desperdicio de material y se investigan lubricantes ecológicos y reutilizables, junto con sistemas de reciclaje del material sobrante. Todo esto convierte a la embutición en un proceso clave para la fabricación moderna, combinando productividad, calidad y respeto al medio ambiente.
Proceso de embutido industrial
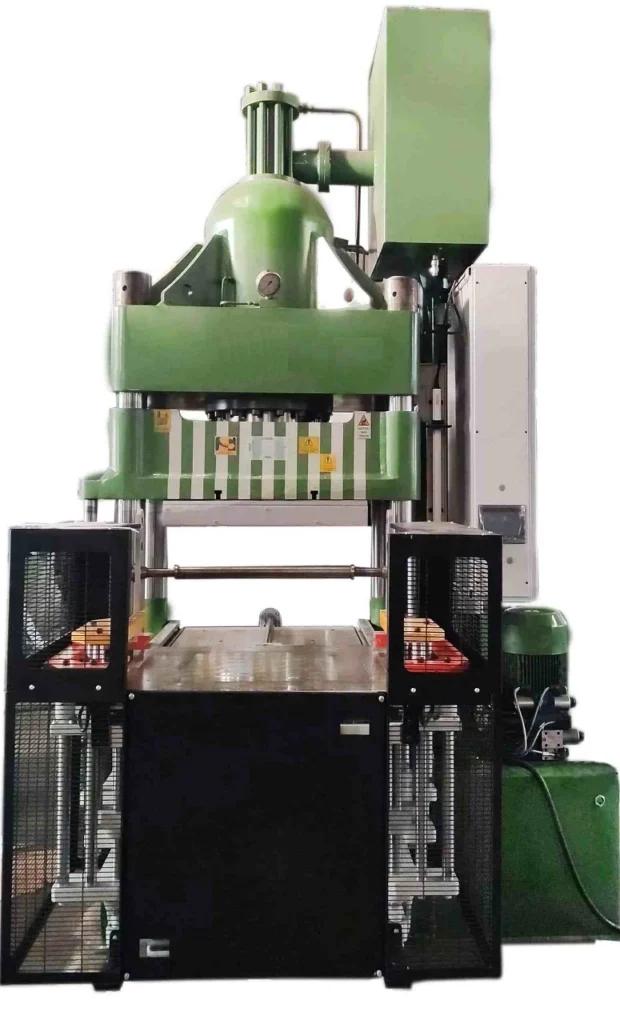
El proceso de embutido industrial es una técnica de conformado en frío que transforma una lámina metálica plana en una pieza tridimensional hueca, mediante la aplicación controlada de fuerzas mecánicas. Este proceso es ampliamente utilizado en la producción masiva de componentes metálicos, ofreciendo alta precisión, repetibilidad y economía en materiales.
El ciclo típico comienza con el suministro del material, generalmente en forma de discos o blanks, que son colocados sobre la matriz de la prensa de embutición. Un punzón presiona el metal contra la matriz, forzándolo a adoptar la forma deseada. Para evitar que el metal se desplace o arrugue en exceso, un aro sujetador o prensachapa mantiene el blank firmemente en su lugar durante la deformación. La velocidad, presión y secuencia del punzón son parámetros críticos que deben ajustarse según el material, espesor y geometría.
En embuticiones profundas o piezas complejas, el proceso puede realizarse en varias etapas sucesivas, conocidas como embutición progresiva o reembutición, donde cada etapa reduce gradualmente el espesor y da forma al producto final. Esto minimiza riesgos de defectos como grietas o arrugas y mejora la uniformidad del espesor. Asimismo, operaciones complementarias como el estirado o el alisado pueden aplicarse para afinar dimensiones y acabados.
La maquinaria industrial para embutido puede ser mecánica, hidráulica o servoaccionada, con prensas de alta precisión que permiten programar movimientos y fuerzas para adaptarse a diferentes diseños y materiales. La automatización incluye alimentación automática de blanks, lubricación controlada y sistemas de inspección en línea para garantizar la calidad de cada pieza.
En resumen, el proceso industrial de embutido es una combinación de diseño de utillaje, control preciso de fuerzas y velocidades, y la correcta selección del material y lubricantes, que permite la fabricación eficiente de piezas metálicas con formas complejas, gran resistencia y acabado óptimo, ampliamente usado en sectores como automotriz, electrodomésticos, envases y construcción.
Durante el proceso industrial de embutido, es fundamental controlar cuidadosamente la fricción entre la lámina y las herramientas para evitar defectos y garantizar un flujo uniforme del material. Para ello se emplean lubricantes especializados que reducen la resistencia al deslizamiento y protegen tanto el metal como las matrices de desgaste prematuro. La elección del lubricante varía según el tipo de metal y el espesor, y su aplicación puede ser manual, por inmersión, pulverización o mediante sistemas automáticos. Además, el diseño del punzón y la matriz debe estar optimizado para facilitar la deformación plástica sin causar concentraciones excesivas de tensión que puedan provocar grietas. La velocidad de la prensa también influye en la calidad; velocidades demasiado altas pueden generar calor y tensiones internas, mientras que velocidades muy bajas pueden afectar la productividad. Para piezas con geometrías complejas o requerimientos estrictos de precisión, se emplean simulaciones por computadora que permiten prever el comportamiento del material, ajustando parámetros antes de la fabricación real. El control dimensional y la inspección de calidad son etapas integrales del proceso, realizándose a menudo mediante sistemas de visión artificial o mediciones táctiles automatizadas para detectar imperfecciones, desviaciones o defectos superficiales. La automatización avanzada incluye además la manipulación robótica para alimentar, extraer y apilar piezas, reduciendo tiempos y riesgos para los operadores. La embutición industrial, por su eficiencia y versatilidad, es clave en la producción en serie de componentes metálicos, permitiendo fabricar desde envases hasta piezas estructurales con alta repetibilidad y bajo costo unitario.
Además, la embutición industrial moderna se complementa con procesos auxiliares que mejoran la funcionalidad y acabado de las piezas. Entre ellos destacan el estampado posterior, que añade detalles como perforaciones o relieves; el troquelado, para recortar piezas o crear ventanas; y el tratamiento superficial, que puede incluir decapado, pintado o recubrimientos protectores para aumentar la resistencia a la corrosión o mejorar la estética. La integración de estas operaciones en líneas automatizadas permite reducir manipulación y acelerar el flujo productivo.
En cuanto a los materiales, la embutición se adapta a una amplia gama, desde aceros blandos y aleaciones ligeras hasta metales más difíciles de conformar, siempre considerando la ductilidad y el límite elástico para evitar fallas durante el doblado. El control de temperatura también puede intervenir en ciertos casos, usando procesos semi-calentados para mejorar la maleabilidad sin afectar la estructura del material.
La trazabilidad es otro aspecto que se ha vuelto crucial, sobre todo en industrias reguladas como la automotriz o aeroespacial, donde cada pieza puede ser identificada y rastreada a lo largo del proceso mediante códigos QR, RFID o marcación láser. Esto facilita el control de calidad, la gestión de inventarios y la respuesta ante posibles defectos o fallos en producción.
Finalmente, el mantenimiento preventivo y predictivo de las prensas y utillajes asegura la continuidad del proceso y reduce tiempos muertos. El desgaste de las matrices, la pérdida de presión hidráulica o el fallo en sensores son monitoreados constantemente para intervenir antes de que se produzcan paradas no programadas.
Así, la embutición industrial representa un equilibrio entre tecnología, diseño, control y logística, permitiendo fabricar piezas metálicas con altos estándares de calidad, eficiencia y costo competitivo.
Etapas del proceso de embutido
Las etapas del proceso de embutido son las siguientes:
- Preparación del material: Se cortan discos o blanks de lámina metálica con el tamaño y forma adecuados para la pieza a fabricar.
- Colocación del blank: El disco se posiciona sobre la matriz de la prensa, asegurando una correcta alineación y soporte.
- Sujeción: Un aro o prensachapa sujeta firmemente el blank para evitar arrugas y deslizamientos durante la deformación.
- Embudo o punzonado inicial: El punzón desciende y comienza a empujar la lámina hacia dentro de la matriz, iniciando la deformación plástica.
- Formado o embutición propiamente dicha: El material fluye y adopta la forma interna de la matriz, transformándose en una pieza hueca con las dimensiones deseadas.
- Reembutición (si es necesaria): En piezas profundas o complejas, se realizan varias etapas sucesivas para evitar defectos, moldeando gradualmente la pieza.
- Alisado o calibrado: Operaciones complementarias para corregir arrugas, mejorar el acabado superficial o ajustar dimensiones.
- Desmoldeo: El punzón o mecanismos auxiliares extraen la pieza terminada de la matriz.
- Inspección y control de calidad: Verificación dimensional y visual para asegurar que la pieza cumple con las especificaciones.
- Procesos adicionales (si aplican): Troquelado, perforado, tratamiento superficial u otros acabados.
Estas etapas pueden variar según el tipo de embutición, material y complejidad de la pieza, pero en general siguen este flujo básico para obtener piezas metálicas conformadas con precisión y calidad.
Después de la inspección y control de calidad, las piezas embutidas pueden pasar por procesos de acabado como el pulido, recubrimiento o pintura, dependiendo del uso final y los requerimientos estéticos o funcionales. En algunas líneas productivas, se incorpora la automatización para transportar las piezas entre estaciones mediante sistemas de rodillos, brazos robóticos o cintas transportadoras, lo que aumenta la velocidad y reduce la manipulación manual. Además, durante el proceso, el monitoreo constante de parámetros como la presión aplicada, el desgaste del utillaje y la lubricación permite detectar a tiempo cualquier desviación que pueda afectar la calidad o provocar fallos, facilitando el mantenimiento predictivo. En la etapa de reembutición, la secuencia y el número de ciclos se determinan con base en simulaciones y pruebas, buscando un balance óptimo entre la calidad de la pieza y la eficiencia del proceso. Las matrices y punzones deben mantenerse en condiciones óptimas, ya que cualquier desgaste o daño puede causar imperfecciones, arrugas o incluso fallos en el material. Por último, la trazabilidad y documentación de cada lote permiten identificar rápidamente problemas en la producción, facilitando la mejora continua y el control de calidad a lo largo del tiempo.
Además, en el proceso de embutido industrial se considera fundamental la capacitación del personal y la estandarización de procedimientos para garantizar la repetibilidad y minimizar errores humanos. El diseño de los utillajes se realiza siempre con enfoque en la facilidad de mantenimiento y rápido cambio, para reducir los tiempos de paro en la producción. En la actualidad, se incorporan tecnologías digitales como la realidad aumentada y sensores inteligentes para asistir a los operadores en el montaje y ajuste del equipo, así como para monitorear en tiempo real las condiciones de trabajo. Esto contribuye a aumentar la seguridad laboral y la eficiencia operativa. Por otro lado, el desarrollo de nuevos materiales y aleaciones con mejores propiedades mecánicas impulsa la innovación en técnicas de embutición, permitiendo fabricar piezas más ligeras y resistentes, cruciales en sectores como la automoción y aeroespacial. Finalmente, la integración de todo el proceso en sistemas de manufactura avanzada hace que la embutición deje de ser un simple proceso de conformado para convertirse en un eslabón clave dentro de cadenas productivas inteligentes y sostenibles.
El proceso de embutido industrial comienza con la preparación del material, donde se selecciona y corta la lámina metálica en discos o blanks con dimensiones específicas. Esta etapa es fundamental para garantizar que el material base cumpla con las propiedades mecánicas necesarias para soportar la deformación plástica que tendrá lugar sin generar fisuras o roturas. Los materiales más comunes son el acero al carbono, acero inoxidable, aluminio y sus aleaciones, seleccionados según la aplicación final. Además, se evalúa el espesor del material y se comprueba que esté libre de defectos superficiales que puedan afectar el resultado final.
A continuación, el blank es colocado sobre la matriz de la prensa embutidora. Esta acción debe realizarse con alta precisión para asegurar una correcta alineación entre la pieza y las herramientas, evitando defectos en el conformado. Para mantener el blank en su lugar y controlar el flujo del metal durante el proceso, un aro sujetador o prensachapa presiona sobre los bordes externos del disco. Esta sujeción evita que la chapa se desplace o arrugue, lo que es especialmente importante en piezas con altos grados de deformación o en embuticiones profundas.
Cuando la prensa inicia la carrera, el punzón desciende lentamente, haciendo contacto con el blank y forzándolo a entrar en la matriz. El metal comienza a fluir de manera plástica, adoptando gradualmente la forma hueca deseada. La interacción entre el punzón, la matriz y el prensachapa es crítica para distribuir correctamente las tensiones y evitar la aparición de defectos tales como grietas o arrugas. La presión y la velocidad del punzón deben estar cuidadosamente controladas; un avance muy rápido puede generar fallas internas por acumulación de tensiones, mientras que uno demasiado lento puede afectar la productividad.
Para piezas con geometrías complejas o grandes profundidades, el embutido se realiza en múltiples etapas llamadas reembuticiones o embuticiones sucesivas. Cada etapa reduce progresivamente el espesor del material y conforma la pieza en pasos controlados, lo que minimiza el riesgo de daños y permite alcanzar formas que no serían posibles con una sola pasada. Entre estas etapas, puede aplicarse el proceso de alisado para corregir pequeñas irregularidades y mejorar el acabado superficial, garantizando dimensiones más precisas.
Un aspecto clave durante el proceso es la lubricación. La fricción entre el material y las herramientas influye directamente en la calidad del embutido, la fuerza necesaria y el desgaste de las matrices. Por ello, se aplican lubricantes especializados que pueden ser en base aceite, emulsiones o sólidos, elegidos según el tipo de material y las condiciones del proceso. Una lubricación adecuada reduce la fricción, facilita el flujo del metal y prolonga la vida útil de las herramientas, además de mejorar el acabado de la pieza.
Tras completar el embutido y las posibles etapas adicionales, la pieza es retirada de la matriz mediante sistemas automáticos o manuales. Este desmoldeo debe ser cuidadoso para no deformar o dañar la pieza terminada. En líneas de producción modernas, esta operación está integrada con sistemas robóticos que permiten manipular las piezas rápidamente y reducir la intervención humana, aumentando la seguridad y la productividad.
La inspección y el control de calidad son esenciales para asegurar que cada pieza cumpla con las especificaciones dimensionales, mecánicas y estéticas. Se utilizan instrumentos de medición precisos, desde calibres y micrómetros hasta sistemas de visión artificial y sensores táctiles automatizados. Además, se verifica la ausencia de defectos superficiales como grietas, arrugas o marcas de herramienta. En industrias con altos requerimientos, la trazabilidad se implementa mediante códigos o marcas láser que permiten seguir la pieza a lo largo de toda la cadena productiva.
Por último, las piezas embutidas pueden pasar a procesos secundarios como troquelado, perforado, estampado o tratamientos superficiales como pintura, galvanizado o recubrimientos protectores, que dotan a la pieza de propiedades adicionales o cumplen requerimientos estéticos.
El éxito del proceso de embutido industrial depende no solo de la maquinaria y herramientas empleadas, sino también del diseño del utillaje, la selección correcta de materiales, la optimización de parámetros operativos y la gestión integral de la producción. Además, las tecnologías actuales como la simulación por elementos finitos permiten prever el comportamiento del material y optimizar el proceso antes de realizar pruebas físicas, ahorrando tiempo y costos. La automatización y la digitalización contribuyen a aumentar la productividad, mejorar la calidad y reducir los tiempos de ciclo, haciendo que el embutido sea un proceso altamente eficiente y versátil en la fabricación de piezas metálicas para múltiples industrias, desde la automotriz hasta la de envases y electrodomésticos.
Tipos de embutido de metales
Claro, aquí tienes una explicación detallada sobre los tipos de embutido de metales, con texto extenso para cubrir cada modalidad:
El embutido de metales abarca varios tipos o técnicas, cada una adaptada a diferentes requisitos de forma, profundidad, material y aplicación final. Comprender las diferencias entre estos tipos permite seleccionar el método más adecuado según las características de la pieza y la producción requerida. A continuación, se describen los principales tipos de embutido utilizados en la industria:
- Embutido superficial (Shallow Drawing):
Este tipo de embutido se caracteriza por una profundidad relativamente pequeña en comparación con el diámetro del blank. Se utiliza principalmente para fabricar piezas que requieren una deformación leve, como tapas, platos o recipientes poco profundos. La deformación es sencilla y generalmente se realiza en una sola etapa, sin necesidad de reembuticiones adicionales. Este proceso es rápido, con menor demanda de fuerza y desgaste en las herramientas, y permite alta velocidad de producción. - Embutido profundo (Deep Drawing):
El embutido profundo implica una deformación más significativa, donde la profundidad de la pieza es igual o mayor que su diámetro inicial. Este tipo de embutido es habitual para fabricar piezas como latas, cilindros, vasos, ollas y componentes automotrices. Debido a la mayor deformación, suele requerir múltiples etapas de embutido o reembuticiones para evitar fallos como arrugas o fracturas. La gestión adecuada del flujo de material, la lubricación y la selección de herramientas es crucial en este proceso. Además, se requiere una prensa con mayor capacidad de fuerza. - Embutido inverso o redibujo (Reverse Drawing or Redrawing):
En este proceso, la pieza embutida inicialmente se somete a un segundo embutido en sentido opuesto para aumentar su profundidad o modificar sus dimensiones internas. El redibujo se emplea para obtener formas más profundas o con paredes más delgadas, permitiendo mejorar las propiedades mecánicas y la uniformidad del espesor. Es común en la fabricación de recipientes metálicos, componentes de automoción y artículos de cocina. - Embutido incremental:
Este método utiliza herramientas que deforman el material de manera gradual y localizada, en lugar de aplicar la fuerza sobre toda la superficie a la vez. El embutido incremental permite fabricar piezas con geometrías complejas y con menores requerimientos de fuerza, ya que el material se va conformando poco a poco. Además, reduce el riesgo de fallas en materiales con baja ductilidad o espesores variables. Este tipo de embutido es útil en prototipado, producción de pequeñas series y aplicaciones especiales. - Embutido por hidroformado:
En el hidroformado, en lugar de un punzón sólido, se utiliza un fluido a alta presión para conformar la lámina contra un molde cerrado. Este proceso permite obtener formas muy complejas con excelente acabado superficial y mayor uniformidad en el espesor. Es especialmente valioso para fabricar piezas automotrices, aeroespaciales y tuberías complejas. El hidroformado puede ser realizado en frío o en caliente, dependiendo del material y la aplicación. - Embutido con soporte o con respaldo:
En este tipo, durante el embutido se utiliza un soporte o respaldo que ayuda a controlar el flujo del material y evitar arrugas o fracturas, mejorando la calidad de la pieza. Es especialmente útil en embuticiones profundas o en materiales difíciles de conformar. - Embutido por estampado:
Combina el embutido con operaciones de estampado, donde el material no solo se deforma para tomar forma, sino que también puede recibir relieves, perforaciones o cortes en un solo ciclo o en procesos consecutivos. Este tipo es común en la fabricación de carcasas, paneles y piezas decorativas.
Cada tipo de embutido tiene sus ventajas, limitaciones y aplicaciones específicas. La elección del método adecuado depende del diseño de la pieza, el material, el volumen de producción, la complejidad geométrica y las propiedades mecánicas requeridas. En la industria moderna, muchas veces se combinan varias técnicas para optimizar la fabricación, reducir costos y mejorar la calidad del producto final.
Además de los tipos mencionados, es importante destacar que el embutido puede combinarse con otras operaciones de conformado para ampliar las posibilidades de diseño y funcionalidad de las piezas metálicas. Por ejemplo, el embutido profundo puede integrarse con procesos de estampado para agregar detalles como relieves, ranuras o perforaciones sin necesidad de separar la pieza del ciclo de conformado. Esta combinación permite producir piezas más complejas en menos tiempo y con mayor precisión.
En el caso del embutido incremental, aunque es más lento que los métodos convencionales, ofrece una gran ventaja en la fabricación de prototipos y series pequeñas, ya que no requiere herramientas costosas ni cambios complejos en el utillaje. Además, su capacidad para trabajar materiales con propiedades difíciles, como aleaciones de titanio o acero inoxidable de alta resistencia, lo hace muy útil en sectores aeroespaciales y médicos.
El hidroformado, por su parte, ha revolucionado la fabricación de piezas con geometrías intrincadas y gran relación entre altura y diámetro, gracias a la presión uniforme que ejerce el fluido. Esto no solo mejora la calidad superficial, sino que también optimiza la distribución del espesor, evitando puntos de tensión que pueden causar fallas. Sin embargo, este proceso requiere equipos especializados y un control preciso de la presión y temperatura, lo que implica una inversión mayor y capacitación técnica avanzada.
Por otro lado, el embutido con soporte o respaldo permite manejar mejor las tensiones durante la deformación, lo que es fundamental cuando se trabaja con materiales delicados o con espesores muy reducidos. El soporte actúa como una barrera que guía el flujo del material, ayudando a prevenir defectos y facilitando un acabado más uniforme.
Finalmente, la integración de tecnologías digitales y de simulación ha permitido optimizar cada tipo de embutido, anticipando posibles defectos y ajustando parámetros para maximizar la calidad y la eficiencia. La elección del tipo de embutido adecuado, junto con una correcta planificación y diseño del proceso, son factores clave para lograr productos metálicos con altos estándares, cumpliendo con las demandas de sectores tan diversos como el automotriz, electrónico, aeroespacial y de envases.
Sumando a lo anterior, el desarrollo de nuevos materiales y la creciente demanda de piezas con geometrías cada vez más complejas han impulsado la innovación en las técnicas de embutido. Por ejemplo, la utilización de aceros de alta resistencia y aleaciones ligeras como el aluminio y el magnesio requiere adaptar los procesos para mantener la ductilidad y evitar defectos durante el conformado. En estos casos, es común aplicar técnicas de embutido asistido por calor, donde el material se calienta a temperaturas controladas para facilitar su deformación sin perder propiedades mecánicas.
Asimismo, la industria está adoptando cada vez más soluciones híbridas que combinan embutido con otros métodos de conformado, como el estirado o el plegado, para fabricar piezas multifuncionales que cumplen con estándares de peso, resistencia y estética. Esto es especialmente relevante en sectores como el automotriz y aeroespacial, donde la reducción de peso y el rendimiento estructural son prioritarios.
La automatización juega un rol crucial en la optimización del embutido, no solo en la operación de las prensas sino también en el manejo y seguimiento de las piezas. Los sistemas robotizados alimentan blanks, realizan múltiples embuticiones consecutivas, inspeccionan las piezas y las preparan para procesos posteriores, todo con mínima intervención humana. Esto aumenta la capacidad productiva, reduce errores y mejora la seguridad en planta.
Finalmente, la integración de sensores y tecnologías de Industria 4.0 permite recopilar datos en tiempo real sobre las condiciones de proceso, el desgaste de herramientas y la calidad de las piezas, facilitando el mantenimiento predictivo y la mejora continua. De este modo, el embutido industrial evoluciona hacia procesos más inteligentes, flexibles y sostenibles, capaces de satisfacer las demandas actuales de la fabricación avanzada.
Si te interesa, puedo continuar explicando cómo se aplican estas tecnologías específicas o cómo se diseñan los utillajes para cada tipo de embutido.
Equipos hidráulicos para bordonado de metales
Los equipos hidráulicos para bordonado de metales son máquinas diseñadas para realizar operaciones de rebordeado (o bordonado) sobre piezas metálicas, generalmente de forma circular o cilíndrica, como tapas, fondos, recipientes, tubos y cuerpos embutidos. El proceso de bordonado consiste en formar un borde o pestaña en la periferia de una pieza, ya sea para reforzar su estructura, facilitar un ensamble, mejorar el acabado o cumplir una función técnica o estética. El accionamiento hidráulico ofrece la fuerza controlada y constante necesaria para conformar metales sin generar grietas ni deformaciones no deseadas.
Estos equipos utilizan cilindros hidráulicos de gran precisión para aplicar presión de manera gradual y controlada sobre la zona del borde, moldeándolo mediante rodillos perfiladores o herramientas específicas que giran sobre la pieza mientras esta rota sobre su eje. En muchos casos, se combinan con mesas giratorias motorizadas o cabezales rotativos que permiten mantener una velocidad constante durante el proceso. El sistema hidráulico regula la presión de contacto y la velocidad de avance de la herramienta, lo que garantiza uniformidad y acabado superficial de alta calidad, incluso en metales duros o en piezas de gran espesor.
Los equipos hidráulicos de bordonado pueden ser de configuración horizontal o vertical, dependiendo del tipo de pieza y del flujo de producción. Algunos modelos están diseñados exclusivamente para tareas de bordonado, mientras que otros forman parte de estaciones múltiples que combinan embutido, corte, perfilado y otras operaciones en un solo ciclo. En las versiones más avanzadas, el proceso es completamente automatizado mediante CNC o PLC, lo que permite programar diferentes radios, ángulos y profundidades de rebordeado, y adaptarse a una gran variedad de diseños sin cambiar herramientas manualmente.
El bordonado hidráulico se utiliza ampliamente en la fabricación de depósitos presurizados, ollas, extintores, filtros, componentes automotrices, y estructuras metálicas de precisión. Su ventaja principal es la capacidad de trabajar piezas robustas con resultados consistentes, sin comprometer la integridad estructural del material. Además, al combinar fuerza, precisión y control, estos equipos permiten producir bordes reforzados que aumentan la rigidez, mejoran la resistencia a la fatiga y optimizan el comportamiento funcional de la pieza final.
En el funcionamiento de los equipos hidráulicos para bordonado, la precisión en el control de la fuerza y del desplazamiento de la herramienta es esencial para evitar que el material se agriete, se arrugue o se deforme de manera irregular. Por eso, muchos de estos sistemas incorporan válvulas proporcionales y servoválvulas que permiten ajustar dinámicamente la presión y la velocidad de los cilindros durante el ciclo de trabajo. Además, los sensores de posición y de presión instalados en los actuadores hidráulicos envían datos en tiempo real a la unidad de control, asegurando una retroalimentación constante para mantener tolerancias estrechas en la operación.
El cabezal de bordonado, normalmente fabricado en acero de alta resistencia o materiales endurecidos, aloja los rodillos conformadores, los cuales pueden intercambiarse fácilmente para adaptarse a diferentes radios de borde, perfiles o espesores de material. La rotación de la pieza durante el bordonado puede realizarse mediante mandriles motorizados o platos giratorios sincronizados con el avance de la herramienta, lo que garantiza una formación continua y uniforme del reborde sin pausas ni solapamientos. En algunas configuraciones, especialmente aquellas destinadas a piezas de grandes dimensiones, el cabezal puede desplazarse radialmente y axialmente para trabajar en diferentes zonas del componente sin necesidad de reposicionarlo.
La estabilidad y robustez de la estructura del equipo también son fundamentales para absorber las cargas de trabajo sin generar vibraciones o desviaciones. Las máquinas de tipo bastidor cerrado o con diseño en C reforzado proporcionan la rigidez necesaria para soportar el empuje hidráulico sin comprometer la precisión del proceso. Además, muchas versiones incluyen sistemas de refrigeración y filtrado del aceite hidráulico para mantener una operación estable, prolongar la vida útil del equipo y evitar calentamientos excesivos durante ciclos continuos.
En aplicaciones donde se manejan materiales sensibles o acabados visibles, como en productos de línea blanca o artículos de cocina, el bordonado debe ejecutarse con especial cuidado para no dejar marcas o rayaduras. Para ello, se utilizan rodillos pulidos, recubrimientos especiales o lubricantes específicos que reducen la fricción entre la herramienta y la superficie del metal. En el caso de metales recubiertos o anodizados, también se pueden emplear herramientas con geometrías personalizadas que respetan los radios mínimos y evitan esfuerzos innecesarios sobre el material.
Los equipos hidráulicos para bordonado pueden trabajar sobre acero al carbono, acero inoxidable, aluminio, cobre y otras aleaciones, adaptando la presión y velocidad según la dureza y comportamiento de cada material. La flexibilidad del sistema hidráulico permite también realizar bordes de diferentes tipos: bordes rectos, curvos, doblados hacia dentro o hacia fuera, y pestañas reforzadas con múltiples pasadas. En líneas de producción de alta demanda, estos equipos pueden formar parte de celdas robotizadas que incluyen alimentación automática de piezas, cambio rápido de herramientas y sistemas de inspección visual, asegurando una producción continua, trazable y de alta calidad.
En líneas de fabricación avanzadas, los equipos hidráulicos para bordonado pueden integrarse con sistemas de visión artificial y sensores de escaneo láser para verificar, durante o inmediatamente después del proceso, que el borde formado cumpla con los parámetros de diseño establecidos. Esto permite una corrección inmediata de desviaciones, la detección de imperfecciones como rebabas, pliegues irregulares o deformaciones, y garantiza una calidad constante sin necesidad de inspección manual pieza por pieza. Este nivel de control es especialmente crítico en sectores como el aeroespacial, farmacéutico o de envases presurizados, donde cualquier desviación puede comprometer la seguridad o el rendimiento del producto.
A nivel de diseño, muchas de estas máquinas incluyen software especializado que permite simular el ciclo de bordonado antes de ejecutarlo físicamente. Con ello, se pueden ajustar virtualmente la trayectoria del rodillo, el número de pasadas, la presión y la velocidad según las características del material y la geometría de la pieza. Esta capacidad de simulación reduce el número de pruebas físicas, ahorra tiempo de puesta a punto y evita el desperdicio de material durante la fase de configuración. Además, permite documentar parámetros específicos para diferentes lotes de producción o modelos, facilitando la repetibilidad del proceso.
En cuanto a mantenimiento, los sistemas hidráulicos de bordonado requieren una rutina preventiva bien establecida para asegurar el rendimiento constante de los cilindros, válvulas y elementos de control. El aceite hidráulico debe mantenerse limpio, a la temperatura adecuada y con una viscosidad constante para garantizar la respuesta del sistema. También es común utilizar sistemas de autodiagnóstico que alertan sobre caídas de presión, fugas, desgaste en los sellos o anomalías en la alineación de las herramientas. Esto permite programar intervenciones técnicas sin necesidad de detener la producción inesperadamente.
Un aspecto cada vez más importante en el diseño de estos equipos es la eficiencia energética. Aunque los sistemas hidráulicos tradicionales han sido considerados menos eficientes que los eléctricos, los avances en servo-hidráulica y en bombas de caudal variable han mejorado significativamente el consumo de energía. Hoy en día, muchas prensas de bordonado hidráulicas están equipadas con unidades de potencia inteligentes que ajustan automáticamente la presión y el caudal según la carga del proceso, reduciendo el uso energético cuando la máquina está en reposo o en ciclos de baja exigencia.
En conjunto, los equipos hidráulicos para bordonado representan una solución versátil, potente y adaptable para una amplia gama de aplicaciones industriales. Son ideales para tareas que requieren gran fuerza, deformación progresiva y precisión dimensional, y gracias a los avances tecnológicos, ahora ofrecen también altos niveles de automatización, control, eficiencia y trazabilidad. Esta combinación de fuerza mecánica y control inteligente convierte al bordonado hidráulico en una herramienta clave dentro de la fabricación avanzada de componentes metálicos.
Bordonadoras de alta presión hidráulicas
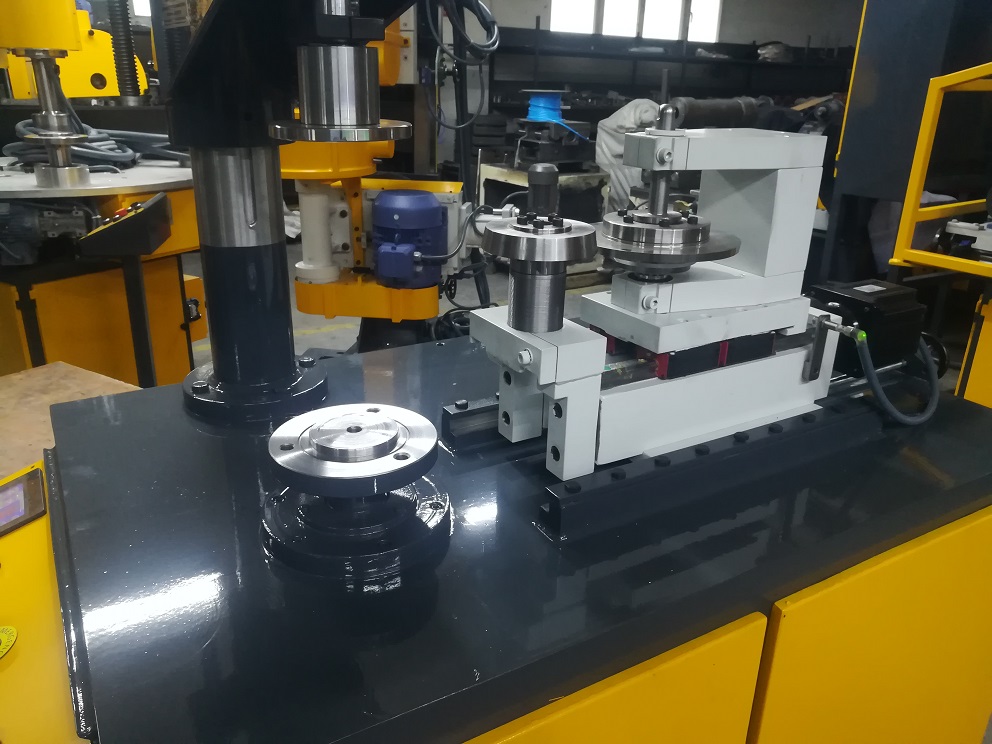
Las bordonadoras de alta presión hidráulicas son equipos industriales especializados diseñados para realizar operaciones de rebordeado en piezas metálicas que requieren altos niveles de fuerza, precisión y resistencia estructural. A diferencia de bordonadoras convencionales, estas máquinas están preparadas para aplicar presiones elevadas —habitualmente superiores a 150 bar e incluso por encima de 300 bar en aplicaciones exigentes— lo que las hace especialmente adecuadas para trabajar con materiales de alto espesor, metales duros o piezas de grandes dimensiones donde se requiere una deformación intensa y controlada.
Estas bordonadoras emplean cilindros hidráulicos reforzados, capaces de desarrollar grandes fuerzas de empuje, manteniendo una progresión suave y constante a lo largo del borde de la pieza. El proceso se realiza generalmente mediante rodillos conformadores montados sobre cabezales móviles o herramientas de contorno que, al girar sobre la periferia de la pieza, generan el borde deseado con alta precisión. El diseño robusto de estos equipos asegura que las deformaciones no generen vibraciones ni desviaciones estructurales, manteniendo una calidad uniforme incluso en ciclos prolongados o condiciones de carga extrema.
En aplicaciones como la fabricación de tanques presurizados, fondos bombeados, ollas industriales, depósitos cilíndricos, tubos estructurales o tapas reforzadas, las bordonadoras de alta presión hidráulicas ofrecen una solución insustituible. La posibilidad de aplicar rebordeados con múltiples pasadas, variando presión y velocidad según la etapa del ciclo, permite obtener rebordes reforzados, con radios grandes o bordes doblados hacia el interior o exterior, sin comprometer la integridad del material.
La regulación de presión se realiza mediante válvulas hidráulicas proporcionales y unidades de potencia controladas por PLC o CNC, lo que permite ajustar el proceso con alta precisión y repetirlo de forma totalmente automatizada. La pieza puede girar sobre platos motorizados o ejes sincronizados, y el cabezal puede desplazarse radial y axialmente para adaptarse a diferentes geometrías. En equipos de gama alta, los sistemas de compensación electrónica y monitoreo por sensores garantizan una presión uniforme durante toda la operación, independientemente de la dureza del material o las variaciones de espesor.
El control inteligente también permite registrar los parámetros de cada ciclo, identificar tendencias de desgaste o desviación, y hacer ajustes automáticos en tiempo real. Esto reduce el margen de error, minimiza el desperdicio de material y mejora la trazabilidad del producto final. Además, muchas de estas máquinas incluyen sistemas de cambio rápido de herramientas, facilitando la adaptación del equipo a distintos modelos o familias de piezas sin tiempos prolongados de preparación.
Las bordonadoras hidráulicas de alta presión son, por tanto, una solución indispensable en líneas de producción donde la calidad estructural, la resistencia mecánica del borde y la fiabilidad del proceso son requisitos clave. Gracias a su capacidad de trabajo continuo, su potencia y su integración con sistemas de control avanzados, se convierten en una herramienta crítica para sectores como el automotriz, naval, aeroespacial, energético, alimentario y químico, donde se trabaja con piezas metálicas sometidas a exigencias extremas de funcionamiento.
En el funcionamiento continuo de una bordonadora hidráulica de alta presión, la coordinación precisa entre fuerza aplicada, trayectoria del cabezal y velocidad de rotación de la pieza es esencial para mantener una formación uniforme del borde sin generar tensiones internas excesivas ni deformaciones no deseadas. A medida que el rodillo de bordonado entra en contacto con la superficie metálica, la fuerza hidráulica presiona el metal de manera gradual contra el molde o contra sí mismo, dependiendo del diseño, permitiendo crear perfiles curvos, pestañas externas, acanalados o dobleces estructurales con alto grado de repetibilidad. Este tipo de conformado no solo mejora la resistencia del borde ante cargas mecánicas o presión interna, sino que también incrementa la rigidez de la pieza, evita vibraciones y puede facilitar su posterior ensamblaje o sellado.
Gracias al sistema hidráulico de alto rendimiento, estas máquinas pueden mantener una presión constante durante toda la pasada, independientemente del diámetro de la pieza o de las pequeñas variaciones de espesor que pueda presentar el material. Esto es especialmente importante en piezas grandes, donde el rebordeado recorre superficies extensas y cualquier pérdida de presión provocaría irregularidades perceptibles en el borde. La potencia generada por los cilindros hidráulicos permite trabajar con espesores superiores a los que podrían manejar equipos mecánicos o eléctricos, y con materiales difíciles como acero al carbono de alta resistencia, inoxidable endurecido, bronce estructural, aleaciones níquel-cromo o incluso titanio en procesos especiales.
Además, la posibilidad de integrar múltiples rodillos en un solo cabezal, cada uno con una función específica —por ejemplo, uno para doblar el borde, otro para formar el perfil, y un tercero para compactar o alisar la pestaña— permite realizar en una sola operación lo que normalmente requeriría varias estaciones de trabajo. Este diseño modular y adaptable agiliza el proceso productivo y asegura que cada pasada se ejecute con parámetros optimizados según el comportamiento real del material, lo que es posible gracias a la información recogida por sensores de presión, esfuerzo, vibración y temperatura montados directamente en los componentes clave del sistema.
En cuanto a mantenimiento, las bordonadoras de alta presión están diseñadas con sistemas hidráulicos cerrados y filtros de alta eficiencia que mantienen el aceite limpio y estable incluso bajo condiciones extremas de operación. Los controles integrados monitorean el estado del fluido, la presión del sistema, el desgaste de los sellos y la alineación de los actuadores. Cualquier desviación puede ser reportada automáticamente al sistema de gestión, permitiendo programar el mantenimiento antes de que surjan fallas, reduciendo así el tiempo de inactividad y prolongando la vida útil del equipo.
Por otro lado, estas máquinas están preparadas para cumplir con altos estándares de seguridad, integrando barreras fotoeléctricas, controles bimanuales, paradas de emergencia redundantes y monitoreo en tiempo real de sobrepresión o bloqueo de herramientas. En entornos automatizados, los robots colaborativos pueden encargarse de cargar, posicionar y descargar las piezas, optimizando el flujo de trabajo sin comprometer la seguridad del operador. Las interfaces hombre-máquina son cada vez más intuitivas, con pantallas táctiles, visualización gráfica del ciclo y conexión a redes industriales, permitiendo supervisión remota, análisis de rendimiento, y trazabilidad completa de cada operación realizada.
Así, una bordonadora hidráulica de alta presión no es solo una máquina de fuerza, sino una plataforma tecnológica altamente precisa y adaptable, capaz de afrontar con eficiencia y confiabilidad los desafíos actuales de la fabricación avanzada de componentes metálicos de alto valor añadido.
Además, la evolución tecnológica ha impulsado la incorporación de sistemas de control avanzado basados en inteligencia artificial y aprendizaje automático para optimizar el rendimiento de las bordonadoras hidráulicas de alta presión. Estos sistemas pueden analizar grandes volúmenes de datos provenientes de sensores en tiempo real, detectar patrones y predecir posibles fallos o desviaciones antes de que afecten la producción. Esto permite implementar ajustes automáticos en la presión, velocidad o trayectoria, adaptándose dinámicamente a las variaciones del material o condiciones ambientales, garantizando una calidad constante y reduciendo el desperdicio.
La flexibilidad de estas máquinas también facilita la fabricación de lotes pequeños o personalizados sin perder eficiencia, gracias a la rápida reprogramación de los parámetros y el cambio automático de herramientas. Esto responde a las necesidades actuales del mercado, donde la producción masiva convive con la demanda de productos más variados y con tiempos de entrega reducidos.
En cuanto a la sostenibilidad, las bordonadoras modernas buscan minimizar el consumo energético y el impacto ambiental mediante el uso de sistemas hidráulicos con bombas de velocidad variable, recuperación de energía y lubricantes biodegradables. Además, la precisión del proceso reduce la cantidad de material desperdiciado y la necesidad de retrabajos o reprocesos, contribuyendo a una fabricación más responsable y económica.
Por último, la integración con sistemas de gestión de manufactura y planificación de recursos empresariales (ERP) permite coordinar el proceso de bordonado dentro de una cadena productiva digitalizada, facilitando el seguimiento de pedidos, la gestión de inventarios y la optimización logística. Esto convierte a la bordonadora hidráulica de alta presión en un elemento clave dentro de fábricas inteligentes, capaces de responder con agilidad y calidad a los retos industriales actuales y futuros.
Si deseas, puedo profundizar en aspectos específicos como el diseño hidráulico, los tipos de herramientas para bordonado o ejemplos de aplicaciones en diferentes industrias.
Sistemas hidráulicos de bordonado
Los sistemas hidráulicos de bordonado son el conjunto de componentes y mecanismos que permiten aplicar fuerzas controladas y precisas para realizar el rebordeado o perfilado de piezas metálicas mediante presión hidráulica. Estos sistemas constituyen el corazón de las máquinas bordonadoras, ya que la calidad y repetibilidad del proceso dependen en gran medida de la eficiencia y precisión con la que se genere y regule la presión, el flujo y el movimiento de los actuadores hidráulicos.
En un sistema hidráulico típico de bordonado, la energía se suministra mediante una bomba hidráulica que impulsa aceite a presión hacia uno o varios cilindros hidráulicos. Estos cilindros actúan sobre herramientas como rodillos o punzones que deforman el metal en la zona del borde. La regulación de presión y velocidad se realiza a través de válvulas proporcionales, servoválvulas o válvulas direccionales, que permiten ajustar dinámicamente la fuerza y el movimiento para adaptarse a diferentes materiales, espesores y geometrías de las piezas.
El circuito hidráulico incluye además acumuladores para estabilizar la presión, filtros para mantener la pureza del fluido y enfriadores para controlar la temperatura del aceite, asegurando así una operación constante y prolongada sin degradación del sistema. Los sensores de presión, temperatura y posición instalados en puntos estratégicos proporcionan datos en tiempo real a la unidad de control, que puede ser un PLC o un CNC, encargados de supervisar y ajustar automáticamente los parámetros de trabajo según las condiciones detectadas.
En bordonadoras modernas, la integración del sistema hidráulico con la electrónica de control permite la programación de perfiles de presión y velocidad variables durante el ciclo, lo que es fundamental para realizar bordes complejos, múltiples pasadas o adaptarse a cambios en la dureza del material. Esta capacidad aumenta la precisión del rebordeado, reduce el desgaste de las herramientas y minimiza defectos como grietas o arrugas.
El diseño hidráulico debe considerar también aspectos de seguridad, incorporando dispositivos para evitar sobrepresiones, fugas o fallos bruscos en el sistema. Además, la disposición compacta y modular de los componentes facilita el mantenimiento y la rápida sustitución de elementos, reduciendo tiempos de paro y mejorando la disponibilidad de la máquina.
Finalmente, el avance en tecnologías hidráulicas, como las bombas de caudal variable, servomotores hidráulicos y sistemas electrohidráulicos híbridos, está permitiendo que los sistemas hidráulicos de bordonado sean cada vez más eficientes energéticamente, precisos y adaptables a las demandas de la industria 4.0 y las líneas de fabricación inteligentes.
¿Quieres que te explique con más detalle alguna parte específica del sistema hidráulico o cómo se integra con la maquinaria de bordonado?
El sistema hidráulico de bordonado funciona como un mecanismo que convierte la energía hidráulica en fuerza mecánica controlada para dar forma a los bordes de piezas metálicas. La bomba hidráulica, que puede ser de desplazamiento fijo o variable, suministra aceite a alta presión hacia los cilindros que actúan sobre los rodillos o herramientas de conformado. Las bombas de caudal variable son preferidas en máquinas modernas porque ajustan automáticamente el flujo según la demanda, optimizando el consumo energético y mejorando la respuesta dinámica del sistema.
El aceite hidráulico circula a través de válvulas proporcionales o servoválvulas que regulan con precisión la presión y la velocidad del fluido, lo que se traduce en un control fino de la fuerza aplicada y la velocidad del punzón o rodillo de bordonado. Estas válvulas reciben señales de control del PLC o CNC, que ejecuta programas predefinidos para cada tipo de pieza o material, permitiendo variar el perfil de presión a lo largo del ciclo para evitar defectos y lograr un acabado óptimo.
Los cilindros hidráulicos, fabricados con materiales de alta resistencia y precisión, convierten la presión del aceite en un movimiento lineal o rotativo. En bordonadoras, estos cilindros pueden ser simples o dobles efectos, según si se requiere movimiento en una sola dirección o en ambas. La estabilidad y la respuesta rápida de los cilindros son fundamentales para mantener la uniformidad en el bordonado, especialmente en piezas de gran diámetro o espesores variables.
El circuito hidráulico incorpora acumuladores que actúan como amortiguadores de presión, estabilizando el flujo y evitando pulsaciones que puedan afectar la calidad del proceso. Además, filtros de alta eficiencia mantienen el aceite libre de partículas contaminantes, lo que es crucial para evitar daños en las válvulas y cilindros y prolongar la vida útil del sistema. Los enfriadores mantienen la temperatura del fluido dentro de rangos óptimos, evitando el sobrecalentamiento que puede alterar las propiedades del aceite y disminuir la eficiencia.
Los sensores instalados en el sistema monitorean continuamente parámetros clave como presión, temperatura, caudal y posición de los actuadores. Esta información es procesada en tiempo real por el controlador, que ajusta las variables para mantener la operación dentro de los parámetros establecidos y generar alertas tempranas en caso de anomalías. Este nivel de supervisión permite implementar estrategias de mantenimiento predictivo y optimizar la producción.
Además, el diseño modular del sistema hidráulico facilita la integración con otros subsistemas de la máquina, como los mecanismos de rotación y posicionamiento de la pieza, la alimentación automática y los sistemas de inspección. La capacidad de programar ciclos completos y ajustar perfiles de presión y velocidad permite que el bordonado se realice de forma rápida, precisa y repetible, incluso en piezas con geometrías complejas o materiales difíciles de conformar.
En resumen, los sistemas hidráulicos de bordonado combinan potencia, precisión y control avanzado para ofrecer soluciones flexibles y eficientes en la conformación de bordes metálicos. Su evolución continua, basada en mejoras tecnológicas y en la integración con la digitalización industrial, garantiza que estas máquinas sigan siendo una herramienta clave en la fabricación moderna de componentes metálicos.
Además, los sistemas hidráulicos de bordonado suelen incorporar dispositivos de seguridad y protección que evitan daños tanto en la máquina como en las piezas y operadores. Por ejemplo, existen válvulas de alivio que limitan la presión máxima del sistema para prevenir sobrecargas, y sensores de posición que detienen el movimiento si se detectan anomalías o colisiones. Estos elementos son imprescindibles en entornos industriales donde la seguridad es prioritaria y la continuidad operativa es crucial.
En cuanto al mantenimiento, es fundamental realizar inspecciones periódicas del aceite hidráulico, verificando niveles, viscosidad y pureza, además de revisar el estado de los sellos, cilindros y conexiones para evitar fugas. El mantenimiento predictivo apoyado en la telemetría y análisis de datos permite anticipar desgastes o fallos antes de que ocurran, lo que reduce costos y tiempos de inactividad.
Para mejorar la eficiencia energética, muchas bordonadoras modernas utilizan sistemas electrohidráulicos híbridos que combinan la fuerza del hidráulico con la precisión y control de los actuadores eléctricos. Estos sistemas permiten un consumo de energía más bajo, menor generación de calor y mayor velocidad de respuesta, lo que se traduce en una mayor productividad y sostenibilidad ambiental.
Finalmente, la integración del sistema hidráulico con software de simulación y control avanzado facilita la planificación y optimización del proceso de bordonado. A través de modelos digitales, se pueden prever comportamientos del material y ajustar parámetros antes de iniciar la producción física, evitando errores y mejorando la calidad final. Esta digitalización contribuye a la evolución hacia fábricas inteligentes, donde la conectividad y la automatización son pilares fundamentales.
Así, los sistemas hidráulicos de bordonado constituyen un elemento esencial para lograr procesos de conformado metálico eficientes, seguros y adaptables a las exigencias crecientes de la industria actual.
Prensas industriales para embutición
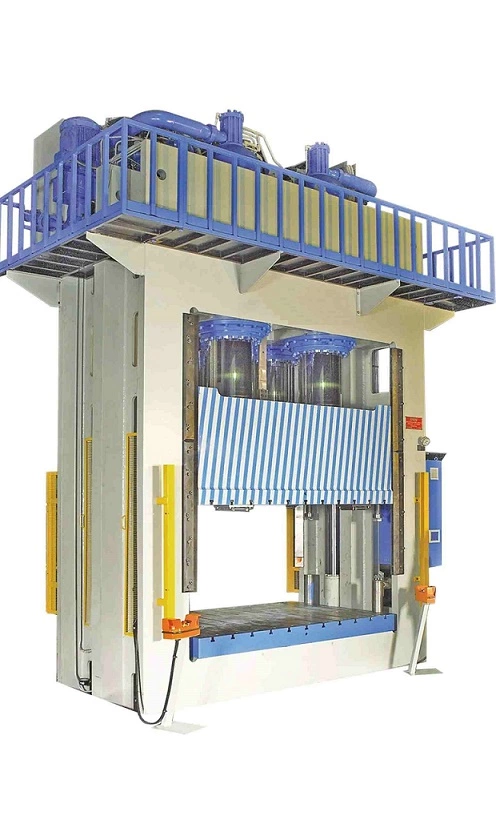
Las prensas industriales para embutición son máquinas especialmente diseñadas para dar forma a piezas metálicas mediante la deformación plástica controlada, utilizando la fuerza ejercida por un punzón que empuja una lámina o disco metálico dentro de una matriz, conformando así piezas huecas o con formas específicas. Estas prensas son esenciales en la fabricación de componentes para industrias como la automotriz, electrodomésticos, envases, aeroespacial, y muchas otras donde se requieren piezas metálicas con alta precisión y calidad superficial.
Existen diversos tipos de prensas para embutición, clasificadas principalmente según su sistema de accionamiento y la capacidad de fuerza que pueden ejercer:
- Prensas mecánicas: Utilizan un sistema de biela-manivela para transformar el movimiento rotativo de un motor en un movimiento lineal del punzón. Son conocidas por su alta velocidad de operación, lo que las hace adecuadas para producción en masa. Sin embargo, la fuerza aplicada varía a lo largo del ciclo, alcanzando su máximo en un punto específico, por lo que es necesario sincronizar bien el proceso para evitar daños en el material.
- Prensas hidráulicas: Operan mediante sistemas hidráulicos que aplican una fuerza constante y ajustable durante todo el recorrido del punzón. Esto permite un mejor control de la presión aplicada, ideal para embuticiones profundas o materiales difíciles de conformar. Aunque tienen velocidades de ciclo más bajas que las mecánicas, ofrecen mayor flexibilidad y precisión.
- Prensas servoeléctricas: Incorporan servomotores eléctricos para controlar con precisión el movimiento, velocidad y posición del punzón. Combina las ventajas de la velocidad mecánica con la precisión hidráulica, además de ofrecer eficiencia energética y menor mantenimiento. Son especialmente útiles para embuticiones complejas y para procesos que requieren cambios frecuentes de configuración.
Las prensas para embutición pueden variar en tamaño y capacidad de fuerza, desde pequeñas prensas para prototipos o piezas delicadas, hasta grandes máquinas capaces de ejercer miles de toneladas de presión para piezas voluminosas o materiales resistentes. La elección depende del tipo de material, el espesor de la lámina, la geometría de la pieza y la producción requerida.
El diseño del utillaje (matrices y punzones) es fundamental para el éxito del proceso. Estos deben estar fabricados con materiales resistentes al desgaste y diseñados para facilitar el flujo del metal, evitar defectos como arrugas o fisuras, y permitir un desmoldeo sencillo. La correcta lubricación y alineación son también aspectos críticos durante la operación.
En la industria moderna, muchas prensas de embutición están integradas en líneas automatizadas que incluyen sistemas de alimentación de material, posicionamiento, inspección y descarga, lo que permite una producción continua y con alta calidad constante. La digitalización y los sistemas de control avanzado permiten programar y monitorear cada ciclo, adaptando parámetros para optimizar resultados y minimizar el desperdicio.
En resumen, las prensas industriales para embutición son herramientas versátiles y potentes, indispensables para la fabricación eficiente de piezas metálicas conformadas, combinando fuerza, precisión y adaptabilidad para satisfacer las demandas de múltiples sectores industriales. ¿Quieres que te explique algún tipo de prensa en particular o detalles sobre el diseño de matrices y punzones?
Además, las prensas industriales para embutición pueden operar en diferentes modos según el tipo de pieza y el proceso requerido. Por ejemplo, en embuticiones profundas, es común que la prensa realice varias etapas o embuticiones sucesivas, donde la pieza pasa por diferentes matrices y punzones que conforman gradualmente la forma deseada. Esto ayuda a evitar defectos como arrugas o grietas y mejora la uniformidad del espesor del material.
El control de la velocidad y la presión durante el ciclo de embutición es crucial para obtener un buen acabado y evitar el desgaste prematuro de las herramientas. Las prensas hidráulicas permiten ajustar estas variables en tiempo real, mientras que las servoeléctricas ofrecen perfiles de velocidad programables que optimizan cada fase del proceso. En las prensas mecánicas, el diseño del volante y la transmisión determina la curva de fuerza y velocidad, por lo que la sincronización con el material y la geometría es clave.
El mantenimiento y la calibración periódica de las prensas son esenciales para mantener la precisión y seguridad en la operación. Esto incluye la revisión de componentes como guías, cojinetes, cilindros hidráulicos, bombas y sistemas electrónicos. Además, las prensas modernas incorporan sistemas de monitoreo que detectan vibraciones anormales, pérdidas de presión o desalineaciones, permitiendo intervenciones preventivas antes de que ocurran fallos mayores.
En cuanto a la seguridad, las prensas cuentan con sistemas de protección que incluyen resguardos físicos, sensores de presencia, paradas de emergencia y controles bimanuales para evitar accidentes. La integración con protocolos de seguridad industrial garantiza un entorno de trabajo seguro para los operarios.
La capacidad de integración con tecnologías de Industria 4.0 permite que las prensas para embutición formen parte de líneas de producción inteligentes, donde el análisis de datos, la simulación y el control en tiempo real mejoran la eficiencia, calidad y trazabilidad. Esto es especialmente valioso en producciones de alta demanda o cuando se fabrican piezas con tolerancias estrictas y requerimientos específicos.
Finalmente, la selección adecuada de la prensa, junto con un diseño óptimo del utillaje y un control riguroso del proceso, son factores determinantes para el éxito en la fabricación mediante embutición. La combinación de fuerza, precisión, flexibilidad y automatización hace que estas máquinas sean una pieza clave en la transformación de materias primas en componentes metálicos funcionales y de alta calidad.
Asimismo, las prensas industriales para embutición han evolucionado para adaptarse a una amplia variedad de materiales, no solo metales tradicionales como acero al carbono o aluminio, sino también aleaciones avanzadas y materiales compuestos que presentan desafíos específicos en cuanto a ductilidad y resistencia. Esto ha impulsado el desarrollo de prensas con sistemas de control más sofisticados que pueden adaptar la fuerza y velocidad de embutición en función del comportamiento del material durante el proceso, evitando fallos y optimizando el rendimiento.
En la fabricación de componentes para la industria automotriz, por ejemplo, donde la reducción de peso es fundamental, las prensas permiten conformar piezas complejas con espesores variables y formas tridimensionales, contribuyendo a la eficiencia energética y seguridad de los vehículos. De igual manera, en la industria aeroespacial, donde las tolerancias son extremadamente estrictas, estas máquinas se combinan con sistemas de medición en línea para asegurar que cada pieza cumpla con los requisitos dimensionales y estructurales.
El uso de tecnologías complementarias, como el embutido asistido por calor, en prensas equipadas con sistemas de calentamiento integrados, amplía la capacidad para conformar materiales de alta resistencia que serían difíciles de moldear en frío sin dañarse. Esto es especialmente útil para aleaciones de titanio, acero inoxidable o aluminio tratado térmicamente.
Además, la modularidad de las prensas modernas facilita la incorporación de accesorios y sistemas periféricos, como alimentadores automáticos, sistemas de cambio rápido de utillaje, robots para manejo de piezas y estaciones de inspección automatizadas. Esto reduce tiempos de ciclo, aumenta la repetibilidad y mejora la ergonomía para los operadores.
La tendencia hacia la digitalización y la manufactura inteligente permite también que las prensas estén conectadas a plataformas de análisis de datos en la nube, facilitando la optimización continua del proceso, la gestión remota y la trazabilidad completa de cada lote de producción. Esto resulta clave para cumplir con normativas de calidad, estándares internacionales y demandas crecientes de transparencia en la cadena de suministro.
En definitiva, las prensas industriales para embutición son una tecnología esencial que continúa evolucionando para responder a los desafíos de la fabricación avanzada, combinando fuerza, precisión, flexibilidad y automatización para transformar láminas metálicas en piezas con valor agregado para múltiples sectores productivos.
Máquinas para conformado hidráulicas
Las máquinas para conformado hidráulicas son equipos industriales que utilizan la presión generada por un fluido hidráulico para moldear, doblar, embutir o deformar piezas metálicas y otros materiales de manera controlada y precisa. Estas máquinas aprovechan la capacidad del sistema hidráulico para aplicar fuerzas elevadas de forma constante y regulable, lo que las hace ideales para procesos de conformado donde se requieren deformaciones complejas, controladas y con alta repetibilidad.
El principio fundamental de las máquinas hidráulicas de conformado se basa en el uso de cilindros y bombas hidráulicas que generan presión sobre un fluido, generalmente aceite, que transmite la fuerza a los actuadores o herramientas de conformado. Esta fuerza puede aplicarse de manera gradual y mantenida, permitiendo realizar operaciones como embutición profunda, doblado, perfilado, estirado, plegado y forjado en frío, entre otros.
Entre las principales ventajas de las máquinas para conformado hidráulicas destacan la capacidad para aplicar fuerzas elevadas y constantes durante todo el recorrido de trabajo, la flexibilidad para ajustar presión, velocidad y recorrido según el material y la geometría de la pieza, y la posibilidad de integrar sistemas de control avanzados para automatizar y optimizar el proceso. Esto contrasta con las máquinas mecánicas, cuya fuerza máxima solo se aplica en ciertos puntos del ciclo.
Estas máquinas se utilizan ampliamente en sectores como el automotriz, aeroespacial, fabricación de electrodomésticos, construcción y fabricación de recipientes a presión, donde la precisión, calidad superficial y propiedades mecánicas de las piezas conformadas son fundamentales. Su diseño puede variar desde prensas hidráulicas verticales y horizontales, hasta sistemas especializados como prensas de embutición, dobladoras hidráulicas, prensas de forjado o máquinas de hidroconformado.
El sistema hidráulico suele estar compuesto por una unidad de potencia que incluye bomba, motor, válvulas de control, acumuladores y circuitos de filtrado y enfriamiento, los cuales trabajan coordinadamente para asegurar una respuesta rápida y estable durante el proceso. Los actuadores, como cilindros hidráulicos o servocilindros, convierten la presión del fluido en movimientos lineales o rotativos necesarios para el conformado.
La integración con tecnologías digitales y de automatización permite que las máquinas hidráulicas de conformado ofrezcan perfiles de presión y velocidad programables, supervisión en tiempo real de variables críticas y adaptación dinámica a variaciones del material o condiciones de proceso. Esto mejora la calidad del producto final, reduce el desgaste de herramientas y minimiza tiempos de ciclo.
En conclusión, las máquinas para conformado hidráulicas son herramientas versátiles, potentes y precisas, capaces de abordar una amplia gama de procesos de deformación metálica con altos estándares de calidad y eficiencia, constituyéndose en piezas clave dentro de la manufactura avanzada moderna. ¿Quieres que te detalle tipos específicos de máquinas hidráulicas para conformado o ejemplos de aplicaciones?
Además de las prensas hidráulicas tradicionales, dentro del ámbito del conformado hidráulico existen tecnologías especializadas que aprovechan la presión del fluido para lograr deformaciones difíciles o complejas, como el hidroconformado y el embutido por presión de fluido. En el hidroconformado, por ejemplo, una lámina metálica o tubo se coloca dentro de un molde cerrado y se somete a una presión hidráulica interna muy alta, que empuja el material contra las paredes del molde, permitiendo obtener formas tridimensionales con alta precisión y uniformidad en el espesor. Esta técnica es especialmente valiosa para fabricar piezas con geometrías complejas, como componentes automotrices o aeroespaciales, donde la reducción de peso y la resistencia estructural son críticos.
Las dobladoras hidráulicas, por su parte, utilizan cilindros hidráulicos para aplicar la fuerza necesaria para doblar perfiles metálicos, placas o tubos con control exacto del ángulo y radio de curvatura. Estas máquinas pueden manejar grandes espesores y se emplean en la fabricación de estructuras metálicas, maquinaria pesada, y fabricación naval, donde la precisión y la repetibilidad son fundamentales para el ensamblaje posterior.
Otra categoría importante son las máquinas de forjado hidráulico, que usan la presión hidráulica para deformar metales en frío o caliente, moldeando piezas con alta densidad y propiedades mecánicas mejoradas. Estas prensas ofrecen una fuerza constante y controlada, lo que permite obtener piezas con acabados superficiales de alta calidad y tolerancias estrictas, comunes en la producción de componentes aeronáuticos o piezas industriales críticas.
El diseño modular de las máquinas hidráulicas de conformado facilita la incorporación de sistemas auxiliares como alimentadores automáticos, sistemas de cambio rápido de herramientas, y estaciones de inspección integradas. Esto mejora la eficiencia de producción y permite una rápida adaptación a diferentes lotes o diseños, reduciendo tiempos muertos y aumentando la flexibilidad.
El control digital y la automatización juegan un rol cada vez más importante, permitiendo programar perfiles de presión y velocidad personalizados para cada tipo de pieza, además de monitorizar variables como temperatura, presión y posición para asegurar la calidad y detectar anomalías en tiempo real. Esto se complementa con tecnologías de simulación que anticipan el comportamiento del material y optimizan el proceso antes de la producción física.
Finalmente, la sostenibilidad también es una consideración creciente, y las máquinas hidráulicas modernas incorporan sistemas de ahorro energético como bombas de caudal variable, recuperación de energía y uso de fluidos hidráulicos biodegradables, contribuyendo a reducir el impacto ambiental sin sacrificar desempeño.
En conjunto, las máquinas para conformado hidráulicas son soluciones integrales que combinan potencia, precisión y flexibilidad, adaptándose a las demandas actuales de la industria para fabricar piezas metálicas con alta calidad, eficiencia y bajo costo operativo.
Asimismo, la evolución tecnológica ha permitido el desarrollo de sistemas electrohidráulicos híbridos que combinan la fuerza y capacidad de carga de la hidráulica con la precisión y eficiencia energética de la tecnología eléctrica. Estos sistemas utilizan servomotores eléctricos para controlar bombas hidráulicas o actuadores, lo que permite una respuesta más rápida, mejor control de la presión y menor consumo energético en comparación con los sistemas hidráulicos convencionales. Esto resulta especialmente útil en aplicaciones donde se requieren movimientos precisos y repetibles, así como ciclos de trabajo variables.
En el ámbito del mantenimiento, las máquinas para conformado hidráulicas modernas cuentan con sistemas de monitoreo en línea que permiten detectar fallas o desgastes en componentes críticos, como válvulas, bombas o cilindros. Estos sistemas recopilan datos en tiempo real y aplican análisis predictivos para anticipar problemas antes de que causen paradas no programadas, optimizando la disponibilidad del equipo y reduciendo costos operativos.
La integración con tecnologías de Industria 4.0 posibilita también la conexión remota y el control de las máquinas, facilitando la gestión centralizada de múltiples equipos en diferentes ubicaciones. Esto permite realizar diagnósticos, ajustes y actualizaciones de software sin necesidad de presencia física, mejorando la eficiencia y la capacidad de respuesta ante cambios en la producción.
Las máquinas hidráulicas para conformado también se adaptan a materiales emergentes y procesos combinados, como la conformación de metales recubiertos, aleaciones ligeras avanzadas o composites metálicos. La capacidad para ajustar con precisión la fuerza y velocidad de conformado minimiza el riesgo de daños en estos materiales sensibles y permite explorar nuevas aplicaciones en sectores como la movilidad eléctrica, energías renovables y fabricación de dispositivos médicos.
Finalmente, la versatilidad de estas máquinas las convierte en herramientas clave para la innovación en diseño y producción, permitiendo fabricar piezas complejas y de alto rendimiento que antes eran difíciles o imposibles de producir con métodos convencionales. Gracias a la combinación de potencia hidráulica, control digital avanzado y flexibilidad operativa, las máquinas para conformado hidráulicas continúan siendo pilares fundamentales en la transformación digital y tecnológica de la industria manufacturera.
Equipos hidráulicos para procesos de conformado
Los equipos hidráulicos para procesos de conformado son sistemas diseñados para aplicar fuerzas controladas y precisas sobre materiales, principalmente metales, con el fin de deformarlos plásticamente y darles formas específicas según los requerimientos de fabricación. Estos equipos aprovechan la capacidad de la hidráulica para generar grandes fuerzas de manera constante y ajustable, lo que permite realizar operaciones complejas como embutición profunda, doblado, estirado, perfilado, forjado y hidroconformado, entre otras.
Un equipo hidráulico típico para conformado incluye una unidad de potencia compuesta por una bomba hidráulica, un motor, acumuladores, válvulas de control y sistemas de filtración y enfriamiento del fluido hidráulico. Esta unidad suministra aceite a presión que se transmite a través de conductos hacia actuadores como cilindros hidráulicos o servocilindros, los cuales convierten la presión en movimiento lineal o rotativo para accionar las herramientas de conformado.
La precisión en el control de presión, velocidad y recorrido del actuador es fundamental para garantizar la calidad del conformado. Por ello, estos equipos incorporan válvulas proporcionales y servoválvulas que permiten regular dinámicamente la fuerza y la velocidad en función del programa de conformado. Los sensores de presión, posición y temperatura monitorean continuamente el proceso y proporcionan datos a un sistema de control (PLC o CNC), que ajusta parámetros en tiempo real para mantener condiciones óptimas.
Los equipos hidráulicos para conformado son muy versátiles y se adaptan a diferentes tipos de máquinas, desde prensas hidráulicas y dobladoras hasta sistemas especializados como máquinas de hidroconformado o prensas de forjado. Su capacidad para aplicar fuerzas elevadas y controlar el proceso con exactitud los hace indispensables en la manufactura de piezas metálicas para sectores como automotriz, aeroespacial, construcción, electrodomésticos y energía.
Además, la integración de tecnologías digitales y automatización permite que estos equipos formen parte de líneas de producción inteligentes, donde la programación avanzada, la supervisión remota y el análisis de datos facilitan la optimización continua del proceso, la reducción de tiempos muertos y la mejora de la calidad del producto final.
En términos de mantenimiento, los equipos hidráulicos requieren cuidados específicos para asegurar la pureza del fluido, el correcto funcionamiento de las válvulas y la integridad de los cilindros, lo que garantiza una operación confiable y prolonga la vida útil del sistema.
En resumen, los equipos hidráulicos para procesos de conformado son sistemas potentes, precisos y adaptables que juegan un rol crucial en la transformación de materiales metálicos en componentes funcionales y de alta calidad, siendo un pilar fundamental en la industria manufacturera moderna. ¿Quieres que te detalle componentes específicos o aplicaciones particulares?
Estos equipos hidráulicos para conformado funcionan mediante la transmisión de presión hidráulica desde una bomba hacia actuadores que transforman esa energía en movimientos precisos para moldear el material. La bomba, que puede ser de desplazamiento fijo o variable, se encarga de generar el caudal necesario de aceite a alta presión, mientras que las válvulas reguladoras controlan el flujo y la presión para adaptar la fuerza y velocidad a cada etapa del proceso. Esta regulación es clave para evitar defectos como grietas, arrugas o deformaciones no deseadas, especialmente cuando se trabaja con materiales sensibles o geometrías complejas.
Los cilindros hidráulicos o servocilindros actúan como los elementos que aplican directamente la fuerza sobre la pieza a conformar. Están diseñados para soportar altas presiones y ofrecer un movimiento suave y controlado, que puede ser lineal o rotativo, según la aplicación. Su respuesta rápida y precisión son vitales para procesos que requieren ciclos cortos y repetibles, garantizando así la uniformidad y calidad del producto final.
Además, estos sistemas hidráulicos suelen incorporar acumuladores que actúan como amortiguadores de presión, estabilizando el flujo de aceite y permitiendo una operación más fluida y eficiente. También cuentan con filtros de alta precisión para mantener el fluido limpio, lo que es fundamental para prevenir daños en componentes sensibles como válvulas y bombas, y para extender la vida útil del sistema. Los enfriadores ayudan a mantener la temperatura adecuada del aceite, evitando pérdidas de eficiencia y posibles daños por sobrecalentamiento.
La integración de sensores para monitorear presión, temperatura, posición y flujo permite un control en tiempo real de las variables del proceso. Estos datos se envían a sistemas de control electrónico que ajustan automáticamente los parámetros de operación para mantener condiciones óptimas, corregir desviaciones y asegurar la trazabilidad del proceso. Esta capacidad es especialmente importante en líneas de producción automatizadas y en industrias donde la calidad debe ser estrictamente controlada.
La flexibilidad de los equipos hidráulicos para conformado los hace aptos para una amplia variedad de aplicaciones, desde la fabricación de piezas pequeñas y delicadas hasta componentes grandes y robustos, cubriendo sectores como automotriz, aeroespacial, maquinaria pesada, y bienes de consumo duradero. Su capacidad para adaptar la fuerza y el movimiento a las necesidades específicas del material y diseño permite trabajar con diferentes metales, espesores y formas.
Finalmente, los avances tecnológicos han impulsado el desarrollo de sistemas electrohidráulicos que combinan la fuerza hidráulica con la precisión y eficiencia de actuadores eléctricos, mejorando el rendimiento, reduciendo el consumo energético y facilitando la integración en entornos de manufactura inteligentes y digitalizados.
En conjunto, los equipos hidráulicos para procesos de conformado representan una solución integral y avanzada que potencia la capacidad productiva y la calidad en la transformación de materiales metálicos, adaptándose a los retos actuales y futuros de la industria.
Además, la evolución de estos equipos hidráulicos para conformado ha permitido la incorporación de tecnologías como el control por servoválvulas, que ofrecen una precisión aún mayor en la regulación de presión y flujo. Esto posibilita perfiles de fuerza y velocidad altamente personalizados durante cada fase del proceso, permitiendo, por ejemplo, iniciar la deformación con una fuerza suave para evitar arrugas y aumentar gradualmente para completar el conformado sin daños.
Los sistemas de retroalimentación avanzada, basados en sensores de posición lineal, presión y acelerómetros, permiten realizar ajustes en tiempo real que compensan variaciones en el material o condiciones ambientales, manteniendo la calidad del producto incluso en producciones largas o variables. Esto es clave para industrias con altos estándares de calidad y normativas estrictas.
Por otro lado, la modularidad de los equipos hidráulicos facilita la integración con otros sistemas automáticos como robots de carga y descarga, estaciones de inspección óptica, o sistemas de lubricación automática, formando líneas de producción totalmente integradas y con mínima intervención manual. Esto no solo incrementa la productividad, sino que mejora la seguridad del personal y reduce errores humanos.
En términos energéticos, se han desarrollado sistemas con bombas de velocidad variable y recuperación de energía hidráulica, que reducen significativamente el consumo eléctrico y las pérdidas térmicas, haciendo que los procesos sean más sostenibles y económicos a largo plazo. También se emplean fluidos hidráulicos ecológicos que disminuyen el impacto ambiental sin comprometer la eficiencia.
El mantenimiento predictivo, apoyado en análisis de datos y algoritmos de inteligencia artificial, permite anticipar fallas en componentes hidráulicos críticos antes de que afecten la producción. Esta capacidad reduce tiempos muertos y costos de reparación, mejorando la disponibilidad y vida útil de los equipos.
Finalmente, la conectividad y digitalización de los equipos hidráulicos para conformado los convierten en nodos inteligentes dentro de fábricas conectadas, facilitando la gestión remota, la optimización continua del proceso y la trazabilidad completa del ciclo productivo, alineándose con los conceptos de Industria 4.0 y manufactura inteligente.
En suma, los equipos hidráulicos para procesos de conformado son tecnologías en constante evolución que combinan potencia, precisión y flexibilidad con innovación tecnológica, contribuyendo decisivamente a la competitividad y calidad en la fabricación industrial moderna.
Prensas de alta presión hidráulicas para embutición
Las prensas de alta presión hidráulicas para embutición son máquinas diseñadas para aplicar fuerzas hidráulicas extremadamente elevadas con el objetivo de conformar piezas metálicas mediante procesos de embutición profunda y otros métodos de deformación plástica. Estas prensas son fundamentales en la fabricación industrial cuando se requieren piezas con geometrías complejas, espesores variables y altos estándares de calidad estructural y superficial.
El principio de funcionamiento de estas prensas se basa en un sistema hidráulico que genera una presión constante y ajustable que se transmite a cilindros hidráulicos capaces de ejercer fuerzas que pueden superar fácilmente las miles de toneladas. Esta capacidad permite conformar metales gruesos o de alta resistencia, así como realizar embuticiones profundas sin riesgo de fisuras o deformaciones indeseadas.
Una de las características clave de las prensas hidráulicas de alta presión es su capacidad para mantener una fuerza constante durante todo el recorrido del punzón o herramienta, a diferencia de las prensas mecánicas donde la fuerza máxima se aplica solo en ciertos puntos del ciclo. Esto garantiza un control óptimo sobre el proceso de embutición, reduciendo defectos y mejorando la uniformidad del producto final.
Estas prensas suelen incorporar sistemas de control avanzados, como PLCs o CNCs, que permiten programar perfiles de presión, velocidad y posición para adaptarse a diferentes materiales y geometrías. La posibilidad de realizar embuticiones en múltiples etapas o con ciclos variables aumenta la versatilidad y precisión en la fabricación de piezas complejas.
El diseño robusto y la ingeniería de estas prensas aseguran estabilidad, minimizan vibraciones y facilitan la integración con utillajes específicos, como matrices y punzones fabricados con materiales de alta resistencia y tratamientos térmicos especiales para soportar las cargas de trabajo. Además, cuentan con sistemas hidráulicos con bombas de caudal variable, acumuladores, válvulas proporcionales y sensores que garantizan la precisión y seguridad del proceso.
Las aplicaciones típicas incluyen la fabricación de carrocerías y componentes automotrices, recipientes a presión, tanques industriales, envases metálicos, electrodomésticos, y piezas para la industria aeroespacial, entre otros. En todos estos sectores, la capacidad de realizar embuticiones profundas con alta repetibilidad y calidad es fundamental para cumplir con normativas estrictas y requerimientos funcionales.
La seguridad es otro aspecto crítico en estas prensas, por lo que están equipadas con sistemas de protección como resguardos, paradas de emergencia, controles bimanuales y monitoreo constante de presión y temperatura para evitar sobrecargas o fallas que puedan poner en riesgo a los operarios o al equipo.
En resumen, las prensas de alta presión hidráulicas para embutición son herramientas potentes, precisas y versátiles que permiten la fabricación eficiente de piezas metálicas complejas y de alta calidad, siendo una pieza clave en la industria manufacturera moderna. ¿Quieres que te detalle algún aspecto técnico o ejemplos específicos de estas prensas?
Estas prensas de alta presión hidráulicas para embutición ofrecen una gran flexibilidad en el control del proceso, permitiendo ajustar en tiempo real parámetros como la presión aplicada, la velocidad de avance del punzón y el tiempo de mantenimiento de la fuerza, lo que es fundamental para adaptar el proceso a distintos tipos de materiales, espesores y diseños. Esta adaptabilidad ayuda a minimizar defectos comunes como arrugas, grietas o variaciones de espesor, mejorando la calidad y reduciendo el desperdicio.
El sistema hidráulico de estas prensas está diseñado para proporcionar una presión estable y constante, incluso en ciclos prolongados o con cargas variables. Esto se logra mediante bombas de desplazamiento variable, acumuladores que regulan el flujo y válvulas proporcionales que modulan con precisión la presión y velocidad. Además, los sensores instalados en el sistema permiten un monitoreo continuo que garantiza la seguridad y la precisión durante todo el proceso.
El utillaje empleado en estas prensas, compuesto por matrices y punzones de alta resistencia, es clave para el éxito del embutido. Estos componentes se fabrican con materiales tratados térmicamente y diseñados para soportar las fuerzas extremas, al tiempo que garantizan un contacto uniforme con la pieza para evitar daños y asegurar un acabado óptimo. Muchas veces, el diseño del utillaje se complementa con sistemas de lubricación automatizados que facilitan el desmoldeo y prolongan la vida útil de las herramientas.
La capacidad de estas prensas para realizar embuticiones profundas permite fabricar piezas con formas complejas y detalles finos, lo que es esencial en sectores como el automotriz, donde se requieren paneles de carrocería con alta precisión, o en la fabricación de recipientes a presión que deben cumplir normas estrictas de seguridad y resistencia. También son utilizadas en la producción de componentes para electrodomésticos, mobiliario metálico y envases industriales, donde la repetibilidad y calidad superficial son cruciales.
Además, la integración de sistemas de automatización y robótica facilita la alimentación y descarga de piezas, así como el cambio rápido de herramientas, aumentando la productividad y reduciendo la intervención manual. La conectividad con sistemas de supervisión y control permite registrar datos de producción, analizar el desempeño y planificar mantenimientos predictivos, optimizando la operación y reduciendo tiempos de inactividad.
En materia de seguridad, estas prensas incorporan múltiples dispositivos como barreras fotoeléctricas, paradas de emergencia, controles bimanuales y monitoreo de sobrepresión para proteger a los operadores y prevenir accidentes. La robustez estructural y la precisión en el diseño aseguran un funcionamiento estable y confiable durante largas jornadas de trabajo.
En definitiva, las prensas de alta presión hidráulicas para embutición representan una solución tecnológica avanzada que combina potencia, precisión y flexibilidad para satisfacer las exigentes demandas de la manufactura moderna, facilitando la producción eficiente de piezas metálicas complejas y de alta calidad.
Además, la evolución de estas prensas ha ido acompañada de mejoras en la eficiencia energética, con la incorporación de sistemas hidráulicos con bombas de caudal variable y recuperación de energía, que optimizan el consumo eléctrico y reducen las pérdidas térmicas. Esto no solo disminuye el costo operativo, sino que contribuye a la sostenibilidad ambiental de los procesos industriales.
El avance en el control digital ha permitido la implementación de interfaces hombre-máquina (HMI) intuitivas que facilitan la programación y supervisión del proceso de embutición. Los operadores pueden configurar perfiles de presión y velocidad personalizados, monitorear en tiempo real las variables críticas y acceder a diagnósticos detallados para anticipar mantenimientos o ajustes necesarios.
Asimismo, la combinación con tecnologías de simulación permite predecir el comportamiento del material durante la embutición, ayudando a optimizar el diseño del utillaje y los parámetros del proceso antes de iniciar la producción física. Esto reduce considerablemente el tiempo y costo de desarrollo, aumentando la tasa de éxito en la fabricación de nuevas piezas.
Las prensas de alta presión hidráulicas para embutición también están diseñadas para ser altamente modulares, permitiendo la integración con sistemas automáticos de carga y descarga, robots manipuladores, y estaciones de inspección y control de calidad. Esta integración completa contribuye a la creación de líneas de producción altamente automatizadas, donde la trazabilidad, la calidad y la productividad están garantizadas.
Finalmente, la seguridad sigue siendo un pilar fundamental en el diseño y operación de estas prensas, con normativas estrictas y dispositivos redundantes que protegen tanto al operador como a la maquinaria, asegurando un ambiente de trabajo seguro y eficiente.
En resumen, las prensas de alta presión hidráulicas para embutición constituyen una tecnología clave que combina fuerza, control preciso, eficiencia y seguridad para atender las demandas crecientes de la industria manufacturera moderna, facilitando la producción de piezas metálicas complejas con altos estándares de calidad.
Prensas hidráulicas para embutir láminas metálicas
Las prensas hidráulicas para embutir láminas metálicas son máquinas diseñadas específicamente para conformar piezas metálicas mediante la aplicación de fuerza hidráulica controlada, que permite deformar láminas en frío o a temperaturas moderadas para obtener formas huecas o con geometrías complejas. Este tipo de prensa es fundamental en procesos industriales donde se requiere alta precisión, repetibilidad y calidad superficial en piezas como carcasas, envases, componentes automotrices, electrodomésticos y productos industriales.
El sistema hidráulico de estas prensas utiliza una bomba que genera presión sobre un fluido (generalmente aceite), el cual se transmite a cilindros hidráulicos que mueven el punzón o herramienta de embutición contra la lámina metálica posicionada sobre una matriz. La fuerza aplicada puede ajustarse con gran precisión mediante válvulas proporcionales o servoválvulas, permitiendo adaptar la presión y velocidad al tipo de material, espesor y complejidad de la pieza.
Una característica esencial de estas prensas es la capacidad para mantener una presión constante durante todo el recorrido del punzón, lo que ayuda a evitar defectos comunes en embutición como arrugas, fisuras o espesores no uniformes. La flexibilidad en la programación del proceso permite realizar embuticiones profundas, múltiples etapas o ciclos personalizados para cada lote o diseño, aumentando la versatilidad y eficiencia.
El utillaje empleado, compuesto por matrices y punzones de alta resistencia y precisión, es clave para lograr un buen resultado. Estos elementos deben estar diseñados para facilitar el flujo del material y minimizar el desgaste, además de contar con sistemas de lubricación adecuados para mejorar el desmoldeo y prolongar la vida útil.
Las prensas hidráulicas para embutir láminas metálicas suelen contar con sistemas de control modernos basados en PLC o CNC, que permiten supervisar en tiempo real parámetros críticos como presión, posición y velocidad, y ajustar automáticamente las condiciones del proceso para mantener la calidad. Asimismo, incorporan sensores y dispositivos de seguridad para proteger al operador y prevenir daños en la máquina o la pieza.
Estas prensas pueden variar en tamaño y capacidad, desde modelos compactos para producción de piezas pequeñas hasta grandes prensas capaces de ejercer miles de toneladas para embuticiones profundas en piezas voluminosas o de materiales resistentes. La selección depende de los requerimientos específicos de producción, material y geometría.
En resumen, las prensas hidráulicas para embutir láminas metálicas son herramientas indispensables para la manufactura moderna, ofreciendo potencia, control y precisión para transformar láminas en piezas funcionales con altos estándares de calidad y eficiencia. ¿Quieres que te explique algún aspecto técnico en particular o ejemplos de aplicación?
Estas prensas hidráulicas para embutir láminas metálicas se destacan por su capacidad para manejar una amplia variedad de materiales, desde aceros blandos hasta aleaciones de alta resistencia como acero inoxidable, aluminio o incluso materiales especiales tratados térmicamente. Gracias al control preciso de la presión y velocidad, es posible adaptar el proceso para evitar daños en materiales delicados o lograr embuticiones profundas en metales más rígidos.
El diseño estructural de estas prensas está pensado para maximizar la rigidez y minimizar las deformaciones durante la operación, garantizando que la fuerza aplicada se transmita de manera uniforme y controlada. Esto es fundamental para obtener piezas con tolerancias ajustadas y acabados superficiales de alta calidad. Además, cuentan con sistemas de guía y alineación que aseguran el correcto posicionamiento del punzón y la matriz, evitando desgastes prematuros y fallos en el proceso.
Los avances en automatización han permitido que estas prensas se integren fácilmente en líneas de producción con sistemas automáticos de alimentación y descarga, robots manipuladores y estaciones de inspección óptica o ultrasónica para asegurar la calidad en cada pieza. Esta integración no solo mejora la productividad, sino que reduce la intervención humana y los riesgos asociados.
El mantenimiento de las prensas hidráulicas para embutir láminas metálicas es fundamental para garantizar su desempeño a largo plazo. Esto incluye la revisión y sustitución periódica del fluido hidráulico, la inspección de sellos, válvulas y cilindros, así como la calibración de sensores y sistemas de control. El mantenimiento predictivo basado en el análisis de datos ayuda a anticipar posibles fallos y optimizar los tiempos de intervención.
Además, estas prensas están diseñadas con estrictos estándares de seguridad, incorporando barreras físicas, sensores de presencia, paradas de emergencia y controles bimanuales para proteger a los operadores durante la operación. La conformidad con normativas internacionales asegura un ambiente de trabajo seguro y confiable.
En definitiva, las prensas hidráulicas para embutir láminas metálicas combinan fuerza, precisión y flexibilidad para ofrecer soluciones eficientes y versátiles en la fabricación de piezas metálicas, siendo componentes esenciales en la industria manufacturera actual.
Además, la tecnología detrás de las prensas hidráulicas para embutir láminas metálicas continúa avanzando con la incorporación de sistemas de control inteligente que permiten ajustar automáticamente los parámetros de embutición según las características específicas de cada lote de material o diseño de pieza. Esto se logra mediante sensores que analizan en tiempo real la respuesta del material, detectando variaciones en espesor, dureza o temperatura, y ajustando la presión y velocidad para optimizar el proceso y minimizar defectos.
El uso de interfaces hombre-máquina (HMI) intuitivas facilita la programación y supervisión del proceso, permitiendo a los operadores configurar perfiles de embutición complejos con facilidad, monitorear variables críticas y recibir alertas tempranas ante posibles fallos o desviaciones. Estas interfaces también almacenan datos históricos que sirven para mejorar continuamente la calidad y eficiencia del proceso mediante análisis estadísticos y ajustes basados en resultados anteriores.
Otra tendencia importante es la integración de estas prensas en sistemas de manufactura inteligente o Industria 4.0, donde la conectividad y el intercambio de datos entre máquinas, sistemas de control y plataformas digitales permiten una gestión centralizada y optimización en tiempo real. Esto no solo mejora la productividad, sino que facilita la trazabilidad completa de cada pieza fabricada, algo vital para sectores con altos estándares de calidad y regulaciones estrictas como el automotriz o aeroespacial.
En cuanto a la sostenibilidad, las prensas hidráulicas modernas incorporan tecnologías que reducen el consumo energético, como bombas de velocidad variable, recuperación de energía y sistemas de lubricación eficientes. Además, el uso de fluidos hidráulicos biodegradables y de bajo impacto ambiental contribuye a minimizar la huella ecológica del proceso de embutición.
Finalmente, la capacitación y formación del personal para operar y mantener estas prensas es esencial para aprovechar al máximo su potencial y asegurar una producción segura y eficiente. La combinación de tecnología avanzada, mantenimiento adecuado y operadores capacitados garantiza que las prensas hidráulicas para embutir láminas metálicas continúen siendo una solución confiable y competitiva en la fabricación industrial moderna.
Máquinas hidráulicas para trabajo en metales
Las máquinas hidráulicas para trabajo en metales son equipos industriales que emplean la fuerza generada por sistemas hidráulicos para realizar diferentes procesos de conformado, corte, doblado, embutición, forjado y estampado de piezas metálicas. Estos sistemas aprovechan la capacidad del fluido hidráulico para transmitir fuerzas muy elevadas de manera controlada y precisa, lo que permite trabajar con materiales diversos y con espesores variados, logrando formas complejas y altos estándares de calidad.
Entre los tipos más comunes de máquinas hidráulicas para trabajo en metales se encuentran las prensas hidráulicas, dobladoras hidráulicas, cizallas hidráulicas, punzonadoras, máquinas de forjado y sistemas de hidroconformado. Cada una está diseñada para cumplir funciones específicas dentro del proceso productivo, adaptándose a las necesidades particulares de la industria y al tipo de material a procesar.
Las prensas hidráulicas son ampliamente utilizadas para operaciones de embutición, estampado, corte y forjado. Su principal ventaja es la capacidad para mantener una fuerza constante y ajustable durante todo el recorrido del actuador, facilitando procesos que requieren precisión y control en la deformación del material. Los sistemas hidráulicos permiten programar perfiles de presión y velocidad, adaptando el proceso a diferentes geometrías y materiales.
Las dobladoras hidráulicas se emplean para modificar la forma de perfiles, chapas y tubos mediante la aplicación controlada de presión. Su flexibilidad permite trabajar con distintos radios y ángulos de curvatura, así como con materiales de alta resistencia, manteniendo la calidad superficial y dimensional de las piezas. Estas máquinas suelen contar con sistemas automáticos para ajustar y memorizar configuraciones, facilitando la producción en serie.
Las cizallas hidráulicas se utilizan para el corte preciso de láminas metálicas de diferentes espesores. Gracias a la fuerza hidráulica, pueden cortar materiales duros y resistentes con bajos esfuerzos mecánicos, prolongando la vida útil de las cuchillas y optimizando el consumo energético. Además, incluyen sistemas de seguridad para proteger al operador y garantizar un funcionamiento confiable.
Las punzonadoras hidráulicas realizan orificios o perforaciones en piezas metálicas mediante el uso de herramientas intercambiables. Su capacidad para aplicar fuerzas elevadas y controlar el ciclo de trabajo las hace ideales para operaciones rápidas y repetitivas, integrándose en líneas de producción automatizadas para maximizar eficiencia.
Los sistemas de hidroconformado utilizan presión hidráulica para conformar metales en moldes complejos, aplicando una fuerza uniforme mediante un fluido que empuja la pieza contra el molde. Esta técnica permite fabricar piezas ligeras, con formas complejas y propiedades mecánicas mejoradas, siendo muy utilizada en la industria automotriz y aeroespacial.
En cuanto a su construcción, las máquinas hidráulicas para trabajo en metales están equipadas con unidades de potencia hidráulica que incluyen bombas, motores, válvulas de control, acumuladores y sistemas de filtración y enfriamiento. Los actuadores, generalmente cilindros hidráulicos o servocilindros, convierten la presión del fluido en movimientos lineales o rotativos precisos para ejecutar las operaciones de conformado o corte.
La incorporación de sistemas electrónicos de control basados en PLC o CNC permite programar y monitorear en tiempo real variables como presión, velocidad, posición y temperatura, mejorando la calidad, seguridad y eficiencia del proceso. Además, la integración con tecnologías de automatización y robótica facilita la alimentación, manipulación y clasificación de piezas, optimizando la productividad y reduciendo la intervención manual.
El mantenimiento adecuado de estos equipos es crucial para garantizar su desempeño y longevidad. Esto implica la revisión periódica del fluido hidráulico, limpieza y cambio de filtros, inspección de sellos y válvulas, así como calibración de sensores y controles. El mantenimiento predictivo, apoyado en análisis de datos, ayuda a anticipar fallas y minimizar tiempos de parada.
En conclusión, las máquinas hidráulicas para trabajo en metales constituyen una categoría esencial en la manufactura moderna, proporcionando la fuerza y precisión necesarias para transformar materiales metálicos en componentes complejos y de alta calidad, con aplicaciones en sectores tan variados como la automoción, aeroespacial, construcción, electrodomésticos y maquinaria industrial. ¿Quieres que profundice en algún tipo específico de máquina hidráulica o en aplicaciones concretas?
Estas máquinas hidráulicas para trabajo en metales se caracterizan por su versatilidad y capacidad para adaptarse a una amplia gama de procesos productivos, desde operaciones simples como corte y doblado, hasta conformados complejos y forjados que requieren altas fuerzas y precisión. La fuerza generada por los sistemas hidráulicos es regulable y puede mantenerse constante durante todo el ciclo de trabajo, lo que permite un control preciso de la deformación del material y reduce el riesgo de defectos o daños.
El diseño robusto y modular de estas máquinas facilita su integración en líneas de producción automatizadas, donde pueden trabajar coordinadamente con robots, sistemas de alimentación automática y estaciones de inspección para lograr altos niveles de productividad y calidad. Además, la implementación de tecnologías digitales y de control avanzado posibilita la supervisión remota y el análisis en tiempo real de parámetros críticos, facilitando la toma de decisiones rápidas y el mantenimiento predictivo.
El uso de materiales de alta resistencia y componentes de precisión en la fabricación de estas máquinas asegura una larga vida útil y una operación fiable incluso bajo condiciones de trabajo intensivas y continuas. La capacidad para operar con diferentes tipos y espesores de metales amplía su aplicación a múltiples industrias, desde la fabricación de piezas pequeñas y delicadas hasta componentes estructurales pesados.
Las mejoras en eficiencia energética, mediante sistemas hidráulicos de caudal variable y recuperación de energía, contribuyen a reducir costos operativos y minimizar el impacto ambiental, alineándose con las tendencias actuales de sostenibilidad industrial. Asimismo, la incorporación de dispositivos de seguridad avanzados garantiza la protección del personal y la prevención de accidentes durante la operación.
En definitiva, las máquinas hidráulicas para trabajo en metales son herramientas esenciales que combinan potencia, precisión, flexibilidad y tecnología avanzada para satisfacer las exigencias de la manufactura moderna, facilitando la producción eficiente de piezas metálicas complejas con altos estándares de calidad y confiabilidad.
Además, el desarrollo de máquinas hidráulicas para trabajo en metales ha incorporado avances tecnológicos como los sistemas electrohidráulicos, que combinan la fuerza y capacidad de carga de la hidráulica con la precisión y eficiencia de actuadores eléctricos. Esta combinación permite un control más fino de la presión, velocidad y posición, reduciendo el consumo energético y mejorando la respuesta dinámica del sistema, lo que es particularmente útil en procesos que requieren movimientos precisos y repetitivos.
La incorporación de sensores inteligentes y sistemas de monitoreo continuo facilita la detección temprana de posibles fallas o desgastes en componentes críticos, lo que permite implementar estrategias de mantenimiento predictivo y evitar paradas no planificadas. Esto mejora la disponibilidad de las máquinas y optimiza los costos operativos.
En cuanto a la automatización, las máquinas hidráulicas para trabajo en metales pueden integrarse con tecnologías de visión artificial, robótica colaborativa y sistemas de control avanzados para crear líneas de producción inteligentes capaces de adaptarse dinámicamente a cambios en el proceso o en la demanda. Esta flexibilidad es clave para responder a las exigencias actuales de personalización y reducción de tiempos de entrega.
Asimismo, la seguridad es un aspecto prioritario en el diseño y operación de estas máquinas. Se implementan múltiples dispositivos de protección, como barreras físicas, sensores de proximidad, sistemas de parada rápida y controles bimanuales, garantizando un entorno de trabajo seguro y conforme a normativas internacionales.
Finalmente, el continuo avance en materiales y diseño estructural permite fabricar máquinas más compactas, eficientes y robustas, que ocupan menos espacio y ofrecen mayor rendimiento, facilitando su instalación y operación en plantas industriales modernas.
En resumen, las máquinas hidráulicas para trabajo en metales representan una combinación óptima de potencia, precisión, tecnología y seguridad, adaptándose a las demandas cambiantes de la industria manufacturera y contribuyendo a la producción eficiente y de alta calidad de componentes metálicos en una amplia variedad de sectores.
Equipos para estampado hidráulicos
Los equipos para estampado hidráulicos son máquinas industriales diseñadas para realizar procesos de conformado y moldeado de piezas metálicas mediante la aplicación de fuerza hidráulica controlada. El estampado hidráulico consiste en la deformación plástica del material usando matrices y punzones, donde la presión hidráulica genera la fuerza necesaria para moldear, cortar o embutir láminas metálicas u otros materiales con alta precisión y repetibilidad.
Estos equipos se componen principalmente de una unidad hidráulica que incluye bomba, motor, válvulas de control, acumuladores y sistemas de filtración y enfriamiento del fluido hidráulico, así como de una estructura mecánica robusta que sostiene el sistema de herramientas de estampado (matrices y punzones). Los cilindros hidráulicos convierten la presión del fluido en movimientos lineales que ejecutan el estampado con fuerza constante y ajustable.
Una de las ventajas principales de los equipos hidráulicos para estampado es la capacidad para mantener una presión constante durante todo el recorrido de la prensa, lo que permite procesos de deformación más uniformes y controlados en comparación con las prensas mecánicas tradicionales. Esto es especialmente útil en operaciones que requieren embuticiones profundas, cortes complejos o formas tridimensionales con detalles finos.
Los sistemas de control modernos integrados en estos equipos permiten programar perfiles de presión, velocidad y tiempo de mantenimiento de la fuerza, adaptándose a las características del material y del diseño de la pieza. Además, la incorporación de sensores para monitorear presión, posición y temperatura asegura la calidad y la seguridad del proceso, permitiendo ajustes en tiempo real.
Los equipos para estampado hidráulicos se emplean ampliamente en industrias como la automotriz, aeroespacial, fabricación de electrodomésticos, y producción de envases metálicos, donde la precisión, calidad superficial y resistencia estructural son esenciales. Pueden variar en tamaño y capacidad, desde prensas compactas para piezas pequeñas hasta grandes sistemas capaces de ejercer miles de toneladas de fuerza.
La integración con sistemas automáticos de alimentación y descarga, así como con robots y estaciones de inspección, permite crear líneas de producción altamente eficientes y automatizadas, reduciendo tiempos de ciclo y mejorando la seguridad del operario.
El mantenimiento de estos equipos es clave para garantizar su desempeño óptimo y durabilidad. Esto incluye la revisión periódica del fluido hidráulico, filtros, válvulas y componentes mecánicos, así como la calibración de sistemas de control y sensores.
En resumen, los equipos para estampado hidráulicos son herramientas fundamentales en la manufactura moderna, proporcionando potencia, precisión y flexibilidad para transformar láminas metálicas en componentes complejos y de alta calidad, adaptándose a las demandas crecientes de la industria. ¿Quieres que te detalle tipos específicos de equipos o aplicaciones concretas?
Estos equipos para estampado hidráulicos destacan por su capacidad para ofrecer una fuerza constante y ajustable durante todo el ciclo de estampado, lo que resulta en una mejor calidad del producto final al evitar defectos como arrugas, fisuras o deformaciones irregulares. La presión hidráulica puede controlarse de manera precisa, permitiendo adaptar el proceso a distintos tipos de materiales, espesores y complejidades geométricas, lo que amplía su versatilidad en la producción.
La estructura de las prensas hidráulicas está diseñada para soportar cargas elevadas y garantizar una alta rigidez, minimizando las vibraciones y deformaciones durante la operación. Esto contribuye a mantener la precisión dimensional y la repetibilidad en la fabricación de piezas en grandes volúmenes, aspectos fundamentales en sectores como el automotriz o aeroespacial.
El sistema hidráulico incorpora componentes como bombas de desplazamiento variable, acumuladores que regulan la presión y válvulas proporcionales que permiten un control dinámico y preciso del flujo y fuerza aplicada. Estos elementos trabajan en conjunto para asegurar un funcionamiento eficiente y seguro, además de reducir el consumo energético.
Los sensores y sistemas de monitoreo en tiempo real recopilan datos sobre presión, temperatura, posición y velocidad, que son procesados por controladores electrónicos para ajustar automáticamente los parámetros del proceso. Esta retroalimentación continua garantiza la calidad constante de las piezas y permite detectar anomalías o desgastes en el equipo antes de que afecten la producción.
La integración de estos equipos con sistemas de automatización, como robots para carga y descarga, estaciones de inspección visual y sistemas de lubricación automatizados, contribuye a aumentar la productividad, mejorar la seguridad laboral y reducir costos operativos. Además, la conexión con plataformas digitales facilita la gestión remota, análisis de datos y mantenimiento predictivo.
El utillaje utilizado en el estampado hidráulico, compuesto por matrices y punzones fabricados con materiales de alta resistencia y tratamientos térmicos especializados, es fundamental para obtener acabados superficiales óptimos y prolongar la vida útil de las herramientas. La correcta lubricación y mantenimiento del utillaje también son esenciales para evitar daños en las piezas y garantizar un proceso fluido.
La flexibilidad de los equipos para estampado hidráulicos permite la fabricación de una amplia gama de productos, desde componentes pequeños y delicados hasta grandes paneles estructurales, adaptándose a las exigencias de diferentes industrias y aplicaciones. Esta adaptabilidad los convierte en una opción preferida para procesos de producción en serie y fabricación personalizada.
Finalmente, la seguridad es un aspecto prioritario en el diseño y operación de estos equipos, que cuentan con dispositivos de protección como resguardos, sistemas de parada de emergencia, controles bimanuales y sensores de presencia para proteger a los operarios y evitar accidentes.
En conjunto, los equipos para estampado hidráulicos constituyen una solución avanzada y confiable para la conformación de metales, combinando potencia, precisión y tecnología de control para satisfacer las demandas actuales y futuras de la industria manufacturera.
Además, la evolución de los equipos para estampado hidráulicos ha llevado al desarrollo de sistemas electrohidráulicos que combinan la potencia de la hidráulica con la precisión y rapidez de los actuadores eléctricos. Estos sistemas permiten una mayor eficiencia energética y un control más detallado de los movimientos, lo que es especialmente beneficioso en procesos que requieren múltiples etapas o conformados complejos.
Los avances en software de simulación y modelado permiten optimizar el diseño del proceso de estampado antes de la fabricación física, reduciendo costos y tiempos de desarrollo. Mediante simulaciones, es posible prever puntos críticos de deformación, espesores y posibles defectos, lo que facilita ajustes en el diseño de matrices, selección de materiales y programación de parámetros hidráulicos para obtener resultados óptimos.
La modularidad y escalabilidad de estos equipos facilitan su adaptación a diferentes líneas de producción, permitiendo desde pequeñas series hasta grandes volúmenes, con rápida reconfiguración para distintos modelos o piezas. Esto es fundamental en mercados donde la personalización y rapidez en la producción son clave para la competitividad.
La implementación de sistemas de mantenimiento predictivo, apoyados en el análisis continuo de datos y tecnologías de inteligencia artificial, ayuda a anticipar fallas en componentes hidráulicos y mecánicos, reduciendo tiempos de inactividad y aumentando la disponibilidad de los equipos. Esto mejora la eficiencia operativa y disminuye los costos asociados a reparaciones no planificadas.
Por último, la creciente demanda de procesos más sostenibles ha impulsado el desarrollo de tecnologías que minimizan el consumo energético y el impacto ambiental de estos equipos, como el uso de fluidos hidráulicos biodegradables, sistemas de recuperación de energía y diseños que optimizan el uso de materiales y recursos.
En conjunto, estos avances consolidan a los equipos para estampado hidráulicos como una tecnología esencial en la manufactura moderna, capaz de ofrecer alta precisión, flexibilidad y eficiencia para responder a las exigencias dinámicas de la industria actual.
Prensas hidráulicas de embutición de láminas
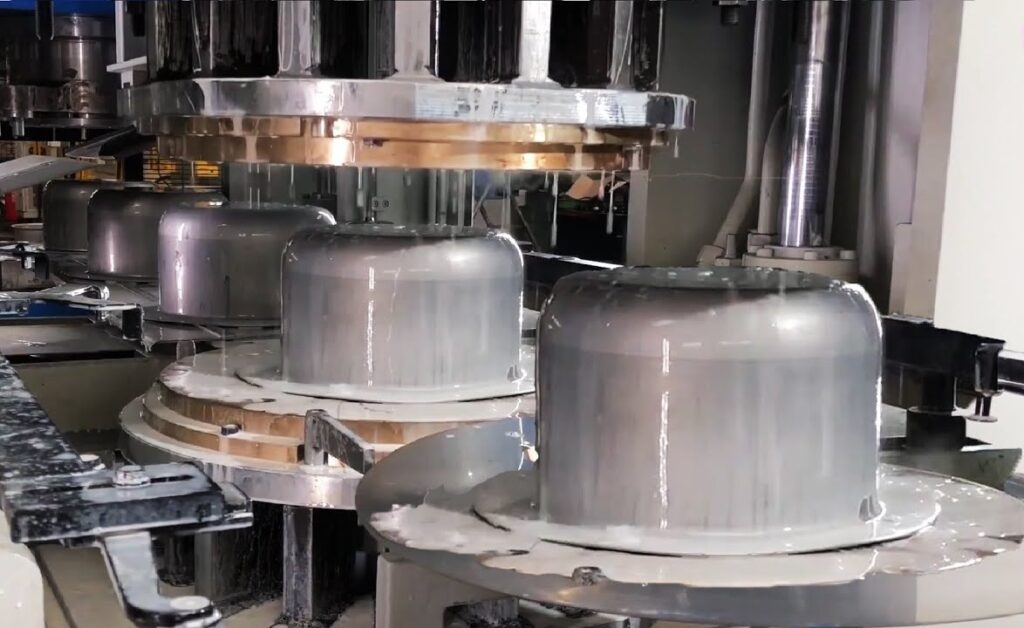
Las prensas hidráulicas de embutición de láminas son máquinas especialmente diseñadas para conformar piezas metálicas a partir de láminas mediante la aplicación de fuerzas hidráulicas controladas y precisas. Este tipo de prensas es fundamental en la fabricación de piezas con formas complejas y profundidades considerables, típicas en la industria automotriz, electrodomésticos, envases metálicos y sectores donde la calidad superficial y dimensional es clave.
El sistema hidráulico de estas prensas permite generar fuerzas elevadas de manera constante durante todo el recorrido del punzón, a diferencia de las prensas mecánicas donde la fuerza máxima se aplica solo en ciertos puntos del ciclo. Esta característica es esencial para lograr embuticiones profundas sin causar daños o deformaciones indeseadas en la lámina, garantizando uniformidad y calidad en el producto final.
Estas prensas cuentan con unidades hidráulicas que incluyen bombas de caudal variable, válvulas proporcionales y acumuladores que permiten ajustar y mantener la presión y velocidad durante el proceso. La capacidad de control dinámico facilita la adaptación a distintos materiales, espesores y geometrías, aumentando la versatilidad del equipo.
El utillaje, formado por matrices y punzones de alta resistencia y precisión, es un componente clave que determina la calidad del embutido. Estos elementos están diseñados para permitir un flujo adecuado del material y evitar desgastes prematuros. Además, los sistemas de lubricación automatizados facilitan el desmoldeo y prolongan la vida útil del utillaje.
Las prensas hidráulicas de embutición suelen estar equipadas con sistemas de control electrónico basados en PLC o CNC, que permiten programar perfiles de presión, velocidad y posición, y supervisar en tiempo real las variables del proceso. Esto mejora la consistencia, reduce desperdicios y facilita ajustes rápidos ante cambios en la producción.
Su estructura robusta garantiza rigidez y estabilidad, minimizando vibraciones y deformaciones que puedan afectar la precisión dimensional. Además, incorporan dispositivos de seguridad como barreras, paradas de emergencia y controles bimanuales para proteger a los operadores.
Estas prensas varían en tamaño y capacidad, desde modelos compactos para piezas pequeñas hasta grandes equipos capaces de ejercer miles de toneladas para embuticiones profundas en piezas voluminosas o materiales de alta resistencia. La selección adecuada depende de las especificaciones del producto y el volumen de producción.
En resumen, las prensas hidráulicas de embutición de láminas combinan potencia, precisión y flexibilidad para transformar láminas metálicas en piezas complejas y de alta calidad, siendo herramientas esenciales en la manufactura moderna. ¿Quieres que te detalle ejemplos específicos, componentes técnicos o aplicaciones concretas?
Estas prensas hidráulicas de embutición de láminas destacan por su capacidad para adaptarse a diferentes tipos de materiales, desde aceros suaves hasta aleaciones de alta resistencia como aluminio o acero inoxidable. Gracias al control preciso de la presión y velocidad, es posible realizar embuticiones profundas y complejas sin comprometer la integridad del material ni la calidad superficial de la pieza.
La construcción robusta de la prensa asegura que la fuerza aplicada se distribuya de manera uniforme y controlada, evitando deformaciones no deseadas en la estructura y manteniendo la precisión dimensional. Los sistemas de guía y alineación garantizan el posicionamiento exacto del punzón y la matriz durante el proceso, lo que es esencial para reproducir piezas con tolerancias estrictas en producciones en serie.
La automatización juega un papel importante en estas prensas, integrándose con sistemas de alimentación y descarga automática, robots manipuladores y estaciones de inspección para mejorar la eficiencia y reducir la intervención manual. Esto contribuye a disminuir los tiempos de ciclo y aumentar la seguridad del operador.
El mantenimiento preventivo y predictivo es fundamental para asegurar la continuidad y calidad del proceso. Esto incluye la revisión periódica del fluido hidráulico, filtros, sellos y componentes mecánicos, así como la calibración de sensores y sistemas de control. La detección temprana de fallos mediante monitoreo en tiempo real ayuda a evitar paradas no programadas y prolongar la vida útil del equipo.
La seguridad es otro aspecto clave en el diseño y operación de estas prensas, que incorporan dispositivos como resguardos físicos, sistemas de parada de emergencia, controles bimanuales y sensores de presencia para proteger al personal durante la operación.
En definitiva, las prensas hidráulicas de embutición de láminas combinan fuerza, precisión, tecnología avanzada y seguridad para ofrecer soluciones eficientes y confiables en la fabricación de piezas metálicas complejas, siendo un componente esencial en la industria manufacturera actual.
Además, el desarrollo tecnológico ha permitido la incorporación de sistemas electrohidráulicos que combinan la potencia de la hidráulica con la precisión y rapidez de los actuadores eléctricos, mejorando la eficiencia energética y el control del proceso. Estos sistemas facilitan la programación de ciclos complejos, con perfiles de presión y velocidad ajustables para cada etapa de la embutición, lo que resulta en una mayor calidad y reducción de desperdicios.
Las interfaces hombre-máquina (HMI) modernas ofrecen paneles táctiles intuitivos que permiten a los operadores configurar, monitorear y ajustar parámetros de manera sencilla y en tiempo real. Esto reduce errores, facilita la capacitación y mejora la trazabilidad del proceso al registrar datos relevantes de producción.
La simulación virtual y el modelado por elementos finitos son herramientas valiosas que se utilizan para diseñar y optimizar tanto el utillaje como los parámetros de embutición antes de iniciar la producción física. Esto reduce significativamente los costos y tiempos de desarrollo, además de minimizar pruebas destructivas y rechazos.
La integración con sistemas de automatización industrial y robótica permite crear líneas de producción altamente eficientes, donde la alimentación, embutición, inspección y manipulación de piezas se realizan de forma coordinada y con mínima intervención humana, aumentando la productividad y seguridad.
Por otro lado, la sostenibilidad cobra cada vez mayor importancia, por lo que las prensas hidráulicas modernas incorporan tecnologías para reducir el consumo energético, como bombas de caudal variable y sistemas de recuperación de energía hidráulica. También se utilizan fluidos hidráulicos ecológicos que disminuyen el impacto ambiental sin sacrificar el rendimiento.
Finalmente, la capacitación continua de los operadores y técnicos es fundamental para aprovechar al máximo las capacidades de estas prensas y mantener altos estándares de calidad y seguridad. La combinación de tecnología avanzada, mantenimiento adecuado y personal capacitado garantiza el éxito en los procesos de embutición con prensas hidráulicas de láminas.
En conjunto, estas características posicionan a las prensas hidráulicas de embutición de láminas como herramientas indispensables para la manufactura moderna, capaces de responder a las demandas de calidad, eficiencia y flexibilidad que exige la industria actual.
Prensas hidráulicas de conformado de metales
Las prensas hidráulicas de conformado de metales son máquinas diseñadas para moldear y dar forma a materiales metálicos mediante la aplicación controlada de fuerza hidráulica. Este tipo de prensas se utiliza ampliamente en procesos como embutición, estampado, doblado, forjado y punzonado, permitiendo transformar láminas, placas o perfiles metálicos en piezas con geometrías complejas y precisas.
El funcionamiento de estas prensas se basa en un sistema hidráulico que genera presión sobre un fluido, transmitiendo esta fuerza a cilindros hidráulicos que mueven el punzón o herramienta contra el material a conformar, el cual está apoyado sobre una matriz. La fuerza generada puede ser ajustada y mantenida constante durante todo el ciclo, lo que facilita un control preciso del proceso y reduce defectos comunes como arrugas, grietas o deformaciones no deseadas.
Las prensas hidráulicas para conformado suelen contar con unidades de potencia que incluyen bombas de desplazamiento variable, válvulas proporcionales y acumuladores, que permiten un ajuste dinámico de presión y velocidad para adaptarse a diferentes materiales y procesos. Los sistemas de control electrónicos, basados en PLC o CNC, proporcionan supervisión en tiempo real y facilitan la programación de perfiles de fuerza y movimiento, aumentando la precisión y repetibilidad.
Estas máquinas están construidas con estructuras robustas y rígidas para soportar altas cargas y minimizar vibraciones y deformaciones, lo que es esencial para mantener la calidad dimensional y superficial de las piezas. Además, incorporan sistemas de guía y alineación que aseguran el correcto posicionamiento del punzón y la matriz durante el proceso.
La versatilidad de las prensas hidráulicas de conformado las hace aptas para trabajar con una amplia variedad de metales, desde aceros blandos hasta aleaciones de alta resistencia, y en diferentes espesores. Esto las convierte en una solución ideal para sectores como la industria automotriz, aeroespacial, electrodomésticos, fabricación de envases metálicos y maquinaria industrial.
La integración con sistemas automatizados de alimentación, descarga y manipulación, así como con tecnologías de inspección y control de calidad, permite la creación de líneas de producción eficientes y seguras. Además, el mantenimiento predictivo y preventivo basado en el monitoreo continuo de componentes hidráulicos y electrónicos contribuye a maximizar la disponibilidad y vida útil de las máquinas.
En resumen, las prensas hidráulicas de conformado de metales combinan potencia, precisión y flexibilidad tecnológica para satisfacer las demandas crecientes de la manufactura moderna, facilitando la producción de piezas metálicas complejas con altos estándares de calidad y productividad. ¿Quieres que profundice en algún proceso específico o en tipos de prensas hidráulicas para conformado?
Estas prensas hidráulicas de conformado de metales destacan por su capacidad para ofrecer una fuerza ajustable y constante a lo largo de todo el ciclo de trabajo, lo que permite controlar con precisión la deformación del material y obtener piezas con tolerancias estrictas y acabados superficiales de alta calidad. Esta característica es especialmente útil en procesos que requieren embuticiones profundas, dobleces complejos o estampados detallados.
El diseño estructural robusto de estas máquinas garantiza rigidez y estabilidad, minimizando vibraciones y deformaciones durante la operación, lo que se traduce en una mayor precisión y repetibilidad en la producción. Además, sistemas avanzados de guía y alineación aseguran el posicionamiento exacto de las herramientas, evitando desgastes prematuros y mejorando la vida útil del utillaje.
La versatilidad es otra ventaja clave, ya que estas prensas pueden adaptarse para trabajar con distintos tipos de metales y espesores, desde láminas delgadas hasta piezas más gruesas o resistentes. Los sistemas hidráulicos modernos cuentan con bombas de desplazamiento variable, válvulas proporcionales y acumuladores que regulan de manera dinámica la presión y velocidad, optimizando el proceso y reduciendo el consumo energético.
La integración con sistemas electrónicos de control, como PLCs o CNCs, facilita la programación y monitoreo en tiempo real de variables críticas como presión, velocidad y posición, permitiendo ajustes automáticos para mantener la calidad y detectar posibles fallas. Esta tecnología también posibilita la implementación de perfiles de trabajo personalizados para diferentes piezas o materiales.
En la industria moderna, estas prensas se combinan con tecnologías de automatización y robótica para mejorar la productividad y seguridad. Sistemas automáticos de alimentación y descarga, así como estaciones de inspección y control de calidad, permiten operaciones continuas y precisas con mínima intervención humana.
El mantenimiento preventivo y predictivo es fundamental para asegurar la eficiencia y prolongar la vida útil de las prensas hidráulicas de conformado. La monitorización constante de componentes hidráulicos, electrónicos y mecánicos ayuda a identificar desgastes o anomalías antes de que provoquen paradas no planificadas o daños mayores.
Finalmente, la seguridad es un aspecto prioritario en el diseño y operación de estas máquinas, incorporando dispositivos como barreras físicas, controles bimanuales, sensores de presencia y sistemas de parada de emergencia para proteger a los operadores y cumplir con normativas internacionales.
En conjunto, las prensas hidráulicas de conformado de metales son herramientas esenciales que combinan potencia, precisión, flexibilidad y tecnología avanzada para responder a las exigencias dinámicas de la fabricación industrial actual, permitiendo la producción eficiente de componentes metálicos complejos y de alta calidad.
Además, las prensas hidráulicas de conformado de metales han evolucionado incorporando tecnologías electrohidráulicas que combinan la fuerza y robustez de los sistemas hidráulicos con la precisión y rapidez de actuadores eléctricos. Esta combinación mejora la eficiencia energética y permite un control más detallado y dinámico de la presión y el movimiento, lo que resulta ideal para procesos complejos y de alta repetibilidad.
El avance en software de simulación y modelado virtual ha permitido optimizar el diseño de las prensas y el utillaje, así como prever el comportamiento del material durante el conformado. Esto reduce el tiempo y costo de desarrollo, minimiza defectos y aumenta la tasa de éxito en la producción, facilitando también la adaptación a nuevos diseños o materiales.
La modularidad de las prensas hidráulicas facilita su integración en líneas de producción flexibles y escalables, permitiendo ajustes rápidos para distintos tipos de piezas o lotes variables, lo que es fundamental en industrias que requieren agilidad y personalización sin sacrificar la calidad o la eficiencia.
Los sistemas de mantenimiento predictivo, apoyados en el análisis continuo de datos recogidos por sensores inteligentes, permiten anticipar fallas y programar intervenciones oportunas, optimizando la disponibilidad de la máquina y reduciendo costos operativos.
Finalmente, la sostenibilidad se ha convertido en un factor clave, impulsando el desarrollo de prensas hidráulicas que incorporan sistemas de recuperación de energía, fluidos hidráulicos ecológicos y diseños que minimizan el consumo eléctrico, contribuyendo así a procesos más responsables con el medio ambiente.
En resumen, las prensas hidráulicas de conformado de metales representan una tecnología avanzada y versátil, esencial para la manufactura moderna, capaz de ofrecer la combinación perfecta de fuerza, precisión, flexibilidad y eficiencia para responder a las exigencias crecientes de la industria global.
Herramientas hidráulicas para conformado
Las herramientas hidráulicas para conformado son dispositivos que utilizan la presión hidráulica para moldear, doblar, estampar, embutir o cortar materiales metálicos con alta precisión y control. Estas herramientas forman parte integral de los sistemas hidráulicos empleados en prensas, dobladoras, punzonadoras y otras máquinas dedicadas al trabajo de metales, proporcionando la fuerza necesaria para transformar láminas o piezas en componentes con geometrías complejas y acabados de calidad.
El principio básico de estas herramientas radica en la transmisión de fuerza mediante un fluido hidráulico a alta presión, que actúa sobre cilindros o actuadores para mover elementos como punzones, matrices, troqueles o dispositivos de sujeción. Gracias a la capacidad del sistema hidráulico para regular la presión y velocidad de manera precisa, las herramientas pueden adaptarse a diferentes procesos y materiales, garantizando uniformidad en la deformación y minimizando defectos.
Entre las herramientas hidráulicas más comunes para conformado se encuentran los cilindros hidráulicos de gran capacidad, que impulsan punzones o martillos para embutición o estampado; matrices hidráulicas que ayudan a dar forma y soporte al material durante el proceso; y sistemas de sujeción o fijación hidráulicos que aseguran la pieza en posición durante la operación, evitando movimientos indeseados.
Las herramientas hidráulicas también incluyen dispositivos especializados como dobladoras hidráulicas para perfiles y chapas, cizallas hidráulicas para cortes precisos y punzonadoras hidráulicas para perforaciones. Estas herramientas se caracterizan por su robustez, capacidad de ajuste y durabilidad, siendo esenciales para mantener la calidad y productividad en procesos industriales.
La incorporación de sensores y sistemas de control en estas herramientas permite monitorear parámetros como presión, fuerza y posición, facilitando ajustes en tiempo real para optimizar el proceso y asegurar la calidad del producto final. Además, estas herramientas pueden integrarse en sistemas automatizados, mejorando la eficiencia y seguridad en la producción.
El mantenimiento adecuado de las herramientas hidráulicas para conformado es vital para prolongar su vida útil y evitar paradas no planificadas. Esto incluye la revisión periódica de sellos, juntas, lubricación y calibración de sensores, así como la limpieza y sustitución de componentes desgastados.
En resumen, las herramientas hidráulicas para conformado constituyen elementos clave en la transformación de metales, ofreciendo la fuerza, precisión y flexibilidad necesarias para fabricar piezas complejas y de alta calidad en diversas industrias. ¿Quieres que te explique alguna herramienta en particular o su aplicación específica?
Estas herramientas hidráulicas para conformado se distinguen por su capacidad para adaptarse a una amplia variedad de procesos y materiales, desde láminas delgadas hasta piezas gruesas o aleaciones de alta resistencia. La precisión en el control de la fuerza y el movimiento permite evitar defectos como arrugas, fisuras o deformaciones irregulares, garantizando la uniformidad y calidad de las piezas fabricadas.
El diseño modular y robusto de estas herramientas asegura una larga vida útil y facilita su mantenimiento, así como la rápida sustitución o ajuste de componentes según las necesidades del proceso. Los cilindros y actuadores hidráulicos están fabricados con materiales resistentes y tratados para soportar altas presiones y ciclos continuos de trabajo, manteniendo un rendimiento constante.
La integración de sensores inteligentes y sistemas de monitoreo en tiempo real permite supervisar parámetros críticos como presión, desplazamiento y temperatura, facilitando la detección temprana de anomalías y la implementación de mantenimiento predictivo. Esto contribuye a minimizar tiempos de inactividad y optimizar la productividad.
Además, estas herramientas pueden incorporarse en sistemas automatizados que incluyen robots, estaciones de carga y descarga, y controles electrónicos avanzados, lo que mejora la eficiencia operativa y reduce la intervención manual, incrementando la seguridad en el entorno de trabajo.
Las herramientas hidráulicas para conformado se utilizan en una gran variedad de industrias, desde la automotriz y aeroespacial hasta la fabricación de electrodomésticos y maquinaria industrial, donde la calidad y precisión de las piezas son fundamentales. Su versatilidad permite adaptar rápidamente la producción a diferentes diseños y materiales, respondiendo a las demandas dinámicas del mercado.
Finalmente, la sostenibilidad es una preocupación creciente, por lo que estas herramientas suelen diseñarse para maximizar la eficiencia energética, reducir el uso de fluidos hidráulicos contaminantes y facilitar procesos de reciclaje y reutilización, contribuyendo a una producción más responsable con el medio ambiente.
En conjunto, las herramientas hidráulicas para conformado representan una combinación óptima de fuerza, control, durabilidad y tecnología avanzada, que permiten transformar metales en componentes complejos y de alta calidad de manera eficiente y confiable.
Asimismo, la innovación en herramientas hidráulicas para conformado ha impulsado el desarrollo de sistemas electrohidráulicos que combinan la potencia del fluido hidráulico con la precisión y velocidad de actuadores eléctricos. Esta combinación permite una respuesta más rápida y un control más detallado sobre el proceso, ideal para aplicaciones que requieren movimientos complejos y alta repetibilidad.
La capacidad de programar perfiles de presión, velocidad y posición mediante interfaces digitales avanzadas facilita la adaptación rápida a diferentes piezas y materiales, reduciendo tiempos de configuración y aumentando la flexibilidad productiva. Además, estas herramientas pueden almacenar y reproducir ciclos predefinidos, asegurando consistencia en la fabricación y facilitando la capacitación del personal.
El uso de materiales avanzados y tratamientos superficiales en la fabricación de las herramientas prolonga su vida útil y mejora su resistencia al desgaste, corrosión y fatiga, lo que es crucial para mantener la calidad del proceso y reducir costos de mantenimiento y reposición.
La incorporación de tecnologías de monitoreo basadas en inteligencia artificial y análisis de datos permite anticipar fallas y optimizar el rendimiento de las herramientas, implementando mantenimiento predictivo y evitando paradas no planificadas que afectan la productividad.
Además, el diseño ergonómico y la implementación de sistemas de seguridad avanzados protegen a los operadores y facilitan el manejo de las herramientas, reduciendo riesgos y mejorando las condiciones laborales.
En resumen, las herramientas hidráulicas para conformado están en constante evolución, integrando tecnologías que mejoran su precisión, eficiencia y durabilidad, y que se adaptan a las exigencias cada vez mayores de la industria moderna para producir piezas metálicas complejas con altos estándares de calidad y productividad.
Máquinas bordonadoras hidráulicas
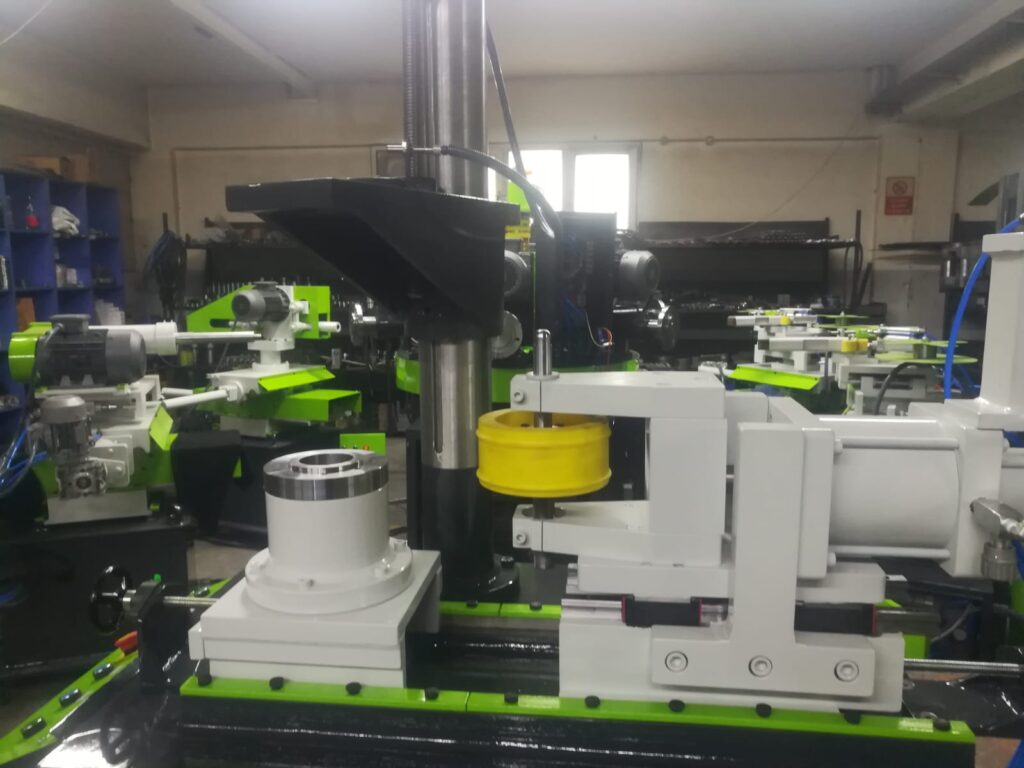
Las máquinas bordonadoras hidráulicas son equipos industriales diseñados para realizar el proceso de bordonado o plegado en láminas metálicas mediante la aplicación controlada de fuerza hidráulica. Este proceso consiste en doblar los bordes de una lámina para reforzarla, mejorar su rigidez estructural, eliminar bordes cortantes o preparar la pieza para su ensamblaje posterior. Son ampliamente utilizadas en sectores como la fabricación de componentes automotrices, muebles metálicos, electrodomésticos, construcción y envases metálicos.
El principio de funcionamiento de estas máquinas se basa en un sistema hidráulico que suministra presión constante y ajustable a través de cilindros hidráulicos que accionan las herramientas de plegado o doblado. La fuerza hidráulica permite realizar bordes con formas precisas y uniformes, incluso en láminas de diferentes espesores y materiales, sin dañar ni deformar la superficie principal de la pieza.
Las máquinas bordonadoras hidráulicas pueden variar desde modelos compactos para trabajos ligeros hasta grandes prensas para piezas voluminosas y espesores considerables. Su diseño robusto garantiza estabilidad y rigidez durante el proceso, lo que es fundamental para obtener resultados repetibles y de alta calidad.
El sistema hidráulico está compuesto por bombas, válvulas de control, acumuladores y sistemas de filtración, que trabajan conjuntamente para mantener la presión adecuada y la velocidad óptima del proceso. Esto permite ajustar parámetros como la fuerza aplicada, la velocidad de plegado y el ángulo final del borde, adaptándose a diferentes requerimientos productivos.
Muchas de estas máquinas cuentan con controles electrónicos y PLC que permiten programar ciclos automáticos, memorizar configuraciones para distintos tipos de piezas y supervisar en tiempo real variables como presión y posición. Esto mejora la precisión, reduce tiempos de configuración y minimiza errores operativos.
La automatización puede incluir sistemas de alimentación y descarga automática, integración con robots para manipulación de piezas y estaciones de inspección, optimizando la productividad y reduciendo la intervención manual, lo que también incrementa la seguridad del operario.
El mantenimiento preventivo es fundamental para asegurar la fiabilidad y longevidad de las máquinas bordonadoras hidráulicas. Esto incluye la revisión periódica del fluido hidráulico, limpieza y cambio de filtros, inspección de sellos y juntas, y calibración de sistemas de control.
En conclusión, las máquinas bordonadoras hidráulicas son herramientas esenciales en la manufactura de piezas metálicas, proporcionando la fuerza, precisión y flexibilidad necesarias para realizar bordes de alta calidad que mejoran la funcionalidad y estética de los productos finales. ¿Quieres que te explique tipos específicos de bordonadoras o aplicaciones concretas?
Las máquinas bordonadoras hidráulicas ofrecen una gran versatilidad al poder trabajar con diferentes tipos de metales y espesores, desde láminas delgadas hasta chapas gruesas y materiales de alta resistencia como aceros inoxidables o aleaciones de aluminio. Esto las convierte en una solución adaptable para múltiples industrias y aplicaciones.
El sistema hidráulico permite un control fino de la fuerza y velocidad durante el proceso de plegado, lo que garantiza bordes uniformes y precisos sin provocar deformaciones indeseadas en la pieza. Además, la capacidad de mantener presión constante durante todo el recorrido del cilindro hidráulico facilita la realización de bordes profundos o con geometrías complejas.
El diseño estructural robusto y estable de estas máquinas minimiza vibraciones y desplazamientos durante la operación, asegurando la repetibilidad y calidad dimensional de las piezas producidas. Asimismo, incorporan guías y sistemas de alineación para un posicionamiento exacto del material y las herramientas de plegado.
La incorporación de sistemas de control electrónico y software avanzado permite programar secuencias de trabajo, almacenar perfiles para diferentes piezas y monitorear parámetros clave en tiempo real, facilitando ajustes rápidos y asegurando la consistencia en la producción. Esto es especialmente útil en procesos de fabricación en serie o cuando se requieren cambios frecuentes de producto.
Las bordonadoras hidráulicas modernas pueden integrarse con sistemas de automatización y robótica, incluyendo alimentación y descarga automáticas, manipulación de piezas y estaciones de inspección, aumentando la eficiencia y reduciendo la necesidad de intervención manual, lo que a su vez mejora la seguridad laboral.
El mantenimiento adecuado de estos equipos es esencial para prolongar su vida útil y mantener su rendimiento. Esto implica la revisión periódica de componentes hidráulicos, como bombas, válvulas, cilindros y filtros, además de la calibración de sensores y controles electrónicos para asegurar un funcionamiento óptimo.
En definitiva, las máquinas bordonadoras hidráulicas constituyen una solución robusta, precisa y flexible para el doblado y refuerzo de bordes en piezas metálicas, siendo fundamentales en procesos industriales que demandan calidad, eficiencia y adaptabilidad.
Además, la evolución tecnológica en máquinas bordonadoras hidráulicas ha permitido la incorporación de sistemas electrohidráulicos que combinan la fuerza hidráulica con la precisión y rapidez de los actuadores eléctricos. Esto resulta en una mayor eficiencia energética, mejor control de la velocidad y fuerza aplicada, y la posibilidad de realizar ciclos de trabajo más complejos y personalizados según las necesidades del proceso.
El uso de interfaces hombre-máquina (HMI) intuitivas y paneles táctiles facilita la configuración, supervisión y ajuste de parámetros, haciendo que la operación sea más accesible para los operadores y reduciendo el margen de error. Estas interfaces también permiten almacenar programas para diferentes tipos de piezas y materiales, agilizando los cambios de producción.
Las máquinas bordonadoras hidráulicas modernas incorporan además sistemas de monitoreo en tiempo real que registran datos sobre presión, posición, temperatura y estado del sistema hidráulico, permitiendo la implementación de mantenimiento predictivo. Esto ayuda a prevenir fallas inesperadas, optimizar los intervalos de mantenimiento y maximizar la disponibilidad de la máquina.
La modularidad en el diseño permite adaptar fácilmente las máquinas a diferentes configuraciones de producción y facilitar la integración con otras etapas del proceso productivo, como corte, estampado o ensamblaje, contribuyendo a la creación de líneas de fabricación integradas y automatizadas.
En términos de seguridad, estas máquinas cuentan con dispositivos como resguardos físicos, sensores de presencia, sistemas de parada de emergencia y controles bimanuales para proteger a los operadores durante la operación, cumpliendo con normativas internacionales y fomentando un entorno de trabajo seguro.
Finalmente, la preocupación por la sostenibilidad ha impulsado el desarrollo de sistemas hidráulicos más eficientes y el uso de fluidos hidráulicos ecológicos, reduciendo el consumo energético y el impacto ambiental asociado con el funcionamiento de estas máquinas.
En conjunto, las máquinas bordonadoras hidráulicas representan una tecnología madura y en constante evolución, que ofrece precisión, potencia, flexibilidad y seguridad para satisfacer las exigencias de la industria moderna en la fabricación de piezas metálicas con bordes reforzados y acabados de alta calidad.
Prensas hidráulicas para fabricación de productos metálicos
Las prensas hidráulicas para fabricación de productos metálicos son equipos fundamentales en la industria manufacturera, diseñados para conformar, cortar, embutir, doblar y ensamblar piezas metálicas mediante la aplicación de fuerzas hidráulicas controladas. Estas prensas ofrecen gran potencia y precisión, permitiendo transformar láminas, perfiles y otros materiales metálicos en componentes con geometrías complejas y acabados de alta calidad.
El principio de funcionamiento se basa en un sistema hidráulico que genera presión sobre un fluido, la cual se transmite a cilindros hidráulicos que mueven herramientas como punzones, matrices o troqueles para moldear el material. La capacidad de ajustar y mantener la fuerza durante todo el ciclo permite un control preciso del proceso y minimiza defectos, lo que es crucial para la fabricación en serie de piezas uniformes y confiables.
Estas prensas varían en tamaño, capacidad y configuración, desde modelos compactos para piezas pequeñas hasta prensas de gran tonelaje utilizadas en la producción de componentes estructurales o partes automotrices de gran tamaño. Pueden ser de doble efecto, de una o dos columnas, o en configuraciones especiales según la aplicación específica.
Los sistemas hidráulicos modernos incorporan bombas de desplazamiento variable, válvulas proporcionales y acumuladores que permiten un control dinámico de la presión y velocidad, optimizando el proceso y reduciendo el consumo energético. Además, la integración con controles electrónicos basados en PLC o CNC facilita la programación de ciclos, el monitoreo en tiempo real y la automatización de la producción.
La robustez estructural y los sistemas de guía y alineación aseguran la estabilidad y precisión durante la operación, reduciendo el desgaste del utillaje y prolongando la vida útil de la prensa. La versatilidad permite trabajar con una amplia gama de materiales, desde aceros blandos hasta aleaciones especiales, y adaptarse a diferentes espesores y formatos.
La incorporación de sistemas de automatización, incluyendo alimentación y descarga automática, robots y estaciones de inspección, mejora la productividad y seguridad, permitiendo ciclos de trabajo más rápidos y reduciendo la intervención manual. Esto es vital para mantener competitividad en industrias como la automotriz, aeroespacial, electrodomésticos, construcción y maquinaria industrial.
El mantenimiento preventivo y predictivo basado en la monitorización constante de componentes hidráulicos, mecánicos y electrónicos es clave para maximizar la disponibilidad y rendimiento de las prensas. Esto incluye la revisión y cambio de fluidos, limpieza y sustitución de filtros, calibración de sensores y controladores, y la inspección de partes mecánicas.
En resumen, las prensas hidráulicas para fabricación de productos metálicos combinan potencia, precisión, tecnología avanzada y flexibilidad para satisfacer las exigencias de la manufactura moderna, facilitando la producción eficiente y de alta calidad de una amplia variedad de piezas metálicas. ¿Quieres que te detalle aplicaciones específicas, tipos de prensas o componentes técnicos?
Estas prensas hidráulicas para fabricación de productos metálicos se caracterizan por su capacidad para ofrecer una fuerza ajustable y constante a lo largo de todo el ciclo de trabajo, lo que permite un control preciso sobre la deformación del material y garantiza la calidad dimensional y superficial de las piezas producidas. Esta característica es fundamental en procesos que requieren embuticiones profundas, cortes complejos o doblados precisos.
El diseño estructural robusto y rígido de estas prensas asegura estabilidad durante la operación, minimizando vibraciones y deformaciones que puedan afectar la precisión. Los sistemas de guía y alineación mantienen la correcta posición del punzón y la matriz, lo que reduce el desgaste del utillaje y prolonga la vida útil del equipo.
La versatilidad es un punto fuerte, ya que estas máquinas pueden adaptarse para trabajar con diferentes materiales y espesores, desde láminas delgadas hasta placas gruesas o aleaciones resistentes. Los sistemas hidráulicos modernos incorporan bombas de caudal variable, válvulas proporcionales y acumuladores que regulan dinámicamente la presión y velocidad, optimizando el consumo energético y la calidad del proceso.
La integración con controles electrónicos como PLC o CNC permite programar ciclos personalizados, monitorear variables críticas en tiempo real y ajustar automáticamente parámetros para mantener la consistencia y detectar posibles fallas o desgastes. Esta automatización mejora la productividad y reduce errores humanos.
En entornos industriales, estas prensas suelen formar parte de líneas de producción automatizadas, combinándose con sistemas de alimentación y descarga automática, robots manipuladores y estaciones de inspección, lo que aumenta la eficiencia y la seguridad laboral al reducir la intervención manual directa.
El mantenimiento preventivo y predictivo es esencial para garantizar la disponibilidad y el rendimiento óptimo de las prensas hidráulicas. Esto implica la revisión periódica del fluido hidráulico, limpieza y cambio de filtros, inspección de sellos y juntas, calibración de sensores y controles, y supervisión del estado mecánico mediante análisis de vibraciones o termografía.
En términos de seguridad, las prensas hidráulicas incorporan dispositivos como barreras físicas, sensores de presencia, controles bimanuales y sistemas de parada de emergencia para proteger a los operarios y cumplir con normativas internacionales.
En conjunto, las prensas hidráulicas para fabricación de productos metálicos representan una tecnología confiable y avanzada, capaz de proporcionar la combinación ideal de fuerza, precisión, flexibilidad y automatización que requiere la industria manufacturera moderna para producir piezas metálicas complejas y de alta calidad.
Además, la evolución tecnológica en prensas hidráulicas ha impulsado la integración de sistemas electrohidráulicos que combinan la potencia de la hidráulica con la precisión y rapidez de actuadores eléctricos. Esto mejora la eficiencia energética y permite un control más detallado y dinámico del proceso, ideal para aplicaciones que requieren movimientos complejos y alta repetibilidad.
Los avances en software de simulación y modelado permiten optimizar tanto el diseño del utillaje como los parámetros de operación antes de iniciar la producción física, reduciendo tiempos y costos asociados a pruebas y ajustes. La simulación ayuda a prever puntos críticos de deformación, esfuerzos y posibles defectos, facilitando la toma de decisiones para mejorar la calidad y productividad.
La modularidad y escalabilidad de estas prensas facilitan su adaptación a diferentes volúmenes y tipos de producción, desde series pequeñas hasta grandes lotes, con rápida reconfiguración para distintas piezas o materiales. Esto es fundamental en mercados que demandan flexibilidad y rapidez sin sacrificar la calidad.
La incorporación de mantenimiento predictivo apoyado en análisis de datos y monitoreo continuo permite anticipar fallas, programar intervenciones oportunas y maximizar la disponibilidad de las máquinas. Esta práctica reduce costos operativos y evita paradas no planificadas que impactan la producción.
En términos de sostenibilidad, las prensas hidráulicas modernas buscan minimizar su consumo energético mediante el uso de bombas de caudal variable, sistemas de recuperación de energía y fluidos hidráulicos biodegradables, contribuyendo a procesos más respetuosos con el medio ambiente.
Finalmente, la capacitación constante del personal es clave para aprovechar al máximo las capacidades tecnológicas de estas prensas, garantizar la seguridad y mantener altos estándares de calidad en la fabricación de productos metálicos.
En resumen, las prensas hidráulicas para fabricación de productos metálicos son equipos esenciales y en constante evolución, que combinan fuerza, precisión, flexibilidad y tecnología avanzada para satisfacer las exigencias dinámicas de la manufactura moderna.
Equipos de bordonado hidráulicos
Los equipos de bordonado hidráulicos son máquinas industriales diseñadas para realizar el proceso de doblado o plegado de bordes en láminas metálicas utilizando la fuerza controlada de sistemas hidráulicos. Estos equipos son esenciales para reforzar, dar forma o preparar las piezas metálicas para etapas posteriores de ensamblaje, mejorando su rigidez, seguridad y estética. Se utilizan en sectores variados como la fabricación de muebles metálicos, componentes automotrices, electrodomésticos, construcción y envases metálicos.
El principio de funcionamiento de estos equipos se basa en un sistema hidráulico que transmite presión mediante fluidos a cilindros o actuadores, los cuales accionan herramientas específicas que doblan o pliegan el borde de la lámina con precisión y uniformidad. La fuerza hidráulica permite adaptar el proceso a distintos materiales y espesores, logrando bordes consistentes sin causar daños o deformaciones no deseadas en la pieza.
Existen diversos tipos de equipos de bordonado hidráulicos, que varían en tamaño, capacidad y configuración según la aplicación. Pueden ser prensas hidráulicas con herramientas de doblado, máquinas específicas de plegado con cilindros múltiples, o sistemas integrados en líneas de producción automatizadas. La versatilidad y capacidad de ajuste hacen que estos equipos sean aptos para una amplia gama de trabajos, desde piezas pequeñas hasta grandes paneles metálicos.
Los sistemas hidráulicos modernos incorporan bombas de caudal variable, válvulas proporcionales y acumuladores que permiten un control dinámico de la presión y velocidad, optimizando la calidad del doblado y la eficiencia energética. Además, la inclusión de controles electrónicos y PLC facilita la programación de ciclos, el monitoreo en tiempo real y la repetibilidad de procesos, reduciendo errores y tiempos de configuración.
La estructura robusta de los equipos garantiza estabilidad y rigidez durante el proceso, lo que es fundamental para mantener la precisión dimensional y prolongar la vida útil de las herramientas. Los sistemas de guía y alineación aseguran el correcto posicionamiento del material y las herramientas, evitando desgastes prematuros.
La automatización puede incluir sistemas de alimentación y descarga automáticos, integración con robots para manipulación de piezas y estaciones de inspección, mejorando la productividad y seguridad laboral al reducir la intervención manual.
El mantenimiento preventivo y predictivo es crucial para asegurar el buen funcionamiento y longevidad de los equipos, incluyendo la revisión del fluido hidráulico, filtros, sellos, calibración de sensores y limpieza general.
En resumen, los equipos de bordonado hidráulicos son herramientas clave para la conformación de bordes metálicos con precisión, fuerza y flexibilidad, adaptándose a diversas aplicaciones industriales y contribuyendo a la fabricación eficiente y segura de productos metálicos de alta calidad. ¿Quieres que te detalle algún tipo específico de equipo o proceso de bordonado?
Los equipos de bordonado hidráulicos se destacan por su capacidad para adaptarse a diferentes tipos de metales y espesores, desde láminas delgadas hasta chapas gruesas o aleaciones resistentes, lo que los hace versátiles para múltiples industrias y aplicaciones. La fuerza hidráulica aplicada puede ser regulada con precisión para asegurar bordes uniformes y consistentes, evitando deformaciones o daños en la pieza durante el proceso.
El diseño robusto de estos equipos garantiza estabilidad y rigidez, minimizando vibraciones y desplazamientos que puedan afectar la calidad del doblado. Los sistemas de guía y alineación mantienen la posición exacta del material y las herramientas, prolongando la vida útil del utillaje y asegurando resultados repetibles.
La integración de controles electrónicos avanzados, como PLCs y sistemas de supervisión, permite programar y monitorear ciclos de trabajo, almacenar configuraciones para diferentes productos y realizar ajustes en tiempo real. Esto facilita la operación, reduce tiempos de cambio y mejora la consistencia en la producción.
Además, la automatización en estos equipos, mediante sistemas de alimentación y descarga automática, robots manipuladores y estaciones de inspección, incrementa la eficiencia productiva y reduce la necesidad de intervención manual, lo que también contribuye a mejorar la seguridad en el entorno laboral.
El mantenimiento adecuado es fundamental para el rendimiento y la durabilidad de los equipos de bordonado hidráulicos. Esto incluye la revisión periódica del sistema hidráulico, limpieza y cambio de filtros, inspección de sellos y juntas, y calibración de sensores para garantizar un funcionamiento óptimo.
La evolución tecnológica ha impulsado el desarrollo de sistemas electrohidráulicos que combinan la fuerza del fluido hidráulico con la precisión y rapidez de los actuadores eléctricos, mejorando la eficiencia energética y el control del proceso. Asimismo, el uso de fluidos hidráulicos ecológicos y sistemas de recuperación de energía contribuyen a una producción más sostenible.
En conjunto, los equipos de bordonado hidráulicos representan una solución confiable, precisa y flexible para la conformación de bordes en piezas metálicas, siendo indispensables para la fabricación moderna de productos metálicos con altos estándares de calidad y productividad.
Asimismo, la innovación en equipos de bordonado hidráulicos ha permitido incorporar interfaces hombre-máquina (HMI) intuitivas y paneles táctiles que facilitan la programación, supervisión y ajuste de parámetros en tiempo real. Estas interfaces permiten a los operadores configurar ciclos personalizados, almacenar perfiles para diferentes piezas y materiales, y acceder a diagnósticos y alertas, lo que mejora la eficiencia operativa y reduce errores.
El uso de tecnologías de monitoreo avanzado, como sensores inteligentes y análisis de datos, permite implementar mantenimiento predictivo basado en el estado real del equipo. Esto ayuda a anticipar posibles fallas, optimizar intervalos de mantenimiento y minimizar tiempos de inactividad no planificados, incrementando la productividad y reduciendo costos.
La modularidad en el diseño de los equipos facilita la adaptación a diversas configuraciones de producción y la integración con otras etapas del proceso, como corte, estampado o ensamblaje. Esto es clave para crear líneas de fabricación flexibles y escalables que respondan rápidamente a cambios en la demanda o en el diseño del producto.
En cuanto a la seguridad, los equipos de bordonado hidráulicos cuentan con dispositivos como resguardos físicos, sensores de presencia, controles bimanuales y sistemas de parada de emergencia para proteger a los operadores durante la operación y cumplir con normativas internacionales de seguridad industrial.
Finalmente, la sostenibilidad es una prioridad creciente, impulsando el desarrollo de sistemas hidráulicos más eficientes y el uso de fluidos ecológicos que minimizan el impacto ambiental. Además, el diseño de estos equipos busca reducir el consumo energético y facilitar procesos de reciclaje y reutilización de materiales.
En conjunto, los equipos de bordonado hidráulicos son soluciones tecnológicas avanzadas que combinan precisión, potencia, flexibilidad y seguridad para satisfacer las exigencias de la manufactura moderna, permitiendo la producción eficiente de piezas metálicas con bordes reforzados y acabados de alta calidad.
Las bordonadoras industriales hidráulicas son máquinas diseñadas para realizar el proceso de doblado o plegado de bordes en piezas metálicas con la aplicación de fuerza hidráulica controlada. Estas máquinas son fundamentales en la fabricación industrial porque permiten reforzar bordes, mejorar la rigidez estructural de las piezas, eliminar bordes cortantes y preparar componentes para su posterior ensamblaje o acabado.
El principio operativo se basa en un sistema hidráulico que suministra presión a través de cilindros o actuadores que mueven herramientas específicas para doblar la lámina metálica de forma precisa y uniforme. La fuerza hidráulica permite trabajar con una amplia variedad de materiales y espesores, adaptándose a las necesidades de cada proceso industrial.
Las bordonadoras hidráulicas industriales varían en tamaño, capacidad y configuración, desde modelos compactos para piezas pequeñas hasta equipos robustos capaces de procesar chapas de gran espesor y dimensiones considerables. Su diseño estructural garantiza estabilidad y rigidez, minimizando vibraciones y desplazamientos que puedan afectar la calidad del doblado.
Estos equipos suelen incorporar sistemas hidráulicos avanzados con bombas de caudal variable, válvulas proporcionales y acumuladores que regulan dinámicamente la presión y velocidad, optimizando el proceso y reduciendo el consumo energético. Los controles electrónicos, generalmente basados en PLC o CNC, permiten programar ciclos automáticos, almacenar configuraciones para diferentes piezas y supervisar variables en tiempo real.
La automatización juega un papel clave en las bordonadoras industriales hidráulicas, integrándose con sistemas de alimentación y descarga automática, robots manipuladores y estaciones de inspección, mejorando la productividad, la precisión y la seguridad operativa al reducir la intervención manual.
El mantenimiento preventivo es esencial para garantizar la fiabilidad y prolongar la vida útil de estas máquinas. Incluye la revisión periódica del sistema hidráulico, filtros, sellos, calibración de sensores y limpieza general del equipo.
En resumen, las bordonadoras industriales hidráulicas son herramientas versátiles, precisas y potentes que permiten conformar bordes metálicos con altos estándares de calidad, siendo indispensables en múltiples sectores industriales que requieren eficiencia y flexibilidad en sus procesos de fabricación. ¿Quieres que te describa modelos específicos o aplicaciones comunes?
Estas máquinas de bordonado hidráulicas destacan por su versatilidad para trabajar con diferentes tipos de metales y espesores, desde láminas finas hasta chapas gruesas, lo que las hace aptas para diversas industrias como la automotriz, construcción, electrodomésticos y fabricación de mobiliario metálico. La capacidad de regular con precisión la fuerza y velocidad hidráulica asegura bordes uniformes y sin defectos, evitando deformaciones o daños en las piezas.
El diseño robusto y estable minimiza vibraciones y desplazamientos durante el proceso, lo que contribuye a mantener la precisión dimensional y prolongar la vida útil del utillaje y la máquina. Además, los sistemas de guía y alineación garantizan el posicionamiento exacto del material y las herramientas de plegado, asegurando resultados repetibles y de alta calidad.
La integración de controles electrónicos avanzados permite programar y supervisar ciclos de trabajo, almacenar configuraciones específicas para distintos productos y ajustar parámetros en tiempo real, facilitando la operación y reduciendo tiempos de cambio. La automatización puede complementarse con sistemas de alimentación y descarga automáticos, robots manipuladores y estaciones de inspección, incrementando la eficiencia productiva y la seguridad laboral.
El mantenimiento adecuado, que incluye la revisión y cambio periódico del fluido hidráulico, limpieza y sustitución de filtros, inspección de sellos y calibración de sensores, es fundamental para preservar el rendimiento óptimo de los equipos y evitar paradas no planificadas.
Los avances tecnológicos han impulsado el desarrollo de sistemas electrohidráulicos que combinan la fuerza hidráulica con la precisión y rapidez de actuadores eléctricos, mejorando la eficiencia energética y el control del proceso. Asimismo, la adopción de fluidos hidráulicos ecológicos y sistemas de recuperación de energía contribuye a una producción más sostenible.
En conjunto, los equipos de bordonado hidráulicos son soluciones confiables, precisas y flexibles para la conformación de bordes metálicos, desempeñando un papel esencial en la fabricación moderna de productos metálicos con altos estándares de calidad y productividad.
Además, la incorporación de interfaces hombre-máquina (HMI) intuitivas y paneles táctiles en los equipos de bordonado hidráulicos facilita la programación y supervisión del proceso, permitiendo a los operadores configurar ciclos personalizados, monitorear variables en tiempo real y acceder a diagnósticos y alertas que mejoran la eficiencia operativa y reducen errores.
El uso de tecnologías de monitoreo avanzado, como sensores inteligentes y análisis de datos, permite implementar mantenimiento predictivo basado en el estado real del equipo, anticipando fallas y optimizando los intervalos de mantenimiento. Esto contribuye a maximizar la productividad y reducir costos operativos.
La modularidad en el diseño de estos equipos facilita su adaptación a diversas configuraciones de producción y su integración con otras etapas del proceso, como corte, estampado o ensamblaje, permitiendo crear líneas de fabricación flexibles y escalables que responden ágilmente a cambios en la demanda o el diseño del producto.
En términos de seguridad, los equipos cuentan con resguardos físicos, sensores de presencia, controles bimanuales y sistemas de parada de emergencia para proteger a los operarios y cumplir con normativas internacionales, garantizando un entorno de trabajo seguro.
Finalmente, la sostenibilidad es una prioridad creciente, impulsando el desarrollo de sistemas hidráulicos más eficientes y el uso de fluidos ecológicos que minimizan el impacto ambiental. El diseño de estos equipos busca reducir el consumo energético y facilitar procesos de reciclaje y reutilización de materiales.
En conjunto, los equipos de bordonado hidráulicos representan una solución tecnológica avanzada que combina precisión, potencia, flexibilidad y seguridad para satisfacer las exigencias de la manufactura moderna, permitiendo la producción eficiente de piezas metálicas con bordes reforzados y acabados de alta calidad.
Maquinaria hidráulica para bordonado
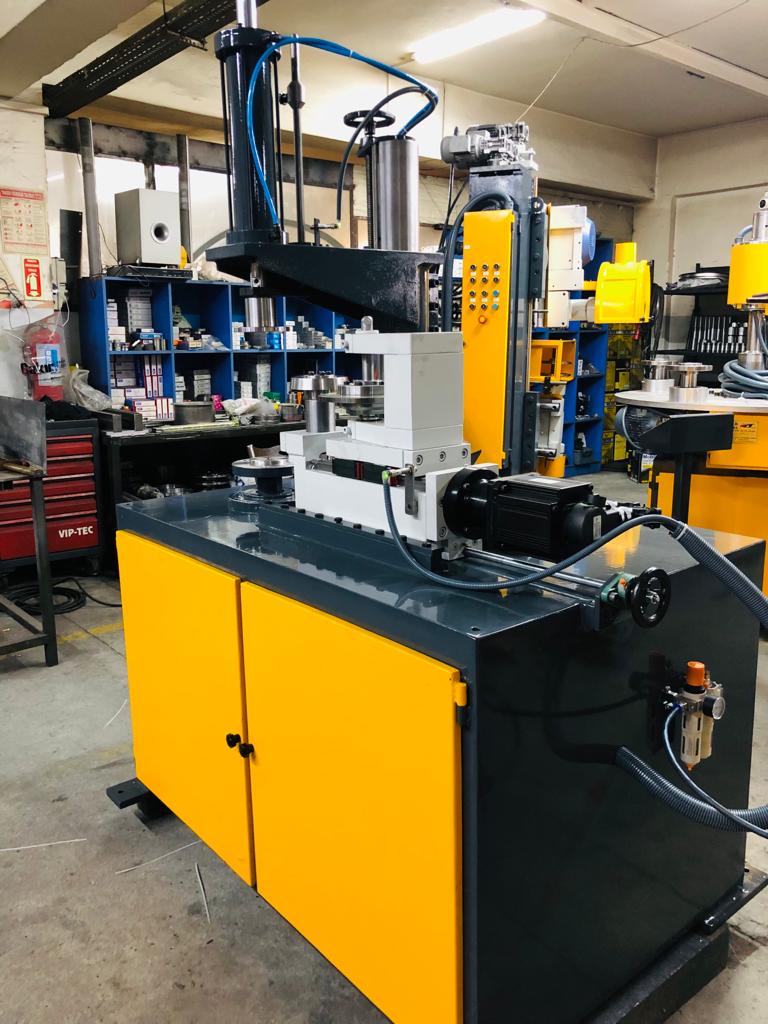
La maquinaria hidráulica para bordonado está especialmente diseñada para realizar el proceso de doblado o plegado de bordes en piezas metálicas utilizando sistemas hidráulicos que aplican fuerzas controladas y precisas. Este tipo de maquinaria es fundamental en la industria metalmecánica, ya que permite reforzar bordes, mejorar la rigidez estructural, eliminar bordes cortantes y preparar las piezas para su ensamblaje o acabado posterior.
El funcionamiento de esta maquinaria se basa en un sistema hidráulico compuesto por bombas, cilindros, válvulas y acumuladores que transmiten presión al fluido hidráulico, generando una fuerza constante y regulable sobre las herramientas de plegado o doblado. Gracias a este sistema, es posible trabajar con diferentes materiales y espesores, desde láminas finas hasta chapas gruesas, con alta precisión y repetibilidad.
Entre los principales tipos de maquinaria hidráulica para bordonado se encuentran las prensas hidráulicas de plegado, las dobladoras hidráulicas con cilindros múltiples, y los equipos integrados con controles electrónicos que permiten programar ciclos automáticos y ajustar parámetros como la presión, velocidad y ángulo de doblado. Esto facilita la adaptación a distintos diseños y procesos productivos.
La estructura de estas máquinas es robusta y está diseñada para garantizar estabilidad durante la operación, minimizando vibraciones y asegurando la repetibilidad del proceso. Los sistemas de guía y alineación precisos permiten posicionar correctamente el material y las herramientas, lo que contribuye a la calidad y uniformidad del bordonado.
La incorporación de controles PLC o CNC en la maquinaria hidráulica de bordonado permite una operación más eficiente y segura, con monitoreo en tiempo real de variables clave y la posibilidad de almacenar perfiles de trabajo para distintos productos. Esto reduce los tiempos de ajuste y aumenta la productividad.
Además, estos equipos pueden integrarse en líneas de producción automatizadas, incluyendo sistemas de alimentación y descarga automáticos, robots para manipulación de piezas y estaciones de inspección, lo que mejora la eficiencia y reduce la intervención manual.
El mantenimiento preventivo es esencial para prolongar la vida útil de la maquinaria hidráulica de bordonado, incluyendo la revisión del fluido hidráulico, limpieza y cambio de filtros, inspección de sellos y calibración de sensores y sistemas de control.
En resumen, la maquinaria hidráulica para bordonado es una herramienta clave en la fabricación de piezas metálicas, combinando potencia, precisión, flexibilidad y tecnología avanzada para asegurar la calidad y eficiencia en procesos industriales de doblado y plegado de bordes. ¿Quieres que te explique detalles técnicos específicos o aplicaciones comunes?
La maquinaria hidráulica para bordonado se adapta a una amplia variedad de metales y espesores, lo que la hace versátil para diferentes industrias, desde la automotriz y aeroespacial hasta la fabricación de electrodomésticos y mobiliario metálico. La capacidad de controlar con precisión la fuerza y velocidad hidráulica asegura que los bordes doblados sean uniformes, resistentes y libres de defectos como arrugas o deformaciones no deseadas.
El diseño robusto y estable de estas máquinas minimiza las vibraciones y desplazamientos durante la operación, manteniendo la precisión dimensional y prolongando la vida útil tanto del equipo como de las herramientas de plegado. Los sistemas de guía y posicionamiento garantizan que el material se coloque correctamente, lo que resulta en resultados repetibles y de alta calidad.
La integración de sistemas electrónicos avanzados, como PLCs y pantallas táctiles, facilita la programación y supervisión de los ciclos de trabajo. Esto permite almacenar configuraciones para diferentes piezas, realizar ajustes en tiempo real y acceder a diagnósticos que optimizan la operación y reducen errores humanos.
Además, la automatización puede incluir alimentación y descarga automática de piezas, así como la incorporación de robots manipuladores y estaciones de inspección, aumentando la eficiencia productiva y mejorando la seguridad al minimizar la intervención manual.
El mantenimiento regular es crucial para mantener el rendimiento óptimo de la maquinaria hidráulica para bordonado. Esto implica la revisión y sustitución del fluido hidráulico, limpieza y cambio de filtros, inspección de sellos y juntas, además de la calibración periódica de sensores y controles para asegurar la precisión del proceso.
Los avances tecnológicos han impulsado la incorporación de sistemas electrohidráulicos que combinan la potencia hidráulica con la precisión y rapidez de actuadores eléctricos, mejorando la eficiencia energética y el control del proceso. También se emplean fluidos hidráulicos ecológicos y sistemas de recuperación de energía para reducir el impacto ambiental.
En conjunto, la maquinaria hidráulica para bordonado ofrece una solución potente, precisa y flexible para la conformación de bordes metálicos, siendo esencial en la fabricación moderna de productos metálicos que requieren altos estándares de calidad, productividad y sostenibilidad.
Además, la evolución de la maquinaria hidráulica para bordonado ha llevado al desarrollo de interfaces hombre-máquina (HMI) más intuitivas y sistemas de control basados en software avanzado, que facilitan la configuración, monitoreo y optimización del proceso. Esto permite a los operadores ajustar parámetros como presión, velocidad y ángulo de plegado de forma sencilla, almacenando perfiles para diferentes piezas y materiales, lo que reduce significativamente los tiempos de cambio y mejora la consistencia en la producción.
El monitoreo en tiempo real mediante sensores inteligentes y análisis de datos posibilita la implementación de mantenimiento predictivo, anticipando posibles fallas antes de que ocurran y programando intervenciones en momentos óptimos, lo que reduce costos y evita paradas no planificadas que afectan la productividad.
La modularidad y escalabilidad de la maquinaria permiten adaptarla a distintas capacidades y requerimientos productivos, facilitando la integración con otras etapas del proceso como corte, estampado o ensamblaje, creando líneas de producción flexibles y eficientes que pueden responder rápidamente a cambios en la demanda o en el diseño de los productos.
En cuanto a la seguridad, estos equipos incorporan múltiples sistemas de protección, incluyendo barreras físicas, sensores de presencia, controles bimanuales y dispositivos de parada de emergencia, garantizando un entorno de trabajo seguro y cumpliendo con normativas internacionales.
Por último, la creciente preocupación por la sostenibilidad impulsa el diseño de sistemas hidráulicos más eficientes, el uso de fluidos biodegradables y tecnologías que minimizan el consumo energético, contribuyendo a una producción más responsable con el medio ambiente.
En conjunto, la maquinaria hidráulica para bordonado representa una solución tecnológica avanzada que combina potencia, precisión, flexibilidad y seguridad para satisfacer las exigencias de la industria moderna, facilitando la fabricación eficiente de piezas metálicas con bordes reforzados y acabados de alta calidad.
La maquinaria de transformación de chapa metálica engloba un conjunto de equipos industriales diseñados para modificar la forma, tamaño y propiedades de las láminas metálicas mediante procesos como corte, doblado, embutido, estampado, conformado y soldadura. Estos procesos son fundamentales en la fabricación de piezas y componentes para sectores como la automoción, construcción, electrodomésticos, aeroespacial, mobiliario metálico y maquinaria industrial.
Entre las principales máquinas para la transformación de chapa metálica destacan las prensas hidráulicas y mecánicas, que permiten aplicar fuerzas controladas para doblar, embutir o estampar la chapa con alta precisión y repetibilidad. También se utilizan plegadoras, guillotinas, cizallas y punzonadoras para cortar y conformar las láminas según las especificaciones del diseño.
Las máquinas hidráulicas de conformado y doblado utilizan sistemas de presión hidráulica que permiten trabajar con materiales y espesores variados, garantizando uniformidad y calidad en las piezas producidas. La capacidad de ajustar la fuerza y velocidad facilita la adaptación a diferentes procesos y productos.
Los sistemas de corte incluyen guillotinas, cizallas y máquinas de corte por láser o plasma, que permiten obtener piezas con bordes precisos y acabados limpios, optimizando el aprovechamiento del material y reduciendo desperdicios. El corte por láser, en particular, ofrece alta precisión y versatilidad para formas complejas.
El embutido y estampado son procesos realizados con prensas y matrices especializadas que transforman la chapa plana en piezas tridimensionales con geometrías complejas, empleando fuerzas controladas para evitar defectos como arrugas o fisuras.
La automatización y digitalización han avanzado significativamente en esta área, integrando controles electrónicos, PLCs, CNCs y sistemas de monitoreo en tiempo real que mejoran la precisión, repetibilidad y eficiencia productiva. Esto permite programar ciclos, almacenar configuraciones, detectar anomalías y optimizar el mantenimiento.
La integración de robots y sistemas de manipulación automática facilita la alimentación, traslado y descarga de piezas, aumentando la seguridad y reduciendo tiempos muertos en la producción.
El mantenimiento preventivo y predictivo es clave para asegurar la disponibilidad y buen funcionamiento de la maquinaria, involucrando la revisión de sistemas hidráulicos, mecánicos y electrónicos, además de la limpieza y calibración periódica.
En resumen, la maquinaria de transformación de chapa metálica es esencial para la fabricación moderna, ofreciendo una combinación de fuerza, precisión, flexibilidad y tecnología avanzada que permite convertir materiales planos en componentes metálicos de alta calidad y complejidad para múltiples aplicaciones industriales. ¿Quieres que te explique algún tipo de máquina en particular o proceso de transformación?
La maquinaria de transformación de chapa metálica abarca una amplia variedad de equipos diseñados para modificar la forma, dimensiones y propiedades de láminas metálicas mediante procesos como corte, doblado, embutido, estampado y conformado. Estas máquinas son esenciales en sectores industriales diversos, permitiendo fabricar piezas con alta precisión, repetibilidad y eficiencia.
Los sistemas hidráulicos desempeñan un papel fundamental en muchas de estas máquinas, ofreciendo la fuerza y control necesarios para procesos exigentes como el embutido profundo o el doblado de chapas gruesas. La capacidad de ajustar parámetros como presión, velocidad y recorrido facilita la adaptación a distintos materiales y diseños, mejorando la calidad y reduciendo desperdicios.
Los avances tecnológicos han incorporado controles electrónicos avanzados, como PLC y CNC, que permiten programar ciclos automáticos, supervisar variables en tiempo real y almacenar configuraciones para diferentes productos. Esto incrementa la productividad, minimiza errores y facilita la integración en líneas de producción automatizadas.
Las tecnologías de corte, incluyendo láser, plasma y cizallas, permiten obtener piezas con acabados precisos y formas complejas, optimizando el aprovechamiento del material. Por su parte, las prensas y plegadoras hidráulicas aseguran doblados y conformados uniformes y resistentes.
La incorporación de sistemas de automatización y robótica para la manipulación y transporte de piezas contribuye a mejorar la seguridad laboral y la eficiencia, permitiendo ciclos de trabajo más rápidos y consistentes.
El mantenimiento preventivo y predictivo basado en el monitoreo constante de la maquinaria es vital para garantizar su buen funcionamiento, evitando fallas inesperadas y prolongando la vida útil de los equipos.
En conjunto, la maquinaria de transformación de chapa metálica combina potencia, precisión, flexibilidad y tecnología avanzada para satisfacer las demandas dinámicas de la industria moderna, facilitando la producción eficiente y de alta calidad de componentes metálicos complejos y diversos.
Además, la maquinaria de transformación de chapa metálica ha evolucionado incorporando tecnologías de Industria 4.0, que permiten la interconexión de equipos, recopilación y análisis de datos en tiempo real, y la implementación de mantenimiento predictivo mediante inteligencia artificial y sensores inteligentes. Esto optimiza la productividad, reduce tiempos de inactividad y mejora la calidad del producto final.
La modularidad y flexibilidad en el diseño de estas máquinas facilitan su adaptación a diferentes volúmenes y tipos de producción, permitiendo cambios rápidos entre productos y configuraciones. Esto es especialmente importante en mercados que demandan variedad y rapidez sin sacrificar precisión ni eficiencia.
La sostenibilidad también juega un papel creciente, con el desarrollo de sistemas más eficientes energéticamente, el uso de fluidos hidráulicos ecológicos y técnicas que minimizan el desperdicio de material y el impacto ambiental.
Los operadores y técnicos requieren capacitación continua para manejar estas tecnologías avanzadas, asegurando un uso óptimo de las máquinas y el cumplimiento de normativas de seguridad y calidad.
En resumen, la maquinaria de transformación de chapa metálica representa una combinación de innovación tecnológica, robustez y versatilidad que permite a la industria manufacturera responder a los retos actuales de productividad, calidad y sostenibilidad, facilitando la fabricación de componentes metálicos complejos y de alta precisión.
Equipos de fabricación de piezas de chapa
Los equipos de fabricación de piezas de chapa metálica son máquinas especializadas diseñadas para transformar láminas planas en componentes con formas, tamaños y propiedades específicas, a través de procesos como corte, doblado, embutido, estampado, punzonado y conformado. Estos equipos son esenciales en industrias como la automotriz, aeroespacial, electrodomésticos, construcción y mobiliario metálico, donde la precisión y la eficiencia en la fabricación de piezas es fundamental.
Entre los principales equipos para la fabricación de piezas de chapa destacan las prensas hidráulicas y mecánicas, que aplican fuerzas controladas para moldear la chapa según el diseño requerido. Estas prensas pueden estar equipadas con matrices y troqueles específicos para cada pieza, permitiendo procesos repetitivos y de alta productividad.
Las plegadoras o dobladoras permiten realizar ángulos y formas precisas en la chapa, usando sistemas hidráulicos o mecánicos que aseguran la uniformidad y calidad del doblado. Las dobladoras CNC ofrecen control automatizado, facilitando la producción de piezas complejas con gran exactitud.
Las máquinas de corte, como guillotinas, cizallas, láser, plasma o chorro de agua, permiten obtener piezas con formas y dimensiones específicas, garantizando bordes limpios y reduciendo el desperdicio de material. La tecnología láser, en particular, ofrece alta precisión y versatilidad para cortes complejos y delicados.
El embutido y estampado se realizan con prensas equipadas con matrices especiales que transforman la chapa plana en piezas tridimensionales, utilizando fuerzas adecuadas para evitar defectos como arrugas o fisuras. Este proceso es común en la fabricación de carcasas, recipientes y partes estructurales.
La automatización de estos equipos, mediante el uso de PLC, CNC y sistemas robotizados para alimentación, manipulación y descarga de piezas, mejora la eficiencia, reduce errores y aumenta la seguridad laboral. Además, los sistemas de monitoreo en tiempo real facilitan el mantenimiento predictivo y el control de calidad durante la producción.
El mantenimiento adecuado y programado es vital para garantizar la disponibilidad y el rendimiento óptimo de estos equipos, incluyendo la revisión de componentes hidráulicos, mecánicos y electrónicos, así como la limpieza y calibración periódica.
En conjunto, los equipos de fabricación de piezas de chapa metálica combinan potencia, precisión y tecnología avanzada para ofrecer soluciones flexibles y eficientes, permitiendo la producción en serie de componentes metálicos con altos estándares de calidad y complejidad. ¿Quieres que te detalle algún tipo específico de equipo o proceso?
Los equipos de fabricación de piezas de chapa metálica son fundamentales para transformar láminas planas en componentes con formas y características específicas mediante procesos como corte, doblado, embutido, estampado y conformado. Estas máquinas están diseñadas para trabajar con una amplia variedad de materiales y espesores, adaptándose a las exigencias de diferentes industrias como la automotriz, aeroespacial, electrodomésticos y construcción.
Las prensas hidráulicas y mecánicas son esenciales en este tipo de fabricación, ya que aplican fuerzas controladas para moldear la chapa con precisión, utilizando matrices y troqueles específicos que permiten procesos repetitivos y de alta productividad. Las plegadoras, tanto hidráulicas como CNC, facilitan la creación de ángulos y formas exactas, asegurando uniformidad en cada pieza producida.
Para el corte, se emplean guillotinas, cizallas, máquinas de corte por láser, plasma o chorro de agua, que garantizan bordes limpios y reducen el desperdicio de material. La tecnología láser destaca por su precisión y capacidad para realizar cortes complejos en diferentes tipos de chapa.
El embutido y estampado se realizan mediante prensas equipadas con matrices especializadas, transformando la chapa plana en piezas tridimensionales sin defectos como arrugas o fisuras, procesos comúnmente usados en la fabricación de carcasas, recipientes y piezas estructurales.
La automatización, a través de PLC, CNC y sistemas robotizados para la alimentación, manipulación y descarga de piezas, incrementa la eficiencia, reduce errores y mejora la seguridad laboral. Además, el monitoreo en tiempo real permite llevar a cabo mantenimiento predictivo y controlar la calidad durante la producción.
El mantenimiento periódico de estos equipos, incluyendo la revisión de sistemas hidráulicos, mecánicos y electrónicos, así como la limpieza y calibración, es vital para asegurar su rendimiento y longevidad.
En conjunto, los equipos para fabricar piezas de chapa metálica combinan potencia, precisión y tecnología avanzada, proporcionando soluciones flexibles y eficientes para la producción en serie de componentes metálicos complejos y de alta calidad.
Además, la incorporación de tecnologías digitales y sistemas de control avanzados ha revolucionado la fabricación de piezas de chapa metálica. Los controles CNC y PLC permiten programar con precisión cada etapa del proceso, desde el corte hasta el doblado y estampado, garantizando reproducibilidad y minimizando errores humanos. Estas tecnologías facilitan también la rápida adaptación a nuevos diseños y la producción de lotes pequeños o personalizados con la misma eficiencia que las series grandes.
La interconexión de máquinas y la implementación de soluciones Industria 4.0 permiten la recopilación y análisis de datos en tiempo real, lo que ayuda a optimizar parámetros de producción, mejorar la calidad y anticipar posibles fallos mediante mantenimiento predictivo. Esto se traduce en una mayor disponibilidad de los equipos y una reducción de los costos operativos.
La modularidad y flexibilidad en el diseño de los equipos posibilitan su integración en líneas de producción automatizadas que combinan corte, conformado, soldadura y acabado, ofreciendo soluciones completas y adaptables a diferentes sectores y requerimientos productivos.
Los avances en robótica y sistemas de manipulación automatizada han mejorado la ergonomía y seguridad en las plantas, reduciendo la intervención manual en tareas repetitivas o peligrosas y aumentando la productividad.
Por último, la sostenibilidad es un aspecto cada vez más importante en la fabricación de piezas de chapa metálica. Se desarrollan máquinas y procesos que optimizan el consumo energético, reducen el desperdicio de material y utilizan fluidos y lubricantes ecológicos, contribuyendo a una producción más responsable con el medio ambiente.
En resumen, los equipos para fabricación de piezas de chapa metálica combinan innovación tecnológica, precisión, potencia y flexibilidad, ofreciendo soluciones eficientes y de alta calidad para responder a las demandas dinámicas de la industria moderna.
Máquinas para moldear chapa
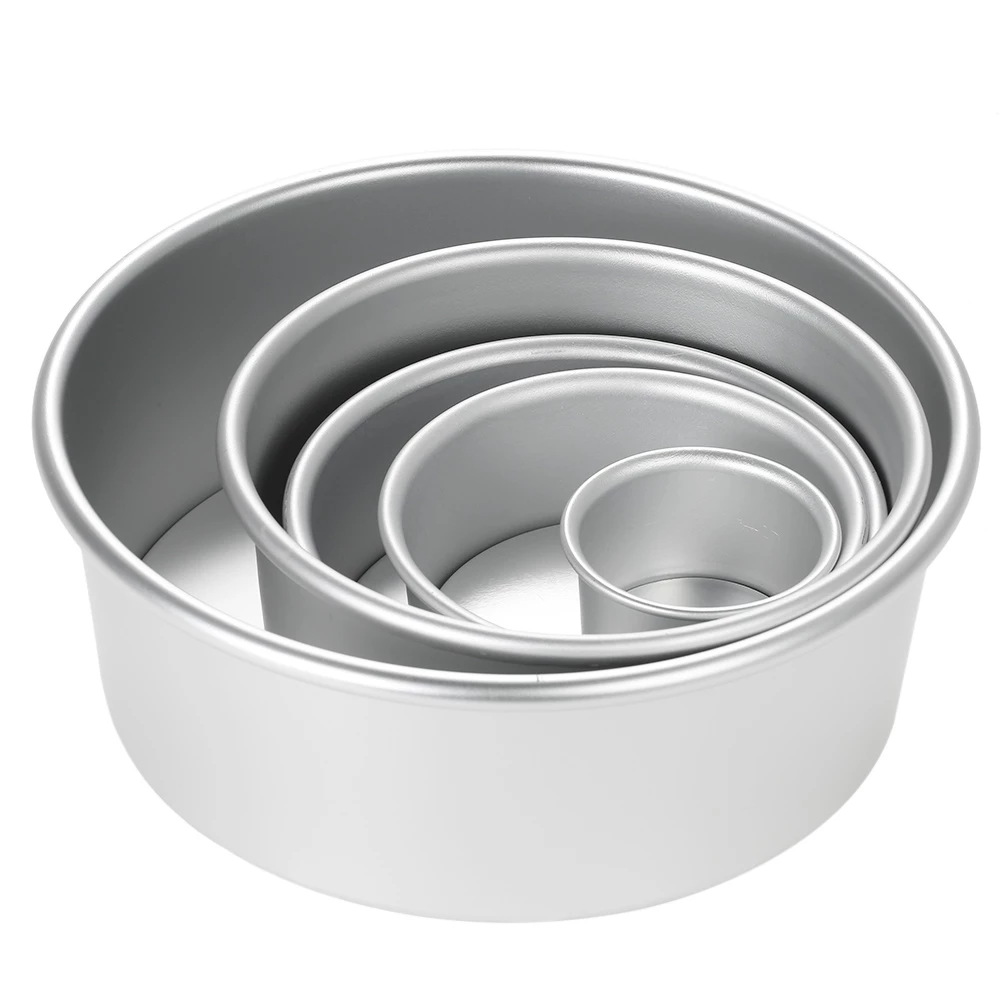
Las máquinas para moldear chapa son equipos industriales diseñados para dar forma a láminas metálicas mediante procesos que incluyen doblado, embutido, estampado, conformado y troquelado. Estas máquinas permiten transformar chapa plana en piezas tridimensionales con geometrías complejas, necesarias en sectores como la automoción, aeroespacial, construcción, fabricación de electrodomésticos y mobiliario metálico.
Entre los tipos más comunes de máquinas para moldear chapa se encuentran las prensas hidráulicas y mecánicas, que aplican fuerzas controladas para moldear el material mediante el uso de matrices y troqueles específicos. Las prensas hidráulicas se destacan por su capacidad para manejar grandes espesores y producir embutidos profundos con precisión, mientras que las mecánicas son más rápidas en ciclos repetitivos y aptas para series largas.
Las plegadoras o dobladoras permiten realizar ángulos y curvas en la chapa con alta precisión, utilizando sistemas hidráulicos, eléctricos o mecánicos. Las dobladoras CNC añaden automatización y control digital, facilitando la producción de piezas complejas con gran exactitud y rapidez.
El embutido es un proceso clave para moldear chapa en formas huecas o profundas, realizado con prensas y matrices que moldean el metal sin causar defectos como arrugas o fisuras. Este proceso es fundamental para la fabricación de carcasas, recipientes y componentes estructurales.
Las máquinas de estampado utilizan matrices que imprimen formas, relieves o perforaciones en la chapa, combinando rapidez y precisión para la producción en masa. Los troquelados permiten cortar o perforar la chapa con alta repetibilidad, esenciales para piezas que requieren orificios o formas específicas.
La incorporación de controles electrónicos, sistemas CNC y automatización ha mejorado la precisión, repetibilidad y eficiencia de estas máquinas, permitiendo programar ciclos de trabajo, ajustar parámetros y monitorear el proceso en tiempo real.
La integración con sistemas robotizados y de manipulación automática optimiza la productividad y seguridad, facilitando la alimentación, transporte y descarga de piezas durante el moldeado.
El mantenimiento preventivo es fundamental para garantizar la durabilidad y correcto funcionamiento de las máquinas para moldear chapa, incluyendo revisión de sistemas hidráulicos, eléctricos y mecánicos, así como calibración y limpieza de componentes.
En conjunto, estas máquinas son herramientas esenciales para la fabricación moderna de piezas metálicas, combinando fuerza, precisión y tecnología avanzada para producir componentes con alta calidad y complejidad. ¿Quieres que te detalle algún tipo específico de máquina o proceso de moldeado?
Las máquinas para moldear chapa son fundamentales en la industria metalmecánica, ya que permiten transformar láminas metálicas planas en piezas con formas complejas y funcionales mediante procesos como doblado, embutido, estampado y troquelado. Estas máquinas están diseñadas para trabajar con diversos tipos de materiales y espesores, adaptándose a las necesidades específicas de cada aplicación industrial.
Las prensas hidráulicas ofrecen una fuerza controlada y constante, ideal para embutidos profundos y conformados que requieren alta precisión y repetibilidad. Su capacidad para ajustar presión y velocidad permite trabajar con materiales delicados sin dañarlos, además de gestionar espesores variados. Por otro lado, las prensas mecánicas son más adecuadas para ciclos rápidos y producción en serie, brindando eficiencia en piezas de geometrías menos complejas.
Las plegadoras y dobladoras, tanto hidráulicas como CNC, facilitan la formación de ángulos y curvas precisas en la chapa. Las versiones CNC permiten programar y automatizar los procesos, aumentando la velocidad y exactitud, así como la posibilidad de producir piezas complejas y personalizadas con rapidez.
El embutido es un proceso clave para moldear chapa en formas tridimensionales huecas o profundas, realizado con matrices especializadas que evitan defectos como arrugas o fisuras. Este método es común en la fabricación de carcasas, recipientes y piezas estructurales que requieren resistencia y acabado estético.
El estampado y troquelado permiten crear relieves, perforaciones y cortes precisos en la chapa, siendo procesos altamente repetitivos y eficientes para producción en masa. Estas máquinas suelen integrarse con sistemas automáticos para alimentar y manipular las piezas, aumentando la productividad y seguridad operativa.
Los avances tecnológicos han impulsado la incorporación de controles electrónicos, sistemas CNC y automatización, que facilitan la programación, monitoreo y ajuste de parámetros en tiempo real, garantizando consistencia y calidad en la producción.
La integración con robótica y sistemas de manipulación automatizada mejora la ergonomía y seguridad, reduce el trabajo manual repetitivo y permite ciclos de trabajo más rápidos y confiables.
El mantenimiento preventivo y predictivo es esencial para asegurar el funcionamiento óptimo de estas máquinas, abarcando revisiones de componentes hidráulicos, mecánicos y electrónicos, limpieza, lubricación y calibración periódica.
En resumen, las máquinas para moldear chapa combinan potencia, precisión, flexibilidad y tecnología avanzada para satisfacer las demandas de la manufactura moderna, permitiendo fabricar piezas metálicas complejas y de alta calidad en diversos sectores industriales.
Además, la constante innovación en máquinas para moldear chapa ha llevado a la incorporación de tecnologías digitales y sistemas inteligentes que optimizan el proceso de fabricación. Las interfaces hombre-máquina (HMI) con pantallas táctiles permiten una operación más intuitiva, facilitando la programación de ciclos, ajustes finos y acceso a diagnósticos en tiempo real.
El uso de sensores avanzados y sistemas de monitoreo continuo posibilita la implementación de mantenimiento predictivo, detectando desgastes o fallas potenciales antes de que afecten la producción. Esto reduce costos por paradas imprevistas y prolonga la vida útil del equipo.
La modularidad y adaptabilidad de estas máquinas facilitan su integración en líneas de producción flexibles y automatizadas, capaces de responder rápidamente a cambios en diseño, volumen o tipo de pieza sin comprometer la eficiencia ni calidad.
En términos de seguridad, estas máquinas incorporan múltiples dispositivos de protección, como resguardos, sensores de presencia, controles bimanuales y sistemas de parada de emergencia, garantizando un entorno de trabajo seguro y cumplimiento de normativas internacionales.
El compromiso con la sostenibilidad ha impulsado el desarrollo de sistemas hidráulicos y eléctricos más eficientes, el uso de fluidos ecológicos y tecnologías que minimizan el consumo energético y el desperdicio de material, contribuyendo a una producción más responsable con el medio ambiente.
En conjunto, las máquinas para moldear chapa representan la combinación perfecta entre robustez, precisión, tecnología avanzada y sostenibilidad, siendo piezas clave para la competitividad y calidad en la fabricación industrial moderna.
La maquinaria especializada en el conformado de chapa está diseñada para transformar láminas metálicas planas en piezas con formas y características específicas mediante procesos como doblado, embutido, estampado, perfilado y troquelado. Esta maquinaria es fundamental en industrias como la automotriz, aeroespacial, construcción, fabricación de electrodomésticos y mobiliario metálico, donde la precisión y calidad en el conformado de piezas metálicas son esenciales.
Entre las principales máquinas especializadas en conformado de chapa se encuentran las prensas hidráulicas y mecánicas, que aplican fuerzas controladas para moldear la chapa mediante matrices y troqueles específicos. Las prensas hidráulicas destacan por su capacidad para manejar piezas con espesores variables y realizar embutidos profundos, mientras que las prensas mecánicas son más adecuadas para ciclos rápidos y producción en serie.
Las plegadoras o dobladoras permiten dar forma a la chapa mediante el doblado en ángulos precisos, utilizando sistemas hidráulicos, eléctricos o mecánicos. Las versiones CNC automatizadas facilitan la programación y control digital, lo que permite fabricar piezas complejas con alta repetibilidad y exactitud.
El embutido, que consiste en moldear la chapa en formas tridimensionales, se realiza mediante prensas equipadas con matrices especializadas que evitan defectos como arrugas o fisuras. Este proceso es común en la fabricación de carcasas, recipientes y componentes estructurales.
El estampado permite imprimir formas, relieves o perforaciones en la chapa, combinando rapidez y precisión para la producción masiva. El perfilado y troquelado permiten cortar y conformar bordes y formas específicas, esenciales para piezas que requieren alta exactitud.
La incorporación de tecnologías avanzadas como controles CNC, PLC y sistemas de automatización mejora la eficiencia, precisión y seguridad en el conformado de chapa, permitiendo la programación de ciclos, ajustes en tiempo real y monitoreo constante del proceso.
Además, la integración con sistemas robotizados para la alimentación, manipulación y descarga de piezas optimiza la productividad y reduce la intervención manual, mejorando la ergonomía y seguridad laboral.
El mantenimiento preventivo y predictivo es fundamental para garantizar la durabilidad y buen funcionamiento de la maquinaria especializada, incluyendo la revisión de sistemas hidráulicos, mecánicos y electrónicos, así como la limpieza y calibración periódica.
En conjunto, la maquinaria especializada en conformado de chapa ofrece soluciones potentes, precisas y flexibles que permiten fabricar piezas metálicas de alta calidad y complejidad, respondiendo a las demandas dinámicas de la industria moderna. ¿Quieres que te detalle algún equipo o proceso específico?
Las máquinas para moldear chapa son esenciales en la industria metalúrgica para transformar láminas planas en piezas con formas y funciones específicas. Utilizan procesos como doblado, embutido, estampado y troquelado, adaptándose a diferentes materiales y espesores según los requerimientos del producto final. Las prensas hidráulicas permiten aplicar fuerzas ajustables y constantes para conformados profundos y precisos, mientras que las prensas mecánicas ofrecen ciclos rápidos para producción en serie. Las plegadoras, manuales o CNC, facilitan la creación de ángulos y curvas con alta exactitud, mientras que el embutido moldea formas tridimensionales evitando defectos como arrugas o fisuras. El estampado y troquelado permiten agregar relieves, perforaciones o cortes con repetitividad y rapidez. La integración de sistemas electrónicos y automatización mediante PLC, CNC y robots mejora la precisión, productividad y seguridad, además de facilitar el monitoreo y control en tiempo real. El mantenimiento preventivo y predictivo asegura la durabilidad y funcionamiento óptimo de los equipos. En conjunto, estas máquinas combinan potencia, precisión y tecnología avanzada para fabricar piezas metálicas complejas y de alta calidad, respondiendo a las exigencias de la manufactura moderna.
Además, la evolución tecnológica ha permitido que estas máquinas incorporen interfaces digitales intuitivas, que facilitan la programación y supervisión de los procesos, permitiendo ajustes precisos de parámetros como presión, velocidad y ángulo de doblado o estampado. Esto agiliza los cambios de producción y mejora la consistencia en la calidad de las piezas.
La incorporación de sensores y sistemas de monitoreo continuo permite realizar mantenimiento predictivo, anticipando fallos antes de que ocurran y optimizando los tiempos de servicio, lo que reduce costos y evita paros inesperados en la producción. La modularidad de las máquinas facilita su adaptación a diferentes volúmenes y tipos de producción, permitiendo líneas flexibles y escalables.
En cuanto a la seguridad, estas máquinas están equipadas con resguardos, sistemas de detección y controles de emergencia que garantizan un ambiente de trabajo seguro para los operarios, cumpliendo con las normativas internacionales más exigentes.
Finalmente, la sostenibilidad ha cobrado gran relevancia, impulsando el diseño de sistemas hidráulicos y eléctricos más eficientes, el uso de fluidos ecológicos y técnicas que minimizan el desperdicio de material y el consumo energético. Esto contribuye a una fabricación más responsable y alineada con los objetivos ambientales actuales.
En conjunto, las máquinas para moldear chapa representan un equilibrio entre robustez, precisión, innovación tecnológica y compromiso con la sostenibilidad, constituyéndose en pilares fundamentales para la fabricación industrial moderna y competitiva.
La evolución de las máquinas para moldear chapa ha estado marcada por un avance constante en tecnologías que buscan optimizar la eficiencia, precisión y flexibilidad de los procesos de fabricación. En este sentido, la integración de sistemas digitales y automatización ha transformado radicalmente la manera en que se diseñan, operan y mantienen estos equipos, convirtiéndolos en piezas clave dentro de la industria manufacturera moderna.
Una de las mejoras más significativas es la implementación de controles CNC (Control Numérico por Computadora) y PLC (Controlador Lógico Programable), que permiten la programación precisa y repetible de los movimientos y fuerzas aplicadas durante el moldeado. Esto no solo incrementa la calidad y uniformidad de las piezas producidas, sino que también reduce considerablemente los tiempos de ajuste entre diferentes series de producción. Gracias a estas tecnologías, los operadores pueden modificar fácilmente parámetros como la velocidad de plegado, el ángulo de doblado, la presión aplicada o la profundidad de embutido, ajustándose rápidamente a las especificaciones de cada pieza sin la necesidad de cambios mecánicos complejos.
Los sistemas de interfaz hombre-máquina (HMI) modernos, con pantallas táctiles y menús intuitivos, facilitan la interacción entre el operario y la máquina, permitiendo una supervisión constante del proceso, así como diagnósticos y alertas tempranas en caso de anomalías. Esto contribuye a un mejor control de calidad y a la reducción de errores humanos, factores clave para la producción en masa con altos estándares.
Además, el desarrollo de sensores inteligentes y sistemas de monitoreo en tiempo real ha abierto la puerta al mantenimiento predictivo, una estrategia que se basa en la recopilación y análisis continuo de datos operativos para anticipar y prevenir fallos antes de que ocurran. Esta modalidad de mantenimiento permite optimizar los intervalos de servicio, reducir costos y evitar paradas imprevistas que pueden impactar negativamente en la productividad y la rentabilidad.
La modularidad y flexibilidad en el diseño de estas máquinas permiten su rápida adaptación a diferentes tamaños y formas de piezas, así como la integración con otras etapas del proceso productivo, como corte, soldadura o acabado superficial. Esta capacidad facilita la creación de líneas de producción automatizadas y configurables que responden con agilidad a cambios en la demanda o en el diseño del producto final, un aspecto fundamental en mercados donde la personalización y la rapidez son cada vez más valoradas.
En el ámbito de la seguridad, las máquinas para moldear chapa modernas incorporan múltiples dispositivos de protección, desde resguardos físicos y barreras ópticas hasta sistemas de parada de emergencia y controles bimanuales, garantizando un entorno de trabajo seguro y conforme a normativas internacionales. La automatización reduce la necesidad de intervención manual en operaciones peligrosas, minimizando riesgos y mejorando las condiciones laborales.
Por otro lado, la sostenibilidad es un pilar cada vez más relevante en el desarrollo de estas máquinas. Se han implementado sistemas hidráulicos y eléctricos con mayor eficiencia energética, el uso de fluidos hidráulicos biodegradables y tecnologías que permiten reducir el consumo de energía y minimizar el desperdicio de material durante el proceso de conformado. Estas iniciativas contribuyen a que la fabricación industrial sea más respetuosa con el medio ambiente y alineada con los objetivos globales de desarrollo sostenible.
Finalmente, la capacitación continua del personal que opera y mantiene estas máquinas es esencial para aprovechar al máximo sus capacidades tecnológicas y asegurar un funcionamiento óptimo. La combinación de tecnología avanzada con talento humano capacitado es la base para alcanzar altos niveles de productividad, calidad y competitividad en la industria metalúrgica actual.
En resumen, las máquinas para moldear chapa representan una convergencia de robustez mecánica, precisión tecnológica, innovación digital y compromiso ambiental, configurándose como herramientas indispensables para la fabricación eficiente y de alta calidad de piezas metálicas en múltiples sectores industriales. Su evolución constante responde a las demandas dinámicas del mercado, facilitando la producción flexible, segura y sostenible que caracteriza a la industria moderna.
Los equipos de manufactura para chapa metálica comprenden una amplia gama de máquinas y sistemas diseñados para procesar láminas metálicas mediante diversos métodos que transforman la materia prima en componentes funcionales y de alta calidad. Estos equipos son esenciales en múltiples sectores industriales, incluyendo la automoción, aeroespacial, construcción, electrodomésticos, mobiliario metálico y maquinaria pesada, donde la precisión, eficiencia y versatilidad en el manejo de la chapa son fundamentales.
Dentro de estos equipos se encuentran las prensas hidráulicas y mecánicas, que constituyen el núcleo de los procesos de conformado, embutido, estampado y troquelado. Las prensas hidráulicas son particularmente valiosas por su capacidad para aplicar fuerzas ajustables y constantes, facilitando el moldeado de piezas con geometrías complejas y espesores variados, manteniendo una alta repetibilidad y calidad en la producción. Por su parte, las prensas mecánicas, aunque ofrecen ciclos más rápidos, son preferidas para series largas y procesos donde la rapidez es prioritaria.
Las dobladoras o plegadoras hidráulicas y CNC permiten realizar doblados precisos y consistentes en las láminas metálicas, generando ángulos y curvas de acuerdo con especificaciones exactas. Las versiones controladas por CNC añaden una capa de automatización que facilita la programación y ejecución de secuencias complejas, reduciendo errores y aumentando la productividad.
Los sistemas de corte incluyen guillotinas, cizallas, máquinas de corte láser, plasma y chorro de agua, cada una con características específicas que permiten obtener piezas con acabados limpios, formas complejas y mínimos desperdicios. El corte láser, en particular, es altamente valorado por su precisión y capacidad para trabajar con diferentes tipos de metales y espesores sin contacto físico, lo que minimiza la deformación.
Las máquinas de embutido y estampado emplean matrices y troqueles especializados para transformar la chapa plana en piezas tridimensionales, con procesos que requieren un control cuidadoso de la fuerza y velocidad para evitar defectos como arrugas, fisuras o deformaciones indeseadas. Estas operaciones son esenciales para la fabricación de carcasas, recipientes y componentes estructurales.
La automatización y robotización han revolucionado la manufactura de chapa metálica, integrando sistemas que permiten la alimentación, manipulación y descarga automática de piezas, así como inspección y control de calidad en línea. Esto mejora la seguridad, reduce el trabajo manual repetitivo y eleva la eficiencia productiva.
Los sistemas de control electrónico, incluyendo PLCs, CNCs y software avanzado, facilitan la programación, monitoreo y optimización de los procesos, permitiendo ajustar parámetros en tiempo real, almacenar configuraciones para diferentes productos y generar reportes detallados que apoyan la gestión de calidad.
El mantenimiento preventivo y predictivo es una práctica imprescindible para preservar la operatividad y longevidad de los equipos, involucrando la revisión y conservación de sistemas hidráulicos, mecánicos, eléctricos y electrónicos, además de la limpieza y calibración periódica.
En conjunto, los equipos de manufactura para chapa metálica combinan potencia, precisión, flexibilidad y tecnología avanzada, proporcionando soluciones integrales para la producción eficiente de piezas metálicas complejas y de alta calidad, adaptándose a las necesidades dinámicas y exigentes de la industria moderna. ¿Deseas que te describa algún equipo o proceso en particular?
Los equipos para la fabricación de piezas de chapa metálica abarcan una amplia gama de tecnologías y sistemas diseñados para transformar láminas planas en componentes tridimensionales con formas y dimensiones específicas. Estos equipos incluyen prensas hidráulicas y mecánicas, plegadoras, cortadoras láser y de plasma, punzonadoras, máquinas de embutido y estampado, así como sistemas automatizados de manipulación y control. Las prensas hidráulicas son especialmente valoradas por su capacidad para aplicar fuerzas precisas y constantes, ideales para procesos de embutido profundo y conformado complejo, mientras que las prensas mecánicas ofrecen velocidad y eficiencia para producciones en serie de piezas con geometrías menos complicadas. Las plegadoras y dobladoras permiten formar ángulos exactos y curvaturas en la chapa, con modelos CNC que facilitan la automatización y repetibilidad, reduciendo tiempos de configuración y errores. El corte mediante láser, plasma o chorro de agua ofrece alta precisión y versatilidad para formas complejas, minimizando desperdicios y mejorando la calidad del borde. El embutido y estampado utilizan matrices especializadas para dar forma a la chapa, controlando cuidadosamente la presión y velocidad para evitar defectos como arrugas o fisuras, esenciales en la fabricación de carcasas, recipientes y piezas estructurales. La integración de sistemas electrónicos avanzados, como PLC y CNC, permite la programación y monitoreo en tiempo real, optimizando el proceso y facilitando ajustes precisos. Además, la automatización con robots y sistemas de manipulación automática mejora la productividad, seguridad y ergonomía, minimizando la intervención manual en tareas repetitivas o peligrosas. El mantenimiento preventivo y predictivo basado en la recopilación y análisis de datos operativos contribuye a prolongar la vida útil de los equipos y evitar paradas no planificadas. En conjunto, estos equipos combinan potencia, precisión, flexibilidad y tecnología avanzada para satisfacer las exigencias de la industria moderna, permitiendo la producción eficiente y de alta calidad de piezas metálicas complejas en diversos sectores industriales.
Además, el avance tecnológico ha llevado a la incorporación de interfaces digitales intuitivas en estos equipos, facilitando la programación, supervisión y ajuste de procesos desde pantallas táctiles y sistemas integrados. Esto permite a los operarios modificar parámetros como presión, velocidad o ángulo de trabajo de manera rápida y precisa, adaptándose con agilidad a distintos diseños y requerimientos sin necesidad de cambios mecánicos extensos.
Los sistemas de monitoreo continuo y sensores inteligentes posibilitan la implementación de mantenimiento predictivo, que anticipa desgastes o fallos antes de que ocurran, optimizando los tiempos de mantenimiento y reduciendo costos asociados a paradas inesperadas. Esta inteligencia aplicada a la maquinaria mejora también el control de calidad en tiempo real, detectando anomalías y permitiendo correcciones inmediatas para evitar lotes defectuosos.
La modularidad y flexibilidad de los equipos favorecen su integración en líneas de producción automatizadas y adaptables, donde diversas máquinas se coordinan para realizar operaciones secuenciales como corte, conformado, soldadura y acabado. Esta capacidad de adaptación es crucial para responder a las demandas de mercados dinámicos que requieren variedad y rapidez sin sacrificar calidad.
En materia de seguridad, los equipos modernos cuentan con múltiples dispositivos de protección como resguardos físicos, barreras ópticas, controles bimanuales y paradas de emergencia, garantizando un entorno de trabajo seguro y cumpliendo con las normativas internacionales más estrictas. La automatización reduce la exposición del operario a tareas peligrosas o repetitivas, mejorando la ergonomía y bienestar laboral.
Finalmente, el compromiso con la sostenibilidad impulsa el desarrollo de tecnologías más eficientes en el uso de energía y recursos, como sistemas hidráulicos optimizados, fluidos biodegradables y técnicas que minimizan el desperdicio de material. Esto contribuye a una producción más responsable con el medio ambiente y alineada con las tendencias globales hacia la economía circular.
En síntesis, los equipos para fabricación de piezas de chapa representan la combinación perfecta entre robustez mecánica, precisión tecnológica, innovación digital y responsabilidad ambiental, posicionándose como pilares esenciales para la competitividad y calidad en la manufactura industrial actual.
Sistemas automáticos de conformado de chapa
Los sistemas automáticos de conformado de chapa son conjuntos integrados de máquinas y tecnologías diseñadas para transformar láminas metálicas planas en piezas tridimensionales con formas específicas, a través de procesos como doblado, embutido, estampado y troquelado, todo ello de manera automatizada para maximizar la eficiencia, precisión y repetibilidad en la producción industrial. Estos sistemas son fundamentales en industrias como la automotriz, aeroespacial, electrodomésticos, construcción y fabricación de maquinaria, donde la demanda de componentes metálicos de alta calidad y producción en serie es constante.
Estos sistemas combinan maquinaria avanzada, como prensas hidráulicas y mecánicas controladas por CNC o PLC, con tecnologías de automatización que incluyen robots para la alimentación, manipulación y descarga de piezas, transportadores, sensores inteligentes y sistemas de visión artificial. La integración de estos elementos permite una producción continua y coordinada, minimizando la intervención manual, aumentando la seguridad laboral y reduciendo el riesgo de errores.
En el proceso de conformado automático, las láminas metálicas son alimentadas a la máquina mediante sistemas de carga automática o robots, que posicionan y fijan la pieza correctamente para su procesamiento. Las prensas aplican fuerzas precisas y controladas para realizar doblados, embutidos o estampados, con movimientos programados que garantizan uniformidad en cada ciclo. Los sensores y sistemas de monitoreo detectan cualquier desviación o defecto durante el proceso, activando ajustes automáticos o paros de emergencia para mantener la calidad.
La programación mediante software especializado permite definir secuencias de operación, ajustar parámetros como presión, velocidad, recorrido y ángulo, y almacenar configuraciones para diferentes productos, facilitando cambios rápidos y flexibles en la producción. Además, la conectividad con sistemas de gestión y monitoreo centralizados posibilita el análisis de datos en tiempo real, mantenimiento predictivo y optimización continua del proceso.
Los sistemas automáticos de conformado de chapa también incorporan tecnologías de seguridad avanzada, incluyendo resguardos electrónicos, barreras fotoeléctricas, controles bimanuales y sistemas de parada inmediata, asegurando un entorno de trabajo seguro para los operarios y cumpliendo con normativas internacionales.
En cuanto a la sostenibilidad, estos sistemas están diseñados para minimizar el consumo energético, reducir el desperdicio de material y utilizar fluidos hidráulicos ecológicos, contribuyendo a prácticas de producción responsables con el medio ambiente.
En resumen, los sistemas automáticos de conformado de chapa representan una solución tecnológica integral que combina potencia, precisión, flexibilidad y automatización para optimizar la fabricación de piezas metálicas complejas, mejorando la productividad, calidad y seguridad en la industria moderna. ¿Quieres que te detalle algún tipo específico de sistema o tecnología dentro de estos sistemas automáticos?
Los sistemas automáticos de conformado de chapa combinan maquinaria avanzada, controles digitales y tecnologías de automatización para transformar láminas metálicas planas en piezas tridimensionales con alta precisión y eficiencia. Estos sistemas incluyen prensas hidráulicas y mecánicas controladas por CNC o PLC, que ejecutan procesos como doblado, embutido, estampado y troquelado con movimientos programados y fuerzas ajustables según el tipo de material y diseño requerido. La alimentación y posicionamiento de la chapa se realiza mediante robots o sistemas automáticos que garantizan la correcta colocación y fijación, optimizando los tiempos de ciclo y reduciendo la intervención manual.
Los sensores inteligentes y sistemas de visión artificial supervisan continuamente la operación, detectando cualquier desviación o defecto en tiempo real y permitiendo ajustes automáticos o paradas de emergencia para mantener la calidad y seguridad del proceso. La programación flexible mediante software especializado facilita la configuración rápida para diferentes productos, permitiendo cambios ágiles entre lotes y personalizaciones sin necesidad de modificar físicamente la maquinaria.
La integración con sistemas de gestión y monitoreo centralizados posibilita la recopilación y análisis de datos operativos para implementar mantenimiento predictivo, optimizar recursos y mejorar continuamente la productividad. Además, la automatización avanzada reduce riesgos laborales al minimizar la exposición de los operarios a tareas repetitivas o peligrosas, incorporando dispositivos de seguridad como barreras fotoeléctricas, resguardos y controles bimanuales que cumplen con estrictas normativas internacionales.
Estos sistemas también están diseñados con un enfoque en la sostenibilidad, empleando tecnologías que reducen el consumo energético, utilizan fluidos hidráulicos biodegradables y minimizan el desperdicio de material durante el conformado, apoyando prácticas responsables con el medio ambiente. En conjunto, los sistemas automáticos de conformado de chapa representan una solución integral que combina robustez, precisión, flexibilidad y tecnología digital para optimizar la fabricación de piezas metálicas complejas, adaptándose a las demandas dinámicas y competitivas de la industria actual.
Además, la evolución de los sistemas automáticos de conformado de chapa ha incorporado tecnologías emergentes como la inteligencia artificial y el aprendizaje automático, que permiten optimizar los procesos mediante el análisis avanzado de datos y la adaptación continua a variaciones en el material o condiciones de operación. Esto se traduce en una mayor eficiencia energética, reducción de desperdicios y mejora en la calidad final de las piezas.
La conectividad IoT (Internet de las cosas) facilita la comunicación entre máquinas y sistemas de gestión, creando entornos de fabricación inteligentes donde se puede supervisar y controlar remotamente el estado y rendimiento de cada equipo. Esta interconexión también permite la trazabilidad completa del proceso productivo, importante para cumplir con estándares de calidad y normativas industriales.
La modularidad de estos sistemas automáticos permite su configuración personalizada según las necesidades específicas de cada producción, desde líneas compactas para lotes pequeños y medianos hasta sistemas integrados de alta capacidad para producción masiva. Esta flexibilidad es clave para responder rápidamente a cambios en el mercado o en los requerimientos del producto.
El diseño ergonómico y la implementación de sistemas de seguridad avanzados garantizan la protección del personal, mientras que la automatización contribuye a mejorar las condiciones laborales al reducir tareas repetitivas, pesadas o peligrosas. Asimismo, la facilidad para realizar mantenimiento predictivo y correctivo, apoyada en sensores y diagnósticos en tiempo real, aumenta la disponibilidad y vida útil de los equipos, optimizando la inversión a largo plazo.
En definitiva, los sistemas automáticos de conformado de chapa representan una convergencia entre robustez mecánica, tecnología avanzada y sostenibilidad, configurándose como herramientas indispensables para la fabricación eficiente, segura y de alta calidad en la industria moderna. Su desarrollo continuo impulsa la competitividad de las empresas y facilita la producción de componentes metálicos complejos y precisos en diversos sectores industriales.
Maquinaria para trabajo en chapa metálica
La maquinaria para trabajo en chapa metálica comprende un conjunto diverso de equipos diseñados para transformar láminas metálicas planas en piezas útiles mediante procesos como corte, doblado, embutido, estampado, perforado, laminado y soldadura. Esta maquinaria es fundamental en industrias que requieren componentes metálicos de alta precisión y resistencia, como la automotriz, aeronáutica, construcción, electrodomésticos, mobiliario metálico y fabricación de maquinaria.
Entre las máquinas más comunes destacan las cizallas y guillotinas, utilizadas para cortar láminas en formas rectangulares o irregulares con gran precisión. Las máquinas de corte láser, plasma o por chorro de agua ofrecen una solución más versátil y precisa para cortes complejos, especialmente en materiales de diversos espesores y con formas geométricas variadas. Estas tecnologías permiten trabajar sin contacto físico directo con la chapa, lo que minimiza la deformación térmica o mecánica del material.
Las plegadoras o dobladoras, especialmente en su versión CNC, permiten realizar dobleces en ángulos controlados con gran exactitud. Estas máquinas están equipadas con matrices intercambiables y sistemas hidráulicos o eléctricos que aseguran fuerza y estabilidad durante el doblado, independientemente del espesor de la lámina.
Las prensas hidráulicas y mecánicas son fundamentales para operaciones de embutido, estampado o troquelado. Con el uso de matrices específicas, estas prensas permiten formar piezas tridimensionales, huecas o con geometrías complejas, necesarias para carcasas, paneles estructurales y recipientes metálicos. Las prensas hidráulicas destacan por su control sobre la fuerza aplicada y su capacidad de adaptarse a diferentes tipos de trabajos con precisión y suavidad.
Las punzonadoras automáticas permiten realizar perforaciones y cortes rápidos mediante herramientas intercambiables, ideales para series grandes con alta repetitividad. También existen rodillos perfiladores para formar perfiles continuos a partir de una lámina que avanza de forma automática, utilizados en estructuras metálicas, techos o canaletas.
La automatización ha permitido integrar muchas de estas máquinas en células de producción robotizadas, donde la manipulación de la chapa, el posicionamiento y la descarga de piezas terminadas se realizan mediante brazos robóticos y transportadores inteligentes. Esto mejora la seguridad, reduce la fatiga del operario, aumenta la productividad y asegura una calidad constante del producto final.
Además, el uso de software de diseño y simulación permite previsualizar cada etapa del proceso, programar parámetros con exactitud y corregir errores antes de la producción real, lo que reduce costos por retrabajos y desperdicios.
Estas máquinas modernas también incorporan sistemas de seguridad avanzados, como barreras ópticas, controles bimanuales, paradas de emergencia y protección perimetral, garantizando un entorno de trabajo seguro y cumpliendo con las normas internacionales.
Finalmente, muchas de estas máquinas están diseñadas con criterios de sostenibilidad, incluyendo sistemas hidráulicos de bajo consumo, reciclado de materiales, reducción del desperdicio de metal y menor generación de residuos industriales, lo que responde a las crecientes exigencias de una producción eficiente y responsable con el medio ambiente.
En conjunto, la maquinaria para trabajo en chapa metálica constituye una base tecnológica indispensable para una producción moderna, precisa, flexible y sostenible, capaz de adaptarse a los más variados requisitos técnicos y de diseño en el mundo industrial.
La maquinaria para trabajo en chapa metálica representa uno de los pilares fundamentales de la industria moderna, ya que permite transformar láminas metálicas planas en componentes funcionales mediante una amplia variedad de procesos mecánicos, térmicos y automatizados. Este tipo de maquinaria no solo abarca herramientas básicas como cizallas y plegadoras, sino también equipos altamente sofisticados como punzonadoras CNC, prensas hidráulicas de embutición profunda, máquinas de corte láser con automatización integrada y líneas completas de producción robotizada. Lo que distingue a estas tecnologías es su capacidad para ejecutar operaciones con una precisión milimétrica, manteniendo una alta repetibilidad en ciclos continuos de producción y permitiendo fabricar piezas con tolerancias estrictas, geometrías complejas y acabados consistentes. Las máquinas modernas, controladas por sistemas CNC y PLC, permiten preprogramar cada parámetro operativo, como la fuerza de trabajo, el ángulo de doblado, la velocidad de corte o la profundidad de embutido, de modo que el operario puede adaptar el equipo a diferentes diseños y espesores con tan solo modificar un archivo digital.
Esta flexibilidad hace posible responder rápidamente a cambios en la demanda o en los requisitos del cliente, sin necesidad de detener la línea ni hacer grandes ajustes mecánicos. Además, las máquinas para trabajo en chapa metálica suelen estar integradas con sensores y dispositivos inteligentes que supervisan el estado de cada componente en tiempo real, lo cual habilita el mantenimiento predictivo, reduce drásticamente los tiempos muertos y extiende la vida útil del equipo. Gracias a la conectividad IoT, estas máquinas también pueden formar parte de redes de producción interconectadas, donde los datos se comparten con sistemas de planificación, control de calidad y gestión de almacenes, permitiendo una sincronización total de la cadena productiva.
Otro aspecto clave es la automatización de la manipulación de materiales, que se realiza con transportadores automáticos, alimentadores de bobina, brazos robóticos y mesas de posicionamiento motorizadas, los cuales permiten mantener una producción continua sin necesidad de intervención humana directa. Esto no solo aumenta la eficiencia, sino que mejora significativamente la seguridad laboral, ya que elimina la exposición directa de los operarios a zonas de riesgo. La evolución de estas máquinas también ha estado marcada por una creciente atención a la sostenibilidad. Los sistemas hidráulicos actuales, por ejemplo, están diseñados para consumir menos energía y utilizar fluidos ecológicos, mientras que los procesos de corte y conformado optimizan el aprovechamiento del material, reduciendo los residuos al mínimo. Muchas líneas de producción incluso están equipadas con sistemas de recuperación de calor o reciclado de residuos metálicos, cerrando el ciclo productivo y alineándose con los principios de la economía circular.
En definitiva, la maquinaria para trabajar chapa metálica ha pasado de ser una herramienta manual a convertirse en una plataforma tecnológica de alta complejidad que integra automatización, inteligencia artificial, control digital y sostenibilidad. Este tipo de maquinaria no solo es capaz de responder a las exigencias técnicas de la industria actual, sino que también ofrece una ventaja competitiva clave en términos de productividad, flexibilidad operativa, ahorro de costes y cumplimiento de estándares ambientales. En un entorno industrial cada vez más orientado a la personalización masiva y a la eficiencia de procesos, contar con maquinaria avanzada para el trabajo de chapa metálica ya no es una opción, sino una necesidad estratégica para cualquier planta de producción que aspire a mantenerse competitiva en el mercado global.
Esta maquinaria ha transformado radicalmente la manera en que se diseña y fabrica prácticamente cualquier componente metálico, desde simples estructuras hasta piezas de alta precisión para aplicaciones críticas. El trabajo en chapa metálica, gracias al desarrollo de estas tecnologías, ya no se limita a procesos manuales ni a producciones rígidas. Hoy es posible combinar gran diversidad de procesos dentro de una sola celda automatizada: una chapa entra como materia prima en una estación inicial y, sin intervención humana, pasa por corte, conformado, punzonado, marcado, doblado y apilado final, saliendo como una pieza completamente acabada, lista para el ensamblaje. Esto es posible gracias a la integración entre la maquinaria física y los entornos digitales de control, donde las máquinas están programadas para reconocer cada tipo de pieza, ajustar automáticamente sus parámetros y comunicarse entre sí para coordinar cada movimiento.
La introducción de simulación previa mediante software CAD/CAM también ha sido crucial para minimizar errores antes de la producción. El diseño de cada pieza se prueba digitalmente antes de tocar el metal, lo que reduce desperdicio, evita fallas estructurales y permite afinar detalles sin perder tiempo ni recursos. La conexión directa entre el diseño y la maquinaria permite que incluso series pequeñas y personalizadas se fabriquen con la misma eficiencia que una línea de producción masiva. Esto ha abierto las puertas a nuevos modelos de negocio, como la producción bajo demanda, fabricación distribuida o adaptación rápida a cambios de diseño, sin tener que interrumpir la operación global del sistema.
Al mismo tiempo, los fabricantes de maquinaria para trabajo en chapa han priorizado el desarrollo de entornos operativos más amigables y seguros. El operario ya no tiene que realizar tareas físicas pesadas ni intervenir constantemente en los puntos críticos del proceso. En su lugar, se convierte en un supervisor que gestiona sistemas complejos desde paneles de control intuitivos, analiza datos, interpreta alertas y programa los cambios necesarios para optimizar el rendimiento general. Los nuevos diseños de maquinaria también consideran la ergonomía y la facilidad de mantenimiento como partes fundamentales, permitiendo accesos rápidos a componentes internos, cambios de herramientas sin necesidad de detener la producción y autodiagnósticos que informan sobre el estado del sistema con antelación.
En términos económicos, esta tecnología no solo mejora los tiempos de producción, sino que reduce costos asociados a reprocesos, errores humanos, mantenimiento correctivo y uso ineficiente de materiales. Incluso en industrias de alta demanda como la automotriz o aeroespacial, donde las tolerancias y controles de calidad son extremadamente exigentes, estas máquinas ofrecen la garantía de que cada pieza fabricada será idéntica a la anterior, con acabados perfectos, sin deformaciones ni desviaciones en las medidas.
El avance continuará, con la inclusión progresiva de inteligencia artificial que permitirá a las propias máquinas tomar decisiones operativas en función del comportamiento del material, las condiciones ambientales o la evolución de desgaste en las herramientas. Así, la maquinaria para trabajo en chapa metálica no solo representa una herramienta de fabricación, sino un nodo inteligente dentro de un ecosistema productivo digital, autónomo, eficiente y completamente conectado. La industria que sepa adaptarse a este nuevo paradigma con visión y agilidad será la que defina los estándares del futuro.
Prensas para conformado de chapa
Las prensas para conformado de chapa son equipos fundamentales en el procesamiento industrial de láminas metálicas, ya que permiten transformar la chapa plana en piezas tridimensionales mediante la aplicación controlada de fuerza. Estas prensas realizan operaciones como embutido, doblado, troquelado, estampado, acuñado y recalcado, todas esenciales para dar forma precisa a componentes utilizados en sectores como automoción, electrodomésticos, aeronáutica, construcción y fabricación de maquinaria.
Existen distintos tipos de prensas empleadas en el conformado de chapa, siendo las hidráulicas y las mecánicas las más comunes. Las prensas hidráulicas utilizan un sistema de cilindros impulsados por fluido a presión, lo que les permite aplicar fuerzas constantes y ajustables a lo largo de todo el recorrido del émbolo. Son ideales para operaciones de embutición profunda, donde se requiere un control cuidadoso de la velocidad, la presión y la resistencia del material durante la deformación. Su capacidad para mantener la fuerza en todo el trayecto también las hace adecuadas para trabajar con materiales de espesores variables o con geometrías irregulares.
Por otro lado, las prensas mecánicas funcionan mediante un sistema de engranajes y volante de inercia que convierte el movimiento rotativo del motor en movimiento lineal. Su principal ventaja es la alta velocidad de ciclo, lo que las convierte en una solución eficiente para la producción en serie de piezas con formas menos complejas. Aunque su fuerza máxima se concentra en el punto medio del recorrido, son ampliamente utilizadas en troquelado, estampado y operaciones repetitivas que requieren precisión dimensional constante.
También existen prensas servoeléctricas, una tecnología más reciente que combina la precisión de un control electrónico con la eficiencia energética de los motores eléctricos. Estas prensas ofrecen una excelente repetibilidad, menor consumo de energía y la posibilidad de programar perfiles de movimiento muy detallados. Son especialmente valoradas en procesos de alta precisión, con menor ruido y sin necesidad de sistemas hidráulicos o neumáticos.
Las prensas modernas están equipadas con sistemas CNC y controles inteligentes que permiten programar cada fase del ciclo, ajustar automáticamente la presión, la velocidad de avance y el retorno, y registrar datos del proceso para análisis posteriores. La incorporación de sensores, sistemas de visión artificial y monitoreo en tiempo real permite mantener la calidad, reducir defectos y anticipar problemas mecánicos o de producción antes de que afecten a toda la línea.
En líneas de producción automatizadas, estas prensas se integran con alimentadores de bobinas, robots de carga y descarga, mesas de centrado y transportadores de piezas acabadas, lo que permite mantener un flujo continuo sin intervención manual. Esto no solo aumenta la productividad, sino que también mejora la seguridad, ya que se reducen las tareas repetitivas o peligrosas para el operario.
Desde el punto de vista del mantenimiento y la durabilidad, las prensas modernas están diseñadas para facilitar el acceso a sus componentes críticos, realizar diagnósticos automáticos y permitir intervenciones programadas sin comprometer la producción. La implementación de mantenimiento predictivo, basado en datos de uso y desgaste, también ha ganado terreno como estrategia para evitar fallos y prolongar la vida útil del equipo.
En términos de sostenibilidad, las prensas actuales buscan reducir el consumo energético, optimizar el uso del material mediante procesos más precisos y minimizar los residuos generados. Algunas prensas hidráulicas incluyen sistemas de recuperación de energía o utilizan aceites biodegradables, mientras que las servoeléctricas, al no utilizar fluidos, reducen tanto el impacto ambiental como los requerimientos de limpieza y mantenimiento.
En resumen, las prensas para conformado de chapa son herramientas clave en la fabricación de piezas metálicas, capaces de ofrecer fuerza, precisión y repetibilidad en procesos exigentes. Su evolución tecnológica, impulsada por la digitalización y la automatización, las convierte en soluciones versátiles, eficientes y sostenibles, perfectamente adaptadas a las necesidades cambiantes de la industria moderna.
Las prensas para conformado de chapa representan uno de los elementos más esenciales en la fabricación de componentes metálicos debido a su capacidad para aplicar fuerzas controladas que transforman una simple lámina plana en una pieza tridimensional compleja y funcional. El proceso de conformado por prensa puede abarcar operaciones como embutido profundo, troquelado, acuñado, plegado y repujado, entre otros, dependiendo del diseño del troquel, la naturaleza del material y la configuración del equipo. En este sentido, la prensa actúa como el corazón de la celda de trabajo, y su rendimiento determina en gran medida la calidad, la velocidad y la consistencia del producto final. En aplicaciones industriales, especialmente aquellas que requieren grandes volúmenes de producción, como la automoción o la fabricación de electrodomésticos, las prensas deben no solo ser potentes, sino también extremadamente precisas y repetibles. Una de las grandes ventajas del uso de prensas en el conformado de chapa es que permiten mantener tolerancias dimensionales muy estrictas en ciclos continuos, algo fundamental cuando se busca estandarización y calidad constante en piezas que luego serán ensambladas con otros componentes.
Con la evolución de la tecnología, las prensas hidráulicas han ganado protagonismo por su capacidad de controlar de forma extremadamente precisa la presión y el desplazamiento, lo que resulta especialmente útil en operaciones de embutición profunda o conformado de materiales más exigentes. Estas prensas permiten aplicar la misma presión en todo el recorrido, a diferencia de las mecánicas, cuya fuerza máxima se concentra en un punto específico. Este control hidráulico se traduce en menor estrés en el material, menor tasa de defectos y una mayor capacidad de adaptarse a variaciones en espesor o en las propiedades del material. Sin embargo, en aplicaciones donde la velocidad de ciclo es prioritaria, como en líneas de troquelado rápido, las prensas mecánicas siguen siendo preferidas debido a su eficiencia y rapidez, aunque hoy muchas de estas también se complementan con sistemas de automatización avanzada para aumentar su productividad y seguridad. En el caso de las prensas servoeléctricas, su crecimiento reciente se debe principalmente a su precisión de posicionamiento, su bajo mantenimiento y su funcionamiento más limpio y silencioso. La capacidad de programar exactamente el perfil de movimiento del émbolo las hace ideales para piezas complejas o materiales delicados, con ciclos totalmente configurables en función del producto, lo cual también reduce el desgaste de herramientas y matrices.
La digitalización ha revolucionado la forma en que las prensas se integran a los sistemas de producción. Equipadas con sistemas de control CNC o PLC, estas máquinas pueden recibir órdenes desde un sistema de gestión centralizado, realizar ajustes en tiempo real y reportar continuamente su estado operativo. Esto permite una trazabilidad completa de cada pieza producida, registro automático de condiciones de operación y una capacidad de respuesta inmediata frente a desviaciones o alertas. Además, la recopilación de datos de sensores permite implementar estrategias de mantenimiento predictivo, anticipándose a fallas por desgaste, desequilibrios hidráulicos o desalineaciones, lo que reduce los tiempos de parada y extiende la vida útil del equipo. En entornos de producción automatizados, las prensas se integran completamente con robots de alimentación, descargadores, clasificadores y sistemas de transporte inteligentes que permiten mantener una operación continua y coordinada sin intervención manual directa. Este nivel de automatización no solo mejora el rendimiento global del sistema, sino que también incrementa significativamente la seguridad laboral al minimizar la exposición del operario a riesgos asociados con la manipulación directa de piezas, troqueles o zonas de presión.
A nivel de sostenibilidad, las nuevas generaciones de prensas han sido diseñadas con criterios de eficiencia energética, incluyendo sistemas de gestión de potencia hidráulica que consumen solo lo necesario según la fase del ciclo, el uso de fluidos biodegradables y la incorporación de frenos regenerativos en modelos servoeléctricos que recuperan parte de la energía generada durante el frenado. Este enfoque no solo reduce el impacto ambiental de la operación, sino que también disminuye los costos operativos a mediano y largo plazo. Además, la precisión en el conformado evita desperdicio de material, reduce la generación de rebaba y disminuye la necesidad de retrabajo, contribuyendo a una fabricación más limpia y rentable. En definitiva, las prensas para conformado de chapa han evolucionado hasta convertirse en sistemas de fabricación inteligentes, adaptables y sostenibles que no solo cumplen con los requerimientos técnicos más exigentes, sino que también permiten a las empresas avanzar hacia modelos de producción más flexibles, eficientes y conectados con los desafíos actuales de la industria.
La versatilidad de las prensas para conformado de chapa también se manifiesta en su capacidad de adaptarse a diferentes tipos de materiales y formas, lo que permite su aplicación tanto en la fabricación de piezas grandes y estructurales como en componentes de alta precisión con geometrías detalladas. Las aleaciones ligeras como el aluminio o el magnesio, cada vez más utilizadas en industrias que buscan reducir el peso sin sacrificar la resistencia, requieren un control preciso de la presión, la velocidad de conformado y la lubricación. En este contexto, las prensas modernas ofrecen parámetros ajustables en tiempo real que permiten trabajar con materiales sensibles sin que estos se agrieten, deformen indebidamente o sufran tensiones residuales que afecten su desempeño en el producto final.
El diseño de herramientas y troqueles utilizados en estas prensas ha evolucionado en paralelo con la maquinaria. Hoy en día, los troqueles son desarrollados mediante simulaciones computacionales que modelan la deformación del material bajo diferentes condiciones de carga, fricción, temperatura y velocidad. Este análisis previo permite optimizar el diseño antes de su fabricación, lo cual reduce significativamente los costos asociados a pruebas físicas y ajustes posteriores. Una prensa moderna no es simplemente una fuente de presión, sino un sistema de precisión que actúa en sincronía con los troqueles, los controles digitales, los sensores de presión, desplazamiento y temperatura, así como los sistemas externos de alimentación y descarga. La capacidad de estas máquinas de “leer” lo que está ocurriendo en cada milisegundo del ciclo de producción y reaccionar en consecuencia es lo que las convierte en piezas clave dentro del concepto de industria inteligente.
En muchas plantas industriales, las prensas trabajan en líneas completas donde cada estación realiza una operación secuencial específica: corte inicial, conformado parcial, embutido final, recorte y orificiado, y hasta marcado láser. Estas líneas automatizadas están coreografiadas con precisión, y cualquier variación en el comportamiento de una prensa puede ser comunicada instantáneamente al resto del sistema para que se adapten los procesos posteriores o se detenga la línea si es necesario, evitando errores en cascada. La confiabilidad de estas máquinas es, por tanto, crucial no solo para el rendimiento individual, sino para la continuidad y la eficiencia general de toda la producción.
A medida que las exigencias del mercado demandan productos cada vez más personalizados, con cambios frecuentes en diseño, lote y geometría, la flexibilidad operativa de las prensas para conformado de chapa se convierte en un factor diferenciador. Gracias a sistemas de cambio rápido de herramientas y programación digital de perfiles de movimiento, es posible pasar de un tipo de pieza a otra en minutos, sin necesidad de detener la línea por largos periodos o realizar intervenciones mecánicas complejas. Este tipo de configuración es ideal para empresas que trabajan bajo el modelo de fabricación flexible o bajo demanda, donde la producción debe adaptarse dinámicamente sin sacrificar productividad ni calidad.
Más allá del aspecto técnico, el papel de estas prensas dentro de la estrategia productiva de una empresa es también decisivo. Invertir en una prensa moderna no solo significa adquirir una máquina más potente o precisa, sino incorporar una herramienta capaz de generar datos, integrarse en redes de producción, reducir el impacto ambiental, elevar los estándares de seguridad laboral y abrir la puerta a nuevas oportunidades de innovación en producto. A medida que la industria sigue evolucionando hacia entornos cada vez más automatizados, conectados y exigentes, las prensas para conformado de chapa seguirán ocupando un lugar central en la arquitectura tecnológica de la manufactura avanzada. Su capacidad de adaptación, precisión y robustez continuará siendo esencial para fabricar con eficiencia, calidad y sostenibilidad en un mundo industrial cada vez más competitivo.
Maquinaria para deformación de chapa
La maquinaria para deformación de chapa constituye uno de los pilares más importantes de la industria metalmecánica, ya que permite transformar láminas metálicas planas en piezas tridimensionales funcionales mediante la aplicación controlada de fuerzas mecánicas. Esta categoría abarca un amplio conjunto de equipos especializados en procesos como doblado, embutido, troquelado, punzonado, repujado, estirado, acuñado y rolado, entre otros. La deformación plástica del metal, a través de estos métodos, permite fabricar componentes resistentes y ligeros, optimizando el uso del material sin comprometer su integridad estructural. Estas máquinas están diseñadas para trabajar con una gran variedad de metales como acero al carbono, acero inoxidable, aluminio, cobre y aleaciones especiales, y su aplicación se extiende a sectores tan diversos como la automoción, la aeronáutica, la electrodoméstica, la construcción y la fabricación de maquinaria.
Uno de los grupos más representativos dentro de esta categoría son las prensas, tanto hidráulicas como mecánicas. Las prensas hidráulicas, gracias a su capacidad de aplicar fuerzas constantes y regulables, son ampliamente utilizadas en procesos de embutido profundo y conformado de geometrías complejas, ya que permiten una gran sensibilidad en el control del movimiento del émbolo. Las prensas mecánicas, por otro lado, destacan por su alta velocidad y eficiencia en procesos de troquelado y estampado en serie. En la actualidad, también han cobrado protagonismo las prensas servoeléctricas, que ofrecen un control extremadamente preciso del desplazamiento y velocidad, con menor consumo energético y sin necesidad de sistemas hidráulicos. Estas prensas modernas están equipadas con sistemas CNC y sensores inteligentes que permiten programar parámetros como fuerza, velocidad, recorrido y sincronización, garantizando un proceso de conformado altamente repetible y controlado.
Además de las prensas, la maquinaria para deformación de chapa incluye equipos especializados como las dobladoras, que permiten plegar la lámina en ángulos exactos sin dañarla ni fracturarla. Existen dobladoras manuales para trabajos simples, así como dobladoras CNC automatizadas capaces de realizar secuencias de doblez complejas con gran velocidad y precisión. Otra máquina esencial es el rolador, utilizado para curvar láminas y formar cilindros o conos mediante el paso progresivo entre rodillos. Estas máquinas pueden ser manuales, hidráulicas o eléctricas, y algunas incorporan control numérico para curvaturas variables.
En aplicaciones más específicas, también se utilizan equipos de repujado, una técnica que deforma la chapa mediante presión localizada para crear relieves, cavidades o decoraciones, muy común en la fabricación de utensilios de cocina, piezas ornamentales o componentes metálicos del sector eléctrico. Por su parte, los sistemas de estirado se emplean para fabricar piezas de gran superficie con espesores controlados, típicos en la industria automotriz y aeronáutica.
La automatización de estos procesos ha llevado a la creación de líneas completas de deformación de chapa, donde varias máquinas se integran con alimentadores automáticos, robots de manipulación, sistemas de posicionamiento y transporte, sensores de control de calidad en línea y software de gestión de datos. Esta integración reduce el tiempo de ciclo, mejora la calidad del producto final, aumenta la seguridad operativa y permite la trazabilidad de cada pieza fabricada.
La digitalización también ha tenido un impacto profundo en este tipo de maquinaria. Los modernos sistemas de simulación permiten prever cómo se comportará la chapa bajo diferentes condiciones de carga y deformación antes de iniciar la producción real, lo que ayuda a optimizar el diseño de herramientas y a reducir el número de pruebas físicas necesarias. Además, la recopilación y análisis de datos operativos en tiempo real permite implementar mantenimiento predictivo, evitando fallos no planificados y extendiendo la vida útil de los equipos.
Por último, la eficiencia energética y la sostenibilidad también se han vuelto objetivos centrales en el diseño de maquinaria para deformación de chapa. Los fabricantes buscan reducir el consumo de energía, implementar tecnologías limpias, utilizar aceites hidráulicos biodegradables y minimizar el desperdicio de material mediante técnicas de conformado más precisas. En conjunto, estas máquinas representan una solución tecnológica indispensable para cualquier empresa que trabaje con chapa metálica, ya que ofrecen robustez, precisión, adaptabilidad y eficiencia en un entorno industrial cada vez más exigente y orientado a la innovación.
La maquinaria para deformación de chapa ha evolucionado significativamente para responder a las crecientes exigencias de productividad, precisión, versatilidad y sostenibilidad en la industria moderna. Estas máquinas no solo aplican fuerza para moldear metal, sino que constituyen sistemas altamente controlados que gestionan de forma inteligente cada etapa del proceso de deformación plástica. Desde el momento en que una lámina entra en contacto con la herramienta, comienza una secuencia milimétricamente programada, en la que factores como la velocidad de deformación, la presión ejercida, el recorrido del útil, la fricción y el retorno del material son medidos y regulados en tiempo real. Esta precisión es indispensable cuando se trabaja con materiales de alto valor, geometrías complejas o requisitos de tolerancia estrictos, como ocurre en sectores como la automoción, la aeronáutica o la industria médica. Ya no se trata solamente de conformar chapa, sino de hacerlo con total control, mínima pérdida, y la capacidad de repetir el proceso miles de veces sin desviaciones apreciables.
Uno de los cambios más notables en los últimos años ha sido la integración de estos equipos con tecnologías digitales que permiten simular, programar, ajustar y supervisar cada operación desde interfaces intuitivas. La comunicación entre máquina y software permite anticipar deformaciones no deseadas, redistribuir esfuerzos internos del material y prevenir problemas de elasticidad o fractura antes de que se genere la primera pieza. Esto resulta especialmente importante en aplicaciones donde la resistencia del componente final es crítica o donde una falla estructural podría comprometer la seguridad del producto. Además, la digitalización permite una transición más fluida entre diseños distintos. Una línea equipada con maquinaria avanzada puede cambiar de producto sin necesidad de paros prolongados, ajustes físicos ni reposicionamientos manuales: basta con seleccionar una configuración digital previamente guardada, ajustar los troqueles o matrices si es necesario, y reiniciar la producción bajo nuevos parámetros en cuestión de minutos.
Otro aspecto que define la maquinaria moderna para deformación de chapa es la interconectividad. En un entorno de producción inteligente, las máquinas no operan de forma aislada. Cada prensa, dobladora o roladora está conectada con el resto del sistema: alimentadores, robots, transportadores, sensores de calidad y estaciones de inspección trabajan coordinadamente, comunicando constantemente su estado operativo, consumos, tiempos de ciclo, alarmas y desviaciones. Esta sinergia no solo optimiza el rendimiento general, sino que reduce drásticamente el margen de error humano, incrementa la seguridad operativa y permite alcanzar velocidades de producción que eran impensables hace una década. Asimismo, estas máquinas recopilan datos históricos sobre el comportamiento de cada componente, lo cual permite anticipar el desgaste de herramientas, programar mantenimientos sin afectar la línea, y detectar anomalías antes de que se conviertan en fallas mayores.
La tendencia hacia una producción más sostenible también ha tenido un fuerte impacto en el diseño y uso de maquinaria de deformación. Las nuevas generaciones de prensas hidráulicas, por ejemplo, utilizan sistemas de servo-hidráulica que ajustan el caudal y la presión según la fase del ciclo, evitando el uso continuo de energía a máxima capacidad cuando no es necesario. Los equipos servoeléctricos, que operan sin sistemas hidráulicos ni neumáticos, reducen no solo el consumo eléctrico, sino también la necesidad de mantenimiento, los riesgos de fugas y los residuos industriales. Además, la optimización del diseño de cada pieza mediante software avanzado permite reducir la cantidad de material usado, minimizar la chatarra generada y facilitar el reciclaje de los residuos metálicos, todo lo cual contribuye a una producción más limpia y eficiente. Estas prácticas, lejos de ser únicamente beneficiosas para el medio ambiente, también representan ventajas económicas para las empresas al reducir sus costos operativos y mejorar su imagen ante clientes cada vez más conscientes del impacto ambiental de sus proveedores.
En definitiva, la maquinaria para deformación de chapa ya no es solo una herramienta industrial, sino una plataforma tecnológica que combina fuerza, inteligencia, adaptabilidad y responsabilidad ambiental. Es la columna vertebral de muchas cadenas de producción modernas, capaz de fabricar con exactitud componentes metálicos de alta complejidad y exigencia técnica. Su evolución continuará impulsada por la automatización, la conectividad, la inteligencia artificial y la necesidad de responder de forma ágil a un mercado global que demanda productos más sofisticados, personalizados y sostenibles. En este contexto, las empresas que inviertan en maquinaria avanzada no solo estarán mejor preparadas para competir en términos de calidad y coste, sino que también podrán adaptarse más rápidamente a los desafíos tecnológicos y ecológicos del futuro.
La capacidad de adaptación de la maquinaria para deformación de chapa también ha hecho posible atender tanto producciones masivas como series cortas personalizadas, un aspecto cada vez más crucial en una economía orientada a la flexibilidad y la personalización. Hoy, las mismas máquinas que son capaces de fabricar miles de piezas idénticas con total exactitud pueden también ajustarse en cuestión de minutos para producir una pieza distinta, con otra geometría o espesor, sin necesidad de detener completamente la línea ni sustituir grandes conjuntos mecánicos. Esta versatilidad está impulsada por el uso de herramientas de cambio rápido, sistemas de sujeción automática, troqueles modulares y programación digital que gestiona incluso los más mínimos parámetros de proceso. Esto significa que una planta equipada con tecnología avanzada no necesita elegir entre volumen y variedad: puede tener ambas capacidades simultáneamente, y esto redefine la competitividad industrial.
Otro punto esencial es la creciente autonomía que estas máquinas pueden alcanzar. Los desarrollos más recientes en visión artificial, inteligencia de sensores y algoritmos de autoajuste permiten que las máquinas “aprendan” de cada ciclo, adaptando dinámicamente su operación en función del comportamiento del material, las condiciones del entorno o la detección de desviaciones mínimas. Por ejemplo, una prensa con sensores de fuerza y desplazamiento integrados puede corregir la trayectoria del émbolo en tiempo real si detecta una resistencia diferente a la esperada en la chapa, lo que evita defectos o fallas prematuras sin necesidad de intervención humana. En procesos de repujado o embutido profundo, donde las variables físicas son múltiples y complejas, este tipo de inteligencia de máquina representa una ventaja decisiva que antes solo podía compensarse con experiencia operaria y múltiples ajustes manuales.
Al integrar estas funciones en redes de producción digital, se abre paso a un ecosistema donde cada máquina no solo cumple su función operativa, sino que aporta datos útiles al sistema completo de fabricación. Información sobre la eficiencia energética, la calidad de las piezas, el desgaste de herramientas, el consumo de lubricantes o el estado de las uniones estructurales puede ser analizada para tomar decisiones estratégicas, desde reprogramar un mantenimiento hasta optimizar el diseño de un nuevo producto. Todo esto, en conjunto, representa una transformación profunda de la relación entre el operador humano y la máquina: el operario ya no es un técnico de fuerza y reacción, sino un supervisor de procesos, un programador de eficiencia y un analista de resultados. Esta transformación de roles también implica un cambio en la formación profesional y en la cultura organizativa de las empresas industriales.
En paralelo, el desarrollo de materiales más avanzados, como aceros de alta resistencia, aleaciones ligeras y metales especiales, ha exigido que la maquinaria de deformación también evolucione en términos de robustez, sensibilidad y capacidad de respuesta. Hoy se fabrican prensas, dobladoras, roladoras y sistemas combinados que pueden trabajar con estos materiales exigentes sin comprometer la precisión ni la integridad estructural de la pieza. A través del control exacto de la deformación, estas máquinas permiten aprovechar al máximo las propiedades mecánicas de los materiales, fabricando componentes más resistentes, más ligeros y más eficientes, lo cual es esencial para industrias donde cada gramo cuenta, como la aeroespacial o la automotriz.
En este escenario, las empresas que adoptan maquinaria avanzada para deformación de chapa no solo están invirtiendo en capacidad de producción, sino en inteligencia productiva, reducción de residuos, seguridad operativa y visión a largo plazo. Con la capacidad de escalar producción, diversificar productos, mejorar calidad, reducir costos y alinearse con las nuevas exigencias ambientales, este tipo de maquinaria deja de ser un simple activo físico para convertirse en una palanca estratégica del crecimiento industrial. Su presencia, en cualquier planta moderna, define el ritmo, la precisión y la inteligencia con la que se transforman las ideas en piezas reales, las hojas metálicas en componentes funcionales, y las líneas de producción en sistemas dinámicos capaces de responder al mundo cambiante que hoy define el sector manufacturero global.
Equipos para el procesamiento de chapa
Los equipos para el procesamiento de chapa constituyen la base tecnológica de muchas industrias manufactureras que dependen de componentes metálicos de alta precisión y eficiencia estructural. Estos equipos permiten transformar láminas metálicas en productos finales o semiacabados mediante una amplia variedad de operaciones como corte, conformado, doblado, embutido, punzonado, soldadura, ensamblaje, rolado y acabado superficial. Desde el punto de vista productivo, el procesamiento de chapa no solo implica la deformación del material, sino también su manipulación, posicionamiento, inspección y trazabilidad, por lo que los sistemas actuales deben combinar fuerza, control digital, flexibilidad y automatización avanzada.
Entre los principales equipos utilizados en este campo, los sistemas de corte de chapa representan uno de los primeros pasos. Aquí se incluyen guillotinas mecánicas e hidráulicas para cortes rectos, sierras de disco para cortes longitudinales o transversales, y tecnologías más modernas como el corte por láser de fibra, plasma CNC y chorro de agua, que permiten realizar cortes complejos, limpios y de alta precisión sobre una gran variedad de materiales y espesores. Estas máquinas se integran con software CAD/CAM que traduce directamente el diseño en movimientos de corte, permitiendo optimizar el uso del material y reducir el desperdicio.
Tras el corte, los equipos de conformado toman protagonismo. Las plegadoras CNC o prensas de doblado permiten generar ángulos definidos con exactitud, adaptándose a diferentes geometrías sin deformar la estructura del metal. Las prensas hidráulicas y mecánicas, por su parte, realizan embutición, estampado y troquelado, esenciales para fabricar piezas tridimensionales con volúmenes precisos. Estas prensas pueden trabajar de forma autónoma o como parte de una línea integrada, y hoy están equipadas con sensores de presión, sistemas de retroalimentación y controles digitales que garantizan consistencia entre piezas.
En procesos continuos, los sistemas de rolado permiten curvar chapas para obtener cilindros, conos u otras formas curvas, usando combinaciones de rodillos motorizados. Este tipo de equipo es común en la fabricación de tanques, conductos, recipientes a presión o estructuras metálicas tubulares. También se incluyen aquí las perfiladoras, que deforman la chapa a medida que avanza en línea, produciendo perfiles estructurales o decorativos para aplicaciones como la construcción, la fabricación de marcos o mobiliario metálico.
Otro grupo esencial son las punzonadoras automáticas, capaces de perforar, cortar o marcar la chapa mediante herramientas intercambiables. Son ideales para piezas con muchos orificios, ranuras o patrones repetitivos. Con control CNC y alimentación automática de material, permiten un trabajo rápido, preciso y replicable, integrándose fácilmente en líneas de producción digitalizadas.
El procesamiento de chapa también involucra tecnologías de ensamblaje y unión, como las máquinas de soldadura por puntos, por arco o láser, que permiten unir chapas entre sí sin afectar su resistencia estructural. Estos sistemas están automatizados, con robots que realizan soldaduras repetitivas y homogéneas, además de sistemas de inspección por cámara o ultrasonido para verificar la calidad de cada unión. En los casos donde se requiere rigidez sin soldadura, también se emplean remachadoras automáticas, clinchadoras o sistemas de pegado industrial.
Finalmente, los sistemas de acabado superficial como lijadoras, pulidoras, decapadoras y pintadoras en polvo o líquido, completan el ciclo de procesamiento. Estas máquinas preparan las superficies metálicas para su uso final, removiendo imperfecciones, aplicando recubrimientos protectores o generando acabados estéticos, según el producto requerido.
La tendencia actual es integrar todos estos equipos en líneas automatizadas e interconectadas, donde cada máquina se comunica con las demás, ajusta sus parámetros automáticamente y reporta datos en tiempo real a un sistema de gestión central. Esto no solo mejora la eficiencia productiva, sino que permite realizar trazabilidad total del producto, aplicar mantenimiento predictivo, reducir paros imprevistos y adaptarse rápidamente a nuevos diseños.
En conjunto, los equipos para el procesamiento de chapa ya no son solo herramientas de deformación, sino plataformas tecnológicas que conectan el diseño, la producción y la inteligencia operativa de la fábrica moderna. Su evolución ha hecho posible una fabricación más limpia, precisa, segura y sostenible, y seguirá siendo un factor clave en la capacidad de las industrias para innovar, competir y responder a un mercado en constante transformación.
El conjunto de equipos para el procesamiento de chapa ha experimentado una transformación profunda gracias a la incorporación de tecnologías avanzadas que han redefinido los límites de la fabricación metálica. La capacidad de estos sistemas para integrar múltiples procesos dentro de una misma línea o célula productiva representa una ventaja estratégica en términos de productividad, calidad y flexibilidad. Desde la llegada del corte láser de alta potencia hasta la automatización robótica en el manejo y ensamblaje, cada etapa del procesamiento de chapa se ha optimizado para reducir tiempos, minimizar desperdicios y aumentar la precisión.
Uno de los factores clave en esta evolución es la convergencia entre hardware robusto y software inteligente. Los equipos de corte, conformado y ensamblaje ya no operan como elementos independientes; forman parte de un ecosistema digital donde los datos fluyen continuamente, permitiendo ajustes en tiempo real y facilitando la toma de decisiones informadas. Por ejemplo, un sistema de corte por láser conectado a un software CAD/CAM puede ajustar automáticamente la potencia, velocidad y trayectoria del haz según las propiedades específicas de la chapa que está procesando, ya sea acero inoxidable, aluminio o una aleación especial. Esto garantiza no solo un corte limpio y preciso, sino también la optimización del uso del material y la prolongación de la vida útil de los consumibles.
En cuanto a la conformación, las prensas hidráulicas y servoeléctricas representan un salto cualitativo al ofrecer perfiles de movimiento totalmente programables y adaptativos. La posibilidad de cambiar rápidamente de un programa a otro, junto con sistemas automáticos de cambio de herramientas, facilita la producción de lotes pequeños con alto grado de personalización, sin sacrificar la eficiencia. La integración de sensores de fuerza, desplazamiento, temperatura y fricción permite monitorear cada ciclo para asegurar que el conformado se realice dentro de parámetros ideales, evitando defectos como arrugas, grietas o deformaciones indeseadas. Esta capacidad es especialmente crítica cuando se trabaja con materiales avanzados o diseños complejos que exigen un control exhaustivo de la deformación plástica.
Por otro lado, la automatización en el manejo de materiales ha permitido que los sistemas de procesamiento de chapa reduzcan al mínimo la intervención humana en tareas repetitivas y peligrosas. Los robots colaborativos, sistemas de visión artificial y dispositivos de alimentación automática gestionan la carga y descarga de láminas, la transferencia entre estaciones y el posicionamiento exacto de la pieza, garantizando un flujo continuo y eficiente. Esto no solo aumenta la velocidad de producción sino que mejora la seguridad del operario al mantenerlo alejado de las zonas de riesgo, y permite una mayor consistencia en la calidad del producto final.
La unión y el acabado son otras áreas donde los avances tecnológicos han marcado una diferencia notable. Las máquinas de soldadura robotizadas, por ejemplo, realizan uniones uniformes y resistentes con una velocidad y precisión que superan ampliamente el trabajo manual, mientras que los sistemas de inspección automatizados detectan cualquier defecto en tiempo real, evitando que piezas fuera de especificación avancen en la cadena productiva. Asimismo, los procesos de acabado como el pulido, la aplicación de recubrimientos protectores o la pintura en polvo, están cada vez más integrados en líneas automatizadas que aseguran la uniformidad y la calidad estética necesaria para cumplir con los estándares más exigentes de sectores como el automotriz o el electrónico.
Desde la perspectiva del mantenimiento y la gestión operativa, la implementación de tecnologías de Internet Industrial de las Cosas (IIoT) y análisis de datos ha transformado el enfoque tradicional hacia uno predictivo y preventivo. Los sensores distribuidos en cada máquina monitorizan parámetros críticos como vibraciones, temperaturas, presiones y ciclos de uso, generando alertas tempranas que permiten planificar intervenciones antes de que se produzcan fallas graves. Esto reduce drásticamente los tiempos muertos no programados, optimiza el uso de repuestos y prolonga la vida útil del equipo, lo que representa un ahorro significativo para las empresas.
Finalmente, la sostenibilidad es un aspecto cada vez más central en el diseño y operación de los equipos para procesamiento de chapa. La optimización del consumo energético, el uso de fluidos hidráulicos ecológicos, la minimización de desperdicios y la incorporación de sistemas de reciclaje interno de materiales son prácticas que se están generalizando en la industria. Además, la capacidad para producir piezas más ligeras y resistentes mediante técnicas avanzadas de conformado contribuye a la reducción de emisiones indirectas en sectores como el transporte o la construcción, donde el peso y la durabilidad del componente son determinantes para el desempeño ambiental del producto final.
En conjunto, los equipos para el procesamiento de chapa se han convertido en plataformas tecnológicas integrales que permiten a las industrias transformar materias primas en productos complejos con niveles de calidad, eficiencia y sostenibilidad que solo hace unos años eran impensables. Esta evolución continúa impulsada por la convergencia de la mecánica, la electrónica, la informática y la inteligencia artificial, y se posiciona como un factor decisivo para la competitividad y la innovación en la manufactura del futuro.
La evolución constante de los equipos para el procesamiento de chapa también se refleja en la capacidad de adaptarse a nuevos materiales y técnicas de fabricación que surgen en respuesta a las demandas cambiantes del mercado y la innovación tecnológica. Por ejemplo, la aparición de aceros de ultra alta resistencia, aleaciones ligeras y materiales compuestos ha llevado a desarrollar máquinas capaces de operar con tolerancias cada vez más estrictas, aplicando fuerzas y movimientos adaptativos que respetan las propiedades específicas de cada material para evitar defectos como fisuras, microgrietas o deformaciones permanentes indeseadas. Esto requiere no solo componentes mecánicos robustos y precisos, sino también sistemas de control avanzados que integran sensores y algoritmos de aprendizaje automático para ajustar los parámetros de operación en tiempo real.
En este sentido, el procesamiento de chapa está cada vez más ligado a conceptos como la fabricación inteligente y la industria 4.0, donde las máquinas no solo ejecutan órdenes, sino que forman parte de un ecosistema conectado y coordinado. La interoperabilidad entre equipos permite, por ejemplo, que un sistema de corte reciba información directa del área de diseño y envíe datos de progreso a la planificación de producción, mientras que las prensas y dobladoras pueden ajustar su rendimiento según la calidad detectada en etapas previas o las exigencias del siguiente proceso. Esta comunicación fluida reduce tiempos muertos, errores de programación y la necesidad de inspecciones manuales, aumentando la agilidad y eficiencia de la planta.
La flexibilidad es otro pilar fundamental en la maquinaria actual para el procesamiento de chapa. Frente a la demanda de lotes más pequeños y productos personalizados, las máquinas están diseñadas para cambios rápidos de configuración, mediante sistemas modulares de herramientas, ajustes automáticos y programación intuitiva. Esto permite a los fabricantes responder con rapidez a pedidos variables, sin sacrificar la calidad ni incrementar significativamente los costos de preparación. Además, la integración de interfaces amigables y asistentes digitales facilita la capacitación de operadores y reduce la dependencia de técnicos especializados para realizar ajustes complejos.
En cuanto a la sostenibilidad, la incorporación de tecnologías que permiten un uso más eficiente de la energía, la reducción de desperdicios y la minimización del impacto ambiental es una prioridad creciente. Por ejemplo, los sistemas hidráulicos de última generación cuentan con bombas de caudal variable, recuperación de energía y uso de fluidos biodegradables que disminuyen el consumo y la contaminación. La optimización de los procesos de corte y conformado mediante simulaciones y control en línea reduce el material sobrante y la necesidad de reprocesos, contribuyendo a una producción más limpia y económica. Asimismo, la posibilidad de utilizar chapas recicladas o de menor espesor sin perder calidad es un avance importante que responde a las exigencias regulatorias y sociales actuales.
Finalmente, la seguridad operativa es un aspecto que ha sido profundamente mejorado en la maquinaria para procesamiento de chapa. Los sistemas modernos incorporan múltiples sensores de proximidad, barreras ópticas, sistemas de parada de emergencia inteligentes y protocolos de monitoreo continuo que aseguran la protección del personal sin comprometer la productividad. La automatización y robotización también han desplazado las tareas más riesgosas fuera del alcance directo de los operarios, reduciendo accidentes y mejorando las condiciones laborales. En conjunto, estas mejoras hacen que el entorno de trabajo sea más seguro, lo que repercute en una mayor satisfacción y retención del talento humano.
En síntesis, los equipos para el procesamiento de chapa representan una convergencia de ingeniería mecánica, electrónica, informática y gestión ambiental, configurándose como pilares indispensables de la manufactura avanzada. Su evolución continúa impulsando la capacidad productiva, la innovación técnica y la responsabilidad sostenible de las industrias que dependen de ellos, proyectándose como protagonistas en la transformación industrial hacia modelos cada vez más inteligentes, flexibles y conscientes del entorno.
Maquinaria para modelado de chapa
La maquinaria para modelado de chapa es fundamental en la industria metalúrgica y manufacturera, ya que permite transformar láminas metálicas planas en piezas con formas complejas, superficies curvas, relieves y volúmenes tridimensionales que son esenciales para múltiples aplicaciones industriales. Este tipo de maquinaria abarca una variedad de equipos especializados en procesos como el embutido, el repujado, el doblado, el acuñado y el estirado, cada uno con características particulares que responden a diferentes necesidades de conformado y acabado.
Entre los equipos más destacados para el modelado de chapa se encuentran las prensas hidráulicas y mecánicas, que aplican fuerzas controladas para deformar la chapa a través de matrices y troqueles diseñados específicamente para cada pieza. Las prensas hidráulicas son especialmente valoradas por su capacidad para ejercer una presión constante durante todo el recorrido, lo que permite un control preciso en procesos de embutido profundo o conformado de formas complejas sin dañar el material. Por su parte, las prensas mecánicas, que funcionan mediante sistemas de leva y biela, ofrecen ciclos rápidos y repetitivos ideales para producciones en serie donde la velocidad es un factor clave.
Las máquinas de repujado son otro tipo esencial dentro de la maquinaria para modelado de chapa. Utilizan presión localizada para crear relieves, texturas o cavidades en la superficie del metal, técnica ampliamente utilizada en la fabricación de piezas decorativas, utensilios de cocina, componentes eléctricos y piezas automotrices con detalles estéticos o funcionales. Este proceso requiere un control cuidadoso de la fuerza y el posicionamiento para evitar defectos y garantizar la uniformidad del diseño.
El estirado y el acuñado son procesos que se realizan con máquinas diseñadas para estirar la chapa mediante la aplicación de fuerza desde uno o varios puntos, logrando formas curvas, cónicas o cilíndricas con espesores uniformes. Estas técnicas son especialmente importantes en la fabricación de piezas como carcasas, tapas, paneles y otros componentes donde la resistencia mecánica y la integridad dimensional son fundamentales. Las máquinas para estirado pueden ser hidráulicas o eléctricas, y suelen contar con sistemas de control digital que permiten ajustar parámetros como la velocidad, la presión y el recorrido para adaptarse a distintos materiales y diseños.
Las dobladoras CNC también forman parte de esta familia de maquinaria, permitiendo realizar dobleces precisos y complejos en la chapa mediante el uso de controles numéricos que automatizan la posición y el ángulo de plegado. Estas máquinas son esenciales para la fabricación de piezas con ángulos exactos y repeticiones constantes, con aplicaciones en sectores que van desde la construcción hasta la fabricación de muebles metálicos y componentes electrónicos.
En los últimos años, la incorporación de tecnologías digitales y sistemas de automatización ha revolucionado la maquinaria para modelado de chapa. La integración de sensores, sistemas de retroalimentación en tiempo real y software avanzado permite programar perfiles de movimiento personalizados, detectar y corregir desviaciones durante el proceso, y facilitar el cambio rápido de herramientas o configuraciones. Esto no solo incrementa la productividad y reduce los errores, sino que también extiende la vida útil de las herramientas y mejora la calidad final de las piezas.
Además, la maquinaria moderna para modelado de chapa está diseñada teniendo en cuenta la eficiencia energética y la sostenibilidad. Los sistemas hidráulicos con bombas de caudal variable, el uso de fluidos biodegradables, y los motores eléctricos de alta eficiencia contribuyen a reducir el consumo energético y minimizar el impacto ambiental de la producción. También se implementan técnicas para optimizar el uso del material, reducir residuos y facilitar el reciclaje de las piezas y sobrantes metálicos.
En conjunto, la maquinaria para modelado de chapa es un componente esencial para cualquier industria que requiera piezas metálicas con formas complejas y alta precisión. Su evolución continúa impulsando la innovación en diseño y producción, facilitando la fabricación de productos cada vez más sofisticados, resistentes y adaptados a las exigencias de mercados diversos y competitivos.
La maquinaria para modelado de chapa ha experimentado un avance significativo que ha ampliado su capacidad para atender procesos cada vez más complejos y exigentes en la fabricación de componentes metálicos. Esta evolución responde tanto a la creciente diversidad de materiales, desde aceros convencionales hasta aleaciones ligeras y compuestos metálicos, como a la necesidad de producir geometrías más elaboradas que combinan funcionalidad y estética, además de cumplir con estrictos requerimientos dimensionales y de resistencia. En este contexto, las máquinas de modelado de chapa no solo deben ser robustas y potentes, sino también inteligentes y adaptativas, capaces de controlar en detalle cada fase del proceso para garantizar resultados óptimos.
Las prensas hidráulicas, por ejemplo, han incorporado sistemas servo-hidráulicos que permiten un control dinámico y preciso de la fuerza y la velocidad en función del perfil de la pieza a fabricar. Esto es fundamental cuando se trabaja con embutidos profundos o repujados donde la distribución de tensiones en la chapa debe ser uniforme para evitar defectos como arrugas o fisuras. Estos sistemas avanzados integran sensores de presión, desplazamiento y temperatura que alimentan algoritmos de control en tiempo real, ajustando la operación para mantener la calidad y reducir el desgaste de las herramientas. Además, la modularidad en el diseño de las prensas facilita el cambio rápido de matrices y troqueles, adaptándose con agilidad a lotes pequeños o producciones diversificadas.
Por su parte, las máquinas de repujado han evolucionado para trabajar con alta precisión en la creación de relieves y texturas superficiales complejas. La incorporación de sistemas de posicionamiento digital y control numérico permite reproducir diseños detallados con repetibilidad exacta, lo que es esencial para piezas decorativas o con requerimientos funcionales específicos, como disipadores térmicos o superficies con propiedades aerodinámicas. Estas máquinas pueden operar en conjunto con sistemas robotizados que automatizan la carga y descarga de piezas, optimizando el flujo de trabajo y reduciendo la intervención manual.
Las dobladoras CNC han alcanzado niveles avanzados de precisión y flexibilidad, con capacidades para ejecutar secuencias de doblez múltiples y variar ángulos dentro de una misma pieza. Esto es posible gracias a la integración de sistemas inteligentes que controlan la posición del punzón y la matriz, además de sensores que detectan la resistencia del material durante el proceso para prevenir deformaciones no deseadas. Este nivel de control es especialmente importante cuando se conforman chapas delgadas o materiales sensibles a esfuerzos excesivos. La facilidad para programar y simular el proceso antes de la ejecución real minimiza los errores y reduce los tiempos de puesta a punto.
En cuanto a las máquinas de estirado y acuñado, la innovación tecnológica ha permitido mejorar la uniformidad del espesor, la calidad superficial y la precisión dimensional. Equipos equipados con sistemas hidráulicos de alta respuesta y controles electrónicos avanzados ajustan la fuerza aplicada en función del comportamiento del material, evitando defectos y logrando acabados finos que satisfacen exigencias técnicas muy estrictas, como las requeridas en la industria aeroespacial o médica. La posibilidad de combinar estos procesos con tratamientos térmicos o superficiales en línea amplía las capacidades de producción y reduce la necesidad de operaciones adicionales.
La integración de la automatización y la digitalización en la maquinaria para modelado de chapa también ha transformado la manera en que se planifica, supervisa y controla la producción. El uso de sistemas SCADA, IoT industrial y análisis de datos permite un monitoreo continuo del estado de la máquina, anticipando mantenimientos y ajustando parámetros en función de variaciones detectadas en tiempo real. Esta conectividad también facilita la gestión de la trazabilidad del producto, esencial para industrias con altos estándares de calidad y normativas estrictas, ya que cada pieza puede ser rastreada desde su origen hasta el producto final.
Además, la sostenibilidad y la eficiencia energética son prioridades en el desarrollo de estas máquinas. El uso de motores eléctricos de alta eficiencia, sistemas de recuperación de energía, y fluidos hidráulicos ecológicos contribuye a disminuir el consumo de recursos y la huella ambiental de la producción. El diseño modular y la fabricación con materiales reciclables también forman parte de un enfoque integral para promover prácticas industriales más responsables y competitivas en un mercado global cada vez más consciente del impacto ambiental.
En definitiva, la maquinaria para modelado de chapa se ha consolidado como un componente esencial dentro de la manufactura avanzada, capaz de combinar fuerza, precisión, flexibilidad y sostenibilidad para responder a los retos actuales y futuros de la industria metalmecánica. Su constante innovación impulsa el desarrollo de productos metálicos complejos, eficientes y de alta calidad, posicionando a las empresas que la emplean en la vanguardia tecnológica y competitiva del sector.
La maquinaria para modelado de chapa continúa su evolución impulsada por las demandas de un mercado global que exige rapidez, precisión y personalización, además de una producción más sostenible y eficiente. Uno de los factores clave en esta evolución es la integración creciente de tecnologías inteligentes que permiten que las máquinas no solo ejecuten movimientos mecánicos, sino que analicen, adapten y optimicen el proceso en tiempo real. Esto incluye sistemas de visión artificial que inspeccionan cada pieza conforme se modela, detectando defectos microscópicos, desviaciones dimensionales o variaciones en el acabado superficial, y que a su vez pueden comunicar estas observaciones a los controles para corregir automáticamente parámetros como fuerza, velocidad o trayectoria.
Esta inteligencia integrada también permite implementar procesos de autocalibración y autodiagnóstico, que reducen significativamente los tiempos de preparación y mantenimiento. La maquinaria puede ajustar automáticamente la posición de matrices y herramientas para compensar el desgaste o pequeñas variaciones en las condiciones de operación, garantizando que la calidad de la producción se mantenga constante durante largos períodos y evitando la necesidad de intervenciones manuales frecuentes. Asimismo, los sistemas de monitoreo predictivo, basados en análisis de datos históricos y en tiempo real, anticipan fallas o desgastes antes de que afecten la operación, optimizando la planificación del mantenimiento y evitando costosos tiempos muertos.
Por otro lado, la flexibilidad operativa es un aspecto cada vez más valorado. Las máquinas modernas están diseñadas para permitir cambios rápidos entre diferentes programas y configuraciones, mediante sistemas modulares y automatizados de cambio de herramientas y ajustes. Esto es fundamental para atender a mercados que requieren lotes pequeños o personalizados sin perder eficiencia ni incrementar costos. La capacidad para programar y simular procesos antes de su ejecución, mediante software avanzado, reduce las pruebas físicas y acelera la puesta en marcha de nuevos productos.
La ergonomía y la seguridad de los operarios también han sido foco importante en el desarrollo de la maquinaria para modelado de chapa. Se implementan sistemas avanzados de protección, sensores de presencia, zonas de trabajo restringidas y dispositivos de parada inmediata, que permiten proteger al personal sin afectar la productividad. Además, la automatización de tareas repetitivas o de alto riesgo ha reducido la exposición directa de los trabajadores a condiciones potencialmente peligrosas, mejorando las condiciones laborales y contribuyendo a un entorno de trabajo más saludable.
En cuanto a la sostenibilidad, se ha profundizado el uso de tecnologías que reducen el consumo energético, minimizan los residuos y utilizan materiales y fluidos ecológicos. La optimización del diseño y fabricación de herramientas permite alargar su vida útil y disminuir el consumo de materias primas. Además, la maquinaria está preparada para procesar chapas recicladas o materiales alternativos, alineándose con las tendencias globales hacia la economía circular y la reducción de la huella ambiental.
Finalmente, el futuro de la maquinaria para modelado de chapa apunta a una mayor integración con tecnologías emergentes como la inteligencia artificial, el aprendizaje automático y la fabricación aditiva. Estas herramientas permitirán desarrollar sistemas aún más autónomos, capaces de diseñar, optimizar y ejecutar procesos complejos con mínima intervención humana, y de fabricar piezas con geometrías imposibles de lograr con métodos convencionales, combinando técnicas de conformado con impresiones 3D metálicas para crear productos híbridos de alto valor agregado.
En resumen, la maquinaria para modelado de chapa se encuentra en un proceso continuo de transformación tecnológica que amplía sus capacidades y mejora su eficiencia, calidad y sostenibilidad. Este avance la posiciona como un elemento estratégico para la industria metalmecánica y manufacturera, clave para responder a los desafíos actuales y futuros, y para mantener la competitividad en un mercado global cada vez más exigente y dinámico.
Tecnología de conformado de chapa
La tecnología de conformado de chapa es un conjunto de procesos industriales que permiten transformar láminas metálicas planas en piezas con formas complejas, tridimensionales y funcionales, mediante la aplicación controlada de fuerzas para deformar el material sin fracturarlo. Esta tecnología es fundamental en numerosas industrias, como la automotriz, aeroespacial, electrodomésticos, construcción y fabricación de maquinaria, debido a su capacidad para producir componentes con alta precisión, repetibilidad y eficiencia.
El conformado de chapa abarca diversas técnicas, entre las que destacan el doblado, embutido, estirado, repujado, corte, punzonado y rolado, cada una con características específicas que se adaptan a distintos tipos de materiales, espesores y diseños. Estas técnicas se realizan generalmente en máquinas especializadas que combinan sistemas mecánicos, hidráulicos, neumáticos o servoeléctricos, junto con controles numéricos computarizados (CNC) para garantizar la precisión y repetibilidad del proceso.
El doblado es una de las técnicas más comunes y consiste en deformar la chapa en ángulos definidos utilizando prensas plegadoras, dobladoras CNC o plegadoras hidráulicas. La precisión del doblado depende del control del radio de curvatura, la fuerza aplicada y la calidad del material. En aplicaciones complejas, se emplean sistemas automatizados que permiten secuencias de doblez múltiples y control en tiempo real para evitar deformaciones no deseadas.
El embutido y el estirado son procesos que permiten conformar piezas huecas o con volúmenes mediante la aplicación de fuerzas para estirar o empujar la chapa sobre matrices específicas. Estos procesos son esenciales para fabricar recipientes, carcasas y componentes estructurales. La maquinaria empleada en embutido y estirado suele ser hidráulica, para garantizar una presión constante y un control preciso durante todo el ciclo de conformado.
El repujado es una técnica especializada utilizada para crear relieves o texturas en la superficie de la chapa, combinando precisión y fuerza localizada para lograr detalles estéticos o funcionales en piezas como utensilios de cocina, componentes eléctricos o decorativos. La tecnología moderna ha incorporado sistemas CNC y robotizados que permiten reproducir patrones complejos con alta repetibilidad.
El corte y punzonado, aunque no son procesos de conformado en sentido estricto, forman parte integral de la tecnología de chapa, ya que preparan las piezas para su posterior conformado o ensamblaje. Las tecnologías de corte han avanzado desde sistemas mecánicos hasta el uso de láser, plasma y chorro de agua, que permiten cortes de alta precisión, complejos y sin afectar la integridad del material.
El rolado o curvado es otra técnica vital que utiliza rodillos motorizados para transformar chapas planas en cilindros, conos u otras formas curvas. Esta técnica es esencial en la fabricación de conductos, tanques y componentes estructurales.
La tecnología de conformado de chapa moderna incorpora sistemas avanzados de automatización y digitalización que permiten optimizar los parámetros de proceso, reducir desperdicios y mejorar la calidad del producto final. El uso de sensores, sistemas de visión artificial, software de simulación y control numérico facilita la supervisión en tiempo real, la programación precisa y la adaptación a diferentes materiales y geometrías.
Además, la sostenibilidad es un aspecto creciente dentro de esta tecnología, promoviendo el uso eficiente de materiales, la reducción del consumo energético mediante sistemas servoeléctricos y hidráulicos de alta eficiencia, y la implementación de procesos que minimizan los residuos y facilitan el reciclaje.
En definitiva, la tecnología de conformado de chapa representa una combinación sofisticada de ingeniería mecánica, electrónica e informática, cuyo desarrollo continuo impulsa la capacidad industrial para fabricar piezas metálicas complejas, resistentes y adaptadas a las necesidades actuales de producción eficiente, calidad y sostenibilidad.
La tecnología de conformado de chapa se ha consolidado como un pilar fundamental en la fabricación industrial moderna, caracterizándose por su capacidad para transformar materiales metálicos planos en componentes tridimensionales con alta precisión y repetibilidad. Este proceso no solo implica la deformación física del material, sino también una profunda integración de conocimientos en mecánica, materiales, control automatizado y análisis de procesos que garantizan la calidad y eficiencia productiva. En este sentido, el avance tecnológico ha llevado a la creación de sistemas cada vez más sofisticados que permiten un control minucioso de cada etapa, desde la preparación de la materia prima hasta el acabado final de la pieza.
Uno de los aspectos más relevantes en la evolución de la tecnología de conformado de chapa es la incorporación de sistemas de control numérico computarizado (CNC) y automatización avanzada, que han permitido superar las limitaciones de los métodos tradicionales. Las máquinas CNC ofrecen la posibilidad de programar complejas secuencias de doblado, embutido o estirado con alta precisión, adaptándose rápidamente a cambios en el diseño o en el lote de producción. Esto se traduce en una gran flexibilidad para fabricar desde piezas estándar en grandes cantidades hasta prototipos personalizados, con mínimos tiempos de ajuste y configuración. Además, la automatización reduce la dependencia de la intervención manual, disminuyendo errores y mejorando la seguridad operativa.
La integración de sensores inteligentes y sistemas de retroalimentación en tiempo real representa otro salto cualitativo en esta tecnología. Sensores de presión, desplazamiento, temperatura y fuerza monitorean constantemente el comportamiento del material y la respuesta de la máquina, permitiendo ajustar automáticamente parámetros clave durante el proceso. Por ejemplo, en el embutido profundo, donde el material es susceptible a defectos como arrugas o fisuras, estos sistemas ajustan la velocidad y fuerza aplicada para mantener la deformación dentro de límites seguros. Esto mejora la calidad de la pieza, reduce el desperdicio de material y prolonga la vida útil de las herramientas, impactando directamente en la eficiencia y rentabilidad.
En el ámbito de los materiales, la tecnología de conformado de chapa ha evolucionado para manejar no solo aceros convencionales, sino también materiales avanzados como aceros de ultra alta resistencia, aleaciones ligeras y composites metálicos. Estos materiales presentan desafíos específicos, como mayor resistencia a la deformación o sensibilidad a fisuras, que requieren máquinas con sistemas de control aún más precisos y adaptativos. El desarrollo de procesos asistidos por simulación numérica permite prever el comportamiento del material durante el conformado, optimizar los parámetros y diseñar herramientas adecuadas, reduciendo el ensayo y error y acelerando la puesta en producción.
Además, la conectividad y digitalización han convertido a la tecnología de conformado en parte integral de la llamada Industria 4.0. Las máquinas y sistemas están conectados en redes que permiten la monitorización remota, el análisis predictivo y la gestión integral de la producción. Esta capacidad no solo incrementa la eficiencia operativa, sino que facilita la trazabilidad y control de calidad, fundamentales en sectores con altos estándares normativos. La implementación de plataformas digitales también promueve la toma de decisiones basada en datos, impulsando la mejora continua y la innovación.
Por otro lado, la sostenibilidad es un principio que cada vez está más presente en la tecnología de conformado de chapa. La optimización del uso del material, la reducción del consumo energético mediante tecnologías servoeléctricas y hidráulicas de alta eficiencia, así como el empleo de lubricantes y fluidos ecológicos, contribuyen a disminuir el impacto ambiental. Asimismo, el diseño de procesos que minimizan los residuos y facilitan el reciclaje forman parte de un enfoque integral que responde a las crecientes demandas regulatorias y sociales. La fabricación de piezas más ligeras y resistentes también contribuye a la eficiencia energética en el uso final del producto, impactando positivamente en toda la cadena de valor.
En términos operativos, la ergonomía y la seguridad han sido incorporadas como elementos esenciales en el diseño de equipos y procesos de conformado. La automatización de tareas repetitivas y peligrosas, la implementación de sistemas de protección y monitoreo continuo, y el desarrollo de interfaces de usuario intuitivas contribuyen a crear ambientes de trabajo más seguros y eficientes. Esto favorece no solo la salud y bienestar de los operadores, sino también la productividad y calidad del proceso.
Finalmente, la tecnología de conformado de chapa continúa avanzando hacia la integración con otras tecnologías emergentes, como la fabricación aditiva, la inteligencia artificial y la robótica colaborativa. Estas combinaciones abren nuevas posibilidades para fabricar piezas con geometrías imposibles o mejorar la personalización masiva, además de optimizar la cadena de producción completa. En conjunto, estos desarrollos posicionan a la tecnología de conformado de chapa como un elemento clave para la competitividad y sostenibilidad de las industrias metalmecánicas y manufacturas avanzadas, capaces de enfrentar los retos de un mercado global cada vez más dinámico y exigente.
La continua innovación en la tecnología de conformado de chapa también ha impulsado el desarrollo de materiales y técnicas complementarias que enriquecen el proceso productivo y amplían las capacidades de diseño y funcionalidad de las piezas metálicas. La colaboración entre el diseño asistido por computadora (CAD) y la manufactura asistida por computadora (CAM) permite una integración fluida entre la concepción del producto y su fabricación, facilitando la optimización de formas, la reducción de puntos críticos y la mejora en la distribución de esfuerzos durante el conformado. Esta sinergia entre diseño y fabricación asegura que las piezas no solo cumplan con las especificaciones dimensionales, sino que también presenten propiedades mecánicas adecuadas y un desempeño confiable en su aplicación final.
Los avances en simulación computacional han sido fundamentales para anticipar el comportamiento del material bajo diferentes condiciones de conformado. Herramientas basadas en elementos finitos permiten modelar con precisión la deformación, tensiones residuales, posibles fallas y distribución de espesores en las piezas. Esto reduce considerablemente los tiempos y costos asociados a pruebas físicas y prototipos, permitiendo validar diseños y procesos antes de la producción real. Asimismo, estas simulaciones facilitan el desarrollo de herramientas y matrices que optimizan el flujo de material y minimizan defectos, elevando la calidad del producto final.
En paralelo, la integración de sensores avanzados y sistemas de control adaptativo en las máquinas de conformado ha propiciado una fabricación más inteligente y responsiva. Estos sistemas pueden detectar en tiempo real variaciones en las propiedades del material, desviaciones en la fuerza aplicada o anomalías en el proceso, ajustando automáticamente los parámetros operativos para mantener la consistencia y prevenir fallas. Esta capacidad de autoajuste es especialmente valiosa cuando se trabajan materiales nuevos o mezclas de lotes con características variables, garantizando la estabilidad del proceso y reduciendo desperdicios.
La incorporación de tecnologías de automatización y robótica ha revolucionado la forma en que se ejecutan los procesos de conformado de chapa. Los robots industriales, tanto en estaciones individuales como en líneas integradas, gestionan tareas de carga y descarga, manipulación de piezas, inspección y hasta procesos complejos de conformado en colaboración con máquinas CNC. Esto no solo aumenta la productividad y reduce los tiempos de ciclo, sino que también mejora la seguridad laboral al limitar la exposición de operarios a zonas de riesgo y tareas repetitivas. La colaboración hombre-máquina, a través de robots colaborativos o “cobots”, también se está adoptando para combinar la precisión tecnológica con la adaptabilidad humana en entornos de producción flexibles.
Por otro lado, la preocupación por la sostenibilidad y la economía circular está influyendo cada vez más en el desarrollo y aplicación de la tecnología de conformado de chapa. Se promueven prácticas que maximicen la eficiencia en el uso del material, como el anidado optimizado de piezas en las láminas, la reutilización de recortes y la selección de materiales reciclables. Los procesos buscan reducir el consumo energético, empleando sistemas hidráulicos y eléctricos de alta eficiencia, así como fluidos y lubricantes biodegradables que minimizan el impacto ambiental. Además, la producción de piezas más ligeras y resistentes contribuye a la eficiencia energética en etapas posteriores, como el transporte y uso final, generando un efecto positivo en toda la cadena de valor.
La digitalización también ha permitido el desarrollo de gemelos digitales, representaciones virtuales exactas de las máquinas y procesos de conformado, que facilitan la simulación, monitoreo y optimización continua sin interrumpir la producción física. Estas plataformas permiten experimentar con diferentes configuraciones, prever mantenimientos y evaluar el impacto de modificaciones en tiempo real, lo que se traduce en una gestión más eficiente de los recursos y una respuesta ágil a las demandas del mercado.
Finalmente, el horizonte tecnológico apunta a una mayor integración entre el conformado de chapa y tecnologías emergentes como la fabricación aditiva metálica, la inteligencia artificial y el análisis avanzado de datos. Estas convergencias permitirán fabricar piezas híbridas con estructuras internas optimizadas, realizar ajustes predictivos basados en aprendizaje automático y desarrollar procesos autónomos que eleven los estándares de calidad, velocidad y personalización. En conjunto, estas innovaciones aseguran que la tecnología de conformado de chapa mantenga su rol estratégico en la industria manufacturera, contribuyendo a la competitividad, sostenibilidad e innovación de las empresas en un entorno global cada vez más exigente y dinámico.
Equipos para dar forma a chapa
Los equipos para dar forma a chapa constituyen una categoría esencial dentro de la industria metalúrgica y manufacturera, diseñados para transformar láminas metálicas planas en piezas con formas complejas, superficies curvas, volúmenes tridimensionales y detalles funcionales o estéticos. Estos equipos están orientados a diversos procesos de conformado, incluyendo doblado, embutido, estirado, repujado, corte y punzonado, cada uno con características específicas que permiten adaptar la maquinaria a los requerimientos del material, el diseño y el volumen de producción.
Entre los equipos más utilizados para dar forma a chapa destacan las prensas hidráulicas, que aplican fuerzas controladas mediante sistemas hidráulicos para deformar el material con alta precisión y consistencia. Estas prensas son especialmente adecuadas para procesos de embutido profundo, donde se requiere una presión constante y un control cuidadoso para evitar defectos como arrugas o fisuras. La capacidad de ajuste de la fuerza y la velocidad, junto con sistemas avanzados de control, permite trabajar con diferentes tipos y espesores de chapa, adaptándose a una amplia gama de aplicaciones industriales.
Las prensas mecánicas, por otro lado, funcionan mediante sistemas de leva y biela que transforman el movimiento rotativo en un movimiento lineal para presionar la chapa contra matrices o troqueles. Estas máquinas se caracterizan por ciclos rápidos y repetitivos, ideales para producciones en serie donde la velocidad y la eficiencia son prioritarias. Aunque su fuerza de prensado es limitada en comparación con las hidráulicas, su diseño simple y robusto las hace muy utilizadas en industrias como la automotriz y la fabricación de piezas estándar.
Las dobladoras o prensas plegadoras permiten realizar dobleces precisos en la chapa, creando ángulos y formas definidas. Equipadas con controles numéricos (CNC), estas máquinas ofrecen la posibilidad de programar secuencias complejas de doblez, facilitando la producción de piezas con geometrías sofisticadas y reduciendo el tiempo de ajuste. Las dobladoras pueden ser hidráulicas, eléctricas o híbridas, y se emplean en sectores que van desde la construcción hasta la fabricación de electrodomésticos y muebles metálicos.
Los equipos de estirado y embutido incluyen máquinas hidráulicas especializadas que conforman piezas huecas o volumétricas mediante la aplicación de presión controlada. Estas máquinas cuentan con matrices y punzones diseñados para distribuir la fuerza de manera uniforme y evitar daños en el material, siendo esenciales en la fabricación de recipientes, tapas, carcasas y componentes estructurales. Los sistemas modernos incorporan sensores y controles para monitorear la deformación y ajustar parámetros en tiempo real, garantizando la calidad y uniformidad de las piezas.
Las máquinas de repujado y acuñado permiten crear relieves, texturas y detalles decorativos o funcionales sobre la superficie de la chapa. Utilizan presión localizada y movimientos precisos para dar forma sin comprometer la integridad del material. En la actualidad, estas máquinas suelen estar integradas con sistemas CNC y automatización para reproducir patrones complejos con alta repetibilidad, siendo comunes en la fabricación de utensilios de cocina, componentes eléctricos y piezas decorativas.
El corte y punzonado forman parte integral del proceso de dar forma a la chapa, preparando las piezas para su posterior conformado o ensamblaje. Los equipos de corte han avanzado desde métodos mecánicos convencionales hacia tecnologías de corte por láser, plasma o chorro de agua, que permiten realizar cortes precisos, complejos y sin afectar la estructura del material. Los punzonadores, tanto mecánicos como hidráulicos, realizan orificios y formas específicas en la chapa con gran rapidez y precisión, siendo esenciales en líneas de producción automatizadas.
Además, los sistemas automáticos y robotizados se están incorporando cada vez más en la operación de estos equipos, optimizando la carga y descarga de piezas, el cambio de herramientas y la inspección de calidad. Esta integración aumenta la productividad, reduce la intervención manual y mejora la seguridad laboral.
Finalmente, la evolución tecnológica ha permitido que estos equipos sean más flexibles, eficientes y sostenibles, incorporando sistemas de control avanzado, motores eléctricos de alta eficiencia, fluidos ecológicos y diseños modulares que facilitan el mantenimiento y la adaptación a diferentes procesos y materiales. En conjunto, los equipos para dar forma a chapa representan una inversión estratégica para las industrias que requieren precisión, calidad y productividad en la fabricación de piezas metálicas complejas y de alto valor agregado.
Los equipos para dar forma a chapa representan la convergencia de múltiples disciplinas tecnológicas que han evolucionado para responder a las exigencias de precisión, eficiencia y versatilidad que plantea la manufactura moderna. La complejidad creciente de los diseños y la diversidad de materiales empleados, desde aceros convencionales hasta aleaciones avanzadas y composites, han impulsado la innovación constante en estos equipos, dotándolos de capacidades que van mucho más allá de la simple aplicación de fuerza para deformar metales.
En este contexto, las prensas hidráulicas han alcanzado un nivel de sofisticación notable, incorporando sistemas servo-hidráulicos que combinan la fuerza robusta del sistema hidráulico con la precisión y rapidez de la tecnología servoeléctrica. Estos sistemas permiten un control dinámico y adaptable de la presión, el recorrido y la velocidad, ajustándose en tiempo real a las características específicas del material y la geometría de la pieza. Además, la integración de sensores inteligentes y sistemas de retroalimentación continua garantiza que la deformación se mantenga dentro de los parámetros óptimos, minimizando defectos y prolongando la vida útil de las herramientas, lo que repercute directamente en la eficiencia y la calidad de la producción.
Por otro lado, las prensas mecánicas, aunque más tradicionales, han incorporado mejoras significativas en términos de control y seguridad. La incorporación de controles numéricos programables (CNC) y sistemas de monitoreo permite gestionar con precisión el ciclo de trabajo, optimizar la secuencia de operaciones y detectar anomalías antes de que se produzcan daños. Estos avances han ampliado la aplicabilidad de las prensas mecánicas, permitiendo su uso en procesos que requieren alta velocidad y repetitividad sin sacrificar la calidad.
Las dobladoras CNC se han convertido en piezas clave para la fabricación de componentes con geometrías complejas y múltiples dobleces. Estas máquinas no solo controlan el ángulo y la posición de plegado con gran exactitud, sino que también pueden ejecutar secuencias de doblez coordinadas, evitando deformaciones no deseadas y asegurando la integridad dimensional de la pieza final. La programación avanzada y la simulación previa facilitan la adaptación rápida a diferentes diseños y reducen el tiempo de configuración, aspectos cruciales para responder a la demanda actual de producción flexible y personalizada.
En cuanto a los procesos de embutido y estirado, las máquinas especializadas han incorporado sistemas hidráulicos de alta precisión y software de control avanzado que permiten gestionar la presión y el desplazamiento con extrema exactitud. Estos sistemas son fundamentales para fabricar piezas con paredes delgadas y formas complejas sin comprometer la resistencia estructural. La posibilidad de ajustar parámetros en tiempo real según el comportamiento del material reduce la tasa de rechazo y optimiza el uso de materias primas, aspectos críticos para mantener la competitividad en industrias como la automotriz o aeroespacial.
Las máquinas de repujado y acuñado han evolucionado hacia configuraciones altamente automatizadas, donde robots y sistemas CNC coordinan movimientos precisos para crear relieves y texturas con alta calidad y repetibilidad. Estas tecnologías permiten no solo mejorar el aspecto estético de las piezas, sino también incorporar funcionalidades como disipación térmica o propiedades aerodinámicas, ampliando su valor agregado.
El corte y punzonado, complementarios al conformado, han avanzado en paralelo con tecnologías de corte por láser, plasma y chorro de agua, que ofrecen cortes limpios, rápidos y con mínima deformación térmica, permitiendo trabajar con materiales delicados o de alta dureza. La integración de estas tecnologías con sistemas automatizados de alimentación y descarga contribuye a la optimización de la línea productiva y a la reducción de desperdicios.
Además, la digitalización y conectividad forman el corazón de la transformación de los equipos para dar forma a chapa. La implementación de plataformas de Industria 4.0, que incluyen gemelos digitales, análisis de datos y mantenimiento predictivo, permite maximizar la disponibilidad de los equipos, anticipar fallas y mejorar continuamente los procesos mediante el aprendizaje basado en datos reales de operación. Esto incrementa la agilidad y la capacidad de adaptación de las plantas manufactureras, clave en mercados donde la rapidez y la calidad son decisivas.
La sostenibilidad se ha convertido en un eje transversal que influye en el diseño y operación de estos equipos. El uso de sistemas energéticamente eficientes, la gestión responsable de fluidos y lubricantes, y la optimización del uso de materiales se traducen en un menor impacto ambiental y en ahorros significativos para las empresas. Asimismo, la fabricación de piezas más ligeras y resistentes contribuye a reducir el consumo energético en etapas posteriores como transporte y uso final, generando un efecto positivo en la cadena de valor completa.
Finalmente, la seguridad y ergonomía han sido integradas profundamente en el desarrollo de estos equipos. Sistemas avanzados de protección, sensores de presencia, y protocolos de operación seguros garantizan que los operadores trabajen en un entorno protegido, mientras que la automatización de tareas repetitivas o riesgosas disminuye la exposición a accidentes laborales. Todo esto contribuye a mejorar la productividad y la satisfacción del personal, factores que impactan positivamente en la competitividad y sostenibilidad de la empresa.
En conclusión, los equipos para dar forma a chapa constituyen una combinación avanzada de ingeniería mecánica, electrónica, informática y gestión ambiental, cuyo desarrollo constante impulsa la capacidad de la industria para fabricar piezas metálicas complejas, de alta calidad y con un enfoque sostenible. Esta evolución tecnológica posiciona a dichos equipos como elementos clave en la transformación digital y ecológica de la manufactura moderna, permitiendo a las empresas afrontar los retos de un mercado global competitivo y exigente.
La evolución de los equipos para dar forma a chapa no solo se limita a mejoras en potencia y precisión, sino que también está profundamente marcada por la integración de tecnologías inteligentes y la capacidad para operar en entornos de producción altamente automatizados y flexibles. Este enfoque responde a la necesidad creciente de adaptarse rápidamente a cambios en el diseño del producto, variaciones en los volúmenes de producción y la demanda de una calidad constante sin sacrificar la eficiencia ni incrementar los costos.
La incorporación de inteligencia artificial (IA) y aprendizaje automático está comenzando a transformar estos equipos en sistemas autónomos capaces de analizar grandes volúmenes de datos generados durante el proceso de conformado. Estos sistemas pueden identificar patrones, anticipar posibles fallas, optimizar parámetros operativos y sugerir ajustes en tiempo real para maximizar la calidad y reducir el desperdicio. La IA también facilita la simulación avanzada de procesos, permitiendo evaluar distintas configuraciones y prever resultados antes de la fabricación física, lo que acelera el desarrollo de nuevos productos y procesos.
Además, la conectividad en red a través de tecnologías IoT (Internet de las cosas) permite la interconexión de máquinas, sistemas de control, sensores y plataformas digitales, creando ecosistemas de fabricación inteligentes. Esta interconexión facilita la supervisión remota, el mantenimiento predictivo y la gestión integrada de la producción, contribuyendo a minimizar tiempos de inactividad y mejorar la trazabilidad de las piezas desde la materia prima hasta el producto terminado. La información en tiempo real permite a los responsables de planta tomar decisiones ágiles y basadas en datos, incrementando la productividad y reduciendo costos operativos.
En términos de diseño y flexibilidad, los equipos modernos para dar forma a chapa están concebidos con estructuras modulares que permiten una rápida reconfiguración y adaptación a distintos procesos y materiales. Esto es particularmente relevante en un contexto donde la personalización masiva y la fabricación de lotes pequeños son cada vez más frecuentes. La posibilidad de intercambiar matrices, herramientas y programar secuencias complejas con mínima intervención humana ofrece una ventaja competitiva importante, permitiendo responder con rapidez a los requerimientos del mercado sin perder eficiencia.
La mejora continua en la precisión y repetibilidad también se ha beneficiado del desarrollo de sistemas avanzados de sensores y actuadores, que monitorean variables críticas como presión, velocidad, temperatura y deformación. Estos datos son procesados en tiempo real para ajustar automáticamente el proceso, evitando defectos y garantizando que cada pieza cumpla con las especificaciones técnicas. Este nivel de control es crucial en industrias donde la calidad es vital, como la aeroespacial, automotriz o médica.
Paralelamente, la sostenibilidad se ha convertido en un eje transversal que guía el desarrollo y operación de estos equipos. Se han implementado sistemas que optimizan el consumo energético, como bombas hidráulicas de caudal variable, motores eléctricos de alta eficiencia y sistemas de recuperación de energía. También se promueven prácticas que reducen el uso de materiales y generan menos residuos, junto con la utilización de fluidos de corte y lubricantes biodegradables. Estas iniciativas contribuyen a cumplir con normativas ambientales cada vez más estrictas y a responder a las expectativas sociales sobre responsabilidad corporativa.
En cuanto a la ergonomía y seguridad, los equipos actuales incorporan barreras de protección inteligentes, sistemas de detección de presencia y protocolos automáticos de parada que minimizan riesgos para los operarios. La automatización de tareas repetitivas y peligrosas libera al personal para enfocarse en actividades de supervisión y control, mejorando la satisfacción laboral y reduciendo accidentes. Además, interfaces de usuario intuitivas y sistemas de asistencia remota facilitan la operación y mantenimiento de las máquinas, disminuyendo la curva de aprendizaje y los errores humanos.
Finalmente, la integración futura de tecnologías emergentes como la fabricación aditiva, la realidad aumentada para soporte técnico y la robótica colaborativa ampliará aún más las capacidades de los equipos para dar forma a chapa. Estas innovaciones permitirán combinar procesos convencionales con nuevas técnicas para fabricar piezas con geometrías complejas, optimizar el mantenimiento y facilitar la interacción entre humanos y máquinas en entornos productivos cada vez más inteligentes y adaptativos.
En síntesis, los equipos para dar forma a chapa están en el centro de una transformación tecnológica profunda que potencia la precisión, flexibilidad, sostenibilidad y seguridad en la manufactura metalúrgica. Su desarrollo constante es clave para que las industrias puedan competir eficientemente en un mercado global exigente, ofreciendo productos de alta calidad y valor agregado mientras avanzan hacia modelos de producción más responsables y digitalizados.
Maquinaria industrial para conformar chapa
La maquinaria industrial para conformar chapa constituye el conjunto de equipos y sistemas diseñados para transformar láminas metálicas planas en piezas con formas tridimensionales, complejas y funcionales, mediante procesos que aplican fuerzas controladas para deformar el material sin fracturarlo. Esta maquinaria es fundamental en sectores industriales como la automoción, la aeroespacial, la construcción, la fabricación de electrodomésticos, y la industria metalmecánica en general, donde se requieren componentes metálicos de alta precisión, resistencia y calidad superficial.
Entre los principales tipos de maquinaria industrial para conformar chapa destacan las prensas hidráulicas, prensas mecánicas, prensas plegadoras (dobladoras), máquinas de embutido y estirado, equipos de repujado, así como sistemas de corte y punzonado que preparan la materia prima para su posterior conformado. Cada una de estas máquinas está adaptada para procesos específicos y está equipada con tecnologías que optimizan la eficiencia, precisión y repetibilidad, permitiendo responder a la creciente demanda de piezas complejas y personalizadas.
Las prensas hidráulicas son ampliamente utilizadas debido a su capacidad para aplicar fuerzas variables y constantes durante todo el ciclo de trabajo, lo que las hace ideales para embutidos profundos, estirados y conformados que requieren una presión constante y controlada. Estas máquinas incorporan sistemas de control servo-hidráulicos que permiten ajustar parámetros como fuerza, velocidad y recorrido, adaptándose a diferentes espesores y tipos de material, garantizando la calidad del producto y reduciendo el desgaste de las herramientas.
Por su parte, las prensas mecánicas operan mediante mecanismos de leva y biela, transformando un movimiento rotativo en un movimiento lineal para presionar la chapa. Son adecuadas para procesos de alta velocidad y producción en serie donde la repetitividad es clave. Aunque la fuerza aplicada es fija durante el ciclo, su diseño robusto y simple las hace eficientes para operaciones como corte, punzonado y estampado de piezas estándar.
Las prensas plegadoras o dobladoras permiten realizar dobleces precisos en las chapas, fundamentales para la fabricación de estructuras metálicas, carcasas y componentes diversos. Equipadas con sistemas CNC, estas máquinas permiten programar secuencias complejas de doblez, controlar el ángulo, radio y posición, asegurando la consistencia y calidad en lotes grandes o pequeños. Las versiones hidráulicas o eléctricas ofrecen diferentes ventajas en términos de velocidad, precisión y consumo energético.
Las máquinas de embutido y estirado, especializadas en conformar piezas huecas o con volumen, aplican fuerzas controladas mediante matrices y punzones que distribuyen uniformemente la presión para evitar defectos. Estas máquinas cuentan con sistemas de monitoreo que permiten ajustar en tiempo real parámetros como la velocidad y la fuerza, esenciales para trabajar con materiales sensibles y garantizar la integridad estructural de las piezas.
Los equipos de repujado y acuñado permiten agregar relieves y texturas a las superficies, combinando fuerza localizada con movimientos precisos controlados por CNC y sistemas robotizados. Estos procesos son fundamentales para fabricar piezas decorativas, funcionales o con requisitos específicos de disipación térmica o aerodinámica.
Complementariamente, las máquinas de corte y punzonado, que pueden incluir tecnologías como láser, plasma o chorro de agua, preparan las chapas con precisión para su conformado, permitiendo realizar cortes complejos, limpios y sin afectar la integridad del material. La integración de estos sistemas en líneas automatizadas mejora la productividad y reduce desperdicios.
La maquinaria industrial moderna para conformar chapa se caracteriza además por su integración en sistemas automatizados y digitalizados, incluyendo sensores, plataformas de control, software de simulación y análisis de datos que permiten optimizar el proceso, reducir tiempos de ciclo, anticipar mantenimientos y mejorar la calidad final. Este enfoque es fundamental para responder a la demanda actual de producción flexible, eficiente y sostenible.
Además, la ergonomía y seguridad han sido incorporadas en el diseño de estas máquinas mediante sistemas de protección avanzada, detección de presencia, zonas restringidas y dispositivos de parada de emergencia, reduciendo riesgos para los operarios y mejorando las condiciones de trabajo.
En resumen, la maquinaria industrial para conformar chapa constituye la base tecnológica que permite a las industrias metalúrgicas y manufactureras transformar materias primas en componentes metálicos complejos, precisos y funcionales. Su desarrollo continuo en términos de potencia, precisión, automatización y sostenibilidad es clave para mantener la competitividad y satisfacer las exigencias del mercado global moderno.
La maquinaria industrial para conformar chapa ha experimentado una transformación profunda en las últimas décadas, impulsada por la necesidad de combinar alta productividad con precisión, flexibilidad y sostenibilidad en los procesos de manufactura. Este tipo de maquinaria no solo cumple la función tradicional de aplicar fuerza para deformar el metal, sino que ahora incorpora avanzados sistemas de control, sensores inteligentes y tecnologías digitales que permiten un monitoreo y ajuste continuo del proceso, optimizando cada etapa para reducir defectos, mejorar la calidad y maximizar la eficiencia energética.
Entre las innovaciones más destacadas se encuentran las prensas hidráulicas servoasistidas, que combinan la fuerza y estabilidad de los sistemas hidráulicos con la rapidez y precisión de los servomotores eléctricos. Estos sistemas permiten controlar con exactitud variables como la presión, la velocidad y el recorrido del pistón, adaptándose dinámicamente a las características del material y el diseño de la pieza. La capacidad de realizar ajustes en tiempo real evita problemas típicos del conformado, como arrugas, fisuras o variaciones dimensionales, y reduce el desgaste prematuro de las matrices y punzones, extendiendo su vida útil y minimizando costos de mantenimiento.
Las prensas mecánicas han evolucionado para incluir sistemas de control numérico computarizado (CNC), que permiten programar ciclos de trabajo complejos y repetitivos con alta velocidad y consistencia. Estas prensas son ideales para operaciones de corte, punzonado y estampado en grandes volúmenes, donde la rapidez es esencial. La integración de sensores para monitorear vibraciones, temperatura y fuerza aplicada permite anticipar fallas y realizar mantenimiento predictivo, mejorando la disponibilidad y confiabilidad de la maquinaria.
Las prensas plegadoras CNC han revolucionado el proceso de doblado al ofrecer una precisión milimétrica en el control del ángulo y la secuencia de doblez. Estas máquinas permiten producir piezas con geometrías complejas, como estructuras metálicas de precisión, carcasas y componentes para la industria automotriz y aeroespacial. La posibilidad de simular el proceso en software especializado antes de la producción física reduce considerablemente el tiempo de desarrollo y evita errores costosos. Además, las versiones eléctricas y servoeléctricas ofrecen un menor consumo energético y un mantenimiento más sencillo comparado con sistemas hidráulicos tradicionales.
Las máquinas de embutido y estirado, fundamentales para fabricar piezas huecas y volumétricas, han incorporado sistemas de control avanzado que ajustan la fuerza y la velocidad durante el ciclo de conformado para adaptarse a las propiedades variables del material. Esto es particularmente importante cuando se trabajan aceros de alta resistencia, aleaciones ligeras o materiales compuestos, que exigen condiciones precisas para evitar defectos. La combinación de tecnologías hidráulicas y eléctricas en estas máquinas permite maximizar la eficiencia energética y la calidad del producto final.
Los equipos de repujado y acuñado, cada vez más automatizados, utilizan robots industriales para manipular las piezas y aplicar fuerzas con precisión milimétrica, logrando relieves complejos y detalles finos que antes requerían mano de obra intensiva. Estos sistemas garantizan una alta repetibilidad y calidad superficial, esenciales en sectores como la fabricación de utensilios de cocina, componentes eléctricos y piezas decorativas.
En cuanto a los procesos de corte y punzonado, la incorporación de tecnologías láser, plasma y chorro de agua ha ampliado la capacidad de trabajar materiales de alta dureza y con geometrías complejas, sin generar zonas afectadas térmicamente ni deformaciones. Estos sistemas, combinados con mecanismos automáticos de alimentación y posicionamiento, forman parte integral de líneas de producción inteligentes y flexibles, capaces de adaptarse rápidamente a cambios en el diseño o volumen de producción.
La digitalización y conectividad de la maquinaria industrial para conformar chapa permiten la implementación de sistemas de Industria 4.0, donde la maquinaria está interconectada para monitoreo remoto, análisis predictivo y optimización continua. Los gemelos digitales, representaciones virtuales exactas de la maquinaria y el proceso, facilitan la simulación y prueba de cambios antes de implementarlos físicamente, minimizando riesgos y acelerando la innovación. El análisis de grandes volúmenes de datos operativos mediante inteligencia artificial permite identificar oportunidades de mejora, optimizar parámetros y predecir mantenimientos, aumentando la productividad y reduciendo costos.
La sostenibilidad es un aspecto fundamental en el diseño y operación de la maquinaria moderna para conformar chapa. Se utilizan sistemas hidráulicos de alta eficiencia, motores eléctricos con recuperación de energía y fluidos ecológicos para minimizar el impacto ambiental. Además, la optimización del uso de materiales, reducción de desperdicios y facilidad para procesar materiales reciclados forman parte de un enfoque integral que responde a las exigencias regulatorias y sociales actuales.
La ergonomía y seguridad han sido integradas profundamente en la maquinaria, con sistemas avanzados de protección, sensores de presencia y protocolos de parada inmediata que aseguran un entorno de trabajo seguro para los operadores. La automatización de tareas peligrosas o repetitivas libera a los trabajadores para que puedan concentrarse en actividades de supervisión, mejora continua y control de calidad, elevando la productividad y satisfacción laboral.
En conclusión, la maquinaria industrial para conformar chapa se ha convertido en una plataforma tecnológica altamente sofisticada que integra mecánica, hidráulica, electrónica, informática y sostenibilidad para ofrecer soluciones flexibles, precisas y eficientes. Su constante evolución es esencial para que las industrias puedan fabricar componentes metálicos complejos y de alta calidad, adaptándose a los desafíos de un mercado global cada vez más exigente y orientado hacia la innovación y la responsabilidad ambiental.
La tendencia hacia la digitalización y la automatización avanzada en la maquinaria industrial para conformar chapa está redefiniendo por completo la manera en que se diseñan, operan y mantienen estos equipos. La integración de tecnologías emergentes como la inteligencia artificial, el aprendizaje automático, la robótica colaborativa y la realidad aumentada abre un nuevo horizonte de posibilidades para optimizar no solo la producción, sino también la gestión del ciclo de vida completo de la maquinaria y los productos fabricados.
La inteligencia artificial aplicada permite analizar en tiempo real grandes volúmenes de datos provenientes de sensores instalados en las máquinas, que monitorean parámetros críticos como presión, temperatura, velocidad y fuerzas aplicadas. Con esta información, los sistemas inteligentes pueden detectar patrones anómalos que anticipen fallas, optimizar automáticamente los parámetros operativos para diferentes materiales y diseños, y sugerir ajustes para mejorar la calidad y reducir el consumo energético. Este enfoque predictivo y adaptativo minimiza tiempos de inactividad y costos de mantenimiento, incrementando la disponibilidad y la eficiencia operativa.
La robótica colaborativa (cobots) está ganando protagonismo en las líneas de conformado de chapa al trabajar de manera segura junto a los operadores, realizando tareas como carga y descarga de piezas, cambios de herramientas o inspección visual. Esta colaboración humano-máquina permite una mayor flexibilidad en la producción, adaptándose a lotes pequeños o personalizados sin sacrificar la productividad. Además, reduce la carga física y riesgos para los trabajadores, mejorando las condiciones laborales y reduciendo accidentes.
La realidad aumentada y la realidad virtual están siendo utilizadas para capacitación, mantenimiento y soporte técnico en tiempo real. Los operadores y técnicos pueden visualizar instrucciones, esquemas o alertas superpuestas en su campo de visión mientras trabajan, facilitando la detección rápida de fallas, la correcta ejecución de procedimientos y la reducción de errores. Estas tecnologías también permiten realizar simulaciones virtuales de procesos y configuraciones antes de su implementación física, acelerando la innovación y la adaptación a nuevos productos.
En el ámbito del diseño y desarrollo de productos, la integración entre software CAD/CAM y la maquinaria de conformado facilita una comunicación fluida que reduce tiempos y costos. Las simulaciones avanzadas permiten anticipar el comportamiento del material y los posibles defectos, optimizando el diseño de piezas y herramientas para garantizar que la manufactura sea eficiente y con altos estándares de calidad desde la primera pieza producida.
La tendencia hacia la fabricación sostenible influye en todas las etapas del proceso y en la elección de la maquinaria. Se priorizan equipos con bajo consumo energético, sistemas de recuperación y reutilización de fluidos, y capacidades para trabajar con materiales reciclados o de origen responsable. Este enfoque no solo responde a regulaciones y demandas del mercado, sino que también aporta ventajas competitivas a través de la reducción de costos operativos y mejora de la imagen corporativa.
Asimismo, la modularidad y escalabilidad de la maquinaria permiten adaptar fácilmente las líneas de producción a cambios en la demanda o introducción de nuevos productos. Esto es esencial en un contexto industrial que exige rapidez de respuesta y flexibilidad para producir lotes variables sin incurrir en elevados costos de reconversión.
Finalmente, el enfoque hacia la ciberseguridad es cada vez más relevante, dado que la conectividad y digitalización exponen a las plantas industriales a riesgos de intrusión o sabotaje. Se implementan protocolos, firewalls y sistemas de monitoreo para proteger tanto la integridad de la maquinaria como la confidencialidad de los datos productivos y comerciales.
En resumen, la maquinaria industrial para conformar chapa está en plena transformación hacia sistemas inteligentes, interconectados y sostenibles, capaces de responder a las demandas actuales y futuras de la industria manufacturera. Esta evolución tecnológica permite no solo fabricar piezas metálicas con mayor calidad y eficiencia, sino también integrar la producción dentro de ecosistemas digitales que potencian la innovación, la flexibilidad y la competitividad en un mercado global cada vez más dinámico y exigente.
Máquinas de conformado de láminas metálicas
Las máquinas de conformado de láminas metálicas son equipos industriales diseñados para transformar chapas planas en piezas con formas específicas mediante procesos de deformación plástica controlada. Estas máquinas juegan un papel fundamental en la fabricación de componentes para sectores como el automotriz, aeroespacial, electrodomésticos, construcción, y muchas otras industrias que requieren piezas metálicas con geometrías complejas, alta precisión y calidad superficial.
Entre las principales máquinas de conformado se encuentran las prensas hidráulicas, que utilizan sistemas hidráulicos para aplicar fuerzas variables y controladas durante todo el ciclo de trabajo, lo que resulta ideal para procesos como embutido profundo, estirado y conformado de piezas volumétricas. Estas prensas ofrecen la ventaja de un control preciso de la presión y velocidad, adaptándose a diferentes espesores y tipos de materiales, asegurando la integridad estructural y dimensional de las piezas.
Las prensas mecánicas funcionan mediante mecanismos de leva y biela que convierten el movimiento rotativo en movimiento lineal para presionar la lámina contra matrices o troqueles. Son adecuadas para operaciones de alta velocidad y producción en serie, como el corte, punzonado y estampado, donde la repetitividad y rapidez son esenciales. La incorporación de sistemas CNC ha mejorado la precisión y flexibilidad de estas máquinas, permitiendo programar ciclos complejos y controlar parámetros operativos.
Las prensas plegadoras o dobladoras son máquinas especializadas para realizar dobleces en la chapa, permitiendo crear ángulos y formas específicas. Equipadas con controles numéricos, estas máquinas pueden programar secuencias de doblez complejas y garantizar la precisión en la conformación, lo que es fundamental en la fabricación de estructuras metálicas y carcasas. Las versiones hidráulicas y eléctricas ofrecen distintas ventajas en términos de velocidad, precisión y eficiencia energética.
Las máquinas de embutido y estirado son esenciales para la fabricación de piezas huecas o volumétricas, aplicando fuerzas distribuidas mediante matrices y punzones que evitan defectos como arrugas o fisuras. Estas máquinas incorporan sistemas de monitoreo para ajustar parámetros en tiempo real, lo que es crucial al trabajar con materiales avanzados y piezas de alta complejidad.
Los equipos de repujado y acuñado permiten agregar relieves y texturas mediante presión localizada y movimientos precisos, a menudo controlados por sistemas CNC y robots, garantizando calidad y repetibilidad en aplicaciones decorativas y funcionales.
Adicionalmente, las máquinas de corte y punzonado, que incluyen tecnologías como láser, plasma y chorro de agua, preparan las láminas con alta precisión para los procesos de conformado, permitiendo realizar cortes complejos sin dañar el material.
La digitalización y automatización son aspectos clave en la maquinaria moderna de conformado, incorporando sensores, software de control y análisis de datos que optimizan la producción, mejoran la calidad y permiten mantenimiento predictivo. La sostenibilidad también es prioritaria, con máquinas diseñadas para minimizar el consumo energético y el impacto ambiental.
En conjunto, las máquinas de conformado de láminas metálicas representan una combinación avanzada de tecnología mecánica, hidráulica, electrónica y digital, cuya evolución continua es vital para la competitividad y eficiencia de la industria metalúrgica y manufacturera a nivel global.
Las máquinas de conformado de láminas metálicas representan el núcleo tecnológico de múltiples procesos industriales dedicados a la transformación de materiales planos en componentes tridimensionales con aplicaciones variadas y exigentes. Su evolución ha sido impulsada por la necesidad creciente de fabricar piezas con geometrías cada vez más complejas, tolerancias estrictas y acabados superficiales de alta calidad, al tiempo que se optimizan los costos, tiempos y recursos en entornos productivos cada vez más competitivos y dinámicos.
El diseño y construcción de estas máquinas combinan avanzados principios de ingeniería mecánica, hidráulica y electrónica, integrados mediante sistemas de control sofisticados que permiten una operación precisa y adaptable. Por ejemplo, las prensas hidráulicas modernas utilizan circuitos servo-hidráulicos capaces de modular la presión y velocidad en tiempo real, lo que facilita la producción de piezas con embutidos profundos o estirados complejos sin generar defectos en la chapa, incluso cuando se trabaja con materiales avanzados o aleaciones difíciles de conformar. La capacidad de respuesta rápida y control fino en estas máquinas ha revolucionado procesos tradicionalmente complejos, reduciendo la tasa de rechazo y aumentando la vida útil de las herramientas.
Las prensas mecánicas, aunque basadas en mecanismos clásicos, han incorporado controles numéricos programables que permiten gestionar secuencias complejas y asegurar repetibilidad en ciclos de alta velocidad, fundamentales en la producción masiva de piezas como carcasas, paneles y componentes estructurales. Estos sistemas integran sensores que monitorean parámetros como la fuerza aplicada, la posición y las vibraciones, lo que facilita la detección temprana de anomalías, mantenimiento predictivo y reducción de tiempos muertos. Así, la maquinaria mecánica conserva su vigencia y se adapta a los nuevos requerimientos de flexibilidad y calidad.
Las prensas plegadoras CNC han transformado el proceso de doblado al permitir la programación de secuencias múltiples de doblez con ángulos y radios específicos, esenciales para fabricar piezas con geometrías intrincadas o que requieren precisión dimensional estricta. La simulación digital previa al proceso físico evita errores, reduce la necesidad de prototipos y acelera el desarrollo de nuevos productos. Además, las tecnologías eléctricas y servoeléctricas han optimizado el consumo energético, reducido el ruido y simplificado el mantenimiento en estas máquinas.
Los equipos para embutido y estirado han avanzado para incorporar sistemas inteligentes que ajustan automáticamente la fuerza y velocidad durante el ciclo en función de la respuesta del material, mejorando la calidad de piezas volumétricas y huecas sin comprometer su resistencia estructural. Estos sistemas son especialmente importantes cuando se trabaja con aceros de alta resistencia o aleaciones ligeras que exigen condiciones de conformado muy controladas para evitar fisuras o deformaciones no deseadas.
La automatización en la manipulación de piezas mediante robots colaborativos ha mejorado significativamente la eficiencia y seguridad en las líneas de conformado. Los robots se encargan de tareas repetitivas, como la carga y descarga de las máquinas, inspección visual y el cambio de herramientas, permitiendo que los operarios se centren en la supervisión, ajustes y control de calidad. Esta colaboración humano-máquina aporta flexibilidad para manejar lotes pequeños o personalizados, alineándose con las tendencias de fabricación ágil y producción bajo demanda.
La incorporación de tecnologías de corte avanzadas, como láser, plasma y chorro de agua, ha ampliado las capacidades de la maquinaria de conformado, facilitando el procesamiento de materiales difíciles, geometrías complejas y espesores variados con alta precisión y sin afectar las propiedades del material. La integración de estos sistemas en líneas productivas automatizadas asegura un flujo constante de piezas preparadas para su conformado, minimizando tiempos y desperdicios.
Los sistemas de control y monitoreo digital conforman la columna vertebral de la maquinaria moderna para conformado de láminas, permitiendo la conexión en red de los equipos y su integración dentro de plataformas de Industria 4.0. Esto posibilita la supervisión en tiempo real, análisis predictivo y mantenimiento basado en datos, además de facilitar la trazabilidad completa de cada pieza fabricada. La capacidad para generar gemelos digitales, simulaciones precisas y ajustes automáticos optimiza la eficiencia y calidad, mientras que la conectividad remota permite soporte técnico y actualizaciones sin necesidad de intervención presencial.
La sostenibilidad ha pasado a ser un aspecto central en el desarrollo y operación de estas máquinas. Se priorizan diseños que minimizan el consumo energético mediante motores de alta eficiencia, sistemas hidráulicos de caudal variable y recuperación de energía. La gestión responsable de fluidos y lubricantes, así como la capacidad para procesar materiales reciclados, contribuyen a reducir el impacto ambiental y mejorar la economía circular en la industria metalúrgica.
En términos de seguridad y ergonomía, las máquinas incorporan avanzados sistemas de protección, detección de presencia y paradas de emergencia que garantizan un entorno seguro para los operarios. La automatización de operaciones peligrosas reduce riesgos laborales y mejora la productividad, mientras que interfaces de usuario intuitivas y sistemas de asistencia remota facilitan la operación y el mantenimiento, reduciendo la posibilidad de errores y acelerando la capacitación.
En definitiva, las máquinas de conformado de láminas metálicas representan una convergencia de innovación tecnológica, ingeniería avanzada y prácticas sostenibles, que permiten a la industria manufacturera fabricar piezas metálicas complejas, precisas y de alta calidad, en entornos productivos cada vez más flexibles, eficientes y responsables con el medio ambiente. Su evolución continua es clave para mantener la competitividad y adaptarse a los retos presentes y futuros del mercado global.
La consolidación de las máquinas de conformado de láminas metálicas como piezas clave dentro de la cadena productiva moderna se refleja no solo en la sofisticación técnica, sino también en su integración dentro de sistemas productivos inteligentes que responden a las demandas de flexibilidad, calidad y sostenibilidad que caracterizan la manufactura contemporánea. Este avance implica una transición de equipos autónomos y manuales hacia sistemas interconectados, automatizados y capaces de autoajustarse, optimizar procesos y contribuir a la toma de decisiones en tiempo real.
El desarrollo de sistemas de control basados en inteligencia artificial y aprendizaje automático ha permitido que las máquinas analicen continuamente el comportamiento del material y las condiciones operativas, anticipando posibles desviaciones o defectos en la conformación. Esto posibilita que los parámetros de presión, velocidad y recorrido se modifiquen de manera dinámica para mantener la integridad de la pieza, minimizar desperdicios y evitar paradas imprevistas. Este nivel de autonomía en las máquinas reduce la dependencia del operador, aumenta la consistencia del proceso y mejora la eficiencia general.
Asimismo, la robótica avanzada y los sistemas colaborativos han transformado radicalmente las líneas de conformado. Los robots colaborativos, o cobots, trabajan en conjunto con los operarios para realizar tareas que requieren precisión y repetitividad, como la manipulación, montaje o inspección de piezas, liberando a los trabajadores de labores repetitivas o físicamente exigentes. Esto no solo incrementa la productividad sino que también mejora las condiciones laborales y reduce riesgos de accidentes.
El uso de tecnologías de realidad aumentada y realidad virtual para la capacitación y el mantenimiento representa otro salto cualitativo en el manejo de estas máquinas. Los operarios pueden recibir instrucciones visuales superpuestas durante la operación, acceder a manuales interactivos y realizar diagnósticos en tiempo real, lo que disminuye errores, acelera el aprendizaje y optimiza los tiempos de intervención técnica. Esto es especialmente valioso en contextos donde la rotación de personal o la necesidad de alta especialización pueden representar un desafío.
El diseño modular y escalable de las máquinas permite adaptarlas rápidamente a cambios en los requerimientos productivos, facilitando la fabricación de lotes pequeños o personalizados sin sacrificar eficiencia ni calidad. Esta flexibilidad es esencial en un mercado global donde la personalización y la innovación continua son factores clave para la competitividad.
En términos de sostenibilidad, la maquinaria ha incorporado sistemas que optimizan el uso de energía y recursos, como motores de alta eficiencia, sistemas hidráulicos con recuperación de energía y tecnologías para el uso de fluidos y lubricantes ecológicos. Además, se promueve el diseño para facilitar el reciclaje y reutilización de materiales, contribuyendo a la economía circular y a la reducción del impacto ambiental de la industria.
La conectividad mediante tecnologías IoT posibilita la integración de las máquinas en ecosistemas digitales donde la información fluye entre dispositivos, sistemas de gestión y plataformas analíticas, facilitando una visión global del proceso productivo. Esto permite no solo mejorar la planificación y la gestión operativa, sino también implementar estrategias de mantenimiento predictivo que minimizan las paradas no programadas y prolongan la vida útil de los equipos.
Finalmente, el enfoque en la seguridad se traduce en la implementación de barreras físicas inteligentes, sensores de proximidad, sistemas de emergencia automáticos y protocolos de operación seguros que protegen a los trabajadores sin limitar la productividad. La automatización de tareas peligrosas y el monitoreo constante reducen los riesgos laborales y contribuyen a generar ambientes de trabajo más saludables y sostenibles.
En conclusión, las máquinas de conformado de láminas metálicas son mucho más que simples equipos de deformación; constituyen el centro de un ecosistema tecnológico avanzado que integra mecánica, electrónica, informática y sostenibilidad para ofrecer soluciones productivas adaptadas a los retos actuales y futuros de la industria manufacturera global. Su continua innovación es fundamental para potenciar la competitividad, calidad y responsabilidad ambiental en la fabricación de componentes metálicos, impulsando así el desarrollo industrial en una era cada vez más digitalizada y exigente.
Sistemas de conformado de láminas
Los sistemas de conformado de láminas constituyen un conjunto integrado de máquinas, herramientas, controles y procesos diseñados para transformar chapas metálicas planas en piezas con geometrías complejas mediante la aplicación controlada de fuerzas que generan deformaciones plásticas permanentes. Estos sistemas son esenciales en la manufactura moderna, abarcando desde la preparación y corte inicial de la materia prima hasta el conformado final, acabado y control de calidad, conformando una cadena productiva eficiente, flexible y altamente automatizada.
La base de un sistema de conformado de láminas es la maquinaria especializada, como prensas hidráulicas, prensas mecánicas, prensas plegadoras, máquinas de embutido y estirado, así como sistemas complementarios de corte, punzonado y repujado. Cada equipo está diseñado para procesos específicos, pero su integración en líneas automatizadas permite optimizar el flujo productivo, reducir tiempos de ciclo y garantizar la repetibilidad y calidad de las piezas fabricadas.
Los sistemas modernos incorporan tecnologías digitales avanzadas, como controles numéricos computarizados (CNC), sensores inteligentes, y plataformas de monitoreo que recopilan y analizan datos en tiempo real. Esta digitalización facilita la gestión integral del proceso, permitiendo ajustes dinámicos en parámetros como la presión, velocidad y trayectoria de las herramientas, adaptándose a las características particulares del material y la geometría requerida. Además, la digitalización permite la trazabilidad total de las piezas, desde la materia prima hasta el producto final, un aspecto clave para industrias que exigen altos estándares de calidad y certificaciones.
Un elemento crucial dentro de estos sistemas es la integración de la automatización y robótica, donde robots industriales y colaborativos realizan tareas repetitivas y de alta precisión, como la manipulación de láminas, carga y descarga de prensas, inspección visual y cambios de herramientas. Esta automatización mejora la productividad, reduce riesgos laborales y permite la fabricación flexible de lotes variables, incluyendo producción bajo demanda y personalización masiva.
La simulación virtual y los gemelos digitales forman parte de la estrategia tecnológica para optimizar los sistemas de conformado. Mediante modelos computacionales avanzados se pueden prever comportamientos del material durante el conformado, anticipar posibles defectos y optimizar el diseño de herramientas y secuencias de trabajo antes de ejecutar el proceso físico. Esto reduce costos, acelera el desarrollo de nuevos productos y mejora la eficiencia global.
La sostenibilidad se integra en el diseño y operación de los sistemas de conformado mediante el uso eficiente de energía, gestión responsable de fluidos hidráulicos y lubricantes, y la capacidad para procesar materiales reciclados o de bajo impacto ambiental. Asimismo, se implementan tecnologías para minimizar el desperdicio de material, optimizar el uso de chapas y reducir emisiones, contribuyendo a la responsabilidad ambiental y cumplimiento normativo.
En cuanto a seguridad y ergonomía, los sistemas cuentan con dispositivos inteligentes de protección, sensores de presencia, y protocolos automáticos de parada para garantizar ambientes de trabajo seguros y saludables. La reducción de tareas peligrosas y repetitivas a través de la automatización mejora las condiciones laborales y disminuye los índices de accidentes.
Finalmente, la conectividad y gestión remota permiten integrar estos sistemas dentro de plataformas industriales globales, facilitando la supervisión, diagnóstico y mantenimiento predictivo desde cualquier ubicación. Esto incrementa la disponibilidad operativa, facilita la toma de decisiones basada en datos y soporta la evolución hacia fábricas inteligentes y digitalizadas.
En resumen, los sistemas de conformado de láminas representan una convergencia tecnológica avanzada que integra maquinaria especializada, automatización, digitalización y sostenibilidad para fabricar piezas metálicas de alta calidad, adaptándose a las exigencias dinámicas de la industria moderna y fomentando la competitividad en un mercado global cada vez más exigente.
Los sistemas de conformado de láminas metálicas han evolucionado hasta convertirse en complejas plataformas integradas que combinan la mecánica tradicional con tecnologías digitales y de automatización avanzada, permitiendo afrontar con éxito los desafíos actuales de la manufactura industrial. Estos sistemas no solo aplican fuerzas para modificar la geometría de las chapas, sino que ahora funcionan como ecosistemas inteligentes que controlan cada etapa del proceso, desde la alimentación y posicionamiento del material hasta el acabado y la inspección final de las piezas, garantizando máxima eficiencia, calidad y adaptabilidad.
En la base de estos sistemas se encuentran las máquinas de conformado, que pueden incluir prensas hidráulicas, mecánicas, plegadoras CNC, embutidoras, estiradoras, y equipos de repujado, entre otros, cada una especializada para diferentes tipos de deformaciones y geometrías. La correcta coordinación y sincronización de estas máquinas es vital para mantener un flujo continuo y sin interrupciones, optimizando los tiempos de ciclo y minimizando pérdidas. Esto se logra mediante sistemas de control centralizados que integran datos provenientes de sensores distribuidos a lo largo de la línea productiva, permitiendo un monitoreo exhaustivo y una respuesta rápida ante cualquier desviación.
La implementación de tecnologías de control numérico computarizado (CNC) en estas máquinas ha sido fundamental para alcanzar altos niveles de precisión y repetibilidad. Los programas CNC permiten definir con exactitud los parámetros de conformado, como la fuerza aplicada, la velocidad, el ángulo de doblado o la trayectoria del punzón, adaptándose fácilmente a diferentes diseños y materiales. Esta flexibilidad es crucial para responder a las demandas de lotes pequeños, producción personalizada y ciclos cortos de desarrollo, características cada vez más comunes en la industria actual.
Además, la digitalización ha facilitado la integración de sistemas de simulación y gemelos digitales, que permiten modelar el comportamiento del material durante el conformado y anticipar posibles problemas como arrugas, fisuras o tensiones residuales. Estas simulaciones ayudan a optimizar el diseño de matrices y herramientas, así como a definir las mejores secuencias de trabajo, reduciendo el tiempo y costo asociados a pruebas físicas y prototipos. De esta manera, se mejora la calidad del producto final y se acelera la puesta en marcha de nuevas líneas o productos.
La automatización y robotización son componentes esenciales en los sistemas modernos de conformado. Robots industriales y colaborativos asumen tareas de manipulación, transporte, carga y descarga de chapas y piezas, así como inspección visual mediante sistemas de visión artificial. Esta automatización no solo incrementa la productividad y la consistencia del proceso, sino que también mejora la seguridad al reducir la exposición de los operarios a movimientos peligrosos o repetitivos, permitiendo que el personal se enfoque en actividades de supervisión, mantenimiento y mejora continua.
La eficiencia energética y la sostenibilidad son también pilares en el diseño y operación de estos sistemas. Se emplean motores y bombas hidráulicas de alta eficiencia, sistemas de recuperación y reutilización de energía, y fluidos ecológicos para minimizar el impacto ambiental. Además, el diseño de procesos optimizados busca reducir el desperdicio de material y facilitar el reciclaje, contribuyendo a la economía circular y al cumplimiento de normativas ambientales cada vez más estrictas.
En términos de seguridad, los sistemas cuentan con dispositivos avanzados como sensores de proximidad, cortinas de luz, paradas de emergencia automáticas y enclavamientos que garantizan la protección de los operadores sin comprometer la productividad. La ergonomía también se considera en el diseño de las estaciones de trabajo y en la interacción hombre-máquina, promoviendo ambientes de trabajo saludables y eficientes.
La conectividad de los sistemas de conformado con plataformas industriales y tecnologías IoT permite la supervisión remota, mantenimiento predictivo y análisis de grandes volúmenes de datos para la toma de decisiones informadas. Esta integración facilita la gestión de la producción en tiempo real, la optimización de recursos y la rápida adaptación a cambios en la demanda o en los diseños de producto.
En definitiva, los sistemas de conformado de láminas representan una convergencia avanzada de tecnologías mecánicas, electrónicas, informáticas y de automatización que transforman la materia prima en componentes metálicos complejos, con altos estándares de calidad, eficiencia y sostenibilidad. Su desarrollo y mejora continua son fundamentales para que las industrias puedan competir en un mercado global exigente, ofreciendo productos innovadores y adaptados a las necesidades del futuro.
Los sistemas de conformado de láminas metálicas continúan evolucionando impulsados por la convergencia de nuevas tecnologías que redefinen los procesos tradicionales, permitiendo una manufactura más inteligente, adaptable y sostenible. La incorporación de inteligencia artificial y aprendizaje automático en el control de estos sistemas ha abierto nuevas posibilidades para la optimización automática y continua del proceso productivo, donde las máquinas pueden “aprender” a partir de datos históricos y en tiempo real para ajustar parámetros, anticipar problemas y mejorar la calidad sin intervención humana constante.
La capacidad para recolectar y analizar grandes volúmenes de datos a través de sensores distribuidos en toda la línea de conformado permite implementar estrategias de mantenimiento predictivo, reduciendo paradas no planificadas y extendiendo la vida útil de los componentes críticos. Esto no solo mejora la eficiencia operativa, sino que también representa un ahorro económico importante al evitar reparaciones mayores y optimizar la gestión de repuestos.
La robótica colaborativa, o cobots, se integra cada vez más en estos sistemas para complementar la labor humana, ejecutando tareas que requieren alta precisión, repetitividad o condiciones peligrosas, mientras que el operador se encarga de la supervisión y toma de decisiones estratégicas. Esta simbiosis humano-máquina mejora la productividad y reduce riesgos laborales, además de permitir una mayor flexibilidad para adaptarse a cambios rápidos en los procesos o productos.
El uso de tecnologías de realidad aumentada y virtual para la capacitación, asistencia remota y mantenimiento ha demostrado ser un recurso valioso para reducir tiempos de formación y mejorar la eficiencia en las intervenciones técnicas. Operadores y técnicos pueden recibir instrucciones visuales y apoyo en tiempo real, lo que disminuye errores y acelera la resolución de incidencias.
En paralelo, el desarrollo de materiales avanzados, como aceros de alta resistencia, aleaciones ligeras y compuestos metálicos, plantea nuevos retos para los sistemas de conformado, que deben adaptar sus capacidades para trabajar con estas materias primas más exigentes sin comprometer la calidad o productividad. La mejora en los sistemas de control y la precisión de las máquinas es clave para lograr deformaciones complejas sin generar defectos, manteniendo la integridad y propiedades mecánicas del material.
La sostenibilidad se posiciona como un principio transversal, promoviendo no solo la eficiencia energética y la reducción de desperdicios, sino también el diseño de procesos que faciliten el reciclaje y la reutilización de materiales. Las empresas buscan minimizar su huella ambiental cumpliendo con regulaciones cada vez más estrictas y respondiendo a una creciente conciencia social sobre la responsabilidad ambiental.
Por último, la digitalización completa de los sistemas de conformado permite su integración dentro de fábricas inteligentes y cadenas de suministro conectadas, donde la información fluye libremente para optimizar desde la planificación y producción hasta la logística y atención al cliente. Esta integración facilita la personalización masiva, reducción de tiempos de entrega y mejora continua, elementos indispensables para competir en mercados globales altamente dinámicos y exigentes.
En suma, los sistemas de conformado de láminas metálicas representan un campo de innovación constante que combina ingeniería avanzada, tecnologías digitales y enfoques sostenibles para transformar la fabricación de componentes metálicos. Su desarrollo permanente es vital para que las industrias respondan a los desafíos actuales y anticipen las necesidades futuras, manteniendo la competitividad y excelencia en la producción metalmecánica.
Maquinaria para formar chapa metálica
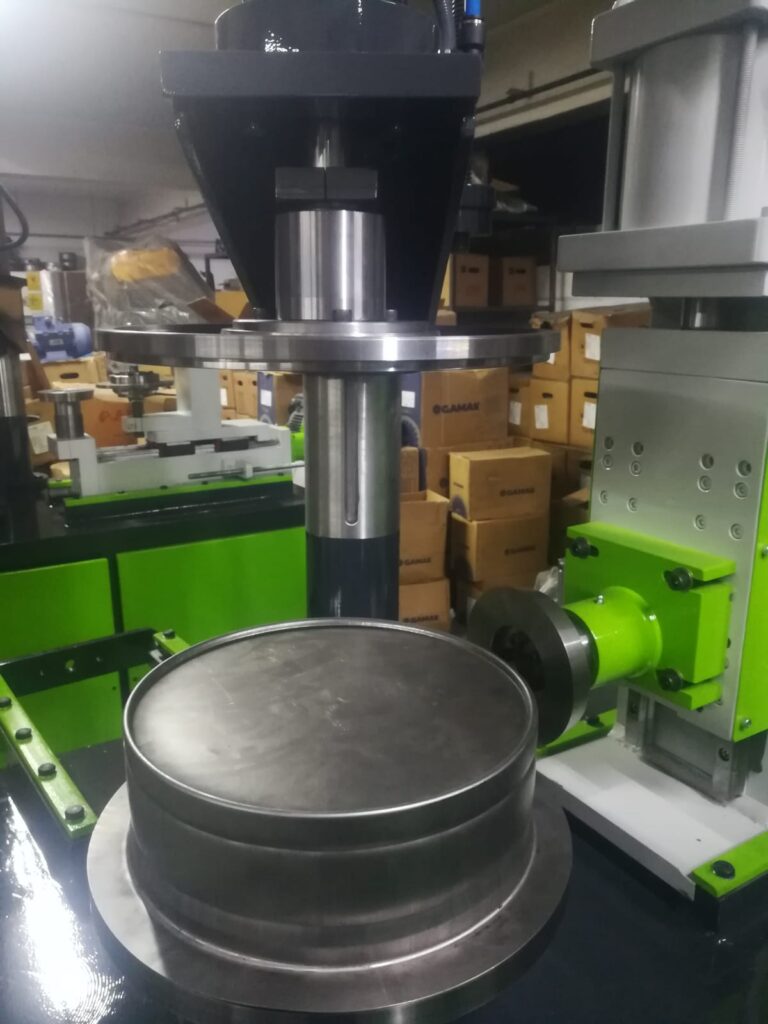
La maquinaria para formar chapa metálica es fundamental en la industria manufacturera, pues permite transformar láminas planas de metal en piezas con formas, dimensiones y propiedades específicas que son esenciales para una amplia variedad de aplicaciones. Estas máquinas están diseñadas para realizar procesos de deformación plástica controlada, donde la chapa metálica se somete a fuerzas que modifican su geometría sin romperse ni perder sus características mecánicas básicas.
Entre los equipos más comunes y versátiles en este ámbito se encuentran las prensas hidráulicas, que aplican fuerzas mediante sistemas hidráulicos ajustables y precisos. Gracias a su capacidad para controlar la presión y la velocidad durante todo el ciclo de conformado, son ideales para procesos que requieren embutido profundo, estirado, doblado o conformado de piezas volumétricas y complejas. Su flexibilidad y potencia las convierten en una opción preferida para trabajos con materiales de distintos grosores y resistencias.
Las prensas mecánicas, por otro lado, utilizan sistemas mecánicos de leva y biela para transmitir fuerza de manera rápida y repetitiva, lo que las hace óptimas para procesos de corte, punzonado y estampado a altas velocidades. Incorporan controles CNC que facilitan la programación de ciclos de trabajo, incrementando la precisión y permitiendo la fabricación en serie de componentes metálicos con alta consistencia dimensional.
Las prensas plegadoras o dobladoras especializadas permiten crear dobleces y ángulos precisos en las chapas metálicas. Equipadas con sistemas CNC, estas máquinas pueden programar secuencias complejas y asegurar la repetibilidad de los ángulos y radios, factores fundamentales en la producción de estructuras metálicas, carcasas y componentes industriales que requieren exactitud y acabado de calidad. Las versiones modernas de estas máquinas ofrecen mejoras en ergonomía, eficiencia energética y facilidad de operación.
Además, las máquinas de embutido y estirado están diseñadas para conformar piezas huecas o con volúmenes específicos, como tanques, recipientes o partes automotrices, mediante la aplicación de fuerzas controladas que evitan defectos típicos como arrugas o grietas. La incorporación de sistemas inteligentes que ajustan parámetros en tiempo real garantiza una producción más eficiente y piezas con mayor calidad.
Para procesos complementarios, las máquinas de repujado y acuñado permiten agregar relieves y texturas mediante presión localizada, siendo ampliamente utilizadas en la fabricación de piezas decorativas o con requerimientos funcionales específicos. Su automatización y control preciso permiten obtener acabados uniformes y repetibles.
En la preparación de la materia prima para el conformado, las máquinas de corte y punzonado, que pueden emplear tecnologías avanzadas como láser, plasma o chorro de agua, permiten obtener piezas con formas complejas y bordes limpios, listos para el proceso posterior. La precisión y rapidez de estos equipos son clave para mantener la eficiencia y calidad en la cadena productiva.
Finalmente, la integración de estas máquinas dentro de líneas automatizadas y sistemas de control digital ha transformado la manufactura de chapa metálica, permitiendo una producción más flexible, rápida y con menores costos operativos. La conectividad, la capacidad de monitoreo en tiempo real y la implementación de mantenimiento predictivo aseguran una operación continua y optimizada, además de facilitar la adaptación a las demandas cambiantes del mercado.
En conclusión, la maquinaria para formar chapa metálica es un conjunto avanzado de equipos que combinan potencia, precisión y tecnología para transformar láminas en componentes complejos y funcionales, siendo pieza clave en la fabricación de una gran variedad de productos industriales y de consumo, y su continua innovación es esencial para el desarrollo y competitividad de la industria metalmecánica.
La maquinaria para formar chapa metálica se ha convertido en un pilar esencial de la industria manufacturera moderna, debido a su capacidad para adaptar materiales planos y uniformes en piezas tridimensionales que cumplen con especificaciones técnicas rigurosas y variadas. Este tipo de maquinaria abarca una amplia gama de tecnologías y sistemas que se han desarrollado y perfeccionado para responder a la creciente complejidad de los diseños, la diversidad de materiales y la demanda por procesos eficientes y sostenibles.
El proceso de conformado de chapa implica someter la lámina metálica a esfuerzos que generan una deformación plástica controlada, modificando su forma sin comprometer su integridad estructural. Para ello, las máquinas deben ser capaces de aplicar fuerzas precisas, distribuirlas uniformemente y adaptar su comportamiento según el tipo de material y la geometría deseada. Por ejemplo, las prensas hidráulicas ofrecen una gran versatilidad, ya que permiten controlar la presión y velocidad de manera continua durante el ciclo de trabajo, posibilitando la fabricación de piezas con embutidos profundos y formas complejas, incluso en materiales de alta resistencia o gran espesor.
Las prensas mecánicas, aunque con un funcionamiento más tradicional basado en mecanismos de leva y biela, han evolucionado gracias a la incorporación de sistemas CNC que ofrecen control y programación avanzada de los movimientos y fuerzas. Estas máquinas destacan por su rapidez y capacidad para producción en serie, siendo indispensables en procesos de estampado, corte y punzonado donde la velocidad y precisión son críticas para la productividad y calidad.
En el ámbito del doblado, las prensas plegadoras han experimentado un importante desarrollo tecnológico. Equipadas con controles numéricos computarizados, permiten realizar dobleces con precisión milimétrica, programar secuencias complejas y adaptar los procesos a distintos grosores y tipos de metal. Estas máquinas son vitales en la fabricación de estructuras metálicas, paneles y carcasas que requieren ángulos específicos y acabados uniformes. Además, las mejoras en ergonomía y automatización facilitan el manejo y reducen el desgaste físico del operador.
La maquinaria para embutido y estirado aborda la conformación de piezas volumétricas y huecas, procesos que implican mayores desafíos debido a la necesidad de controlar tensiones y evitar defectos como arrugas o fisuras. Para esto, las máquinas incorporan sistemas hidráulicos avanzados que regulan la fuerza y velocidad, además de sensores que monitorean el comportamiento del material en tiempo real. Esta inteligencia incorporada permite optimizar el ciclo de conformado y garantizar la calidad final, incluso en aleaciones modernas que presentan dificultades adicionales para la deformación.
Los procesos complementarios como el repujado, acuñado y texturizado se realizan mediante máquinas especializadas que aplican presión localizada para crear relieves o patrones decorativos y funcionales. La automatización y control preciso en estas máquinas aseguran resultados uniformes y permiten integrar estas operaciones en líneas productivas automatizadas, aumentando la capacidad de producción y reduciendo los tiempos.
En cuanto a la preparación y corte de las láminas, las máquinas de corte por láser, plasma o chorro de agua han revolucionado el proceso al ofrecer cortes de alta precisión, sin generar zonas afectadas térmicamente o mecánicamente. Esto permite obtener piezas con geometrías complejas y bordes limpios, listas para ser conformadas, reduciendo retrabajos y desperdicios. La integración de estos equipos en líneas automatizadas agiliza el proceso productivo y garantiza un flujo constante de materiales.
La digitalización es un factor transformador en la maquinaria para formar chapa metálica. La incorporación de sensores, sistemas de control CNC, software de simulación y análisis de datos permiten no solo optimizar cada ciclo de trabajo, sino también anticipar fallas mediante mantenimiento predictivo, mejorar la calidad y adaptarse rápidamente a cambios en los diseños o en la producción. Esta conectividad facilita la integración con sistemas de gestión empresarial, contribuyendo a una manufactura inteligente y eficiente.
La sostenibilidad también está presente en el desarrollo de estas máquinas, con énfasis en el uso eficiente de energía mediante motores y sistemas hidráulicos de alta eficiencia, recuperación de energía, y reducción del uso de lubricantes y fluidos contaminantes. El diseño de procesos que minimizan desperdicios y permiten la reutilización de materiales refuerzan el compromiso ambiental de la industria metalmecánica.
La seguridad y ergonomía en estas máquinas han sido priorizadas para proteger a los operadores, implementando sistemas de detección, barreras de seguridad inteligentes, paradas de emergencia automáticas y diseño ergonómico de estaciones de trabajo. La automatización reduce la exposición a tareas peligrosas o repetitivas, mejorando las condiciones laborales y contribuyendo a la productividad.
En resumen, la maquinaria para formar chapa metálica es un conjunto complejo y avanzado de tecnologías que combina potencia, precisión, automatización y sostenibilidad para transformar láminas metálicas en componentes funcionales y de alta calidad. Su evolución continua es indispensable para que la industria pueda responder a los desafíos de mercados cada vez más exigentes, garantizando eficiencia, innovación y responsabilidad ambiental. Esta maquinaria no solo impulsa la producción, sino que también abre caminos hacia la fabricación digital, flexible y sostenible del futuro.
El avance continuo de la maquinaria para formar chapa metálica no solo responde a las exigencias de productividad y calidad, sino que también impulsa nuevas formas de diseñar y fabricar productos, permitiendo una mayor libertad creativa y adaptación a ciclos de desarrollo cada vez más cortos. La capacidad de estas máquinas para trabajar con una amplia variedad de materiales —desde aceros al carbono hasta aleaciones ligeras como el aluminio o incluso metales inoxidables complejos— las convierte en herramientas clave en sectores tan diversos como la automoción, la aeronáutica, la construcción, los electrodomésticos y la fabricación de maquinaria industrial.
La flexibilidad es un atributo cada vez más buscado en estas máquinas. Los sistemas modernos permiten cambios rápidos de herramientas, programación de múltiples formas en una misma línea y la producción de lotes pequeños sin perder eficiencia. Esto es fundamental para enfrentar las demandas actuales del mercado, donde la personalización del producto y la variación en los modelos son la norma. La integración de software de diseño asistido por computadora (CAD) y manufactura asistida por computadora (CAM) permite crear una conexión directa entre el diseño digital del producto y su ejecución en la máquina, reduciendo errores humanos y acelerando los ciclos de producción.
Otro aspecto crucial es la precisión dimensional. Muchas aplicaciones requieren tolerancias muy ajustadas, especialmente en industrias como la aeroespacial o la médica, donde cada milímetro cuenta. Para satisfacer estas necesidades, las máquinas incorporan medidores láser, reglas ópticas y sistemas de retroalimentación que permiten corregir la trayectoria o la fuerza de manera instantánea. Estos sistemas aseguran que incluso en procesos repetitivos o con materiales que pueden variar ligeramente entre lotes, el resultado final mantenga una calidad constante.
La automatización también ha llevado al desarrollo de celdas de trabajo robotizadas donde varias máquinas funcionan de forma sincronizada, alimentadas por robots que cargan y descargan piezas, las giran, las posicionan y las entregan listas para la siguiente etapa del proceso. Estas células de trabajo inteligentes se autoajustan mediante algoritmos que responden a cambios en la línea, ya sea por la introducción de un nuevo modelo o por condiciones variables en la materia prima. Este tipo de arquitectura modular y flexible representa el futuro de la fabricación en masa altamente personalizada.
Además, el uso de inteligencia artificial en el análisis de datos recopilados por los sensores de estas máquinas permite prever patrones que afectan la calidad o eficiencia de producción. Por ejemplo, una leve variación en la temperatura del entorno puede influir en el comportamiento del material, y sistemas inteligentes pueden sugerir ajustes en la configuración de la máquina antes de que se produzcan defectos. Esta capacidad de anticipación transforma la relación entre operador y máquina, haciendo de la producción un proceso más robusto y resiliente.
La conectividad con plataformas industriales en la nube permite que todas estas máquinas formen parte de un sistema mayor de gestión de operaciones y recursos. Esto facilita, entre otras cosas, el control remoto de las líneas, la actualización del software de los equipos sin detener la producción y la coordinación de varias fábricas o centros de producción en distintas ubicaciones. Así, no solo se estandarizan los procesos a escala global, sino que también se mejora la capacidad de respuesta ante la demanda o posibles interrupciones logísticas.
En lo que respecta al diseño y mantenimiento, las máquinas actuales están pensadas para facilitar el acceso a sus componentes, reducir los tiempos de intervención y maximizar la disponibilidad. El mantenimiento predictivo, basado en el análisis de vibraciones, consumo energético o temperatura interna de ciertos componentes, permite programar paradas de forma planificada y precisa, reduciendo al mínimo las pérdidas de tiempo y los costes asociados a fallos imprevistos. Esta estrategia, combinada con el soporte remoto ofrecido por muchos fabricantes, ha transformado el enfoque tradicional del mantenimiento, haciéndolo más eficiente y menos costoso.
Por otro lado, el impacto ambiental ha llevado a una revisión completa de los sistemas hidráulicos tradicionales, que solían ser intensivos en el uso de aceite y energía. Nuevas generaciones de maquinaria han adoptado tecnologías como la hidráulica servoaccionada, sistemas híbridos o directamente accionamientos eléctricos que eliminan la necesidad de circuitos hidráulicos. Esto reduce el consumo energético, mejora la limpieza del entorno de trabajo y simplifica el mantenimiento.
En definitiva, la maquinaria para formar chapa metálica no solo constituye una herramienta esencial de transformación de materiales, sino que se ha convertido en un componente inteligente de sistemas de producción más amplios, capaces de aprender, adaptarse y operar de forma autónoma. Su evolución constante refleja la convergencia entre la ingeniería mecánica, la electrónica, la informática y la sostenibilidad, asegurando que la industria de conformado de chapa siga siendo un motor de innovación, eficiencia y competitividad a escala global.
Máquinas para conformado de chapa
Las máquinas para conformado de chapa constituyen una categoría esencial dentro de la ingeniería de fabricación, ya que permiten transformar láminas metálicas planas en componentes funcionales con geometrías específicas mediante procesos de deformación plástica controlada. Estas máquinas no solo deben aplicar fuerzas precisas, sino también asegurar que cada operación mantenga la integridad estructural del material, las dimensiones exactas y la calidad superficial requerida por las especificaciones técnicas. En la actualidad, este tipo de maquinaria se encuentra profundamente integrada con sistemas digitales, controles automatizados y tecnologías de análisis de datos, lo que ha llevado el conformado de chapa a un nivel sin precedentes de precisión, velocidad y eficiencia.
Entre las máquinas más comunes y utilizadas se encuentran las prensas hidráulicas, las cuales funcionan mediante un sistema de pistones y fluidos presurizados capaces de generar grandes fuerzas. Estas son especialmente eficaces para procesos como el embutido profundo, el estirado y el repujado, donde se requiere una aplicación constante y regulable de presión durante todo el ciclo. Gracias a su flexibilidad, pueden adaptarse a una amplia variedad de materiales y formas, siendo ideales tanto para piezas simples como para componentes de geometrías complejas. Los sistemas hidráulicos actuales han mejorado notablemente en cuanto a eficiencia energética y control dinámico, incorporando bombas de caudal variable, servoválvulas y sensores de retroalimentación.
Las prensas mecánicas, por su parte, funcionan mediante mecanismos de cigüeñal y volante que transforman la energía rotacional en movimiento lineal. Su mayor ventaja radica en la velocidad del ciclo, lo que las hace muy apropiadas para procesos de estampado, punzonado y corte en líneas de producción de gran volumen. Su diseño más rígido permite operaciones rápidas y repetitivas con alta precisión, especialmente cuando están equipadas con controladores numéricos y sistemas automatizados de alimentación y evacuación de piezas. En entornos industriales donde el tiempo de ciclo es crítico, estas máquinas ofrecen una combinación eficiente de robustez y rendimiento.
Otro grupo importante lo constituyen las plegadoras CNC, diseñadas para ejecutar dobleces con exactitud milimétrica sobre láminas metálicas de distintos grosores. La tecnología de control numérico computarizado permite programar múltiples secuencias de doblado en una sola configuración, ajustando automáticamente la posición de las herramientas, el ángulo de aplicación y la presión necesaria. Estas máquinas son esenciales en sectores como la carpintería metálica, la fabricación de gabinetes eléctricos, envolventes, estructuras y componentes arquitectónicos. La integración de sistemas de retroalimentación ópticos y medición láser permite realizar ajustes en tiempo real durante el proceso de doblado para asegurar la uniformidad incluso con materiales de propiedades variables.
Asimismo, las embutidoras y estiradoras de chapa permiten conformar piezas huecas, recipientes, carcasas automotrices, lavabos, utensilios de cocina o depósitos metálicos. Estas máquinas ejercen presión controlada sobre la chapa mediante un punzón que la empuja hacia una matriz, y a menudo emplean un cojín hidráulico inferior que controla la resistencia de la lámina para evitar roturas o arrugas durante el embutido. Los avances en simulación de procesos y sensores de fuerza han permitido a estas máquinas trabajar con aleaciones livianas como el aluminio, sin comprometer la resistencia ni la estética de las piezas.
Además, las máquinas de rolado o roladoras están diseñadas para curvar y enrollar láminas metálicas a través de la presión ejercida por rodillos motorizados. Estos equipos permiten fabricar cilindros, conos y curvas suaves que luego pueden ser soldados, remachados o ensamblados para formar estructuras mayores. Su precisión en el manejo del radio de curvatura y la posibilidad de integrarlas con sistemas automatizados las convierte en herramientas versátiles para la industria de tanques, silos, conductos y componentes arquitectónicos.
Un desarrollo notable ha sido la implementación de estaciones de trabajo completamente automatizadas, donde varias de estas máquinas funcionan de forma integrada bajo el control de un sistema centralizado. En estas celdas, robots industriales se encargan del transporte de piezas, su posicionamiento exacto, la inspección por visión artificial y el almacenamiento de componentes terminados, todo ello coordinado mediante software de planificación y ejecución en tiempo real. Estas soluciones integradas representan el nivel más avanzado del conformado de chapa, permitiendo producciones flexibles, lotes pequeños y adaptabilidad inmediata a nuevas piezas sin necesidad de detener la producción.
Otro aspecto destacado es la sostenibilidad. Muchas máquinas de conformado actuales han sido rediseñadas para consumir menos energía, utilizar lubricantes biodegradables, reducir el desperdicio de material y facilitar el reciclaje. El diseño de matrices y procesos optimizados ayuda a minimizar los recortes innecesarios y aprovechar al máximo cada lámina, mientras que los sistemas de recuperación de energía y el uso de motores eficientes permiten reducir significativamente el impacto ambiental.
En conjunto, las máquinas para conformado de chapa representan una combinación de fuerza, precisión e inteligencia aplicada. Desde los procesos más tradicionales hasta los sistemas automatizados más modernos, su función esencial sigue siendo transformar un material aparentemente simple como la chapa en productos finales complejos, funcionales y de alto valor añadido. Esta maquinaria es, sin duda, una de las columnas vertebrales de la fabricación avanzada, clave para sectores industriales como el automotriz, aeroespacial, energético, de construcción y electrodomésticos. La evolución constante en diseño, automatización y eficiencia energética garantiza que seguirá siendo una tecnología indispensable en el futuro de la manufactura.
El universo de las máquinas para conformado de chapa continúa expandiéndose gracias a la integración de tecnologías avanzadas que permiten llevar la transformación de láminas metálicas a niveles de precisión, velocidad y adaptabilidad nunca antes vistos. Estas máquinas, tradicionalmente vinculadas a procesos mecánicos y térmicos, hoy son verdaderos nodos inteligentes dentro de cadenas de producción automatizadas, capaces de responder a comandos digitales, adaptarse a diferentes tipos de materiales y geometrías, y operar de manera continua sin perder la trazabilidad ni la calidad del producto final. En este entorno de fabricación inteligente, el diseño, la programación y el análisis de datos se combinan con la fuerza bruta de la maquinaria industrial, generando una sinergia que redefine lo que significa formar chapa metálica.
Uno de los mayores avances se ha dado en la digitalización del proceso completo. Las máquinas modernas no se limitan a ejecutar movimientos previamente programados; están equipadas con sensores de fuerza, temperatura, vibración y posición que recolectan datos en tiempo real para alimentar algoritmos de corrección automática. Estos datos se procesan en plataformas conectadas en red, permitiendo tomar decisiones operativas dinámicas: corregir desviaciones en el ángulo de un doblez, compensar la elasticidad de una aleación específica o ajustar la presión hidráulica en función del comportamiento del material durante el embutido. Esta inteligencia incorporada hace que el proceso sea mucho más robusto frente a variables externas como la humedad ambiental, pequeñas variaciones en el espesor de la chapa o incluso errores humanos.
Otro aspecto que ha transformado el papel de estas máquinas en la industria moderna es la interconectividad con otras fases del proceso productivo. Por medio de protocolos de comunicación industrial como OPC UA, MQTT o Profinet, una plegadora CNC o una prensa hidráulica puede intercambiar datos directamente con el sistema de gestión de producción, las estaciones de inspección automatizada, los robots de alimentación y almacenamiento, y los sistemas de mantenimiento predictivo. Esto permite una integración completa en fábricas que operan bajo el paradigma de la Industria 4.0, donde la producción no es una secuencia lineal de pasos sino un entorno flexible, autorregulado y optimizable desde múltiples puntos de control.
Además, el diseño de estas máquinas ha evolucionado para priorizar no solo la productividad, sino también la eficiencia energética y la sostenibilidad. Las nuevas generaciones de prensas y dobladoras emplean servomotores eléctricos de alta eficiencia o sistemas hidráulicos servoaccionados que solo consumen energía cuando es necesario aplicar fuerza. Esto representa un ahorro energético significativo, especialmente en líneas de producción de gran escala que operan 24/7. Asimismo, el uso de lubricantes secos, sistemas de recuperación de calor y tecnología de corte sin contacto (como el láser de fibra) contribuyen a minimizar el impacto ambiental del proceso de fabricación.
La robótica también ha ganado un rol protagonista en el conformado de chapa. Robots cartesianos, SCARA, de seis ejes o incluso robots colaborativos trabajan junto a las máquinas para realizar tareas como la carga y descarga de piezas, el posicionamiento en estaciones de trabajo, el transporte entre celdas o la manipulación precisa de chapas de gran tamaño o peso. Estos sistemas automatizados no solo mejoran la velocidad del proceso, sino que permiten manejar piezas que por sus dimensiones o geometrías serían difíciles o peligrosas de manipular manualmente. Además, al reducir la exposición del operario a los riesgos físicos del proceso, también se mejora la seguridad laboral y se reduce la fatiga.
A nivel de desarrollo de producto, las máquinas para conformado de chapa también permiten una mayor agilidad gracias al uso de software de simulación y análisis de elementos finitos. Antes de fabricar una sola pieza, los ingenieros pueden simular el comportamiento del material durante la deformación, predecir zonas de riesgo de fisura o pliegue, y ajustar las matrices, punzones o parámetros del proceso para evitar defectos. Esto acelera el desarrollo de nuevos productos, reduce la necesidad de prototipos físicos y permite una validación técnica más precisa desde etapas tempranas del diseño.
Cabe destacar también el papel fundamental que tienen estas máquinas en sectores industriales clave. En la industria automotriz, por ejemplo, se utilizan para formar piezas estructurales, paneles de carrocería, refuerzos internos y componentes de seguridad, muchas veces con materiales de alta resistencia que requieren procesos de embutido y doblado altamente controlados. En el sector aeroespacial, la exigencia en cuanto a tolerancias dimensionales y comportamiento mecánico es aún mayor, lo cual exige el uso de máquinas extremadamente precisas, capaces de trabajar con aleaciones livianas y costosas sin margen para error. Incluso en sectores como la construcción, los electrodomésticos, la electrónica de consumo o las energías renovables, estas máquinas permiten fabricar componentes estéticos y funcionales con rapidez y economía de escala.
En última instancia, las máquinas para conformado de chapa metálica ya no son simplemente herramientas industriales; son plataformas tecnológicas completas que encarnan la evolución de la manufactura hacia modelos más inteligentes, flexibles y sostenibles. Su desarrollo constante no solo responde a la necesidad de eficiencia y precisión, sino que también está moldeando una nueva forma de pensar la producción, en la que cada pieza fabricada forma parte de una red de decisiones automatizadas, análisis de datos en tiempo real y objetivos de mejora continua. En este contexto, la chapa metálica deja de ser una materia prima pasiva y se convierte en un lienzo técnico sobre el que las máquinas, guiadas por datos y algoritmos, construyen el futuro de la industria moderna.
A medida que la tecnología industrial continúa avanzando, las máquinas para conformado de chapa metálica están adoptando un enfoque aún más centrado en la adaptabilidad y el control de calidad automatizado. Uno de los grandes avances recientes es la capacidad de estas máquinas para operar en ciclos de producción mixtos, donde diferentes modelos de piezas, materiales y especificaciones pueden fabricarse en secuencia sin detener la línea ni requerir reconfiguraciones manuales. Esta capacidad, conocida como “fabricación en lote unitario,” permite a las empresas responder con agilidad a la personalización masiva y a las demandas cambiantes de los clientes, acortando el tiempo entre el diseño y la entrega del producto final.
El monitoreo en línea y la inspección automática son aspectos fundamentales en este nuevo entorno. Las máquinas actuales pueden integrar sistemas de visión artificial de alta resolución, que inspeccionan cada pieza durante y después del conformado para verificar dimensiones críticas, detectar imperfecciones superficiales, verificar geometrías y asegurar el cumplimiento de tolerancias. Esta inspección no solo garantiza la calidad, sino que también permite retroalimentar al sistema de control para realizar ajustes inmediatos en los parámetros del proceso si se detectan desviaciones, corrigiendo errores antes de que se repitan o se propaguen a lo largo de la producción.
Los avances en inteligencia artificial y aprendizaje automático permiten que estas máquinas aprendan de patrones históricos de fallos o variaciones en los materiales para anticipar problemas. Por ejemplo, si se detecta que una determinada aleación tiende a arrugarse en ciertas condiciones, el sistema puede ajustar automáticamente la velocidad de embutido o el perfil de presión para evitar defectos, sin necesidad de intervención humana. Esta capacidad de autoajuste representa una verdadera evolución hacia la fabricación autónoma, en la que la máquina se convierte en un agente activo dentro del proceso, con capacidad para adaptarse al contexto y optimizar su comportamiento.
El diseño de las herramientas también ha evolucionado profundamente. En lugar de fabricar moldes y matrices tradicionales mediante mecanizado, muchas empresas están utilizando impresión 3D con metales o materiales compuestos para producir herramientas personalizadas en menor tiempo y con geometrías optimizadas. Esto no solo reduce los costos y tiempos de desarrollo, sino que permite incorporar estructuras internas complejas, como canales de refrigeración o zonas de elasticidad variable, que mejoran la eficiencia del proceso y la calidad del producto final. Esta fabricación aditiva, combinada con simulaciones digitales, crea un entorno donde el diseño de herramientas y el diseño de producto están cada vez más interconectados y co-dependientes.
Otro componente clave del avance tecnológico es la integración del operario humano en el entorno digital. Las máquinas modernas para conformado de chapa suelen contar con interfaces gráficas intuitivas, paneles táctiles, sistemas de realidad aumentada para asistencia técnica, y conectividad móvil para diagnóstico remoto. Estas herramientas no solo facilitan la operación diaria, sino que también reducen la curva de aprendizaje, permitiendo que los trabajadores se conviertan en supervisores de sistemas complejos sin necesidad de conocimientos profundos en programación o automatización.
Incluso el mantenimiento de estas máquinas se ha transformado. Las alertas predictivas no solo notifican cuándo será necesario un cambio de aceite o la sustitución de una válvula, sino que también ofrecen recomendaciones precisas basadas en el uso real, el historial de rendimiento y las condiciones ambientales. Muchas máquinas incluyen módulos de autodiagnóstico que evalúan el estado de los componentes críticos, generan reportes y comunican directamente con el departamento técnico o con el fabricante, reduciendo tiempos muertos y evitando paradas inesperadas.
En lo referente al entorno de producción, las máquinas para conformado de chapa metálica también se están integrando en sistemas más amplios que comprenden logística automatizada, trazabilidad de materiales, y planificación dinámica de la producción. Esto significa que no solo se forma la chapa, sino que se rastrea su origen, su paso por cada estación, el lote al que pertenece, su historial de inspección y hasta su destino logístico. Esta trazabilidad es fundamental para industrias reguladas como la aeroespacial, la médica o la alimentaria, donde cada componente debe cumplir con exigencias de documentación, validación y seguridad muy estrictas.
Finalmente, es importante subrayar que todas estas transformaciones no hacen que la maquinaria para conformado de chapa sea más compleja en su manejo, sino más intuitiva, segura y eficiente. La tendencia es hacia un entorno de producción altamente automatizado pero al mismo tiempo accesible, donde los operarios interactúan con las máquinas mediante entornos digitales amigables, la inteligencia artificial colabora en las decisiones y la eficiencia del proceso se mide en tiempo real con indicadores claros y visuales.
En resumen, el futuro de las máquinas para conformado de chapa metálica ya no se define solamente por su capacidad física para doblar, cortar o embutir, sino por su nivel de inteligencia, su flexibilidad operativa, su integración digital y su capacidad para generar productos de alta calidad de forma sostenible, ágil y personalizada. Este nuevo paradigma consolida a estas máquinas como piezas centrales en la arquitectura de la fábrica del futuro: una fábrica automatizada, conectada y capaz de reinventarse con cada nuevo desafío de la industria.
Equipos de conformado de chapa
Los equipos de conformado de chapa representan el núcleo de una amplia gama de procesos industriales que transforman láminas metálicas planas en componentes funcionales, complejos y altamente precisos. Su evolución ha estado marcada por la necesidad de responder a requerimientos cada vez más exigentes en términos de geometría, tolerancia, eficiencia energética y automatización. Estos equipos no solo deben aplicar fuerzas adecuadas para moldear el material sin dañarlo, sino también integrarse a sistemas de producción inteligentes que optimizan cada etapa del ciclo de fabricación, desde la entrada de materia prima hasta el control de calidad final.
Dentro de este conjunto, destacan las prensas hidráulicas y mecánicas, que siguen siendo el estándar para tareas como el embutido, el punzonado, el estampado o el recorte. Las prensas hidráulicas permiten aplicar presiones controladas con gran precisión, ideales para trabajos que requieren adaptabilidad y fuerza variable, como el embutido profundo o el conformado de piezas con espesores irregulares. Por su parte, las prensas mecánicas destacan por su alta velocidad de trabajo, siendo la elección habitual para producción en masa con tiempos de ciclo reducidos, especialmente en el sector automotriz o de electrodomésticos. En ambos casos, los equipos modernos cuentan con controles CNC que permiten ajustar todos los parámetros de operación, memorizar configuraciones y asegurar una repetibilidad exacta de cada operación.
También son fundamentales las plegadoras CNC, que permiten realizar dobleces controlados con gran exactitud. Estos equipos están equipados con sistemas de retroalimentación automática, medición en tiempo real y compensación de flexión, lo que garantiza que cada pieza mantenga su forma sin importar pequeñas variaciones en el grosor o la composición del material. Son herramientas indispensables en la fabricación de gabinetes eléctricos, envolventes metálicas, estructuras tubulares o perfiles personalizados, donde cada ángulo y cada milímetro cuentan.
Además, existen equipos de rolado o curvado, diseñados para transformar chapa plana en cilindros, conos o formas curvas mediante rodillos motorizados. Estos equipos pueden operar en frío o en caliente y se utilizan ampliamente en la industria de tanques, tuberías, silos o estructuras arquitectónicas. Su control automático permite manejar radios variables y programar múltiples pasadas, adaptándose incluso a materiales de alta resistencia o gran espesor.
Los equipos de embutido, por su parte, están optimizados para conformar piezas huecas mediante la acción combinada de punzones y matrices. Incluyen sistemas de cojín hidráulico para controlar la presión de sujeción de la chapa y evitar arrugas o rupturas, especialmente al trabajar con geometrías complejas o materiales sensibles como aleaciones ligeras. Son muy utilizados en la producción de carcasas, utensilios de cocina, componentes estructurales automotrices o elementos de almacenamiento metálicos.
Otro tipo de equipo esencial es el punzonador CNC, que utiliza herramientas intercambiables y programación digital para perforar, cortar o marcar chapas con rapidez y flexibilidad. Su capacidad para realizar múltiples operaciones en una misma pieza, sin necesidad de cambiar de estación, lo convierte en una solución rentable para series cortas o producción de prototipos. Puede integrarse con cargadores automáticos y sistemas de apilado, optimizando el flujo de trabajo y reduciendo el tiempo de intervención humana.
En paralelo, los equipos de corte por láser, plasma o chorro de agua completan el ecosistema de conformado de chapa, proporcionando la preparación precisa del material antes de su transformación final. Estas tecnologías permiten cortes limpios, sin rebaba y con gran libertad geométrica, lo que resulta fundamental cuando se trabaja con piezas decorativas, estructuras livianas o componentes que requieren ensamblaje posterior sin mecanizado adicional.
Los equipos modernos de conformado también están diseñados para operar dentro de células automatizadas, donde robots industriales o sistemas de alimentación programada manipulan las piezas, las trasladan de una estación a otra, y las posicionan con exactitud para cada operación. Este enfoque no solo incrementa la productividad, sino que permite mantener altos estándares de calidad y uniformidad, reducir riesgos laborales y optimizar el uso de espacio en planta.
Finalmente, toda esta maquinaria se complementa con software de simulación y control que permite prever deformaciones, planificar secuencias de trabajo, detectar interferencias o incluso predecir fallos de herramientas. La trazabilidad digital de cada pieza, desde su diseño hasta su conformación, forma parte de un enfoque integral que une mecánica, electrónica y datos, abriendo paso a fábricas cada vez más inteligentes y autosuficientes.
En definitiva, los equipos de conformado de chapa han trascendido su rol tradicional como máquinas de fuerza para convertirse en plataformas tecnológicas avanzadas, capaces de ofrecer precisión, flexibilidad y conectividad en cada operación. Ya no son solo parte de la línea de producción: son el corazón de una manufactura moderna, digital y orientada a la excelencia.
En la actualidad, los equipos de conformado de chapa no solo representan la base técnica para la transformación de láminas metálicas, sino que son la columna vertebral de una nueva era de manufactura donde convergen precisión mecánica, automatización inteligente y sostenibilidad productiva. Lejos de limitarse a operaciones convencionales, estas máquinas se han convertido en nodos tecnológicos avanzados, capaces de interactuar en tiempo real con sistemas de diseño, planificación, logística y control de calidad, permitiendo la producción flexible de piezas cada vez más complejas, en menos tiempo y con una eficiencia energética superior.
En el núcleo de estos sistemas se encuentran las prensas, tanto hidráulicas como mecánicas, que durante décadas han sido el motor de procesos como el embutido, el estirado, el corte y el repujado. Las prensas hidráulicas modernas están equipadas con unidades de potencia servoaccionadas que permiten un control dinámico de la fuerza aplicada en función de la resistencia del material en tiempo real. Esto no solo optimiza el ciclo de conformado, sino que reduce el desgaste de los componentes internos y evita errores como la formación de grietas o deformaciones asimétricas. La precisión con la que estas máquinas pueden regular el flujo de presión hidráulica permite que materiales tradicionalmente difíciles de trabajar, como aceros inoxidables endurecidos, aleaciones de aluminio o compuestos multicapa, puedan procesarse de forma segura, predecible y repetible.
Las prensas mecánicas, por otro lado, destacan por su velocidad de trabajo y su robustez, siendo ideales para series de producción masiva. La incorporación de sistemas de sincronización y automatización digital ha elevado sus capacidades, permitiendo ejecutar operaciones complejas en cuestión de segundos con mínimas tolerancias de error. Estas prensas están diseñadas para integrarse en líneas automáticas donde el ritmo de producción debe mantenerse sin interrupciones, como sucede en las fábricas de componentes automotrices o electrónicos.
Complementando a las prensas están las plegadoras CNC, que han evolucionado hasta convertirse en estaciones de trabajo extremadamente versátiles. Su precisión angular, combinada con la posibilidad de realizar ajustes dinámicos en la fuerza, la posición y la velocidad, hace posible doblar perfiles de geometría variable sin necesidad de cambiar herramientas entre piezas. Este nivel de adaptabilidad es esencial en la producción de envolventes metálicos, gabinetes, perfiles estructurales y piezas de diseño arquitectónico, donde el diseño cambia con frecuencia pero la calidad debe mantenerse constante. El uso de escáneres ópticos y sensores láser permite verificar en tiempo real la geometría de cada doblez, y los datos generados pueden ser almacenados para análisis posteriores o para la mejora continua del proceso.
En paralelo, los equipos de embutido profundo permiten producir piezas huecas de alta complejidad geométrica, como tanques, carcasas, cubiertas o recipientes de presión. Estas máquinas requieren un control exacto de la interacción entre punzón, matriz y prensa de retención, y muchos de los modelos actuales incluyen algoritmos que ajustan la curva de velocidad del punzón para reducir la tensión localizada en la chapa. Los procesos son asistidos por simulaciones digitales en las que se predice con antelación la forma del material en cada etapa, identificando zonas críticas donde podrían aparecer arrugas, roturas o tensiones residuales. Estos resultados se utilizan luego para ajustar automáticamente la programación de la máquina antes de iniciar la producción real.
Además, los equipos de rolado y curvado de chapa han alcanzado un nivel de precisión tal que permiten formar cilindros, conos o superficies cóncavas de gran tamaño sin necesidad de mecanizado posterior. Estos equipos, que en versiones anteriores operaban mediante presión manual o hidráulica, hoy están automatizados y equipados con control numérico que regula la presión y velocidad de cada rodillo con precisión absoluta. Esta tecnología es indispensable en la fabricación de estructuras como depósitos, conductos de ventilación, componentes para turbinas eólicas o instalaciones industriales de gran envergadura, donde las tolerancias deben mantenerse incluso a lo largo de varios metros de longitud.
Una dimensión crucial en el funcionamiento actual de los equipos de conformado de chapa es su integración con entornos automatizados y robotizados. Las piezas ya no son manipuladas manualmente entre una máquina y otra, sino que robots industriales o sistemas de transporte inteligentes se encargan de tomar la chapa desde el área de corte, posicionarla con exactitud en la estación de conformado, girarla si es necesario y transferirla luego a procesos secundarios como punzonado, soldadura o inspección. Este flujo continuo no solo elimina tiempos muertos, sino que también mejora la ergonomía del entorno de trabajo, reduce el riesgo de accidente humano y mantiene la coherencia dimensional entre piezas.
La trazabilidad y el monitoreo en tiempo real completan el panorama tecnológico. Cada equipo de conformado puede registrar información detallada sobre el ciclo de trabajo de cada pieza: temperatura del material, presión aplicada, tiempos de contacto, fuerza ejercida, desplazamiento real y más. Esta información se transmite al sistema central de la planta, donde puede ser utilizada para análisis de eficiencia, mantenimiento predictivo, control de calidad estadístico o auditorías de certificación. Los datos acumulados también permiten crear gemelos digitales de los equipos y procesos, simulando escenarios para anticipar el comportamiento del sistema bajo distintas condiciones o al introducir nuevas piezas en el flujo de trabajo.
Todo este avance tecnológico no sería posible sin un diseño centrado en la eficiencia energética, la facilidad de mantenimiento y la integración digital. Los nuevos equipos están construidos con estructuras reforzadas pero más ligeras, sistemas hidráulicos de bajo consumo, motores eléctricos de alto rendimiento, y interfaces amigables que permiten a los operarios controlar complejas operaciones con una pantalla táctil o una aplicación conectada. El mantenimiento predictivo reemplaza al mantenimiento reactivo, permitiendo intervenir en la máquina antes de que se produzca una falla, y los repuestos se gestionan de forma anticipada con sistemas inteligentes que detectan desgaste, fricción o calentamiento anómalos.
En conclusión, los equipos de conformado de chapa de hoy no son simples herramientas industriales: son plataformas tecnológicas integradas, conectadas e inteligentes, capaces de procesar metales con exactitud milimétrica, registrar cada variable del proceso y adaptarse a entornos de producción flexibles y exigentes. Representan un puente entre la ingeniería tradicional y la manufactura digital, y su evolución constante seguirá definiendo la forma en que concebimos, diseñamos y producimos todo tipo de estructuras y componentes metálicos en el siglo XXI.
La progresiva evolución de los equipos de conformado de chapa no solo ha transformado la forma en que se producen componentes metálicos, sino que también ha redefinido la interacción entre diseño, fabricación y logística industrial. En este nuevo paradigma, la chapa metálica no es simplemente un material base, sino una plataforma que responde activamente a procesos programados, ajustes automáticos y decisiones tomadas por sistemas integrados que coordinan toda la línea de producción. Desde la selección del tipo de acero o aleación hasta el acabado final, cada etapa está regulada por herramientas tecnológicas que maximizan la eficiencia, reducen errores y garantizan la calidad.
Uno de los desarrollos más importantes ha sido la incorporación de sistemas de control adaptativo en tiempo real. Estos controles se encargan de ajustar de forma continua los parámetros del proceso basándose en variables como la elasticidad de la chapa, su temperatura, el grado de tensión acumulada o el comportamiento de la herramienta en ciclos previos. Por ejemplo, si durante un ciclo de embutido el sistema detecta que la chapa ofrece más resistencia de la habitual —lo que podría deberse a una variación en el lote del material— el control adaptativo ajusta automáticamente la velocidad del punzón y la presión del cojín para evitar rupturas. Este tipo de respuestas instantáneas, imposibles en los sistemas tradicionales, son el resultado de años de desarrollo en automatización avanzada y algoritmos de autoaprendizaje aplicados a la maquinaria.
Asimismo, se ha incrementado la capacidad de personalización en serie, una demanda creciente en industrias como la automoción, la electrónica y los electrodomésticos, donde cada pieza puede requerir pequeñas variaciones según el modelo o el cliente. Los equipos de conformado actuales permiten cambiar matrices, programaciones, herramientas y parámetros sin detener la línea de producción, lo que abre la posibilidad de producir piezas totalmente distintas en una misma jornada con solo modificar las instrucciones digitales enviadas desde el sistema central de planificación. Esto no solo aumenta la versatilidad de la maquinaria, sino que también reduce drásticamente los costos asociados a los cambios de modelo, lo que hasta hace poco era una limitación en la producción de bajo volumen o personalizada.
También destaca la influencia que ha tenido la fabricación aditiva (impresión 3D) en la generación de utillajes y componentes auxiliares de los equipos de conformado. Matrices, punzones, apoyos y fijaciones personalizadas se fabrican ahora en materiales compuestos o en metales especiales mediante impresión tridimensional, reduciendo el tiempo de desarrollo de herramientas de semanas a días. Esta rapidez es especialmente útil en sectores que trabajan con prototipos o que deben reaccionar con agilidad ante nuevas necesidades del mercado. Además, las herramientas fabricadas aditivamente pueden incorporar soluciones de diseño que serían imposibles por métodos convencionales, como canales internos de refrigeración o geometrías de alivio de tensiones que prolongan su vida útil y mejoran la calidad del proceso.
Por otro lado, la sostenibilidad y el consumo responsable de recursos también se han convertido en objetivos clave en el desarrollo de nuevos equipos. La reducción del desperdicio de material se logra mediante un diseño optimizado de procesos de corte y troquelado, el reciclaje automático de retales y el uso de software de anidado inteligente que maximiza el aprovechamiento de cada lámina. En cuanto al consumo energético, los nuevos sistemas hidráulicos solo activan la bomba cuando es necesario aplicar presión, a diferencia de los antiguos sistemas de flujo constante. Esto se traduce en una reducción significativa del consumo eléctrico, disminución del calentamiento interno y aumento de la vida útil de los componentes del sistema. A su vez, muchas fábricas están implementando equipos alimentados con fuentes de energía renovable, cerrando así un ciclo de producción más limpio y eficiente.
En este contexto de innovación, también se está transformando el papel de los operarios. Ya no se trata únicamente de técnicos que manipulan maquinaria pesada, sino de supervisores digitales que interpretan datos, configuran procesos en pantallas táctiles, resuelven incidencias mediante diagnósticos asistidos por IA y coordinan la colaboración entre hombre y máquina. Para facilitar esta transición, los fabricantes de maquinaria están incorporando interfaces cada vez más visuales e intuitivas, así como entornos de realidad aumentada o formación virtual que permiten al personal capacitarse sin detener la producción. Esta combinación de tecnología y talento humano es uno de los motores clave de la industria moderna.
La conexión en red de todos los equipos dentro de una planta también permite operar con lógica distribuida: cada máquina comparte datos sobre su estado, consumo, eficiencia y rendimiento con un sistema central, que redistribuye tareas, reorganiza prioridades y activa procesos de mantenimiento o recarga según sea necesario. Esta lógica de “fábrica conectada” también permite que la producción no se detenga frente a incidentes inesperados. Si un equipo entra en mantenimiento, otro puede asumir su función o redistribuir la carga de trabajo para que el flujo de piezas continúe, lo que da como resultado una cadena productiva más resiliente y autosuficiente.
A futuro, el desarrollo de los equipos de conformado de chapa apunta a una mayor autonomía operativa, capacidades de autoaprendizaje y la posibilidad de producir piezas complejas en una sola estación, reduciendo el número de etapas necesarias y, por tanto, los costos y tiempos asociados. El uso de inteligencia artificial para analizar big data de producción, predecir la vida útil de componentes, adaptar procesos a materiales nuevos o incluso sugerir rediseños de piezas con mejor comportamiento estructural será cada vez más común. La máquina no solo formará chapa, sino que interpretará el comportamiento del material, aprenderá de sus errores y propondrá mejoras continuas.
En definitiva, los equipos de conformado de chapa han superado su antigua función de ser simplemente herramientas de presión o corte. Hoy son dispositivos ciberfísicos, conectados, inteligentes y precisos, que forman parte de una red de manufactura interconectada y adaptable. Su evolución es el reflejo directo de las exigencias de un mercado que ya no se conforma con volumen, sino que exige precisión, personalización, velocidad y sostenibilidad. Y todo esto, sin comprometer la robustez mecánica ni la excelencia en los acabados, lo cual convierte al conformado de chapa en una de las disciplinas industriales más dinámicas y tecnológicamente avanzadas de nuestro tiempo.
Máquinas de fabricación de piezas metálicas
Las máquinas de fabricación de piezas metálicas constituyen una parte esencial del ecosistema industrial moderno, ya que permiten transformar materiales metálicos en productos acabados o semielaborados con altos niveles de precisión, resistencia y repetibilidad. Estas máquinas abarcan una variedad de tecnologías que van desde la conformación mecánica y térmica hasta el arranque de viruta, la soldadura, el corte avanzado y la fabricación aditiva, y están presentes en prácticamente todos los sectores industriales: automotriz, aeronáutico, ferroviario, construcción, energía, electrodomésticos, defensa y maquinaria pesada, entre otros. Su evolución ha sido impulsada por la necesidad de aumentar la productividad, reducir tiempos de entrega, minimizar desperdicios y adaptarse a geometrías cada vez más complejas.
En el ámbito del conformado, destacan prensas hidráulicas y mecánicas que permiten procesos como embutición, doblado, punzonado, repujado o laminado. Estas máquinas utilizan grandes fuerzas para deformar plásticamente láminas, tubos o perfiles metálicos sin romperlos, generando así estructuras huecas, carcasas, superficies curvadas y componentes estructurales. En particular, las prensas hidráulicas modernas integran sistemas de control servoaccionado, retroalimentación en tiempo real y ajustes automáticos que garantizan una deformación uniforme incluso en materiales difíciles como aceros de alta resistencia o aleaciones de aluminio y titanio. Estos sistemas, además, están diseñados para consumir solo la energía estrictamente necesaria durante cada ciclo, contribuyendo a procesos más sostenibles.
Por otro lado, el mecanizado convencional y CNC (control numérico computarizado) representa otro pilar clave. Centros de torneado, fresadoras, taladros, rectificadoras y máquinas multitarea permiten transformar piezas brutas mediante arranque de viruta, con tolerancias del orden de micras. Estos equipos no solo realizan cortes precisos, sino también acabados superficiales, perforaciones complejas, roscados internos o ranuras, lo que los convierte en imprescindibles para piezas de precisión, como componentes de motores, transmisiones, moldes, matrices, piezas hidráulicas o herramientas de corte. Las máquinas CNC actuales incorporan simulación previa al mecanizado, monitoreo en línea de herramientas, compensación térmica y ajustes automáticos en función del desgaste, lo que eleva la calidad y reduce la intervención del operario.
También tienen un papel destacado las máquinas de corte, como las de láser de fibra, plasma CNC, oxicorte y chorro de agua. Estas permiten separar con extrema precisión piezas de láminas metálicas o placas gruesas, sin necesidad de contacto físico y con mínima deformación térmica, en el caso del láser. Su programación digital facilita la creación de geometrías personalizadas y de alta complejidad, y su velocidad y exactitud las hacen indispensables en líneas de producción automatizadas, donde cada segundo y cada milímetro cuentan.
En paralelo, las máquinas de soldadura —ya sean por arco, MIG/MAG, TIG, láser, resistencia o fricción— unen piezas metálicas de forma permanente y controlada. Estas máquinas, hoy en día, operan muchas veces en estaciones robotizadas, donde brazos automatizados ejecutan cordones de soldadura perfectos, con trayectorias repetibles, en atmósferas controladas y sin interrupciones. La calidad del cordón, la penetración y la protección gaseosa se controlan con sensores y sistemas de visión que garantizan la integridad de las uniones, incluso en aplicaciones críticas como en aeronáutica o estructuras de presión.
La fabricación aditiva metálica ha ganado también un espacio creciente. Impresoras 3D de metales por sinterizado láser (SLM, DMLS) o por deposición de energía dirigida (DED) permiten producir piezas de geometría compleja directamente a partir de polvo metálico, sin necesidad de moldes o utillajes. Esta tecnología es ideal para prototipos funcionales, componentes ligeros, estructuras topológicamente optimizadas y piezas imposibles de obtener mediante métodos convencionales. En sectores como aeroespacial, médico o energía, se utiliza ya para producir componentes en acero inoxidable, titanio, Inconel, cobre o aluminio con propiedades mecánicas comparables a los procesos de forja.
A nivel de integración, muchas de estas máquinas están conectadas entre sí mediante sistemas MES (Manufacturing Execution System), SCADA y plataformas industriales IIoT que permiten la gestión completa de la producción: planificación de órdenes, monitoreo del estado de cada máquina, control de inventario, calidad y mantenimiento predictivo. La trazabilidad es total: cada pieza producida tiene un historial digital de su proceso, desde la materia prima hasta el tratamiento térmico o recubrimiento final. Esta digitalización permite detectar desviaciones, optimizar tiempos de ciclo, gestionar cuellos de botella y tomar decisiones estratégicas con base en datos reales.
Además, los avances en automatización han permitido que estas máquinas trabajen en líneas de producción sin intervención humana directa, gracias a la integración con robots, sistemas de transporte autónomos, sensores inteligentes y estaciones de inspección óptica. Todo esto conduce a una fábrica más flexible, capaz de adaptarse rápidamente a cambios de producto, aumentar la eficiencia energética, reducir el desperdicio y garantizar una calidad constante incluso en series cortas o producción bajo demanda.
En resumen, las máquinas de fabricación de piezas metálicas ya no son simples herramientas, sino sistemas de producción avanzados que combinan fuerza, precisión, inteligencia digital y adaptabilidad. Su capacidad para transformar el metal en productos funcionales con rapidez, calidad y bajo costo las convierte en un recurso imprescindible en la industria moderna, marcando el ritmo de la innovación en múltiples sectores. El futuro de la manufactura metálica se apoya en ellas, no solo por lo que hacen, sino por cómo lo hacen: con eficiencia, conectividad y evolución constante.
En el contexto industrial contemporáneo, las máquinas de fabricación de piezas metálicas representan mucho más que simples instrumentos de transformación material: son elementos centrales dentro de un ecosistema productivo digitalizado, donde cada operación forma parte de un flujo de información, control, análisis y retroalimentación continua. Su evolución ha estado guiada por múltiples exigencias, entre ellas la búsqueda de precisión extrema, la reducción del tiempo de ciclo, la mejora en la calidad superficial y estructural de los productos y, especialmente, la capacidad de adaptarse de manera ágil a los constantes cambios en el diseño de piezas, materiales empleados y volúmenes de producción. En este sentido, la máquina ya no se concibe como una herramienta aislada, sino como un nodo interconectado de una cadena industrial mucho más amplia y dinámica.
Entre los grupos más representativos de estas máquinas destacan las que trabajan por conformado, arranque de viruta, corte, unión y adición de material. Cada una responde a necesidades específicas y, en conjunto, forman el abanico completo de opciones para fabricar casi cualquier componente metálico, desde una tuerca de precisión hasta una carcasa estructural para un vehículo aeroespacial. Las prensas hidráulicas y mecánicas, por ejemplo, se utilizan para modificar la forma del metal aplicando grandes fuerzas de manera controlada, deformando láminas, perfiles o tubos sin generar desperdicios significativos. En sus versiones más avanzadas, estas máquinas cuentan con sistemas servoaccionados, retroalimentación en tiempo real mediante sensores y software de control adaptativo que modifica los parámetros de operación en función del comportamiento del material durante el proceso. Esto es especialmente útil cuando se trabaja con metales sensibles a la fatiga, como el titanio, o en geometrías complejas donde una fuerza mal distribuida podría generar grietas o deformaciones incontroladas.
Por otro lado, el mecanizado CNC ha revolucionado la fabricación de piezas metálicas con formas tridimensionales complejas o tolerancias extremadamente ajustadas. Centros de mecanizado de cinco ejes, tornos de doble husillo, fresadoras de alta velocidad y rectificadoras cilíndricas o planas forman parte de una red de máquinas capaces de esculpir piezas con exactitud micrométrica, muchas veces en una sola sujeción. Estas máquinas operan con códigos numéricos generados a partir de modelos CAD/CAM, lo que garantiza una precisión absoluta entre el diseño digital y la pieza física, minimizando errores humanos e incrementando la repetibilidad. Además, gracias a la inclusión de sondas de medición internas, sistemas de cambio automático de herramientas y control térmico del entorno, es posible mantener estables las condiciones del proceso incluso durante largas jornadas de producción continua.
Las tecnologías de corte, como el láser de fibra óptica, el chorro de agua y el plasma CNC, complementan el trabajo de conformado y mecanizado. Estas máquinas permiten realizar cortes rápidos, limpios y con gran libertad geométrica sobre láminas, placas o tubos metálicos. Son especialmente útiles en procesos donde el diseño puede cambiar con frecuencia o cuando se requiere reducir al máximo la zona afectada por el calor, como sucede en materiales tratados térmicamente o aleaciones con alto contenido de cromo y níquel. Además, el corte por láser es altamente automatizable, integrándose en líneas robotizadas donde la carga, descarga, etiquetado y apilado de piezas se realiza sin intervención humana. Esto permite no solo acelerar el proceso de producción, sino también garantizar la trazabilidad completa de cada lote, una exigencia cada vez más frecuente en industrias como la aeroespacial o la médica.
Otro campo esencial dentro de la fabricación de piezas metálicas lo representan las máquinas de soldadura industrial. Estas permiten unir componentes metálicos con gran robustez y durabilidad, mediante procesos como soldadura MIG/MAG, TIG, por resistencia, por fricción o incluso por láser. En las líneas de producción automatizadas, los sistemas de soldadura robotizada garantizan una calidad constante en cada unión, incluso cuando se trata de miles de cordones por turno. Equipadas con cámaras de visión artificial, sensores de penetración y software de corrección de trayectoria en tiempo real, estas estaciones no solo ejecutan la soldadura, sino que evalúan automáticamente su calidad y registran los parámetros de cada operación para análisis posteriores. Esto es fundamental en sectores donde la seguridad estructural es crítica y cada unión debe cumplir con normas internacionales estrictas.
Además de estos métodos tradicionales, la fabricación aditiva metálica se ha incorporado en los últimos años como una alternativa disruptiva para producir piezas con geometrías imposibles de obtener mediante mecanizado o fundición. Utilizando tecnologías como el sinterizado láser directo (DMLS) o la deposición de energía dirigida (DED), estas máquinas construyen componentes capa por capa a partir de polvo metálico fundido por láser o haz de electrones. Si bien aún se usan principalmente para aplicaciones de alto valor añadido —como componentes aeroespaciales, médicos o de I+D—, su integración en entornos industriales reales se está acelerando gracias a la mejora en la velocidad de impresión, la reducción de costos de los materiales y la validación de sus propiedades mecánicas.
Todos estos equipos, sin importar su principio de funcionamiento, tienden hoy a una misma dirección: la conectividad total. Las fábricas modernas ya no se basan únicamente en la destreza operativa, sino en el flujo inteligente de datos. Las máquinas recopilan información sobre cada ciclo, cada pieza, cada variable del proceso, y la comparten en tiempo real con plataformas digitales que gestionan la producción, detectan ineficiencias, programan mantenimientos preventivos y generan análisis predictivos. Este modelo de operación en red, conocido como manufactura inteligente o Industria 4.0, ha permitido mejorar radicalmente la eficiencia, la calidad y la capacidad de respuesta de las plantas productivas ante cambios en la demanda o interrupciones logísticas.
El factor humano tampoco ha desaparecido. Lo que ha ocurrido es una transformación profunda del rol del operario. Las nuevas generaciones de máquinas están diseñadas para interactuar con sus usuarios mediante interfaces intuitivas, pantallas táctiles, realidad aumentada y entornos de simulación virtual. El operario ya no necesita memorizar secuencias ni realizar ajustes manuales complejos: ahora interpreta información, supervisa procesos automáticos y toma decisiones con base en datos que la propia máquina le entrega. Esta evolución también ha dado lugar a una formación profesional más especializada, donde convergen conocimientos de mecánica, automatización, electrónica y análisis de datos.
En síntesis, las máquinas de fabricación de piezas metálicas constituyen el corazón físico de la industria moderna, pero también su cerebro digital. Son sistemas ciberfísicos complejos, capaces de transformar una materia prima en un componente de alta precisión bajo condiciones controladas, conectadas y optimizadas. Su papel va mucho más allá de dar forma al metal: definen la capacidad de innovación, adaptación y competitividad de las empresas que las operan. En una economía global donde la rapidez, la personalización y la sostenibilidad son tan importantes como el precio, estas máquinas son el instrumento clave para mantener el ritmo, responder al mercado y construir, pieza a pieza, el futuro de la producción industrial.
En esta misma línea de evolución tecnológica, las máquinas de fabricación de piezas metálicas están siendo diseñadas no solo para cumplir con los estándares actuales de producción, sino también para anticiparse a los desafíos futuros. Uno de los enfoques más significativos es la implementación de sistemas de inteligencia artificial dentro de las propias máquinas, que permiten la toma de decisiones autónoma basándose en el análisis de grandes volúmenes de datos operativos. Estas capacidades no solo elevan la productividad y reducen errores, sino que también permiten a la máquina aprender patrones de desgaste, variaciones de materia prima y fluctuaciones en el entorno de trabajo, ajustando automáticamente sus parámetros para mantener el rendimiento óptimo sin necesidad de intervención constante.
En paralelo, el concepto de fabricación flexible ha cobrado fuerza. A diferencia de las plantas tradicionales orientadas a la producción en masa, las nuevas configuraciones permiten cambiar rápidamente entre lotes de productos distintos, con mínimas o nulas reconfiguraciones mecánicas. Esta flexibilidad se logra a través de tecnologías como los sistemas modulares, los cabezales intercambiables automatizados, las estaciones de trabajo reprogramables y la automatización adaptativa. Por ejemplo, un mismo centro de mecanizado puede, en cuestión de minutos, pasar de fabricar componentes para sistemas hidráulicos industriales a producir piezas personalizadas para el sector médico, simplemente cargando un nuevo programa y ejecutando una calibración automática.
Otro aspecto crucial es la sostenibilidad en la fabricación metálica. Las nuevas generaciones de máquinas no solo se centran en producir más rápido o con mayor precisión, sino también con una menor huella ambiental. Los sistemas de refrigeración están siendo rediseñados para minimizar el consumo de agua y emplear fluidos biodegradables. La recuperación de calor residual para reutilización energética dentro de la misma planta es otra tendencia que ha comenzado a implementarse. Asimismo, los residuos metálicos generados por arranque de viruta son separados, comprimidos y reciclados de manera automatizada para reincorporarlos en procesos de fundición, cerrando el ciclo de utilización del material.
El diseño de las propias piezas también se está viendo influenciado por las capacidades de estas máquinas. Gracias a la posibilidad de fabricar geometrías antes imposibles —como estructuras con retículas internas, canales internos de refrigeración, superficies con curvaturas múltiples o ensamblajes sin soldadura— los ingenieros están liberados de muchas de las restricciones que antes imponían los métodos tradicionales. Esto ha dado lugar a piezas más ligeras, más resistentes, con menos puntos de falla, y mejor adaptadas a su función específica, lo que en última instancia se traduce en productos finales más competitivos, más seguros y con un mejor comportamiento en servicio.
La interacción entre la fabricación de piezas metálicas y el mundo digital continúa intensificándose a través del uso de gemelos digitales (digital twins). Cada pieza que pasa por la máquina puede tener su equivalente virtual, donde se simula su comportamiento estructural, térmico y dinámico incluso antes de su fabricación. Esta capacidad permite validar diseños, predecir el comportamiento bajo carga, reducir errores en prototipos y mejorar el desarrollo de producto. En muchos casos, estas simulaciones están conectadas directamente con la máquina, que adapta sus movimientos, fuerzas o trayectorias en tiempo real en función del comportamiento previsto del material y de la pieza.
Finalmente, no puede dejarse de lado el papel fundamental que juegan los sistemas de seguridad integrados. A medida que las máquinas se hacen más potentes y autónomas, también deben garantizar un entorno de trabajo seguro para el operario humano que las supervisa o mantiene. Sensores de presencia, barreras fotoeléctricas, protocolos de parada de emergencia inteligentes y análisis continuo del estado estructural de la máquina son parte del nuevo estándar de diseño. Estas funciones no solo protegen a las personas, sino que también prolongan la vida útil del equipo al detectar posibles fallos antes de que ocurran.
En conjunto, el panorama de las máquinas para la fabricación de piezas metálicas se está configurando como un entorno cada vez más sofisticado, donde mecánica, electrónica, software e inteligencia artificial convergen para redefinir los límites de lo que puede hacerse con el metal. Esta transformación no es superficial, sino estructural: cambia los procesos, los tiempos, los costos, las exigencias de personal, las posibilidades del diseño y las capacidades del producto final. En esta transformación, las máquinas no son solo herramientas de producción, sino actores inteligentes dentro de un sistema que aprende, optimiza y evoluciona de forma constante. Así, lo que antes era un taller de manufactura hoy se convierte en un entorno industrial ciberfísico, automatizado, flexible y adaptado al ritmo vertiginoso de la innovación global.
Sistemas de conformado de materiales metálicos
Los sistemas de conformado de materiales metálicos representan un conjunto complejo e interconectado de procesos, tecnologías y equipos cuyo objetivo es transformar metales en formas útiles sin eliminar material, sino modificando su geometría mediante deformación plástica controlada. Este tipo de sistemas son esenciales en la fabricación moderna, ya que permiten obtener piezas con alta integridad estructural, aprovechamiento eficiente del material y reducción de procesos secundarios como el mecanizado o el ensamblaje. A medida que la ingeniería avanza, estos sistemas se vuelven cada vez más versátiles, automatizados y precisos, adaptándose a las exigencias de industrias tan diversas como la automotriz, aeroespacial, energética, médica y de bienes de consumo duradero.
En el núcleo de los sistemas de conformado se encuentra el principio de trabajar el metal en estado sólido, llevándolo a deformaciones permanentes mediante esfuerzos superiores a su límite elástico pero sin llegar a su punto de fractura. Esto requiere un control riguroso de parámetros como fuerza, velocidad, temperatura, fricción y resistencia del material. Las tecnologías más representativas incluyen el embutido profundo, la extrusión, el laminado, el estirado, el forjado, el plegado y el rolado, cada una con sus variantes y aplicaciones específicas según la forma final deseada, las propiedades mecánicas requeridas y el tipo de metal a utilizar.
En los sistemas de embutido profundo, por ejemplo, se transforma una lámina metálica en una pieza hueca cerrada como una carcasa, un recipiente o un cuerpo cilíndrico, mediante la acción combinada de un punzón y una matriz, junto con un cojín o retentor que controla el flujo del material. El éxito de este proceso depende del equilibrio perfecto entre la presión ejercida, la lubricación, el espesor inicial de la chapa y su capacidad de alargamiento sin desgarrarse. En los sistemas avanzados, todo esto se regula mediante sensores y controles numéricos que adaptan el ciclo a las condiciones reales del material durante cada embutido.
Por otro lado, en el laminado se utiliza un sistema de rodillos que presionan el metal para reducir su espesor o cambiar su sección transversal, produciendo chapas, cintas, perfiles o placas con tolerancias muy ajustadas. Este proceso puede realizarse en frío o en caliente, según las propiedades deseadas y la aleación trabajada. En las líneas modernas de laminación, los rodillos están asistidos por actuadores hidráulicos de alta precisión, sistemas de refrigeración controlada, sensores de espesor en línea y algoritmos de corrección automática que ajustan la separación entre cilindros en función de la expansión térmica y la carga ejercida.
Los sistemas de extrusión metálica, aunque más frecuentes en la fabricación de perfiles de aluminio, también se utilizan en aceros, cobres y titanios. Aquí, el material es empujado a través de una matriz con la forma deseada, dando lugar a perfiles macizos o huecos con geometrías complejas y longitud continua. La precisión dimensional, la homogeneidad del flujo del metal y la integridad superficial se controlan mediante variables como la velocidad de extrusión, la temperatura de trabajo, la presión y la calidad del material previo. Las plantas de extrusión modernas integran hornos de calentamiento por inducción, sistemas de control de presión multizona y seguimiento por visión artificial para garantizar un proceso estable y repetible.
En cuanto al forjado, los sistemas de conformado trabajan con matrices abiertas o cerradas y aplican esfuerzos de compresión, obteniendo piezas macizas de gran resistencia mecánica, como bielas, engranajes, ruedas o ejes. El forjado puede realizarse en frío, semicaliente o caliente, y las máquinas que lo ejecutan —prensas de impacto, de tornillo o hidráulicas— están dotadas de sistemas de lubricación automatizada, monitoreo térmico y control de trayectoria que aseguran un llenado óptimo de la cavidad sin defectos internos ni rebabas innecesarias. Además, los sistemas modernos de forjado incluyen simulaciones numéricas que predicen la fluencia del metal, el desgaste de herramientas y las tensiones residuales en la pieza final.
Otro tipo esencial es el sistema de estirado de alambre o tubo, donde el material pasa por una serie de dados que reducen progresivamente su sección mientras aumentan su longitud. Estos sistemas se emplean para fabricar cables de alta resistencia, conductores eléctricos, resortes o tubos estructurales. La precisión geométrica, la limpieza superficial y la ausencia de defectos se aseguran mediante lubricación controlada, tensado automático, alineación con láser y sistemas de inspección continua por ultrasonido o corrientes inducidas.
En todos estos sistemas, la tendencia actual es la integración total con tecnologías digitales. Las máquinas de conformado ahora funcionan bajo control CNC, con ajustes automáticos de parámetros en función de las propiedades detectadas del material o los datos históricos de producción. Esto permite implementar un enfoque de producción inteligente, donde cada operación queda registrada, evaluada y optimizada en tiempo real. El uso de sensores distribuidos, plataformas IoT industriales y sistemas de análisis predictivo permite mantener un control estricto sobre la calidad del producto, detectar desviaciones en el proceso y evitar tiempos muertos o defectos costosos.
La automatización y robotización son también elementos claves en los sistemas de conformado actuales. Robots colaborativos se encargan de cargar y descargar piezas, girarlas entre operaciones, controlar herramientas, cambiar matrices y realizar inspecciones dimensionales sin detener la línea. Estos sistemas no solo aumentan la productividad y reducen el trabajo manual, sino que también eliminan errores humanos, mejoran la seguridad y permiten operar en entornos de alta demanda sin comprometer la calidad.
Finalmente, un aspecto cada vez más importante en los sistemas de conformado es la sostenibilidad. La eficiencia energética, la reducción del desperdicio, la reutilización de calor y el reciclaje de fluidos de proceso son ya prioridades de diseño. Los fabricantes de equipos están desarrollando sistemas que minimizan el uso de recursos, aplican únicamente la fuerza necesaria y ofrecen modos de espera o recuperación de energía para reducir el consumo eléctrico en períodos de inactividad. Esto convierte a los sistemas de conformado no solo en herramientas de producción de alto rendimiento, sino también en actores clave de una manufactura responsable y orientada al futuro.
En conjunto, los sistemas de conformado de materiales metálicos son estructuras tecnológicas complejas, interactivas y cada vez más inteligentes, capaces de responder con precisión a los desafíos actuales de la producción industrial. Su integración con el diseño, la automatización, la digitalización y la sostenibilidad los convierte en el corazón operativo de la industria metálica avanzada, donde cada pieza formada es el resultado de una interacción entre fuerza, conocimiento, datos y eficiencia.
Los sistemas de conformado de materiales metálicos han experimentado un desarrollo notable gracias a la integración de múltiples disciplinas tecnológicas, transformándose en complejas cadenas de producción capaces de generar piezas con características específicas y propiedades mecánicas optimizadas. Este avance no solo se basa en la mejora de las máquinas individuales, sino en la sinergia entre diseño de producto, análisis de materiales, simulación numérica, control automatizado y gestión integral de procesos. La transición hacia sistemas inteligentes ha permitido que el conformado deje de ser un simple proceso mecánico para convertirse en una operación multidimensional donde intervienen variables físicas, químicas y digitales coordinadas de manera precisa.
Un factor determinante en esta evolución es la capacidad de simular digitalmente el comportamiento del material durante el conformado. Las herramientas de simulación por elementos finitos permiten prever cómo el metal reaccionará frente a diferentes cargas, velocidades, temperaturas y condiciones de contacto, identificando posibles zonas de defectos como arrugas, grietas o espesores insuficientes antes de iniciar la producción física. Esto permite optimizar el diseño de matrices y herramientas, ajustar los parámetros del proceso y prever modificaciones en la geometría de la pieza para evitar reprocesos o desperdicios. El resultado es una reducción significativa en el tiempo y costo de desarrollo, así como un aumento en la calidad y fiabilidad de las piezas fabricadas.
Además, la incorporación de sensores distribuidos en las herramientas y matrices ha abierto un nuevo campo para la monitorización en tiempo real de las condiciones de trabajo. Sensores de presión, temperatura, desgaste y vibraciones integrados en puntos estratégicos proporcionan datos continuos durante cada ciclo de conformado, que son analizados por sistemas de control para realizar ajustes automáticos o alertar sobre posibles fallos inminentes. Esta capacidad es fundamental para mantener la estabilidad del proceso en materiales con comportamiento variable, como las aleaciones de alta resistencia o los metales ultrafinos, y para extender la vida útil de las herramientas mediante el mantenimiento predictivo.
Los sistemas de conformado modernos también se benefician enormemente de la modularidad y la flexibilidad. En lugar de máquinas monolíticas diseñadas para una sola operación o tipo de pieza, se utilizan estaciones modulares que pueden ser reconfiguradas rápidamente, combinadas en diferentes secuencias y equipadas con diferentes herramientas según las necesidades del producto. Esto permite fabricar lotes pequeños, personalizados o con diseños cambiantes sin la penalización tradicional en tiempos de setup o inversión en utillajes costosos. A su vez, estos sistemas se integran en líneas automatizadas que incorporan robots para la manipulación de piezas, sistemas de visión para inspección y feedback, y plataformas de control centralizado que coordinan toda la producción.
En cuanto a los procesos específicos, la tendencia hacia la fabricación de piezas más ligeras y resistentes ha impulsado el desarrollo de técnicas avanzadas como el conformado incremental, donde se deforma el metal de manera localizada y progresiva, reduciendo los esfuerzos globales y evitando defectos estructurales. Este método, junto con el uso de láminas y aleaciones de alta tecnología, permite obtener geometrías complejas que anteriormente solo podían lograrse mediante costosos procesos de soldadura o ensamblaje. La combinación de conformado incremental con máquinas CNC permite un control exquisito del proceso y abre nuevas posibilidades para la producción industrial en sectores como la automoción y la aeronáutica, donde el peso y la resistencia son críticos.
El control de la fricción y la lubricación es otro aspecto fundamental en estos sistemas, ya que influyen directamente en la calidad superficial, el consumo energético y la vida útil de las herramientas. La selección de lubricantes, la aplicación precisa mediante sistemas automatizados y la gestión de residuos lubricantes forman parte integral del diseño de un sistema de conformado eficiente y sostenible. Recientemente, se están desarrollando lubricantes ecológicos y técnicas de lubricación en estado sólido que minimizan el impacto ambiental sin sacrificar el rendimiento, alineándose con las crecientes demandas de producción responsable.
Adicionalmente, el avance en materiales compuestos y recubrimientos para matrices y herramientas ha mejorado notablemente su resistencia al desgaste, la corrosión y las altas temperaturas, permitiendo operar en condiciones extremas con menor mantenimiento y mayor calidad de las piezas conformadas. La aplicación de recubrimientos como nitruro de titanio, carbono amorfo o recubrimientos cerámicos se ha convertido en un estándar en la fabricación de utillajes, incrementando la productividad y reduciendo costos operativos a largo plazo.
La digitalización del proceso también ha potenciado la trazabilidad y la certificación de las piezas fabricadas. Cada pieza conformada puede ser asociada a un código único que registra no solo sus dimensiones, sino también los parámetros exactos del proceso, las condiciones ambientales, la vida útil de las herramientas y los resultados de inspección. Esta información es clave en industrias reguladas, donde la garantía de calidad debe estar respaldada por datos detallados y verificables, y permite implementar estrategias de mejora continua basadas en análisis estadísticos y aprendizaje automático.
Por último, la capacitación y formación del personal que opera estos sistemas ha evolucionado paralelamente, incorporando simuladores virtuales, realidad aumentada y plataformas interactivas que permiten un aprendizaje más seguro, rápido y efectivo. Los operarios pueden practicar la configuración, operación y mantenimiento de las máquinas en entornos digitales antes de intervenir físicamente, reduciendo errores y tiempos de capacitación. Además, la cooperación entre humanos y robots, conocida como cobotización, permite una colaboración segura y eficiente donde cada parte aporta sus fortalezas: la precisión y repetitividad de la máquina junto con la capacidad de supervisión, interpretación y resolución de problemas del ser humano.
En conjunto, los sistemas de conformado de materiales metálicos configuran una infraestructura tecnológica avanzada, dinámica y multidisciplinaria, que permite a la industria moderna responder con eficacia a las exigencias crecientes de calidad, eficiencia, personalización y sostenibilidad. Su evolución continúa marcando el ritmo de innovación en la manufactura metálica, consolidándose como un pilar fundamental para el desarrollo de nuevos productos y la competitividad global.
La evolución constante de los sistemas de conformado de materiales metálicos también ha impulsado la incorporación de nuevas tecnologías emergentes que potencian la capacidad de producción y la calidad de las piezas fabricadas. Entre estas innovaciones destacan el uso de la inteligencia artificial (IA) para la optimización de procesos, el aprendizaje automático para la predicción de fallos y la adaptación dinámica de parámetros, así como la aplicación de tecnologías de realidad aumentada y virtual para el diseño, simulación y entrenamiento. La IA puede analizar grandes volúmenes de datos generados por sensores instalados en máquinas y herramientas para detectar patrones sutiles que anticipan problemas o para ajustar los procesos en tiempo real, mejorando la precisión y minimizando rechazos o retrabajos.
Otro aspecto relevante es la tendencia hacia la fabricación aditiva híbrida, donde los sistemas de conformado tradicionales se combinan con tecnologías de impresión 3D metálica para complementar piezas, reparar componentes o fabricar geometrías imposibles de obtener por métodos convencionales. Este enfoque híbrido permite aprovechar lo mejor de ambos mundos: la rapidez y eficiencia del conformado y la libertad geométrica de la fabricación aditiva. Por ejemplo, en la industria aeroespacial se están desarrollando piezas conformadas que luego son reforzadas mediante deposición láser para optimizar su resistencia y peso.
La integración de la automatización robótica avanzada también juega un papel crucial en la modernización de los sistemas de conformado. Robots multifuncionales se encargan no solo de manipular materiales y piezas entre estaciones, sino también de realizar inspecciones no destructivas mediante técnicas como ultrasonidos, termografía o visión artificial, garantizando la calidad sin detener la producción. Estos robots trabajan en entornos colaborativos, interactuando con operarios y ajustándose a las variaciones del proceso mediante algoritmos de inteligencia artificial, lo que incrementa la flexibilidad y seguridad de las plantas.
En cuanto a la sostenibilidad, los sistemas de conformado han adoptado estrategias integrales que incluyen la optimización del consumo energético, el reciclaje de materiales y la reducción del impacto ambiental de los fluidos de proceso. Las máquinas actuales incorporan sistemas de recuperación energética que aprovechan la energía generada en frenadas o en ciclos de baja carga, transformándola en electricidad para alimentar otros procesos. Asimismo, la gestión inteligente de lubricantes y refrigerantes permite minimizar su uso y facilitar su tratamiento y reutilización, contribuyendo a una manufactura más limpia y responsable.
La digitalización completa de la cadena de conformado facilita también la personalización masiva, donde piezas adaptadas a necesidades específicas pueden fabricarse sin incrementar los costos o tiempos de producción significativamente. Esto es posible gracias a la combinación de diseño asistido por computadora, fabricación flexible y sistemas inteligentes de control que permiten cambiar parámetros y herramientas rápidamente. En sectores como el médico, automotriz o de bienes de consumo, esta capacidad se traduce en productos más funcionales, adaptados ergonómicamente y con ciclos de vida optimizados.
Finalmente, el futuro de los sistemas de conformado metálico apunta hacia una integración aún mayor con tecnologías emergentes como la computación cuántica, que podría revolucionar la simulación y optimización de procesos; la nanotecnología, que permitirá tratamientos superficiales y mejoras en materiales a escala molecular; y la conectividad 5G o superior, que garantizará una comunicación instantánea y segura entre máquinas, sensores y plataformas de gestión en tiempo real. Estos avances prometen llevar la manufactura metálica a niveles de eficiencia, precisión y adaptabilidad nunca antes vistos, consolidando su papel como motor fundamental de la industria global y la innovación tecnológica.
Equipos de embutición
Los equipos de embutición son máquinas diseñadas específicamente para conformar láminas metálicas en piezas huecas o con formas tridimensionales mediante un proceso de deformación plástica controlada, conocido como embutición. Este proceso es fundamental en la fabricación de componentes para diversas industrias como la automotriz, electrodomésticos, envases metálicos, construcción y aeroespacial, debido a su capacidad para producir piezas con alta precisión dimensional, buen acabado superficial y resistencia estructural sin necesidad de unir partes mediante soldadura o ensamblaje.
El núcleo de un equipo de embutición consiste en un conjunto de elementos principales: un punzón que aplica la fuerza sobre la lámina metálica, una matriz que define la forma externa del producto y un anillo o cojín que controla el flujo del material durante la deformación. La lámina metálica, generalmente en forma de disco o blank, se coloca entre estos componentes y, al accionar el punzón, el material se desplaza y se adapta a la cavidad de la matriz, formando la pieza deseada. La coordinación precisa entre la fuerza aplicada, la velocidad de avance, la presión del cojín y las condiciones de lubricación es clave para evitar defectos comunes como arrugas, grietas o espesores irregulares.
Existen diferentes tipos de equipos de embutición, clasificados según su capacidad, mecanismo de acción y grado de automatización. Las prensas hidráulicas para embutición son las más comunes en procesos que requieren grandes fuerzas y control fino de la presión. Estas máquinas utilizan sistemas hidráulicos para aplicar fuerzas elevadas y regulables, permitiendo una deformación uniforme y controlada, especialmente útil en piezas con geometrías complejas o materiales de alta resistencia. Por otro lado, las prensas mecánicas funcionan mediante un sistema de excéntrica o volante que transforma el movimiento rotativo en movimiento lineal, ofreciendo ciclos rápidos y alta repetitividad, siendo más adecuadas para producciones en masa con piezas de geometría relativamente sencilla.
Los equipos de embutición modernos incorporan sistemas de control numérico (CNC) y automatización avanzada que permiten programar parámetros específicos para cada tipo de pieza y material, ajustando en tiempo real la fuerza, la velocidad y la presión ejercida. Además, la integración de sensores de presión, deformación y temperatura facilita la monitorización continua del proceso, detectando posibles desviaciones y corrigiéndolas automáticamente para garantizar la calidad y reducir el desperdicio de material. En plantas industriales avanzadas, estos sistemas están integrados en líneas de producción automatizadas donde robots realizan la carga y descarga de blank, inspección y transporte de piezas.
Otro componente importante dentro de los equipos de embutición es el sistema de lubricación, que minimiza la fricción entre la lámina y las herramientas, favoreciendo el desplazamiento del material y previniendo el desgaste prematuro de matrices y punzones. Los lubricantes deben ser seleccionados cuidadosamente para cada tipo de metal y proceso, y su aplicación puede ser manual, por aspersión o mediante sistemas automatizados que controlan la cantidad y distribución exacta del fluido.
Además, los equipos de embutición pueden estar diseñados para realizar procesos complementarios como el rebordeado, el troquelado o el recorte de piezas, integrando diferentes etapas de fabricación en una sola máquina o línea, lo que aumenta la eficiencia y reduce los tiempos de producción. Esta modularidad es especialmente valiosa en industrias con alta demanda de piezas complejas y con requisitos estrictos de calidad y trazabilidad.
En términos de capacidad, los equipos de embutición varían desde máquinas pequeñas, utilizadas en talleres o para prototipos, hasta prensas de alta tonelaje capaces de aplicar fuerzas de cientos o miles de toneladas para embutir materiales gruesos o aleaciones difíciles. La selección del equipo adecuado depende del tipo de material, el espesor de la lámina, la geometría de la pieza y el volumen de producción esperado.
En resumen, los equipos de embutición son elementos tecnológicos fundamentales en la manufactura metálica, que combinan mecánica, hidráulica, automatización y control avanzado para transformar láminas metálicas en piezas funcionales con alta precisión y calidad. Su continua evolución, impulsada por la demanda de eficiencia, flexibilidad y sostenibilidad, los posiciona como pilares esenciales en la industria moderna, capaces de responder a los retos de producción actuales y futuros.
Los equipos de embutición constituyen una parte fundamental de la industria metalúrgica y de manufactura, dada su capacidad para transformar láminas metálicas planas en piezas tridimensionales complejas con alta precisión y repetibilidad. La embutición es un proceso que, aunque tiene raíces históricas profundas, ha evolucionado con la incorporación de tecnologías avanzadas que mejoran su desempeño, eficiencia y calidad de producto. Estos equipos se caracterizan por ser sistemas robustos, diseñados para soportar grandes cargas y operar con ciclos rápidos, integrando elementos mecánicos, hidráulicos, electrónicos y software de control que trabajan en perfecta armonía para lograr resultados óptimos.
El proceso de embutición en sí mismo requiere de un control minucioso de múltiples variables simultáneas, entre ellas la fuerza aplicada por el punzón, la presión del cojín que modera el flujo del metal, la lubricación para minimizar la fricción, la velocidad de desplazamiento y la temperatura, especialmente cuando se trabajan aleaciones que requieren conformado en caliente. Los equipos modernos incorporan sensores distribuidos en puntos clave que recopilan información en tiempo real, permitiendo que el sistema de control adapte automáticamente los parámetros de operación. Esto es especialmente crucial para evitar defectos comunes como arrugas, desgarros o distorsiones dimensionales, que pueden originar pérdidas económicas importantes.
Las prensas hidráulicas para embutición son especialmente valoradas por su capacidad para ejercer fuerzas regulables y mantener la presión constante durante el ciclo, lo que asegura una deformación uniforme y la posibilidad de manejar geometrías complejas o materiales con comportamiento no lineal. Estas máquinas utilizan bombas de alta presión, válvulas proporcionales y acumuladores que permiten ajustar con gran precisión la velocidad y fuerza del punzón, lo que también se traduce en un mejor aprovechamiento energético. En contraparte, las prensas mecánicas, aunque menos flexibles en cuanto a ajuste de presión, ofrecen ciclos de trabajo extremadamente rápidos y son ideales para producciones masivas donde la geometría de la pieza es sencilla y el material es relativamente dúctil.
Un aspecto innovador en los equipos de embutición es la integración de sistemas CNC que no solo controlan la trayectoria y la fuerza aplicada, sino que también pueden almacenar perfiles de embutición para múltiples piezas, permitiendo una rápida reprogramación y cambios entre lotes sin necesidad de intervenciones mecánicas extensas. Estos sistemas trabajan en conjunto con interfaces de usuario amigables, donde el operario puede supervisar el proceso mediante gráficos en tiempo real, alarmas y reportes automáticos, facilitando la toma de decisiones y la optimización continua del proceso.
El sistema de lubricación es otro componente esencial que ha evolucionado considerablemente. Más allá de la simple aplicación manual o por aspersión, los equipos modernos cuentan con sistemas automatizados que dosifican la cantidad exacta de lubricante necesario, aplicándolo en zonas críticas con precisión milimétrica. Esto reduce el consumo de lubricantes, minimiza la contaminación ambiental y mejora la calidad superficial de las piezas. Además, se están explorando lubricantes ecológicos y técnicas de lubricación en seco o con recubrimientos especiales para disminuir el impacto ambiental y mejorar la eficiencia del proceso.
En cuanto a la capacidad de integración, muchos equipos de embutición forman parte de líneas de producción completamente automatizadas, donde robots colaborativos realizan la carga y descarga de blank, la transferencia entre estaciones de trabajo, la inspección dimensional mediante visión artificial y el embalaje final. Esta automatización reduce la intervención humana, aumenta la seguridad operativa y asegura una mayor consistencia en la calidad del producto. La trazabilidad completa se logra mediante sistemas de marcado y registro digital que documentan cada pieza, facilitando la gestión de calidad y la respuesta rápida ante cualquier incidencia.
Los avances en materiales y tecnología también han permitido que los equipos de embutición puedan trabajar con aleaciones avanzadas, como aceros de alta resistencia, aluminio aeronáutico, titanio y magnesio, que requieren condiciones específicas para evitar fallos durante la deformación. Para estos casos, algunas máquinas incorporan sistemas de calentamiento o enfriamiento localizados, que permiten conformar el material en condiciones térmicas óptimas, extendiendo la vida útil de las herramientas y mejorando las propiedades mecánicas de las piezas terminadas.
Finalmente, la evolución de los equipos de embutición se orienta cada vez más hacia la sostenibilidad y la eficiencia energética. Los fabricantes están desarrollando sistemas hidráulicos con bombas de velocidad variable, recuperación energética en fases de frenado y modos de operación inteligente que adaptan el consumo eléctrico según la demanda real. Asimismo, la reducción de desperdicios de material, el reciclaje interno de recortes y la optimización del ciclo productivo contribuyen a minimizar el impacto ambiental y los costos asociados, alineándose con los objetivos globales de manufactura responsable.
En resumen, los equipos de embutición son sistemas complejos y sofisticados que combinan tecnología mecánica, hidráulica, electrónica y digital para transformar materia prima metálica en piezas funcionales de alta calidad y precisión. Su desarrollo continuo responde a la necesidad de la industria de contar con soluciones flexibles, eficientes, sostenibles y adaptadas a las exigencias crecientes de producción y personalización en un mercado globalizado y competitivo.
La evolución de los equipos de embutición también ha venido acompañada de importantes avances en el diseño y fabricación de las herramientas y matrices que intervienen directamente en el proceso. Estas herramientas deben soportar grandes esfuerzos y desgaste, mantener tolerancias estrictas y garantizar un contacto uniforme con la lámina metálica para evitar defectos en las piezas finales. Para ello, se emplean materiales de alta dureza y resistencia al desgaste, como aceros aleados tratados térmicamente, con recubrimientos superficiales avanzados —por ejemplo, nitruro de titanio, carbono amorfo o recubrimientos cerámicos— que prolongan su vida útil y mejoran el rendimiento durante el proceso.
El diseño de matrices ha incorporado asimismo la simulación digital, permitiendo predecir con exactitud cómo se comportará el metal durante la embutición y cómo distribuir las tensiones en la herramienta para evitar puntos críticos de fallo o desgaste prematuro. Gracias a la simulación por elementos finitos y otros métodos numéricos, es posible optimizar la geometría de la matriz, el ángulo de los radios, la distribución de fuerzas y los tiempos de ciclo, lo que reduce la necesidad de prototipos físicos y acorta los tiempos de desarrollo.
En líneas de producción automatizadas, los sistemas de cambio rápido de matrices permiten reducir significativamente los tiempos muertos entre diferentes series o tipos de piezas. Estos sistemas están diseñados para que un operador o un robot pueda desmontar e instalar matrices en cuestión de minutos, lo que aporta gran flexibilidad a la producción y permite responder con agilidad a cambios en la demanda o en el diseño del producto.
La integración de tecnología de visión artificial es otra innovación clave en los equipos de embutición modernos. Cámaras y sensores ópticos inspeccionan continuamente las piezas durante y después del proceso, verificando dimensiones, detectando defectos superficiales, controlando la alineación y asegurando la conformidad con las especificaciones. Estos sistemas pueden intervenir en tiempo real, señalando alertas al operador o incluso modificando parámetros del proceso para corregir desviaciones antes de que se generen piezas defectuosas.
La ergonomía y seguridad en el diseño de estos equipos también han recibido gran atención, adaptándose a las normativas internacionales y mejorando las condiciones de trabajo para los operarios. Se incorporan sistemas de protección física como barreras, sensores de proximidad, paradas de emergencia automáticas y controles remotos que permiten manejar las máquinas desde posiciones seguras. La interfaz hombre-máquina está diseñada para ser intuitiva, con paneles táctiles, gráficos claros y retroalimentación instantánea, facilitando la operación, mantenimiento y diagnóstico de fallos.
Desde el punto de vista energético, los avances en los sistemas hidráulicos han permitido desarrollar prensas con bombas de desplazamiento variable y acumuladores que almacenan energía durante las fases de baja demanda para liberarla en picos de fuerza, mejorando la eficiencia energética y reduciendo costos operativos. La incorporación de tecnologías de recuperación y reutilización de energía hace que estos equipos sean cada vez más sostenibles, un aspecto fundamental en la industria actual.
La versatilidad de los equipos de embutición también se refleja en su capacidad para trabajar con una amplia gama de materiales metálicos, desde aceros al carbono hasta aleaciones ligeras de aluminio, cobre, titanio y metales especiales para aplicaciones aeroespaciales o médicas. Cada material presenta desafíos específicos relacionados con su ductilidad, resistencia y comportamiento al deformarse, lo que exige una configuración precisa de la máquina y las herramientas, así como un control estricto de las condiciones del proceso.
Finalmente, la creciente demanda de personalización y producción de lotes pequeños ha llevado al desarrollo de equipos de embutición con capacidades avanzadas de automatización y programación flexible, donde se pueden almacenar múltiples programas de producción, cambiar parámetros y ajustar herramientas sin necesidad de paradas prolongadas. Esta adaptabilidad es clave para que los fabricantes puedan responder rápidamente a los cambios del mercado, reducir tiempos de entrega y ofrecer productos adaptados a requerimientos específicos sin perder competitividad.
En conjunto, los equipos de embutición representan una convergencia de tecnologías mecánicas, hidráulicas, electrónicas y digitales, diseñadas para transformar láminas metálicas en piezas complejas con altos estándares de calidad y eficiencia. Su desarrollo continúa orientado a la mejora constante en precisión, flexibilidad, sostenibilidad y facilidad de operación, consolidándolos como piezas clave en la cadena productiva de la industria metalmecánica contemporánea.
Máquinas Formadoras de Metales EMS
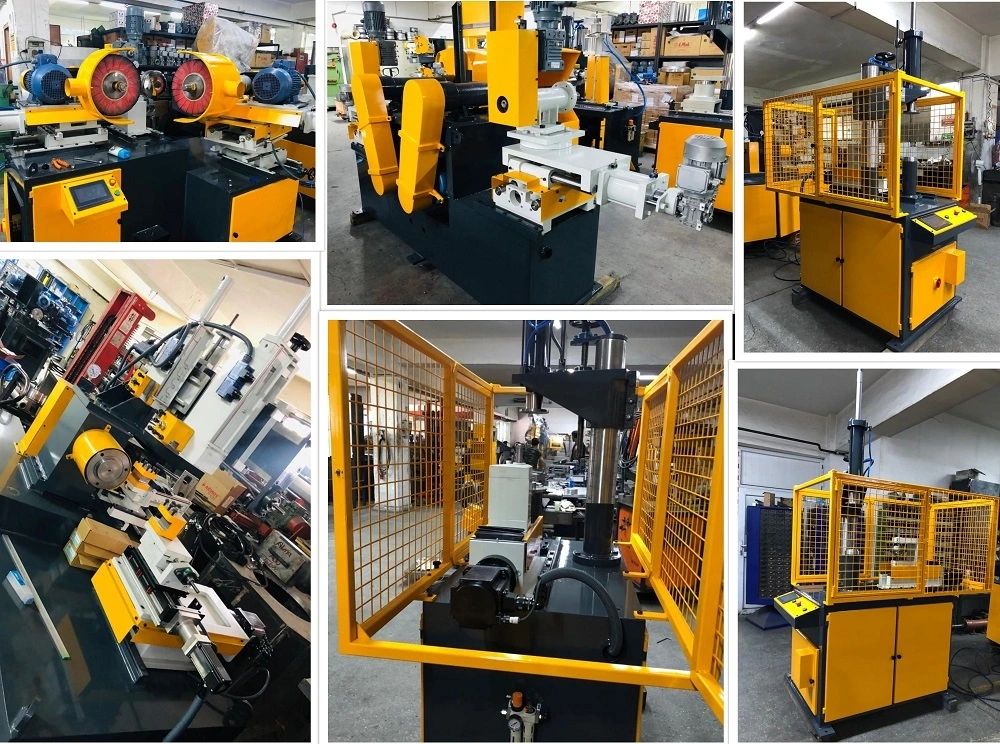
Diseñamos, fabricamos y montamos maquinaria metalmecánica como:
Prensa de transferencia hidráulica
Prensa para mosaicos de vidrio
Prensa hidráulica de embutición profunda
prensa de fundición
Prensa hidráulica de conformado en frío
Prensa de hidroformado
prensa compuesta
Prensa de moldeo de caucho de silicona
Prensa de pastillas de freno
Prensa de melamina
Prensa SMC y BMC
prensa labrotaroy
Máquina cortadora de bordes
Máquina rizadora de bordes
Máquina recortadora de abalorios
Máquina de recorte y jogging
Línea de producción de utensilios de cocina.
Máquina dobladora de tubos
Máquina dobladora de perfiles
Sierra de cinta para metal
Máquina de soldar cilíndrica
Prensas horizontales y utensilios de cocina.
Menaje de cocina, artículos de hotelería
Maquinaria para la producción de utensilios para hornear y cubiertos.
como una línea completa así como una máquina individual como:
Máquinas cortadoras de bordes y biseladoras
Pulidoras y rectificadoras de ollas y sartenes.
Prensas hidráulicas de trefilado
Máquinas troqueladoras circulares
remachadora
Punzonadoras
Máquina de alimentación de prensa
Puede consultar nuestra maquinaria en funcionamiento en: EMS Máquinas Formadoras de Metales EMS – YouTube
Aplicaciones:
Punzonado de bridas
Abalorios y nervaduras
Bridas
Guarnición
Curling
costura de bloqueo
Nervaduras